Отчет по производственной практике на уомз в цехе №315
Вид материала | Отчет |
- Отчет по производственной практике место прохождения практики, 9.49kb.
- Методические рекомендации по проведению и защите производственной практики, 942.15kb.
- Рабочая программа и методические указания по второй производственной практике для студентов, 304.42kb.
- Отчет о производственной практике по хирургической стоматологии Студента 4 курса стоматологического, 27.36kb.
- Отчет по производственной практике Место прохождения практики: зао «УралСтройЭкспо», 384.14kb.
- Программа и методические указания по учебно-производственной промыслово-геологической, 281.58kb.
- Отчет о производственной практике в 2010 году, 133.51kb.
- Отчёт о преддипломной практике Вотделе опеки и попечительства администрации Кимовского, 184.56kb.
- Методическое руководство и дневник по летней производственной практике для студентов, 458.11kb.
- Рабочая программа по производственной практике, преддипломной практике (наименование, 162.05kb.
Шлифовальный инструмент.
Для шлифования свободным абразивом применяют металлические шлифовальники: плоские планшайбы, сферические чашки и грибы. Материал шлифовальников – латунь, серый чугун или мягкая сталь. Шлифование сферических поверхностей оптических деталей выполняют комплектом шлифовальников по переходам, применяя абразивный порошек с убывающей зернистостью. Радиус рабочей поверхности шлифовальника рассчитывают для каждого перехода с учетом припуска на обработку и зернистости абразива. При переходе от более крупного абразива к мелкому Rсф у грибов увиличевается, а у чашек – уменьшается. Диаметры плоских планшайб определяют в зависимости от диаметра обрабатываемой детали.
6.5.3. Полировальный инструмент.
Полировальный инструмент представляет собой металлический корпус, на поверхность которого приклеен войлок, фетр и т.п. или нанесен слой полировочной смолы. Корпус приготовляют из алюминиевых сплавов АЛ2 и АЛ9, а также из литейного цинкового сплава. Размеры полировальников устанавливают в зависимости от диаметра обрабатываемого блока и положения инструмента относительно обрабатываемых деталей.
При изготовлении полировальников из технических грубошерстных тканей материал раскрашивают по выкройке и наклеивают на нагретый корпус с помощью смолы.
Слой расплавленной смолы наносят на поверхность нагретого корпуса, равномерно распределяя ее лопаточкой. После загустения до вязкого состояния смолу формуют увлажненным формовочным приспособлением, имеющим обратный знак радиуса кривизны. В центре полировальника делается выемка, а края обрезают ножом. Сферу полировальника располировывают по поверхности шлифовального блока деталей на шлифовально-полировальном станке.
Для закрепления оптических деталей используют следующие приспособления: вакуумный и мембранный патроны, приспособление с механическим креплением, наклеечные приспособления для призм, крепления на оптическом контакте.
Так как полировальный инструмент не соприкасается с обрабатываемым стеклом, то выбор материала его дешевизной, малым удельным весом и простотой обработки. Н: чугун, латунь, дюралюминий. Подложки из ткани наклеиваются на полировальный инструмент так, чтобы радиус кривизны поверхности подложки совпадал бы с радиусом кривизны отполированного блока.

Rδ – радиус блока,
∆п – толщина подложки,
δ – толщина слоя наклеечной смолы.
Смоляная подложка при полировке плоскостей и блоков с малой кривизной формируется в виде слоя постоянной толщины. При полировке блоков значительной кривизны сохранение постоянство толщины слоя и кривизны поверхности невозможно. Так как смола, нагреваясь, будет постепенно течь от середины к краям блока, то толщина ее слоя в середине δс должна быть больше, чем на краю δк.
Размеры диаметра и высоты полировального инструмента связаны с размерами подложки:
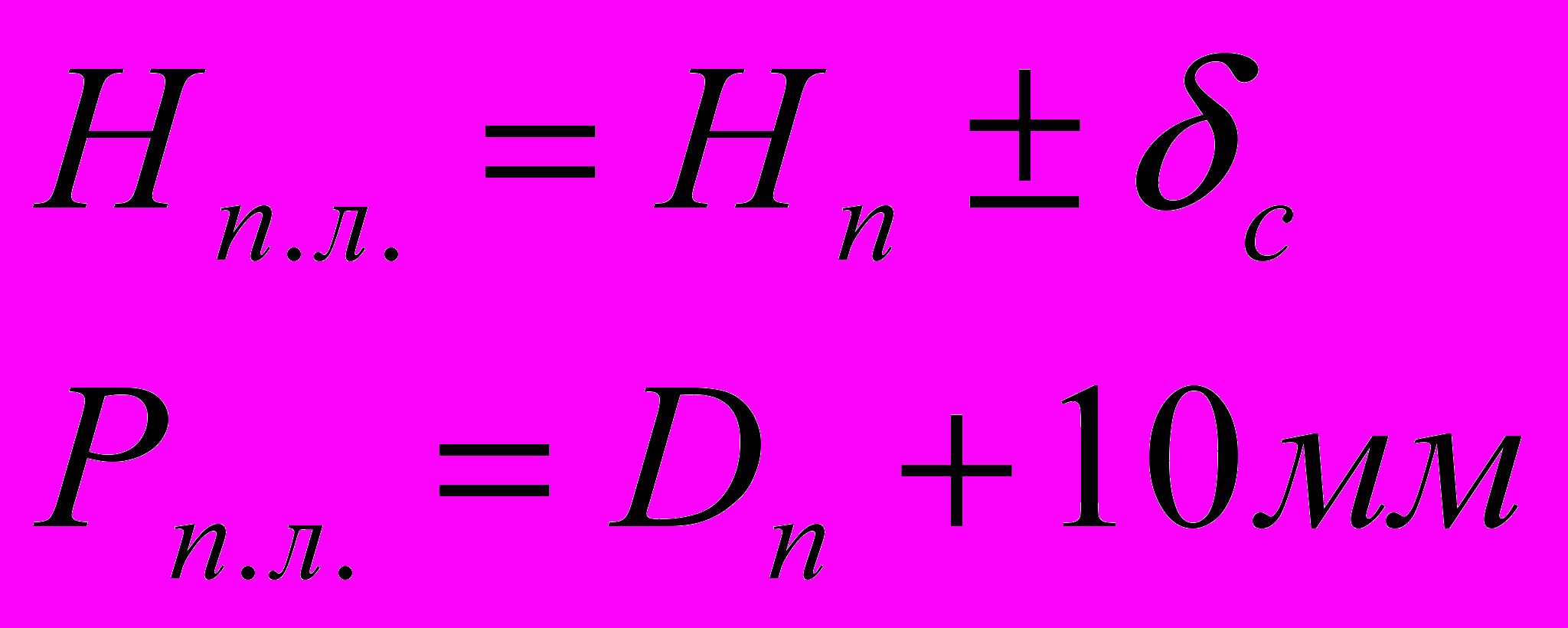
6.6 Центрировка линз.
В правильно изготовленной линзе ее оптическая ось, проходящая через центры сфер, совпадает с геометрической осью, равноудаленной от края линзы. Такая линза симметрична своей оси, имеет постоянную толщину края и называется центрированной.
Величина l не совмещения геометрической и оптической осей называется децентрировкой линзы. Наличие децентрировки приводит к резкому ухудшению разрешающей силы и качества изображения оптической системы.
Процесс центрировки линз заключается в округливании ее относительно оптической оси до заданного диаметра D. Отыскание положения и фиксирование оптической оси линзы производятся на центрировочных патронах. Существует два метода: оптический и механический. Оптический метод заключается в центрировке:
а) по изображению источника света, полученному при отражении света от поверхности линзы (центрировка по блику),
б) по изображению сетки, полученному после прохождения света через линзу (центрировка по прибору).
Механический способ:
- центрировка линз сжатием,
- центрировка линз сжатием с корректировкой оптическим способом.
Допустимая децентровка 0,005 – 0,02.
6.7. Фасетировка линз.
Фасетировка осуществляется следующими способами:
- обработка шлифовальным кругом или фрезой на центрировочным станке;
- шлифовка при помощи абразива на шлифовальнике вручную по одной штуке;
- шлифовка при помощи чашек на специальном станке по несколько штук одновременно.
6.8. Основные типы инструментов для обработки стекла.
Для выполнения различных технологических операций обработки оптических деталей широко используют: алмазный инструмент, плоские планшайбы, сферические чашки, грибы, полировальный инструмент.
Алмазный инструмент.
Основные характеристики, форма и размеры алмазного слоя, зернистость и массовая концентрация алмазного порошка, материал связки. Широко распространены алмазные инструменты следующих типов притиры для тонкого шлифования, фасонные фрезы, сборные круги, специальные сверла. Вид и зернистость алмазного порошка выбирают из условий работы инструмента, требований к производительности и шероховатости обрабатываемой поверхности. Связка также влияет на производительность работы и износостойкость инструмента. Связка должна прочно удерживать алмазные зерна, обладать по отношению к ним и корпусу хорошей адгезией и быть достаточно термостойкой. Износостойкость связки не должна препятствовать самозатачиванию инструмента. В основном используют многокомпонентные металлические связки на основе порошков меди, алюминия, железа, кобальта. Связки на основе меди (М, М1, М10 и др.) с добавкой олова, никеля, цинка хорошо спекаются при Т=750градусов Цельсия, имеют высокую прочность. Связки на основе алюминия и железа (МО и МЖ) применяют для изготовления инструментов, работающих с большими нагрузками.
Изготовление. Алмазоносный слой закрепляют на корпусе инструмента путем прессования порошков связки, смешанной с алмазом, электрохимическим осаждением связки (гальваностегия) или закаткой алмазных зерен в мягкую основу корпуса инструмента.
Основной метод – прессование металлических порошков с последующим спеканием. Технологический процесс состоит из следующих операций: составление шихты связки и алмазного порошка, брикетирование, спекание и прессование.
Электрохимическим осаждением металлической связки изготовляют алмазный инструмент с тонкими режущими крошками или с фасочной рабочей поверхностью. Металлический корпус инструмента помещают в гальваническую ванну с электролитом, соединяют с источником постоянного тока. Корпус является катодом. Анод изготовляют из материала связки, обычно никеля. В процессе электролиза положительные ионы металла связки устремляются к катоду, проходят через алмазные зерна, размещенные на поверхности корпуса инструмента, и, восстанавливаясь, образуют слой металлической связки.
стандарт | Эскиз профиля инструмента | Область применения |
Круг чашечный конический ГОСТ 16172-80 | ![]() | Обработка плоских и сферических поверхностей |
Круг плоский прямого профиля ГОСТ 16167-80 | ![]() | Обработка цилиндрических поверхностей, центрирование |
Круг плоский трехсторонний ГОСТ 16169-81 | ![]() | Обработка пазов, торцов, канавок |
Круг плоский ГОСТ 17007-80 | ![]() | Нанесение фасок на призмах, пластинках |
Круг кольцевой ГОСТ 17006-80 | ![]() | Обработка сферических и плоских поверхностей, сверление |
Круг плоский с выточкой ГОСТ 16170-81 | ![]() | Обработка плоских поверхностей широких фасок на пластинах |
7. Системы и методы контроля производства.
Каждый технологический процесс в линии производства оптического стекла и деталей из него сопровождается контрольными мероприятиями.
Контроль процесса варки.
Большое значение в производстве оптического стекла имеет контроль оптических свойств в процессе варки. Обычно для контроля используются полированные детали правильной геометрической формы.
Разработанный профессором И. В. Обреимовым метод контроля стекла в кусках неправильной формы позволил использовать показатель преломления стекла в процессе его варки. Сущность метода заключается в следующем: в процессе варки стекла берется проба в момент, когда стекломасса достаточно однородна. Проба, остывая на воздухе, закаляется. После этого измеряется показатель преломления (n) методом Обреимова и сравнивают nр пробы с nр эталонного образца. Если показатель преломления испытываемого стекла окажется выше, чем эталонного, то в стекломассу вводят стеклобой с более низким показателем преломления и продолжают варку, и, наоборот. Также в плавку можно добавлять какой – либо компонент шихты, легко усваиваемый стекломассой и регулирующий показатель преломления.
Данные для корректировки состава шихты можно получить в течение 15 -20 минут. При использовании данного метода брак при изготовлении стекол снижается до 2 -3%.
Окончательный контроль заготовок и правила их приемки.
Все заготовки после окончательного отжига подвергаются тщательному контролю по своим оптическим свойствам, качеству стекол и внешними дефектами.
К внешним дефектам относятся:
- “Шамот”- брак заготовок, вызванный прониканием непрозрачных включений в поверхностный слой стекла;
- Дымки – включения мелких частиц порошка – подсыпки или же мелких пузырей;
- Складка – глубокая борозда по поверхности заготовки, образовавшаяся при прессовке;
- Вмятина – поверхностное углубление прессовки, образовавшееся при прессовании или охлаждении заготовки;
- Просечка – поверхностная неглубокая трещина, возникшая при прессовании или охлаждении заготовки;
- Заколы – неглубокие трещины, образовавшиеся от удара;
- Выколки – повреждения поверхности, имеющие раковистую структуру и образовавшиеся от удара.
Размеры заготовок измеряются штангенциркулем, толщемером или скобами с точностью до 0,1 мм. Сферичность поверхности проверяются радиусными шаблонами, а плоскостность – линейкой. Размеры дефектов определяется наружным осмотром при сильном боковом освещении и смачивании заготовок иммерсионной жидкости.
Приемка заготовок осуществляется отделом технического контроля завода – изготовителя. На каждую партию составляется паспорт, в котором указываются номер и дата паспорта, завод - изготовитель, наименование заготовки, количество заготовок в партии, марка стекла, номера плавок, номера отжигов, категории и классы стекла по оптическим свойствам и показателям качества стекла.
Контроль при резании, раскалывании и распиливании стекла.
При резании и раскалывании основным видом брака является неправильная форма поверхностей, полученных после проведения данных операций. В процессе распиливания причинами такого брака стекла в нем могут образоваться трещины и выколки. При контроле рассмотренных операций проверяются размеры полученных заготовок. Мерительным инструментом выступает штангенциркуль. Допускаемые отклонения размеров
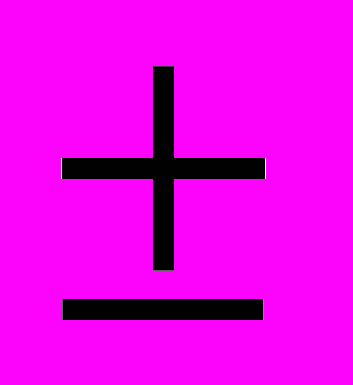
Контроль при сверлении стекла.
Основные виды брака при сверлении:
- Отступление от диаметра;
- Выколка на краях отверстия.
Диаметр отверстия проверяется порядка
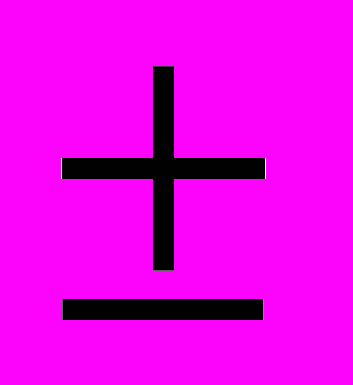
Контроль при обработке стекла фрезами и шлифовальными кругами.
Контроль линейных размеров заготовок после обработки фрезами и шлифовальными кругами производится с точностью до 0,1 – 0,01 мм. Измерения выполняются штангенциркулем, толщемером, глубиномером и микрометрами. Для контроля однотипных деталей широко применяют скобы. Контроль размера и профиля пазов и закруглений осуществляется шаблонами. Контроль толщины слоя стекла, снятого при фрезеровании линз, производится по диаметру круга радиуса r, остающегося на площадке после фрезерования. Радиус кривизны фрезерованной поверхности проверяется методом притирки. Поверхность блока должна притираться к поверхности контрольного притирочного инструмента зоной определенной ширины. Контроль плоскости производится при помощи линейки.
Контроль чистоты поверхности производится с помощью лупы с трехкратным увеличением при наблюдении поверхности в отраженном свете.
Контроль кривизны поверхности шлифовальников.
Контроль плоскостей осуществляется металлическими линейками со скошенными кроями. При незначительной сферичности поверхности радиус ее кривизны может быть приближенно определен по формуле:
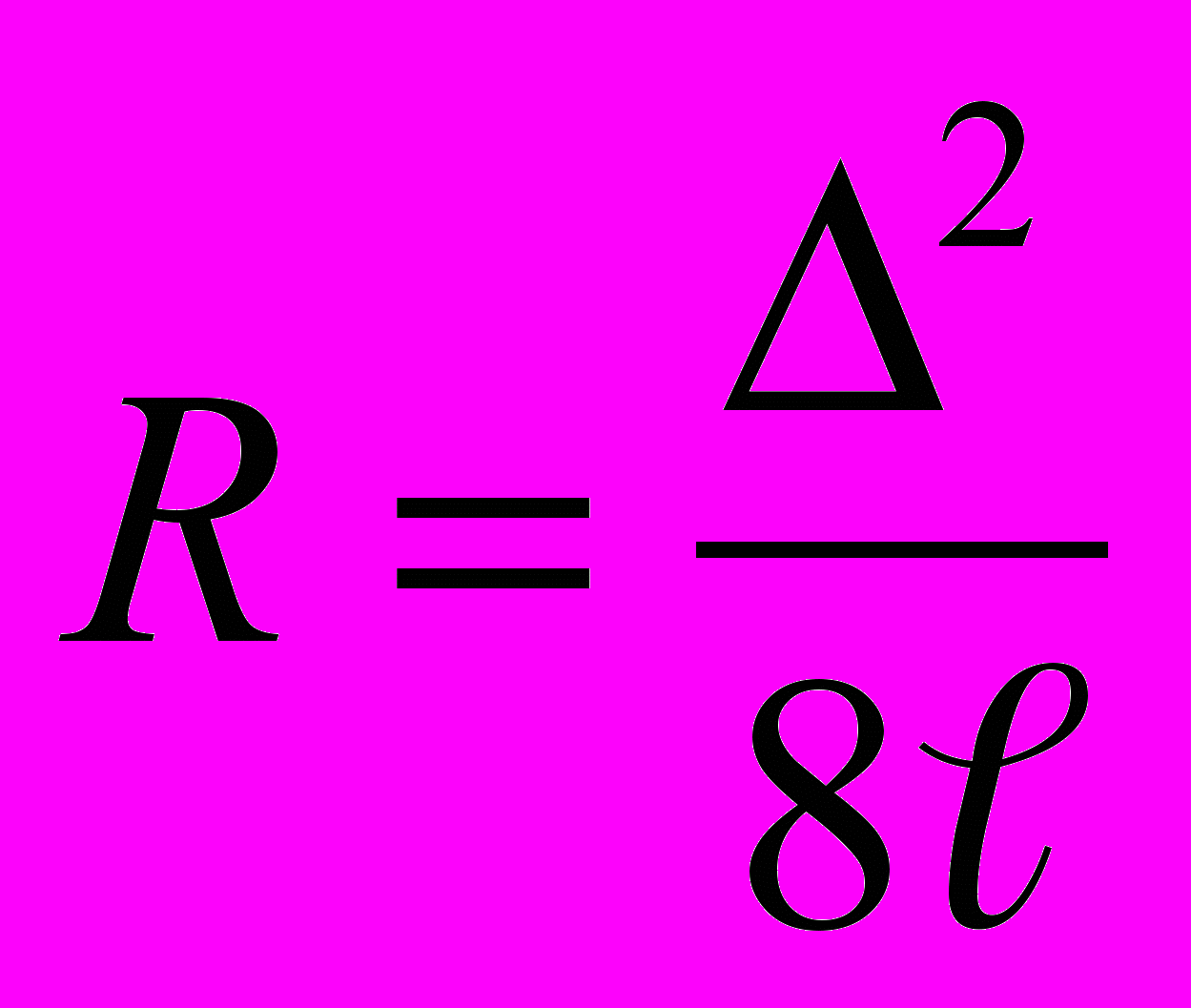
∆ - глубина просвета;
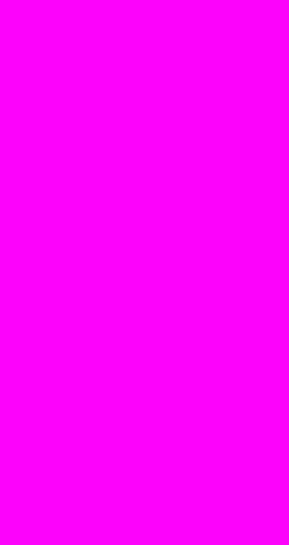
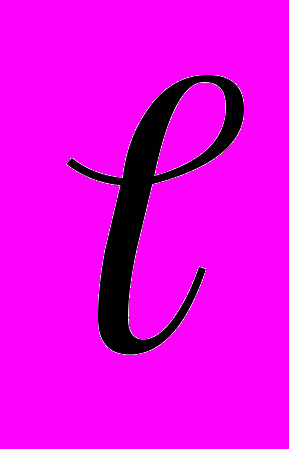
Контроль сферических поверхностей выполняется при помощи шаблонов, имеющих скошенный край. При контроле поверхности шаблона должен накладываться в плоскости дуги большого круга. Если между поверхностью детали и краем шаблона имеется просвет, то отступление радиуса шаблона может быть определено с точностью до малых второго порядка
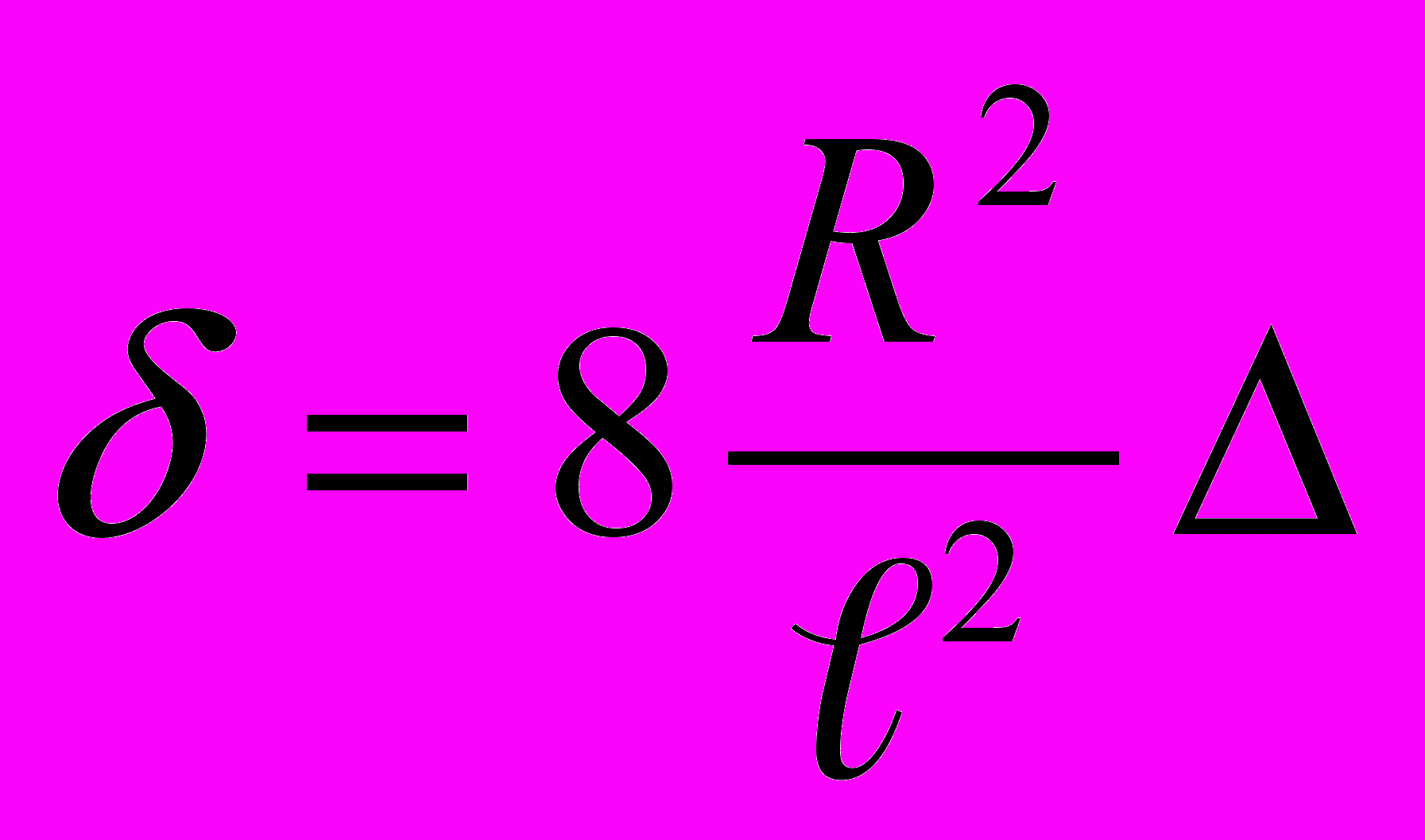
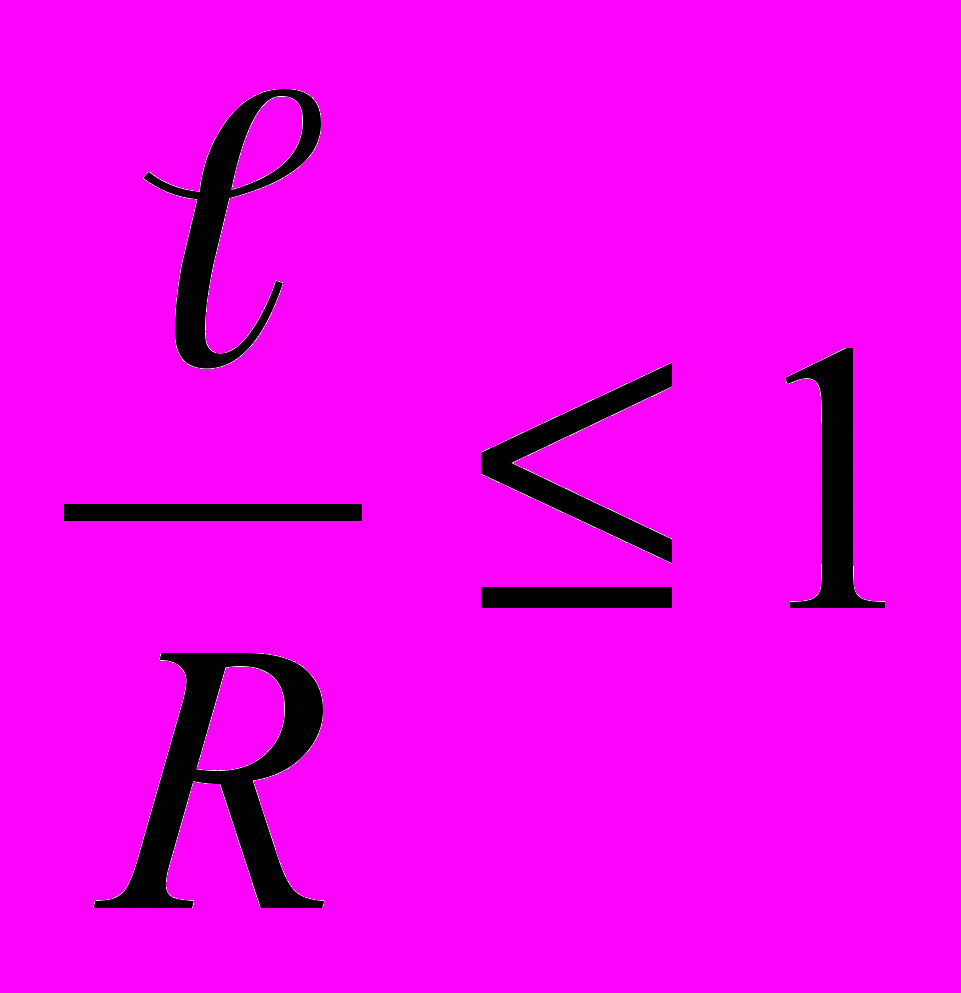
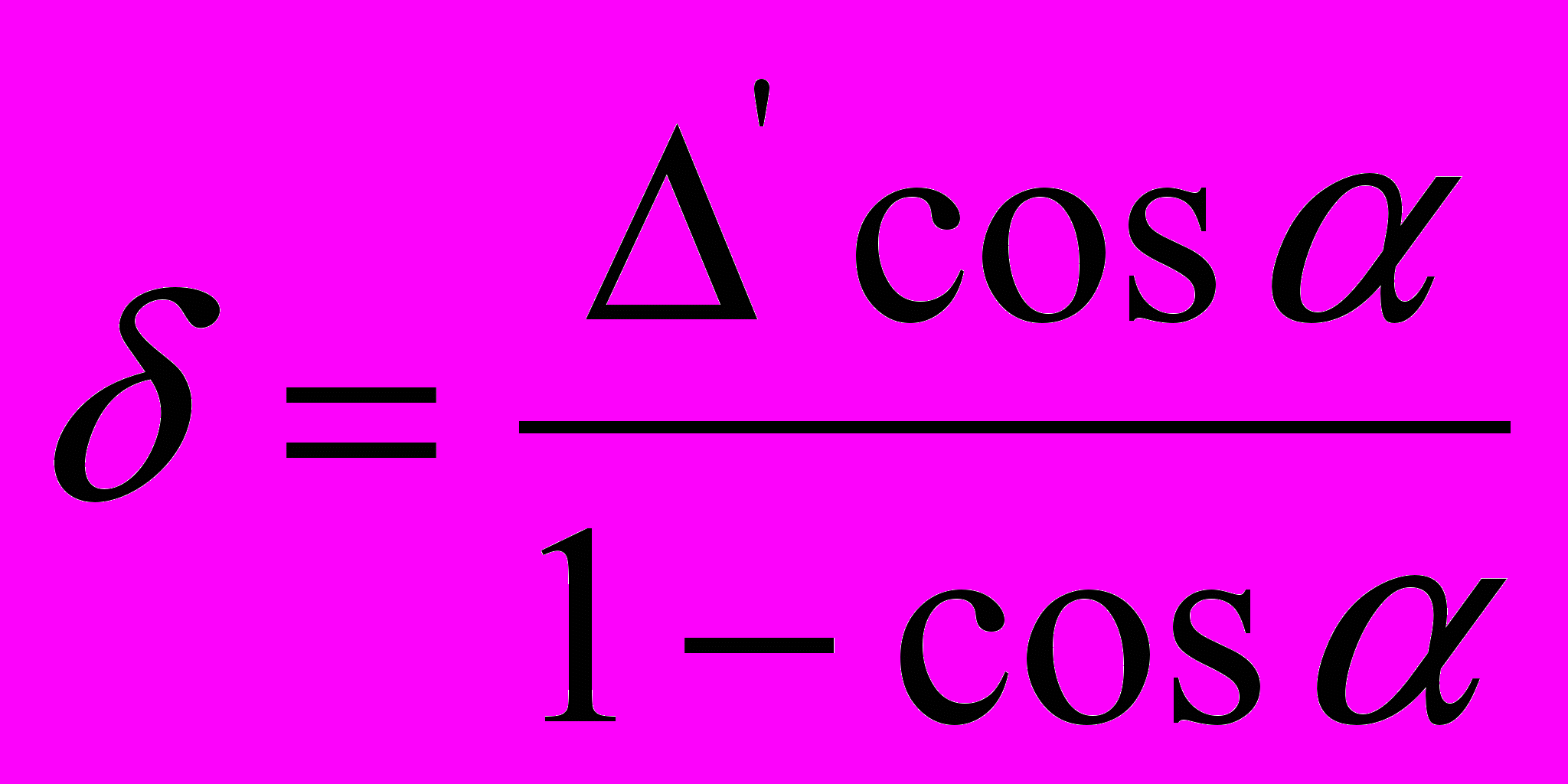
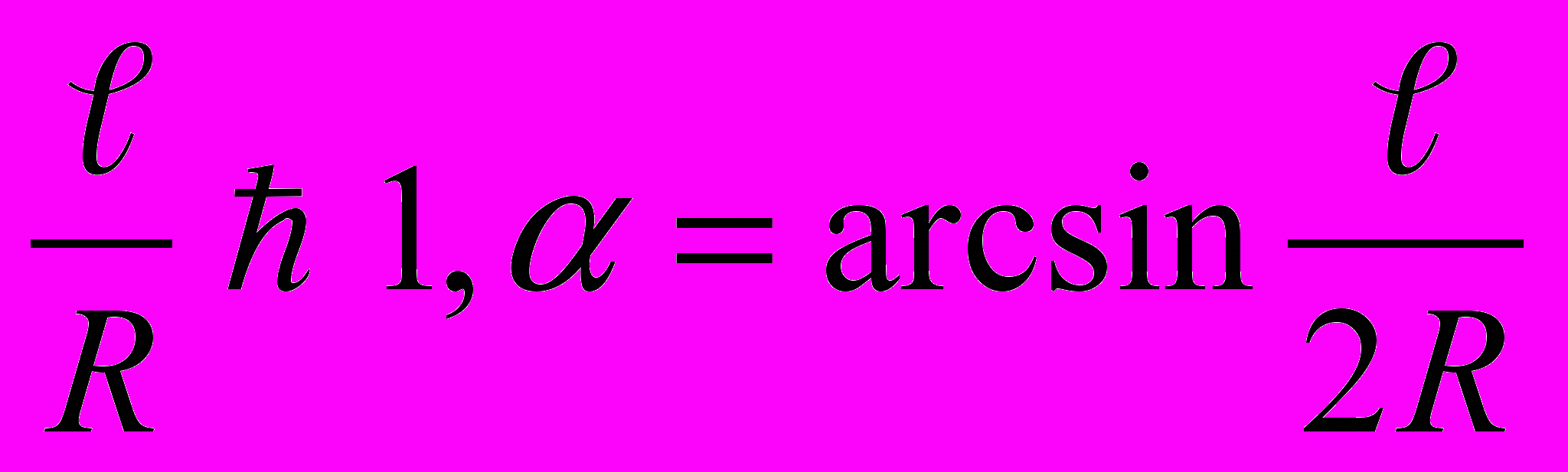
Радиусы контрольных грибов (или чашек) по своей величине соответствуют радиусам рабочих грибов и чашек, применяемых для последующей обработки.
Контроль кривизны поверхности шлифовальника пробным стеклом возможен только на последней стадии мелкой шлифовке. Отполировав слегка блок, накладывают пробное стекло на одну из крайних линз. Число интерференционных колец определяет величину отклонения поверхности блока от заданной, а, следовательно, и шлифовальника.
Чтобы избежать полировки, применяют метод растра, предложенный академиком В. П. Линником и разработанный А. Л. Курицким, для контроля кривизны шлифовальных металлических и стеклянных поверхностей.
Растр представляет собой систему прозрачных и непрозрачных штрихов, нанесенных на поверхность стекла путем резания, травления и фотографическим способом. Наиболее освоено изготовление плоского растра и растра, нанесенного на сферическую поверхность малой кривизны. Если наложить систему двух растров на контролируемую поверхность и освещать растр под некоторым углом, то при определенном положении глаза будет наблюдаться муаровая картина. Появление муара объясняется следующим образом. При прохождении света через решетку каждого растра свет распределится в виде двух синусоид. При частичном перекрытии двух растров соответствующие синусоиды дадут результирующую кривую А распределения света с переменной интенсивностью. Кривая Б, огибающая результирующую кривую, будет являться графиком изменения этой интенсивности и представляет кривую света в муаровой картине. Расстояние
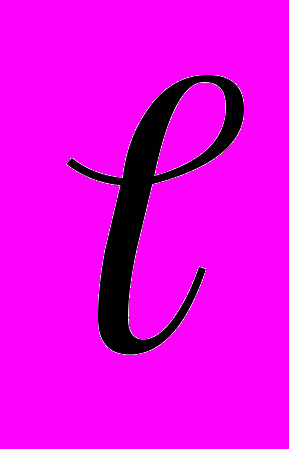
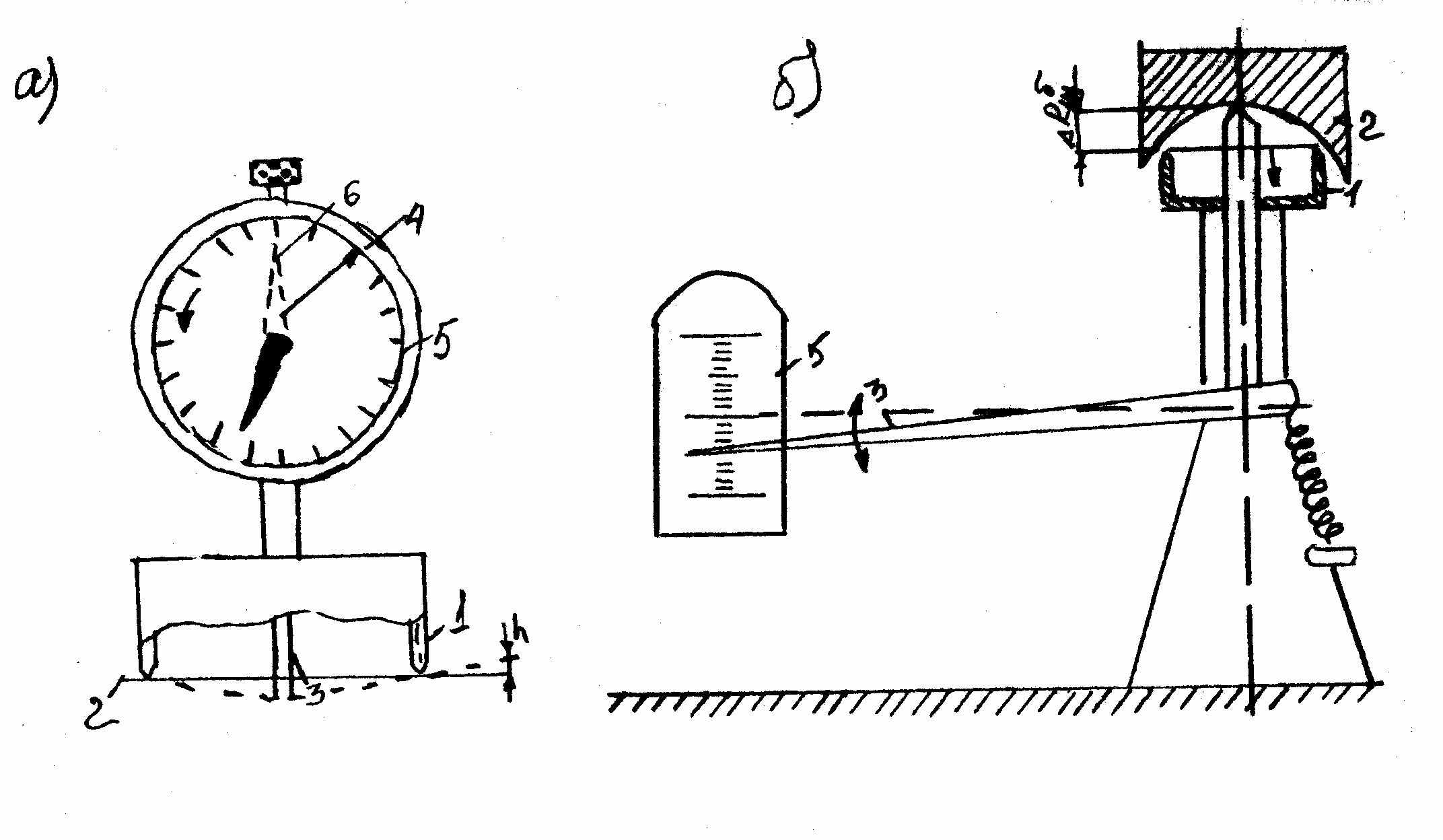
Рис. 2.Схемы индикаторных приборов для контроля кривизны поверхности шлифовальников.
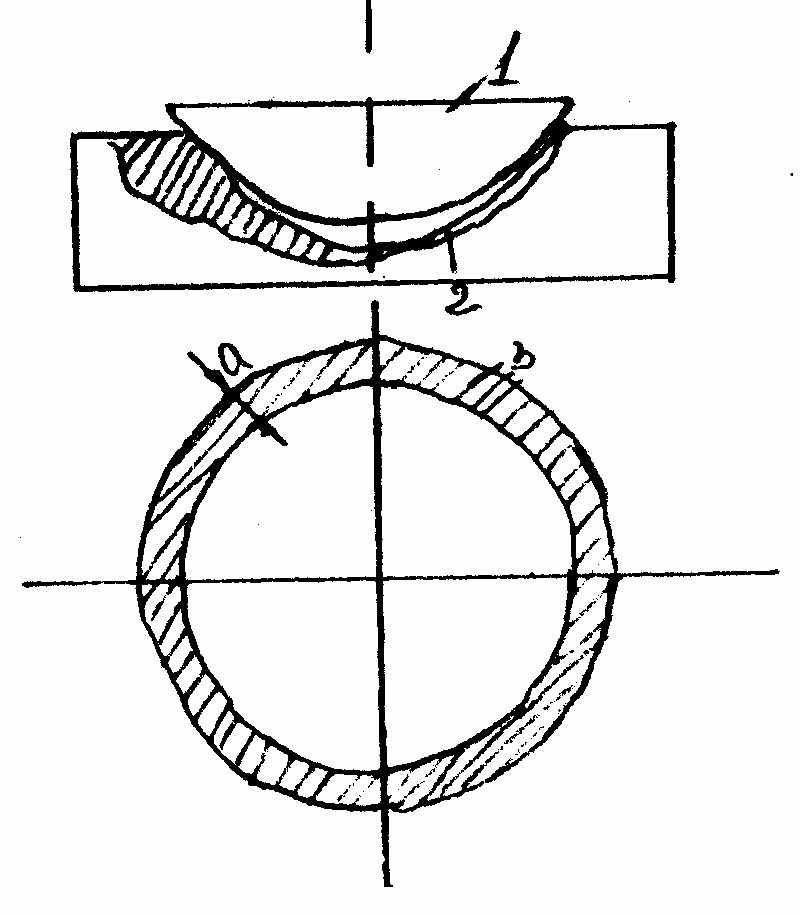
Рис. 3. Схема контроля кривизны поверхности шлифовальников притирочным инструментом
Рис. 4. Схема контроля кривизны шлифовальников при помощи растра
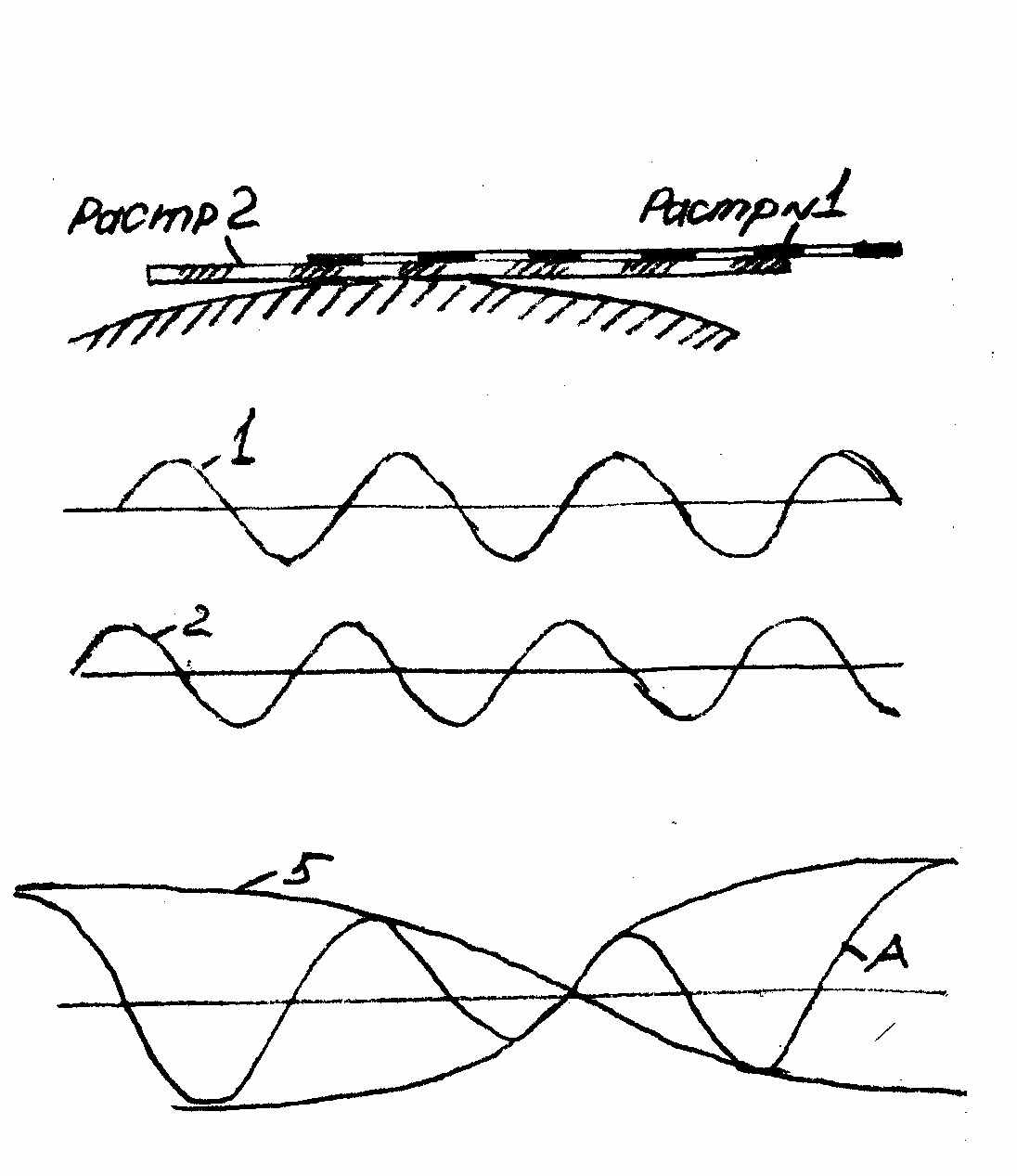
Контроль деталей при мелкой шлифовке.
Контроль линейных и угловых размеров выполняется на приборах, используемых и при грубой шлифовке, но обеспечивающих большую точность измерения, соответствующую данной стадии обработки.
Кривизна поверхности контролируется при помощи рычажного сферометра. Осязатель сферометра устанавливаются предварительно по соответствующей поверхности чашки или гриба; при совмещении шлифуемой поверхности с кольцом сферометра его стрелка показывает отклонение значения радиуса кривизны в долях стрелы прогиба. Широко применяется также контроль кривизны при помощи притирочного инструмента.
Контроль чистоты поверхности производится с помощью лупы шестикратного увеличения при ярком освещении поверхности. Источником света является мощная лампа. Для наилучшей концентрации светового потока применяются конденсаторы.
Качество шлифованной поверхности стекла характеризуется максимальной глубиной выколок (h) рельефного слоя. В цеховых условиях принят качественный метод контроля величины неровностей и равномерности их распространения на поверхности стекла. Контроль осуществляется осмотром хорошо освещенной поверхности через лупу с увеличением порядка 3 – 6. Такой метод контроля дает возможность легко и быстро выявить дефекты всей поверхности блока - царапины, выколки, точки и др., однако не позволяет изменить величину неровностей рельефного слоя.
Для оценки микрогеометрии поверхности деталей в экспериментальных целях можно пользоваться различными приборами: контактными, измеряющими глубину рельефного слоя механической иглой и измеряющими микронеровности оптическими методами.
Из контактных приборов в оптическом производстве наиболее распространены профилографы. При контроле поверхностей с небольшой площадью, когда влияние температуры, механических деформаций можно не учитывать, точность измерения на профилографе такая же, как и при интерференционном методе. Обеспечивается точность порядка 0,6 мкм. Оптимальной формой рабочего конца иглы является шаровой
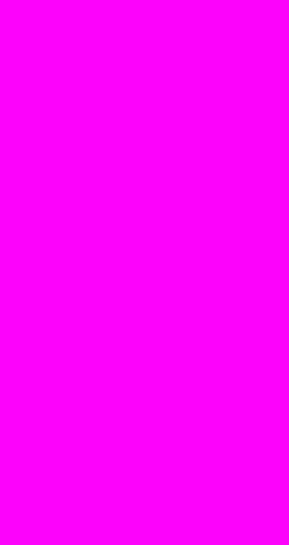
Рассмотрим профилограф Б. М. Левина (ИЗП – 5), рисунок 5 ИЗП -5 представляет собой оптический индикатор. При контроле микрогеометрии поверхности деталь 1 движется, соприкасаясь с неподвижной иглой 2 прибора. В зависимости от глубины рельефного слоя игла, закрепленная в чувствительном подвесе, начинает вертикально перемещаться, отклоняя зеркало 3 по отношению к неподвижному зеркалу 4. При повороте зеркала 3 лучи, идущие от источника света 5 через конденсатор 6, диафрагму 7 и объектив 8 – 9, отклоняются и, отразившись от зеркала 4, проходят через объективы 10 – 11 и систему зеркал 12 – 13. После этого лучи проходят цилиндрическую линзу 14 и падают на осциллографную бумагу на барабане 15, на которой образуется профилограмма 16 поверхности. Прибор позволяет контролировать качество поверхности с глубиной рельефного слоя от 0,06 до 260 мкм.
Измерение микронеровностей поверхности оптическим методом производится двойным микроскопом академика В. П. Линника (МИС – 11). Контролируемая глубина выколок от 0,8 до 62,5 мкм. Основными узлами прибора МИС – 11 (рис.6) являются два микроскопа: осветительный I и наблюдательный II, которые расположены под углом 90 градусов друг к другу. В точке пересечения осей микроскопов находится испытуемая поверхность ММ, закрепленная на предметном столике 1. Прямоугольная щель 2 микроскопа I, освещается источником света 3 при помощи конденсотора 4, проектируется объективом 5 на испытуемую поверхность. Наблюдательный микроскоп фокусируется так, чтобы изображение щели и испытуемой поверхности были в плоскости сетки 6. Неровности испытуемой поверхности деформируют изображение щели в плоскости сетки, представляя профиль поверхности как бы в разрезе.

Рис. 5. Схема установки профилографа ИЗП – 5.
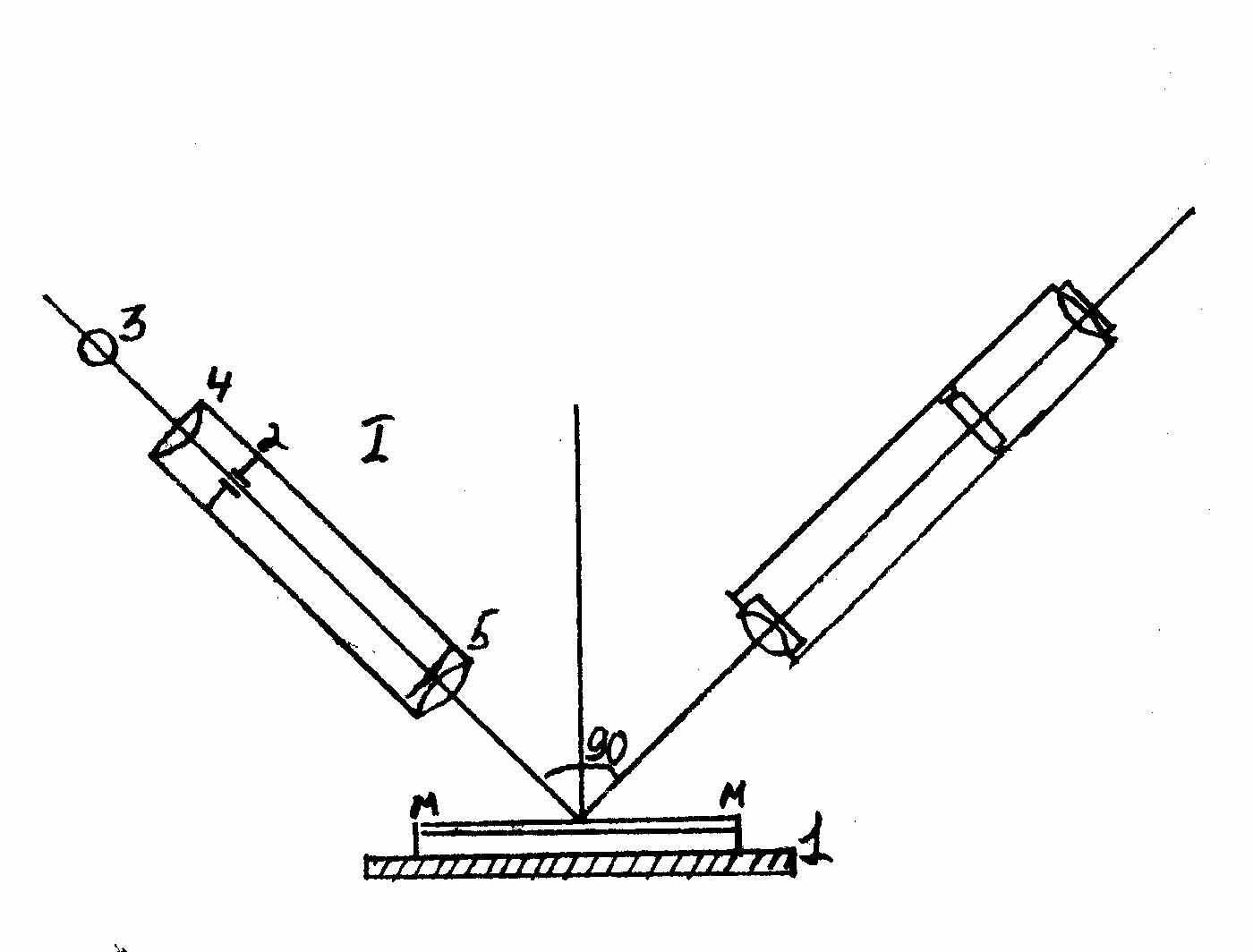
Рис. 6. Схема установки прибора МИС – 11.
Контроль качества поверхности пробным стеклом.
Этот метод применяется для оценки общих и местных ошибок поверхности, начиная от 0,01 до 2,5 – 3,0 мкм. Ошибки поверхности от 0,3 полосы и выше проверяются в белом свете. При контроле с большой точностью следует применять монохроматический источник света (ртутные дуги λ= 0.546 мкм). Контроль ведется в диффузноотраженном свете. Наблюдение следует вести по нормали к поверхности.
На рисунке 7 показаны интерференционные картины при типовых ошибках поверхностей.
При «бугре» (схема а) в зоне касания поверхностей видно пятно желто – соломенного цвета, окруженное широкими редкими кольцами.
При «яме» (схема б) в средней зоне зазора максимальной величины наблюдается темное пятно, а около краев располагаются узкие тонкие кольца. Если толщина возможного клина соответствует ошибке менее одного кольца или полосы, то характер неправильности поверхности проверяется притиранием пробно стекла к одному из краев детали. При «яме» будут иметь место полосы равной толщины, направленные выпуклостью к месту притирания (схема г), при «бугре» наоборот (схема д). Величина воздушного зазора определяется по кривизне полос (схема в). Проведя касательную прямую к вершине С кривизны любой полосы или через ее края, определяют отрелку h дуги в долях ширины
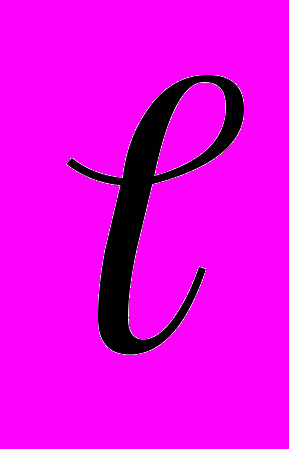
Если кривизна поверхности в двух взаимноперпендикулярных сечениях не одинакова
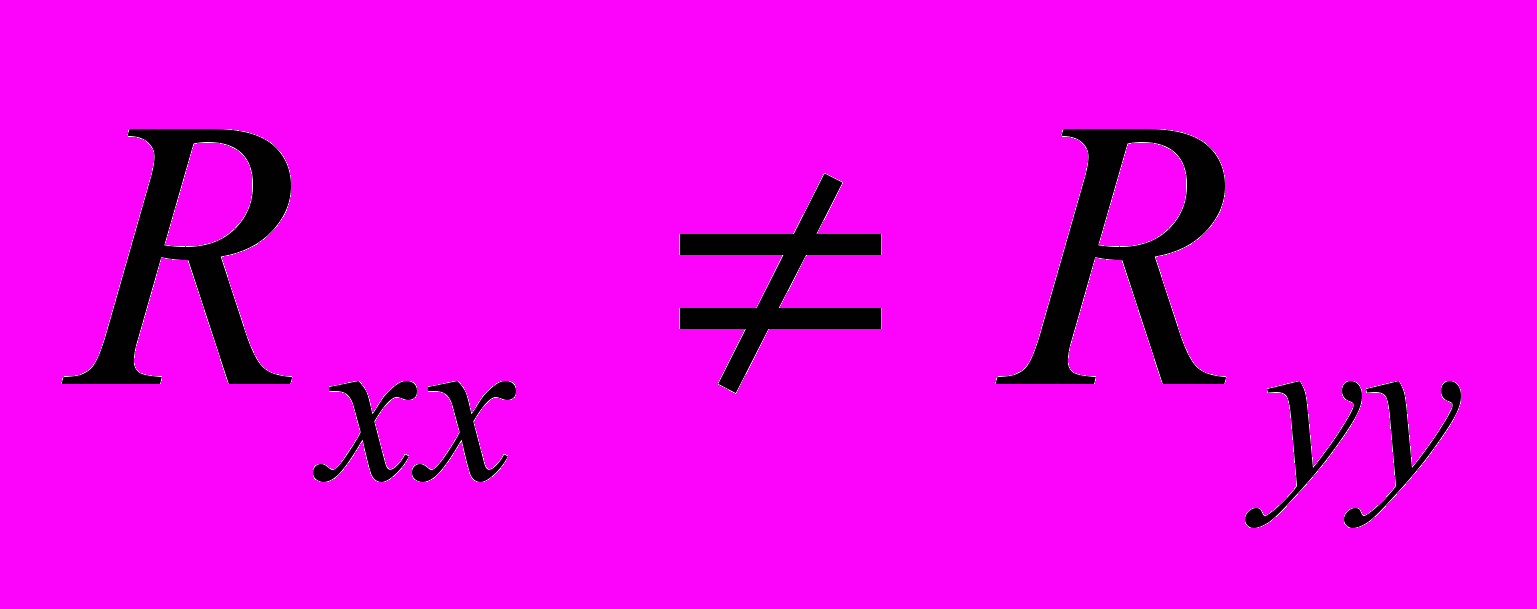
Материал для изготовления пробных стекол должен обладать максимальной устойчивостью пробных стекол должен обладать максимальной устойчивостью к истиранию и минимальным коэффициентом расширения.
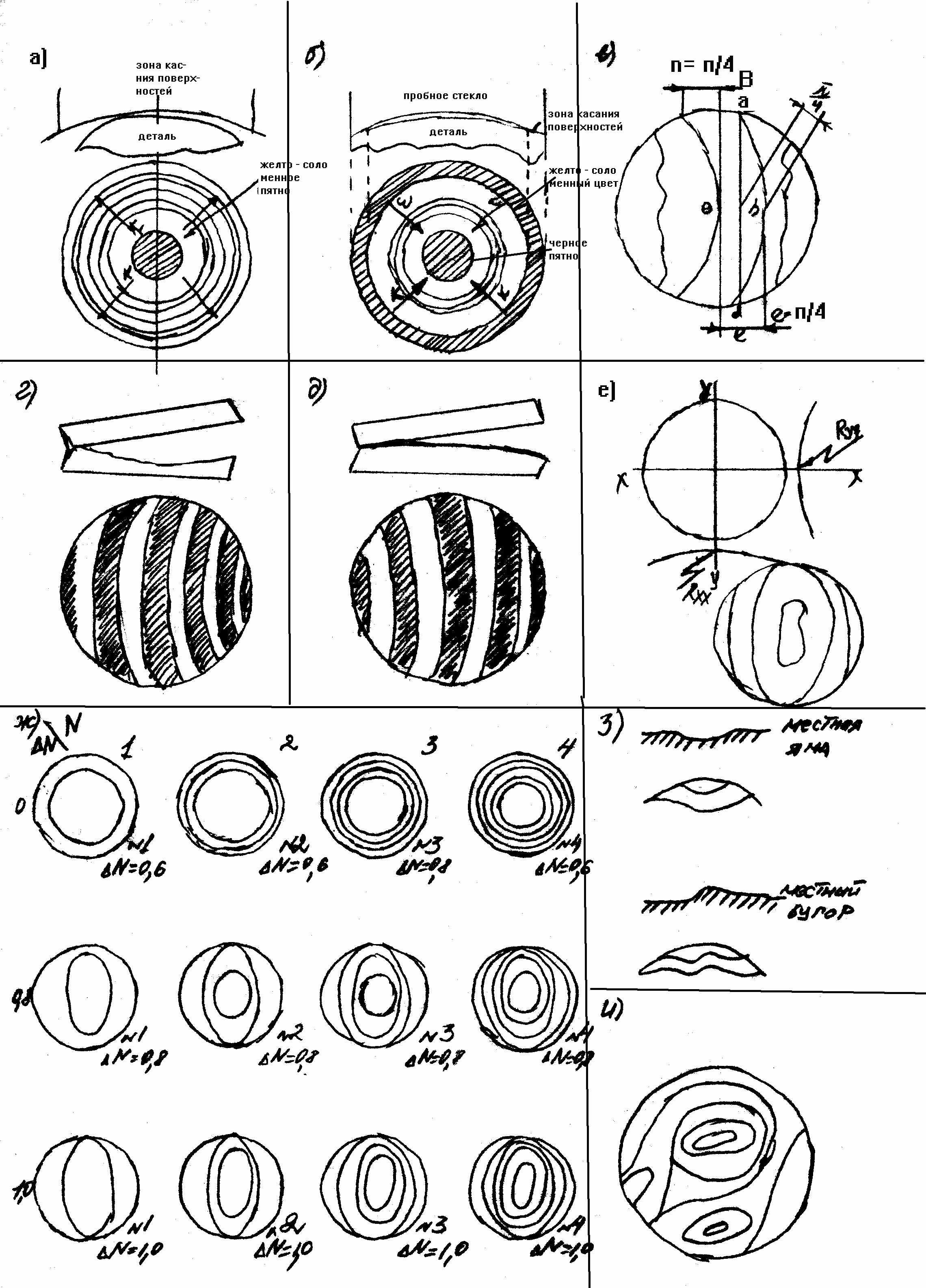
Рис. 7.Схемы интерференционной картины при контроле типовых ошибок обрабатываемых поверхностей.
Контроль деталей при полировке.
Контроль чистоты поверхности производится наблюдением в лупу с увеличением 6 – 8х при освещении поверхности «солнцем». Контроль кривизны поверхности и местных ошибок выполняются при помощи пробных стекол. Перед этим деталям необходимо дать остыть, чтобы исключить влияние температурных деформаций поверхности.
Также для контроля качества полированных поверхностей широко применяется цеховой инструмент (рис. 8). Основными узлами интерферометра является: осветительная система 1, наблюдательная труба 2, длиннофокусное вогнутое зеркало 3, разделительная призма 4, эталонная клиновидная пластина 5, подъемный столик 6. Интерферометр работает при монохроматическом освещении создаваемом лампой 7 и зеленым фильтром 8. Лучи света собираются и направляются конденсатором 9 на отражающую грань 10 разделяющей призмы, проходя через фокус Fз зеркала. Отразившись от зеркала, лучи пройдут параллельными пучками на поверхность 11 эталонной пластинки. Часть лучей преломится и пройдет через нее. Контролируемый плоский блок 12 устанавливается на столике 6 и поднимается вместе с ним так, чтобы между проверяемой плоскостью блока и плоскостью 13 эталонной пластинки был воздушный промежуток δ шириной 2 – 3 мм. Лучи, прошедшие через эталонную пластинку, попадут на поверхность блока, отразятся от него и вновь пройдут эталонную пластинку. После отражения лучей от зеркала они попадают на вторую грань разделяющей призмы и далее в наблюдательную трубку 2. Лучи, отраженные от плоскости 13 и поверхности блока 14, будут интерферировать вследствие разности хода, обусловленной зазором между плоскостями блока и пластины. Интерференционная картина, рассматриваемая посредством трубки 2, будет соответствовать профилю поверхности блока. Расшифровка интерференционной картины производится так же, как и при обычном контроле, пробными стеклами. Наклон плоскости 11 на угол
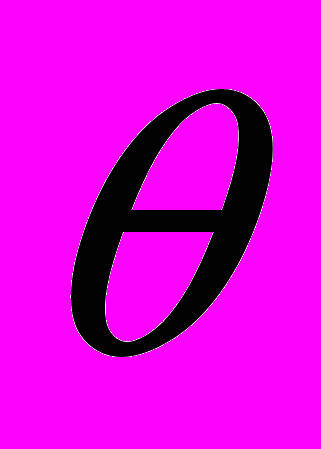
Контроль небольших углов клиньев и клиновидности полированных пластинок производится на автоколлимационных и интерференционных угломерах.
На рисунке 10 дана принципиальная схема автоколлимационного прибора для контроля клиновидности плоскопараллельных пластинок. В случае отсутствия клиновидности пластинки, установленной нормально к оси прибора, автоколлимационное изображение М’ марки М будет расположено на сетке прибора симметрично относительно его оси (а1 = а2 = а). Если пластинка представляет собой клин с углом θ, то, помимо яркого блика М’, будет наблюдаться М”, появляющийся в результате отражения лучей.
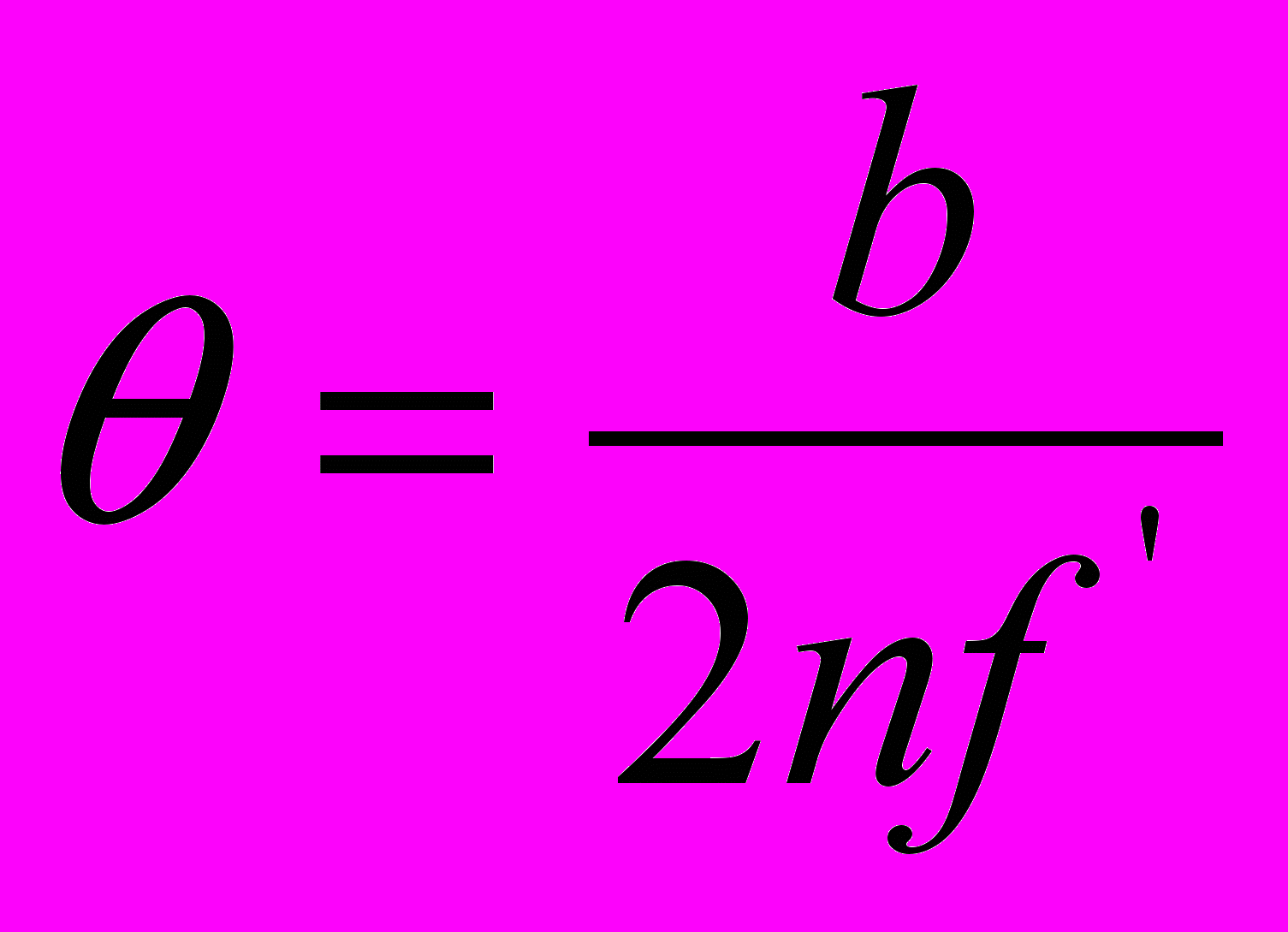
в – смещение М’ от М”, f’-фокусное расстояние объектива.
Измерять величину клина следует в главном сечении. Прибор определяет клиновидность с точностью до 2 – 5”.
Интерференционный угломер позволяет определять клиновидность с точностью до 0,02 мкм (рис. 9). Лучи, идущие от точечного источника света 1, направляются конденсором 2 через призму 3 и объектив 4 на контролируемую пластину 5. Лучи, отразившись от поверхностей пластинки, дадут интерференционную картину в фокальной плоскости объектива F’об. Разность хода лучей, отраженных от поверхностей пластинки, определяют по формуле:
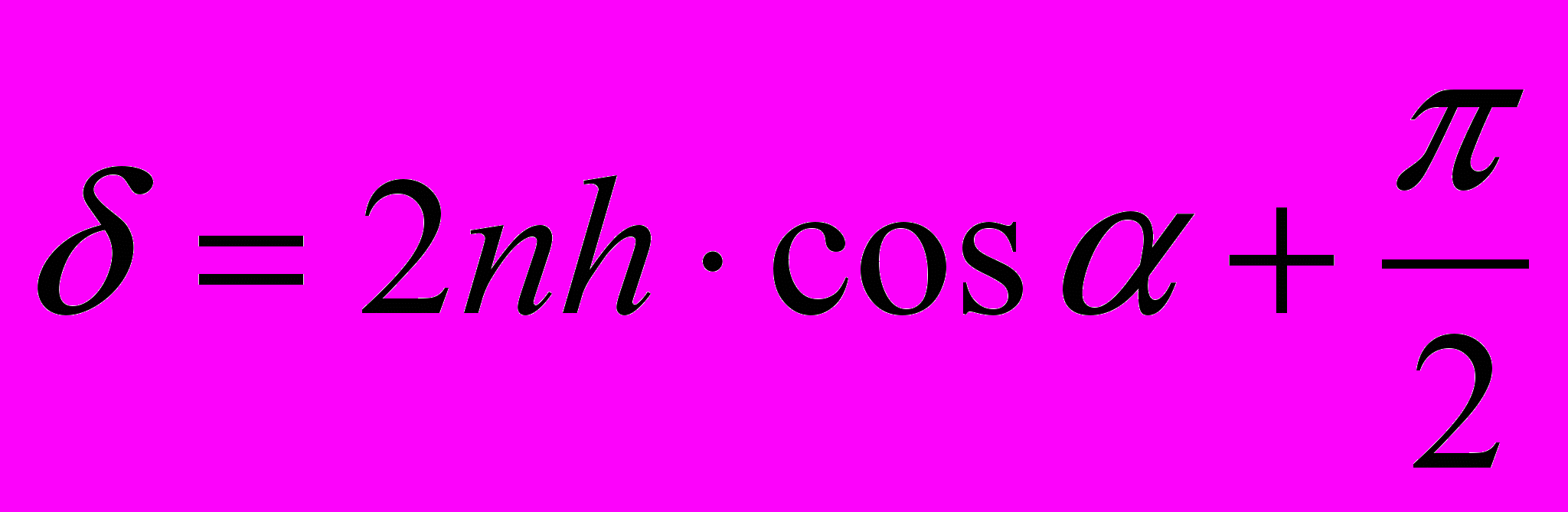
h – толщина пластины в наблюдаемом сечении;
n – показатель преломления пластинки;
α – угол падения луча на пластинку.
Если пластинка клиновидна, то перемещая ее по столику 6, установленному горизонтально, будет изменять величину h, следовательно, кольца, наблюдаемые в окуляр 7 трубки, будут смещаться. При смещении к тонкому концу пластинки кольца будут стягиваться к центру.
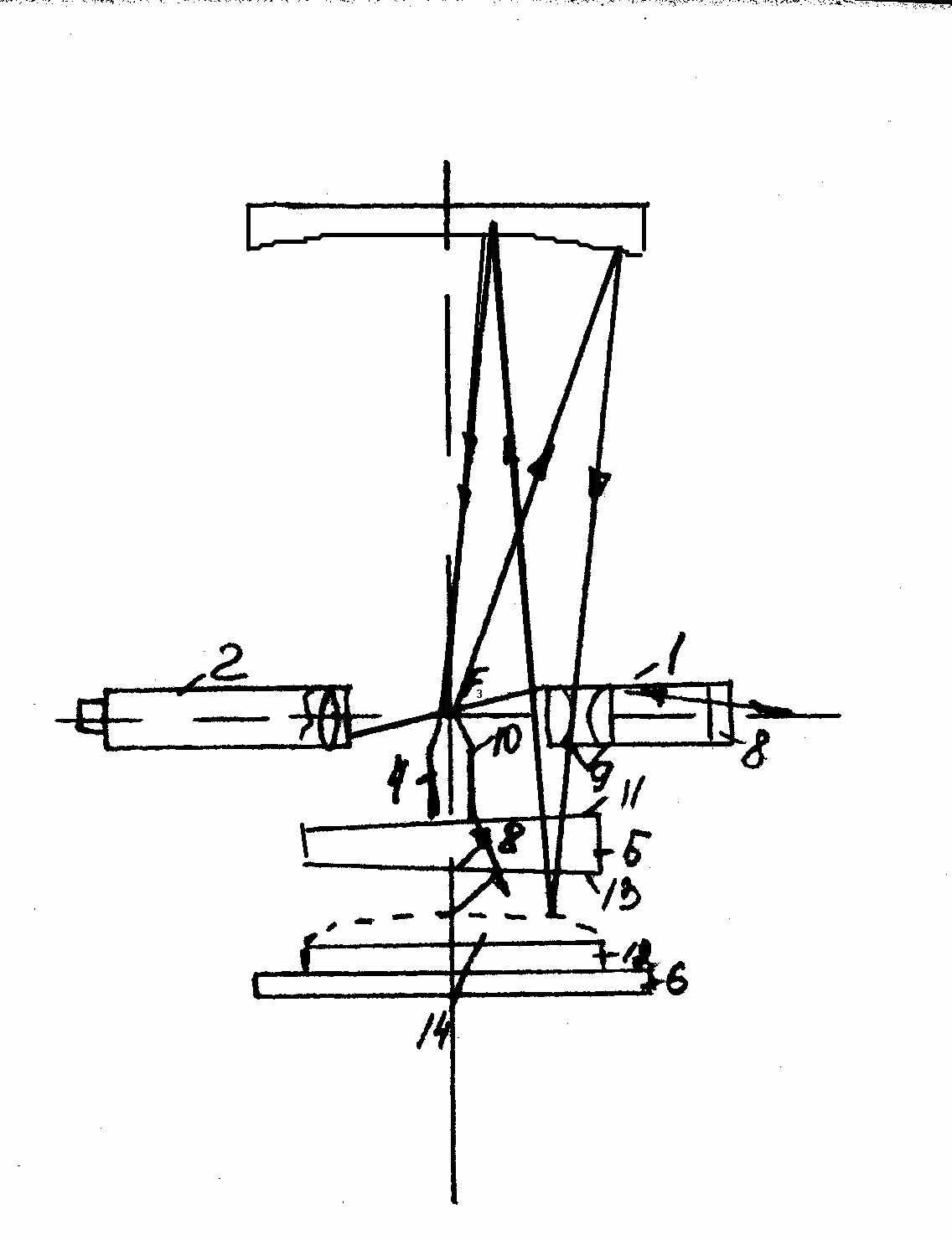
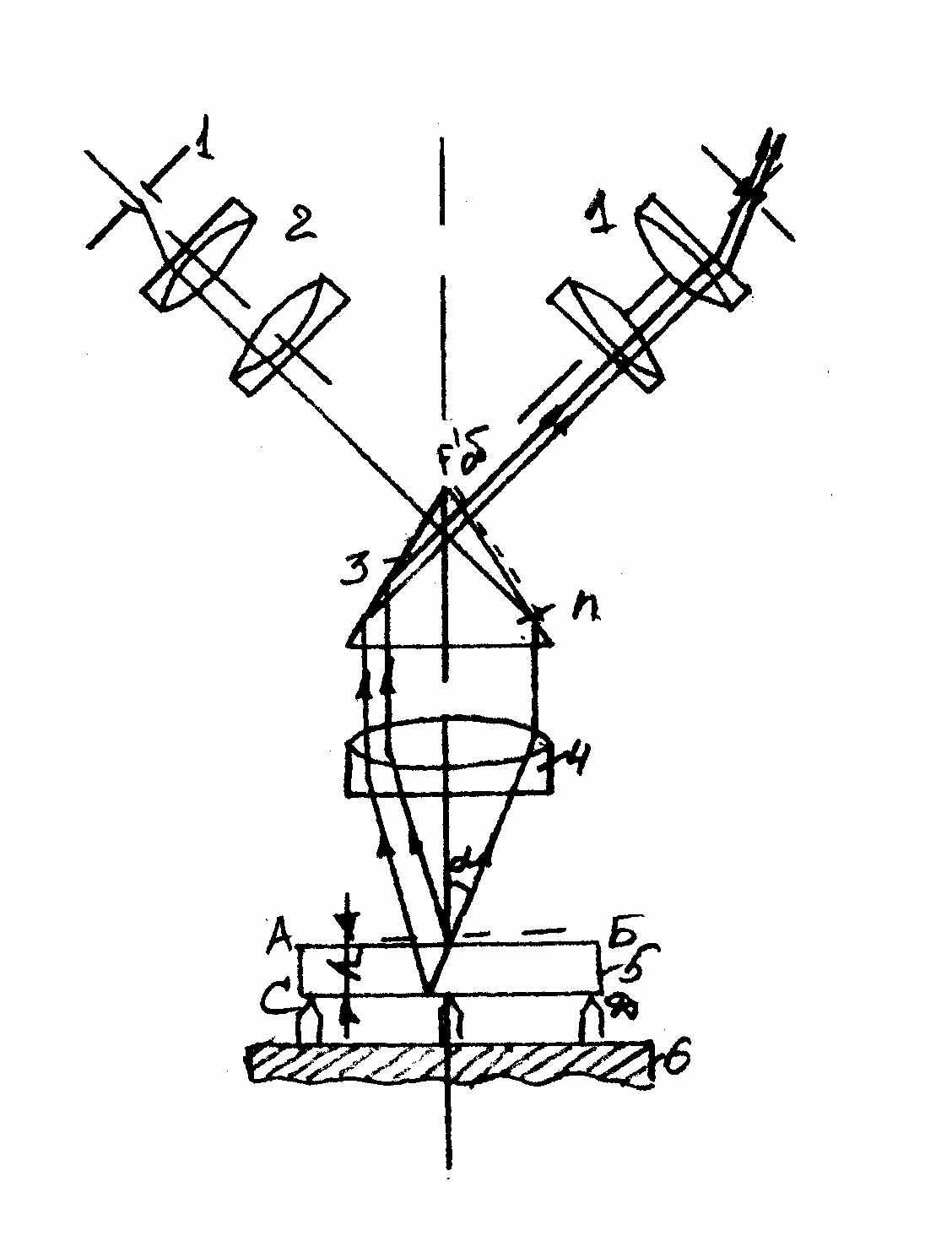
Рис. 8. Схема цехового интерферометра для контроля качества плоскостей.
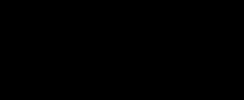
Рис. 9. Схема интерференционного угломера для контроля клиновидности плоскопараллельных пластин.
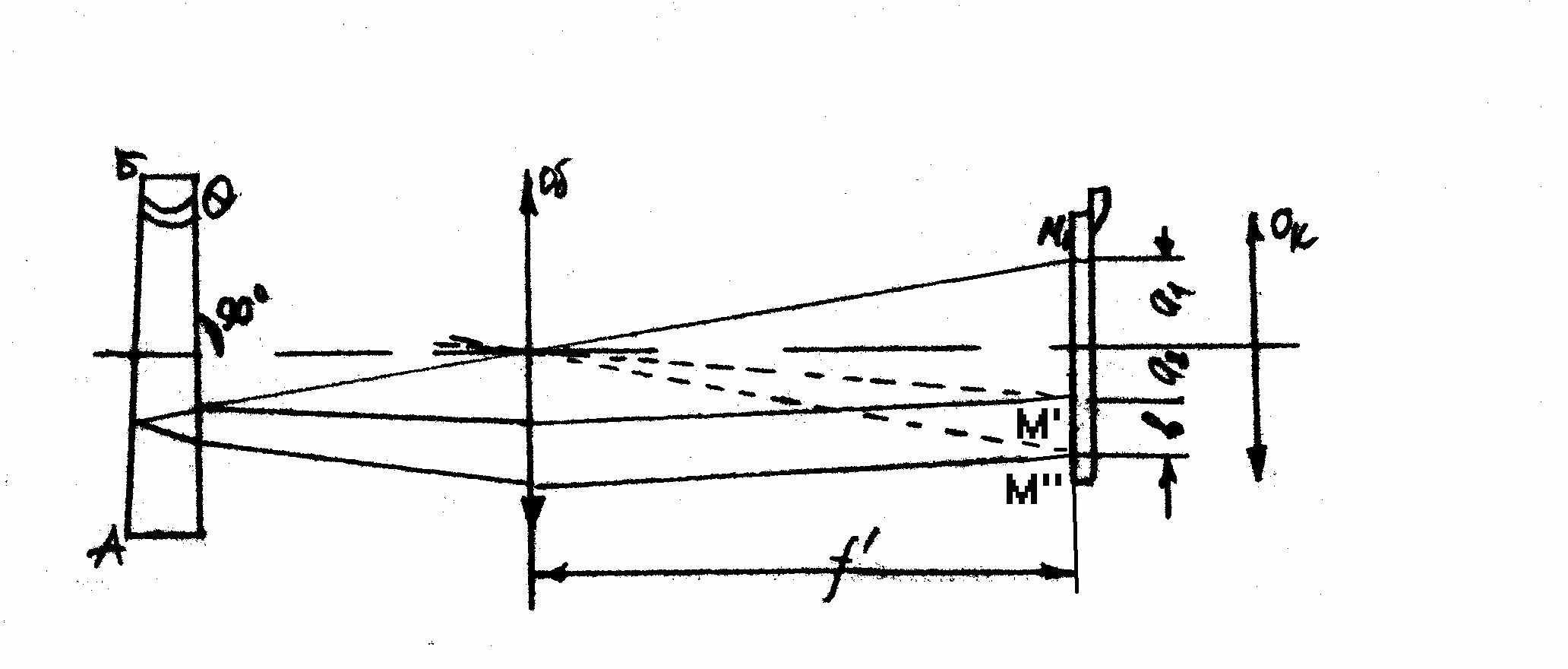
Рис. 10. Схема автоколлимационного прибора для контроля клиновидности пластинок.
Контроль центрировки линз.
На рисунке 11 представлена схема типового прибора для контроля центрировки линз. Контролируемая линза 1 помещается в оправку 2, ось которой совпадает с осью коллиматора 3. Оправка с испытуемой линзой момент перемещается в вертикальном направлении до совмещения заднего фокуса F’л линзы с сеткой 4 окуляра 5, вследствие чего образуется зрительная труба, объективом которой служит испытуемая линза. На сетке 6 коллиматора нанесено перекрестие, а на сетке 4 - допусковое поле шириной ∆ на центрировку или шкала. Величина децентровки линзы определяется по формуле:
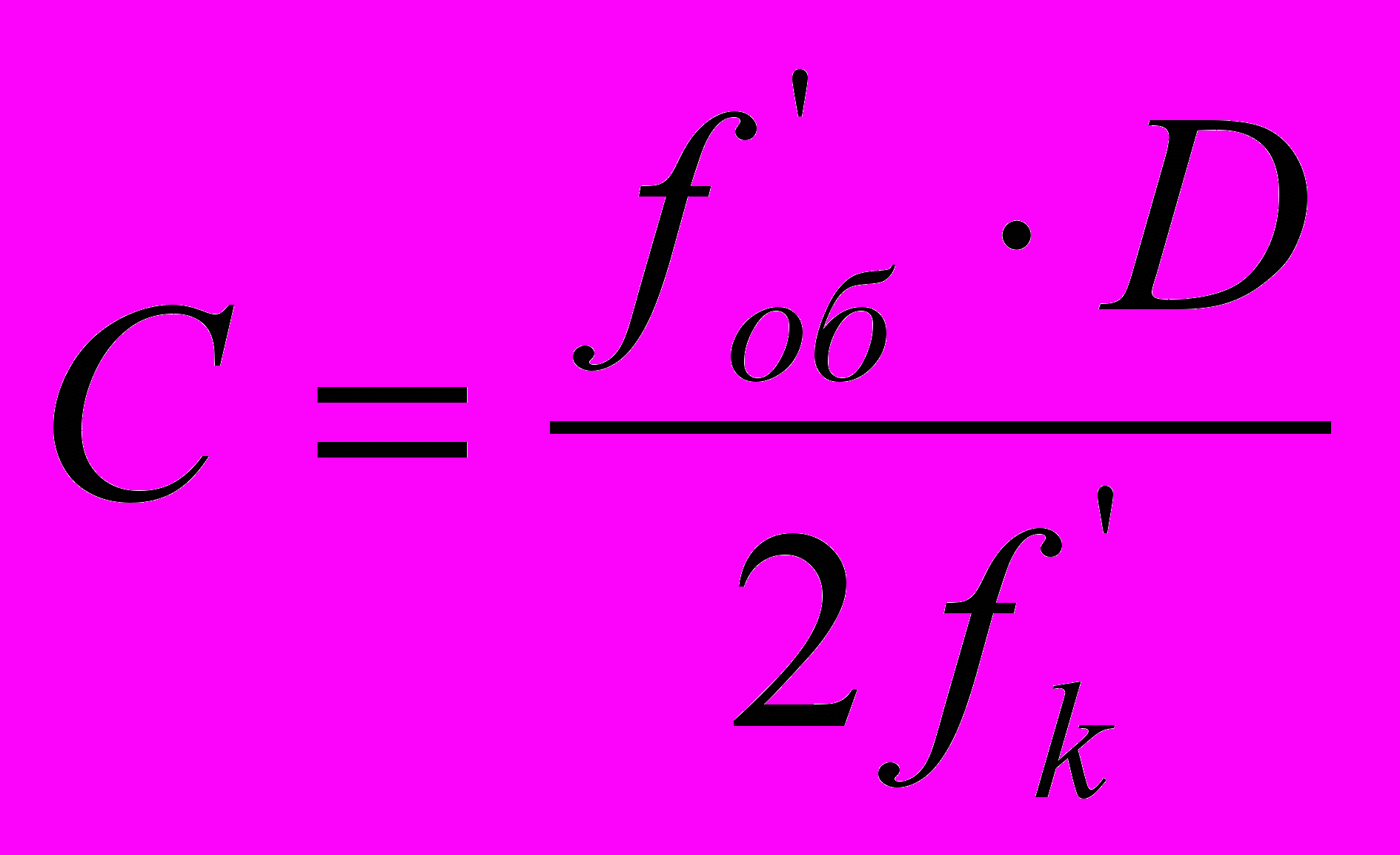
D – диаметр круга, описываемого центром изображения перекрестия сетки коллиматора;
f’об – фокусное расстояние объектива коллиматора;
f’л – фокусное расстояние контролируемой линзы.
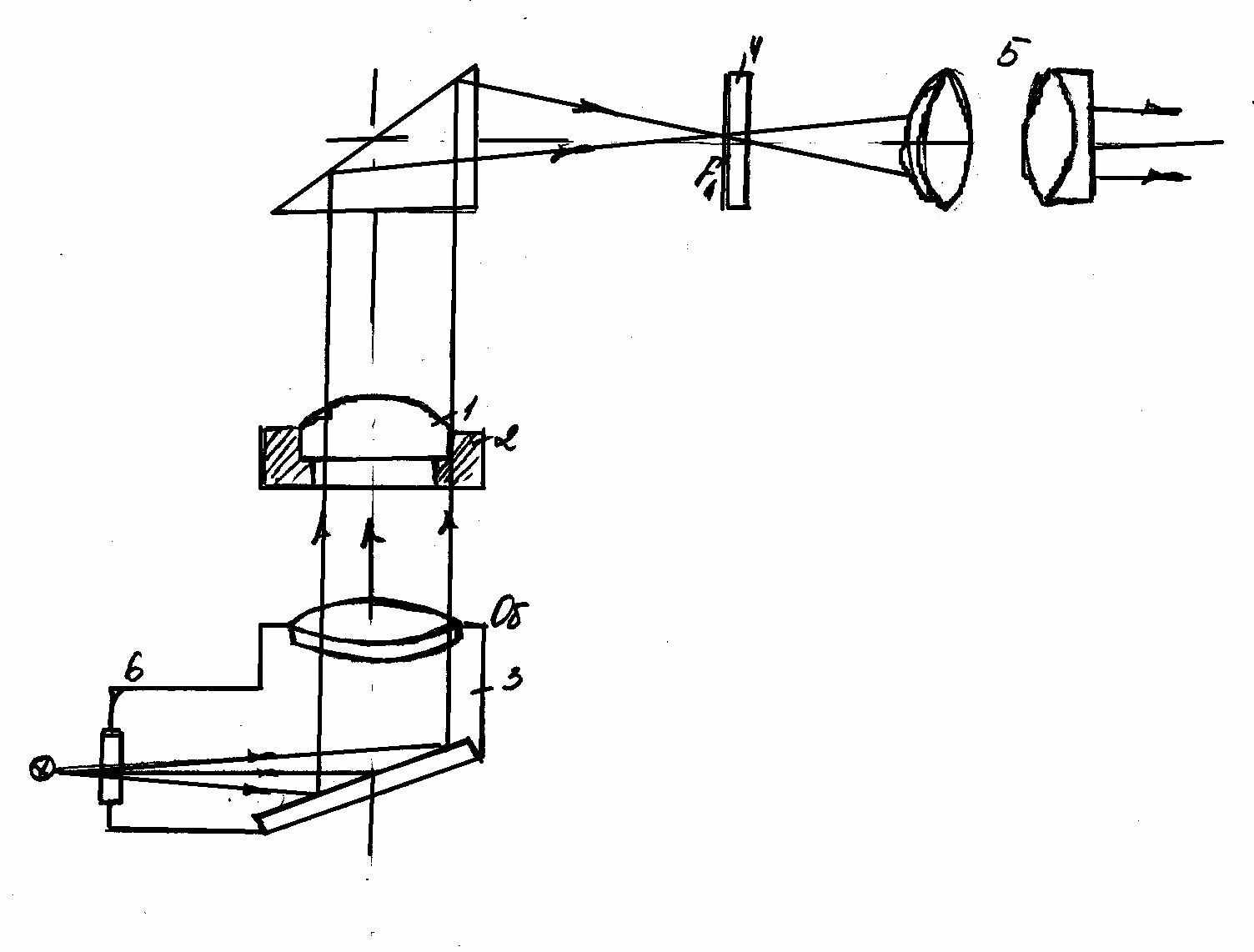
Контроль при переходе от грубой шлифовки к мелкой.
Для контроля плоскостей применяют стеклянные линейки, рабочие грани которых представляют собой точные отполированные плоскости.
Значительно более эффективны индикаторные приборы, измеряющие величину стрелы прогиба h поверхности с точностью до 1 -2 мкм. Перед контролем кольцо индикатора помещается на эталонную поверхность, причем осязатель индикатора устанавливает стрелку на нулевой отсчет шкалы. Далее кольцо перемещается по поверхности контролируемого шлифовальника и осязатель отклоняется на величину отступления поверхности от плоскости.
Контроль сферических поверхностей шлифовальников, рассчитанных по методу И. Е. Александрова, а также контроль поверхностей блоков весьма удобно вести при помощи рычажного сферометра, позволяющего определять непосредственно отступление ∆Rδ и ∆Rш., которые измеряются сравнительным методом: путем последовательной установки на кольцо прибора поверхностей эталона и контролируемой поверхности блока или шлифовальника. Отклонение стержня на поверхности осуществляется пружиной. Отсчет стержня ∆Rδ и ∆Rш производится рычагом по шкале, при наблюдении в шестикратную лупу. Точность измерения ∆Rш до 2мкм. При контроле блока следует проводить измерение в четырех зонах поверхности: одно измерение в центре и три – по краям. Определенное значение ∆R’ ш несколько отличается от фактического значения ∆Rш. величина ∆R’ш=∆RшК, где
К – коэффициент относительности (табличное значение). Контролируемые поверхности должны быть тщательно промыты и протерты от абразивных материалов и шлама.
Для качественного контроля кривизны шлифовальников применяют метод притирки. Сущность метода состоит в том, что поверхность шлифовальника должна притираться к поверхности контрольной чашечки в кольцевой зоне определенной ширины а. Так как обработка блока начинается с края, то и зона притертости должна быть с края инструмента.
8. Основные мероприятия по технике безопасности и охране труда. Вредность, связанная с условиями производства.
Наиболее специфическими требованиями техники безопасности в оптическом цехе являются требования при выполнении заготовительных работ и обработке деталей на станках, при работе с промывочными материалами, нагревательными устройствами, горючими и клеящими материалами.
Требования при обработке деталей.
Ручное резание стекла и обламывание разрезных пластин должны производится в защитных очках. Перед работой на станках необходимо завязать рукава спецовки и спрятать концы тесемок. Необходимо проверить исправность станка и его электрооборудования. Планшайбы, грибы и чашки не должны иметь острых краев и заусенцев. При обдирке небольших деталей на пальцы следует надевать «напальчники» во избежания травмы кожи. Недопустимо устанавливать или снимать приспособления и переключать скорость до останови шпинделя, проверять «биение» инструмента рукой. Подрезку шлифовальника следует производить только по направлению вращения шпинделя.
При центрировке линз и обработке стекла на круглошлифовальном станке необходимо проверить прочность абразивного круга и надежность его охлаждения. При центрировке следует проверять исправность центрировочного патрона, спиртовой лампы или газопровода; для предохранения глаз от попадания в них отработанных частей круга и воды необходимо применять защитные экраны. Фасетировка линз чашкой или грибом после центрировки разрешается только после остановки абразивного круга или фрезы. При пользовании газом или спиртовой лампой следует остерегаться воспламенения волос и одежды.
Требования к блокировке и разблокировке.
Необходимо проверить исправность нагревательных устройств и вытяжной вентиляции. Следует соблюдать осторожность при работе с горячей смолой. Пользоваться защитными очками при разблокировке ударами молотка.
Требования при промывке деталей.
Применяемые жидкости относятся к легко воспламеняющимся и быстро испаряющимся. Промывочные легко воспламеняющиеся жидкости (ЛВЖ) вредны для организма и весьма опасны в пожарном отношении. Пары бензина и эфира, взятые в определенном отношении в смеси с воздухом, могут взорваться от искры и открытого пламени.
К работам с ЛВЖ допускаются лица не моложе 18 лет, имеющие разрешение врача и прошедшие специальный инструктаж. Промывочные материалы необходимо хранить в герметичных сосудах; работа с ЛВЖ должна производиться при работающей вытяжной вентиляции. Промывка деталей производится в специальных бачках с крышками; наблюдение за ходом промывки следует вести через чистое наклонное стекло. Изъятие деталей из промывочного стола производится после испарения вредных паров. Загрязненные ЛВЖ сливаются в специальные герметизированные сосуды, а не в канализацию. Прием пищи, хранение продуктов и курение в промывочной мастерской не допускается.
Список литературы.
- Бардин А. Н. Технология оптического стекла. Государственное издательство литературы по строительным материалам, 1955.
- Халилов. Основы технологии оптического стекла. Промстройиздат, 1989.
- Русинов М. М. Техническая оптика. Машиностроение, 1979
- Зубаков В. Г. И др.Технология оптических деталей. Машиностроение, 1985.
- Фатыхова Р. К. Контроль оптико – механических приборов. Машиностроение, 1988.
Оглавление.
- История завода и перспективы развития
- Ассортимент Выпускаемой продукции
- Основные заказчики и потребители
- Оптическое стекло
- Основные оптические свойства стекла
- Классификация стекол
- Примерные составы различных марок оптических стекол
- Влияние состава стекла на его оптические свойства
- Основные оптические свойства стекла
- Варка оптического стекла
- Характеристики и устройство горшковых печей, электрических тигельных ВЧ или ванной печи сопротивления
- Устройство и типы мешалок системы подачи топлива
- Огнеупоры, применяемые для изготовления печи, футировка печей
- Основы технологии варки и выработки стекла, режимы варок различных оптических стекол
- производство заготовок в виде «плиток» и «прессовок»
- Отжиг стекла. Режимы отжига
- Характеристики и устройство горшковых печей, электрических тигельных ВЧ или ванной печи сопротивления
- Технологическая схема цеха
- типы оптических деталей
- Производство заготовок для получения оптических деталей
- Виды обработки стекла
- Основные типы инструментов
- Общие сведения о технологии обдирки и грубой шлифовки
- Абразивные материалы
- Классификация абразивов по зернистости
- Обработка линз
- Обработка призм
- Общие сведения о технологии обдирки и грубой шлифовки
- Мастерская шлифовки и полировки
- типы оптических деталей
6.5.1. Технология мелкой шлифовки и полировки
6.5.2. Мелкое шлифование
6.5.3. Полированный инструмент
6.6 Центрировка линз
6.7 Фасетировка линз
6.8 Основные типы инструментов для обработки стекла.
7. Системы и методы контроля
8. Техника безопасности
Список литературы
Оглавление