Проект сто ассоциация «национальный союз организаций в области обеспечения пожарной безопасности» («нсопб»)
Вид материала | Документы |
- Михайличенко Сергей Алексеевич Тема доклад, 147.89kb.
- Тема: «Об итогах работы Ассоциации «Национальный союз организаций в области обеспечения, 118.56kb.
- Вления по вопросам организационно-правового, финансового, материально-технического, 47.34kb.
- Приказ о мерах обеспечения пожарной безопасности в ООО, 10.89kb.
- План основных мероприятий Министерства культуры Республики Бурятия в области гражданской, 114.79kb.
- Программа обучения мерам пожарной безопасности населения, отдельных категорий работников, 152.35kb.
- Методические рекомендации, 1018.35kb.
- Постановлени е, 103.8kb.
- Нарушение требований пожарной безопасности невыполнение или ненадлежащее выполнение, 208.81kb.
- Методические рекомендации по вопросам обеспечения пожарной безопасности объектов защиты, 834.77kb.
Проект СТО
АССОЦИАЦИЯ «НАЦИОНАЛЬНЫЙ СОЮЗ ОРГАНИЗАЦИЙ В ОБЛАСТИ ОБЕСПЕЧЕНИЯ ПОЖАРНОЙ БЕЗОПАСНОСТИ» («НСОПБ») С ![]() ![]() УПЛОТНИТЕЛИ ВСПУЧИВАЮЩИЕСЯ Методы испытаний СТО ___ - 2011 Москва 2011 |
информационные данные о СТО
УТВЕРЖДЕН | | ||
ЗАРЕГИСТРИРОВАН | ______________ 2011 г. рег. №___________ | ||
ДАТА ВВЕДЕНИЯ | | ||
ПЕРИОДИЧНОСТЬ ПЕРЕСМОТРА | Без ограничения срока действия |
содержание
1 | Область применения | 2 |
2 | Нормативные ссылки | 2 |
3 | Термины и определения | 3 |
4 | Цель проведения испытаний | 3 |
5 | Средства, условия и порядок проведения испытаний | 4 |
6 | Методы испытаний | 5 |
7 | Представление результатов испытаний | 8 |
| Приложение А | 9 |
| Приложение Б | 10 |
| Приложение В | 11 |
| Приложение Г | 12 |
СТАНДАРТ ОРГАНИЗАЦИИ


УПЛОТНИТЕЛИ ВСПУЧИВАЮЩИЕСЯ
Методы испытаний

1 ОБЛАСТЬ ПРИМЕНЕНИЯ
Настоящая стандарт распространяется на организацию и порядок проведения испытаний уплотнителей вспучивающихся, заполняющих стыки строительных конструкций и изделий (далее – конструкции) при повышенных температурах (далее – материал) предотвращающего проникновение продуктов горения и пламени на необогреваемую поверхность конструкции с целью определения соответствия технических и функциональных характеристик установленных в технических спецификациях на конкретный материал.
Стандарт устанавливает требования к идентификации материалов, необходимые виды испытаний, последовательность, правила и условия проведения инструментального контроля характеристик вспучивания материала уплотнителя, а также порядок оформления результатов испытаний.
-
Нормативные ссылки
В настоящей методике используются ссылки на следующие нормативные документы:
ГОСТ Р 12.3.047 98 Пожарная безопасность технологических процессов. Общие требования. Методы контроля
ГОСТ Р 51293-99 Идентификация продукции Общие положения
ГОСТ Р 53293-2009 Пожарная опасность веществ и материалов. Материалы вещества и средства огнезащиты. Идентификация методами термического анализа
ГОСТ 2.114-95 ЕСКД. Технические условия
ГОСТ 12.1.004 91* ССБТ. Пожарная безопасность. Общие требования
ГОСТ 12.1.007 76* ССБТ. Вредные вещества. Классификация и общие требования
ГОСТ 12.1.019 79* ССБТ. Электробезопасность. Общие требования и номенклатура видов защиты
ГОСТ Р 8.568-97 ГСОЕИ Аттестация измерительного оборудования. Основные положения.
ГОСТ 166-89 Штангенциркули. Технические условия.
ГОСТ 427-77 Линейки измерительные металлические. Технические условия.
ГОСТ 30247.0 -94 Конструкции строительные. Методы испытаний на огнестойкость. Общие требования
ПР 50.2.006 ГСИ-94 Поверка средств измерений. Организация и порядок проведения
ГОСТ Р 50277-92(ИСО 9864-90) Материалы геотекстильные. Метод определения поверхностной плотности.
- ТЕРМИНЫИ ООПРЕДЕЛЕНИЯ
В настоящем документе применены следующие термины с соответствующими определениями:
3.1 Вспучивание материала – свойство материала в пластическом состоянии увеличиваться в объеме под воздействием выделившихся летучих веществ.
3.2 Давление вспучивания – давление, развивающееся при вспучивании материала в условиях ограниченного объема.
3.3 Коэффициент вспучивания – показатель, определяемый как отношение высоты исходного образца к высоте вспученного образца материала в условиях нагревания.
-
ЦЕЛЬ ПРОВЕДЕНИЯ ИСПЫТАНИЙ
4.1 Целью испытаний является проверка показателей материалов приведенных в таблице 1 на соответствие характеристик приведенных в технических спецификациях на конкретные материалы.
Таблица 1
п/п | Наименование показателей | Условия испытаний |
1 | Толщина | при нормальных условиях |
2 | Поверхностная плотность | ГОСТ Р 50277-92 |
3 | Идентичность материала от двух партий | линейный нагрев от 30◦С до 1000◦С со скоростью 20◦С/мин |
4 | Кратность вспучивания | При t= 450◦С в течении свыше 30 минут с дополнительной нагрузкой |
5 | Давление вспучивания | при t =350◦С свыше 30минут с возрастающей нагрузкой |
4.2 Место проведения испытаний
Испытания проводятся в аккредитованных испытательных лабораториях (центрах).
4.3 Перечень документов необходимых для проведения испытаний:
Техническое задание;
Нормативная документация на испытываемый материал;
Паспорт на испытываемый материал;
Акт отбора образцов;
Протокол идентификационных испытаний.
5 СРЕДСТВА, условия И ПОРЯДОК ПРОВЕДЕНИЯ ИСПЫТАНИЙ
5.1 Требования к образцам.
Для проведения испытаний необходимо отобрать 3 образца от одной партии и:
- при производстве в виде пласта (20×50) мм ± 0,1 мм;
- при производстве в виде ленты длина образца выбирается с таким учетом, чтобы площадь образца составляла 1000 мм2.
5.2 Испытательное оборудование и средства измерений.
Для проведения испытаний по определению толщины, поверхностной плотности и линейных характеристик вспучивания могут использоваться используются средства измерений приведенные в приложении А.
5.3 Порядок проведения испытаний
Испытания проводятся в два этапа:
Первый этап:
- проверка комплектности документов;
- первичная идентификация образцов материала поступивших на испытания.
Второй этап:
- испытания с использованием измерений для получения характеристик вспучивания на соответствие функциональным и иным требованиям в соответствии с технической спецификацией на конкретный материал.
5.4 Условия проведения испытаний
Испытания должны проводиться при следующих условиях:
- температура окружающего воздуха, ◦С - 20±2;
относительная влажность, % - от 30 до 80;
атмосферное давление, кПа - от 84 до 106;
частота питающей электросети, Гц - 50±1;
напряжение питающей сети переменного тока, В –
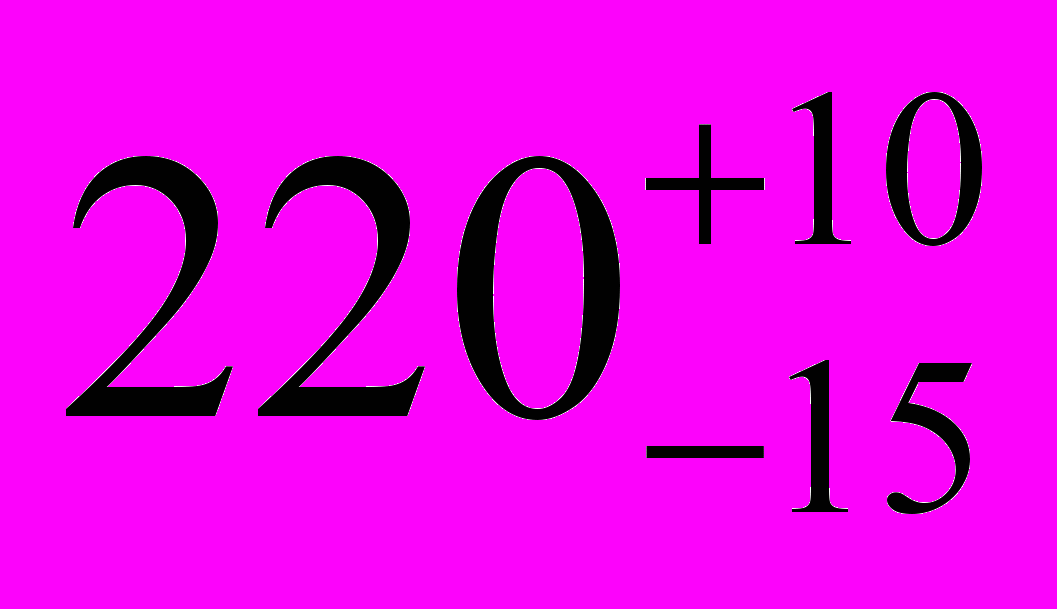
5.5 Требования к техническому обслуживанию
Средства измерений применяемые при испытании материалов должны быть поверены в соответствии с требованиями ПР 50.2.006 в аккредитованных организациях, а испытательное оборудование должно быть аттестовано по ГОСТ Р 8.568-97.
5.6 Требования к персоналу
Все работы по испытаниям проводятся персоналом, прошедшим соответствующую подготовку, под руководством лица ответственного за испытания.
5.7 Требования безопасности
При проведении испытаний должно быть обеспечено соблюдение требований безопасности установленных ГОСТ 12.2.007.0, ГОСТ 12.2.007.03, Правилами техники безопасности при эксплуатации электроустановок потребителей и Правилами технической эксплуатации электроустановок потребителей.
Ответственность за технику безопасности при проведении испытаний возлагается на лицо ответственное за проведение испытаний.
6 МЕТОДЫ ИСПЫТАНИЙ
6.1 Проверка комплектности документации и первичная идентификация материала.
6.1.1 Комплектность предъявляемой на испытания документации проводится на соответствие 4.3.
6.1.2 Первичная идентификация материалов проводится органолептическим методом по ГОСТ Р 51293 и включает в себя:
- описание внешнего вида;
- определение толщины;
- иные идентификационные признаки.
6.2 Контроль толщины материала допускается проводить штангенциркулем или толщиномером.
6.2.1 Контроль толщины образца материала с использованием штангенциркуля.
Толщина материала контролируется штангенциркулем по ГОСТ 166. Один образец по 5.1 подвергается испытанию в 5 точках (местах) отстоящих один от другого на расстояние не менее 10 мм.
За результаты измерения принимается среднее арифметическое значение пяти измерений.
Результаты испытаний считаются положительными, если среднеарифметическое значение толщины не превышает соответствующую толщину в соответствии с требованиями 4.1.
6.2.2 Контроль толщины образца материала с использованием толщиномера.
Толщина образцов материала контролируется толщиномером. Испытанию подвергаются три образца материала.
Каждый из 3-х образцов наклеивается на стальную подложку толщиной 1мм. Геометрические размеры подложек должны соответствовать размерам образцов материала + 1 мм.
За результаты измерения принимается среднее арифметическое значение 3 измерений.
6.3. Испытание поверхностной плотности
Поверхностная плотность материала в кг/м2 определяется как отношение общей массы к площади поверхности по. ГОСТ Р 50277.
Контроль массы образцов производится на весах лабораторных электронных AND GH-200 или на аналогичных им весах.
Испытанию подвергаются 3 образца уплотнителя.
За единицу поверхности образца материала принимается 1000 мм2 в соответствии с 5.1.
За результаты измерения принимается среднее арифметическое значение по трем измерениям.
Результаты испытаний считаются положительными, если среднеарифметическое значение поверхностной плотности не превышает соответствующую величину в соответствии с 4.1.
6.4 Идентификация с использованием термогравиметрии
Испытания проводятся с использованием аппаратуры термического анализа (ТА).
Для испытаний используется аппаратура термического анализа - термоанализатор SDT Q 600 или аналогичная по своим техническим характеристикам.
Условия нагревания:
- линейный нагрев от 30◦С до 1000◦С со скоростью 20◦С/мин в атмосфере инертного газа(азот) со сменой на воздух при температуре 850◦С 0С;
- масса навески от 3 до 7мг в форме диска.
Порядок проведения испытаний, идентификация по полученным характеристикам ТА и представление результатов проводятся по ГОСТ Р 53293.
Примечание: скорость нагревания, предельная температура нагрева, время нагрева, масса навески выбираются с учетом вспучивания материала, таким образом, чтобы отсутствовал перелив вспученного образца через край тигля.
Критериями идентификации служат термогравиметрические характеристики (ТГ) потери массы при фиксированных температурах, температуры при фиксированных потерях массы, температуры и координаты(температура и амплитуда) максимумов дифференциальных кривых потери массы (ДТГ), а также величины коксовых и зольных остатков. ТГ и ДТГ кривые представляются в виде характерных графических зависимостей (Приложение Б). Проводится не менее двух съемок образцов материалов.
6.5 Испытание по определению коэффициента вспучивания при нагреве
6.5.1 Сущность метода испытаний заключается в определении коэффициента вспучивания - К, которое вычисляется как отношение толщины вспученного образца материала в миллиметрах, полученного при нагреве в течении не менее 30 минут при температуре вспучивания.
Примечание: Температуру вспучивания рекомендуется выбирать с учетом термограммометрического анализа.
Испытания проводятся с использованием дифференциально-термического анализатора ДТА – 850, входящего в термоаналитический комплекс «Du Pont – 9900», которое имеет компьютер, программное обеспечение для записи температурного режима печи и управления скоростью нагревания.
6.5.2 Требования к образцам для испытания давления вспучивания.
Испытания проводятся на 3 образцах диаметром 3мм; толщина собственная.
6.5.3 Методика испытаний.
Перед началом испытаний производится измерение толщин образцов по 6.2.1. Затем вырубаются 3 образца по 6.5.1. Затем каждый образец размещают в стеклянной капсуле с внешним диаметром 3.2мм. Образец нагружают дополнительным грузом не более 0,01Н. Между образцом и грузом помещают прокладку из фольги. Затем капсула помещается в ячейку нагревательного блока ДТА - 850. Схема дифференциально-термического анализатора ДТА – 850 приведена в Приложении В.
Нагревание образца материала проводится от окружающей температуры до температуры по 6.5.1 и выдержке в течение 30мин. Капсула с образцом извлекается из ячейки через 30 минут после начала испытания. Образец остывает и по достижению температуры окружающей среды и производится измерение толщины вспученного образца с использованием линейки по ГОСТ 427.
Испытанию подвергаются 3 образца.
Коэффициент вспучивания определяется по формуле:

δ0, мм – первоначальная толщина образца
δ1, мм - толщина образца после вспучивания.
Результаты расчета коэффициента вспучивания материала считаются положительными, если все значения кратности находятся в поле допуска соответствующего показателя в соответствии с требованиями 4.1.
Если результаты хотя бы одного расчетного показателя кратности не укладываются в допуск, результаты испытаний признаются отрицательными.
6.6 Испытание по определению давления вспучивания
Сущность метода определения давления вспучивания (Р0, Н/мм2) заключается в определении функции (зависимости) величины вспучивания образца материала (Δi, мм) при нагревании от величины последовательно задаваемой нагрузки (Fi, г), нахождения уравнения регрессии в виде линейной функции Δ = a + b∙F (a и b определяются с использованием программ графических редакторов) и определения нагрузки (F0, г), при которой величина вспучивания Δ0=0мм (т.е имеет место отсутствие вспучивания).
6.6.1 Требования к образцам для испытания давления вспучивания.
Испытания проводятся на образцах диаметром 3м и собственной толщиной.
6.6.2 Испытательное оборудование включает в себя:
- термоанализатор ДТА-850;
- стеклянная капсула с образцом;
- шток керамический;
- индикатор часового типа с диапазоном измерения не менее 0÷30мм и измерительным усилием не более 0.01Н;
- набор разновесов от1г до 100г.
- платформа для расположения разновесов.
Схема нагружения образца утеплителя представлена в Приложении Г.
В качестве нагрузки используется набор разновесов массой от 1г до 100г.
6.6.3 Условия испытаний.
Испытания для определения давления вспучивания уплотнителя проводятся при температуре по 6.5.1 и выдержке в течение не менее 30мин.
Температура программатора печи контролируется платинелевой термопарой, образца материала хромель-алюмелевой термопарой (Приложение В).
6.6.4 Методика испытания.
Испытание проводится в следующей последовательности:
- образец помещается в стеклянную капсулу;
- капсула с образцом загружается в ячейку нагреваемого блока;
- внутрь капсулы помещается шток с платформой;
-на платформу ставится груз (Fi), создающий давление Рi на образец;
- на плоскость платформы устанавливается удлинитель индикатора часового типа в соответствии со схемой приведенной в Приложении Г. При соприкосновении удлинителя и платформы показание индикатора «обнуляется»;
- проводится нагревание образца по 6.6.3;
- на индикаторе часового типа фиксируется максимальное значение при нагревании и расширении образца в капсуле;
- испытания проводятся последовательно при разных нагрузках (20, 50 и 100г);
- величина вспучивания в миллиметрах ;
По результатам испытаний составляется таблица 2.
Таблица 2
Нагрузка Fi, г | F1 | F2 | F3 |
Величина вспучивания Δi, мм | Δ1 | Δ2 | Δ3 |
Продолжение таблицы 2
Уравнение регрессии(при линейной аппроксимации) | Δ = a + b∙F |
Коэффициент детерминации | Не менее 0.93 |
Расчетная нагрузка F0(г) при Δ=0 | F0 = - а/b |
Расчетная площадь штока S, мм2 | S = (π ∙d2 )/4 (где d – диаметр штока) |
Расчетное давление вспучивания (P0, H/мм2) при Δ=0мм | P0 = F0∙g / 1000∙S, g – ускорение свободного падения |
По результатам испытаний образцов проводится расчет давления вспенивания в Н/мм2 по формулам таблицы 2.
Результаты расчета давления вспучивания материала считаются положительными, если все значения давления находятся в поле допуска соответствующего показателя в соответствии с 4.1.
Если результаты хотя бы одного расчетного показателя давления вспенивания не укладываются в допуск, результаты испытаний признаются отрицательными.
7 ПРЕДСТАВЛЕНИЕ РЕЗУЛЬТАТОВ ИСПЫТАНИЙ
По результатам испытаний составляют протокол и пояснительную записку к нему.
Протокол испытаний должен содержать следующие данные:
- наименование организации, проводящей испытания;
- полный адрес организации, проводящей испытания;
- наименование организаций заказчика и изготовителя материала, подлежащего испытанию, с указанием их полных адресов;
- наименование материала, его маркировку с указанием нормативного документа;
- дату выработки партии материала;
- идентификационные признаки материала по ГОСТ Р 51293:
- дату проведения испытания;
- обозначение нормативного документа на метод испытания;
- применяемые средства измерений и испытательное оборудование;
- виды и перечень воздействий;
- результаты испытания;
- заключение.
Пояснительная записка к протоколу испытаний должна состоять из титульного листа, основной части и обязательных приложений.
Титульный лист должен содержать следующие данные:
- наименование организации, проводящей испытания;
- полный адрес организации, проводящей испытания;
- наименование организаций заказчика и изготовителя материала, подлежащего испытанию, с указанием их полных адресов;
- наименование материала, его маркировка с указанием нормативного документа на этот материал;
- дату проведения испытания;
- обозначение нормативных документов на методы испытаний.
Основная часть должна включать следующие разделы:
- характеристика объекта испытаний с указанием основных размеров испытываемых образцов, описанием материала и способом его применения на образце;
- метод испытаний с указанием основных предельных состояний испытываемых образцов;
- процедура испытаний (условия окружающей среды и порядок проведения испытаний);
- испытательное оборудование, средства измерения и регистрации параметров с указанием типов приборов, диапазона их измерений, погрешности измерений и срока очередной поверки;
- результаты испытаний (результаты визуального наблюдения за поведением образцов в ходе проведения испытаний);
- результаты анализа экспериментальных данных;
- выводы.
Обязательные приложения должны содержать следующие сведения:
- график изменения температуры в печи;
- графики термогравиметрических характеристик;
- фотоснимки образцов после испытания.
Приложение А
(рекомендованное)
Перечень средств измерений
1. Штангенциркуль по ГОСТ 166 или толщиномер с погрешностью измерения ±0,5%;
2. Линейка металлическая по ГОСТ 427 с пределом измерения не менее 300мм;
3. Весы лабораторные электронные AND GH 200, погрешностью измерения ± 0,1 мг;
4. Индикатор часового типа с диапазоном измерения не менее 0÷30мм и измерительным усилием не более 0.01Н;
5. Термоанализатор совмещенный SDT Q600 для получения идентификационных характеристик вспучивания.
6.Термоанализатор «DuPont – 9900» с печью ДТА - 850
Основные технические характеристики
Диапазон температур до 1500°C
Калибровка шкалы температур Металлические стандарты (от 1 до 5 точек)
Контроль атмосферы образца;
Скорость нагрева – до 10000 C -от 0.1 до 100° C/мин; скорость нагрева – до 15000C - от 0.1 до 25° C/мин;
Охлаждение печи - принудительное воздушное, от 1500 до 50°C за < 30 мин
Конструкция весов: Двухчашечные, горизонтальные
Масса образца - до 200 мг (350 мг вместе с держателем образца)
Чувствительность весов - 0.1 мкг
Калориметрическая точность/воспроизводимость 2% (по металлическим стандартам)
Чувствительность ДТА 0.001°C; Термопары Pt / PtRh (тип R)
Вакуум до 7 Па (0.05 тор) .
Тигли Платиновые: 40 мкл, 110 мкл, керамические (Al2O3): 40 мкл, 90 мкл:
Приложение Б
(справочное)
Форма представления критериев идентификации по ГОСТ Р 53293
Р
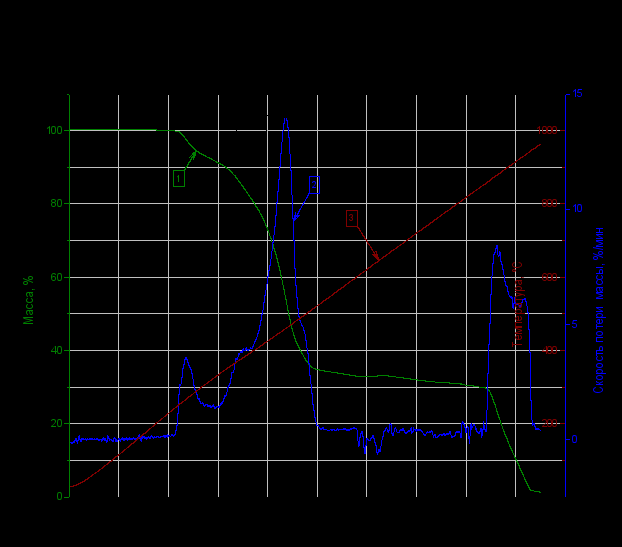
Приложение В
(справочное)
Схема печи ДТА – 850 термоанализатора «DuPont – 9900»
![]() | |
Рисунок В1 Схема расположения термопар в нагревательном блоке ДТА - 850 S – место (ячейка), в которое помещается стеклянная капсула с образцом; R – термопара образца сравнения; C – контрольная термопара. |
Приложение Г
(справочное)
Схема измерения давления вспучивания
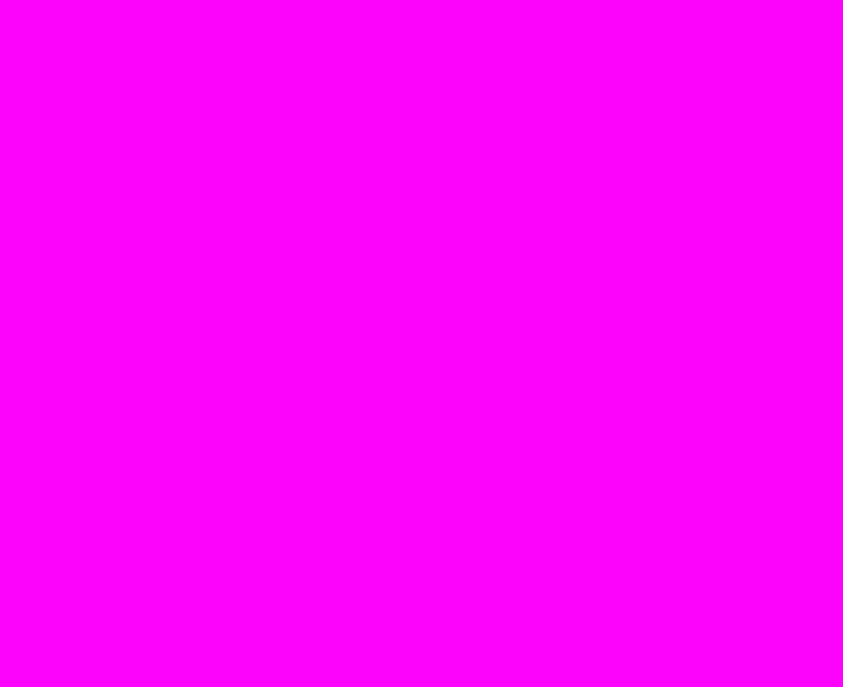
Рисунок Г1. Схема измерения величины вспучивания Δi в термоанализаторе ДТА-850 при нагрузке Fi