Министерство образования и науки Российской Федерации государственное образовательное учреждение высшего профессионального образования Московский государственный открытый университет отчёт раздел 4 1
Вид материала | Документы |
- Правила приема в государственное образовательное учреждение высшего профессионального, 314.94kb.
- Министерство транспорта российской федерации федеральное государственное образовательное, 1267.4kb.
- Министерство образования и науки российской федерации федеральное агентство по образованию, 32.48kb.
- Проект программы 00 45 Регистрация участников Конференции. 45- 10., 38.19kb.
- Федеральное агенство по образованию министерство образования и науки российской федерации, 332kb.
- Правительство Российской Федерации Государственное образовательное бюджетное учреждение, 91.24kb.
- Правительство Российской Федерации Государственное образовательное бюджетное учреждение, 344.56kb.
- Правительство Российской Федерации Государственное образовательное бюджетное учреждение, 371.48kb.
- Программа по дисциплине, 288.37kb.
- Программа по дисциплине, 448.54kb.
6.4.1.1.2.1. НИМ - Применение проходческих машин с рабочим органом ударного действия
В настоящее время имеется опыт проведения горизонтальных горных выработок с применением ударных инструментов (гидроударников), монтируемых на передвижных установках, в частности на экскаваторах небольших габаритов.
В последние 15–20 лет за рубежом разработали и используют при проведении горизонтальных выработок агрегаты с навесными пневмо- или гидроударниками. Машины применяют, как при проведении выработок в слоистых или трещиноватых породах, легко выкрашивающихся и разрушающихся под действием удара, так и в однородных горных массивах средней крепости.
По сравнению с комбайнами проходческие машины с рабочим органом ударного действия имеют значительно меньшие габариты, массу и стоимость, однако при их использовании необходимо наличие оборудования для погрузки горной массы, что связано с потребностью в дополнительной рабочей силе и усложнением обслуживания механизмов в забое. В качестве погрузочного оборудования в комплексе с проходческими машинами обычно используют погрузочные машины с боковой разгрузкой ковша.
Ударный рабочий орган может быть смонтирован на шагающем, пневмоколесном, гусеничном или рельсовом шасси. Некоторые модели проходческих машин имеют шасси портальной конструкции, позволяющее пропускать погрузочное и транспортное оборудование. Однако наибольшее распространение, ввиду своей мобильности, получили машины на гусеничном и пневмоколесном ходу.
Как правило, проходческие комбайны с рабочим органом ударного действия оснащают погрузочным устройством типа «нагребающие лапы» или ковшом с боковой разгрузкой.
Гидроударники, используемые на проходческих комбайнах, монтируют на телескопических стрелах-манипуляторах. Пневмо- и гидроударники, которые применяют в качестве рабочего органа комбайнов и проходческих машин, выпускают многие фирмы мира.
Установки с рабочим органом ударного действия, производимые различными фирмами, по техническим параметрам близки между собой.
Фирма «Хаусхерр» (ФРГ) выпускает машины и комбайны для проходки выработок в крепких породах, которые имеют погрузочный орган с парными нагребающими лапами и перегрузочным скребковым конвейером.
6.4.1.1.2.2. Анализ проходки горных выработок проходческими машинами с гидроударниками за рубежом
С использованием проходческой машины фирмы «Галлик Добсон» на шахте «Фрайстон» был пройден штрек площадью поперечного сечения 4х3,3 м в сланцах. Скорость проходки составила в среднем 1,52 м/смену. На шахте «Эктон Хилл» при проведении штрека площадью поперечного сечения 3,4х3,1 м по породам средней крепости скорость проходки составила 1,83 м/смену, производительность труда – 0,2 м/смену, что в 2 раза превышает производительность труда и в 1,4 раза скорость при проведении выработок с применением буровзрывных работ.
Проходка горизонтальных горных выработок скалыванием массива забоя с помощью ударного инструмента – гидроударника – новый метод, при котором применяют гидроударники массой 2500–6000 кг с минимальной энергией удара 6000 Дж. Одной из первых была фирма «Раммер» – изготовитель гидроударников, отвечающих вышеуказанным требованиям (рис. 4.1).
Гидроударник монтируется на экскаватор вместо ковша. Это позволяет исключить расходы на покупку дорогого бурильного оборудования. Применение гидроударников в качестве разрушающего инструмента сводит к минимуму применение взрывных веществ.
Разработка тоннеля начинается с середины тоннеля на высоте 1,0–1,5 м. Глубина разработки 1,5…2,0 м. После этого разрабатывают боковые стороны вдоль пробитого отверстия как можно ближе к контуру тоннеля. Затем разработка продолжается ярусами вверх до кровли тоннеля. После уборки разрушенной горной массы и оконтуривания тоннеля до проектной величины на уходку l ух цикл повторяется.
Самый эффективный способ разработки тоннеля – снизу вверх. Таким образом, используется внутреннее напряжение (сила давления и гравитационные силы) породы и одновременно естественное и наиболее благоприятное направление разрушения. В горном массиве появляются изломы и растяжения, которые вместе с состоянием напряжения породы способствуют образованию трещин в горном массиве.
Наиболее оптимальным условием для проведения выработок способом разрушения горного массива скалыванием является наличие естественной трещиноватости или сланцевание горного массива, которые ускоряют процесс проходки. Удар, производимый гидроударником, при трещиноватости массива вызывает в точке удара локальную, местную концентрацию напряжений, способствующую более качественному разрушению горного массива с применением минимальных энергетических затрат.
При наличии сланцевания в массиве разработка ведется вдоль направления сланцевых слоев вверх одновременно с использованием природных разломов, трещин.
При площади сечения тоннеля в 30…70 м2 можно проводить одновременно уборку и транспортировку отбитого материала, после чего оконтуривание стены и кровли тоннеля, придавая ему законченную форму.
Проходка горной выработки сечением около 70 м2 позволяет проводить погрузку и транспортировку разрушенной горной массы транспортным средством одновременно с самим разрушением забоя тоннеля. В широком тоннеле экскаватор и погрузчик работают вместе.
Сам процесс разрушения забоя отличается от предыдущего тем, что тоннель разрабатывают последовательно справа и слева. Тогда погрузку и транспортировку отбитого материала проводят одновременно, что облегчает работу водителя экскаватора, который следит за продвижением вперед и направляет удары гидроударника именно в места наибольшего разрушения.
Если порода очень твердая, на отдельных строительных площадках сочетают разработку гидроударником с традиционными методами проходки. В таком случае проходку начинают гидроударником, однако окончательная форма тоннеля достигается путем бурения и последующего контурного взрывания до необходимого сечения тоннеля в свету. Лучшие качества обоих методов используются эффективно: невысокая трудоемкость, простота и быстрота разработки массива гидроударником и точность формы тоннеля в результате применения взрывных работ. Количество шпуров для взрывчатых веществ – около 20, при площади сечения тоннеля около 100 м2. В больших тоннелях разработка проходит в две стадии, во второй стадии разрабатывается основание тоннеля уступами вниз.
Погрузочное и транспортное оборудование не отличается от традиционного оборудования для проходки тоннеля. Оборудование выбирают в зависимости от величины площади сечения. На погрузке работают обычно колесные погрузочно-доставочные машины типа «Торо 301» и на перевозке – колесные грузовики.
При небольшой площади сечения тоннеля (менее 30 м2) используются небольшие гидроударники, энергия удара которых, естественно, меньше. В этом случае производственная мощность может снизиться и ее необходимо сравнивать с традиционными способами проходки
Проходка тоннеля в Риете. Строительство тоннеля в Риете, в 80 км от Рима на север было начато в конце сентября – начале октября. Этот тоннель являлся частью проекта по модернизации автомагистрали между городами Риете и Терни.
Фактические данные:
общая длина тоннеля около 2500 м;
площадь сечения тоннеля около 90 м2;
количество отбитого материала 225 000 м3;
ширина тоннеля 12 м и высота 7,5 м.
Тип породы:
слоистый и трещиноватый, белый известняк;
толщина слоя менее 50 см;
прочность на сжатие около 1500 кг/см2;
плотность расслоения около 2,1 трещины/м.
Разработка выполнялась в полном рабочем цикле по всей высоте тоннеля. Проходку вели поочередно с левого и правого краев, продвигаясь постепенно вверх, что позволяло отгружать и транспортировать дробленый материал независимо от процесса разрушения забоя. Одновременно выполняли и гладкую оборку поверхности. Достигнутая точность проходки высока. Строительство тоннеля начали в начале октября 1987 года и производительность проходки выработки за неделю составила около 20 метров. Тогда же было начато строительство встречного тоннеля. На строительстве использовался гидроударник С 86. Строительство тоннеля выполнено за 1,5 года.
Тоннель в Понтеббе. Строительство выполняли в деревне Понтебба к северу от Удине, вблизи австрийской границы. Железнодорожный тоннель с двухсторонним движением прокладывали одновременно навстречу друг другу. Строительство тоннеля – часть проекта по обновлению сети железных дорог для повышения движения поездов от города Удин до границы с Австрией. Главный подрядчик – Импресса Карибони, две субподрядные фирмы – Каппалетто Бротхерс и Надотто.
Фактические данные:
длина тоннеля около 1800 м;
площадь сечения около 98 м2;
количество отбитого материала около 176 400 м3.
Вид породы:
слоистый известняк;
плотный доломит (вулканический мафит) встречается полосами в известняковой породе;
толщина слоев 5–50 см;
прочность на сжатие около 1500 кг/см2;
плотность расслоения около 2,2 трещины/м.
Разработка проводилась в две стадии: сначала разрабатывали верхнюю часть тоннеля, а затем уступ, глубиной около 2 м, так как обычно в этом случае не применяют взрывных работ и тоннель настолько широк, что позволяет грузить и транспортировать материал одновременно с работой гидроударника. Это во многом ускоряет работу водителя, который видит перед собой весь фронт работ. Проведение погрузочных работ влияет на то, что разрушение ведется периодически то справа, то слева. Обычно снизу вверх. Местами появлялся плотный доломит (часто полосами), который представлял трудности из-за высокой твердости и плотности. Тогда обработку поверхности проводили буровзрывным методом. Были использованы патронированные взрывчатые вещества, применяемые для проходки тоннелей. Но и в этих случаях основная часть работ была выполнена гидроударником.
Сравнивая полученные результаты производительности труда, необходимо принять во внимание два фактора. При большой площади сечения, позволяющей производить одновременно погрузку отбитой горной массы и транспортирование ее, данные по производительности увеличиваются. Продвижение вперед составило около 7 м в сутки. Второй фактор, значительно влияющий на производительность – прочность и особенно целостность материала. Если скала плотная, выработка замедляется и, как следствие, производственные цифры уменьшаются.
Человеческий фактор необходимо тоже принять во внимание. На производительность гидроударника во многом влияет профессиональное умение водителя. Водитель, прошедший специальную подготовку, умеющий использовать эффективно гидроударник и заинтересованный в труде, достигает наилучших результатов.
Большим преимуществом является возможность многоцелевого использования: наряду с проходкой горных выработок гидроударники на экскаваторном основании или основании погрузочно-доставочной машины применяют как для оборки кровли при образовании в горном массиве не обрушенных негабаритов, так и для разрушения негабаритов при их обрушении. Наибольшее распространение получили установки для оборки кровли типа «Скейлер» и «Рокскейлер». Под оборкой кровли имеется в виду выравнивание стен и кровли горных выработок при строительстве шахт и тоннелей и очистных работах при разработке месторождений подземным способом. При этом от поверхности кровли откалывают лишние каменные выступы и обломки пород. Обычно оборка кровли и стенок производится сразу после взрывания, а затем производится повторная оборка, при которой удаляются куски, отсоединившиеся от горного массива со временем в течение ведения горных работ.
Из операций, проводимых в шахтах, ручная оборка кровли одна из самых опасных и тяжелых. Куски породы («заколы») отрываются вручную при помощи лома с изогнутым концом, способствующим эффективному захвату. Работа весьма тяжелая и опасная, так как нередко приходится работать в неестественном рабочем положении; горняк часто вынужден находиться очень близко от срывающихся камней.
Вначале применяли пневматические, а позже гидравлические ударники. Затем появились установки, которые были сконструированы специально для оборки кровли. Гидроударники стали меньше по размеру, а движения стрелы более маневренные. Установки, оснащенные гидроударником, вытеснили другие механические установки, - как, например крючки, закрепляемые к торцу стрелы для отделения обломков от массива.
Механизация оборки позволила резко увеличить безопасность, эффективность и качество работы. По исследованиям, проведенным в Швеции, из всех несчастных случаев в шахтах 20…35 % вызвано падающими кусками пород – «заколами». Оператор, управляющий установкой для оборки кровли, защищен от падающих сверху камней металлическим козырьком, а от падающих впереди кусков его безопасность обеспечивает защитная сетка. Оператор работает на расстоянии в 10 метрах от обрабатываемого участка кровли. Работа не утомляет оператора, который сидит на эргономическом сидении, с которого обеспечена хорошая видимость.
Выполненные исследования показали, что механизированная оборка кровли сокращает время подготовительных работ на 50…70 %.. При механизированной оборке улучшается качество работы, в результате чего уменьшается потребность во вторичной оборке кровли. Опыт работы показал, что механизированная оборка позволяет сократить персонал с трех человек до одного; уменьшилось и время использования транспортных средств, в среднем на 50 часов. Средняя производительность механизированной оборки составляет 50…100 м3/ч, включая время на подключение и перемещение.
Благодаря повышенному качеству оборки кровли уменьшается потребность в упрочнении горного массива анкерным креплением, что позволяет значительно сократить объем затрат.
Управление стрелами можно выполнять и дистанционно, что обеспечивает хорошую видимость на обрабатываемый объект даже в узких местах. Благодаря дистанционному управлению установка может быть смонтирована на стационарном шасси с электрическим приводом. Шасси такого типа представляет собой эффективное исполнение, применяемое в узких местах.
Стрелы и гидроударники Роксон конструктивно дополняют друг друга для успешной совместной эксплуатации.
Области применения гидравлических ударников Роксон. Гидравлические ударники Роксон производства фирмы «Коне» разрушают, раскалывают, подрубают, разрыхляют:
– в коммунальном строительстве;
– в шахтах, карьерах и на дробильных станциях;
– в металлургии в литейных и плавильных цехах;
– в обрабатывающей промышленности.
Гидроударники Роксон механизируют тяжелую и опасную ручную работу по дроблению и устраняют необходимость буровзрывных работ, что ведет к сокращению расходов и повышению безопасности. Гидроударники Роксон улучшают использование экскаваторов и расширяют диапазон их применения. Гидроударники Роксон сконструированы и изготовлены на базе передовой технологии и новейшего оборудования, что делает их наиболее надежными и эффективными из предлагаемых на мировом рынке.
Конструкция гидравлического ударника Роксон предусматривает много узлов, уменьшающих износ экскаватора при проведении дробильных работ и повышающих удобство эксплуатации:
– начиная с модели В700, во всех последующих более тяжелых моделях установлен амортизирующий механизм, уменьшающий износ в соединении стрелы;
– благодаря гидравлической системе с двумя контурами, в более тяжелых моделях Роксон перепады давления в насосе экскаватора оказываются менее 10 %, что продлевает срок службы насоса;
– монтаж гидравлики гидроударников Роксон производится легко вследствие широких пределов изменения объема протекающего масла;
– благодаря патентованной конструкции, энергия удара остается постоянной, независимо от объема протекающего масла; изменение объема масла влияет только на частоту ударов.
Стреловая установка с гидроударником Роксон является многоцелевым и полностью укомплектованным агрегатом, готовым к эксплуатации сразу после установки на опору или шасси и подключения электропитания.
Среди многих областей применения необходимо отметить следующие:
– разрушение и расчистка забивки грунтов на грохотах, питателях и дробилках;
– очистка и удаление шлака с литейных сосудов;
– разрыхление уплотненных или мерзлых материалов.
Другие условия применения стреловой установки с гидроударником Роксон-400 СВЕ. Возможность разрушения горного массива в условиях криолитозоны позволяет удлинить рабочий сезон и повысить рентабельность предприятия. Целесообразная конструкция и высокая ударная вязкость материала делают Роксон ведущим для работ в холодных климатических условиях; он может быть использован как на подземных работах, так и на поверхности.
Роксон-200. Гидроударник предназначен для широкого применения. В сочетании с гидроударником землеройный трактор представляет собой агрегат многоцелевого назначения.
6.4.1.1.3. Подраздел. Проходка горных выработок и добыча крепких руд бурением скважин большого диаметра
Применение буровых установок для добычи крепких руд требует решения целого ряда задач: от обеспечения точности бурения и полноты извлечения руды из залежи с заданной производительностью до доставки и транспортирования рудной мелочи и обеспечения высокого качества обогатительного передела. Одной из главных проблем в настоящее время является порядок ведения очистных работ, обеспечивающий поточность технологии и предотвращающий опасное проявление горного давления. Кроме того, для промышленного производства добычи руды из тонких залежей необходимо решать вопрос уменьшения габаритных размеров добычных агрегатов.
В настоящее время, как отмечалось выше, отклонение от заданного направления бурения наиболее сложных горизонтальных выработок и скважин составляет от 0,2–0,5 % до 1,0–1,5 %; разработаны лазерные и компьютерные установки, позволяющие осуществлять бурение с высокой степенью точности в заданном направлении. Имеются технические решения, позволяющие осуществлять направленное бурение вслед за изменяющейся гипсометрией рудного тела в различных направлениях.
Производительность буровых установок при бурении в крепких породах достигает 80 тыс. т. в год и более (с учетом возможности чистого времени бурения). Такая производительность (по предварительным расчетам) обеспечивает экономически целесообразную добычу крепких руд из залежей мощностью 0,6 м и менее. В последнее время разработаны буровые головки с соплами для подачи воды под давлением более 300 МПа, что позволяет увеличить скорость проходки вдвое.
Габариты буровых самоходных установок типа Рино-400 или «ВМ50N» позволяют осуществлять технологическое бурение из выработок сечением 15–18 м2. По данным фирм-производителей технические возможности позволяют изменить габариты этих установок для работы в выработках сечением 10–12 м2 без изменения буровой мощности станков.
Для предотвращения проявления горного давления и концентрации напряжений в выработках, где находятся люди, разработана технологическая схема выбуривания, позволяющая управлять процессом перераспределения напряжений во время проведения очистных работ.
6.4.1.1.3.1. НОМ – Проходка выработок комбайном КД800Э с опережающей скважиной
При отработке маломощных месторождений крепких руд выбуриванием добычным комбайном КД800Э его можно использовать для строительства этих выработок (как горизонтальных, так и вертикальных). Применение добычного комбайна при проходке горных выработок позволяет объединить обе задачи управления горным давлением за счет выбуривания по центральной оси выработки опережающей скважины диаметром от 0,3 до 0,8…1,2 м на всю длину выработки (например, штрека).
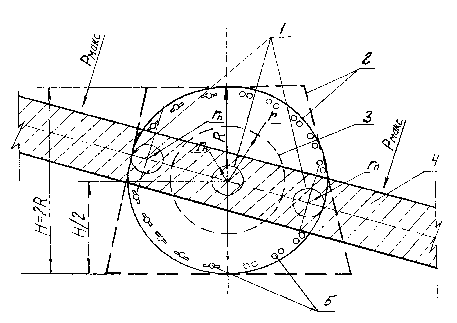
Проведение оконтуривающих горных выработок
с применением добычного комбайна КД800Э:
1 – пионерные пилот – скважины с радиусом rп; 2 – проектные контуры проходимой горной выработки; 3 – компенсационная скважина большого диаметра с радиусом r; 4 – рудное тело (залежь); 5 – контурные сближенные шпуры, или шпуры с бороздой; R – радиус выработки круглого сечения; H – высота выработки трапециидального сечения; Pмакс – направление максимальных напряжений в горном массиве
Вначале бурят опережающую пионерную скважину 1 диаметром 0,3 м по центральной оси штрека и боковые по краям выработок 2, а затем расширяют центральную скважину 3 до диаметра 0,8 или 1,2 м в зависимости от длины штрека или технической необходимости. Пионерные скважины бурят в плоскости препендикулярной направлению максимальных напряжений Pмакс.. Как правило это плоскость простирания рудного тела (залежи) 4.
Восстающие выработки можно проходить на полное сечение без применения взрывных работ – это сразу приводит к разгрузке напряженного состояния массива, предотвращению горных ударов и минимальному объему крепления. Круглое сечение выработки обеспечивает одинаковое сопротивление разрушению от проявлений горного давления при любом направлении максимальных напряжений.
Взрывание отбойных и контурных шпуров (скважин) при проходке горизонтальных выработок осуществляют на образовавшееся свободное пространство. При этом наибольшая эффективность достигается при использовании парно сближенных шпуров (скважин) или скважин (шпуров) с бороздами 5 по контуру выработки.
Таким образом, бурение опережающей скважины добычным комбайном по оси выработки диаметром 0,3–1,2 м при проведении подготовительных работ для отработки рудного блока маломощной залежи крепких руд позволяет решить одновременно обе задачи управления горным давлением удароопасных месторождений:
– привести напряженное состояние горного массива в неудароопасное за счет создания опережающего выработанного пространства, что приводит к перераспределению напряжений в горном массиве с выносом опасной зоны концентрации напряжений за область нахождения людей при проведении горных работ (более 30 м);
– обеспечить устойчивую форму выработки за счет контурного взрывания, выполняемого в наиболее благоприятных условиях, которые позволяют энергию взрыва максимально использовать для дробления и выброса породы за область ее разрушения с минимальным воздействием на приконтурную часть выработки. Это происходит потому, что действие взрыва в данном случае распространяется на две обнаженные поверхности – забой выработки и свободное пространство, образованное центральной скважиной (выработкой) большого диаметра.
Однако при проведении горной выработки с опережающей центральной скважиной большого диаметра необходимо учитывать следующие обстоятельства. Во-первых, взрывные работы необходимо выполнять в строгом соответствии с паспортом взрывных работ, обеспечивающим применение оптимального удельного заряда ВВ, то есть такого заряда, при котором максимально используется его энергия на образование наибольшего объема воронки разрушения и качественного дробления руды (дробления, при котором вместе с отсутствием негабарита не происходит чрезмерного переизмельчения руды). Каждому месторождению присущ свой удельный заряд ВВ, который является обобщающим показателем и зависит как от горно-геологических условий месторождения, так и от физико-механических свойств горных пород. Разработана и испытана в опытно-промышленных блоках методика определения оптимального заряда ВВ. В основу методики положена теория кратера Ливингстона.
Серии экспериментальных взрывов шпуровых зарядов различных диаметров проводили на Юкспорском и Кировском рудниках.
Взрывы шпуровых зарядов диаметром 40 мм проводили в условиях Юкспорского месторождения в блоке 8–12. Взорвано 20 экспериментальных шпуров с ЛНС 0,5; 0,6; 0,7; 0,9; 1,1 м. Длина шпуров во всех случаях составляла 2,5 м. Взрывание проводили гранулитом АС-8, зарядка шпуров – зарядчиком ЗП-1. Величина заряда в шпуре составляла 3,5 кг; конструкция его представляла собой сплошной колонковый заряд с расположением патрона-боевика первым от забоя шпура. В качестве патрона-боевика использовали патроны аммонита № 6 ЖВ весом 250 г с капсюлем-детонатором мгновенного действия.
В условиях Кировского рудника проводили взрывы шпуровых зарядов диаметром 56 и 78 мм. При этом интервал исследуемой ЛНС составлял при диаметре 56 мм – 0,9; 1,1; 1,3; 1,5 м, а при диаметре 78 мм – 1,3; 1,6; 1,9 м. Вес заряда соответственно составлял 5,0 и 11,5 кг АС-8. Остальные условия те же, что и при взрывании шпуровых зарядов диаметром 40 мм.
Результаты проведенных экспериментов показывают, что оптимальный удельный заряд ВВ (кг/м3 ) необходимо определять по формуле:
qopt = 1/ K2opt n,
где qopt – оптимальный удельный заряд ВВ, кг/м3; Kopt – оптимальный коэффициент деформации породы (коэффициент приведенной ЛНС; Кopt = W/G1/2 , где W – линия наименьшего сопротивления; G – вес заряда ВВ, приведенного на 1 погонный метр); n – показатель степени дробления, n = r/W = tgJ (r – радиус воронки, 2J – угол раскрытия воронки).
Вычисленный по этой формуле оптимальный удельный заряд ВВ для апатитонефелиновых руд равен qopt = 1,37 кг/м3, что хорошо согласуется с нормативным удельным расходом ВВ, принятым на предприятии и составляющим 1,35…1,45 кг/м3.
Таким образом, применение для взрывных работ оптимального удельного заряда ВВ позволяет максимально использовать энергию взрыва с минимальным воздействием на формируемый контур выработки и приконтурную часть массива и минимальным расходом самого ВВ.
Во-вторых, необходимо оптимизировать длину уходки отбойными и оконтуривающими шпурами за один цикл. Длина отбойки и образовавшаяся взорванная масса должны рассчитываться таким образом, чтобы не допустить запрессовки центральной скважины с целью возможности ее дальнейшего использования. Другими словами, должны увязываться как длина уходки за один цикл, так и различные ступени замедления взрыва при различных диаметрах центральной скважины (0,3; 0,8; 1,2 м). Кроме того, объем отбиваемой горной массы необходимо увязывать с производительностью уборочно-доставочной техники, чтобы обеспечить циклично-поточную технологию. Таким образом, сечение штрека (минимальные размеры которого зависят от габаритов добычного комбайна), диаметр центральной опережающей скважины и паспорт взрывных работ должны быть взаимоувязаны.
В-третьих, учитывая сложность комбинации отбойных и контурных шпуров, необходимость обеспечения «гладкой» поверхности контура выработки и недопущения запрессовки центральной скважины, отбойка должна выполняться только электровзрывным короткозамедленным способом. Особенности электровзрывания и условия его безопасного применения подробно изложены в соответствующих работах.
Высокая степень безопасности проведения горных выработок в условиях удароопасного месторождения обеспечивается также за счет применения крепи с разнопеременными нагрузками на массив.
Вместе с тем опережающее бурение центральной скважины при проведении горных выработок (оконтуривающих рудный блок) позволяет получить чистую рудную массу с минимальным разубоживанием руды вследствие возможности ее селективной выемки при проходке по рудному телу.
Необходимо отметить: безопасность проведения горных выработок в условиях удароопасного массива при разработке месторождений выбуриванием обеспечивается, во-первых, приведением горного массива в неудароопасное состояние за счет переноса опасной зоны концентрации напряжений вне сферы деятельности людей бурением центральной скважины большого диаметра; во-вторых, за счет принятия мер по обеспечению устойчивого состояния выработки на весь период ее эксплуатации:
– придание выработке сводчатой формы с оформлением контура выработки «гладким» взрыванием с применением оптимального удельного заряда ВВ;
– применение короткозамедленного электровзрывания;
– применение податливой крепи с обеспечением податливости в направлении максимальных напряжений;
– применение крепи, обеспечивающей разнопеременные нагрузки на массив с учетом реологических свойств массива и перераспределения напряжений в результате строительства последующих подземных сооружений или ведения очистных работ.
Оптимальные параметры выемочного участка связаны с выбором оптимальной длины скважины, ее диаметра относительно мощности рудного тела и высоты очистного пространства, ценности руды, гипсометрии залежи. Главным критерием, позволяющим учесть все эти факторы, является минимум приведенных затрат на килограмм условного металла, который рассчитывают отдельно в каждом конкретном случае.
Главными критериями оптимальности выбуривания руд являются показатели извлечения полезного ископаемого: разубоживание и потери. Они зависят от технических характеристик применяемого оборудования, которые влияют на точность бурения, отклонения скважин при бурении от заданного профиля, в зависимости от глубины бурения и гипсометрии залежи. При бурении скважины происходит ее отклонение в вертикальной плоскости, при этом ось скважины отклоняется от средней плоскости залежи. Необходимо учитывать, что для обеспечения полноты извлечения диаметр расширяющей скважины принимают больше мощности залежи.
В действительности скважина представляет собой изогнутый цилиндр, однако в расчете радиус кривизны оси скважины принимают за прямую линию. Поскольку диаметр скважины больше мощности пласта, за пределами пласта образуются две фигуры, представляющие собой часть цилиндра, отсеченного плоскостью залежи и составляющую один и тот же угол с осью цилиндра. Коэффициент разубоживания определяют как отношение объема породы к объему скважины. Крайним значением применимости бурения следует считать полный выход скважины из рудной залежи.
Бурение скважины прекращают, исходя из анализа содержания полезного ископаемого в добываемой руде и его ценности.
Опыт отработки рудных залежей малой мощности средней крепости шнековым бурением показывает, что наиболее целесообразным являются технологические схемы, отличающиеся видом применяемого транспорта, подъема, средствами и способами первичного обогащения.