Тезисы Одесский национальный университет имени И. И. Мечникова
Вид материала | Тезисы |
- Научный, 8.03kb.
- Учебное пособие одесский национальный университет имени И. И. Мечникова 2010 ббк 83., 3007.67kb.
- Украины Одесский Национальный политехнический университет Кафедра «Информационные системы, 334.62kb.
- С задачами и упражнениями, 4649.95kb.
- Одесский Национальный Политехнический Университет Программное обеспечение автоматизированных, 41.53kb.
- Одесский Национальный Политехнический Университет курсовая, 457.95kb.
- Национальный Университет Узбекистана имени Мирзо Улугбека Номер паспорта: 30 Полное, 152.58kb.
- Одесский Национальный Политехнический Университет курсовая, 433.89kb.
- Положение о премировании работников ргкп «Евразийский национальный университет имени, 60.28kb.
- Конференция пит-2010 проведена на базе Самарского государственного аэрокосмического, 176.83kb.
Разработка противофильтрационного экрана для полигона захоронения отходов металлургии
Пугин К.Г.
Пермский государственный технический университет,
г. Пермь, Россия
Металлургия является источником большого количества твердых отходов от 5 до 2 класса опасности. При выплавке 1 тонны чугуна образуется до 0,5 тон отходов, которые необходимо утилизировать. В настоящее время металлургические комбинаты используют до 90% шлака 4 категории опасности оставшийся объем необходимо утилизировать на специализированных полигонах.
Основой любого полигона является его основание. Основная характеристика основания это фильтрационная способность, которая в идеале должна стремиться к нулю. Подбор составов для оснований полигонов захоронения отходов металлургии является актуальной задачей. На кафедре ООС Пермского гос. техн. университета произведен подбор состава для противофильтрационного слоя полигона утилизации с использованием лигнинсодержащими отходами.
Источниками лигнинсодержащих отходов являются гидролизные производства и целлюлозно-бумажная промышленность. Выход лигнина после гидролиза углеводов составляет 30-40% от перерабатываемого сырья, а в целлюлозно-бумажной промышленности лигнин составляет 20-30% от веса перерабатываемой древесины.
Исследованы физико-химические и противофильтрационные свойства образцов глинистых экранов. Выявлены гидрофобные свойства глинистого грунта, обработанного лигносульфонатами ЦБК «Кама», а также установлены противофильтрационные характеристики глинистых грунтов (таблица), обработанных лигнинсодержащими отходами и модифицированными лигнинсодержащими отходами.
№ обр. | Характеристики образца (состав) | Влажность набухания, % | Набуха ние, % | Коэффициент фильтрации, м/сут. | |
1 | 2 | 3 | 4 | 5 | |
1 | Глина природная нарушенная – 100 % (влажность 16 %) | 17 | 120 | 1,15∙10-5 | |
2 | Глина – 75,8 % Нитролигносульфонаты – 24 % | 23,4 | 640 | 1,11∙10-7 | |
3 | Глина – 83,3 % Нитролигносульфонаты – 16% | 27,2 | 850 | 1,11∙10-7 | |
4 | Глина – 86,2 % Нитролигнин - 13,8 % | 24,2 | 650 | 1,12∙10-7 |
Глинистые грунты, обработанные нитролигносульфонатами, нитролигнином имеют величину набухания в 6-8 раз большую, чем природная глина. Глинистые грунты, обработанные лигносульфонатами имеют достаточно низкую величину набухания, что говорит о гидрофобных свойствах данного материала.
При обработке глинистого грунта лигносульфонатами, нитролигносульфонатами, нитролигнином коэффициент фильтрации грунта снижается в 100 раз, что говорит о возможности использования данных свойств при создании противофильтрационных экранов полигон твердых бытовых отходов.
Результаты работы могут найти применение в получении противофильтрационных материалов для полигонов твердых отходов металлургии и бытовых отходов.
УДК 621.357.7
РЕГЕНЕРАЦИЯ СЕРЕБРА ИЗ ОТХОДОВ ФОТО- , КИНО-
И ПОЛИГРАФИЧЕСКИХ МАТЕРИАЛОВ
Смирнова О.Л., Дерибо С.Г., Глушкова М.А., Мишина Е.Б.
НТУ “ХПИ”, г. Харьков, Украина
В настоящее время серебро – это важнейший составной элемент при производстве светочувствительных материалов. Ежегодно на эти цели расходуется несколько тысяч тонн металла общей стоимостью более 500 млн. долларов. Использованные фото-, кино- и полиграфические материалы представляют собой ценное вторичное сырье для получения вторичного серебра, запасы которого не безграничны, а объем его потребления в различных отраслях промышленности на сегодняшний день значительно превышает уровень его добычи из руд. Высокие концентрации соединений серебра опасны для здоровья, а обычные очистные сооружения не в состоянии обезвредить воду, в которой эти ионы окажутся, если сливать отработанные реактивы в канализацию. Поэтому полное извлечение серебра из промышленных отходов является важной экономической и экологической задачей.
В литературе достаточно широко описаны процессы и оборудование для извлечения серебра из жидких и твердых отходов. Однако, присущие им недостатки, а именно: дефицитность реактивов, токсичность промежуточных и конечных продуктов выделения, технологическая сложность процессов, высокая стоимость оборудования, делают их трудно осуществимыми на практике, особенно для малых форм производств фото-, кино- и полиграфической индустрии.
В работе изучены процессы получения серебра высокой чистоты из материалов, к которым относятся отработанные фиксажные растворы и полиграфические пленки. На основании проведенных экспериментальных исследований разработаны технологии, включающие в себя сочетание простых, но эффективных методов получения серебряного порошка чистотой 99, 98 %.
Процесс регенерации серебра из фиксажных растворов, в которых содержание металла составляет от 5 до 8 г/л, предусматривает вытеснение серебра из раствора латунными пластинами. Полученный порошок серебра последовательно отделяется от пластин, собирается, отмывается от примесей цинка и меди разбавленными растворами кислоты и щелочи с промежуточными промывками водой. Подобраны оптимальное соотношение рабочей поверхности пластин, объема фиксажного раствора и время выделения серебра контактным способом. К достоинствам данного метода следует отнести простоту проведения процесса и отсутствие выделения сероводорода, являющегося весьма токсичным продуктом.
Извлечение серебра из эмульсионного слоя полиграфических пленок предлагается осуществлять за счет растворения последнего в разбавленной азотной кислоте при температуре 70 - 800С. Основа пленки при этом не подвергается разрушению. Последующее охлаждение раствора, отделение желатины, осаждение хлорида серебра и восстановление его формалином до металла позволяют получить с 1 м2 пленки до 6 - 7 г серебра в виде порошка (с 1 кг пленки не менее 10 г серебра).
Таким образом, предложенные технологии отличаются простотой, эффективностью, экономичностью и практической доступностью для широкого круга потребителей, позволяют значительно сэкономить ценный металл с последующим возвращением его в государственный фонд.
УДК 502.174
МЕМБРАННИЙ ЕЛЕКТРОЛІЗЕР ДЛЯ ВИЛУЧЕННЯ ІОНІВ КОЛЬОРОВИХ МЕТАЛІВ З ВІДПРАЦЬОВАНИХ ТЕХНОЛОГІЧНИХ РОЗЧИНІВ
*Тевтуль Я.Ю., *Нечипоренко О.В., **Гутт С., **Сучавський М.
*Чернівецький національний університет імені Юрія Федьковича,
м. Чернівці, Україна
** «Штефан чел Маре» університет, м. Сучава, Румунія
Зменшення викидів шкідливих речовин у об’єкти довкілля – важливе завдання сьогодення. Зокрема це стосується попередження забруднення природних вод і грунтів сполуками кольорових металів у зв’язку з можливим попаданням токсичних катіонів у ланцюги харчування тварин і людей та їх негативним впливом на здоров’я людини.
Мідь, нікель, кобальт та їх сплави широко використовуються у приладо- і машинобудуванні. Вельми поширені технологічні процеси травлення деталей з цих металів і сплавів, які супроводжуються утворенням великих об’ємів відпрацьованих технологічних розчинів.
Відомо низку методів зменшення викидів шкідливих речовин у довкілля. Серед них досить поширені хімічні – утворення й вилучення малорозчинних сполук катіонів металів. Належним чином розроблені методи адсорбційні, іонообмінні, електрохімічні, які крім позитивних рис мають і деякі недоліки. Зокрема це стосується втрати властивостей технологічних розчинів й необхідності витрачати реактиви на приготування свіжих сумішей хімічних речовин. Для уникнення цього недоліку застосовують способи регенерації відпрацьованих технологічних розчинів.
Для регенерації відпрацьованих хлоридних розчинів травлення міді пропонуємо використовувати мембранний електролізер. Його можна застосовувати для поновлення властивостей розчинів травлення на основі гідроген пероксиду і хлоридної кислоти, купрум(ІІ) хлориду, калій хлориду і хлоридної кислоти чи інших.
Зроблено аналіз складу комплексних сполук Купруму, що утворюються у хлориднокислих розчинах травлення міді. Для прогнозу параметрів електрохімічної регенерації відпрацьованих розчинів травлення міді проведено вольтамперні обстеження. Свіжоприготовлені розчини травлення міді містили (г/л): CuCl2∙2H2O–160÷200, KCl–250÷300, HCl–9÷12. Під час розчинення міді у розчинах зі значним вмістом калій хлориду велика ймовірність утворення комплексу K2CuCl3 і подальше його перетворення у сполуку купрум(ІІ). Вміст іонів Купруму у відпрацьованих розчинах травлення міді дорівнював 70,0÷90,6 г/л у складі комплексних сполук купрум(І) і купрум(ІІ).
Для регенерації розчинів травлення міді шляхом вилучення іонів Купруму з відпрацьованих розчинів використано як двокамерний так і трьохкамерний електролізери, у яких католіт і аноліт розділені катіонообмінною мембраною. Католіт – відпрацьовані розчини травлення, катод мідний. Анод нерозчинний – титан, покритий рутеній(ІУ) оксидом чи манган(ІУ) оксидом. Аноліт – водні розчини сульфатної кислоти чи натрій сульфату. Вилучення іонів Купруму проводили до досягнення їх вмісту у свіжоприготовлених розчинах травлення міді. Авторські права на електролізер захищені патентом України.
Визначено умови, за яких можна отримувати щільні чи порошкові осади міді, вплив густини струму на вихід за струмом металу, питому витрату електроенергії та інші. Встановлено, що швидкість травлення міді у свіжоприготовленому і регенерованому розчині травлення збігаються.
Використання мембранного електролізеру дозволяє не тільки попередити викиди іонів Купруму у об’єкти довкілля, але й створити ресурсозберігаючий процес.
УДК 669.791.3.
ВАКУУМТЕРМИЧЕСКАЯ ДЕМЕРКУРИЗАЦИЯ ОТРАБОТАННЫХ ЛЮМИНИСЦЕНТНЫХ ЛАМП
Требухов С.А., Храпунов В.Е., Исакова Р.А., Марки И.А
АО «Центр наук о Земле, металлургии и обогащения»,
г. Алматы, Республика Казахстан
Люминесцентные лампы дневного света являются наиболее экономичными по потребляемой электрической энергии и получили широкое применение во многих странах мира. В связи с тем, что в настоящее время из-за практически полного отсутствия их утилизации во многих странах сложилась сложная экологическая обстановка, связанная с ртутным загрязнением окружающей среды.
Разработанные АО «ЦНЗМО» вакуумтермическая технология и непрерывно действующая вибровакуумная установка для переработки ртутьсодержащего минерального и техногенного сырья не имеют аналогов в мировой практике, содержат значительное количество элементов ноу-хау и позволяют извлечь более 99% ртути из различных отработанных приборов, изделий и отходов металлургической, химической и теплоэнергетической промышленности с получением её в виде товарного металла, соответствующего марке Р3, и удовлетворяют современным требованиям к экологической безопасности. При переработке ртутьсодержащих материалов по предлагаемому способу полученные отвальные продукты (огарки, содержание Hg не более 0,01 %) и выбрасываемые в атмосферу технологические газы по содержанию ртути соответствуют международным стандартам (менее 0,01 мг/м3).
Процесс демеркуризации осуществляется в вакууме при давлении 1,33-4,0 кПа, температуре 350-450оС из виброожиженного слоя материала. Виброожижение слоя осуществляется наложением на него вертикальных и дополнительно горизонтальных колебаний частотой 16-50 Гц и амплитудой 0,5-5,0 мм. При этом материал непрерывно перемещается через возгоночную зону и за 5-10 минут его пребывания в ней степень отгонки ртути достигает более 99%. Это обусловлено тем, что все возгоночные процессы, протекающие в вакууме, характеризуются значительно большей скоростью, а виброожижение слоя ведёт к увеличению коэффициентов тепло-, массообмена в 5-7 раз по сравнению со стационарным слоем. Технология и аппаратура отработаны, испытаны в укрупнённом и опытно-промышленном масштабах, характеризуются небольшим расходом тепла (200-250 кВт ч/т), высокой надёжностью и эффективностью.
Преимущества предлагаемой технологии и непрерывно действующей аппаратуры по сравнению с используемыми в мировой практике методами переработки ртутьсодержащего сырья в вакууме в аппаратах периодического действия позволяют значительно повысить извлечение ртути в товарный продукт и резко сократить её механические потери и выбросы в окружающую среду. Кроме того, вакуумная технология является безреагентной, а её осуществление в непрерывно действующей аппаратуре позволяет существенно снизить непроизводительные затраты тепловой энергии, что характерно для периодических вакуумных аппаратов.
На основании проведённых исследований и технологических испытаний на опытной базе АО «Центр наук о Земле, металлургии и обогащения» создана пилотная вибровакуумная установка для утилизации отработанных ламп дневного света производительностью 50-60 тыс. штук в месяц.
УДК 621.357.7
ЭЛЕКТРОХИМИЧЕСКАЯ ПЕРЕРАБОТКА ЖИДКИХ И ТВЕРДЫХ МЕТАЛЛСОДЕРЖАЩИХ ОТХОДОВ С ПОЛУЧЕНИЕМ ТОВАРНЫХ ПРОДУКТОВ
Трубникова Л.В., Байрачный Б.И., Майзелис А.А.
НТУ «ХПИ», г. Харьков, Украина
Извлечение металлов из металлсодержащих отходов необходимо как для непосредственного обезвреживания содержащих ионы тяжелых металлов жидких отходов, так и для снижения потребности в более экологически вредном гидрометаллургическом производстве из исходных руд металлов, соответствующих количеству находящихся в твердых отходах. Срок окупаемости, да и сама возможность окупаемости затрат на реализацию процессов переработки зависит от используемой технологии, а также возможности эффективной утилизации полученного из отходов металла. Поэтому разработка технологических процессов, позволяющих перерабатывать металлсодержащие отходы с получением товарных продуктов является актуальной задачей.
На кафедре Технической электрохимии НТУ «ХПИ» разработан ряд электрохимических процессов:
- скоростной переработки медьсодержащих отходов с получением фосфорсодержащих анодов, при использовании которых в сернокислых электролитах меднения допустимая анодная плотность тока увеличивается в 2 раза, а электролит не загрязняется шламом;
- снятия медных покрытий с изделий из диэлектрика без образования вторичных отходов с одновременным осаждением меди на катоде;
- обработки промывных вод после нанесения гальванических покрытий из тетрафторборатных электролитов с обезвреживанием 95-98 % тетрафторборат-ионов и катодным извлечением чистых металлов из раствора ванны улавливания;
- формирования в процессе электролитического извлечения ионов меди из ванны улавливания электролита меднения электрода с электрохимически доступной развитой поверхностью;
- никелирования изделий из алюминиевых сплавов с нанесением подслоя никеля из ванны улавливания электролита никелирования, прочно сцепленного с основой;
- осаждения безпористого мультислойного медно-никелевого покрытия из ванн улавливания электролитов меднения и никелирования, позволяющего снижать толщину никелевого покрытия;
- извлечения металлов из ванн улавливания гальванических линий в виде анодных материалов;
- регенерации отработанных аммиачно-персульфатных растворов травления печатных плат с получением медных анодов;
- извлечения металлов в виде сплавов из шламов станций реагентной очистки гальванических стоков.
Разработанные технологические процессы извлечения металлов из металлсодержащих отходов с получением товарных продуктов в виде анодных материалов, сплавов и покрытий металлами и сплавами обеспечивают технико-экономическое стимулирование мероприятий по предотвращению загрязнения водного бассейна страны ионами тяжелых металлов.
УДК 622.7
флотация полиметаллической руды с применением Экологически безопасного наноразмерного активатора сфалерита на основе оксигидроксида меди
Тусупбаев Н.К., Семушкина Л.В., Калиева Р.С.,
Кайржанова Н.С.,Сулейменова У.Я.
АО «Центр наук о земле, металлургии и обогащения»,
г. Алматы, Казахстан
Полиметаллические руды – очень сложный объект обогащения, что обусловлено тесным взаимопрорастанием полезных компонентов и минералов пустой породы друг в друга. Основными полезными минералами таких руд являются халькопирит, галенит и сфалерит.
Известен способ обогащения медно-цинковых руд по схеме прямой селективной флотации. Из хвостов медной флотации после активации сфалерита медным купоросом получают цинковый концентрат. Такая схема применяется при флотации медно-цинковых вкрапленных и сплошных руд, в которых медные минералы представлены в основном халькопиритом, а сфалерит не активирован ионами меди. Такая флотация применялась на Сибайской фабрике (СССР), фабриках «Руттен», «Фокс», «Экстол» и «Квемонт» (Канада), а также на фабриках Финляндии и Норвегии [1,2]. Основными недостатками способа являются недостаточно высокое содержание цинка в цинковом концентрате и значительный расход активатора (до 800 г/т) при цинковой флотации [3].
В связи с этим создание наноразмерных экологически безопасных селективных активаторов дешевого неорганического происхождения взамен базовым реагентам является актуальной задачей. На основании проведенных исследований найден оптимальный способ получения наноразмерного активатора на основе оксигидроксида меди (II). Рентгено-фазовым анализом и методом ИК-спектроскопии установлено, что активатор оксигидроксид меди (II) находится в различных формах, в основном, в виде биядерных комплексов[4-6].
Использование предлагаемого способа флотации медно-свинцово-цинковых руд позволяет полностью заменить при цинковой флотации традиционный активатор медный купорос на новый активатор - оксигидроксид меди, что позволяет получить цинковый концентрат более высокого качества с меньшим расходом реагента. Активатор оксигидроксид меди ранее во флотационном обогащении полиметаллических руд не применялся. Получают его методом химической конденсации из растворов солей меди.
Исследования проводили на медно-свинцово-цинковой руде Артемьевского месторождения, содержание основных компонентов в которой составляет, масс. %: меди – 1,3-1,7; свинца – 2,3-2,8; цинка – 6,9-7,3.
Руду обогащали по схеме коллективной медно-свинцовой флотации с последующей флотацией цинковых минералов с получением цинкового концентрата. Схема включала медно-свинцовый цикл и цинковый цикл, состоящие из основной, контрольной и перечистной флотации. В схеме с использованием в качестве активатора сфалерита медного купороса, получили цинковый концентрат с содержанием цинка 33,85 %, меди 0,93 %, свинца 1,6 %.
В случае использования нового наноразмерного активатора оксигидроксида меди, расход его в основной цинковой флотации составил 200 г/т. При этом получен цинковый концентрат с содержанием цинка 52,7 %, меди 0,8 %, свинца 1,5 %.
Использование более активного оксигидроксида меди при цинковой флотации обеспечивает прирост содержания цинка в цинковом концентрате на 18,85 %, при этом расход реагента снижается в четыре раза.
Литература
1. Полькин С.И., Адамов Э.В. «Обогащение руд цветных металлов» - М.: Недра, 1983. - С.66 - 68.
2. Абрамов А. А. Флотационные методы обогащения. - М.: Недра, 1993. - 414 с.
3. Глембоцкий В.А., Классен В.И. Флотационные методы обогащения. - М.:Недра, 1981.- С. 288-289.
4. Шабанова Н.А., Попов В.В., Саркисов П.Д. Химия и технология нанодисперсных оксидов. - М., ИКЦ “Академкнига” . - 2007. 10с.
5. Сергеев Г.Б. Нанохимия. - Изд. Московского университета, 2007. – 336 с.
6. Carnes C.L., Klabunde K.J. // Langmuir. - 2000. - V.16. - P. 3764 - 3772.
УДК 622.7
изучение распределения редкоземельных элементов в труднообогатимой свинцово-цинковой руде
месторождения шалкия
Тусупбаев Н.К., Турысбеков Д.К., Семушкина Л.В., Кайржанова Н.С., Абсиметова Н.А.
АО «Центр наук о земле, металлургии и обогащения»,
г. Алматы, Казахстан
В Казахстане редкоземельные металлы, в частности, группы лантаноидов, содержатся в углистых свинцово-цинковых рудах, а также в лежалых хвостах и техногенном сырье. В Республике до сих пор не создана горнодобывающая и перерабатывающая промышленность из собственного редкоземельного сырья. В частности, «Иртышская редкоземельная компания» для производства редкоземельных металлов закупает сырье за рубежом, в основном в России.
Редкие металлы, обладающие комплексом специфических свойств (механических, оптических, магнитных, электрических и др.) играют существенную роль в техническом прогрессе многих отраслей промышленности, науки и техники. Их использование, особенно в виде высокочистых металлов, соединений и материалов на их основе, во многом определяет развитие электроники, автомобилестроения, авиации, космической, лазерной и ядерной техники. Разработка научных основ и технологий, позволяющих извлекать редкоземельные металлы в коллективный редкометальный концентрат из свинцовых, свинцово-цинковых и других руд, является актуальным направлением в области обогащения руд.
Проводилось много исследований по комплексной переработке труднообогатимой руды Шалкиинского месторождения [1-3], но большинство испытаний касалось извлечения цветных металлов (свинца и цинка).
Изучен вещественный состав руды месторождения «Шалкия» и формы нахождения редкоземельных элементов в ней. Анализировалось несколько проб руды, отобранных с верхнего и нижнего горизонтов месторождения. Руда этого месторождения относится к труднообогатимым из-за тонкой вкрапленности минералов, их тесного взаимопрорастания между собой и с породообразующими минералами, наличия тонких углистых веществ. Исследование вещественного состава руды проводилось минералогическим, спектральным, рентгенофазовым и химическим методами анализа. Радиометрический анализ руды показал, что содержание радиоактивных элементов находится в пределах нормы.
Результаты исследований показали присутствие в пробах руды следующих редкоземельных элементов – лантан, церий, иттрий, диспрозий, празеодим, неодим, гадолиний. Все эти элементы представлены в руде в виде оксидов. Содержание лантана в руде составило 1,8-4,0 г/т; церия – 38,6-66 г/т; иттрия – 4-5,8 г/т; диспрозия – 1,1-2,3 г/т; празеодима – 7,8-8,2 г/т; неодима – 2,6-4,7 г/т; гадолиния – 34,3-44,2 г/т.
Анализ показал большую рассеянность редкоземельных элементов в руде. Суммарное содержание РЗМ в руде в разных пробах составляет 100-120 г/т. Исследования показали, что основная доля редкоземельных элементов приходится на церий и гадолиний.
Литература
1. Бектурганов Н.С., Турысбеков Д. К., Тусупбаев Н.К., Муханова А.А., Барменшинова М. Б., Семушкина Л. В. О новом депрессоре углистых веществ при флотации труднообогатимых полиметаллических руд //Сборник материалов VI Конгресса обогатителей стран СНГ- Москва, 28-30 марта 2007 г. - II том - С.167-168.
2. Bekturganov N.S., Turysbekov D.K., Amirova M.D., Temirova S.S. New flotation modifiers used in complex ores processing. Proceedings of the XXIV International Mineral Processing Congress. Bejing, China, 24-28 September, 2008. Vol.2, P.1720-1727.
3. Турысбеков Д. К., Бектурганов Н.С., Тусупбаев Н.К., и др Способ переработки труднообогатимой тонковкрапленной свинцово-цинковой руды. //Предварительный патент №19554 РК. Заявка № 2006/0117.1 от 7.02.2006 г.
УДК 662.971.2
РАЗРАБОТКА ЭНЕРГОСБЕРЕГАЮЩЕГО РЕЖИМА ОТЖИГА БУНТОВ СТАЛЬНОЙ ПРОВОЛОКИ В КОЛПАКОВОЙ ЭЛЕКТРОПЕЧИ ТИПА СГЗ
Усенко Ю.И., Сапов В.Ф.,
НМетАУ, г. Днепропетровск, Украина,
Иванов В.И., Нестеренко Т.Н., Скачков В.А.,
ЗГИА, г. Запорожье, Украина
В условиях ОАО «Запорожский сталепрокатный завод» бунты проволоки марки БСтОМ в стопах отжигают в колпаковых электропечах типа СГЗ согласно режиму: нагрев при максимальной тепловой нагрузке до температуры 750С и охлаждение под отключенным колпаком до температуры 150С.
При отжиге по данной технологии нагрев проволоки характеризуется наличием существенного (до 100С) перепада температуры на наружной боковой поверхности бунтов по высоте стопы, что указывает на нерациональность использования установленной мощности нагревательного колпака. Как следствие, значительная часть нижнего бунта стопы не нагревается до заданного температурного уровня.
Результаты ряда исследований, проведенных на разработанной авторами электрической модели колпаковой электропечи, позволили установить необходимость перераспределения установленной мощности нагревательного колпака между его первой (нижней) и второй (верхней) зонами, а также выявить пути рационального размещения мощности нагревательных элементов по высоте первой зоны.
Как показали промышленные испытания модернизированной электропечи типа СГЗ, сосредоточение мощности нагревательного колпака в его нижней зоне с последующим перераспределением по ее высоте позволяет значительно улучшить равномерность подвода теплоты к наружным виткам бунтов проволоки. Однако наличие значительного разницы температуры (60…70С) по сечению стопы в конце периода нагрева исследуемой проволоки ограничивает скорость подъема температуры ее внутренних витков для всех бунтов. В связи с этим необходимо проведение комплекса исследований, связанных с выявлением рациональных температурно-временных параметров отжига данной проволоки, обеспечивающего как высокое качество термической обработки, так и достаточно высокую скорость ее нагрева.
Для достижения поставленной задачи осуществляли вычислительный эксперимент с использованием ПЭВМ. Установлено, что вышеперечисленным требованиям в наибольшей степени удовлетворяет режим, предусматривающий нагрев проволоки (в первой зоне - при командной температуре 850 С, во второй зоне - при температуре 820 С) в течение 8...9 ч и последующую ее выдержку под отключенным колпаком в течение 2...3 ч. Испытания предложенного режима отжига на электропечи типа СГЗ, оборудованной нагревательным колпаком с рациональным размещением установленной мощности, зафиксировали достаточно однородное поле температуры отжигаемой проволоки, а также возможность сокращения на 3,5 ч продолжительности ее нагрева. Энергетическую эффективность применения разработанного мероприятия оценивали путем составления тепловых балансов колпаковой электропечи данного типа до и после ее модернизации при отжиге бунтов проволоки по существующему и разработанному режимам. Анализ полученных результатов позволил выявить рост полезно используемой тепловой энергии, который соответствует повышению производительности данного агрегата, и возрастание величины термического коэффициента полезного действия данной печи, что свидетельствует о повышении ее тепловой экономичности. Дальнейшее совершенствование использования энергии в колпаковой электропечи типа СГЗ необходимо осуществлять в направлении рационального размещения источников тепловой энергии на стенде и во внутренней полости стопы бунтов проволоки, а также реализации, как предварительного подогрева металла, так и утилизации его теплоты при охлаждении.
УДК 622.73:667.629.825
ПОЛУЧЕНИЕ СЛЮДЯНОЙ ПРОДУКЦИИ ПЕРЕРАБОТКИ ТЕХНОГЕННОГО СЫРЬЯ, НАХОДЯЩЕГОСЯ В РАЙОНЕ ДЕЯТЕЛЬНОСТИ ОАО «КОВДОРСЛЮДА»
Хохуля М.С., Гершенкоп А.Ш.
Учреждение Горный институт Кольского научного центра РАН, г. Апатиты, Россия
В условиях существования рыночных отношений и конкуренции в последние годы резко сократилось производство листовой слюды. По этой причине произошло закрытие или затопление большинства слюдяных рудников России на предприятиях Восточной Сибири и в Карелии. Также полностью прекращена добыча мусковита и в Мурманской области.
Поскольку реанимировать работу рудников без привлечения серьезных инвестиций невозможно, для возрождения слюдяной отрасли необходимо обратить внимание на техногенные отвалы, образованные из отходов после извлечения листовой слюды, в которых сосредоточена также и мелкоразмерная слюда, которая практически не извлекалась. Такая ситуация создает благоприятные предпосылки для вовлечения в переработку техногенных отвалов флогопита и мусковита, накопленных в результате многолетней работы предприятия ОАО ,,Ковдорслюда”.
По выполненной оценке только в техногенных отвалах находится около 180 тыс. т, которые могут стать основным источником получения молотых слюд. При производительности фабрики на уровне 10 тыс.т по концентрату и при извлечении в него около 70% флогопита склад данных отвалов может перерабатываться 20 лет. Более чем на 25 лет обеспечат работу горнообогатительного предприятия и отвалы мелкоразмерного мусковита, количество которых составляет около 300 тыс.т.
Предлагаемая технологическая схема переработки отвалов учитывает специфические свойства слюды и основана на выявленных закономерностях движения частиц пластинчатой формы на наклонной поверхности и в восходящих потоках разделительной среды. Она предусматривает применение специальных способов и аппаратов для переработки техногенных отвалов мусковита и флогопита: щелевого сепаратора для разделения по форме материала крупных фракций (-20+10 мм), гидравлического сепаратора для получения концентратов из руды крупностью менее 5 мм и разделение на концентрационных столах фракции крупностью -0,5+0,16 мм, а также барабанных грохотов для классификации материала на машинные классы.
Как в лабораторных, так и опытно-промышленных условиях были выделены мусковитовые и флогопитовые концентраты с содержанием 96-98% слюды при извлечении 65-70% от всей слюды крупностью менее 20 мм с учетом ее потерь в материале крупностью -0,2 мм.
Выделенные из техногенных отвалов слюды концентраты в случае реализации технологии в промышленном масштабе могут быть использованы как по целевому назначению, так и в производстве молотых слюд для их последующего применения на предприятиях лакокрасочной, резиновой и химической промышленности (производство композиционных материалов, сварочных электродов и т.д.), фабриках по выпуску обоев, мягкой кровли, косметики и т.д.
На основании геолого-экономической оценки целесообразности использования техногенных отвалов флогопита в районе деятельности ОАО ,,Ковдорслюда” показано, что прибыль предприятия по одному из примеров расчета после налогообложения должна составить не менее 50 млн.руб., в случае если годовая производительность по рудной массе соответствует 40 тыс. т в год. Срок окупаемости вкладываемых средств по предварительным расчетам составит около 2 лет.
УДК 662.665.7.032.52:547.576:66.061
PROCESS DEVELOPMENT OF VANILLIN EXTRACTION OBTAINED FROM WOOD PROCESSING WASTES
Chelbina J.V., Tarabanko V. E
Institute of chemistry and chemical technology
Siberian Branch of Russian Academy of Sciences,
Krasnoyarsk, Russia
The traditional source of raw material for vanillin production is chemical and mechanical wood processing wastes containing lignin. The main part of lignin wastes is generated at enterprises of pulp-and-paper (50 million tons per year all over the world), hydrolytic (30% of the initial wood mass) and woodworking industries (60 million m3 per year ) [1,2].
A very important stage in the processes of vanillin sinthesis is its extraction from the lignin oxidation products containing up to 10 g/l of vanillin and much more byproducts.
The literature review shows that the selectivity of vanillin extraction, that is the concentration of vanillin in the extract decreases, but the distribution coefficient increases among extractants: hexane – toluene – benzene – 1,2-dichlorethane – chloroform [3]. That is why it is impossible to select the individual extractant combining high selectivity and extraction efficiency.
The goal of this work is to study vanillin extraction process using two-component organic solutions, which consist of nonpolar hydrocarbon and effective extractants: octylamine, C6-C8 aliphatic alcohols, and vanillin stripping with sodium bisulphite or alkali solutions.
The main laws of vanillin extraction by octylamine was studied in а system water - heptane. It is shown, octylamine extracts vanillin with distribution coefficient up to 600, and in case of moderate extractant concentrations or high pH values, high vanillin extraction selectivity from the reaction mass of lignin oxidation could be attained.
Investigations of vanillin extraction processes in the system water-aliphatic alcohol-heptane depending on pH helped to define that C6-C8 alcohols can be used to extract vanillin from the reaction solutions of oxidized lignin without their acidification practically with the expenses similar to that in the technology of vanillin extraction by benzene from acidified solutions.
Vanillin stripping from the alcohol solutions with alkali or sodium bisulphite is studied, vanillin to be concentrated in water phase. The equilibrium constant of vanillin-bisulphate derivative formation has been estimated (K=350).
The obtained results allow to implement the estimations required to realize new technological processes of vanillin extraction by the investigated extractants and its stripping by water solutions of alkali and sodium bisulphate.
REFERENCES:
1. Fengel D., Wegener G. Wood (Chemistry, Ultrastructure) Moscow, 1988, 511 p.
2. Chudakov M.I. Industrial application of lignin, Lesn. Prom.: Moscow, 1983, 154 p.
3. Tarabanko V.E., Koropachinskaya N.V. Catalytic methods for producing the aromatic aldehydes from lignins. Chemistry of plant raw materials (Russia), 2003, № 1, P. 5-25.
УДК 662.91
ИССЛЕДОВАНИЕ СОСТАВА И СВОЙСТВ ЦИТРАТНОГО ЭЛЕКТРОЛИТА ДЛЯ ПОЛУЧЕНИЯ НАНОКРИСТАЛЛИЧЕСКИХ Co-W ПОКРЫТИЙ ПРИ ЕГО ДЛИТЕЛЬНОЙ ЭКСПЛУАТАЦИИ
Яхова Е. А., Шульман А. И., Косова А. В., Тиханская Е. В.
Приднестровский государственный университет имени
Т. Г. Шевченко, г. Тирасполь, Молдова
Учитывая экологические риски, связанные с технологией электрохимического хромирования из соединений хрома (VI), ведутся интенсивные исследования в области разработки альтернативных технологий получения износостойких покрытий. Индуцированное соосаждение тугоплавких металлов (W, Мо) с металлами группы железа (Fe, Со, Ni) в определенных условиях позволяет получать аморфные (нанокристаллические) покрытия, обладающие уникальными коррозионными и механическими свойствами. В частности, осаждение Co-W сплавов из цитратного электролита с добавкой борной кислоты и равными концентрациями сульфата кобальта и вольфрамата натрия (0,2 моль/л) при повышенных температурах позволяет получить покрытия, износные характеристики которых в условиях сухого трения являются лучшими, чем покрытия из электролитического хрома.
Возможность практического использования цитратного электролита в значительной степени определяется тем, насколько его свойства сохраняются (изменяются) со временем. Решению этой задачи посвящена настоящая работа.
Экспериментально было установлено, что при выдержке электролита в течение месяца (без его проработки), электропроводность цитратного раствора уменьшается в 1,3 раза. При этом меняется и состав раствора. Происходит снижение концентрации и Со2+ и W042- в растворе. Причем наблюдалось менее резкое уменьшение концентрации Со2+ (до 0, 170 моль/л) и более резкое W042- (до 0,157 моль/л)
Концентрацию кобальта и вольфрама определяли фотоколориметрически, измеряя оптическую плотность раствора Со2+ с нитрозо-R-солью, a W042- после его восстановления Sn(II) и Ti(III) до W(V) (с образованием соответствующего окрашенного комплекса). В обоих случаях построение калибровочных графиков осуществляли из растворов, содержащих не только Со2+ и W042-, но и все компоненты раствора электролита при концентрациях, используемых в электролите.
рН электролита со временем практически не изменялся. Его величина находилась в пределах рН=6,5-6,9. Также эксперименты показали, что с увеличением температуры удельная электропроводность раствора прямолинейно увеличивается.
При выдержке в течение месяца электролита, не содержащего вольфрамат натрия, концентрации Со2+ уменьшается до 0,140 моль/л, а в отсутствие сульфата кобальта в растворе – концентрация W042- уменьшается до 0,145 моль/л. При этом электропроводность раствора уменьшается и в том и в другом случае в 1,4 раза.
Экспериментальные данные говорят о том, что в растворе происходит процесс, в результате которого уменьшается количество гидратированных ионов Со2+ и W042-, вследствие чего уменьшается и электропроводность раствора. В работе показано, что данный процесс, возможно, связан с образованием комплексных соединений Со2+ и W042- с цитратом, например в виде [CoCit]- и [CoCitWО4]3-, а также гетерополисоединений.
СЕКЦИЯ 2
ПРОМЫШЛЕННЫЕ
БИОГЕОТЕХНОЛОГИИ
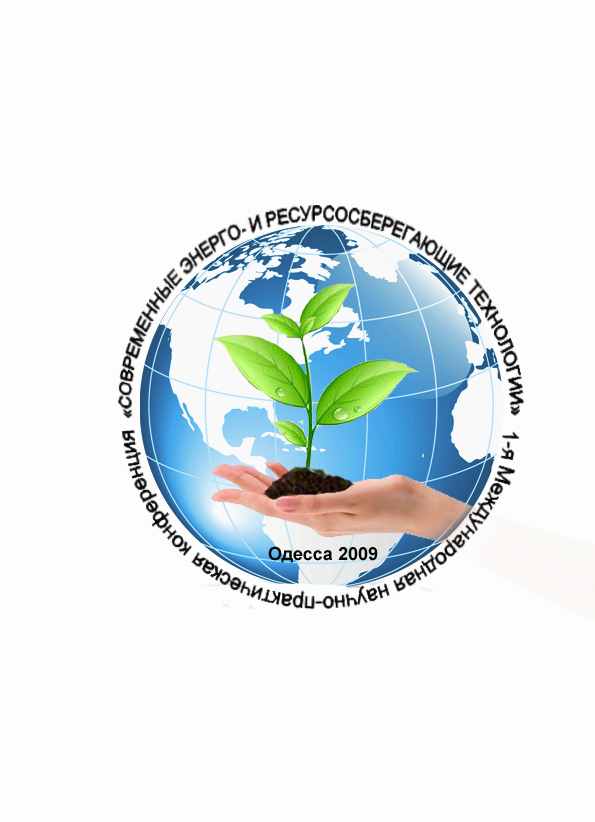
УДК 579.68
ИЗУЧЕНИЕ ВЛИЯНИЯ МИКРОБИОЛОГИЧЕСКОЙ СОСТАВЛЯЮЩЕЙ ИСХОДНОГО СЫРЬЯ НА ПРОЦЕСС ВОДНОГО ВЫЩЕЛАЧИВАНИЯ ГЕРМАНИЙСОДЕРЖАЩИХ ОТХОДОВ
Блайда И.А., Васильева Т.В., Хитрич В.Ф.,
Слюсаренко Л.И., Барба И.Н.
ОНУ имени И. И. Мечникова, г. Одесса, Украина
Технологические приемы переработки германийсодержащих промпродуктов и отходов с целью извлечения ценных компонентов достаточно изучены и отработаны. В большинстве своем в их основе лежит гидрометаллургический подход, относящийся к сугубо химическим, – обработка исходного твердого сырья водными растворами, чаще всего сильно кислыми или щелочными. Однако интенсивное развитие в последнее время биогеотехнологии и знаний геологической микробиологии требует учитывать тот факт, что в геологических процессах формирования полезных ископаемых микроорганизмы принимали и принимают активное участие. Биологические свойства различных групп микроорганизмов и особенности их жизнедеятельности в природных месторождениях значительно влияют на определенные окислительно-восстановительные реакции, могут катализировать окисление серосодержащих соединений, окисление-восстановление азотсодержащих соединений и т.д. Вклад и геохимическая роль микробиологической составляющей исходного сырья на процессы выщелачивания металлов из твердых субстратов в каждом конкретном случае определяется групповым составом микроорганизмов: тионовых, аммонифицирующих и сульфатредуцирующих бактерий, - а также их способностью проявлять свои мезофильные или термофильные свойства.
Целью данной работы являлось установление геохимической роли микроорганизмов, присутствующих в исходном германийсодержащем сырье, в процессах так называемого химического выщелачивания металлов из него. В качестве исходного использовали сульфидное германийсодержащее сырье, являющееся отходом свинцово-цинкового производства, и возгоны от сжигания энергетических углей. Для учета возможного влияния термофильных свойств микроорганизмов, присутствующих в сырье, процессы вели при нагревании до 80-90 оС и при комнатной температуре. Для учета возможного воздействия тионовых кислотолюбивых бактерий на процесс выщелачивания в качестве вскрывающего реагента использовали воду (рН 5,6) и сернокислый раствор (рН 1,8). Для снятия возможного влияния микробиологической составляющей сырья на протекающие при его обработке процессы все опыты проводили при соблюдении постоянства параметров с предварительно автоклавированными исходными продуктами и реактивами.
Полученные результаты свидетельствуют о том, что во всех случаях коэффициент влияния микроорганизмов на извлечение металлов в раствор К > 1, т.е. независимо от условий проведения процесса выщелачивания существует довольно значительный вклад микробиологической составляющей на эффективность процесса в целом. Это сказывается на увеличении степени извлечения металлов в раствор в присутствии собственной микрофлоры по сравнению с автоклавированными образцами на 1,34-11,79 %.Увеличение коэффициентов влияния микроорганизмов на показатели процессов (до значений 2,04) при подкислении выщелачивающего раствора свидетельствуют в пользу присутствия и активизации группы собственных микроорганизмов типа T.ferrooxidans. При увеличении температуры процесса также несколько возрастает величина К, что, по-видимому, связано с проявлением и усилением термофильных свойств присутствующих микроорганизмов.
Таким образом, гидрометаллургические процессы, в которых в качестве вскрывающих растворов используются не агрессивные среды рН-ой области, можно отнести к бактериально-химическим. Механизм протекающих при этом реакций, а также пути интенсификации процессов должны рассматриваться с учетом этого подхода.
УДК 579.546.289
ИЗУЧЕНИЕ АЦИДОФИЛЬНЫХ СЕРООКИСЛЯЮЩИХ БАКТЕРИЙ И ОЦЕНКА ИХ СПОСОБНОСТИ
ВЫЩЕЛАЧИВАТЬ МЕТАЛЛЫ
Васильева Т.В., Блайда И.А., Васильева Н.Ю., Слюсаренко Л.И.
Одесский национальный университет имени И.И. Мечникова,
г. Одесса, Украина
Микробное выщелачивание признано привлекательной альтернативой традиционным физическим и химическим методам извлечения металлов, благодаря сокращению потребления энергии, транспортных затрат и отсутствию пагубного воздействия на окружающую среду. Ведущую роль в процессах биовыщелачивания уже давно играют ацидофильные тионовые бактерии, обитающие в специфических экологических нишах. Представители рода Acidithiobacillus обладают уникальной способностью переводить металлы из нерастворимых в растворимую форму.
В данном сообщении приведены результаты выделения из металлсодержащих отходов штаммов бактерий, способных к их выщелачиванию. Из свинцево-цинкового концентрата и отходов металлургической промышленности изолированы два штамм сероокисляющих бактерий - Acidithiobacillus sp. 11 и Acidithiobacillus sp. 13. Выделение штаммов осуществляли методом накопительной культуры.
Штаммы охарактеризованы по 19 фенотипическим признакам. Проведенные исследования показали, что по морфорлогическим и физиологическим признакам Acidithiobacillus sp. 11 и Acidithiobacillus sp. 13 представляют собой грамнегативные подвижные палочки с . одним или двумя жгутиками. Изучены способность изолированных штаммов окислять различные соединения серы, отношение к органическим веществам, диапазон и оптимальные для роста значения рН и температуры, способность восстанавливать нитраты до нитритов и азота. В отдельной серии экспериментов показана возможность использования изолированных штаммов в процессах бактериального выщелачивания металлов.
В условиях автотрофного роста исследованные штаммы в качестве источника энергии использовал различные соединения серы - Na2S2O3, C2H6O S, Na2S, KCNS, ZnS, S+2 и FeSO4. Acidithiobacillus sp. 11 и Acidithiobacillus sp. 13 также обладали способностью к росту и окислению тиосульфата в присутствии 0,03 - 0,3 % дрожжевого экстракта и глюкозы. Оба штамма растут в диапазоне температур от 4,0 до 15,0 0С при оптимальных значениях 28,0 – 32,0 0С. Оптимальные значения рН для роста 1,0-2,0.
Acidithiobacillus sp. 11 окислял тиосульфат в течение суток на 50,0 % с образованием промежуточных продуктов (тетратионата) и сульфита. Снижение концентрации тиосульфата в среде культивирования с Acidithiobacillus sp. 13 регистрировали на 70,0-80,0 %, при этом в среде обнаруживали только сульфит.
В условиях лабораторных экспериментов оба штамма переводили германий, кальций, свинец, цинк, железо и алюминий из твердого субстрата в раствор. В течение суток Acidithiobacillus sp. 11 и Acidithiobacillus sp. 13 выщелачивали из свицово-цинкового концентрата и золоуносов 100,0 % германия и кальция, 80,0 % железа и 60,0 % алюминия.
Изолированные штаммы хранятся в коллекции кафедры микробиологии и вирусологии Одесского национального университета имени И.И. Мечникова.
УДК 579.546.289
БАКТЕРИАЛЬНОЕ ВЫЩЕЛАЧИВАНИЕ ГЕРМАНИЯ
(В УСЛОВИЯХ ЛАБОРАТОРНЫХ ЭКСПЕРИМЕНТОВ)
Васильева Т.В., Васильева Н.Ю., Блайда И.А., Слюсаренко Л.И.
Одесский национальный университет имени И.И. Мечникова
Одесса, Украина
Научные достижения в области автоматики, радиоэлектроники и преобразовании различных видов энергии обусловлены применением германия в полупроводниковой технике; большое внимание уделяется устройствам с применением монокристаллических германиевых пленок. Основные производители германия – США и Бельгия; США извлекают его из цинковых руд, Бельгия – использует германиевые концентраты, получаемые из месторождений Намибии и Заира. В последние годы приобретают значения и нетрадиционные сырьевые источники редких металлов, в том числе и германия. К ним с полным правом можно отнести природные минерализованные воды, угли, золоуносные шлаковые отходы. Золоуносы – это твердый продукт сжигания углей, они многофазны, полимерные и представляют собой в определенном смысле техногенный концентрат редких металлов. Золоуносы, обогащенные германием, скандием, иттрием и другими редкими элементами рассматриваются как вторичные сырьевые ресурсы. Для извлечения германия и других редких металлов техногенных отходов возникает необходимость использования современных технологий. К таким технологиям относится и биовыщелачивание; это экологически чистая технология, позволяющая экономить материалы и энергию, которая может стать в перспективе самой распространенной по извлечению металлов. В ее основе лежит использование существующих в природе бактерий для извлечения металлов из сульфидных руд или концентратов за счет ускорения естественного разложения сульфидов на оксиды. Основная роль в процессах биовыщелачивания принадлежит представителям рода Thiobacillus.
Приведенные результаты исследований являются логическим продолжением научно-исследовательских работ, проводимых на кафедре микробиологии Одесского национального университета им. И. И. Мечникова, и представляют собой новое направление – использование микроорганизмов с практически полезными свойствами для бактериального выщелачивания металлов из промышленных отходов и природных минералов. В работе использованы типовые (Acidithiobacillus ferrooxidans 23270), коллекционные (Acidithiobacillus thinooxidans 336) и природные (Acidithiobacillus sp. 11, Acidithiobacillus sp. 13) штаммы тионовых бактерий. Известно, что в процессе бактериального выщелачивания ведущую роль играют физико-химические особенности поверхностей клеток и твердых материалов, в первую очередь, способности микроорганизмов прикрепляться к субстратам. В процессе выполнения исследований определена способность изученных штаммов прикрепляться к твердым субстратам – силикагелю, свинцово-цинковому концентрату и золоуносам. Максимальное количество клеток бактерий закреплялось на поверхности твердых частиц при рН от 3,5 до 1,5; в этом же диапазоне рН наиболее активно проходил процесс высвобождения металлов. Определена кинетика перехода металлов из твердой фазы в жидкую: в первые сутки регистрировали появление в среде культивирования кальция и германия, на третьи сутки железа, цинка и свинца. На разных стадиях процесса биовыщелачивания образуется сложный комплекс различных соединений, основным из которых являются промежуточные продукты соединений серы – тиосульфат, тетратионат, сульфит, серная кислота. Полученные данные позволяют считать, что используемые штаммы способны удалять накопления твердой серы.
Результаты, полученные в ходе лабораторных экспериментов, могут быть положены в основу технологии выщелачивания металлов из твердых отходов.
УДК. 631.879.25:631.826.0 04.14
ОБЕЗВРЕЖИВАНИЕ И ОБЕЗЗАРАЖИВАНИЕ ОСАДКОВ СТОЧНЫХ ВОД АМИНОКИСЛОТНЫМИ РЕАГЕНТАМИ ДЛЯ ПОЛУЧЕНИЯ КОМПОСТА
Демин Д.В., Севостьянов С.М., Татаркин И.В.
Институт фундаментальных проблем биологии РАН
г. Пущино
В Институте фундаментальных проблем биологии РАН (г.Пущино, лаб.Функциональной экологии) разработана технология переработки осадков городских очистных сооружений в органическое удобрение путем их обезвреживания и обеззараживания специальными реагентами и с последующим компостированием.
Технология включает несколько взаимосвязанных ключевых звеньев и выглядит следующим образом: производство аминокислотных реагентов (обезвреживание и обеззараживание осадков реагентами и получение нетоксичного и экологически безопасного субстрата (органоминеральной композиции) (приготовление компоста на основе органоминеральной композиции (исследования и оценка токсикологических и агрохимических свойств компоста.
Бактерицидно-детоксицирующие аминокислотные реагенты по специальной технологии производятся из токсичных и биологически опасных отходов кожевенного, мехового, мясо- и птицеперерабатывающих производств и токсичных медьсодержащих отходов гальванотехнических производств.
Обработка загрязненных тяжелыми металлами и содержащих патогенную микрофлору осадков городских очистных сооружений аминокислотными реагентами переводит их в нетоксичный и экологически безопасный субстрат — органоминеральную композицию.
Органоминеральная композиция по составу и физико-химическим свойствам представляет собой хороший субстрат для компостирования с использованием различных органических наполнителей (твердые бытовые отходы, древесные отходы, торф, солома и т.п.). Для интенсификации биотермического процесса и ускорения созревания компоста добавляются микробиологические препараты.
Компост — ценное органическое удобрение, имеет высокие удобрительные характеристики, содержит почвенную микрофлору, макро- и микроэлементы.
Экологическая безопасность технологии подтверждена результатами многочисленных исследований на каждом этапе работ и наличием сертификатов и заключений по ним. Проведенные ЦГСЭН бактериологические и паразитологические анализы показали отсутствие в компосте патогенной микрофлоры, жизнеспособных гельминтов и их яиц, тогда как в исходных осадках они были.
Приготовленный на основе обезвреженных и обеззараженных осадков городских очистных сооружений компост по предлагаемой технологии можно использовать в качестве почвоулучшающей добавки и органического удобрения вместо навоза и почвы, на которые ощущается острый дефицит, при рекультивации свалок и карьеров, восстановлении плодородия нарушенных, сильноэродированных и сильнозагрязненных земель, при благоустройстве городских территорий, придорожных полос, в питомнических хозяйствах.
Таким образом, внедрение данной технологии компостирования будет способствовать экологически безопасной и экономически эффективной переработке в полезную продукцию нескольких видов отходов, утилизация которых по отдельности в настоящее время является серьезной проблемой.
Работа выполнена по программе Инновации РАН 2009
УДК 579.002.68
БИОГЕТЕХНОЛОГИИ В РЕШЕНИИ ПРОБЛЕМЫ
ТЕХНОГЕННЫХ РЕСУРСОВ
Иваница В.А., Васильева Т.В.
Одесский национальный университет, Одесса, Украина
С интенсивным развитием научно-технического прогресса и ростом объемов производства, проблемы взаимодействия природы и общества становятся все острее. В результате истощения природных ресурсов приходится использовать полезные ископаемые с предельно низким содержанием ценных компонентов; возрастает количество отходов и происходит загрязнение окружающей среды. Твердые техногенные отходы, накопившиеся в результате производственной деятельности, имеют значительную сырьевую ценность и содержат железо, свинец, цинк, редкие и драгоценные металлы - германий, скандий, бериллий, галлий, золото. Вопрос их утилизации рассматривается как одна из важнейших медико-экологических и социально-экономических задач. Для извлечения металлов из твердых отходов применяют стандартные пиро- и гидрометаллургические методы, предусматривающие использование сильных кислот, высоких температур и давления. Однако в связи с ужесточением мер по охране окружающей среды стандартные химические методы нецелесообразны как с экологических, так и с экономических позиций. В сложившейся ситуации возникает обоснованная необходимость разработки и внедрения современных технологий. В настоящее время уже сформировалась новая научная дисциплина – биогеотехнология металлов, в рамках которой разрабатываются способы извлечения металлов из руд, концентратов, горных пород и растворов под воздействием микроорганизмов или их метаболитов при нормальном давлении и температуре. К настоящему времени сформировалось два основных направления биогеотехнологии - биогеотехнология выщелачивания металлов и биогеотехнология обессеривания углей. В основе бактериального выщелачивания металлов лежит использование существующих в природе бактерий для извлечения металлов из сульфидных руд или концентратов за счет ускорения естественного разложения сульфидов на оксиды. В процессе бактериального выщелачивания ведущую роль играют физико-химические особенности поверхностей клеток бактерий и твердых материалов, в первую очередь, способности микроорганизмов прикрепляться к субстратам. При прямом контакте бактерий с поверхностью частиц происходит стимулирование бактериальной клеткой окисления минерала с перекачкой электронов на клетку. В этом случае речь идет об анодно-катодном или донорно-акцепторном механизме биокоррозии минеральной частицы клетками бактерий. До настоящего времени использование микробных технологий в горнодобывающей и металлургической промышленностях ограничивалось применением микроорганизмов, обитающих в естественной среде. Однако все большое значение для извлечения металлов из руд, концентратов и сточных промышленных вод приобретает использование высокоактивных штаммов микроорганизмов, полученных путем целенаправленной селекции и обеспечивающих высокую скорость прямого окисления металлсодержащих отходов и сульфидных минералов за счет ускорения естественного разложения сульфидов на оксиды. В целом использование новых биотехнологических подходов позволит увеличить сырьевые ресурсы, обеспечить комплексность извлечения металлов, решить многие проблемы охраны окружающей среды.
В Одесском национальном университете имени И.И. Мечникова получены высокоактивные штаммы тионовых бактерий, которые использованы для бактериального выщелачивания металлов из природных свинцово-цинковых концентратов и золоуносов, образующихся при сгорании каменного угля.
УДК 621.182.12.
БІОСОРБЦІЙНАТЕХНОЛОГІЯ ОЧИЩЕННЯ ПРОМСТОКІВ
ВІД ВАНН МЕТАЛОПОКРИТТІВ
Іваниця В.О., Шилов В.І., Менчук В.В., Норочевська С.М.,
Рибаков С.В.,
Краєвський В.М., Драгуновська О.І., Баранов О.О.
Національний університет імені І. І. Мечникова,,
Санітарно-епідемічнa станція Київського р-ну,
м. Одеса, Україна
Біосорбційна технологія відноситься до області обробки води, зокрема, до технології очищення промстоків від ванн металопокриттів з температурою електролітів більше ніж 55 оС, і може використовуватися на ділянках хромування, нікелювання, цинкування, оливування, мідніння, свинцювання, оксидування сталей та інш. Такі ванни є майже на кожному машинобудівному підприємстві. При цьому параметри забруднення стічних вод металами та іншими забрудненнями залежать від технології очищення деталей перед процесом нанесення металопокриттів, а також від рецептур електролитів в ваннах металопокриттів.
Найбільш доцільне застосування пропонуємої технології для підприємств і цехів з обмеженим водопостачанням, а також при нанесенні металопокриттів у ваннах, які тривалий час працюють без заміни електроліту і які містять різні органічні забруднення крім металів: жирові речовини, мастильно-охолодні рідини, пасти, які застосовують при шліфуванні, хонінгуванні, поліруванні деталей і інш. Забруднення попадають у ванни нанесення покриттів на поверхні недостатньо очищених деталей. Недостатнє очищення деталей у наш час обумовлено високою вартістю енергоресурсів, що необхідні для якісного очищення деталей від забруднень перед нанесенням покриттів: деталі необхідно очищати в декількох ваннах з гарячими (60-80 оС) лужними розчинами-електролітами, для нагрівання яких потрібна велика кількість енергоресурсів. При цьому ряд ванн нанесення металопокриттів самі мають властивості очищення поверхні деталей при температурі понад 55 оС, наприклад, шляхом подачі на деталі постійного струму зворотної полярності.
Згідно описуваної технології очищена вода відповідає санітарним вимогам і має можливість бути повторно використаною у виробництві, для чого іонів металів в очищеній воді не перевищує гранично-допустимих концентрацій (ГДК),
Докладно технологія викладена в описі до патенту України №39220. Автори: В.О.Іваниця, В.І. Шилов , В.В. Менчук та інш. опубл. 10.02.2009. Патентовласник - ОНУ імені І. І. Мечникова пропонує ліцензії для використання патенту і допомогу в реалізації.