Учебно-методический комплекс Павлодар Министерство образования и науки Республики Казахстан Павлодарский государственный университет им. С. Торайгырова Факультет металлургии, машиностроения и транспорта
Вид материала | Учебно-методический комплекс |
- Учебно-методический комплекс Павлодар Министерство образования и науки Республики Казахстан, 850.57kb.
- Тесты Павлодар Министерство образования и науки Республики Казахстан Павлодарский государственный, 1034.55kb.
- Министерство образования и науки Республики Казахстан Павлодарский государственный, 2226.3kb.
- Методические указания Министерство образования и науки Республики Казахстан Павлодарский, 118.15kb.
- Программа дисциплины для студентов Министерство образования и науки Республики Казахстан, 245.4kb.
- Программа дисциплины Форма для студентов ф со пгу 18. 2/07 Министерство образования, 272.92kb.
- Павлодарский государственный университет им. С. Торайгырова, 537.91kb.
- Учебное пособие Павлодар удк 622 012 (07) ббк 30. 3я7, 2078.83kb.
- Торайгырова Факультет Металлургии, машиностроения и транспорта Кафедра Транспортной, 488.16kb.
- Итоговый отчет об использовании Гранта Содержание отчет о выполненной работе в соответствии, 202.14kb.
7.3 Практическое занятие 3. Выбор схем механизации переработки ТШГ на прирельсовых складах
Цель занятия – научить выбирать схемы механизмов переработки ТШГ на прирельсовых складах
7.3.1 Общие сведения
Определяем длину склада НСК для 200 крупнотоннажных (20 т) контейнеров, расположенных в пролёте козлового крана КК-20 при устройстве железнодорожных путей в пролёте крана и использовании пространства под консолями крана для проезда автомобилей.
7.3.2 Порядок выполнения работы
7.3.3 Составим схему расположения железнодорожного пути и ряда контейнеров на элементарной площадке в пролёте крана с учётом необходимых зазоров и технологических проходов.
7.3.4 Вместительность элементарной площадки V при расположении поперечных проходов шириной 1 м через 5 рядов по длине составит 30 контейнеров. Длина элементарной площадки определяется:
l = 5·lK+1
где lK – длина контейнера, м; lK =6,058;
1 – учёт зазоров между контейнерами.
7.3.5 Длина склада определяется по формуле
hCK = l + lT,
где lT – длина свободной зоны для производства ремонтных работ, а также размещения контейнеров, отнесённых в разряд технического и коммерческого брака и хранения запасных частей, сменных грузозахватных органов – 25 м.
пПЛ – число элементарных площадок на складе
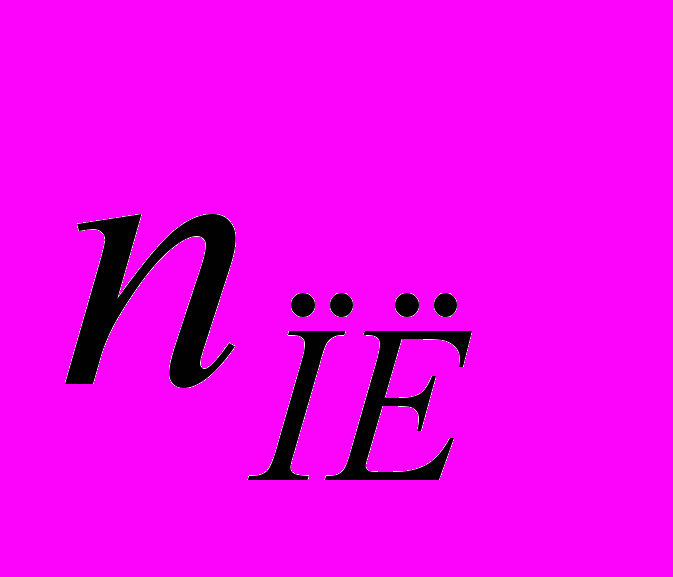
7.4 Практическое занятие 4. Проектирование схем механизации погрузочно-разгрузочных работ
Цель занятия – научить проектировать схемы механизации ПРР
7.4.1 Общие сведения
Процесс проектирования схем механизации погрузочно-разгрузочных работ – это расчёт параметров взаимодействия груза заданных средств его транспортирования с характеристиками выбранного перегрузочного и вспомогательного оборудования и складов. В общем виде требования к схемам определяют тем же перечнем, что и требования к погрузочно-разгрузочному оборудованию, которая в ряду составляющих элементов процесса груз – подвижной состав, погрузочное устройство. Склад рассматривается как наиболее активная часть, от которой зависит эффективность всего технического процесса.
Схема механизации является основным применяемым на практике видом моделей технического процесса. Её разработка сопровождается расчётами, связанными с использованием других принципов моделирования: математического, графического, ленточных и др. Основной целью при этом является поиск размеров и перерабатывающей способности грузовых фронтов с учётом характеристик имеющегося или выделяемого оборудования и при условии задания параметров грузопотока (рода груза, способа транспортирования, так и условий обеспечения производства работ всеми необходимыми видами обслуживания).
Задание:
1) спроектировать схему механизации погрузочно-разгрузочных работ насыпных грузов;
2) спроектировать схему механизации погрузочно-разгрузочных работ наливных грузов;
3) спроектировать схему механизации погрузочно-разгрузочных работ тарно-штучных грузов.
7.5 Практическое занятие 5. Определение основных параметров крытых складов
Цель занятия – научить определять основные параметры крытых складов
7.5.1 Общие сведения
При проектировании или выборе типовых проектов склада необходимо определить его основные параметры: вместимость, потребную площадь, длину, ширину, высоту, размеры погрузочно-разгрузочных фронтов.
Параметры склада определяют исходя из объёма грузопереработки склада и режима работы грузового двора.
Режим работы грузового двора может быть детерминированным (достоверным) или случайным (недетерминированным).
Таблица 7.5– Исходные данные
Род груза | Грузовые устройства | Продолжительность хранения, сут | Средняя нагрузка на пол склада, т/м2 | Коэффициент, учитывающий дополнительную площадь | |
до отправления | по прибытии | ||||
Тарные и штучные грузы: -повагонные отправки - мелкие отправки -в контейнерах | Крытые склады и платформы То же Площадки | 1,5 2,0 1,0 | 2,0 2,5 2,0 | 0,85 0,4 0,5 | 1,7 2,0 1,9 |
Тяжеловесные грузы | - | 1,0 | 2,5 | 0,9 | 1,6 |
Колёсные грузы и сельхозтехника | - | 1,0 | 2,5 | - | - |
Грузы, перевозимые навалом | - | 2,5 | 3,0 | 1,1 | 1,5 |
Лесоматериалы | - | 2,5 | 3,0 | 0,5 | 1,6 |
Цемент, известь, алебастр мел | Склады | - | 2,5 | 1 | 1,5 |
Минеральные удобрения | Склады | - | 2,5 | 1,1 | 1,5 |
Промышленные товары широкого потребления (трикотаж, обувь, одежда) | Специализированные крытые склады | 1,5 | 2,0 | 0,25 | 1,7 |
Мебель | То же | 1,5 | 2,0 | 0,25 | 1,7 |
Бумага | » | 1,5 | 2,0 | 1,1 | 1,7 |
7.5.2 Вместимость склада
ЕСК= QС*ТХР*КСК;
где QС – среднесуточный объём грузопереработки, т;
КСК – коэффициент складочности, учитывающий перегрузку из одного транспортного средства в другое, 0,8;
ТХР – продолжительность хранения груза на складе, сут, выбрать из таблицы 1.
7.5.3 Потребная площадь склада, м2
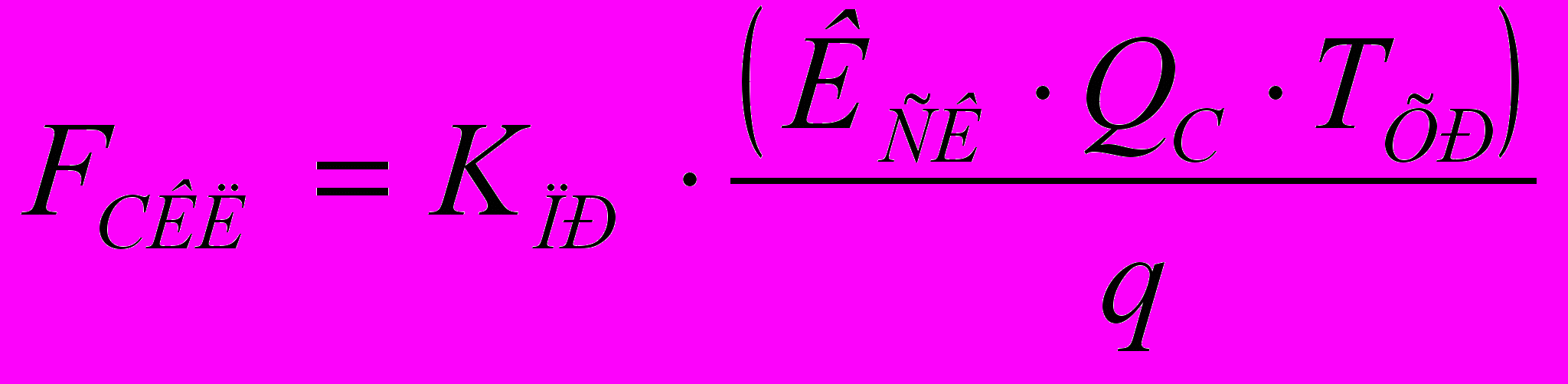
где КПР – коэффициент, учитывающий дополнительную площадь для проходов, проездов и др.(таблица 1);
q – средняя нагрузка на пол склада, т/м2 (табл.1).
7.5.4 Длина склада
LСКЛ=FСКЛ/BСКЛ
где BСКЛ – типовая ширина склада, м.
Длина склада не должна превышать 300м. По типовым проектам принимают 72 м, 144 м, 216 м, 288 м.
7.5.5 Длина фронта подачи вагонов
LФП=(пВ1В/Zn)+ам,
где пВ – среднесуточное число вагонов, поступающих на грузовой фронт;
1В – длина вагона, м;
пВ= QС/ qВ
где qВ – средняя загрузка вагонов, т;
ам – удаление грузового фронта, необходимое для манёвров (15-25 м);
Zn – число подач.
LСКЛ LФП
7.5.6 Длина фронта погрузки и выгрузки
а) для вагонов
LВ=( пВ1В)/(Zn ZС)
где ZС – число смен (перестановок).
б) для автомобилей
LА= (QСLФ tА)/( qАТ)
где LФ – фронт, требующийся для одного автомобиля в зависимости от способа его постановки (вдоль склада, перпендикулярно, под углом);
tА – средняя продолжительность операции под одним автомобилем, ч;
qА – средняя загрузка одного автомобиля, т;
Т – продолжительность работы грузового двора, ч.
Длина фронта для одного автомобиля
- при установке машин вдоль склада
LФ=1А+С
- при установке машин перпендикулярно складу
LФ=bА+С
где 1А – длина автомобиля без прицепа(4,2 – 4,4 м);
С – расстояние между машинами(4,2 – 4,4 м)
bА – ширина автомобиля(2,0 – 2,6 м);
С – расстояние между машинами(1,5 м).
Условие: длина склада должна быть больше или равна длине погрузочно-разгрузочного фронта, и кратна 12м, для открытых платформ – 3м.
LСКЛ LФП; LСКЛ LА.
7.6 Практическое занятие 6. Определение размеров вместимости контейнерных площадок
Цель занятия – научить определять размеры вместимости контейнерных площадок.
7.6.1 Общие сведения
На грузовых ж.д. станциях для переработки контейнеров (погрузки, выгрузки, сортировки, кратковременного хранения, текущего осмотра и ремонта, а также оформления документов) созданы контейнерные пункты. На них находятся складские площадки, подъездные ж.д. пути и автомобильные дороги, подъемно-транспортные средства, мастерские, служебные и бытовые помещения. По назначению контейнерные пункты делятся на:
- грузовые
- грузосортировочные;
- сортировочные.
Каждая контейнерная площадка делится на секторы контейнеро-мест. Контейнеро-место предназначено для хранения одного контейнера массой брутто 3 тонны. Контейнер массой брутто 5 тонн занимает два контейнер-места.
Сектором называют два ряда контейнеро-мест, расположенных поперек площадки. Секторам присваивают порядковые номера и объединяют их в специализированные участки
Покрытие площадок может быть асфальтовым, наиболее эффективно асфальтобетонное. Продольный уклон допускается не мене 0,4‰ и не более 6‰.
Таблица 7.6 – Исходные данные
Варианта | Тип крана | Q, т | Пролёт, м | QГВ, тыс.т | QГО, тыс.т | qК | KВН=KoH | О | В | ПК | Груз. конт., т | F |
1 | КД-05 | 5 | 11,3 | 120 | 120 | 1,8 | 1,2 | 0,9 | 0,85 | 24 | 3 | 10 |
2 | КК-6 | 6 | 16 | 130 | 130 | 1,8 | 1,3 | 0,9 | 0,85 | 36 | 3 | 15 |
3 | ККС-10 | 10 | 20 | 140 | 140 | 1,8 | 1,4 | 0,9 | 0,85 | 40 | 3 | 20 |
4 | ККДК-10 | 10 | 24 | 150 | 150 | 1,8 | 1,5 | 0,9 | 0,85 | 45 | 3 | 25 |
7.6.2 Порядок выполнения работы
7.6.3 Среднесуточная погрузка и выгрузка
ПВ=
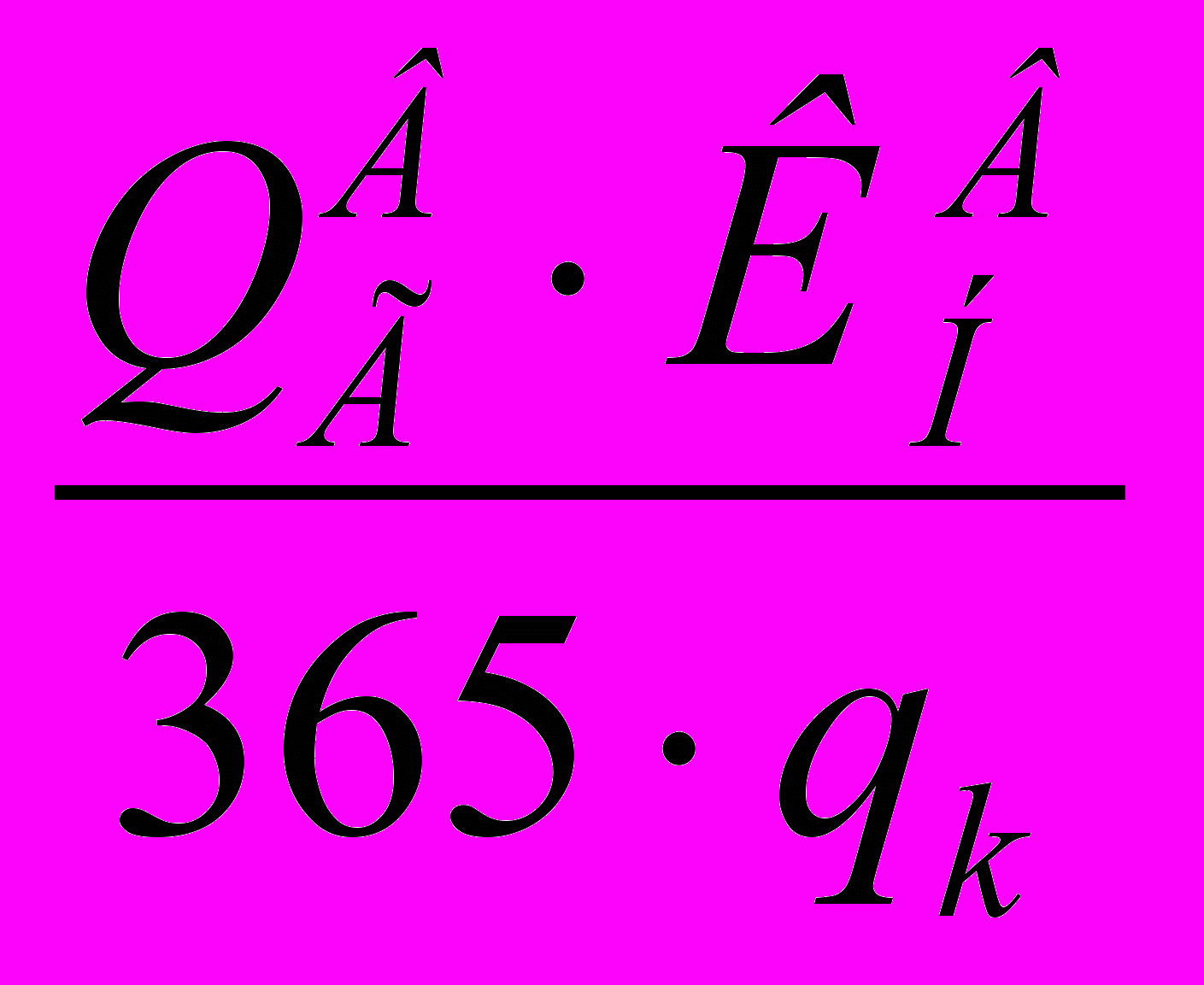
где ПВ ,ПП – годовой объём поступления и отправления груза в контейнерах, т/см;
QГВ, QГО – коэффициент неравномерности поступления и отправления;
KВН, KОН – масса груза нетто в контейнере.
Число платформ для отправления контейнеров в течение суток
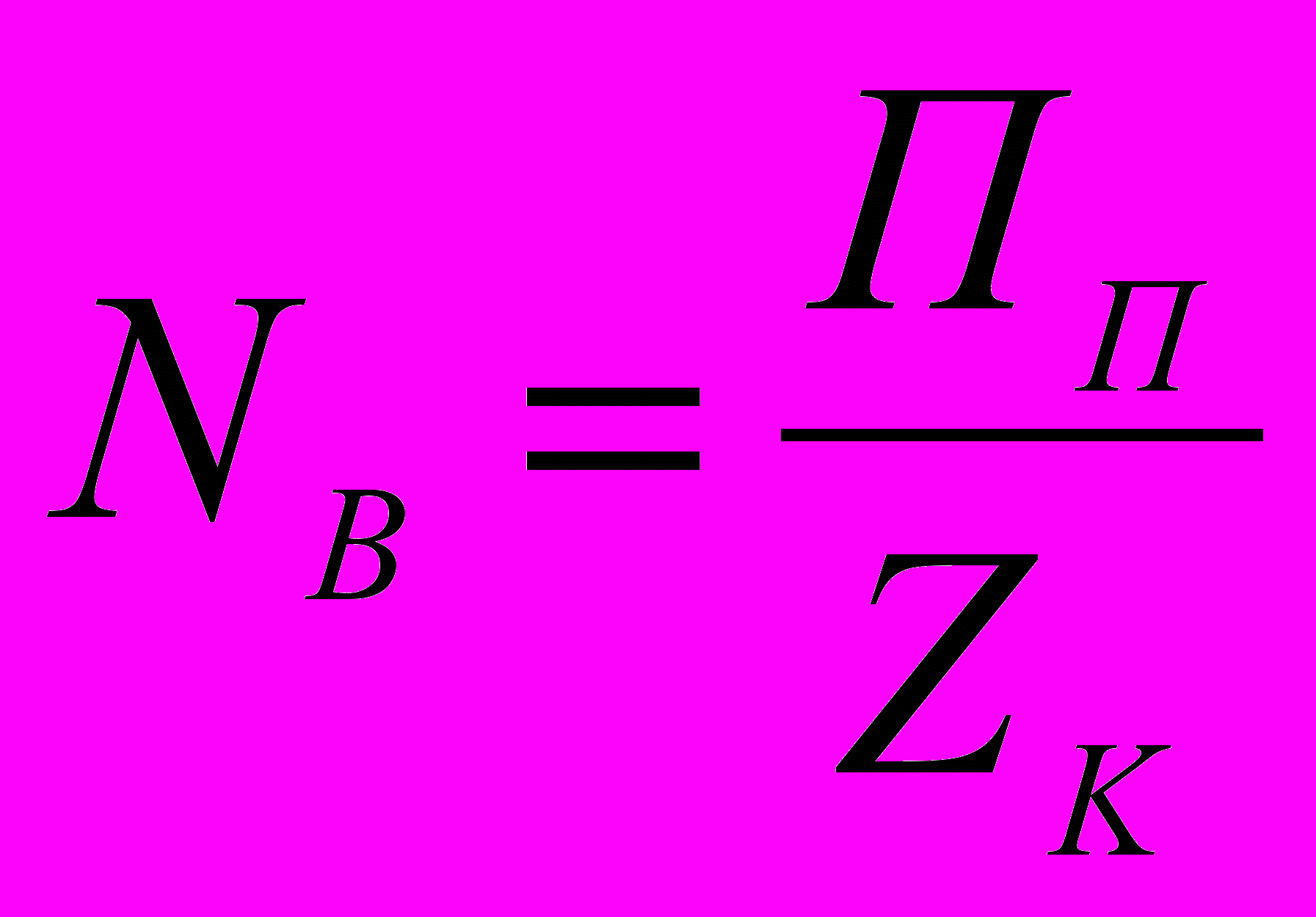
где ZК – число контейнеров на каждой платформе.
Вместимость контейнерной площадки, контейнеро-мест
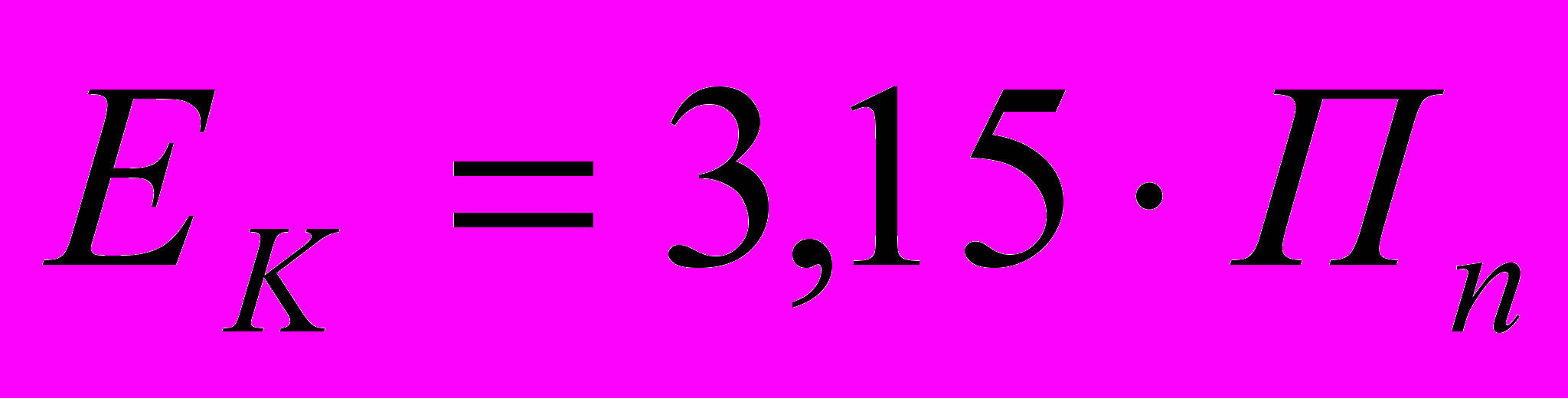
7.6.4 Ширину контейнерной площадки определяют исходя из пролёта крана

где 1,4 –габарит приближения контейнера к оси подкранового пути, м.
Длина контейнерной площадки
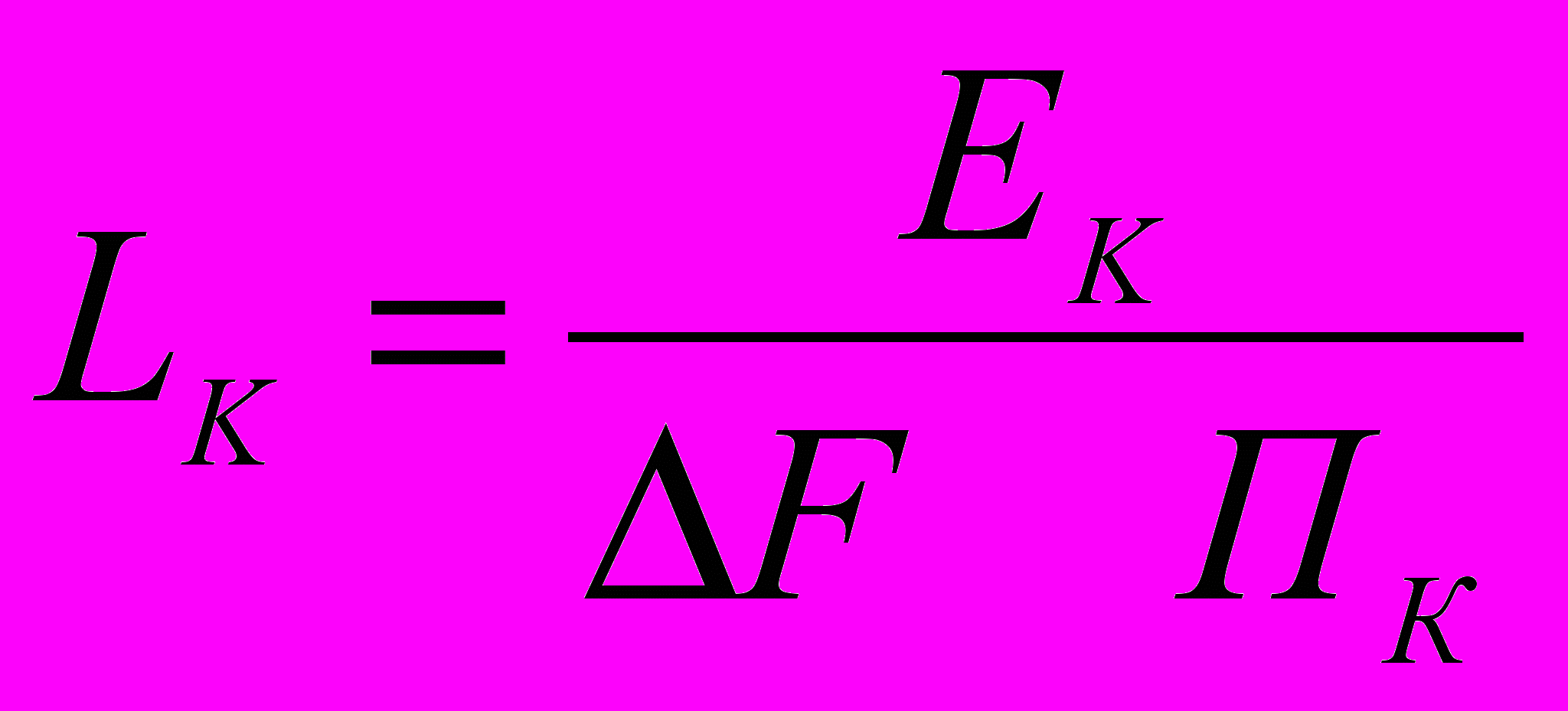
где ПК – количество контейнеров на элементарной площадке;
F – длина элементарной площадки.
7.7 Практическое занятие 7. Определение параметров бункера
Цель занятия – научить определять пропускную способность (или производительность) бункера.
7.7.1 Общие сведения
Проектирование емкостей бункерно-силосного типа состоит в определении их геометрических размеров, отвечающих ряду условий.
Этими условиями являются:
- соответствие геометрической вместимости бункера требуемому объему размещаемого груза;
- отсутствие торможения частиц груза на наклонных стенках бункера;
- беспрепятственный выпуск груза через разгрузочное отверстие (отсутствие сводообразования над разгрузочным отверстием);
- обеспечение требуемой производительности по выдаче груза из бункера.
Основные геометрические параметры бункеров приведены на рисунке 7.
Вместимость прямоугольного бункера Vб, состоящего из верхней части в форме параллелепипеда и нижней части в виде усеченной пирамиды, определяется по формуле

где А, В – размеры выпускного отверстия бункера, м.
Объем бункера цилиндрической формы, состоящего из цилиндра в верхней части и усеченного конуса в нижней, находим по следующей формуле

где R1 – радиус цилиндрической части емкости, м;
R2 – радиус выпускного отверстия, м.
Геометрические размеры бункера принимаются конструктивно, исходя из места его расположения на складе и выполняемых функций.
Углы наклона боковых стенок бункера αс, αс1 и ребра αр должны
быть проверены на отсутствие торможения груза
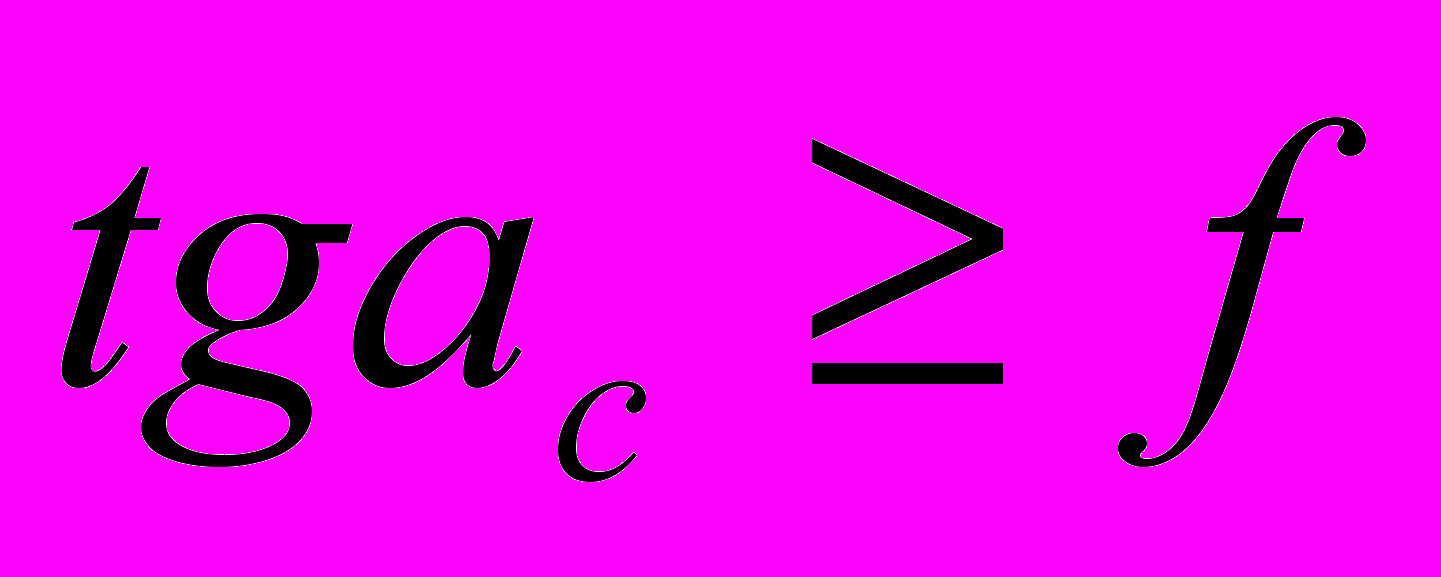
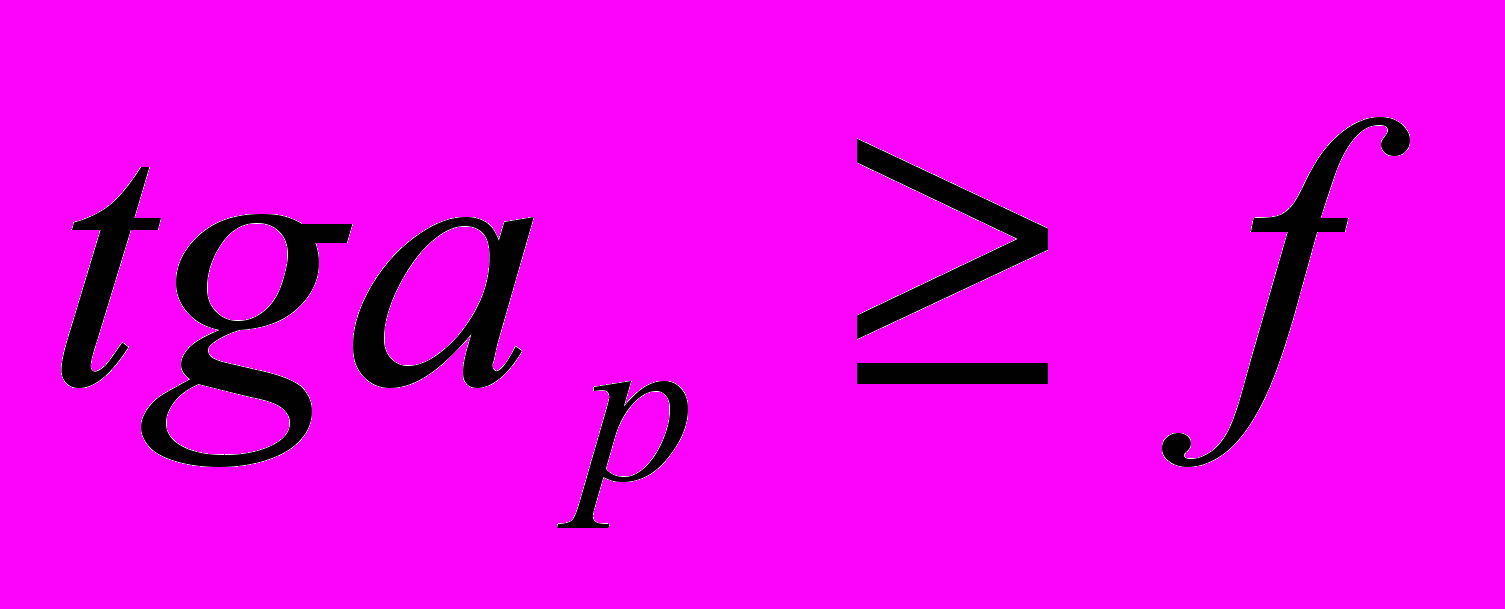
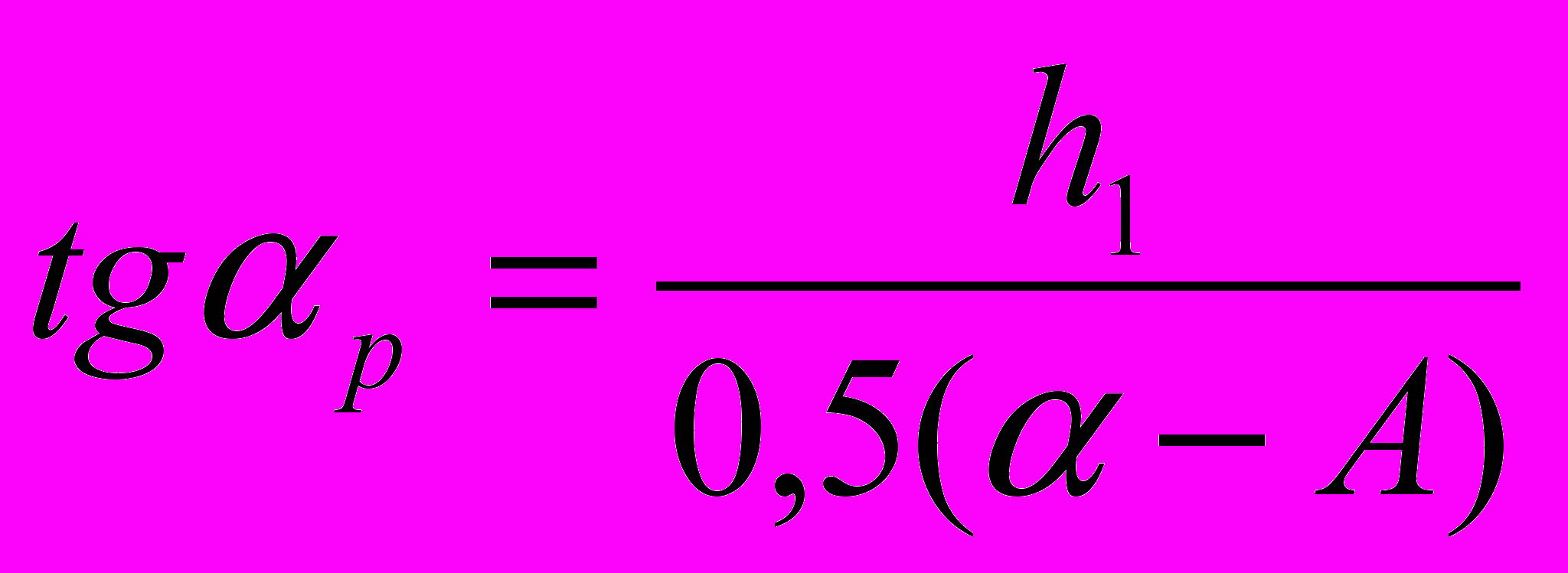
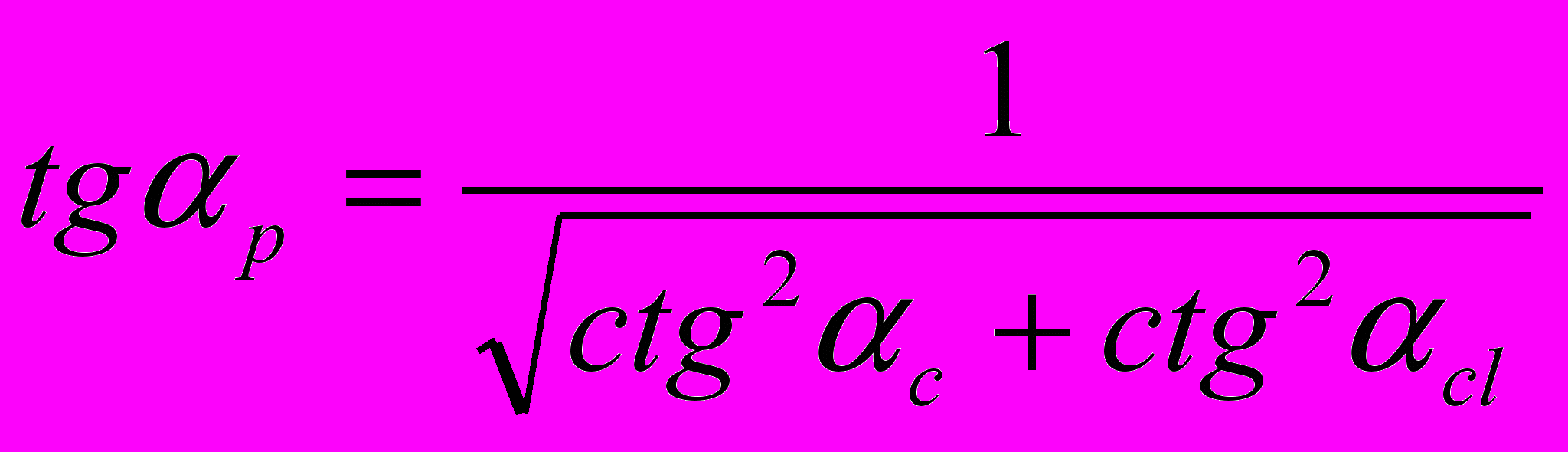
где ƒ – коэффициент трения груза по стенкам бункера; при движении груза по металлической поверхности рекомендуется принимать: для угля, щебня, гравия, глины, земли ƒ=0,75...0,80; для мела, цемента, муки, зерна, земли ƒ=0,60...0,75; при движении грузов
по бетонным стенкам бункеров указанные величины коэффициентов трения следует увеличивать на 15...20 % .
Размеры выпускного отверстия бункера А и В должны быть достаточными для обеспечения требуемой пропускной способности (производительности). Вместе с тем они должны исключать сводообразование (зависание) груза в бункере. Во избежание опасности резкого обрушения больших масс груза через отверстия, а также утяжеления затворов выпускные отверстия не должны быть излишне большими.
Для кусковых сыпучих грузов с типичной крупностью кусков αгр наименьший размер выпускного отверстия бункера прямоугольной
формы составит
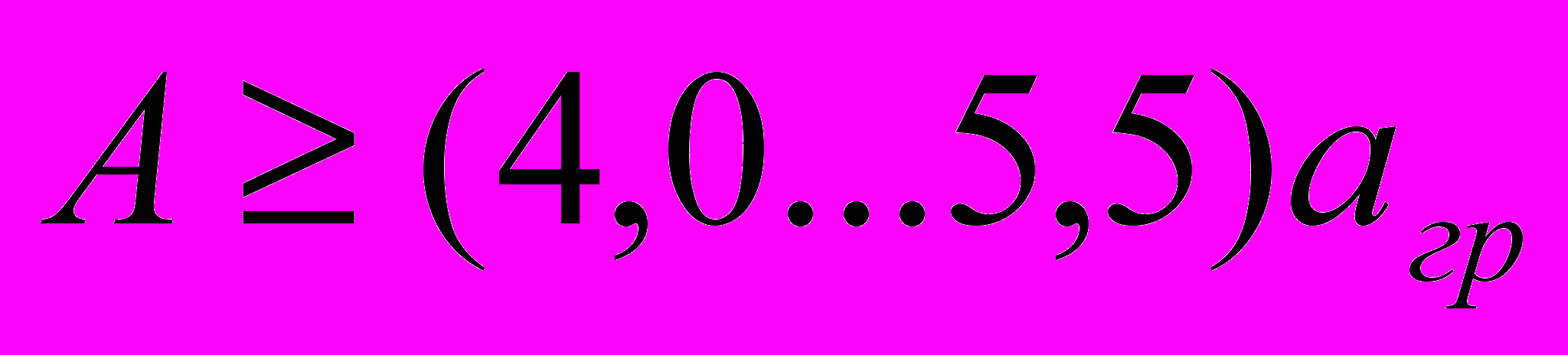
Для мелкокусковых и порошкообразных грузов размеры выпускных отверстий принимают в зависимости от пропускной способности (производительности) бункера, но не менее 300...400 мм (обычно 500...600 мм).
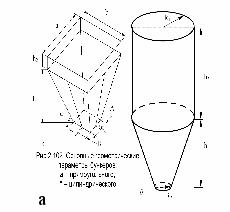
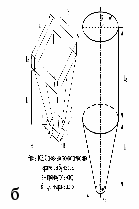
а

Рисунок 7 – Основные геометрические параметры бункеров
Одним из наиболее важных параметров бункеров является пропускная способность (или производительность), которую можно рассчитать по формуле

где υист – скорость истечения сыпучего груза из выпускного отверстия бункера, м/с;
γ – объемная плотность груза, т/м3;
wp – расчетная площадь выпускного отверстия бункера, м2;
- для прямоугольного отверстия

- для круглого отверстия

Скорость истечения сыпучего груза из выпускного отверстия бункера определяется по эмпирической зависимости, м/с

где λ – коэффициент истечения; для сухих, хорошосыпучих грузов λ =0,6; для кусковых материалов λ=0,4; для пылевидных и порошкообразных λ=0,22;
g – ускорение свободного падения, м/с2;
Rг – гидравлический радиус, м, определяемый по формуле
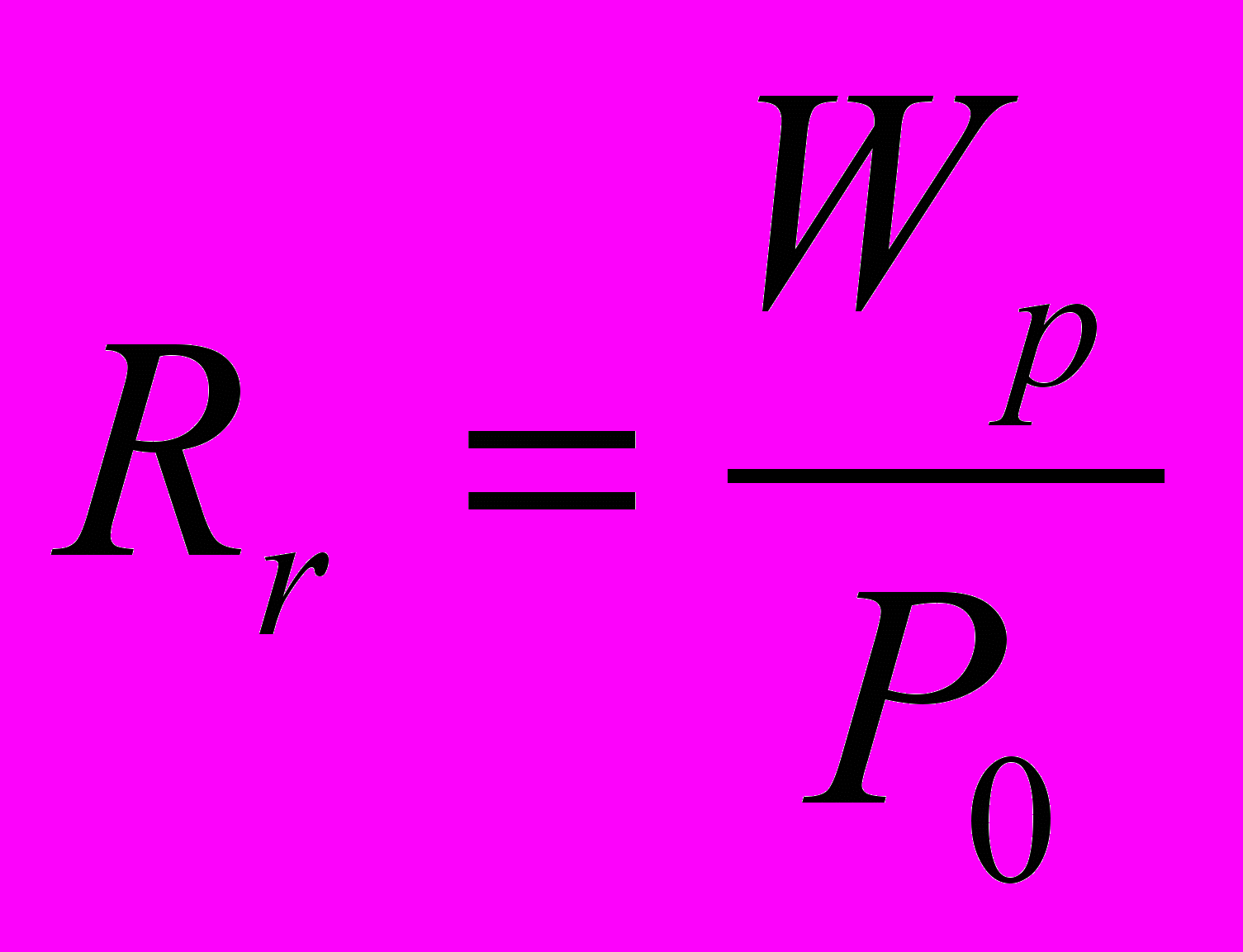
где Р0 - периметр выпускного отверстия бункера, м;

8 Материалы для самостоятельной работы студентов
8.1 Задания на самостоятельное изучение дисциплины
Тема 1. Организация погрузочно-разгрузочных работ на транспорте
Механизированная дистанция погрузочно-разгрузочных работ, их назначение и задачи. Типовой технологический процесс работы механизированной дистанции погрузочно-разгрузочных работ и его содержание
Рекомендуемая литература: [12].
Тема 2. Классификация и основные технико-эксплуатационные показатели погрузочно-разгрузочных машин и средств автоматизации
Определение эксплуатационной производительности машин и устройств. Производственные нормы, их роль и значение в организации выполнения грузовых работ. Порядок разработки и установление производственных норм.
Рекомендуемая литература: [3, с. 156-157]; [5, с. 29-36].
Тема 3. Машины и устройства непрерывного действия
Трубопроводный капсульный и пневмоконтейнерный транспорт и область применения. Основы теории пневматического транспортирования: схемы, общее устройство и организация работы, технико-экономические показатели, определение производительности и мощности привода.
Рекомендуемая литература: [12, с. 133-146].
Тема 4. Машины и устройства периодического действия
Определение производительности и мощности привода кранов. Основные виды экскаваторов и их применение на погрузочно-разгрузочных работах.
Электро- и автопогрузчики. Механические и автоматические лопаты. Скреперные установки.
Рекомендуемая литература: [12, с. 42-59].
Тема 5 . Машины и оборудование специального назначения
Механические и автоматические откатки, их устройство и область применения. Подвесные дороги с жестким рельсом. Подвесные канатные дороги, схема устройства, основные размеры и область применения. Технико-экономические показатели.
Рекомендуемая литература: [12, с. 159-175].
Тема 6. Основы проектирования комплексной механизации и автоматизации погрузочно-разгрузочных работ и складских операций
Единая модульная система при проектировании и сооружении складов. Технические условия и эксплуатационные требования к сооружениям механизированных цехов, складов в связи с комплексной механизацией погрузочно-разгрузочных работ.
Определение фронтов погрузочно-разгрузочных работ, вместимости и размеров грузовых цехов, сооружений и складских устройств.
Рекомендуемая литература: [3, с. 161-167].
Тема 7. Технология и механизация погрузки и выгрузки тарно-штучных грузов
Технико-экономические показатели вариантов комплексной механизации и автоматизации погрузочно-разгрузочных работ со штучными грузами.
Рекомендуемая литература: [1, с. 35-42].
Тема 8. Технология и механизация погрузочно-разгрузочных работ с грузами, перевозимыми в контейнерах
Технология и механизация загрузки в контейнеры и выгрузки грузов из контейнеров. Типы автоконтейнеровозов и область их применения. Передовые методы организации работы контейнерных пунктов и терминалов.
Определение вместительности и размеров контейнерных пунктов и количества машин для переработки контейнеров.
Рекомендуемая литература: [1, с. 47-68].
Тема 9. Технология и механизация погрузки и выгрузки тяжеловесных длинномерных грузов
Типы грузозахватных приспособлений для перегрузки тяжеловесных грузов. Техника безопасности при производстве работ. Технико-экономические показатели различных среде механизации и автоматизации при перегрузке тяжеловесных грузов.
Рекомендуемая литература: [1, с. 74-82].
Тема 10. Технология и механизация погрузки и выгрузки лесных грузов
Специальные агрегаты и машины для пакетной погрузки и выгрузки лесных грузов. Прогрессивная технология, передовые методы организации работы складов.
Рекомендуемая литература: [1, с. 153-161].
Тема 11. Технология и механизация погрузки и выгрузки сыпучих и кусковых грузов
Средства восстановления сыпучести и механизации выгрузки смерзающихся и слеживающихся навалочных грузов и очистка подвижного состава (тепляки, генераторы инфракрасного излучения, бурорыхлительные установки, виброрыхлители, установки ударного действия, вибро- и щеточные машины для очистки вагонов и др.
Рекомендуемая литература: [1, с. 97-120].
Тема 12. Технология и механизация погрузки и выгрузки зерновых грузов и овощей
Передовые методы комплексной механизации погрузки-выгрузки в случае отсутствия элеваторов и механизированных складов зерна на железнодорожных станциях.
Склады и комплексная механизация погрузочно-разгрузочных работ при перевозках овощей, картофеля, свеклы и др.
Рекомендуемая литература: [1, с. 126-138].
Тема 13. Склады и комплексно-механизированный налив и слив жидких грузов
Типы насосов и устройств, применяемых для перекачки кислот. Определение времени налива и слива. Автоматические устройства контроля заполнения цистерны.
Устройства для подогрева и слива сгущающихся жидких продуктов. Техника личной и противопожарной безопасности при производстве работ с наливными грузами.
Рекомендуемая литература: [1, с. 175-186].
Тема 14. Технология и механизация погрузки и выгрузки грузов в пунктах перевалки
Перевалка грузов с железной дороги на воду и обратно в речных и морских портах.
Рекомендуемая литература: [8].
8.2 Методические рекомендации и указания к выполнению курсовой работы
На промышленном транспорте осуществляется переработка многообразующих грузов в значительных количествах.
Переработка грузов требует создания высокопроизводительных механизированных и автоматизированных транспортно-погрузочных и складских комплексов, обеспечивающих эффективное использование подвижного состава.
Курсовая работа имеет своей целью научить практически решать вопросы в области создания комплексной механизации и автоматизации погрузочно-разгрузочных, транспортных и ремонтных работ в условиях массовых перевозок грузов на промышленном транспорте, организации рациональной эксплуатации и ремонта используемых машин и механизмов.
Выполняя курсовую работу, обобщается опыт в данной отрасли, используя отечественную и зарубежную информацию, а также результаты научных исследований и практические решения в развитии складского хозяйства, организации погрузочно-разгрузочных работ. При этом необходимо предусмотреть применение подвижного состава и новых перегрузочных технических средств, а наибольшей степени отвечающего требованиям технологий производства и условиям работы транспорта.
Методические указания содержат основные сведения о назначении и области применения устройств непрерывного транспорта, знакомят с конструкцией основных узлов ленточных конвейеров, характеристиками транспортируемых грузов. Рассмотрены основы теории расчета ленточных конвейеров. Приведенная в методических указаниях информация поможет студентам получить практические навыки при расчетах транспортно-технологического оборудования, обосновывать целесообразность принимаемых технических решений.
Рекомендуемые темы
1. Тяговый расчет автомобильного транспорта при перевозке природного мела автомобилем МАЗ-503А.
2.Тяговый расчет автомобильного транспорта при перевозке гравия для строительных работ автомобилем КрАЗ-256В.
3. Тяговый расчет автомобильного транспорта при перевозке песка строительных работ автомобилем БелАЗ-540.
4. Расчет ленточного конвейера производительностью 100 тонн/час при транспортировке крупнокусковых абразивных грузов (руда) на расстояние 100м.
5. Расчет ленточного конвейера производительностью 120 тонн/час при транспортировке среднекусковых абразивных грузов (камень) на расстояние 50м.
6. Расчет ленточного конвейера производительностью 160 тонн/час при транспортировке малоабразивных среднекусковых грузов (уголь) на расстояние 70м.
7. Расчет ленточного конвейера производительностью 100 тонн/час при транспортировке абразивных мелкокусковых и зернистых грузов (гравий) на расстояние 60м.
8. Расчет ленточного конвейера производительностью 140 тонн/час при транспортировке пылевидных грузов (цемент) на расстояние 50м.
9. Определить сменную производительность башенного крана КБ-160.
10. Определить сменную производительность башенного крана КБ-306А.
11. Определить сменную производительность башенного крана КБ-100.
12. Определить сменную производительность башенного крана КБ-60.
Цели и задачи курсовой работы
Основная цель курсовой работы – обучение эксплуатационным и проектным расчетам механизмов и узлов транспортирующих машин.
Задачи курсовой работы:
1) закрепление, углубление и обобщение знаний, приобретенных при изучении дисциплины «Технология и механизация погрузочно-разгрузочных работ»;
2) ознакомление с различными конструкциями машин, являющихся средством комплексной механизации погрузочно-разгрузочных, транспортных и складских работ;
3) совершенствование умения использовать нормативную, учебно-методическую, научно-техническую и справочную литературу подготовка к выполнению дипломного проекта.
Темой курсовой работы по дисциплине «Технология и механизация погрузочно-разгрузочных работ» ведущим преподавателем может быть выбран расчет одной из транспортирующих машин, изучаемых в теоретическом курсе дисциплины.
Цели и содержание задания
Произвести тяговый расчет автомобильного транспорта при транспортировке грузов, определить производительность и сменный пробег автомобиля:
1) определить возможную силу тяги автомобиля по условию сцепления с дорогой на каждом участке;
2) определить скорость движения груженного и порожнего автомобиля на каждом участке пути;
3) определить продолжительность движения автомобиля на каждом участке пути в оба конца;
4) подсчитать время загрузки автомобиля;
5) подсчитать длительность рейса автомобиля, учитывая время на разгрузку загрузку;
6) Определить сменную производительность и сменный пробег машины.
По заданной производительности ленточного конвейера определить ширину ленты и мощность электродвигателя:
1) определить площадь поперечного сечения материала на ленте;
2) определить ширину ленты;
3) вычислить мощность на валу приводного барабана конвейера.
4) вычислить необходимую мощность двигателя;
5) вычислить окружное усилие на приводном барабане и натяжение набегающей и сбегающей ветвей ленты;
6) определить количество прокладок в ленте;
7) определить диаметр приводного барабана и передаточное отношение приводного редуктора.
Определить сменную производительность башенного крана:
1) определить необходимую высоту подъема крана и вылет стрелы соответствующей этой высоте;
2) вычислить коэффициент использования крана по грузоподъемности;
3) начертить рабочую зону крана в масштабе;
4) определить продолжительность отдельных операций рабочего цикла крана;
5) вычислить длительность рабочего цикла крана без совмещения операций и при совмещении операций;
6) начертить схемы последовательности операций рабочего цикла;
7) определить эксплуатационную производительность башенного крана при работе по совмещенному и несовмещенному циклу.
Тяговый расчет автомобильного транспорта (варианты заданий к выполнению курсовой работы по темам 1-3 приведены в таблице Б.1-Б.4 и на рисунке 8.1)
Считая постоянной скорость движения, определяем возможную силу тяги автомобиля по условию сцепления с дорогой на каждом участке пути (рисунок 9.1.) по формуле
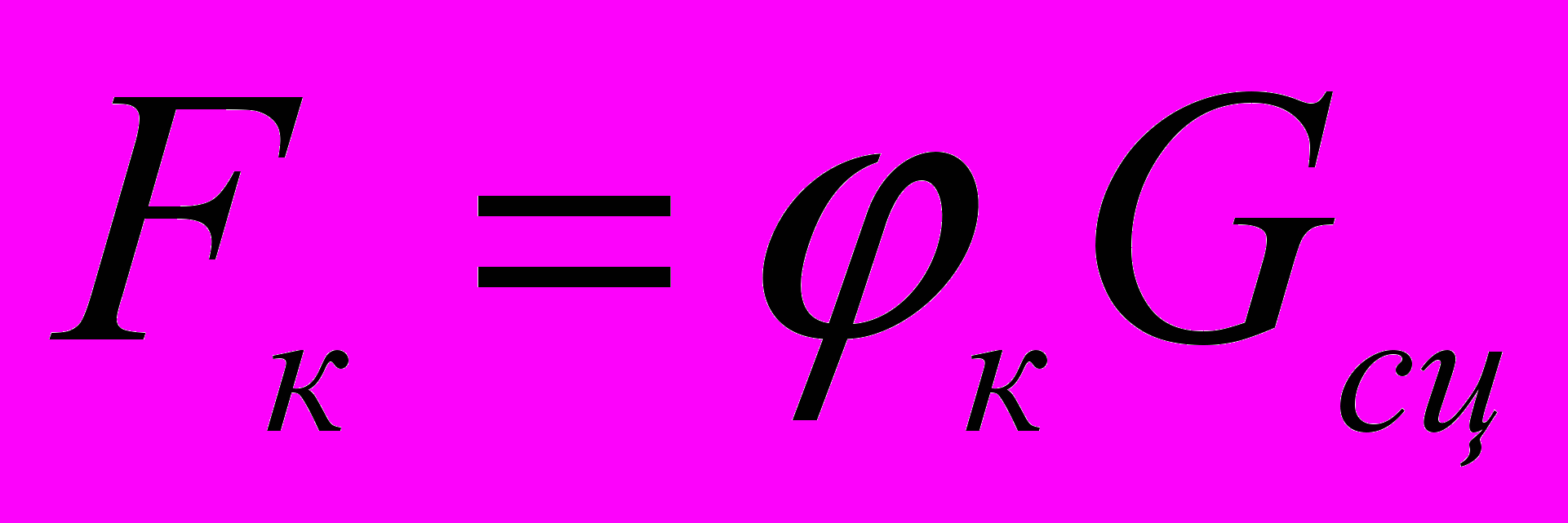
где φк – коэффициент сцепления шин с дорогой на к-том участке пути (таблица Б.2, приложение Б).
Gсц – сила сцепления веса автомобиля, Н (таблица Б.2, приложение Б).
Должно выполняться условие
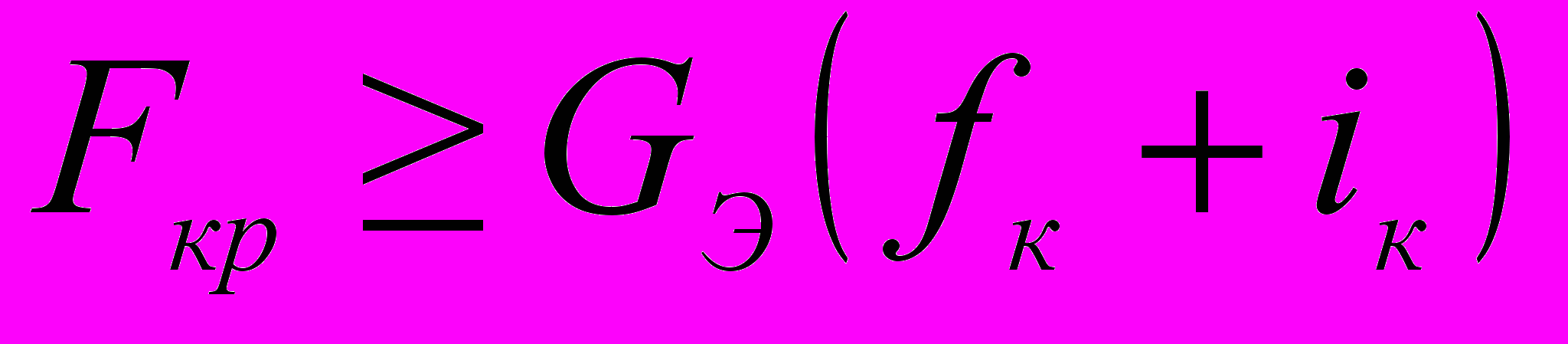
где GЭ – сила веса груженного автомобиля, эксплуатационная, Н (таблица Б.2, приложение Б);
fк – удельное сопротивление движению на к-том участке пути (таблица Б.3, приложение Б);
iк – уклон к-того участка пути (таблица Б.1, приложение Б).
Рассчитываем динамический фактор груженного Д и Д0 порожнего автомобиля для каждого участка по формулам
Д = f + i,
Д0 = f – i. (8.3)
Пользуясь значениями динамического фактора выбираем по динамической характеристике (рисунок 8.2) скорость движения груженного и порожнего автомобиля. При определении скорости порожнего автомобиля пользуемся шкалой: Д0, Д-V
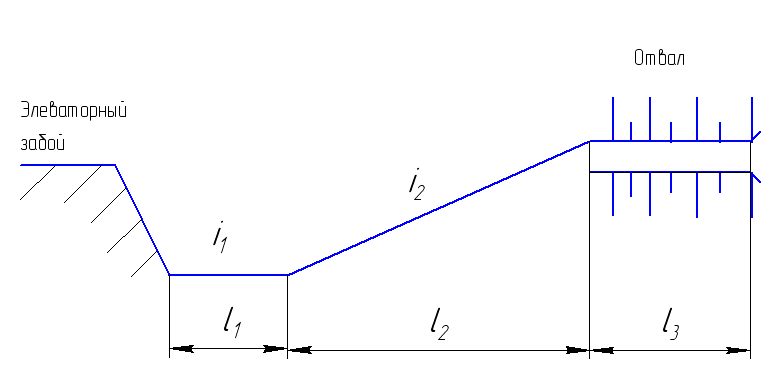
Рисунок 8.1 – Схема трассы движения автомобиля
В случае отрицательного значения динамического фактора рассчитываем скорость движения на участке по формуле 8.4, задаваясь величиной ST тормозного пути.

Для условий строительной площадки можно принимать ST=5 м.
Определяем продолжительность движения на каждом участке трассы
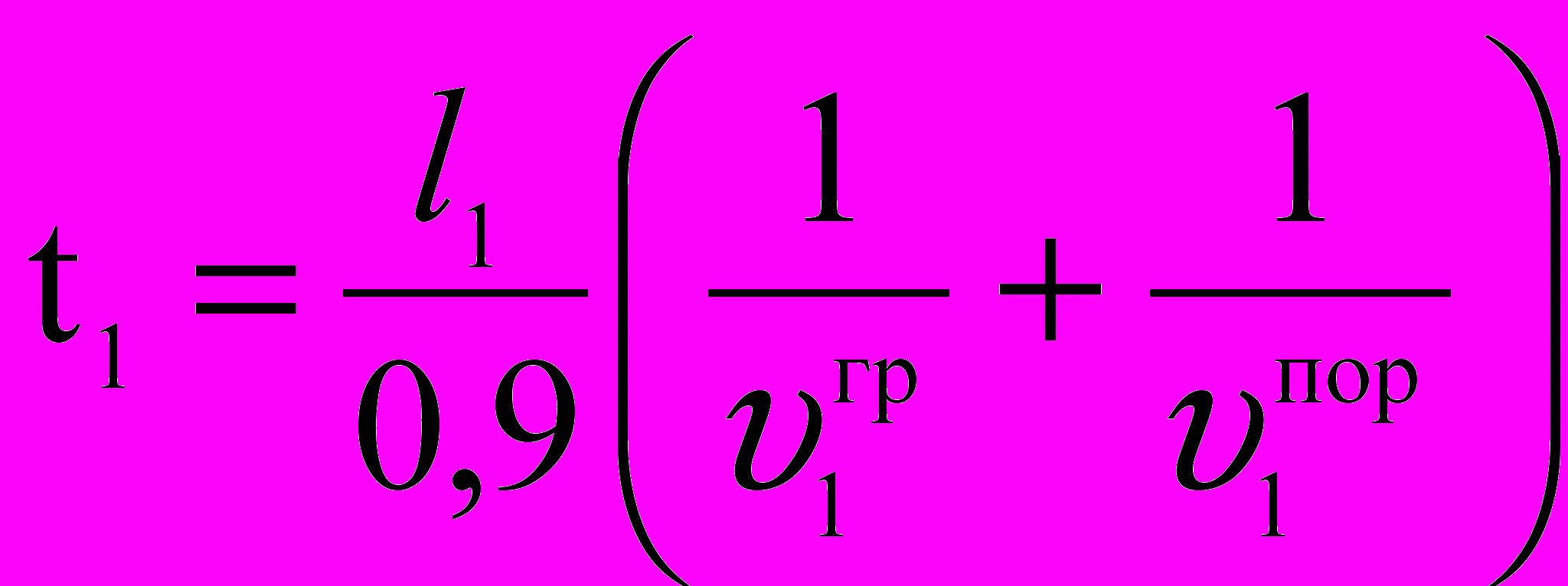
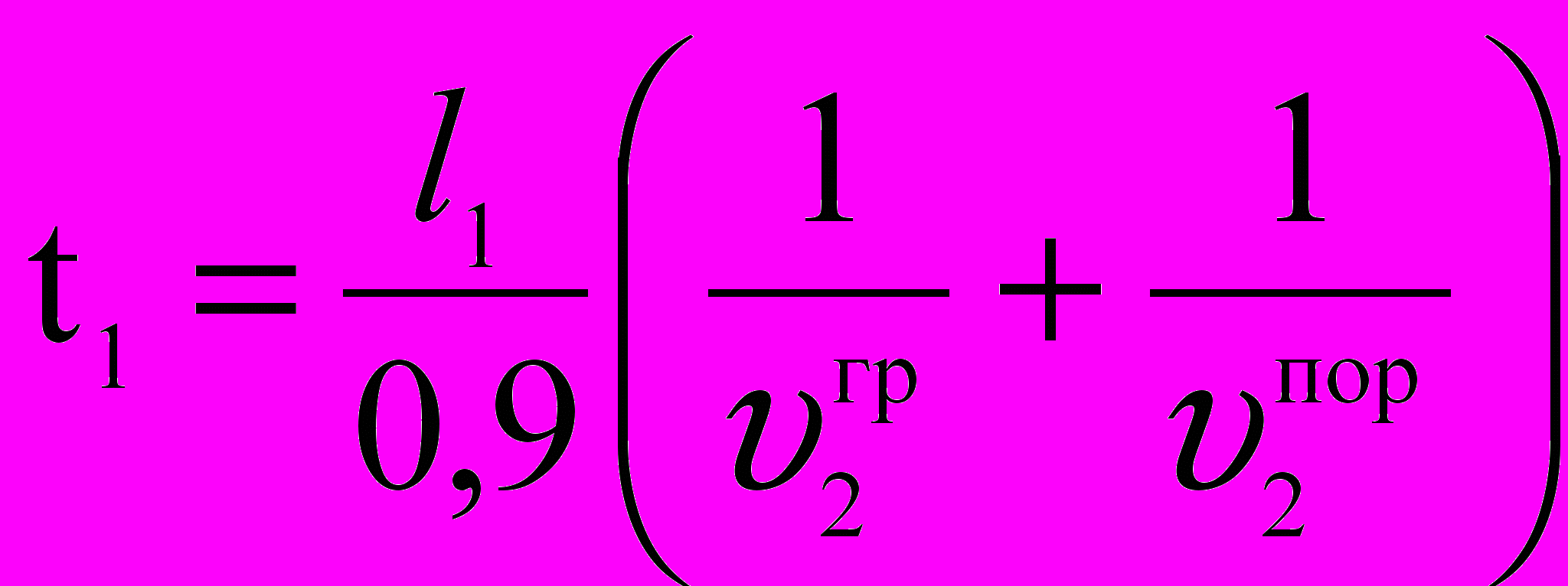
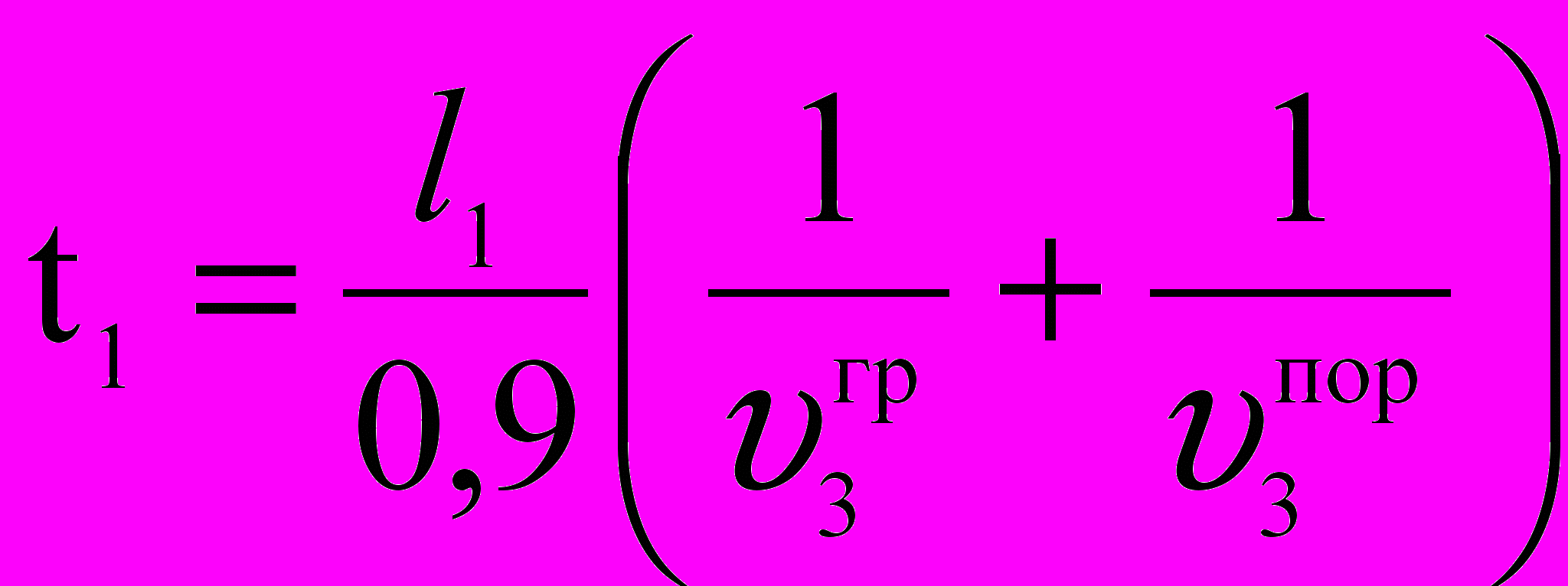
где l1, l2, l3 – длины участков трассы, м (таблица Б.1, приложение Б);
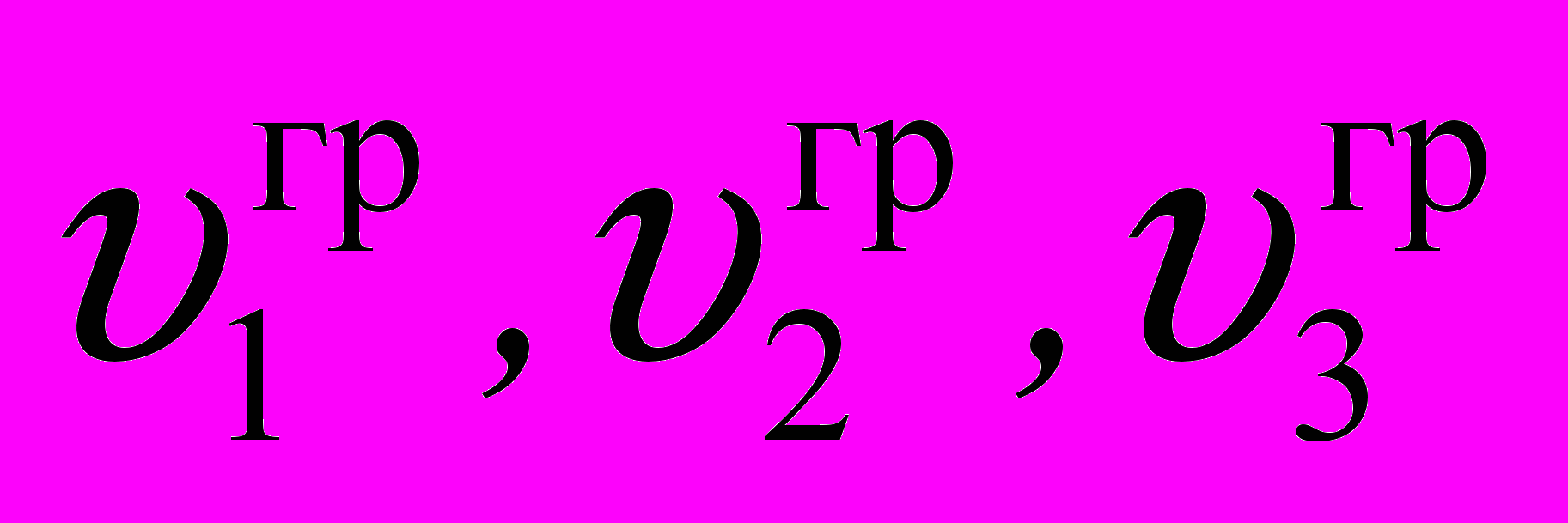
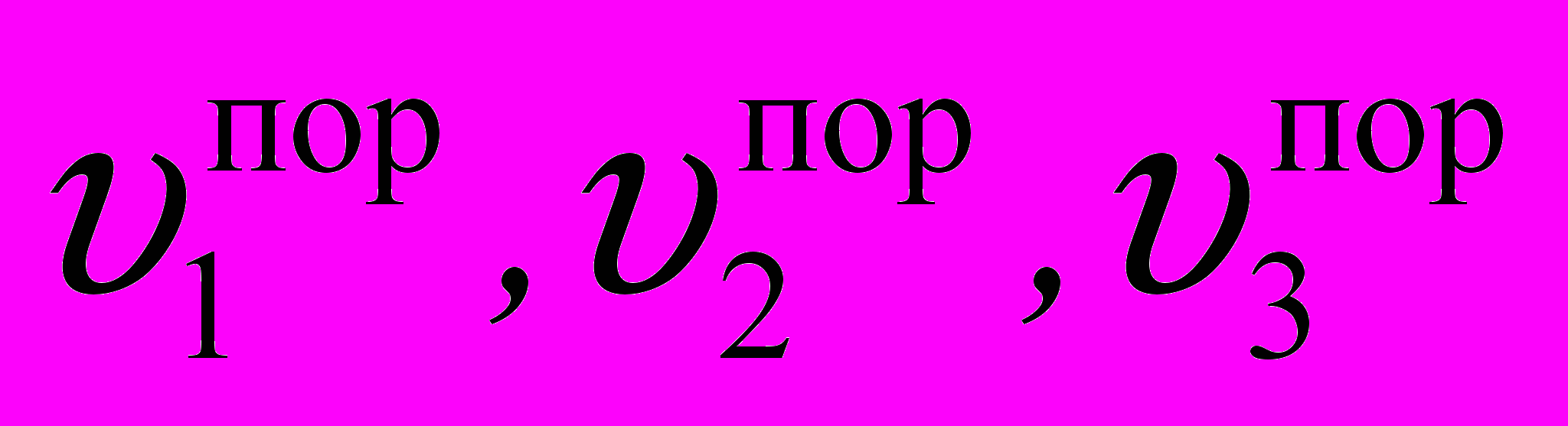
0,9 – коэффициент, учитывающий затраты времени на ускорение и замедление движения.
Вычисляем продолжительность загрузки автомобиля
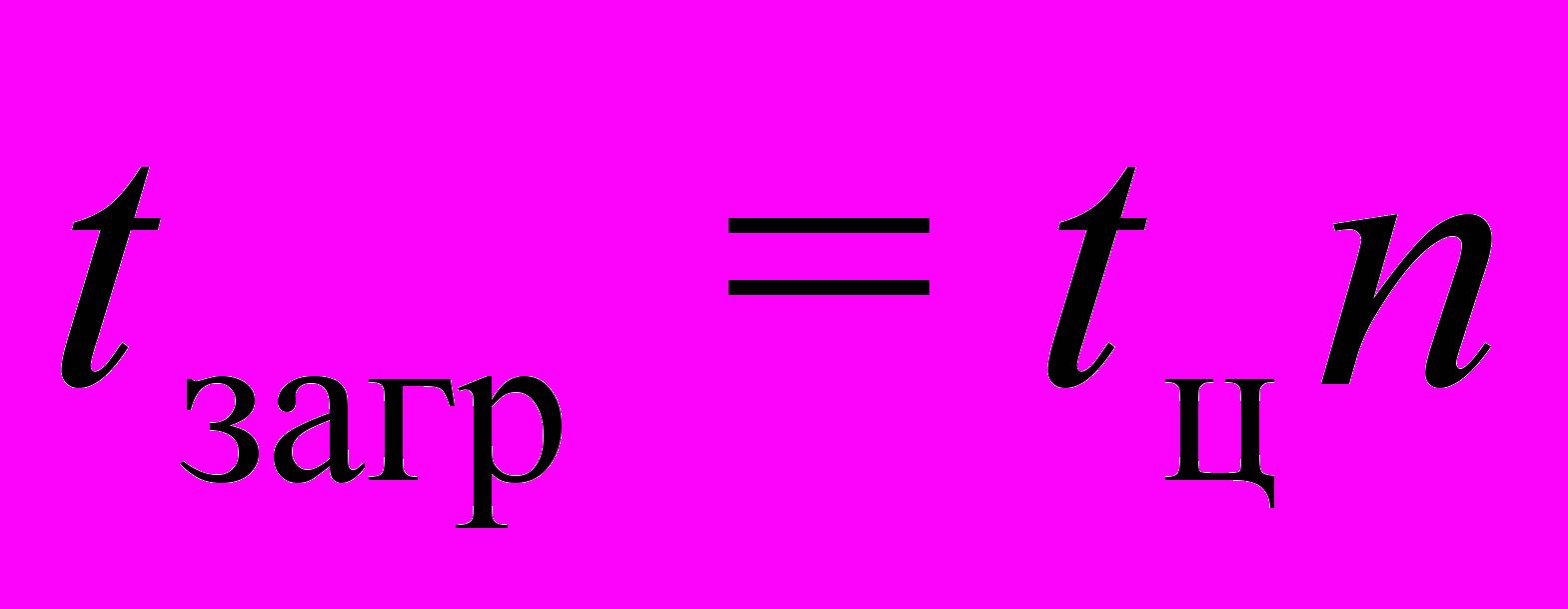
где tц – рабочий цикл экскаватора, с (таблица Б.2, приложение Б)
n – количество ковшей вмещающихся в кузов автомобиля, (таблица Б.2, приложение Б).
Необходимо проверить условие грузоподъемности автомобиля
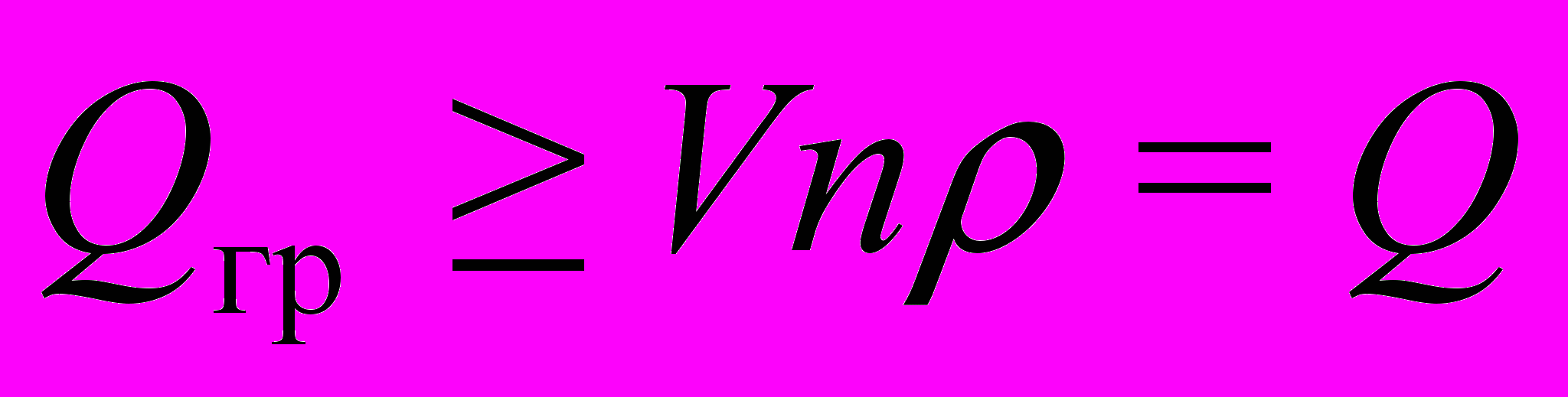
где Qгр – грузоподъемность автомобиля, кг (таблица Б.2, приложение Б);
Vков – емкость ковша экскаватора, м3;
Q – масса груза, кг.
Если условие (9.7) не выполняется, необходимо уменьшить количество ковшей грунта, засыпаемых в кузов автомобиля и уточнить время загрузки.
Подсчитываем длительность рейса автомобиля, учитывая время на загрузку и выгрузку

где tразгр – длительность разгрузки автомобиля с учетом маневров, с (таблица Б.2, приложение Б).
Определяем сменную производительность автомобиля
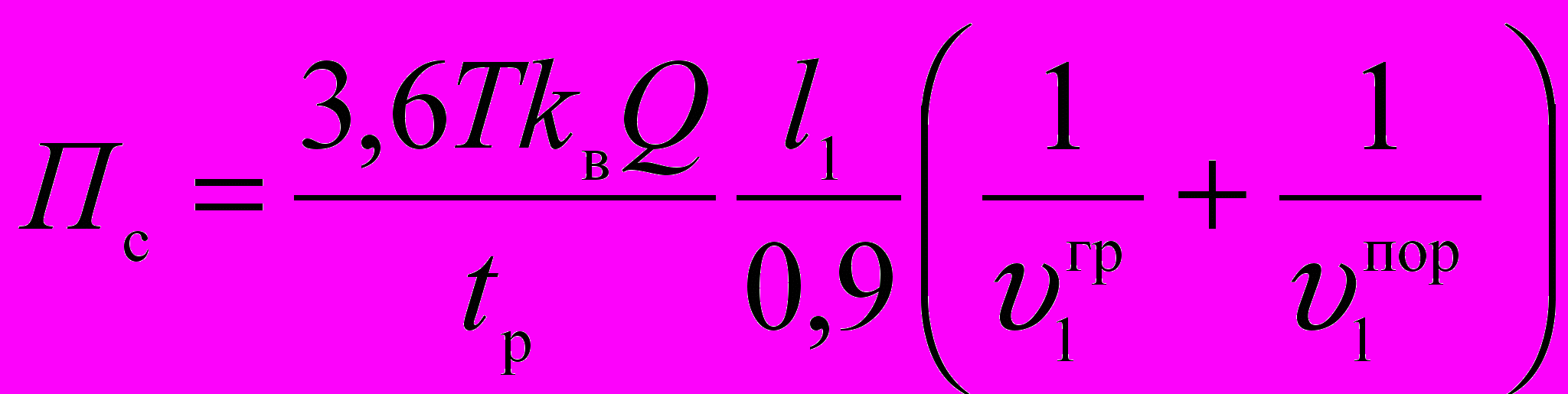
Определить сменный пробег автомобиля
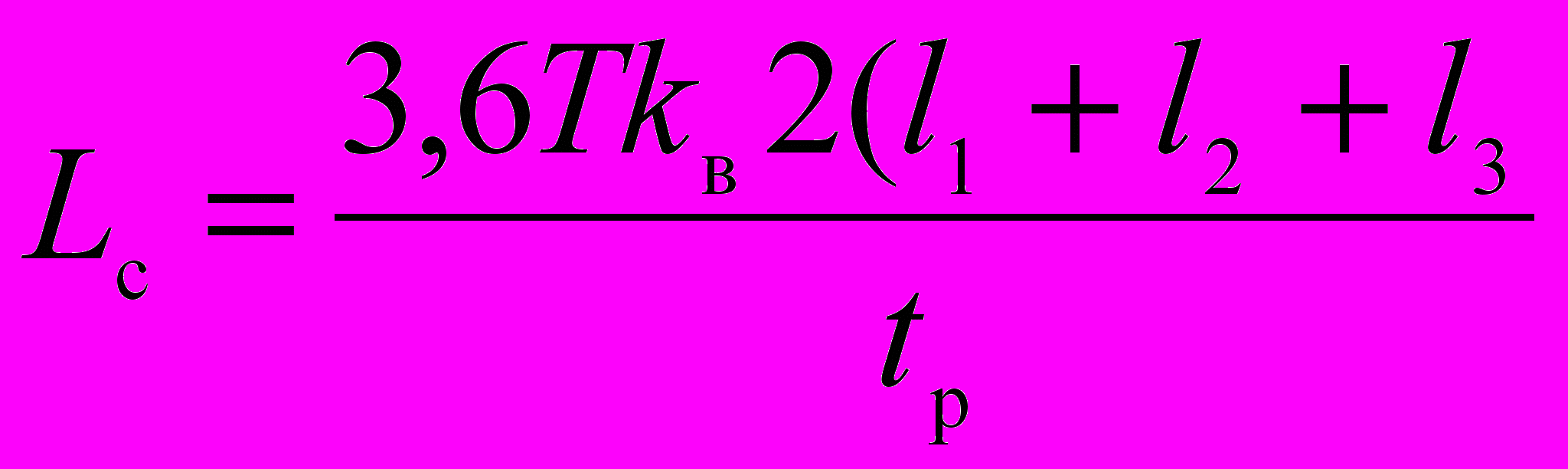
где Lc – сменный пробег автомобиля, т/смену;
T – количество часов в смену, 8,2 часа;
kв – коэффициент использования сменного времени равный 0,85-0,9.
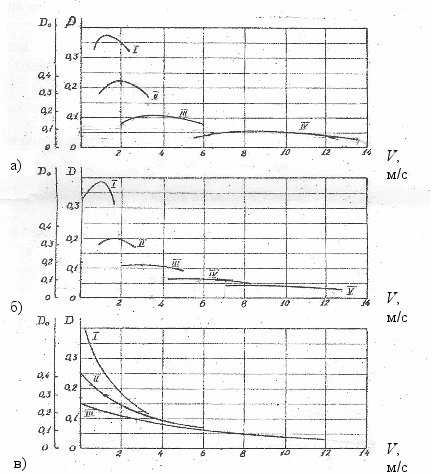
а – МАЗ-503А; б – КрАЗ-256В; в – БелАЗ-540
Рисунок 8.2 – Динамические характеристики автосамосвалов
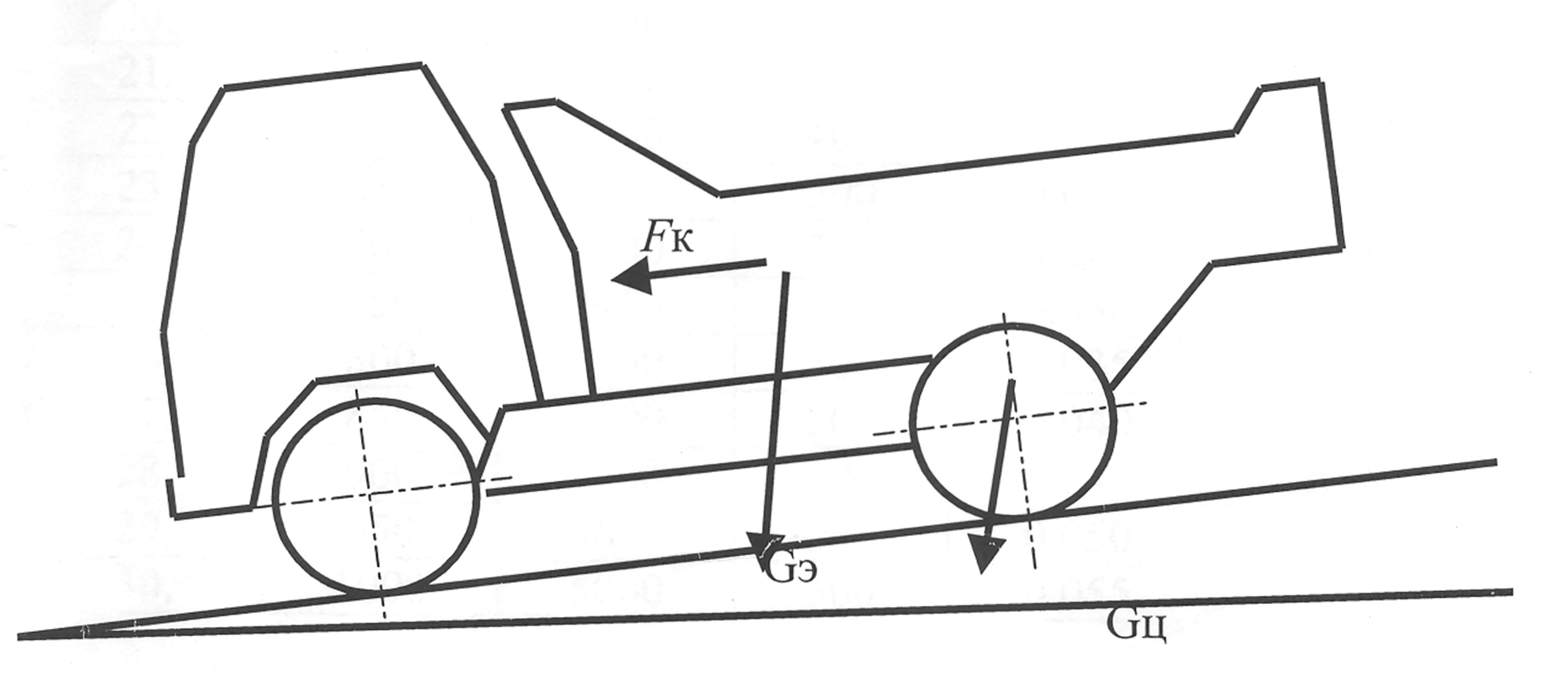
Рисунок 8.3 – Схема сил, действующих на автомобиль
Расчет ленточного конвейера (варианты заданий к выполнению курсовой работы по темам 5-8 приведены в таблице Б.5-Б.14 и на рисунках 8.4 и 8.5)
Ленточные конвейеры применяют для непрерывного транспортирования различных материалов в горизонтальном или наклонном направлении. Они обеспечивают высокую производительность (до нескольких тысяч тонн в час) и значительную дальность транспортирования (до нескольких десятков километров). В строительстве используют передвижные и стационарные ленточные конвейеры, перемещающие грузы на сравнительно небольшие расстояния.
Основным транспортирующим и тяговым органом является бесконечная прорезиненная лента 4 ленточного конвейера (рисунок 8.4,а), огибающая два барабана – приводной 6 и натяжной 2. Поступательное движение ленты с грузом создаётся силами трения, действующими в зоне контакта ленты с приводным барабаном. Вращение барабан получает от приводного электродвигателя 10 через редуктор 9. Для увеличения тягового усилия рядом с приводным барабаном устанавливают отклоняющий барабан 7, увеличивающий угол обхвата (рисунок 8.4,в). Верхняя рабочая и нижняя холостая ветвь поддерживаются верхними 5 и нижними 8 роликоопорами. В целях получения наибольшей производительности конвейеров верхние роликоопоры делают желобчатой формы, при прохождении по ним лента той же ширины способна нести больше материала по сравнению с плоской (рисунок 8.4,б). Для предотвращения провисания ленты между роликоопорами, а также для увеличения тягового усилия лента предварительно натягивается посредством винтового или грузового натяжного устройства 1.
Загрузка транспортируемого материала на ленту производится через специальную воронку 3. Съём материала может производиться через приводной барабан или в промежуточных пунктах с помощью специальных сбрасывающих устройств. Для предотвращения самопроизвольного обратного хода ленты после остановки конвейера на валу приводного барабана устанавливают тормоз. Угол наклона конвейера зависит от подвижности транспортируемого материала и коэффициента трения материала о транспортерную ленту при движении.
Чтобы обеспечить нужное натяжение ленты для передачи ей движения трением, применяют винтовое или грузовое устройство.
По заданной производительности (таблица Б.5, приложение Б) определяем площадь поперечного сечения материала на ленте конвейера
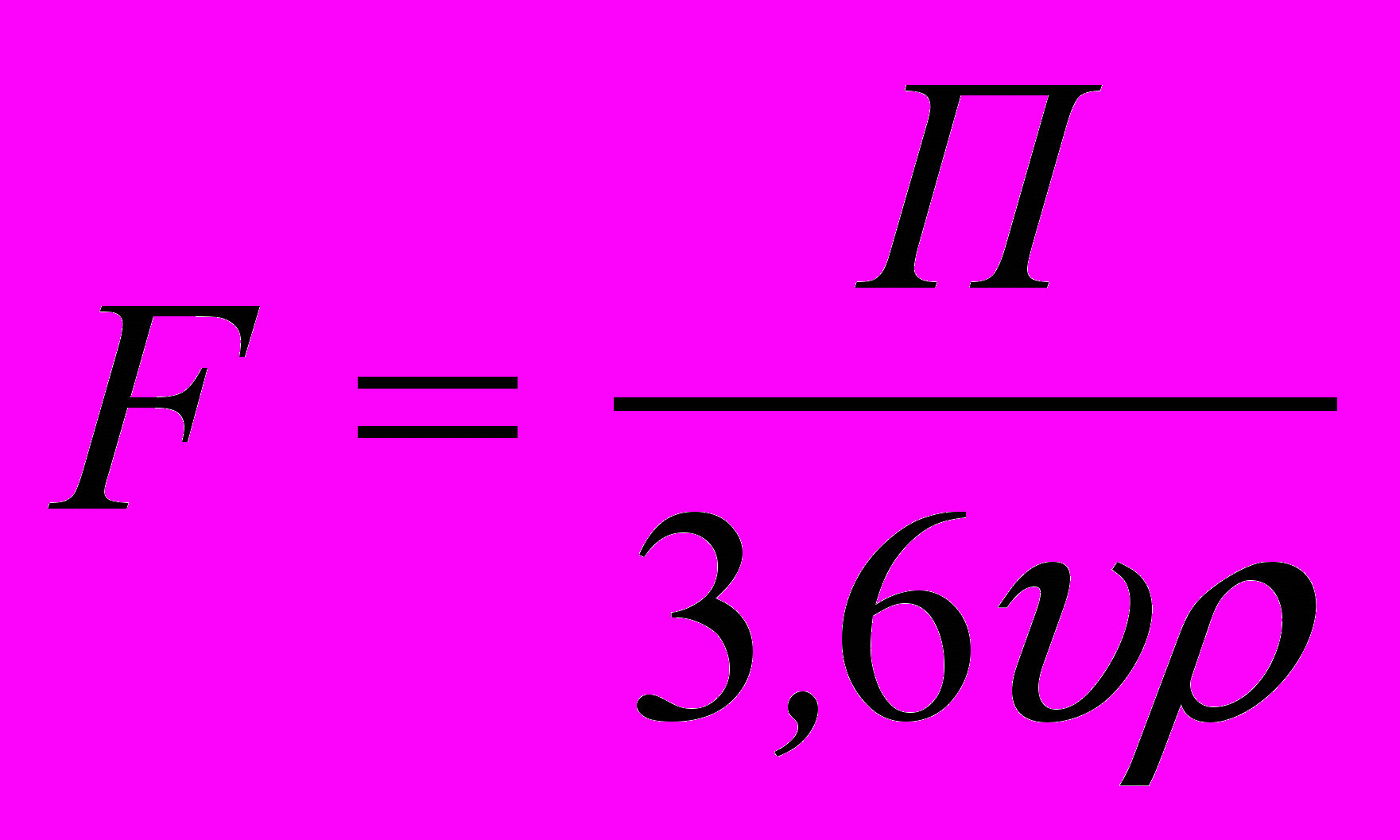
где П – производительность конвейера, т/ч;
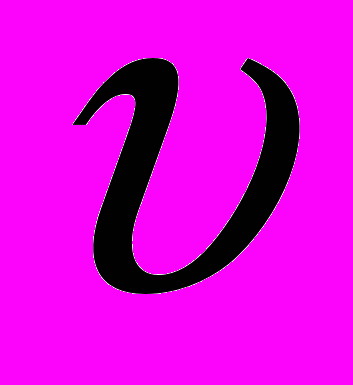
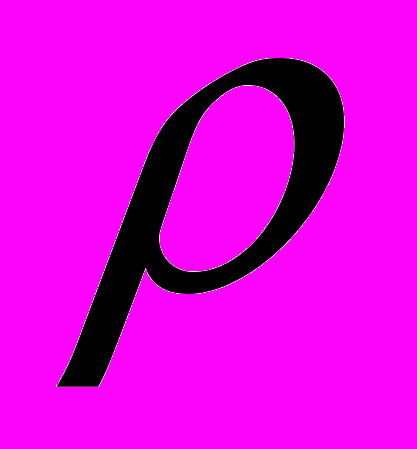
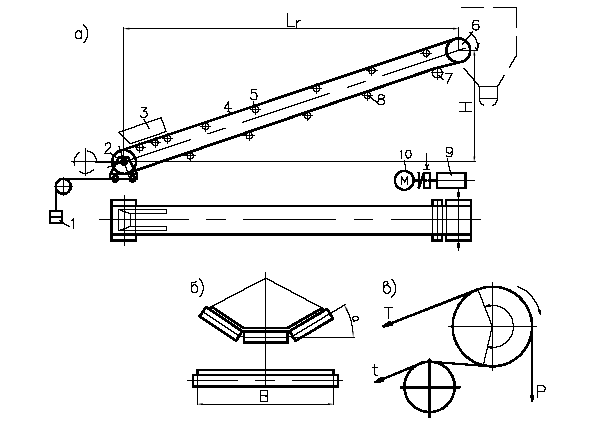
а – схема ленточного конвейера; б – поперечный разрез; в – механизм натяжения ленты
Рисунок 8.4 – Ленточный конвейер
Определяем ширину ленты по одной из формул (8.12)-(8.14) в зависимости от формы ленты (рисунок 8.5). Форма ленты выбирается по последней цифре зачетки: а – 0,1,2; б – 3,4, 7; в – 5,6,8, 9.
Лента плоская без бортов (рисунок 8.5, а)
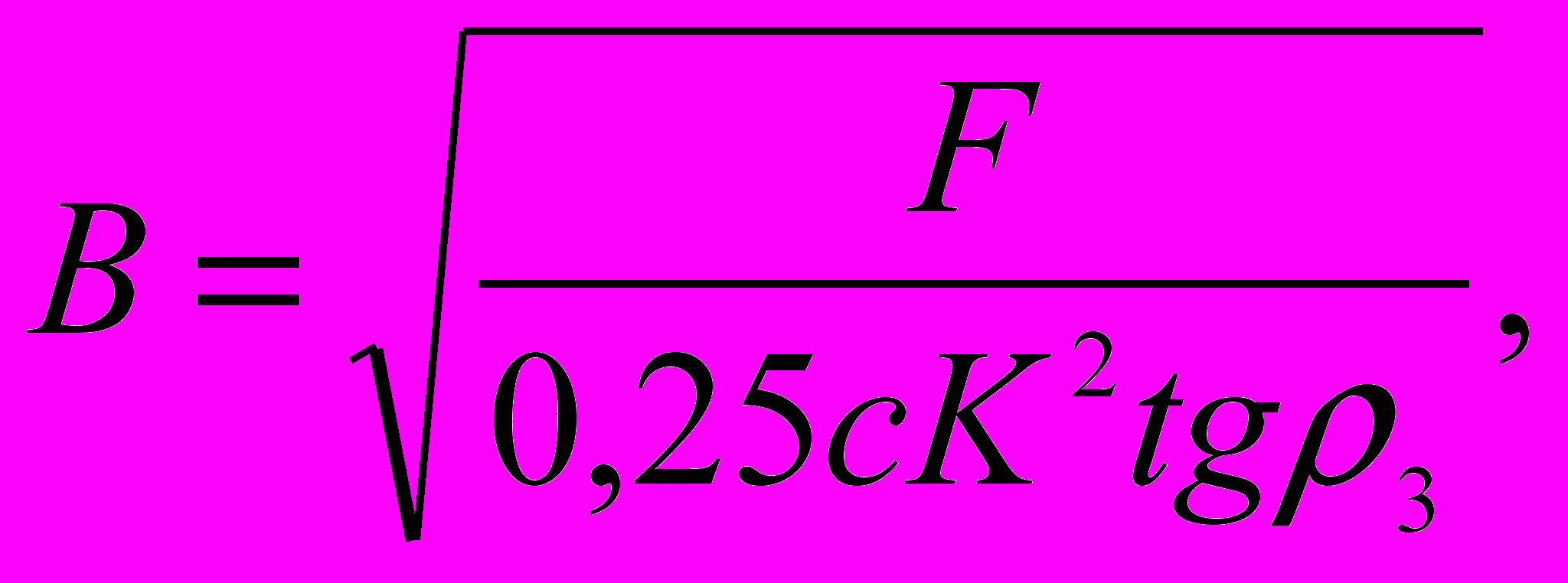
где с – коэффициент, учитывающий уменьшение площади сечения от ссыпания материала назад при транспортировании его наклонным конвейером (таблица Б.8, приложение Б);
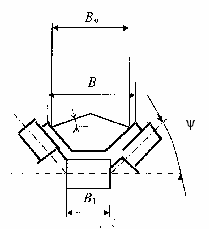
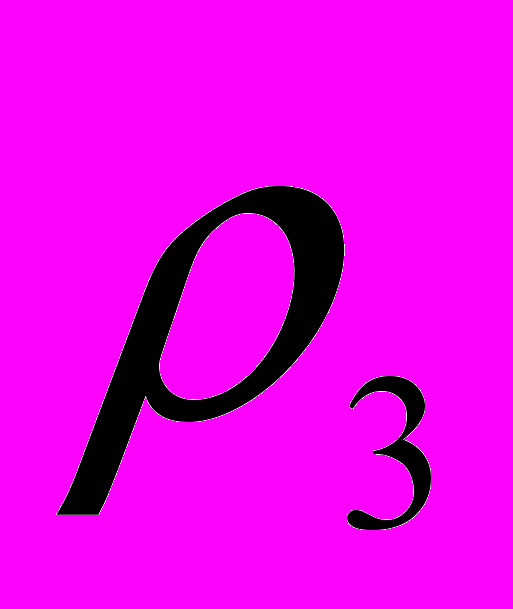
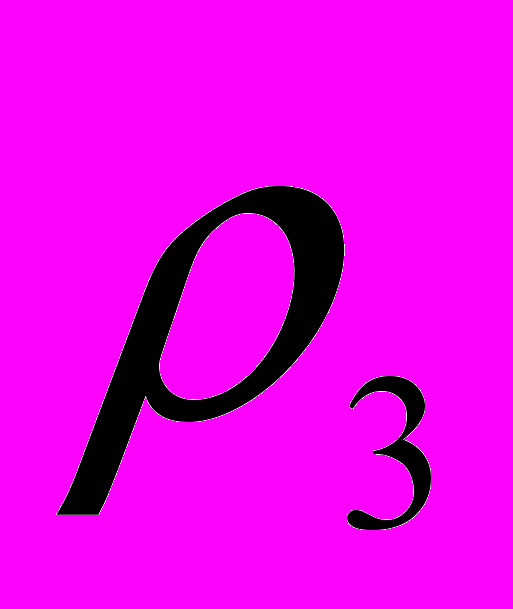
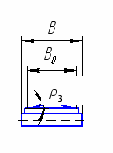
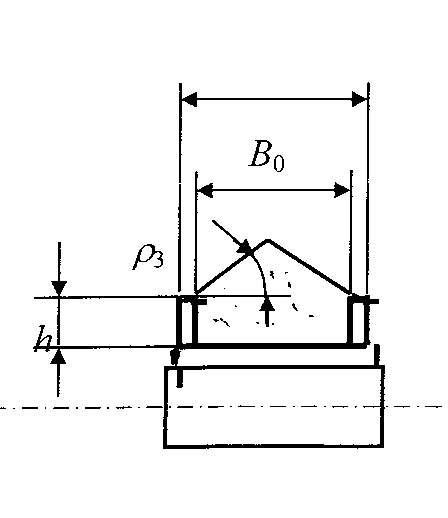
а – плоская лента без бортов; б – плоская лента с бортами; в – желобчатая лента
Рисунок 8.5 – Размещение транспортируемого материала на ленте при различных формах поперечного сечения конвейера
Плоская лента с бортами (рисунок 8.5, б)
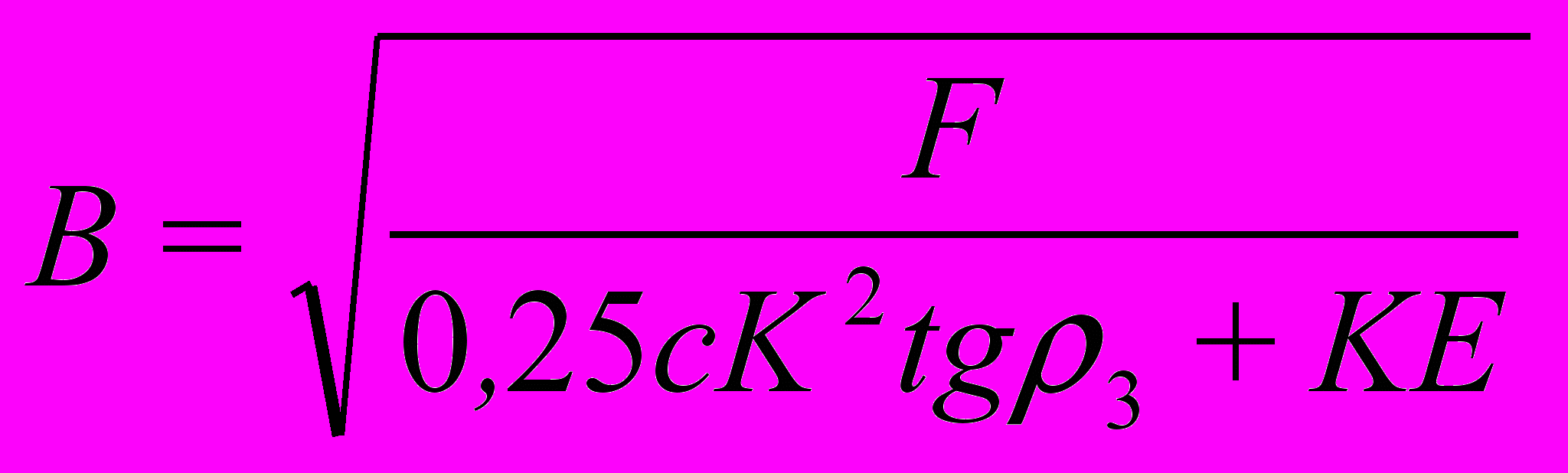
где Е – отношение, численно равное
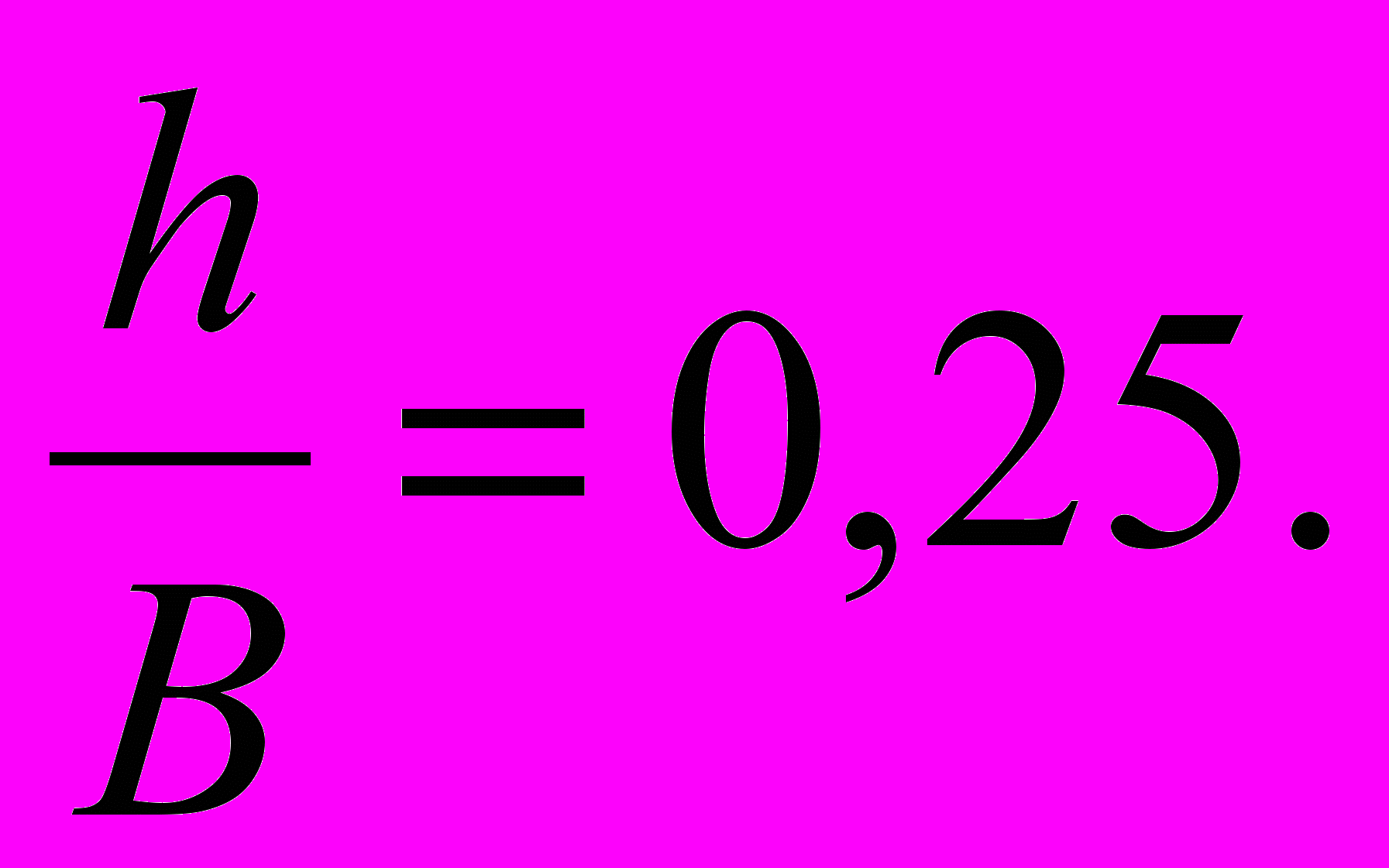
Желобчатая лента (рисунок 8.5, в)

где К1 – отношение, численно равное
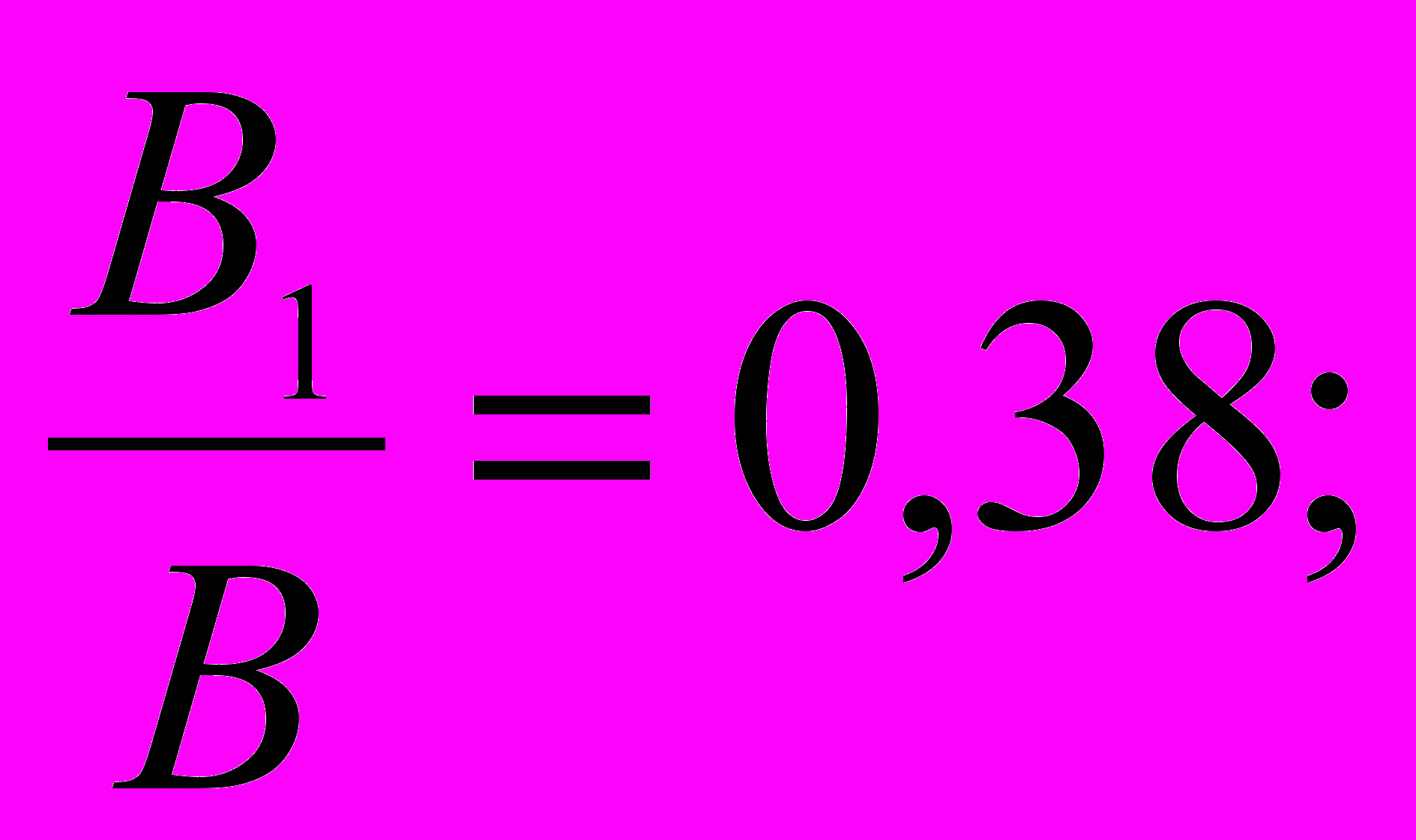
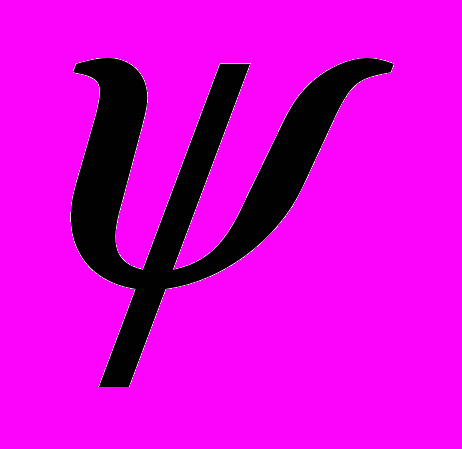
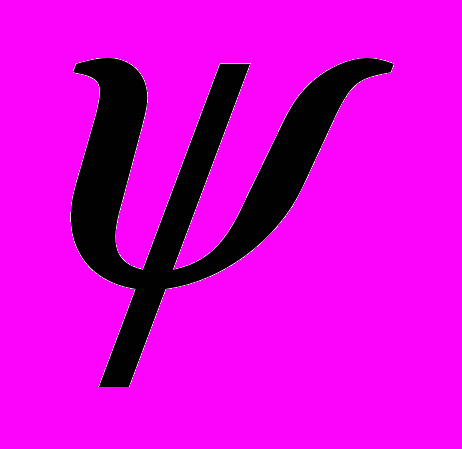
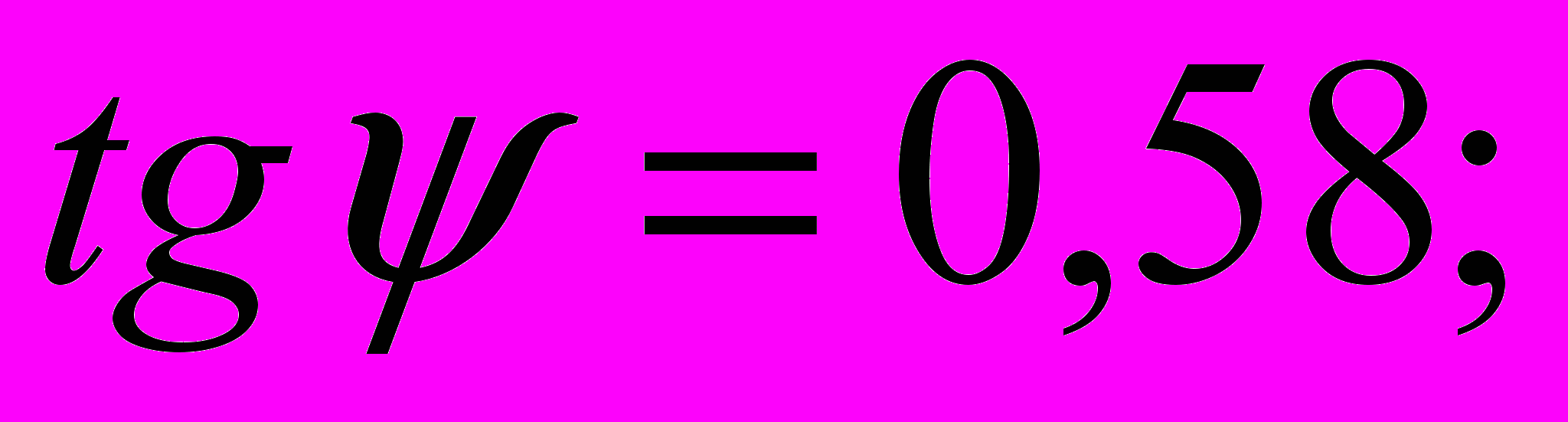
К – отношение, численно равное
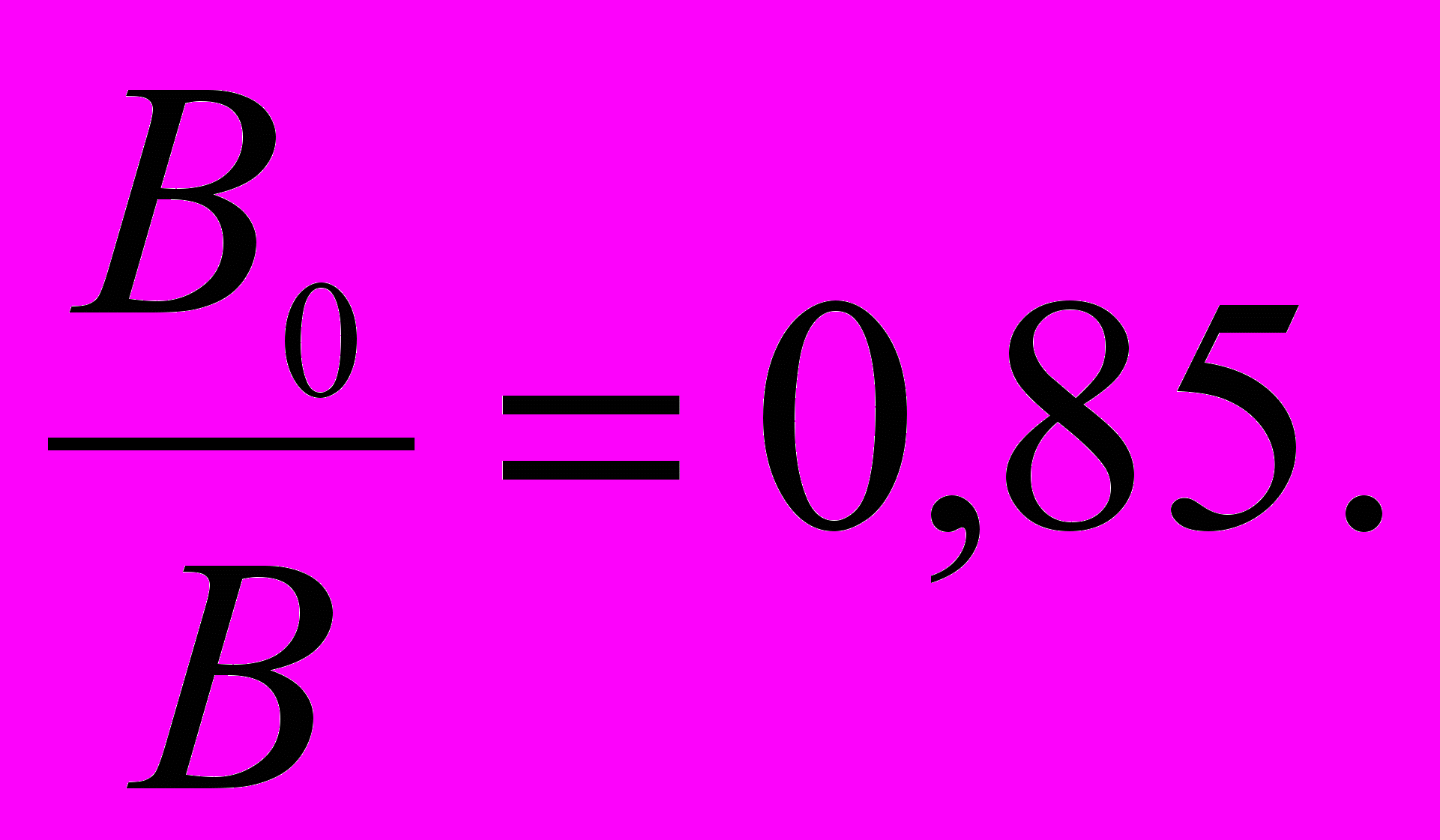
Получили ширину ленты, принимаем ее уточненное значение в сторону увеличения из таблицы 2.9 для дальнейших расчетов.
Вычисляем мощность на валу приводного барабана конвейера

где Н – высота подъема материала (рисунок 8.6)
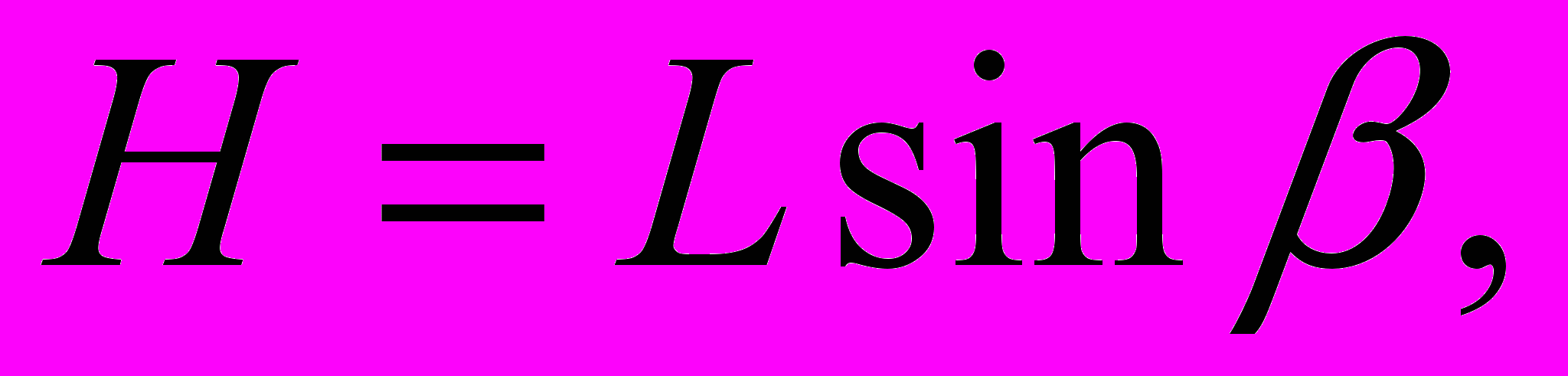
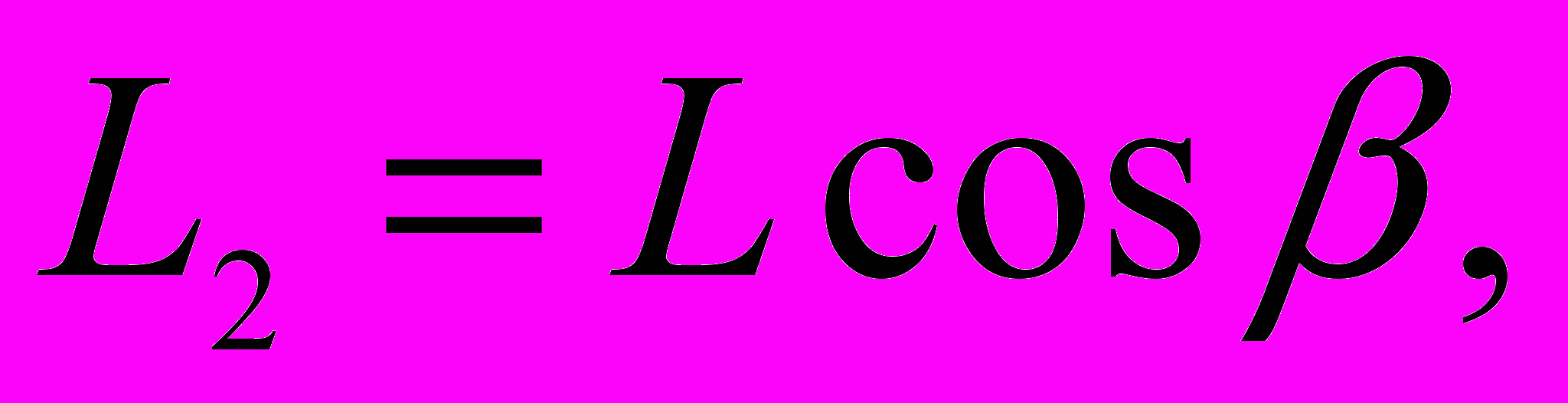
где L – длина конвейера, м (таблица Б.5, приложение Б);
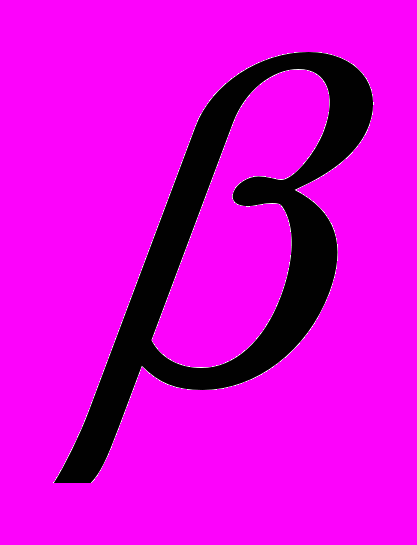
L2 – длина горизонтальной проекции конвейера, м;
k1 – эмпирический коэффициент, учитывающий влияние относительной длины конвейера (таблица Б.9, приложение Б);
k2 – коэффициент, учитывающий расход энергии на преодоление сопротивлений, возникающих при прохождении ленты через сбрасывающую тележку (таблица Б.6, приложение Б);
k – коэффициент, учитывающий расход энергии на работу сбрасывающего устройства (таблица Б.6, приложение Б).
Вычисляем необходимую мощность электродвигателя
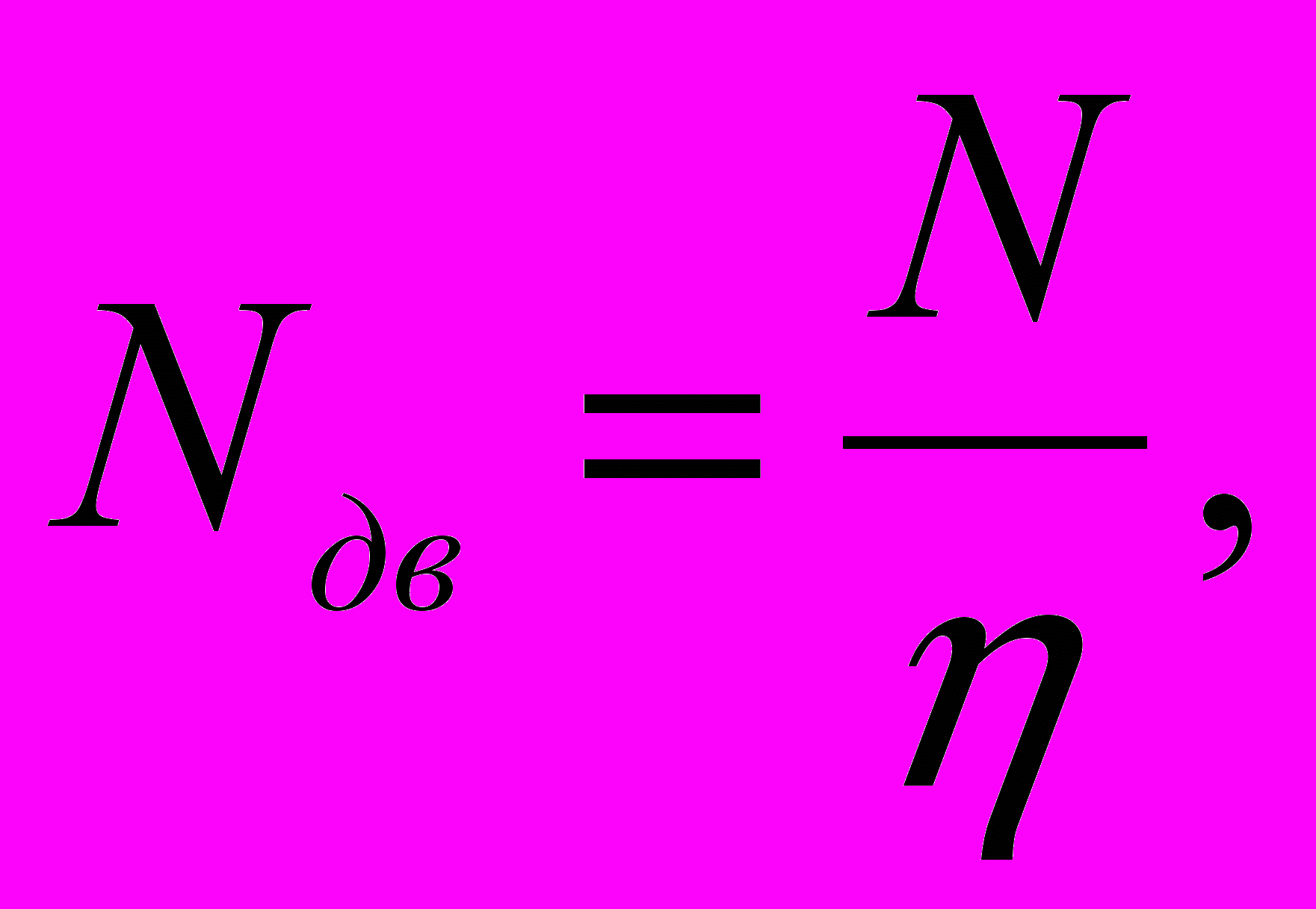
где
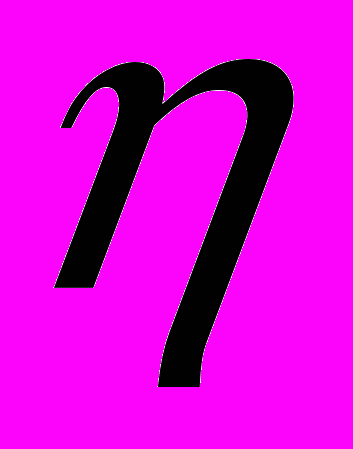
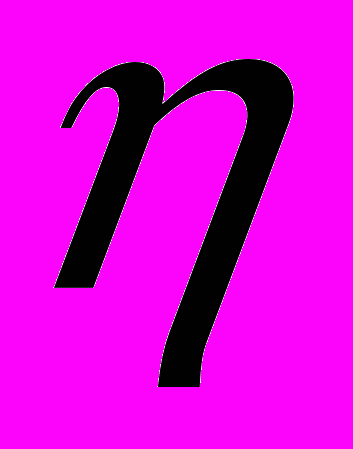
Из таблицы Б.14 (приложение Б) подбираем марку электродвигателя.
Вычисляем окружное усилие на приводном барабане
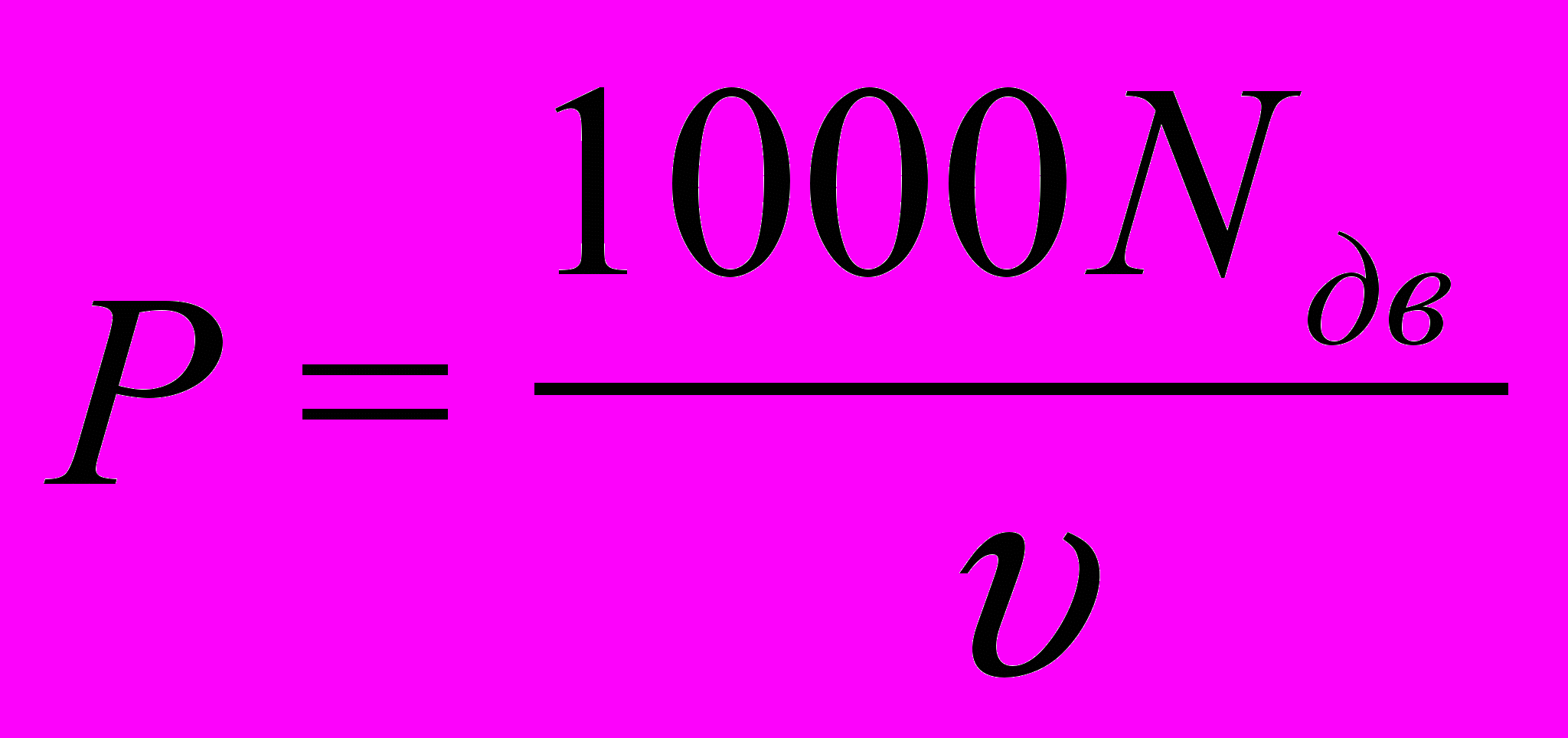
и натяжение набегающего и сбегающего концов ленты
сбегающего
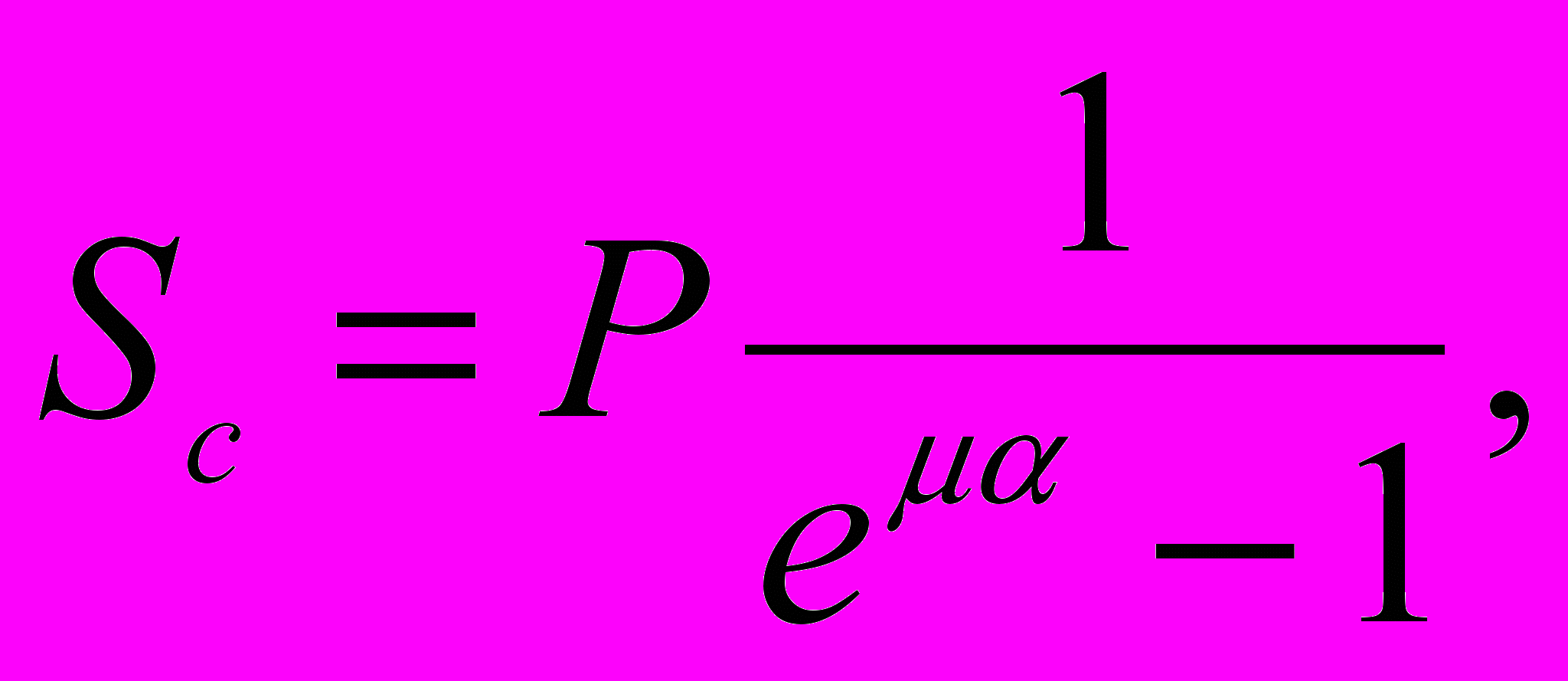
набегающего
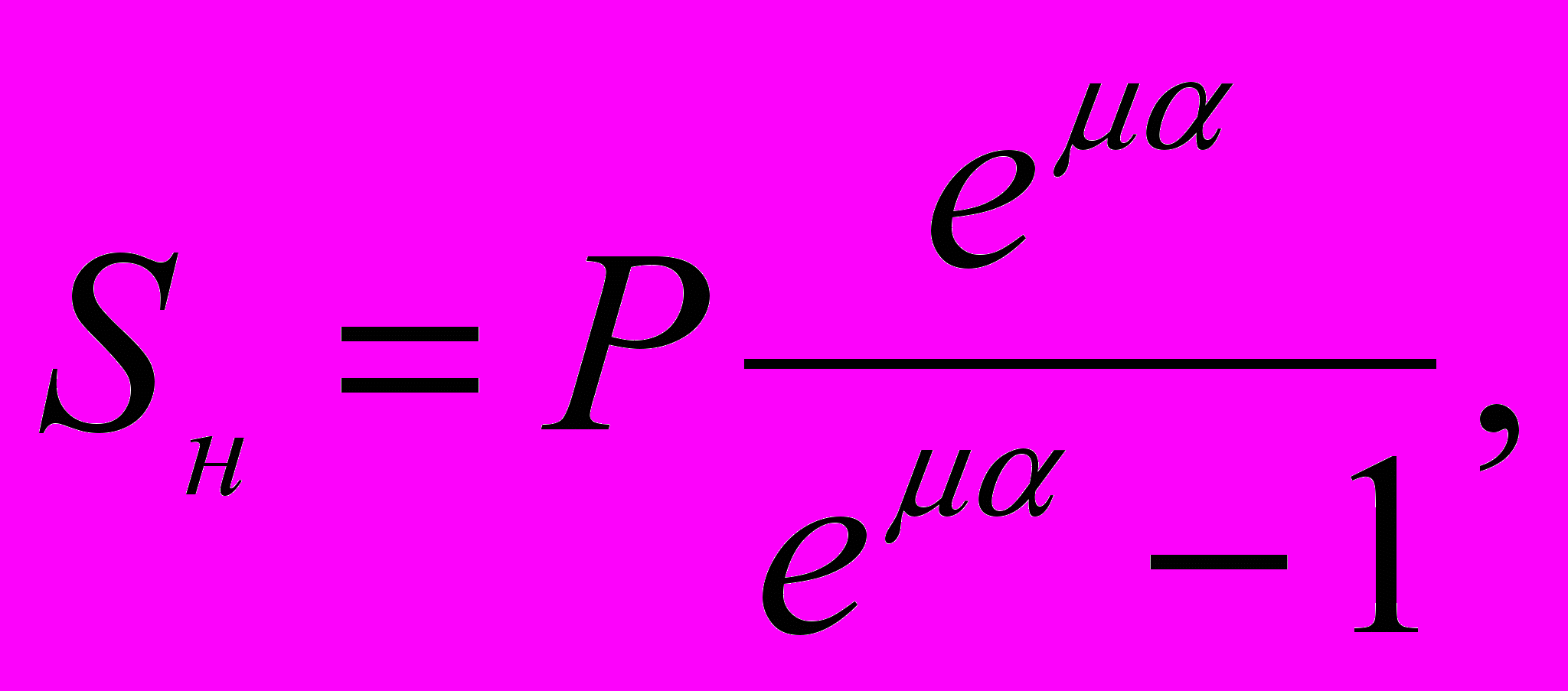
где
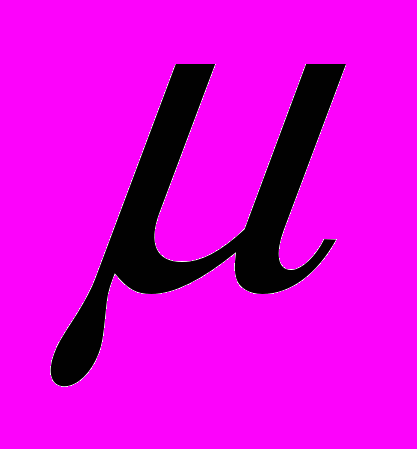
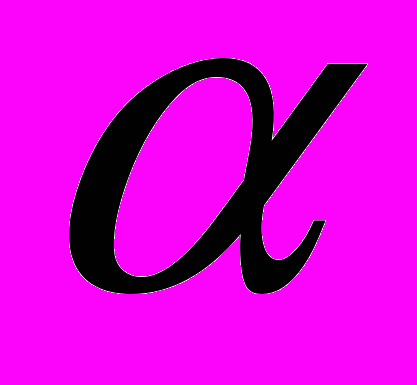
Значение
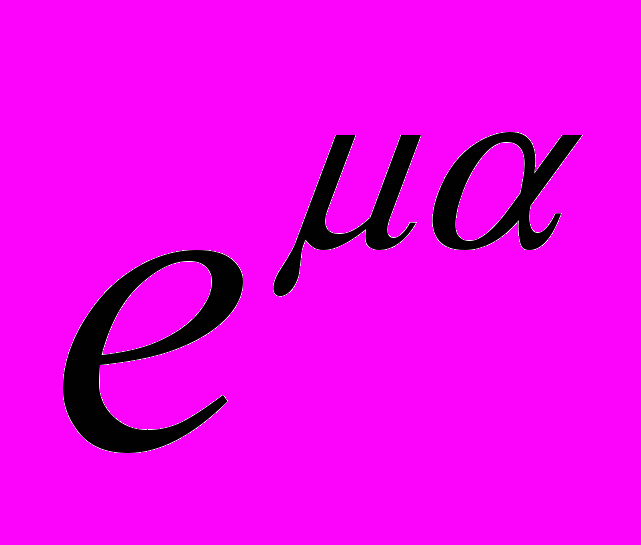
Определяем количество прокладок в ленте
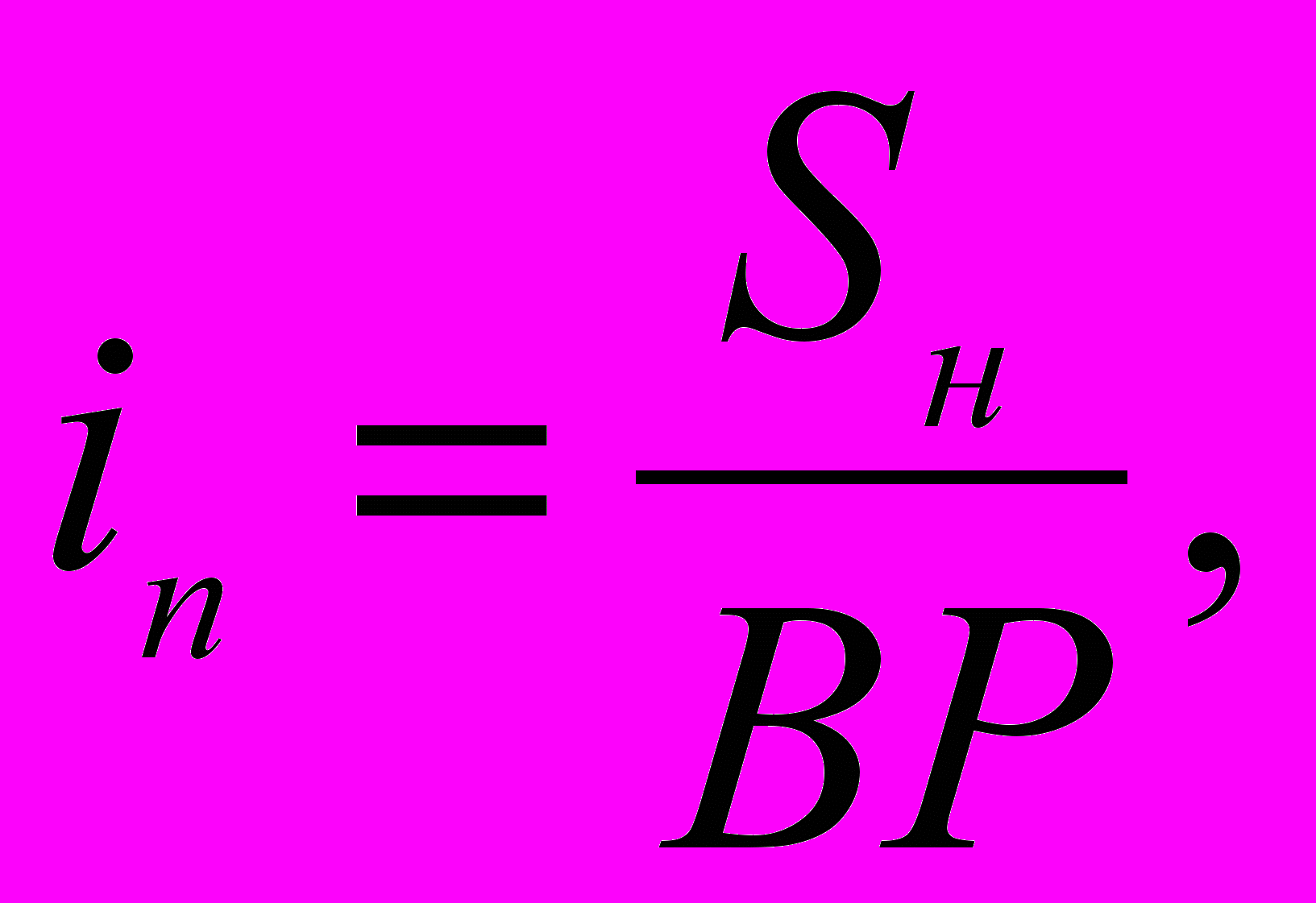
где Р – допускаемая нагрузка на 1 м ширины одной прокладки, Р=5500 н/м.
Подсчитанное число прокладок должно находиться в пределах, приведенных в таблице Б.13 (приложение Б).
Определяем диаметр приводного барабана и лебедки

и передаточное отношение приводного редуктора
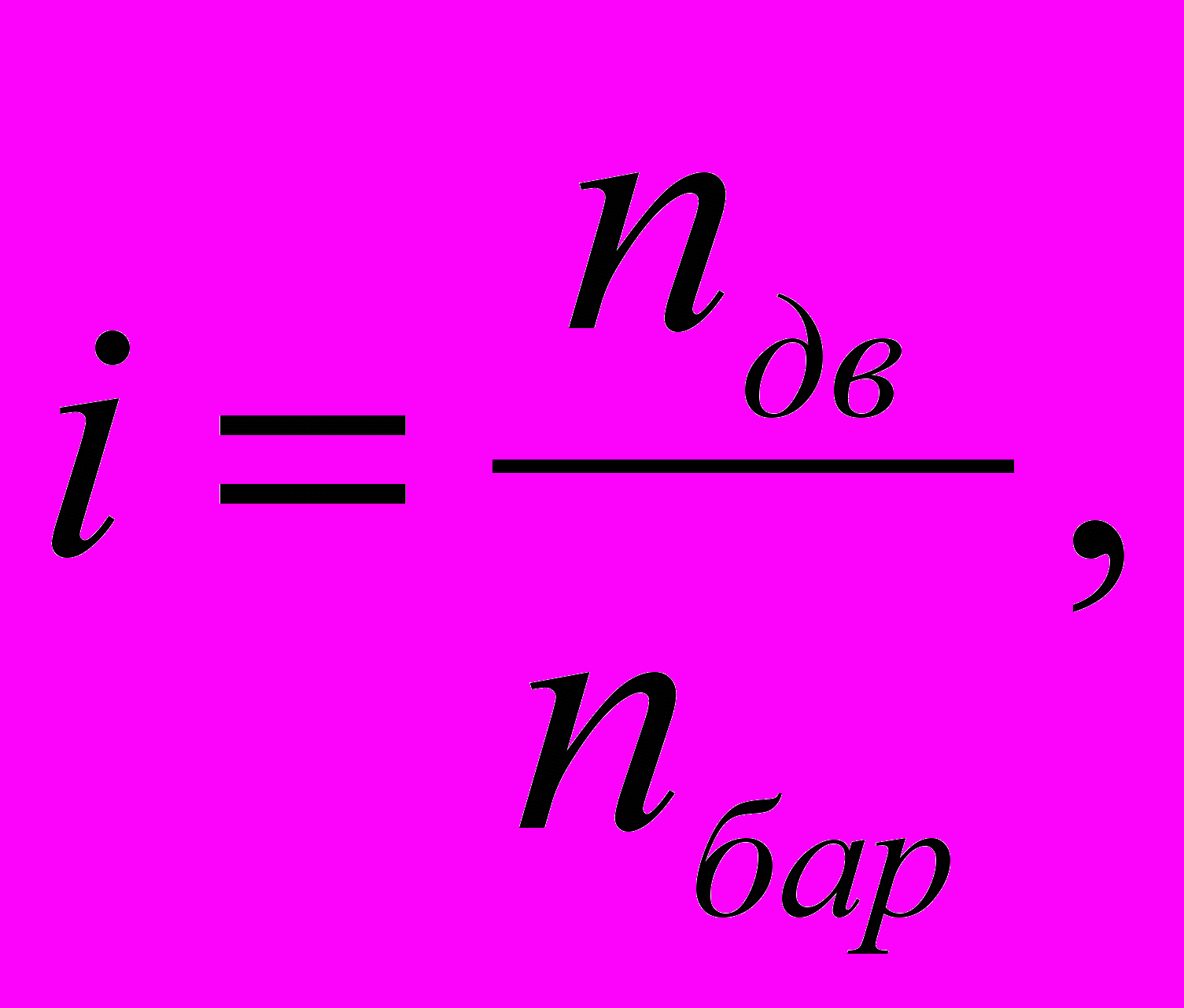
где пдв – частота вращения ротора электродвигателя, об/мин.
Значение пдв берем из таблицы Б.14 по марке подобранного электродвигателя.
пбар – частота вращения приводного барабана
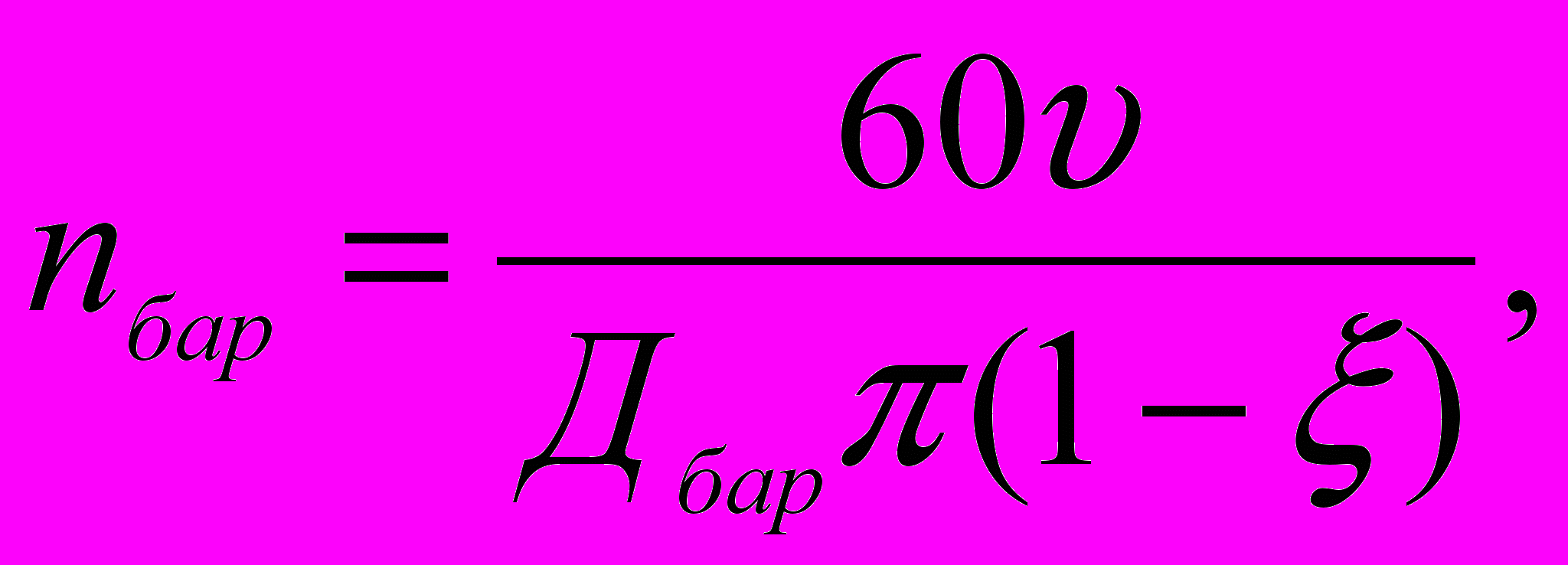
где
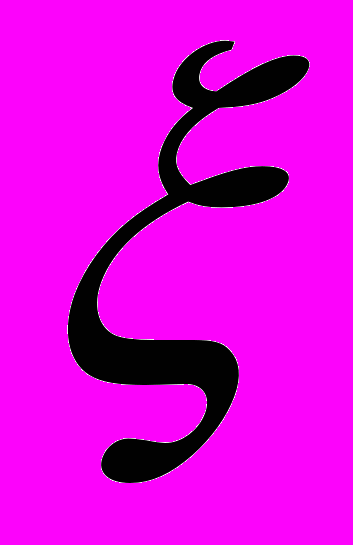
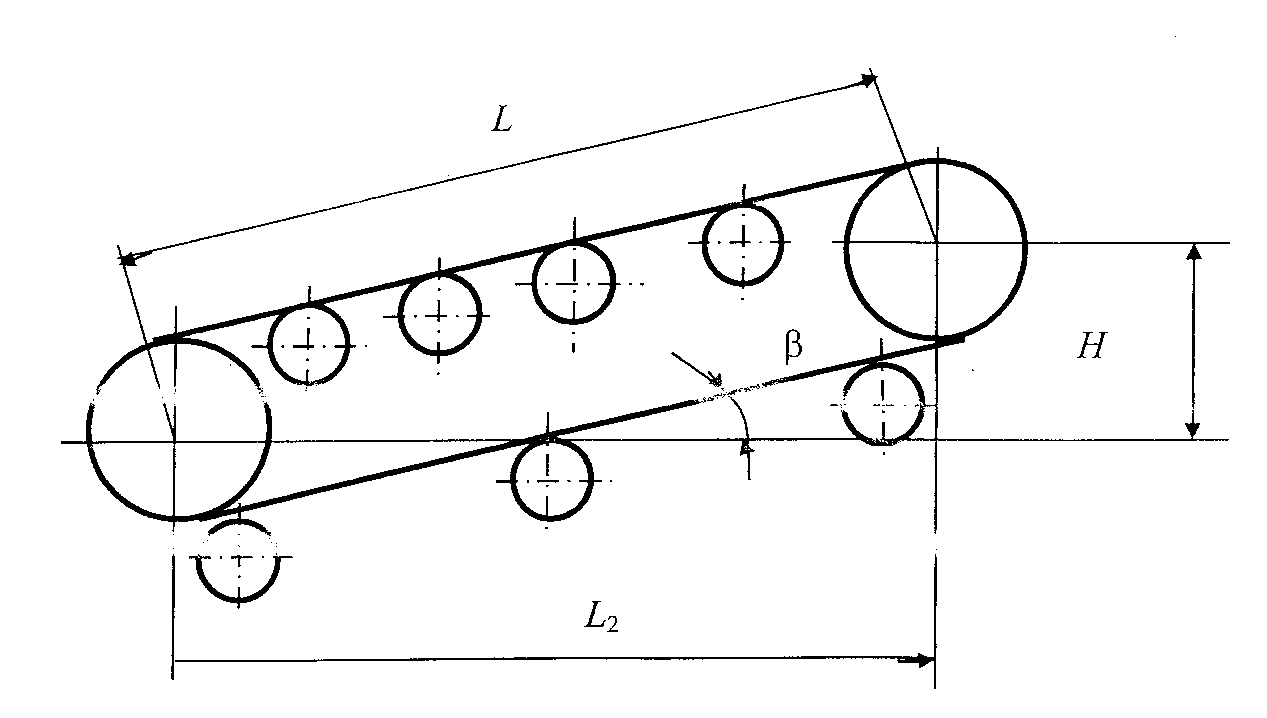
Рисунок 8.6 – Схема ленточного конвейера
Требования к содержанию и оформлению
Расчетно-пояснительная записка является одной из основных частей конструкторской документации. По объему, содержанию и оформлению записка должна быть понятной без чертежа.