Разработка технологии изготовления индивидуального зуборезного инструмента для мелкомодульных зубчатых колес
Вид материала | Автореферат |
- Нормирование точности зубчатых колес, 105.1kb.
- Гост 11902-77. Головки зуборезные для конических и гипоидных зубчатых колес с круговыми, 13.3kb.
- Методические указания к курсовому проекту, 194.16kb.
- Основы высокоэффективн ой технологии изготовления цилиндрических зубчатых колес, 532.88kb.
- Возможные исходные реечные контуры для нарезания зубчатых колес, 77.82kb.
- Программные средства компьютерного проектирования зубчатых передач в обобщающих параметрах, 26.58kb.
- 1. в номинации «Энергоэффективные и ресурсосберегающие технологии, оборудование и материалы, 23.2kb.
- Курсовой проект по дисциплине: Конструирование акустических приборов и систем на тему:, 611.37kb.
- «Разработка технологии изготовления детали «Корпус» с применением станков с чпу и организации, 48.43kb.
- Разработка технологии и инструмента для непрерывного деформационного получения ультрамелкозернистой, 291.68kb.
На правах рукописи
КОПТЕВ Александр Иванович
РАЗРАБОТКА ТЕХНОЛОГИИ ИЗГОТОВЛЕНИЯ ИНДИВИДУАЛЬНОГО ЗУБОРЕЗНОГО ИНСТРУМЕНТА
ДЛЯ МЕЛКОМОДУЛЬНЫХ ЗУБЧАТЫХ КОЛЕС
Специальность 05.02.07 - Технология и оборудование
механической и физико-технической
обработки
05.02.08 - Технология машиностроения
АВТОРЕФЕРАТ
диссертации на соискание ученой степени
кандидата технических наук
Воронеж - 2012
Работа выполнена в ФГБОУ ВПО "Воронежский государственный технический университет"
Научный руководитель | доктор технических наук, доцент Кузовкин Алексей Викторович |
Научный консультант | кандидат технических наук, доцент Мандрыкин Андрей Владимирович |
Официальные оппоненты: | доктор технических наук, профессор Козлов Александр Михайлович; |
| доктор технических наук, профессор Ткаченко Юрий Сергеевич |
Ведущая организация | ОАО "Научно-исследовательский институт автоматизированных средств производства и контроля" (ОАО НИИАСПК) (г. Воронеж) |
Защита состоится 21 марта 2012 г. в 1400 часов в конференц-зале на заседании диссертационного совета Д 212.037.04 ФГБОУ ВПО "Воронежский государственный технический университет" по адресу: 394026, г. Воронеж, Московский просп., 14.
С диссертацией можно ознакомиться в научно-технической библиотеке ФГБОУ ВПО "Воронежский государственный технический университет".
Автореферат разослан 14 февраля 2012 г.
Ученый секретарь
диссертационного совета Кириллов О.Н.
ОБЩАЯ ХАРАКТЕРИСТИКА РАБОТЫ
Актуальность темы. В современном гибкоструктурном производстве и развивающемся малом и среднем бизнесе все большее внимание уделяется выпуску мелкосерийной продукции для авиационно-космической отрасли, станкостроения и приборостроения, конкурентоспособность которой возможно обеспечить путем создания новых наукоемких изделий, конструктивными элементами которых являются зубчатые колеса. Наибольшую сложность в изготовлении таких изделий представляют мелкомодульные колеса и инструмент для их изготовления, где допустимая погрешность по кинематической точности может составлять от 3 до 10 мкм. Из опыта промышленного производства и литературных источников известно, что точные эвольвентные профили с модулем менее 2 мм экономически целесообразно изготавливать долблением. На большинстве машиностроительных предприятий имеются зуборезные участки, оснащенные долбежными станками. При этом становится обоснованным использование для производства мелкомодульных зубчатых колес долбяков, к которым предъявляются высокие требования по точности, стойкости и износоустойчивости. Как правило, такие колеса производятся малыми сериями или единично (в случае их использования для ремонта). Это приводит к многократному возрастанию стоимости производства единичного зуборезного инструмента по сравнению с его серийным выпуском. Поэтому требуется обоснование выбора метода и разработка технологии нетрадиционного способа изготовления сборных твердосплавных и закаленных стальных долбяков с возможностью получения профиля зуба универсальным (непрофилированным) инструментом. В этом случае достигается возможность быстрого изготовления качественных износостойких долбяков за счет перенесения основной трудоемкости подготовки производства на автоматизированное проектирование управляющих программ для современного (в частности электроэрозионного) оборудования, имеющегося в достаточном количестве на предприятиях оборонных отраслей машиностроения. Это ускоряет выпуск индивидуального зуборезного инструмента, сокращает сроки освоения новых конкурентоспособных изделий, снижает себестоимость продукции, что актуально в современных условиях ведения хозяйственной деятельности.
Разработанные для сборного мелкомодульного зубообрабатывающего инструмента технологии изготовления на основе параметрической взаимосвязи профиля обрабатываемого зубчатого колеса и геометрии режущей части долбяка, реализуемые за счет изготовления последнего непрофилированным электродом-инструментом, имеют хорошие перспективы по их использованию для производства зубчатых колес мелкого модуля с высокой точностью профиля. Такой способ экономически целесообразен на стадии выпуска опытных изделий, а также при изготовлении мелкосерийной и единичной продукции в процессе серийного выпуска наукоемких, сложных объектов ракетно-космической техники и в других отраслях машиностроения.
Рассматриваемое направление исследований по получению эвольвентного профиля непрофилированным электродом без его последующей финишной обработки представляет интерес для опытно-конструкторских фирм и предприятий, работающих в области производства высокоточного оборудования, поэтому тема работы является актуальной, имеющей большие перспективы использования и развития в современном машиностроении.
Работа выполнялась в соответствии с Государственной программой "Мобильный комплекс", раздел "Техническое перевооружение" (постановление правительства РФ №2164-П) и федеральной целевой программой "Научные кадры инновационной России" на 2009-2013 годы" (постановление правительства РФ №568 от 26.07.08), а также по научному направлению ФГБОУ ВПО "Воронежский государственный технический университет" "Наукоемкие технологии в машиностроении, авиастроении и ракетно-космической технике".
Целью работы является обоснование способа и разработка технологии процесса получения индивидуальных эвольвентных профилей малого модуля для инструментального производства с обеспечением высоких технологических и эксплуатационных показателей сборного зуборезного инструмента за счет использования непрофилированного электрода-проволоки для формообразования высококачественных поверхностей, находящихся в параметрической взаимосвязи с формируемым рабочим профилем зубчатого колеса.
Для достижения поставленных целей были сформулированы и решены следующие задачи:
1. Обоснование метода эффективного изготовления мелкомодульных долбяков из труднообрабатываемых материалов для гибкоструктурного производства.
2. Разработка путей обеспечения качества мелкосерийного инструмента при минимизации потребности в материальных ресурсах.
3. Создание метода определения рациональных технологических режимов обработки с минимальным ресурсопотреблением.
4
2
. Разработка технологии чистовой электроэрозионной размерной обработки непрофилированным электродом-проволокой эвольвентных поверхностей зубьев мелкомодульных сборных долбяков.
5. Создание системы автоматизированного проектирования сопрягаемых поверхностей сборного зуборезного инструмента с малым модулем для применения в гибкоструктурном производстве.
6. Обоснование расширения технологических возможностей предлагаемого метода на изготовление сложнопрофильных деталей инструментального и основного гибкоструктурного производства.
Объект и предмет исследования.
Объектами исследования являются процессы электроэрозионного и комбинированного изготовления эвольвентного профиля с помощью непрофилированного инструмента-проволоки, методики проектирования и реализации технологического процесса, инструмент и оборудование для реализации чистовой обработки комбинированным методом.
Методы исследования.
В работе использованы классические закономерности электроэрозионной обработки электродом-проволокой, технологии машиностроения, анализ и статистическая обработка результатов экспериментальных исследований с применением программного обеспечения MathCad, моделирование процесса конструирования твердосплавных долбяков и электроэрозионной обработки с автоматизированной генерацией управляющих программ для станков с ЧПУ Inventor2012 и InventorCAM2011.
Научная новизна работы заключается в:
1. Раскрытии механизма получения чистовой обработкой рабочего профиля твердосплавных режущих элементов без дальнейшей размерной обработки путем параметрического автоматизированного проектирования кромок режущего инструмента с эвольвентным профилем и его коррекцией с учетом реального контура присоединительных размеров корпуса и рабочих элементов (на примере мелкомодульного сборного долбяка).
2. Моделировании процессов, протекающих в межэлектродных зазорах, с учетом динамики изменения сечения проволоки и влияния формы электрода в процессе работы на точность геометрических размеров применительно к эвольвентному профилю сборных долбяков.
3. Создании системы подбора рациональных режимов обработки эвольвентного профиля мелкомодульного твердосплавного инструмента с учетом специфики автоматизированного производства и частой сменой номенклатуры обрабатываемых деталей основного производства.
Практическая значимость работы:
1
3
. Разработаны сборные конструкции мелкомодульных долбяков, позволяющих снизить трудоемкость изготовления эвольвентных профилей и ускорить технологическую подготовку при запуске в гибкоструктурное производство новых изделий.
2. Установлены взаимосвязи технологических режимов электроэрозионной обработки непрофилированным электродом-проволокой и геометрии рабочей части сборных долбяков, что дало возможность получить технологические показатели, обеспечивающие чистовую обработку изделий без заключительных операций размерной обработки абразивным инструментом.
3. Предложены новые способы обработки эвольвентных профилей, обеспечивающие возможность высокоточного изготовления непрофилированным электродом зубчатых и шлицевых поверхностей без использования последующих операций чистовой механической обработки.
Личный вклад соискателя заключается в:
1. Исследовании механизма протекания процесса электроэрозионной обработки твердосплавного инструмента однослойными и многослойными электродами-проволоками, позволяющей увеличить производительность процесса, расширить область использования данного метода на мелкомодульный режущий инструмент (долбяки), повысить точность инструмента за счет создания прецизионных режущих кромок без последующей механической обработки.
2. Разработке методов изготовления и комбинированного упрочнения мелкомодульного твердосплавного сборного инструмента для нарезания зубчатых колес за счет создания теории обеспечения геометрической формы режущих кромок с учетом воздействия на них высокоэнергетических электроимпульсов.
3. Предложении новых (на уровне патентов) способов обработки твердосплавного инструмента в условиях гибкоструктурного производства с учетом требований по точности и качеству зубчатых колес, выпускаемых в основном производстве.
4. Обосновании особенностей технологического процесса производства мелкомодульного твердосплавного инструмента, учитывающего характеристики современного оборудования и требования по экономической целесообразности применения автоматизированных технологических процессов единичного и мелкосерийного производства. Новый технологический процесс расширяет технологические возможности ЭЭО в части повышения точности обрабатываемых эвольвентных профилей ввиду стабилизации условий формообразования на всей поверхности режущей кромки обрабатываемого инструмента.
Р
4
еализация и внедрение результатов работы. Работа внедрена на "Воронежском механическом заводе" – филиале ФГУП "ГКНПЦ им. М.В. Хруничева", ООО ПФК "Воронежский станкозавод - Холдинг" и научно-производственном предприятии "Гидротехника" со значительным экономическим эффектом. Разделы диссертации, посвященные проектированию технологии обработки эвольвентных профилей с использованием непрофилированного электрода-проволоки, используются при чтении лекций по специальным дисциплинам в ФГБОУ ВПО "Воронежский государственный технический университет".
Апробация работы. Основные положения работы докладывались и обсуждались на следующих конференциях: Международной научно-технической конференции "Прогрессивные технологии и оборудование в машиностроении и металлургии" (Липецк, 2010); III Международной научно-практической конференции "Студент, специалист, профессионал" (Воронеж, 2010); II Всероссийской научно-практической конференции "Проектирование механизмов и машин" (Воронеж, 2010); Международной научно-технической конференции "Технологические методы повышения качества продукции в машиностроении" (Воронеж, 2010); ежегодных научно-практических конференциях профессорско-преподавательского состава ФГБОУ ВПО "Воронежский государственный технический университет" (Воронеж, 2009 - 2011).
Публикации. По теме диссертации опубликовано 9 научных работ, из них 3 - в изданиях, рекомендованных ВАК РФ, поданы 2 заявки на патент РФ, по которым принято положительное решение. Общий объем материала 5,1 печ. листов, где доля соискателя составляет 3,2 печатных листа. В работах, опубликованных в соавторстве и приведенных в конце автореферата, лично соискателю принадлежат: [1] - предложена схема и установка для определения показателей процесса обработки мелкомодульных зубчатых колес; [2] - предложен алгоритм автоматизированного проектирования мелкомодульных долбяков; [3] - даны рекомендации по назначению рациональных режимов обработки непрофилированным электродом-проволокой; [4] - предложены рациональные геометрические параметры режущей части мелкомодульного долбяка; [5] - получены расчетные зависимости для определения точности обрабатываемого профиля; [6] - предложена схема повышения износостойкости инструмента для зубообработки; [7] - обработаны экспериментальные данные по влиянию системы инструмент - деталь на точность эвольвентного профиля; [8] - разработан алгоритм исследований характера поведения инструмента при зубообработке; [9] - предложена методика определения износостойкости твердосплавного мелкомодульного режущего инструмента.
С
5
труктура и объем работы. Диссертация состоит из введения, 5 глав, заключения, списка литературы из 133 наименований, 4 приложений. Основная часть работы изложена на 122 страницах, содержит 52 рисунка и 9 таблиц.
ОСНОВНОЕ СОДЕРЖАНИЕ РАБОТЫ
Во введении обоснована актуальность темы, сформулированы цель, научная позиция автора, приведены задачи исследований, раскрыты научная и практическая значимость работы, методы исследований, уровень обсуждения материалов.
В первой главе рассмотрены способы изготовления прецизионного режущего инструмента для нарезания зубчатых колес с мелким модулем в условиях гибкоструктурного производства. Показана перспективность изготовления твердосплавного инструмента с применением электроэрозионной обработки (ЭЭО). Определено, что изготовление такого инструмента возможно без последующих финишных операций за счет повышения точности обрабатываемых эвольвентных профилей ввиду стабилизации условий формообразования на всей поверхности режущей кромки обрабатываемого инструмента.
Анализ существующего положения в области изготовления мелкомодульного зуборежущего инструмента показывает, что:
1. Наиболее перспективным инструментом для изготовления зубчатых колес с малым модулем является применение сборных твердосплавных долбяков с оптимальной геометрией режущей части. Однако существующие на сегодняшний момент технологии механической обработки эвольвентного профиля твердосплавной части высокозатратны, не производительны и нуждаются в модернизации на основе применения новых наукоемких технологических процессов с наложением электрического поля.
2. В литературе имеются сведения о возможности обработки твердых сплавов на основе электроэрозионного процесса с применением непрофилированного электрода-проволоки. При этом отсутствуют сведения по расчету и выбору режимов обработки и определению выходных технологических показателей процесса.
3. Имеющиеся данные по созданию гибкоструктурных технологических процессов единичного инструментального производства носят фрагментарный характер и требуют своего развития в направлении создания технологических рекомендаций и типовых технологических процессов, пригодных для использования в основном производстве.
4. Опыт применения твердосплавного инструмента с мелким модулем показал его экономическую целесообразность, однако нуждается в детальной проверке на классе прецизионных деталей авиационной и ракетно-космической техники.
5
6
. Проведенные ранее исследования служат основой для разработки модели процесса электроэрозионной и комбинированной технологии ЭЭО сборного твердосплавного инструмента с малым модулем.
Во второй главе рассмотрены вопросы выбора путей для достижения поставленной цели и решения заявленных задач. Из ранее выполненных исследований ясно, что для повышения точности и качества рабочей части сборного зуборезного инструмента на основе использования ЭЭО необходимо выявление рациональных режимов обработки, обеспечивающих исключение последующих финишных операций. Это налагает определенные требования к порядку проектирования как конструкции инструмента, так и разработке управляющих программ для современного оборудования на основе цифрового прототипа изделия в условиях гибкоструктурного производства. Сформулированы рабочие гипотезы, раскрывающие направления исследований:
1. Диапазоны точности, достижимые при электроэрозионной обработке непрофилированным электродом-проволокой, обеспечивают выполнение требований, предъявляемых к прецизионным эвольвентным профилям зубообрабатывающего инструмента из твердого сплава.
2. Процесс изготовления эвольвентного профиля непрофилированным электродом-проволокой позволяет исключить последующую чистовую обработку путем притирки профиля в начале процесса эксплуатации на мягких режимах.
3. Повысить точность мелкомодульных долбяков возможно за счет управления положением инструмента относительно заготовки по высоте зоны обработки с учетом износа электрода-проволоки и применения многослойного инструмента с фасонным профилем.
4. Мобильность перехода на новые типоразмеры долбяков можно обеспечить за счет автоматизации технологической подготовки производства на основе параметрического проектирования режущей части сборного мелкомодульного зубодолбежного инструмента и возможностей современного электроэрозионного оборудования.
5. Сократить сроки выпуска прецизионного единичного инструмента (мелкомодульных долбяков) возможно за счет определения научно-обоснованных рациональных технологических режимов формирования профиля зуба непрофилированным электродом с экономически обоснованным получением требуемого качества поверхностного слоя, обеспечивающего необходимую стойкость твердосплавного инструмента.
В главе представлены характеристики и возможности экспериментального и промышленного оборудования для ЭЭО, которое применялось в исследованиях, дано обоснование методик обработки экспериментальных данных и повышения прочностных свойств мелкомодульного зуборезного инструмента, на что поданы заявки на патенты РФ, по которым получены положительные решения.
В
7
целом это позволило определить структуру и порядок дальнейших исследований и перейти к теоретическому моделированию процессов.
Третья глава посвящена изучению механизма получения непрофилированным электродом прецизионных эвольвентных профилей для твердосплавного инструмента. В качестве исходных факторов для построения теоретической модели процесса было выбрано следующее.
Точность получения деталей на ЭЭ оборудовании зависит от характеристик электрода-инструмента, определяющих выбор или расчет технологических режимов. Точность контура, получаемого при разделении материалов, в основном зависит от износа проволоки за счет электроэрозионной составляющей процесса. На большинстве ЭЭ станков с непрофилированным электродом в качестве инструмента используется латунная проволока диаметром от 0,1 до 0,3 мм, которая в процессе работы изнашивается и приобретает каплевидную форму (рис. 1, а). При применении многослойной проволоки, где в качестве покрытия применяют цинк, кадмий и другие термоактивные материалы, способные за счет кумулятивного эффекта до 8-10 раз ускорять процесс обработки, износ происходит в направлении рабочей подачи и с боковых сторон. Изменение размеров h1 и h2 (рис. 1, б) не сказывается на точности детали, а боковой износ вызывает снижение ширины прорезаемого паза и погрешность обработки (δ).
Для однослойной проволоки погрешность определяется как
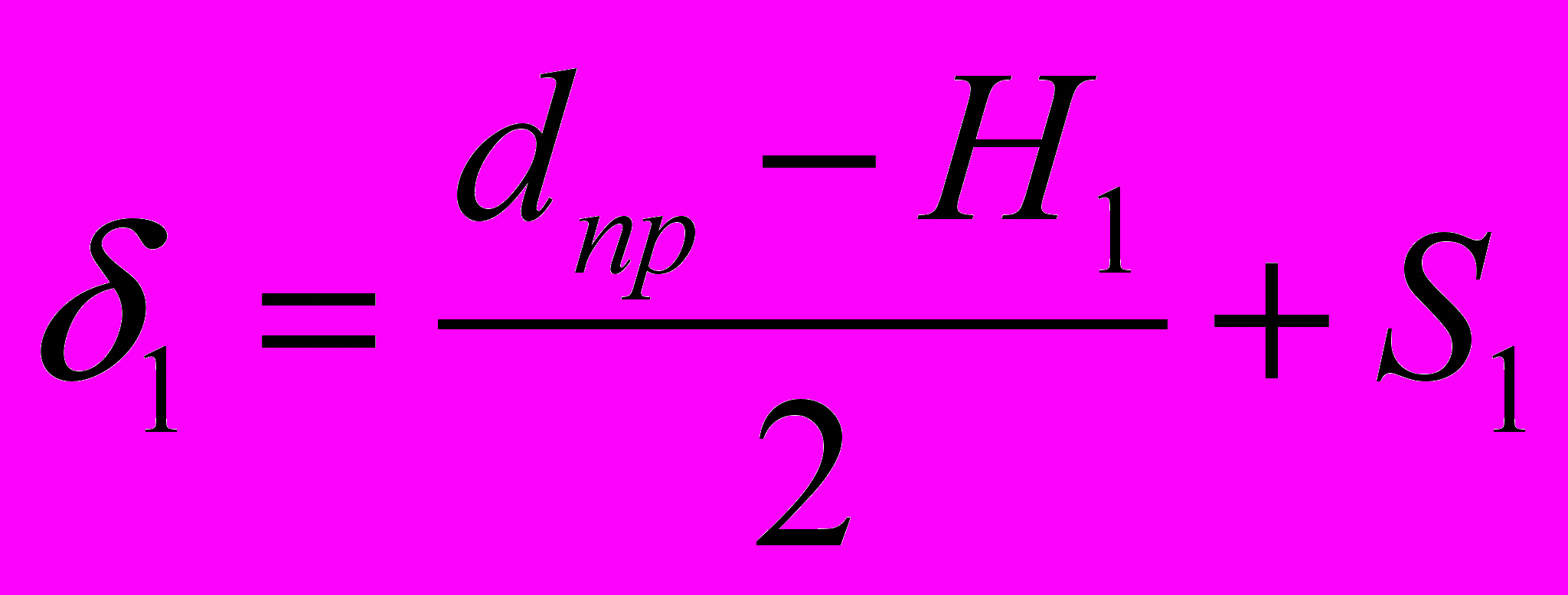
где dпр - исходный диаметр электрода-проволоки, мм;
H1 - размер сечения проволоки и выхода из зоны обработки, мм;
S1 - межэлектродный зазор, для однослойной проволоки диаметром 0,1 - 0,3 мм его расчетная величина составляет для стальных деталей 0,013 - 0,015 мм и 0,015 - 0,018 мм для твердосплавных.
Погрешность обработки двухслойной проволокой оценивается по зависимости
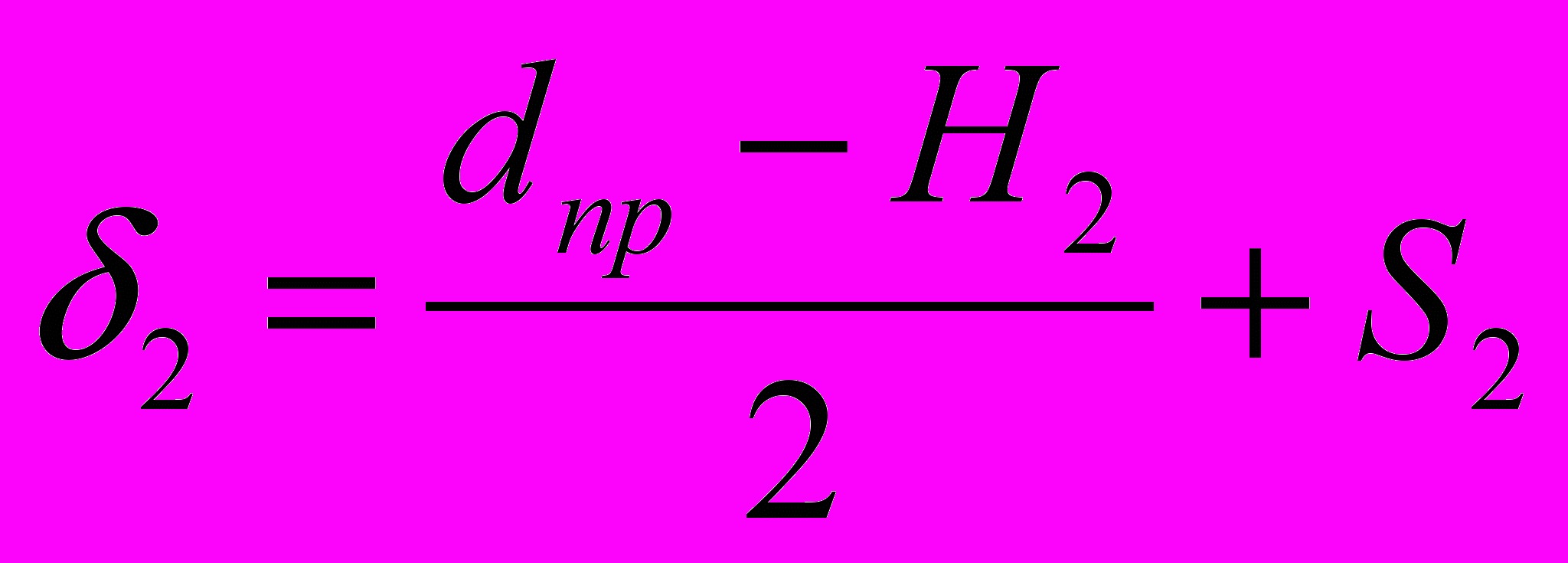
где H2 в первом приближении можно принять равной диаметру d0 силовой проволоки, а S2 = S1.
Стабильность протекания процесса обработки обеспечивается условием, когда по всей высоте заготовки на силовой проволоке 1 остается покрытие 2, которое может устраняться за счет износа не ранее, чем проволока выйдет из зоны обработки. Поэтому скорость перемотки многослойной проволоки, как правило, выше чем однослойной и рассчитывается (в зависимости от материала заготовки, ее толщины и толщины слоя покрытия) с учетом полного удаления покрытия 2.
8
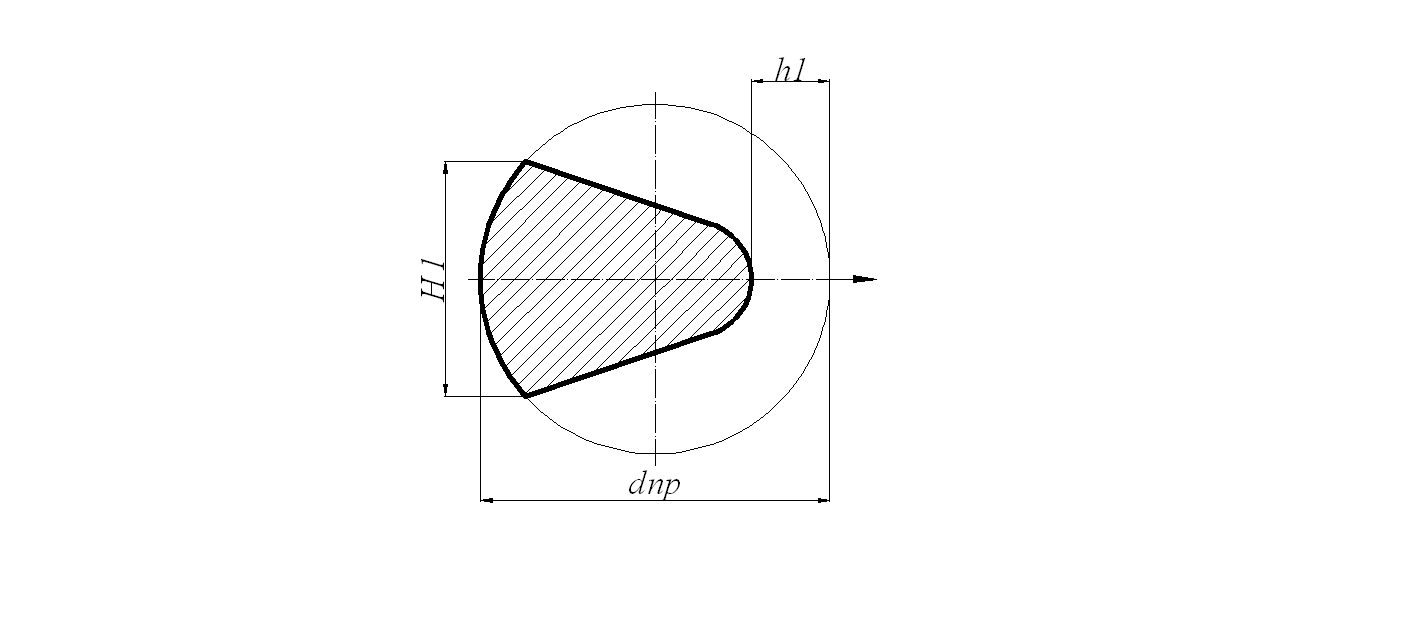

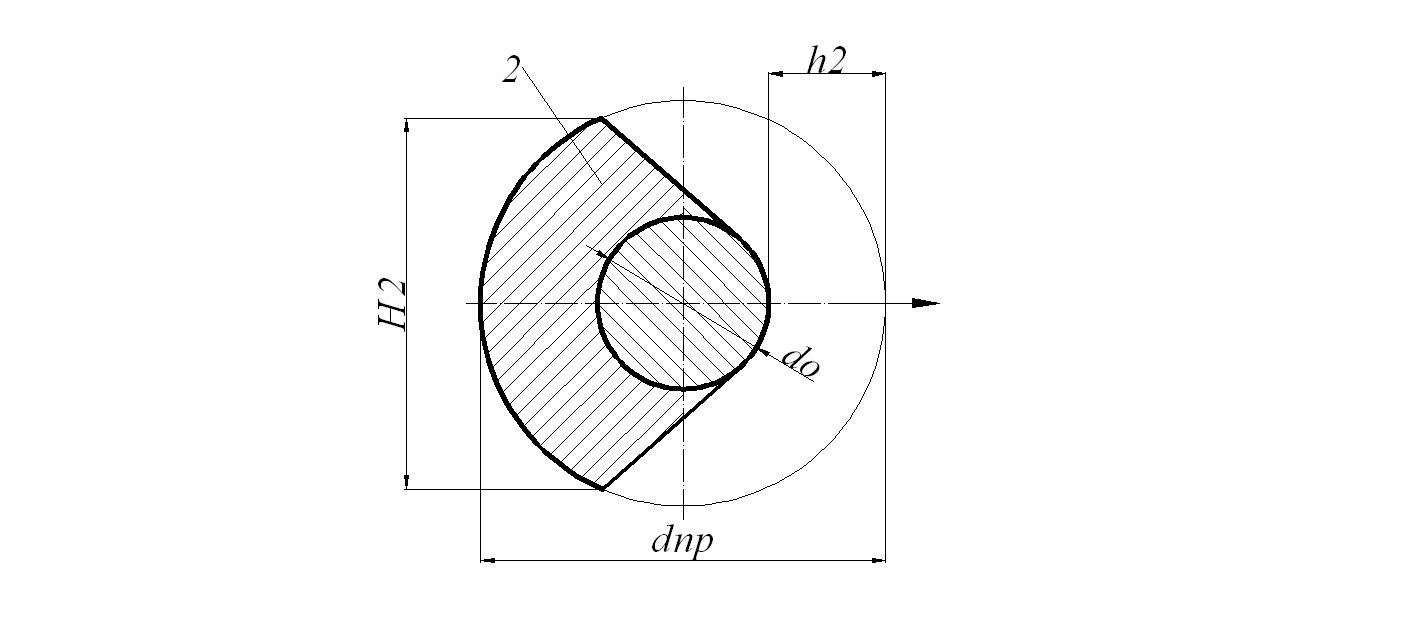
а) б)
Рис. 1. Сечение проволочного электрода-инструмента на выходе из зоны обработки: а) электрод без покрытия, б) двухслойный электрод, 1 - силовая проволока, 2 - термоактивное покрытие; стрелками показано направление рабочей подачи электрода-инструмента
Для режущего инструмента точность переходных участков является одной из определяющих величин. Геометрия таких участков определяется с применением диаметра проволоки после обработки заготовки эквивалентным (dэкв) параметру для круглого сечения, имеющего площадь сечения изношенной проволоки, приведенной на рис. 1. Тогда величина сужения на сторону (Δl1 ) (рис. 2) при одинаковых межэлектродных зазорах
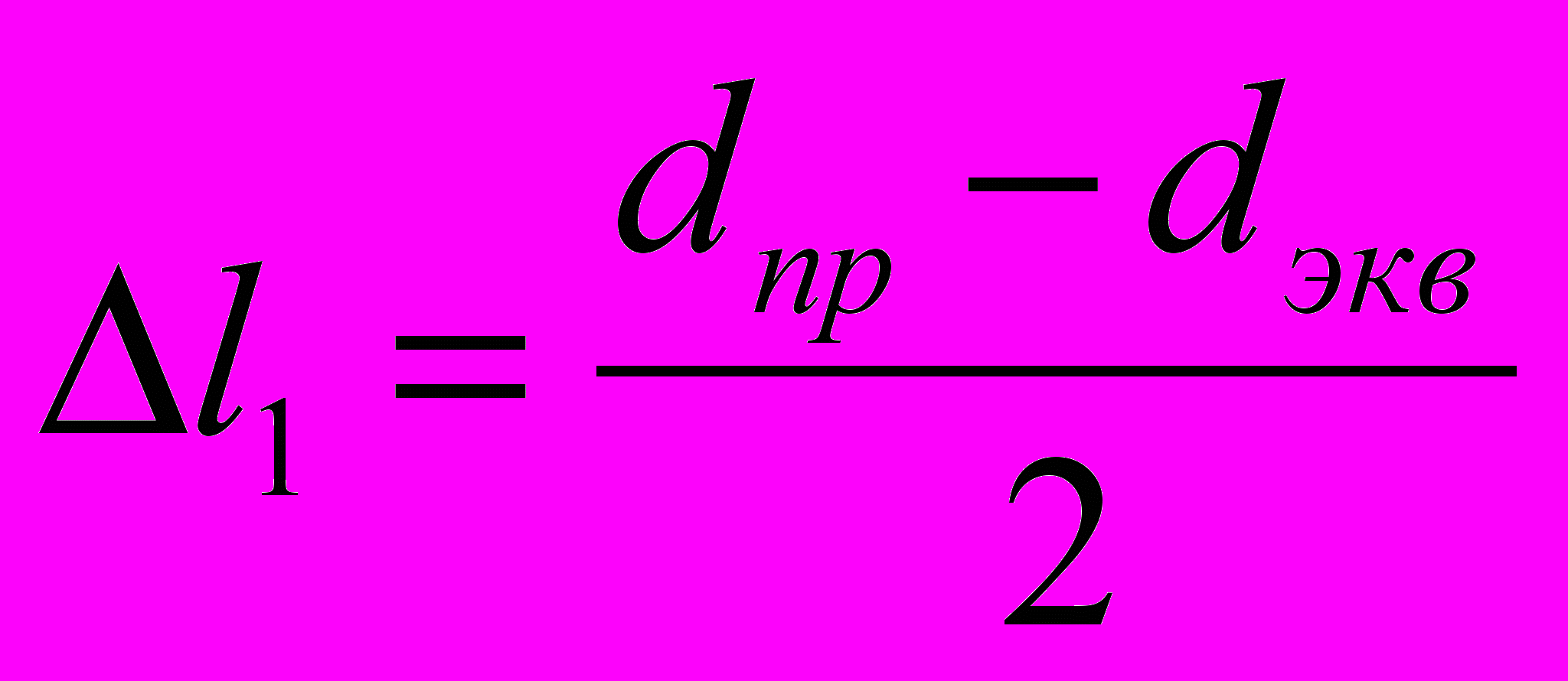
где dэкв - эквивалентный диаметр на выходе из зоны обработки, мм:
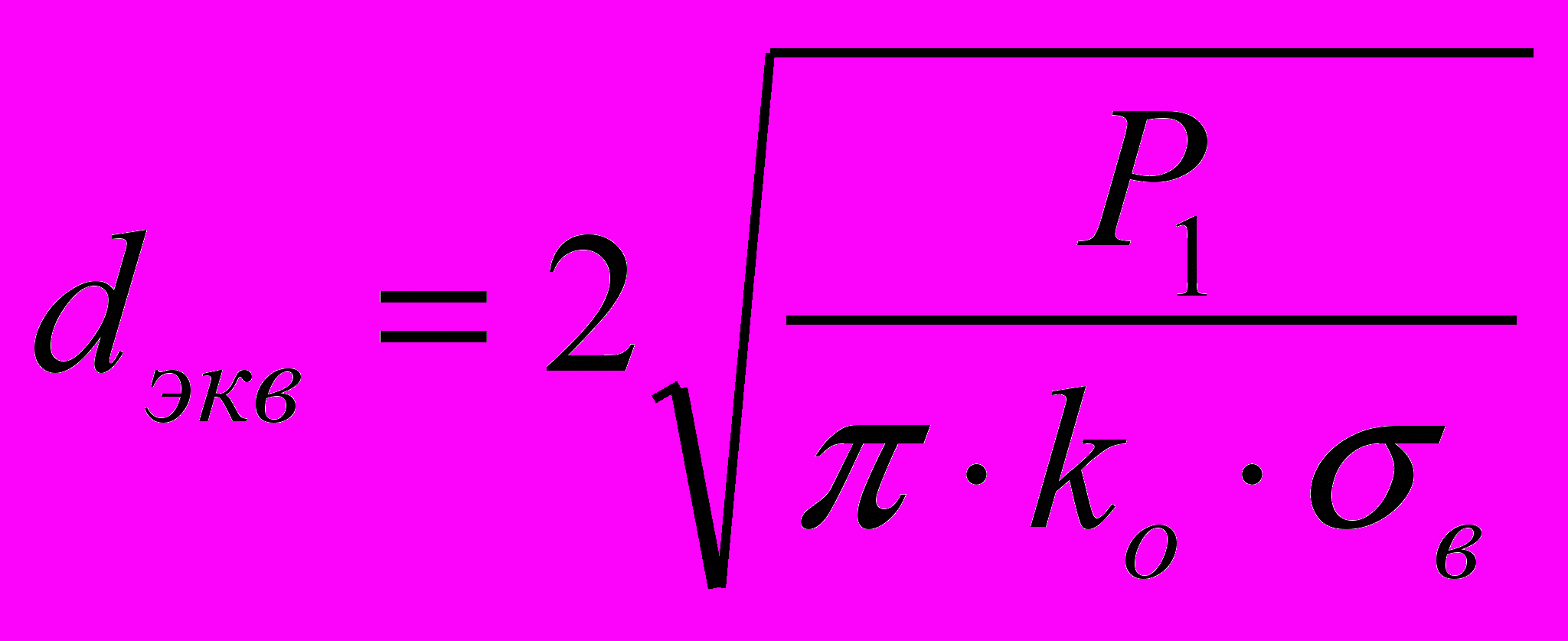
где P1 - сила, с которой растягивают проволоку, достаточной для ее выпрямления и устойчивости под действием импульсов разрядов в рабочей зоне, Н;
kо - коэффициент запаса прочности материала (неоднородность свойств, местные концентраторы напряжений и др.), коэффициент kо имеет значение 0,8 - 0,9;
σв - предел прочности материала проволоки на растяжение, Н/м2.
В современных станках для ЭЭО проволочным электродом, как правило, имеется координата, изменяющая наклон стенок паза по высоте заготовок (на рис. 2 угол α). При известных Δl1 (Δl2) (зависимость 2) можно рассчитать угол α.
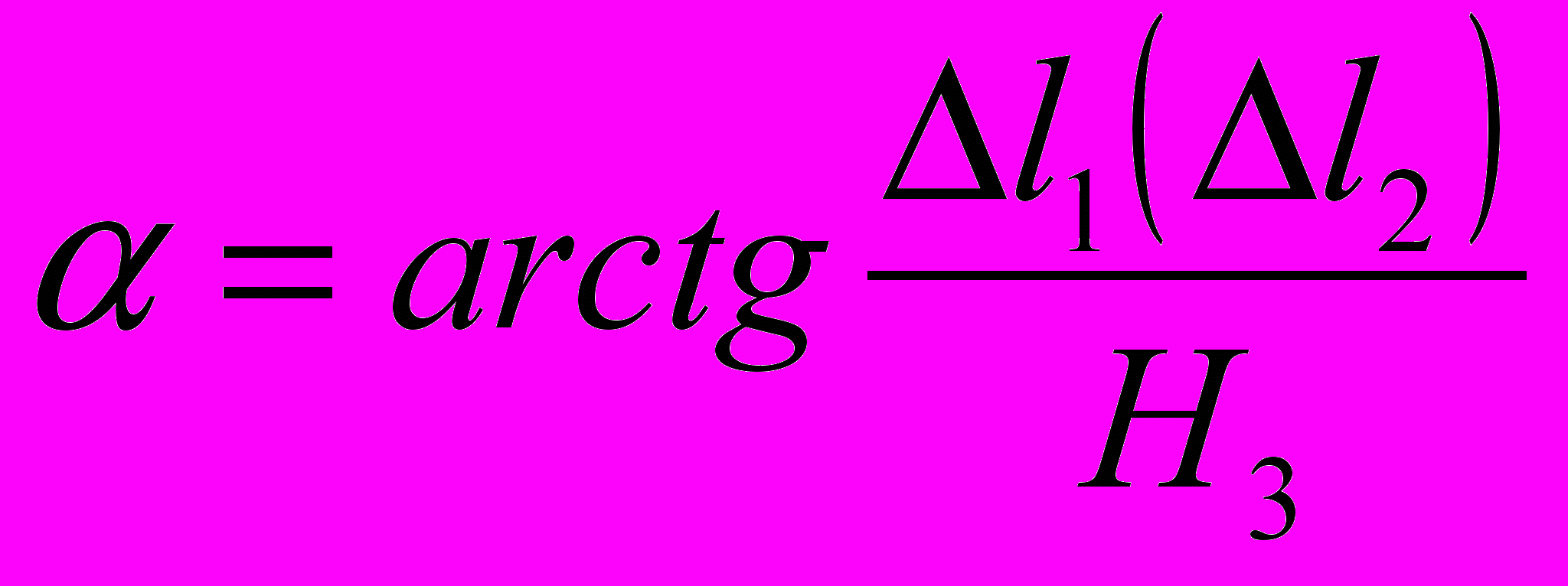
9
. (5)
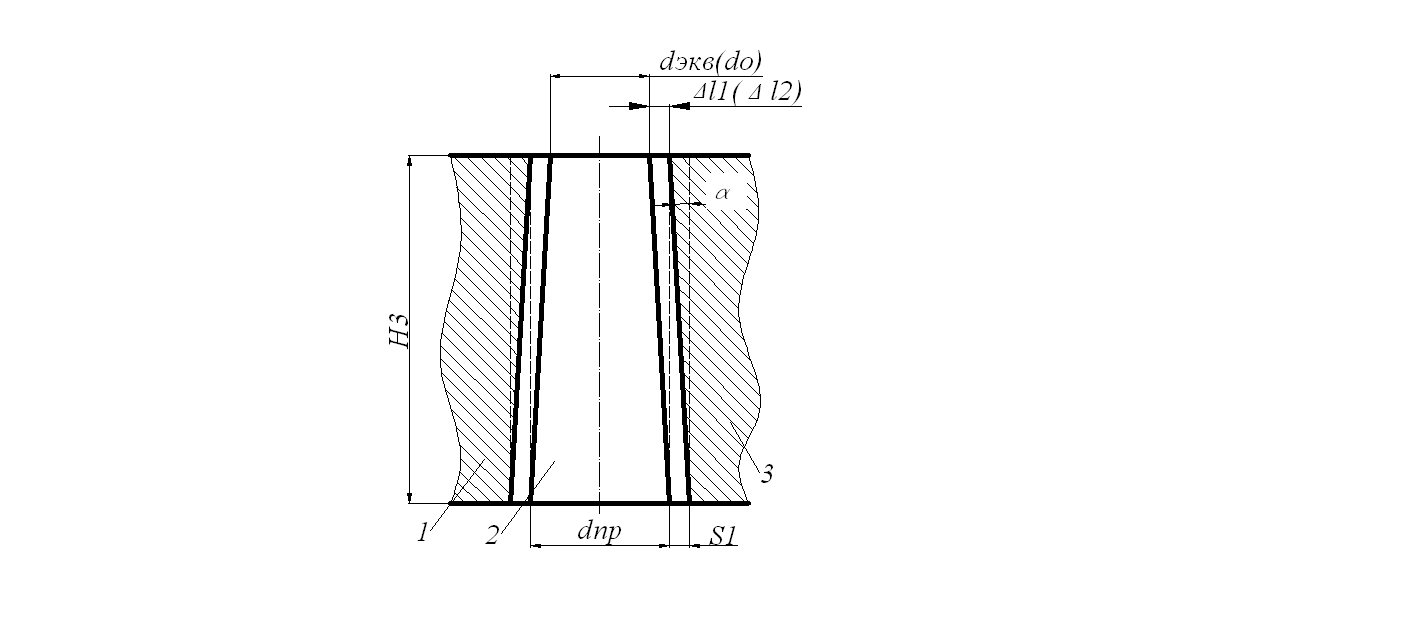
Рис. 2. Расчет углового положения боковой поверхности разделенной заготовки: 1 - отход материала; 2 - сечение проволоки-электрода перпендикулярно поверхности разделения заготовки; 3 - деталь (пунктиром показаны контуры электрода-проволоки и зоны разделения материала без учета износа инструмента)
Величина α составляет для однослойной проволоки от 1'15" до 1'30" (для твердосплавных заготовок) и до 2 угловых градусов для сталей. Для двухслойной проволоки угол уклона возрастает на 15-20%.
При соблюдении обоснованных в работе технологических режимов и методов повышения точности профиля обеспечивается точность профиля в пределах ±3 мкм (при высоте заготовки до 50 мм). При проектировании технологического процесса следует учитывать технологические показатели процесса:
погрешность (рис. 3):
- обработка однослойной проволокой - от ± 3 мкм;
-двухслойной и многослойной проволокой - от ± 5 мкм;
шероховатость Rа , мкм:
- твердосплавных заготовок - 0,32-0,63;
- конструкционных сталей -0,63-1,25;
- расход материала инструмента в % от объема снятого металла - 10-30.
Проведенные исследования показали, что даже твердосплавный инструмент с эвольвентным рабочим профилем, полученным проволочным электродом, не требует дополнительной механической обработки (притирки, чистового шлифования и др.) с целью повышения его эксплуатационных характеристик и через короткое время работы имеет шероховатость в 2 раза ниже исходной, не вызывая при этом дополнительных погрешностей.
С
10
остояние поверхностного слоя инструмента оказывает существенное влияние на стойкость инструмента. Основное влияние на поверхностный слой оказывают режимы ЭЭО (мощность импульсов, тип применяемой схемы генератора, однослойность и многослойность непрофилированного электрода) и материал детали. В работе проведена оценка состояния поверхностного слоя после обработки твердого сплава ВК10-ОМ для случаев обработки однослойным и многослойным электродом-проволокой, которые показали, что измененный слой на образцах в обоих случаях имеет четко выраженную структуру, однако он неравномерен по толщине. При увеличении на микроскопе в 200 раз видно, что толщина слоя (от 7 до 10 мкм) значительно больше, чем величина шероховатости поверхности, следовательно, он оказывает и большее влияние на прочностные качества твердосплавного инструмента. При исследовании образцов, не удалось обнаружить на внешней поверхности микротрещин и растрескиваний, что оказывает положительное влияние на стойкость твердосплавного инструмента.
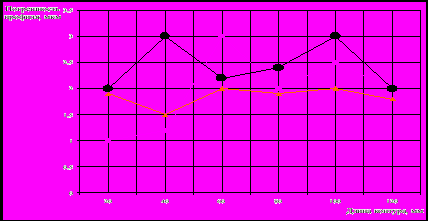
Рис. 3. Зависимость погрешности профиля от длины обрабатываемого контура (данные представлены по выборке из 8 образцов, приведена средняя величина для каждой точки): ■ - толщина обрабатываемого контура 10 мм, проволока без покрытия; ● - толщина контура 20 мм, проволока без покрытия; ▲ - толщина контура 20 мм, проволока с термоактивным покрытием
В четвертой главе освещены вопросы автоматизации проектирования технологических процессов обработки непрофилированным электродом инструмента для нарезания эвольвентного профиля на деталях.
К
11
особенностям проектирования и изготовления сборных долбяков с твердосплавными режущими элементами (втулками, пластинами) следует отнести малую жесткость элементов, большое соотношение длины пластин к их сечению в поперечном направлении, что снижает прочность этой части сборной конструкции. Современные ЭЭ станки позволяют разделять заготовки на точные элементы, в частности, пластины требуемой толщины (в нашем случае до 2 - 3 мм) с линейной скоростью до 8 мм/мин. Также проволочный инструмент дает возможность формировать геометрию рабочей кромки в процессе резания заготовки и получать профиль рабочей части с погрешностью менее 2 - 3 мкм при шероховатости (Ra) поверхностного слоя около 0,12 мкм (для сплавов вольфрамокобальтовой группы). Тогда заточка долбяков сводится к притирке рабочего контура собранных изделий алмазной пастой с удалением припуска не более 0,02 – 0,03 мм до достижения шероховатости 0,1 – 0,16 мкм, при которой уже не наблюдаются микродефекты, являющиеся концентраторами напряжений, снижающими стойкость инструмента.
Для получения качественных мелкомодульных долбяков требуется рассчитать профиль рабочей части инструмента и совместить его с установочными элементами корпуса долбяка. Созданная технология изготовления инструмента включает следующие этапы автоматизированной технологической подготовки:
- анализ геометрии корпусов долбяков, оценка жесткости корпуса и возможности установки режущей части из твердого сплава в форме цельного элемента, обладающего прочностью, достаточной для работы инструмента. Если диаметр долбяка не позволяет использовать цельную режущую часть, то проектируют твердосплавные пластины;
- выбор и назначение исходных сведений для расчета рабочего профиля и выбора режущих элементов (учет технических и экономических возможностей процессов разделения заготовок, сведений о геометрии и характеристиках непрофилированного электрода-проволоки, величинах межэлектродных зазоров, геометриях и свойствах заготовки, характеристиках материалов режущей части и др.);
- автоматизированное проектирование рабочего профиля режущих элементов с базированием от установочных баз корпуса и создание индивидуальной программы обработки каждого рабочего элемента, что обеспечивает необходимую точность инструмента после сборки;
- изготовление непрофилированным электродом-проволокой режущих элементов с формированием рабочей части инструмента, что позволяет получить для сборных твердосплавных долбяков рабочую часть с погрешностью не более ± 0,005 мм. Это устраняет необходимость в абразивной (в том числе алмазной) заточке, создающей повышенный нагрев, коробление и микрорастрескивание рабочей кромки инструмента;
- сборка изделия (как правило, с натягом, высокотемпературная пайка или диффузионная сварка) и установка режущих элементов на фиксированные базы корпуса;
-
12
контроль положения и профиля рабочей части инструмента, а также оценка погрешностей относительно расчетных параметров автоматизированного проектирования;
- контроль шероховатости поверхностного слоя (общий или выборочный);
- приемочный контроль инструмента.
Пятая глава отражает результаты опытно-промышленной эксплуатации метода изготовления прецизионных мелкомодульных долбяков в условиях гибкоструктурного производства. Его основной особенностью является частая смена номенклатуры выпускаемых деталей и узлов и, как следствие, переналадка технологического оборудования не только основного, но и вспомогательного производств. Здесь под вспомогательным производством понимается разработка конструкций и технологий изготовления режущего инструмента и средств технологического оснащения процесса. В основу таких производств положено использование современного высокопроизводительного оборудования на основе числового программного управления как механообрабатывающей группы, так и станков для электрических методов обработки. Сроки подготовки и освоения производства в таких условиях предельно сжаты и обеспечиваются за счет применения программных средств проектирования конструкции деталей, технологических процессов, их оптимизации и отладки и генерации управляющих программ для систем ЧПУ оборудования.
Применительно к мелкомодульному твердосплавному инструменту этот процесс содержит следующие этапы:
- получение технического задания на проектирование и производство инструмента;
- разработка конструкции инструмента на основе оптимальной геометрии и рациональном выборе твердосплавной режущей части;
- выбор и назначение режимов обработки с учетом имеющегося на предприятии оборудования;
- генерация, отладка и опытная апробация ЭЭО твердосплавной режущей части мелкомодульного инструмента;
- внесение, при необходимости, изменений в конструкцию и технологические режимы;
- повторная генерация и отладка управляющей программы для ЧПУ;
- передача технологического процесса в инструментальное производство и изготовление требуемого количества инструмента на электроэрозионном оборудовании с ЧПУ для нужд основного производства.
Примерные оценки времени на реализацию представленной последовательности действий показывают существенное его сокращение (8 - 10 раз) по сравнению с традиционной технологией получения долбяков.
Д
13
ля сокращения времени на проектирование режущего инструмента использованы программные продукты AutoDesk Inventor2012 (создание параметрических твердотельных моделей инструмента) и InventorCAM2011 (разработка и отладка технологии ЭЭО и генерация управляющих программ для стоек ЧПУ), установленные на Воронежском механическом заводе в конструкторских и технологических службах предприятия. С целью исключения ошибок при проектировании инструмента первоначально была создана оптимальная твердотельная параметрическая модель эвольвентного профиля твердосплавного мелкомодульного долбяка (рис. 4). Такой подход позволяет:
- при проектировании различных типоразмеров мелкомодульного зуборезного долбяка всегда оставаться в пределах его оптимальной геометрии;
- сократить сроки проектирования, так как цифровой прототип будущего инструмента уже имеется, при этом смена материала режущей части с переопределением физико-механических свойств конструкции происходит практически мгновенно;
- осуществлять быстрый пересчет всех параметров эвольвентного профиля, в зависимости от типоразмеров обрабатываемого зубчатого колеса, для этого предусмотрена возможность контроля взаимодействия долбяка с обрабатываемым колесом малого модуля (рис. 5).
Данные программные средства позволяют автоматизировать процесс оформления всей технической документации в соответствии с требованиями ЕСКД, включая рабочие и сборочные чертежи, спецификации, ведомости, карты техпроцессов и т.п.
![]() | ![]() |
Рис. 4. Твердотельная параметрическая модель заготовки для мелкомодульного твердосплавного долбяка | Рис. 5. Пример контроля зубообрабатывающего инструмента при контакте с объектом обработки |
С
14
оздание цифрового прототипа инструмента дает возможность моделирования технологии ЭЭО, ее отладку, коррекцию и визуализацию с помощью программного продукта InventorCAM2011 (рис. 6). При этом отрабатывается геометрия заготовки и готовой детали, которые передаются из Inventor2012, определяется траектория движения непрофилированного электрода-проволоки, назначаются режимы обработки, осуществляется визуальный контроль правильности созданного техпроцесса (рис. 7).
![]() | ![]() |
Рис. 6. Назначение режимов ЭЭО твердосплавного мелкомодульного инструмента | Рис. 7. Визуальный контроль и генерация управляющей программы по обработке долбяка |
На окончательном этапе осуществляется генерация управляющей программы для стойки ЧПУ имеющегося на предприятии электроэрозионного оборудования.
ОСНОВНЫЕ РЕЗУЛЬТАТЫ И ВЫВОДЫ
Разработан новый технологический процесс производства единичных прецезионных мелкомодульных режущих инструментов, выполненных в том числе из твердых сплавов, позволяющий в условиях гибкоструктурного производства сократить сроки (8 - 10 раз) перехода на новую номенклатуру основного производства, повысить производительность обработки мелкомодульных зубчатых колес от 1,5 до 2-х раз за счет повышения ресурса применяемого инструмента, снизить или исключить потребность в специализированном зуборезном механообрабатывающем оборудовании за счет его замены на современное электроэрозионное оборудование с ЧПУ.
1. В современном машиностроении с гибкоструктурной системой производства требуется большое количество наименований деталей с эвольвентными зубьями, шлицами и единичной программой выпуска. Мелкомодульные долбяки для этих целей требуется выпускать с твердосплавными режущими элементами, т.к. использование других инструментальных материалов не обеспечивает стойкость инструмента при обработке зубчатых венцов из высокопрочных материалов. Применяемые традиционные технологии изготовления сборного инструмента весьма трудоемки и сильно удорожают изделия с зубчатыми передачами и эвольвентными соединениями. В работе предложен новый способ изготовления мелкомодульных долбяков с твердосплавными элементами электроэрозионным методом непрофилированным электродом, показавший большие преимущества перед традиционными видами обработки (заявка № 2010130694, 2010 г.).
2
15
. Предложены конструкции долбяков, учитывающие специфику нового метода обработки, в частности, с рабочей частью в форме цельной втулки, обеспечивающей получение наибольшей точности нарезания эвольвентных зубьев. Обоснована возможность исключения шлифования на специальном дефицитном оборудовании, что заметно снижает потребности в материальных ресурсах в условиях гибкоструктурного производства (заявка № 2010141234, 2010 г.).
3. Разработан технологический процесс обработки непрофилированным электродом-проволокой, даны методики расчета углов резания и их обеспечение на имеющемся автоматизированном оборудовании, обеспечивающие точность и качество поверхности, исключающие последующую финишную механообработку зубодолбежного инструмента.
4. Показана область использования электроэрозионной обработки непрофилированным инструментом с покрытием, обеспечивающим производительность и повышающим возможности механообработки зубчатых колес в основном производстве, что делает рентабельным использование этого метода для изготовления не только мелкомодульных долбяков, но и зубчатых колес основного производства.
5. Показано место комбинированного процесса в общей структуре основного производства с обоснованием информационно-технологических связей с учетом его гибкоструктурности, позволяющее проводить обработку и накопление конструкторско-технологической информации инструментального и, в частности, зуборезного характера.
6. Создана, апробирована и применена в производстве система автоматизированного проектирования сопрягаемых поверхностей сборного зуборезного инструмента с малым модулем и ограниченным применением, которая сокращает ресурсозатраты как основного, так и инструментального производства.
7. Раскрыты пути повышения технологических возможностей предлагаемого метода на сложнопрофильные детали инструментального и основного гибкоструктурного производства за счет применения цифровых прототипов и моделирования условий их работы.
Основные результаты диссертации опубликованы в следующих работах:
Публикации в изданиях, рекомендованных ВАК РФ
- Кузовкин А.В. Силовые и тепловые факторы при формообразовании мелкомодульных зубчатых колес/А.В. Кузовкин, А.И. Коптев //Фундаментальные и прикладные проблемы техники и технологии. 2010. № 4. С. 15 – 21 (доля автора 0,4 п.л.).
- К
16
оптев А.И. Проектирование и изготовление сборных мелкомодульных долбяков с твердосплавной рабочей частью/А.И. Коптев, А.В. Кузовкин //Сборка в машиностроении, приборостроении. 2011. № 1. С. 17 - 27 (доля автора 0,5 п.л.).
- Кузовкин А.В. Режимы электроэрозионной и комбинированной обработки электродом-проволокой/А.В. Кузовкин, А.И. Коптев //Фундаментальные и прикладные проблемы техники и технологии. 2012. № 1. С. 25 – 28 (доля автора 0,3 п.л.).
Статьи и материалы конференций
- Кузовкин А.В. Особенности проектирования инструмента для зубообработки/А.В. Кузовкин, А.И. Коптев //Обеспечение качества продукции на этапах конструкторской и технологической подготовки производства: межвуз. сб. науч. тр. - Воронеж: ВГТУ, 2009. Вып. 4. С. 83 - 87 (доля автора 0,3 п.л.).
- Коптев А.И. Комбинированная обработка осесимметричного инструмента/А.И. Коптев, А.В. Кузовкин //Обеспечение качества продукции на этапах конструкторской и технологической подготовки производства: межвуз. сб. науч. тр. – Воронеж: ВГТУ, 2010. Вып. 5. С. 7 - 12 (доля автора 0,3 п.л.).
- Коптев А.И. Повышение прочностных характеристик осевого инструмента с мелким модулем /А.И. Коптев, А.В. Кузовкин// Обеспечение качества продукции на этапах конструкторской и технологической подготовки производства: межвуз. сб. науч. тр. – Воронеж: ВГТУ, 2010. Вып. 5. С. 31 - 35 (доля автора 0,3 п.л.).
- Коптев А.И. Влияние жесткости системы на точность профиля зуба с малым модулем /А.И. Коптев, А.В. Кузовкин //Студент, специалист, профессионал: сб. тр. III междунар. науч.-техн. конф. Воронеж: ВГТУ, 2010. С. 34 – 39 (доля автора 0,3 п.л.).
- Коптев А.И. Исследования твердосплавного инструмента при прерывистом резании /А.И. Коптев, А.В. Кузовкин //Обеспечение качества продукции на этапах конструкторской и технологической подготовки производства: межвуз. сб. науч. тр. – Воронеж: ВГТУ, 2011. Вып. 6. С. 54 - 59 (доля автора 0,4 п.л.).
- Коптев А.И. Исследование проблемы износа режущей части твердосплавного инструмента для нарезания зубчатых колес с мелким модулем /А.И. Коптев, А.В. Кузовкин //Обеспечение качества продукции на этапах конструкторской и технологической подготовки производства: межвуз. сб. науч. тр. - Воронеж: ВГТУ, 2011. Вып. 7. С. 65 - 74 (доля автора 0,4 п.л.).
Подписано в печать 10.02.2012.
Формат 60х84х16. Бумага для множительных аппаратов.
Усл. печ. л. 1,0. Тираж 100 экз. Заказ № ___
ФГБОУ ВПО "Воронежский государственный технический университет"
3
17
94026 Воронеж, Московский просп., 14