Исследование гидрометаллургических процессов в многокомпонентных системах производства вторичных цветных металлов
Вид материала | Исследование |
В первой главе Вторая глава В третьей главе Четвертая глава |
- Гост 1639-78: лом и отходы цветных металлов и сплавов общие технические условия, 1661.44kb.
- Разработка экологически чистых технологий комплексного извлечения благородных и цветных, 759.54kb.
- «производство отливок из сплавов цветных металлов», 38.25kb.
- Московский Государственный Институт Стали и Сплавов (Технологический Университет) Кафедра, 461.38kb.
- Темы рефератов по дисциплине «Материаловедение», 19.05kb.
- Исследование переходных процессов в замкнутых нелинейных системах управления 111, 347.96kb.
- Правительства Российской Федерации от 23 июля 2002 г. # 552 "Об утверждении Положения, 136.41kb.
- Извлечение цветных и редких металлов из отходов металлургического производства и нетрадиционных, 531.33kb.
- Гост 1639-93 Лом и отходы цветных металл. Общие технические условия, 1007.65kb.
- А. Б. Коростелев, А. В. Тарасов, Парецкий, 208.73kb.
В первой главе приведены результаты исследования химического растворения многокомпонентных металлических систем в сернокислых растворах.
Снятие вольтамперных кривых проводили на потенциостате IPC-Pro, сопряженном с персональным компьютером. Применяли потенцио- и гальваностатические режимы. Использовали медно-цинковые сплавы (до 12% Zn) и медь-цинк-оловянные сплавы (до 10% Sn).
Результаты изучения зависимости бестокового потенциала Ек от времени показали, что на Ек-t - кривой имеется задержка потенциала в области
-0,4-0,5 В. Примерно через 600 с Ек довольно резко смещается в положительную сторону на 0,2 В с последующим установлением стационарного значения. Подобный ход Ек- - кривой, очевидно, свидетельствует о наличии селективного растворения цинка. При введении в состав сплава до 5% Sn задержка на Ек- кривой практически отсутствует, а на iZn--кривой наблюдается более быстрый спад iZn до нуля. Это дает основания предполагать, что при введении олова происходит торможение первичного селективного растворения цинка.
Аналогичные исследования были выполнены при потенциалах, отвечающих анодному растворению обоих компонентов сплава (рис. 1).
Чтобы выяснить причину столь сложного характера i- - кривой, проследили за изменением во времени концентрации меди (СCu) и цинка (СZn) в растворе в процессе снятия показаний. Анализ поводили с использованием чувствительного метода инверсионной вольтамперометрии (анализатор ИВА-5). Как видно из рис. 2, ССu сначала возрастает, примерно через 1 ч достигает максимального значения и далее снижается (кривая 1). Следовательно, медь, вышедшая в раствор в начальный период, через некоторое время начинает обратно осаждаться на электроде, тогда как величина СZn возрастает в течение всего опыта (кривая 2). Из наклона этих кривых были рассчитаны величины iZn и iCu. Результаты приведены на рис. 1 а. Как видно, iZn в. течение первых 200 с резко снижается до некоторого минимального значения, а затем возрастает до стационарной величины (кривая 2). Величина iСu в течение первых 40 мин остается практически постоянной (кривая 5), в дальнейшем снижается, и примерно через 1 ч ток изменяется с анодного на катодный. При этом, начиная с 200 с, сумма парциальных токов растворения меди и цинка ip (кривая 5) в пределах ошибки эксперимента (10—15%) совпадает с внешним током.
В качестве нейтрализатора перспективно применение порошковой меди, получаемой методом воздушного распыления. Этот материал имеет большую реакционную поверхность, а для ее получения пригодны вторичное сырье или отходы и полупродукты производства.
Проведенные поисковые исследования показали, что скорость растворения нерассеянного порошка сплава (6,2% Zn, 3,4% Sn) в среднем в 1,5 раза ниже, чем классифицированного порошка крупностью -0,1 мм.
Порошок, полученный распылением расплава сжатым воздухом, имел следующие свойства:, насыпная масса – 4,4 г/см3, удельная поверхность – 0,09 м2/г, форма частиц – близкая к сферической.
Результаты исследований по растворению порошка при механической агитации с подачей в раствор воздуха показали, что при растворении сплавов (353-358 К, H2SO4:Cul) достигнута максимальная скорость процесса до 56-60 г/(дм3ч). Эта величина сопоставима со скоростью растворения меди при нейтрализации отработанного электролита медного производства. Скорость процесса ограничивается диффузией окислителя через образующиеся поверхностные солевые пленки.
Полученные зависимости использованы для определения средней скорости растворения меди при изменяющихся во времени концентрациях ионов меди (II) и серной кислоты.
Вторая глава посвящена исследованиям электрохимических процессов в многокомпонентных системах.
Для исследования кинетики электродных процессов нами использован потенциодинамический метод, который позволяет определить формальный потенциал, константу скорости при этом потенциале, коэффициенты переноса и особенно удобен для анализа циклических кривых необратимого процесса в случае образования на поверхности анодного сплава прочных пленок.
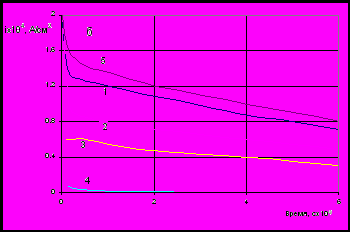
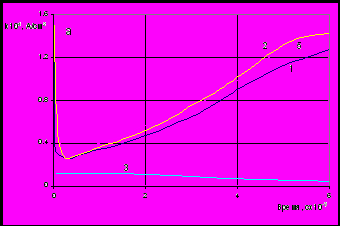
Рис. 1. Зависимость от времени внешнего тока (1), парциальных токов растворения цинка (2), меди (3) олова (4) их суммы (5) при анодном растворений (Е=-0,1 В) сплавов 12% Zn (а) и 12% Zn+5% Sn (б)
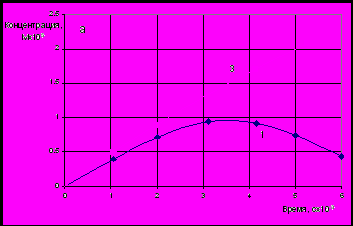
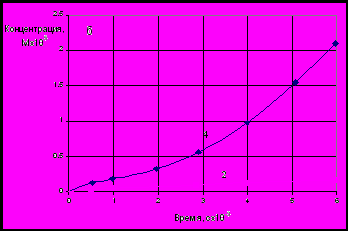
Рис. 2. Изменение во времени содержания меди (а) и цинка (б) в растворе (отнесенного к 1 см2 площади электрода) при анодном растворении сплавов 12% Zn (а) и 12% Zn+5% Sn (б)
Проведены исследования анодного поведения медных сплавов в следующих направлениях:
- поведение легирующих компонентов при анодном растворении и механизм поляризации;
- условия пассивации медных сплавов;
- характер зависимости анодной поляризации от состава сплава и электролита.
При анодной поляризации сплава образуются ионы, диффузия которых в объем раствора может являться лимитирующей стадией процесса, при этом величина потенциала определяется уравнением Нернста. Экспериментальные результаты даже для простейших систем показывают, что переход компонентов сплава в раствор не всегда описывается поляризационной кривой для чистого металла, т.е. принцип протекания независимых параллельных реакций не соблюдается.
С использованием теории абсолютных скоростей для реакций 1-го порядка предложено выражение для расчета энергии активации ионизации сложных сплавов, которое достаточно точно объясняет полученные нами зависимости:
Ea=E0-zFa-Qадс(1-), (9)
где: - степень заполнения, определяемая отношением поверхностной концентрации разряжающегося иона к его концентрации в объеме электролита; Qадс - теплота адсорбции, кДж/моль.
По нашим данным, при относительно малых a (менее 0,16 В) вторым членом в уравнении можно пренебречь (его расчетное значение составляет 3,6 кДж/моль), тогда как Qадс (1-) при <0,5 превышает 60 кДж/моль. Следовательно, с ростом и a эффективная энергия активации возрастает.
При относительно больших a (для сплава Cu-Sn около 0,5 В) возрастает роль второго члена в уравнении (9) (особенно при больших ), значение Ea резко убывает. Таким образом, при анодной поляризации медных сплавов наблюдали смещение процесса растворения из кинетической области в область смешанной кинетики, а затем в диффузионную.
Для сплавов Cu-Sn и Cu-Pb скорость ионизации не зависит от интенсивности перемешивания раствора в переходной, пассивной и транспассивной областях; скорость реакции определяется массопередачей через слой шламовой пленки, а не внешней диффузией в объеме электролита. Для исследований в областях невысоких поляризаций наиболее применим метод вращающегося дискового электрода (ВДЭ) и импульсные электрохимические методы.
В используемом варианте импульсного потенциостатического метода потенциал электрода резко смещали от равновесного значения на несколько милливольт и затем поддерживают постоянным. После установления заданного Е (10-6-10-7 с) емкость ДЭС остается постоянной, а зависимость i от определяется только изменением концентрации реагирующих веществ вблизи поверхности электрода. Если <10-3 с, то зависимость тока от времени подчиняется уравнению:
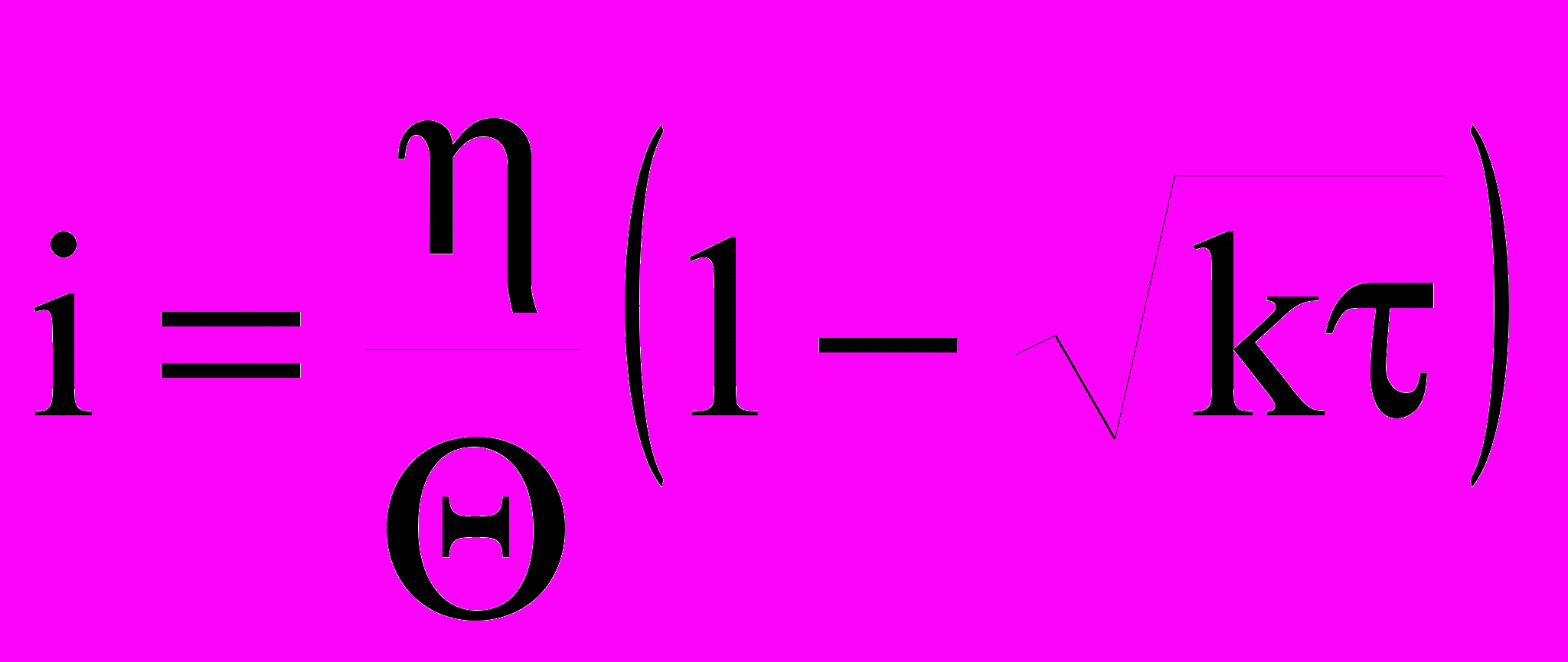
где - заданное смещение потенциала; =RT/(i0nF) - сопротивление стадии разряда-ионизации; k - коэффициент, равный:
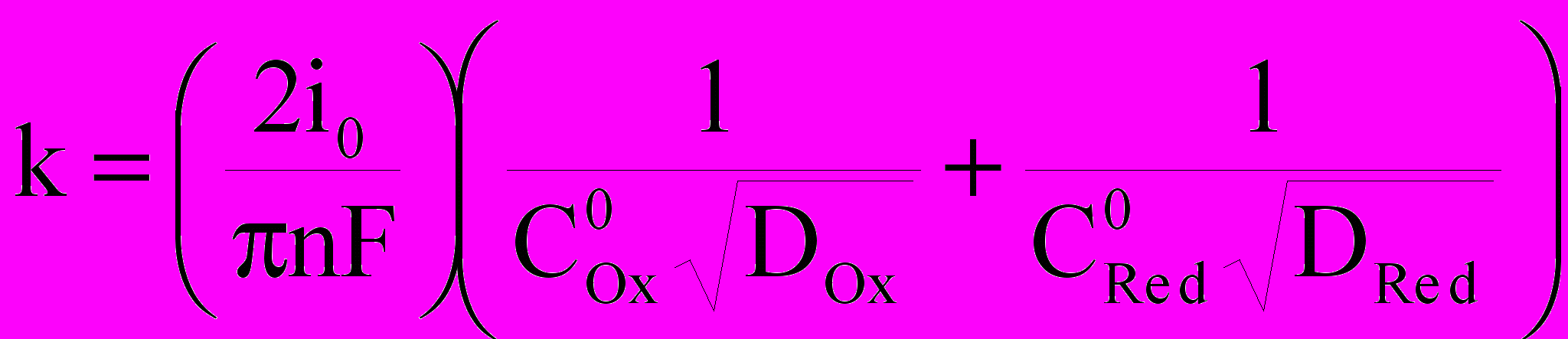
Изученные закономерности и особенности анодной ионизации сложных медных сплавов легли в основу лабораторных исследований по оптимизации технологических параметров электролиза вторичных бронз, составлению материального баланса процесса и формированию технологической схемы.
Влияние концентрации серной кислоты в электролите на показатели электролиза изучали при катодной плотности тока 200 А/м2, температуре 333 К и постоянной скорости циркуляции электролита. Эти условия приняты по результатам предварительных исследований:
- при плотности тока выше 220-250 А/м2 происходит ухудшение морфологии поверхности и качества катодной меди, расход электроэнергии увеличивается;
- при температуре меньше 333 К возрастает вероятность пассивации анода и образования в объеме раствора плавучего шлама;
- выбранная скорость циркуляции обеспечивает необходимую полноту протекания массообменных процессов без взмучивания донного шлама.
Уменьшение кислотности приводит к росту омического сопротивления электролита (рис. 3). При анодном растворении вторичных бронз в растворах с кислотностью выше 10-12 г/дм3 происходит выкрашивание анода и образование на границе раздела фаз анод - электролит порошковой меди, что подтверждает результаты теоретических исследований. Нами установлено, что в шламах от электролиза бронз в слабокислых электролитах, металлической фазы в 10-15 раз меньше, а содержание олова достигает 33-35 % (10-15% при 100-150 г/дм3 H2SO4).
Зависимость между содержанием олова и свинца в сплаве и анодным выходом по току показывает, что при низкой кислотности электролита эти металлы количественно переходят в шлам, их ионизация сопровождается реакциями сульфатизации и гидролиза. Электролиз вторичных бронз в электролитах с содержанием серной кислоты 8-12 г/дм3 позволяет полностью перевести свинец и олово в шлам и свести до минимума содержание в нем металлической меди.
П
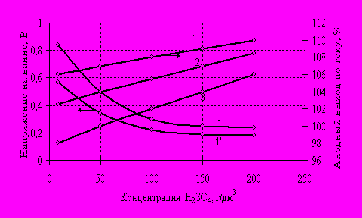
Содержание в сплаве, %: 1,1’- 12,0 Sn, 1.6 Pb,
2 – 5,0 Sn, 1,0 Pb, 3,3’ – 2,0 Sn, 0,4 Pb
Состав электролита, г/дм3: 30 Cu, 20 Zn
Рис. 3 Зависимость напряжения на ванне и анодного выхода по току от концентрации серной кислоты
ри практической реализации процесса следует учитывать сложный характер изменения солевого состава электролита. Снижение содержания меди в растворе связано со значительным различием катодного и анодного выхода по току.
Пассивационные явления на медно-свинцовых анодах сопровождаются переходом меди в шлам в виде металлического порошка при ведении процесса в сильнокислых растворах. При содержании свинца в сплаве 0,32, 4,24 и 6,15 % концентрация меди в анодном шламе составляет 0,81, 4,20 и 6,90 % соответственно. Эти данные согласуются с результатами теоретических исследований. При электролизе сплавов со значительным количеством свинца расход электроэнергии выше, чем для олово- и цинксодержащих двойных систем. Характер кривых «расход электроэнергии - состав сплава» в слабо- и сильнокислых растворах аналогичен, что указывает на определяющую роль омического сопротивления электролита.
В третьей главе приведены результаты физико-химических исследований процессов очистки растворов и разделения металлов.
Поскольку в ходе электролиза многокомпонентных анодов в электролите накапливаются ионы металлов-примесей, нами были изучены термодинамические и кинетические особенности очистки цинковых растворов от железа методом гидролитического осаждения с предварительным электрохимическим окислением, а также вывод из растворов меди и основного количества никеля методом электроцементации.
Окисление Fe(II) до Fe(III) является необходимой операцией очистки цинковых растворов, поскольку при этом рН гидролиза железа не превышает 4, что исключает соосаждение меди и, что особенно важно, цинка. Использование в качестве окислителей кислорода и озона приводит к образованию дополнительных количеств воды, что зачастую требует введения в технологическую схему энергозатратной стадии выпарки растворов. Хлор как окислитель требует значительных затрат на меры безопасности. Поэтому электрохимическое окисление Fe(II) до Fe(III) представляется наиболее перспективным методом для обработки цинковых растворов, содержащих железо.
Поскольку равновесный потенциал E0Fe(III)/Fe(II) более отрицателен, чем потенциалы выделения хлора и кислорода, окисление Fe(II) при низких потенциалах является основной реакцией, а при высоких сопровождается побочными анодными реакциями выделения газа. Газовыделение отрицательно сказывается на работе электрохимического реактора по следующим причинам:
- снижение в выходе по току;
- загрязнение электродной поверхности продуктами реакции;
- кинетические осложнения, связанные с основной реакцией.
Вместе с тем, при газовыделении хотя и увеличивается общее омическое сопротивление раствора, но выделяющийся газ способствует увеличению турбулентности, усиливая массообмен к электроду.
Изучены особенности электрохимического окисления Fe(II) на вращающемся дисковом электроде. Использовали потенциостат IPC c компьютерной системой управления, сбора и обработки данных, а также систему вращающегося дискового электрода фирмы VOLTA. Все эксперименты были проведены при 300 К и скорости развертки 2 мВ/с. Влиянием реакции окисления Fe(II) кислородом, как очень медленной для выбранного времени эксперимента, в расчетах пренебрегали.
Из наклона графиков в координатах Левича рассчитан коэффициент диффузии Fe(II), равный 4,6210-10 м2/с, значение которого не противоречит расчетным данным.
Получены зависимости предельного тока окисления Fe(II) и коэффициентов в уравнении Тафеля от концентрации железа и меди в исходном растворе, позволяющие оценить влияние этих параметров на скорость процесса. Очевидно, что присутствие меди в растворе оказывает положительное влияние на окисление железа, однако экстремальный характер зависимостей в диапазоне концентраций 0-2 г/дм3 Cu требует экспериментального подтверждения в ходе дополнительных лабораторных исследований.
Отсутствие в литературе данных о зависимости рНнач от способа его определения, а также систематических данных о поведении основных примесей (железо, медь) для сульфатных цинковых растворов, вызвало интерес к оценке рНнач и к определению его как функции концентрации и температуры в широком диапазоне изменения этих параметров, а для сопоставления - и рНнач цинка.
В первых сериях опытов использовали метод потенциометрического титрования. Одновременно с титрованием исследуемого раствора (автоматический дозатор, цифровой рН-метр И-160) 1М раствором NaOH снимали показатели по расходу щелочи и изменению рН раствора. Управление приборами, сбор и обработку данных осуществляли с помощью персонального компьютера. Специально разработанная нами программа «Титратор» позволяла в режиме реального времени преобразовывать полученные аналоговые данные в форму электронной таблицы «Exсel» и строить соответствующие парные и групповые зависимости (в том числе в дифференциальной форме).
Использовали исходные растворы ZnSO4 с концентрациями Fe3+, г/дм3: 10, 7, 5, 3 и 1 г/дм3; 100 г/дм3 Zn; 1, 2 г/дм3 Cu.
В табл. 3 приведены результаты обработки кривых потенциометрического титрования, полученных для растворов различного исходного состава. Значения рН соответствуют максимуму дифференциальной кривой, т.е. соответствуют «потенциалу полуволны» или максимальной скорости процесса образования осадка.
Таблица 3 - Показатели рН гидролитического осаждения Fe3+ при различных условиях
CFe3+, г/дм3 | 1 | 3 | 5 | 7 | 10 | 1 | 3 | 5 | 7 | 10 | 1 | 3 | 5 | 7 | 10 |
CCu2+, г/дм3 | - | - | - | - | - | 1 | 1 | 1 | 1 | 1 | 2 | 2 | 2 | 2 | 2 |
pH | 4,67 | 4,27 | 4,10 | 2,50 | 1,91 | 4,33 | 4,67 | 4,16 | 4,04 | 3,87 | 3,26 | 3,14 | 2,83 | 2,64 | 2,42 |
Очевидно, что присутствие меди в растворе оказывает положительное влияние как на рН гидратообразования в системе данного солевого состава при всех выбранных концентрациях Fe(III), так и на брутто-скорость этого процесса (наклон восходящих участков кривых в координатах «рН-расход щелочи».
В
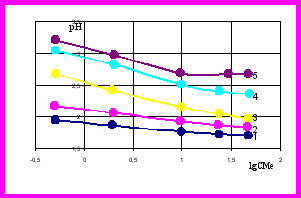
лияние фона ZnSО4 на рНнач, проверяли при одинаковых прочих условиях по СМе при 0=15 мин. Установлено, что для Сu(II) рНнач практически одинаков как в цинковых растворах, так и в растворах без цинка. Лишь при 360 К и низких ССu(~0,5 г/дм3) рНнач на фоне ZnSО4 на 0,1 ед. рН выше, чем без фона ZnSO4 (рис. 4).
Для железа рНнач в растворах с ZnSО4 и без ZnSО4 отличаются (рис. 3.30). Влияние фона ZnSО4 усиливается с понижением температуры и уменьшением СFe и проявляется в том, что в растворах с ZnSO4 рНнач выше, чем в растворах без ZnSO4 при прочих равных условиях.
Для тонкой очистки электролита после операций электроэкстракции меди и гидролитической очистки от железа (с электрохимическим окислением Fe(II)) перспективна электроцементация меди, кадмия и основного количества никеля с генерированием металла-цементатора (цинка) непосредственно из очищаемого раствора.
Процессы электроцементации электроположительных ионов в объеме раствора протекают параллельно с реакциями электроосаждения металла-цементатора и примесей.
Выше было показано, что процесс совместного электроосаждения компонентов раствора необходимо рассматривать с учетом возможности сплавообразования, что представляет собой один из частных случаев протекания параллельных электрохимических реакций, которые не всегда являются независимыми.
Рассматриваемая электрохимическая система включает в себя взаимодействие основных компонентов Zn, Cu, Ni, для которой был принят следующий подход поэтапных исследований:
- разбили систему на парциальные составляющие;
- провели исследование снятием поляризационных кривых из растворов, содержащие ионы этих металлов;
- исследовали парные взаимодействия в системе Cu-Zn, Ni-Zn;
- обобщили результаты и исследовали систему Cu-Ni-Zn.
При электрохимических исследованиях возникает проблема разделения двух процессов; одновременно протекающих на электроде в определенном интервале потенциалов. Она может быть решена при помощи вращающегося дискового электрода в том случае, когда скорость одного из процессов лимитируется диффузией и, следовательно, зависит при заданном потенциале от интенсивности перемешивания, а скорость другого процесса не зависит от гидродинамических параметров системы.
Для изучения электрохимического поведения примесей в цинковых растворах использовали описанную выше установку вращающегося дискового электрода СВА-1Б с электроприводом, цифровым датчиком числа оборотов диска, автоматическим датчиком температуры и термостатом. Вся система управлялась компьютером. Сбор данных с системы осуществлялся с помощью системы аналогового ввода-вывода PCL818L.
Состав исходного электролита, г/дм3: 100 Zn; 2 Cu; 0.2 Ni; pH исходного раствора 3-4.
Для проведения экспериментов были выбраны следующие условия:
- скорость вращения диска от 0 (стационарный электрод) до 4250 об/мин;
- температура электролита 298, 323, 348 К;
- объем исследуемого раствора 0,05 дм3;
- типы электродов: стальной или графитовый, диаметром 3 мм.
При исследовании электроосаждения с образованием многокомпонентных систем наиболее распространенным экспериментальным методом является определение и интерпретация парциальных поляризационных кривых для каждого компонента, основанные на анализе химического состава осадков, полученных при различных потенциалах и плотностях тока. Относительно простым является образование фаз, состоящих из двух металлов, на примере которых можно рассмотреть основные закономерности подобных процессов и особенности получаемых осадков.
По результатам выполненных термодинамических расчетов, равновесный потенциал ионов Zn2+ равен -781 мВ. Площадки предельного тока разряда ионов Zn2+ не наблюдается из-за совместного разряда ионов цинка и водорода. Фактический потенциал начала разряда ионов Zn2+ -784 мВ.
Поляризационные кривые разряда ионов Cu2+ (рис. 5) и Ni2+ (рис. 6) из раствора (содержащего, г/дм3: 2 Cu ,0.2 Ni) сняты на стационарном электроде при различных скоростях развертки потенциала; для сохранения ионной силы раствора добавляли 30 г/дм3 Mg2+. С 200 мВ начинается разряд ионов Cu2+ до площадки предельного тока. Идентификация площадок предельного тока разряда ионов Cu2+ представляется трудной задачей, поскольку в стационарных условиях на электроде происходит процесс роста поверхности свежеосажденной металлической фазы с одновременным уменьшением реальной плотности тока, что, в свою очередь, дает две волны на поляризационной кривой в области предельных токов разряда ионов меди.
Для скорости развертки потенциала 10 мВ/с на увеличение высоты пика оказывает влияние нестационарная диффузия. В условиях равнодоступности поверхности (ВДЭ) и постоянного гидродинамического режима явления внешней диффузии устраняются.
Достаточно высокая скорость развертки потенциала была выбрана для уменьшения воздействия химических процессов на свежеобразованную фазу осадка. Наличие площадок предельного тока при потенциалах –400 мВ отвечает нестационарной диффузии.
![]() Рис. 5 Поляризационные кривые разряда ионов Cu2+ | ![]() Рис. 6 Поляризационная кривая разряда ионов Ni2+ |
Расчетный равновесный потенциал ионов Ni2+ равен -329 мВ. С 330 мВ начинается разряд ионов Ni2+, далее до площадки предельного тока. Потенциал начала разряда ионов Ni2+ составляет –344 мВ, а начало разряда водорода происходит при потенциале -800 мВ. Роль состояния поверхности подложки и ее тип не имеют определяющего значения.
Для количественного определения доли водорода при осаждении получили поляризационную кривую, из которой видно, что при образовании новой фазы доля тока, который расходуется на образование водорода незначительна и не вносит ошибок в определение мольной доли компонента.
Зависимость предельного тока разряда ионов меди от скорости вращения ВДЭ близка к линейной, что указывает на протекание процесса в диффузионном режиме при принятых в экспериментах плотностях тока. Коэффициент диффузии
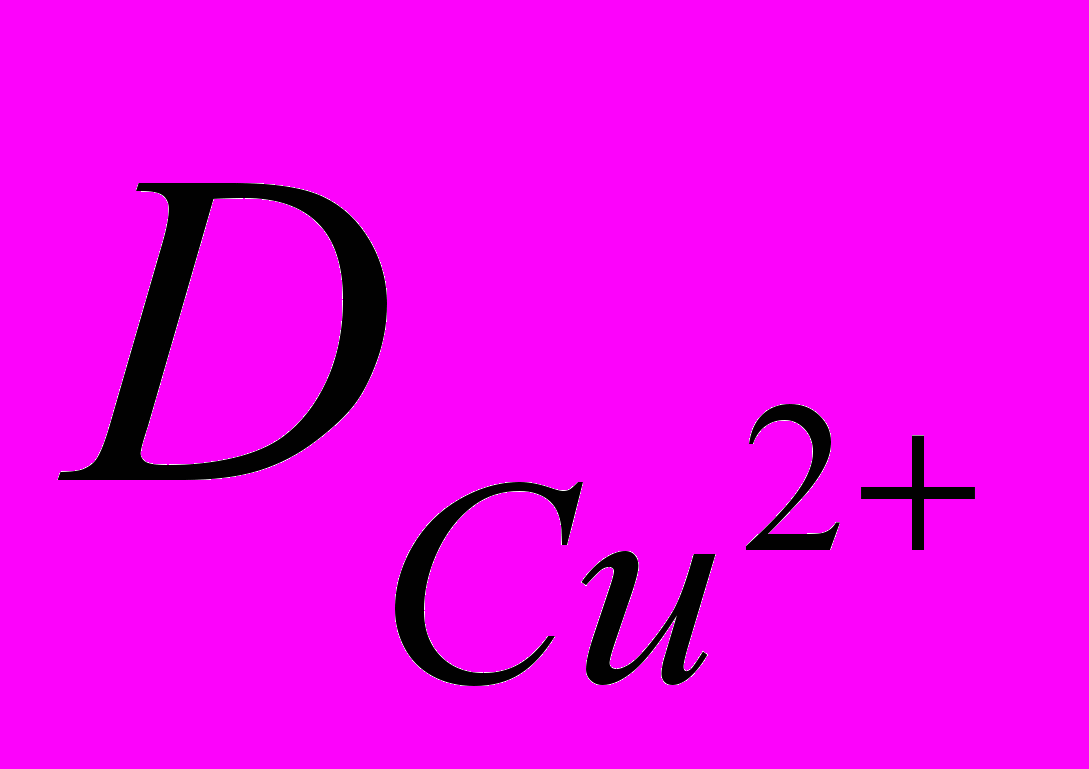
Выше было показано, что можно прогнозировать состав фазы, осаждаемой на электроде при данном потенциале. На рис. 7 представлена зависимость мольной доли более электроположительного компонента NCu в твердой фазе в зависимости от потенциала осаждения. Для системы Cu-Zn:
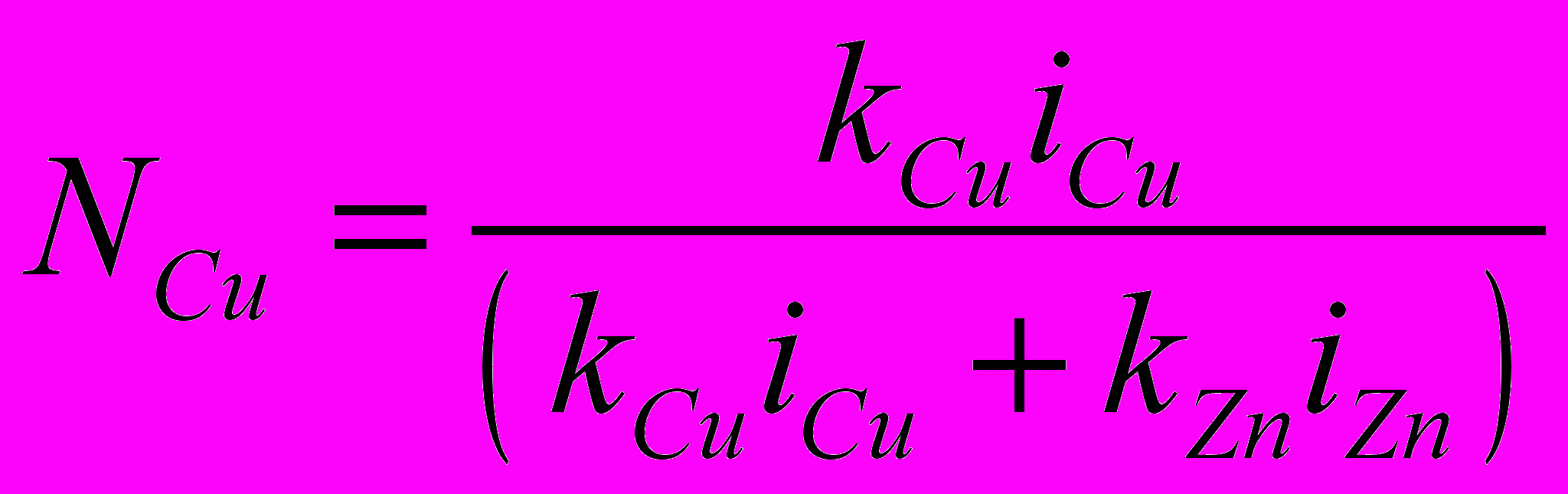
Проведенные исследования с применением ВДЭ использованы для расчета параметров электрохимических реакций: плотности тока обмена для разряда металлов и водорода, разряда водорода на подложке, коэффициентов диффузии и т.д. (методом стационарных кривых и вращающегося диска), что составило исходные данные для моделирования протекающих взаимодействий при электроцементационной очистке растворов. Смоделированные анодная и катодная поляризационные кривые, показывают возможность протекания процессов осаждения примесей, выделения водорода на примесном катоде, анодного растворения дендритов цинка (ток локального элемента). При внешней поляризации электрода -0,8 В, смещение потенциала в теле пористого электрода должно составлять ≥0,2 В.
В
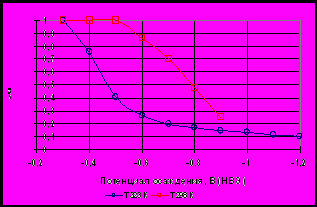
Рис. 7 Зависимость мольной доли NCu от потенциала осаждения
ыполненные расчеты и исследования приводят к следующим выводам:
- присутствие ионов Ni2+ увеличивает глубину и воздействует на скорость осаждения меди из данных растворов;
- присутствие ионов Cu2+ в растворе увеличивает скорость разряда ионов Ni2+, и по сравнению с системой Ni-Zn; содержание никеля в осадке возрастает.
Исходя из полученной модели, определили факторы, влияющие на эффективность электроцементационной очистки, выбрали диапазоны регулирования и условия исследований по очистке сульфатных цинковых растворов в лабораторном электролизере.
Для проведения лабораторных исследований электроцементационного процесса очистки модельных сульфатных цинковых растворов создана аппаратно-программная система компьютерного сбора данных лабораторного электролизера, позволяющая с высокой точностью и надежностью фиксировать параметры работы установки при изменяющихся условиях эксперимента с созданием базы данных для последующей обработки.
Условия эксперимента: состав исходного электролита поступающего на электроцементацию, г/дм3: Zn-80, Cu-1,86, Ni-0,095.
- плотность тока 250 А/м2;
- температура электролита 293К, 333К;
- объем исследуемого раствора 0,5 дм3;
- циркуляция электролита 1 дм3/ч.
За 5 часов (Рис. 8) удается снизить концентрацию меди в электролите до 0,005 г/дм3. Повышение температуры раствора отрицательно влияет на скорость извлечения меди, что связано с увеличением скорости обратного растворения как цементатора, так и осажденной примеси. Извлечение никеля из растворов достигает своего максимума 65% за 4 часа работы электролизера. Никель практически не осаждается в чистом виде, а образует фазы с цинком; далее скорости осаждения никеля и растворения вновь образовавшейся фазы, уравниваются.
Полученные (Рис. 9) зависимости приведенной концентрации меди в растворе от логарифма времени, близкие к прямолинейным, подтверждают, что процесс в начальных стадиях подчиняется уравнениям, характерным для диффузионно контролируемых процессов. Осаждение никеля имеет затруднения кинетического характера. Цементный осадок содержит, %: 80-85 меди, 2-3 никеля и 15-20 цинка.
![]() | ![]() |
Рис. 8 Изменение концентраций металлов примесей в ходе опыта: 1 – Cu 293K, 2 – Cu 333K, 3 – Ni 293K | Рис. 9 Зависимость приведенной концентрации меди и никеля от ln(t) при различных температурах: 1 – Cu 293K, 2 – Cu 333K, 3 – Ni 293K |
Для оптимизации процесса электроцементационной очистки использовали метод планирования эксперимента. Варьировали следующие факторы: C0Cu - начальное содержание меди в растворе, от 0,5-2,1 г/дм3; C0Ni - начальное содержание никеля в растворе, от 0,044-0,168 г/дм3; I - сила тока приложенная на электролизер, от 1-2 А.
Извлечение никеля во всей серии опытов колеблется от 32 до 87%. При обработке экспериментальных данных получены следующие уравнения, описывающие извлечение меди и никеля в осадок (ZMe, %):
ZCu =95,06103+C0Ni0,01138+C0Cu0,00198+I 1,70309–C0Ni·I·0,00393–
-C0Cu·I·0,00068, (12)
ZN i= 40,2341–C0Ni·0,10308+C0Cu·0,00222+I·3,09956–C0Ni·C0Cu·0,00009 –
– C0Ni·I·0,01943+C0Cu·I·0,00601+C0Ni·C0Cu·I·0,00004. (13)
Положительное влияние на извлечение меди оказывают сила тока, начальная её концентрация и концентрация никеля в растворе, что подтверждает высказанные теоретические предположения о положительном влиянии ионов никеля на предельный ток разряда ионов меди. Наибольшее положительное влияние на извлечение никеля в осадок оказывает начальная концентрация меди, а также сила тока и совместное влияние этих факторов; наибольшее отрицательное влияние оказывает начальная концентрация никеля.
Рентгенофазовый (табл. 4) и лазерный микрозондовый анализ осадка показывает наличие фаз меди, цинка, никеля и интерметаллидов. Цинк с никелем образуют интерметаллические соединения, которые нестабильны и подвержены распаду, но могут достаточно полно участвовать в процессе контактного обмена.
Таблица 4 - Результаты рентгенофазового анализа осадка
d, A | 1,277 | 1,803 | 2,008 | 2,084 | 2,111 | 2,147 | 2,673 | 2,861 | 3,721 |
Фаза | Cu | Cu8Ni | CuNi | Cu3Ni | CuZn2 | CuZn5 | Cu6ZnO8 | Zn | CuZn |
Четвертая глава посвящена результатам укрупненных и опытно-промышленных испытаний технологии комплексной переработки многокомпонентных вторичных медных сплавов.
Испытания по электролизу анодов, отлитых из вторичных медных сплавов проводили на промышленной установке гидрометаллургического цеха опытного свинцового завода института ВНИИЦветмет (г. Усть-Каменогорск).
Исходные данные:
- cостав анода, %: 84,72 Cu, 1,24 Zn, 2,07 Ni,
2,44 Sn, 5,07 Pb, 0,1 Fe;
- cостав электролита, г/дм3 32 Cu, 38 Zn, 8,7 H2SO4;
- масса анода (350×560×43 мм), кг 190
- масса катода (нерж. сталь, 870×500×3 мм), кг 10
- катодная плотность тока, А/м2 200
- температура электролита, К 333
- объем ванны, дм3 940
- количество анодов/катодов, шт 6/7
- продолжительность непрерывной работы, ч 440
Основные результаты опытно-промышленных испытаний:
- масса растворившейся части анодов, кг 525,1
- получено катодной меди, кг 460,2
- получено анодного шлама, кг 71,2
- среднее напряжение на ванне, В 1,72
- выход по току, % катодный 93,0
анодный 107,9
- состав анодного шлама, %: с анода 11,8 Cu, 1,0 Zn, 0,3 Fe,
0,5 Ni, 20,1 Sn, 32,5 Pb
c фильтра 2,1 Cu, 0,16 Zn, 1,2 Fe,
0,02 Ni, 52,0 Sn, 1,35 Pb
Полученная катодная медь имела плотную кристаллическую структуру и по химическому составу соответствовала марке М1. Заметного изменения состава электролита по содержанию меди и серной кислоты в ходе испытаний не отмечено.
При разработке методики проведения опытно-промышленных испытаний очистки цинковых растворов (отработанного электролита электрорафинирования вторичных медных сплавов) на ЗАО «Технический центр С» (г. Кировград) исходили из того, что электролизер непрерывного действия (рис. 10) должен быть встроен в существующую периодическую схему действующего производства.
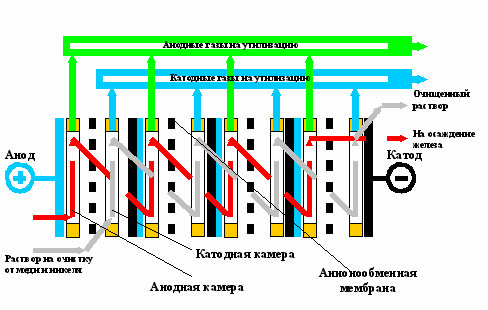
Рис. 10 Принципиальная схема биполярного электролизера
Растворы после электролизера направляли в основную технологическую схему: из анодной камеры – на гидролитическую очистку, из катодной камеры – на операцию контрольной цементации примесей. За основу конструкции приняли проточный электролизер с биполярными электродами.
Испытания проводили на производственных растворах с содержанием, г/дм3: 130-160 Zn, 0,04-0,8 Fe, 2,7-5 Cl, 1-1,8 Cu; pH 0,6-2,1. Силу тока изменяли в пределах 70-90 А.
В процессе испытаний была опробована возможность осуществления непрерывной работы электролизера в течение длительного времени. Испытания проводились на скоростях подачи раствора в электролизер от 8 до 14 дм3/мин, что было обусловлено необходимостью обеспечить вынос частиц, образующихся на катоде.
Процесс окисления двухвалентного железа наблюдали при полупромышленных испытаниях электролизера с разделением катодного и анодного пространств анионообменной мембраной. Во всех сериях опытов достигнуто допустимое остаточное содержание железа (50 мг/дм3). Эмпирические зависимости, полученные при полупромышленных испытаниях, позволяют автоматизировать процесс на базе микропроцессорной техники.
Общий годовой экономический эффект при объеме выпуска 100 тонн цинка в цинковом купоросе в месяц в ценах 2007 г. составит 8000 тыс. рублей. Срок окупаемости капиталовложений 0,5 года.
Испытания технологии электроцементационной очистки сульфатных цинковых растворов проводили в том же электролизере на базе цеха по производству сульфата цинка ЗАО «Технический центр С». Состав промышленного раствора, г/дм3: 135-140 Zn, 1,4 Cu, 0,25 Ni. Исходный pH 4,1-4,3.
Технологический процесс обеспечивает очистку растворов от меди до концентрации 0,01 г/дм3 (извлечение 99,28%). Концентрация цинка на выходе из аппарата после 7 часового пускового периода не изменяется. При интенсивной газовой флотации осадок свободно перемещается из камеры в камеру и не образует пробок в патрубках.
Концентрация никеля в очищенном растворе составляет 0,19 г/дм3. Нестабильность извлечения никеля связана с высокой скоростью обратного растворения никеля или фазы Zn-Ni внутри камер электролизера.
Работу десятикамерного опытно-промышленного электролизера можно представить следующей схемой:
- в 1-3 камерах преобладает процесс электрохимического осаждения;
- во 2-5 камерах преобладает процесс контактного вытеснения;
- в камерах 6-10 протекает глубокая очистка раствора от меди; образуется избыточное количество цинка, который предотвращает обратное растворение цементного осадка.
Цементные осадки характеризуются более высоким содержанием меди по сравнению с осадками, полученными по классической цементационной схеме, и пригодны для дальнейшей переработки.
Серию опытно-промышленных испытаний провели по методике планирования эксперимента. Контролируемые параметры: концентрация меди, цинка, pH раствора на выходе из аппарата; содержание меди, цинка свинца, железа, никеля в цементном осадке; температура на входе и выходе электролизера; напряжение на электролизере и плотности тока, дополнительный контроль состава раствора по камерам.
Результаты испытаний представлены обобщены на рис. 11,12. Обозначения: CCu0 начальное содержание меди в растворе г/дм3; Is-плотность тока А/м2; IzCu-извлечение меди в осадок, %; CCu-содержание меди в осадке %, CZn- содержание цинка в осадке %.
Разработанный процесс при внедрении его в производственную практику, позволяет получить экономический эффект в размере 1,15 млн. руб. Экономический эффект образуется за счет сокращения расхода цинкового порошка на операцию цементации, до 95 % от исходного.
В главе 5 приведено описание разработанной технологической схемы переработки низкокачественных вторичных медных сплавов.
Приведенные выше результаты лабораторных исследований и укрупненных испытаний позволили сформулировать основы технологической схемы комплексной переработки низкосортного вторичного медного сырья (рис. 13). Можно выделить ее следующие основные блоки (подробно условия проведения операций приведены в предыдущих главах):
![]() | ![]() |
Рис. 11 Поверхность отклика для факторов, влияющих на извлечение меди из раствора | Рис. 12 Поверхность отклика для факторов, влияющих на содержание меди в цементном осадке |