Тянуще-правильное устройство машины непрерывного литья заготовок
Вид материала | Документы |
Содержание3 Надежность, ремонт и Эксплуатация 3.2 Техническое обслуживание 3.3 План профилактического обслуживания |
- Моделирование и разработка методов расчета процессов теплопередачи в кристаллизаторе, 251.19kb.
- Назовите первое вычислительное устройство, 70.24kb.
- Коммерческое предложение ООО «Технология литья», 38.64kb.
- Комплекс машин для заготовки прессованного сена. Марки машин и их технические характеристики, 8.88kb.
- Учебное пособие Машины непрерывного транспорта: лаб практикум /; Воронеж гос арх строит, 411.42kb.
- План-конспект для проведения занятия по тп с л/с дизелистов. Тема : «Устройство и эксплуатация, 55.25kb.
- План конспект проведения занятия по технической подготовке с личным составом танковой, 374.57kb.
- Лекция 19. Специальные способы литья, 177.96kb.
- Программа вступительного экзамена в магистратуру по специальности 6М080600 аграрная, 36kb.
- 4 Выбор заготовок и способов их изготовления, 1308.48kb.
3 Надежность, ремонт и Эксплуатация
3.1 Надежность
Машина непрерывного литья заготовки представляет собой комплекс последовательно взаимосвязанных механизмов. Эксплуатационная надежность оборудования оценивается вероятностью безотказной работы за промежуток времени без учета простоев в текущие и капитальные ремонты.
Вероятность безотказной работы в периоды между текущими ремонтами одинакова независимо от времени, прошедшего после ремонта. Капитальные ремонты повышают надежность, что свидетельствует о необходимости сокращения текущих ремонтов и повышения эффективности капитальных ремонтов.
Детали и узлы металлургического оборудования, подвергающиеся в процессе эксплуатации действию различных нагрузок, изнашиваются и разрушаются. Разрушение деталей металлургических машин происходит как при превышении внешней нагрузкой уровня предельной статической прочности деталей, так и в результате усталостных разрушений. Размеры внешних нагрузок и параметры прочности являются случайными величинами. Поэтому возможно превышение внешней нагрузкой пределов прочности деталей и их разрушение, несмотря на большие запасы прочности, определенные по средним значениям максимальных нагрузок и характеристик прочности.
Находящееся в эксплуатации механическое оборудование металлургических цехов вследствие постепенного изменения размеров деталей в результате износа, а также поломок при переменных по величине и направлению нагрузок теряет способность выполнять технологические функции.
К основным факторам, оказывающим влияние на надежность и долговечность металлургического оборудования, следует отнести: механические свойства металлов, из которых изготовлены детали, качество их изготовления и конструктивное выполнение, упрочняющую обработку, законы нагружения и условия эксплуатации.
Выход из строя деталей металлургического оборудования происходит в основном по трем причинам: вследствие износа, внезапных поломок и образования и роста усталостных трещин, вызывающих в конце концов поломку детали.
Детали машины непрерывного литья заготовок, работающие при соприкосновении с раскаленным металлом в условиях высоких и быстро меняющихся температур, также подвергаются интенсивному износу. Поверхность прокатных валков выкрашивается вследствие высоких удельных давлений между валком и прокатываемым металлом. Из-за быстрой смены температур на поверхности валков появляется сетка разгара.
Внезапные поломки деталей металлургического оборудования, возникающие от однократных перегрузок, являются, как правило, следствием нарушений технологического режима, вызванных недосмотром технического персонала или несоответствием перерабатываемого сырья предъявляемым к нему требованиям.
В случае поломки детали проводят тщательный анализ причин, вызвавших поломку, изучают вид излома, исследуют макро- и микроструктуру материала и на основе получаемых данных намечают мероприятия по предотвращению поломок.
Анализ изломов является объективным методом, позволяющим оценивать величину перегрузки, концентрацию напряжений, условия развития усталостной трещины и другие особенности разрушения деталей. Он позволяет конструкторам и эксплуатационникам оценивать прочность деталей и предупреждать их поломки.
Условия нагружения, вызвавшие усталостное разрушение, могут быть установлены по таким признакам, как характер излома, глубина развития усталостной трещины, степень и характер наклона поверхности излома, число очагов развития трещины, характер и частота следов линий фронта распространения трещины, число очагов возникновения трещин.
При анализе изломов необходимо учитывать влияние следующих факторов на прочность и вид износа детали: свойства материала, метода изготовления и обработки детали; ее конструктивных особенностей; условий работы и нагружения. Для этого необходимо знать особенности механизма усталостного разрушения и закономерности влияния различных факторов.
Для усталостных изломов характерно наличие в сечении четко выраженных зон разрушения с мелкозернистой, фарфоровидной или шлифованной поверхностью и зоны статического (быстрого) разрушения остальной части сечения с волокнистым строением для вязких металлов или крупнозернистым для хрупких. В соответствии с постепенным развитием разрушения в изломе можно обнаружить следующие характерные зоны: зарождения усталостных трещин (микроскопические и макроскопические локальные места), развития трещин (усталостное разрушение), ускоренного разрушения (переходная зона) и окончательного быстрого разрушения (статический долом).
Характер излома определяется уровнем действующих напряжений: чем выше перегрузка, тем меньше зона усталостного разрушения и больше зона статического разрушения. При больших перегрузках может возникнуть несколько очагов развития трещин, которые затем могут дать несколько зон усталостного разрушения. Блеск поверхности зоны усталостного разрушения увеличивается с уменьшением перегрузок и увеличением числа циклов нагружений до разрушения.
Направление развития трещин зависит от вида напряженного состояния и ориентировки главных напряжений: при растяжении, сжатии и изгибе трещины развиваются на поверхности действия главных нормальных напряжений, а при кручении — сначала в плоскости действия касательных напряжений, а затем в плоскости главных нормальных напряжений. Развивающаяся трещина проникает в глубь сечения, образуя линию фронта ее продвижения. На скорость ее продвижения влияют величина и характер действующих напряжений. По расположению усталостных линий можно приближенно судить о режимах работы детали.
3.2 Техническое обслуживание
Назначение плана технического обслуживания:
- поддержание установок в хорошем рабочем состоянии для обеспечения высокой производительности, высокого качества и нормального соотношения издержек производства.
- предупреждение (по возможности) аварий и остановок.
уменьшение затрачиваемого времени на мелкий ремонт и/или остановку машины (по мере возможностей).
- своевременное и аккуратное профилактическое обслуживание (согласно инструкциям секте, карт) снижает количество вмешательств (ремонта) во время работы машины.
Расчет численности ремонтного персонала
Количество физических единиц –7
Количество ремонтных единиц-988
1) Расчет численности слесарей-ремонтников для выполнения плановых ремонтов (ППР) по МНЛЗ
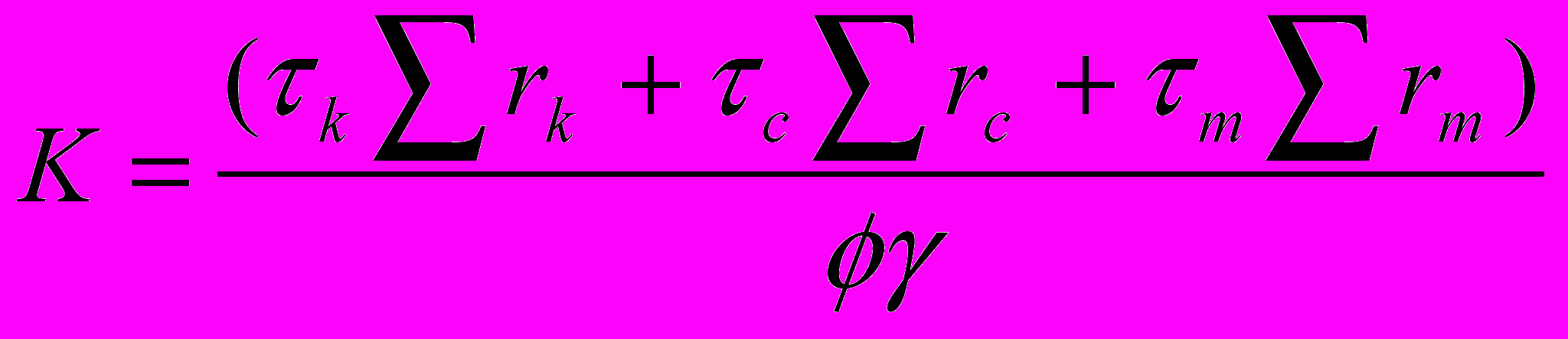

где
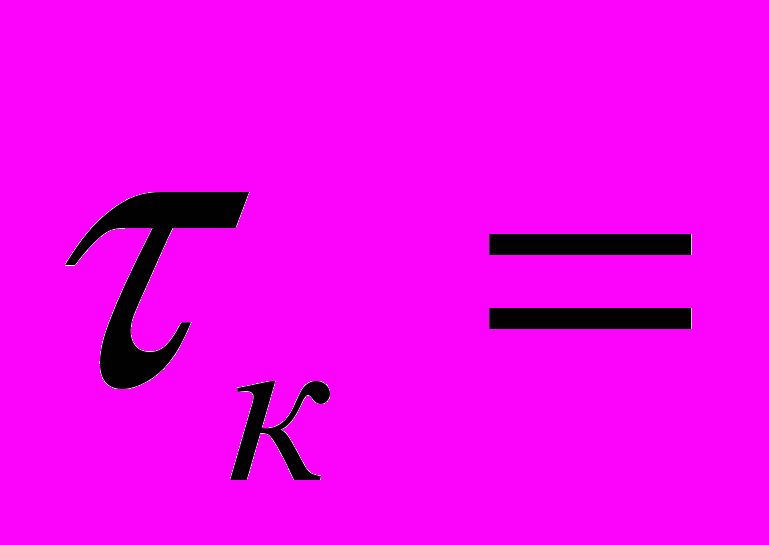
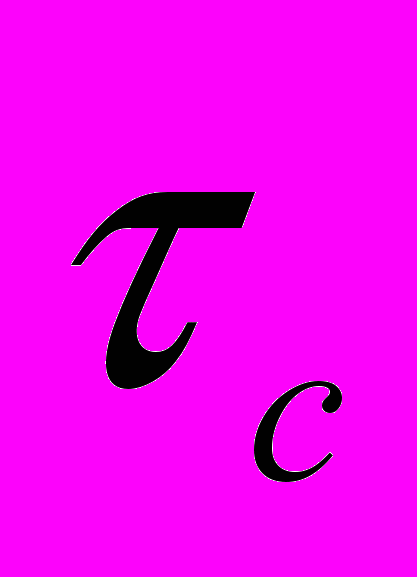
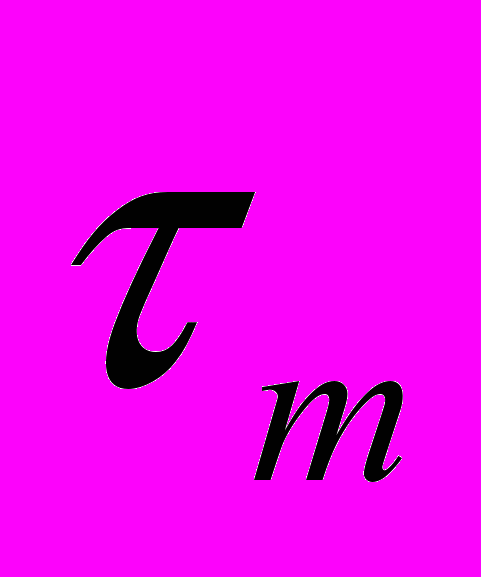
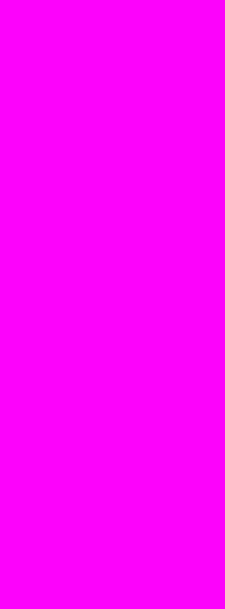
ф- годовой фонд рабочего времени
2) Потребное количество слесарей для межремонтного обслуживания

где Н-норматив межремонтного обслуживания на 1 слесаря в смену
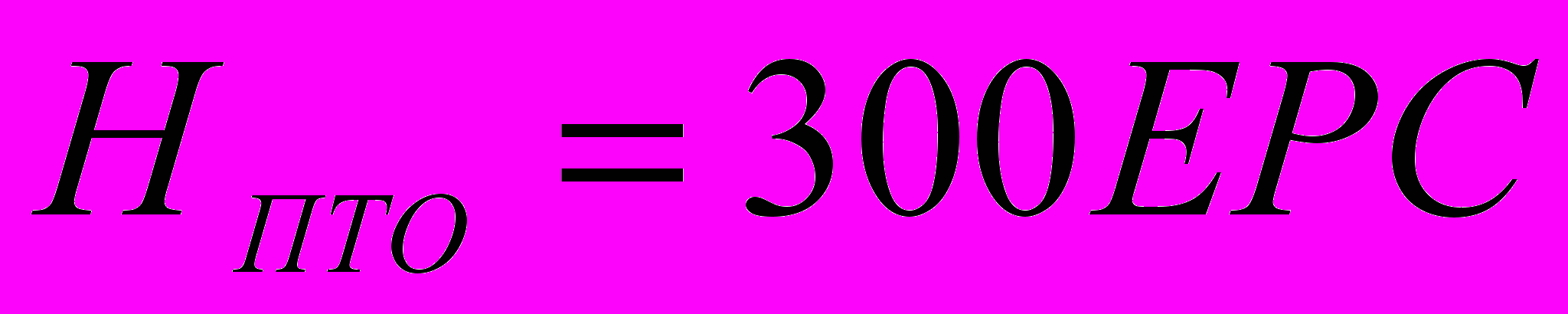
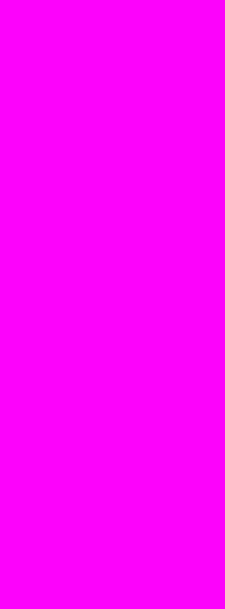
ИТОГО: по МНЛЗ слесарей ремонтников- 29 человек
сменных слесарей –10 человек
В том числе газосварщиков -10% от общего количества
(29+10) ·10%=3,9чел≈4чел
3.3 План профилактического обслуживания
Профилактическое обслуживание включает в себя все проверки и операции, необходимые для обеспечения эффективной работы установки и для предупреждения неполадок и поломок. Выше указанные работы, основанные на опыте и/или теоретических расчетах, заключаются в периодическом контроле и подналадке, для предупреждения дальнейших поломок. Посредством такого контроля проверяется состояние деталей машины. Данные проверки основываются на результатах наблюдения рабочего персонала и "включают" в себя:
- визуальное наблюдение: на предмет утечек жидкостей и вибраций при просачивании газов, трещин, износа и т.д.
- прослушивание: на предмет каких либо подозрительных шумов(скрип, шипение, вибрации.)
- контактный способ: выявление повышенных температур, вибраций, шероховатостей.
Такие проверки и под наладки должны выполняться в соответствии с заранее установленными сроками, как указано в руководстве по профилактическим работам. Эти сроки могут варьироваться в соответствии с эксплуатационным режимом. Все данные об отклонениях и неполадках, должны записываться оператором в специальном журнале.
Увеличение количества проводимых проверок с помощью специальных инструментов (приборов), а также наблюдения персонала, позволяет определить, нужно ли проводить под наладку в настоящее время или отложить эти работы до ближайшей запланированной остановки рабочего цикла.
Карта профилактического технического обслуживания