Методические указания составлены в соответствии с примерной и рабочей программой учебной дисциплины «Технология сельскохозяйственного машиностроения». Обсуждены на заседании кафедры «Надежность и технический сервис машин» протокол №5 от
Вид материала | Методические указания |
- Методические указания и контрольные задания для студентов- заочников, экстерната образовательных, 211.24kb.
- Методические указания и контрольные задания для студентов заочников образовательных, 369.95kb.
- Методические указания к контрольной работе по учебной дисциплине Международные стандарты, 200.84kb.
- Методические указания по изучению дисциплины и выполнению контрольной работы Специальность, 128.89kb.
- Учебно-методический комплекс учебной дисциплины педагогический этикет часть II. Методические, 259.57kb.
- Методические указания составлены в соответствии с новой программой и предназначены, 2132.37kb.
- Методические указания и контрольные задания для студентов- заочников образовательных, 559.1kb.
- Рекомендации по организации, выполнению и защите курсового проекта дисциплина: Техническое, 1241.64kb.
- Методические указания к лабораторным работам по дисциплине: «Технология производства, 994.91kb.
- Методические рекомендации по выполнению контрольной работы студентам заочной формы, 429.26kb.
3.3. Разработка технологического маршрута обработки детали
Перед разработкой маршрута следует определить последовательность обработки поверхностей детали, которая обусловлена требованиями к их шероховатости, таблица 4 [1].
Рекомендуется разделить технологический процесс (ТП) изготовления детали на три технологических перехода:
- на первом переходе необходимо произвести черновую подрезку торцов заготовки и их зацентровку, тем самым создаются базы для обработки детали на последующих основных переходах;
- на втором переходе рекомендуется выполнить черновую обработку поверхности всей детали;
- на третьем переходе – получистовую и чистовую.
После определения маршрута обработки детали выбирается оборудование (станок), определяется метод установки и закрепления заготовки, а также выбираются приспособления, режущий и мерительный инструменты.
Длину заготовки можно принять равной длине детали плюс припуски на подрезку торцов. Диаметр заготовки определяется как ближайший большой из сортамента стального круглого проката (таблица 2).
3.4. Выбор и описание оборудования
В данной работе рекомендуется использовать универсальные токарно-винторезные станки, технические характеристики которых приводятся в справочной литературе [2]. Модель станка выбирают с учетом габаритных размеров заготовки. При этом внутренний диаметр шпинделя станка должен быть больше диаметра круглого проката заготовки.
3.5. Выбор и описание режущего инструмента
Выбор режущего инструмента следует начинать с определения марки материала его режущей части по справочной литературе [2]. Рекомендуемое сечение державки 16х20, угол φ 45º для чернового прохода и угол φ 90º для получистового и чистового прохода с уступом. Материал режущей части Т15К6 или Р6М5.
3.6. Выбор измерительных средств
Конкретное средство измерений и условий его применения выбирают сравнением допустимой и предельной погрешности измерения. Результаты измерений признаются достоверными, если предельная погрешность не превышает установленную величину допустимой погрешности измерения. Допустимая погрешность измерения составляет приблизительно 30% от величины допуска на измеряемый размер. Погрешности измерения различными инструментами приводятся в таблице 5.
3.7. Определение режимов резания (таблица 6)
Режимы резания устанавливаются в следующем порядке:
- определяют глубину резания t,мм; для черновой обработки t max= 8-10 мм для получистовой обработки t =0,5-2 мм, для чистового точения t= 0,1- 0,4 мм
- выбирают подачу S, мм/об;
- определяют с учетом выбранного периода стойкости инструмента (принимаем Т=60 мин) скорость резания V, м/мин.
Скорость резания также как мощность определяется аналитическим путем. Их приблизительные значения можно определить по таблицам, что допустимо в данной контрольной работе.
Зацентровку деталей следует производить при скорости резания 12-25 м/мин и подачей 0,03 мм/об. Время на перемещение пиноли задней бабки можно принять равным времени перемещения суппорта станка, мин. (табл. 8).
3.10. Определение трудоемкости технологической операции
Норма времени может устанавливаться на любой объем работы: отдельную операцию, группу операций, законченный комплект работ и т.д. Структуру штучного времени можно представить формулой:
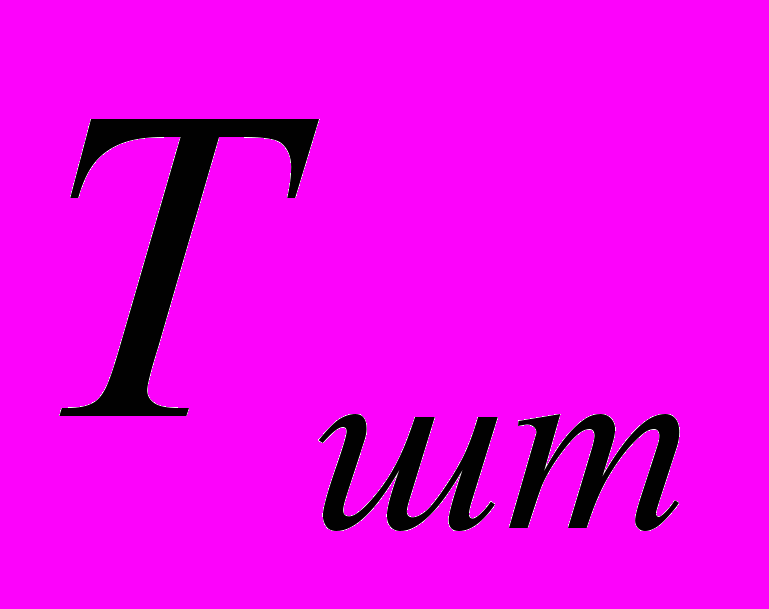
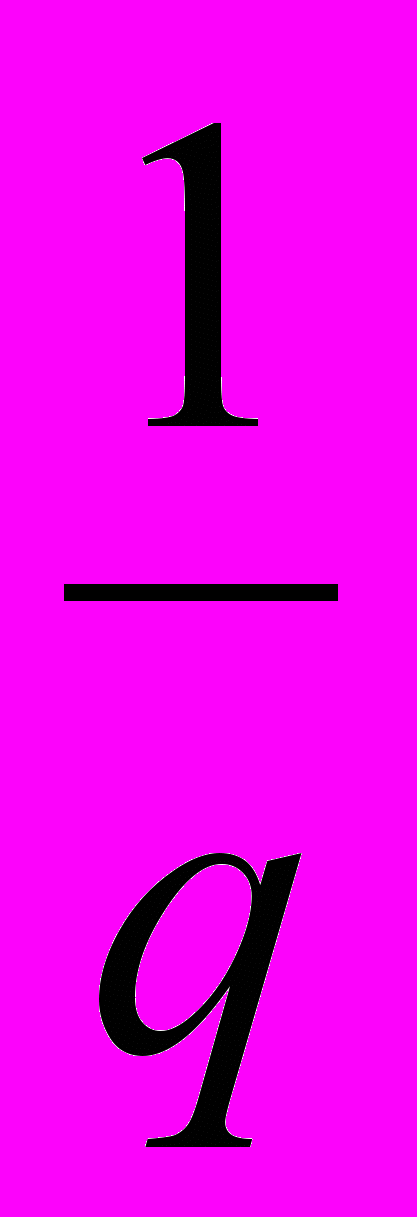
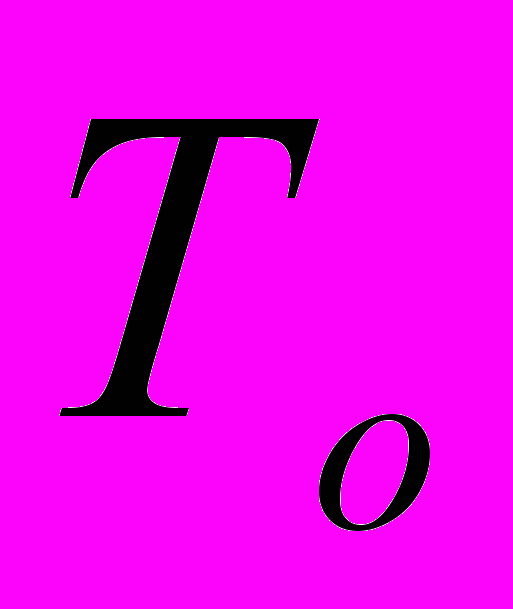
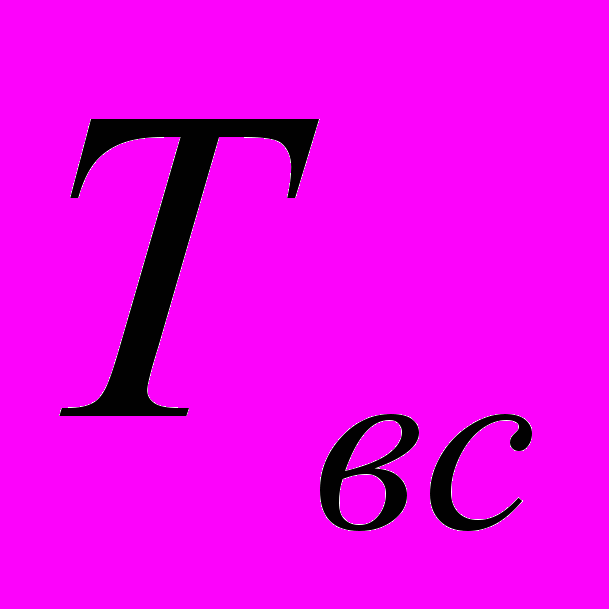
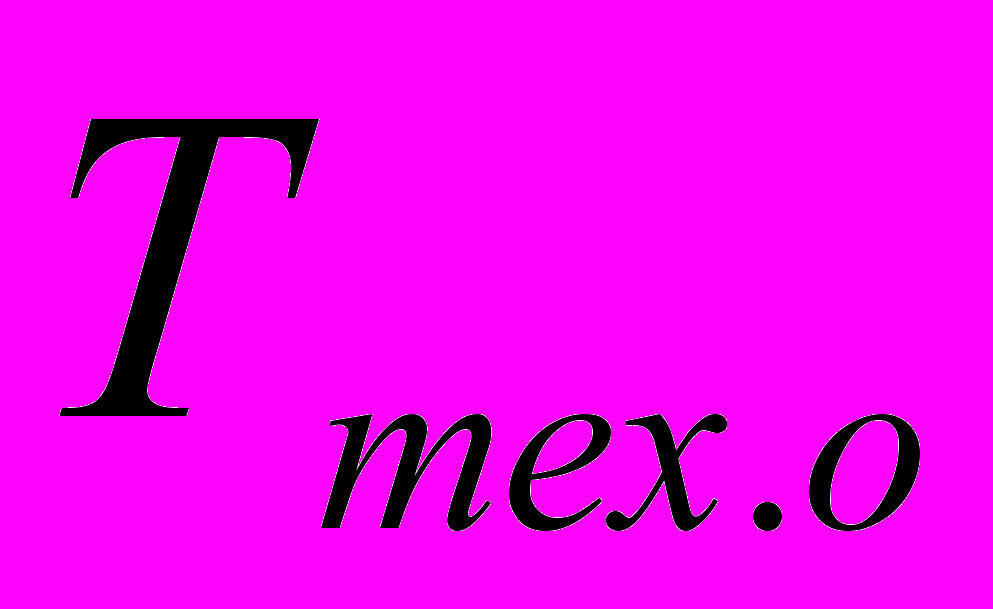
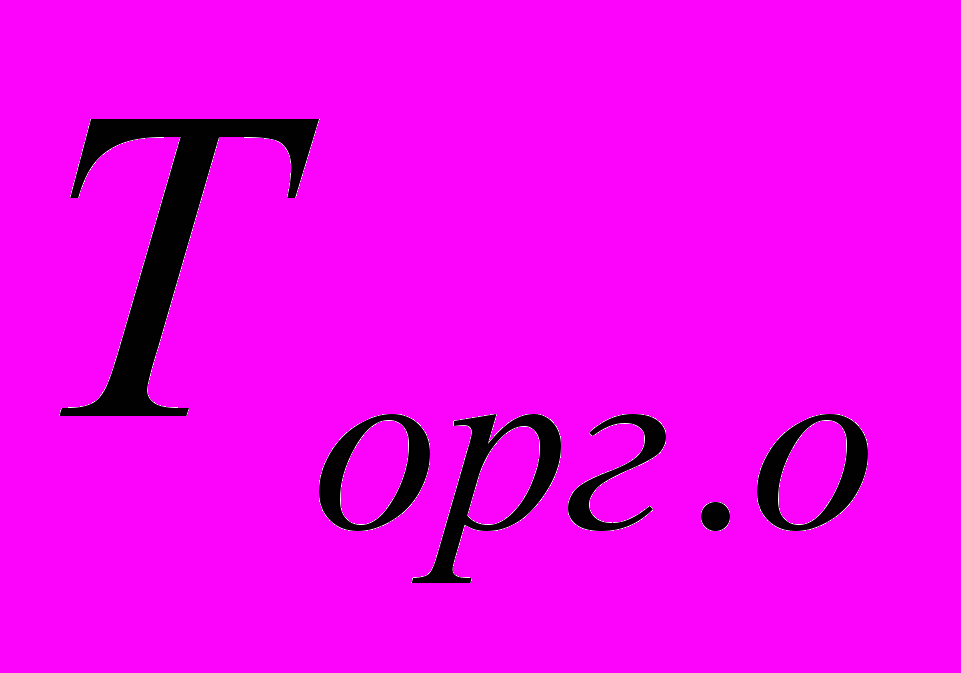
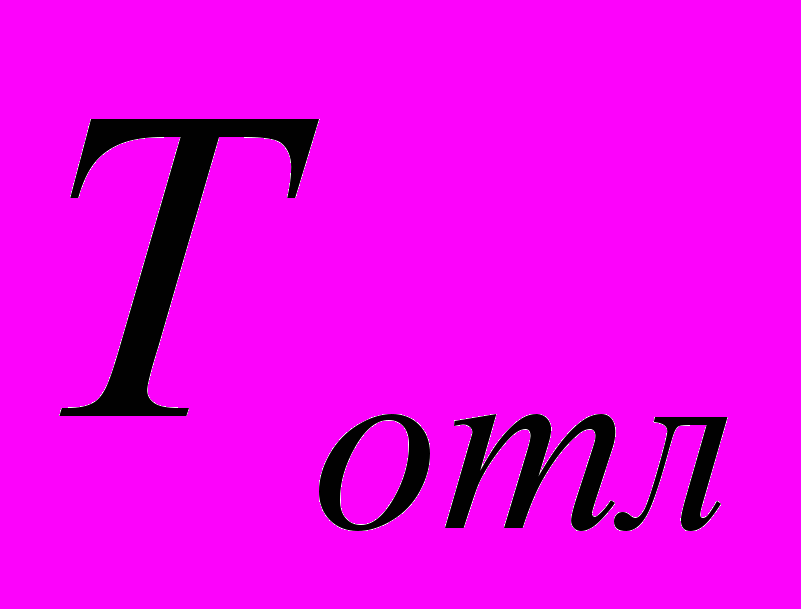
где
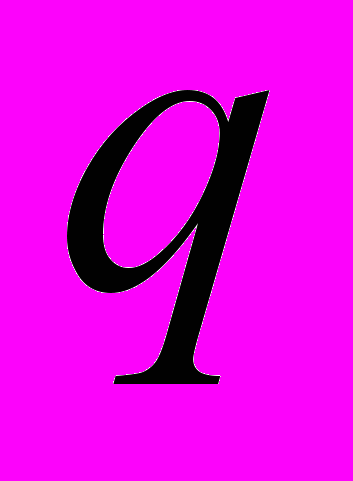
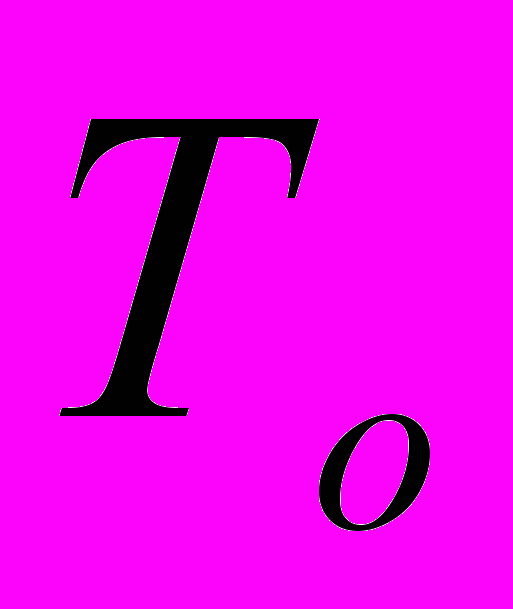
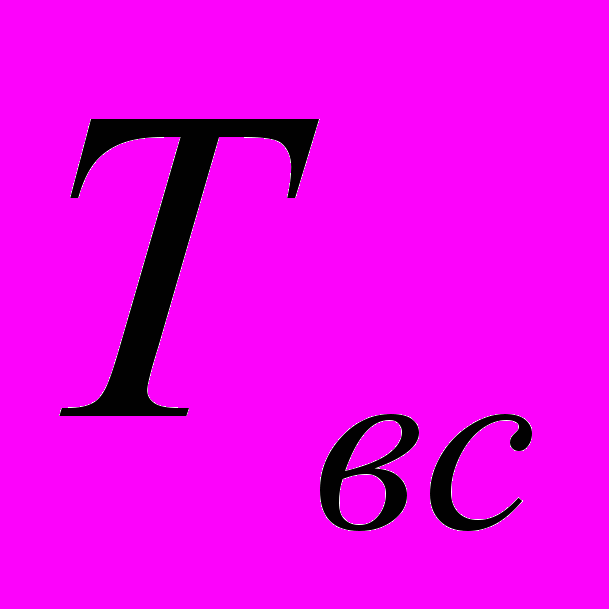
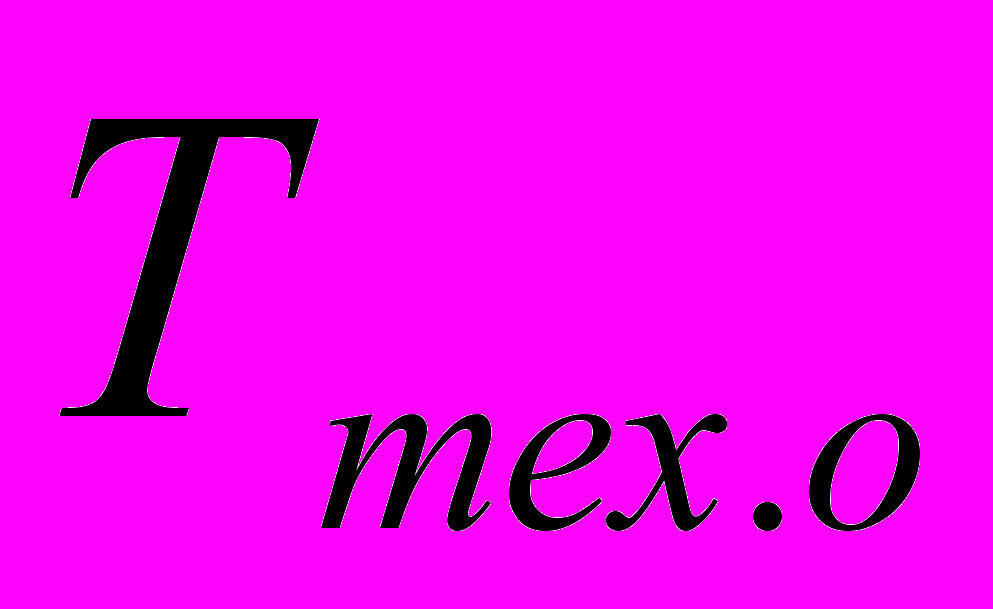
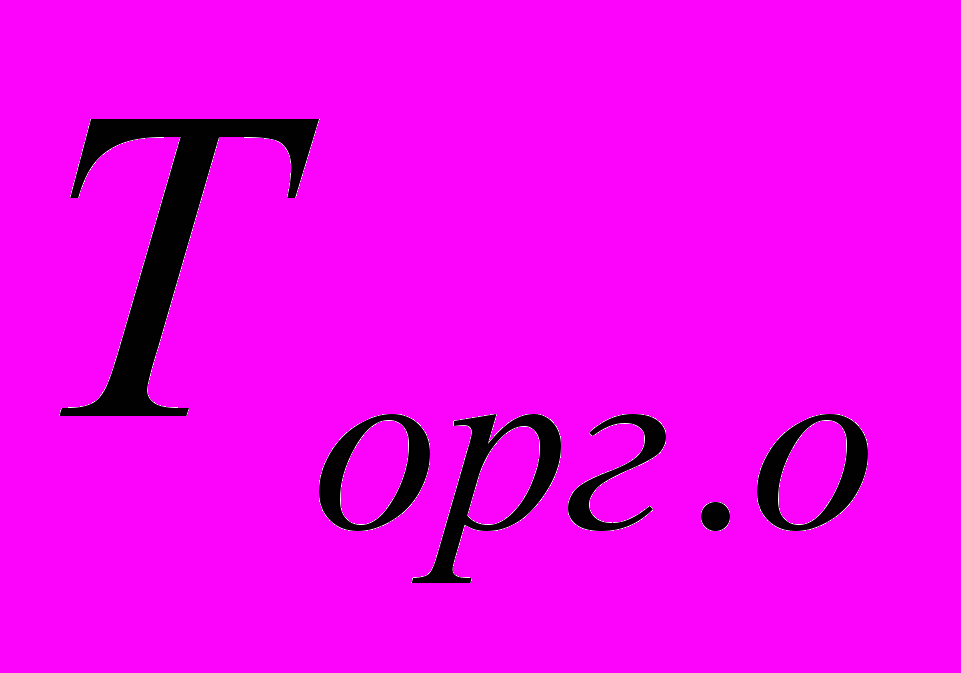
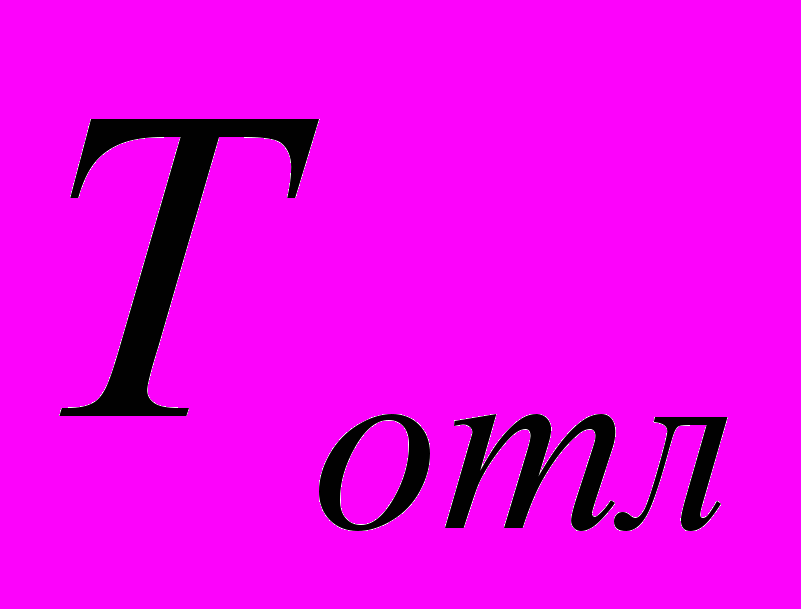
Выполняя контрольную работу, при определении
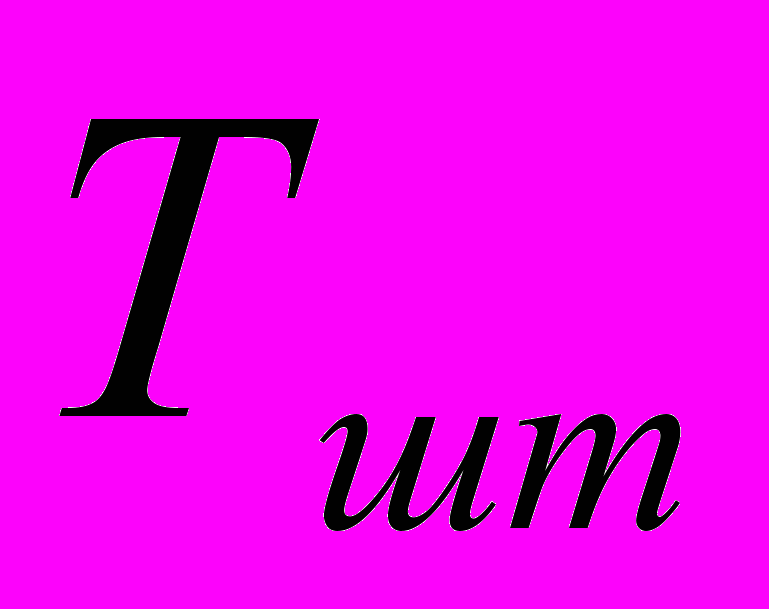
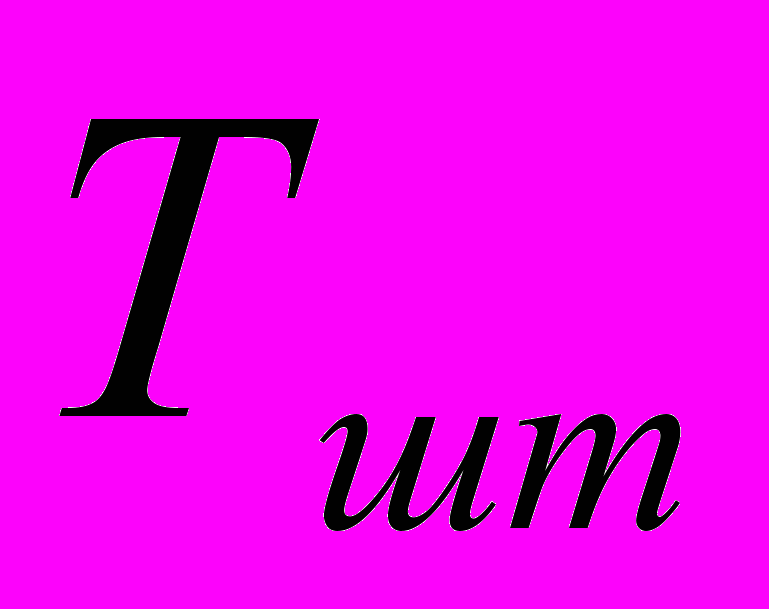
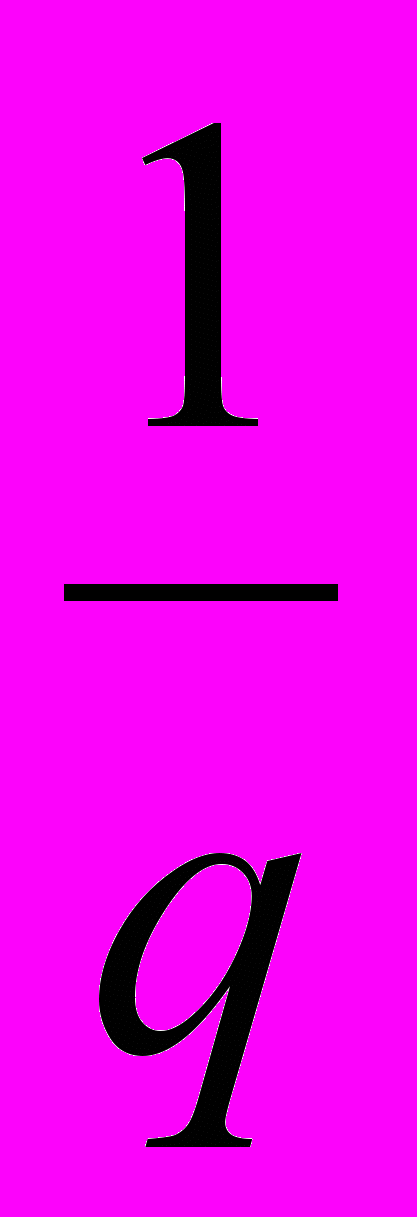
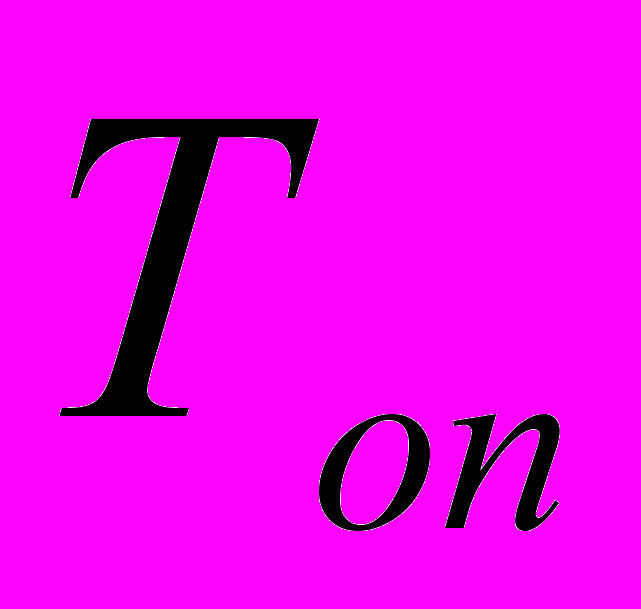
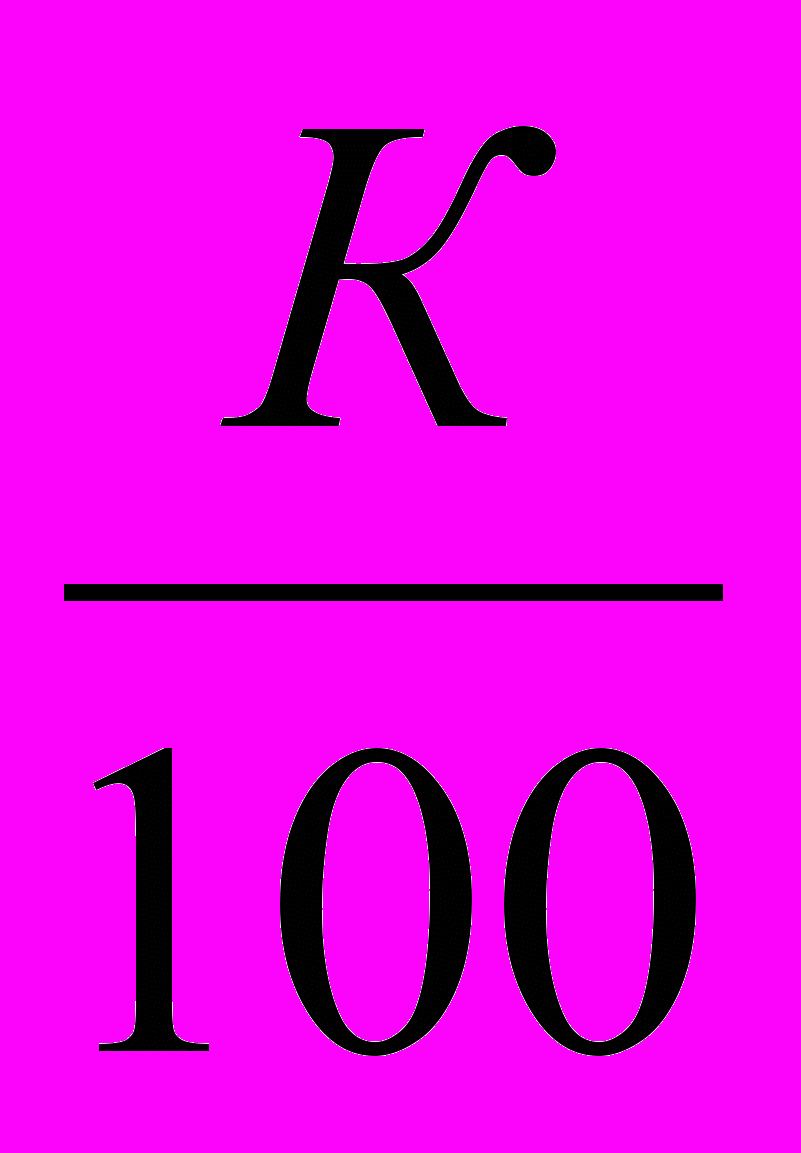
где
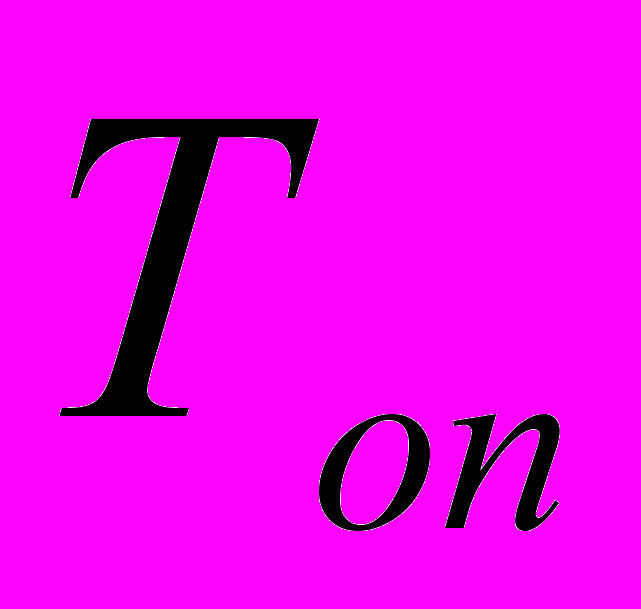
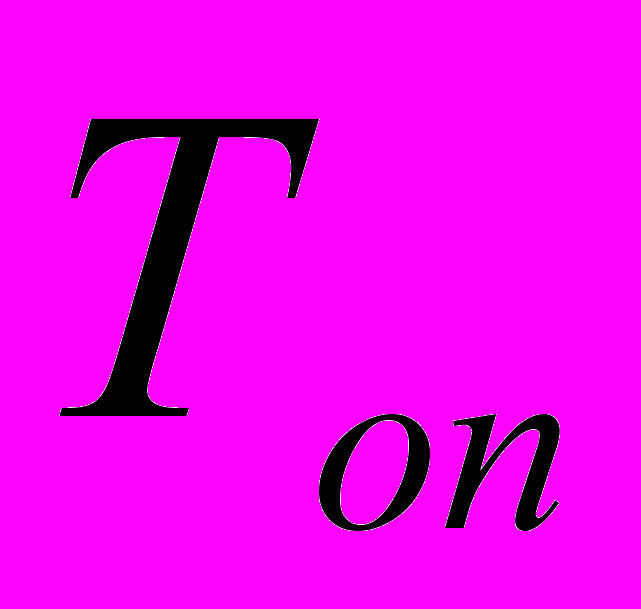

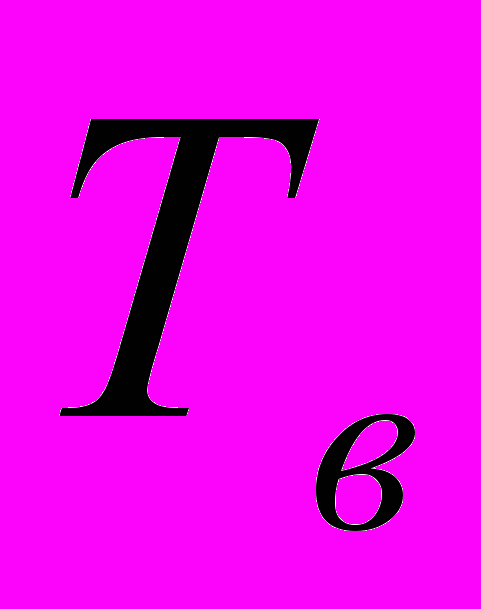
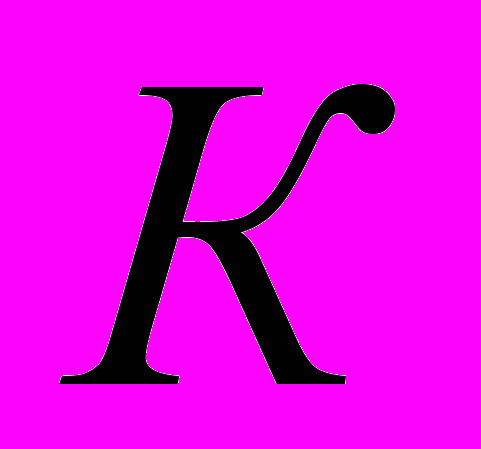
После определения содержания переходов, выбора оборудования, инструментов и режимов резания, нормы времени определяются в такой последовательности:
- на основании выбранных режимов по каждому переходу вычисляется
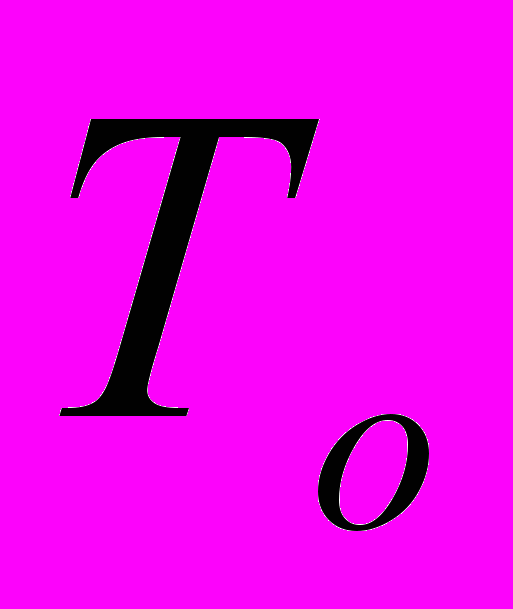
- по содержанию каждого перехода устанавливается необходимый комплекс вспомогательной работы и определяется вспомогательное время
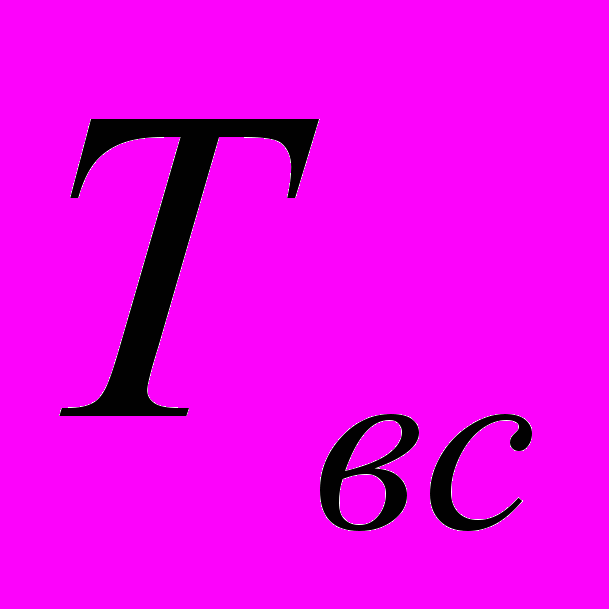
Таблица 5.
Предельные погрешности измерения различными измерительными инструментами
Измерительный инструмент | Условия измерения | Предельные погрешности измерения (±), мкм для диапазонов размеров, мм | ||||||||
Наименование | Виды контакта и установки инструмента | 0-25 | 25-50 | 50-75 | 75-100 | 100-125 | 125-150 | 150-175 | 175-200 | 200-250 |
Штангенциркули с отчетом по нониусу 0,05 мм | – | 80 | 80 | 90 | 90 | 100 | 100 | 100 | 100 | 100 |
Штангенциркули с отчетом по нониусу 0,10 мм | – | 150 | 150 | 160 | 170 | 170 | 190 | 190 | 200 | 200 |
Микрометры гладкие, при настройке на нуль по установочной мере | Все виды контактов, микрометр находится в руках | 5,5 | 7,5 | 9,5 | 12 | 14 | 16 | 18 | 22 | 25 |
Таблица 6
Режимы резания при точении конструкционных сталей
Глубина резания t, мм | Подача, S мм/об | Скорость резания, м/мин | |||||||
Т15К10 | Р6М5 | ||||||||
φ = 45º | φ = 90º | φ = 45º | φ = 90º | ||||||
V, м/мин | Np, кВт. | V, м/мин | Np, кВт. | V, м/мин | Np, кВт. | V, м/мин | Np, кВт. | ||
1,0 | 0,15 0,30 0,50 | 203 175 167 | 1,0 1,5 2,4 | 164 141 147 | 0,7 1,1 2,0 | 120 90 65 | 0,8 1,1 1,1 | 79 59 43 | 0,6 0,8 0,8 |
1,5 | 0,15 0,30 0,50 | 190 164 138 | 1,5 2,2 2,7 | 153 133 111 | 1,1 1,6 2,0 | 110 81 58 | 1,2 1,5 1,5 | 72 53 38 | 0,85 1,0 1,1 |
2,0 | 0,20 0,30 0,50 | 173 159 133 | 2,2 2,8 3,6 | 139 128 107 | 1,6 2,0 2,6 | 91 76 55 | 1,6 1,8 1,9 | 60 50 36 | 1,1 1,3 1,3 |
3,0 | 0,20 0,30 0,50 | 162 149 125 | 3,2 4,0 5,1 | 131 120 101 | 2,3 2,9 3,7 | 83 69 49 | 2,2 2,4 2,6 | 54 45 32 | 1,6 1,7 1,8 |
4,0 | 0,30 0,50 1,0 | 143 120 92 | 5,2 6,5 8,7 | 115 97 74 | 3,7 4,7 6,3 | 64 45 36 | 3,0 3,1 4,5 | 42 30 18,5 | 2,1 2,3 2,4 |
6,0 | 0,30 0,50 1,0 | 134 112 86 | 6,4 9,3 12,4 | 108 91 48 | 5,3 6,7 8,9 | 58 42 26 | 4,2 4,3 4,5 | 38 27 11 | 3,0 3,1 3,2 |
8,0 | 0,40 0,30 1,5 | 116 96 68 | 10,7 14,0 18,5 | 86 78 49 | 7,7 10,0 15,0 | 45 31 18,7 | 5,3 5,6 6,0 | 30 20 12,4 | 3,8 3,95 4,3 |
В данной контрольной работе следует разделить вспомогательное время на две части: время
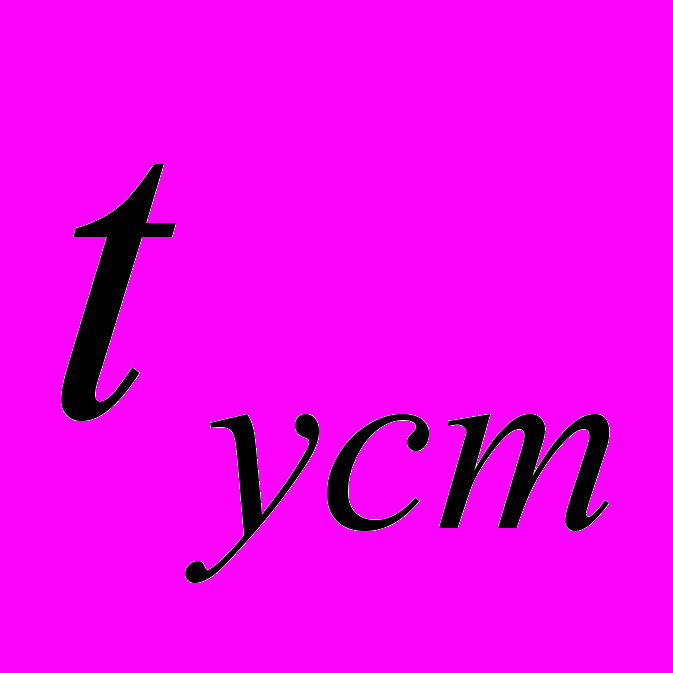
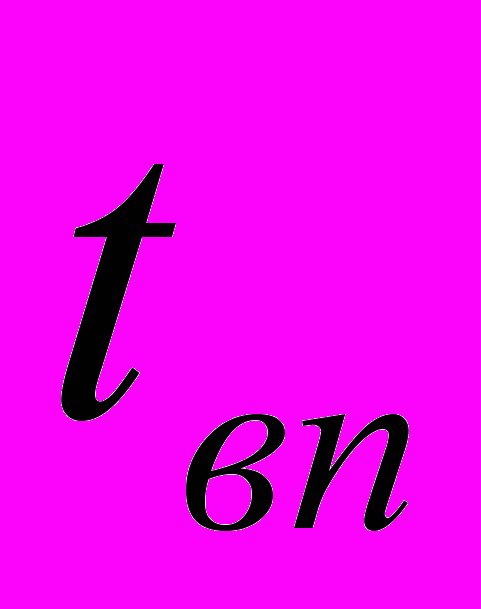

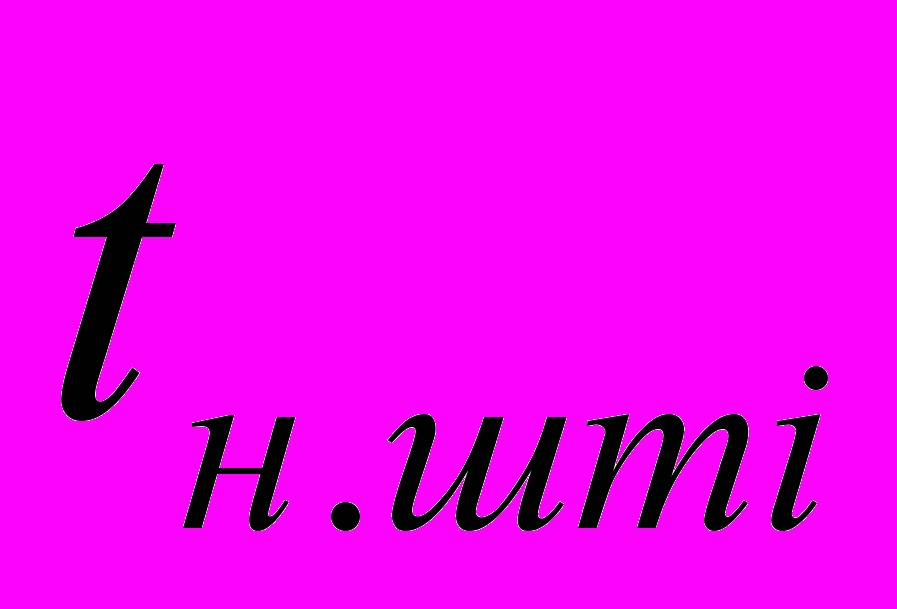

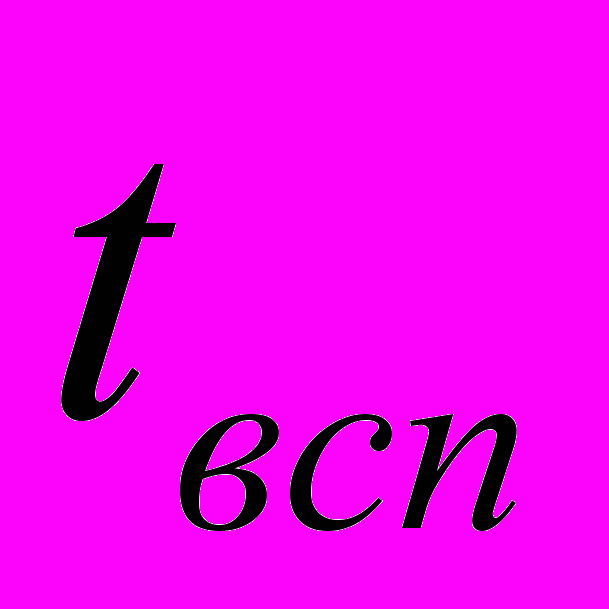
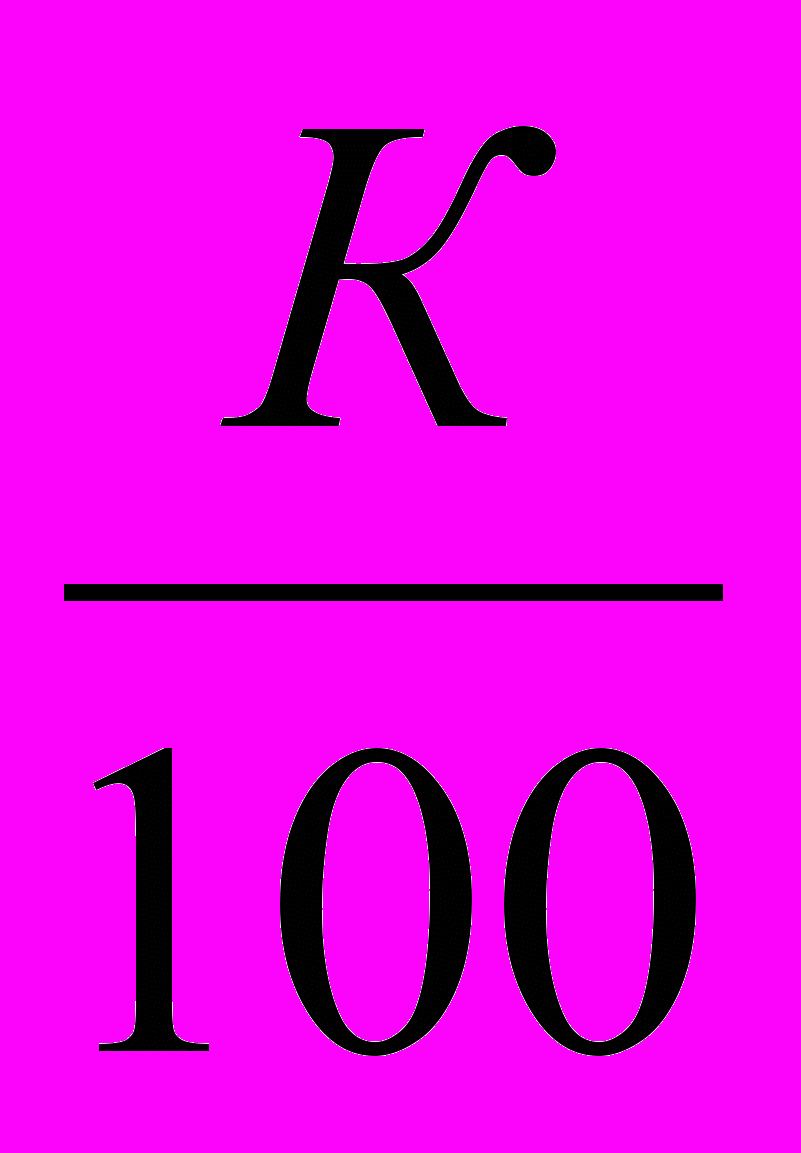
В этом случае штучное время операции будет равно:
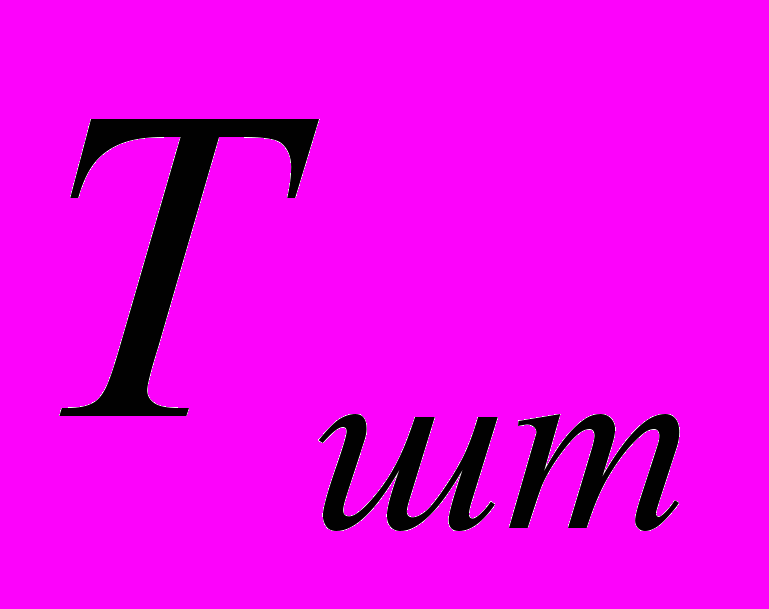
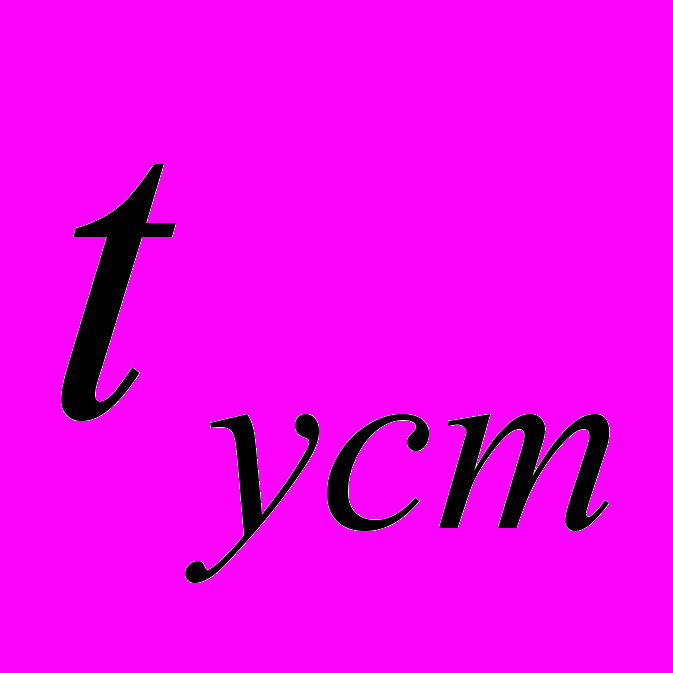
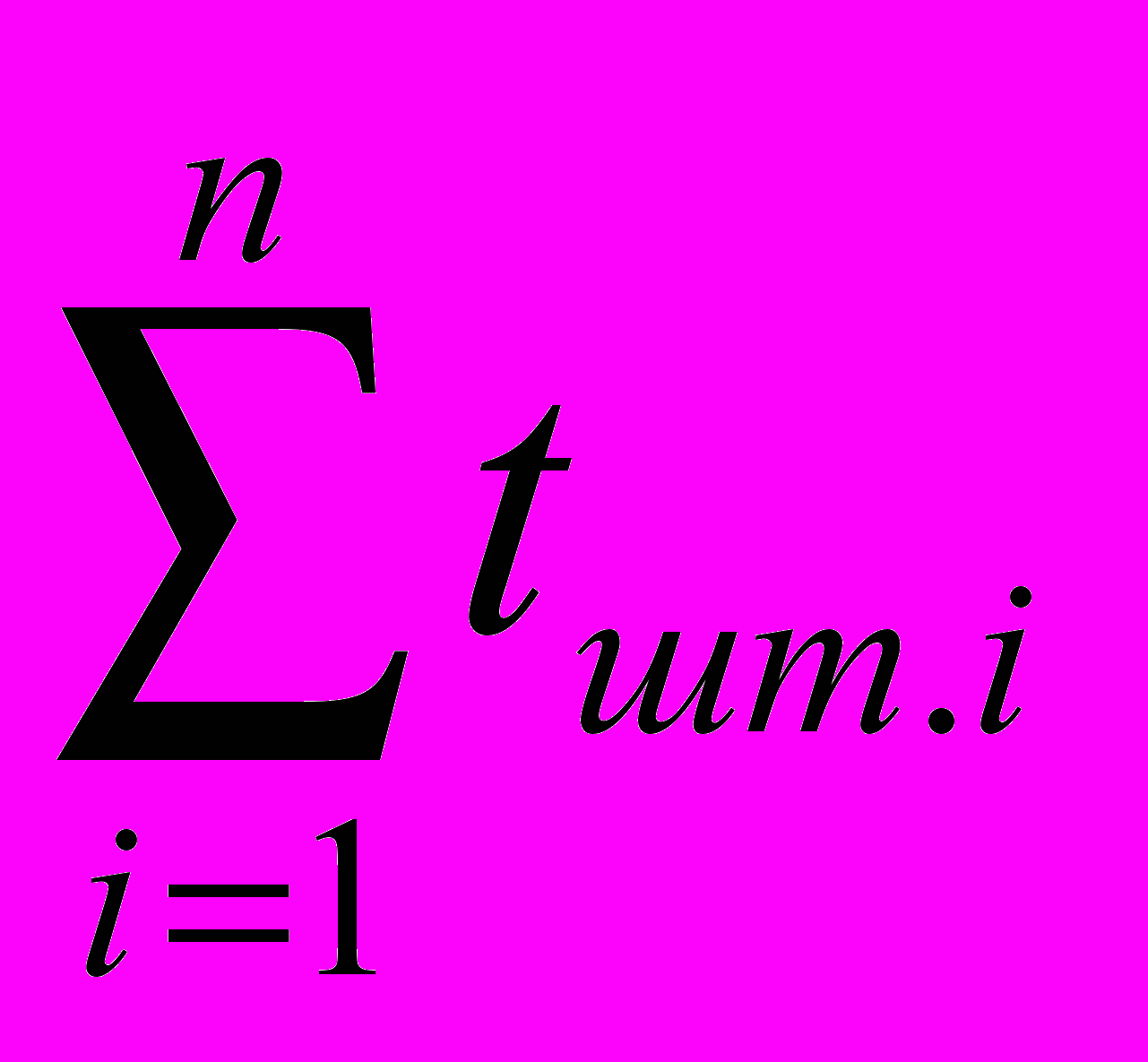
где
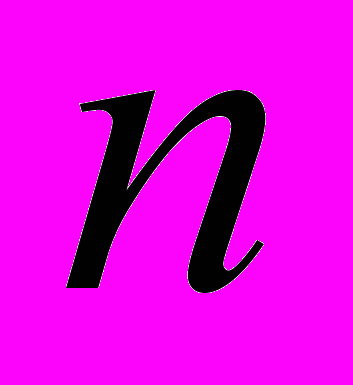
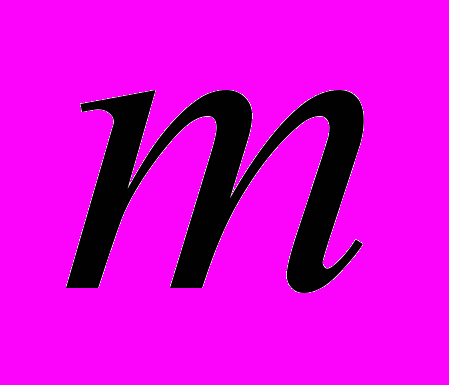
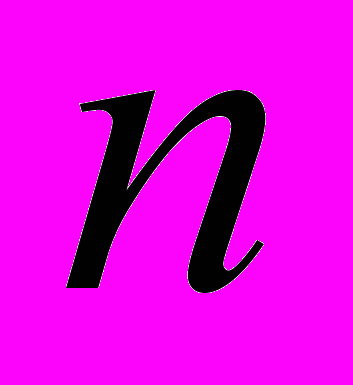
Определение основного времени
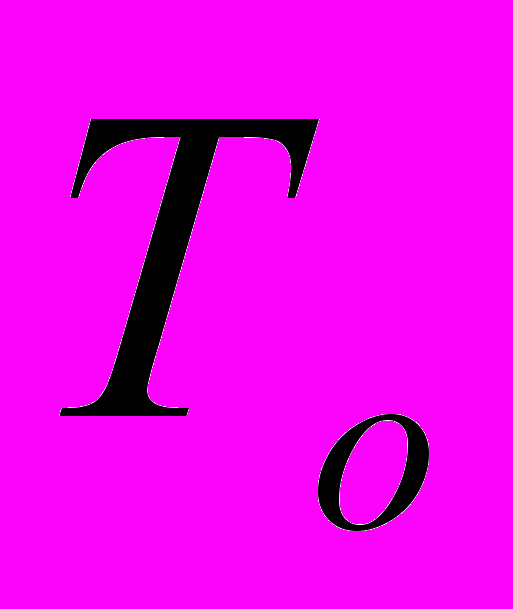
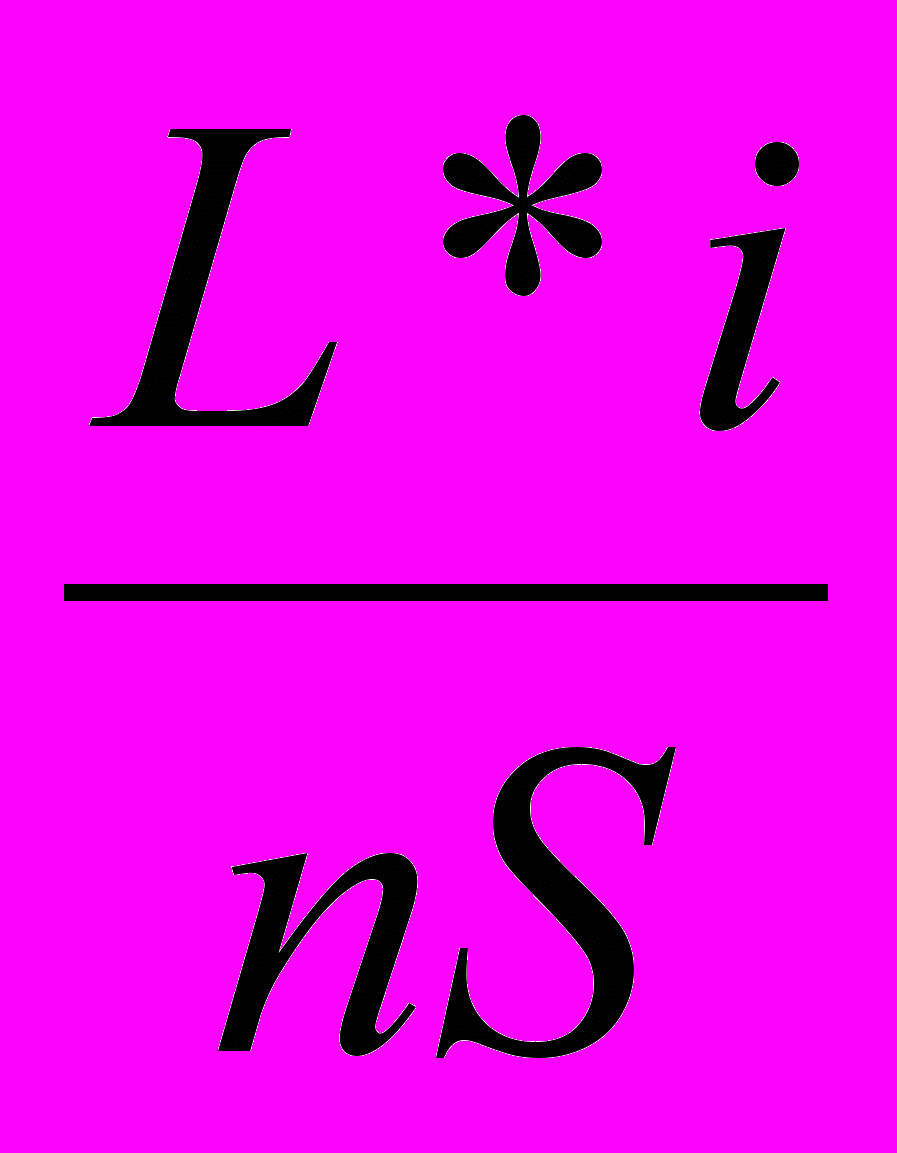
где
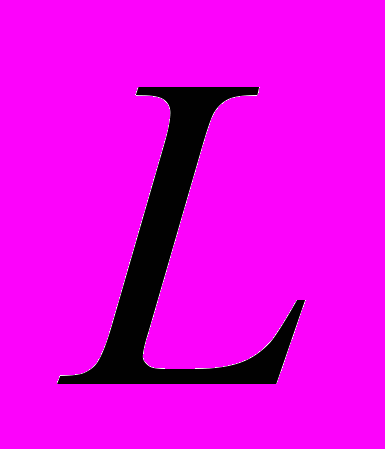
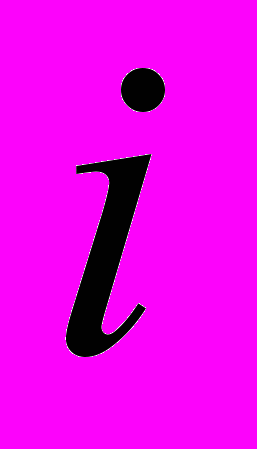
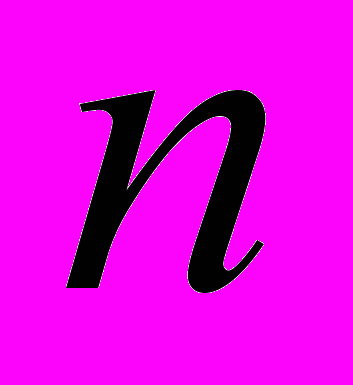
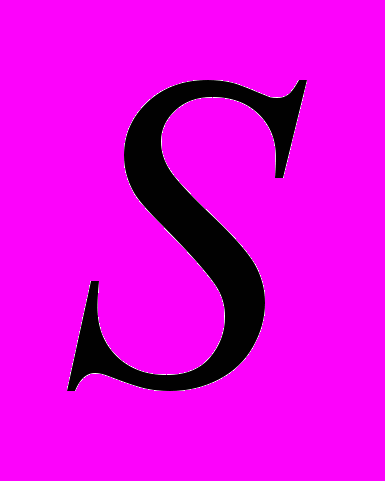
Условная длина обработки определяется по формуле:
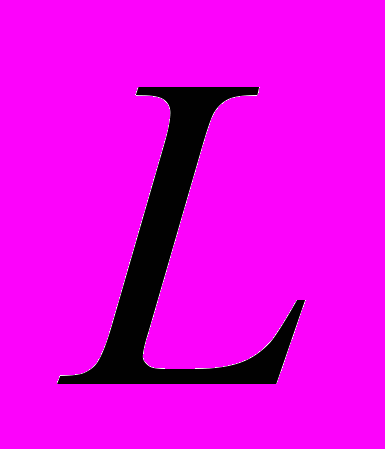
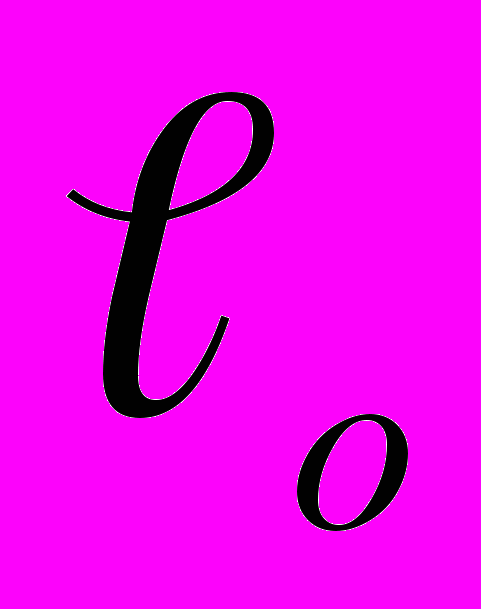

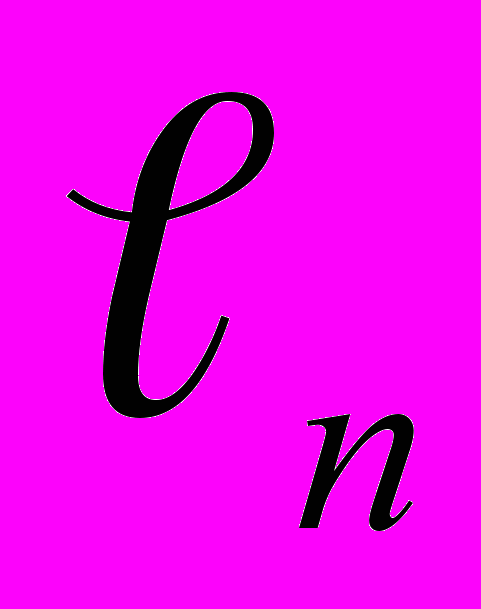
где
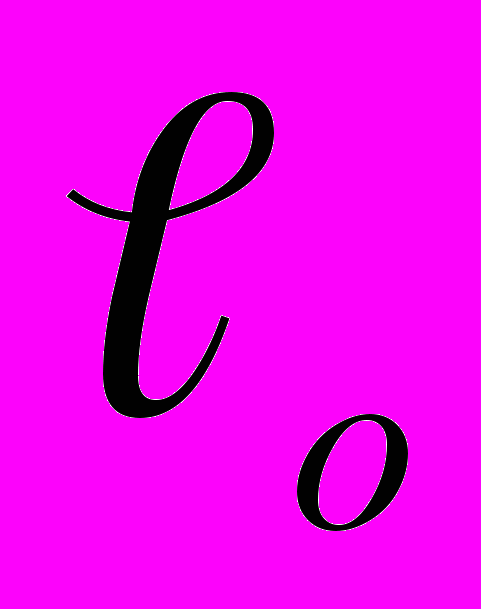
подачи, мм;
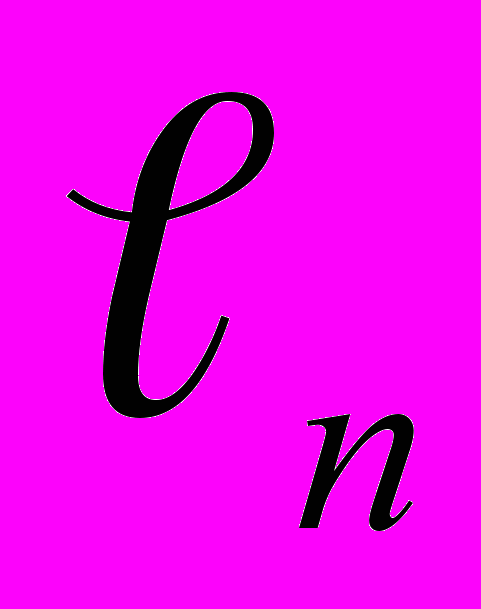


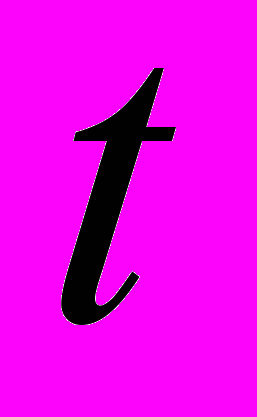
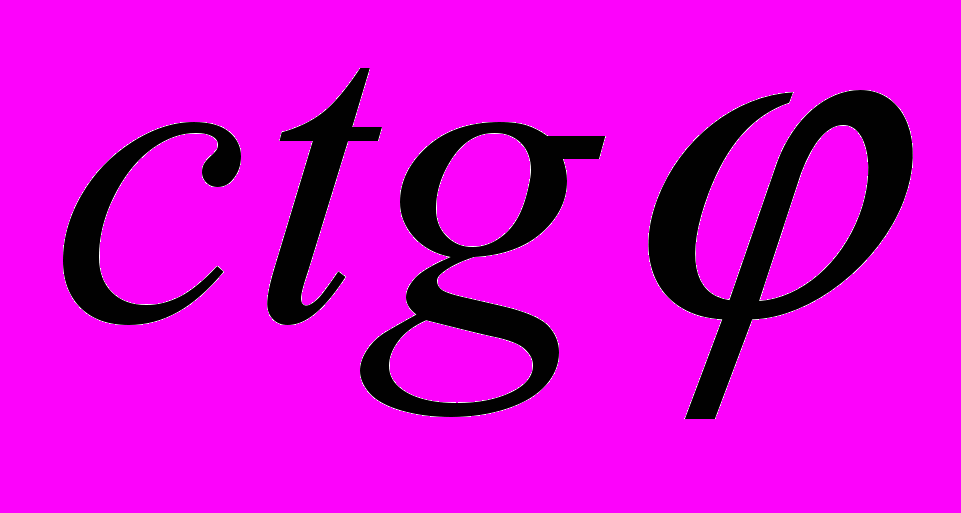
где
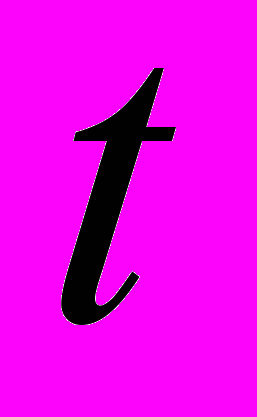
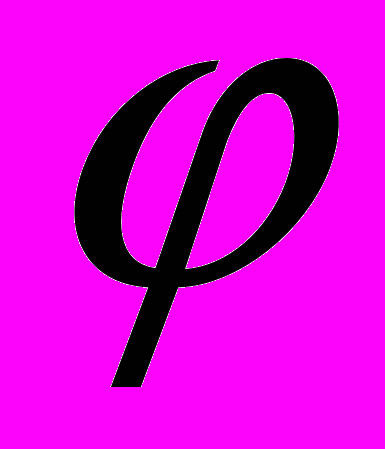
частота вращения детали определяется по формуле:
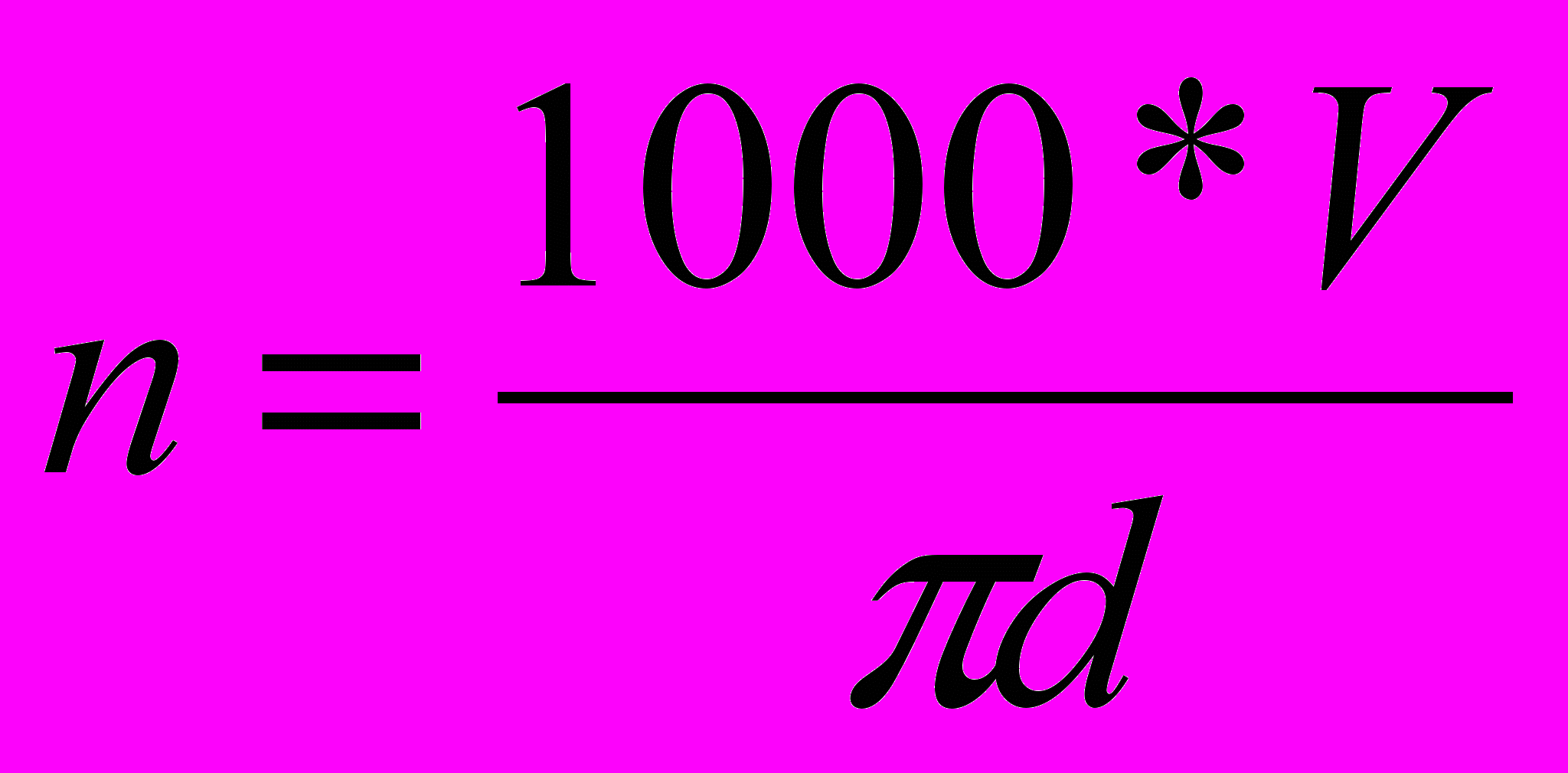
Определение вспомогательного времени
Вспомогательное время определяется по содержанию каждого перехода по таблицам, 7, 8, 9, 10 извлеченными из общемашиностроительных нормативов.
Таблица 7
Вспомогательное время на установку и снятие детали, мин.
№№ ПП | Способ установки детали | Условия выполнения работы | Масса детали, кг | |||||||
0,25 | 0,5 | 1 | 3 | 5 | 8 | 12 | 20 | |||
1. | В центрах | Без надевания хомутика | 0,16 | 0,17 | 0,18 | 0,20 | 0,24 | 0,26 | 0,29 | 0,34 |
2. | В центрах | С надеванием хомутика | 0,24 | 0,25 | 0,27 | 0,30 | 0,34 | 0,40 | 0,48 | 0,60 |
3. | В центрах с ведущим передним центром | | 0,17 | 0,18 | 0,19 | 0,22 | 0,26 | – | – | – |
4. | В самоцентри-рующем патроне | С креплением ключом, без выверки | 0,16 | 0,17 | 0,18 | 0,19 | 0,22 | 0,26 | 0,32 | 0,39 |
Окончание таблицы 7
5. | В самоцентри-рующем патроне | С креплением ключом. С выверкой по мелу | 0,37 | 0,39 | 0,41 | 0,44 | 0,52 | 0,60 | 0,70 | 0,85 |
6. | В патроне с пневматическим зажимом | | 0,10 | 0,11 | 0,12 | 0,13 | 0,14 | 0,16 | 0,19 | 0,24 |
Примечание: Время на переустановку детали принимать равным времени на установку и снятие детали.
Таблица 8
Время на проход при продольной и поперечной обточке, мин.
№№ ПП | Наименование приемов | Высота центров станка в мм | |||
125 | 200 | 300 | 500 | ||
1. | Установка резца на стружку по лимбу с точностью 0,2 мм | 0,15 | 0,17 | 0,20 | 0,28 |
2. | Установка резца по упору или лимбу грубо | 0,13 | 0,15 | 0,18 | 0,24 |
3. | Со взятием одной пробной стружки (JT10-JT11) | 0,37 | 0,40 | 0,46 | 0,57 |
4. | Со взятием двух пробных стружек (JT8-JT9) | 0,78 | 0,81 | 0,89 | 1,05 |
5. | Перемещение суппорта, ручное на расстоянии до 500 мм 1000 мм | 0,02 0,06 | 0,02 0,08 | 0,03 0,12 | 0,06 0,18 |
6. | Изменить частоту вращения шпинделя Изменить величину или направление подачи Сменить резец поворотом резцовой головки | 0,07 0,05 0,07 | 0,07 0,05 0,07 | 0,08 0,06 0,07 | 0,08 0,06 0,08 |
7. | Закрыть или открыть щиток ограждения от стружки Включить или выключить вращение шпинделя | 0,02 0,02 | 0,02 0,02 | 0,03 0,02 | 0,03 0,02 |
При обработке поверхностей JT1-JT9 рекомендуется 100% контроль размеров. При более грубой обработке 60%.
Оперативное время перехода на снятие фасок можно определить по таблице 10.
Таблица 9
Вспомогательное время на контрольные промеры, мин.
№№ ПП | Измерительный инструмент | Точность измерения | Измеряемый диаметр, мм | Измеряемая длина, мм | |||||
50 | 100 | 200 | 300 | 500 | 1000 | ||||
1. | Линейка, метр | | | 0,06 | 0,07 | 0,08 | 0,09 | 0,10 | 0,13 |
2. | Штангенциркуль | 0,05-0,1 | 50 | 0,12 | 0,15 | 0,18 | 0,20 | 0,24 | 0,28 |
3. | Микрометр | 0,01 | 100 | 0,22 | 0,22 | 0,23 | 0,28 | 0,33 | 0,37 |
Таблица 10
Оперативное время на снятие фасок, мин.
Ширина фаски, мм | Диаметр обрабатываемой поверхности | |||||||
50 | 100 | 200 | 300 | 400 | 500 | 600 | 800 | |
2 | 0,14 | 0,18 | 0,20 | 0,20 | 0,20 | 0,30 | 0,30 | 0,40 |
3 | 0,16 | 0,20 | 0,30 | 0,30 | 0,30 | 0,40 | 0,40 | 0,40 |