1. Общая характеристика
Вид материала | Документы |
- Содержание лекций Модели местного самоуправления в России Местное самоуправление:, 786.51kb.
- Задачи физического воспитания детей дошкольного возраста. Общая характеристика средств, 34.6kb.
- Реферат по курсу: экология на тему: Общая характеристика экосистем, как, 726.64kb.
- П. П. Грицая ст. Солдатской публичный доклад, 739.97kb.
- «Физико-химические методы анализа» Общая трудоемкость изучения дисциплины составляет, 16.86kb.
- Общая характеристика изменений требований к современному образованию. Принципы построения, 23.19kb.
- План введение Общая характеристика гражданско правового статуса личности по Конституции, 591.34kb.
- Реестр требований кредиторов 14. Понятие, виды и цели процедур банкротства 15. Юридическая, 24.49kb.
- Учебное пособие Москва 2007 Содержание Лекция № Принцип действия лазеров, классификация, 799.05kb.
- I общая характеристика и перспективы развития региона относительно потребности в магистрах, 112.28kb.
РАЗДЕЛ 2. Вяжущие материалы
1. Общая характеристика
Вяжущие вещества материалы, способные при определенных условиях (смешении с водой, нагревании и т.д.) образовывать пластично-вязкое тесто, затвердевающее с течением времени и образующее камнеподобное твердое тело.
В зависимости от состава бывают
- неорганические (известь, цемент, гипсовые вяжущие и т.д.), затворяемые водой, реже водными растворами солей;
- органические (битумы, дегти, синтетические полимеры и олигомеры), приобретающие рабочие свойства нагревом или при помощи растворителей либо сами являющиеся вязко-пластичными жидкостями.
В основном используются неорганические вяжущие вещества.
Основные показатели качества вяжущих прочность на сжатие и изгиб, скорость твердения и сроки схватывания (потеря тестом вязко-пластичных свойств).
2. Органические вяжущие вещества. Физико-химические основы их производства и области применения
Органические вяжущие вещества – это природные или синтетические вещества, способные:
- приобретать жидко-вязкую консистенцию при нагревании, при действии растворителей или же имеющие жидко-вязкую консистенцию в исходном состоянии;
- с течением времени самопроизвольно или под действием определенных факторов (температуры, УФ-облучения, веществ-отвердителей и др.) переходить в твердое состояние.
В зависимости от происхождения, химического и вещественного состава органические вяжущие делят на следующие группы:
- черные вяжущие (битумы и дегти);
- природные смолы, клеи и полимеры;
3.синтетические полимерные продукты.
Самая обширная группа органических вяжущих – синтетические полимеры. Их получают из низкомолекулярных продуктов (мономеров) полимеризацией и поликонденсацией. Специфически группа полимеров – каучуки и каучукоподобные полимеры, обладающие высокоэластичными свойствами – способностью к большим упругим деформациям; их также называют эластомерами.
В зависимости от отношения к нагреванию и растворителям органические вяжущие делят на термопластичные и термореактивные.
Термопластичными называют вещества, которые при нагревании переходят из твердого состояния в жидкое (плавятся), а при охлаждении вновь затвердевают; причем такие переходы могут повторяться много раз. Термопластичность объясняется линейным строением молекул и невысоким межмолекулярным взаимодействием. По этой же причине большинство термопластов способно растворяться в соответствующих растворите лях. К термопластам относятся битумы, смолы, многие широко распространенные полимеры – полиэтилен, поливинилхлорид, полистирол и др.
Термореактивными называют вещества, у которых переход из состояния в твердое происходит необратимо. При этом у них меняется молекулярная структура: линейные молекулы соединяются в пространственные сетки – гигантские макромолекулы, необратимое твердение (этот процесс называют также «отверждение», «сшивка», «вулканизация») происходит не только под действием нагрева (отсюда пошел термин «термореактивные вещества), но и под действием веществ-отвердителей, УФ и -излучения и т.п. Отвержденные термореактивные полимеры, как правило, более теплостойки, чем термопластичные.
К термореактивным органическим вяжущим относятся, например, эпоксидные и полиэфирные олигомеры (смолы), олифы, каучуки в смеси с вулканизаторами и др.
Органические вяжущие существенно отличаются от неорганических (минеральных). Их адгезионные свойства как в жидком, так и в твердом состоянии, как правило, значительно выше, чем у минеральных вяжущих. Прочность на сжатие у них сопоставима с прочностью минеральных, а при изгибе и растяжении во много раз выше. При этом у термопластичных вяжущих прочность быстро падает при повышении температуры из-за размягчения полимера. Органические вяжущие характеризуются низкой термостойкостью. В зависимости от состава и строения температура их размягчения составляет 80-250°С. В большинстве своем это горючие вещества.
Большинство органических вяжущих водо- и химически стойки (они хорошо противостоят действию кислот, щелочей и солевых растворов). Стоимость органических вяжущих значительно выше, чем минеральных, а объемы их производства намного ниже.
В последние годы широко используется модификация минеральных вяжущих органическими с целью получения композиционных материалов с принципиально новым набором свойств.
Органические вяжущие используются в строительстве для получения клеев, мастик, лакокрасочных материалов, полимерных и полимерцементных растворов и бетонов. Большая же часть синтетических полимеров используется при производстве пластмасс, в состав которых обычно входят наполнители и другие компоненты, снижающие стоимость и придающие пластмассам специальные свойства.
Наиболее широко полимерные вяжущие применяются для получения тонких облицовочных плиток, покрасочных и клеящих составов, защитных химически стойких покрытий, а также для изготовления газонаполненных пластмасс – теплоизоляционных материалов с низкой плотностью (10-50 кг/м3).
3. Неорганические вяжущие вещества. Общие сведения. Классификация – порошкообразные материалы, которые при смешивании (затворении) с водой образуют пластично-вязкое тесто, со временем самопроизвольно затвердевающее и переходящее в камневидное состояние Их используют для скрепления отдельных элементов сооружений; приготовления строительных растворов, бетонов; а также при производства различных изделий и конструкций. Минеральные вяжущие вещества в природе не встречаются, а искусственно приготавливаются промышленностью. Основные этапы их производства:
В качестве сырья для производства минеральных вяжущих веществ используют широко распространенные горные породы и искусственные смеси из них, а также отходы или побочные продукты некоторых отраслей промышленности (металлургической, химической и других). По условиям твердения и по отношению к воздействию окружающей среды минеральные вяжущие вещества подразделяют на
|
4. Известь
4.1. Сырьевые материалы. Получение
Строительная известь неорганическое вяжущее вещество, являющееся продуктом умеренного обжига при температуре 1000-1200С кальциево-магниевых горных пород (мела, известняков и доломита), содержащих не более 6% глинистых примесей, до возможно более полного удаления углекислоты:
CaCO3CaOCO2
Куски обоженной извести комовую известь подвергают гашению водой:
CaO+H2OCa(OH)2+1160 кДж/кг
При гашении куски увеличиваются в объеме и распадаются на мельчайшие частицы (до 1 мкм).
В зависимости от количества взятой воды получают гидратную известь пушонку (50-70% воды от массы извести), известковое тесто (воды в 3-4 разабольше чем извести) или известковое молоко (воды больше в 8-10 раз).
Образующееся тесто используют в качестве вяжущего. При испарении воды тесто загустевает и переходит в камневидное состояние.
По содержанию CaO и MgO бывает:
- кальциевая MgO до 5 %;
- магнезиальная MgO 5-20%;
- доломитовая MgO 20-40%.
По условиям твердения бывает воздушная и гидравлическая.
Негашеную порошкообразную известь получают помолом комовой в шаровых мельницах в тонкий порошок. При помоле часто вводят активные добавки (гранулированные доменные шлаки, золы ТЭС и т.д.) в количестве 10-20 % от массы извести.
Воздушная известь – единственное вяжущее, которое диспергируется не только размолом, но и самопроизвольно при гашении водой.
Известь получают двумя способами мокрым (сырье W25%) и сухим.
Мокрый способ
Сырьевые материалы
Обогащение (дробление и удаление каменных включений)
Приготовление и гомогенизация шлама (+50% Н2О)
Обжиг при 1000-1100С
Охлаждение до 120-140С
Помол в шаровой мельнице
Сухой способ
Сырьевые материалы
Обогащение (дробление и удаление каменных включений)
Подогрев и подсушка
Обжиг при 1000-1100С
Дробление в дисмембраторе
Помол в шаровой мельнице
4.2. Механизм твердения. Свойства
Растворы и бетоны на гашеной извести твердеют на воздухе при обычных температурах в результате главным образом двух одновременно протекающих процессов – карбонизации и кристаллизации гидроксидов кальция, вызванной испарением воды. В процессе карбонизации, т.е. взаимодействия гидроксида кальция с углекислым газом воздуха, образуется карбонат кальция и выделяется вода:
Ca(OH)2+ CO2 = CaCO3+ H2O.
Испарение воды способствует сближению мельчайших кристаллов гидроксида кальция, их срастанию между собой и образованию кристаллических сростков, связывающих зерна заполнителя в монолитное тело.
Образование СаСО3 и кристаллизация Са(ОН)2 происходят только при положительной температуре и в обычных условиях протекают очень медленно. Карбонизация захватывает только поверхностные слои, что объясняется малой концентрацией С02 в воздухе (0,03%) и большой плотностью пленки образующегося карбоната кальция, затрудняющей проникание углекислоты во внутренние слои раствора.
Прочность при сжатии растворов на гашеной извести через 28 сут твердения на воздухе редко превышает 0,5...1,0 МПа. При длительном твердении (десятки и даже сотни лет) прочность возрастает до 5...7 МПа и более. Это объясняется не только дальнейшей карбонизацией и кристаллизацией извести, но и накоплением с течением времени гидросиликатов кальция, которые образуются, хотя и крайне медленно, при взаимодействии гидроксида кальция с диоксидом кремния кварцевого песка.
Процесс образования гидросиликатов кальция в системе известь – кварцевый песок ускоряют путем тепловлажностной обработки в автоклавах с получением более высокой прочности изделий (силикатобетоны, силикатный кирпич, газосиликаты и т.д.).
Превращение в твердое камневидное тело известковых растворных или бетонных смесей на молотой негашеной извести обусловлено гидратационным твердением такой извести. Твердение извести протекает в результате гидратации оксида кальция. Это возможно как через раствор, так и вследствие присоединения воды к твердой фазе с последующей коллоидацией и кристаллизацией гидроксида кальция. По мере испарения воды гидрогель уплотняется, образовавшиеся субмикрокристаллические кристаллы гидроксида кальция СаОН2О взаимно сцепляются и срастаются, что вызывает рост прочности твердеющей извести. Теплота, выделяющаяся при гидратации, со своей стороны, способствует ускорению твердения и росту прочности, что особенно важно при зимних работах (каменной кладке, штукатурке и др.). Последующая карбонизация гидроксида кальция также повышает прочность затвердевшего раствора.
Необходимые условия для хорошего твердения молотой негашеной извести:
- тонкий помол (остаток на сите с сеткой № 008 не более 10%);
- содержание воды в растворной или бетонной смеси должно быть 100-150% от массы извести;
- для предупреждения интенсивного разогревания смеси необходимо отводить теплоту или использовать другие приемы (например, использовать добавки, замедляющие гидратацию извести).
В отличие от гашеной молотая известь обладает способностью быстро схватываться и твердеть. Прочность при сжатии через 28 сут твердения на воздухе при обычных условиях достигает 2-3 МПа и более.
Важным свойством воздушной извести, особенно гашеной, является высокая пластичность, которая связана се высокой водоудерживающей способностью.
4.3. Применение
Известь используется при производстве силикатного кирпича и стеновых силикатобетонных изделий, при отделочных работах, приготовлении кладочных растворов и т.д.
Воздушную известь используют также в производстве местных вяжущих веществ и для получения дешевых красочных составов.
5. Гипсовые вяжущие вещества
5.1. Сырьевые материалы. Получение
Гипсовые вяжущие вещества группа воздушных вяжущих веществ, в затвердевшем состоянии состоящих из двуводного сульфата кальция (CaSO42H2O), включающая непосредственно гипсовые вяжущие (гипс) и ангидритовые вяжущие (ангидритовый цемент и эстрихгипс).
Гипс быстротвердеющее воздушное вяжущее, состоящее из полуводного сульфата кальция CaSO40,5H2O, получаемого низкотемпературной ( 200С) термообработкой гипсового сырья и его помолом в шаровых мельницах до или после термообработки.
Гипсовый камень характеризуется следующими свойствами:
- прочность при сжатии – около 80 МПа;
- истинная плотность – 2200-2400 кг/м3;
- насыпная плотность – 1300-1600 кг/м3;
- твердость по шкале Мооса – 2.
В природе гипс встречается в виде 3-х минералогических разновидностей, отличающихся кристаллической структурой:
- алебастра – плотного мелкозернистого минерала с сахаровидным изломом или крупнозернистого с беспорядочно ориентированными в пространстве кристаллами;
- селенита – волокнистого, сложенного из правильно расположенных нитевидных кристаллов минерала, имеющего характерный шелковистый отлив;
- гипсового шпата – пластинчатого минерала с плоскими прозрачными кристаллами слоистой структуры.
Сырье природный гипсовый камень, состоящий из двуводного сульфата кальция CaSO42H2O и различных механических примесей (глины и др.), а также гипсосодержащие промышленные отходы.
Гипсосодержащие породы (глиногипс; гажа; арзик) состоят из трех основных компонентов: гипса, глины и карбонатов и представляют собой тонкодисперсную механическую смесь или непрочные образования се- рого, желтоватого или бурого цвета.
Гипсосодержащие отходы представляют собой влажные порошки или шламы с характерным цветом и запахом, содержащие в той или иной форме значительное количество различных модификаций сульфата кальция.
При различных температурах и условиях термообработки получают различные модификации гипса: безобжиговые, низкообжиговые, высокообжиговые и смешанные гипсовые вяжущие материалы (см табл.).
5.2. Твердение
Твердение гипсовых вяжущих обусловлено экзотермической реакцией гидратации полугидрата с образованием двуводного гипса. Механизм твердения протекает в три стадии:
- растворение при затворении водой полуводный гипс начинает растворятся с поверхности до образования насыщенного раствора (пластичного теста);
- коллоидация образование коллоидно дисперсной системы двуводного гипса в виде геля, в которой кристаллики новообразований связаны силами молекулярного сцепления. Этот период характеризуется загустеванием теста (схватыванием);
- кристаллизация образовавшийся неустойчивый гель перекристаллизовывается в более крупные кристаллы, которые срастаются между собой, что сопровождается твердением системы и ростом ее прочности. Дополнительному сращиванию кристаллов способствует испарение воды из затвердевшего двуводного гипса. Полное высушивание завершает период формирования кристаллического каркаса и обеспечивает максимальную прочность гипсовым изделиям.
- Конечной стадией твердения, заканчивающегося через 1-2 ч, является образование кристаллического сростка из достаточно крупных кристаллов двуводного гипса.
Схема твердения гипса может быть представлена в виде:
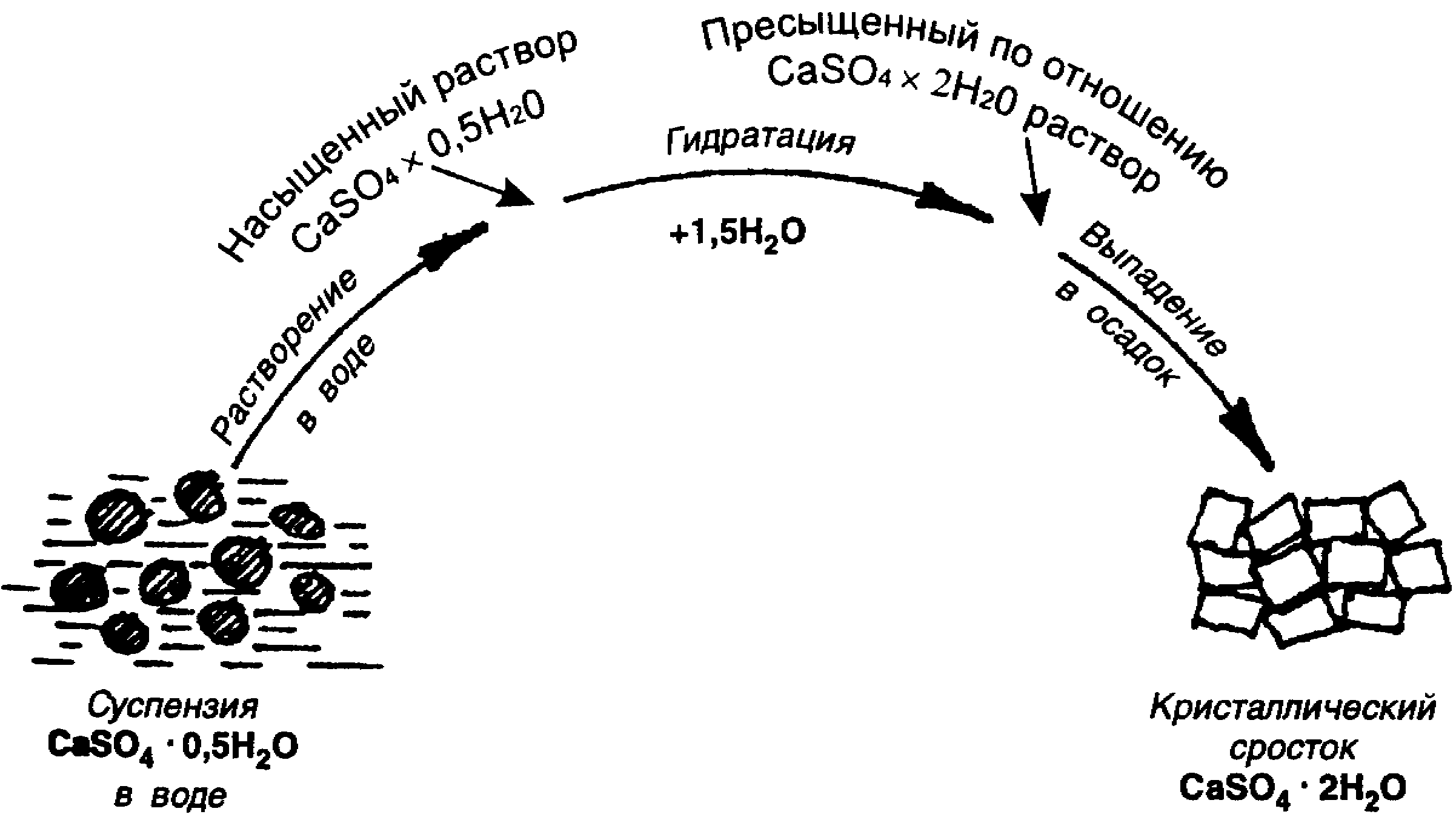
5.3. Основные свойства
Основные технические свойства гипсовых вяжущих сроки схаватывания, тонина помола, марка по прочности.
Тонкость помола оценивают по остатку на сите 200 мкм и делят ГВВ на три вида:
- I грубого помола (остаток не более 23%);
- II среднего помола (14%);
- III тонкого помола (2%).
- По срокам схватывания гипс делят на три группы:
- быстротвердеющий (А) 2 мин. - 15 мин.;
- нормальнотвердеющий (Б) 6 – 30 мин.;
- медленнотвердеющий (С) 20 - не нормир.
По прочности установлено 12 марок гипса от Г-2 до Г-25 (цифра показывает нижнее значение предела прочности при сжатии, МПа).
ГВВ – одни из немногих, расширяющихся при твердении: увеличение в объеме при усадке достигает 0,2%, вследствие чего они не растрескиваются при усадке и могут использоваться без заполнителей, а также для снятия копий в формовочном деле.
ГВВ негорючи, вследствие пористости замедляют передачу теплоты, а при действии температур в результате термической диссоциации выделяют воду, тем самым тормозя распространение огня.
Гигроскопичны – интенсивно поглощают влагу из воздуха – поэтому в гипсе стальная арматура интенсивно коррозирует.
Хорошо сцепляются с древесиной, бумагой и т.д.
5.4. Области использования
Основная область применения гипса устройство перегородок в виде панелей, гипсовых камней или гипсокартонных листов. Помимо этого используют для изготовления форм в керамике, фиксации переломов в медицине и т.д.
6. цементы
Цементом называется гидравлическое вяжущее вещество, получаемое совместным помолом клинкера и специальных добавок.
Портландцементый клинкер – специальный продукт, получаемый высокотемпературным обжигом (1450-1480С) из смеси минерального сырья определенного состава
СаО (известь) – 63-6%
SiO2 (кремнезем) – 21-24% = 95-97%
Al2O3 (глинозем) – 4-8%
Fe2O3 – 2-4%
6.1. Производство цемента
В качестве основных компонентов сырьевой смеси используются мергели (порода, состоящая из смеси известняка с глиной), известняк, глина. Помимо этого в смесь вводят корректирующие добавки (гипс) и промышленные отходы, обеспечивающие требуемый состав клинкера.
Производство цемента включает ряд технологических операций, которые можно разделить на две основные группы.
Первая это операции по производству клинкера, вторая измельчение клинкера совместно с гипсом, а в ряде случаев и с другими добавками, т.е. приготовление цемента.
Производство клинкера состоит из добычи сырьевых материалов, дробления, помола и смешивания их в определенном соотношении, обжига сырьевой смеси и магазинирования клинкера.
Комплекс операций по получению из клинкера портландцемента включает следующие технологические процессы: дробление клинкера, сушку минеральных добавок, дробление гипсового камня, тонкое измельчение клинкера совместно с активными минеральными добавками и гипсом, складирование, упаковку и отправку цемента потребителю.
Существует три способа производства, отличающихся технологическими приемами подготовки сырьевых смесей: мокрый, сухой и комбинированный.
При мокром способе тонкое измельчение сырьевой смеси производят в водной среде с получением шихты в виде водной суспензии шлама влажностью 30-50%.
Мокрый способ
Известняк Глина
Дробление Получение глиняного шлама
Совместный помол
Корректировка состава
Гипс + активные добавки
Обжиг при 1450С
Охлаждение
Тонкий помол
Силосное хранение
В водной среде облегчается измельчение материалов и улучшается их перемешивание. В результате снижается расход электроэнергии (при мягком сырье экономия может достигать 36 МДж/т сырья) и получается более однород ная шихта, что в конечном счете приводит к росту марки цемента. Кроме того, при мокром способе упрощается транспортировка шлама и улучшаются санитарно-гигиенические условия труда. Сравнительная простота мокрого способа и возможность получения высокомарочной продукции на сырье пониженного качества обусловили его широкое распространение в цементной промышленности нашей страны. В настоящее время этим способом выпускается около 85 % клинкера. В то же время введение в шлам значительного количества воды обусловливает резкое повышение расхода теплоты на ее испарение. В результате расход теплоты при мокром способе (5,8-6,7 МДж/кг) на 30-40% выше, чем при сухом способе. Кроме того, при мокром способе возрастают габариты и соответственно металлоемкость печей.
При сухом способе сырьевую шихту готовят в виде тонкоизмельченного сухого порошка, поэтому перед помолом или во время него сырьевые материалы высушивают.
Сухой способ
Сырьевые материалы
Дробление
Сушка (до W =1%) с совместным помолом (получение сырьевой муки)
Корректировка состава и гомогенизация
смеси
Обжиг при 1450С
Охлаждение
Тонкий помол
Силосное хранение
Необходимость экономии расхода топлива вынуждает перерабатывать по сухому способу материалы со все более высокой влажностью. Предварительное измельчение материалов повышенной влажности при сухом способе целесообразно осуществлять в мельницах самоизмельчения типа «Аэрофол», позволяющих перерабатывать сырье с влажностью до 25%.
Однако полностью высушиться сырье при этом не успевает и в шаровой мельнице одновременно с доизмельчением крупных частиц и получением однородной сырьевой смеси производится ее досушка.
Приготовление сырьевой смеси в виде порошка усложняет технологическую схему. Увеличивается число энергоемкого оборудования, более «капризного» при эксплуатации. Сложнее при сухом способе обеспечить санитарные условия и охрану окружающей среды. Но решающим его преимуществом является снижение расхода теплоты на обжиг клинкера до 3,4-4,2 МДж/кг. Кроме того, на 35-40% уменьшается объем печных газов, что соответственно снижает стоимость обеспыливания и дает больше возможностей по использованию теплоты отходящих газов для сушки сырья. Помимо этого происходит более высокий съем клинкера с 1 м3 печного агрегата, что позволяет проектировать и строить печи по сухому способу в 2-3 раза более мощные, чем по мокрому.
В целом по технико-экономическим показателям сухой способ превосходит мокрый. При использовании мощных печей он обеспечивает снижение удельного расхода топлива на обжиг клинкера примерно вдвое, рост годовой выработки на одного рабочего примерно на 40%, уменьшение себестоимости продукции на 10% и сокращение капиталовложений при строительстве предприятий на 50%. Это обусловило интенсивное его распространение в мировой цементной промышленности. Однако надо учитывать, что возможности применения сухого способа ограничены влажностью перерабатываемого сырья. Переработка сырья с влажностью более 20-25% по сухому способу связана с высокими расходами теплоты на сушку, и этот способ становится неэкономичным.
Наиболее перспективна технологическая схема комбинированного способа производства. Она может базироваться как на мокром, так и на сухом способе приготовления шихты.
В первом случае сырьевую смесь готовят по мокрому способу в виде шлама, а затем обезвоживают на фильтрах до влажности 16-18% и подают на обжиг в печь в виде полусухой массы. Во втором варианте сырьевую смесь готовят по сухому способу, а затем гранулируют с добавкой 10-14% воды и подают на обжиг в виде гранул диаметром 10-15 мм.
Комбинированная схема позволяет использовать преимущества подготовки сырьевой смеси по мокрому способу и одновременно снизить расход теплоты на обжиг. При этом почти на 30% уменьшается расход топлива и примерно на 10% капитальные затраты по сравнению с мокрым способом, но на 15-20% повышается расход электроэнергии. Такая схема наиболее реальный путь снижения расхода топлива предприятиями, работающими на сырье высокой влажности.
Сложность создание и внедрение надежных и высокопроизводительных аппаратов для фильтрации шлама.
6.2. Минеральный состав портландцементного клинкера. Расчет сырьевой смеси для получения клинкера
Минеральный состав портландцементного клинкера:
- Трехкальциевый силикат (алит)
ЗСаОSiO2 (C3S) 42-65%;
- Двухкальциевый силикат (белит)
2СаОSiO2 (C2S) 12-35%;
- Трехкальциевый алюминат
ЗСаОА12О3 (С3А) 4-14%;
- Четырехкальциевый алюмоферрит
4СаОА12О3Fe2O3 (C4AF) 10-18%.
Для расчета сырьевой смеси портландцементного клинкера широкое применение находят методы, основанные на использовании модулей, устанавливающих связь между содержанием основных окислов в смеси и их влиянием на свойства цементов (см. расчетную работу №1).
6.3. Классификация цементов
По назначению
- общестроительные и специальные.
По виду клинкера
- портландцементные;
- глиноземистые;
- сульфатоалюминатные;
- сульфатоферритные.
По вещественному составу
- бездобавочные;
- с минеральными добавками.
По прочности на сжатие
- с нормируемой прочностью (М200, М300, М400, М500, М550, М600);
- без нормирования прочности.
По скорости твердения
- нормальнотвердеющие;
- быстротвердеющие.
По срокам схватывания:
- быстросхватывающиеся (менее 45 мин);
- нормальносхватывающиеся (45 мин 2 ч);
- медленносхватывающиеся (свыше 2 ч).
6.4. Механизм твердения
При затворении цемента водой минералы клинкера химически взаимодействуют с ней, образуя гидратные новообразования, среди которых преобладают гидросиликаты кальция. Химический состав продуктов гидратации одного и того же минерала, их структура и вяжущие свойства в основном зависят от следующих факторов:
- состава исходного портландцемента;
- количества воды в системе, или так называемого водоминерального отношения. От этого соотношения зависит степень пересыщения раствора;
- наличия и концентрации извести, гипса и щелочей в растворе;
- температуры внешней среды;
- вида и количество добавок;
- взаимного влияния друг на друга отдельных реакций, происходящих при твердении.
Процесс гидратационного твердения цемента, является длительным, может продолжаться годами в уже готовом изделии.
Алит представляет собой соль, способную к гидролизу. Поэтому С3S при воздействии воды не только гидратируется, но и подвергается гидролизу. Он быстро взаимодействует с водой, образуя гидросиликаты кальция (продукты гидратации) и гидрооксид кальция (продукт гидролиза):
2(ЗСаО.SiO2,) + 6H2О 3Ca(OH)2 +
+ 3CaO.2SiO2.3H2O
Гидратация других минералов клинкера протекает в среде, насыщенной гидрооксидом кальция, поэтому их гидролиз частично или полностью подавляется.
Белит взаимодействует с водой медленно. Его твердые растворы гидролизуются в значительно меньшей степени, чем С3S:
2(2СаО.SiO2,) + 4H2О Ca(OH)2 +
+ 3CaO.2SiO2.3H2O
Трехкальциевый алюминат гидролизу не подвергается, а гидратируется с образованием крупных кристаллов по уравнению:
ЗСаОА12О3 + H2O ЗСаОА12О36Н2О
Четырехкальциевый алюмоферрит так-же только гидратируется, образуя гидро-алюминат и гидроферрит кальция:
4СаО.Аl2О3.Fe2O3 + 7H2O
ЗСаО.А12О3.6Н2О + CaO.Fe2O3.H2O
Основной продукт твердения портландцемента гидросиликаты кальция, которые практически нерастворимы в воде. Они выпадают из раствора сначала в виде геля, пронизывающего кристаллы Са(ОН)2 , который со временем кристаллизируется. Остальные продукты взаимодействия клинкера с водой также участвуют в формировании структуры цементного камня и влияют на его свойства.
6.5. Механизм гидратации минералов клинкера портландцемента
Процесс гидратации портландцемента подразделяют на три периода, между которыми, однако, невозможно провести четкие временные границы.
Первый период. Сразу же после затворения водой на поверхности соприкосновения частиц цемента с водой начинается процесс растворения безводных минералов. В результате вода в течение нескольких минут пересыщается ионами Са2+ и ОН- и насыщается ионами SO42-, K+, Na+. В раствор переходят также небольшие количества ионов А13+, Fe3+ и SiO32-. Пресыщение ионами Са2+ и ОН--ионами обусловлено гидролизом 3CaO.SiО2. Растворение гипса, добавленного при помоле в клинкер, приводит к быстрому насыщению воды затворения SO42--ионами.
Вследствие разогрева при измельчении двуводный гипс CaS04 .2H2О частично обезвоживается и потому может находиться в цементном порошке в виде ангидрита СаSO4 и полуводного гипса СаSO4.1/2H2O.
На этой же стадии начинаются реакции гидратации и гидролиза отдельных минералов и фаз клинкера, приводящие к возникновению гидратных новообразований. Из пересыщенного раствора кристаллизуются Са(ОН)2 и эттрингит (продукт преобразования гипса), покрывающие тонкой гелеподобной пленкой поверхность частиц цемента. Так как при этом затрудняется диффузия воды к негидратированным слоям частиц, то процесс гидратации замедляется. В формировании гелевой пленки на частицах участвуют также кристаллы образующихся гидросиликатов. Продолжительность начального периода составляет 1-3 часа.
Второй период – это стадия завершения формирования эттрингита. На этой стадии происходит интенсивное выделение кристаллов гидратных новообразований. Затем растущие под гелевой пленкой кристаллы эттрингита разрывают ее и процесс образования гидратов, в том числе эттрингита, ускоряется. Таким образом, через 4-6 часов наступает стадия ускоренной гидратации. По мере накопления продуктов реакций разрушенная оболочка вновь восстанавливается и процесс гидратации вновь замедляется до следующего разрыва пленки. Продолжительность этих повторяющихся процессов определяется концентрацией ионов SO42-. Процесс связывания cульфат-ионов в эттрингит продолжается примерно 24 ч. Причем образование эттрингита сопровождается значительным увеличением объема. Его кристаллы заполняют поры и межзерновое пространство теста и придают камню повышенную прочность. Кристаллы гидросиликатов кальция на этой стадии образуются в виде длинных волокон, заполняя межзерновое пространство.
Третий период конечный период твердения (до полной гидратации исходных минералов). На этой стадии нарастающая на частичках гелевая пленка все более уплотняется, так как вода отсасывается внутренними негидратированными слоями частичек.
Кроме того, происходит рост первичных мельчайших кристаллов гидратных новообразований. Поэтому в этом периоде скорость гидратации определяется скоростью диффузии воды через уплотняющуюся оболочку частиц цемента.
6.6. Коррозия цементного камня (бетона)
Совокупность самопроизвольно протекающих процессов разрушения бетона под воздействием окружающей среды называется коррозией бетона.
Разрушение бетона начинается с коррозии цементного камня, стойкость которого меньше, чем у наполнителей. Различают физическую и химическую коррозии цементного камня.
Физическая коррозия заключается в растворении и вымываиии водой составляющих цементного камня, прежде всего гидроксида кальция Ca(OH)2 (выщелачивание Са(ОН)2). Вымывание структурных компонентов понижает плотность и прочность бетона.
Физическую коррозию ускоряет фильтрование воды через толщу бетона.
Замедляющее действие на физическую коррозию оказывает жесткая вода. Содержащиеся в ней ионы Са2+ понижают растворимость Ca(ОH)2. Также уменьшению физической коррозии способствует карбонизация Са(ОН)2 на поверхности бетона, т.к. образуется малорастворимый СаСО3.
Для защиты бетона от физической коррозии в состав портландцемента вводят активные минеральные добавки. Компоненты последних (например, активный SiО2) реагируют с Са(ОН)2, превращая его в менее растворимые соединения. Степень физической коррозии также понижается при применении плотных бетонов.
Химическая коррозия подразделяется на следующие виды:
- углекислотную;
- магнезиальную и магнезиально-сульфатную;
- сульфатную.
- Углекислотная коррозия бетона происходит под воздействием природных (или промышленных) вод, содержащих “агрессивную углекислоту”, вымывающую легкорастворимые продукты.
- Магнезиальная коррозия обусловлена действием вод, содержащих растворенные соли магния. При этом вымывается растворимый CaCl2, а гидроксиды магния, алюминия и кремнекислота выделяются в виде рыхлых, аморфных масс, не препятствующих проникновению воды в толщу бетона.
- Cульфатная коррозия бетона происходит при действии вод, содержащих растворенные сульфаты кальция, магния, щелочных металлов. Сульфаты взаимодействуют с гидроалюминатом кальция и гидроксидом кальция цементного камня, в результате чего происходит образование гидросульфоалюмината кальция в порах и капиллярах бетона, которое сопровождается значительным увеличением его объема (в 4,7раз) и растрескиванием затвердевшего камня.
Способы защиты бетона от коррозии сводятся, в основном, к двум главным принципам:
1. изоляция бетона от контакта с агрессивной средой, для чего используют различные покрытия: масляные краски, полимерные лаки, битумные обмазки, облицовка природным камнем и т.п.;
2. уменьшение содержания в цементном камне (бетоне) минералов, способных к взаимодействию с компонентами среды, что достигается введением в исходный портландцемент активных минеральных добавок, содержащих тонкоизмельченный кремнезем SiO2.
Кроме того, для борьбы с коррозией бетона необходимы правильный выбор вида цемента в зависимости от условий эксплуатации изделия, конструкции и т.д., а также по возможности применение плотных бетонов.
6.5. Свойства и области применения
Свойства портландцемента и области использования зависят от его минерального состава и тонкости помола клинкера (см. табл.).
Основные свойства:
- прочность на сжатие;
- сроки схватывания;
- тонкость помола.