Ф. У. Харрис. Экономичный размер заказа
Вид материала | Документы |
- Сьюзен Виггс «Дом у озера», 3783.76kb.
- Условия и размер предоставления скидок, 247.71kb.
- Создание кроссворда в Microsoft Excel, 36.47kb.
- Правила оформления тезисов доклада, 26.87kb.
- Лекция 13 Потребитель «Потребитель король рынка», 57.33kb.
- Список литературы, рекомендуемой для чтения летом, 15.95kb.
- Лекция: Виртуальная память. Архитектурные средства поддержки виртуальной памяти, 156.96kb.
- За счет средств краевого бюджета Размер субсидии, 97.01kb.
- Министерство образования и науки, молодежи и спорта Украины, 56.14kb.
- Годовой отчет ОАО "аниитиву" за 2011 год Основные показатели работы Общества за год, 134.35kb.
Ф. У. Харрис. Экономичный размер заказа
О контроле за производством продукции начали задумываться только с начала XIX века. Первая полная система контроля была внедрена на заводе в Уотертауне в 1880 году. Первоначально промышленников интересовало, прежде всего, наиболее эффективное управление собственными линиями, а точнее - чтобы на складе всегда были материалы, необходимые для производства товаров; иными словами, чтобы линии не простаивали. Чтобы достичь оптимального уровня загруженности линии, естественно, требуется решить задачу планирования производства.
В 1915 году Харрис изобретает EOQ (economic order quantity) - одну из первых моделей оптимального определения объема заказа (производственного или на закупку), которая позволяет сократить издержки на возобновление и хранение запасов материалов, полуфабрикатов или готовой продукции. В 1934 году Уилсон вводит понятие точки (пере)заказа - ROP (reorder point). В течение довольно долгого времени главным для промышленников при оптимизации производства является умелое сочетание моделей EOQ и ROP. Если предположить, что мы производим товар, который пользуется постоянным спросом, а поставщики нас никогда не подводят, то с расчетом показателей EOQ и ROP справится даже ребенок. Так, экономичный объем заказа рассчитывается по формуле
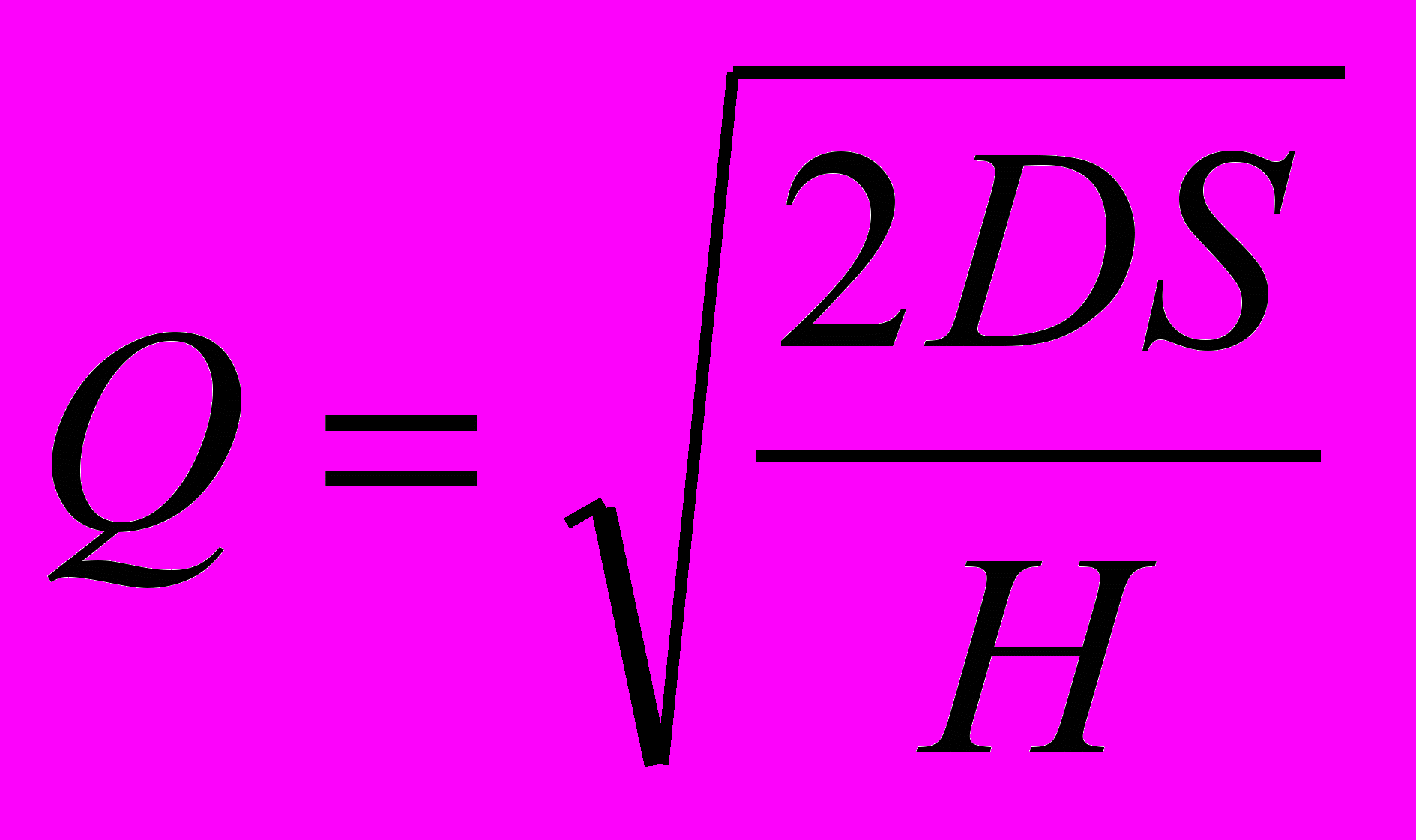
D - объем годового производства нашего товара,
S - стоимость заказа,
H - стоимость хранения единицы продукции в течение года.
Точка перезаказа в этом случае рассчитывается не намного сложнее.
Понятие ROP позволяет определить момент времени, когда запасы предприятия становятся меньше допустимого уровня и требуется инициировать их возобновление. К началу сороковых было создано довольно много разработок, позволяющих оптимизировать производство и запланировать требуемый объем выдаваемой на-гора продукции.
И только благодаря использованию связки EOQ и ROP удалось добиться снижения загруженности складских помещений на 15%, что, разумеется, привело к снижению производственных затрат (в некоторых случаях - до 20%).
Уолтер Шьюхарт. Тотальное управление качеством
Руководствуясь новаторскими концепциями Деминга (1993), Джурана (1988) и ряда других авторов, японские руководители и инженеры взяли на вооружение методы, которые в конечном итоге преобразовались во всеобъемлющую систему управления, основанную на базовой концепции качества.
В принципиальном плане эта система являет собой новое слово в образе мышления.
Традиционная точка зрения гласила, что качество должно уравновешиваться затратами на его обеспечение.
Деминг и Джуран настаивали на том, что повышение качества ведет к снижению общих затрат и что системный подход к совершенствованию технологических процессов будет содействовать решению обеих задач.
Японские руководители приняли эту управленческую концепцию, инженеры обучились методам статистического контроля качества и применили их на практике, рабочие прошли соответствующую подготовку и включились в процесс технологического совершенствования, и в результате произошел резкий качественный скачок (Ишикава 1985; Имаи 1986).
К началу 80-х годов руководители в Европе и Америке, стремясь остановить разрушение своих традиционных рынков и расширить свою долю в мировой экономике, приступили к поиску путей восстановления прежней конкурентоспособности.
В течение последующих 15 лет все больше и больше компаний приходили к пониманию принципов, лежащих в основе управления качеством, и применяли их на практике – сначала в промышленном производстве, а затем и в сфере обслуживания.
Указанная управленческая система имеет множество названий, однако наиболее других распространена формула “тотальное управление качеством” (ТУК). Исключением является область здравоохранения, в которой наиболее часто используется термин “непрерывное повышение качества” (НПК).
Система ТУК существует во многих вариантах, однако важно другое - осознать ее именно как систему, включающую в себя одновременно и управленческую концепцию, и эффективный комплекс средств повышения производительности технологических процессов.
Общие элементы концепции тотального управления качеством (Файгенбаум, 1991; Манн, 1989; Сенге, 1991):
- приоритетное внимание качеству
- акцент на удовлетворение потребностей клиента ("удовлетворение клиента")
- обязательное участие и включение сотрудника в процесс повышения качества ("наделение полномочиями")
- подход к организации как к системе ("оптимизация")
- отслеживание статистических показателей технологических процессов ("управление по факту")
- руководство ("видение")
- повышенное внимание подготовке сотрудников ("превращение в самообучающуюся организацию").
Сбор статистических данных является стандартным и основополагающим шагом, предпринимаемым работниками и специальными группами для выявления путей совершенствования технологического процесса. Деминг и другие исследователи разработали указанные методы путем адаптации более ранних работ Шьюхарта, выполненных в 20-е годы (Шмидт и Финниган, 1992).
К наиболее эффективным средствам ТУК относятся:
(а) график Парето – графический метод для выявления наиболее часто встречающихся проблем, которые соответственно требуют первостепенного внимания;
(б) график статистического контроля – аналитический метод для подтверждения степени варьирования в рамках неусовершенствованного процесса;
(в) схема последовательности операций – метод объективного документирования хода процесса в текущий момент.
По-видимому, наиболее распространенным и важным в этом плане инструментом является диаграмма Ишикавы (или диаграмма “рыбья кость”), право авторства на которую принадлежит Каору Ишикаве (1985). Этот метод являет собой простое и в то же время эффективное средство, предоставляющее членам рабочей группы возможность эффективно взаимодействовать в выявлении основных причин порочности изучаемого процесса и таким образом намечать пути для его совершенствования.
В случае ее реальной реализации, концепция ТУК может по многим направлениям сыграть важную роль и для самих работников, и для сохранения их здоровья. Например, принятие на программы ТУК способно производить косвенное воздействие. В самом широком смысле организация, осуществляющая качественные преобразования, значительно повышает шансы на экономическое выживание как свои собственные, так и своих сотрудников. Более того, в основе деятельности такой компании, скорее всего, будет лежать уважение к коллективу.
Эксперты в области тотального управления качеством часто говорят об “общих ценностях”, которые должны быть стержнем в поведении и руководства, и кадрового состава организации. Эти идеи официально распространяются внутри организации и, как правило, включают выраженные в эмоциональной форме понятия типа “доверие”, взаимное уважение”, “открытость контактов” и “уважение к нашим отличиям” (Ховард, 1990).
Таким образом, мы оказываемся перед возможностью предположить, что качественные рабочие места будут “благоприятны для работника”, причем усовершенствованные самим работником процессы становятся менее опасны, а общий климат менее сопряжен со стрессом.
Логика повышения качества заключается во встраивании качества в продукцию или услугу, а не в выявлении провалов постфактум. Все это можно суммировать одним словом – упреждение (Уидфельдт и Уидфельдт, 1992). Такая логика недвусмысленно совместима с логикой охраны здоровья, которая акцентирует внимание на предотвращении профессиональных заболеваний. Уильямс (1993) приводит следующий гипотетический пример – «если улучшить качество и дизайн отливок в литейном производстве, снизится воздействие вибрации, поскольку снизится необходимость в отделке отливок».
Второй этап. Система Тейлора дала великолепный механизм управления качеством каждого конкретного изделия (деталь, сборочная единица). Однако продукция – это результат осуществления производственных процессов, и вскоре стало ясно, что управлять надо процессами.
В 1924 г. в «Bell Telephone Laboratories» (ныне корпорация AT&T) была создана группа под руководством Р.Л. Джонса, заложившая основы статистического управления качеством. Это были разработки контрольных карт, выполненные В. Шухартом, первые понятия и таблицы выборочного контроля качества, разработанные Г. Доджем и Г. Ромингом, ставшие началом статистических методов управления качеством, которые в последствии благодаря Э. Демингу получили очень широкое распространение в Японии и оказали весьма существенное влияние на экономическую революцию в этой стране.
Деминг выдвигает идею об отмене оценки заданий и результатов выполнения работы, т. к. по его мнению, они создают атмосферу страха, способствуют краткосрочному вкладу в работу, игнорируя долгосрочные задачи, и разрушают работу в командах. Опираясь на точку зрения Э. Деминга и развивая ее, Д. Джуран ввел термин качества в духе «соответствия требованиям потребителя», в значительной степени ориентированный на требования потребителей, («Fitness for use»). Он показал ответственность менеджмента за хронические последствия несоответствий и дополнил статистические методы контроля качества систематическими методами решения проблем качества.
В то время, как в работах Деминга основное внимание уделяется улучшению качества применительно прежде всего к процессам, системам и статистике, Джуран подчеркивает необходимость для каждого менеджера непосредственно заниматься деятельностью, приводящей к повышению качества. Он является сторонником подхода, который предусматривает вовлеченность всего персонала организации в процедуры, обеспечивающие повышение качества и решение производственных проблем. Системы качества усложнились, т. к. в них были включены службы, использующие статистические методы. Усложнились и задачи в области качества, решаемые конструкторами, технологами и рабочими, понимающими, что такое вариации и изменчивость, а также знающими, какими методами можно достигнуть их уменьшения. Появилась специальность — инженер по качеству, который должен анализировать качество и причины дефектов изделий, строить контрольные карты и т. п. В целом акцент с инспекции и выявления дефектов был перенесен на их предупреждение путем определения причин дефектов и их устранения на основе изучения процессов и управления ими.
Более сложной стала мотивация труда, т. к. теперь учитывалась точность настроенности процесса, анализ тех или иных контрольных карт, карт регулирования и контроля. К профессиональному обучению добавилось обучение статистическим методам анализа, регулирования и контроля. Стали более сложными и отношения поставщик — потребитель. В них большую роль начали играть стандартные таблицы и статистический приемочный контроль.
- Мэйо