Конспект лекций Омск 2002 удк 629. 424. 01
Вид материала | Конспект |
2. Технико-экономические последствия низкой 3. Надежность как составляющая качества 4. Краткие сведения из истории развития науки |
- Конспект лекций минск 2011 удк 629., 3872.02kb.
- Краткий конспект лекций Кемерово 2002 удк: 744 (075), 1231.26kb.
- Конспект лекций (для студентов всех форм обучения) Кемерово 2002, 1424.32kb.
- Конспект лекций по дисциплине «психология и педагогика» омск 2005, 2020.42kb.
- Конспект лекций по курсу "Начертательная геометрия и инженерная графика" Кемерово 2002, 786.75kb.
- Конспект лекций Утверждено редакционно-издательским советом университета Омск 2002, 466.51kb.
- Конспект лекций Соответствует государственному образовательному стандарту высшего профессионального, 899.55kb.
- Н. В. Рудаков Краткий курс лекций, 1552.23kb.
- Удк 656 08; 629 072 ббк 52. 5: 88., 1958.04kb.
- Конспект лекций москва 2004 удк 519. 713(075)+519. 76(075) ббк 22. 18я7, 1805.53kb.
Показанный выше рост важности и сложности функций, возлагаемых на создаваемые ТО, вызывает не только усложнение устройства ТО, но и повышение ответственности за своевременное качественное, эффективное выполнение этих функций, что усиливает требования к надежности.
10
С течением времени росли не только количественные показатели «техносферы» (число видов ТО различного назначения и их модификаций, серий-
ность или объем партий одноименных инструментов, машин, аппаратов, систем, сложность или число элементов в них), но и качественные показатели, характеризующие функциональные параметры, влияющие на производительность и эффективность оборудования (мощность, скорость, точность и др.), а также определяющие интенсивность влияния нагрузок и эксплуатируемых машин на их детали (механические и электромагнитные нагрузки, температура и т. п.).
Первые паровые машины, как и первые двигатели внутреннего сгорания, имели мощность в несколько лошадиных сил. В начале века мы гордились первенцем советской энергетики Волховской ГЭС, имевшей мощность
66 тыс. кВт. Построенные через 30 50 лет ГЭС (Красноярская, Саяно-Шушенская и др.) оборудованы большим количеством гидротурбин, каждая из которых превосходит по мощности Волховскую ГЭС более чем в десять раз. В нашей стране освоен выпуск гидротурбин для ГЭС, паровых турбин для ТЭС, АЭС мощностью свыше 1 млн кВт. Мощность двигателей современных космических ракет достигает фантастических величин сотен миллионов киловатт. За семь, восемь десятилетий развития локомотивов и их мощность возросла в 10 15 раз. Например, рост мощности тепловозов с 1924 г. характеризуется так: ТЭ1 1000 л.с., ТЭ2 2000, 2ТЭ3 4000, 2ТЭ10 6000, 2ТЭ121 8000, 2ТЭ136 12000 л. с.
Весьма показателен рост удельной мощности ДВС, приходящейся на единицу массы двигателей различных годов выпуска (табл. 1.5).
Т а б л и ц а 1.5
Удельная мощность ДВС
Годывыпуска | 11900 | 11913 | 11931 | 11953 | 11954 | 11955 | Современный авиационный поршневой | Современный авиационный реактивный |
Удельная мощность, л.с./кг | 00,004 | 00,007 | 00,016 | 00,033 | 00,100 | 00,330 | 0,7 1,2 | 2,0 – 3,5 |
Данные табл. 1.5 показывают, что за 80 90 лет удельная мощность поршневых ДВС возросла в 300 раз, соответственно возросли нагрузки на детали и, конечно, снизился удельный расход металлов.
11
Важнейшими требованиями к современному технологическому оборудованию являются точность обработки деталей и чистота поверхности. Ко-
гда-то Джеймс Уатт с гордостью сообщал, что в его машине между поршнем и цилиндром «нельзя просунуть даже маленький палец». А российский изобретатель И. И. Ползунов, делая первую паровую машину, проверял зазоры в ней екатерининским пятаком, толщина которого достигала 6 мм. В своем наказе тульским оружейникам в 1706 г. Петр I требовал точности производства до «сотых доль нигов» (дюймов). Современные же станки позволяют обрабатывать детали с точностью до микрометров и даже их долей. Так, например, точность геометрических форм отверстий и валов нередко колеблется в пределах 0,5 2,0 мкм, а неконцентричность, непараллельность и неперпендикулярность поверхностей ряда деталей требуется выдержать в пределах 0,6 – 3,0 мкм.
В топливных насосах высокого давления тепловозных дизелей зазор между втулкой и плунжером измеряется в долях микрометра.
Поразительные результаты достигнуты в отношении точности попадания. Точность попадания ракет в цель измеряется несколькими метрами при дальности стрельбы в десятки и сотни километров. Корабль «Вояжер-2» за 12 лет полета к Нептуну, пройдя на расстоянии 5 тыс. км от него, накопил следующие ошибки от расчетных параметров: 30 км расстояния и 1,4 с времени (это при пройденном пути в 4,5 млрд км).
Новые принципы и методы регистрации светового излучения интенсивностью до одного кванта в секунду предложили белорусские ученые. Созданные ими приборы нашли применение в астрофизике, ядерной физике, оптике, электронике, технологии производства микросистем и многих других отраслях науки и техники. В современных приборах, в генной инженерии, в квартовой механике атом вещества стал реальным объектом, который не только изучается, но и перемещается на нужное место по желанию исследователя (речь идет о расстояниях, измеряемых в нанометрах 109 м). В принципе современный силовой атомный микроскоп обладает достаточной чувствительностью для детектирования единичного электрона.
В распоряжении наших ученых и инженеров имеются приборы, измеряющие вес с точностью до двух миллионных долей грамма, температуру до одной стотысячной доли градуса, регистрирующие отклонения силы тока в миллиардные доли ампера, происходящие на протяжении миллионных долей секунды, и столь же быстрые колебания напряжения в стотриллионные доли вольта. Какова же должна быть точность деталей этих приборов? И что полу-
12
чится, если хоть одна деталь не будет удовлетворять крайне жестким требованиям точности? Такой прибор не сможет правильно контролировать технологический процесс. А в результате отказ одной ненадежной детали может привести к выпуску крупной партии негодной продукции или к аварии крупной технической системы.
Скорость является основным функциональным показателем многих современных машин, предназначенных не только для транспортировки грузов и пассажиров, но и для переработки (обработки) материалов, энергии или ин-
формации. И этот показатель ТО в ходе научно-технического прогресса постоянно повышался, особенно в период научно-технической революции XX в.
Так, за период развития авиации скорость самолетов увеличилась более, чем в 100 раз: первые летательные аппараты обладали скоростью не более
40 км/час, а скорость космических кораблей и ракет достигла уже 40 тыс. км/час, что в 1000 раз превышает скорость первых самолетов. Увеличивается скорость движения и подвижного состава наземного транспорта: на отечественных железных дорогах скорость движения грузовых поездов до 100 км/час, пассажирских до 160 км/час, на скоростных участках до 200 250 км/час, на зарубежных высокоскоростных железнодорожных линиях до 450 км/час; для грузовых автомобилей до 100 120 км/час, легковых до 200 250 км/час.
Высокие скорости широко используются и в производстве. Конструктивное и технологическое совершенствование станков позволяет, например, довести число оборотов шпинделя внутришлифовального станка до
120 150 тыс. об/мин. Роторы газотурбинных двигателей имеют частоту вращения до 40 60 тыс. об/мин.
Огромные скорости достигнуты в области переработки информации путем автоматизации этого сложного процесса с помощью компьютеров. Английскому математику Шенксу потребовалось 15 лет, чтобы узнать число «пи» с точностью до 707-го знака. Электронная вычислительная машина (еще образца 60-х гг.) менее чем за одни сутки «выдала» это число с 2048 знаками после запятой, попутно исправив ошибки Шенкса. Проведенные в Институте кибернетики Академии наук УССР исследования показали, что при ручном методе проектирования железной дороги длиной в несколько сотен километров, проходящей по горной местности, решение с нужной точностью лишь одной из частей этой задачи оптимального профилирования потребует не менее 50 лет. Вычислительная машина решает эту задачу за несколько часов.
13
Комплексная автоматизация производственных процессов позволяет достигнуть таких быстроты, точности, постоянства параметров, экономии, которых человек обеспечить не может. В табл. 1.6, 1.7 приведены данные о быстроте
реакции человека на различные раздражители и об ошибках считывания показаний прибора при различных формах шкал. Автоматы могут улавливать то, что недоступно человеку, невидимый свет, неслышимые звуки и многое другое. И, разумеется, они могут это сделать лишь в том случае, если работают надежно, безотказно.
Автоматика является основой дальнейшего научно-технического про-
гресса. Однако чем сложнее и многограннее становятся ее задачи, тем большие требования предъявляются к ее надежности. Уже сейчас внедрение автоматизации в раде случаев тормозится не отсутствием необходимых приборов и устройств, а их недостаточной надежностью. Еще в начале XX в. проблема надежности технических устройств была не такой острой, как сейчас; основной задачей технического прогресса являлось повышение эффективности и производительности машин. В настоящее время, в век небывалой технической революции, перед человечеством открываются возможности почти безграничного развития и совершенствования техники. Поэтому сейчас решающим условием технического прогресса становится проблема обеспечения высокой надежности машин и оборудования, всех технических объектов.
Т а б л и ц а 1.6
Время реакции человека на различные раздражители
Раздражитель | Время, мс |
Зрительный | 150 – 225 |
Слуховой | 120 – 182 |
Температурный | 150 – 240 |
Болевой | 400 – 1000 |
Т а б л и ц а 1.7
Ошибки считывания оператором показаний прибора при различных формах шкал
Форма шкалы | Ошибка, % |
Вертикальная линейка | 35,5 |
Горизонтальная линейка | 27,5 |
Полукруглая | 16,6 |
Круглая | 10,9 |
Окно | 0,5 |
14
Прежде чем излагать инженерную сущность проблемы надежности техники и пути ее решения, нужно взять несколько уроков у природы [1]. Она хороший учитель, ей во многом человек обязан каждым своим достижением. Создатели первых кораблей и подводных лодок изучали строение организма
рыб. Н. Е. Жуковский при разработке теории воздухоплавания изучал полет птиц. И современным создателям машин невредно поучиться у природы создательницы живых организмов, посмотреть, как решается проблема надежности в природе.
Посмотрим с этих позиций на человеческий мозг. Можно смело сказать, что сегодня среди всех творений человеческих рук, среди всех чудес техники нет ничего, что хотя бы приближалось к нему по сложности, экономичности, а главное – по надежности и гибкости работы. Мозг человека состоит примерно из 14 млрд нервных клеток нейронов (а по последним данным немного больше), которые целеустремленно управляют 100 трлн клеток организма. Тело человека имеет 639 мускулов, 206 костей скелета, его костные «шарниры» обладают 105 степенями свободы и всем этим автоматически управляет
наш мозг.
Каждый нейрон, как известно, может находиться либо в возбужденном, либо в заторможенном состоянии, упрощенно его можно уподобить по функциям двухпозиционному реле электромеханического, лампового, транзисторного или другого тока.
Предположим, что необходимо создать электронную машину с количеством элементов релейного действия, соответствующим количеству нейронов, имеющихся в мозге человека. Если бы в качестве таких элементов использовали триггеры на полупроводниковых приборах объемом в 1 см3 каждый и разместили бы их вплотную один к другому, объем такой машины был бы равен примерно новому зданию Московского государственного университета. Для питания такой машины потребовалась бы электростанция мощностью в несколько десятков киловатт, а для ее охлаждения мощная река. А человеческий мозг свободно умещается в черепной коробке, занимая лишь около 1,5 дм3 , потребляет всего несколько ватт и при всем этом выполняет свои сложнейшие функции с поразительной надежностью, которой может позавидовать самое совершенное в мире техническое устройство.
За счет чего же достигается надежность работы человеческого мозга? Может быть, за счет очень высокой надежности каждого нейрона? Оказывается, нет. Отдельно взятый нейрон представляет собой элемент, значительно ме-
15
нее надежный, чем, например, электромеханическое реле или транзистор. Благодаря исключительно целесообразной организации, выражающейся в множественности резервных элементов и связей между ними, надежность работы человеческого организма оказывается значительно выше, чем надежность каждого из его органов. Таким образом, живые организмы представляют собой яркий пример высоконадежных систем, состоящих из огромного количества менее надежных, а порой и крайне ненадежных взаимодействующих элементов.
Высокая надежность характерна не только для мозга человека. Мы часто жалуемся на свое сердце, сетуем на то, что к старости оно начинает пошаливать, но задумываемся ли мы над тем, какую гигантскую работу в течение жизни человека выполняет сердце? Наше сердце сокращается 60 70 раз в минуту и при каждом сокращении выбрасывает в сосуды 60 70 см3 крови. Это значит, что за час сердце перекачивает около 300 л крови, за сутки свыше
7 тыс. л, за год 2 млн 500 тыс. л, за 70 лет 175 млн л, или 175 тыс. м3. За 70 лет жизни человека сердце сокращается почти три миллиарда раз. Можно ли назвать хоть одно техническое устройство, которое могло бы выдержать хотя бы сотую часть такого количества включений и выключений? Все это показывает, насколько далека еще надежность самых совершенных технических устройств и систем от надежности работы живых организмов.
Великий русский ученый И. П. Павлов писал: «Человек есть, конечно, система (грубее говоря машина), как и всякая другая в природе, подчиняющаяся неизбежным и единым для всей природы законам; но система, в горизонте нашего современного видения, единственная по высочайшему саморегулированию». Именно эта саморегулируемая и благодаря этому исключительно надежная система может во многом служить примером для создания сложнейших технических систем. Проблема создания высоконадежных и эффективных технических устройств с использованием принципов биологических систем легла в основу новой науки бионики («бион» по-гречески «ячейка жизни»). Бионика занимается изучением живых организмов с целью использования полученных знаний при решении инженерных задач создания принципиально новых и совершенствования существующих технических систем.
Изучение живой природы содействовало успешному решению вопросов надежности при конструировании многих сложных технических устройств. Всем известно, какие исключительно высокие требования предъявляются к надежности космических кораблей и ракет, особенно несущих на себе человека. Благодаря чему же обеспечивалось выполнение этих требований? Кроме со-
16
вершенствования конструкций и технологии изготовления деталей и узлов использовалось несколько путей.
Первый и наиболее простой путь уже упоминавшееся резервирование элементов, выполняющих определенную функцию, когда в случае отказа одно-
го элемента функция выполняется резервным элементом. Однако хотя резервирование позволяет повысить надежность системы, возможность его применения при создании, например, космической аппаратуры очень ограничена, так как это связано с увеличением ее размеров и массы.
Второй путь, заимствованный из арсенала природы, использование так называемой функциональной избыточности – способности организма при выходе из строя тех или иных его элементов возлагать выполнение их функций на другие элементы.
Более сложным путем, также заимствованным у природы, является самоперераспределение функций элементов системы. В этом случае сохранившие работоспособность элементы не только принимают на себя функции элементов, вышедших из строя, но и перестраиваются и даже меняют свою «квалификацию», чтобы обеспечить жизнеспособность организма при меньшем числе элементов.
Очевидно, основной путь к достижению высокой надежности состоит в создании таких технических систем, которые не только автоматически предупреждают о возможности выхода из строя той ли иной части системы (встроенные диагностические системы), но, подобно тому, как это делается в живом организме, автоматически вводят в действие резервные элементы и каналы, исключая опасность того, что система прекратит работать. Приведенные примеры показывают, какую огромную пользу в борьбе за повышение надежности новой техники может извлечь человек, изучая уроки живой природы. Это позволит ученым инженерам, техникам и рабочим создавать технические устройства столь высокой надежности, которая требуется от современной и перспективной техники.
2. ТЕХНИКО-ЭКОНОМИЧЕСКИЕ ПОСЛЕДСТВИЯ НИЗКОЙ
НАДЕЖНОСТИ ТЕХНИКИ
Достигнутый уровень надежности еще далек от требуемого у значительной части ТО. От низкой надежности технических средств экономика страны терпит громадный экономический ущерб. Последствия отказов машин, техни-
ческих систем и объектов можно разделить на две категории:
17
1) прямые потери из-за отказа, аварии, катастрофы (простой отказавших машин, производства, т. е. невыполнение заданных функций, задач; влияние на
здоровье и жизнь людей; вредное экологическое воздействие на окружаю-
щую среду);
2) затраты на восстановление отказавших технических устройств, их ремонт и восстановление работоспособности.
Чернобыльская катастрофа наглядно показывает огромную величину ущерба от отказа: прекращение подачи электроэнергии множеству потребителей, радиационное заражение громадных территорий нашей страны и ряда зарубежных стран, облучение огромного числа людей обслуживающего персонала и населения, смерть и тяжелые заболевания многих тысяч людей. Велики и производственно-экономические потери в результате отказов техники.
На автозаводе им. Лихачева работает автоматическая линия обработки головок блока двигателя. В ней 59 станков. Чтобы привести в движение их инструменты, транспортеры, накопители деталей и управлять работой всех этих устройств, нужно меть 150 электродвигателей, около 1000 различных реле, 9000 концевых выключателей, 450 электромагнитов, 165 магнитных пускателей. В течение часа на линии совершается около 400 тысяч переключений. Простой расчет показывает, что если каждая пара контактов на 100 тысяч переключений откажет хотя бы один раз, то через каждые четверть часа один из станков будет останавливаться, выводя из строя поточную линию. Стоит не сработать лишь одной из тысяч автоматических задвижек в химическом производстве, как может произойти тяжелая катастрофа с человеческими жертвами. А что будет, если из-за недостаточной надежности внезапно откажет система автоблокировки на железной дороге, выйдет из строя какая-либо деталь экипажной части локомотива? К каким огромным потерям может привести выход из строя автоматов защиты линий электропередачи?
В наш атомный век, когда в руках агрессивных сил, стремящихся развязать новую мировую войну, имеются средства огромной разрушительной силы, ненадежность одной незначительной детали может привести к мировой ядерной катастрофе.
Исключительно велики затраты на ремонт и восстановление отказавшей и изношенной техники. На машиностроительных заводах СССР расходы на ремонт и содержание оборудования составляли 12 18 % от общей величины цеховых расходов. Ежегодно 11 12 % технологического оборудования подвер-
галось капитальному ремонту, 20 25 % среднему и 90 100 % текущему.
18
Ежегодные расходы на ремонт техники в угольной, горнорудной, лесозаготовительной промышленности и сельском хозяйстве достигали 15 20 % ее стоимости.
Только на ремонт металлорежущих станков ежегодно расходовалось
240 тыс. т чугуна, стали и много цветных металлов. Из этих материалов можно было бы дополнительно изготовить 150 тыс. токарных станков средней мощности. На ремонт тракторов ежегодно расходовалось такое количество металла, что из него можно было бы собрать 180 тыс. новых тракторов. Например, в 1962 г. стоимость поставленных запасных частей к тракторам и автомобилям превышала стоимость поставок новых тракторов и автомобилей. В стране свыше трети всех металлорежущих станков и каждый четвертый рабочий были занят ремонтом.
Затраты на ремонт и техническое обслуживание за срок службы машины в несколько раз превышают ее стоимость: для автомобилей – в шесть раз, для самолетов до пяти раз, для станков до восьми раз. На долю тракторостроительных заводов приходится лишь 22 % мощностей, а на долю заводов по выпуску запчастей к тракторам 34 %, на долю ремонтных предприятий 44 %. Иначе говоря, на ремонт тракторов затрачивается в четыре раза больше производственных мощностей, чем на их изготовление.
Трудоемкость ремонта и технического обслуживания многих строительных и дорожных машин за срок их службы примерно в 15 раз превышает трудоемкость изготовления новых. Ремонтом техники в СССР было занято
7 млн человек, одна треть станочного парка находилась на ремонтных предприятиях, на запчасти расходовалось больше одной пятой выплавленного металла. Размер средств на ремонт машин ежегодно увеличивался: в 1960 г. называлась цифра 12,3 млрд р., в 1970 г. на эти цели расходовался 21 млрд р., в 1980 г. 49 млрд р. (включая амортизационные расходы), т. е. шло удвоение расходов на ремонт за каждые 10 лет.
Сказанное выше в полной мере относится к железнодорожной технике, в частности к подвижному составу. Затраты на ремонт локомотивов, мотор-вагонных поездов и вагонов составляли около 20 % эксплуатационных расходов железных дорог страны (данные 1975 г.). В области ремонта и технического обслуживания подвижного состава было занято 860 тыс. работников. Ежегодные затраты на ремонт составляли около 4 млрд р. Только в депо ремонтом локомотивов и вагонов было занято 527 тыс. чел., затраты превышали 1 млрд р.
19
Около 30 % работников локомотивного хозяйства занято на ремонте локомотивов. Ремонт каждого локомотива за весь срок службы обходится дороже более чем в 10 раз его первоначальной стоимости.
Недостаточная надежность технических средств железных дорог приводит к задержкам поездов, снижению пропускной и провозной способности железных дорог. Так, к середине 80-х гг. ввиду быстрого роста грузонапряженности железнодорожной сети, а также технического состояния локомотивного и вагонного парков резко повысились как абсолютные, так и относительные задержки поездов. Это привело к ухудшению показателей работы железнодорожного транспорта, осложнило нормальную работу промышленности, сельского хозяйства и народного хозяйства в целом, нанесло ему крупный ущерб. Доля дополнительной «омертвленной» грузовой массы на колесах, образующаяся в результате только задержек поездов, увеличилась с 0,75 млрд р. в 1968 г. до
2 млрд р. в 1980 г.
Аналогичное положение отмечается на железных дорогах зарубежных стран и, в частности, в США, где годовые расходы на ремонт локомотивов в 1960 1970-е гг. составляли до 550 млн долларов, т. е. 24 26 % от общих расходов хозяйства подвижного состава.
3. НАДЕЖНОСТЬ КАК СОСТАВЛЯЮЩАЯ КАЧЕСТВА
ТЕХНИЧЕСКИХ ОБЪЕКТОВ
В разд. 1, 2 кратко рассмотрены вопросы обострения проблемы надежности технических устройств, систем и объектов по мере расширения техносферы, развития научно-технического прогресса, а также последствия низкой надежности техники. Все орудия труда, машины, сооружения создавались человеком с единственной целью более полного удовлетворения своих постоянно растущих потребностей путем использования этих технических средств по функциональному назначению. И в процессе этого использования они смогут удовлетворить потребности человека лишь в том случае, если они выполняют функции, ради которых созданы, т. е. обладают совокупностью потребительских качеств.
Каждой вещи, изделию, виду продукции свойственны свои, особые, присущие только им показатели качества. Когда мы покупаем продукты питания, для нас важно, чтобы они были свежими, питательными, вкусными. Приобретая ткань, мы интересуемся не только ее внешним видом, но и ее плотностью,
20
прочностью на растяжение и на разрыв, узнаем, сильно ли она мнется, линяет,
садится ли после стирки. Для оценки качества изделий промышленного назначения существуют свои технические показатели, параметры, характеристики. Например, для оценки качества тепловоза необходимо учитывать в первую очередь функциональные показатели мощность, скорость, силу тяги (при трогании, на руководящем подъеме), удельный расход топлива на единицу выполненной работы и др.
По каждому виду технического устройства имеется свой набор параметров, показателей качества, указанных в паспорте. Однако можно ли, посмотрев паспорт, например, нового станка и узнав его технические характеристики, сделать безапелляционный вывод о качестве этого станка? Любой опытный производственник скажет: «Давайте все же предварительно испытаем станок в работе». И с таким предложением трудно не согласиться. Дело в том, что все паспортные показатели и параметры характеризуют лишь технические возможности станка, но эти возможности реализуются только при производственной эксплуатации станка. Причем различные машины могут вести себя в работе по-разному. Один станок работает устойчиво, безотказно, длительное время подтверждает свои первоначальные технические показатели, другой, наоборот, часто простаивает из-за тех или иных неисправностей, его первоначальные характеристики (точность, производительность и др.) быстро снижаются. Совершенно естественно, что при оценке качества любой машины важны не только ее высокие номинальные технические данные, но и ее фактическая способность безотказно работать в течение возможно более длительного времени, сохраняя свои первоначальные технические характеристики. Ведь любой «инструмент, машина… служат в процессе труда лишь до тех пор, пока они сохраняют свою первоначальную форму, пока они завтра могут вступить в процесс труда в той самой форме, как и вчера » ( Маркс К. Капитал. М.: Госполитиздат,
1953. Т. 1. С. 210).
Каждому понятно, что ни один станок, как бы отлично он ни был сделан, не может работать бесконечно долго без единой неисправности, без постепенного ухудшения своих первоначальных характеристик. Любое техническое устройство может проработать безотказно лишь некоторое положенное для него, строго обоснованное время, зависящее от заложенного ресурса и от конкретных условий эксплуатации, и потребует восстановления потерянной работоспособности путем ремонта или замены элементов.
Таким образом, каждое техническое устройство обладает в той или иной
21
степени способностью, свойством сокращать в течение эксплуатации свои на-
чальные характеристики и способность выполнять заданные функции, т. е. сохранять исправность, работоспособность, и это свойство определяет надежность ТО. Следовательно, физический смысл надежности изделия заключается в его свойстве сохранять свои эксплуатационные характеристики во времени. Очевидно, чем дольше изделие сохраняет свою исправность, работоспособность, чем реже отказывает, тем оно надежнее. Иными словами, надежность как свойство изделия, машины, станка является одной из составляющих общего качества наряду с функциональными, технологическими, экономическими и эргономическими показателями этих изделий. Таким образом, высокое качество изделия должно включать в себя не только высокие показатели таких его свойств, как производительность, скорость, мощность, точность и др., но и его высокую надежность. Эти составляющие качества органически взаимосвязаны, имеют значение только во взаимодействии друг с другом.
Сама по себе отдельно взятая надежность еще не определяет высокого качества станка, машины, локомотива. Они могут быть исключительно надежными, но обладать очень несовершенными техническими характеристиками малой мощностью, малой производительностью, низкой точностью, скоростью (например, лом, кувалда). Но, с другой стороны, какими бы отличными начальными характеристиками ни обладал технический объект, если он будет ненадежным в работе, его высокие технические данные не могут быть полноценно использованы (например, высокопроизводительный, но ненадежный пневмоинструмент перфоратор).
Итак, надежность это одна из обязательных составляющих качества любого технического объекта, часть его качества. Однако, являясь лишь одним из элементов качества, надежность существенно отличается от всех других его элементов, от остальных его свойств:
надежность является наиболее общим комплексным свойством, характеризующим качество любого технического изделия, машины, прибора;
это единственное общее свойство огромного большинства промышленных изделий;
реализуется во времени, все остальные свойства имеют мгновенные
значения;
не подлежит инструментальному измерению, а определяется расчетами (вероятностными или статистическими).
Комплексность свойства «надежность» состоит в том, что техническое
22
устройство считается тем надежнее, чем реже оно отказывает, чем дольше ра-
ботает до потери работоспособности, чем проще и дешевле восстанавливается
после отказа. Для более полной и детальной оценки вводят в рассмотрение частные свойства, формирующие комплексное свойство «надежность», безотказность, долговечность, ремонтопригодность и сохраняемость. Для их определения следует рассмотреть состояния, в которых могут находиться ТО, и события, под которыми понимают переходы ТО из одного состояния в другое.
Исправным состоянием ТО (например, локомотива или его узла, детали) называется такое, при котором оно удовлетворяет всем требованиям нормативно-технической документации. Если ТО не удовлетворяет хотя бы одному из этих требований, то оно находится в неисправном состоянии. Находясь в неисправном состоянии, ТО может быть работоспособным или неработоспособным в зависимости от степени влияния неисправности на выполнение рабочих функций ТО в конкретных условиях эксплуатации. Под отказом ТО (например, локомотива, его узла) понимается событие, заключающееся в потере им работоспособности и нарушении установленного порядка нормальной эксплуатации и ремонта. Дефект ТО это неисправность, которая не вызывает нарушения установленного порядка нормальной эксплуатации и ремонта. Отказом узла или детали ТО считается событие, приведшее к потере их работоспособности и требующее ремонта или замены узла или детали.
Безотказностью ТО (или его узла, детали) называется свойство непрерывно сохранять работоспособность в течение требуемого времени в конкретных условиях эксплуатации.
Под долговечностью ТО (узла, детали) понимается свойство длительно, с возможными перерывами на ремонт сохранять работоспособность до отказа или другого предельного состояния.
Ремонтопригодность ТО это его свойство, заключающееся в приспособленности к предупреждению, обнаружению и устранению отказов и де-фектов.
Под сохраняемостью ТО понимается его свойство непрерывно сохранять рабочие свойства в заданных пределах в течение требуемого времени в конкретных условиях хранения.
На основании сказанного выше можно определить надежность ТО как его комплексное свойство, обусловленное безотказностью, долговечностью, ремонтопригодностью и сохраняемостью.
Рассмотренная составляющая качества любого технического объекта
23
его надежность проявляется во времени работы, эксплуатации в конкретных условиях, поэтому надежность оценивается количественными показателями, определяемыми на основе обработки опытно-статистических данных методами математической статистики и теории вероятностей.
4. КРАТКИЕ СВЕДЕНИЯ ИЗ ИСТОРИИ РАЗВИТИЯ НАУКИ
О НАДЕЖНОСТИ
Наука о надежности технических устройств является одной из самых молодых и бурно развивающихся прикладных инженерных наук, хотя проблема, являющаяся предметом этой науки, проблема надежности одна из самых древних. Несмотря на то, что вопросами обеспечения надежности человек занимается с момента создания первого орудия труда (охоты), в самостоятельную науку теория надежности выделилась совсем недавно в начале научно-технической революции, т. е. в середине XX в. До этого времени проблема надежности решалась с использованием накопленного практического опыта, эмпирически, без научного анализа, обоснования, расчета. Как известно, до
XVII XVIII вв. наука и производство развивались разрозненно, без взаимной связи и влияния, без взаимного использования научных результатов и практического опыта. Прикладные исследования, направленные на изучение существовавшей тогда техники, отсутствовали, как и многочисленные сегодня технические науки. В них тогда просто не было необходимости.
До наступления эпохи машинного производства инструмент, простейшие машины были не серийными, как сейчас, а единичными, изготовленными конкретным мастером, имевшим свой опыт, свои «секреты» изготовления качественных изделий.
Это не означает, что требования к надежности технических устройств и сооружений отсутствовали. Исторические свидетельства говорят о том, что еще в древности надежности сооружений, оружия уделялось достойное внимание. Почти 4000 лет назад в Вавилоне существовал закон, который гласил, что если построенный архитектором дом развалится и при этом погибнет его владелец, архитектор подлежит смертной казни. Если погибнут и члены семьи владельца дома, то казни подлежат и члены семьи архитектора (отголоском этого закона в наше время является традиция: при испытании построенного моста автор стоит под мостом).
Известен указ Петра I, показывающий, какое значение придавал он каче-
ству изготовляемого оружия, его надежности. Этот указ гласил:
24
«П.1. Повелеваю хозяина тульской оружейной фабрики Корнилу Белоглаза бить кнутом и сослать в работу в монастыри, понеже он, подлец, осмелился войску государеву продавать негодные пищали и фузеи. Старшину олдермана Фрола Фукса бить кнутом и сослать в Азов, пусть не ставит клейма на плохие ружья.
П. 2. Приказываю ружейной канцелярии из Петербурга переехать в Тулу и денно и нощно блюсти исправность ружей. Пусть дьяки и подъячие смотрят, как олдерман клейма ставит, буде сомнение возьмет, самим проверять и смотром и стрельбою. А два ружья каждый месяц стрелять, пока не испортятся».
Так более двухсот пятидесяти лет назад царским указом были установлены одни из первых испытаний оружия на надежность.
До выделения теории надежности в самостоятельную науку вопросы надежности решались разрозненно, эмпирически, интуитивно. Такое положение объяснялось тем, что некоторое игнорирование надежности изделий не сильно сказывалось на эффективности их применения и наносило не столь значительный ущерб экономике, тем более что существовавшие в то время ТО выполняли не столь ответственные, важные и сложные функции, как в наше время.
В последующее время в связи с началом научно-технического прогресса и, в особенности, нынешней научно-технической революции особую важность приобрели многочисленные вопросы технической и экономической эффективности различного рода технических устройств и систем. Резко возросли: количество ТО, их сложность, важность выполняемых ими функций, экономический эффект от использования и размер ущерба от отказов, влияние на безопасность людей и экологическое воздействие на природную среду.
В первую очередь это почувствовали в области военной техники, связи, кибернетики, автоматики, энергетики, космической техники. Для победы в сражениях второй мировой войны требовалось громадное количество мощной, качественной, высоконадежной военной техники самолетов, артиллерии, танков, подводных и надводных кораблей, стрелкового оружия устройств связи и транспортных средств. Ускоренное развитие в послевоенные годы кибернетики, космической техники, механизации и автоматизации всех отраслей производства потребовало решения проблем качества и надежности всех элементов быстрорасширяющейся техносферы. Поэтому теория надежности зародилась после второй мировой войны в применении к указанным областям техники.
25
Произошедшие в последующие десятилетия аварии и катастрофы техногенного характера показали, к какому громадному ущербу приводит низкая надежность сложных технических систем (отказ энергетической системы в США, авария при запуске космического корабля «Шаттл», Чернобыльская катастрофа и др.). Для недопущения подобных трагедий потребовалась разработка научных методов анализа, расчета и обеспечения высокой надежности ТО и их элементов, т. е. теории надежности.
Справедливости ради следует отметить, что в нашей стране еще
в 30-х гг. по инициативе выдающегося советского академика Чаплыгина С. А. была создана комиссия при АН СССР по изучению надежности и долговечности машин (1934 г.) В ней, например, была разработана методика расчета долговечности подшипников, не потерявшая своей ценности и в наше время. Однако деятельность этой комиссии не получила должной оценки и поддержки, и вскоре комиссия была расформирована.
Конечно, высокие требования к безотказности и долговечности предъявляются и в других областях техники, в том числе на транспорте, так как последствия отказов транспортной техники (влияние на безопасность движения, экологический ущерб) весьма велики. Академик Бэр А. И. писал, что “было бы неправильно ограничивать значение проблемы надежности лишь одними средствами электронной автоматики и электроники. По мере развития и усложнения всех видов техники проблема надежности приобретает общее значение”.
Академик Гнеденко Б. В. дает следующее определение теории надежности как прикладной науки: «Общая научная дисциплина, изучающая общие методы и приемы, которых следует придерживаться при проектировании, изготовлении, приемке, транспортировке и эксплуатации изделий для обеспечения максимальной их эффективности в процессе использования, а также разрабатывающая общие методы расчета качества устройств по известным качествам составляющих их частей, получила название теории надежности». Таким образом, теория надежности технических объектов
устанавливает закономерности возникновения отказов ТО и методы их прогнозирования;
изыскивает способы повышения надежности изделий при конструировании и последующем изготовлении, а также приемы поддержания надежности при эксплуатации и во время хранения;
разрабатывает методы проверки надежности изделий и способы контроля надежности при приемке больших партий продукции;
26
вводит в рассмотрение количественные показатели качества техники. Предмет изучения теории надежности не является чем-то принципиально новым. Она рассматривает вопросы, которые были поставлены и в какой-то мере решались давно, но решает их более системно и комплексно, применяя при этом количественные показатели, определяемые с использованием эффективных вероятностно-статистических методов.
Учитывая сказанное выше, можно сказать, что теория надежности является методологической основой, определяющей целевую направленность общеинженерных и специальных технических дисциплин при решении задачи обеспечения качества промышленной продукции.
Первые работы, посвященные анализу и повышению надежности технических средств железнодорожного транспорта, в частности, тягового подвижного состава, появились в начале 60-х гг., т. е. время их выполнения совпало с переходом железных дорог на новые, более совершенные, эффективные виды тяги электрическую и тепловозную. Прошедший сорокалетний период работы ученых и производственников по решению проблемы надежности локомотивов, у истоков которой были профессора Е. С. Павлович (ОмИИТ) и
И. П. Исаев (МИИТ), можно разделить на четыре этапа.
На первом этапе для принципиально новых, не изученных в эксплуатации локомотивов потребовалось проанализировать повреждаемость, изнашивание узлов и деталей в конкретных условиях работы, для чего необходимо было разработать соответствующие научные методы. К этой работе вскоре подключились локомотивные кафедры и остальных вузов МПС, а также соответствующие лаборатории ВНИИЖТа и ВНИТИ. Этому способствовала активная поддержка нового научного направления локомотивным главком МПС в лице главного инженера ЦТ МПС Б. Д. Никифорова. Среди многих мероприятий этого этапа по решению проблемы надежности можно назвать основные:
разработка рабочей группой из сотрудников ОмИИТа, МИИТа,
ТашИИТа, ВНИИЖТа, ВНИИТИ первого отраслевого стандарта "Надежность тягового подвижного состава. Основные понятия и термины";
издание сборников научных трудов по проблеме надежности тягового подвижного состава, методических материалов по определению количественных показателей надежности узлов, деталей и локомотивов в целом;
разработка учебных программ, курсов лекций и методических пособий для ведения занятий по проблеме надежности локомотивов со студентами и слушателями ФПК инженерно-технических работников железных дорог;
27
создание на сети железных дорог системы сбора и анализа статистических данных о надежности локомотивов в виде групп надежности в депо, локомотивных службах дорог и в ЦТ МПС.
Таким образом, на первом этапе были разработаны математические, методические и организационные основы анализа надежности локомотивов, определения количественных показателей надежности и влияющих на нее факторов. Результаты этой работы были обсуждены в 1969 г. на первой межвузовской научно-технической конференции по надежности дизельного подвижного состава, проведенной ОмИИТом совместно с ДорНТО Западно-Сибирской железной дороги.
На втором этапе (с 1970 г.) целью научных исследований явилось обеспечение надежности локомотивов и их узлов путем совершенствования системы их технического обслуживания и ремонта (СТОР) и разработки технологических процессов для восстановления теряемой в эксплуатации работоспособности. Анализ количественных показателей надежности локомотивов, выполненный многими научными коллективами с помощью групп надежности в депо на различных дорогах, показал, что они изменяются в зависимости от климатических условий, интенсивности эксплуатации и режимов работы, качества изготовления и ремонта, квалификации локомотивных бригад и других факторов. Отсюда сделан вывод о том, что система ТОР, предназначенная для восстановления работоспособности локомотивов, должна соответствовать уровню их надежности в конкретных условиях эксплуатации. На основе этого были сформулированы основные направления совершенствования системы ТОР локомотивов путем оптимизации таких ее параметров, как величина межремонтных периодов для основных узлов, агрегатов и деталей, набора видов технических обслуживаний и ремонтов, их чередования в ремонтном цикле. При этом в качестве критериев оптимальности были приняты минимум суммарных затрат на плановые и неплановые ремонты с учетом ущерба от отказов локомотивов на линии и обеспечение заданного уровня безотказности узлов, влияющих на безопасность движения.
Основные результаты исследований этого этапа были обсуждены с широким участием работников депо, служб локомотивного хозяйства дорог, локомотивного главка МПС, локомотивостроительных и локомотиворемонтных заводов, ученых вузов МПС, ВНИИЖТа, ВНИИТИ, ЦНИДИ на двух представительных совещаниях, проведенных ОмИИТом совместно с ЦП НТО и ДорНТО Зап.-Сиб. ж. д.: сетевой научно-технической конференции "Динамика и меры
28
повышения эксплуатационной надежности локомотивов в условиях железных дорог Урала и Сибири" (октябрь 1972 г.) и сетевом научно-техническом совещании "Повышение надежности локомотивов и система их ремонта" (февраль 1975 г.).
В принятом решении совещания были одобрены основные направления совершенствования системы технического обслуживания и ремонта тягового подвижного состава, в частности, дифференциация межремонтных периодов в соответствии с уровнем надежности локомотивов на различных полигонах эксплуатации и фактическим техническим состоянием каждого локомотива, определяемым путем диагностирования. Рекомендации этого совещания использованы при подготовке приказа МПС от 31.07.75 № 22 Ц "О дальнейшем совершенствовании системы технического обслуживания и ремонта электровозов, тепловозов и мотор-вагонного подвижного состава".
Уже тогда, в 70-х гг., сотрудниками локомотивных кафедр ОмИИТа и других вузов МПС была начата разработка методов и технических средств диагностирования узлов локомотивов как основного направления повышения надежности и совершенствования системы ТОР тягового подвижного состава, сформулированы теоретические и методические основы перехода к более гибкой и дифференцированной системе ТОР от жесткой планово-предупредительной. И это явилось основным содержанием научных работ, выполненных на третьем этапе сотрудниками локомотивных кафедр совместно с работниками железных дорог. Обсуждению этой проблемы была посвящена всесоюзная научно-техническая конференция "Методы и средства диагностирования технических средств железнодорожного транспорта", проведенная в 1989 г. в ОмИИТе совместно с ЦП НТО МПС. Учитывая важность разработок по диагностике, выполненных ОмИИТом совместно с локомотивщиками Западно-Сибирской и ряда других дорог (в частности, создание филиалов кафедр в депо и станций диагностики), конференция в своем решении рекомендовала считать ОмИИТ базовым по проблеме диагностирования технических средств железнодорожного транспорта. В соответствии с этим в ОмИИТе создан и до сих пор работает научно-технический семинар для рассмотрения крупных научных разработок по этой проблеме.
В этот же период была включена в учебный план для студентов-локомотивщиков учебная дисциплина "Надежность и диагностика локомотивов", и для ее реализации в вузах МПС были подготовлены в ОмИИТе учебная
29
программа и учебное пособие "Надежность тягового подвижного состава", вышедшее в издательстве "Транспорт" в 1981г.
В настоящее время Министерством путей сообщения принято решение о переходе на систему ремонта с учетом технического состояния каждого локомотива (указание МПС № 2185у от 30.09.99), а оно определяется количественными показателями надежности и результатами диагностирования узлов и систем конкретного тепловоза, электровоза. Поэтому не теряет остроты проблема сбора объективной информации об отказах локомотивов, износе, старении деталей и их материалов, об изменении рабочих параметров узлов, а также оперативной обработки, анализа огромных массивов статистической информации. Это можно обеспечить лишь с помощью современной вычислительной техники. В соответствии с упомянутым указанием МПС "Об организации работ для перехода на ремонт по техническому состоянию локомотивов и МВС", например, на Западно-Сибирской дороге издан приказ № 9/Н от 14.01.2000, где были определены пять базовых депо, лучше других оснащенные диагностическими комплексами, имеющие определенный опыт их работы, утверждена согласованная с локомотивным департаментом МПС новая цикличность, т. е. межремонтные пробеги. Это локомотивные депо Карасук, Московка, Тайга, Омск, Новосибирск.
В депо Омск и Новосибирск в 2000 г. начали опытные работы и говорить о каких-то результатах рано, а по депо Московка, Тайга, Карасук, где весь эксплуатационный парк работает по новой схеме с применением диагностических средств, выводы можно сделать. Кстати, только этим трем депо департамент разрешил перейти на ремонт по состоянию всего эксплуатационного парка. Больше таких депо на сети пока нет.
Таким образом, предлагается плановая постановка локомотивов на ремонт с широким использованием средств диагностики для определения объема ремонта в зависимости от технического состояния с обязательным увеличением межремонтных пробегов и снижением трудоемкости.
С целью оперативного и грамотного влияния службы на эти процессы на дороге созданы три дорожные лаборатории:
по внедрению новых технологий ремонта ТПС (депо Омск);
по внедрению автоматических систем управления в локомотивном хозяйстве (депо Новосибирск);
неразрушающего контроля (депо Омск).
На технико-экономическом совете службы было принято решение
30
в каждом депо должны быть специализированные, высокомеханизированные стойла для проведения диагностики локомотивов в полном объеме, где будет обеспечиваться входной и выходной контроль с определением фактического объема работ. Эта программа уже реализуется. Идет наработка и реализация программ внедрения передовых технологий. Руководством службы утверждена программа перехода на ремонт по состоянию всех локомотивных депо до 2005 г. Безусловно, руководящим документом в решении этой непростой задачи являются разработанные технические регламенты для всех локомотивных депо. Опыт Западно-Сибирской дороги и ОмГУПСа был обсужден и одобрен сетевой школой по вопросам диагностики локомотивов, проведенной в мае 2000 г. в Омске и Новосибирске.
В связи с этим научный коллектив кафедры "Локомотивы" в тесном сотрудничестве с организованной при локомотивном депо Омск дорожной лабораторией работают над проблемой автоматизации и компьютеризации следующих процессов: сбор, обработка и анализ статистических данных об отказах, определение количественных показателей надежности локомотивов и их узлов, диагностирование узлов и агрегатов, определение остаточного ресурса и принятие решения о постановке локомотива на ремонт того или иного объема. На нынешнем, четвертом этапе решения проблемы надежности локомотивов нужно создавать автоматизированные комплексы и автоматизированные рабочие места, необходимые для реализации системы технического обслуживания и ремонта каждого локомотива с учетом его фактического состояния.
Проблема обеспечения надежной работы тягового подвижного состава остается по-прежнему одной из главных, надежностью необходимо управлять, а для этого нужно постоянно контролировать и изучать состояние подвижного состава в эксплуатации. Для этого кроме дорожных лабораторий диагностики в каждом депо нужно иметь группу специалистов по анализу надежности и осуществлению диагностирования, как это было сделано в 70-х гг.
ЗАКЛЮЧЕНИЕ
В заключение можно сформулировать основные задачи, которые решает научная дисциплина по надежности локомотивов:
количественная оценка уровня надежности парка локомотивов в конкретных условиях эксплуатации на различных полигонах тяги;
31
создание новых локомотивов с заданным (оптимальным) уровнем надежности для различных условий эксплуатации;
разработка оптимальной системы технического обслуживания и ремонта локомотивов;
разработка методов и технических средств диагностирования локомотивов, а также автоматизации процессов анализа, контроля надежности в эксплуатации;
разработка и применение современных технологий восстановления работоспособности отказавших и изношенных узлов и деталей локомотивов;
оптимизация системы снабжения запасными частями и материалами для ремонта локомотивов.
Надежность локомотивов как прикладная наука должна стать научной базой для создания системы управления надежностью локомотивов в эксплуатации для обеспечения устойчивости перевозочного процесса и повышения эффективности.
Библиографический список
- С о р и н Я. М., Л е б е д е в А. В. Беседы о надежности. М., 1964.
224 с.
2. Г н е д е н к о Б. В. Математические методы в теории надежности. М., 1965. 524 с.
32
ЧЕТВЕРГОВ Виталий Алексеевич,
ОВЧАРЕНКО Сергей Михайлович
НАУЧНО-ТЕХНИЧЕСКИЙ ПРОГРЕСС И
ПРОБЛЕМА НАДЕЖНОСТИ ТЕХНИКИ
Конспект лекций
_____________________
Редактор Н. А. Майорова
Лицензия ИД № 01094 от 28.02.2000.
Подписано в печать . . .
Формат 60 84
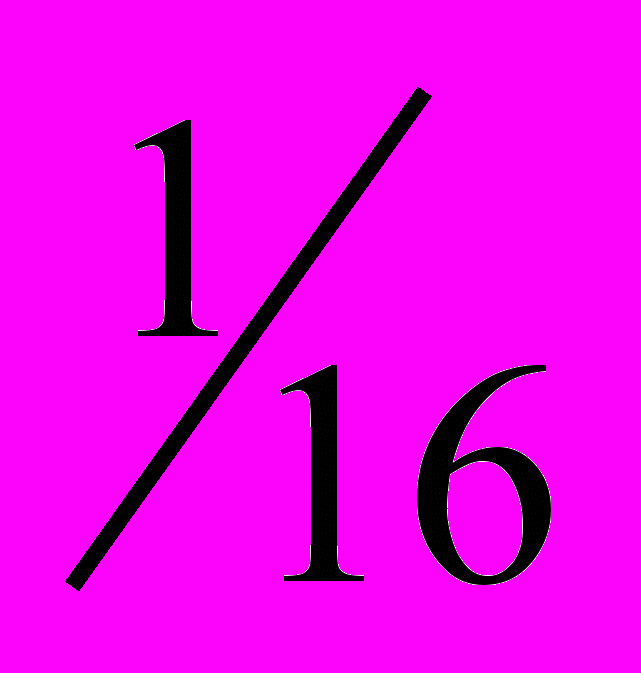
Усл.-печ. л. 2,0. Уч.-изд. л. 1,9. Тираж 230 экз. Заказ .
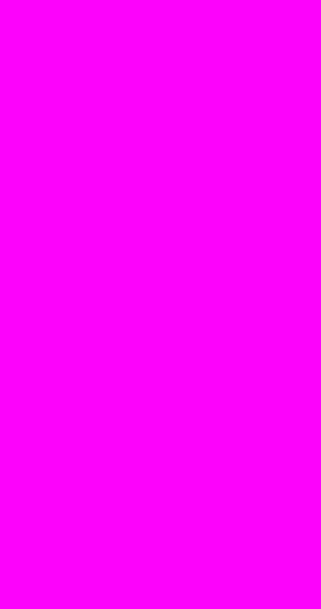
Редакционно-издательский отдел ОмГУПСа
Типография ОмГУПСа
644046, г. Омск, пр. Маркса, 35