Курсовой проект по дисциплине: Конструирование акустических приборов и систем на тему: Разработка конструкции и технологии изготовления ультразвукового медицинского преобразователя с электронным сканированием 5 мгц)
Вид материала | Курсовой проект |
Содержание4 Расчет основных технических параметров 12 Выполняемые операции |
- Курсовой проект по курсу «Проектирование и конструирование приборов и систем неразрушающего, 108.93kb.
- Афанасьев Михаил Геннадьевич исследование, разработка конструкции и технологии изготовления, 128.79kb.
- Методические указания к курсовому проекту, 194.16kb.
- Курсовой проект по учебной дисциплине «Микропроцессорные средства» на тему «Система, 521.9kb.
- Проект производственно-технической базы атп на 200 автомобилей с разработкой участка, 496.28kb.
- Реферат по дисциплине " Технологические процессы микроэлектроники " на тему: Технологические, 1398.5kb.
- Задание на курсовой проект; реферат, 294.21kb.
- «Разработка технологии изготовления детали «Корпус» с применением станков с чпу и организации, 48.43kb.
- Методы визуализации акустических полей и их применение в диагностике, 313.37kb.
- Курсовой проект по дисциплине: «Микропроцессорные информационно-управляющие системы, 542.35kb.
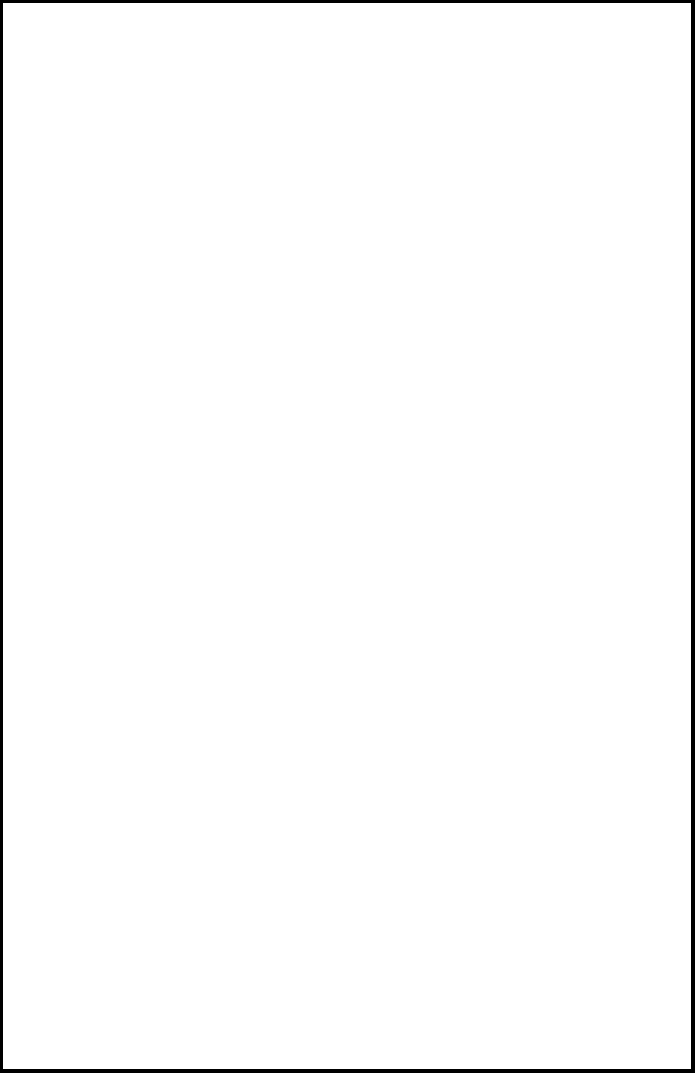
Национальный технический университет Украины
“Киевский политехнический институт”
Кафедра акустики и акустоэлектроники
КУРСОВОЙ ПРОЕКТ
по дисциплине: Конструирование акустических приборов и систем
на тему: Разработка конструкции и технологии изготовления ультразвукового медицинского преобразователя с электронным сканированием (2.5 МГц)
Выполнил:
Студент 5-го курса
группы
зачётная книжка
№
Проверил:
Дрозденко А.И.
Киев 2010
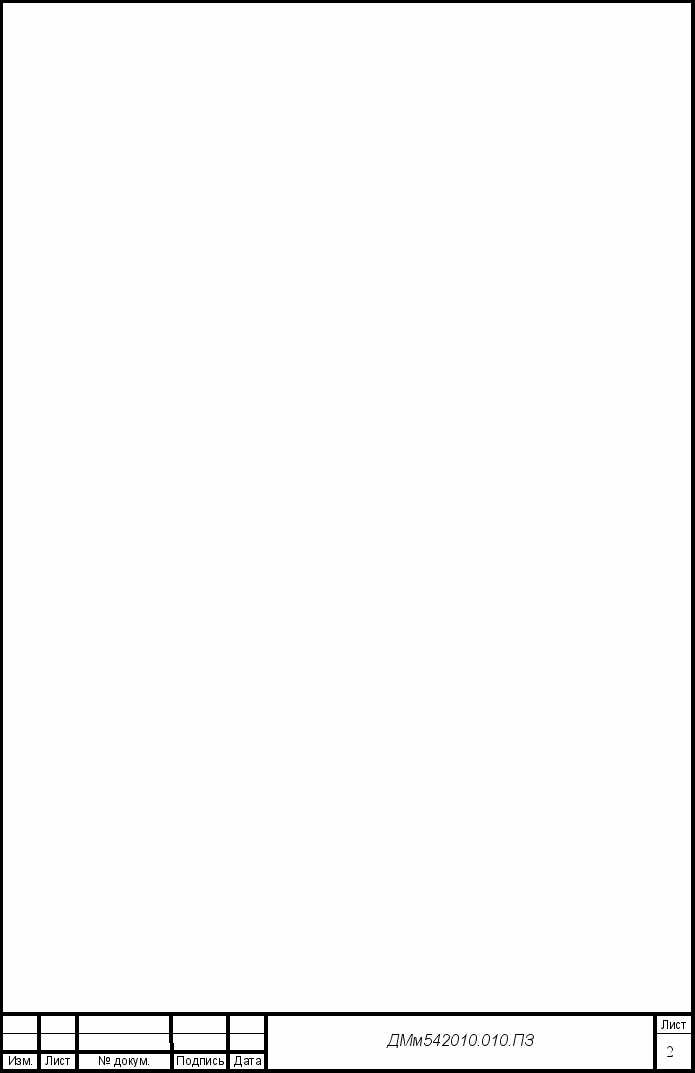
ВВЕДЕНИЕ 3
1 Анализ существующих прототипов конструкции 4
2 Разработка технического задания на конструирование прибора 7
3 Выбор и обоснование перечня конструкционных материалов 11
^ 4 Расчет основных технических параметров 12
5 Разработка технологии изготовления прибора 18
ВЫВОДЫ 23
ЛИТЕРАТУРА 24
ПРИЛОЖЕНИЕ 1
ПРИЛОЖЕНИЕ 2
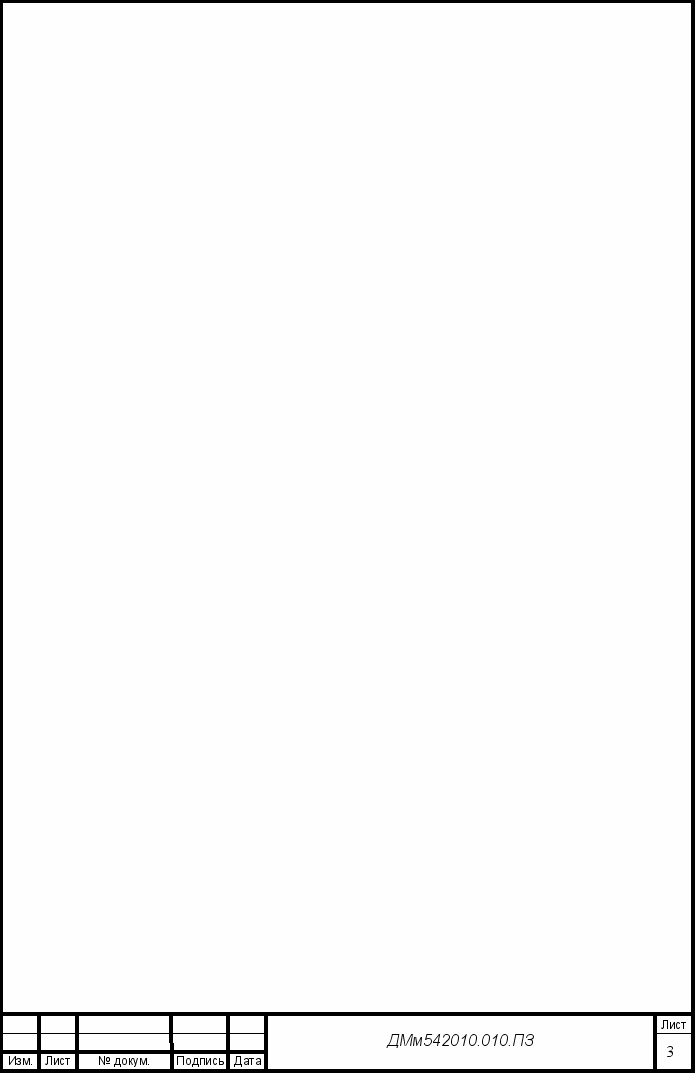
Ультразвуковые сканирующие устройства в общем случае включают совокупность электроакустических, электромеханических и электронных элементов, выполняющих одновременно функции электроакустических преобразователей и акустических антенн, концентрирующих излучаемую акустическую энергию в узком луче вдоль заданного направления и осуществляющих пространственную селекцию эхо-сигналов по этому же направлению. Кроме того, с помощью сканирующих устройств осуществляется акустический контакт между электроакустическим преобразователем и исследуемым объектом в процессе ввода и вывода ультразвуковой энергии, а также усиление эхо-сигналов и согласование их с устройствами обработки и отображения информации. К ультразвуковым сканирующим устройствам обычно предъявляются высокие требования в плане обеспечения пространственной направленности и скорости сканирования при минимальных энергетических затратах, массогабаритных параметрах и сложности управления. Важными показателями также являются размеры области ультразвукового обзора, частота сканирования, возможность динамического управления параметрами ультразвукового луча.[2]
В зависимости от способа реализации изменения направления ультразвукового луча, сканирующие устройства делятся на две основные группы: с механическим и с электрическим управлением. Сканирующие устройства независимо от способа управления еще подразделяют по виду сканирования, функциональному назначению, способу создания акустического контакта с исследуемым объектом или по конструктивным признакам, например портативные или стационарные, и т. д.[2]
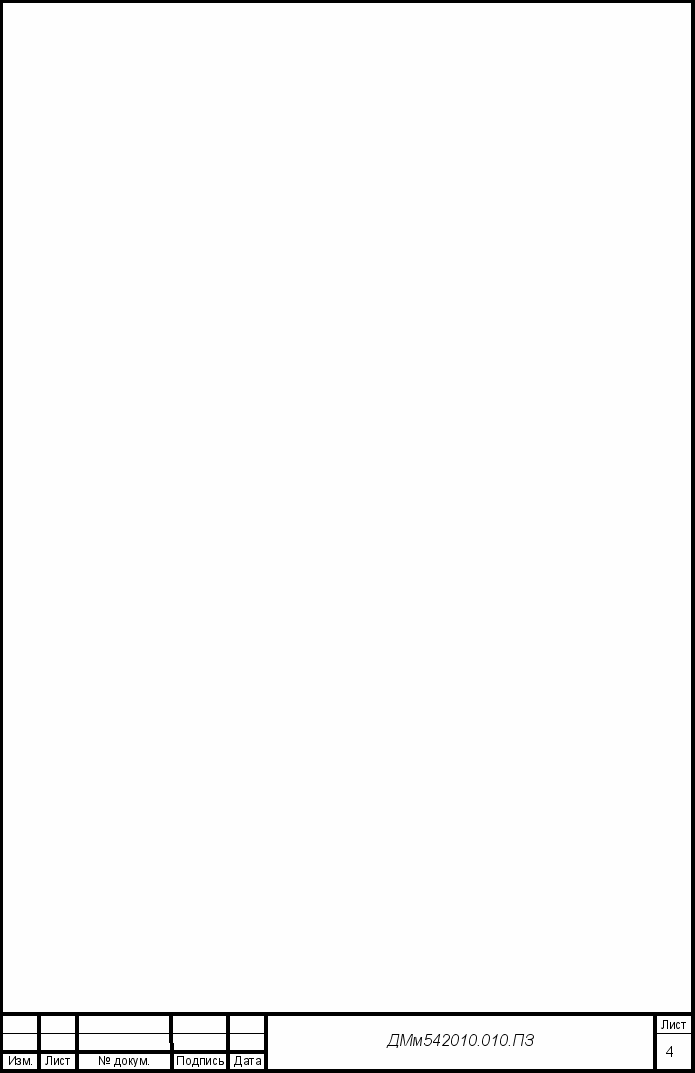
1 Анализ существующих прототипов конструкции
Был проведён патентный поиск существующих аналогов разрабатываемого устройства (см. Приложение 2).
К распространенному типу электрических сканирующих ультразвуковых преобразователей относятся устройства с шаговым сканированием ультразвукового луча коммутируемых матриц пьезопреобразователей (рис. 2.1). Перемещение ультразвукового луча в таких устройствах достигается путем последовательного электрического переключения пьезоэлементов матрицы с шагом, равным ширине одного элемента. Коммутируемые матрицы позволяют реализовать, в принципе, различные виды ультразвукового сканирования в зависимости от формы сканирующих апертур (рис. 2.2). Однако на практике до настоящего времени в основном применялись линейные и веерные сканирующие матрицы. Конструктивно линейные и веерные (конвексные) коммутируемые матрицы отличаются от фазированных только пространственной протяженностью самой матрицы, геометрической формой апертуры и числом коммутируемых при сканировании ультразвукового луча пьезоэлементов.[2]
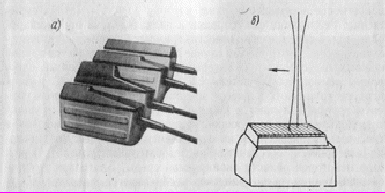
Рис. 2.1. Линейный сканирующий ультразвуковой преобразователь с коммутируемой матрицей пьезоэлементов: а — внешний вид; б — принцип сканирования
В данном случае для обеспечения достаточной протяженности перемещения ультразвукового луча требуются, например, матрицы длиной до 100 и более миллиметров с числом пьезоэлементов, достигающим нескольких сотен. Шаг сканирования ультразвукового луча в этом случае зависит от размеров элементов и составляет несколько длин ультразвуковых волн. Для обеспечения необходимой разрешающей способности в управляющие цепи коммутируемых матриц могут дополнительно включаться фазирующие элементы, обеспечивающие фокусировку и небольшую угловую подкачку луча при сканировании. Последним приемом может быть обеспечено снижение
дискретности перемещения луча, которая для этих матриц существенна. [2]
Реализация фокусировки и подкачки луча при сканировании приводит к
необходимости групповой коммутации пьезоэлементов (рис. 2.2). В этом случае из матрицы выделяется группа смежных пьезоэлементов, которые работают как обычный одномерный пьезопреобразователь со сплошной апертурой, равной апертуре группы. В процессе зондирования среды все пьезоэле-менты группы излучают и принимают соответствующие сигналы. Затем подключается следующая группа пьезоэлементов, смещенная относительно предыдущей на один элемент, и процесс зондирования повторяется, обеспечивая последовательный ультразвуковой обзор некоторой области сканируемой среды. Благодаря групповой коммутации пьезоэлементов увеличивается апертура излучения — приема акустической антенны, чем обеспечивается лучшая направленность луча по всей глубине зондирования, а также повышается эффективность электроакустического преобразования.[2]
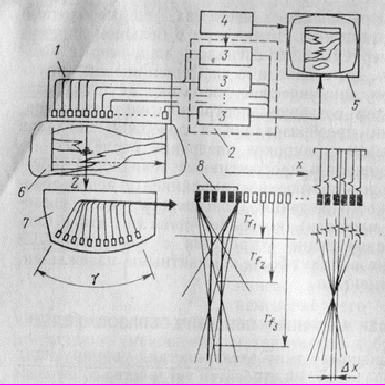
Рис. 2.2. Обобщенная структура сканирующего устройства на основе коммутируемой матрицы:
/ — линейная матрица пьезоэлементов; 2 — коммутирующие цепи; 3 — передающие и приемные каналы; 4 — управляющие цепи; 5 — дисплей; 6 — объект исследования; 7 — веерная матрица пьезоэлементов; 8 — одновременно коммутируемая группа пьезоэлементов; х, у — линейная и угловая переменные соответственно; rf1, rf2, rf3, — фокусные расстояния; х — линейное отклонение при «подкачке» луча
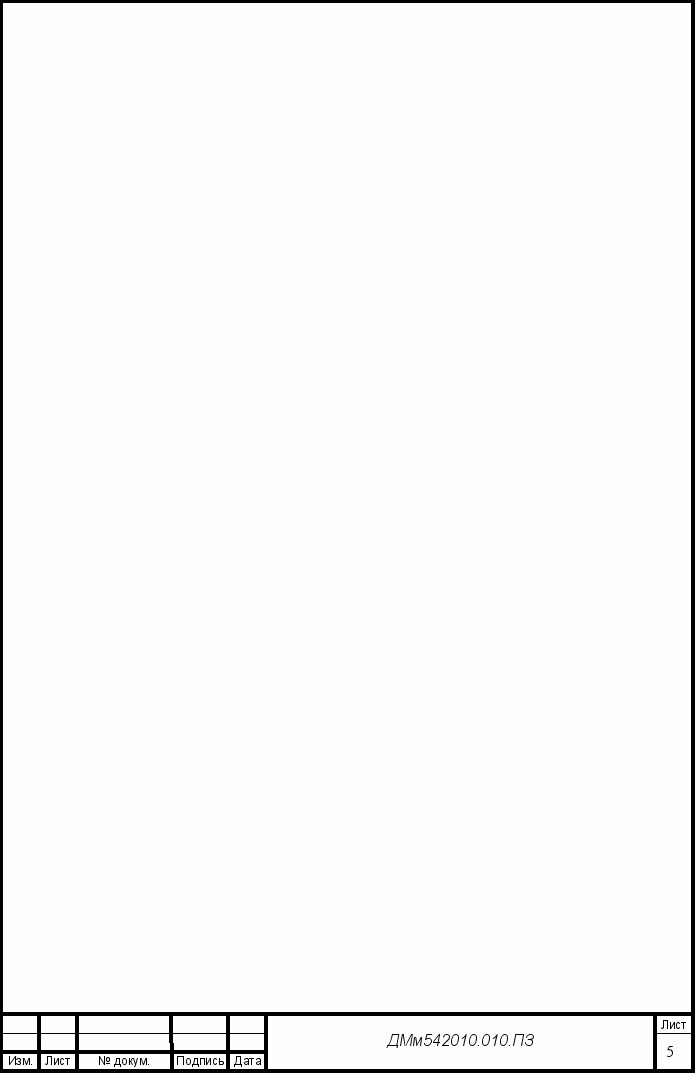
При конструировании устройств с линейной иди выпуклой криволинейной коммутируемой матрицей число пьезоэлементов, объединяемых в группу, определяется из требований, разрешающей способности, чувствительности электроакустического преобразования и дискретности перемещения ультразвукового луча. Поскольку, эти требования противоречивы, выбор осуществляется компромиссным путем из известного соотношения,
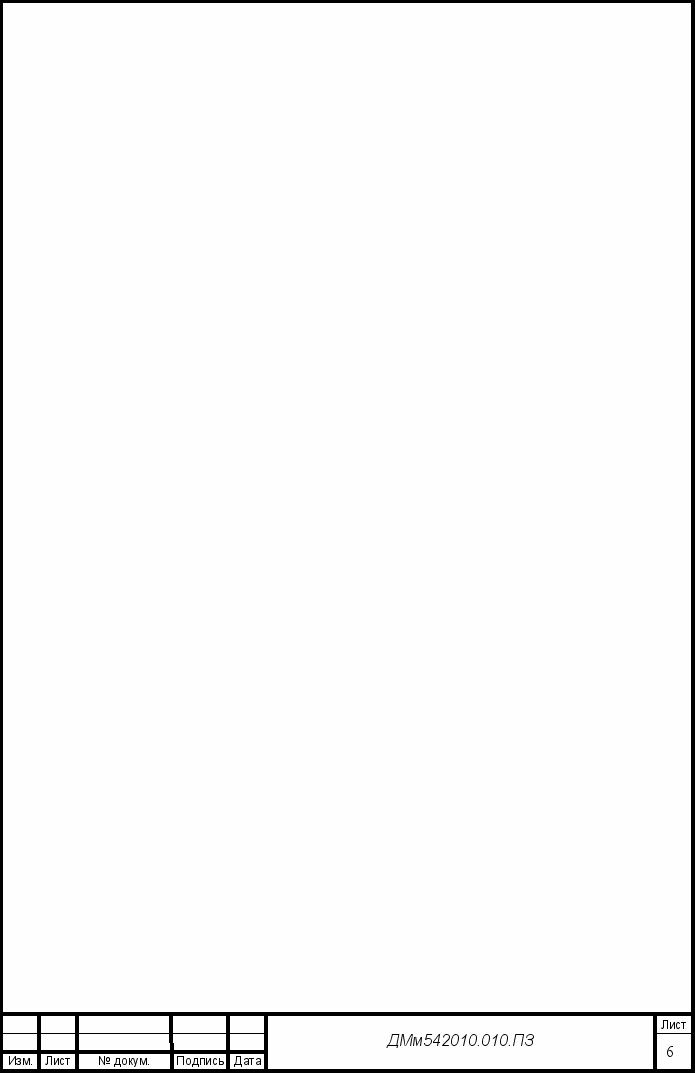
Линейные и веерные сканирующие коммутационные ультразвуковые устройства находят широкое применение при построении современных динамических систем ультразвуковой визуализации благодаря небольшой массе, стоимости и относительной простоте электронных схем управления. В настоящее время сканирующие устройства такого типа используются наиболее массово, на их основе строятся ультразвуковые преобразователи, предназначенные для внутриполостиых исследований, применения во время операций и пункций органон (рис. 2.3).[2]
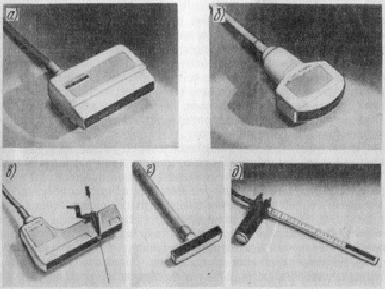
Рис. 3.33. Разные типы коммутируемых ультразвуковых преобразователей фирмы «Алока» (Япония) для биомедицинской эхоскопии: а — линейный; б — веерный; я — пунктурный;
г — операционный; д — внутриполостной
Основной проблемой, возникающей при изготовлении сканирующих матриц с коммутацией пьезоэлементов, является обеспечение максимальной повторяемости и однородности характеристик ультразвукового сканирования. Проблема эта обусловлена значительной протяженностью апертур матриц этого типа, большим числом пьезоэлементов и тем, что в процессе ультразвукового сканирования используются разные пьезоэлементы. При изготовлении матриц для работы в мегагерцевом диапазоне ультразвуковых частот проблема еще усложняется снижением габаритных размеров пьезоэлементов и значительным повышением требований к геометрическим допускам при их изготовлении. Для примера приведем конструктивные параметры линейной сканирующей матрицы с рабочей частотой пьезоэлементов 3,5 МГц:[2]
Число коммутируемых элементов матрицы N | ≥80 |
Общее число пьезоэлементов n | 320 |
Шаг матрицыb’ = b + d'. мм | 0.4±0.05 |
Ширина пьезоэлемента b, мм | 0.3 |
Зазор между пьезоэлементами d', мм | 0.09±0.05 |
Число пьезоэлементов, объединяемых в один коммутируемый элемент n' | 3; 4 |
Общая длина матрицы L, мм | 90 |
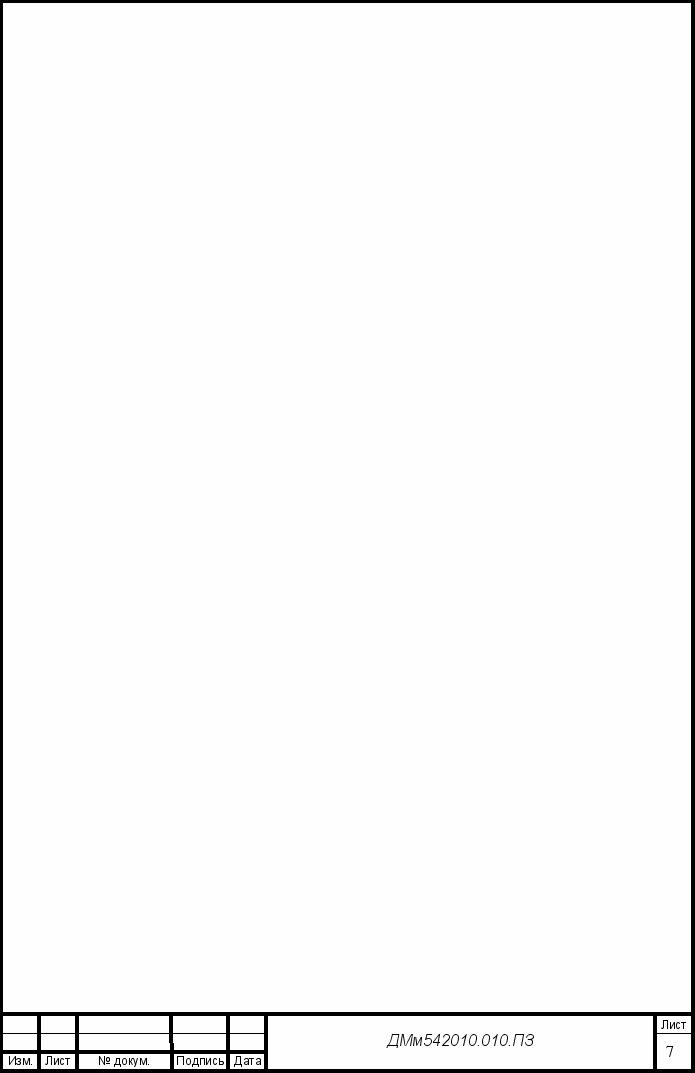
С другой стороны, на конструктивные особенности практических решений и достигаемые электроакустические характеристики матриц существенное влияние оказывает выбор материалов и способы изготовления таких ее элементов, как демпфер, согласующие и акустические фокусирующие слои, система многоканальных электрических соединений и др. [2]
2 Разработка технического задания на конструирование прибора
- Наименование и область применения
Ультразвуковой медицинский преобразователь с электронным сканированием (2.5 МГц) для применения в медицине, а именно – ультразвуковой диагностике.
- Основание для разработки
Задание на курсовой проект на тему: «Разработка конструкции и технологии изготовления ультразвукового медицинского преобразователя с электронным сканированием (2.5 МГц) ».
- Цель и назначение разработки
Разработка данного проекта производится с целью усовершенствования существующих его аналогов. Проектируемый узел предназначен для преобразования ультразвуковых акустических волн на частоте 2.5 МГц в электрические сигналы.
- Технические требования
4.1. Состав продукции и требования к конструкции
1) Пояснительная записка;
2) Набор черетежей.
4.1.2. Требования к конструкции.
1) масса датчика не более 0,5 кг;
2) длина кабела 1,5-2 м;
3) защитное декоративное покрытие.
Изделие выполнить в соответствии с требованиями ГОСТ 9.301-78 и ГОСТ 9.303-84.
4.1.3. Требования к средствам защиты от воздействия окружающей среды.
По защищенности от воздействия окружающей среды должен соответствовать ГОСТ 15150.
По устойчивости к действию температуры должен сохранять работоспособность при изменении температур в диапазоне +1°С - +40 °С.
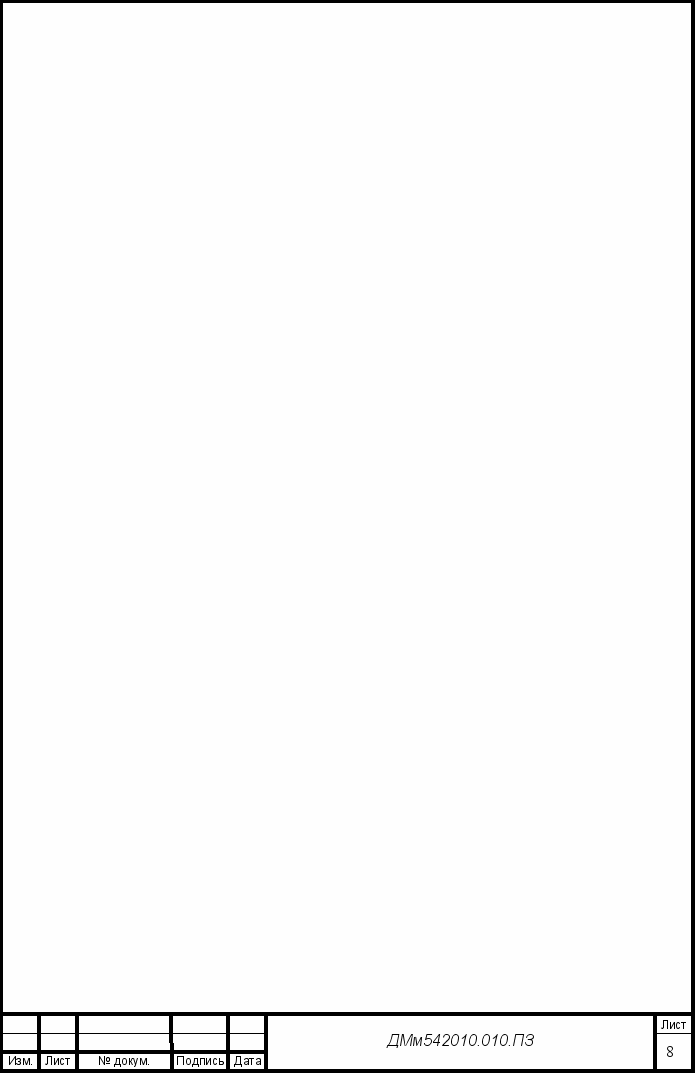
- Рабочая частота - 2.5 МГц;
- Режим работы - непрерывный;
- Потребляемая мощность от сети - не более 55 ВА;
- Интенсивность ультразвука – не более 0,55 Вт/см²
4.3.Требования к надежности
- Устойчивость к механическим воздействиям по ГОСТ 20.790-82
- Устойчивость к климатическим факторам по ГОСТ 20.790-82 по виду климатического исполнения категории 4.2.
- По условиям транспортирования датчики должны быть устойчивыми к различным воздействиям по ГОСТ 15.150; группа 5 – транспортировка допускается всеми видами транспорта при температуре
-50…+40, влажности до 85% при условии защиты от прямого попадания осадков и пыли
- По условиям хранения – должен быть указан тип упаковки, ящика, поглотителя (ГОСТ 15.150)
- Поверхность датчика должна быть устойчива к дезинфекции перекисью водорода (3%) с добавлением моющего средства (0.5%)
- По надежности: средняя наработка на отказ – не менее 5000 часов, средний срок службы не менее 5 лет, средний срок сохраняемости – не менее 1 года.
- Уровень радиопомех не должен превышать значений, указанных в нормативных документах («Нормаль-82»)
4.4. Требования к технологичности
Изделие проектируется в соответствии с требованиями ГОСТ 26.831-86.
4.5. Требования к стандартизации и унификации
При проектировании изделия используются стандартные, унифицированные и заимствованные из ранее разработанных изделий детали и сборочные единицы.
- Требования к безопасности
Требования по электробезопасности (ГОСТ 12.2.23-78) класс 1, степень защиты 3.
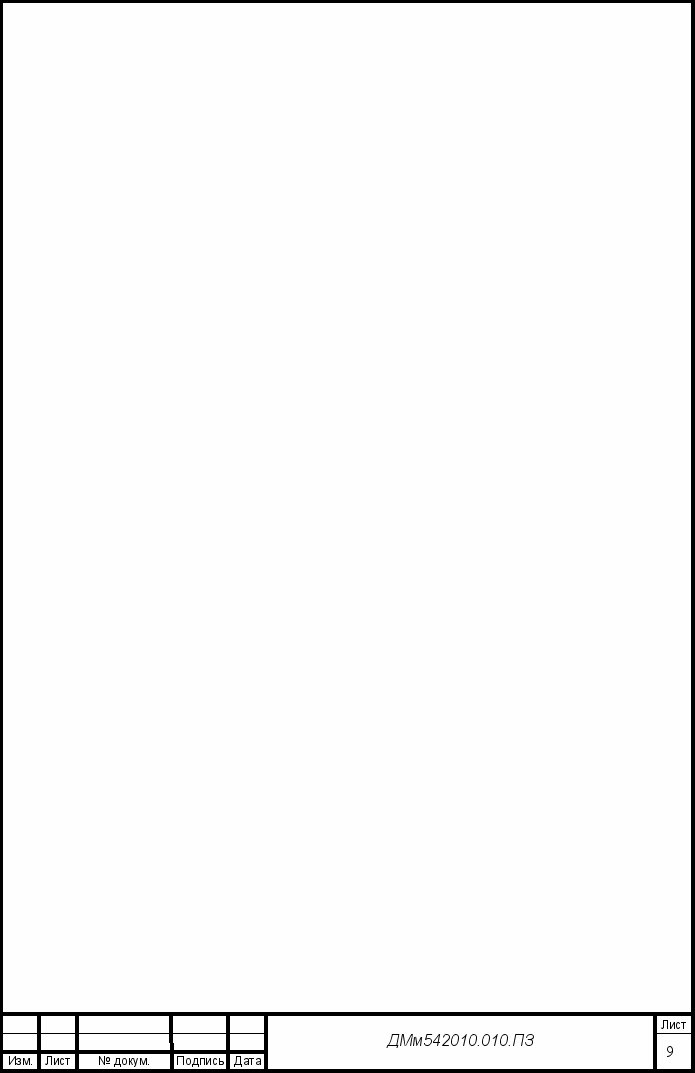
Обеспечить удобство обслуживания и эксплуатации инструмента в соответствии с требованиями к технической эстетике современных медицинских приборов.
4.8. Требования к патентной чистоте.
Перечень стран, в отношении которых должна быть обеспечена патентная чистота проектируемого инструмента, прилагается. Патентный поиск проведён за 1992-2009 г.г.
4.9. Требования к составным частям, исходным и эксплуатационным материалам.
Ограничения на применяемые покупные материалы и покрытия не налагаются.
4.10. Условия эксплуатации.
Питание ультразвукового медицинского преобразователь с электронным сканированием осуществляется от сети переменного тока частотой 50±0,5 Гц, с номинальным напряжением 220В ±10%.
Ультразвуковой медицинскиё преобразователь при эксплуатации сохраняет работоспособность при изменении температур в диапазоне +1°С - +40 °С.
Преобразователь при эксплуатации обладает устойчивостью к механическим воздействиям по ГОСТ 50444 для изделий группы 1.
4.11. Требования к маркировке и упаковке.
Маркировка инструмента должна соответствовать ГОСТ 50444.
Маркировка потребительской тары должна соответствовать ГОСТ 50.444.
Каждый ультразвуковой медицинскиё преобразователь должен быть снабжен фирменной табличкой, на которой указаны:
а) товарный знак предприятия-изготовителя;
б) наименование и обозначение ультразвукового медицинского преобразователя;
в) заводской номер;
г) год изготовления;
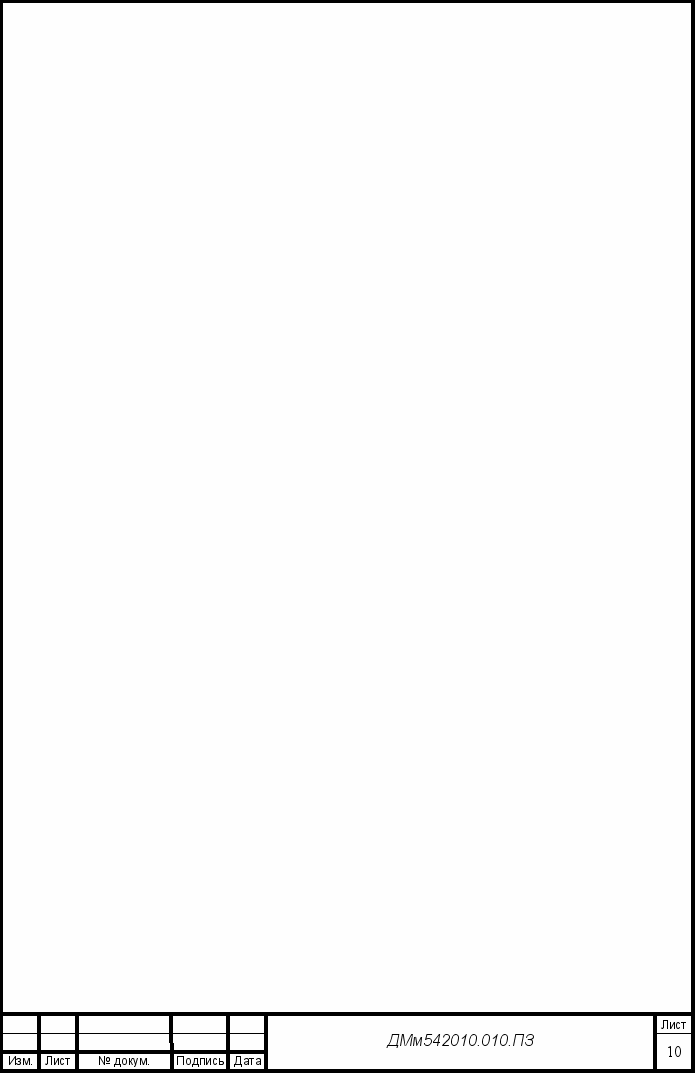
е) маркировка питания от сети в соответствии с ГОСТ 50267.0.
4.12. Требования к транспортировке и хранению.
Условия хранения ультразвукового медицинского преобразователя на складе изготовителя (потребителя) должны соответствовать требованиям условий хранения по ГОСТ 15.150. УЗ инструменты должны храниться на стеллажах на расстоянии не менее 1 метра от отопительных приборов. При хранении не допускается складирование инструментов друг на друга. В помещениях склада не допускается наличие агрессивных паров и газов.
УЗ инструмент в транспортной упаковке должен быть устойчив к механическим воздействиям при транспортировке по ГОСТ 50.444 для изделий группы 1-5.
Транспортная маркировка инструмента по ГОСТ 14192 с нанесением манипуляционных знаков: «ВВЕРХ», «ХРУПКОЕ, ОСТОРОЖНО», «БЕРЕЧЬ ОТ ВЛАГИ».
3. Выбор и обоснование перечня конструкционных материалов
При конструировании акустических приборов используется широкая номенклатура материалов.
Это, в первую очередь, активные материалы для преобразователей, резины и пластмассы для звукоотражающих экранов, электроизоляционные материалы, провода и кабели, герметизирующие резины, клеи, герметики, компаунды, металлы, лаки, краски, припои, флюсы и влагопоглотители.
Используемые материалы должны обладать не большим весом для обеспечения портативности прибора, соответствовать требованиям ГОСТ 20.790-82.
В настоящее время титанобариевые пьезоэлектрические преобразователи вытесняются преобразователями из пьезокерамических материалов на основе цирконата-титаната свинца или на основе ниобатов. По сравнению с пьезокерамиками титаната бария эти материалы обладают повышенной температурной стабильностью и лучшими пьезоэлектрическими свойствами.[2]
Изготавливаемые в станах СНГ пьезокерамики цирконата— титаната свинца сокращенно обозначаются ЦТС, в США - PZT. Отдельные марки, отличающиеся химическим составом, снабжаются соответствующими цифрами и буквами, например ЦТС-19, ЦТС-21, ЦТСНВ-1 и т. д. Пьезокерамики ЦТС являются твердыми растворами цирконата свинца PbZrO3, и титаната свинца PbTiO3 с примесями некоторых трех- и пятивалентных элементов и частичным
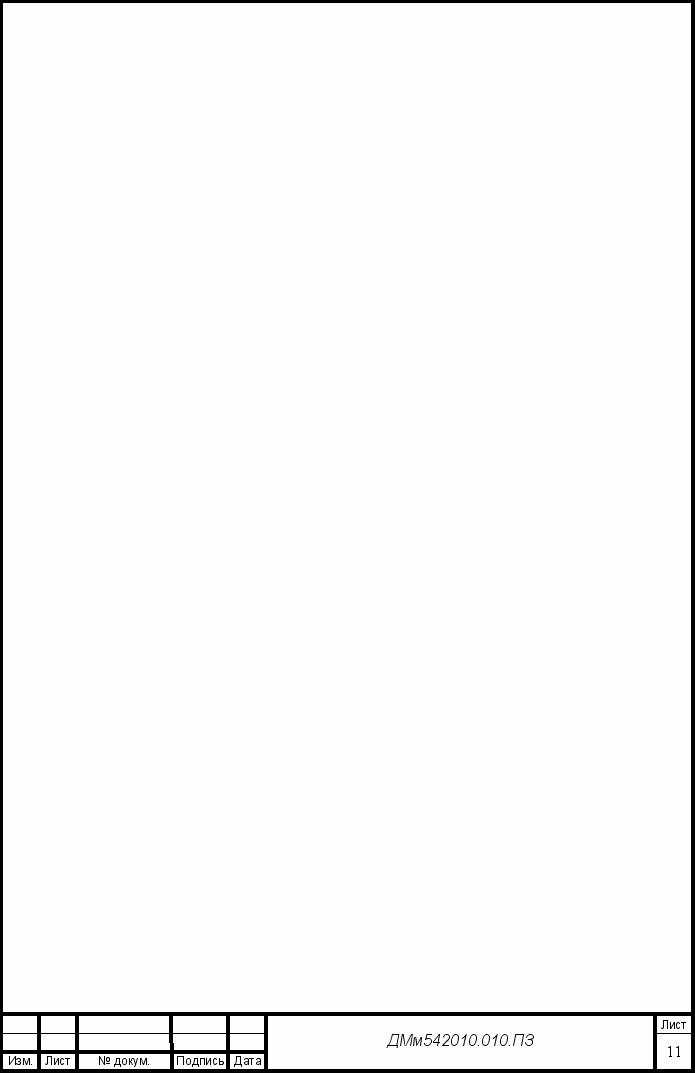
В качестве материала для пьезопластин была выбрана пьезокерамика ЦТСНВ-1:
Разработана на основе цирконат-титаната бария свинца с добавлением натрия и висмута. Обладает малой сегнетожесткостью. Применяются в электроакустических преобразователях, работающих в режимах приема и излучения малой и средней мощности при небольших механических напряжениях в интервале температур от -60º до +150ºС.[2]
Физико-механические свойства:
- плотность ρ=7300 кг/м3;
- модуль Юнга Е31=0,62·1011 Н/м2, Е33=0,49·1011 Н/м2
- коэффициент Пуассона 0,35;
- добротность механическая в воздухе 70;
- скорость ультразвука c=4380 м/с ;
- пьезомодуль d31=-166·10-12К/Н, d33=371·10-12К/Н;
- электрическая прочность Епр=2,9 кВ/мм;
- удельное объемное сопротивление 108 Ом·м;
- максимальное напряжение
.
Согласно ГОСТ 13927-74 «Материалы пьезокерамические» ЦТСНВ-1 относится к материалам I класса, и пригодна для производства пьезоэлементов приемников и излучателей малой и средней мощности.
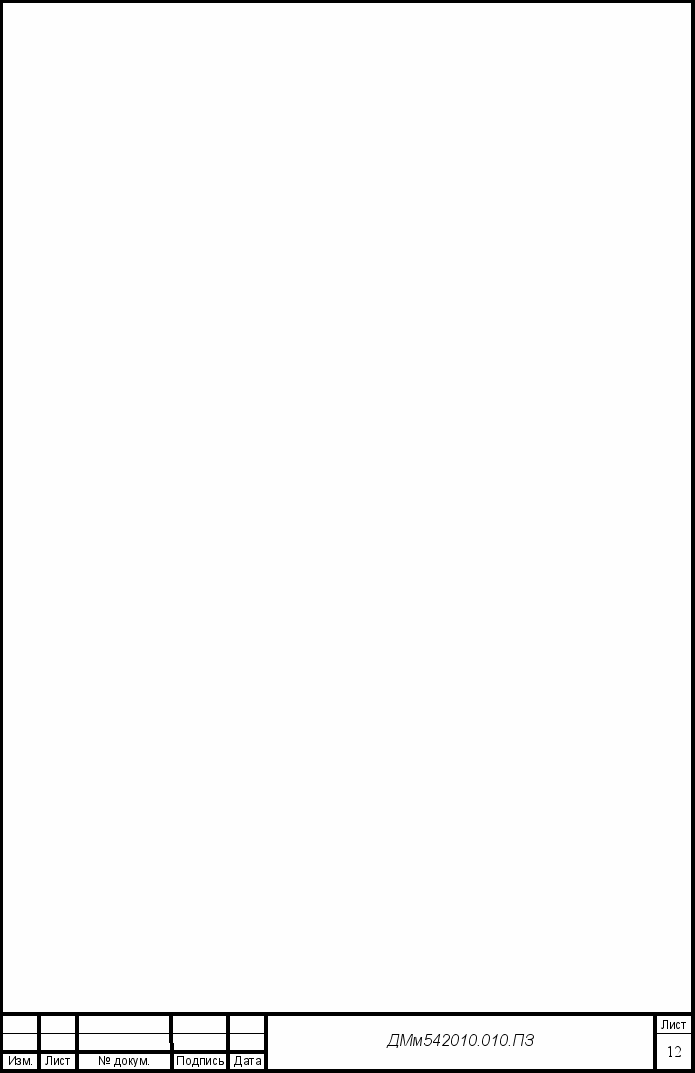
4. Расчет основных технических параметров
Линейная решетка пьезоелементов для медицинского сканера с резонансной частотой
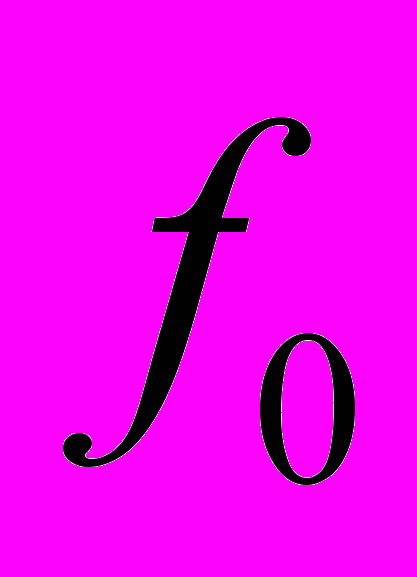
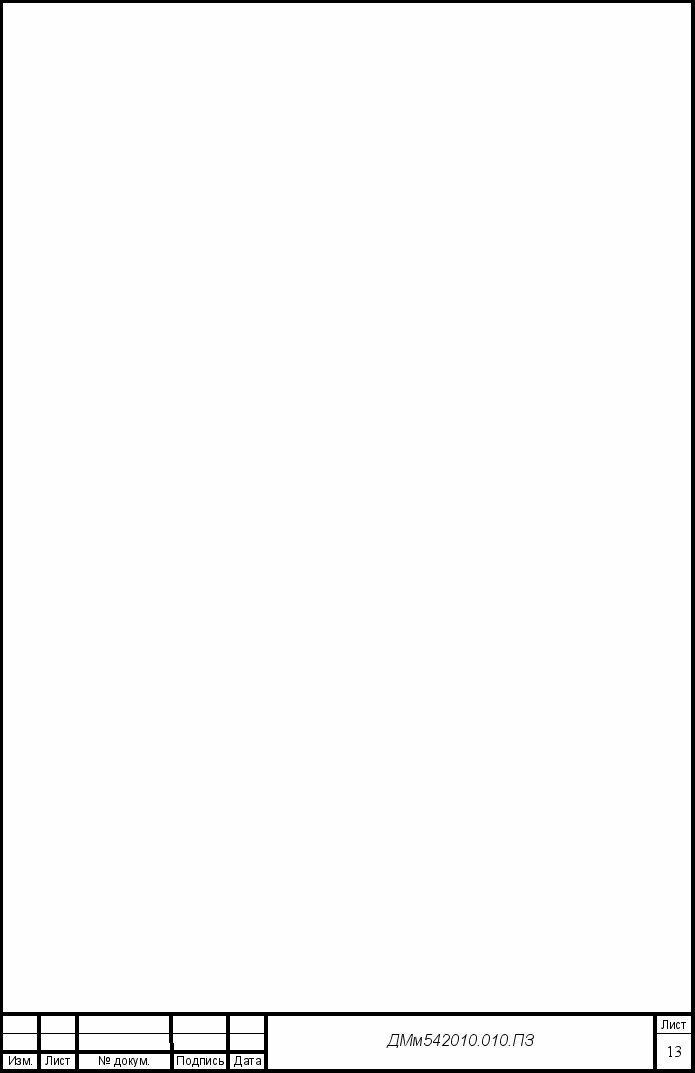
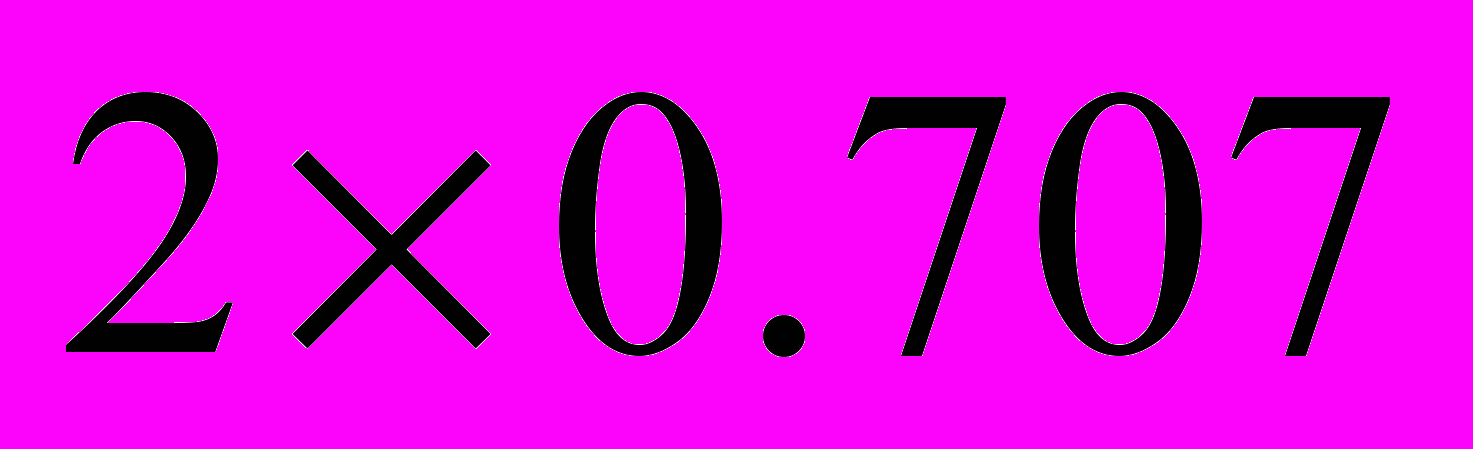
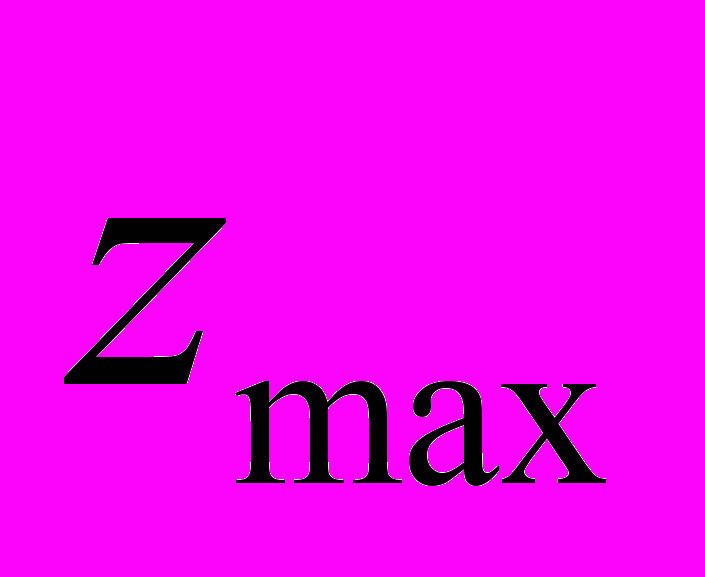
Дано:
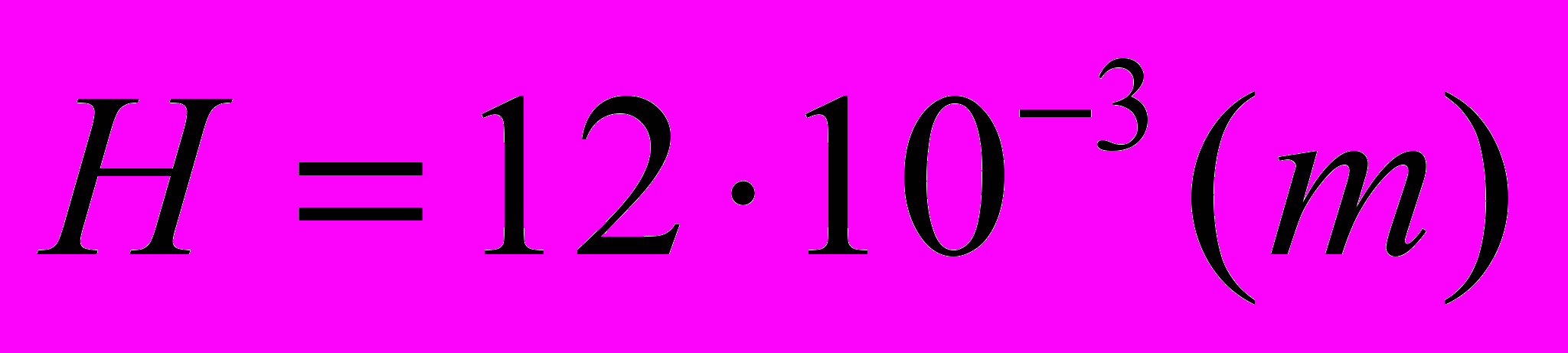
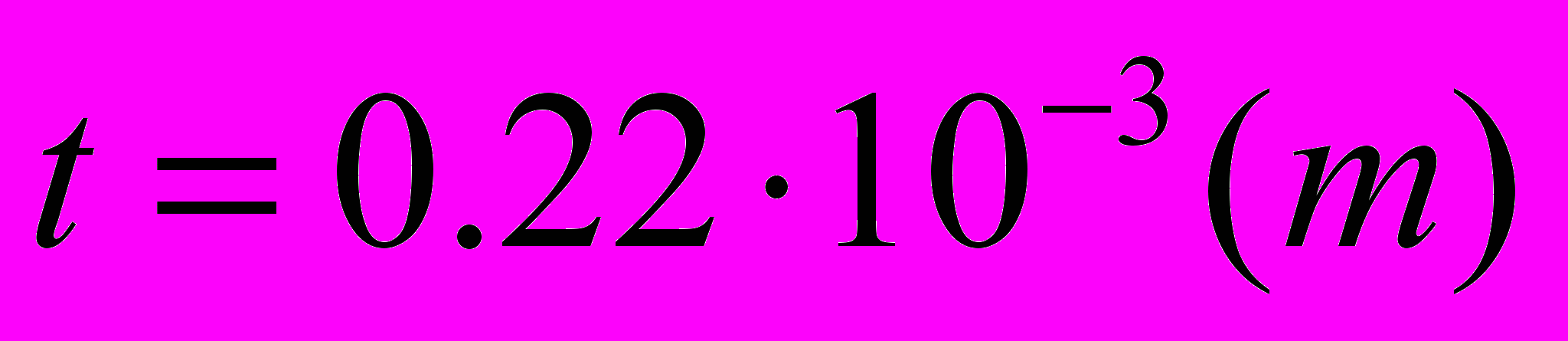
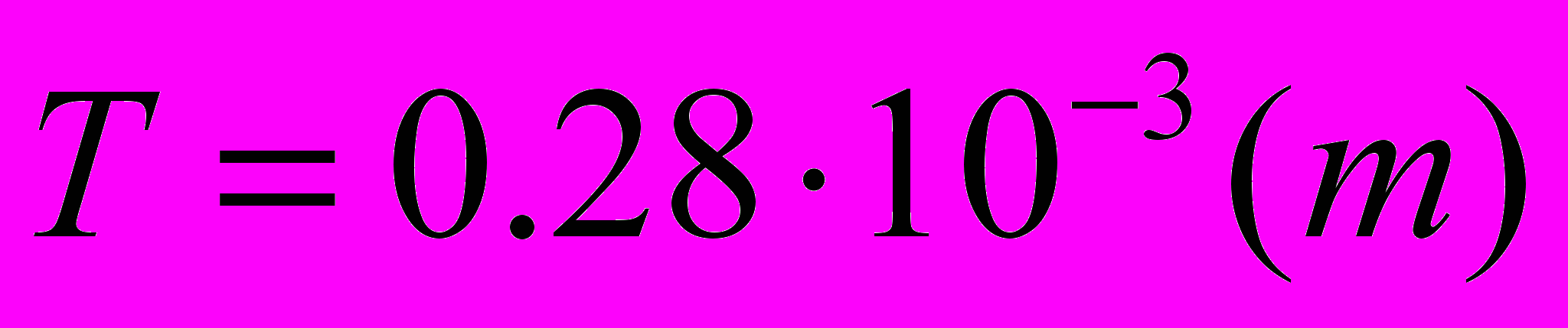
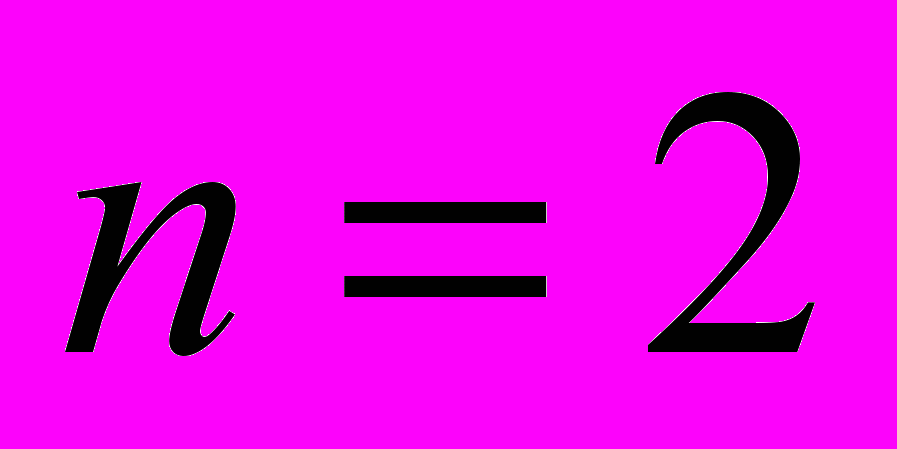
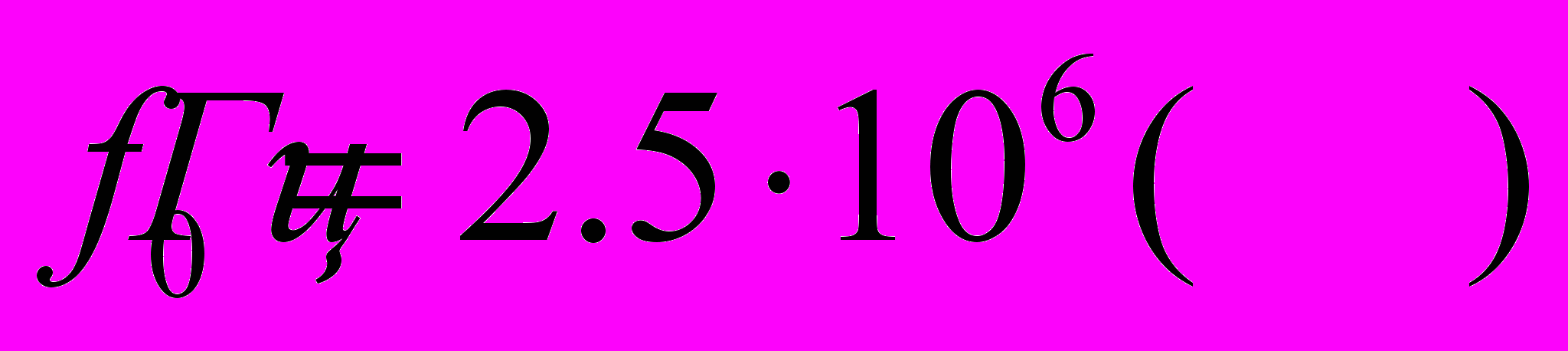
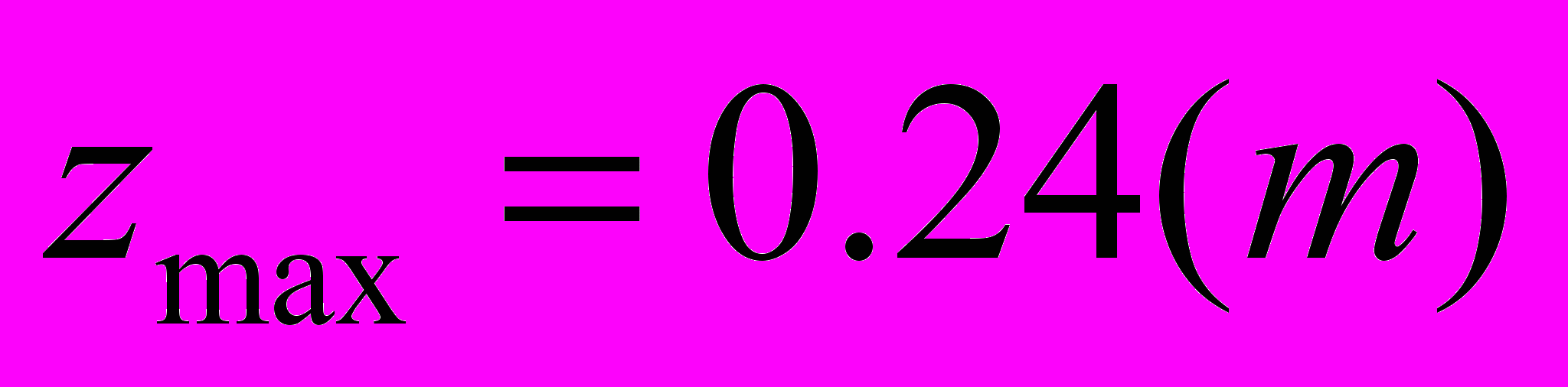
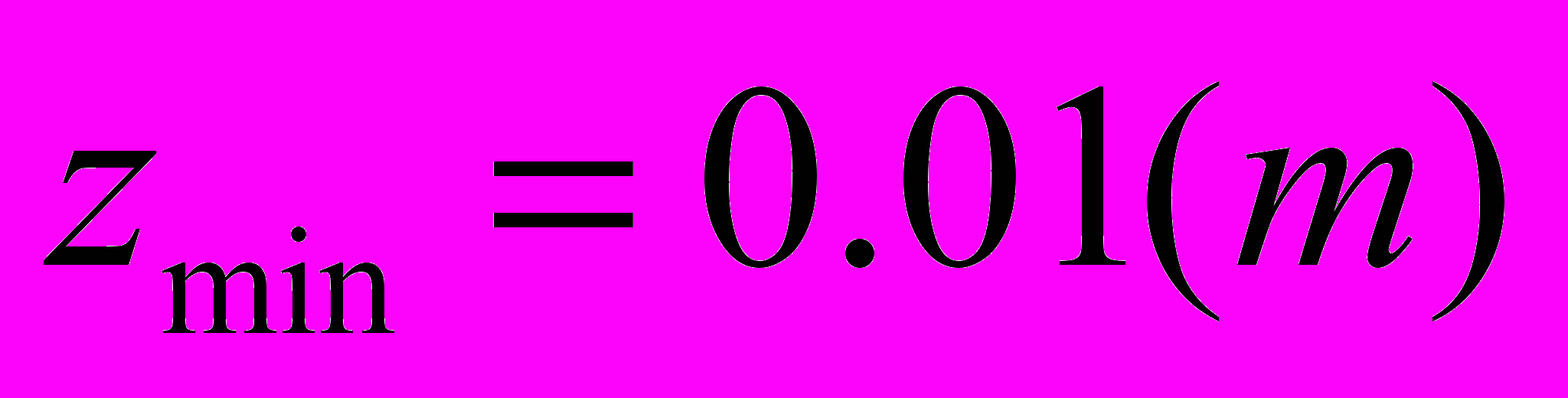
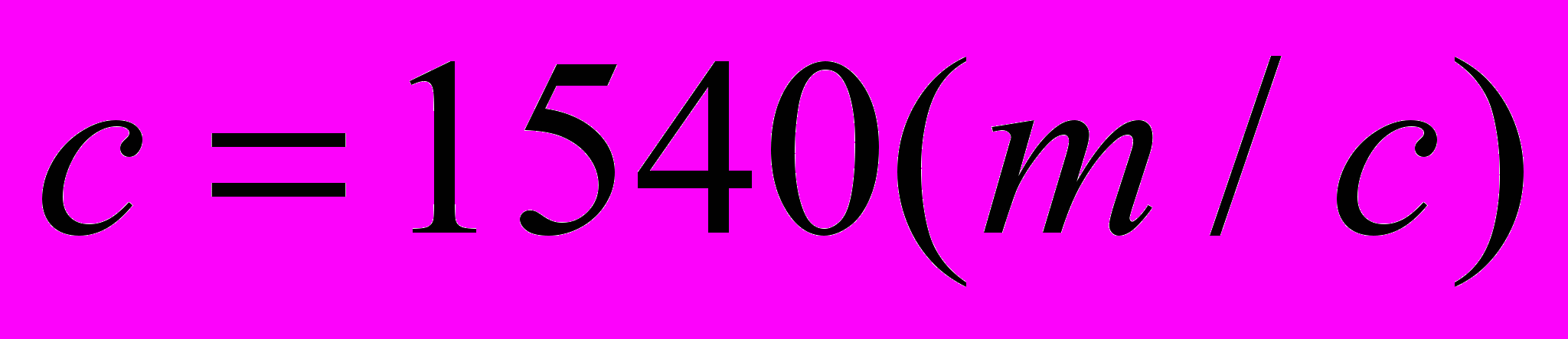
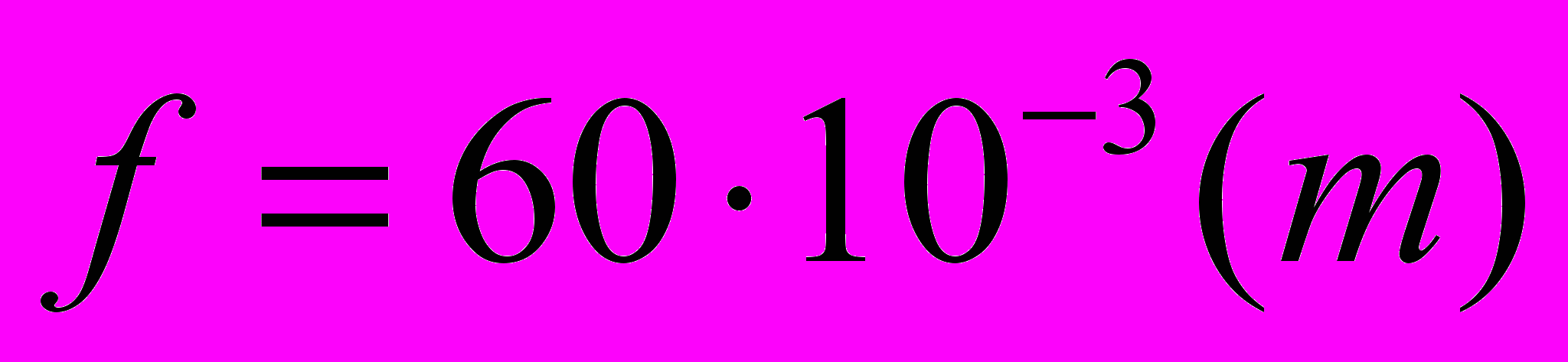
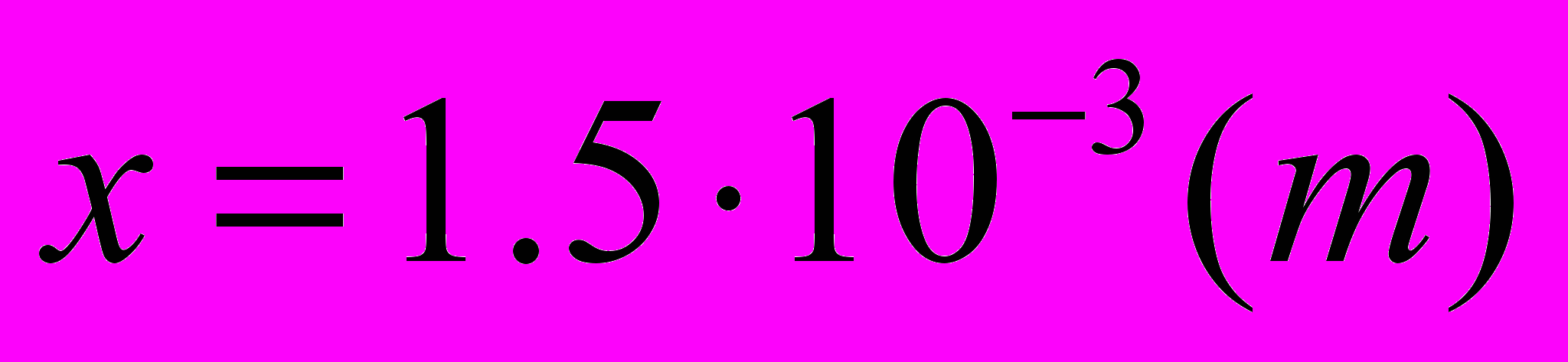

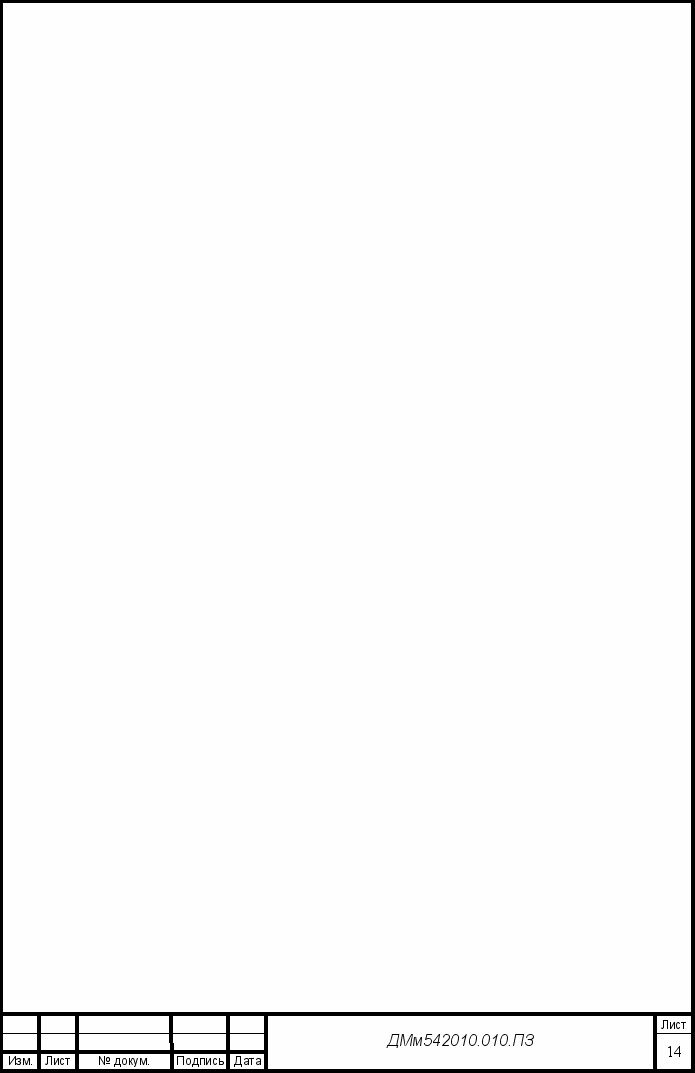
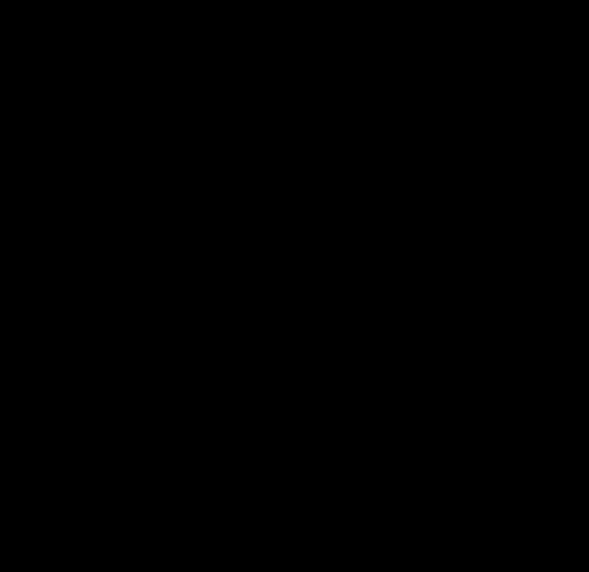
n-количество синфазно возбуждаемых элементов в одном канале;
N-количество каналов, участвующих в формировании пучка;
t-ширина излучающей поверхности одного элемента;
T-расстояние между фазовыми центрами соседних элементов;
g – зазор между элементами;
L-расстояние между фазовыми центрами крайних элементов антенной решетки;
H-длина одного элемента;
D-апертура антенной решетки.
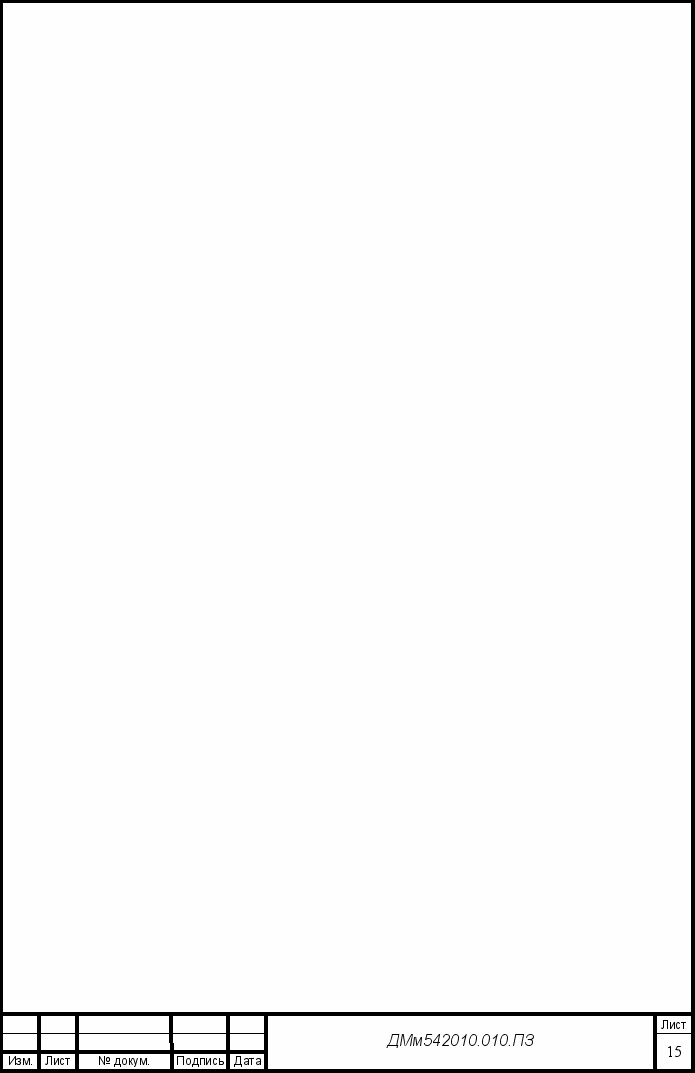
Моделью бесконечного цилиндрического фронта можно пользоваться при расчете реальных фокусирующих систем, если выполняется условие:
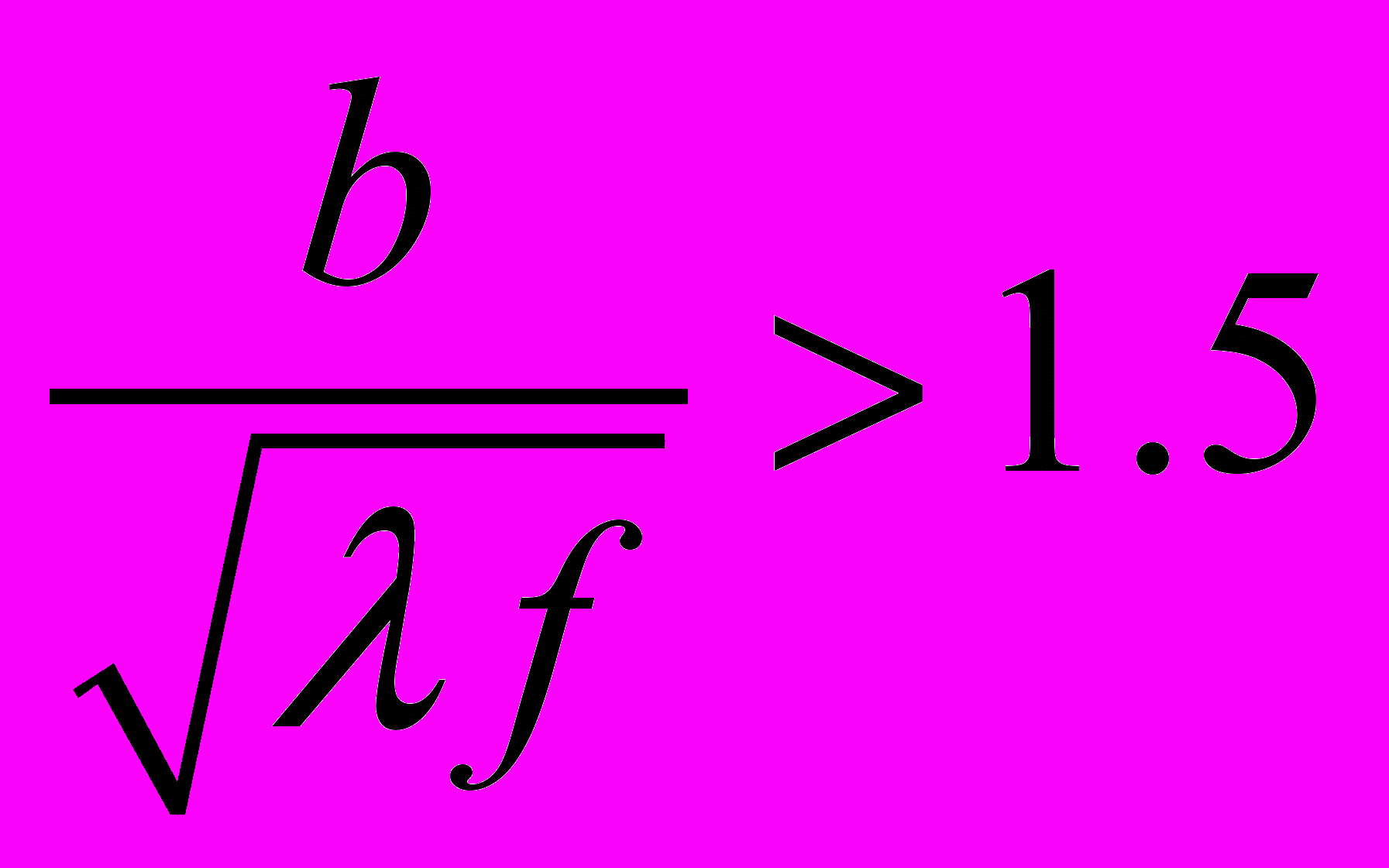
Где f- фокусное расстояние, которое определяется как
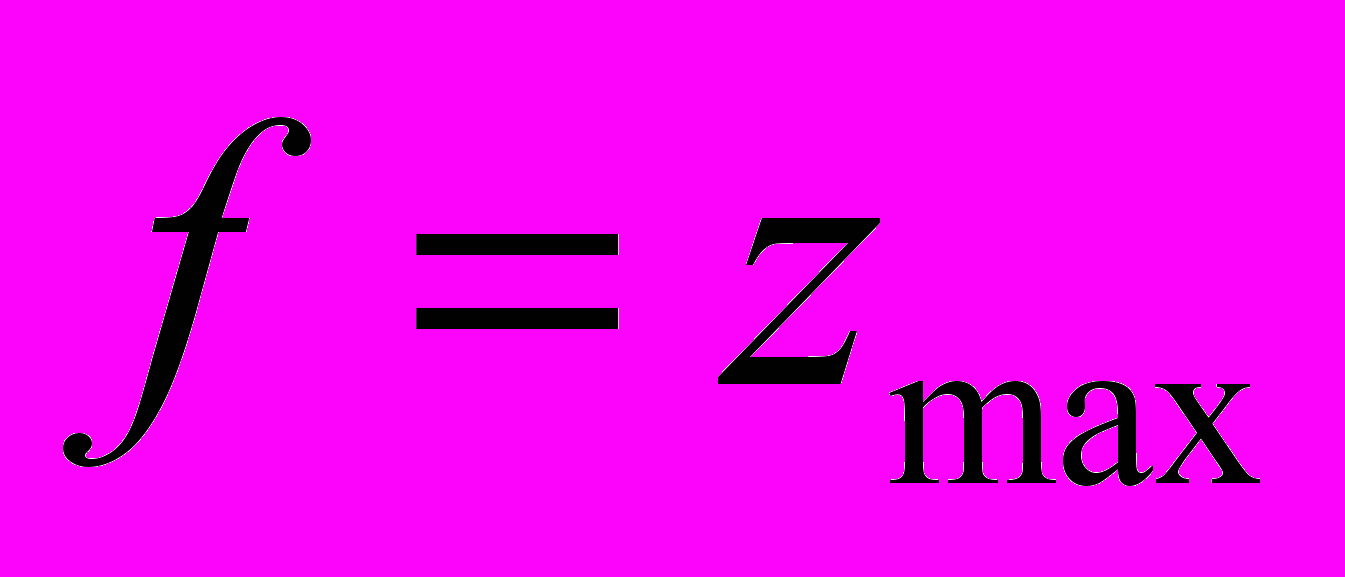
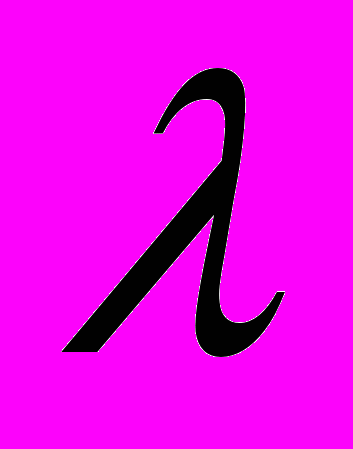
0,4935<1.5 – условие не выполняется
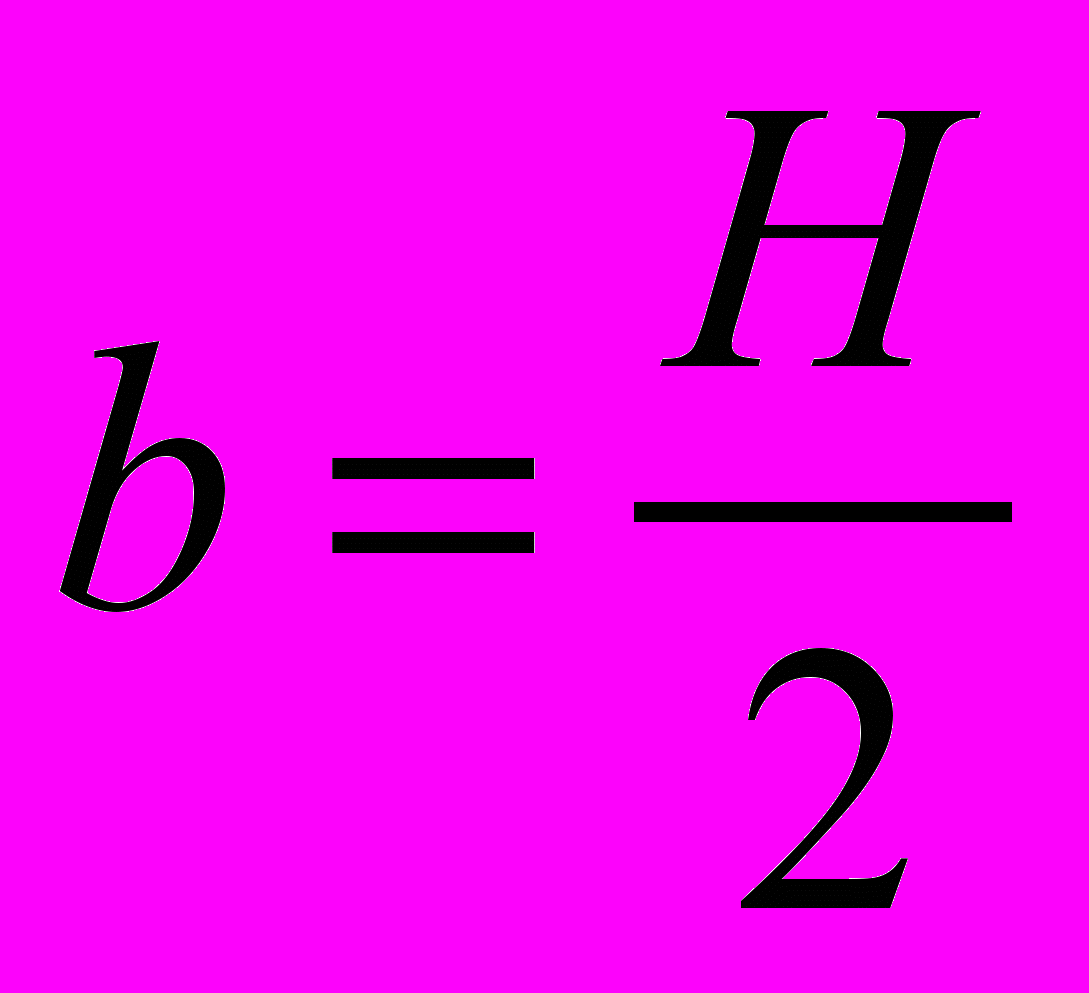
b=0.006 (м)
Рассчитаем отношение (f/D), где D-апертура из условия:
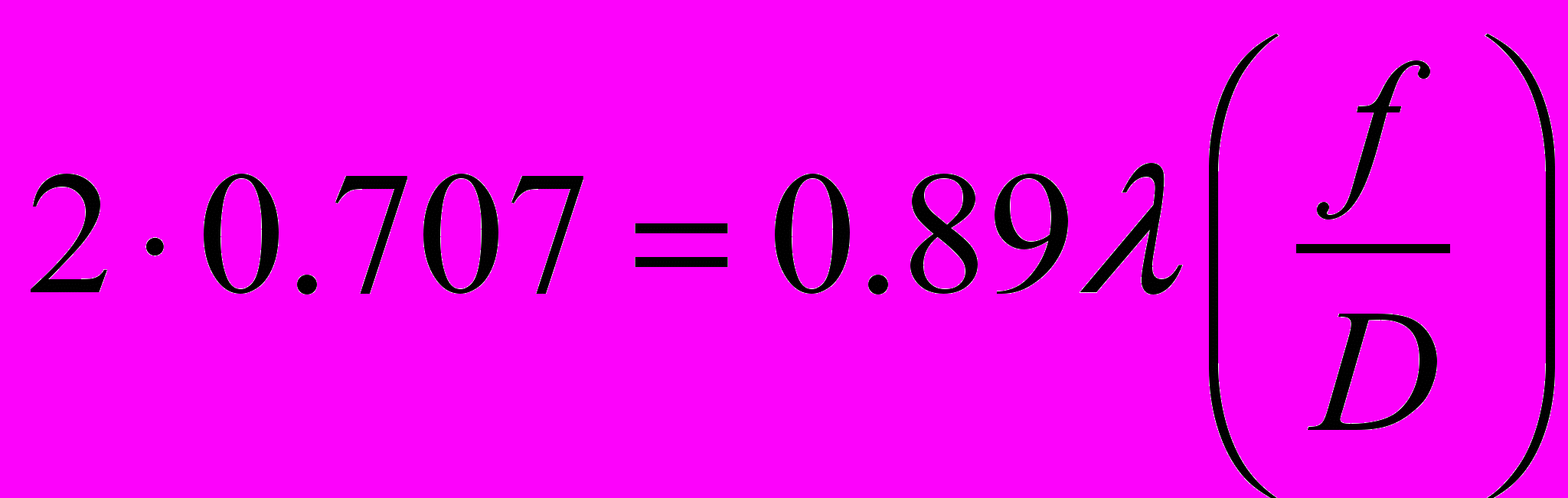
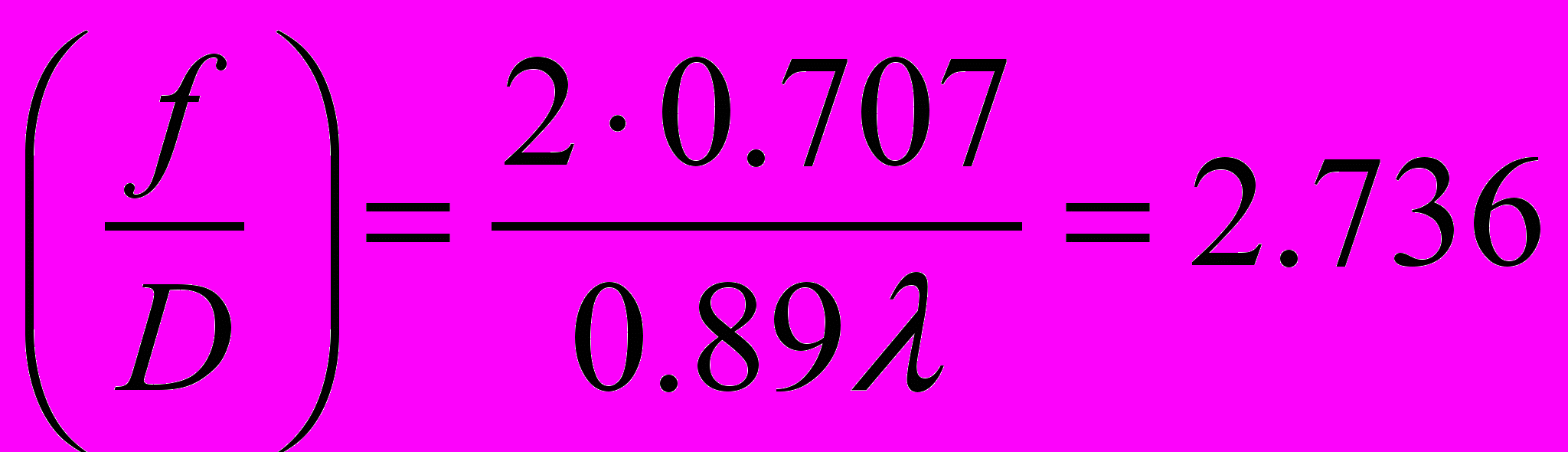
в дальнейшем будем пользоваться обозначением:
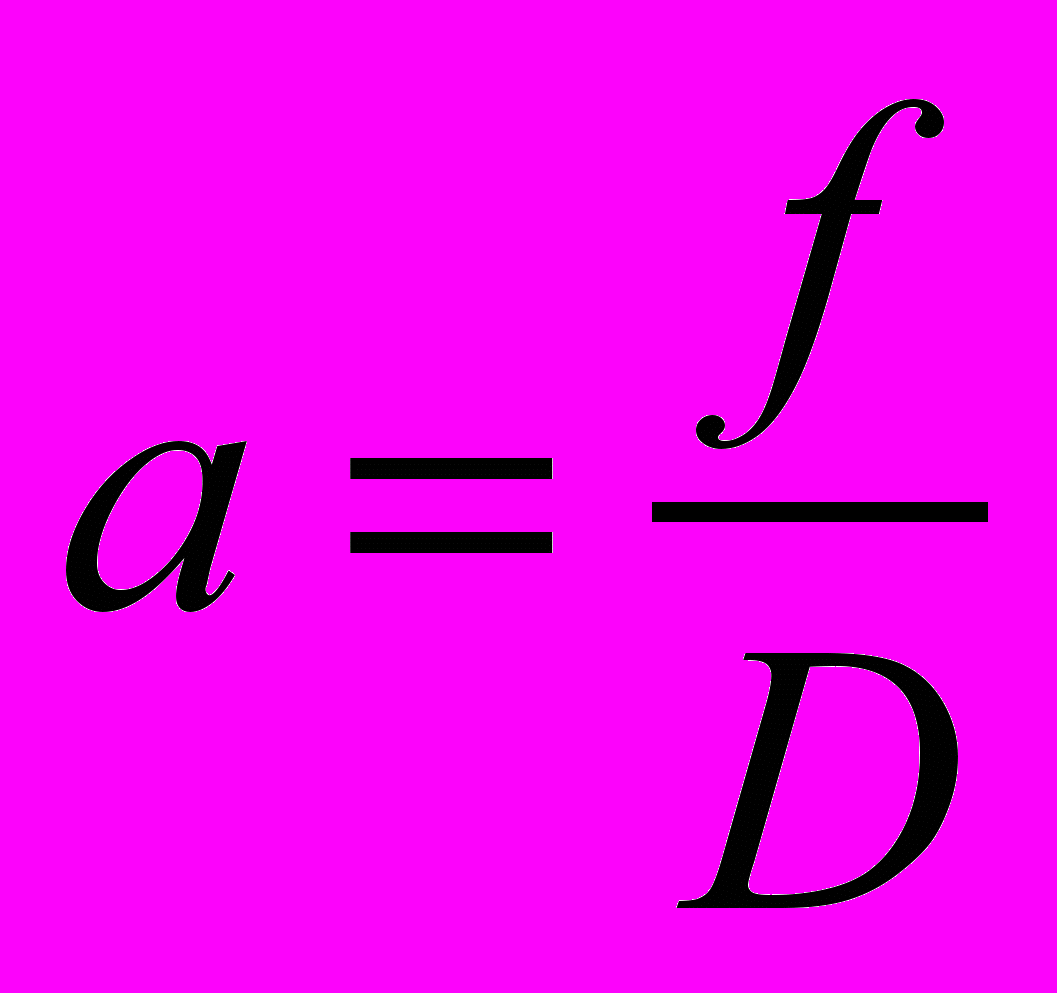
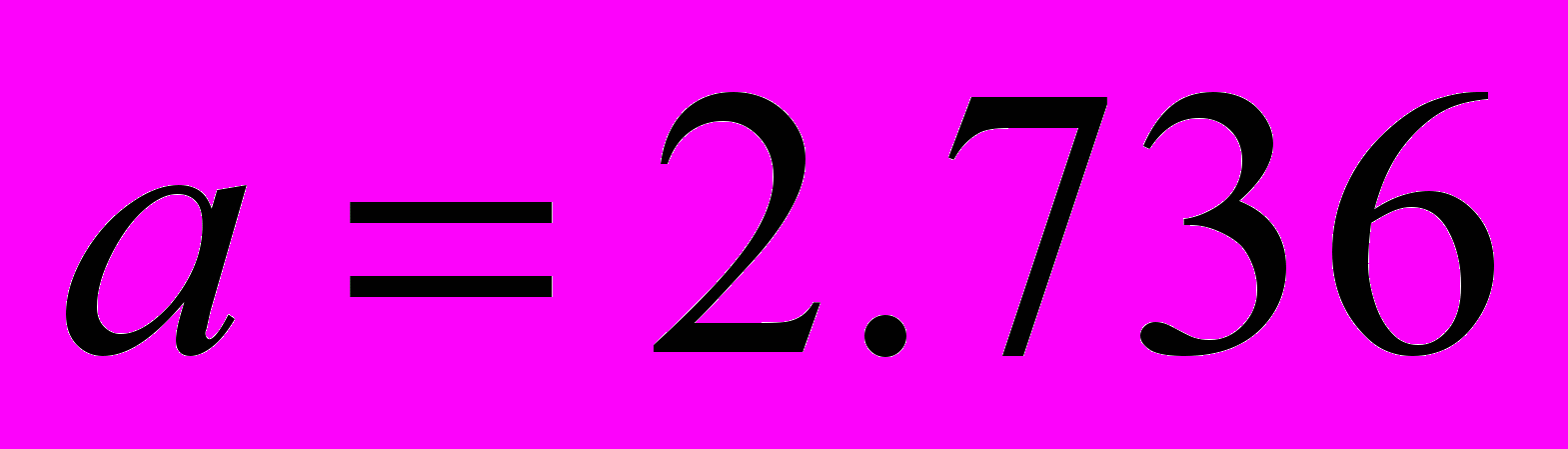
Рассчитаем протяженность фокальной области:
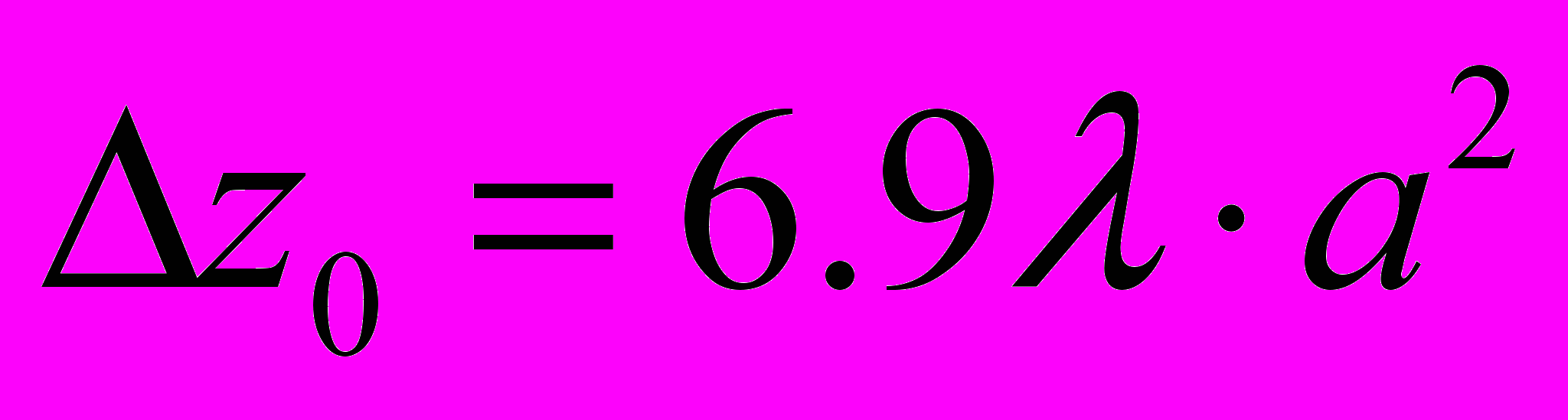
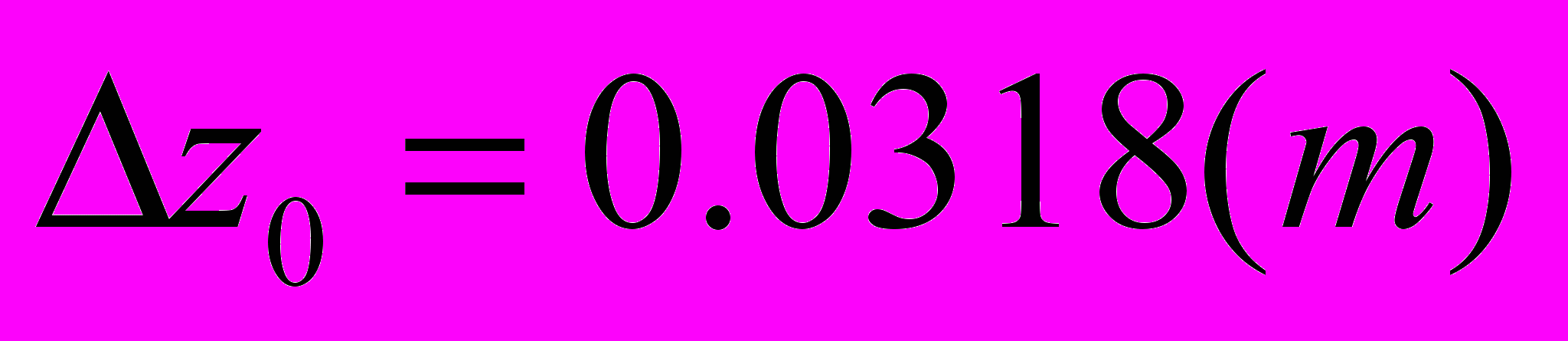
Определим число зон фокусировки
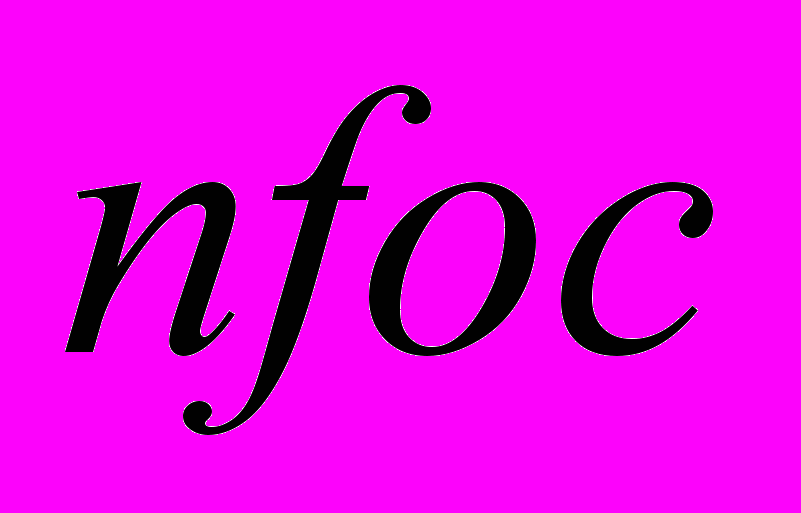
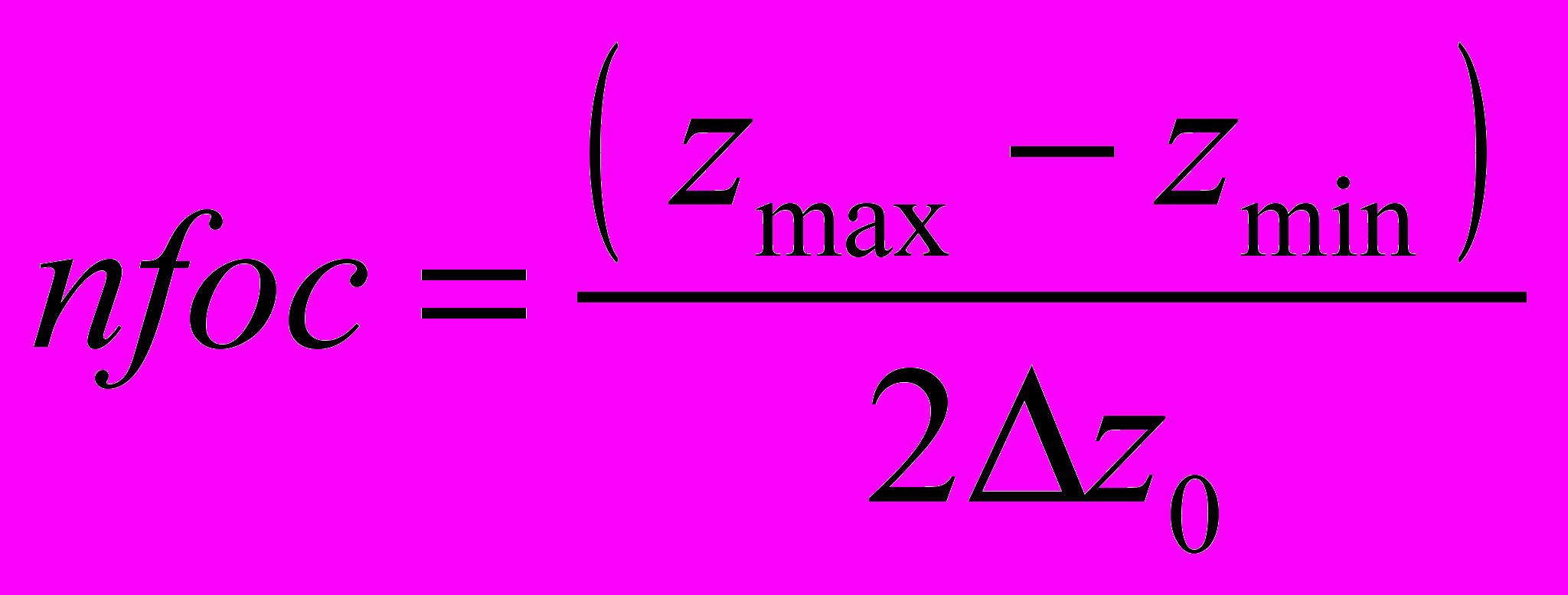
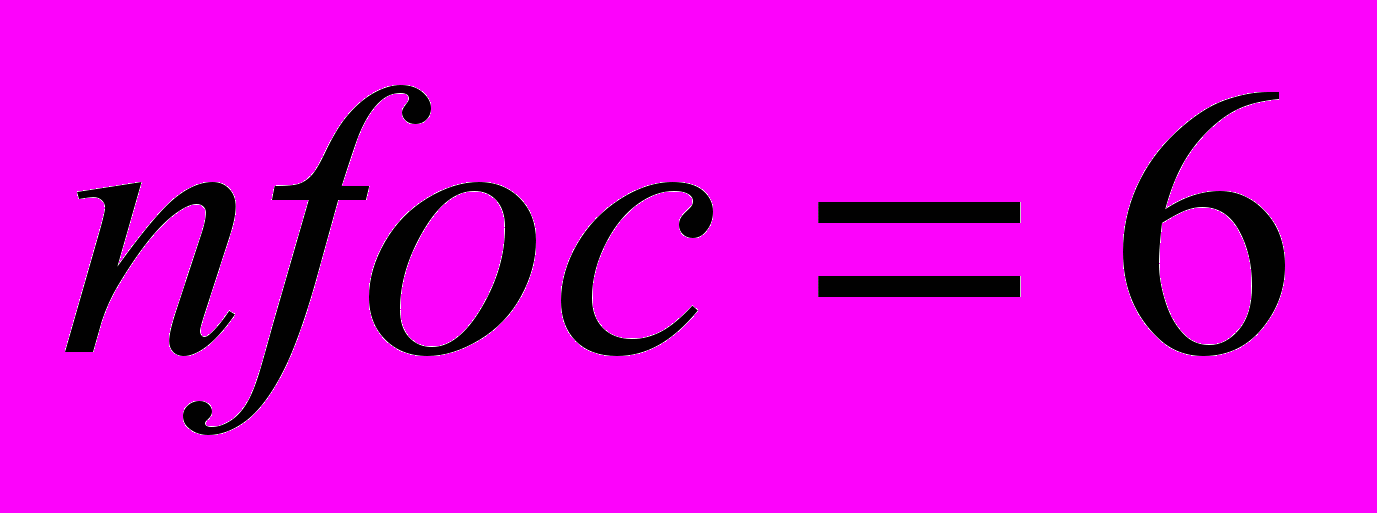
Найдем в первом приближении значения фокусных расстояний, сдвиг акустического фокуса от геометрического, значения апертур.
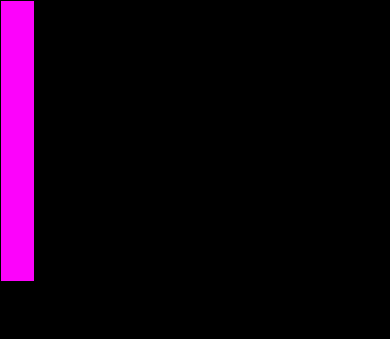
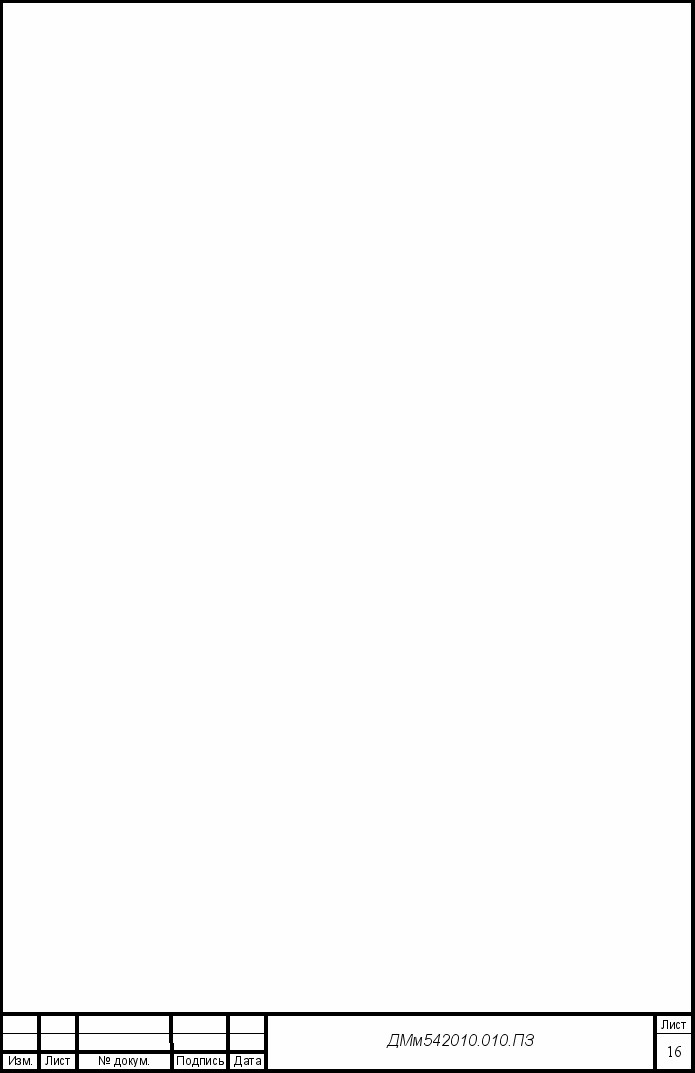
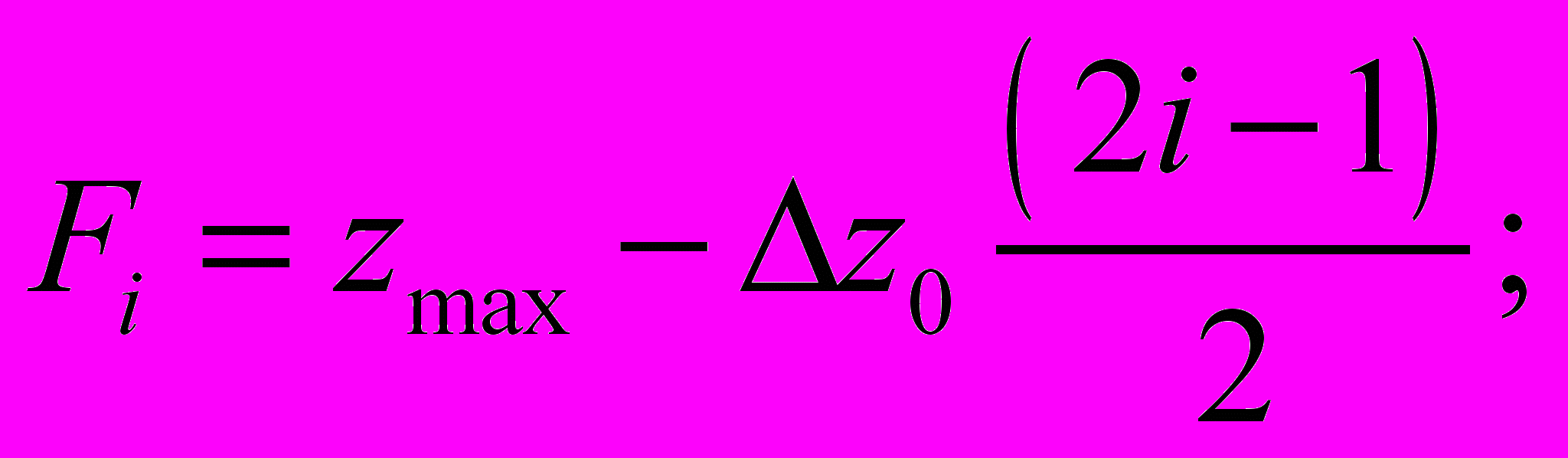
F1 =0.1841 (м)
F2 =0.1523 (м)
F3 =0.1205 (м)
F4 =0.0886 (м)
F5 =0.0568 (м)
F6 =0.0250 (м)
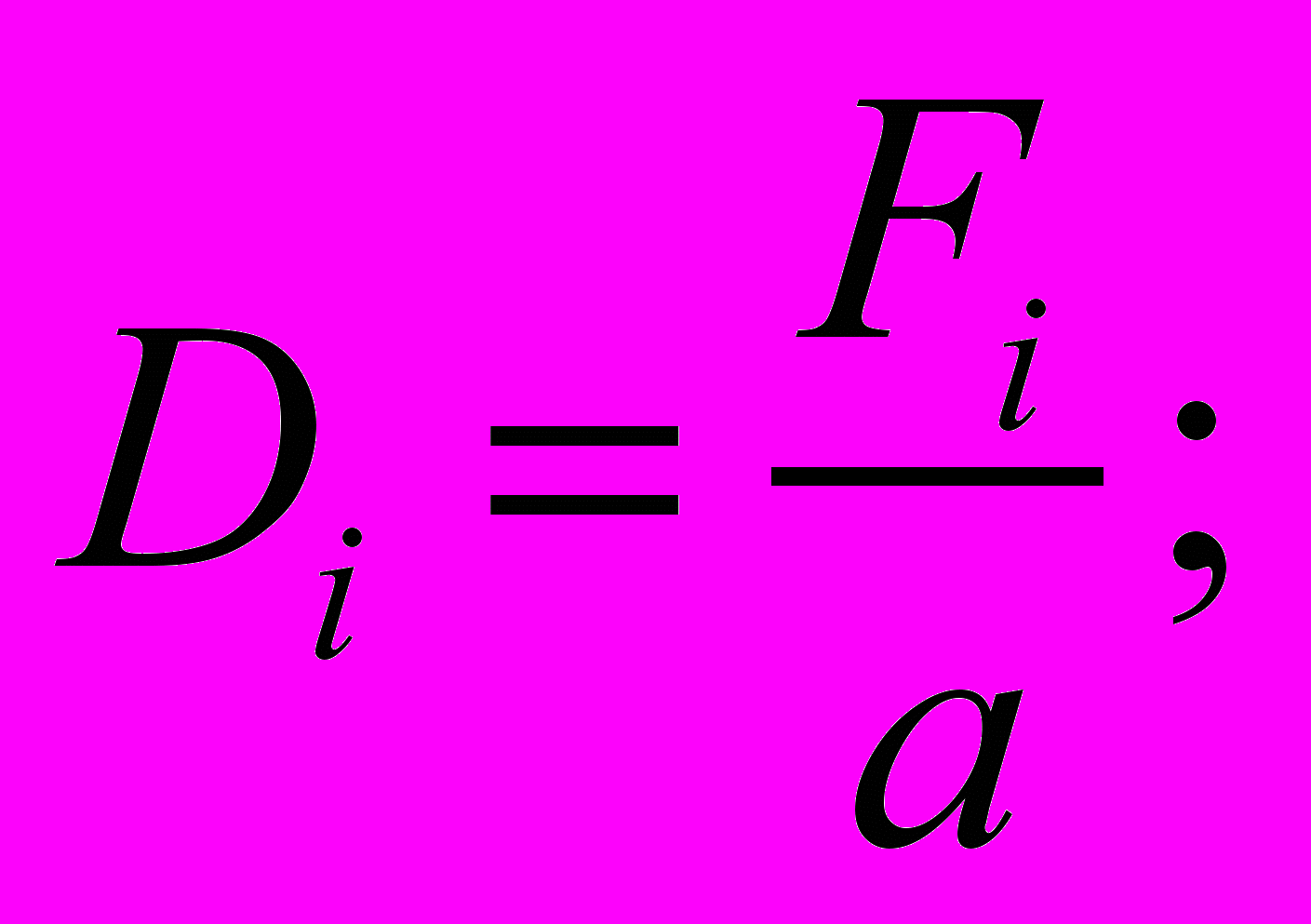
D1 =0.0673 (м)
D2 =0.0557 (м)
D3 =0.044 (м)
D4 =0.0324 (м)
D5 =0.0208 (м)
D6 =0.0091 (м)
От значений апертур перейдем к числу элементов N
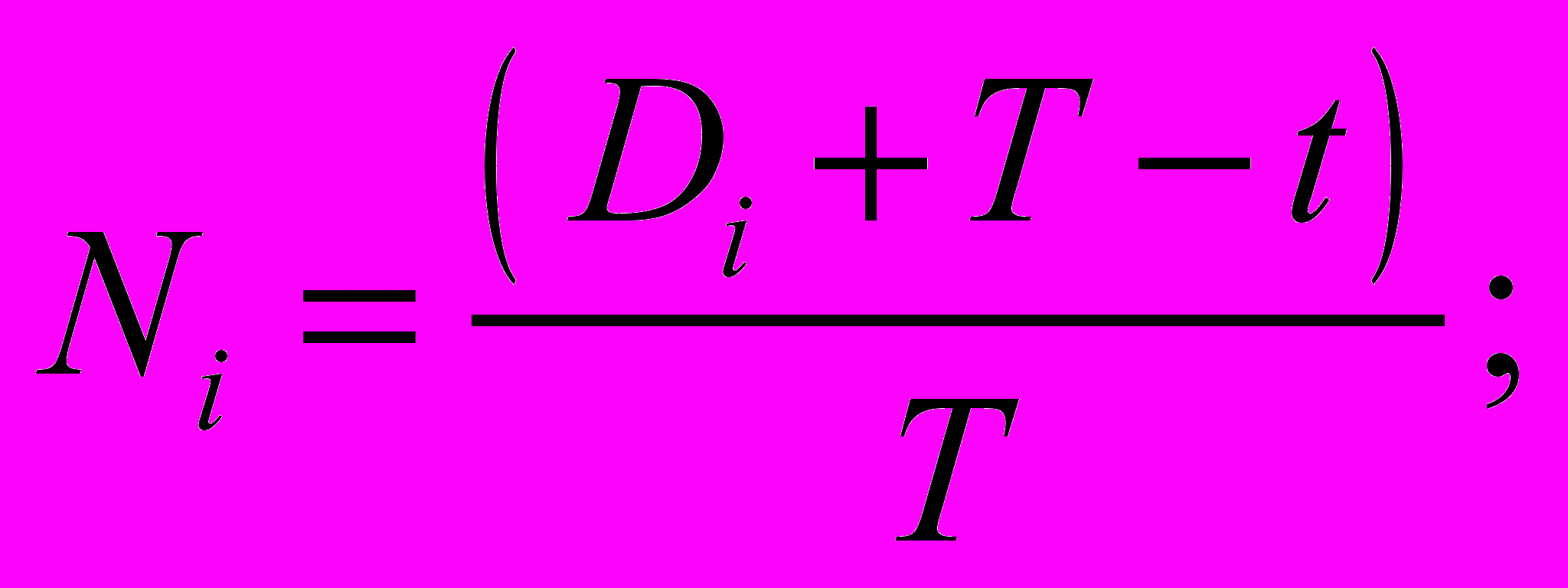
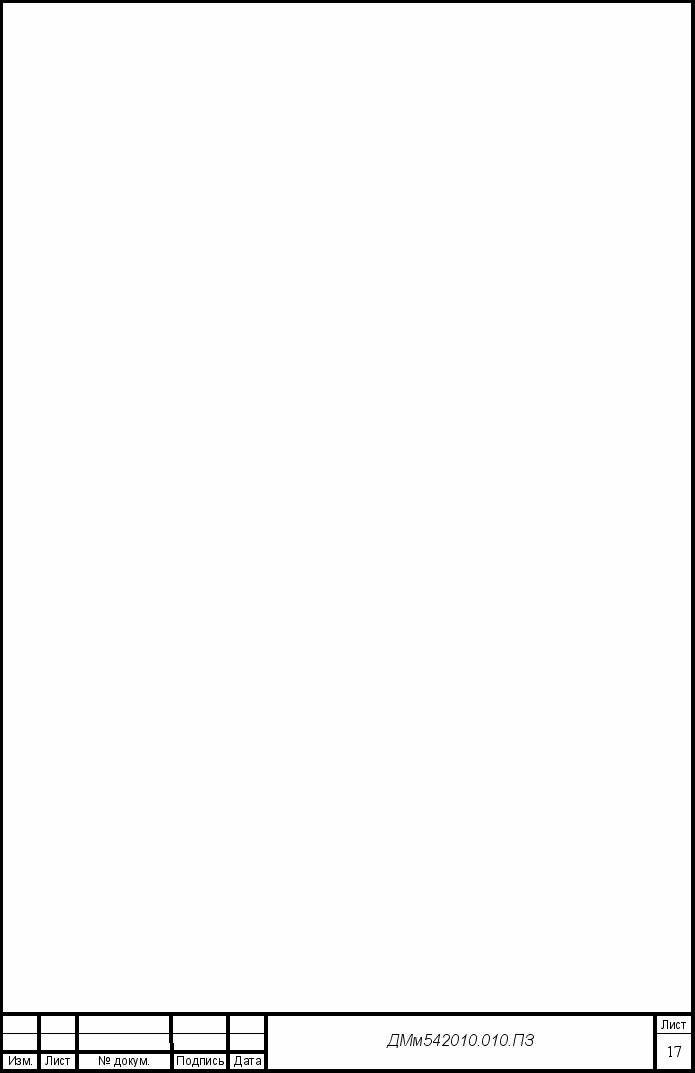
Полученные значения округляем до ближайших целых чисел. Таким образом получаем:
N1 = 241
N2 = 199
N3 = 157
N4 = 116
N5 = 74
N6 = 33
Рассчитаем коэффициент усиления по давлению
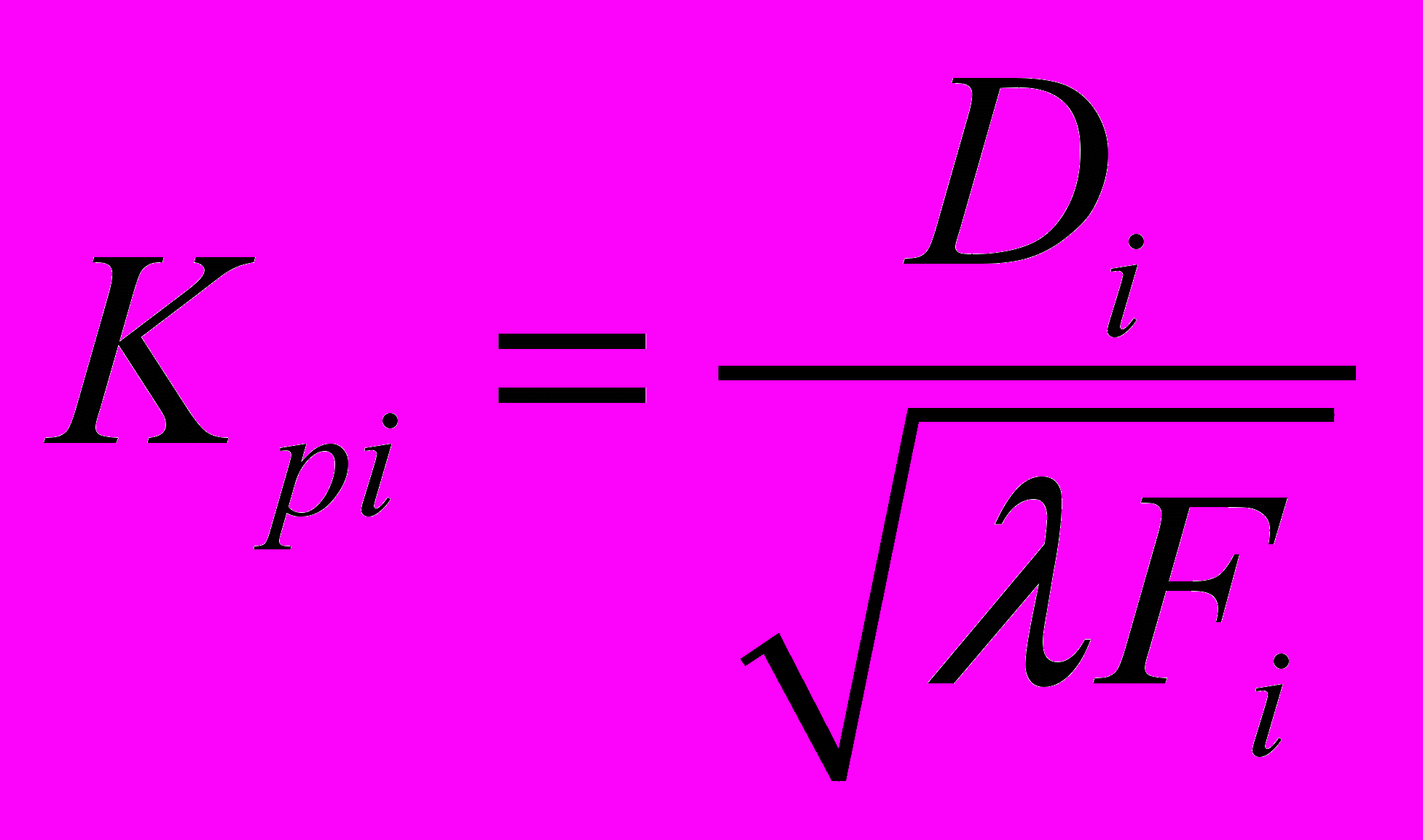
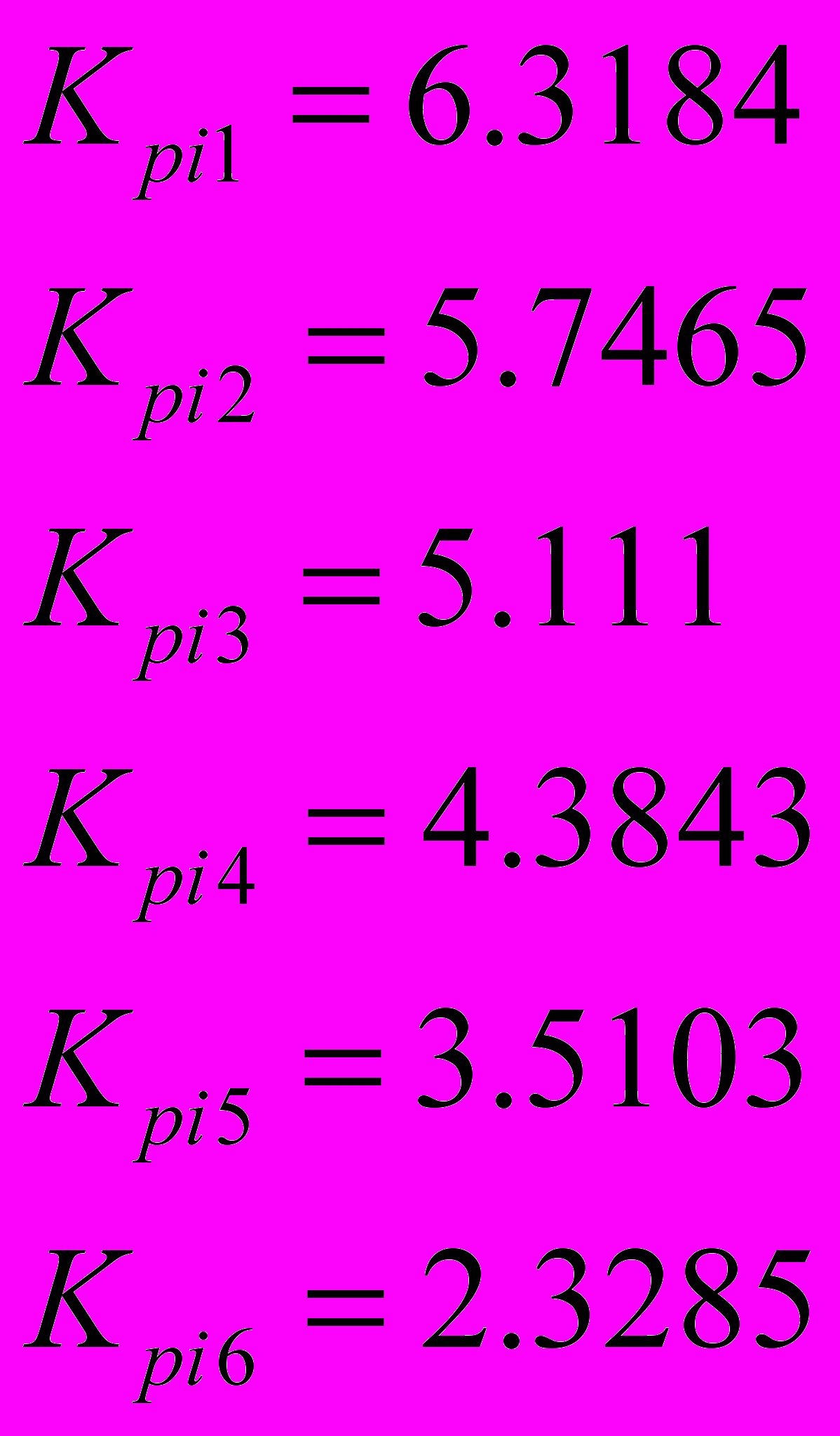
Рассчитаем смещение фокуса акустического от геометрического:
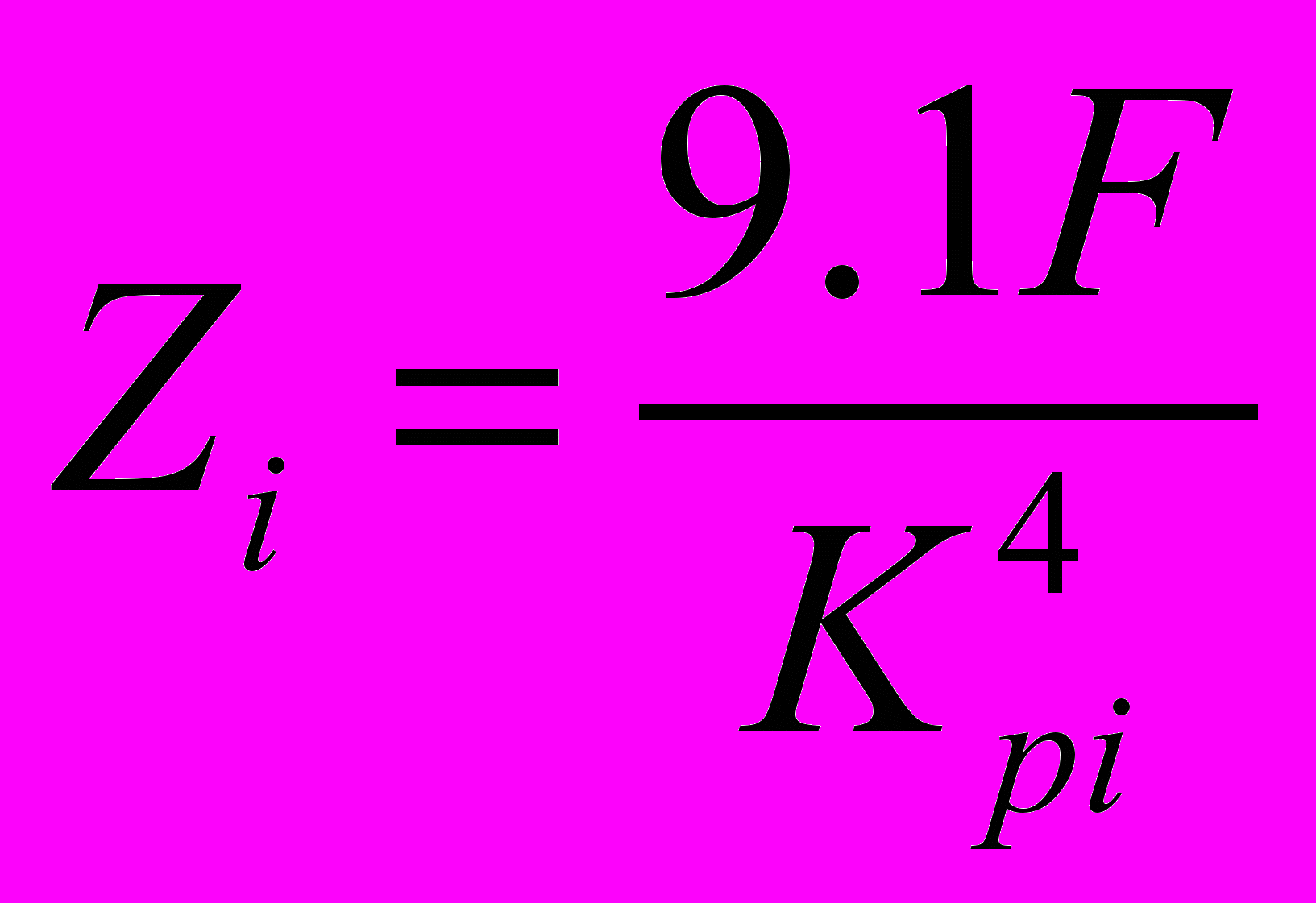
z1 =0.0011 (м)
z2 =0.0013 (м)
z3 =0.0016 (м)
z4 =0.0022 (м)
z5 =0.0034 (м)
z6 =0.0077 (м)
Пересчитаем фокусные расстояния, значения апертур и число элементов N:
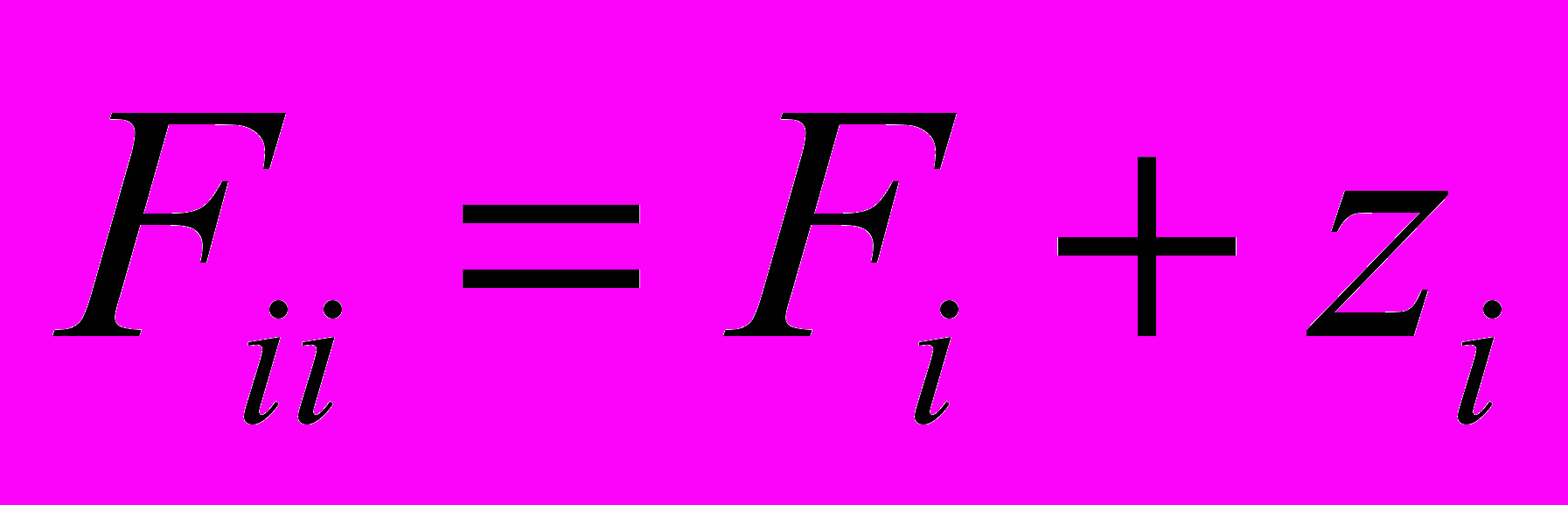
F11 =0.1851 (м)
F22 =0.1535 (м)
F33 =0.1221 (м)
F44 =0.0908 (м)
F55 =0.0602 (м)
F66 =0.0327 (м)
D11 =0.0677 (м)
D22 =0.0561 (м)
D33 =0.0446 (м)
D44 =0.0332 (м)
D55 =0.022 (м)
D66 =0.012 (м)
N11 =242
N22 =201
N33 =160
N44 =119
N55 =79
N66 =43
5. Разработка технологии изготовления прибора
Линейный сканирующий многоэлементный пьезопреобразователь состоит из конструктивно объединенных в матрицу дискретных пьезоэлементов, размещенных в ряд на плоскости. Тыльная сторона матрицы покрыта слоем демпфирующего материала, рабочая поверхность — согласующим слоем (рис. 5.1). Электроды, покрывающие пьезоэлементы со стороны рабочей поверхности матрицы, гальванически соединены между собой и заземлены, а электроды на тыльной стороне пьезоэлементов соединены многожильным кабелем с многоконтактным разъемом, к которому подключаются электронные устройства возбуждения — приема электроакустических колебаний (на рис.5.1 не показаны).
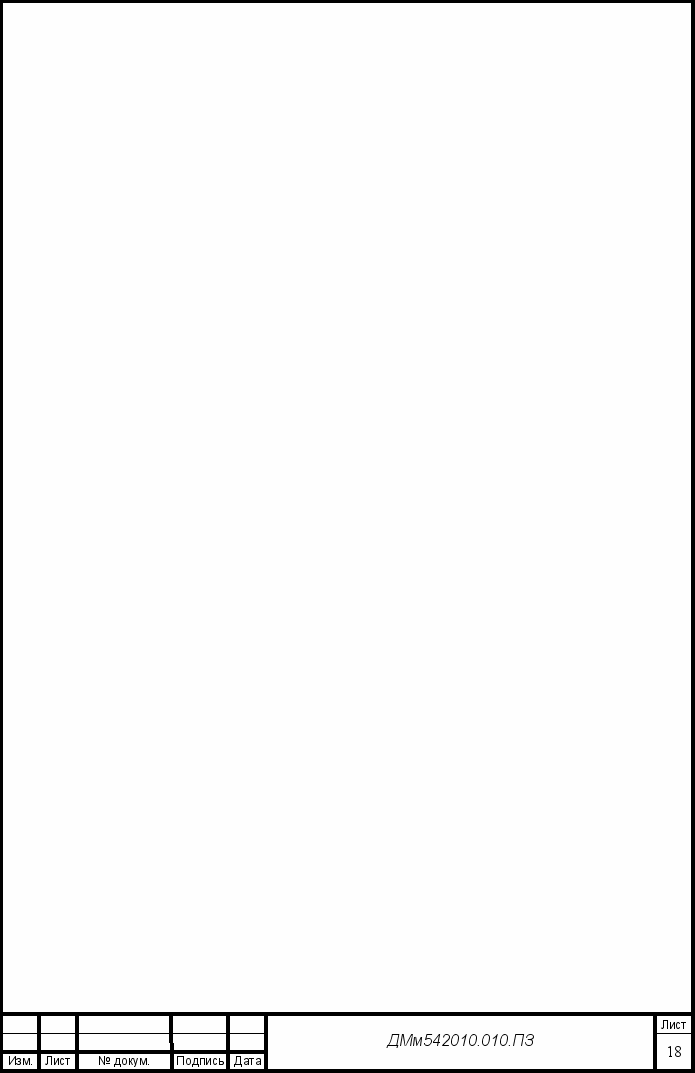
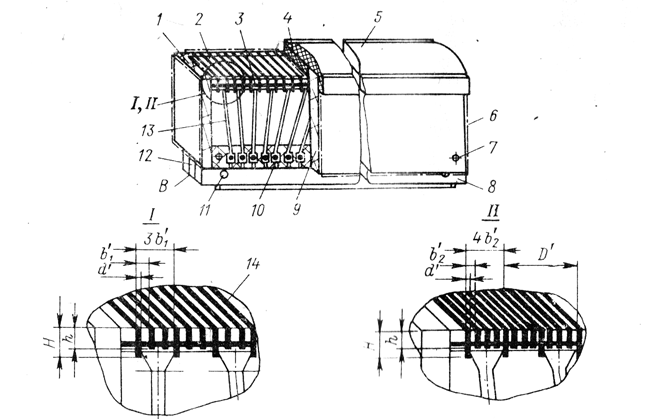
Рис. 5.1. Модуль линейной сканирующей коммутируемой матрицы пьезоэлементов (/, // - - варианты нарезки пьезэлементов на подэлементы и пайки к ним токоотводящих проводников):
1— демпфер: 2 — пьезоэлементы; 3 — легкоплавкий припой; 4 — согласующий слой; 5 — фокусирующая линза; 6 — металлизиронииное покрытие; 7 — земляные контакты; 8, 13 — печатные шлейфы токоотводящих проводников; 9 — эпоксидный компаунд; 10 — припой; 11 — винт; 12 — рамка крепления разъема; 14 — клей.
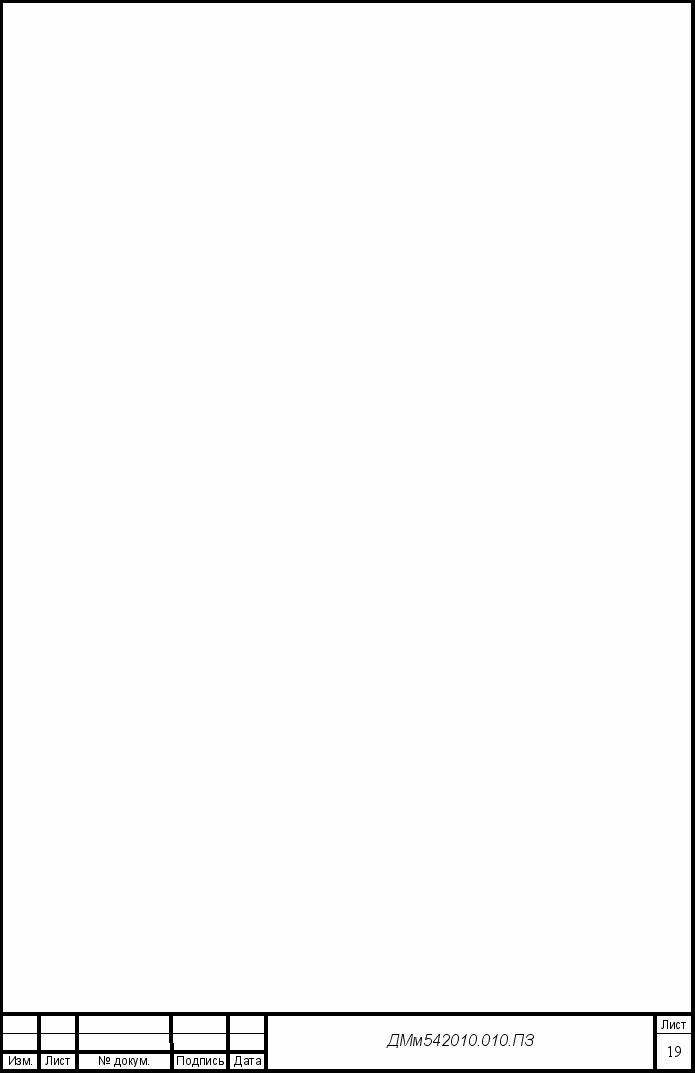
Возможен и другой способ изготовления подобного пьезопреобразователя, когда матрица изготавливается из монолитной пьезопластины путем нанесения электродов или нарезки пазов, разделяющих элементов. Однако и в этом случае не удается достичь высоких точностных характеристик из-за сильного взаимовлияния элементов. Наиболее рациональным является способ, предполагающий нарезку пьезоэлементов из монолитной пьезопластины после сборки конструктивного модуля матрицы, например следующим образом. Многоэлементный модуль пьезоэлектрической матрицы (рис. 1) изготавливается из монолитной, поляризованной по толщине пьезопластины 1, покрытой электродом, на тыльную сторону которой наносится демпфер 2 в форме параллелепипеда так, чтобы края продольных граней пьезопластины 1 остались непокрытыми демпфером 2. На тыльную часть демпфера 2 в процессе полимеризации укрепляется рамка 5, придающая модулю жесткость. К боковым противоположным поверхностям демпфера 2 вдоль пьезопластины 1 крепятся гибкие шлейфы печатных проводников 8, 13 нанесенных на подложку с шагом, равным удвоенному шагу размещения пьезоэлементов 1 в модуле. Проводники шлейфов припаиваются групповым методом к непокрытым демпфером 2 граням электрода пьезопластины 1, а обратная их сторона распаивается к контактам разъемов 6, установленных на рамке 5. Полученная конструкция дополнительно покрывается по боковому контуру эпоксидным компаундом. Далее модуль используется для резки пьезопластины на элементы и составные подэлементы, для чего с рабочей стороны модуля в пьезопластине 1 нарезаются параллельные пазы. Сначала на пьезопластине 1 нарезаются пазы с шагом b’ (см. рис. 1) на глубину H. Образовавшиеся пазы заполняются клеем 14. После этого нарезаются пазы, образующие подэлементы с шагом b1’ или b2’ в зависимости от рабочей частоты пьезопластины 1 на глубину h. При этом электрический контакт, объединяющий группу подэлементов, сохраняется за счет контактной площадки токоотводящего проводника 7, которая равна ширине пьезоэлемента (см. рис. 1). Технологические зазоры d’ заполняются клеем 14. Нанесением на модуль металлического покрытия 10 обеспечивается электрической сочинение рабочей поверхности всех пьезоэлементов, образующих общий электрод, который соединяется с земляными выводами 9 разъемов 6. После металлизации модуля наносятся согласующий
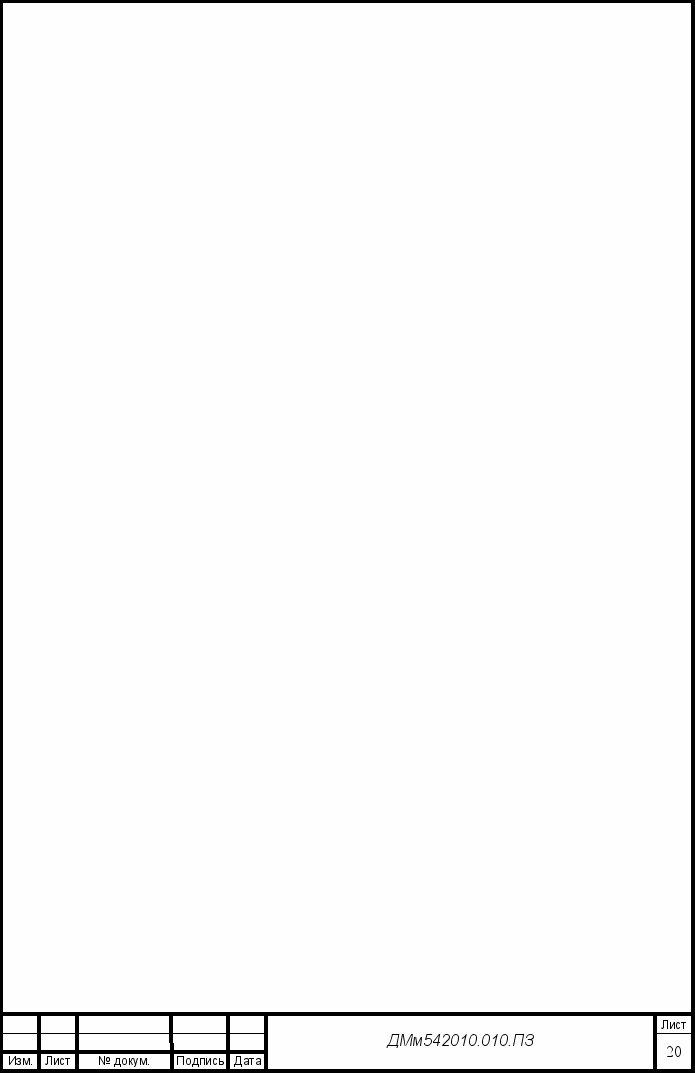
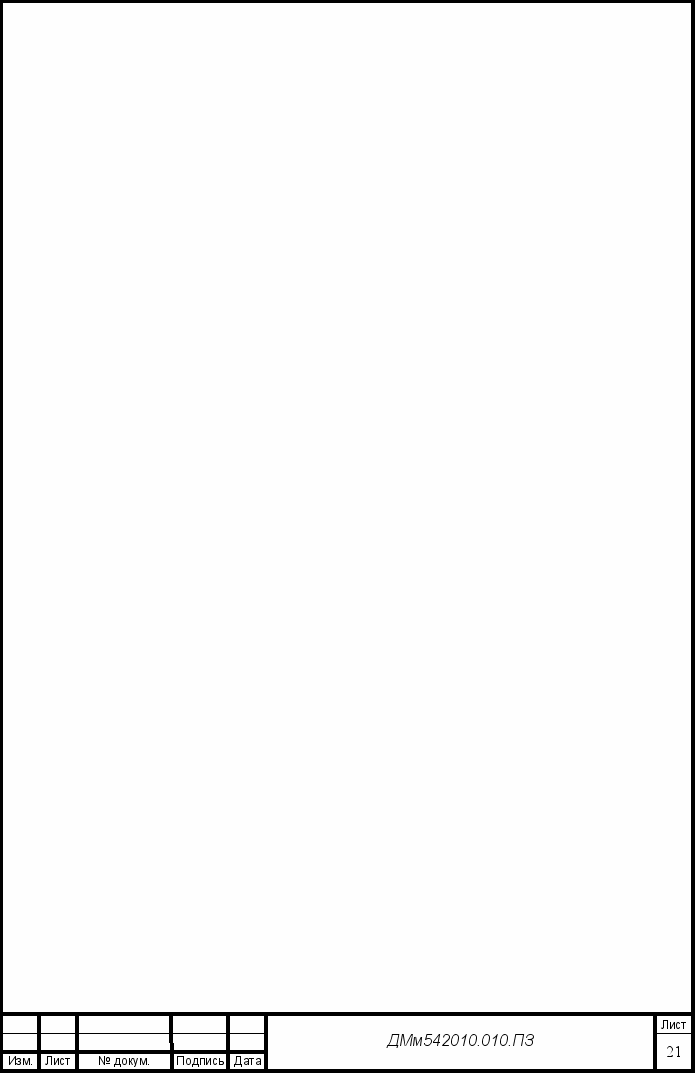
Описанная конструкция и способ изготовления многоэлементного линейного сканирующего пьезопреобразователя обеспечивают: высокую точность взаимного расположения отдельных элементов, простоту создания общего «земляного» электрода (за счет исключения индивидуальной распайки), получение высокой однородности согласующих и фокусирующих слоев, индивидуальную подстройку параметров пьезоэлементов и малые потери сигналов в электрических соединительных цепях.[2]
Существует клеевой и без клеевой технологический процесс конструкции.
Преимущества клеевых конструкций:
- относительная простота конструкции активного элемента и меньшее количество нестационарной оснастки;
- более короткий технологический цикл (в 1.5 раза короче чем у без клеевых);
- простая форма оснастки, что обеспечивает меньшую стоимость самой оснастки и уменьшает стоимость подготовки производства;
Недостатки клеевых конструкций:
- потребность в более квалифицированном персонале;
- наличие в конструкции клеевых соединений, что при не достаточной отработке технологического процесса и процесса операционного контроля приводит к увеличению процента брака и увеличивает разброс параметров преобразователя;[1]
Основываясь на преимуществах и недостатках клеевых конструкций, выберем клеевую конструкцию для технологического процесса сборки.
Опишем поэтапно технологический процесс клеевой конструкции (Рис. 5.2).
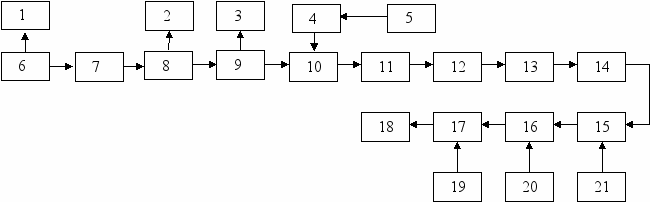
Рис. 5.2 Технологический процесс клеевой конструкции.
Материалы:
1 – пьезопластина;
2 – демпфер;
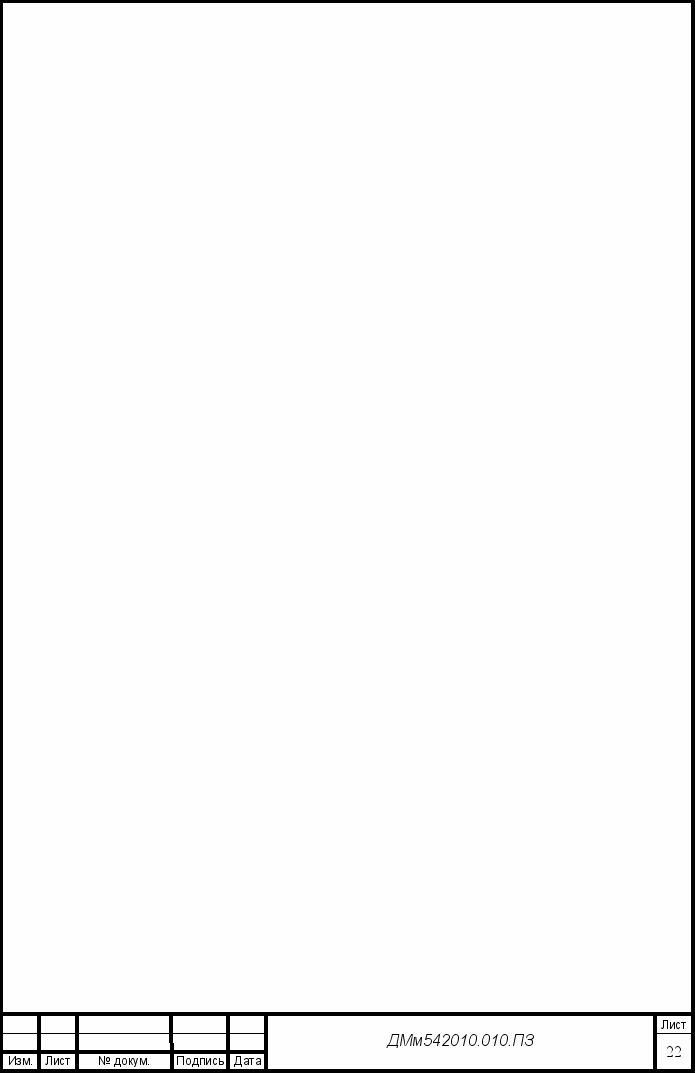
5 – розетка;
19 – кабель;
20 – акустическая линза;
21 – согласующий слой.
^ Выполняемые операции:
4 – монтаж розетки;
6 – отрезка пьезопластины по размерам;
7 – лужение кромок пьезопластины;
8 – склейка демпфера и пьезопластины;
9 – электрический монтаж гибких шлейфов;
10 – электрический монтаж розетки;
11 – заливка кромок пьезопластины;
12 – нарезка пьезопластины;
13 – заполнение пазов клеем;
14 – металлизация поверхности пьезопластины;
15 – приклейка согласующего слоя;
17 – электрический монтаж кабеля;
18 – установка в корпус и заливка матрицы в корпусе. [1]
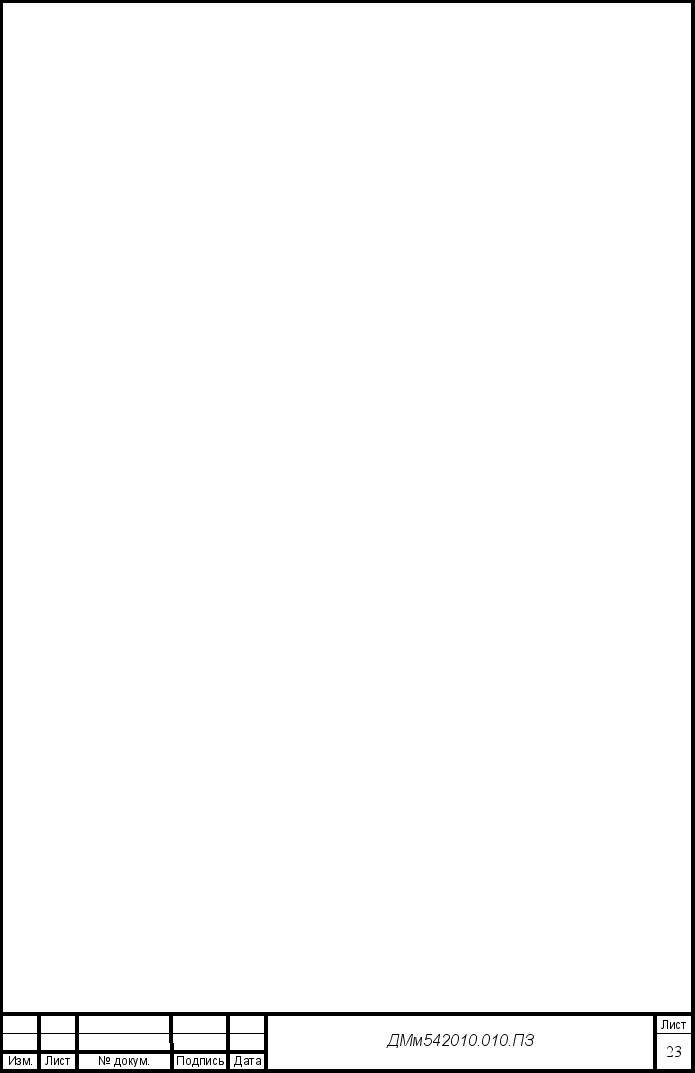
В данном курсовом проекте была разработана конструкция и изучена технология изготовления ультразвукового медицинского преобразователя с электронным сканированием (2.5 МГц). Был проведён аналитический обзор литературы и патентный поиск существующих аналогов устройств, выбрана схема построения прибора, проведён расчёт основных параметров, описан поэтапно технологический процесс клеевой конструкции.
Были проанализированы существующие типы пьезокерамики, и в качестве материала для пьезопластин была выбрана пьезокерамика ЦТСНВ-1. Для изготовления многоэлементного преобразователя выбран метод нарезки пьезоэлементов из монолитной пьезопластины после сборки конструктивного модуля матрицы. Для технологического процесса сборки был выбран клеевой технологический процесс.
С помощью системы КОМПАС-3D была разработана 3D модель устройства, и необходимый набор чертежей.
ЛИТЕРАТУРА
- Конспект лекций по дисциплине «Конструирование медицинских акустических приборов и аппаратов»
- Домаркас В. Й., Пилецкас Э. Л. Ультразвуковая эхоскопия. Л.: Машиностроение. 1988г. 276 с
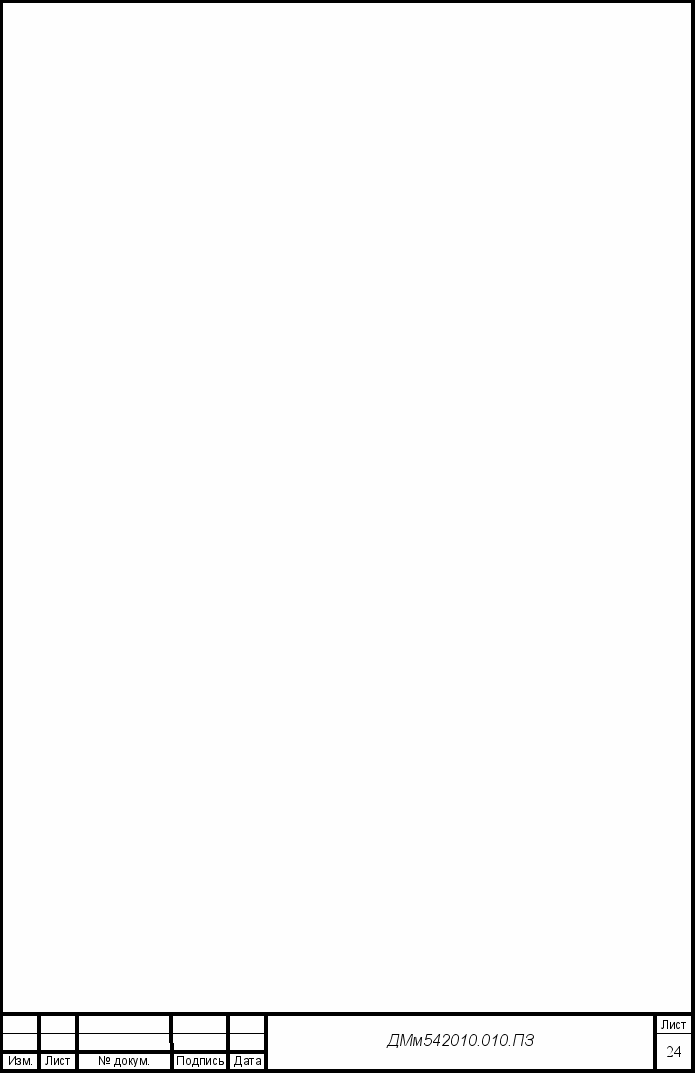