Отчет по производственной практике на уомз в цехе №315
Вид материала | Отчет |
- Отчет по производственной практике место прохождения практики, 9.49kb.
- Методические рекомендации по проведению и защите производственной практики, 942.15kb.
- Рабочая программа и методические указания по второй производственной практике для студентов, 304.42kb.
- Отчет о производственной практике по хирургической стоматологии Студента 4 курса стоматологического, 27.36kb.
- Отчет по производственной практике Место прохождения практики: зао «УралСтройЭкспо», 384.14kb.
- Программа и методические указания по учебно-производственной промыслово-геологической, 281.58kb.
- Отчет о производственной практике в 2010 году, 133.51kb.
- Отчёт о преддипломной практике Вотделе опеки и попечительства администрации Кимовского, 184.56kb.
- Методическое руководство и дневник по летней производственной практике для студентов, 458.11kb.
- Рабочая программа по производственной практике, преддипломной практике (наименование, 162.05kb.
Распиливание производят для разделения бесформенных кусков сырьевого материала на части. Выбор того или иного метода разделки заготовки определяется в основном ее толщиной, формой и точностью размеров получаемых кусков.
Перед началом распиливания куска или плитки выполняют разметку восковым или графитным карандашом.
Листовое стекло толщиной до 20 мм режут резцами или рамками. Операция резанья состоит в образовании трещины и раскалывании стекла по поверхности трещины. Чтобы трещина на всем участке разреза приближалась к плоскости и была нормальна к поверхности образца, давление инструмента должно быть постоянным по всей длине разреза, а направление действия режущего инструмента перпендикулярно к поверхности заготовки.
При разделении больших кусков на части применяют распиловочные станки. Распиливание выполняется отрезными алмазными кругами, закрепленным на специальной оправке, на которой возможно одновременная параллельная установка нескольких отрезных алмазных кругов. Распиливание стекла производится для получения заготовок сложной формы.
6.3. Виды обработки стекла.
В производстве оптических деталей можно выделить три группы операций обработки стекла:
- основная,
- специальная,
- вспомогательная.
Основные операции сопровождаются удалением с обрабатываемой поверхности заготовки слоев стекла различной толщины, а также изменение формы заготовки, ее размеров и качество поверхности. Такими операциями являются: резанье, раскалывание, сверление, фрезирование, шлифование, полировка.
Специальные операции изменяют свойства полированных поверхностей. К операциям такого типа относятся:
1) соединение отдельных деталей в сложные склеиванием или силами молекулярного сцепления – оптический контакт;
2) нанесение пленок, уменьшающих коэффициент отражения света – просветляющие покрытия;
3) нанесение пленок увеличивающих коэффициент отражения – зеркальные покрытия;
- нанесение пленок, частично отражающих и частично пропускающих свет в определенном соотношении – светоделительные покрытия;
- нанесение пленок, изменяющих коэффициент пропускания по определенному закону – нейтральные фильтры;
- нанесение различных сеток и шкал.
Вспомогательные операции производятся для выполнения основных и специальных операций обработки. К таким операциям относятся: крепление заготовок и деталей на приспособлениях – блокировка, снятие деталей с приспособлений – разблокировка, промывка деталей и приспособлений, нанесение на обработанные поверхности защитных пленок – покрытий.
6.4. Основные типы инструментов.
При обработки стекла, вследствие его твердости и хрупкости используются различные абразивные и полировальные материалы. Металлическим инструментом стекло обрабатывается редко.
Абразивные материалы применяются в виде отдельных зерен или же зернистой и порошкообразной массы. Полировальные материалы используются только в виде мелких порошков. Абразивные материалы воздействуют на стекло при его обработки в двух состояниях – связанным и свободным; полировальные - только в свободном состоянии.
При обработке стекла одиночным связанным абразивным зерном оно жестко крепится в оправе, например, при резании и сверлении стекла алмазом. Зернистая абразивная масса закрепляется жестко или находится в вязком состоянии. В первом случае абразивные материалы смешиваются со связками, полученная смесь формуется и подвергается термической обработке, образуя различный абразивный инструмент – шлифовальные круги, пилы и фрезы.
При другом способе закрепления абразивные материалы смешиваются с вязкой массой (например, вазелином) и вводятся в пазы металлических тем. – пилы, фрезы и сверла.
При свободном состоянии абразивного или полировального материалов зернистая или порошкообразная увлажненная масса применяется без закрепления.
Увлажненные абразивные порошки наносятся на различные металлические приспособления: диски при распиливании, трубки при сверлении, сферические или плоские поверхности при шлифовании.
Полировальные порошки наносятся на неметаллические подложки, закрепляемые на полировальниках. Металлический инструмент без абразивов применяется только для грубой обработки стекла – резании и сверлении.
Процесс изготовления оптических деталей может быть разделен на две основных части: предварительная и точная.
Предварительная обработка заключается в подготовке исходного полуфабриката. Заготовкам придается форма будущих деталей, при изготовлении линз из листа постоянной толщины выполняются следующие операции: сначала лист режется на куски близкие по размерам и форме к параметрам линзы. Края кусков обламывают. Куски склеивают в столбики. Столбики округливают либо специальным абразивом на планшайбе, либо фрезированием фрезой или шлифовальным кругом. Грубая обработка – обрезка сферических поверхностей заготовки выполняется поштучно.
Точная обработка начинается обычно после закрепления заготовок на приспособлении. Стороны заготовок шлифуют и полируют до обеспечения нужных размеров и качества поверхности. Линзы после полировки центрируются.
6.4.1. Общие сведения о технологии обдирки и
грубой шлифовки.
Обдирка и грубая шлифовка стекла составляет важный этап в процессе изготовления оптических деталей. При обдирке и грубой шлифовке заготовкам придают форму будущих деталей и их основные угловые и линейные размеры.
О

Г


На начальной стадии обдирки заготовка подвергается обработке на станке ОШ-469. Это шлифовальный станок, у которого связанный абразив нанесен на планшайбу. В качестве абразива используется алмазосодержащий слой. Далее деталь обрабатывается на станке ОС-350, где обработка производится свободным абразивом, в качестве которого используется наждак №5. Для выравнивания размеров деталь шлифуют на станке 3Д756, в котором для обработки также используется связанный абразив, но при этом поверхность получается менее грубая. Детали наклеиваются на планы с помощью воска и затем устанавливаются на магнитный вращающийся стол станка для последующей обработки. При использовании стеклянных планов их крепят к столу с помощью магнитных прокладок.
Окончательная доводка осуществляется на станке ОС-350 с использованием наждака М-40.
На конечной стадии осуществляется фасировка и далее деталь направляется на контроль.
6.4.2. Абразивные материалы.
Абразивные материалы представляют собой зерна определенного химического состава различной крупности и кристаллического строения.
К важнейшим свойствам абразивов, определяющих их воздействие на стекло, относят: твердость, прочность и размер зерен, постоянство гранулометрического состава порошков, а также способность давать при дроблении зерна с острыми краями.
Абразивные материалы разделяют на естественные и искусственные.
Абразивы ест естественного происхождения: алмаз, корунд, наждак и кварцевый песок.
Кварцевый песок. Кварц (SiO2) самый распространенный в природе минерал. Твердость – 7, удельный вес – 2,6. Представляет собой сыпучую горную породу, состоящую из зерен величиной от 0,1 до 1-2 мм, имеющих разную форму.
Наждак представляет собой мелкозернистые разновидности корунда и содержит до 65% Al2O3 с примесями соединений железа и кремнезема. Удельный вес 4-6, излом раковистый; менее хрупок и более загрязнен, чем корунд. Применяется для шлифовки стекла.
Корунд – кристаллический минерал Al2O3 гексагональной системы. Твердость – 9. Удельный вес – 3,9 – 4,0. Излом сильно раковистый. Применяется для шлифовки стекла и изготовления абразивных шлифовальных кругов и фрез.
Алмаз – чистый углерод кристаллического строения; в виде октаэдров. Твердость – 10. удельный вес – 3,4-3,6. К разновидностям алмаза относятся тонкозернистые, пористые агрегаты буровато – черного цвета, называемые карбонатами, и более мелкие – балласами. Агрегаты, имеющие шаровидную форму, называются бортом. Алмаз применяют для резания, растирания, фрезерования и сверления стекла.
Абразивы искусственного происхождения.
Карбид кремния (SiC) соединение углерода с кремнеземом, получаемое нагреванием смеси кварцевого песка с углем в электропечи при t = 2000˚ и выше. Кристаллы ромбического типа. Удельный вес – 3,1-3,99. Твердость 9,5-9,75. Карборунд применяется для обдирки и изготовления шлифовальных кругов.
Электрокорунд Al2O3 представляет собой кристаллический глинозем, получаемый электроплавкой коксита с углем при t = 2000˚. Удельный вес от 3,2 до 4,0. Электрокорунд применяется в виде шлифовальных порошков различной крупности и для изготовления абразивных инструментов.
6.4.3. Классификация образцов по зернистости.
В процессе дробления абразивные материалы превращаются в осколки различных размеров. По ГОСТ 3238 - 46 осколок с размерами поперечника
= 5 мм и отношением наибольшего размера к наименьшему не более 3:1, называется абразивным зерном. Для зерен длиной > 40 мк размерной характеристикой является длина зерна; для зерен менее 40 мк определяющим размером является полусумма их длины и ширины. Группа зерен, диаметры которых ограничены определенными размерами, называется абразивной фракцией.
Размер зерен абразивного материала является одной из главных характеристик, определяющих его производительность при обработке стекла. В соответствии с ГОСТ 3647 – 47 абразивные материалы классифицируют по размерам зерна на группы: 1) шлифзерно, 2) шлифпорошки, 3) микропорошки.
Все группы абразивных материалов маркируются по условным номерам зернистости. Практически порошок каждого номера зернистости состоит из нескольких фракций, определяющих гранулометрический состав. Фракция, содержащаяся в наибольшем количестве, называется основной и характеризует номер зернистости абразива. Чем ближе размеры зерен порошка к размерам основной фракции, тем однороднее абразивный материал, выше производительность обработки и лучше качество поверхности деталей. На качество обрабатываемой поверхности особенно отрицательно действуют зерна более крупных размеров, вызывающие появления царапин, сколов, точек.
Шлифующая способность определяется производительностью процесса шлифовки, т.е. снятием с образца слоя стекла определенной толщины при стандартных условиях проведения опыта.
При постоянном размере зерен абразива шлифующая способность зависит в основном от твердости абразива и выражается удельным сошлифовыванием, определяемым весовым количеством удаленного стекла, приходящегося на 1 г абразивного порошка, затраченного при шлифовании в стандартных условиях.
Относительная шлифующая способность показывает скорость шлифовки данной фракцией по сравнению со скоростью шлифовки какой – либо другой фракцией.
Прочность зерен абразива характеризуется способностью их сохранять свой размер при давлении шлифовальника в процессе обработки стекла.
6.4.4. Обработка линз.
При изготовлении линз проводятся два вида обдирочных работ:
- Обработка сферических поверхностей с обеспечением нужных радиусов кривизны (r1 и r2); при этом выдерживается толщина d линзы по оси и толщина ее t по краю;
- Округливание заготовки для получения детали нужного диаметра D.
Рассмотрим технологию отдельных обдирочных работ, начиная с предварительной обработки заготовок.
Подшлифовка пластин для обеспечения заданной толщины.
Данная операция применяется для удаления следов распила и придания пластинам плоско – параллельной формы и определенной толщины d.
Обработка одной из поверхностей пластин производится поштучно вручную. Обдирка производится наиболее крупным абразивом (№80) до получения плоской поверхности. После обдирки первой стороны пластин они наклеиваются обратной стороной на планшайбу; затем обрабатывается вторая сторона пластин и выдерживается их толщина.
Округливание столбиков.
Для ускорения этого процесса углы квадратных пластин предварительно обламывают плоскогубцами.
Округливание столбиков свободным абразивом производится двумя способами: 1) обдиркой незакрепленного столбика на планшайбе обдирочного станка и 2) обдиркой столбика при помощи металлического приспособления – сдирки; в этом случае столбик приклеивается к шпинделю ножного станка.
Округливание столбиков на планшайбе производится вручную. Ввиду различия линейной скорости в разных зонах планшайбы столбик надо периодически поворачивать на 180º, чтобы избежать разнотолщинности столбика. При круглении проверяется: 1) прямой угол столбика; 2) правильность цилиндрической поверхности столбика; 3) диаметр столбика D. Угол между основанием и образующей цилиндра обычно проверяют металлическими угольниками после того, как с цилиндрической поверхности уже сняты крупные выступы, в противном случае правильное измерение невозможно. Когда поверхность столбика станет ровной, проверяют его диаметр по всей длине. Обнаруженные выступы удаляют дальнейшей обработкой.
При круглении сдиркой столбик укрепляется на шпинделе станка с помощью патрона, к которому восковым клеем приклеивают основание столбика. Затем быстро, не давая воску застыть, навинчивают патрон на шпиндель и, вращая его рукой, смотрят, “бьет” ли свободный конец столбика или нет, после чего столбик двигают, центрируя его относительно оси патрона.
Изготовление линз из цилиндрических дисков.
При такой форме заготовки сферические поверхности обрабатывают двумя путями. В большинстве случаев абразивом одного номера обрабатывают попеременно обе стороны заготовки. При обработке первой стороны контролируется радиус кривизны поверхности и ее качество (глубина рельефного слоя и чистота поверхности); при обработке второй поверхности дополнительно проверяется толщина линзы d по оси. У плохо центрирующихся линз необходимо проверять косину, определяемую разнотолщинностью Δt края t линзы. Плохо центрируются линзы, у которых толщина от центра к краю изменяется медленно. Двояковыпуклые и двояковогнутые линзы плохо центрируются в том случае, когда радиусы кривизны их поверхностей велики по отношению к диаметру линзы, а мениски - когда их поверхности концентричны.
При другой схеме обработки сначала обрабатывается одна сторона заготовки всеми номерами абразива, а затем другая с подгонкой толщины d.
О
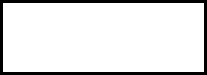
rф = Dл

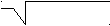
Изготовление линз из прессовок перед
пластичной блокировкой.
Основной особенностью обработки прессовок является удаление с их поверхности шамотного слоя. Шамотный слой выгоднее удалять на планшайбе. Если прессовки имеют нормальный припуск на округливание линз при центрировке, приступают к обработке сфер.
Учитывая возможность глубокого проникновения шамота в стекло, следует сначала обработать чистую поверхность, снимая по возможности, минимальный слой стекла. Тогда при обработке другой стороны более грязной можно будет снять весь припуск на толщину заготовки.
При изготовлении плосковыпуклых или плосковогнутых линз из прессовок всех видов сначала обрабатывают сферические поверхности абразивами всех номеров. После этого заготовки наклеиваются на планшайбу и обрабатываются плоские поверхности.
Изготовление линз перед жесткой блокировкой.
Исходными заготовками являются прессовки. Перед блокировкой удаляется шамотный слой обдиркой. Так как обработка прессовок ведется блоком, начиная с обдирки и кончая полировкой, контроль качества стекла будет невозможен. Если одна из поверхностей двояковыпуклой и двояковогнутой линзы обрабатывается поштучно, то первой обрабатывается поверхность с меньшим радиусом кривизны. Обдирка поверхностей может проводиться фрезами и свободным абразивом.
Перед фрезеровкой для контроля толщины снимаемого слоя на выпуклых поверхностях линз наносятся кружки, а на вогнутых – лунки. Лунки либо засверливаются алмазным сверлом, либо обдираются на грибах. Для получения кружков поверхность обрабатывается на планшайбе. После фрезерования блок шлифуется и полируется на станках с верхним звеном.
При обработке блока свободным абразивом поверхность прессовок обдирается карборундом и затем шлифуется. После этого ведется мелкая шлифовка.
6.4.5. Обработка призм.
При изготовлении призм можно выделить следующие основные виды обдирочных работ:
- обработка боковых сторон призм с обеспечением их параллельности и заданной ширины детали;
- обработка отражающих и преломляющих граней призмы с обеспечением их параллельности, выдерживанием линейных и угловых размеров, включая и пирамидальность;
- обработка фасок и закруглений на ребрах призмы.
При изготовлении призм следует применять приспособления, позволяющие одновременно обрабатывать несколько заготовок и контролировать их основные размеры. Точность изготовления призм на стадии обдирки и грубой шлифовки зависит от заданной точности детали и метода блокировки перед мелкой шлифовкой и полировкой.
Обработка боковых сторон призм не отличается от операции шлифовки. обдирка и грубая шлифовка является обычно окончательной обработкой и должна обеспечивать нужную ширину призмы. Наиболее рационально обрабатывать стороны в сепараторном устройстве.
После обработки боковых сторон обрабатываются рабочие грани призмы.
Штучная обработка столбиков равнобедренных прямоугольных призм начинается с обработки плоскости гипотенузы. Во избежании возникновения пирамидальности столбика при обработке выдерживается прямой угол между гипотенузой и торцом столбика. Далее обрабатываются плоскости катетов. В заключении на ребра столбика наносят фаску.
При обработке такого же столбика в приспособлениях, сначала обрабатываются плоскости гипотенузы, контролируя пирамидальность. Затем на ребре вершины прямого угла снимается фаска и выдерживается размер. После этого столбики вклеиваются в пазы приспособления обработанной плоскостью гипотенузы. При этом необработанные плоскости (призмы) катетов займут произвольное положение. Обрабатывают 1-й катет, переклеивают столбик и обрабатывают 2-й катет.
6.5. Мастерская шлифовки и полировки.
6.5.1. Технология мелкой шлифовки и полировки.
Основной задачей технологии средней и мелкой шлифовки является уточнение размеров деталей после обдирки и грубой шлифовки и улучшение качества поверхностей. Характерная особенность – обработка деталей блоками на станках с верхним звеном. Положение деталей в блоке зафиксировано по отношению к поверхности притирочного инструмента или относительно поверхности наклеечного приспособления. Поверхность обрабатывающего инструмента должна быть концентрична поверхности блока. Поэтому после окончания шлифовки какой-либо поверхности блока ее необходимо и отполировать в том же блоке.
П






Для того , чтобы шлифованные поверхности стали прозрачными их полируют. В процессе полировки также уточняется профиль поверхности в пределах заданного допуска (IV) на общие ошибки и устраняются местные ошибки поверхности (ΔIV). Технология полировки определяется заданной точностью обработки деталей. Выбирается тип подложки полировальника, конструкция станка и вид полировального материала.
Для неответственных деталей допускаются следы недополировки. Качество 13. Для оптических деталей, у которых следы недополировки недопустимы, качество обработки поверхности обозначается знаком - 14.


6.5.2. Мелкое шлифование.
Шлифовка линз при эластичной блокировке.
Перед началом обработки производится настройка станка. При этом устанавливается положение и длина штриха поводка верхнего звена, скорость вращения шпинделя станка и скорость движения механизмов верхнего звена. Откинув каретку верхнего звена, закрепляют блок или шлифовальник на шпинделе звена. Абразив наносят кисточкой на поверхность шлифовальника или блока. Затем на верхнее звено станка надевают груз и , включив механизмы движения, начинают шлифовку установленным набором абразива. Добившись правильного срабатывания поверхности, периодически контролируют ее качество, чистоту и кривизну слегка прополировывая отшлифованную поверхность и применив контроль пробным стеклом.
После окончания шлифовки кривизна поверхности должна отличаться от заданной на величину, позволяющую начать полировку с края блока и в конце полировки гарантировать заданный допуск, выражаемый числом колец (IV). Так как обработка всегда ведется с края, то при контроле должна быть всегда «яма» или «узкий цвет». Также необходимо минимизировать местные ошибки. Они могут быть исправлены в процессе полировки. Значительное изменение кривизны поверхности, порядка 6 колец, недопустимо исправлять при полировке.
Шлифовка линз при жесткой блокировке.
Этот вид обработки проводится непосредственно после грубой шлифовки и выполняется также как и при эластичной блокировке.
Режимы мелкой шлифовки.
Основными факторами повышения производительности обработки является повышение скорости и удельного давления. Повышение скорости ограничивается малой термостойкостью блокировочных смол и недостаточной жесткостью механизмов верхнего звена станков. При мелкой шлифовке электрокорундовыми порошками рекомендуют: для стекол типа крон – абразив М-20 ~ 2 м/сек, М-10 ~ 0,6 м/сек, для флинтов υобр понижают. Повышение давления также приводит к размягчению смолы.