Энергосберегающая технология сольвентной деасфальтизации нефтяных остатков 05. 17. 07 Химия и технология топлив и специальных продуктов
Вид материала | Диссертация |
- Программа-минимум кандидатского экзамена по специальности 05. 17. 07 Химическая технология, 190.12kb.
- Московский Государственный Университет пищевых производств Ю. А. Косикова методические, 725.64kb.
- Программа вступительного экзамена в магистратуру Cпециальность 6M072700 -технология, 430.68kb.
- Наши научные труды вызывают интерес зарубежных ученых, 201.11kb.
- Курс 2 Семестры 3,4 Всего аудиторных часов 136, в том числе: 3 семестр 58 час; 4 семестр, 252.62kb.
- Рабочая программа по дисциплине опд. Ф. 12 «Микробиология» направления 260200 Производство, 368.1kb.
- Учебное пособие для студентов, обучающихся по специальности 260502 «Технология продуктов, 2230kb.
- Конспект лекций по дисциплине опд «Экономика отрасли» для студентов специальности 260502, 1005.84kb.
- Качество мяса африканского страуса и технология функциональных пищевых продуктов, 320.35kb.
- Образовательная программа 240100 Химическая технология и биотехнология Дисциплина Химия, 54.66kb.
Таблица 5 - Выходы продуктов и качественные показатели при деасфальтизации гудрона западно-сибирской нефти (содержание пропана в пропан-бутановой смеси 41-44%, соотношение растворитель: гудрон 6:1 по объему)
Показатели | № опыта | |||||
1 | 2 | 3 | 4 | 5 | 6 | |
Температура, °С Давление, МПА Выход деасфальтизата, % Качество деасфальтизата: | 75 2,0 67,0 | 80 2,3 58,2 | 90 3,0 53,0 | 100 3,4 48,8 | 110 4,0 39,2 | 120 4,5 30,1 |
плотность, кг/м3 коксуемость, % масс. | 974 6,1 | 961 4,3 | 958 4,1 | 953 3,6 | 942 3,0 | 944 3,3 |
Температура размягчения асфальта, °С | 76 | 75 | 61 | 59 | 49 | 45 |
В экспериментах по деасфальтизации различных гудронов в целом наблюдается прямая зависимость между качественными показателями деасфальтизата и его выходом. Однако эта зависимость неоднозначная и зависит от состава растворителя. На рис. 6 приводятся опытные данные по коксуемости Сд деасфальтизата в зависимости от его выхода D. В опытах использовались гудроны различного происхождения (МГЗСН, ГЗСН, ГАН (табл.2 )). Проведенные исследования позволяют сделать следующие выводы.
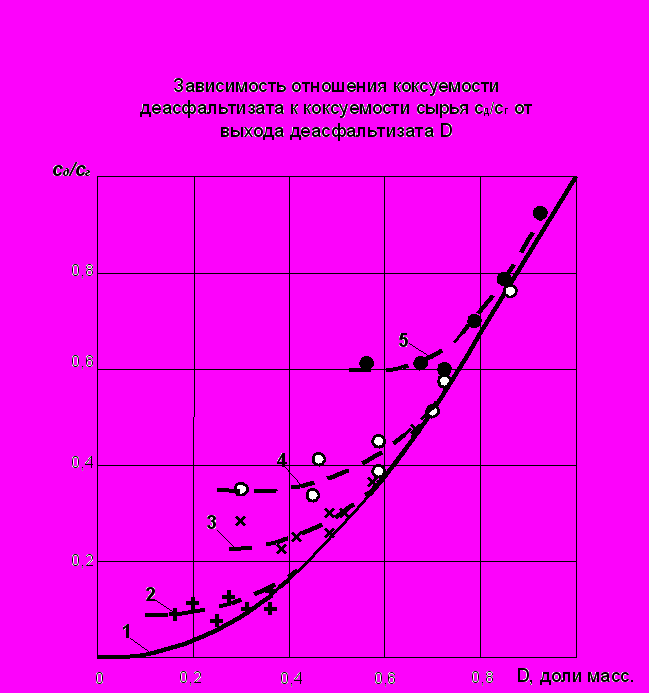
Рис. 6 Зависимость отношения коксуемости деасфальтизата к коксуемости сырья от выхода деасфальтизата D
- Р
асчетная асимптотическая зависимость (линия 1)
- О
пытные зависимости для различных растворителей (2-пропан, 3-пропан-бутан, 4-бутан, 5*-легкий бензин)
*-данные взяты из литературы по процессу ДОБЕН.
В относительных (безразмерных) величинах влияние происхождения гудрона на зависимость коксуемости деасфальтизатов от выхода незначительно, тогда как влияние состава растворителя на эту зависимость, наоборот, существенное. Коксуемость деасфальтизата, полученного на одном растворителе, определяется его выходом: чем больше выход деасфальтизата, тем больше его коксуемость. С увеличением в составе растворителя бутанов, в особенности, нормального бутана, качественные показатели полученного деасфальтизата ухудшаются. Аналогичный вид имеют зависимости других характеристик деасфальтизата в относительных единицах, таких как плотность деасфальтизата, содержание в нем металлов, асфальтенов, от выхода.
Например, при применении в качестве растворителя нормального бутана для деасфальтизации ГЗСН с коксуемостью 12,4% получаемый деасфальтизат имеет коксуемость не ниже 6 - 7 %, плотность не ниже 950-970 кг/м3 даже при очень низких выходах (20-30 %), тогда как для пропан-бутановой смеси, состоящей из 30-40 % пропана и 60-70 % бутана, нижние пределы по коксуемости деасфальтизата (при низких выходах) составляют 3,5 – 4,5 %, по плотности 930-940 кг/м3, а для чистого пропана, соответственно, 1 - 1,5 % и 920-925 кг/м3.
Таким образом, выбор растворителя процесса деасфальтизации определяется требуемым качеством получаемого продукта и качеством используемого сырья. Например, для получения из гудрона западносибирской нефти деасфальтизата коксуемостью не выше 4,0% (I тип остаточного сырья для каталитического крекинга), можно использовать пропан или пропан-бутановые смеси. При использовании пропана выход деасфальтизата не превышает 40 %, тогда как при использовании в качестве растворителя пропан-бутановой смеси с содержанием пропана 30-40%, выход деасфальтизата может достигать 50 %. С помощью н – бутана невозможно получить из ГЗСН деасфальтизат с коксуемостью ниже 4%.
На рис. 6 сплошной линией 1 представлена расчетная зависимость (6) для коксуемости деасфальтизата. При сравнении опытных данных с расчетной зависимостью можно заметить, что расчетная кривая является огибающей кривой (асимптотикой) для опытных данных, полученных с использованием различных видов сырья и растворителей, со стороны больших выходов деасфальтизата. Таким образом, расчетные асимптотические зависимости (6) дают оценку нижнего достижимого предела показателя качества деасфальтизата при заданном его выходе или, наоборот, определяют максимально возможный выход деасфальтизата при заданном качестве.
При обработке экспериментальных данных по пропан-бутановой деасфальтизации различных гудронов было выведено следующее эмпирическое уравнение для определения оптимального состава пропан-бутанового растворителя при получении асфальта с требуемой температурой размягчения из различных гудронов:

где Сп – содержание пропана в пропан-бутановой смеси, % масс.; - плотность гудрона, кг/м3; Са – содержание асфальтенов в гудроне, % масс.; Тр – температура размягчения асфальта, °С.
Перспективы применения продуктов пропан-бутановой деасфальтизации
Эффективность процесса пропан-бутановой деасфальтизации определяется квалифицированным использованием его продуктов. В работе проведены исследования по использованию продуктов пропан-бутановой деасфальтизации в различных направлениях. По результатам исследования получены 9 патентов РФ.
Путем селективной очистки и депарафинизации из пропан-бутанового деасфальтизата были получены масла для прокатных станов ПС-28 и П-40.
Использование смеси: остаточное базовое масло - пропан-бутановый деасфальтизат в соотношении 60-70 к 30-40% позволило получить образцы масла, отвечающие требованиям на “цилиндровое масло - 38”. В случае применения смеси остаточное базовое, дистиллятное базовое масло (И-40) и пропан-бутановый деасфальтизат с добавлением всего 4% присадки “Англамол-99” было получено трансмиссионное масло ТАД-17И. При обычной технологии приготовления этого масла требуется ввести 6,5 % присадки “Англамол-99”.
Проведены пилотные опыты по каталитическому крекингу вакуумных газойлей и смесей вакуумный газойль – пропан-бутановый деасфальтизат и вакуумный газойль – мазут. Показано, что при смешении вакуумного газойля с деасфальтизатом выход кокса меньше, чем при смешении вакуумного газойля с мазутом. Кроме того, использование смеси вакуумного газойля с деасфальтизатом в качестве сырья каталитического крекинга позволяет добиться увеличения выхода бензиновой фракции на 2,3 – 3,1 % по сравнению с чистым вакуумным газойлем и на 3,6–4,5% по сравнению со смесями вакуумного газойля с мазутом.
Пропан-бутановая деасфальтизация гудрона и компаундирование асфальта с различными подходящими разбавителями является наиболее универсальным способом производства высококачественных неокисленных дорожных битумов. Наилучшие результаты при получении компаундированных битумов на основе асфальтов пропан-бутановой деасфальтизации дает использование в качестве разбавителя остаточных экстрактов селективной очистки. Результаты испытания таких битумов в составе асфальтобетонных смесей показали существенно лучшие показатели по водостойкости. Результаты сопоставительных исследований термической стабильности окисленного, остаточного и компаундированного битумов так же показали, что наиболее высокой термической стабильностью обладают компаундированные битумы.
Опытно-промышленное производство компаундированных битумов на установках 36/1 и 19/3 ОАО ”Уфанефтехим” было начато в 1993г. В 1994г. ПРСО “Башкиравтодор” с использованием компаундированных битумов ОАО ”Уфанефтехим” были построены опытные участки дорог протяженностью свыше 10 км с целью осуществления многолетних квалификационных испытаний. За пятнадцать лет наблюдений за качеством дороги на этом опытном участке не произошли существенные изменения, отсутствуют следы глубокого износа, разрушения. В те же сроки соседние участки, построенные с применением обычных окисленных битумов, уже неоднократно подвергались ремонту.
Летом 1998г. на ОАО «Новойл» в ходе опытного пробега на установках 36/2 и 19/3 также было наработано и отгружено потребителям около 4000т компаундированного битума марок БНН 50/80 и БНН 80/120
По результатам проведенных лабораторных и опытно-промышленных исследований разработаны, согласованы и утверждены в установленном порядке постоянно действующие технические условия на дорожные неокисленные битумы БНН (ТУ-0256-097-00151807-97).
Разработаны варианты утилизации асфальта пропан – бутановой деасфальтизации путем его использования в производстве брикетирования углей. Исследования, проведенные на экспериментальной базе Института обогащения твердых топлив (ИОТТ), показали, что при использовании в качестве связующего асфальта пропан-бутановой деасфальтизации улучшаются все характеристики углебрикета.
Нами подготовлена техническая документация по процессу термополиконденсации асфальта, его смесей с гудроном в виде Базового проекта, Исходных данных для проектирования производства нефтяных пеков взамен канцерогенных каменноугольных пеков.
Образцы асфальта пропан-бутановой деасфальтизации, полученные из гудрона Павлодарского НПЗ, были испытаны в качестве сырья процесса коксования. Полученные коксы имели низкие содержание серы (до 1%), выход летучих веществ -6,4% и соответствовали требованиям ГОСТ 2898-78 на малосернистые коксы, предназначенные для применения в электродной, алюминиевой промышленностях.
Результаты использования процесса пропан-бутановой деасфальтизации гудронов в промышленных масштабах
В 1993-94г.г. на ОАО ”Уфанефтехим” были проведены первые в России опытно-промышленные пробеги по получению деасфальтизата и асфальта пропан-бутановой деасфальтизации гудрона из западно-сибирской нефти. В ходе пробега были опробованы в промышленном масштабе режимы проведения процесса пропан-бутановой деасфальтизации и наработаны партии деасфальтизата и асфальта для последующих испытаний в производствах масел и неокисленных дорожных битумов.
В 1998 г. технология пропан-бутановой деасфальтизации гудрона была опробована на ОАО «Новойл». На установке 36/1-2 из гудрона западно-сибирской нефти была наработана партия пропан-бутанового деасфальтизата, часть которого (650 м) прошла последующую селективную очистку на установке 37/1 и депарафинизацию на установке 39/2 ОАО «Новойл».
Условия работы этих установок отличались от обычного режима их работы только по одному показателю соотношению растворителя к сырью. Некоторые показатели качества образцов деасфальтизата, рафината и депарафинированного масла, полученные в ходовых анализах, даны в табл.6.
Таблица 6 - Характеристика сырья и продуктов селективной очистки
Наименование продукта | Плотность, кг/ м3 | Вязкость, 100, сСт | Коксуемость, % | Температура, С | |
вспышки | застывания | ||||
Деасфальтизат (в потоке) | 952 | 55,1 | 4,5 | 238 | 46 |
Рафинат (в потоке) | 896 | 31,3 | 1,1 | 241 | 56 |
Экстракт (в потоке) | 973 | 61,1 | 6,4 | 234 | - |
Депарафинированное масло (в потоке) | 901 | 33,5 | 1,0 | 270 | - 13 |
Депарафинированное масло (в резервуаре) | 898 | 27,1 | 0,8 | 262 | - 10 |
Петролатум (в потоке) | 871 | 15,9 | 0,4 | 235 | 60,5 |
В ходе опытного пробега были наработаны опытно-промышленные партии масел для прокатных станов ПС-28 и П-40, имеющие вязкость 100=27 сСт и 100=34 сСт и удовлетворяющие требованиям ГОСТ 12672–77 и ТУ 38.101312 - 78, соответственно.
Выход деасфальтизата на установке 36/1-2 составил 56-58%, выход рафината на установке 37/1 достигал 40-42%, а выход депарафинированного высоковязкого масла на установке 39/2 – 82-83%.
В ходе опытно-промышленных экспериментов нами была проверена возможность применения пропан-бутанового деасфальтизата в качестве компонента сырья установки пропановой деасфальтизации 36/1-1 без изменения режима ее работы. Пропановый деасфальтизат, выводимый с установки, практически не отличался по качеству от обычно получаемого из гудрона. Получаемый асфальт имел более низкие значения температуры размягчения (20 - 25С) и коксуемости (10,4 - 10,5 %), чем обычный пропановый асфальт (tразм. = 36 - 43С, коксуемость = 17,5 - 22,7 %). Выход деасфальтизата с установки 36/1-1 повысился на 27 - 32 % от обычно достигаемого для гудрона.
Асфальт пропан-бутановой деасфальтизации, получаемый на установке 36/1-2, полностью направляли на битумную установку 19/3 для приготовления неокисленных дорожных битумов марок БН 50/80 и БН 80/120.
По результатам исследований были разработаны рекомендации для перепрофилирования существующих, но в настоящее время незагруженных установок пропановой деасфальтизации гудрона на режим пропан-бутановой деасфальтизации. В настоящее время три установки деасфальтизации гудрона ОАО «Уфанефтехим» и две установки деасфальтизации на ОАО «Новойл» по нашим рекомендациям переведены на топливный вариант работы с применением в качестве растворителя пропан – бутановых смесей.
5 Технология процесса
Оформление процесса деасфальтизации нефтяного остатка со сверхкритическим узлом регенерации растворителя
В работе рассмотрены различные варианты технологического оформления процесса деасфальтизации нефтяного остатка со сверхкритическим узлом регенерации растворителя. Показано, что применение системы регенерации растворителя в сверхкритических условиях совместно с двухступенчатой инжекторной системой компремирования газов низкого давления снижает энергозатраты и количество металлоемкого оборудования для проведения процесса и повышает гибкость технологического процесса. Двухступенчатая инжекторная система компремирования потока газообразного растворителя низкого давления позволяет организовать абсорбционную очистку растворителя от сероводорода, который образуется при регенерации растворителя из асфальтового раствора за счет высокотемпературного нагрева потока в печи и концентрируется в регенерированных растворителях низкого и среднего давления.
Принципиальная технологическая схема установки деасфальтизации со сверхкритическим узлом регенерации растворителя с использованием двухступенчатой инжекторной системы очистки и компремирования газообразного растворителя представлена на рис.7.
Гудрон в смесителе С-1 разбавляется небольшой частью циркулирующего растворителя и подается в экстракционную колонну К-1. Выводимый с верха К-1 деасфальтизатный раствор бустерным насосом Н-1 через теплообменники Т-1, Т-3 подается в сепаратор Р-1, работающий в сверхкритическом режиме. В сепараторе происходит разделение смеси на две фазы: верхнюю - пропан-бутановую и нижнюю - деасфальтизатную. Верхняя фаза, состоящая практически из чистого растворителя, проходит через теплообменники Т-1 и Т-6, нагревая потоки деасфальтизатного и асфальтного растворов из экстракционной колонны, и далее подается в струйный компрессор второй ступени сжатия СК-2, где используется ее повышенное давление для компремирования газообразного растворителя из системы регенерации низкого и среднего давления. Нижняя фаза, содержащая 90-95% деасфальтизата и 5-10% растворителя, направляется в испаритель Э-1б для отделения паров растворителя, после чего в отпарную колонну К-2, для отпарки остатков растворителя из деасфальтизата водяным паром.
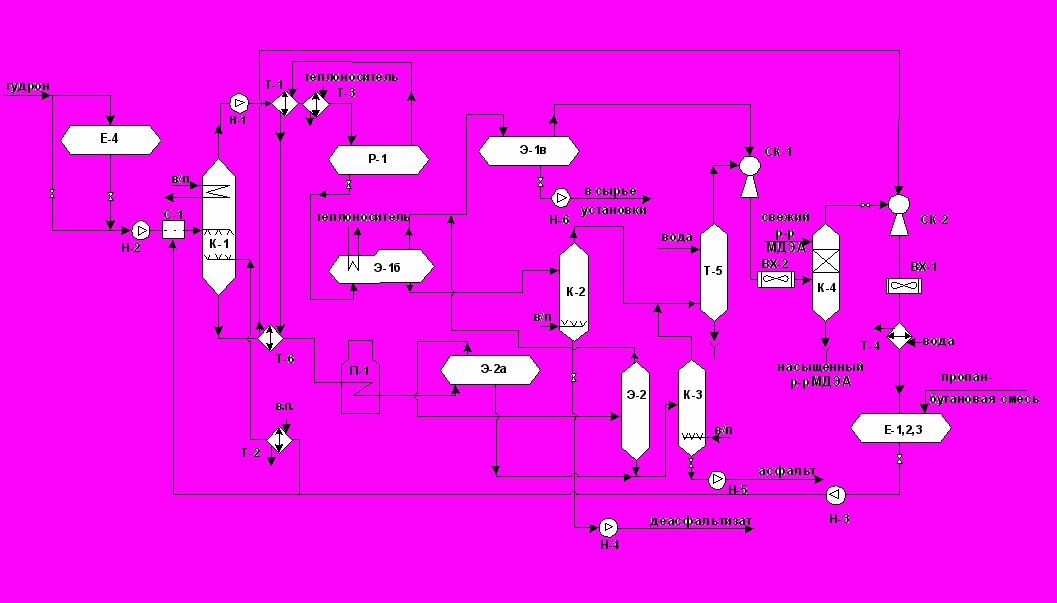
Рис. 7 Принципиальная схема установки деасфальтизации гудрона со сверхкритическим узлом регенерации растворителя
К-1 экстракционная колонна; Р-1 сверхкритический сепаратор; П-1 печь; Э-1б, Э-2а испарители; Э-1в, Э-2 каплеотбойники; Е-1 емкость сжиженного растворителя; Е-4 – сырьевая емкость; К-2, К-3 отпарные колонны; Т-1, Т-2, Т-3, Т-4, Т-6 теплообменники; Т-5 – конденсатор смешения; ВХ-1, ВХ-2 – воздушные холодильники; СК-1, СК-2 струйные компрессоры; С-1 – смеситель, Н-1, Н-2, Н-3, Н-4, Н-5, Н-6 – насосы.
Регенерация растворителя из асфальтового раствора, выводимого с низа экстракционной колонны, производится путем нагрева в теплообменнике Т-6 и технологической печи П-1, однократного испарения в испарителе Э-2а и отпаривания в отпарной колонне К-3. Потоки газообразного растворителя из отпарных колонн К-2, К-3 соединяются и направляются через конденсатор смешения Т-5, где поддерживается давление 0,015-0,02 МПа и температура 20-40 °С, в камеру всасывания струйного компрессора первой ступени сжатия СК-1. В качестве рабочего тела в струйном компрессоре используют потоки паров растворителя среднего давления 1,6-2,0 МПа, отделенных от деасфальтизатного и асфальтового растворов в испарителях Э-1б и Э-2а. После струйного компрессора СК-1 пары растворителя при давлении 0,55 – 0,60 МПа охлаждаются в воздушном холодильнике ВХ-2 и направляются в абсорбционную колонну К-4 на аминную очистку. С верха К-4 очищенный газ подается в приемную камеру струйного компрессора второй ступени сжатия СК-2, где в качестве рабочего тела используется поток растворителя высокого давления из сепаратора Р-1 (4,3 – 5,1 МПа).
После СК-2 суммарный поток очищенного растворителя, выходящий под давлением 1,5 – 2,0 МПа, охлаждается, конденсируется в конденсаторах холодильниках воздушного ВХ-1 и водяного Т-4 охлаждения и через емкость сжиженного растворителя Е-1 насосом Н-3 направляется на стадию экстракции для повторного использования. Содержание сероводорода в потоке растворителя после СК-2 не превышает допустимого уровня 0,01%.
В результате реализации данной технологии из состава обычной установки деасфальтизации исключаются два испарителя, поршневой двухступенчатый компрессор и ряд других связанных с ним аппаратов.
Предложенная схема может быть реализована на установках деасфальтизации, работающих как по масляному варианту с использованием пропанового растворителя, так и по топливному варианту с использованием в качестве растворителя пропан - бутановых смесей. Технологическая схема установки пропан–бутановой деасфальтизации с узлом сверхкритической регенерации растворителя отличается от известной схемы установки пропановой деасфальтизации гудрона наличием дополнительной системы нагрева и циркуляции органического теплоносителя АМТ–300, который используется вместо водяного пара. Это связано с необходимостью нагрева деасфальтизатного раствора до довольно высокой температуры (около 1600С) в Т-3.
В 2006 – 2007 гг. по исходным данным, разработанным ГУП «Институт нефтехимпереработки РБ», была спроектирована и осуществлена реконструкция установки деасфальтизации гудрона 36/2 ОАО «Уфанефтехим». После проведения пуско-наладочных мероприятий в сентябре 2007г. установка 36/2 ОАО «Уфанефтехим» была принята в эксплуатацию. В настоящее время установка работает на повышенной производительности 41 м3/ч (проектная – 38 м3/ч).
При реконструкции установки были разработаны и реализованы следующие мероприятия (рис. 7):
- увеличение производительности установки по гудрону до 38 м3/ч (исходная производительность 28 м3/ч);
- использование в качестве растворителя пропан-бутановой смеси;
- осуществление регенерации растворителя из деасфальтизатного раствора при сверхкритических условиях;
- замена поршневых компрессоров на струйные аппараты для сжижения растворителя системы низкого давления;
-применение в экстракционной колонне регулярных насадок, разработанных ООО «ИМПА Инжиниринг»;
- включение в схему установки дополнительных узлов нагрева и циркуляции органического теплоносителя АМТ-300, используемого взамен водяного пара, и аминной очистки растворителя от сероводорода.
Опытно – промышленный пробег данной установки после ее реконструкции показал работоспособность и высокую эффективность технологии сверхкритической регенерации растворителя и правильность выводов научно-технических разработок, использованных при проектировании реконструкции.
В результате реконструкции установки потребление водяного пара сократилось в 5,7 раза, оборотной воды – в 14 раз, а расход электроэнергии увеличился в 1,9 раза, расход топлива в 3,2 раза, содержание сероводорода в циркулирующем растворителе снизилось с 2% до 0,01%. Экономия энергоресурсов в результате реконструкции установки составила 39,4%, в стоимостном выражении 28,7 млн. руб. в год.
Поиск новых направлений применения процесса деасфальтизации нефтяных остатков
Проблема рациональной переработки тяжелых нефтей является одной из важных задач нефтепереработки России и многих стран мира. Нами в качестве наиболее рациональной и перспективной схемы переработки таких нефтей предлагается сочетание процессов прямой перегонки нефти и деасфальтизации мазута с получением в качестве товарной продукции деметаллизированной нефти (смесь легких дистиллятов и деасфальтизата) и неокисленного дорожного битума (смесь мазута и асфальта). Были выполнены исследования и подготовлены технико-экономические расчеты (ТЭР) применительно к сырьевой базе России и Казахстана. Из тяжелых нефтей плотностью 930 - 970 кг/м3 возможно получение 49 - 72% деметаллизированной нефти и 28 - 51% дорожных битумов. Деметаллизированную нефть, полученную по такой технологии, предлагается отдельно транспортировать на отечественные НПЗ, она содержит 15 – 20 ppm тяжелых металлов, 40 – 60% легких углеводородов при полном отсутствии асфальтенов, поэтому является более ценным углеводородным сырьем, чем обычная нефть.
Свойства образца тяжелой нефти, отобранной в Башкортостане, мазута, полученного из тяжелой нефти, и продуктов деасфальтизации мазута представлены в табл.7.
Деасфальтизаты, отобранные из мазута с выходами 72-80% на мазут отличаются отсутствием асфальтенов, низкой коксуемостью (4,9 - 6,4%) и имеют вязкость при 100°С в пределах 42 - 77 сСт. Асфальты имеют высокую плотность, их высокая температура размягчения (104-120°С) и высокая коксуемость (29-31%) связаны со значительным содержанием асфальто-смолистых соединений (72-74%), что дает возможность производить дорожные битумы простым компаундированием асфальта с исходным мазутом.
Дорожные битумы, полученные смешением асфальта с мазутом, соответствуют требованиям ГОСТ 22245-90 на дорожные битумы марок БНД 60/90, БНД 90/120.