Методические указания составлены в соответствии с примерной и рабочей программой учебной дисциплины «Технология сельскохозяйственного машиностроения». Обсуждены на заседании кафедры «Надежность и технический сервис машин» протокол №5 от
Вид материала | Методические указания |
- Методические указания и контрольные задания для студентов- заочников, экстерната образовательных, 211.24kb.
- Методические указания и контрольные задания для студентов заочников образовательных, 369.95kb.
- Методические указания к контрольной работе по учебной дисциплине Международные стандарты, 200.84kb.
- Методические указания по изучению дисциплины и выполнению контрольной работы Специальность, 128.89kb.
- Учебно-методический комплекс учебной дисциплины педагогический этикет часть II. Методические, 259.57kb.
- Методические указания составлены в соответствии с новой программой и предназначены, 2132.37kb.
- Методические указания и контрольные задания для студентов- заочников образовательных, 559.1kb.
- Рекомендации по организации, выполнению и защите курсового проекта дисциплина: Техническое, 1241.64kb.
- Методические указания к лабораторным работам по дисциплине: «Технология производства, 994.91kb.
- Методические рекомендации по выполнению контрольной работы студентам заочной формы, 429.26kb.
Тема 8. Проектирование технологической оснастки
Назначение и классификация станочных приспособлений. Установочные элементы (опоры) приспособлений. Элементы для установки и ориентирования инструмента. Зажимные элементы и механизмы приспособлений. Применение пневматического и гидравлического привода в приспособлениях. Вспомогательные элементы и корпуса приспособлений. Приспособления для токарных, сверлильных, фрезерных и шлифовальных станков.
Тема 9. Обработка деталей класса «круглые стержни»
Классификация деталей класса "круглые стержни". Материалы, применяемые для изготовления валов сельскохозяйственных машин. Технические требования по точности и шероховатости поверхности.
Подготовка заготовок к обработке. Правка прутков. Резка заготовок. Подрезка, торцов, центровка валов. Обработка валов на токарных (многорезцовых, револьверных) станках. Обработка конструктивных элементов валов (криволинейные, и конические поверхности, шпоночные канавки, резьбы и др.). Изготовление эксцентричных и коленчатых валов.
Тема 10. Обработка деталей классов «полые цилиндры» и «диски»
Классификация деталей класса "полые цилиндры". Материалы, применяемые для изготовления втулок с.-х. машин. Технические требования по точности и шероховатости поверхности. Заготовки для втулок. Схемы обработки втулок.
Типовая технология обработки втулок. Контроль втулок. Классификация деталей класса "диски". Материалы, применяемые для изготовления шкивов и маховиков. Типовая технология обработки шкивов и маховиков. Статическая балансировка маховиков.
Тема 11. Обработка шлицевых деталей
Преимущества шлицевых соединений. Виды центрирования. Обработка шлицевых деталей при центрировании по наружному, внутреннему диаметрам и по боковым поверхностям. Методы образования шлицев на валах и во втулках при различных типах производства. Преимущества центрирования по наружному диаметру. Контроль шлицевых деталей.
Тема 12. Обработка зубчатых колес
Материалы, применяемые для изготовления зубчатых колес. Технические требования на зубчатые колеса. Заготовки зубчатых колес. Обработка заготовок. Нарезание цилиндрических зубчатых колес дисковой, пальцевой„ червячной фрезами, долбяком, долбежными головками. Накатка зубьев. Типовые методы обработки зубьев цилиндрических колес с внутренними и наружными зубьями. Методы окончательной обработки зубчатых колес.
Тема 13. Обработка червяков и червячных колес
Материалы для изготовления червяков и червячных колес. Технические требования на червяки и червячные колеса. Разновидности червяков. Обработка червяков. Нарезание цилиндрических червяков различных типов (резцами, дисковой фрезой, «вихревым» способом). Окончательная обработка червяков. Обработка червячных колес. Нарезание червячных колес дисковой модульной фрезой, червячной фрезой, с радиальной и тангенциальной подачами и "летучим" резцом. Окончательная обработка червячных колес червяк.
Тема 14. Обработка деталей класса «корпусные детали»
Классификация деталей класса "корпусные детали". Материалы для корпусных деталей с.-х. машин. Технические требования на корпусные детали. Выбор технологических и измерительных баз. Обработка плоских поверхностей фрезерованием, строганием, протягиванием.
Тема 15. Изготовление типовых деталей двигателей
Изготовление блоков, головок и гильз цилиндров; шатунов; коленчатых и распределительных валов; поршней; поршневых колец; клапанов.
Тема 16. Изготовление деталей рабочих органов и трансмиссий сельскохозяйственных машин
Характеристика деталей рабочих органов и трансмиссий с.-х. машин. Изготовление зубьев и штифтов молотильных аппаратов комбайнов, дисков рабочих органов с.-х. машин, лемехов, отвалов, полевых досок и лап культиваторов.
Тема 17. Основные понятия о технологических процессах сборки
Понятие о процессах сборки машин. Исходные данные для проектирования. Классификация соединений деталей. Стадии сборочного процесса. Структура технологического процесса сборки. Организационные формы сборки. Технологические схемы, и их построение. Последовательная и параллельная сборка. Поточная сборка. Темп сборки. Сборочные приспособления. Пути снижения трудоемкости сборочных работ.
Тема 18. Сборка типовых соединений
Виды соединений и технология их сборки. Сборка подвижных и неподвижных соединений. Сборка типовых элементов сборочных единиц. Сборка подшипниковых узлов. Сборка зубчатых и червячных передач. Сборка цепных передач. Сборка клиноременных передач. Сборка прокладочных соединений. Балансировка деталей, узлов, агрегатов. Механизация и автоматизация сборочных работ.
Тема 19. Сборка сельскохозяйственных машин
Сборка с.-х. орудий. Сборка двигателей. Конструктивные и технологические особенности рам и кузовов. Изготовление элементов конструкции рам, кузовов, сборка каркаса. Окраска машин. Схема технологического процесса общей сборки машин. Обкатка и испытание машин и агрегатов. Средства технологического оснащения и, показатели механизации и автоматизации технологических процессов.
Лабораторные занятия
Наименование тем, их содержание и объем в часах
Тема 1. (8 часов). Технологическое оборудование (металлорежущие станки) в машиностроении и его возможности.
Конструкция токарно-винторезного станка 16К25. Конструкция горизонтально-фрезерного станка 6Р81. Конструкция радиально-сверлильного станка 2К52. Конструкция и принцип работы кривошипно-механического пресса. Настройка токарно-винторезного станка 16К25 на нарезание резьбы.
Тема 4. (4 часа). Точность механической обработки и ее оценка статистическими методами
Проверка токарно-винторезного станка 16К25 на точность. Определение жесткости токарно-винторезного станка. Определение погрешности обрабатываемой детали при точении в патроне.
Тема 5. (2 часа). Качество обработанной поверхности
Влияние параметров резания на шероховатость обработанной поверхности.
Тема 6. (3 часа). Проектирование технологических процессов механической обработки и основы технического нормирования
Составление схем технологических процессов изготовления типовых деталей (валы, зубчатые колеса, корпусные детали). Определение норм времени при работе на металлорежущих станках.
3. Методические указания к выполнению контрольной работы
3.1. Задание
Разработать технологический процесс (ТП) механической обработки ступенчатого вала. Вариант задания определяется исходя из последних двух цифр учебного шифра студента. Например, учебный шифр студента – 02152. В таблице 1 находим на пересечении столбца 5 и строки 2 цифру 68 – это номер варианта по таблице 6. Геометрические размеры и шероховатость обрабатываемых поверхностей деталей определяются по приложениям А и Б.
Таблица 1
Варианты заданий
Последняя цифра шифра | Предпоследняя цифра шифра | |||||||||
1 | 2 | 3 | 4 | 5 | 6 | 7 | 8 | 9 | 0 | |
1 | 1 | 2 | 3 | 57 | 58 | 6 | 7 | 62 | 63 | 10 |
2 | 11 | 12 | 13 | 67 | 68 | 16 | 17 | 72 | 73 | 20 |
3 | 21 | 22 | 23 | 24 | 25 | 26 | 27 | 28 | 81 | 83 |
4 | 31 | 8 | 9 | 91 | 92 | 36 | 37 | 38 | 90 | 86 |
5 | 41 | 18 | 19 | 85 | 87 | 46 | 47 | 48 | 49 | 50 |
6 | 51 | 52 | 53 | 54 | 55 | 56 | 84 | 95 | 59 | 60 |
7 | 61 | 82 | 39 | 64 | 65 | 66 | 100 | 99 | 69 | 70 |
8 | 71 | 96 | 98 | 74 | 75 | 76 | 77 | 78 | 79 | 80 |
9 | 32 | 33 | 94 | 93 | 29 | 30 | 34 | 35 | 4 | 5 |
0 | 42 | 43 | 97 | 88 | 89 | 40 | 44 | 45 | 14 | 15 |
При выполнении работы необходимо:
- определить размеры заготовки;
- выбрать соответствующую модель токарно-винторезного станка (в контрольной работе приводятся параметры станка, который нужно знать при разработке ТП изготовления данной детали);
- выбрать приспособление, режущий и измерительный инструмент. Привести характеристики указанных средств технологического оснащения;
- определить последовательность обработки поверхностей детали и последовательность действия рабочего обеспечивающего непосредственно выполнение основной технологической работы (приемы, связанные с установкой, креплением, выверкой, раскреплением и снятием детали, приемы измерения детали). Привести последовательность обработки и действия рабочего в хронологической последовательности; определить технологические режимы обработки:
t – глубину резания, мм;
S – подачу, мм/об;
V – скорость резания, м/мин;
Тшт – определить штучное операционное время изготовления детали, мин.
3.2. Определение размеров заготовки
Детали изготавливаются в условиях мелкосерийного производства. В этом случае заготовкой служит стальной круглый прокат. Диаметр и длина заготовки определяется с учетом наибольшего диаметра детали, ее длины и припусков на ее обработку.
Таблица 2
Сортамент стального круглого проката
Диаметр, мм | Масса 1 п.м., кг | Диаметр, мм | Масса 1 п.м., кг | Диаметр, мм | Масса 1 п.м., кг |
1 | 2 | 3 | 4 | 5 | 6 |
12 | 0,895 | 34 | 7,13 | 56 | 19,30 |
13 | 1,04 | 36 | 7,99 | 58 | 20,70 |
14 | 1,21 | 38 | 8,90 | 60 | 22,20 |
15 | 1,39 | 40 | 9,87 | 65 | 26,00 |
17 | 1,78 | 42 | 10,90 | 70 | 30,20 |
20 | 2,47 | 44 | 11,90 | 75 | 34,70 |
22 | 2,98 | 46 | 13,00 | 80 | 39,50 |
25 | 3,85 | 48 | 14,20 | 85 | 44,50 |
27 | 4,50 | 50 | 15,40 | 90 | 49,50 |
30 | 5,55 | 52 | 16,70 | 95 | 55,60 |
32 | 6,31 | 54 | 18,00 | 100 | 61,70 |
Расчетные размеры заготовки определяются по формулам:
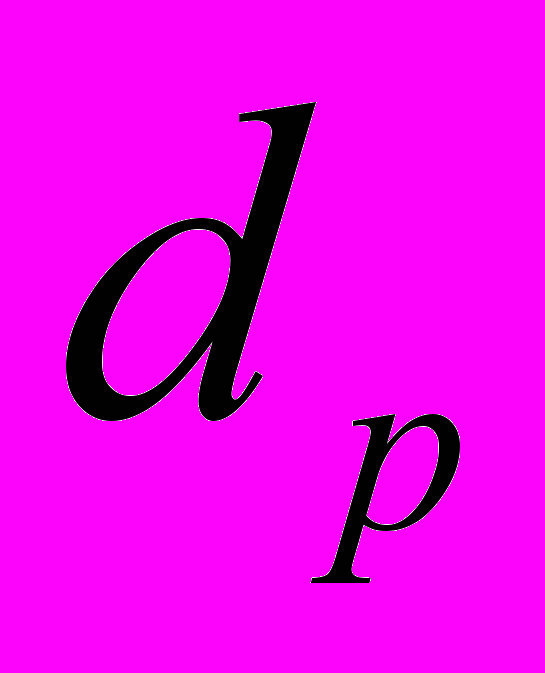
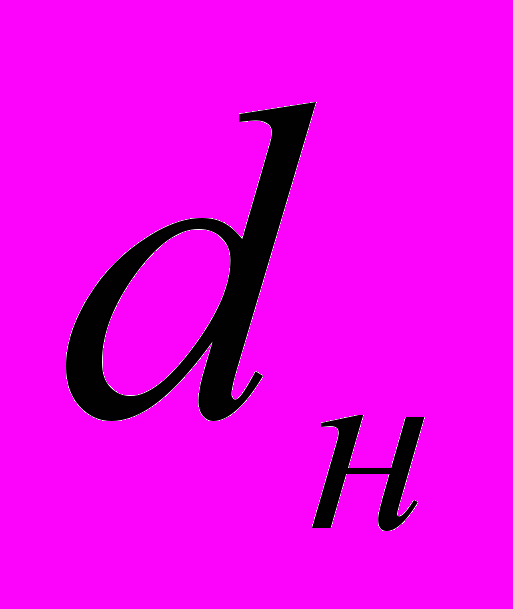
где
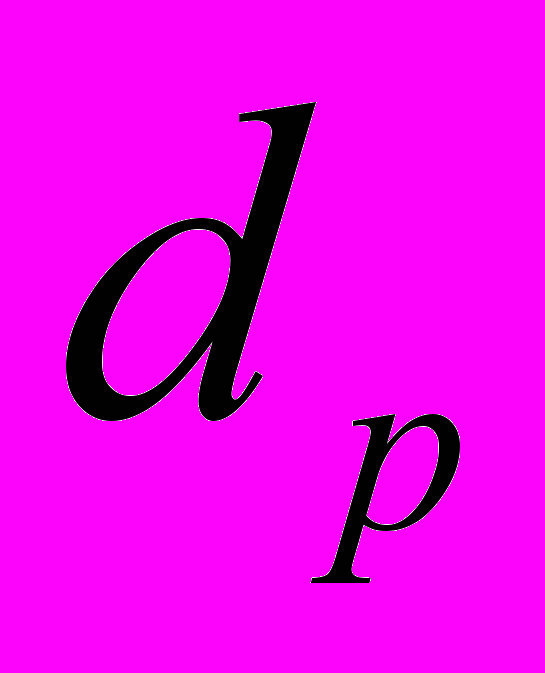
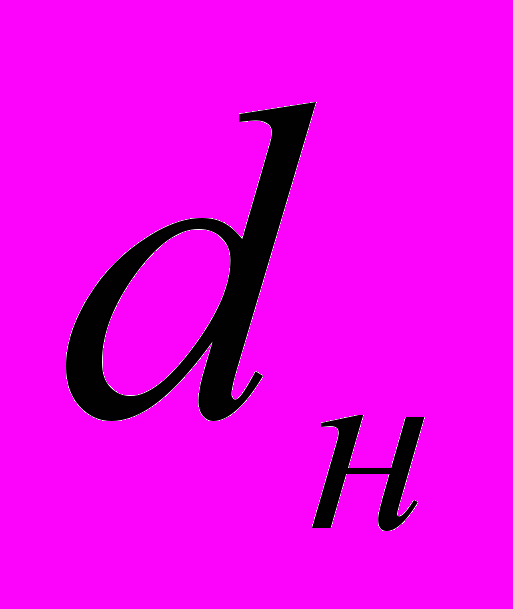
zo- общий припуск на диаметр заготовки из проката, мм
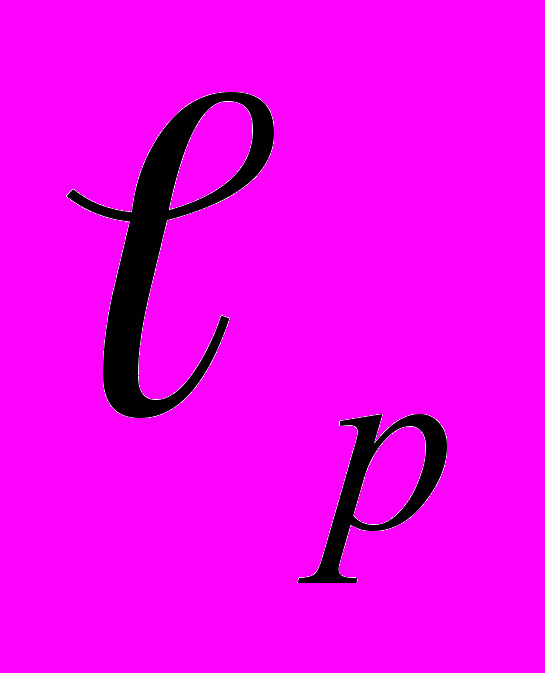
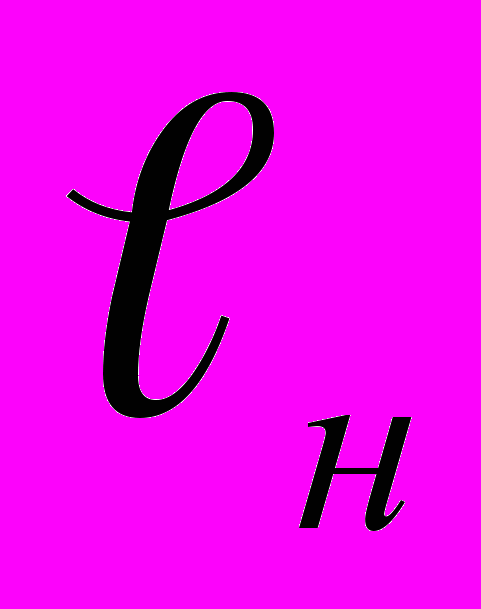
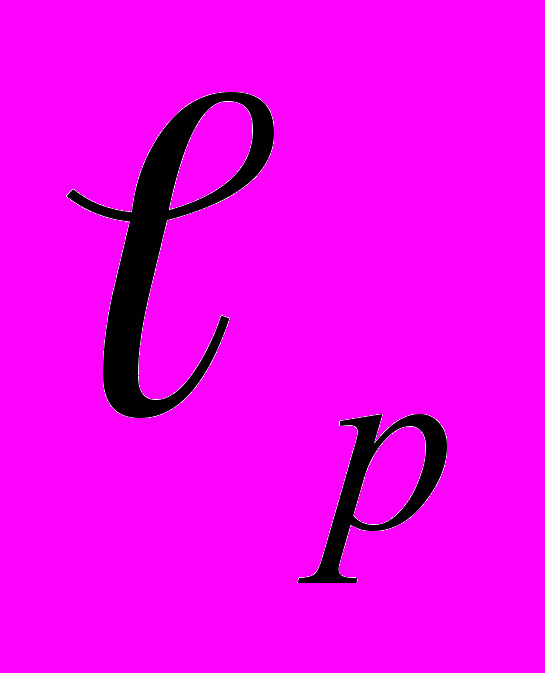
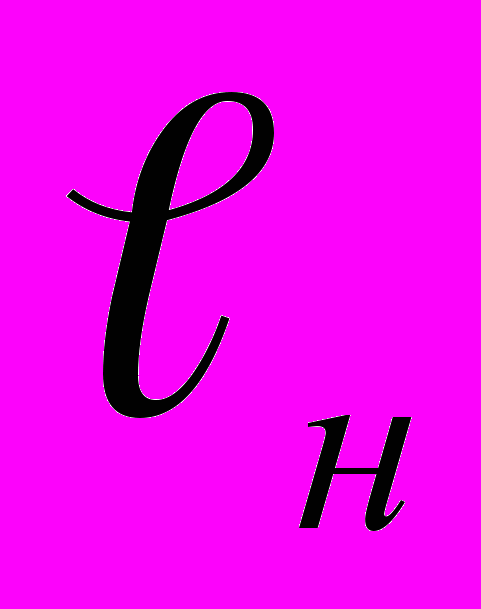
2 zo - общий припуск на подрезание торцов, мм.
Величина промежуточных припусков на обработку деталей определяется по таблицам 3 и 4.
Для определения общего припуска обработки поверхностей детали, необходимо определить последовательность их обработки. Последовательность обработки определяется с учетом требований к шероховатости поверхностей. Таблица 4 [1].
При этом следует учесть, что чистовому точению предшествует получистовое, а получистовому – черновое.
Промежуточные припуски на обработку наружных цилиндрических поверхностей определятся по таблице 3, а при обработке торцов – по таблице 4.
Таблица 3
Промежуточные припуски на обработку наружных цилиндрических поверхностей в мм.
Номинальный диаметр, мм | Вид обработки, (точение) | Длина заготовки мм | |||||
до 25 | 25-63 | 63-100 | 100-160 | 160-250 | 250-400 | ||
1 | 2 | 3 | 4 | 5 | 6 | 7 | 8 |
10-18 | Черновое | 3,0 | 3,0 | 3,0 | 3,5 | 3,5 | 3,5 |
Получистовое | 1,2 | 1,2 | 1,2 | 1,5 | 1,5 | 1,5 | |
Чистовое | 0,3 | 0,3 | 0,3 | 0,3 | 0,3 | 0,4 | |
18-30 | Черновое | 3,5 | 3,5 | 3,5 | 3,5 | 3,5 | 3,5 |
Получистовое | 1,5 | 1,5 | 1,5 | 1,5 | 1,5 | 1,5 | |
Чистовое | 0,3 | 0,3 | 0,3 | 0,3 | 0,4 | 0,4 | |
30-50 | Черновое | 4,0 | 4,0 | 4,0 | 4,5 | 4,5 | 4,5 |
Получистовое | 1,5 | 1,5 | 1,5 | 1,5 | 1,5 | 2,0 | |
Чистовое | 0,4 | 0,4 | 0,4 | 0,4 | 0,4 | 0,4 | |
50-80 | Черновое | 4,0 | 4,0 | 4,0 | 4,5 | 4,5 | 4,5 |
Получистовое | 1,5 | 1,5 | 1,5 | 1,5 | 1,5 | 2,0 | |
Чистовое | 0,4 | 0,4 | 0,4 | 0,4 | 0,4 | 0,5 |
Таблица 4
Припуски на подрезание торцов, в мм
Диаметр заготовки, мм | Длина заготовки, мм | ||||
до 18 | 18-50 | 50-120 | 120-260 | 260-500 | |
до 30 | 0,4 | 0,5 | 0,7 | 0,8 | 1,0 |
30-50 | 0,5 | 0,5 | 0,7 | 0,8 | 1,0 |
50-120 | 0,6 | 0,7 | 0,8 | 1,0 | 1,2 |