Отчет по производственной практике на уомз в цехе №315
Вид материала | Отчет |
- Отчет по производственной практике место прохождения практики, 9.49kb.
- Методические рекомендации по проведению и защите производственной практики, 942.15kb.
- Рабочая программа и методические указания по второй производственной практике для студентов, 304.42kb.
- Отчет о производственной практике по хирургической стоматологии Студента 4 курса стоматологического, 27.36kb.
- Отчет по производственной практике Место прохождения практики: зао «УралСтройЭкспо», 384.14kb.
- Программа и методические указания по учебно-производственной промыслово-геологической, 281.58kb.
- Отчет о производственной практике в 2010 году, 133.51kb.
- Отчёт о преддипломной практике Вотделе опеки и попечительства администрации Кимовского, 184.56kb.
- Методическое руководство и дневник по летней производственной практике для студентов, 458.11kb.
- Рабочая программа по производственной практике, преддипломной практике (наименование, 162.05kb.
Классификация цветного ОС
Цветное ОС применяют для изготовления светофильтров, пропускающих определенную длину волны. Цветные стекла выпускаются 15 типов, каждый из которых содержит несколько марок. УФС – темное ультрафиолетовое, ФС – фиолетовое, СС – синее, СЗС – сине-зеленое, ЗС – зеленое, ЖЗС – желто-зеленое, ЖС – желтое, ОС – оранжевое, КС – красное, ИКС – инфракрасное темное, ПС – пурпурное, НС – нейтральное, ТС – темное, МС – молочное, БС – бесцветное ультрафиолетовое, бесцветное инфракрасное. Требуемая окраска светофильтра достигается в шихту с добавлением соответствующих красителей и режимом термической обработки. Каждая марка цветного стекла характеризуется спектральным пропусканием. По характеру отклонения фактического пропускания от номинальной для различных марок цветного стекла. Установлены две или три категории. Химическая устойчивость цветных стекол, как правило, значительно ниже устойчивости бесцветного ОС.
5. Варка оптического стекла.
5.1 Характеристики и устройство горшковых печей,
электрических – тигельных высококачественных или ванной печи сопротивления.
Требованиям производства оптического стекла лучше всего удовлетворяют горшковые печи. Первые варки оптического стекла проводились в небольших тиглях. Однако вскоре тигель был заменен горшком. Попытки варить оптическое стекло в больших ванных печах потерпели неудачу, так как невозможно обеспечить высокую однородность.
Отличительными способностями горшковых печей являются:
- Возможность достижения достаточно высоких температур, необходимых для протекания реакций стеклообразования и гомогенизации стекломассы (1400-1500ºС).
- Окислительный характер пламени, исключающий восстановление некоторых металлических окислов, входящих в состав стекла, до металлов (н. Pb O).
- Возможность легко регулировать температуру с достаточно большой точностью (10-15ºС).
Оптическое стекло варят в одно- и двух горшковых печах периодического действия, пламенных. Обогреваются они генераторным газом или нефтью. Варка стекла проводится при температурах 1400 - 1500º. Достижение таких температур в пламенных печах стало возможным благодаря применению нагревательных устройств, использующих тепло отходящих из печи газов для подогрева поступающих в печь наружного воздуха и газа. Применение таких устройств позволило значительно повысить температуру горения топлива, увеличить производительность печи и уменьшить расход топлива. Теплоиспользующие агрегаты, предназначенные для стекловаренных печей, разделяют на рекуперативные и регенеративные.
Рекуператоры представляют собой металлические или керамические теплообменники, в которых тепло отходящих газов, движущихся по каналам рекуператора, передается через стенки каналов воздуху, движущемуся на встречу по другой системе каналов.
Регенератор – это решетчатая кладка из шамотного кирпича, которая периодически то нагревается выходящими из печи газами, то охлаждается поступающими через нее в печь газом и воздухом, На рис. 1 представлена схема одногоршковой нефтяной капельниковой регенеративной печи системы профессора Ф.Е.Грум – Гржимайло.
Горшок 1 устанавливается на колосники 2 в рабочей камере 3. Подача воздуха и движение газов в печи происходит следующим образом. При движении сначала через предварительно нагретый клапан 5 , куда при помощи форсунок 6 подается мелкими каплями нефть. Образующиеся в кармане продукты горения омывают горшок, и нагрев его, уходят через каналы 7 левого регенератора, обогревая его. При обратном ходе воздух подается в левый регенератор, а нефть поступает через форсунки 8.
Продолжительность подачи воздуха и газа, дымовых газов 20-30 мин. Отходящие газы при поступлении в генератор нагреты до 1250 - 1350º, что позволяет довести температуру воздуха и газа, идущих в печь, до 900 - 950º. В печах необходимая для варки температура поддерживается автоматически. Контроль температуры осуществляется при помощи термопары 9.
Оптическое стекло варят в открытых горшках круглого сечения. Емкость горшков изменяется в пределах от 170 до 500 литров, а вес выплавляемого стекла от 2 т для ТФ до 0,5 т для кронов. Материал горшка имеет огромное значение для процесса варки стекла и должен отвечать следующим требованиям:
- огнеупорность не менее 1600º;
- высокая стойкость к воздействию расплавленной стекломассы;
- способность хорошо выдерживать резкие изменения температуры;
- достаточная механическая прочность.
Химическая устойчивость материала к действию шихты и стекломассы очень важна, так как при разъедании материала горшка будет ухудшаться качество стекла за счет изменения его химического состава и образования дефектов – свилей, камней и др. Наиболее подходящим материалом является огнеупорная глина. Она обладает высокой пластичностью и содержит минимальное количество Fe2 O3 (0.7-1.2%) во избежание окрашивания стекла. Так как глина при обжиге дает значительную усадку, которая может привести к деформациям и разрыву изделия, то в массу добавляют шамот, предварительно обожженную при 1200º глину.
Формуются горшки 3 способами: пластическим формованием, литьем и трамбованием. При пластическом формовании массу составляют из 50-60% шамота и 50-40% глины, тщательно перемешивают и затворяют водой. Горшок формуют при помощи пресса. При изготовлении горшков литьем шамотную массу разжижают до текучего состояния и заполняют ей толстостенную гипсовую форму с таким же сердечником. При изготовлении горшков путем трамбовки массы значительно ускоряется сушка горшка, уменьшается его пористость и повышается механическая прочность. Масса для трамбования содержит большое количество шамота (85%) и 5-9% воды.
Сушку горшков производят в течение месяца двумя методами: температурного градиента или электротермическим. В первом случае горшок нагревается изнутри, и влага выходит наружу. При втором - стенки горшка прогреваются переменным током.
Обжигают горшки в два приема. Вначале в специальных печах – каленицах (4 – 5 суток) или электропечах (2 суток) путем постепенного повышения температуры до 900-1000º. Особенно осторожно следует вести нагрев при 100º, когда используется вода, и при 500-700º, когда разрушается каолинит – основная составная часть глины. Второй этап заключается в окончательном обжиге горшка при температуре 1450º непосредственно в стекловаренной печи.
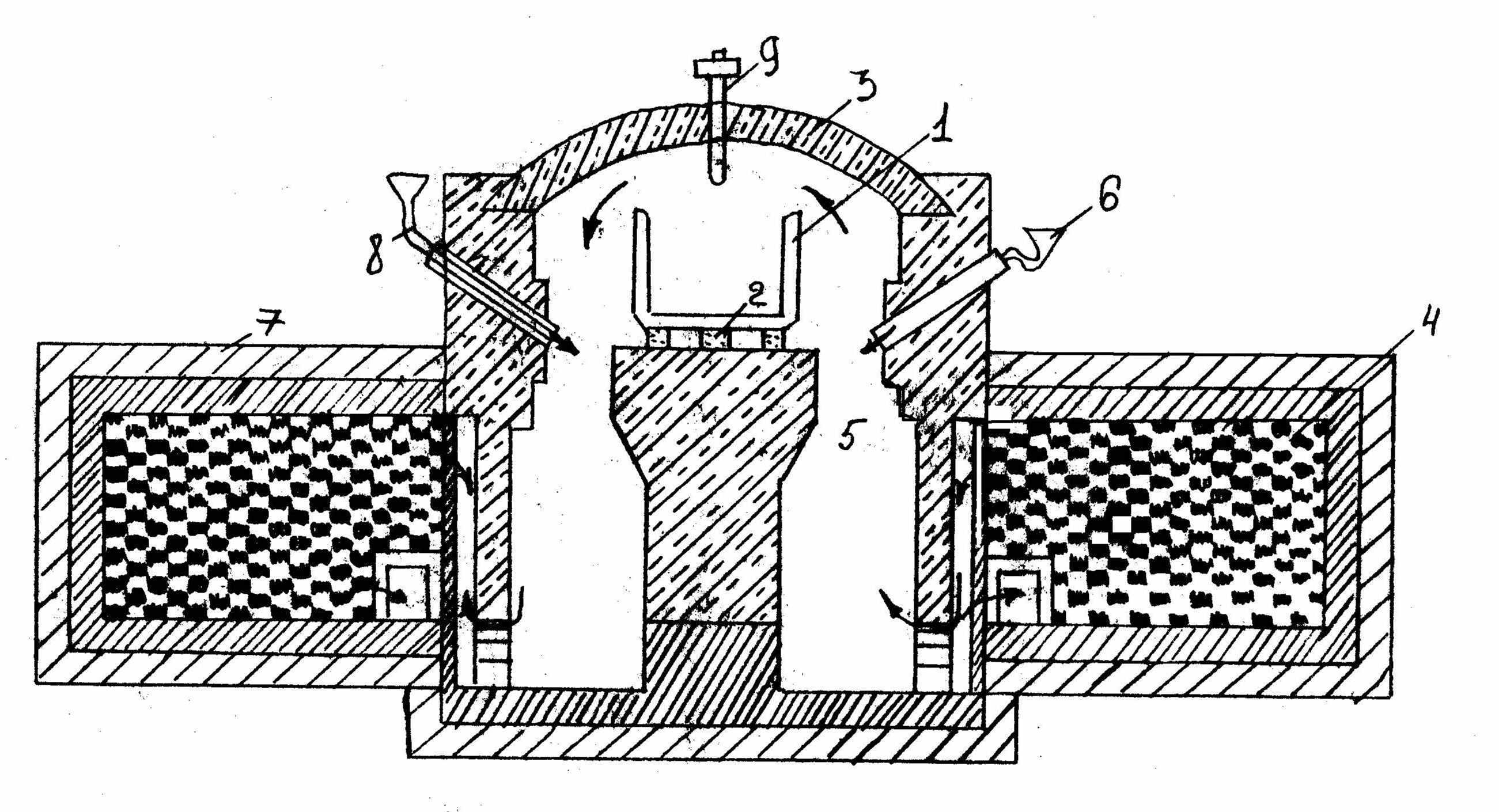
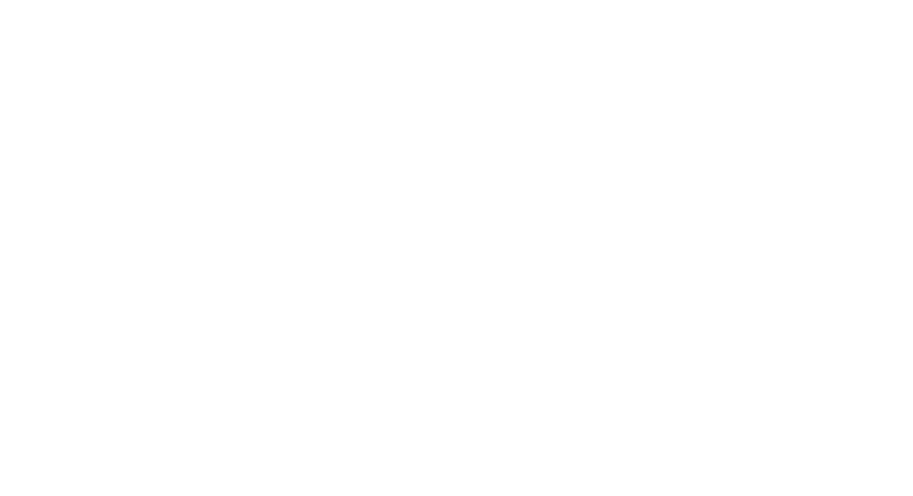
рис. 1. Схема нефтяной капельниковой регенеративной печи системы профессора В. Е. Гоум – Гржимайло.
5.4 Основы технологии варки и выработки стекла, режимы варок различных оптических стекол.
Варка стекла.
Обожженный горшок перед засыпкой в него шихты проходит специальную подготовку – выводку. Обожженный и нагретый до Т=900-1000º горшок при помощи мостового крана или специальной тележки подводится к стекловаренной печи и ставится в ее рабочую камеру. После установки горшка в стекловаренную печь дверь печи опускается и замазывается шамотной массой в местах ее соприкосновения со стенкой. Температура печи поддерживается на уровне 900-1000º. Затем начинается «выводка» горшка – постепенный, но быстрый его разогрев до 1350-1400º. Это необходимо для уплотнения материала горшка и образования спекшегося плотного черепка, устойчивого к действию шихты.
После этого в горшок загружают стеклобой, а затем шихту. Так как объем шихты в 2-3 раза больше объема выплавляемого стекла, то обычно шихта засыпается 3-мя или 4-мя порциями через 1,5-2 часа. Шихта, находящаяся в горшке, нагревается неравномерно. Наиболее интенсивно происходит нагрев ее со стороны, непосредственно сообщающейся с горячими газами рабочей камеры печи, поэтому шихта начинает плавиться сверху и постепенно стекает вниз горшка, частично проникая в спекшуюся массу. Вначале плавятся более легкоплавкие компоненты и различные эвтектические смеси. Верхние слои шихты при этом обедняются плавнями, и всплывают на поверхность расплава, медленно растворяются в нем. Так как температура в различных слоях оказывается неравномерной из-за низкой теплопроводности порошкообразных материалов шихты, то и ход реакции во всей массе происходит неравномерно: на поверхности скорее, чем в центре.
Осветление и гомогенизация (процесс выравнивания стекломасс) производятся в зависимости от марки стекла при различных температурах. Размешивание стекломассы осуществляется лопастной мешалкой, помещаемой в центре горшка. Наиболее интенсивно стекломасса перемешивается при высоких температурах. Студка стекломассы осуществляется в 2 этапа: внутри печи и вне ее. Студку внутри печи начинают, когда в пробах почти полностью исчезли пузыри.
Режим варки.
Основными параметрами режима варки являются: емкость горшка, время его выводки, количество засыпок шихты и их частота, температура провара и осветления стекломассы, скорость вращения мешалки, частота бурления, длительность отдельных этапов варки, температура вывода горшка и длительность студки.
Указанные параметры изменяются в зависимости от заданной марки стекла. Кривая температурного режима варки и температурный максимум устанавливаются в зависимости от состава стекла, его легкоплавкости и способности реагировать с материалом стекловаренного горшка. Для большинства стекол процесс варки длится от 25 до 35 часов, продолжительность этапа засыпки колеблется от3,5 до 10 часов. Быстрее всего варятся флинты и тяжелые флинты (приблизительно 25-30 часов), медленнее – тяжелые баритовые кроны (40-50 часов).
Выработка стекла.
В результате выработки вязкая стекломасса переходит в твердое состояние и превращается в стекло. Существуют следующие способы выработки стекла: прессование, прокатка, отливание, выдувание и вытягивание.
Разделка оптического стекла осуществляется в основном тремя способами:
- охлаждением стекла непосредственно в стекловаренном горшке, с последующей разбивкой на куски;
- прокаткой вязкой стекломассы на чугунном столе с помощью металлического вала в листы заданной толщины;
- отливкой стекла из горшка в форму, где она охлаждается в виде массивного тела – блока.
Выработка стекла прокаткой : стекло выливается на массивный чугунный стол и прокатывается тяжелым чугунным валом, охлаждаемым водой.
“ – ” поверхность прокатного листа морщинится.
“ + ” возможно использование горшков для нескольких варок.
Отливка стекла в форму: после охлаждения стекла стекломасса выливается в форму.
“ – ” заготовка имеет приливы;
неудобно отливать детали маленьких размеров.
“ + ” поверхности отливок довольно чистые и прозрачные.
Охлаждение стекломассы в стекловаренном горшке: горшок со стеклом охлаждают до температуры воздуха мастерской, тепловую изоляцию удаляют и горшок со стеклом разбивают тяжелым стальным ломом или молотком.
“ – ” необходимо соблюдать температурный режим при охлаждении;
разбивается горшок;
очень много непригодного к дальнейшей обработке стеклобоя.
Производство заготовок в виде «плиток» и «прессовок».
Процесс получения заготовок заключается в распиливании смоллированных полуфабрикатов на куски определенных размеров, обдирке и в окончательном контроле стекла для выявления его дефектов.
Моллирование – процесс превращения бесформенных кусков стекла, полученных после разбивки горшка, в куски определенной геометрической формы путем размягчения стекла нагреванием.
Значительная часть отходов стекла, образующихся при распиловке, вновь направляется на прессование плюшек. Обдирка кусков стекла производится для подгонки их размеров к требуемым. После этого противоположные стороны куска слегка полируются для окончательного выявления внутренних дефектов стекла. Линейные размеры заготовок могут отклоняться от номинала на 1,5-2,0 мм в зависимости от веса. Годные заготовки подвергают отжигу.
Прессование – один из видов принудительного прессования вязкой стекломассы и обеспечивает получение заготовок оптических деталей различной формы как для линз, так и для призм с небольшими припусками на механическую обработку.
“ + ” - ускоряет, упрощает и удешевляет процесс обработки оптических
деталей;
- качество стекла выше;
- возможность использовать обрезки стекла;
- можно получить заготовки любой формы.
Формующими элементами при прессовании являются матрица и пуансон. Матрица служит приемником для стекла, неподвижна. Пуансон – движущаяся часть; он давит на стекломассу и заставляет ее заполнять пространство между ним и матрицей. Чтобы избежать прилипания стекла, рабочую поверхность матрицы посыпают тонким слоем измельченного песка.
Операции при прессовании: получение заготовок для контроля дефектов стекла, подготовка заготовок к прессованию, нагрев заготовок, процесс прессования, отжиг прессовок.
5.6 Отжиг стекла. Режимы отжига
Отжигом называется термическая обработка стекла для уменьшения его внутренних напряжений.
Сущность процесса: возникшие при быстром охлаждении внутренние напряжения могут исчезнуть или уменьшиться в том случае, если стекло вновь нагреть так, что частицы его стали подвижны и деформированные слои образца смогли бы принять исходное состояние, до действия сил, вызвавших напряжения. Напряжения исчезают тем быстрее, чем меньше вязкость стекла. При вязкости η = 1*1013 - 2,5*1013 пуаз напряжения почти полностью исчезают – соответствующая Т – температура отжига.
Процесс отжига разделяется на несколько этапов:
I этап: стекло нагревается или охлаждается до Тотж (А=530˚)
II этап: стекло выдерживают при верхней температуре отжига, которая обычно на 5 – 10˚ ниже температуры Тg, до выравнивания Т во всех слоях образца.
III этап: интервал отжига, стекло охлаждается до нижней температуры отжига, которая на 50-60˚ ниже верхней Тотж и соответствует вязкости в 1015 пуаз. Ниже этой температуры остаточные напряжения не возникают. Образец надо охлаждать медленно, чтобы в нем не появились новые напряжения. Скорость охлаждения тем меньше, чем толще образец.
IV этап: стекло достаточно быстро охлаждается.
Температурный режим отжига зависит от состава стекла и толщины изделий. Стекло крон, толщина до 4 см.
- Нагрев до 500˚ со υ = 80˚ в час.
- Выдерживание при 500˚ в течение 15 часов.
- Охлаждение до 400˚ со υ = 7˚ в час.
- Охлаждение со скоростью υ = 40˚.
Для большинства стекол напряжения исчезают в интервале от 670˚ до 370˚
Оптические стекла отжигают в специальных печах периодического или непрерывного действия.
При отжиге в периодической печи изделия укладывают на шамотные плиты, затем печь разогревают и через некоторое время замазывают. После этого печь охлаждается естественным путем.
Печи непрерывного действия имеют форму туннеля, в различных участках которого поддерживается различная температура в соответствии с установленным режимом отжига. Заготовки непрерывно загружаются на вагонетки и движутся по туннелю, проходя последовательно все этапы отжига.
Тонкий отжиг оптического стекла требует правильного распределения температур и строгого выдерживания определенного режима. Эти условия трудно осуществить в туннельных печах, Поэтому в настоящее время оптическое стекло отжигают в печах периодического действия.
Наилучшие результаты могут быть получены при отжиге в электрических печах. Основным видом брака при отжиге является оптическая неоднородность стекла.
Т
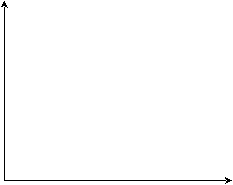
600 II
5
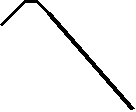
400
300
200 IV
400 t, мин
0 10 20 30 40 50 60
6. Технологическая схема цеха
6.1. Типы оптических деталей.
К оптическим деталям относят: линзы, растры, призмы, зеркала и пластины.
Линзы. Линзой называется оптическая деталь, ограниченная 2-мя преломляющими поверхностями и боковой цилиндрической поверхностью.
Преломляющие поверхности могут быть сферическими (выпуклыми и вогнутыми), параболическими, торическими, и цилиндрическими.
Линзы в оптических приборах служат для создания изображения с нужным увеличением или для создания заданной освещенности оптической системой.
Растры. Растрами называют оптические детали, состоящие из большого числа линзовых или зеркальных элементов малых размеров и имеющие оптическую силу. Простейшей растровой системой является линза Френеля, состоящая из кольцевых преломляющих участков.
Призмы. Призмой называют оптическую деталь, ограниченную плоскими преломляющими и отражающими поверхностями, образующими двугранные углы. Они служат для разложения белого света в спектр.
Зеркала. Зеркалом называют оптическую деталь, ограниченную одной отражающей поверхностью. Применяются для зеркального отражения предмета и фокусировки лучей.
Пластины. Пластиной называют деталь, ограниченную двумя параллельными преломляющими поверхностями. Могут служить защитными стеклами, светофильтрами и сетками.
6.2. Производство заготовок для получения оптических деталей.