1 Общие представления о реструктуризации угольной промышленности Каждая шахта проектируется на определенный, конкретный срок ее службы
Вид материала | Документы |
Вопросы и задания для самоконтроля Вопросы и задания для самоконтроля Вопросы и задания для самоконтроля 8. Что представляет собой твердеющая закладка, ее состав, свойства и характеристики? |
- Установить срок их действия до 1997 года, 832.25kb.
- Забастовки в угольной промышленности, 4834.25kb.
- Постановления Правительства Российской Федерации) в угольной промышленности завершаются, 111.6kb.
- Утверждено Постановлением Госгортехнадзора России от 04. 04. 2000 n 14 Срок введения, 2461.4kb.
- Ми и осуществляющее всю подготовительную работу для заключения брокером договоров, 1347.64kb.
- Перечень групп управленческих должностей, на которые формируется муниципальный резерв, 56.45kb.
- Розділ 3 Економіка підприємства та організація виробництва, 292.16kb.
- Квалификационные требования к группам управленческих должностей, на которые формируется, 171.1kb.
- Вестник Брянского государственного технического университета. 2007. №3(15), 153.72kb.
- Утверждено Постановлением Госгортехнадзора России n 16 от 24 марта 1998 г. Срок введения, 979.62kb.
На практике устанавливают (выделяют) зону возможных деформаций земной поверхности вблизи устья ствола и зону, опасную по скоплению и взрыву вытекаемого из шахты метана.
В нормативных документах Германии указывается, что радиус зоны опасных деформаций R=20+0,5d (d - диаметр ствола в свету, м); в Чехии считают, что зона опасных деформаций поверхности распространяется примерно на 20 м от внешнего контура ствола, в Украине радиус зоны опасных деформаций определяется «Правилами...» и уточняется проектом.
Согласно «Правилам...» зона постоянного контроля ограничивается окружностью радиусом R0=20 м от центра ствола при мощности наносов hH≤ 20 м; если h„> 20м, то радиусом R0=hH, но не более 40 м.
Зона же газового режима при ликвидации стволов на шахтах, опасных по газу, устанавливается на земной поверхности в радиусе не менее 25 м от оси ликвидируемого ствола. Опасность выхода метана здесь велика, особенно в связи с колебаниями атмосферного давления. Для предотвращения скопления метана, его воспламенения яли взрыва поверхность в окрестностях ствола должна быть расчищена и зыравнена.
Исходя из вышеизложенного при определении и оконтуривании границ опасных зон необходимо учитывать:
- местоположение устья ствола относительно открытого проветриваемого пространства;
- виды проводимых работ (сварка, закладка и др.) ;
- вид транспорта по доставке закладочного материала (автомобильный, конвейерный и др.);
- потребность ведения взрывных работ по разрушению надшахтных зданий, сооружений;
- характер застройки над стволом и возле ствола;
- необходимость работ по дегазации, откачке воды и др. Подготовка юсверхности к засыпке ствола.
Если шахта не опасна по взрыву метана и проведена полная очистка ствола (убрана его оснастка), то допускается высыпание закладочного материала из автомобилей непосредственно в ствол. При этом следует предусматривать меры безопасности по предотвращению падения автомашин в ствол и меры контроля устойчивости устья ствола.
В Англии при доставке закладочного материала автомашинами у устья устраивается бункер-накопитель с наклонным заездом и желобом, что гарантирует устойчивость устья и предотвращает разрушение крепи ствола. В Германии бункер-накопитель оборудуется вне опасной зоны, а подача закладочного материала в ствол осуществляется конвейером. Эта же технологическая схема принята за основу и в Украине.
Если оснастка сзола не убрана или убрана не полностью, то засыпка ведется только по центру, причем предусматривается установка грохота перед конвейером, чтобы исключить попадание в ствол крупных (более 250 мм в поперечник кусков.
Однако по опыт-" угледобывающих стран Европы предельный размер кусков закладочного материала следует ограничивать 180-200 мм. Здесь учитывается не только опасность искрообразования и разрушение крепи вообще, но, что более вероятно, разрушение крепи в местах заделки расстрелов, лишая их при этом функции распорных конструкций. Подобное , «удаление» расстрелов ведет к общему ослаблению ствола.
Если же из ствола при его подготовке к засыпке, удалена вся оснастка, то можно использозать материал с поперечником любого размера. Но, при небольшом диаметре ствола и значительном угле естественного относа закладочного материала следует рассчитывать силу удара крупных кусков о крепь ствола. Она может быть значительной, а в местах с плохо заполненным (по различным причинам) закрепным пространством даже разрушительной.
Засыпка ствола.
При засыпке особо важное место занимает контроль качества закладочного материала (кусковатость, плотность и др.) и его объем. При применении твердеющей закладки вопросы контроля этих параметров становятся центральными.
В целях предотвращения скопления и взрыва метана в стволе необхо- дамо, чтобы процесс закладки происходил непрерывно с небольшой скоростью. С этой точки зрения лучшим средством закладки является конвейер, обеспечивающий достаточно медленное и равномерное поступление материала, его уплотнение и взаимодействие с крепью. При закладке твердеющими материалами пульпа подается в ствол по трубам диаметром 150-200 мм.
Выполнение заключительных работ.
На заключительном этапе работ после усадки закладочного материала производится перекрытие устья ствола. В мировой практике чаще всего устье ствола перекрывается железобетонной плитой с упором на крепь или сваи, забитые до коренных пород. Конструкция плиты, её толщина, поперечные размеры, несущая способность определяется практикой и расчетами. При неудовлетворительном прогнозе устойчивости устья необходимо предварительно укреплять окружающие его горные породы. Для исключения возможности поступления ливневых и паводковых вод в ликвидиро-ванный ствол через устье, последнее ограждается не менее чем в 2,5 м водоотводной канавой сечением 0,5 м2. Если отведение ливневых и паводко-вых вод путем сооружения канавы трудно осуществимо, то предусматри-вается глиняный изолирующий экран толщиной 1 м и площадью в 1,5 раза большей сечения ствола.
Окончанием работы по погашению ствола является ликвидация всех подходов к нему (каналов вентилятора, калорифера и др.). В дальнейшем согласно проекту постоянно контролируется оседание закладки и метано-выделение через покрывающую устье плиту.
После очистки и рекультивации территории проводится маркшейдерская съемка промплощадки шахты. На плане показывается устье ликвидированного ствола, границы опасных зон по возможным провалам земной поверхности и взрыву метана, все сохранившиеся здания и сооружения, а также все находящиеся вблизи устья подземные коммуникации, по которым возможно проникновение метана на поверхность в случае разрушения (со временем) крепи ствола.
Законченные ликвидационные работы оформляются актами приемки работ в установленном порядке.
4.1.2. Технологические схемы и технологии ликвидации стволов
В оборудованных лестничными отделениями вертикальных стволах, кик уже было сказано, до начала засыпки производится демонтаж отшивки лестничных отделений по всей их глубине. Демонтируются также стволо-вые кабели, трубопроводы d<100 мм, клети, скипы, противовесы, неиспользуемые металлоконструкции нулевых площадок; производится раз-Лорка проемов в стенах надшахтного здания (в отшивке копра) для пропуска привода скребкового конвейера и трубопроводов вентиляции, пыле-подавления, сжатого воздуха.
Параллельно с этими работами монтируется конвейер для засыпки ствола, устраивается бункер над конвейером и разгрузочный желоб в устье ствола, выполняется специальное ограждение рабочей зоны конвейера и
опасной зоны вокруг ствола. Ограждение ствола со ствольными дверьми сохраняется существующее.
Для монтажа временного оборудования используется автомобильный кран КС-3571 грузоподъемностью 10 тонн.
Для предотвращения расползания засыпаемого в ствол материала в сопряжениях ствола с горизонтальными выработками возводятся опоры-перемычки (упорные слои) из бетона или путем заполнения свободного объема ствола и части примыкающих выработок неразмокаемым, непроса-дочным щебнеподобным материалом прочностью не менее 15-20 МПа (рис. 4.1). Объем заполнения и абсолютные отметки упорного слоя определяются проектом. Параметры опоры (упорного слоя) рассчитываются по методике приведенной в приложение Г «Правил...».
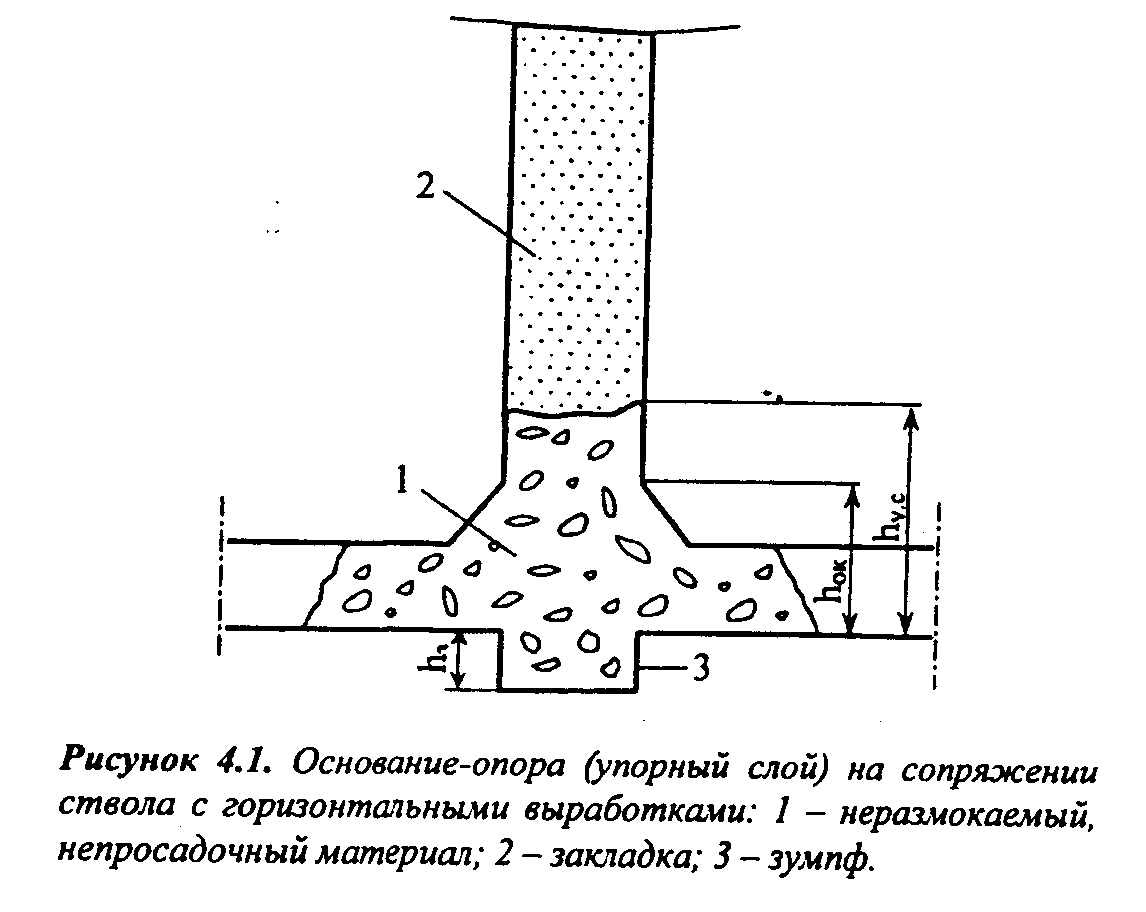
В общем случае высота упорного слоя по разрезу ствола от подошвы сопрягающейся выработки определяется по формуле
hy.c= h0+5, м, (4.1)
где hy.c - высота упорного слоя, м, h0K - высота окна сопряжения, м.
При соответствующем техническом и экономическом обосновании возможны и другие инженерные решения по предотвращению расползания (ухода) закладочного материала в местах сопряжения ствола с горными выработками, в частности путем возведения сооружений из твердеющей закладки.
При ликвидации затопленных выработок засыпка ствола в районе сопряжения должна производиться неразмокаемым материалом. Запрещается использовать для засыпки шлакоблок (от разборки зданий) из-за его токсичности.
К моменту начала работ по засыпке стволов подъемы останавливают и спуск-подъем людей, оборудования и материалов прекращается.
При засыпке стволов шахтной породой ее извлечение из породного отвала выполняется в соответствии с «Инструкцией по предупреждению самовозгорания, тушению и разборке породных отвалов». Выбор отвала определяется комиссией, создаваемой заказчиком проекта ликвидации. В случае отсутствия очевидных признаков перегоревшей породы (красноватый цвет породы, наличие золыгастых шлаковых включений) для определения степени пожароопасности предполагаемой для использования породы отвала привлекаются специализированные организации.
Транспортирование породы к стволу чаще всего производится автосамосвалами КамАЗ-5511, погрузка в них экскаваторами ЭО-3325, Э-1001Д с емкостью ковша 0,5 м3, а доставка породы в зону действия экскаватора - скреперной установкой 17ЛС2СМ к бульдозером ДЗ-116В. Подача породы непосредственно в ствол ведется скребковым конвейером типа СР-70,1СК-38м или СП-202 через перегрузочyый желоб.
В местах установки скребкового конвейера площадка выравнивается, подсыпается, чтобы положение рештачного лава в вертикальной плоскости изменялось не более чем на 0,5 м на длине 30 м.
Для того чтобы исключить попадание з ствол вместе с закладкой металлических предметов, которые могут вызвать искрообразование при ударе о проводники и расстрелы, над конвейером устанавливается электромагнит.
Погрузка породы в бункер, расположенный над конвейером, выполняется породопогрузочный машиной ШНБ-2 или экскаватором ЭО-3322 с емкостью ковша 0,5 м3, а в зону действия погрузочной машины - бульдозером ДЗ-116В (Д—271) (рис. 4.2). Изменение схемы доставки закладочного материала и его засыпки в ствол в процессе ведения работ возможно по согласованию с МакНИИ и УкрНИМИ.
Описанная выше схема доставки закладочного материала и его засыпки в ствол является наиболее типичной. В практике же ликвидации вертикальных стволов специалистами ОАО «Донецкшахтострой» использовалась несколько отличная схема засыпки стволов (рис. 4.3), когда в зоне
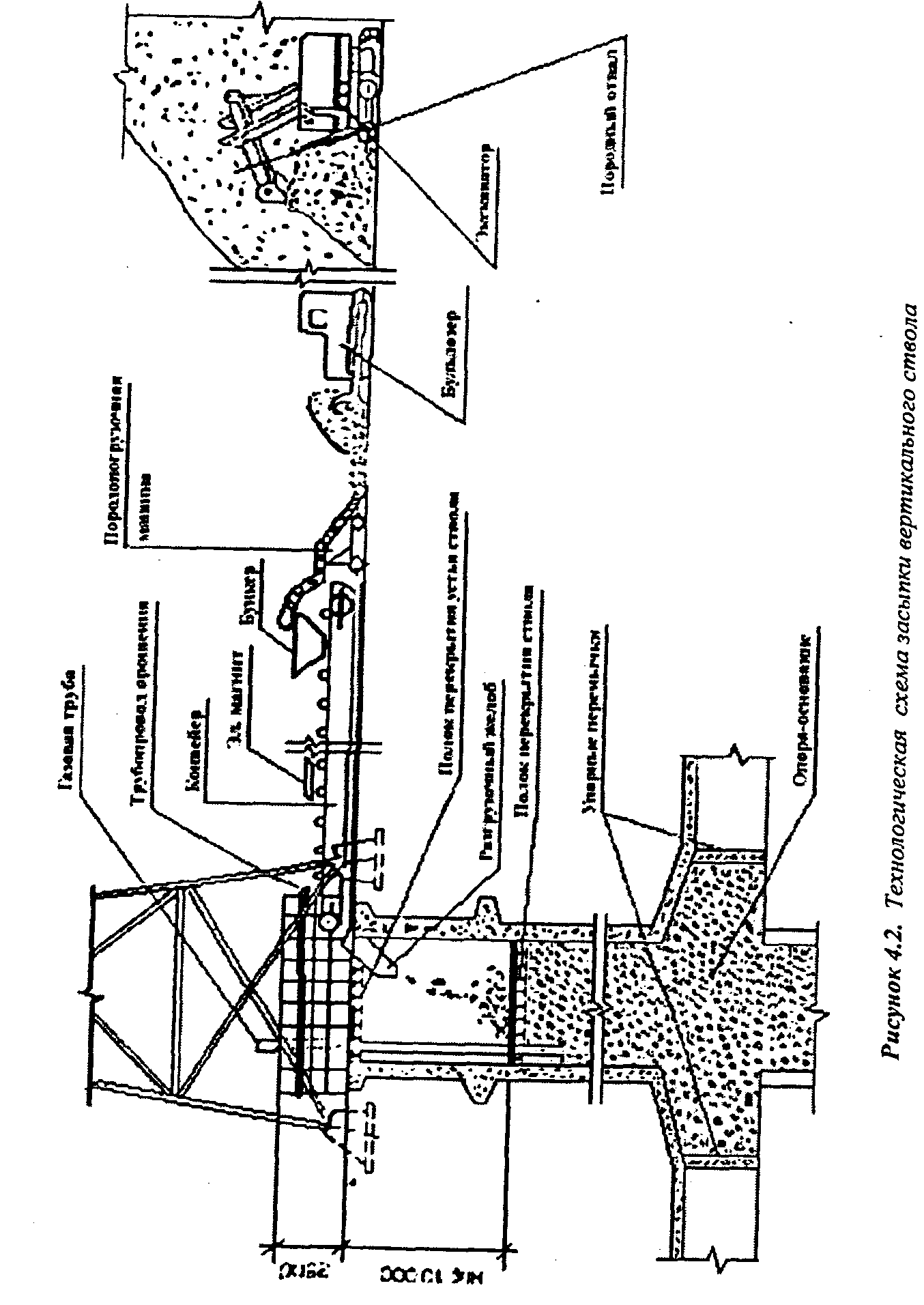
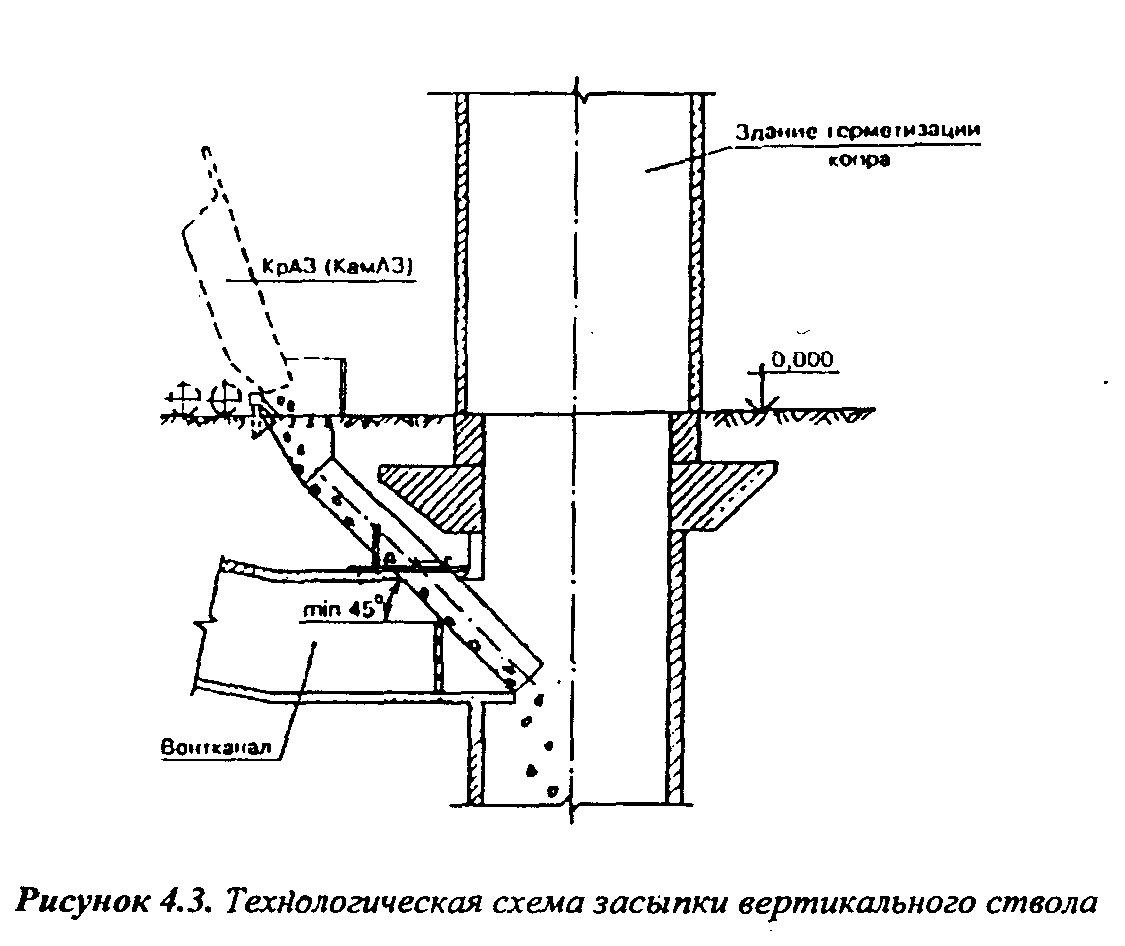
примыкания вентиляционного канала под углом в 45" был выполнен проем, в котором смонтирована труба диаметром 1000 мм. Верхняя ее часть соединялась с приемным бункером, расположенным за пределами надшахтного здания, а нижняя часть опускалась на почву вентиляционного канала с выходом в сечение ствола. Такое техническое решение позволило исключить из технологической схемы установку и длительное обслуживание скребкового конвейера и вести засыпку ствола непосредственно самосвалами. В результате достигнуто снижение стоимости закладочных работ. Вместе с тем при такой технологической схеме соблюдение требований техники безопасности представляется более сложным, здесь необходимы дополнительные специальные мероприятия.
Все оборудование и машины, предназначенные для работы в опасной зоне (зоне газового режима - согласно «Правил...» в радиусе не менее 25 м от ствола) должны быть во взрывобезопасном исполнении.
Пульты управления выносятся за пределы зоны. Допускается ведение огневых работ в пределах зоны газового режима при соблюдении мер безопасности, согласованных с МакНИИ. Нахождение людей в опасной зоне во время работы механизмов по засыпке ствола не допускается.
Пылеподавление осуществляется дренчерными (разбрызгивающими) форсунками. Трубопровод пылеподавления устанавливается над устьем ствола на высоте 2,5 м и крепится к металлоконструкциям копра хомутами.
Подвод воды - по гибкому резиновому рукаву от существующего трубопровода водоснабжения. Расход воды составляет 50 л на 1 м3 закладочного материала.
В процессе засыпки стволов ведется постоянный контроль качества закладочных работ - уровень засыпки ствола измеряется не реже, чем через каждые 50 м заполнения ствола, а также при перерывах в закладке свыше 1 недели. Фактический объем засыпки не должен превышать расчетный более чем на 20%. При уходе закладочного материала в примыкающие выработки и внезапных оседаниях по вертикали на глубину 20 м (при несовершенном контроле соответствия уровня закладки объему засыпанного материала и другим причинам) работы по заполнению ствола приостанавливаются, технология дальнейшего ведения ликвидационных работ уточняется на основании рекомендаций специализированных организаций (УкрНИМИ, МакНИИ и др.).
Если в процессе заполнения обводненных стволов над закладочным материалом скапливается вода, то при достижении уровнем закладочного материала отметки сооружения полка перекрытия ствола, производят откачку воды и организованное направление ее в очистные сооружения через устье ствола.
При ликвидации шахты с полным затоплением горных выработок подземными водами устанавливается (определяется) их статический уровень. Если отметка устьев стволов ниже прогнозируемого статического уровня, то в полках предусматриваются трубы для организованного выпуска воды на поверхность.
Во время ведения закладочных работ запрещается нахождение людей в горных выработках ближе 300 м от ликвидируемого ствола. Для этого все подходы к ликвидируемому стволу со стороны действующих выработок заблаговременно перекрываются путем установки (сооружения) глухих изолирующих перемычек. Если действующие горные выработки расположены на расстоянии менее 300 м от ликвидируемого ствола, подходящие к стволу неиспользуемые выработки должны быть погашены на длине 30-50 м с извлечением крепи и обрушением кровли. Для перепуска воды на погашенном участке по почве выработки прокладывается стальной трубопровод диаметром не менее 100 мм.
З
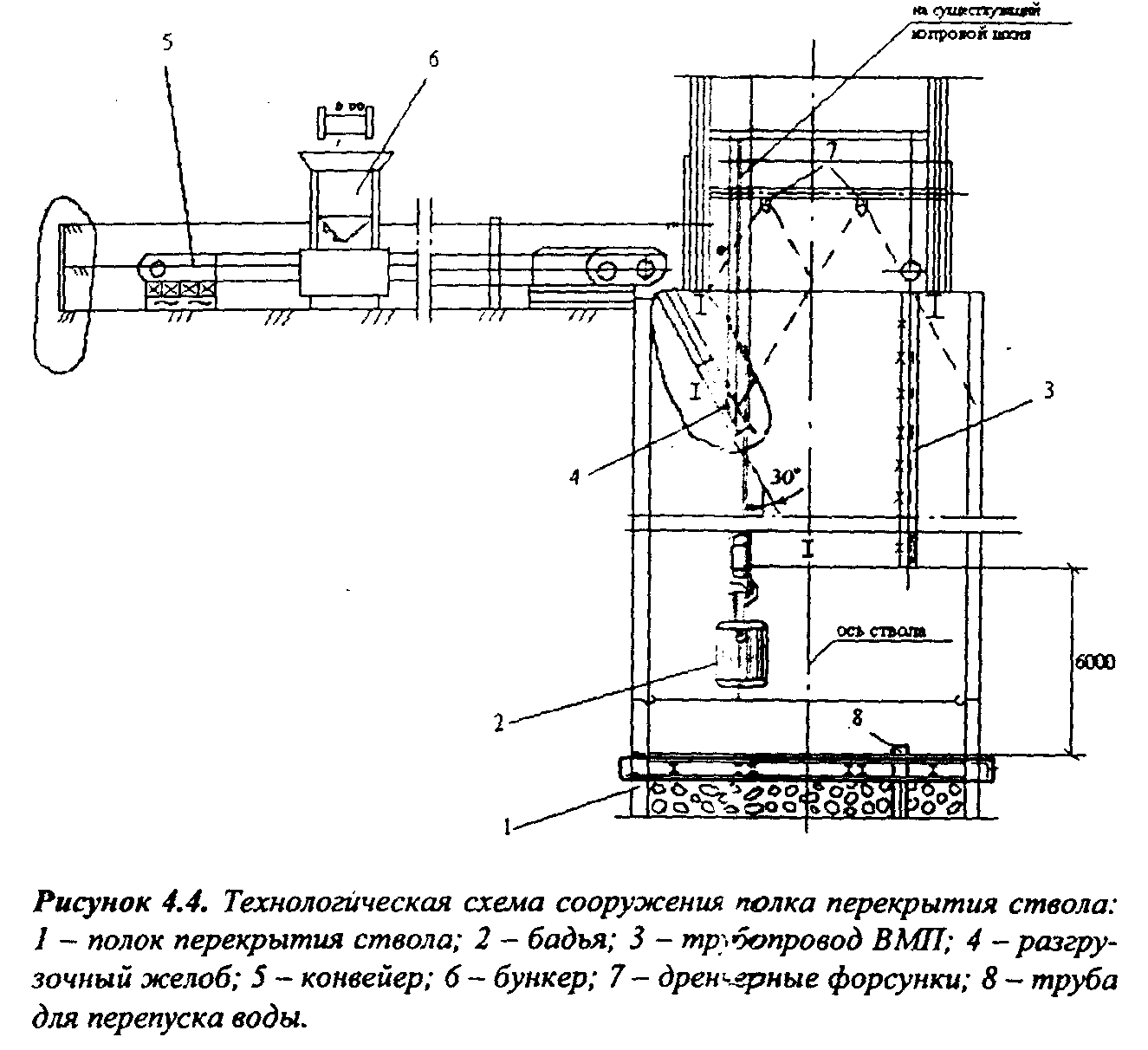
асыпка ствола производится до отметки полка перекрытия ствола, который выполняется с применением тяжелого конструкционного бетона в виде железобетонной плиты (диафрагмы), опирающейся по контуру с помощью металлических балок на коренные породы (песчаники, известняки, сланцы) или на крепь ствола, если она обладает достаточной несущей способностью и долговечностью (рис. 4.4). Глубина заделки металлических балок в монтажные гнезда должна быть не менее 200 мм и определяться в зависимости от толщины крепи ствола и состояния коренных пород. Полок предназначен для обеспечения долговременного квазистатического равновесия вышележащих пород и подземных сооружений и должен обеспечивать восприятие постоянной равномерно распределенной нагрузки от массы закладочного материала с коэффициентом запасы по нагрузке 2. Полок располагается на глубине коренных пород, но не ближе 10 м от поверхности. В полке закладывается труба диаметром 100 мм для перепуска воды в нижнюю часть ствола. При ликвидации стволов с башенными копрами полки перекрытия располагаются в местах фундаментной плиты копра.
До начала работ по сооружению полка перекрытия временно устанавливаются: передвижная проходческая установка типа ЛППР-6,3 (с использованием копрового шкива), вентилятор местного проветривания ВМ-6 с гибким трубопроводом диаметром 600 мм, трубопровод сжатого воздуха, бетоносмеситель, предохранительной полок, зременная металлическая лестница по стволу для спуска рабочих к мест) сооружения полка перекрытия и выхода на поверхность. Налаживается двухсторонняя связь между забоев в стволе и поверхности. При наличие в стволе лестничного отделения его часть (выше места установки полка перекрытия) сохраняется и демонтируется перед засыпкой верхней части ствола от полка перекрытия до поверхности.
Л
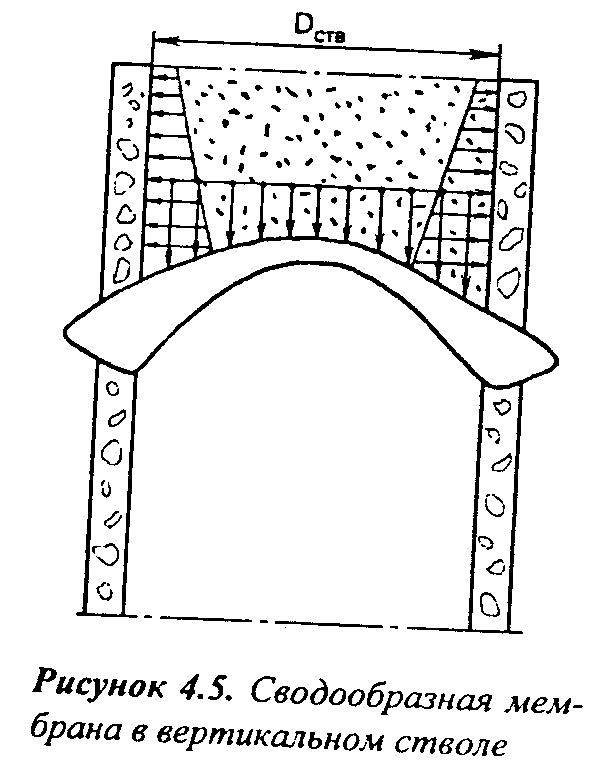
При таких параметрах мембраны вертикальные напряжения концентрируются со стороны торцов мембраны и направлены вглубь массива. Горизонтальные напряжения остаются сжимающими, в целом мембрана находится в состоянии сжатия, что способствует ее длительной устойчивости.
Но для реализации положительного действия мембраны необходимы активная ее пригрузка и распор крепи в окрестности заделки мембраны. Пригрузку можно создать засыпкой мембраны на высоту 20-30 м.
При использовании в качестве полка перекрытия распорной параболической перемычки технология ее возведения (из опыта ликвидации ствола шахты им. Ф.Кона) такова. На расстрелах ствола сооружается опорная плита из балок №36, которые заводятся в заранее подготовленные врубы глубиной 0,5 м. Для возможной дозасыпки в перемычку по центру ствола устанавливается труба диаметром 219 мм. Труба закрывается заглушкой. Сверху на балки укладывается опалубка из досок толщиной 20 мм. Опалубка крепится к опорной плите проволокой 4-6 мм. Производится выемка вруба глубиной 0,5 м по периметру ствола высотой 1,75 м. Затем осуществляется насыпка породной подушки (холма) высотой 1,5 м из мелких фракций. После уплотнения подушки и придания ее поверхности формы параболоида вращения на породу сверху укладывается строительная сетка. Сетка укладывается сегментами внахлестку, сегменты между собой скрепляются проволокой 4-6 мм. Бетон наносится на поверхность холма с помощью установки для набрызгбетона типа «Монолит», расположенной на поверхности у ствола. В процессе набрызга установку обслуживают два специально обученных рабочих. Укладку бетона производится слоями по 10—20 мм. Набрызг начинается от основания холма и постепенно переходит к вершине. Водоцементное соотношение для качественного покрытия ВЦ=0,4 - 0,5. Цемент марки 300. В качестве добавок - ускорителей схватывания и твердения используется жидкое стекло, а заполнителей бетона -песок, дробленый щебень, природный гравий и шлак с максимальными размерами зерен не более 20 мм. Для приготовления смеси цемент, песок и гравий должны быть сухими. Бетонная смесь подается к соплу равномерно без перерывов и пульсаций. Подача воды к соплу осуществляется под давлением на 0,1-0,12 МН/м2 больше давления воздуха в машине и регулируется специальным вентилем. Шланги и сопло перед началом работы продуваются сжатым воздухом.
Контроль состояния стенок (крепи) ствола ниже распорной параболической перемычки может, при необходимости, осуществляться через трубу для дозасыпки основной части ствола при ее усадке с помощью специальных приборов, в частности подземной телекамеры.
Согласно «Правилам...» сооружение полка перекрытия не предусматривается в следующих ситуациях:
• при ликвидации стволов глубиной до 60м;
• в стволах, пройденных в наносах (песок, гравий, галечник, глина, суглинок и т.п.) и неустойчивых породах, имеющих распространение на глубину более 25 м от земной поверхности;
• в технологических скважинах большого диаметра (0,5 м и более), закрепленных стальными трубами;
• в стволах, закрепленных деревянной крепью, крепью из штучного строительного материала;
• при ликвидации стволов, имеющих сопряжения с выработками четырех и более технологических горизонтов (за исключением случая, когда ликвидация ствола выполняется без полной его засыпки на основании заключения УкрНИМИ и согласия органов Госнадзоро-хрантруда).
Принимаемые в указанных случаях технологические решения должны обеспечивать возможность дозасыпки ствола. Дозасыпка технологических скважин диаметром 1 м и менее не требуется.
Одновременно с засыпкой ствола и возведением полка перекрытия монтируется стальной газоотводящий трубопровод диаметром» не менее 100 мм с толщиной стенки не менее 4 мм на проектную высоту (рис. 4.6). Нижний перфорированный (20 отверстий диаметром 20 мм на 1м трубы) конец трубопровода длиной 5 м располагается ниже полка перекрытия ствола.
Верхний конец трубопровода высотой 3 м над уровнем поверхности заваривается металлической сеткой с ячейками 0,35x0,35 мм и оборудуется дефлектором. На расстоянии 1 метр от верхнего конца трубы устанавливается огнепреградитель типа ОПС. Для контроля выхода газа, отбора проб газа на трубопроводе на высоте 1,5 м имеется штуцер или закрываемые заглушками отверстия диаметром 12мм.
Плеть газоотводящего газопровода собирается над стволом методом наращивания с помощью зажимного устройства и по мере наращивания опускается в ствол на глубину установки. Спуск газопровода, как и материалов для сооружения полка перекрытия ствола, осуществляется передвижной проходческой лебедкой ЛППР-6,3. До окончания засыпки ствола «свеча» газоотводящего трубопровода с помощью временного трубопровода отводится от ствола в безопасное место и ограждается. Перед демонтажем копра газоотводящий трубопровод также отводится в безопасную зону.
Для отвода газа допускается использование имеющихся в стволе трубопроводов, если они удовлетворяют изложенным выше требованиям.
П
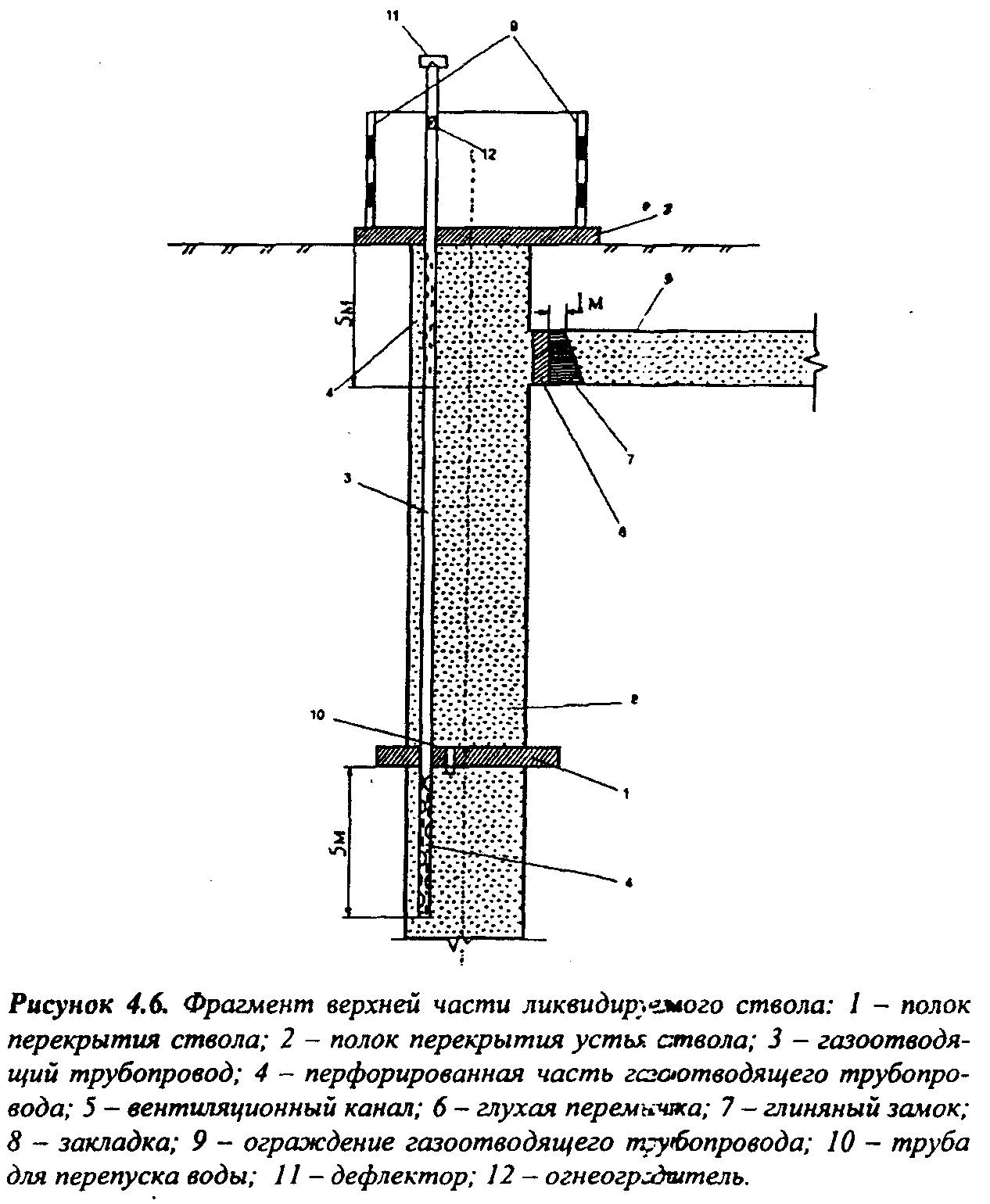
о окончании сооружения полка перекрытия ствола и монтажа газоотводящего трубопровода лестничное отделение выше полка перекрытия (если оно сохранилось) демонтируется, вентиляционный канал перекрывается глухой перемычкой. К этому времени на поверхности разбираются надствольные сооружения (надшахтное здание, копер), настил нулевой площадки. Производится засыпка ствола до верхней части устья. Засыпанная порода с целью уменьшения ее усадки в ряде случаев тампонируется глиноцементным раствором. Для этой цели монтируется тампонажно-растворный узел. Возможно получение закладки большой плотности в
процессе ее возведения путем одновременной подачи в ствол рядовой породы и материала мелких фракций, например песка (рис. 4.7).
Как было отмечено ранее, во время работы механизмов по засыпке ствола нахождение людей в опасной зоне исключается. Это требование отменяется лишь после засыпки ствола до отметки верхнего полка перекрытия устья и монтажа газоотводящего трубопровода на проектную высоту.
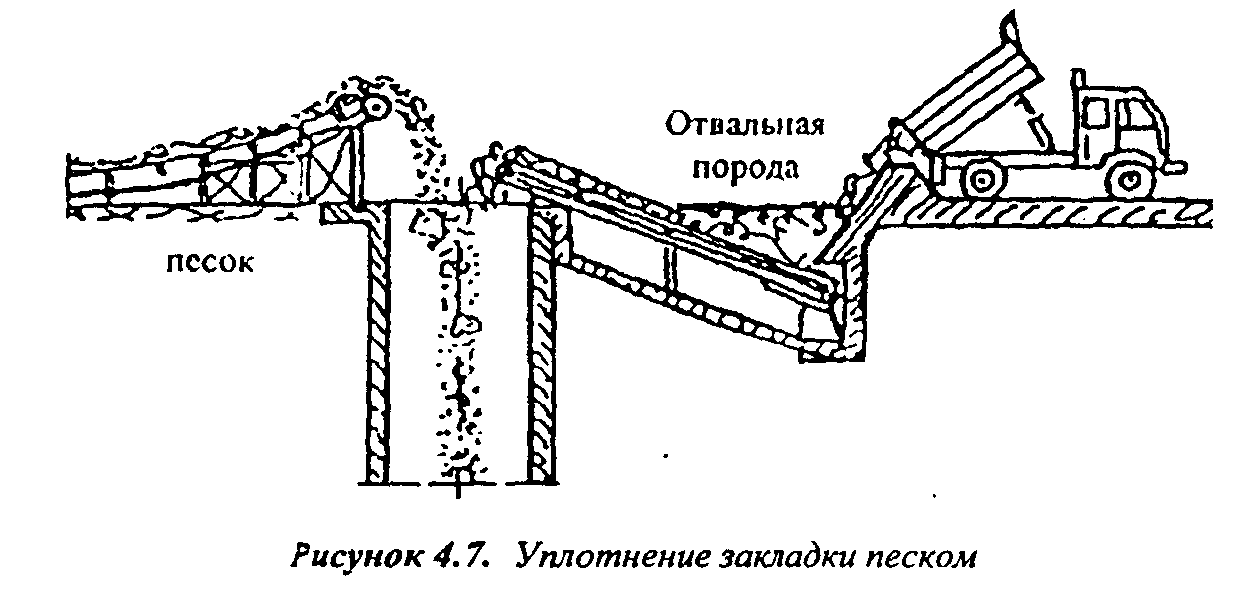
После полной засыпки ствола демонтируется используемое для этого оборудование, демонтируется ограждение опасной зоны, сооружается полок перекрытия устья ствола, «свеча» газоотводящего трубопровода устанавливается в проектное положение.
На постоянном месте «свеча» газоотводящего трубопровода на поверхности ограждается на высоту 2,5 м. Площадка вокруг газоотводящей трубы размером 4x4 м должна иметь твердое покрытие. Ее ограждение на высоту 2 м выполняется из сборных железобетонных конструкций (панелей) без устройства входных проемов. На каждой стороне ограждения газоотводящей трубы ликвидированных вертикальных, крутых, круто наклонных стволов вывешиваются металлические щиты (таблички) с предупреждающей надписью: «Внимание!!! Зона постоянного контроля! Применение открытого огня, движение транспорта, прокладка коммуникаций, строительство опасно!».
После выполнения всех этих работ действие зоны газового режима распространяется только на участок земной поверхности внутри ограждения газоотводящей трубы.
Полок перекрытия устья ствола (рис. 4.8) выполняется с применением тяжелого конструкционного бетона в виде монолитной железобетонной плиты, опирающейся по контуру, как правило, на крепь ствола или грунт в случае недостаточной несущей способности крепи ствола. Полок обеспечивает изоляцию и исключает возможность доступа в ликвидированную выработку, а также служит площадкой для установки долговременных отличительных знаков реперов, газоотводящих труб.
Р
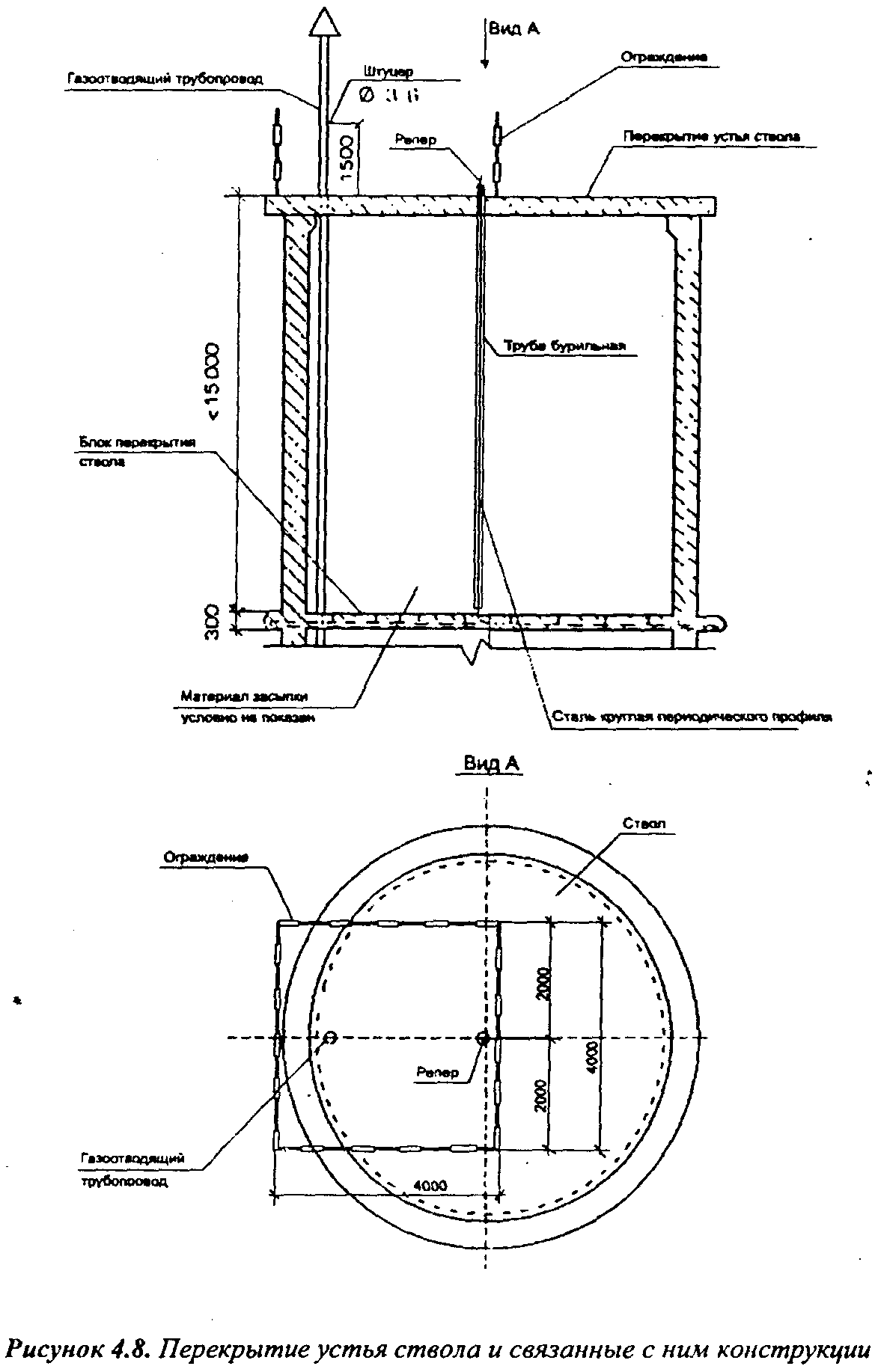
екомендуемая нормативная несущая способность полка от временно равномерно распределенной нагрузки не менее 10 кПа. В случаях, предусматривающих дозасьптку ствола, нормативная нагрузка на полок перекрытия устья ствола принимается не менее 15 кПа.
Для дозасыпки ствола в полке предусматривается люк площадью 0,3-0,5 м2, герметически закрывающийся металлической крышкой (рис. 4.9).
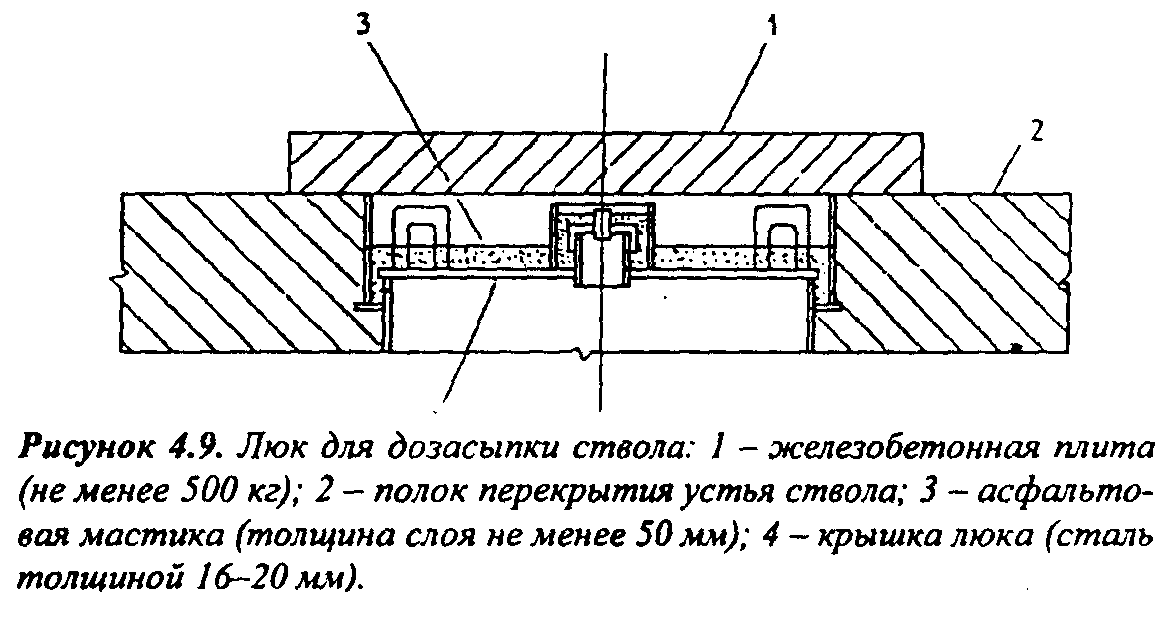
Для обеспечения возможности контроля уровня закладки в стволе крышка люка снабжается патрубком диаметром не менее 100 мм с герметически завинчивающейся пробкой. Съем крышки при засыпке выполняется с использованием расположенных по ее. диагонали двух подъемных петель. С целью исключения случайного (не санкционированного) доступа к люку проем накрывается тяжелой железобетонной плитой, смещение которой невозможно без применения средств механизации. Элементы люка защищаются от коррозии асфальтовой мастикой.
Одновременно с возведением полков перекрытия устанавливается репер для определения перемещения полков (рис. 4.8). Очерчивается и ограждается потенциально опасная зона. Её радиус определятся в каждом конкретном случае, но в средних условия может быть принят равным 20-25 м.
Опасные зоны после ликвидации шахты становятся объектами особого внимания правопреемника.
• Таковы в основе своей технологические схемы и технологии работ по ликвидации вертикальных стволов угольных шахт, принятые в большинстве угледобывающих стран Европы. Однако техногенные аварии и катастрофы в виде внезапных провалов земной поверхности, разрушений зданий и сооружений подобно той, что показана на рис. 4.10, происходят также в большинстве европейских стран и свидетельствуют о том, что эти технологии несовершенны, требуют более глубокого научного анализа, осмысления и на этой основе выработки дополнительных рекомендаций.
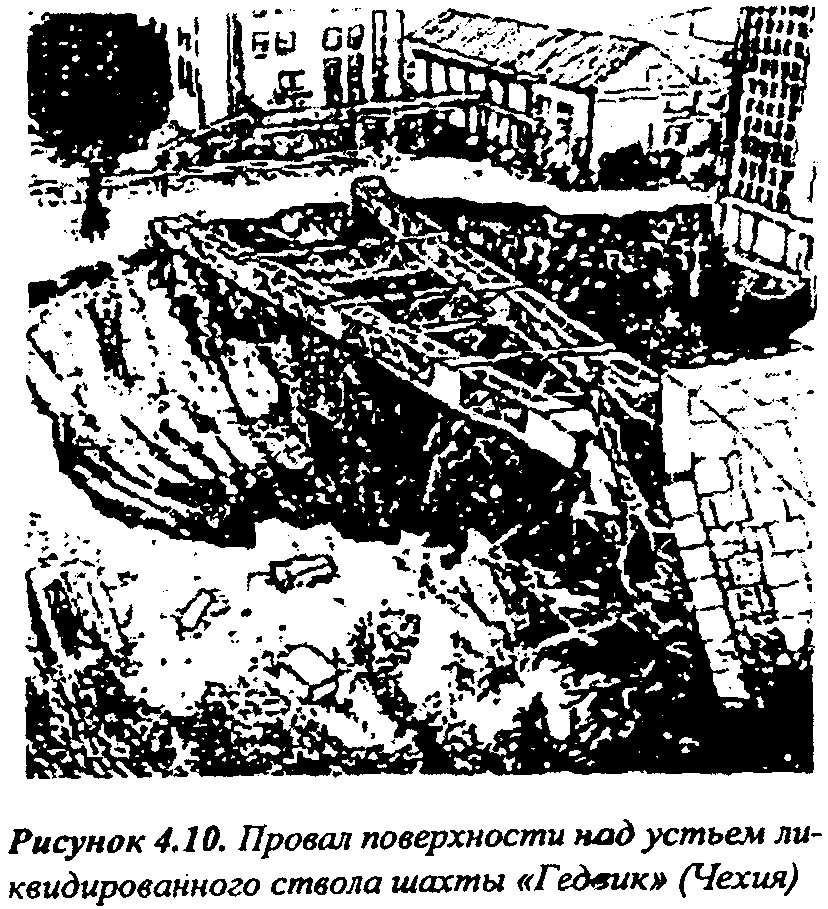
ВОПРОСЫ И ЗАДАНИЯ ДЛЯ САМОКОНТРОЛЯ
/. Какими нормативными документами пользуются при разработке технических решений по ликвидации горных выработок?
2. Какие условия должны соблюдаться при ликвидации горных выработок?
3. Как осуществляется проветривание шахты в подготовительный период?
4. На какие группы подразделяются выработки, имеющие выход на дневную поверхность, по углу наклона?
5. Что включает в себя понятие «ликвидация вертикального ствола»?
6. Всегда ли стволы ликвидируются путей их полной засыпки? В каких условия допускаются отступления от этого правила?
7. Из каких основных частей состоит проект ликвидации вертикально ствола? Изложите кратко их сущность и содержание.
8. Что представляют собой опасные зоны в районе ликвидации вертикальных стволов?
9. Из каких основных этапов состоит весь технологический цикл ликвидации вертикальных стволов:? Изложите кратко содержание каждого из них.
10. Перечислите и кратко охарактеризуйте элементы технологической схемы ликвидации вертикального ствола.
11. Какие машины и оборудование используется при доставке закладочного материала к стволу и засыпке его в ствол? Требование к ним?
12. Назовите основные меры безопасности при засыпке ствола.
13. Что представляет собой полок перекрытия ствола? Назначение, технология возведения? В каких условиях возведение полка не предусматривается.
14. Газоотводящии трубопровод. Назначение, характеристики и технология монтажа?
15. Полок перекрытия устья ствола, его назначение, конструктивные и другие характеристики.
4.1.3. Причины техногенных аварий и концепции долговременной устойчивости погашенных стволов
А
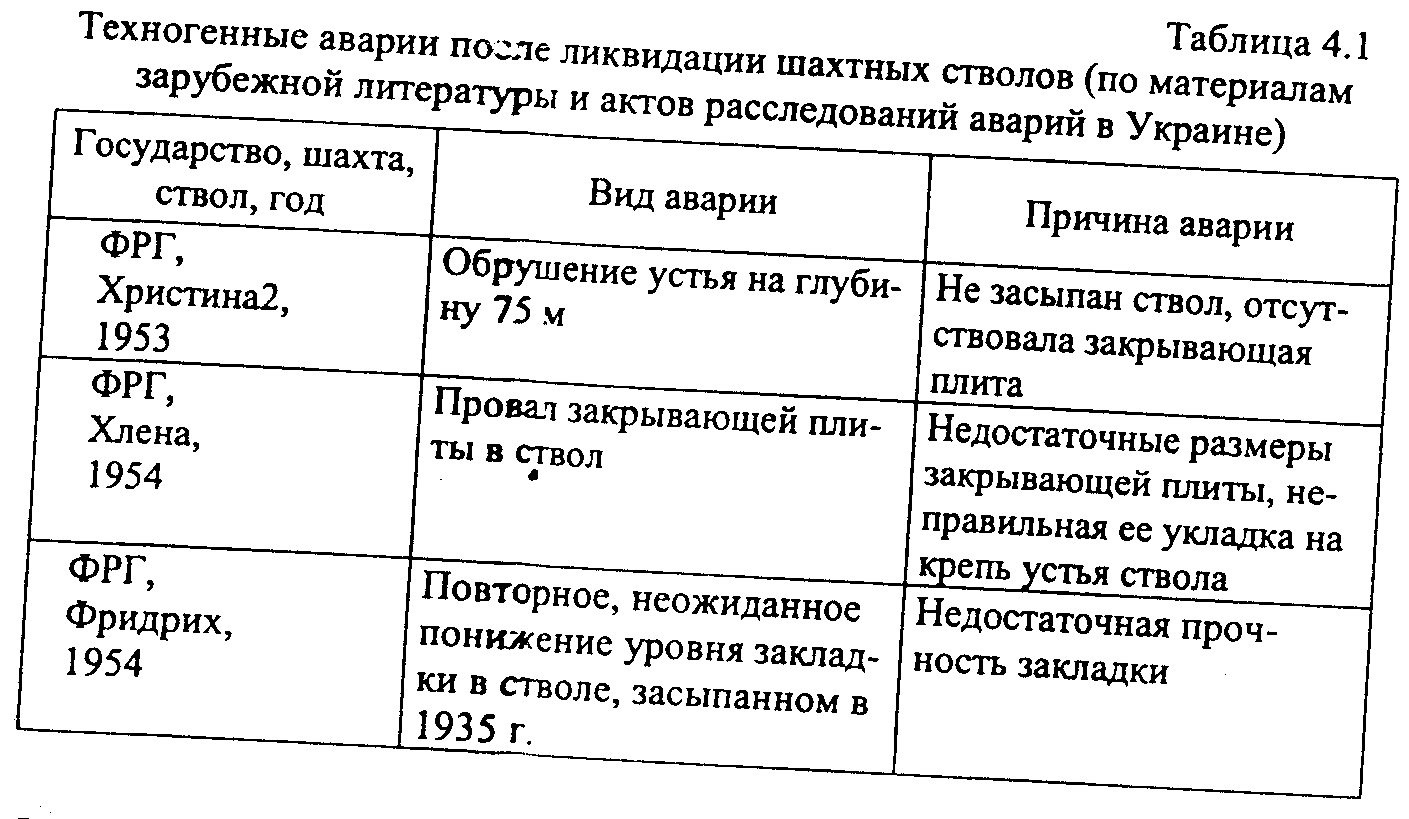
нализ известных техногенных аварий и катастроф в угледобывающих странах Европы (табл. 4.1) показывает, что основными причинами стали: незаполненные или плохо закрытые устья стволов, разрушение под действием горного давления крепи линейных частей стволов при отсутствии в них закладки или чрезмерной ее усадке, разрушение перекрытий стволов или опор на спряжениях ствола с выработками околоствольного двора, утечка закладки из ствола в примыкающие к нему выработки.
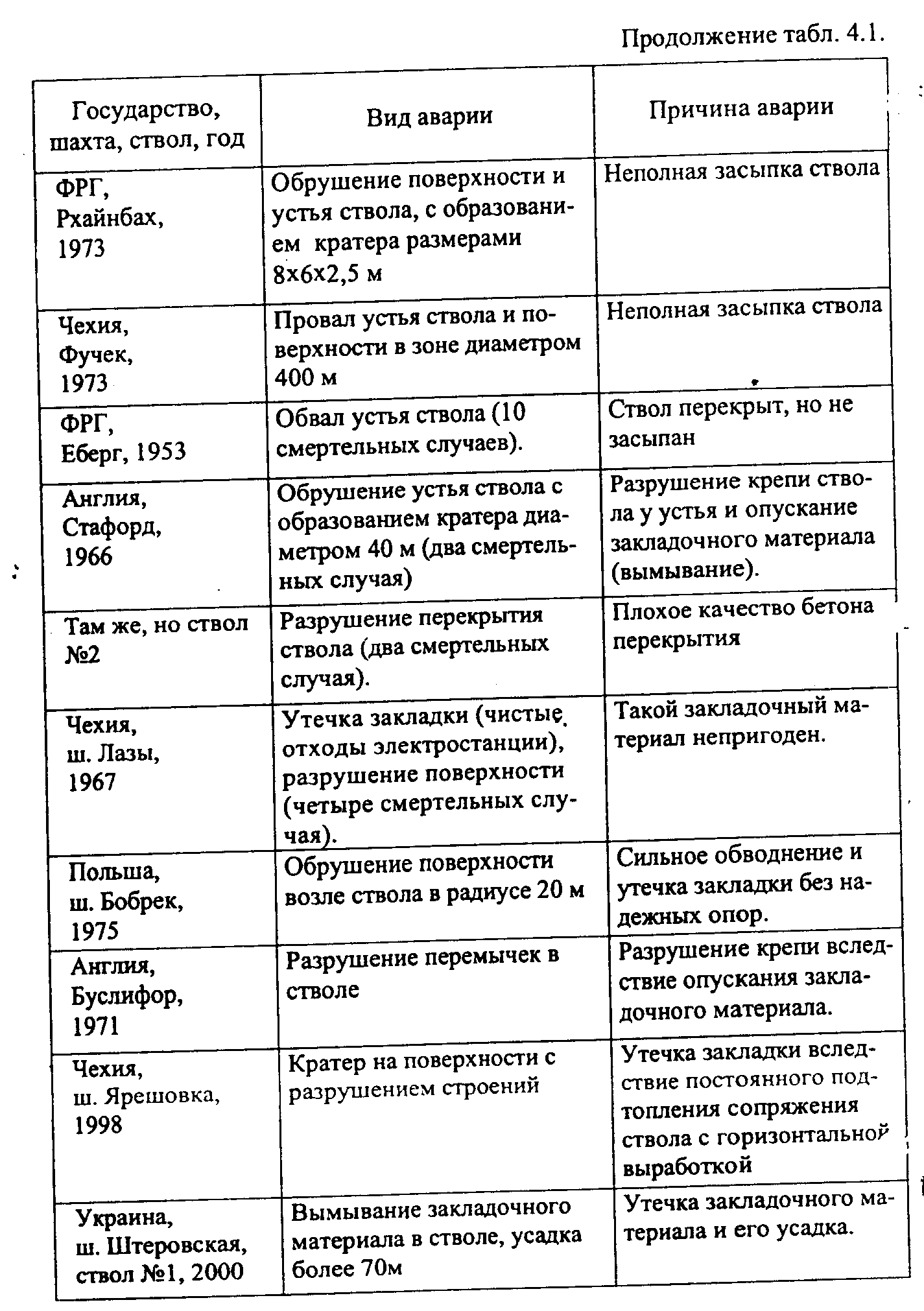
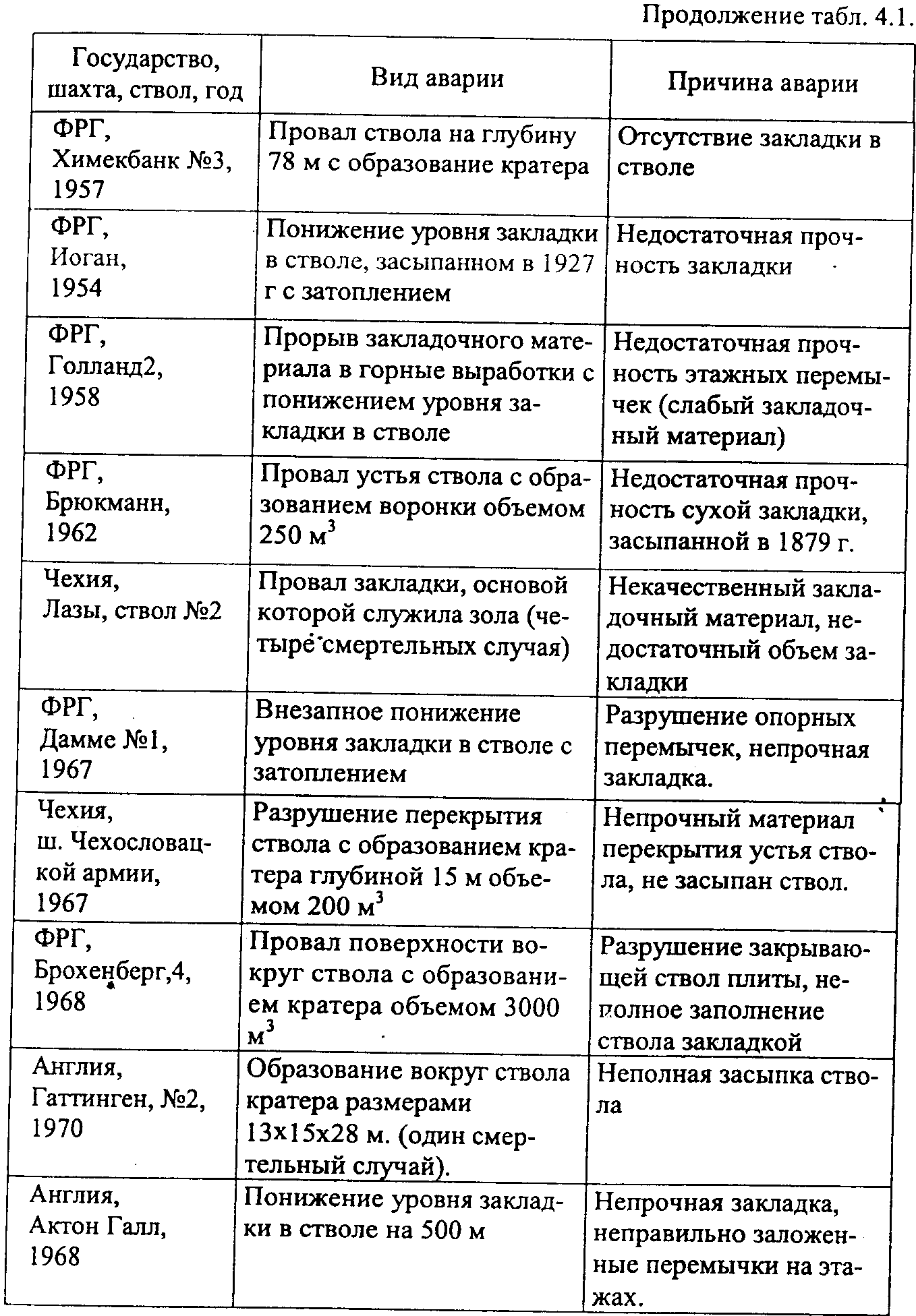
Д
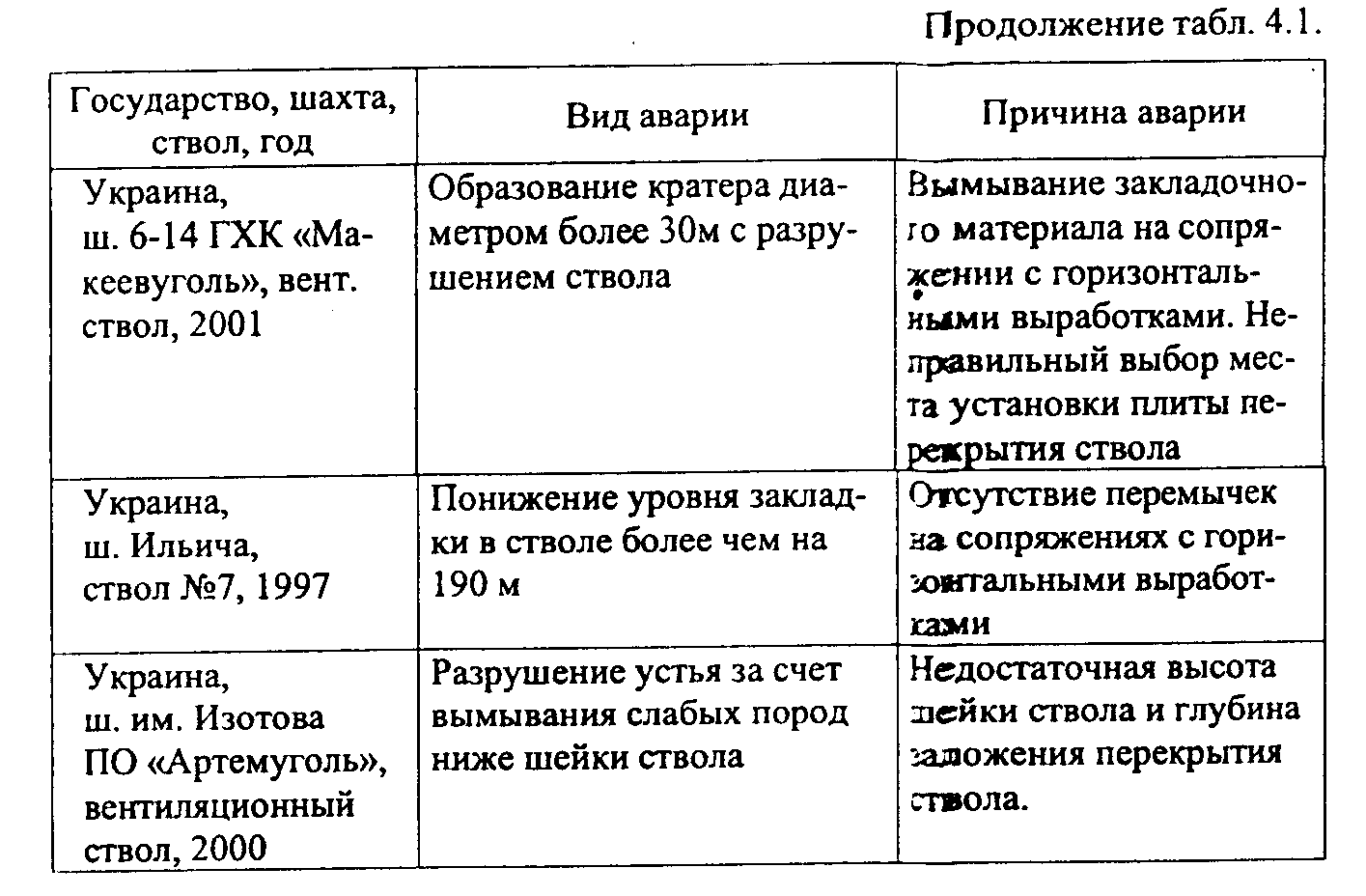
альнейший анализ и некоторые обобщених позволяют заключить, что в общем и целом аварии были предопределены чрезмерным (выше допустимого) горным давлением на крепь ствола ее стороны окружающих его пород, недостаточной в конкретных условиях сопротивляемостью крепи ствола, низким качеством закладки, нарушением устойчивости опорных сооружений в стволе и стабильности собственно устьев стволов. При этом влияющие факторы проявляются раздельно или в различных сочетаниях, но все они безусловно взаимосвязаны и во многом взаимообусловлены. То есть вырисовывается некая геомеханическая система (ГС), которую можно представить в виде взаимовлияющих элементов, в конечном счете, определяющих устойчивость погашенного (ликвидированного) вертикального ствола (рис. 4.11).
В данном случае под геомеханической системой «ликвидированный вертикальный ствол» следует понимать совокупность элементов ее составляющих: вмещающие ствол породы - крепь сгвола - закладка - опорные сооружения в стволе и на спряжениях с горизонтальными выработками - устье ствола, объединенных временным и пространственным взаимодействием и взаимовлиянием.
Под долговременной устойчивостью погашенных стволов, обеспечивающей технологическую и экологическую безопасность (устойчивость земной поверхности в районе ликвидированных ств:люв), следует понимать
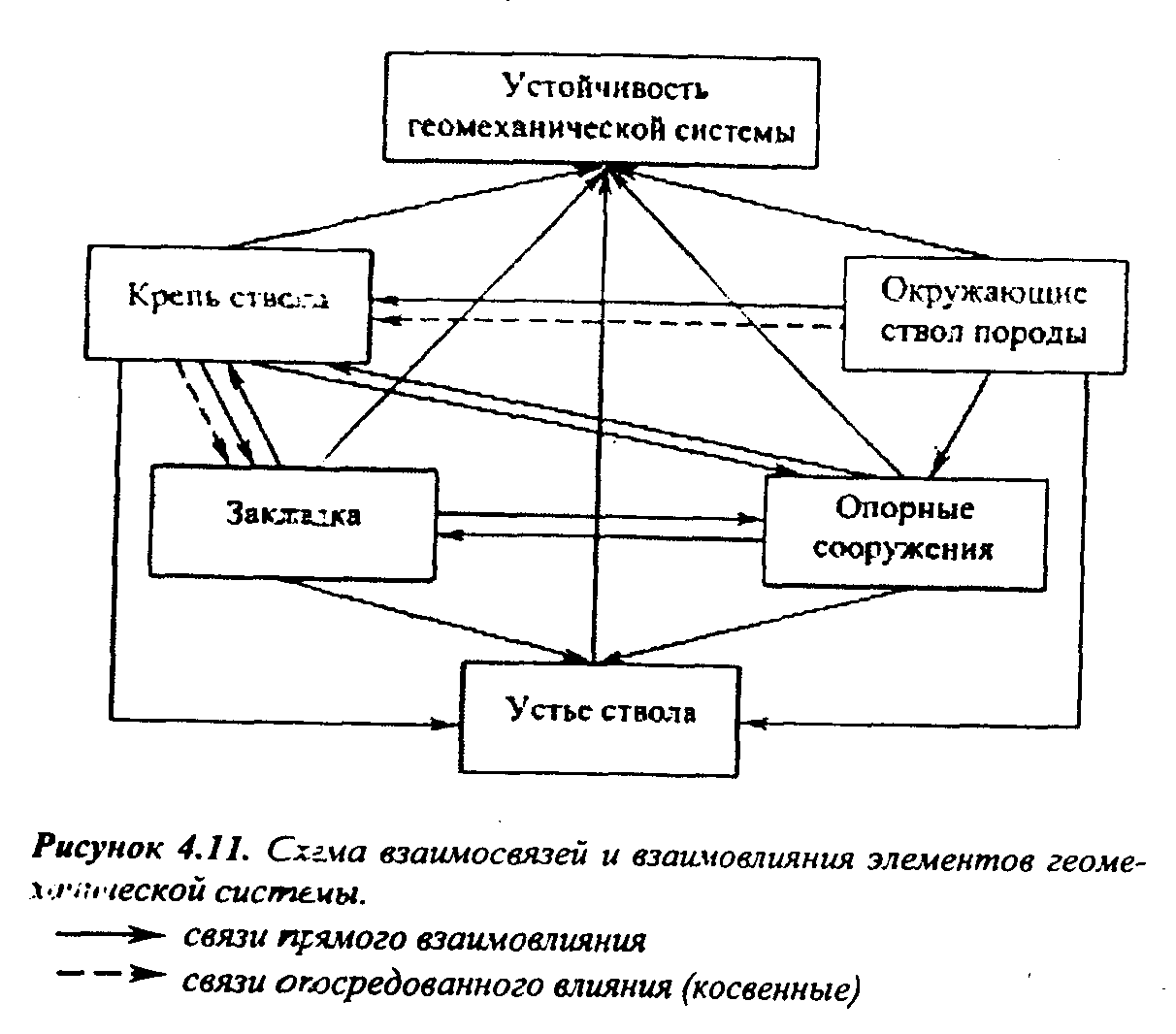
такое состояние геомеханической системы, когда все ее элементы будут уравновешены и это равновесие не нарушится даже при изменении гидрогеологической и сейсмической ситуации. Эта концепция долговременной устойчивости ликвидированных стволов рассматривает систему взаимосвязанных элементов, в которой любой отдельно выделенный элемент нельзя рассматривать и анализировать его влияние в отрыве от иных. Другое дело, что роль и сила влияния каждого элемента могут быть различными в конкретных условиях, однако качественные и количественные связи между ними существуют объективно.
Имеются и другие концептуальные подходы к проблеме долговременной устойчивости погашенных стволов, когда каждый элемент изучается хоть и в увязке с другими элементами, но вне единой геомеханической системы. Здесь речь идет о поиске лучших и даже в какой то мере oптимальных параметров каждого отдельного элемента и на этой основе достижения максимально возможного срока устойчивого состояния ствола (с момента его ликвидации до провала поверхности). Но такое представление о долговременной устойчивости ликвидированного ствола вполне корректно лишь при условии, что погашенный (законсервированный) ствол
через какой-то наперед заданный промежуток времени либо подлежит окончательной ликвидации, либо заново будет использован по своему прямому назначению, или, например, в качестве хранилище.
Как свидетельствует практика эти варианты скорее исключение, чем правило, хотя в определенных условиях могут быть оправданы.
В предлагаемой же редакции речь идет о полной и окончательной ликвидации стволов закрываемых шахт. В связи с этим концепция долговременной устойчивости погашенного ствола на основе единой геомеханической системы, когда ее элементы уравновешены и образуют единый массив близкий к природному, представляется более привлекательной как с теоретической так и практической точек зрения.
Из представленной схемы (рис. 4.11) видно, что все элементы геомеханической системы оказывают прямое влияние на ее устойчивость.
По числу взаимовлияющих связей лидирующее место занимает устье ствола (4 связи), по 3 связи имеют опорные сооружения, крепь ствола и закладка. Это позволяет в определенной степени судить об «ответственности» соответствующего элемента за судьбу системы, ее устойчивость.
С позиции влияния на устойчивость геомеханической системы целесообразно рассматривать как единое целое - закладочный массив, состоящий из закладки и опорных сооружений. В этом случае, как следует из приведенной схемы (и практика тому подтверждение), его роль значительно возрастает.
Прямые и обратные связи, существующие между отдельными элементами системы (крепь ствола - закладка, закладка - опорные сооружения), потенциально позволяют находить альтернативные решения путем усиления одного элемента при ослаблении другого.
Кроме прямых (односторонних и двухсторонних) связей между влияющими факторами следует обращать внимание на возможное появление связей опосредованного влияния, например окружающих ствол пород на закладку.
Решение проблемы долговременной устойчивости вертикальных стволов, а, следовательно, и поверхности возможно только на основе использования системного подхода к решению комплекса вопросов, связанных с конкретным влиянием каждого элемента как во времени так и в пространстве.
Поэтому необходимо должным образом изучить конкретные свойства каждого элемента геомеханической системы, установить их качественные и количественные характеристики, параметры, более глубоко понять и уяснить взаимосвязи элементов, поскольку они оказывают решающие влияние при проектировании технологических схем ликвидации вертикальных стволов, а также на планирование ликвидационных работ в целом.
Чрезвычайно важно и то обстоятельство, что исследование элементов системы позволяет определить возможности изменения их характеристик путем принятия и реализации соответствующих технико-технологических и организационных решений.
Критерием при выборе параметров всей геомеханической системы является обеспечение равновесного силового взаимодействия ее элементов. В таких условиях наиболее целесообразно использовать моделирование и оценку отдельных подсистем с последующей интеграцией в них новых элементов: «вмещающие породы - крепь ствола», «вмещающие породы - крепь ствола - закладка», затем с учетом опор в стволе и на сопряжениях с горизонтальными выработками и т.д., что в конечном итоге позволит сконструировать технологическую схему ликвидации ствола при оптимальных параметрах элементов геомеханической системы..
ВОПРОСЫ И ЗАДАНИЯ ДЛЯ САМОКОНТРОЛЯ
1. Назовите основные принципы техногенных аварий в районе погашенных вертикальных стволов.
2. Что дает основание говорить об объективном существовании ГС «погашенный вертикальный ствол»?
3. Назовите основные элементы ГС «погашенный вертикальный ствол», изобразите их взаимосвязи.
4. Что следует понимать под долговременной устойчивостью ликвидированного ствола? В чем принципиальное отличие этого понимания от других концепций долговременной устойчивости погашенного ствола?
4.1.4. Окружающие ствол породы - крепь ствола
Равновесное состояние этой подсистемы зависит от соотношения сил давления окружающих ствол пород и несущей способности (сопротивляемости) крепи. И пока горное давление не превышает сопротивляемость крепи, ствол находится в устойчивом состоянии.
Но это общая постановка вопроса об устойчивости ствола, которая закладывается на стадиях его проектирования и сооружения в конкретных горно-геологических условиях. В период эксплуатации ствола осуществляется постоянный контроль за состоянием его крепи, при необходимости производится ее ремонт, усиление, частичная замена и др.
Известно, что величина горного давления на крепь главным образом зависит от физико-механических характеристик окружающих ствол пород. Чем слабее породы, тем больше давление. Прочностные же характеристики пород зависят не только от литологического состава, но и от обводненности пород. Поэтому на этапе строительства ствола и его эксплуатации принимаются меры по упрочнению слабых слоев пород, гидроизоляции отдельных участков ствола и т. п.
После же ликвидации ствола описанные выше мероприятия по сохранению его устойчивости практически исключаются. Происходит постепенное разрушение крепи ствола под действием давления окружающих ствол горных пород, напорных и безнапорных подземных вод, других природных процессов, а также естественное разрушение крепи вследствие ее «старения» (эрозия, коррозия бетона, выщелачивание и др.).
Таким образом, с достаточной уверенностью можно утверждать, что в условиях крепких монолитных слабо обводненных пород устойчивость ствола определяется временем несущей способности крепи до ее естественного разрушения, а в слабых обводненных породах разрушение крепи ускоряется за счет роста на нее горного давления, то есть время устойчивого состояния подсистемы «окружающие ствол породы - крепь ствола» (в дальнейшем «порода - крепь») определяется прежде всего скоростью «старения» крепи и характером изменения горного давления во времени.
Однако это главным образом качественная характеристика происходящих процессов. На деле давление на крепь изменяется во времени неравномерно и зависит от многих факторов (неоднородности физико-механических свойств пород, способа проходки ствола, гидрогеологии) и носит неопределенный характер.
Потеря или снижение несущей способности крепи ствола также не поддается точной количественной оценке в связи с тем, что крепь одного и того же ствола возводилась в различных конструктивных вариантах, из неоднородных материалов, в разных вмещающих погодах, в местах с различными гидрологическими условиями. Процессы фильтрации, инфильтрации, выщелачивания, биохимические и другие также труднопрогнозируемы.
Складывается некая неопределенно-вероятностная система, состояние которой можно прогнозировать только с определенным риском. Поэтому для объяснения потери устойчивости ствола принята подтвержденная практикой, логически понятная и физически объяснимая гипотеза: несущая способность крепи (К) снижается во временя (t) вследствие ее «старения» и, в конечном счете, крепь разрушается без внешнего воздействия, а давление окружающих ствол пород (П) на крепь ствола увеличивается или в определенных условиях стабилизируется.
Однако, как было сказано ранее, разрушение крепи может произойти и без влияния потного давления, а в силу ее «старения», т.е. в силу того. что после ликвицации ствола происходит непрерывное снижение несущей способности крепи вплоть до ее естественного разрушения.
И эта закономерность может быть представлена в виде экспонентального распределения (рис. 4.12).
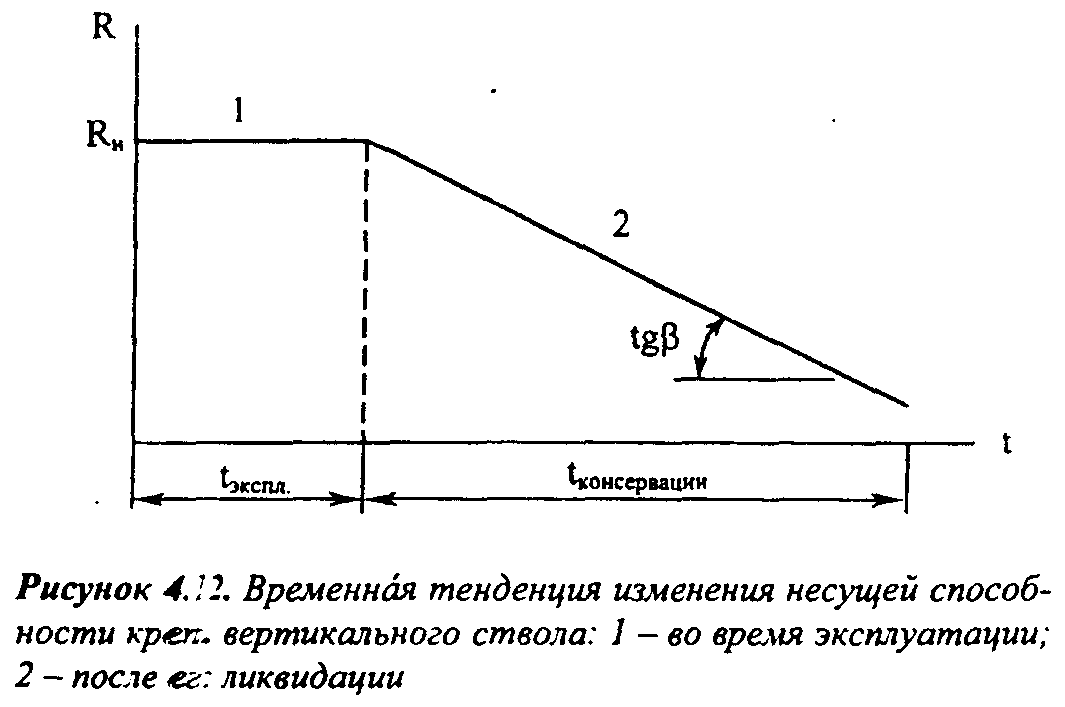
Линию развития тенденции (тренда) 2 можно представить в виде экспоненты
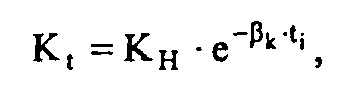
где Кн - начальная несущая способность крепи ствола (на момент окончания его эксплуатации). Определяется опытным путем;
β, — коэффициент временной интенсивности снижения несущей способности крепи, численно равен tg
Величина φ определяется по результатам периодической диагностики состояния крепи ствола в различные периоды его эксплуатации (главным образом перед ремонтными работами) и на заключительном этапе перед его ликвидацией. Экспериментальные данные по диагностике coстояния бетонной крепи стволов позволяют заключить, что в первом приближении tgφ =0,016.
Рост горного давления на крепь зависит от деформируемости окружающего ствол массива, которая происходит даже при постоянных напряжениях в связи с угеличением зоны разрушения пород. А так как напряжения в массиве пород, непосредственно контактирующих с крепью ствола, пропорциональны скорости его деформации, то рост нагрузки на крепь будет подчиняться этому же закону, т.е.
(4.3)
где ПН - начальное давление окружающих ствол пород. Определяется экспериментально.
βп - коэффициент временной интенсивности роста горного давления. В первом приближении
βп = Ε/η. (4.4)
Коэффициент η называется коэффициентом динамической вязкости. Чем больше η, меньше скорость деформации при постоянных напряжениях (более крепкие породы), тем медленнее растет нагрузка на крепь ствола. В гаком смысле геомеханическую подсистему «порода-крепь» можно считать реологической, когда напряженно деформированное ее состояние изменяется во времени.
Значения Ε, η и βп приведены в таблице 4.2
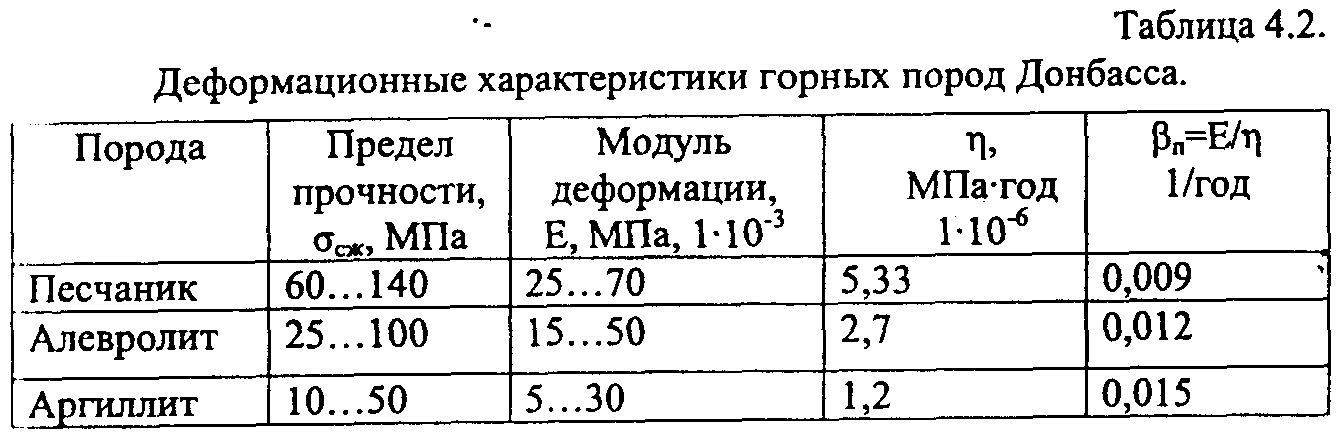
В соответствии с принятой рабочей гипотезой временное развитие тенденции изменения несущей способности крепи ствола и изменения горного давления на крепь представим следующим образом (рис. 4.13). На графике можно выделить три области состояния подсистемы «порода -крепь». Первая К - Π > 0 - система устойчива, разрушения крепи не происходит. Вторая К - Π < 0 - крепь будет разрушаться под действием горного давления. Третья, где даже при формальном К - Π >0 (при отсутствии горного давления) произойдет естественное разрушение крепи в силу ее «старения» (Ккр ).
Таким образом, разрушение крепи ствола может происходить на активных стадиях роста горного давления и снижения несущей способности
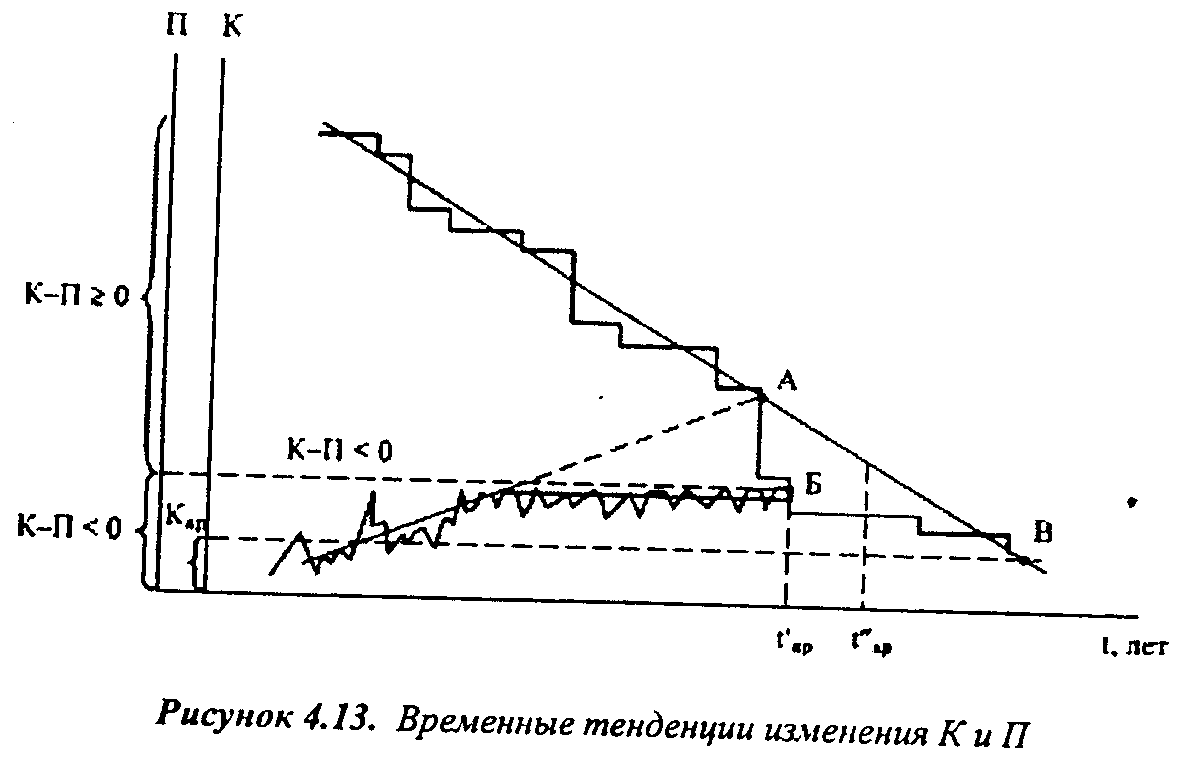
крепи (точка А), это, во-первых, во-вторых, когда давление горных пород возрастает, стабилизируется и «поджидает» момент снижения несущей способности крепи до определенного уровня (точка Б), и, в-третьих - разрушение крепи ствола происходит без участия горного давления за счет «старения» крепи и взаимодействия с окружающей средой (точка В).
Из уравнений (4.2 и 4.3) можно найти время нарушения устойчивого равновесия подсистемы «порода-крепь» под влиянием горного давления и снижения несущей способности крепи ствола в соответствии с временными тенденциями изменения К и П.
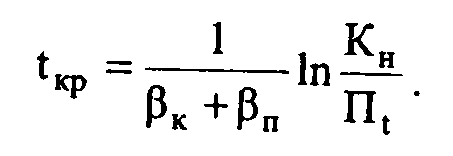
Расчеты показывают, что в идеальных усредненных условиях, когда крепь ствола сохраняет (не меняет) свою несущую способность, ствол (участки ствола) при соотношении Кц/П, -10 сохраняет свою устойчивость: в песчаниках - в течение 250 лет, в алевролитах - 200 лет, в аргиллитах - 150 лет. В условиях же «старения» крепи (наиболее характерная ситуация) эти величины будут равны 100, 80, и 70 годам соответственно.
Полученные расчетные данные следует рассматривать лишь как ориентировочные, максимально возможные, поскольку значения всех входящие в формулу (4.5) параметров по объективным причинам имеют сравнительно невысокую достоверность. Кроме того характеристики одних и тех
же по литологическому составу пересекаемых стволом пород, а также материала крепи по глубине ствола меняются в значительном диапазоне.
Следует заметить, что существуют и другие методики определения времени устойчивости подсистемы «порода- крепь», но все они сложны, а получаемые результаты вряд ли более достоверны.
Итак, достижение стабильности подсистемы «порода-крепь» и на этой основе долговременной устойчивости ствола может идти по двум направлениям: снижение горного давления окружающих ствол пород и повышение несущей способности крепи ствола.
Первое направление менее перспективно. Совершенно очевидно, что на окружающие ствол породы повлиять трудно. Их упрочнение или мало эффективно, или слишком трудоемко и дорого. Обводненность же пород, что при «мокром» способе закрытия шахт случается непременно, сказывается серьезно: уменьшается крепость, снижается устойчивость, увеличивается давление на крепь.
Второе направление имеет более широкие возможности, но здесь временные ограничения весьма существенны. Крепь ствола можно усилить после ее диагностики перед ликвидацией ствола.
В настоящее время методы диагностики достаточно совершенны, а способы усиления крепи сравнительно эффективны. В частности методом электрометрии возможна оценка состояния приконтурной зоны породного массива, качества различных видов крепи, качественного распределения напряжений на сопряжениях ствола с горизонтальными выработками. Этот метод позволяет оценить не только асимметрию формирования зоны неупругих деформаций, но и косвенно определить неравномерность распределения нагрузок на крепь ствола со стороны перемещающегося массива. С использованием метода регистрации естественного электромагнитного излучения материала, находящегося в напряженном состоянии, возможно бесконтактное выявление наиболее напряженных участков поверхности ствола.
При использовании виброакустического метода возможна оперативная оценка степени механического контакта крепи окружающим массивом.
В качестве мер, направленных на стабилизацию подсистемы «порода-крепь» в конкретных условиях, используются ремонтно-профилактические работы, работы по усилению сопряжений, ремонт и замена крепи; цементация, бетонизация или битумизация закрепного пространства, заделка швов крепи и др.
Обследование стволов показало, что нарушение крепи чаще всего происходит на участках пересечения стволом прослойков и слоев глинистых сланцев, когда они залегают между мощными слоями более крепких пород. Особо опасными являются узлы сопряжений стволов с примыкающими выработками. Там напряжения вдвое больше, чем на обычных (протяженных, линейных участках ствола, так как под влиянием ствола крепь сопряжений испытывает повышенное давление пород. Кроме того, нарушение крепи горизонтальной выработки на участке сопряжения, как правило, влечет за собак нарушение крепи ствола. И уж особую опасность в отношении нарушения подсистемы «порода-крепь» представляют устья стволов, расположенные в большинстве своем в слабых и сильно обводненных породах.
Понимание и учет сказанного позволяет принимать обоснованные инженерные решения лри подготовке стволов к ликвидации.
Однако вышеизложенное свидетельствует и о том, что обеспечить абсолютную надежность подсистемы «порода-крепь» невозможно ни с теоретической, ни с тактической точек зрения. Раньше или позже наступит такой момент, когда эта подсистема неизбежно выйдет из равновесия, а это повлечет за собой нарушение устойчивости всей геомехапнической системы «погашенный вертикальный ствол», что в итоге приведет к провалу земной поверхности в его окрестностях.
Повысить же вероятность достижения долговременной устойчивости погашенного вертикального ствола во многом по большому счету может закладка, создающая стпор крепи и уравновешивающая силовое взаимодействие «порода - крепь».
А поскольку загладка является не только важнейшим элементом, определяющим устойчивость геомеханической системы
«ликвидированный вертикальный ствол», но и, как никакой другой, поддается учету, расчету, инженерно-техническому регулированию, оптимизации и экономической оценке, то она и подлежит более углубленному рассмотрению.
ВОПРОСЫ И ЗАДАНИЯ ДЛЯ САМОКОНТРОЛЯ /. От чего зависит равновесное состояние подсистемы «окружающие ствол породы - крепь ствола»? Какие факторы оказывают на это влияние?
2. Назовите основные причины роста горного давления на крепь ствола и потери ее несущей способности.
3. Какая рабочая гипотеза принята для объяснения потери устойчивости системы «порода-крепь»?
4. Как представляется временное развитие тенденций изменения несущей способности крепи ствола и изменения горного давления на крепь в соответствии с принятой рабочей гипотезой?
5. Назовите и охарактеризуйте основные направления повышения стабильности подсистемы «порода-крепь». Какие практические меры позволяют это осуществить?
4.1.5 Закладка и ее роль в достижении стабильности геомеханической системы «погашенный вертикальный ствол»
Как было отмечено ранее, «Правила безопасности в угольных шахтах» при ликвидации вертикального ствола требуют полного его заполнения (засыпки) негорючим, неразмокаемым, нерастворимым и нетоксичным материалом. Материал, которым заполняется ствол, получил название закладочного, а размещенный в стволе - закладки.
По своему агрегатному состоянию различают закладку сыпучую и твердеющую, а по гидрологическим условиям ее нахождения в стволе -сухую и обводненную. Все виды закладок имеют свои особенности, рабочие характеристики, которые следует учитывать при оценке степени их влияния на уровень стабильности геомеханической системы «погашенный вертикальный ствол».
Закладка в стволе, и это ее главная задача, призвана максимально усилить подсистему «порода-крепь» за счет бокового отпора крепи, повысить сопротивляемость крепи горному давлению со стороны окружающих ствол пород.
И эту функцию закладка может выполнить лишь при условии, что она будет обладать нужными качествами, которые зависят прежде всего от характеристик закладочного материала и технологии закладочных работ.
Важнейшими характеристиками и свойствами закладочного материала являются: минеральный состав, механическая прочность, структура (кусковатость, форма частиц, фракционность - гранулометрический состав), величина сцепления частиц - сопротивление сдвигу, связность, компрессионные свойства, величины сил внешнего и внутреннего трения; деформационные характеристики, другие физико-механические свойства, которые в основном определяют плотность, кусковатость и, в конце концов, усадку закладки.
Усадка же закладки определяет величину обнажения крепи ствола, возможное ее разрушение с последующими деформациями ствола и окружающих его пород вплоть до земной поверхности.
Именно вид закладочного материала, прежде всего, определяет основные характеристики закладки и поэтому требует более детального рассмотрения.
В практике ликвидации вертикальных стволов в качестве закладочного материала широко используется карбоновые горные породы. В большинстве своем ориентируются на породы из рядом расположенных шахтных отвалов. И если всесторонний лабораторный анализ этих пород не подтверждает возможных ограничений (горючесть, способность к образованию вредных испарений и токсичных веществ при выщелачивании в условиях затопления (обводнения) ствола, в том числе высокоминерализиро-ванными, афессивными шахтными водами), то эта порода и используется для засыпки стволов.
Оценивая ситуацию в Украине, следует отметить, что и на ближайшую перспективу в качестве закладочного материала будут использоваться породы отвалов угольных шахт. Закладка из этих пород обладает достаточно хорошей водо- и газопропускной способностью. Сухой закладочный материал породных отвалов имеет еще одно положительное свойство -при падении дробиться и самоуплотнятся. Большая привлекательность использования этого закладочного материала объясняется и незначительным удалением его запасов от ликвидируемых стволов, сравнительно малой стоимостью. Кроме того «разборка» породных отвалов улучшает экологическую ситуацию в районе их размещения.
В тоже время следует иметь ввиду, что для пород отвалов характерно присутствие в них большого количества тонкодисперсных глинистых частиц. А это значит, что при значительном обводнении, при наличии фильтрации и инфильтрации воды в стволе они склонны к размоканию и вытеканию в сопрягающиеся со стволом выработки.
В практике ликвидации стволов используются и материала карьеров -щебень, песок, гравий, а также быстроохлажденые металлургические шла ки, которые обладают высокой механической прочностью, узкофракцион-ностью, неразмокаемостью, малой усадкой. Но они дороги.
Диспергированный материал - золы и шлаки электростанций, доменные шлаки, отходы цементных заводов и'др. - однородны по гранулометрическому составу, способны при определенных условиях переходить в твердое агрегатное состояние и «связать» более крупные частицы, но в тоже время и образовывать суспензию, способную вытекать из ствола в примыкающие к нему выработки.
Вышеназванные материалы представляют собой дискретные с определенными формами и размерами физические тела, которые могут, в большей или меньшей мере, претерпевать изменения под воздействием внешних сил - механических, гидродинамических, горного давления, а также физико-химических процессов.
Важнейшими рабочими характеристиками сыпучего закладочного материала является его гранулометрический состав (размеры частиц) и форма частиц. И та и другая характеристики оказывают существенное влияние на процесс укладки материала, который определяет плотность закладки и, в конечном счете, скорость и величину ее усадки в фракционном составе материала плотность закладки становится максимальной, а пустотность - минимальной (рис. 4.14). Из рисунка следует, что при наличии в закладке только крупных (например, более 80 мм в поперечнике) фракций ее пустотность может
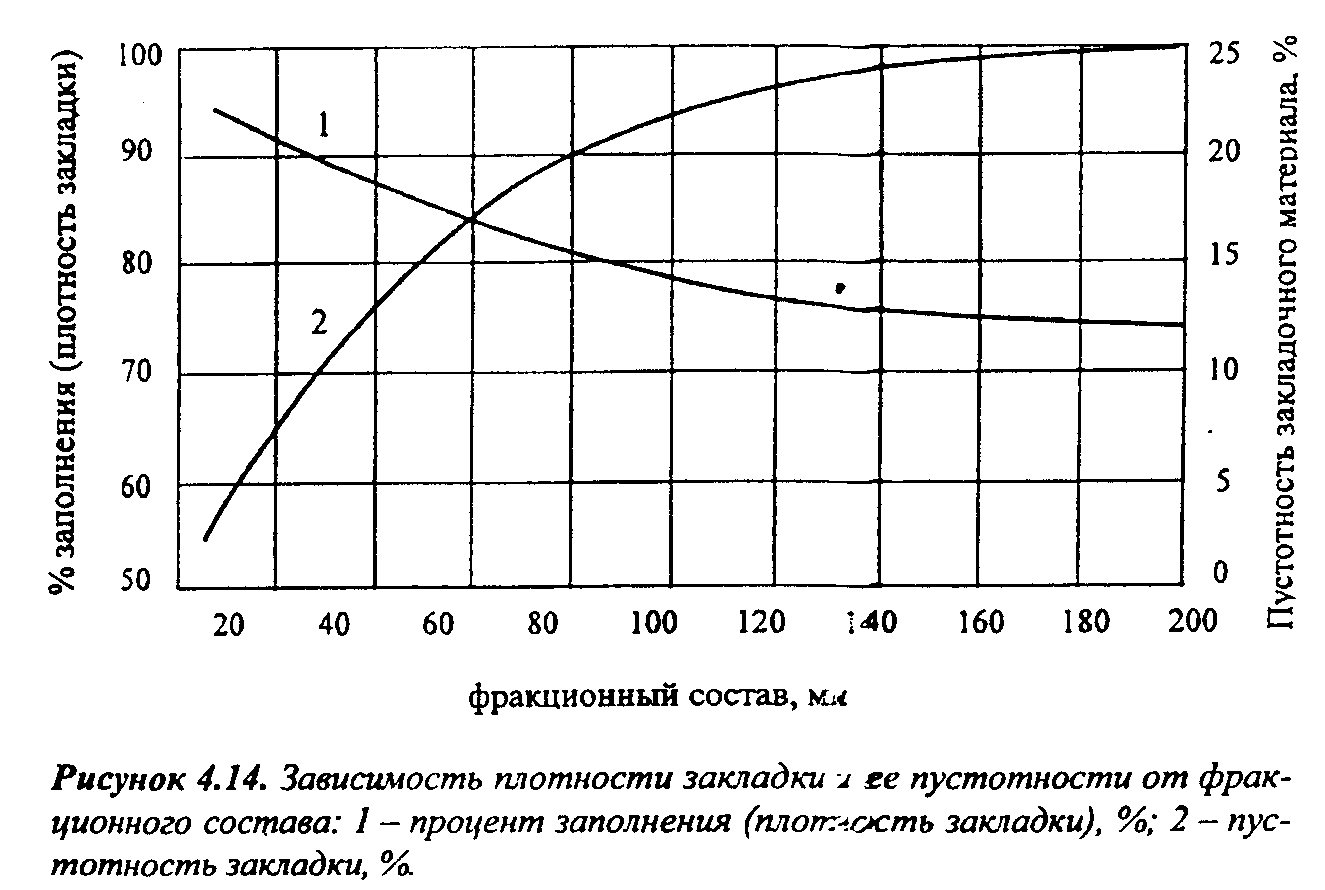
достигнуть 20-25%. А это значит, что с течением некоторого времени усадка закладки в стволе глубиной, к примеру 500 м может в принципе достигнуть 100м и более. На этом участке превзойдет обнажение крепи, что серьезно ослабит подсистему «порода - крепь. Но не следует ориентироваться и на закладку, состоящую исключительно из мелких фракций. Во-первых, получение мелкофракционного состава требует значительных средств на дробление закладочного материала. А, во-вторых, и это может оказаться самым существенным, мелкие фракции в большей степени, чем крупные размокают, частично растворяются, выщелачиваются, усиливая нередко при этом агрессивность водной среды, а затем либо вытекают из ствола, либо образуют непроницаемый массив для воды и газа. Следовательно, речь должна идти об оптимальном фракционном составе в конкретных условиях.
Теоретические и экспериментальные исследования показывают, что наиболее оптимальным гранулометрическим составом закладочного материала, подготовленного на поверхности, являются смеси, содержащие примерно 40% кусков с диаметром 250.. .80 мм, 200 — с диаметром 0.. .30 мм, 15%-30... 15 мм и 25% - с диаметром менее 15 см.
Английскими предписаниями на основании опробованных исследований регламентируется такой состав подготовленной на поверхности смеси: 250..20 мм >80%, 20 мм и менее <20%. При этом фракция до 1 мм не
должна превышать 5 %. Чешские исследователи считают, что плотность закладки будет максимальной, если состав фракции 250...80 мм занимает 74%, 80..50 мм - 7%. менее 50 мм - 19%. Ситовый анализ пород отвалов шахт Донбасса покизывает, что гранулометрический состав многих из них близок к оптимальному и может быть приемлем для засыпки стволов при условии дополнительного дробления на мелкие фракции кусков пород с поперечными размерамий более 180 мм (примерно 15% объема).
Надо иметь в виду, что гранулометрический состав закладки в стволе отличается от подгодхаленного на поверхности. При засыпке ствола кинетическая энергия падающего закладочного материала переходит в потенциальную энергию деформации (процесс дробления, уплотнения) особенно на контакте с жесткой опорой. В результате падения материала в ствол количество крупных фракций (более 25 мм) уменьшается в среднем на 10%, на эту же величину возрастает процентное содержание более мелких фракций. С ростом высоты столба закладки влияние кинетической энергии падающего материала на нижележащие слои закладки уменьшается вследствие появления эффекта «подпружинивания», вязкости и пластичности. Понятно, что степень дробления и уплотнения закладочного материала, а, следовательно, плотность и пористость закладки, зависит от физико-механических свойств материала, крупности кусков и высоты их падения в ствол.
Состояние закладки в стволе можно характеризировать двумя основными временными периодами: во время засыпки и после ликвидации (засыпки) ствола. В первом периоде проявляются динамические нагрузки на закладку в результате самого процесса свободного падения материала. Во втором - закладка населится в статическом состоянии, приобретает как бы свойства вязко-пластического материала с определенными вертикальными и горизонтальными составляющими давления по всей глубине ствола.
Характеристика закладки, определяющая степень ее уплотнения по отношению к плотности подготовленного на поверхности насыпного материала, а также степень заполнения объема ствола, характеризуется коэффициентами уплотнения Ку и заполнения К,.
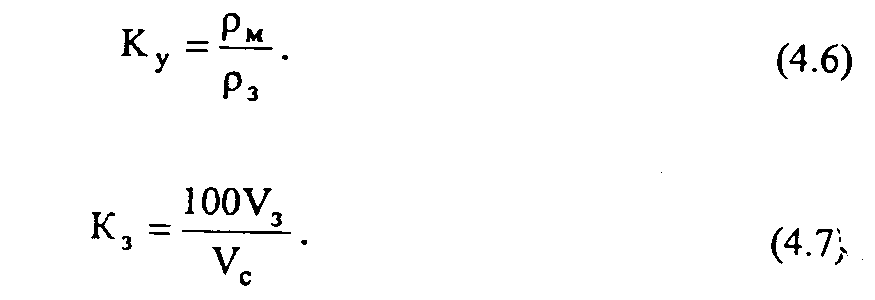
где: рм и р3 - соответственно плотность закладки и закладочного материала;
V3 и Vc - соответственно объемы закладки и заполняемого пространства ствола.
В идеале Ку должен приближаться к единице, а К3 - к 100%.
Характеризуя закладку в вертикальном стволе, следует отметить еще одно важное для практики обстоятельство. В процессе засыпки ствола образуется вертикальная слоевая конструкция закладки с различными по высоте компрессионными свойствами. По мере роста столба закладки нижележащие слои все в большей степени переходят в статическое равновесное состояние стабилизации сил трения о стенки ствола и бокового отпора, а закладочный материал приобретает предельные деформационные характеристики.
Противодействие перемещению закладки вдоль плоскости соприкосновения с крепью ствола вызывается силами внешнего трения. Но поскольку коэффициент трения является величиной довольно неопределенной вследствие неопределенности физических условий (влажность, шероховатость стенок и др.) по глубине ствола, то в качестве количественной характеристики сил трения с некоторыми допущениями можно использовать величину внутреннего трения φ, представив крепь ствола и закладку как единую конструкцию.
Опыты сжатия закладочного материала в цилиндрах показывают, что при отсутствии утечки закладки приращение давления на вертикальную площадку (горизонтальное давление Рг) прямо пропорционально давлению на горизонтальную площадку (Р.). Это отношение и называется боковым распором. Коэффициент бокового распора (ω) зависит от петрографического состава и влажности закладочного материала и колеблется в пределах 0,25...0,5.
Таким образом, давление в нижележащих слоях закладки стабилизируется за счет сил ее трения о стенки ствола, внутреннего трения и бокового распора, а сама закладка в статическом состоянии приобретает, как было сказано ранее, как бы свойства вязкопластического материала с определенными силовыми характеристиками давления в вертикальном и горизонтальном направлениях.
С учетом динамической нагрузки падающего материала статическое вертикальное давление может быть рассчитано по формуле

где ρ - плотность материального закладки, кг/м3,
g = 9.8M/c2,
h - высота столба закладки от его основания, м,
R - радиус ствола, м,
μ - коэффициент трения закладки о крепь ствола,
ω - коэффициент бокового отпора
Характеристики сыпучих материалов, используемых для засыпки стволов, приведены в таблице 4.3.
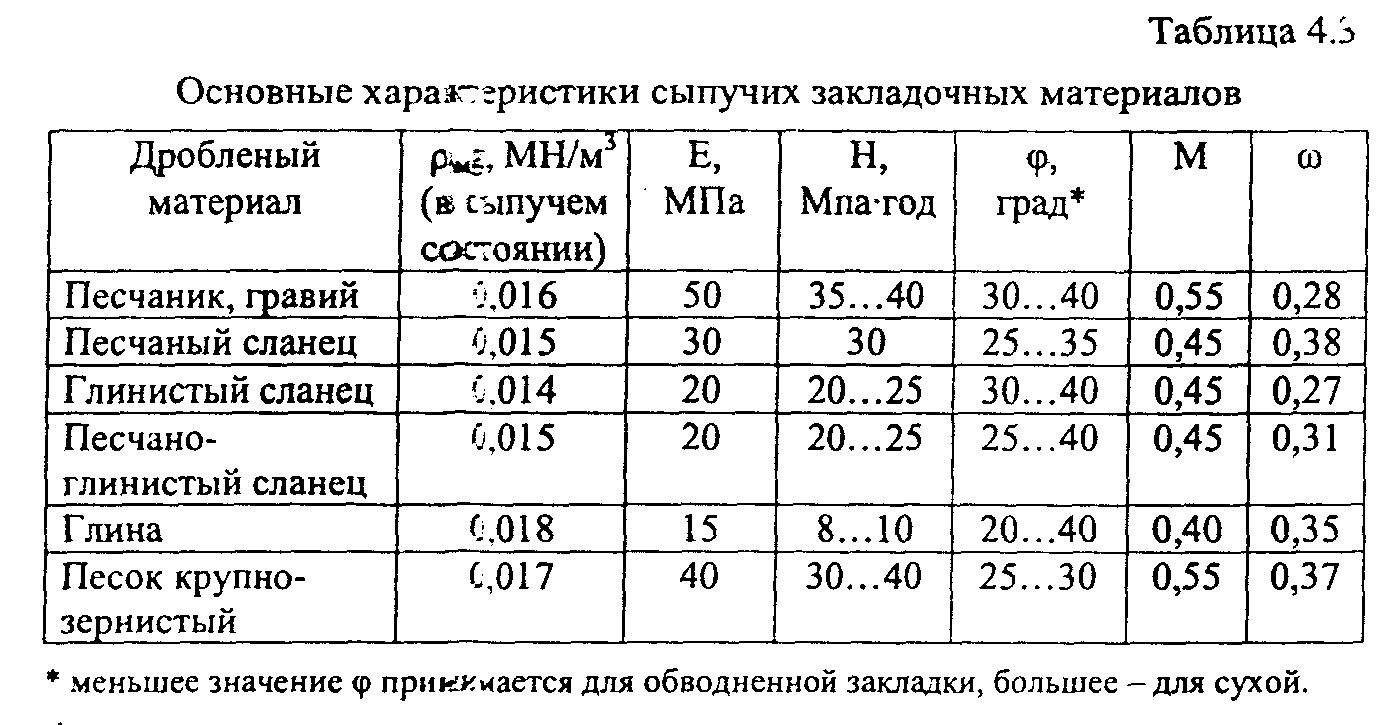
Следует заметить, что усадка зависит и от величины сцепления частиц - сопротивления сдвигу при соответствующем нормальном давленик А сцепление обуславлкьается наличием в закладке связующих веществ (в основном пылевато-глияистых фракций). В практическом плане увеличить плотность закладки и уменьшить величину усадки можно не только за счет добавок пылевато-глинистых и песчаных фракций, но и путем увлажнения материала к примеру раствором NaCl.
Математическое моделирование процесса усадки в стволе с использованием уравнения (4.18) и данных табл. 4.3 показало, что при средних значениях параметров (R=3 м; h=450 м; Е=30 МПа; μ= 0,45; ω = 0,3; η -25 МПа.год- p3g = 0,015 МН/м3 и t= блет) наибольшее влияние на величину усадки оказывает модуль общей деформации. В меньшей степени величина усадки зависит от удельного веса закладки, коэффициента трения закладки о крепь и активного давления закладки (угла внутреннего трения материала). Коэффициент вязкости на величину усадки реального влияния не оказывает. Из технико-технологических параметров примерно пропорциональное влияние на величину усадки оказывают величина столба- закладки и радиус ликвидируемого ствола.
Таким образом, уменьшения усадки закладки в стволе можно достичь за счет использования материала с большим модулем общей деформации меньшим удельным весом, большими коэффициентами трения закладки о крепь ствола и активного давления закладки, а также путем уменьшения высоты ее столба.
Важно для практики и то обстоятельство, что установленные численные эквиваленты влияющих факторов позволяют производить такой подбор технологических параметров, который позволит наиболее удобным способом достичь желаемого результата. Так снижения на 1 м усадки можно добиться за счет увеличения на 0,2 коэффициента трения закладки о крепь ствола или на 0,11 коэффициента активного давления закладки, или уменьшения на 80 м высоты закладочного столба (путем секционирования ствола), или в результате соответствующей комбинации этих параметров.
Представляют научно-практический интерес и сравнительные величины усадки во времени при использовании различных закладочных материалов. На рис. 4.15 приведены графики зависимостей усадки закладки во времени наиболее распространенных видов шихты породных отвалов угольных шахт. Из рис. 4.15 видно, что время (продолжительность) усадки в обоих случаях (1 и 2) практически не превышает 5 лет, причем более 80% усадки происходит в первые 2 - 2,5 года. Эти показатели экспериментально подтверждены проф. И. Алдорфом (Чехия).
Вышеизложенное позволяет сделать два важных для практики вывода. Первый. Зная состав пород в шахтных отвалах, используемых в качестве закладочного материала, их процентное соотношение, можно прогнозировать величину усадки в вертикальном стволе. Состав пород в отвалах, их примерное соотношение можно укрупнено (ориентировочно) определить по объему проведенных и поддерживаемых на шахте различного рода выработок, а более точно путем проведения специальных обследовании ' породных отвалов.
Второй. С учетом влияния каждого фактора на величину усадки можно принять такие инженерные решения по формированию шихты за
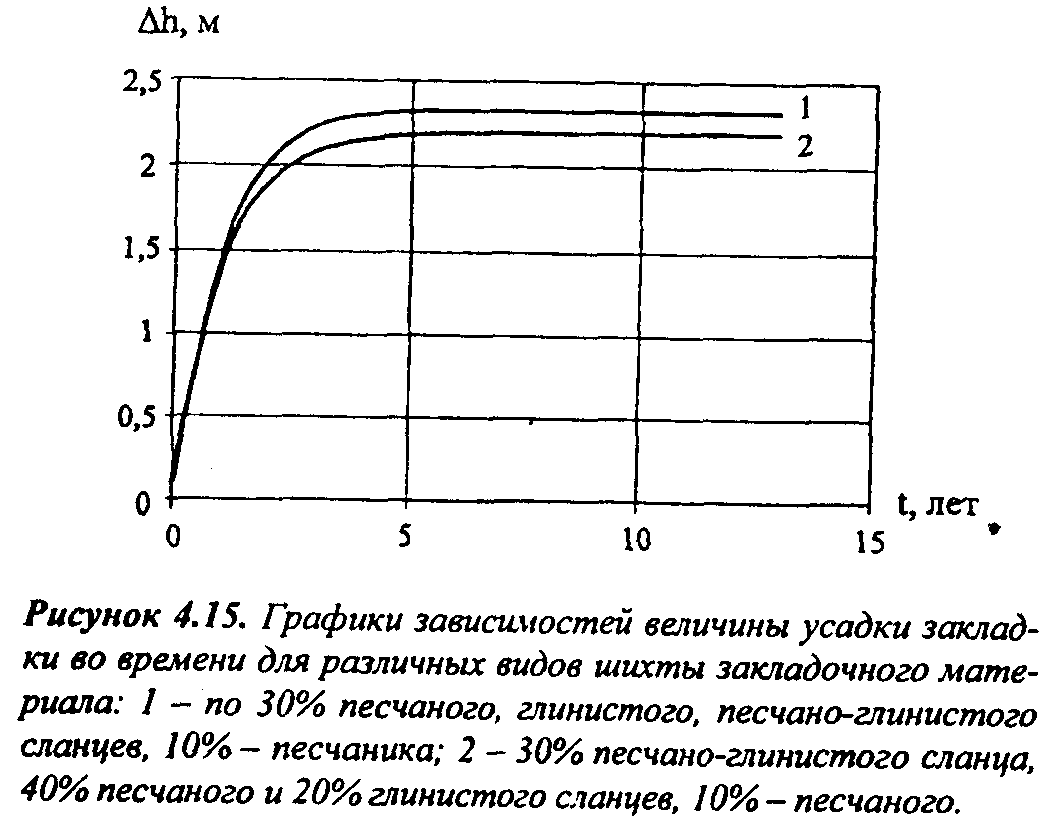
закладочного материала, которые позволят получить наперед заданную усадку, обеспечивающую необходимую стабильность подсистемы «порода-крепь» как важнейшего средства долговременной устойчивости погашенного вертикального ствола.
Но, непременным условием достижения ожидаемого эффекта является постоянное (непрерывное) соблюдение оптимального состава закладочного материала при его засыпке в ствол. В случае использования при засыпке разных участков ствола материалом какого-то определенного гранулометрического состава (при суммарном оптимальном составе) будет наблюдаться и различная плотность закладки, неравномерность ее усадки как на этих участках, так и по всей глубине ствола, что нежелательно с любой точки зрения. Значит надо не просто подбирать оптимальный состав закладочного материала, а готовить шихту оптимального состава и соблюдать рациональную технологию ее засыпки в ствол.
Все изложенное о закладке, ее свойствах, характеристиках и поведении справедливо для случая, когда ствол представляет изолированную от других выработок систему. В случае же появления условий для утечки за. кладки ее компрессионную характеристику можно представить как незатухающую ползучесть, завершающуюся этапом прогрессирующей ползучести (вытекания), что повлечет за собой разрушение закладки как конструкции, обнажение крепи с вытекающими отсюда последствиями. Это крайнее проявление обводненной закладки.
Но даже если утечка обводненной закладки в примыкающие к стволу выработки не происходит, то и тогда оценка ее свойств и характеристик представляет чрезвычайную сложность, поскольку они меняются постоянно. В заполненном закладкой стволе происходят процессы циркуляции, фильтрации и инфильтрации воды, размокания и растворения материала закладки, выщелачивание его составных частей, идет процесс химических превращений. С глубиной растет гидростатическое давление.
Поскольку названные процессы мало изучены, То речь не может идти об управлении ими, а с практической точки зрения надо ориентироваться на принятие таких инженерных мер (изоляция, должные прочностные параметры опор, перемычек, закладочного материала и др.), которые бы сводили до минимума возможность негативных последствий обводнения.
В условиях, когда сыпучая закладка не обеспечивает должной стабильности подсистемы «порода-крепь», применяется твердеющая закладка. Это монолитный материал, набирающий прочность в ликвидируемом стволе с течением времени, имеет лучшие компрессионные характеристики, обеспечивает практически стопроцентную надежность подсистемы «порода-крепь».
Однако хорошо известно, что твердеющая закладка по стоимости ее составляющих, приготовлению и технологии ведения закладочных работ значительно дороже обычной сыпучей. И это обстоятельство нередко априори становится преградой ее рассмотрения и использования при ликвидации вертикальных стволов угольных шахт. А между тем такой подход совершенно не очевиден. Во-первых, в определенных условиях дополнительные, сверх обычных при сыпучей закладке, затраты могут и являться вполне оправданными (например, если прогнозируется утечки сыпучей закладки), а во-вторых, есть реальные апробированные практикой пути удешевления производства твердеющей закладки. Тем более что для различных целей и разных участков ствола требуется закладка с различными прочностными характеристиками, а, следовательно, и различной стоимости.
Основными компонентами твердеющей закладкой являются наполнитель, связывающие добавки и вода.
Классическим и на практике идеальным видом твердеющей закладки является бетон на основе портландцементов. Однако он и самый дорогой. Видимо его следует применять только в самых ответственных местах, где другие виды твердеющей закладки не обеспечивают должную надежность.
В других условиях могут применяться твердеющие закладки на основе более дешевых вяжущих материалов: отвальных, доменных, сталеплавильных и топливных шлаков, золы электрофильтров ТЭЦ, отходов цементной промышленности. Эти материалы доступны и сравнительно недороги. Однако затраты на их сортировку, измельчение, магнитную сепарацию, а главное на доставку к месту назначения могут быть значительными и применение этих материалов в качестве вяжущих становится экономически нецелесообразным. Поэтому в каждом конкретном случае необходимы техниксккономические обоснования получения оптимального состава твердеющей закладки с учетом назначения и объемов ее использования. При этом следует заметить, что одним из наиболее сложных моментов, связанных с применением того или иного вида твердеющей закладки, является правильный выбор ее «рецепта», т.е. процентного содержания отдельных компонентов.
В общем случае прочностные свойства твердеющей закладки при низковяжущих материалах могут оцениваться по их весовому количеству в смеси в пропорциональном отношении к цементу. Так, 1 кг цемента по равнопрочности закладки эквивалентен 8 кг отвального шлака или 4 кг измельченного шлака первого сорта.
Однако применительно к конкретным условиям и материалам необходимо проведение дополнительных лабораторных исследований. Речь идет о получении закладки с нужными характеристиками при минимальных затратах. Одним аз способов снижения стоимости закладки при обеспечении высокой прочности является применение крупнокусковатого заполнителя и отходов металлургических заводов и электростанций. Максимальный размер частиц крупнокусковатого заполнителя не должен прг вышать 40 мм (закладочный материал подается по трубам). Фракции 20.. .40 мм составляют 60%, остальные 40% - более мелкие фракции. Такое соотношение обеспечивает максимальные прочностные характеристики твердеющей закладки. Исследования показывают, что предел прочности закладки на сжатие при применении крупнокусковатого заполнителя в 3.. .4 раза больше, чем без него.
В таблице 4.4 в качестве примера приведены прочностные характеристики твердеющей закладки при различном количестве вяжущего (отвального шлака), обшей массы крупнокусковатого заполнителя и воды.
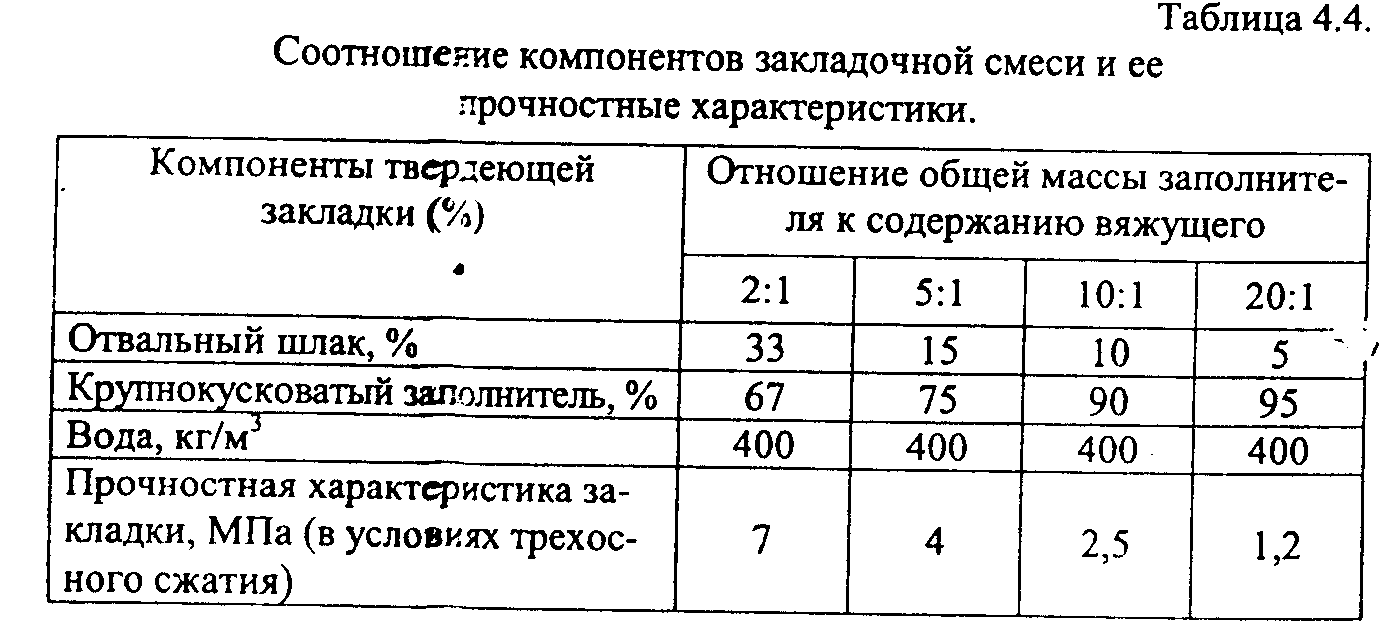
Из таблицы видно, что между содержанием вяжущего и прочностными характеристиками закладки прослеживается четко выраженная количественная связь.
Существенного улучшения реологического состояния твердеющей закладки можно достичь за счет использования пластификаторов (например, глины, 10...15% от массы вяжущего), добавляемых к заполнителю. Пластификаторы повышают текучесть смеси, улучшают заполнение объема ствола, позволяют экономить вяжущие и повышают прочность закладки.
Повысить гидравлическую активность вяжущих веществ в твердеющей закладке, сократить время ее затвердевания и повысить прочность способны некоторые добавки-активизаторы, например, поваренная соль.
Все вышеизложенное позволяет заключить, что правильный выбор закладочного материала для закладки ликвидируемых вертикальных стволов угольных шахт является одновременно научной, технической, экономической, экологической и социальной задачей.
Но выполнить функцию уравновешивающего элемента силового взаимодействия подсистемы «порода-крепь-закладка» (даже при оптимальных параметрах) сможет лишь в том случае, если ее собственное положение в стволе будет стабильным. А это может быть достигнуто в условиях компенсации сил веса столба сухой или обводненной закладки, а также, если будет исключена возможность ее вытекания из ствола в другие выработки.
Вот эту стабильность закладки и призваны обеспечить надежные в конструктивном отношении опоры, перемычки, возводимые на сопряжениях с выработками околоствольного двора, ствольные пробки.
Закладка вместе с опорными сооружениями должна образовывать единый закладочный массив, который объединит и обеспечит незыблемость теперь уже подсистемы «порода-крепь-закладочный массив» и заложит прочную основу долговременной устойчивости всей геомехайической системы «погашенный вертикальный ствол».
ВОПРОСЫ И ЗАДАНИЯ ДЛЯ САМОКОНТРОЛЯ
/. Каково назначение закладки в стволе? Какие виды закладки используются на практике?
2. Какие материалы могут использоваться и используются при закладке стволов?
3. Какие основные характеристики и свойства закладочного материала?
4. Изложите кратко влияние гранулометалического и петрографического состава закладочного материала на поведение закладки в стволе.
5. Охарактеризуйте коэффициенты заполнения и уплотнения закладки в стволе.
6. Чем отличается поведение обводненной сыпучей закладки от необводненной? По каким причинам не следует допускать даже частичного растворения закладочного материала?
7. От чего зависит величина усадки закладки в стволе? Какие характеристики и параметры (качественные и количественные) оказывают наибольшее влияние на величину усадки? Какие практические выводы можно сделать из познания этих показателей?
8. Что представляет собой твердеющая закладка, ее состав, свойства и характеристики?
9. Каковы пути повышения качества твердеющей закладки и снижения ее стоимости?
100>