Основы высокоэффективн ой технологии изготовления цилиндрических зубчатых колес
Вид материала | Автореферат |
- Нормирование точности зубчатых колес, 105.1kb.
- Разработка технологии изготовления индивидуального зуборезного инструмента для мелкомодульных, 266.32kb.
- Гост 11902-77. Головки зуборезные для конических и гипоидных зубчатых колес с круговыми, 13.3kb.
- Программные средства компьютерного проектирования зубчатых передач в обобщающих параметрах, 26.58kb.
- Гост 13133-77. Станки зубошлифовальные с профильным кругом для цилиндрических колес., 14.31kb.
- Возможные исходные реечные контуры для нарезания зубчатых колес, 77.82kb.
- Название программы информационные технологии в эскизном проектировании и оптимизации, 135.84kb.
- Архитектура ЭВМ. Лекция, 236.96kb.
- 2. геометрический расчет прямозубой цилиндрической передачи, 92.65kb.
- Пример выполнения задачи, 48.33kb.
Для определения величины профильной модификации обкаточного катода по методу постоянной приведенной интенсивности было проведено моделирование процесса финишной электрохимической обработки фасонных поверхностей при обкате электродов. Профиль каждой из взаимодействующих поверхностей таких электродов очерчен дугой окружности, радиус которой равен соответственно радиусу кривизны профиля изделия и радиусу кривизны профиля катода в точках, расположенных на одной силовой линии (рис. 10).
Погрешности процесса могут быть компенсированы путем корректирования постоянных параметров (KR и C) и функции F или вводом поправочных коэффициентов.
В качестве заменяющей кривой принята дуга окружности, нормальная к профилям изделия и катода в рассматриваемых точках J2 и J0. В этом случае связь между угловыми параметрами µ и
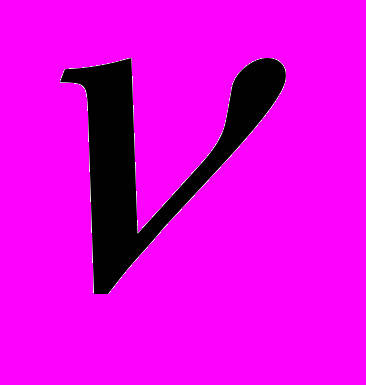
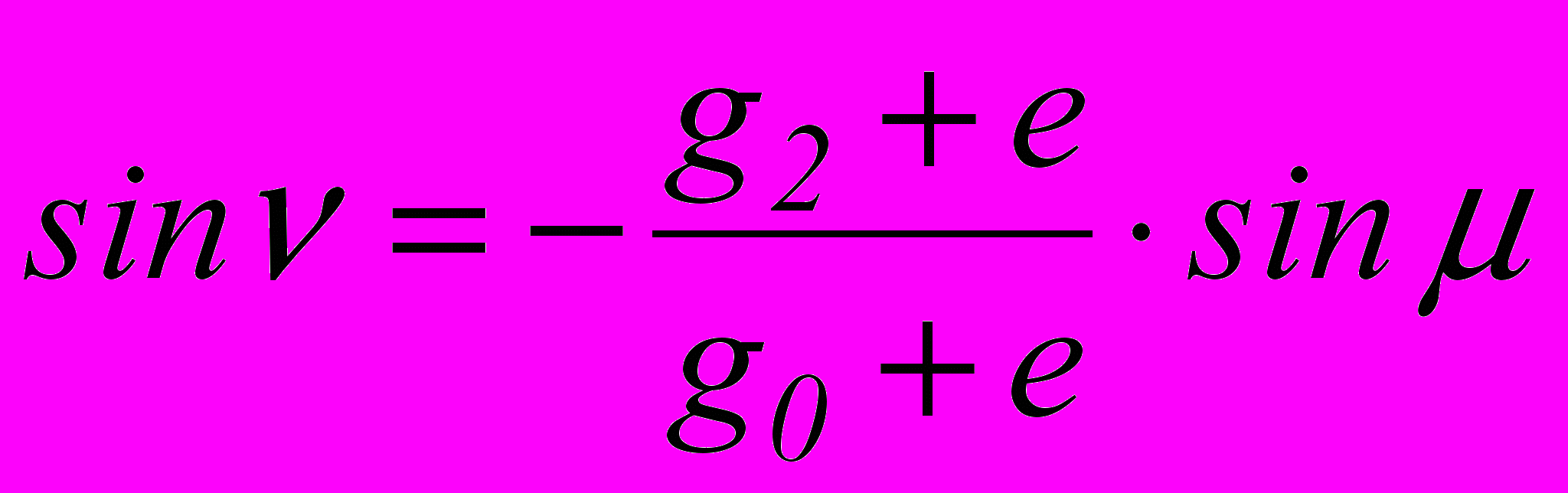
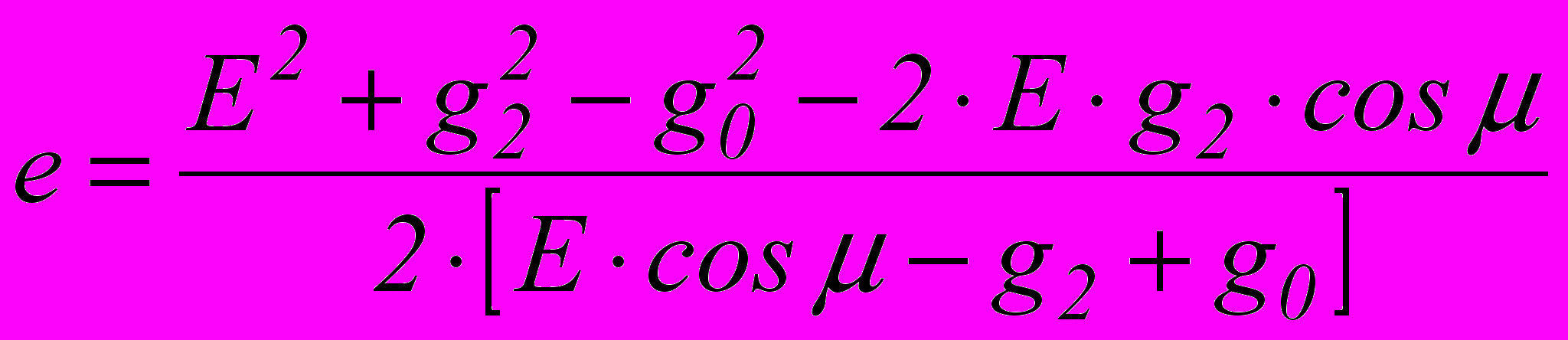
Межэлектродный зазор находили по формуле
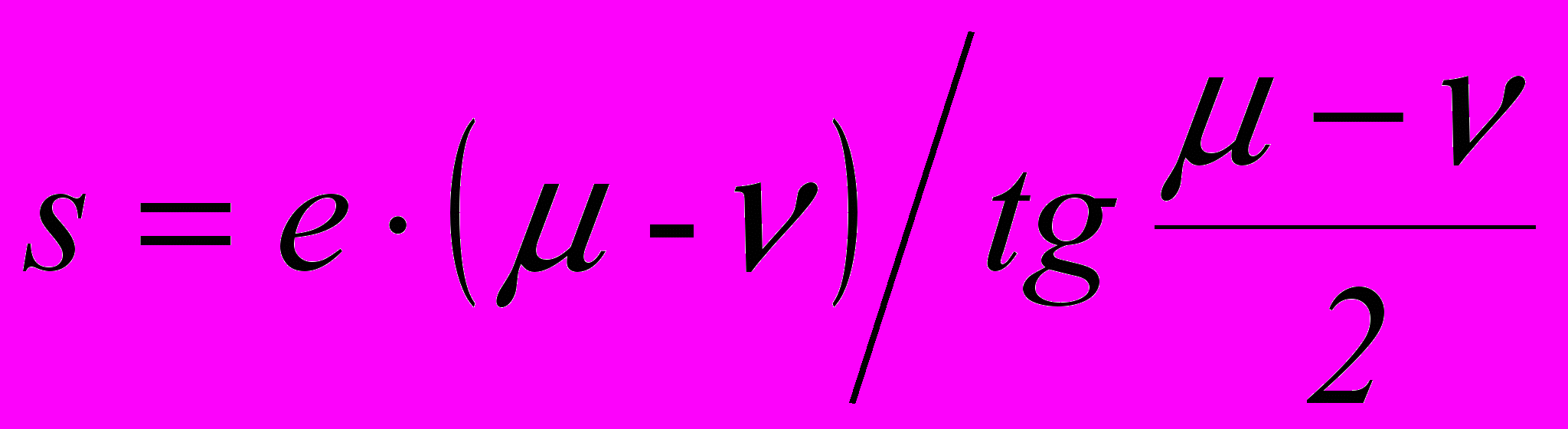
Влияние кривизны взаимодействующих поверхностей на интенсивность процесса электрохимической обработки учитывается функцией F0.
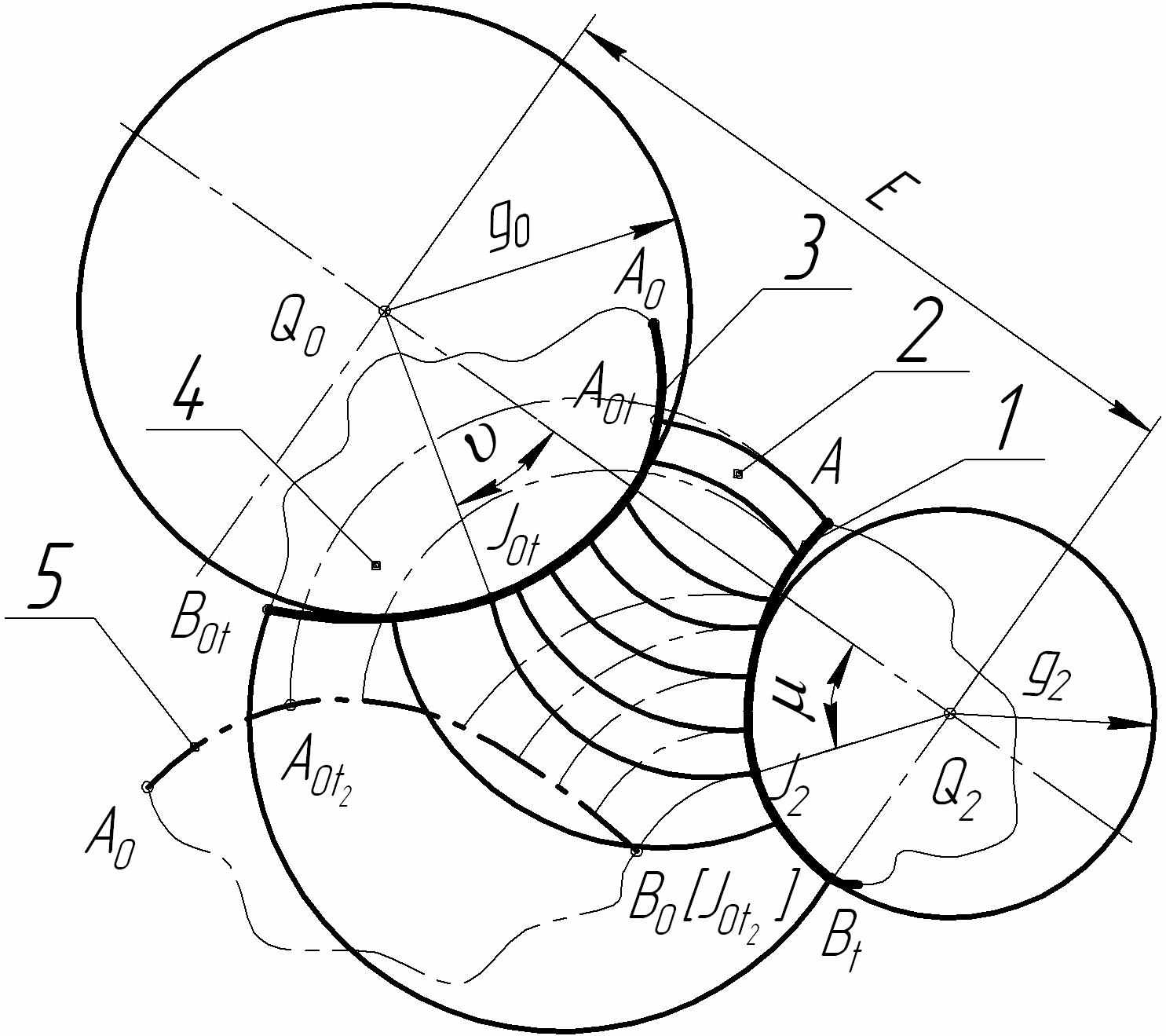
Рис. 10. Расчетная активная зона действия обкаточного катода в моменты времени t и
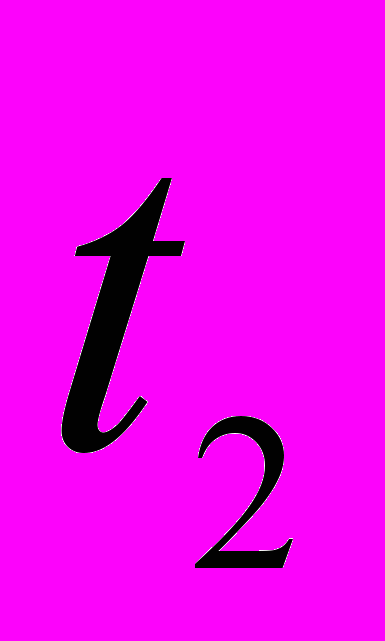
3 – профиль обкаточного катода в положении, соответствующем моменту времени t; 4 – зона действия в момент времени
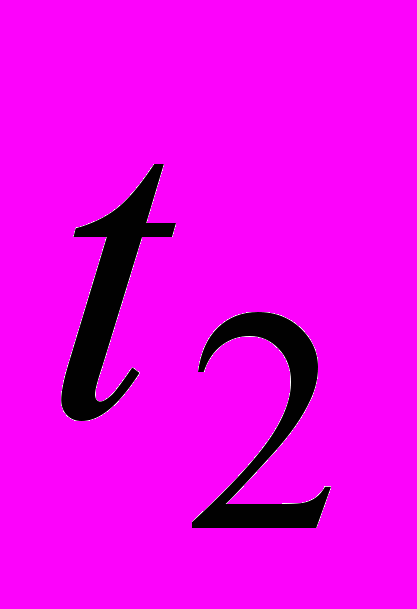
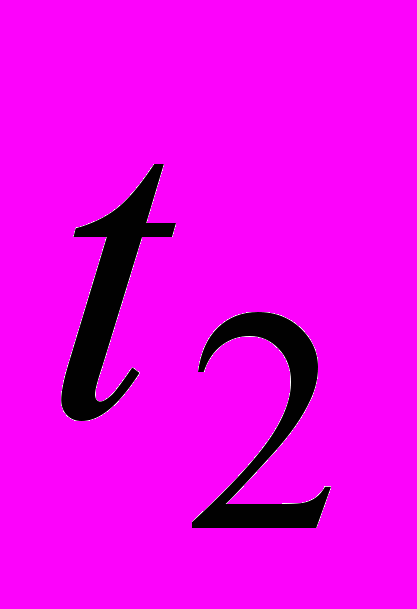
Функция F0 позволяет объяснить некоторые явления, сопровождающие процесс электрохимической обработки, например, «краевой эффект».
Эмпирически были определены зависимости, показывающие, что при надежности 0,90 в пределах принятых сочетаний
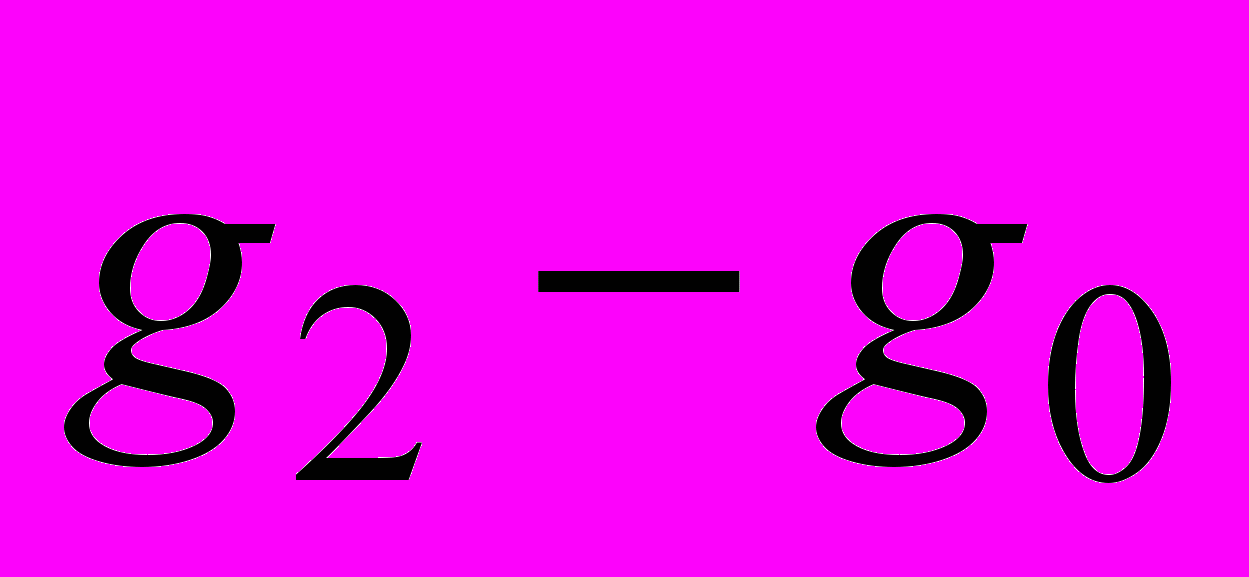
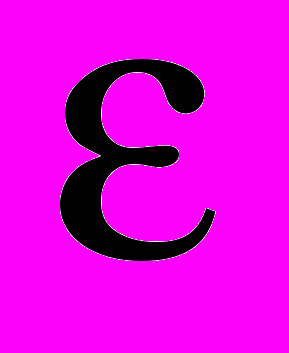
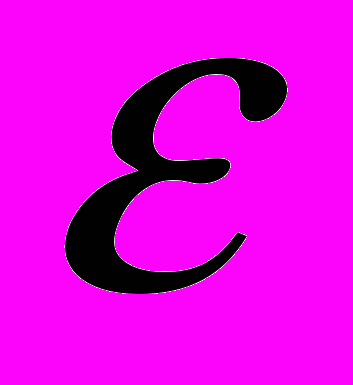
Для каждого из принятых сочетаний
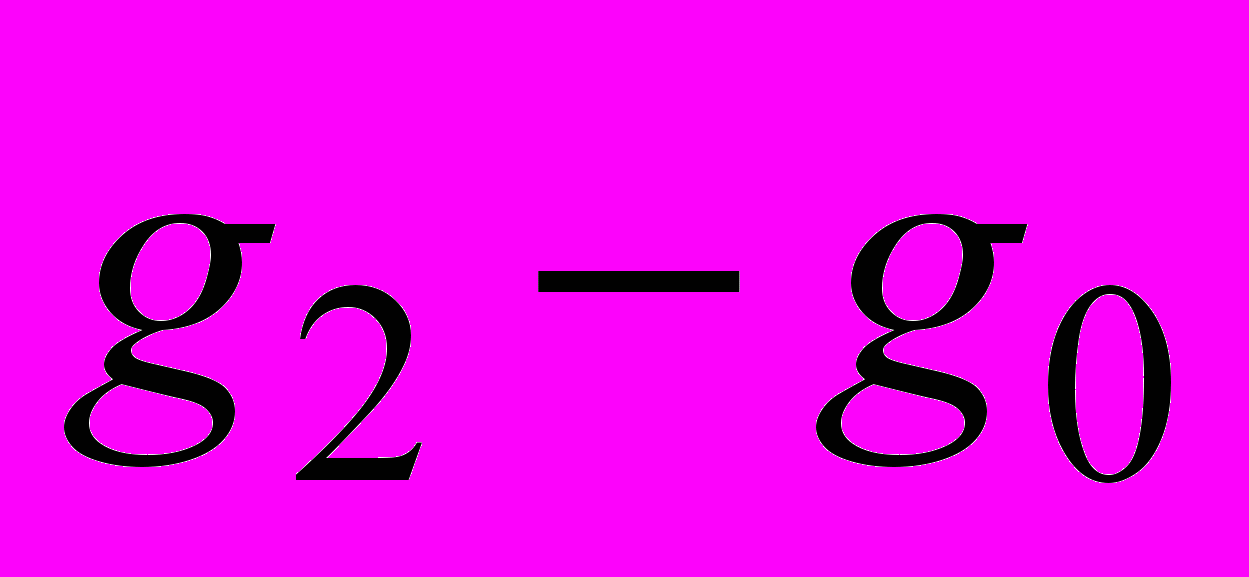

Контрольные расчеты показали, что во всем исследуемом диапазоне межэлектродных зазоров максимальная погрешность эмпирической формулы не превышает 18 %. В диапазоне межэлектродных зазоров 0,3… 1,0 мм, то есть там, где ошибки определения функции F в наибольшей степени влияют на результаты расчетов профильной модификации, погрешность не превышает 7 %
Проверка положений методики проводилась путем плоского моделирования процесса финишной электрохимической обработки зубчатого колеса на ЭВМ. Анализ картины электрического поля, приведенной на рис. 11, показал, что на линии зацепления и вблизи зоны с наименьшими межэлектродными зазорами, форма силовых линий практически не отличается от принятых в расчетах дуг окружностей, нормальных к профилю изделия в рассматриваемой точке и к профилю катода.
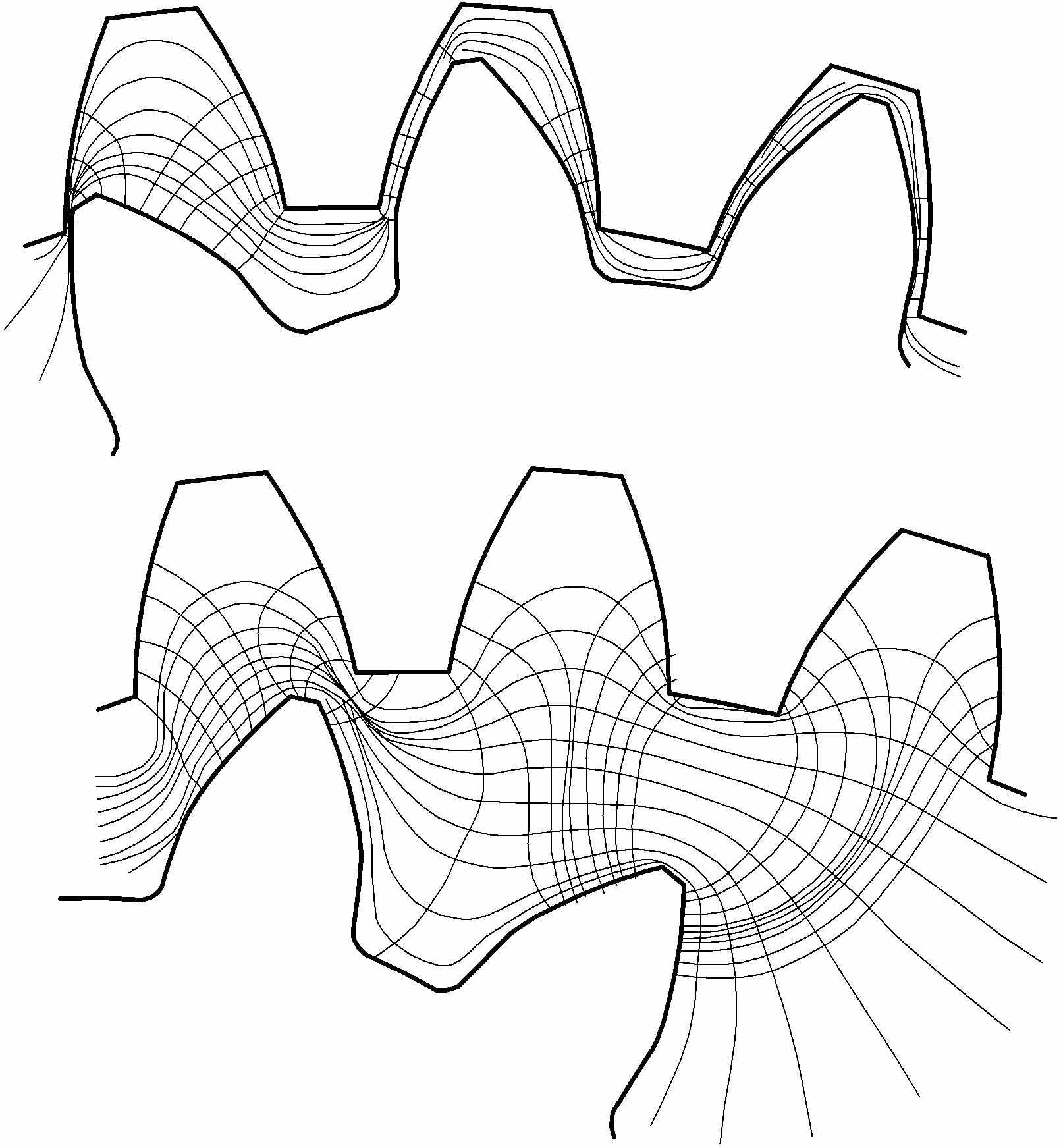
Рис. 11. Моделирование электрического поля между зубчатыми электродами
Количественный анализ, устанавливающий степень соответствия физической и математической моделей, проведенный сравнением величины межэлектродных зазоров, ширины зоны действия, функции
, «условной» интенсивности, показал следующее. В зоне линии зацепления погрешность величин межэлектродных зазоров
несущественна. При увеличении зазоров
и уменьшении «условной» интенсивности в 20… 25 раз, погрешность
достигает 55…64 %. Сравнение величин функции
, косвенно учитывающей влияние неоднородности электрического поля на интенсивность процесса, показало, что в зоне линии зацепления погрешность
не превышает 5…8%.Моделирование поля показывает, что принятая при расчетах профильной модификации математическая модель адекватно отражает действительный физический процесс. Разработанные методы определения параметров формообразующей поверхности зубьев обкаточного катода позволяют автоматизировать полностью или поэлементно процесс проектирования инструмента.
В пятой главе приведены результаты практической реализации предложенной технологии зубообработки незакаленных цилиндрических зубчатых колес.
Совместно с ОАО «АК «Туламашзавод» были изготовлены: комплекс технологической оснастки для получения заготовок цилиндрических колес с зубьями, резцовые головки для нарезания круговых зубьев, шевера-прикатники для чистовой зубообработки и хоны для отделочной зубообработки.
Экспериментальные исследования, проведенные кафедрой технологии машиностроения ТулГУ на производственной базе ОАО «АК «Туламашзавод», показали, что для обработки зубчатых венцов шестерен, полученных методом комбинированного выдавливания, требуется только чистовая зубообработка с удалением минимального припуска 0,12…0,2 мм.
В предложенной технологической схеме чистовая зубообработка осуществляется запатентованным способом двумя инструментами шеверами-прикатниками (рис. 12).
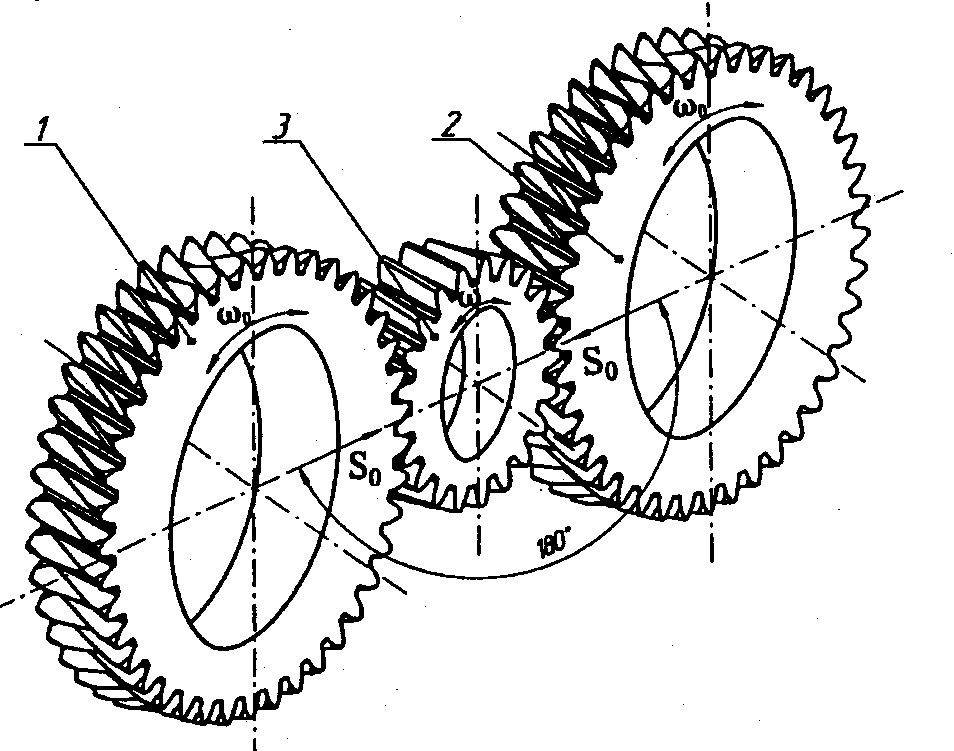
Рис. 12. Схема способа чистовой обработки цилиндрических зубчатых колес
1, 2 - два инструмента шевера-прикатника; 3 – обрабатываемая заготовка
Использование двух шеверов повышает производительность зубообработки. Эти шеверы-прикатники имеют разнонаправленные винтовые стружечные канавки и направления зубьев, что выравнивает условия резания на обеих сторонах обрабатываемых зубьев. Благодаря этому обстоятельству улучшается качество обработки.
Параметры точности цилиндрических зубчатых колес до и после чистовой зубообработки шевингованием-прикатыванием приведены в таблице.
Параметры точности зубчатых колес, обозначение | Величина параметров после обработки, мм | |
предварительной | чистовой | |
Колебание измерительного межосевого расстояния за оборот, Fir | 0,106 | 0,0494 |
Колебание измерительного межосевого расстояния на одном зубе, fir | 0,034 | 0,024 |
Колебание длины общей нормали, Fvw | 0,091 | 0,07 |
Наибольшая погрешность шага, fpr | 0,085 | 0,023 |
Для реализации процесса чистовой зубообработки опытной партии зубчатых колес с круговыми зубьями разработана новая конструкция инструмента шевера-прикатника (рис. 13), представляющего собой закаленное цилиндрическое зубчатое колесо, на боковых поверхностях зубьев 1 которого выполнены режущие кромки 2, образованные пересечением поверхностей зубьев с винтовыми поверхностями стружечной канавки 3. ![]() | Запатентованный шевер-прикатник в зацеплении с обрабатываемой шестерней масляного насоса показан на (рис. 14). ![]() |
Рис. 13. Конструкция шевера-прикатника с круговыми зубьями | Рис. 14. Шевер-прикатник в зацеплении с шестерней масляного насоса |
Была разработана технология нарезания зубьев инструмента. Для профилирования круговых зубьев шевера-прикатника (в соответствии с методикой, приведенной во 2 главе) разработан комплекс технологической оснастки, включающий фрезерные оправки и специальный зуборезный инструмент – резцовые головки.
Зубообработка опытной партии шевингованием-прикатыванием одним инструментом с радиальной подачей заготовки производилась на модернизированном токарном станке (рис. 15). | ![]() |
![]() | |
Рис. 15. Экспериментальная обработка цилиндрических зубчатых колес шевингованием-прикатыванием | Рис. 16. Схема шевингования-прикатывания одним инструментом с радиальной подачей |
Схема процесса показана на рис. 16. Шевер - прикатник 1 был установлен на инструментальной оправке 2 в шпинделе станка. Инструментальная оправка поджималась центром 3, установленным в задней бабке станка. Зубчатая заготовка колеса 4 находилась в беззазорном зацеплении с инструментом и свободно вращалась на оправке 5 приспособления 6, установленного на резцедержателе станка.
На экспериментальной установке была обработана партия из 50 цилиндрических зубчатых колес с модулем 2 мм и числом зубьев 11 цилиндрическим шевером-прикатником с числом зубьев 31.
Обработка осуществлялась с реверсированием за три рабочих цикла с периодической подачей сближения заготовки и два цикла выхаживания без подачи заготовки.
Были установлены оптимальные режимы обработки:
- частота вращения шпинделя n=315 мин-1;
- припуск 0,08…0,12 мм по толщине зуба;
- радиальная подача вдоль оси обрабатываемой заготовки 0,03 мм/цикл.
Шероховатость поверхностей зубьев исходной заготовки составляла
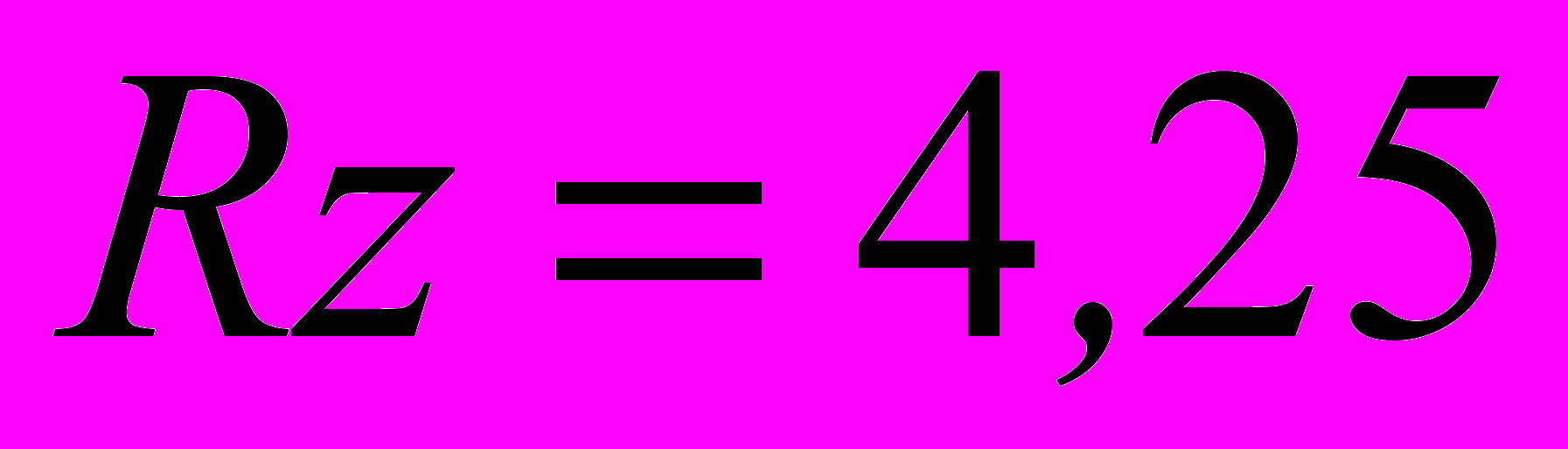
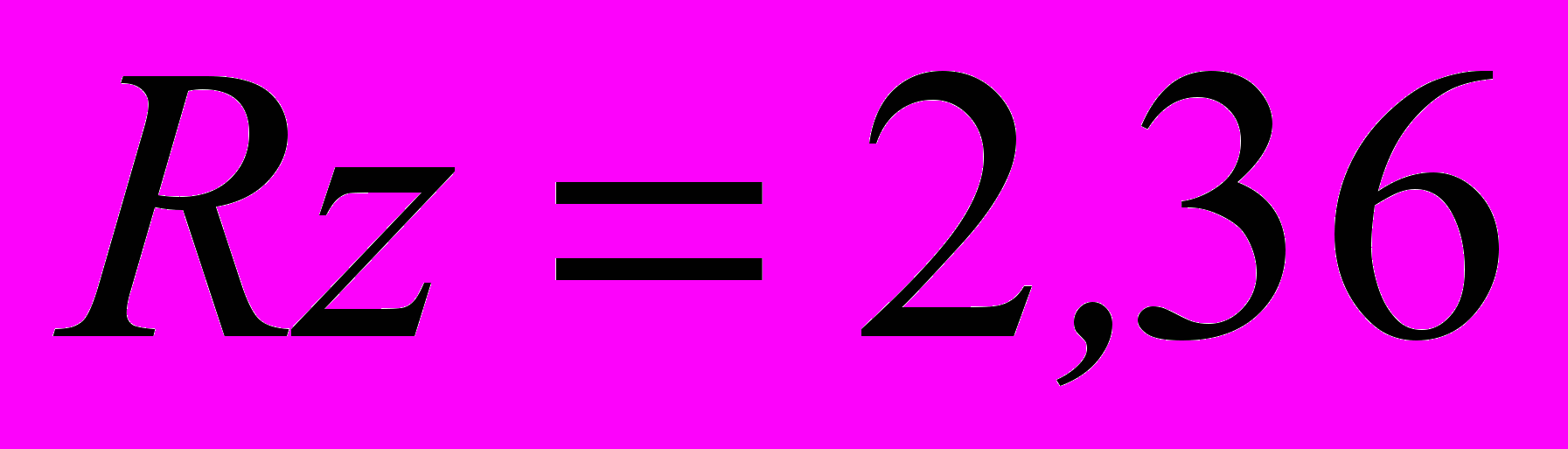
Математическая обработка экспериментальных данных показала, что по параметрам Frr – радиальное биение зубчатого колеса и fir – наибольшее радиальное биение на одном зубе точность повышается на 2…3 степени по ГОСТ 1643-81, по параметрам fPr – погрешность шага и FPr – накопленная погрешность шага на 1 степень. Таким образом, экспериментальные исследования подтвердили высокую исправляющую способность процесса шевингования-прикатывания при повышении производительности в 3…4 раза по сравнению с другими способами чистовой зубообработки, что открывает возможности создания на основе этого процесса инновационных технологий изготовления цилиндрических зубчатых колес из прогрессивных заготовок с предварительно оформленным зубчатым венцом.
Характерной особенностью этого способа является выдавливание металла, которое происходит как в радиальном, так и в осевом направлениях. В результате часть материала заготовки после чистовой зубообработки шевингованием-прикатыванием выдавливается за пределы контура зуба с образованием заусенцев. Высота заусенцев может достигать в радиальном направлении – 0,2…0,4 мм, в осевом – 0,15…0,25 мм.
Для снятия заусенцев и наложения фасок по контуру зубьев колес был разработан высокопроизводительный метод с использованием гребенчатых фрез.
Актуальной задачей является определение параметров профиля исходного контура рейки для этих инструментов и параметров установки инструмента относительно заготовки. Для решения этой задачи в диссертации разработана трехмерная САПР автоматизированного расчета исходного профиля производящей рейки для зубофасочных фрез, работающих по методу обката. Структура специализированной САПР приведена на рис. 17.
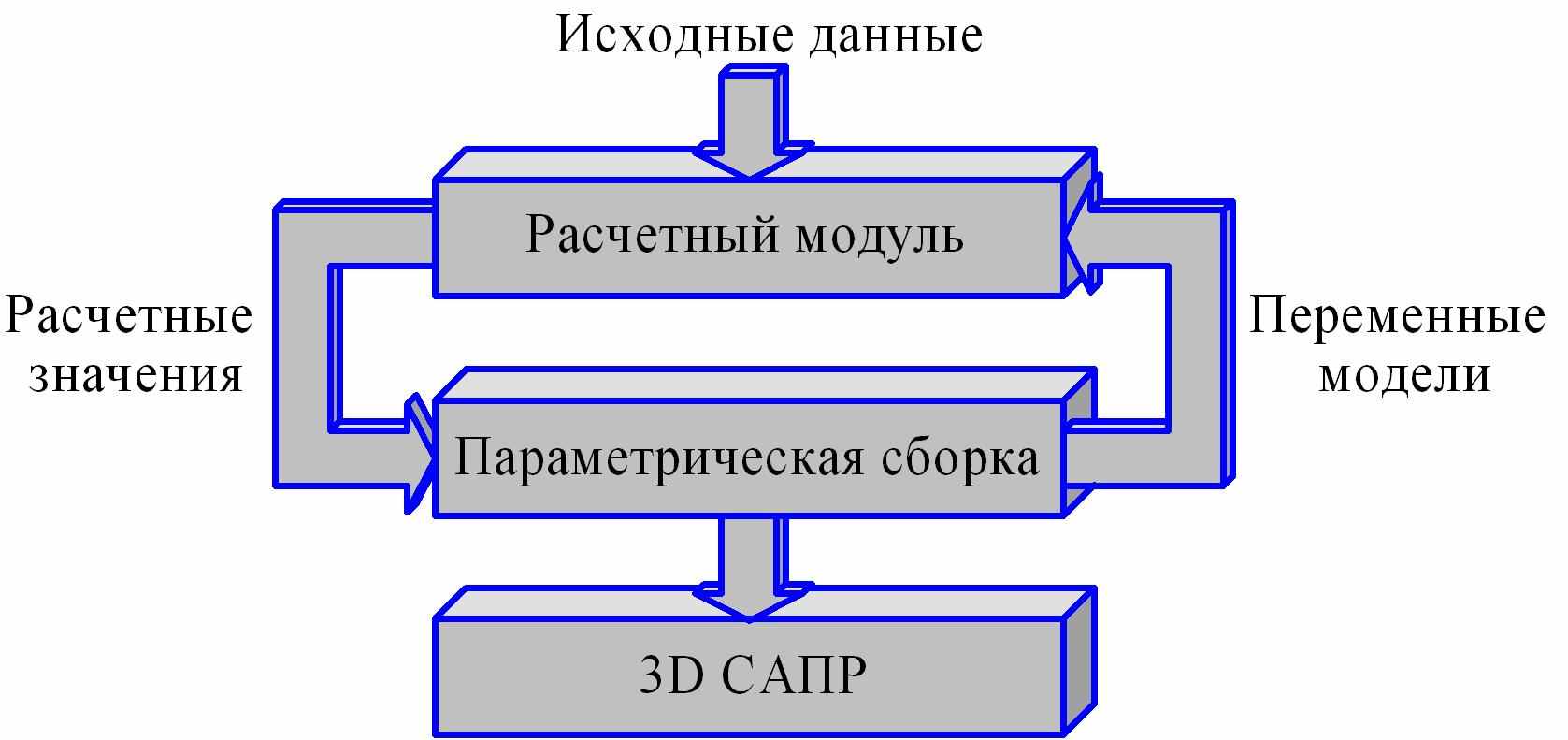
Рис. 17. Структурная схема специализированной САПР
Она основана на трехмерном геометрическом ядре, например, КОМПАС – 3D (рис. 18, а), с помощью которого первоначально создается параметрическая сборка, в которой ряд размеров задаются как переменные параметры. К ядру подключается специализированный расчетный модуль для определения значений переменных параметров проектируемого объекта (рис. 18, б). В итоге получается трехмерная сборка зубофасочной фрезы для обработки конкретного колеса. При этом конструктор получает численные значения параметров и чертежи производящей рейки и всего инструмента.
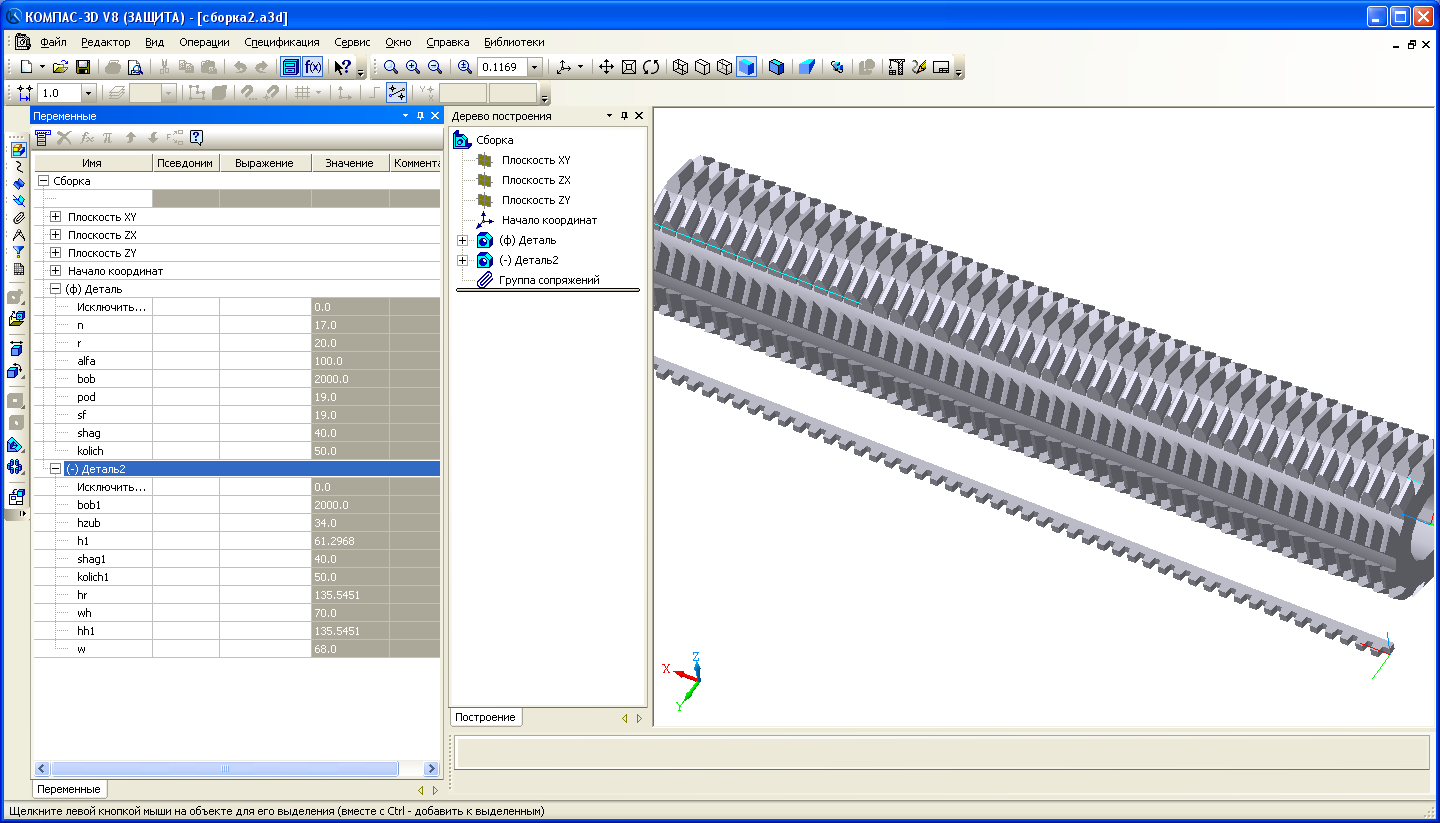
а)
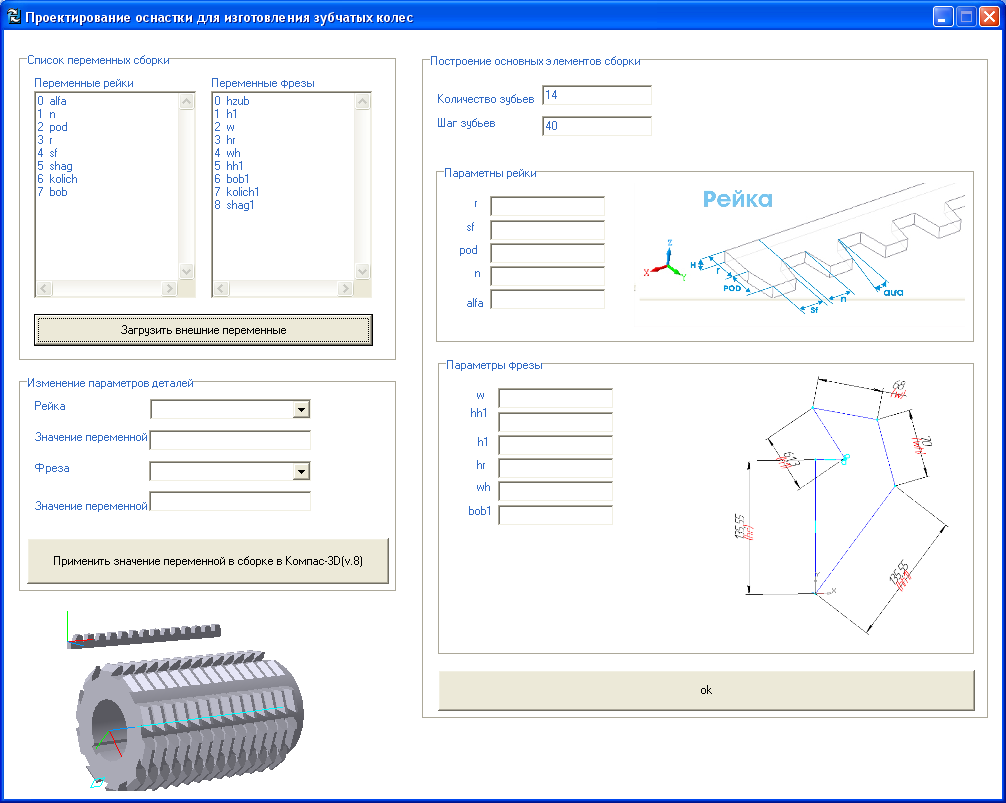
б)
Рис. 18. Специализированная трехмерная САПР автоматизированного расчета исходного профиля производящей рейки для зубофасочных фрез:
a) окно КОМПАС – 3D; б) форма приложения
Шестая глава посвящена реализации новых процессов отделочной обработки закаленных зубьев цилиндрических колес.
Ранее разработанный способ комбинированной электрохимической обработки и алмазного зубохонингования обладает широкими технологическими возможностями, что позволяет использовать его в рамках предложенной ресурсосберегающей технологи изготовления цилиндрических колес для финишной зубообработки колес с внутренними венцами. При этом необходимо учитывать, что ряд таких зубчатых колес относятся к классу тонкостенных деталей, обладающих невысокой жесткостью в радиальном направлении. Такие колеса в наибольшей степени подвержены деформациям вследствие термообработки, что приводит к возникновению геометрических погрешностей зубчатых венцов. Производственные исследования, проведенные на АО «Тулаточмаш» показали, что после закалки происходит ухудшение геометрических параметров таких деталей на одну-две степени по ГОСТ 1643-81. Возрастающие требования к качеству изготовления зубчатых колес вызывают необходимость осуществлять исправление возникших погрешностей в процессе отделочной операции.
При финишной электрохимической обработке зубьев цилиндрических колес с внутренними венцами для жесткой кинематической связи между заготовкой и катодом - инструментом применен так называемый «электрический вал», образованный парой реактивных синхронных электродвигателей. Опытно-промышленная установка для реализации этого процесса создана на базе модернизированного токарного станка, оснащенного фрезерной головкой (рис. 19).
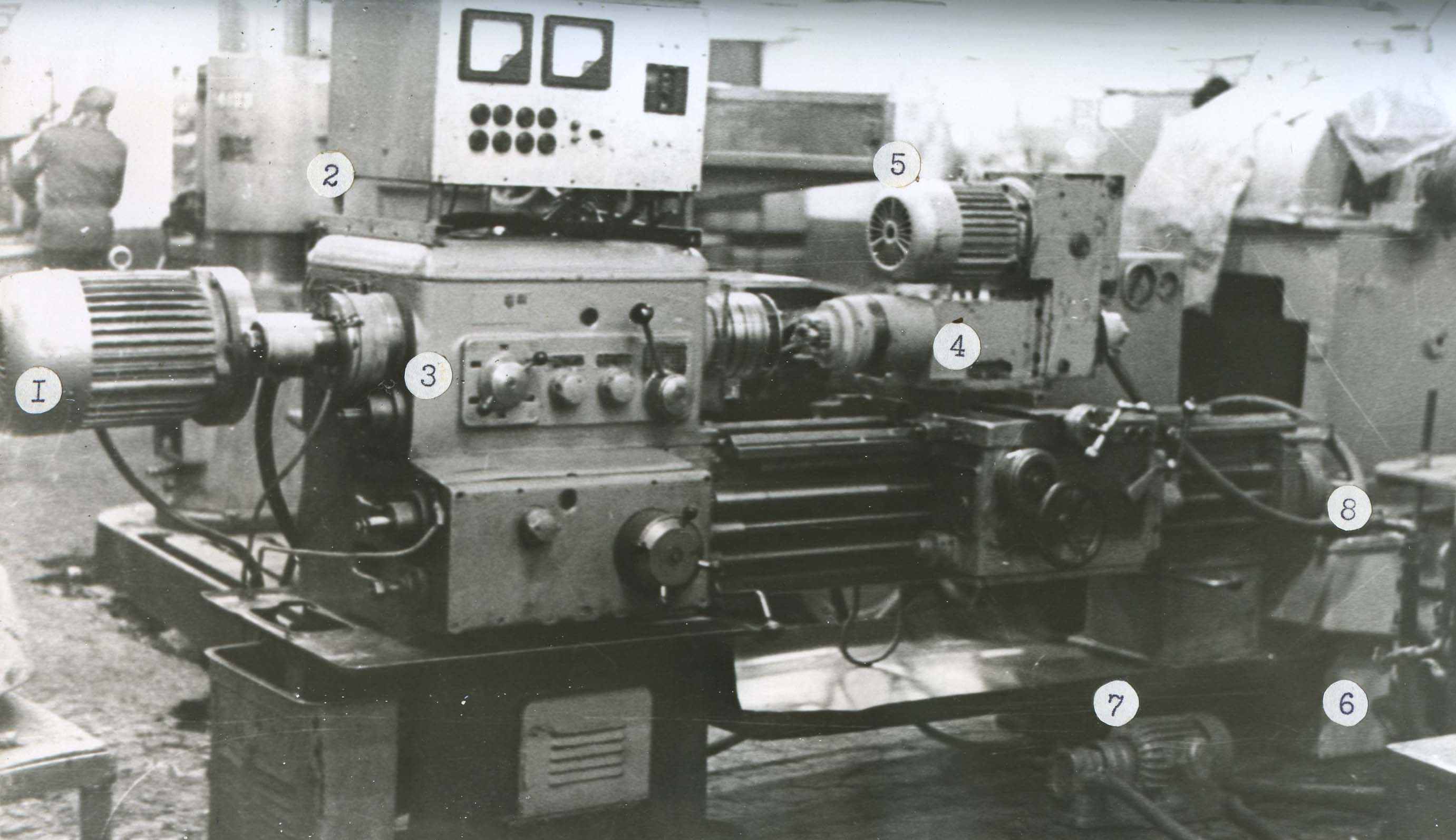
Рис. 19. Опытно-промышленная установка для финишной электрохимической обработки внутренних зубьев закаленных цилиндрических колес
Базовый станок и фрезерная головка были модернизированы для обеспечения необходимой кинематической связи, подвода постоянного напряжения к вращающимся электродам (обрабатываемой заготовке колеса и катоду-инструменту), подачи электролита в активную зону обработки и его слива.
Обработанная в ходе экспериментов коронная шестерня Т25-1901011 с внутренним зубчатым венцом, представлена на рис. 20. Здесь же показаны инструменты для алмазной электрохимической зубообработки закаленных зубчатых колес.
![]() | Заготовки обрабатывали на опытно-промышленной установке при следующих условиях эксперимента: электролит – 15 %-ный водный раствор ![]() |
Рис. 20. Коронная шестерня Т25-1901011 и катоды-инструменты для ее обработки |
Измерения показали, что в результате финишной электрохимической обработки у 50 % деталей опытной партии значения
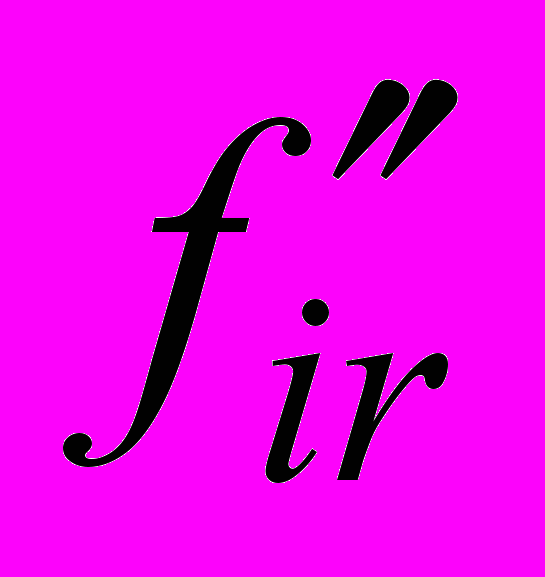
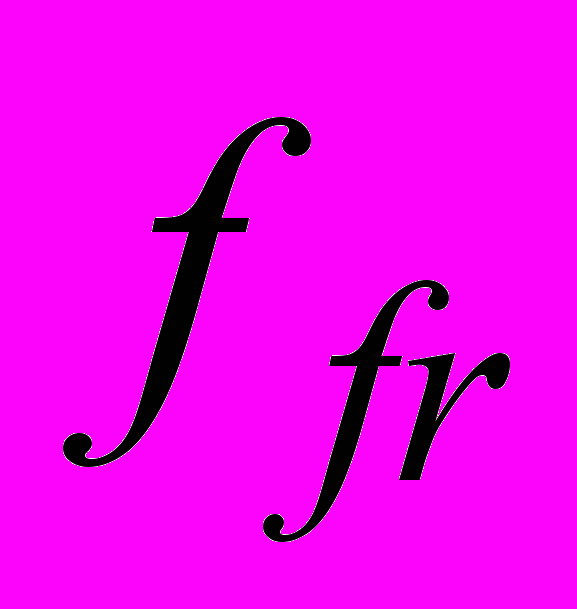
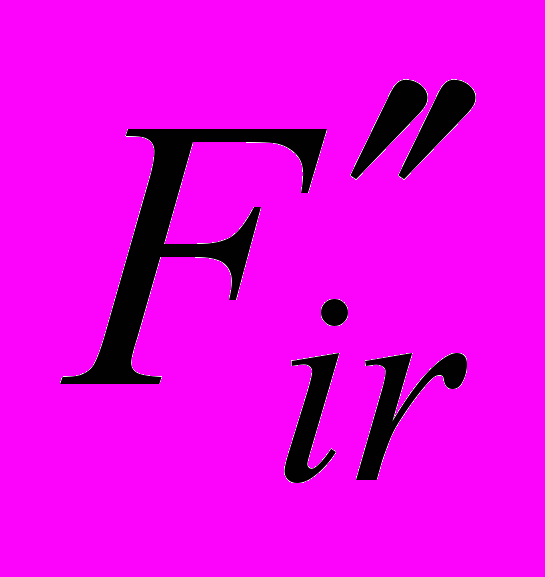
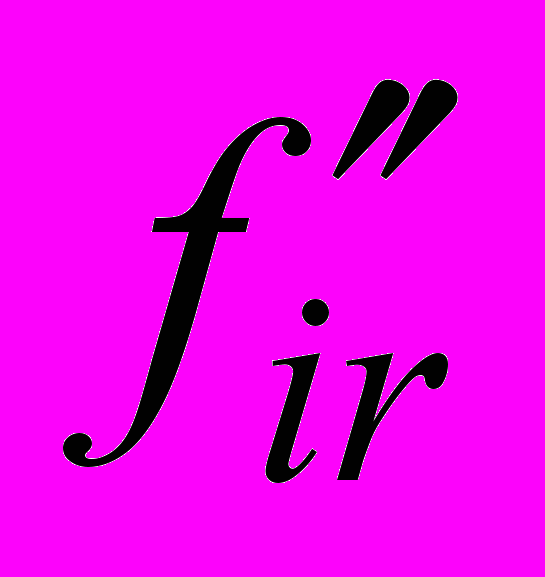
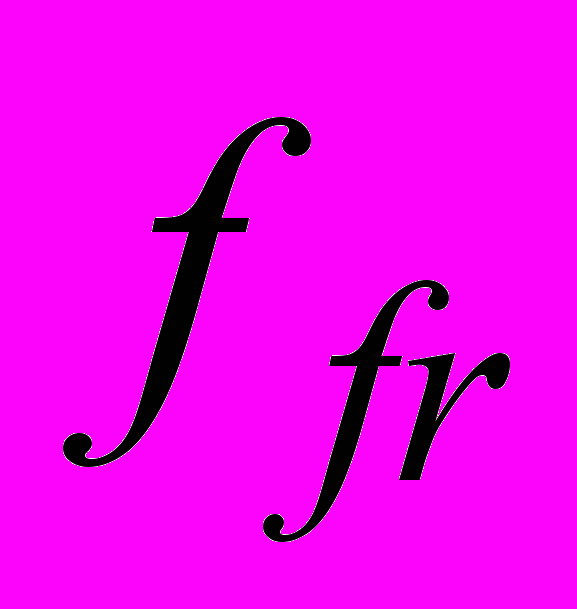
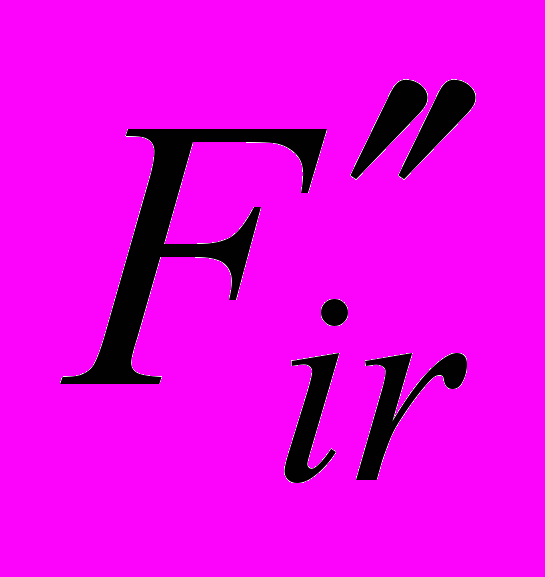
![]() | В целях экономии синтетических алмазных зерен в диссертации разработана новая конструкция зубчатого хона (рис. 21), конструктивно представляющего собой точное стальное цилиндрическое зубчатое колесо с уменьшенной толщиной зубьев. На боковые эвольвентные поверхности зубьев хона 1 нанесен абразивный слой из металлической связки с равномерно распределенными в ней зернами синтетических алмазов. При этом абразивный слой нанесен на участки 2, образующие одно- или многозаходную спираль, шириной b = 2…3 мм. |
Рис. 21. Зубчатый хон |
Данное конструктивное решение позволило существенно уменьшить площадь контакта между инструментом и заготовкой-колесом, что создает благоприятные условия подвода СОЖ к зоне резания и отвода стружки. Такой хон улучшает качество обработки и позволяет повысить производительность процесса за счет увеличения давления на зубья обрабатываемого колеса и лучшего удаления отходов из зоны обработки.
Разработана технология изготовления зубчатых хонов. Решены вопросы синтеза высококачественных монокристаллических алмазов, разработано технологическое оснащение, в частности, блок-матрицы аппаратов высокого давления, проведено исследование технологических возможностей повышения надежности аппаратов высокого давления для синтеза алмазов.
Целый ряд инновационных разработок, выполненных в ходе подготовки диссертации прошли успешные производственные испытания и были рекомендованы для внедрения на ведущих машиностроительных предприятиях региона. В частности:
- на ОАО «Акционерная компания «Тульский машиностроительный завод» успешно прошли испытания и рекомендованы для внедрения в производство в 2008 г.:
1) модифицированная конструкция масляного насоса дизельного двигателя ТМЗ 450Д, оснащенного передачей, состоящей из шестерен с арочными (круговыми) зубьями;
2) цилиндрическая передача с арочными (круговыми) зубьями, состоящая из модифицированных шестерен 077 110 013М и 077 110 014М;
3) метод финишной зубообработки цилиндрических шестерен с арочными (круговыми) зубьями шевингованием-прикатыванием;
4) комбинированный инструмент – шевер-прикатник для финишной зубообработки цилиндрических шестерен с арочными (круговыми) зубьями;
- на предприятиях ОАО « ВеАл » и АО « Полема-чермет» при изготовлении оснастки для получения искусственных алмазов использована научная работа "Технологическое обеспечение ресурса аппаратов высокого давления (АВД) для синтеза монокристаллических алмазов"; по результатам использования данная работа рекомендована для внедрения на предприятиях алмазной промышленности
- на АО «Тулаточмаш» при изготовлении высоконагруженной бандажированной технологической оснастки приняты к внедрению предложенные способы нормирования точности коротких конусов, средства контроля коротких внутренних и наружных конусов, технологические приемы для обеспечения точности механической обработки конусов, а также приспособления для сборки коротких конических соединений с натягом.