Разработка технологии и инструмента для непрерывного деформационного получения ультрамелкозернистой структуры стального сердечника при производстве высокопрочной сталемедной проволоки
Вид материала | Автореферат |
- Разработка и расчет непрерывного процесса получения порошка полиэтилена, 240.91kb.
- А пригодности использования инструментальных наладок и инструмента, формирование структуры, 28.93kb.
- V международная научно-практическая конференциЯ «информационные и коммуникационные, 290.79kb.
- Анализ результатов исследования образцов, наплавленных автоматической наплавкой под, 158.72kb.
- Разработка и строительство экологически безопасной технологии производства кремния, 48.31kb.
- Разработка технологии изготовления индивидуального зуборезного инструмента для мелкомодульных, 266.32kb.
- Рекомендации для расчета режущего инструмента при выполнении дипломного и курсового, 204.72kb.
- Методика расчёта остаточных напряжений при нарезании резьбы с учётом ультразвуковых, 21.57kb.
- Прорывные технологии в системах жизнеобеспечения, 3010.57kb.
- Методические указания к курсовому проекту, 194.16kb.
На правах рукописи
ЕМАЛЕЕВА ДИНАРА ГУМАРОВНА
РАЗРАБОТКА ТЕХНОЛОГИИ И ИНСТРУМЕНТА ДЛЯ НЕПРЕРЫВНОГО ДЕФОРМАЦИОННОГО ПОЛУЧЕНИЯ УЛЬТРАМЕЛКОЗЕРНИСТОЙ СТРУКТУРЫ СТАЛЬНОГО СЕРДЕЧНИКА ПРИ ПРОИЗВОДСТВЕ ВЫСОКОПРОЧНОЙ СТАЛЕМЕДНОЙ ПРОВОЛОКИ
Специальность 05.03.05 – Технологии и машины обработки давлением
Технические науки
АВТОРЕФЕРАТ
диссертации на соискание ученой степени
кандидата технических наук
Магнитогорск
2009
Работа выполнена в ГОУ ВПО «Магнитогорский государственный технический университет им. Г.И. Носова»
Научный руководитель: доктор технических наук,
профессор
Чукин Михаил Витальевич
Официальные оппоненты: доктор технических наук,
профессор
Трофимов Виктор Николаевич
кандидат технических наук
Коломиец Борис Андреевич
Ведущая организация: Научно-исследовательский институт
физики перспективных материалов
ГОУ ВПО «Уфимский государственный
авиационный технический университет»
(г. Уфа)
Защита состоится 29 декабря 2009 г. в 15-30 ч. на заседании диссертационного совета Д 212.111.03 при ГОУ ВПО «Магнитогорский государственный технический университет им. Г.И. Носова» по адресу:
455000,г. Магнитогорск, пр. Ленина, 38, МГТУ, малый актовый зал.
С диссертацией можно ознакомиться в библиотеке ГОУ ВПО «Магнитогорский государственный технический университет им. Г.И. Носова».
Автореферат разослан «27» ноября 2009 г.
Ученый секретарь
диссертационного совета Жиркин Ю.В.
ОБЩАЯ ХАРАКТЕРИСТИКА РАБОТЫ
Актуальность работы. Стабильное функционирование и развитие многих отраслей отечественной промышленности требует расширения сортамента композиционных материалов, в частности, биметаллической сталемедной проволоки. При этом на первый план встает задача повышения прочностных свойств сталемедной продукции, решение которой продиктовано непрерывно возрастающими требованиями железнодорожного транспорта и оборонного комплекса России.
Несмотря на прогрессивность используемых технологий твердофазного соединения элементов композиции, повышение прочностных свойств сталемедной проволоки с использованием углеродистых марок сталей и патентирования биметаллической заготовки невозможно в силу ряда технологических особенностей. К данным ограничениям можно отнести: снижение адгезионной прочности компонентов; охрупчивание проволоки в процессе «осветления» при прохождении ее в горячем состоянии через спиртовой раствор; образование химических соединений на поверхности медной оболочки в процессе патентирования и снижение результативности данного процесса из-за ухудшения теплообмена сердечника с расплавом охлаждающей среды, а также снижение экономической эффективности производства за счет использования более дорогих марок сталей.
Одно из наиболее перспективных направлений повышения прочностных и пластических свойств сталей - формирование ультрамелкозернистой (УМЗ) структуры в материалах деформационными способами. Однако, несмотря на многочисленные разработки, современные способы обладают рядом существенных ограничений в аспекте непрерывности и производительности технологических схем.
Таким образом, разработка новых, научно обоснованных технологических и технических мероприятий, адаптированных к условиям полномасштабного метизного производства и позволяющих получать высокие механические свойства сталемедной проволоки, является важной и актуальной задачей для экономики РФ.
Актуальность работы подтверждена поддержкой программ различного уровня, финансируемых из средств федерального бюджета (ФЦП «Исследования и разработки по приоритетным направлениям развития научно-технологического комплекса России на 2007-2012 годы»; ФЦП «Научные и научно-педагогические кадры инновационной России» на 2009-2013 годы; АВЦП «Развитие научного потенциала высшей школы»; программа «Участник Молодежного Научно-Инновационного Конкурса (У.М.Н.И.К)»).
Цель работы - разработка непрерывной деформационной схемы и инструмента для ее реализации, позволяющих формировать УМЗ структуру стального сердечника для гарантированного достижения высоких прочностных свойств сталемедной продукции.
Основные задачи работы:
1. Исследование эволюции структуры и свойств стального сердечника и сталемедной проволоки в процессе пластической деформации непрерывным способом равноканальной угловой свободной протяжки (РКУ протяжка).
2. Математическое моделирование процесса РКУ протяжки проволоки в среде Deform-3D и критериальная оценка напряженно-деформированного состояния (НДС) материала для разработки конструкции инструмента, обеспечивающего максимальную эффективность процесса обработки.
3. Разработка технологической схемы производства ультрамелкозернистой высокопрочной сталемедной проволоки диаметром 0,20 мм (ПБ-0,20), основанной на интеграции непрерывного способа РКУ протяжки в процессы волочения и адаптированной к условиям отечественных предприятий метизной отрасли. Промышленная апробация разработанных технологических решений и технических средств.
Научная новизна.
1. Предложен и научно обоснован новый непрерывный способ равноканальной угловой свободной протяжки, позволяющий формировать ультрамелкозернистую структуру стального сердечника для гарантированного достижения комплекса высоких механических свойств сталемедной проволоки.
2. Разработана методика критериальной оценки результативности процесса равноканальной угловой свободной протяжки, основанная на комплексной оценке технологической стабильности и достижении заданной степени и однородности напряженно-деформированного состояния проволоки.
3. Получено феноменологическое уравнение состояния ультрамелкозернистой стали марки 10, отражающее зависимость значений сопротивления деформации от степени деформации, для дальнейшего применения при проектировании технологических процессов обработки давлением.
Практическая значимость.
1. Разработана и опробована технологическая схема производства высокопрочной сталемедной проволоки ПБ-0,20 с сердечником из ультрамелкозернистой низкоуглеродистой стали, отличающаяся тем, что процесс многократной равноканальной угловой свободной протяжки внедряется в производственный цикл на стадии волочения и обеспечивающая достижение регламентируемого уровня механических свойств готовой продукции.
2. Разработана конструкция инструмента, предназначенного для формирования ультрамелкозернистой структуры стального сердечника сталемедной проволоки способом равноканальной угловой свободной протяжки.
3. Разработана и внедрена в условиях ООО «ЗМИ-Профит» методика проектирования инструмента, предназначенного для равноканальной угловой свободной протяжки сталемедной проволоки разных диаметров.
4. Впервые на базе технологии твердофазного соединения элементов композиции получена сталемедная проволока с сердечником из ультрамелкозернистой низкоуглеродистой стали, обладающая временным сопротивлением 1370 МПа.
5. Показана эффективность сочетания равноканальной угловой свободной протяжки сталемедной проволоки диаметром 4,3 мм с волочением. Экспериментально установлено, что предварительная многократная (до 8 циклов) равноканальная угловая свободная протяжка обеспечивает повышение показателей пластичности с 17 до 19 перегибов, прирост значений микротвердости - до 45% для поверхности и до 10% для центральной области при сохранении электропроводящих свойств сталемедной проволоки.
Реализация работы.
Результаты работы приняты к внедрению в ООО «ЗМИ-Профит» (г. Магнитогорск). На базе технологической схемы твердофазного соединения компонентов с использованием разработанных технологии и конструкции инструмента изготовлена опытно-промышленная партия высокопрочной сталемедной проволоки ПБ-0,20, соответствующая требованиям ТУ 14-4-691-75.
Результаты теоретико-экспериментальных исследований внедрены в учебный процесс ГОУ ВПО «МГТУ» и используются при подготовке инженеров по специальностям 150106 «Обработка металлов давлением» и 150108 «Порошковая металлургия, композиционные материалы, покрытия» со специализацией «Наноструктурные материалы и покрытия».
Апробация работы. Основные положения работы были доложены и обсуждены на Международном симпозиуме «Объемные наноматериалы: от науки к инновациям» (г. Уфа, 2007г.); VIII Международной научно-технической «Уральской школе-семинаре металловедов-молодых ученых» (г. Екатеринбург, 2007г.); Школе-семинаре «Коммерциализация научных разработок студентов и молодых ученых», проходящей в рамках программы У.М.Н.И.К. (г. Челябинск, 2007г.); Ежегодных научно-технических конференциях ГОУ ВПО «МГТУ» (г. Магнитогорск, 2007-2008 гг.); VI школе-семинаре «Фазовые и структурные превращения в сталях» (Башкортостан, 2008г.); «Втором Международном форуме по нанотехнологиям» (г. Москва, 2009г.).
Публикации. По теме диссертации опубликованы 17 научных публикаций, в т.ч. 2 в рецензируемых изданиях из перечня ВАК РФ.
Структура и объем работы. Диссертация состоит из 4 глав, изложена на 135 страницах машинописного текста (без приложений), иллюстрирована 71 рисунком, содержит 15 таблиц, 5 приложений, библиографический список включает 133 наименования.
СОДЕРЖАНИЕ РАБОТЫ
Во введении обоснована актуальность, сформулированы цель и задачи диссертационной работы.
Первая глава посвящена анализу возможных путей решения проблемы повышения уровня механических свойств биметаллической сталемедной продукции, получаемой в процессе твердофазного соединения компонентов.
Выполнен анализ особенностей технологии производства сталемедной проволоки способом твердофазного соединения компонентов. Выявлены ограничения, определяющие невозможность повышения прочностных свойств сталемедной проволоки с сердечником из средне- и высокоуглеродистой стали патентированием биметаллической заготовки с последующим с волочением на готовый размер.
На основе анализа зависимости свойств металлов и сплавов от размера структурных составляющих показана высокая эффективность применения деформационных методов формирования УМЗ структуры для значительной модификации свойств материалов без изменения их химического состава. Установлено, что при использовании специальных схем деформации переход материала в УМЗ состояние сопровождается существенным повышением прочностных при сохранении пластических свойств материала.
На основе патентных исследований и аналитического обзора данных, опубликованных в ведущих научных изданиях, разработана классификация современных способов пластического структурообразования материалов в зависимости от вида обрабатываемых заготовок (диск, объемные заготовки круглого или квадратного сечения, лист/полоса).
Выполнен комплексный анализ технологических особенностей наиболее эффективных способов пластического структурообразования объемных материалов, включая кручение под высоким давлением (с открытыми бойками и в бойках с полостью), всестороннюю ковку, циклическую деформацию «осадка – экструзия - осадка», способ винтовой экструзии, накапливаемое соединение прокаткой, способ многократного изгиба и выпрямления полосы, сonshearing-процесс, РКУ прессование (РКУП) и его разновидности (РКУП во вращающейся оснастке, РКУП с противодавлением, РКУП в оснастке с параллельными каналами или подвижными стенками, РКУ - «конформ» прессование) комбинированные схемы обработки. Установлено, что среди многочисленных разработок способ РКУП остается наиболее прогрессивной схемой обработки, позволяющей формировать однородную УМЗ структуру с преимущественно большеугловыми границами зерен. Выявлено, что, несмотря на преимущества, существующие способы, обладают низкой технологичностью и ограниченностью использования в промышленных условиях.
Обоснована необходимость развития существующих и создания принципиально новой или модернизированной непрерывной схемы деформации, адаптированной к условиям предприятий метизной отрасли и позволяющей формировать УМЗ структуру проволоки для гарантированного достижения высоких прочностных показателей сталемедной продукции.
В ходе анализа основных теоретических закономерностей, предложенных В.В. Рыбиным, В.М. Сегалом, Р.З. Валиевым, Ф.З. Утяшевым, Г.И. Раабом, В.И. Копыловым, В.Н. Чувильдеевым и др. показано, что в настоящее время не существует принятой научным сообществом единой теории процессов пластического структурообразования, обеспечивающих достижение качественно нового уровня механических свойств объемных материалов.
Вторая глава посвящена экспериментальному исследованию влияния РКУ протяжки на эволюцию структуры и изменение механических свойств длинномерных заготовок (сердечника и составной сталемедной композиции).
Разработан комплекс требований, предъявляемых в соответствии с современным уровнем развития науки и техники к процессу деформационной обработки сталемедной проволоки.
На основе комплексного анализа существующих схем пластического структурообразования, а также с учетом перспективных направлений их развития предложен непрерывный способ РКУ протяжки. В соответствии с предлагаемым способом сталемедная проволока многократно протягивается через сборный инструмент специального профиля. Ключевое отличие предлагаемого способа от большинства существующих деформационных схем формирования УМЗ структур - возможность использования процесса в условиях массового производства метизной отрасли. Непрерывность процесса деформационной обработки может достигаеться сочетанием РКУ протяжки с традиционным способом волочения проволоки.
С целью обеспечения эффективности и технологической стабильности РКУ протяжка реализуется при неполном заполнении инструмента проволокой, которая в процессе обработки сохраняет неизменной площадь поперечного сечения F и последовательно проходит следующие области (рис. 1):
- зона свободного входа проволоки в инструмент (область I);
- зона упруго-пластического контакта и изгиба проволоки в области пересечения каналов инструмента (область II);
- межочаговая область (область III);
- зона упруго-пластического контакта и изгиба проволоки в области выхода из инструмента (область IV);
- зона свободного выхода проволоки из инструмента (область V).
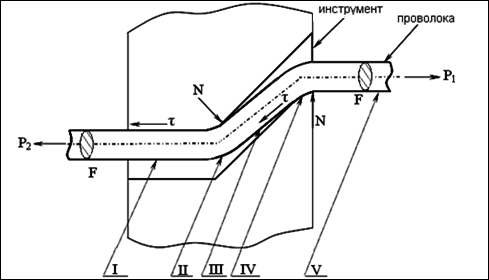
Рис.1. Принципиальная схема процесса РКУ протяжки
Выполнено исследование влияния многократной (до 10-ти раз) РКУ протяжки на эволюцию структуры и изменение свойств сердечника диаметром 5.5, 5.0, 4.5, и 4.2 мм (сталь марки 10), определяющего прочность сталемедной проволоки. Показано, что РКУ протяжка сопровождается значительной фрагментацией структурных составляющих поверхности и центральной области образцов независимо от их диаметра. Уже после N = 2 и вплоть до N = 10 циклов обработки наблюдается интенсивное измельчение структуры проволоки.
В результате анализа структуры образцов разного диаметра выделены следующие стадии формирования УМЗ структуры поверхности проволоки:
- формирование равномерного слоя (1-ый - 4-ый проходы);
- развитие слоя в глубину материала (4-ый - 7-ой проходы);
- стадия накопления дефектов (7-ой - 9-ый проходы);
- частичное разрушение и отслоение поверхностного диспергированного слоя (9-ый и последующие проходы). Накопление дефектов - неприемлемое явление, требующее проведения дальнейших исследований и выбора наиболее эффективных параметров РКУ протяжки.
Посредством дифракционного электронно-микроскопического анализа установлено, что РКУ протяжка обуславливает существенное измельчение структурны не только на поверхности, но и в центре проволоки (Рис 2).
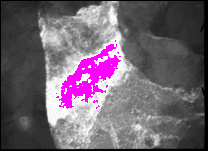
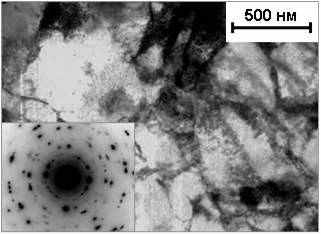
а б
Рис. 2. Типы микроструктур, формирующихся в процессе РКУ протяжки
в центральной области проволоки из стали марки 10:
а - фрагментированные зерна феррита (темнопольное изображение; х 37000);
б – УМЗ структура (светлопольное изображение и электронограмма; х 30000)
Как видно из рисунка, в центре сердечника наблюдаются фрагментированные зерна феррита (размер фрагментов 300-360 нм), т.е происходит образование субграниц, сопровождающееся разориентацией микрообъемов в пределах одного зерна (Рис.2 а). Вместе с тем наблюдаются области с множеством ультрамелких зерен феррита, имеющих большеугловые границы и ориентированных произвольным образом. Указанные границы являются неравновесными – они изогнуты и имеют сложную дислокационную структуру. В соответствии с литературными данными образование такого вида границ, способных на сдвиг, инициирует возникновение специфичного механизма пластической деформации (зернограничное проскальзывание) и, как следствие, повышение пластических свойств материала. Электронограммы аналогичных участков, полученные методом микродифрации электронов, представляют собой множество рефлексов, расположенных по концентрическим окружностям, т. е. являются практически кольцевыми (Рис.2 б).
В ходе исследования образцов, полученных традиционным волочением с суммарным относительным обжатием более 60%, показано, что в отличие от РКУ протяжки при волочении образуются лишь субзеренная структура с ячейками размером порядка 1,25 мкм, окруженными стенками из дислокаций (Рис. 3). Электронограмма состоит из комбинации ярких пятен, что характерно для электронограмм от монокристалла. Формирование такого типа субзеренных структур не может обеспечить достижение высокой прочности при сохранении пластичности материала.
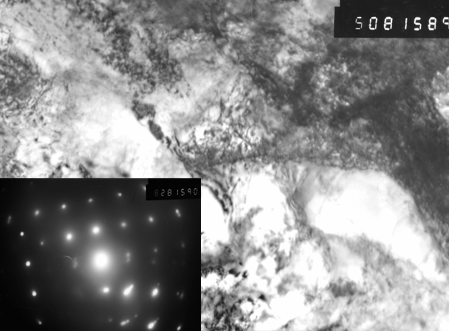
Рис. 3. Структура проволоки из стали марки 10 после волочения
с суммарным относительным обжатием более 60%
(светлопольное изображение и электронограмма; х 50000)
Представленная на рисунке 2 б структура сравнима со структурой стали марки 20, полученной четырехкратным РКУП с предварительным улучшением в условиях ГОУ ВПО «УГАТУ» (г. Уфа) при температуре 4000С. Сравнительный анализ значений микротвердости образцов из УМЗ сталей марки 10 и марки 20, полученных РКУ протяжкой и РКУП соответственно показал, что микротвердость поверхности проволоки из стали марки 10 (
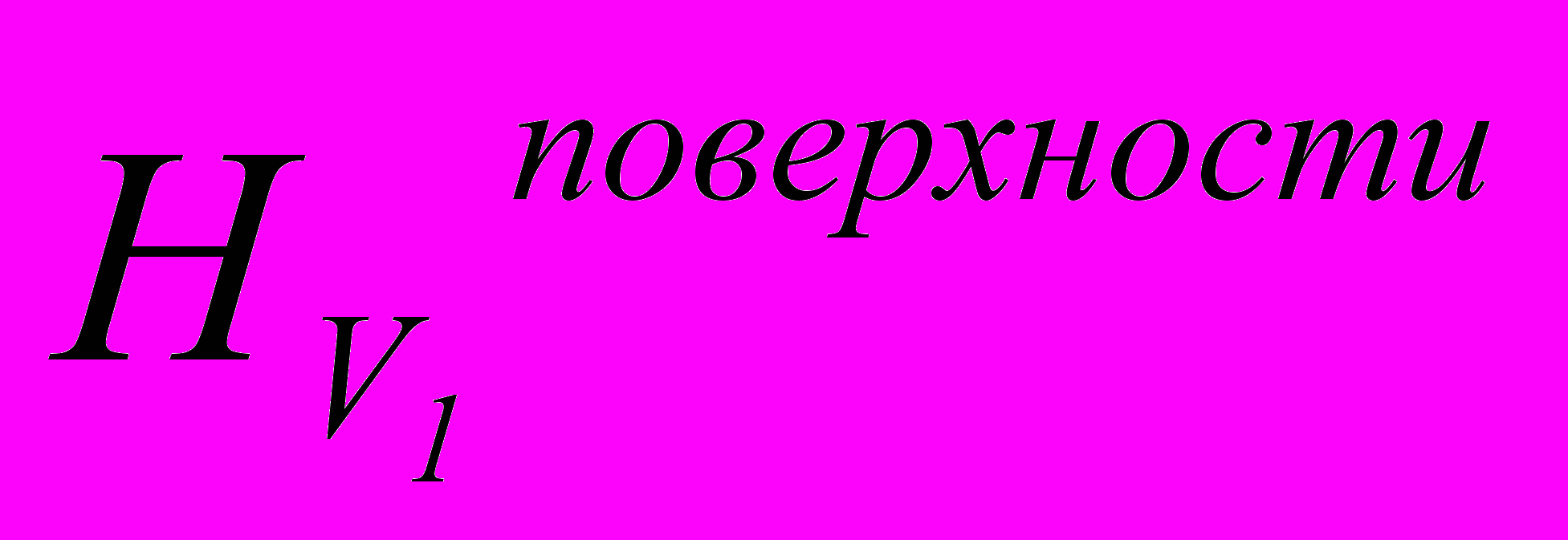
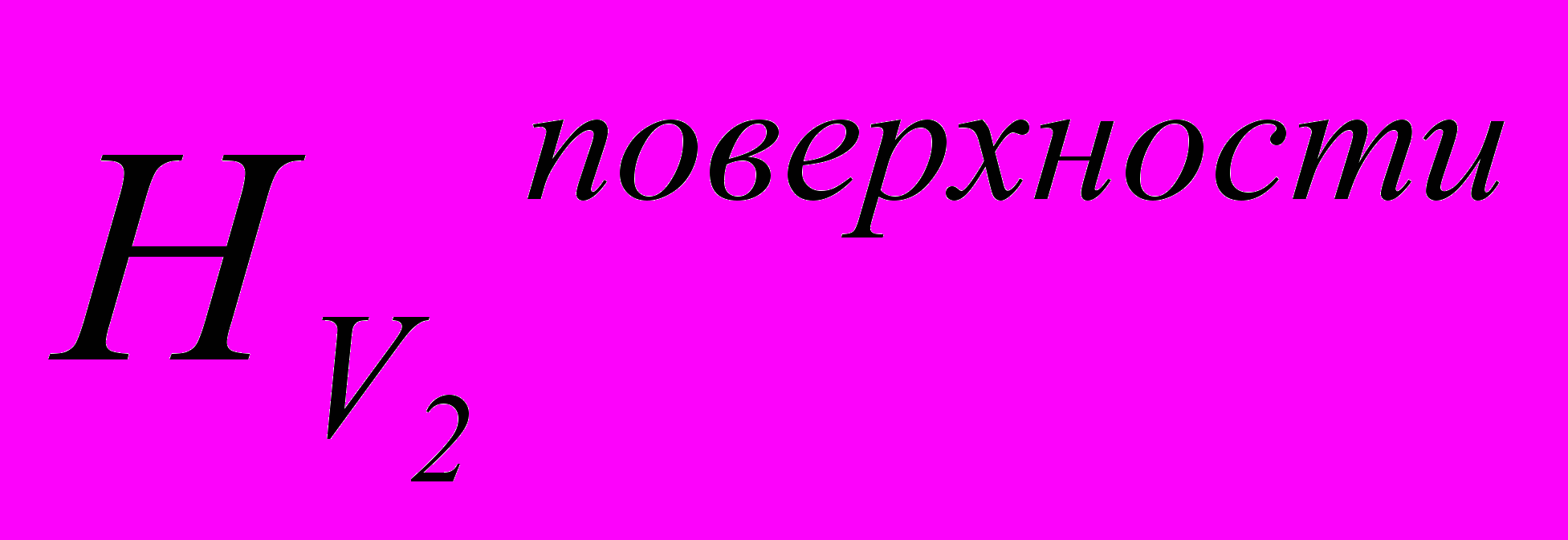
Посредством исследования распределения микротвердости по сечению образцов, полученных РКУ протяжкой, подтверждена неоднородность структуры, сформированной в поперечном сечении проволоки, и закономерность преимущественного упрочнения ее поверхности. Максимальный прирост микротвердости поверхности стальной проволоки относительно центральной области составляет более 1000 МПа (для образца диаметром 5,0 мм, подвергнутого РКУ протяжке за 10 проходов).
Исследованы реологические свойства проволоки из традиционной и УМЗ низкоуглеродистой стали, полученной в процессе РКУ протяжки. Описана методика проведения пластометрических испытаний.
Построены кривые деформационного упрочнения стали марки 10, находящейся в исходном и УМЗ состояниях. В ходе сравнительного анализа значений сопротивления деформации показано, что в зависимости от степени деформации формирование УМЗ структуры позволило повысить значения сопротивление деформации в диапазоне от 5 до 35%. По сравнению с крупнозернистым аналогом максимальное значение прироста сопротивления деформации УМЗ заготовок достигает значения 170МПа и наблюдается при степени деформации порядка 10%. При переходе в УМЗ состояние пластические свойства стали сохраняются и предопределяют возможность обработки проволоки волочением (максимальная степень деформации материала при осадке образцов с традиционной и УМЗ структурой составляет 65%).
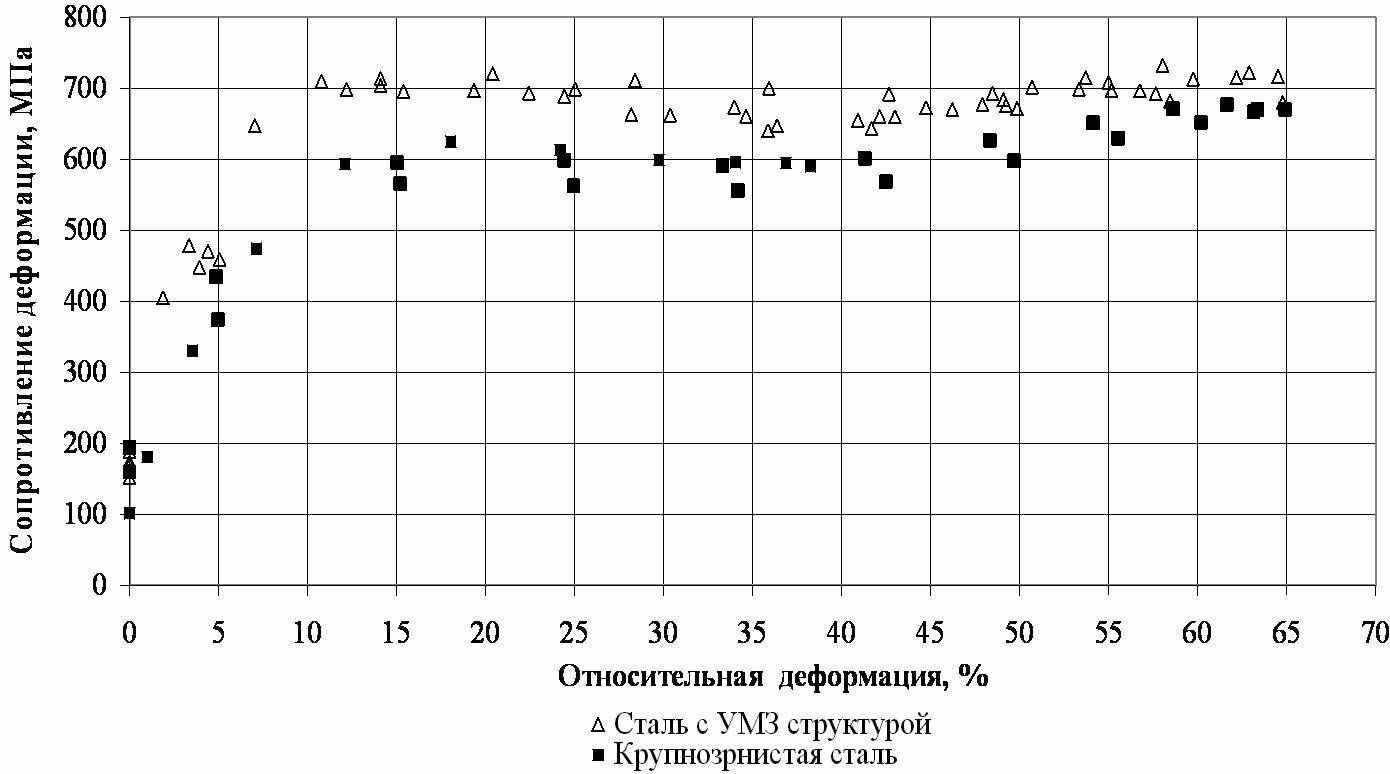
Рис. 4. Исследование влияния процесса РКУ протяжки на реологические свойства низкоуглеродистой стали марки 10
Аппроксимации полей экспериментальных данных полиномом 4-го порядка получены феноменологические уравнения состояния крупно- и УМЗ низкоуглеродистой сталей марки 10, отражающие характер и степень изменения прочностных свойств заготовок в процессе обработки давлением:
1. Уравнение состояния крупнозернистой стали марки 10

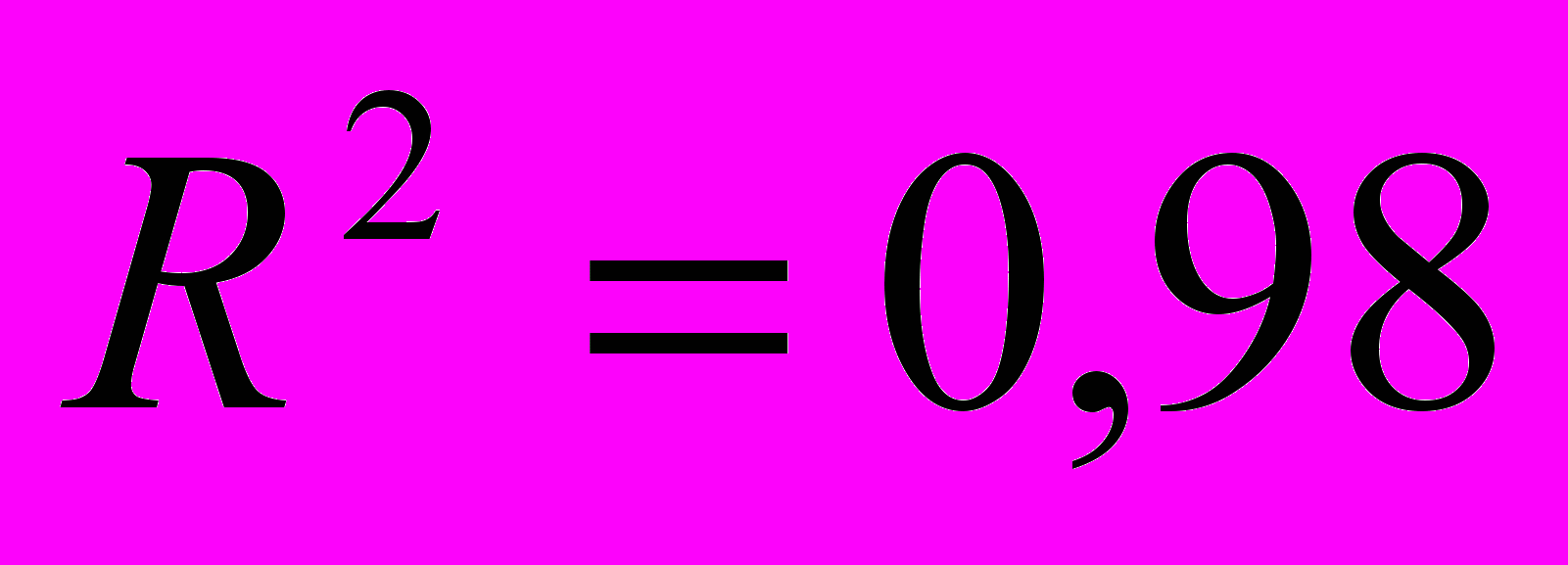
2. Уравнение состояния УМЗ стали марки 10

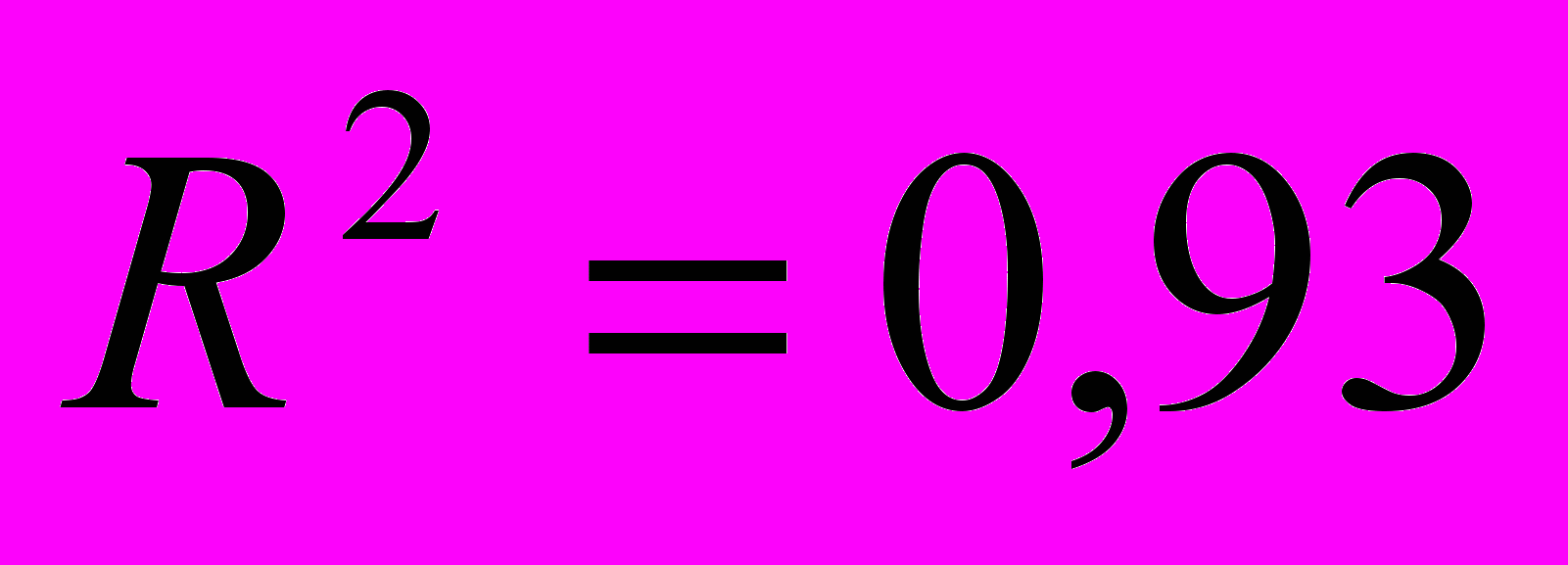
где
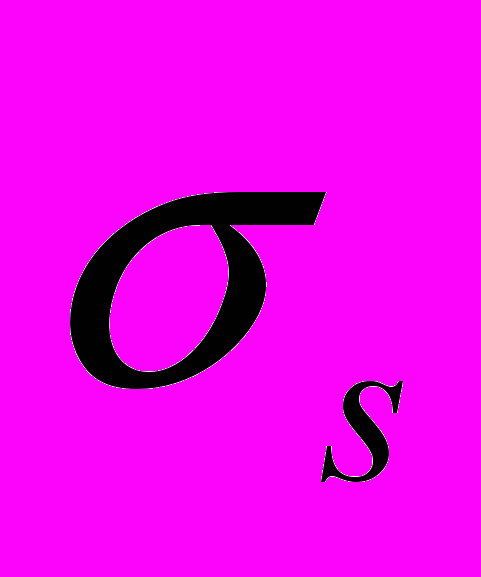
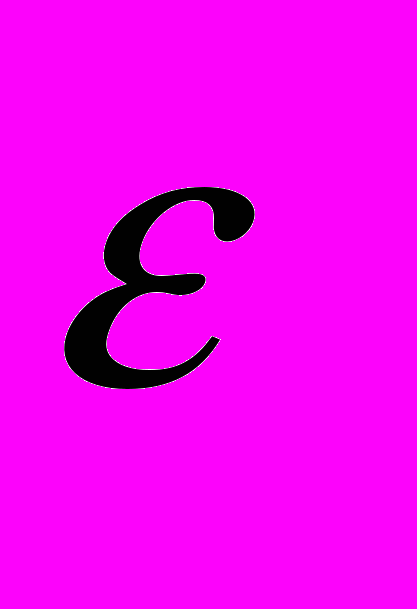
Уравнения (1) и (2) могут быть использованы при проектировании режимов деформирования заготовок и прогнозировании свойств конечной металлопродукции, полученной, в том числе, с использованием УМЗ сталей.
Доказана возможность и эффективность использования РКУ протяжки для значительной модификации структуры и управления свойствами сталемедной проволоки. Показано, что совмещение многократной (до 8 раз) РКУ протяжки с волочением проволоки на меньший диаметр (с 4,2 мм до 3,7 мм) сопровождается значительными структурными изменениями и позволяет добиться следующих наиболее важных результатов:
1. Прирост значений микротвердости - до 45% для поверхности и до 10% для центральной области. Сравнение значений микротвердости сердечника разного диаметра d (d = 3,7 мм и d = 3,2 мм) показало, что упрочнение, обусловленное формированием УМЗ структуры материала, значительно превышает деформационное упрочнение, сопровождающее традиционное волочение на меньший диаметр без предварительной РКУ протяжки.
2. Повышение показателей пластичности с 17 до 19 перегибов (для проволоки, подвергнутой волочению с предварительной РКУ протяжкой 8 циклов).
3. Сохранение электропроводящих свойств проволоки - прирост значений электросопротивления, обусловленный предварительной РКУ протяжкой не превышает 4,5% (полученные значения удовлетворяют требованиям ГОСТ 3822-79).
4. Качественное соединение компонентов проволоки, обеспечивающее целостность меди при действии на проводник знакопеременных напряжений.
Третья глава посвящена математическому моделированию процесса РКУ протяжки проволоки в среде Deform-3D (лицензия: Machine 38808).
Установлена взаимосвязь варьируемых и зависимых геометрических показателей инструмента, предназначенного для РКУ протяжки (Рис.5):
- диаметр горизонтального канала инструмента
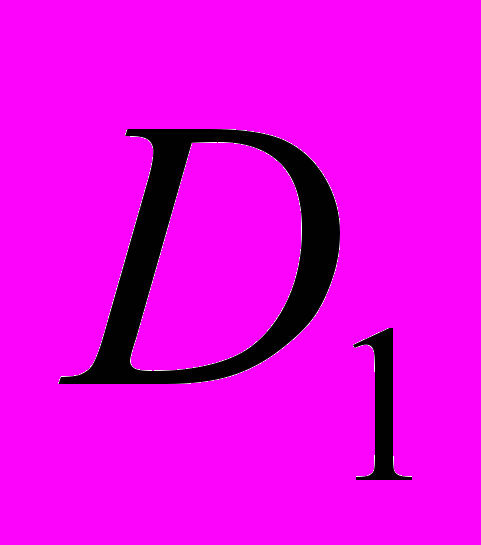
- диаметр наклонного канала инструмента
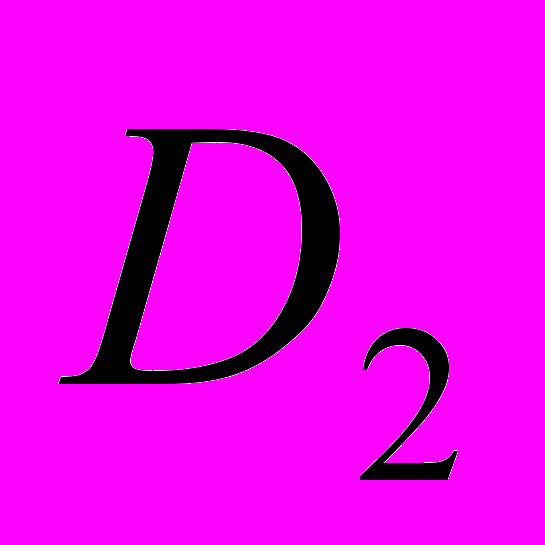
- угол пересечения каналов инструмента Ф=(180º-α), град.
- радиус пластин, образующих инструмент Rп, мм;
- толщина пластины, образующей горизонтальный канал Lвх, мм;
- толщина пластины, образующей наклонный канал Lвых, мм;
- радиусы скруглений кромок каналов r, мм;
- длина оси поперечного сечения выходного канала (эллипс) Н, мм.
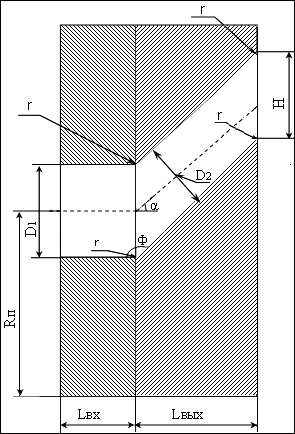
Рис. 5. Принципиальная схема инструмента для РКУ протяжки
В зависимости от соотношения диаметров пересекающихся каналов и их взаимного расположения разработаны 3 варианта конструкции (Рис.6):
- диаметр наклонного канала инструмента изменяется в зависимости от диаметра входного отверстия;
- диаметры каналов равны между собой. Пересечение каналов и образование очага деформации достигается смещением осей их симметрии;
- диаметры каналов равны между собой. Образование очага деформации достигается совмещением осей их симметрии. С учетом относительной простоты изготовления и минимального уровня энергосиловых затрат, сопровождающих процесс деформации, аналогичная конструкция использовалась при проведении теоретико-экспериментальных исследований.
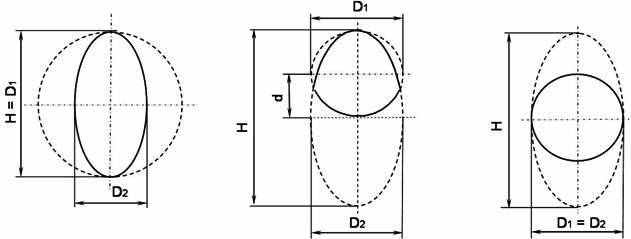
а б в
Рис. 6. Возможный вид сопряжения каналов,
пересекающихся под углом 120º:

С использованием прикладных программ Microsoft Excel разработана методика автоматического расчета и построения проектировочных схем, учитывающих основные геометрические параметры инструмента, предназначенного для РКУ протяжки сталемедной проволоки разных диаметров.
Предложена и научно обоснована методика критериальной оценки результативности процесса РКУ протяжки. Исходя из предназначения и физической сущности РКУ протяжки, предполагающей одновременный знакопеременный изгиб и одноосное растяжение при неизменности геометрических размеров проволоки, разработан комплекс критериев, которые можно разделить на две группы (Рис. 7):
1. Критерий, обеспечивающий технологическую стабильность РКУ протяжки. Физический смысл критерия заключается в недопустимости превышения значений интенсивности напряжений, возникающих в переднем конце стального сердечника под действием усилия протяжки, величины временного сопротивления материала. Нарушение условия приведет к обрыву переднего конца проволоки.
2. Критерии, обеспечивающие достижение необходимой степени и однородности НДС материала:
2.1. Условие пластичности Губера-Мизеса. В соответствии с критерием РКУ протяжка должна обеспечивать пластическое течение, обусловленное достижением интенсивности напряжений, возникающих при прохождении проволоки через инструмент, предела текучести материала.
2.2. Максимальная равномерность распределения интенсивности напряжений по сечению заготовки. Выполнение критерия обеспечивает однородность формируемой УМЗ структуры и свойств по сечению проволоки.
2.3. Стремление уровня интенсивности деформаций сдвига по сечению проволоки к максимальной величине. Выполнение критерия обеспечивает высокий уровень деформаций сдвига, обуславливающих формирование УМЗ структуры проволоки в процессе РКУ протяжки.
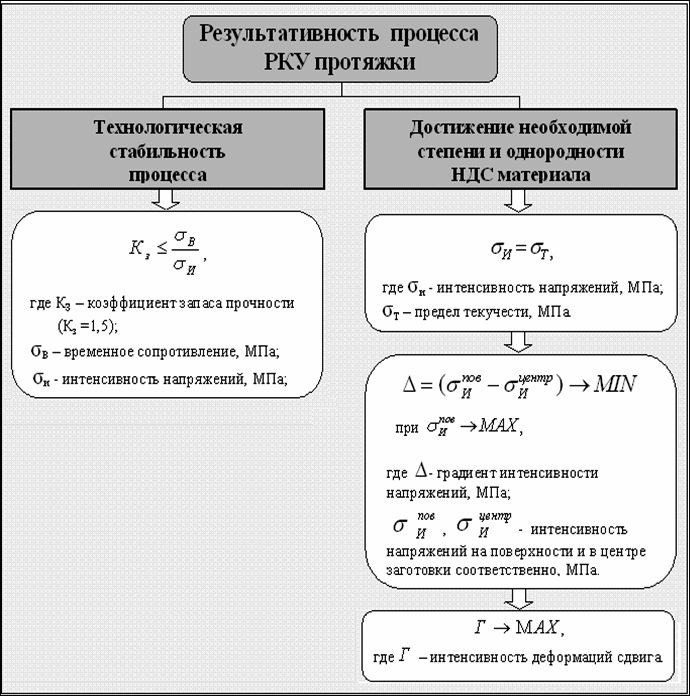
Рис. 7. Критериальная оценка результативности процесса РКУ протяжки
Разработана методика проектирования процесса РКУ протяжки проволоки в программном комплексе Deform-3D. Моделирование выполнялось в два этапа. На первом этапе для стального сердечника, определяющей механические свойства сталемедной проволоки, выполнен полный факторный эксперимент. В качестве варьируемых параметров и диапазонов их изменяемых значений были приняты данные, полученные при анализе результатов лабораторных экспериментов (табл.1).
Таблица 1
Факторы, используемые при моделировании РКУ протяжки в среде Deform-3D
Факторы | Значение факторов | |||
заполнение инструмента, % | угол пересечения каналов, град | толщина пластин каналов, мм | радиус скруглений кромок каналов, мм | |
Основной уровень | 65 | 125 | 7,5 | 0,4 |
Интервал варьирования | 5 | 5 | 2,5 | 0,2 |
Верхний уровень (+1) | 70 | 130 | 10 | 0,6 |
Нижний уровень (-1) | 60 | 120 | 5 | 0,2 |
В ходе проведения модельного эксперимента анализировалось НДС проволоки. В соответствии с разработанной методикой для 16 конструкций, отличающихся геометрическими параметрами, выполнялась критериальная оценка эффективности РКУ протяжки, что позволило выбрать инструмент, обеспечивающий стабильность процесса и достижение необходимых интенсивности и равномерности НДС проволоки диаметром 4,7 мм (табл.2).
Необходимость повышения свойств сталемедной проволоки ПБ-0,20 потребовала разработки конструкции, предназначенной для РКУ протяжки биметаллической проволоки меньшего диаметра. Поэтому с использованием результатов критериальной оценки процесса обработки стального сердечника предложена конструкция и выполнено моделирование РКУ протяжки сталемедной проволоки диаметром 1,0 мм. Толщина пластин L [мм] рассчитывалась по первой теореме геометрического подобия линейных размеров (табл.2). Вследствие небольших размеров конструкции геометрическое подобие радиусов скруглений кромок каналов r [мм] не соблюдалось.
Таблица 2
Конструктивные параметры инструмента, предназначенного для РКУ протяжки поволоки разных диаметров
Параметр | Значение параметра | |
Диаметр проволоки Dп, мм | 4,7 | 1,0 |
Диаметр горизонтального канала D1, мм | 6,7 | 1,43 |
Заполнение инструмента проволокой, % | 70 | 70 |
Угол пересечения каналов Ф, град. | 120 | 120 |
Толщина пластин L, мм | 5 | 1,1 |
Радиус скруглений кромок каналов r, мм | 0,2 | 0,05 |
Как показало моделирование, РКУ протяжка сталемедной проволоки проходит без обрыва и обеспечивает достижение высоких значений интенсивности деформаций сдвига Г (до значения Г = 1,2 -для сердечника и Г = 3 - для медной оболочки), обеспечивающих эффективность процесса обработки.
Посредством моделирования процессов волочения и испытания на одноосное растяжение выполнен сравнительный анализ прогнозируемых прочностных свойств сталемедной проволоки с сердечником из традиционной и УМЗ стали марки 10. Реологические свойства материалов задавались с использованием экспериментальных кривых, полученных в ходе пластометрических испытаний. Максимальный прирост прогнозируемых значений временного сопротивления проволоки с УМЗ сердечником достигает 35%. Таким образом, использование УМЗ стали взамен традиционной обеспечивает существенное повышение прочностных свойств проволоки.
Четвертая глава. В результате комплекса теоретико-экспериментальных исследований разработаны технологическая схема и инструмент, предназначенные для производства высокопрочной сталемедной проволоки ПБ-0,20 и адаптированные к условиям ООО-ЗМИ «Профит». В соответствии с предлагаемой схемой процесс четырехкратной РКУ протяжки заготовки внедряется в производственный цикл на стадии тонкого волочения отожженной сталемедной проволоки диаметром 1,0 мм. Положительное влияние предварительной термообработки подтверждено экспериментально (обусловленный РКУ протяжкой прирост значений временного сопротивления отожженного стального сердечника достигает 30%).
С учетом требований к стойкости, теплопроводности и качеству поверхности инструментов, к применению рекомендованы вольфрамокобальтовые твердые сплавы, соответствующие требованиям ГОСТ 3882-74.
Предложена альтернативная конструкция высокотехнологичного инструмента, используемого в составе традиционного волочильного оборудования и обеспечивающего непрерывность процесса РКУ протяжки проволоки. Выбор вида конструкции определяется геометрическими размерами обрабатываемой проволоки и особенностями волочильного оборудования, в составе которого используется инструмент.
В ходе предварительных экспериментальных исследований подтверждена эффективность предлагаемых технологических режимов и инструмента деформационной обработки. Растровый электронно-микроскопический анализ показал, что РКУ протяжка сталемедной проволоки вызывает значительные изменения как на поверхности, так и в центральной области образцов. Структура центральной области состоит из сильноизогнутых и волнообразных зерен феррита размером от 200 до 430 нм, а также ультрамелких карбидных частиц размером до 60 нм. Среднее значение микротвердости в центре проволоки повышаются с 2090 до 2870 МПа.
В условиях ООО «ЗМИ-Профит» выполнена опытно-промышленная апробация предлагаемой технологической схемой производства высокопрочной сталемедной проволоки ПБ-0,20. Первоначально при апробации РКУ протяжки в производственных условиях отмечена обрывность проволоки и предприняты следующие меры:
- Усовершенствована конструкция технологического инструмента, предназначенного для РКУ протяжки: кромки горизонтального и наклонного деформирующих каналов закруглены.
- Скорректирован технологический маршрут обработки, в соответствии которым РКУ протяжка внедряется в производственный цикл на стадии тонкого волочения отожженной сталемедной проволоки диаметром 1,2 мм. Таким образом, РКУ протяжке подвергается предварительно наклепанная сталемедная проволока диаметром 1,0 мм, обладающая уровнем прочностных свойств достаточным для дальнейшей деформационной обработки.
Использование усовершенствованной конструкции и скорректированного маршрута обработки позволило изготовить опытную партию проволоки ПБ-0,20 с сердечником из УМЗ низкоуглеродистой стали. Посредством независимых испытаний, выполненных в условиях заводской лаборатории ООО «ЗМИ-Профит», подтверждено, что временное сопротивление образцов полученной проволоки принимает значение 1370 МПа; электрическое сопротивление - 1,64 Ом/м число скручиваний на 3600 - 20 раз, навивание на собственный диаметр – удовлетворительно.
ОСНОВНЫЕ ВЫВОДЫ
1. На основе комплексного анализа особенностей существующих деформационных способов формирования УМЗ структуры, а также с учетом перспективных направлений их развития предложен и научно обоснован непрерывный способ равноканальной угловой свободной протяжки (РКУ протяжка) сталемедной проволоки.
2. В ходе комплекса экспериментальных исследований влияния РКУ протяжки на эволюцию структуры и изменение механических свойств длинномерных изделий доказана принципиальная возможность и эффективность использования предлагаемого непрерывного способа для формирования УМЗ структуры и повышения прочностных свойств сталемедной проволоки.
3. Посредством дифракционного электронно-микроскопического анализа и исследования распределения микротвердости по сечению стальной проволоки диаметром 5,0 мм, подвергнутой 10-ти циклам РКУ протяжки, выявлены неоднородность структуры в поперечном сечении проволоки и закономерность преимущественного упрочнения ее поверхности (прирост микротвердости поверхности проволоки относительно центральной области составляет более 1000 МПа).
4. Посредством аппроксимации данных пластометрических исследований получены феноменологические уравнения состояния традиционной и УМЗ стали марки 10, отражающие характер и степень изменения прочностных свойств заготовок в процессе обработки давлением.
5. С использованием прикладных программ Microsoft Excel разработана методика автоматического расчета и построения проектировочных схем, учитывающих основные геометрические параметры инструмента, предназначенного для РКУ протяжки сталемедной проволоки разных диаметров
6. Предложена методика критериальной оценки эффективности процесса РКУ протяжки, основанная на комплексном анализе технологической стабильности, формализуемой отношением значений временного сопротивления к интенсивности напряжений на выходе из инструмента, а также критериев достижения необходимой степени и однородности НДС материала в очагах деформации, формализуемых соблюдением условия пластичности Губера-Мизеса, снижением градиента интенсивности напряжений, действующих на поверхности и в центре проволоки, стремлением интенсивности деформации сдвига к максимальной величине.
7. На основе анализа результатов моделирования процесса РКУ протяжки стальной проволоки в программном комплексе Deform-3D разработана конструкция технологического инструмента, обеспечивающего непрерывность и эффективность процесса РКУ протяжки стальной проволоки диаметром 4,7 мм и сталемедной проволоки лиаметром 1,0 мм.
8. Разработана и апробирована в условиях ООО «ЗМИ-Профит» технологическая схема производства ультрамелкозернистой сталемедной проволоки ПБ-0,20 с сердечником из УМЗ низкоуглеродистой стали, основанная на интеграции способа РКУ протяжки в процессы волочения и адаптированная к условиям предприятий метизной отрасли. Физико-механические свойства полученной проволоки соответствуют требованиям ТУ 14-4-691-75, в том числе: временное сопротивление композиции принимает значение 1370 МПа; электрическое сопротивление - 1,64 Ом/м; число скручиваний на 3600 - 20 раз, навивание на собственный диаметр – удовлетворительно.
Основные положения диссертации опубликованы в работах
1. Емалеева Д.Г. Повышение уровня механических свойств стальной проволоки формированием наноструктуры поверхностного слоя. Инновации молодых учёных: Сборник докладов 65-ой научно-технической конференции. Магнитогорск: ГОУ ВПО «МГТУ», 2007. С. 36-42.
2. Исследование формирования субмикрокристаллической структуры поверхностного слоя стальной проволоки с целью повышения уровня ее механических свойств / Г.С. Гун, М.В. Чукин, Д.Г. Емалеева и [др.]. Вестник МГТУ им. Г.И. Носова. Магнитогорск: ГОУ ВПО «МГТУ», 2007. № 3. С. 84–86 (рецензируемое издание, рекомендованное ВАК РФ).
3. Емалеева Д.Г., Чукин М.В. Влияние термической обработки на эволюцию структуры и свойств стальной проволоки в процессе РКУПротяжки. Вестник МГТУ им. Г.И. Носова. Магнитогорск: ГОУ ВПО «МГТУ», 2008. №2. С. 70 – 71 (рецензируемое издание, рекомендованное ВАК РФ).
4. Гун Г.С., Чукин М.В., Емалеева Д.Г. Формирование субмикрокристаллической структуры поверхностного слоя стальной проволоки с целью повышения уровня её механических свойств. Производство конкурентоспособных метизов. Сб. науч. тр.: под ред. А.Д. Носова. Магнитогорск: ГОУ ВПО «МГТУ», 2007. Вып.2 . С. 103 – 108.
5. Increase of Mechanical Properties of Steel Wire by Formation of Submicrocrystalline Structure of Surface Coating in the Process of Equal Channel Angular Drawing / D.G. Emaleeva, Gun G.C., Chukin M.V. Abstracts of International Symposium “Bulk Nanostructured Materials: from Fundamentals to Innovations”. International Scientific Issue. Ufa. 2007. Р. 134-135.
6. Формирование субмикрокристаллической структуры поверхностного слоя стальной проволоки методом РКУПротяжки / Г.С. Гун, М.В. Чукин, Д.Г. Емалеева и [др.]. Труды седьмого конгресса прокатчиков. Т.1. М.: Черметинформация, 2007. С. 364 – 368.
7. Ефимова Ю.Ю., Емалеева Д.Г., Ситникова М.И. Формирование структуры и свойств сталемедной композиции в процессе равноканальной угловой протяжки. Материалы VIII Международной научно-технической Уральская школы-семинара металловедов-молодых ученых. Екатеринбург: ГОУ ВПО «УГТУ-УПИ», 2007. С. 43-46.
8. Формирование субмикрокристаллической структуры и свойств сталемедной проволоки в процессе равноканальной угловой протяжки / Ю.Ю. Ефимова, Д.Г. Емалеева, А.В. Мохнаткин и [др.]. Межрегион. сб. науч. тр.: под ред. В.М. Колокольцева. Вып. 7. Магнитогорск: ГОУ ВПО «МГТУ», 2008. С. 60 – 64.
9. Increase of Mechanical Properties of Steel Wire by Formation of Submicrocrystalline Structure of Surface Coating in the Process of Equal Channel Angular Drawing / D.G. Emaleeva, Gun G.C., Chukin M.V. Научно-технические ведомости. СПб: ГОУ ВПО «СПбГПУ», 2007. С. 16-20.
10.Исследование влияния схем наноструктурирования на реологические свойства низкоуглеродистых сталей / М.П. Барышников, Д.Г. Емалеева, А.В. Мохнаткин и [др.]. Моделирование и развитие процессов ОМД. Сб. науч. тр.: под ред. В.М. Салганика. Магнитогорск: ГОУ ВПО «МГТУ», 2009. С. 247-252.
11. Критериальная оценка эффективности процесса РКУ протяжки при моделировании в среде Deform-3D / М.П. Барышников, Д.Г. Емалеева, А.С. Кузнецова и [др.]. Моделирование и развитие процессов ОМД: Сб. науч. тр.: под ред. В.М. Салганика. - Магнитогорск: ГОУ ВПО «МГТУ», 2009. С. 253-259.
12. Исследование структуры и свойств стального сердечника с целью повышения качества сталемедной катанки в технологии твердофазного соединения / М.В. Чукин, Н.В. Копцева, Д.Г. Емалеева и [др.]. Фазовые и структурные превращения в сталях: сб. науч. тр., Вып. 5 / Под ред. В.Н. Урцева – Магнитогорск, 2008. С. 533-541.
13. Чукин М.В. Копцева Н.В. Емалеева Д.Г. Исследование структуры и состояния поверхности медной ленты с целью повышения качества сталемедной катанки в технологии твердофазного соединения. Моделирование и развитие процессов ОМД. Сб. науч. тр.: под ред. В.М. Салганика. Магнитогорск: ГОУ ВПО «МГТУ», 2006. С. 215-222.
14. Ефимова Ю.Ю., Емалеева Д.Г., Михайлова Е.А. Влияние процессов термической обработки сталей 20 и 45 на эволюцию структуры и свойств в процессе равноканального углового прессования. Материалы всероссийской научной конференции молодых ученых. Ч. 2. Новосибирск: НГТУ, 2007. С. 150-152.
15. Влияние термической обработки конструкционных углеродистых сталей на эволюцию структуры и свойств в процессе наноструктурирования и последующей пластической деформации / М.В. Чукин, Н.В. Копцева, Д.Г. Емалеева и [др.]. Материалы XIX Уральской школы металловедов-термистов, посвященной 100-летию со дня рождения академика В.Д. Садовского. Екатеринбург: ГОУ ВПО «УГТУ-УПИ», 2008. С. 47-48.
16. Эволюция структуры и свойств сталемедной биметаллической проволоки в процессе равноканальной угловой свободной протяжки / Н.В. Копцева, Ю.Ю. Ефимова, Д.Г. Емалеева и [др.]. Материаловедение и термическая обработка металлов. Междунар. сб. науч. тр.: под ред. А.Н. Емелюшина и Е.В. Петроченко. Магнитогорск: ГОУ ВПО «МГТУ», 2009. С. 143-146.
17. Чукин М.В., Емалеева Д.Г. Разработка непрерывного способа и инструмента интенсивной пластической деформации при производстве высокопрочной сталемедной проволоки. Тезисы Второго международного конкурса научных работ молодых ученых в области нанотехнологий. М.:, 2009. С. 395 – 396.