Технологическое оборудование гап
Вид материала | Задача |
- Рабочая программа по дисциплине дс. 02. 02 «Технологическое оборудование отрасли», 255.51kb.
- Рабочая программа по дисциплине сд 02. 02 «Технологическое оборудование», 267.47kb.
- Памятка для студентов групп мапп-31; мапп-32 по изучению дисциплины "Технологическое, 77.03kb.
- Технологические машины и оборудование, 7.35kb.
- Аннотация рабочей программы дисциплины «Основы расчета и конструирования машин и аппаратов, 40.28kb.
- Аннотация рабочей программы дисциплины «Монтаж, эксплуатация и ремонт технологического, 26.71kb.
- Аннотация рабочей программы дисциплины «Начертательная геометрия. Инженерная графика», 29.27kb.
- Аннотация рабочей программы дисциплины «Теория механизмов и машин» для направления, 28.8kb.
- Аннотация рабочей программы дисциплины «Экономика c/х и перерабатывающих предприятий», 127.54kb.
- Аннотация рабочей программы дисциплины «Технологические процессы переработки молока, 31.06kb.
СОДЕРЖАНИЕ
стр
1. Интегрированные АСУ предприятиями с дискретными технологическими
процессами 2
1.1. Гибкие производственные системы (ГАП) 2
1.2. Принципы создания ГАП 3
- Интегрированные АСУ ГАП (компьютеризированные интегрированные производства 4
- Технологическое оборудование ГАП. Станки с ЧПУ 6
- Промышленные работы и робототехнические системы 8
2. Проектирование АСУ 21
2.1. Предпроектная стадия 21
2.2. Технический проект 22
2.3. Рабочий (технорабочий) проект 23
3. Проектирование информационного обеспечения ИАСУ 24
- Терминология информационного обеспечения 24
- Перечень работ, выполняемых при создании информационной базы 24
- Классификация и кодирование информации 25
- Структура информационного обеспечения ИАСУ 27
- Стадии проектирования информационной БД ИАСУ 28
- Распределенные банки данных в ИАСУ 29
- Документация информационного обеспечения 30
4. Проектирование программного обеспечения 32
5. Техническое обеспечение ИАСУ 34
5.1. Требования к КТС ИАСУ 34
5.2. Структура КТС ИАСУ 35
6. Автоматизация проектирования АСУ 36
6.1. Проблемы и задачи автоматизации проектирования АСУ 36
6.2. Типизация как элемент автоматизации проектирования АСУ 37
6.3. Методы формализации и алгоритмизации задач синтеза структуры АСУ 38
6.4. Методы формализации и автоматизации проектирования информационного
и программного обеспечения 43
6.5. Модульный принцип разработки информационного и программного
обеспечения 48
7. Методы автоматизации управления проектированием АСУ 53
- Проблемы и задачи управления проектированием 53
- Задача составления титульного списка 53
- Модели и методы определения оптимальной очередности разработки задач и 54 подсистем АСУ, а также распределения ресурсов для их разработки
ЛИТЕРАТУРА
- Общеотраслевые руководящие методические материалы по построению ИАСУ, М.,1979, ГКНТ СССР.
- Стефани Е.П., Основы построения АСУТП, М., Энергоиздат,1982.
- Кальфа В., Овчинников В.В. и др., Основы автоматизации управления производственными процессами, М. Сов. Радио, 1980.
4. Юревич Е.И. и др., Системы управления промышленными роботами и манипуляторами, Л-д, Энергия, 1980.
5. Под ред. Майорова С.А, Орловского Г.В., Гибкое автоматическое производство, Л-д, Машиностроение ,1983.
6. Лещенко В.А, Киселев В.М., Гибкие производственные комплексы, М., Машиностроение 1984.
7. Под редакцией Юревича Е.И., Промышленная робототехника и гибкие автоматизированные производства (опыт разработки и внедрения), Л-д, 1984.
8. Мамиконов А.Г., Цвиркун А.Д., Кульба В.В., Автоматизация проектирования АСУ, М., 1981.
1. Интегрированные АСУ предприятиями с дискретными технологическими процессами.
1.1. Гибкие производственные системы (ГПС).
Существенные отличия дискретных технологических процессов от непрерывных вызвали качественно иной подход к системам управления ими.
В течение последних десятилетий развитие АСУДТП шло по пути создания систем числового программного управления станками и станочными линиями, а также разработки промышленных роботов и манипуляторов и систем управления ими.
В восьмидесятые годы появились гибкие производственные системы, которые объединяют производственное оборудование и системы управления станками и вспомогательными операциями.
В соответствии с ГОСТ 26228-84 ГПС - совокупность технологического оборудования и системы обеспечения его функционирования в автоматическом режиме, обладающая свойством автоматизированной переналадки при изменении номенклатуры изделий.
По организационной структуре ГПС подразделяются на следующие уровни:
- Гибкий производственный модуль (1 ИМ) - автономно функционирующая система, состоящая из единицы технологического оборудования и системы программного управления процессом;
- Гибкая автоматизированная линия (ТАЛ) - система, состоящая из нескольких ГПМ, объединенных автоматизированной системой управления;
- Гибкий автоматизированный участок (ГАУ) - система, состоящая из нескольких ГПМ, объединенных АСУ, функционирующая по изменяющемуся технологическому маршруту;
4. Гибкий автоматизированный цех (ГАЦ) - совокупность нескольких ГАЛ и ГАУ;
5. Гибкий автоматизированный завод (ГАЗ) - совокупность ГАЦ.
По ступеням автоматизации ГПС подразделяется на:
- гибкие производственные комплексы (ГПК) - автономно функционирующие системы, состоящие из нескольких ГПМ, объединенных автоматизированной системой управления и автоматизированной транспортно-складской системой;
- гибкие автоматизированные (автоматические) производства (ГАП) - системы, состоящие из одного или нескольких ГПК, объединенных автоматизированной системой управления производством и транспортно-складской автоматизированной системой, и осуществляющие автоматизированное проектирование и изготовление новых изделий при помощи автоматизированных систем научных исследований (АСНИ), автоматизированных систем технологической подготовки производства (АСТПП), автоматизированных систем проектирования (АСПро), автоматизированных обрабатывающих центров (либо станков с ЧПУ), обслуживаемых промышленными роботами.
ГАП рассчитано на выпуск серийных и мелкосерийных изделий. В промышленно развитых странах крупносерийное и единичное производство составляет 20%, а мелкосерийное и серийное производство - 80%. При этом традиционные АСУТП (аналогичные АСУНТП) применимы только для массового производства.
В Японии уже в 1985 г. 20% всей промышленной продукции выпускалось ГАПами. С 1985 г. функционирует ГАЗ фирмы ФАНУК по изготовлению роботов (роботы проектируют и изготавливают роботов). В США первый ГАЗ был построен к 2000 г. -самолетостроительный завод-автомат.
К преимуществам ГАП по сравнению с участками, составленными из универсальных станков и обслуживаемыми рабочими, следует отнести:
• резкое увеличение производительности труда в процессе изготовления серийной и мелкосерийной продукции, благодаря более полной загрузке оборудования, что особенно важно в условиях нарастающего дефицита рабочей силы в стране. (Уменьшение численности рабочих, увеличение отдачи станков при внедрении ГАП происходит на 80-200%. ГАП получили широкое распространение в Европе, США и Японии с начала 70-х годов.)
• быстрое реагирование на изменение требований заказчиков;
• существенное повышение качества продукции за счет устранения ошибок и нарушений технологических режимов, неизбежных при ручном труде;
- сокращение времени производственного цикла (в несколько раз);
- снижение объема незавершенного производства;
• улучшение условий труда, высвобождение человека от малоквалифицированного, сложного, вредного, трудоемкого, монотонного труда.
1.2. Принципы создания ГАП.
1.2.1. Принцип совмещения высокой производительности и универсальности.
Наибольшая производительность достигается на автоматических линиях, а универсальность - на универсальном оборудовании.
Это противоречие устраняется посредством автоматической перенастройки станков программным путем.
Принцип совмещения предполагает нахождение оптимального на данном уровне развития техники соединения универсальности и автоматизации в программно-управляемом и перенастраиваемом оборудовании. Нахождение такого оптимума позволяет наилучшим образом решить задачу технической реализации ГАП.
1.2.2. Принцип модульности.
ГАП строят на базе гибких производственных модулей. Модуль, являясь компонентом ГАП, сам может состоять из компонентов, самостоятельно разрабатываемых и изготовляемых.
1.2.3. Принцип иерархичности.
ГАП представляет собой многоуровневую структуру: на нижнем уровне ГПМ, затем ГПЛ, ГПУ, ГАЦ, ГАЗ. Каждый более высокий уровень взаимодействует с ≥2 элементами нижних уровней, не считая модулей складирования, транспортировки и управления.
Принципы модульности и иерархичности позволяют создавать проекты ГАП любого уровня сложности.
1.2.4. Принцип преимущественной программной перенастройки.
Перенастройка станков должна быть автоматизирована. Перенастройка станков вручную допустима в минимальных объемах и только в случаях очевидной экономической неэффективности программной перенастройки.
1.3. Интегрированные АСУГАП (компьютеризированные интегрированные
производства).
Работа всех производственных комплексов ГАП (технологическое оборудование, складские и транспортные системы) координируются как единое целое многоуровневой системой управления, обеспечивающей изменение программы функционирования компонентов ГАП и тем самым быструю перестройку технологии изготовления при смене объектов производства.
На первом этапе функционирования ГАП может быть автоматизированным, т.е. включать операции, выполняемые человеком.
На рис. 1.1 приведена структурная схема ИАСУ, включающая ГАП.
В общем случае ГАП состоит из исполнительной системы, включающей технологическую, транспортную и складские подсистемы, а также систему управления (СУГАП), координирующую функционирование указанных подсистем.
Технологическая подсистема представляет собой совокупность взаимосвязанных технологических модулей ( станки с ЧПУ, станочные линии с роботами).
Транспортная подсистема состоит из модулей, осуществляющих перемещение заготовок деталей, готовых изделий и инструментов между технологическими ячейками и секциями автоматизированных складов, а также удаление отходов производства.
Складская подсистема обеспечивает автоматический прием, хранение и учет заготовок, готовых изделий и инструмента, а также автоматический поиск и выдачу их транспортному роботу.
Система управления ГАП состоит из средств вычислительной техники, связанных в единый комплекс с помощью устройств передачи данных, а также программного обеспечения для координации всех подсистем нижнего уровня.
Работники в ГАП выполняют следующие функции:
- управление с пультов (при отладке или отказе автоматики);
- обслуживание станков ( при неисправности робота) ;
- обнаружение и устранение неисправностей станков и аппаратуры СУГАП;
- уборка стружки, помещения и т.д.
Дальнейшее развитие систем управления ГАП сводится к объединению отдельных систем: АСУП, АСНИ, АСПро, АСТПП и СУГАП в единую интегрированную систему проектирования и производства, которую в последнее время стали называть компьютеризированным интегрированным производством (КИП).
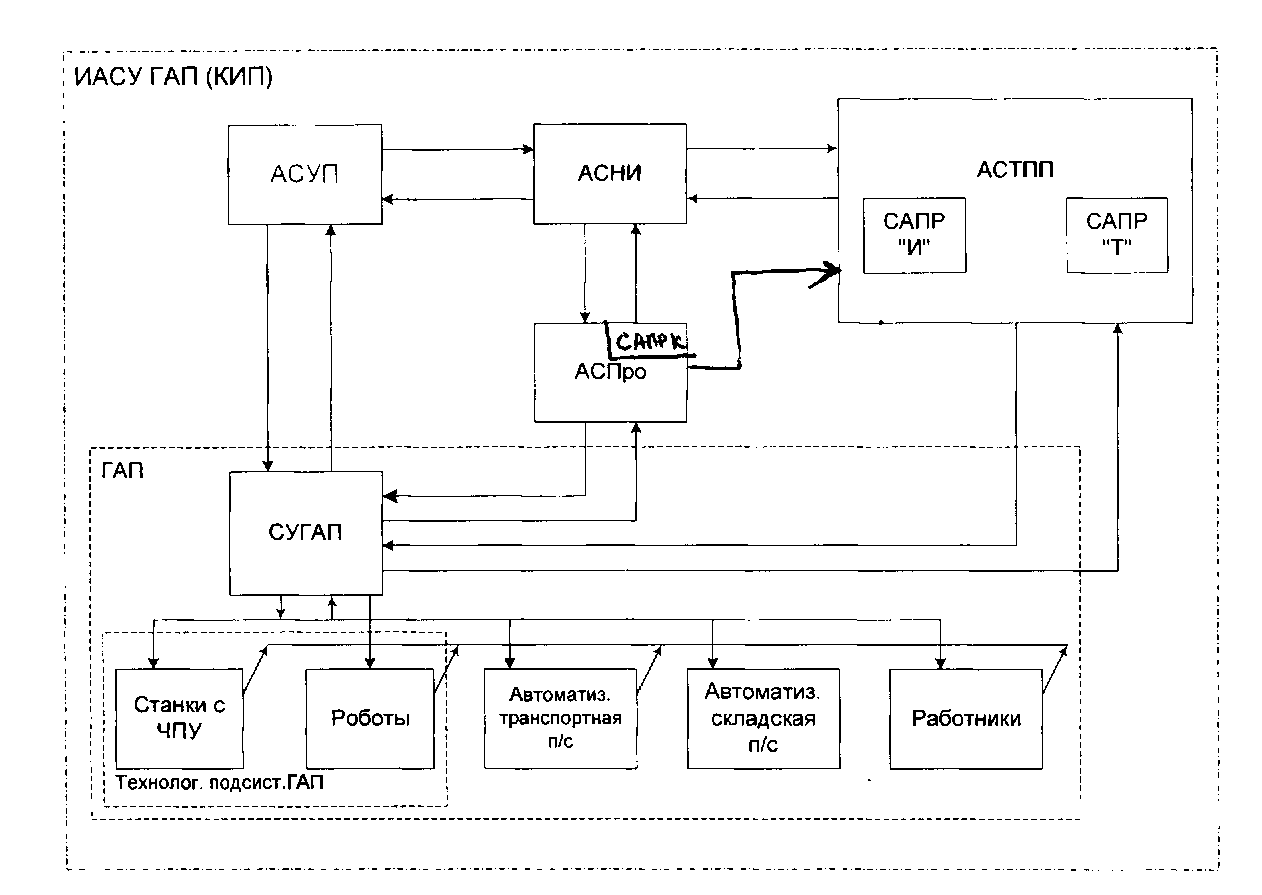
Рис. 1.1
Результаты, формируемые подсистемами верхнего уровня:
- программы научно-исследовательских и проектно-конструкторских работ по расчету, конструированию и проектированию технологии изготовления новых видов изделий (АСУП);
- программы производства, детализированные до уровня технологических операций и очередности запуска партий деталей на обработку (АСУП);
- конструктивные чертежи проектируемых изделий (АСПро);
• управляющие программы работы технологического оборудования (АСТПП). Реализация указанных программ и является функцией ГАП.
Современные вычислительные комплексы, используемые в АСПро и АСТПП, способны передавать данные о конструкции и технологии производства изделий непосредственно в ЭВМ, управляющих работой станков. За счет этого процесс проектирования изделия, технологическая подготовка производства и изготовление изделия возможны в результате взаимосвязи ЭВМ каждой из указанных систем (АСНИ, АСПро, АСТПП и СУГАП) на основе общей базы данных.
Обычно комплексная ИАСУ ГАП (КИП) состоит из АСУП, АСНИ, АСПро, АСТПП и СУГАП, связанных с помощью локальной сети ЭВМ.
1.4. Технологическое оборудование ГАП. Станки с ЧПУ.
1.4.1. Требования к технологическому оборудованию ГАП.
К основному технологическому оборудованию ГАП (металлорежущим станкам) предъявляются следующие требования:
• обработка в автоматическом режиме значительной номенклатуры деталей при максимальной концентрации операций на одних и тех же станках (это позволяет сохранить количество оборудования, число его переналадок и уменьшить продолжительность производственного цикла);
• обеспечение работы оборудования полностью в автоматическом режиме;
- возможность быстрой переналадки оборудования при смене обрабатываемых деталей;
- компоновочная и программная стыковка основного оборудования с транспортно-складскими системами и промышленными роботами.
Указанным требованиям наиболее полно отвечают станки с числовым программным управлением (ЧПУ) ввиду высокой степени автоматизации процесса обработки металла, а также удобства и быстроты переналадки. Следует отметить, что появление ГАП механообработки во многом обусловлено широким распространением в промышленности станков с ЧПУ и необходимостью интенсификации их работы.
Нередко обработка деталей по управляющим программам занимает не более 25 - 40% фонда рабочего времени. Остальное время затрачивается на замену деталей, инструмента, ожидание заготовок, оснастки и прочие организационно-технические мероприятия. За счет автоматизации транспортно-складских операций в ГАП, оптимального оперативно-календарного планирования, цифрового управления оборудованием, автоматического контроля и диагностики неисправностей продолжительность работы станков по управляющим программам достигает 90 - 95% их фонда рабочего времени.
Для обеспечения полной автоматизации производственных процессов в ГАП необходимо автоматизировать загрузку заготовок и выгрузку деталей, закрепление заготовок, смену инструмента, контроль качества обрабатываемых деталей, контроль за степенью износа инструмента, удаление стружки из зоны резания и за пределы станка и т.д. Автоматизация загрузки заготовок и выгрузки деталей на токарных станках в ГАП реализуется, в основном, промышленными роботами (ПР).
1.4.2. Системы ЧПУ.
Систему ЧПУ станком можно представить как систему управления, в состав которой входит:
- источники информации (датчики) об объекте управления и внешней среде;
- исполнительные устройства (двигатели, контакторы, редукторы и др.) ;
- устройство числового программного управления (УЧПУ);
• внешние устройства обмена информацией "УЧПУ-оператор", "УЧПУ-ЭВМ" (или сеть ЭВМ) ;
• вспомогательные блоки и устройства.
Система ЧПУ является подсистемой ИАСУ ГАП. В то же время систему ЧПУ можно разбить на ряд собственных подсистем:
- подготовки и ввода данных;
- управления движения;
- управления инструментом.
В процессе эксплуатации система ЧПУ активно взаимодействует со смежными системами - системой диспетчерского управления работой ГАП, системой оперативного учета и планирования, системой контроля за работой оборудования и т.п.
С момента возникновения сменилось три поколения станков с ЧПУ.
Технические средства ЧПУ первого поколения представляли собой жесткие не перенастраиваемые логические схемы на транзисторах. В такие системы сложно вносить изменения программы из-за неполной взаимозаменяемости отдельных узлов и элементов логической схемы.
Использование мини-ЭВМ и больших ЭВМ в системах ЧПУ второго поколения позволило управлять несколькими станками с помощью одной ЭВМ. Однако, поскольку центральная ЭВМ системы ЧПУ должна была работать в режиме разделения времени и выполнять при этом функции управления движениями, то такие ЭВМ не справлялись с задачами.
С появлением МП на базе БИС ( ЧПУ третьего поколения) появилась возможность реализации функциональных узлов на основе микропроцессорного распределенного управления и создания в результате этого высоконадежных систем (надежность МП на порядок выше надежности мини-ЭВМ).
Устройства ЧПУ можно разделить по технологическим признакам на:
- позиционные,
- контурные,
- универсальные.
Станки с позиционными СУ могут быть:
• с управлением положений отдельных точек, когда технологическая операция обработки детали происходит после позиционирования инструмента или заготовки;
• с управлением перемещениями вдоль отрезков, параллельных направляющим исполнительных устройств ( при этом исполнительные устройства работают поочередно, обходя поверхность обработки по прямоугольному контуру).
В СУ контурного типа (или СУ с программирование криволинейных профилей) сложная траектория обработки обеспечивается совместным и взаимосвязанным движением нескольких исполнительных устройств.
В универсальных СУ осуществляется позиционно-контурная обработка при взаимосвязанном движении исполнительных устройств.
Устройства ЧПУ третьего поколения обеспечивают:
- ввод в систему ЧПУ управляющих программ, параметров настройки станка, а также поправок от датчиков состояний, компенсирующих внешние возмущения;
- расчеты траекторий запрограммированных перемещений, корректирующих поправок и выработку управляющих воздействий на исполнительные органы;
- выдачу на исполнительные органы сигналов управления технологическими режимами обработки.
С учетом этих функций в устройствах ЧПУ выделяют 3 основные части:
- устройства ввода-вывода и связи с оператором,
- устройство обработки информации (процессор),
- устройство связи с объектом (УСО).
Состав функций управления определяется специальным программным обеспечением устройства ЧПУ, сохраняемым во внешней памяти ЭВМ. Там уже хранятся константы настройки станка. В оперативной памяти размещены управляющие программы, оперативно-изменяемые константы законов управления, программы типовых циклов и подпрограммы обработки.
Программирование обработки металла может задаваться через дисплейный терминал в режиме диалога «оператор-УЧПУ». Кроме основной задачи управления перемещением подвижной части станка, ЭВМ может решать также задачи совмещенного управления различными узлами производственной ячейки, включающей системы транспортировки и загрузки-разгрузки. На этой основе при достаточной вычислительной мощности процессора ЭВМ удается решить совокупность новых задач, предъявляемых к УЧПУ при их использовании в ГАП.
В настоящее время УЧПУ Ш поколения реализуются в основном на базе микроЭВМ. Эти УЧПУ обладают достаточными функциональными возможностями при управлении станками и относительно легко могут встраиваться в локальные сети ЭВМ ГАП.
1.5. Промышленные роботы и робототехнические системы. 1.5.1. Определение и структура робота.
Промышленный робот (ПР) - это перепрограммируемая автоматическая машина, способная выполнять аналогичные выполняемым человеком двигательные функции по перемещению предметов производства и технологической оснастки. ПР характеризуется универсальностью движений и быстротой переналадки на новые операции.
Характерная особенность робота - это его активное и целенаправленное информационное и физическое взаимодействие с внешней средой. Это обеспечивается наличием в составе робота чувствительных (сенсорных) устройств и исполнительных органов, с помощью которых робот взаимодействует с внешней средой и перемещается в ней.
Обязательным признаком робота является его многофункциональность. Поэтому, например, однопрограммное загрузочное устройство не является роботом, поскольку это
оперативно не перенастраиваемый автоматический манипулятор. Обобщенная структура робота, управляемого от ЭВМ приведена на рис. 1.2.
Исполнительные органы (ИО) обеспечивают реализацию двигательных функций робота. К ним относятся манипуляторы и устройства передвижения.
Манипулятор - многозвенный механизм с вращательными и поступательными сочленениями с числом степеней подвижности от 3 до 10, заканчивающийся рабочим органом в виде схвата или специального инструмента (вакуумная присоска, сварочный электрод, пульверизатор, гайковерт и т.д.).
Устройства передвижения роботов могут быть основаны на любом из известных способов передвижения (используются гусеничные, колесные, шагающие и др. типы движителей). Например, луноход с отбором проб для анализа.
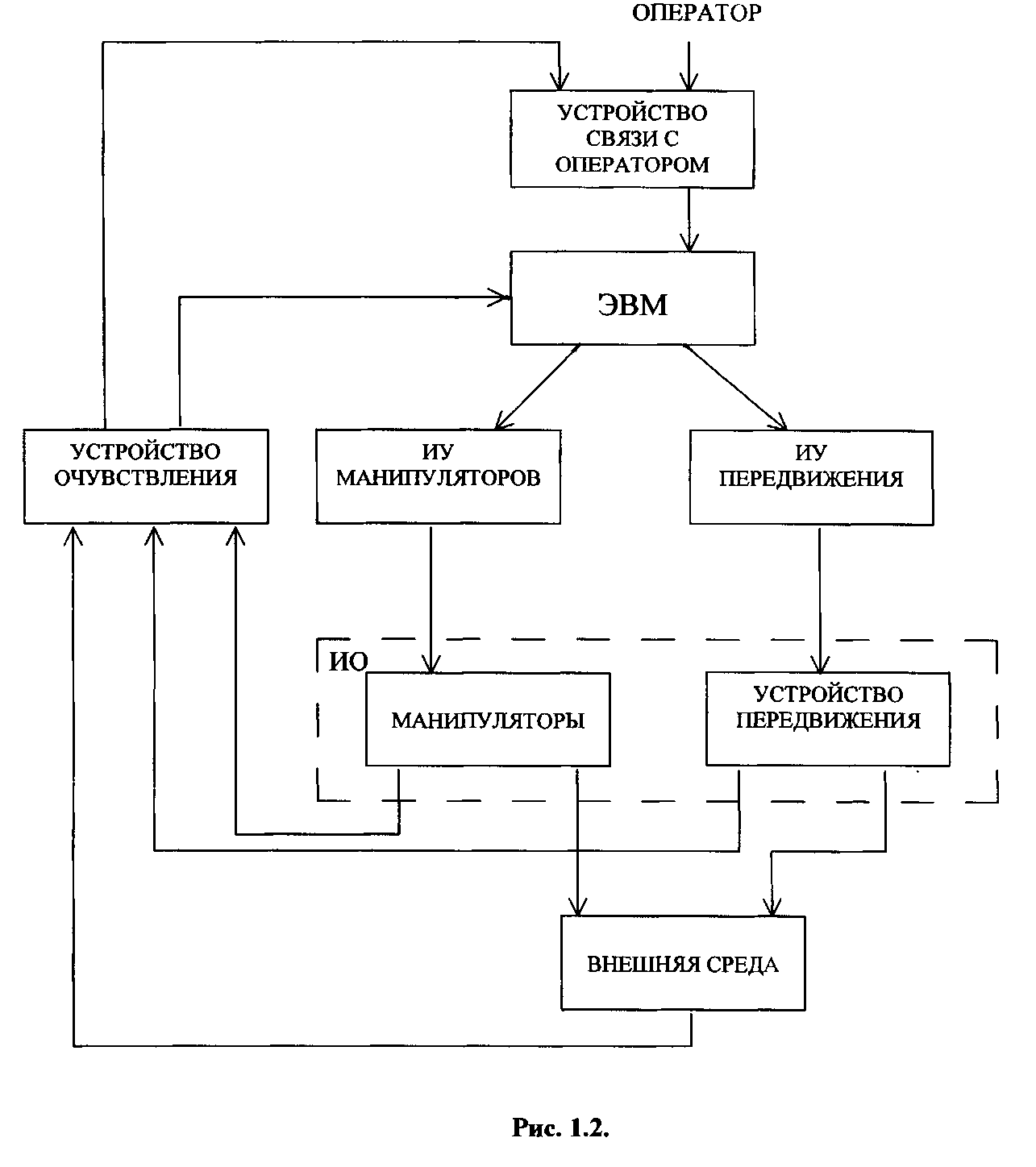
Исполнительные устройства (ИУ) манипуляторов и устройств передвижения представляют собой систему приводов для каждой отдельной степени подвижности. Приводы бывают 3-х основных типов: электрические, гидравлические и пневматические.
Устройства очувствления делятся на 2 группы:
- устройства сбора информации о внутреннем состоянии робота,
- устройства сбора информации о внешней среде.
При помощи первой группы устройств организуются обратные связи внутри робота. Такими устройствами являются измерительные преобразователи угловых и линейных перемещений звеньев манипулятора, а также сенсоры скоростей и ускорений движения звеньев.
Вторая группа устройств дает возможность организовать адаптивное управление роботом в зависимости от состояния внешней среды. К таким устройствам относятся:
- локационные сенсоры (распознавание предметов или препятствий),
- сенсоры усилий (оценка прикладываемого усилия),
- сенсоры проскальзывания (реагирование на выскальзывание объектов манипулирования из схвата),
- датчики промышленного телевидения.
Устройства связи с оператором представляют собой набор различных средств, обеспечивающих связь оператора с роботом и получение им информации о функционировании робота.
К этим средствам относятся видеотерминалы (оператор получает визуальную информацию о процессе функционирования робота, задает с пульта координаты объекта или точку перемещения), принтеры и т.д.
Выдача роботу заданий и различных инструкций может производиться также голосом. В настоящее время существуют программы и специализированные устройства, позволяющие роботу различать до 200 слов. Речевые ответы робота могут осуществляться с помощью синтезатора речи либо с помощью записанных на магнитофоне информационных сообщений.
Наиболее важной составной частью робота является ЭВМ, которая перерабатывает все поступающие от сенсорных устройств данные и с учетом первоначально заложенной программы движения вырабатывает управляющие воздействия на приводы. Алгоритмы и программы обработки информации и выработки управляющих воздействий можно относительно просто модифицировать или заменять.
При управлении роботом иногда применяется иерархическая система нескольких управляющих ЭВМ (например, в подвижных роботах). На подвижном роботе устанавливается бортовая ЭВМ малой мощности (осуществляющая выдачу управляющих воздействий на приводы и первичную обработку информации от сенсоров, размещенных на роботе), а основной объем переработки сенсорной информации и вычисление управляющих воздействий производится на мощной стационарной ЭВМ, которая связывается с бортовой ЭВМ либо по радиоканалу, либо кабельной связью.
При групповом управлении несколькими роботами одним из вариантов системы управления является комбинация центральной ЭВМ и подчиненных ей периферийных ЭВМ малой мощности, управляющих отдельными роботами.