Энергосберегающая технология сольвентной деасфальтизации нефтяных остатков 05. 17. 07 Химия и технология топлив и специальных продуктов
Вид материала | Диссертация |
Таблица 2 - Состав фаз в разделителе при дополнительном подогреве нижней фазы Условия разделения |
- Программа-минимум кандидатского экзамена по специальности 05. 17. 07 Химическая технология, 190.12kb.
- Московский Государственный Университет пищевых производств Ю. А. Косикова методические, 725.64kb.
- Программа вступительного экзамена в магистратуру Cпециальность 6M072700 -технология, 430.68kb.
- Наши научные труды вызывают интерес зарубежных ученых, 201.11kb.
- Курс 2 Семестры 3,4 Всего аудиторных часов 136, в том числе: 3 семестр 58 час; 4 семестр, 252.62kb.
- Рабочая программа по дисциплине опд. Ф. 12 «Микробиология» направления 260200 Производство, 368.1kb.
- Учебное пособие для студентов, обучающихся по специальности 260502 «Технология продуктов, 2230kb.
- Конспект лекций по дисциплине опд «Экономика отрасли» для студентов специальности 260502, 1005.84kb.
- Качество мяса африканского страуса и технология функциональных пищевых продуктов, 320.35kb.
- Образовательная программа 240100 Химическая технология и биотехнология Дисциплина Химия, 54.66kb.
Для верхней пропановой фазы наблюдается корреляция между содержанием в ней деасфальтизата и фракционным составом деасфальтизата. Чем меньше температура выкипания 5-10% масс. деасфальтизата, тем больше содержание масла в пропане.
На рис.3,4 представлены результаты разделения смеси пропана, бутана и деасфальтизата на лабораторной установке АРФ-2.
В экспериментах использовали пропан-бутановую смесь, содержащую 32% пропана и 68% суммы бутанов. Деасфальтизат был наработан из гудрона западно-сибирской нефти на пилотной установке деасфальтизации ЭПД-2 с применением в качестве растворителя этой же пропан-бутановой смеси. Как видно из представленных результатов, для пропан-бутанового растворителя качественный характер изменения состава фаз в сверхкритическом разделителе от режима его работы такой же, что и для пропанового растворителя.
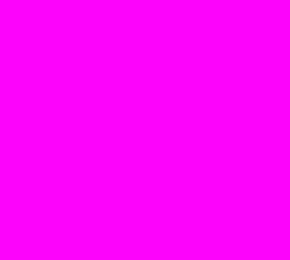
Рис. 3 Содержание деасфальтизата в верхней фазе сверхкритического разделителя
Температура регенерации, °С: 1 – 137; 2 – 145; 3 – 153; 4 – 161.
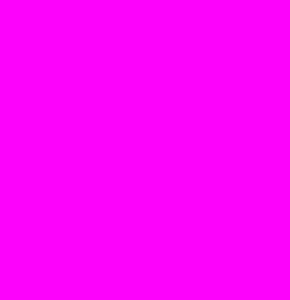
Рис. 4 Содержание растворителя в нижней фазе сверхкритического разделителя
Температура регенерации, °С: 1 – 137; 2 – 145; 3 – 153; 4 – 161.
От состава растворителя сильно зависит режим проведения сверхкритического разделения деасфальтизатного раствора. Если для пропанового растворителя оптимальный режим сверхкритической регенерации находится в области 120°С и 5,0 МПа, для пропан-бутанового растворителя качественное разделение может происходить, как это видно из рис.3,4, при температуре 140–150°С и давлении 4,2-4,5 МПа.
На рис. 3,4 сплошной линией представлены результаты расчетов состава фаз, полученные с помощью уравнений (1). Видно, что результаты термодинамических расчетов состава фаз хорошо согласуются с опытными данными, полученными в статических условиях.
Результаты исследования процесса сверхкритического фазоразделения в промышленных условиях.
Для исследования процесса сверхкритического фазоразделения в промышленных условиях были проведены в 1991-1994г.г. три серии опытно-промышленных экспериментов на установке пропановой деасфальтизации 36/5 ЗАО «РНПК» (рис. 1).
Непосредственные визуальные наблюдения за процессом фазоразделения на пилотном аппарате позволили установить общую гидродинамическую картину образующихся в разделителе потоков и их влияние на степень фазоразделения. Результаты опытов, проведенных в широком диапазоне изменения параметров режима разделения (t=100-140°C, P=4,0-6,5МПа), позволили выявить основные закономерности влияния температуры, давления, высоты уровня фаз, градиента температуры в аппарате на чистоту потока растворителя, выводимого с верха аппарата.
В частности, было установлено, что имеет место резкое увеличение выноса деасфальтизата с растворителем при превышении давления в аппарате выше некоторого порогового значения. Увеличение температуры процесса фазоразделения приводит к увеличению порогового давления. Путем применения внутренних устройств можно существенно расширить область варьирования параметров режима, в котором осуществляется удовлетворительное отделение растворителя от деасфальтизата.
Как в лабораторных, так и опытно-промышленных экспериментах прослеживается общая закономерность улучшения степени разделения деасфальтизатного раствора (уменьшение содержания масла в верхней фазе и уменьшение содержания пропана в нижней фазе) с ростом температуры и понижением давления, что согласуется с результатами термодинамических расчетов.
Влияние гидродинамических факторов хорошо прослеживается при сравнении результатов разделения, полученных в лабораторных опытах, в которых процесс фазоразделения осуществляется в статических условиях, и данных опытно-промышленных экспериментов.
В статических условиях пороговое давление Рн, выше которого содержание деасфальтизата в верхней фазе пропана больше нормы (0,5%), зависит только от температуры, т.е. Рн=Рн (Т). Например, при Т= 120 0С Рн(120 0С) = 6,0 МПа (см. табл. 1). В динамических условиях это пороговое давление Рн(Т) зависит так же от времени пребывания деасфальтизатного раствора в разделителе t и наличия в нем коагулирующих устройств. Так, для пустотелых разделителей объемами 2л (t ≈ 2 мин.) и 0,135л (t ≈ 10с) величина Рн (1200С) составляет 5,4 и 4,8 МПа, соответственно.
При наличии коагулирующих устройств в разделителе, величина Рн (Т) приближается к своему статическому значению и составляет при 120 0С 5,8 МПа. Таким образом, оснащение аппарата сверхкритического фазоразделения коагуляторами позволяет в динамическом режиме фазоразделения обеспечить достижение верхнего предела, определяемого термодинамическими условиями, степени чистоты отделяемого растворителя.
Показано, что при дополнительном подогреве нижней фазы в разделителе на 20-25°С достигается снижение содержания растворителя в деасфальтизате в 2 раза (табл. 2). При этом содержание масла в верхней фазе не превышает 0,4 %.
В 2007-2008г.г. на установке 36/2 ОАО «Уфанефтехим» после проведения реконструкции узла регенерации растворителя с переводом на сверхкритический режим работы по исходным данным ГУП «ИНХП РБ» был проведен опытно-промышленный пробег с целью определения достигнутых технико-экономических показателей ее работы. Показано, что содержание деасфальтизата в регенерированном в сверхкритическом разделителе растворителе не превышает 0,5%, а содержание растворителя в деасфальтизате ниже 10-12%. Таким образом, результаты пробега подтвердили правильность научно-технических разработок, программ расчетов и компьютерных моделей процесса регенерации растворителя при сверхкритическом режиме, использованных при разработке исходных данных на проектирование реконструкции.
Таблица 2 - Состав фаз в разделителе при дополнительном подогреве нижней фазы
№ опытов | Условия разделения | Состав нижней фазы, % мас | |||
давле-ние, МПа | температура, оС | пропан | масло | ||
верхней фазы | нижней фазы | ||||
1 | 5,0 | 110 | 121 | 10,0 | 90,0 |
2 | 5,0 | 109 | 129 | 6,3 | 93,7 |
3 | 5,0 | 111 | 136 | 4,1 | 95,9 |
4 | 5,0 | 120 | 125 | 9,2 | 90,8 |
5 | 5,0 | 120 | 132 | 5,6 | 94,4 |
6 | 5,0 | 119 | 140 | 4,8 | 95,2 |