Повышение надежности карданных передач трансмиссий сельскохозяйственной техники
Вид материала | Документы |
- Программные средства компьютерного проектирования зубчатых передач в обобщающих параметрах, 26.58kb.
- Повышение надежности программного обеспечения ядерных радиационно-опасных объектов, 223.97kb.
- Обеспечение работоспособности и ресурсосбережения при восстановлении и упрочнении сложнопрофильных, 494.07kb.
- Методические указания по выполнению лабораторно практической работы расчет надежности, 151.69kb.
- Программы развитие сельского хозяйства и регулирование рынков сельскохозяйственной, 940.53kb.
- Повышение эксплуатационных свойств трансмиссий транспортных машин специального назначения, 297.76kb.
- Модернизация туннельной печи для обжига керамики зао «комтех», 58.16kb.
- Научно-образовательный материал «надежность электрической изоляции», 32.63kb.
- Вопросы для подготовки к экзамену по дисциплине «Теория надежности», 8-й семестр, 2011, 20.46kb.
- Повышение надежности и эффективности оборудования средствами информационной системы, 273.86kb.
^ Прогнозирование надежности карданных передач в эксплуатации
Методика прогнозирования надежности КП сельхозтехники разработана на основе метода Монте-Карло. Сопоставление долговечности опытного и серийного КШ позволяет установить коэффициент повышения долговечности

где
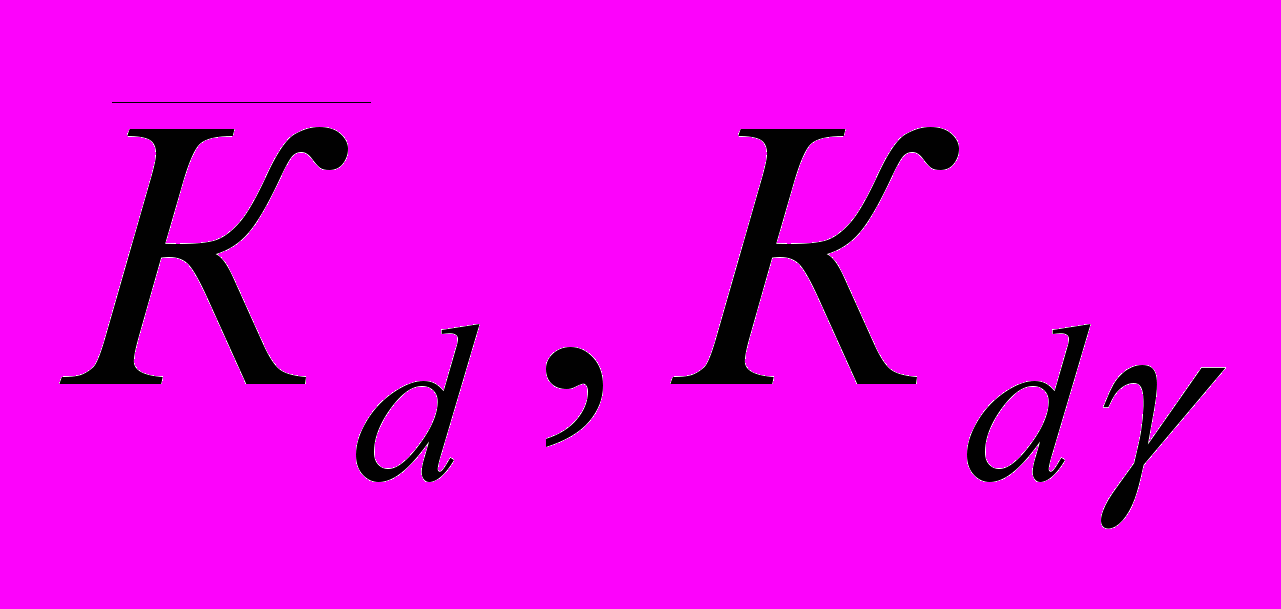
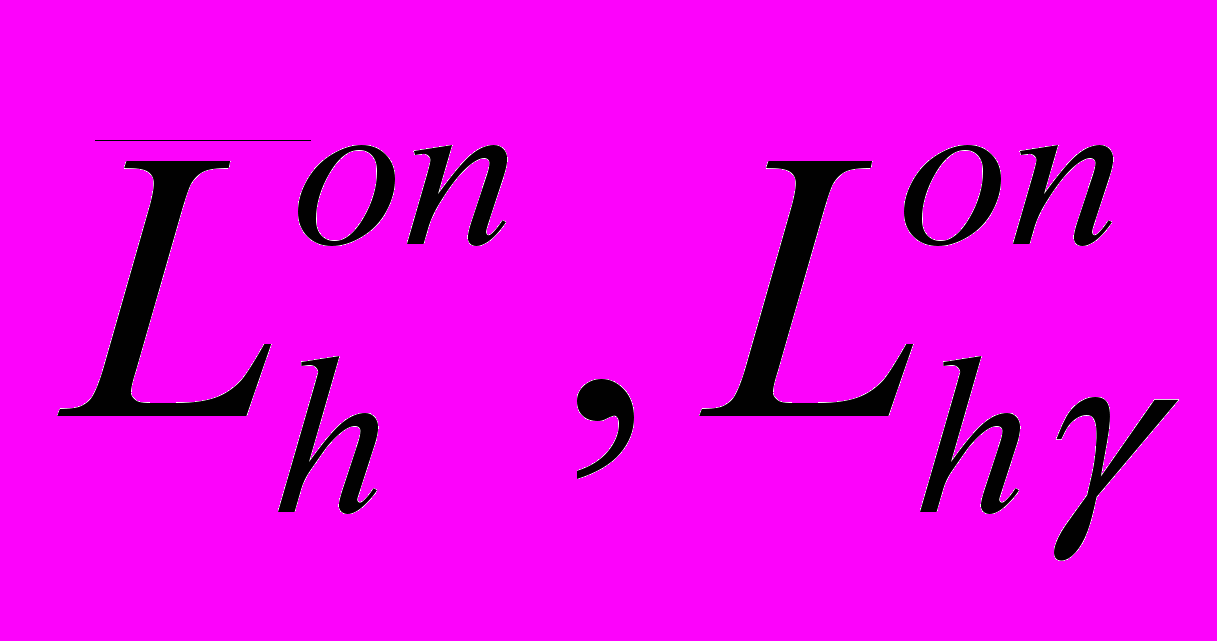
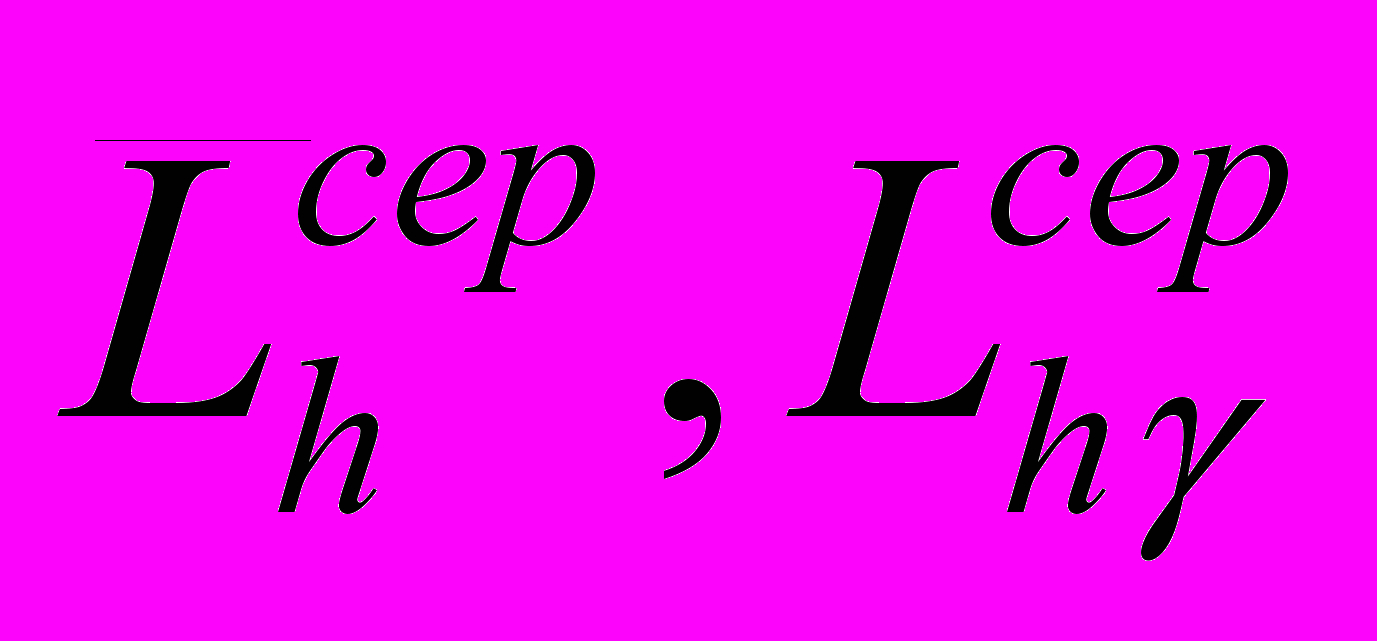
Для оценки конкурентоспособности мероприятий повышения надежности КП на основе способов ТОР, в условиях многокритериальной оценки, используем интегральный критерий – коэффициент КК конкурентоспособности
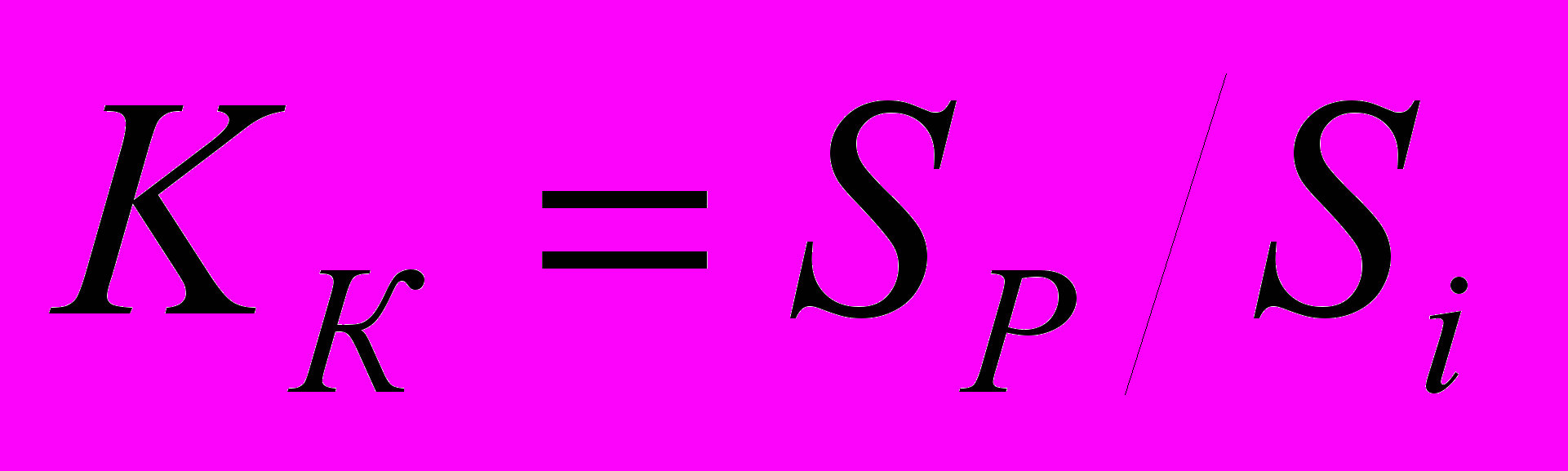

где Sp – площадь радара; Si – общая площадь оценочной фигуры; Хi, Yi – координаты вершин радара; n – число оценочных показателей изделия (показатели рациональности, экономической целесообразности и эффективности способов ТОР).
При оценке конкурентоспособности отремонтированного изделия показателям качества и цене придают разный вес, поэтому конкурентоспособность изделия количественно можно рассчитать с учетом фактора предпочтений

где Цфi, Цmaxф – фактическая цена i-го изделия и максимальное значение цены сравниваемых изделий; – значимость цены изделия для покупателя (0≤λ≤1).
^ 3 Совершенствование карданных передач энергонасыщенной сельскохозяйственной техники
Основные тенденции совершенствования КП направлены на снижение неравномерности распределения нагрузки в ПУ, более полное использование ресурса ПУ и повышение приспособленности КШ к мероприятиям ТОР.
Следствием неравномерности распределения нагрузки в ПУ является возникновение явления перекоса их элементов, что существенно снижает ресурс КШ.
Выражение угла перекоса θ, рад, осей шипа и подшипника имеет вид

где θGr, θеf, θН, θY, θХ – углы перекоса элементов от радиального зазора, упругого прогиба шипа, упругих контактных деформаций элементов соединения «шип – ролик – стакан», изгиба и скручивания проушины вилки, рад (рисунок 8).
![]() | ![]() | ![]() |
![]() | ![]() | ![]() |
а – от радиального зазора; б – от упругого прогиба шипа; в – от упругих контактных деформаций элементов соединения «шип – ролик – стакан»; г – от упругого изгиба проушины вилки; д – при «опрокидовании» подшипника; е – при «самоустановке» подшипника | ||
Рисунок 8 – Графическая иллюстрация перекоса элементов ПУ КШ |
Угол перекоса от радиального зазора θGr в ПУ определяем по формуле

где GrСр, Gr1, Gr2 – среднее и начальные значения радиального зазора в ПУ КШ, м; R=Н/2 – расстояние от торца шипа до центра крестовины Н, м.
Угол перекоса оси шипов крестовины θеf определяем по зависимости
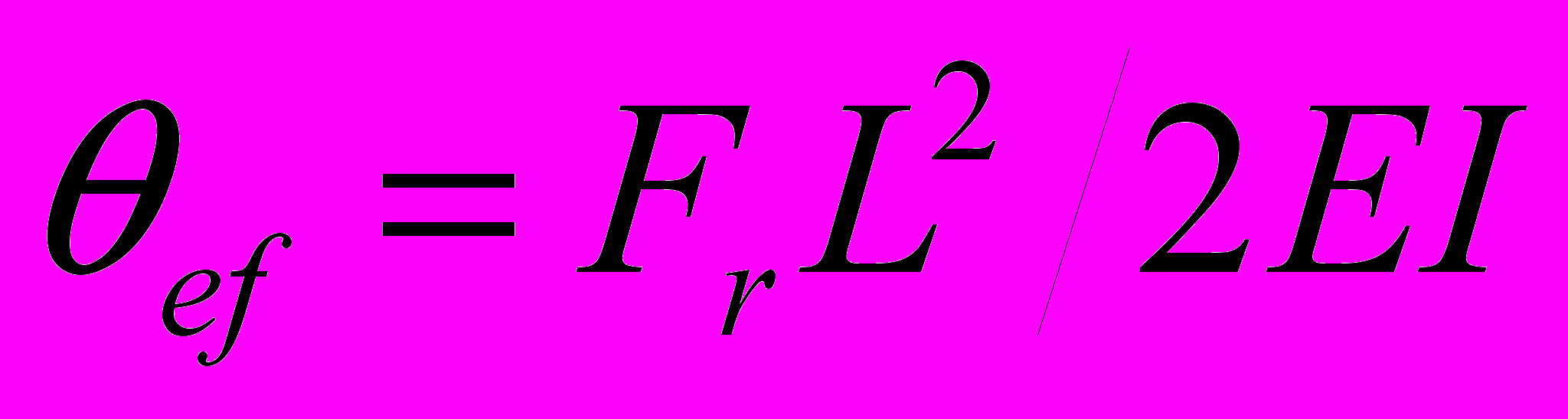
где Fr – радиальная сила ПУ, Н; L – разность длины шипа и половины длины ролика, м; Е – модуль упругости, МПа; I – момент инерции сечения шипа, м4.
Угол перекоса θН осей элементов ПУ от упругих контактных деформаций элементов δН соединения «шип – ролик – стакан» равен
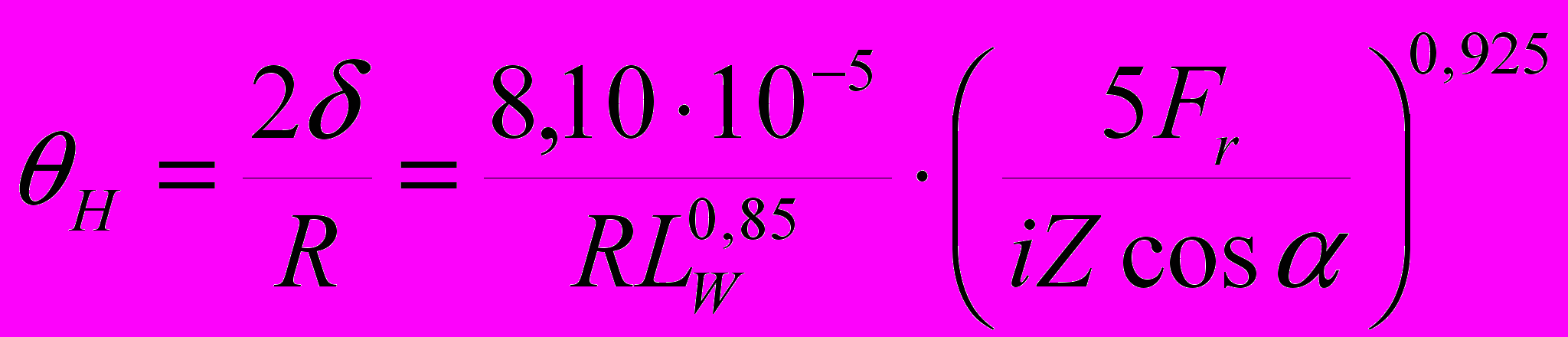
Для определения прогиба проушины δY карданной вилки, определяющего угол перекоса оси стакана θY, принимаем расчетную схему бруса переменной жесткости, нагруженного радиальной силой Fr. Тогда угол перекоса θY оси стакана определяем по геометрической формуле
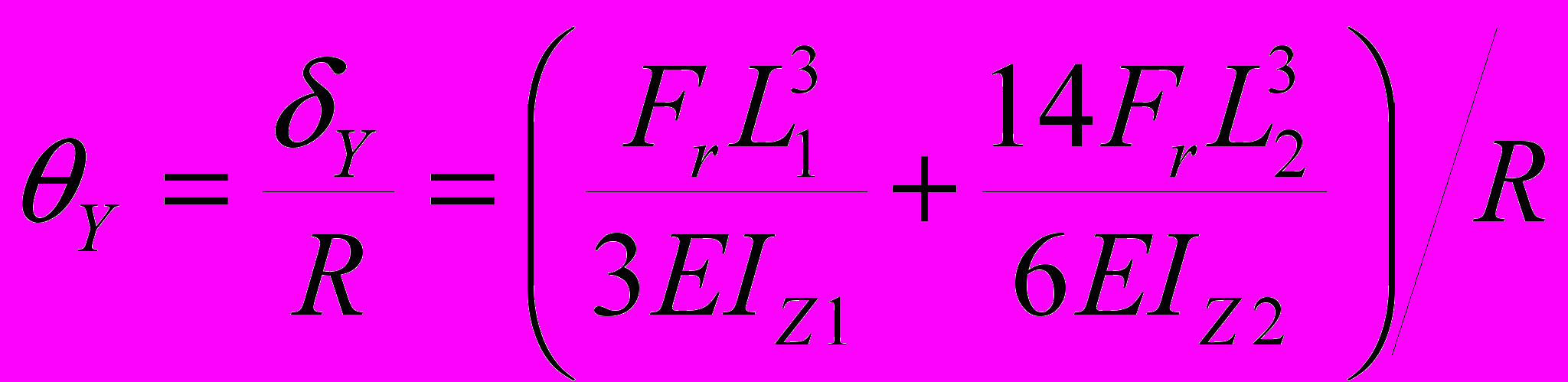
где L1, L2 – длина участков проушины вилки с отверстием и без, м; IZ1, IZ2 – осевой момент инерции сечений проушины, м4.
Угол перекоса θХ оси стакана подшипника в результате скручивания проушины вилки, в виде бруса переменной жесткости, определяем по формуле
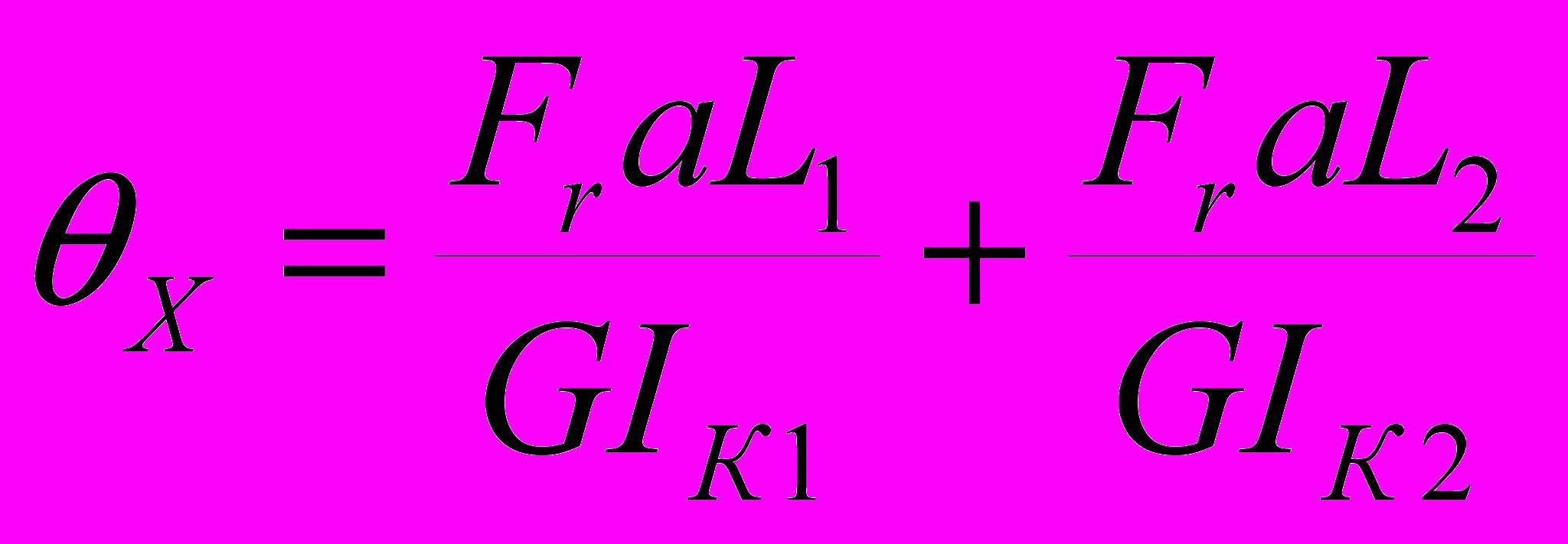
где а – плечо радиальной силы, создающей крутящий момент, м; IК1, IК2 – момент инерции кручения сечений проушины, м4; G – модуль сдвига, МПа.
Итоговое выражение угла перекоса θ, рад, осей шипа и подшипника имеет вид

Расчет выполняем на примере КШ VII типоразмера с подшипниками №804707К4С10 для стендового и эксплуатационного режимов нагружения ПУ, расположенных в двух вилках — серийной и опытной по RU 2106548.
Наибольшее влияние на общий угол перекоса элементов ПУ оказывают деформация кручения проушин вилок и радиальный зазор в ПУ. Угол перекоса осей ПУ опытной вилки по сравнению с серийной уменьшается в 5,0…7,4 раз.
С учетом геометрической связи угла перекоса θ с упругими контактными деформациями δН эффективную длину контакта LWэф в ПУ определяем как
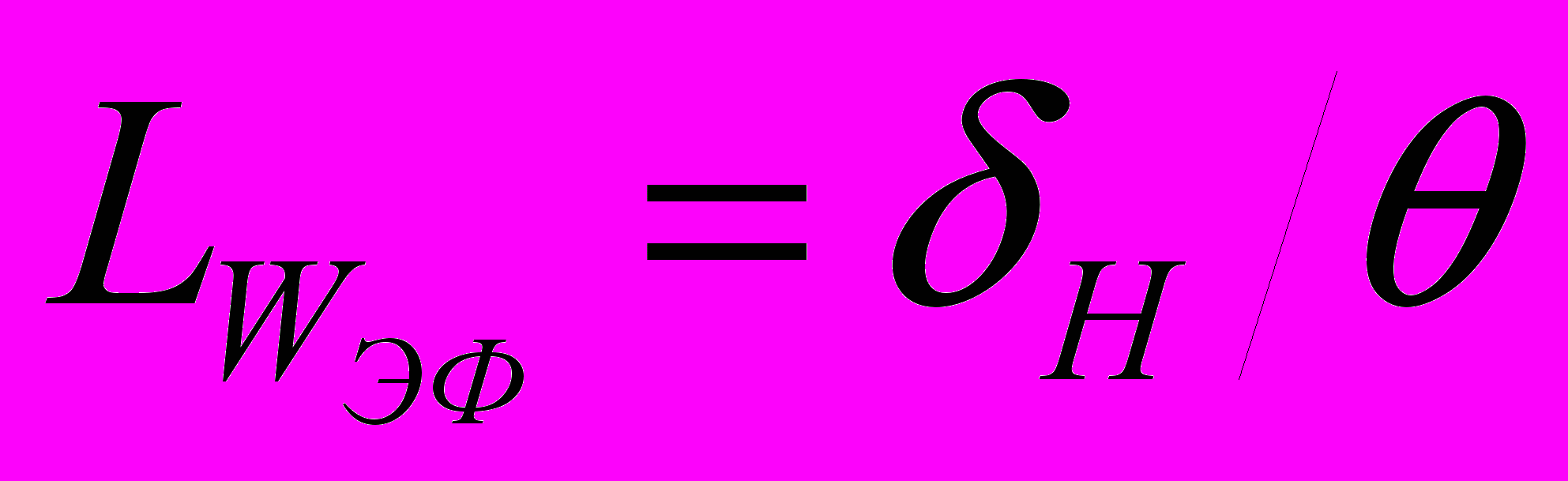
По принятым исходным данным получаем: 1) для серийной вилки при эксплуатационном режиме нагружения LWэф=1,39 мм, при стендовом – LWэф=1,81 мм; 2) для опытной вилки при эксплуатационном режиме нагружения – LWэф=10,3 мм, при стендовом – LWэф=9,04 мм. Следовательно, динамическая грузоподъемность реальных ПУ с радиальным зазором зависит от параметра LWэф

В этом случае динамическая грузоподъемность опытных ПУ в 2,3…17 раз больше серийных ПУ. Доведение величины динамической грузоподъемности ПУ до потенциальной возможно при реализации полного линейного контакта.
Для устранения перекоса в ПУ путем реализации линейного контакта их элементов, предложен КШ RU 2106548 (рисунок 9), который содержит вилки 1, 2 и крестовину 3; вилки 1 и 2 имеют фланцы 4 и 5, к которым посредством гаек 6 крепятся проушины 7 и 8; каждый шип 9 крестовины 3 установлен в проушинах 7 и 8 посредством подшипника с роликами 10 в стакане 11. Наличие оси поворота проушин вилки обеспечивает более равномерное распределение нагрузки в ПУ.
С целью повышения ремонтопригодности предложен КШ RU 2075878 (рисунок 10), который содержит вилки 1 и 2, крестовину 6 и игольчатые подшипники 5; проушины 3 и 4 вилок 1 и 2 выполнены разборными, а их полости в сечении плоскостью, перпендикулярной оси отверстий, имеют форму выпуклого правильного многоугольника с четным числом сторон; наружная поверхность стакана сопряжена с полостями проушин. Наличие разборных проушин позволяет повысить долговечность КШ за счет поворота подшипника относительно оси шипа на угол, определяемый формой полости проушин, без нарушения приработки ПУ. Это позволяет при определенной наработке провести полную замену рабочих поверхностей ПУ путем поворота крестовины в сборе относительно ее центра на 90° без разборки.
![]() | ![]() |
Рисунок 9 – Схема КШ RU 2106548 | Рисунок 10 – Схема КШ RU 2075878 |
С целью повышение надежности КП мероприятиями ТОР предложен способ замены рабочих поверхностей соединений «шип крестовины — игольчатый подшипник» (RU 2234008). Способ включает разборку, очистку, промывку и заправку смазкой ПУ, установку крестовины с поворотом на 90° по оси ее вращения относительно вилок, а также поворот каждого игольчатого подшипника на 180° относительно шипа крестовины. Поворот упомянутых элементов ПУ осуществляют при наработке 0,8…0,9 от расчетной, перед этим для восстановления радиального зазора в соединениях КШ выполняют восстановление изношенной части рабочих поверхностей ПУ до номинального размера (рисунок 11), любым способом нанесения слоя металла. Восстановление только изношенной части рабочей поверхности элементов приводит к снижению затрат труда и материальных ресурсов.
![]() | ![]() |
1 – шип крестовины; 2 – подшипник; А – зона изнашивания подшипника; Б – зона изнашивания шипа; I-I – плоскость действия силы Fr; II-II – плоскость начального зазора | 1 – крестовина; 2 – шип; 3 – втулка; 4 – игольчатые ролики; 5 – корпус подшипника; 6, 7 – отверстия; 8 – уплотнение; 9 – крышка; 10 – винт; 11, 12 – вилки |
Рисунок 11 – Схема изнашивания ПУ | Рисунок 12 – Схема КШ RU 2232309 |
С целью повышения эффективности мероприятий ТОР предложен КШ (рисунок 12) и способ его ТО (RU 2232309). Втулка шипа крестовины КШ выполнена в виде стакана и установлена основанием вверх, при этом в основании корпуса подшипника и втулки выполнены центральные соосные отверстия в виде правильного выпуклого многоугольника.
Способ ТО КШ включает частичную разборку КШ, замену изношенных поверхностей на неизношенные проводят дифференцированно для ПУ путем поворота подшипника и втулки посредством соосных отверстий в их основаниях.
Выполним обоснование и подбор отклонений размеров и натягов Nmin и Nmax в соединении «шип крестовины — втулка» (рисунок 13) по условию
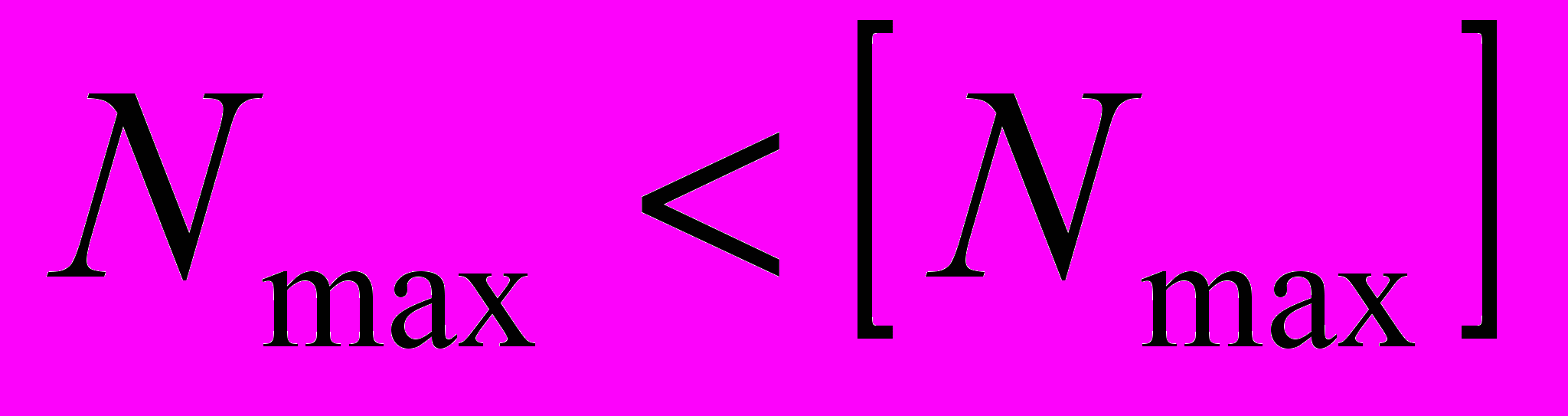
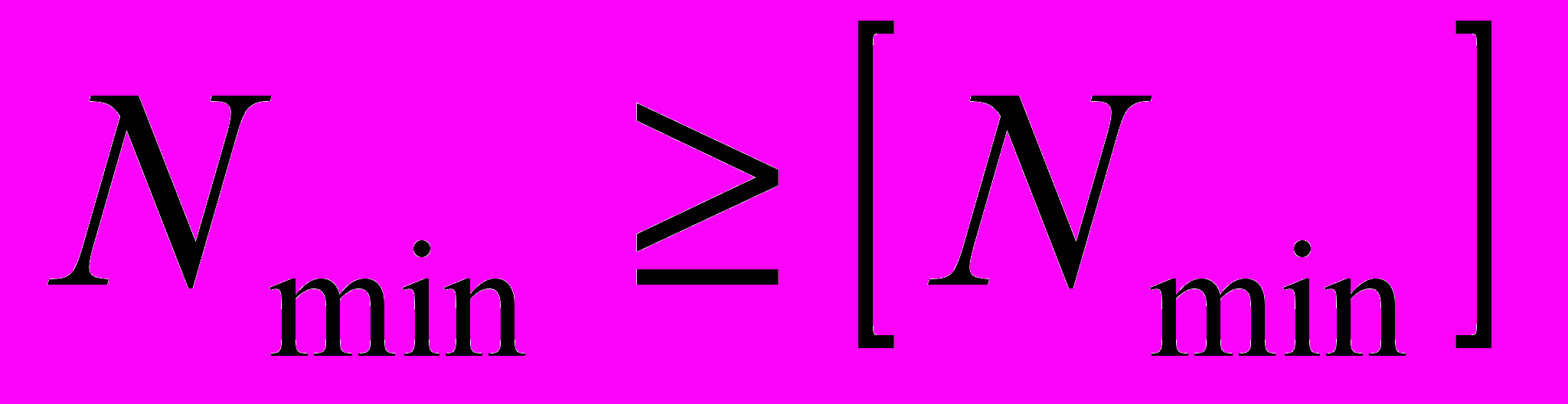
![]() | ТП – момент поворота втулки на шипе, Н·м; RП – усилие сборки соединения, Н; p – удельное давление на контактных поверхностях соединения, Н/м2; l – длина контакта поверхностей соединения, м; d1, dнс, d2 – внутренний диаметр шипа, номинальный диаметр соединения и наружный диаметр втулки, м; D1, D2 – диаметры срединных поверхностей деталей, м |
Рисунок 13 — Схема соединения «шип — втулка» |
Величину минимального допустимого натяга определяем по формуле

где N’min – наименьший расчетный натяг, м; γШ – поправка на смятие контактных поверхностей, м; γt – температурная поправка, учитывающая различие температур деталей и сборки, м; С1, С2 – коэффициенты Лямэ; f – коэффициент трения; Е – модуль упругости, МПа; η – коэффициент смятия шероховатости поверхности; RaD, Rad – параметры шероховатости поверхностей, м; αt – коэффициент линейного температурного расширения, град-1; Δtd=td-20°C, ΔtD=tD-20°C – изменение рабочей температуры td шипа и стакана tD подшипника по сравнению с условиями сборки, град.
Величину максимального допустимого натяга определяем по формуле

где N’max – наибольший расчетный натяг, м; σУ1 – предел текучести шипа, МПа.
Необходимое усилие при сборке соединения RП, Н, равно

где fП=(1,15…1,20)f – коэффициент трения при сборке.
Момент, необходимый для поворота втулки на шипе, равен
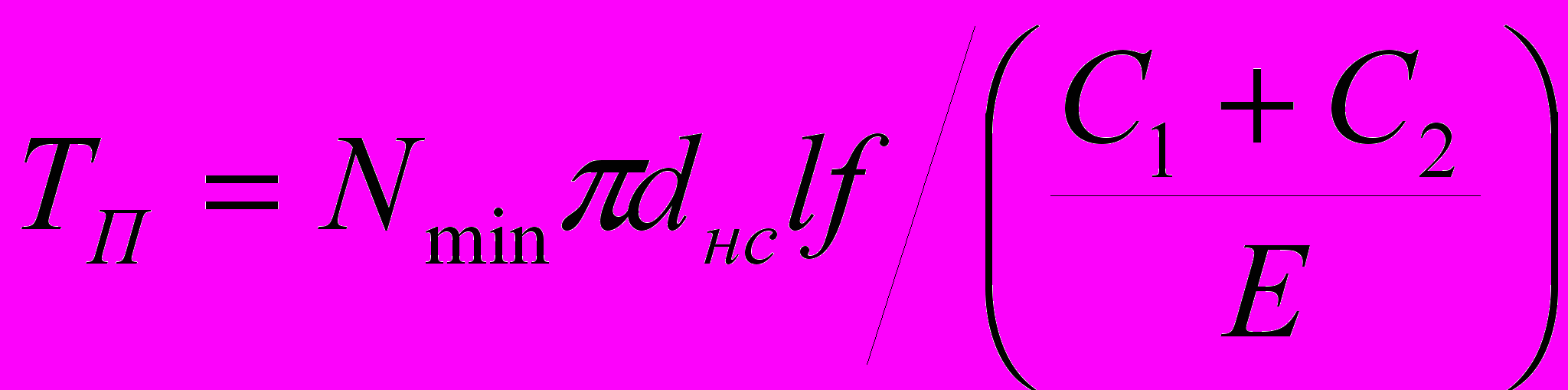
где Nmin – минимальный натяг в соединении, м.
Толщина тонкостенной втулки определяется из условия прочности
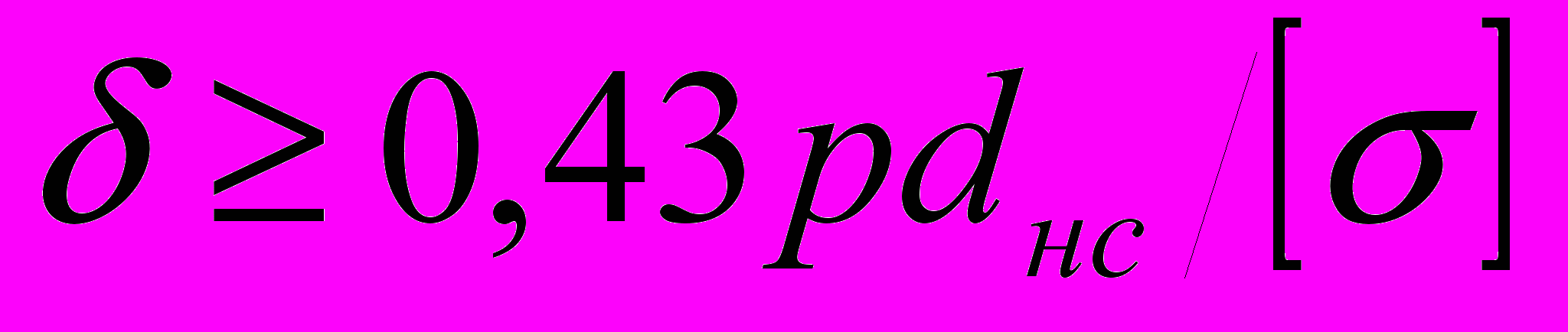
где δ – толщина стенки втулки, м; p=pmax – удельное внутренне давление в соединении, Н/м2; [σ] – допускаемое напряжение, МПа.
Изменение наружного диаметра втулки после посадки λ2, м, равно
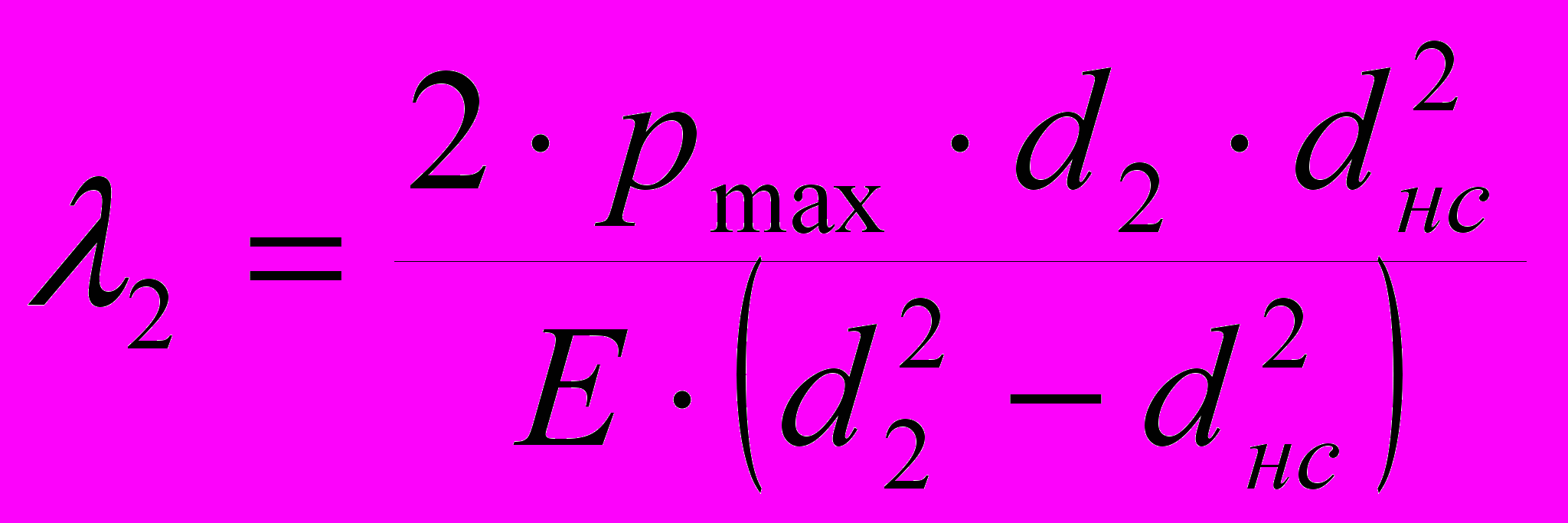
При подборе посадок максимальный момент поворота втулки принимаем не более 50 Н·м, тогда для диаметра соединения 18,5…20,0 мм максимальный натяг должен быть не более 26 мкм.
В результате расчетов на примере КШ с подшипниками № 804704 установлено, что для диаметра соединения 18,05…20,0 мм при толщине втулки 1,00…1,75 мм и натяге 0…26 мкм усилие напрессовки составляет 900…1200 Н, момент поворота втулки – 45…50 Н·м, а увеличение ее диаметра после напрессовки – 0,84…12 мкм. Проверка устойчивости охватываемой и устанавливаемой деталей показывает, что при данных соотношениях размеров деталей соединения «шип крестовины – втулка», максимальный натяг, полученный из условия прочности втулки, принимаем в качестве окончательного.
^ 4 Методы экспериментальной оценки надежности карданных передач
Оценку технического состояния КШ проводили по параметрам износа рабочих поверхностей шипов крестовин, подшипников и роликов. Для контроля размеров шипов крестовин применяли микрометры МК 0-25 ГОСТ 6507-90 и МК 75-100 ГОСТ 6507-90, подшипников — приспособление с индикатором часового типа ИЧ МН–10 ГОСТ 577–68 для измерения радиального зазора на эталонном шипе, комплекта роликов применяли лабораторные весы ВЛКТ - 500 – М ГОСТ 19491-74.
Оптико-поляризационные исследования проводили на прозрачных моделях соединения «шип крестовины — подшипник», при различных вариантах нагружения, в зоне контакта шипа и наиболее нагруженного ролика, на оптической установке VEB-300. В установке размещали нагрузочное приспособление с моделями, производили нагружение до получения четкого изображения интерференционной картины (линий изохром) и фиксировали интерференционную картину.
Объектом статических испытаний с информационным элементом являлся КШ VII типоразмера с подшипниками № 804707К4С10 с серийной и опытной (RU 2106548) вилками. Методика статических испытаний заключалась в следующем: в промытые подшипники вкладывали металлические полоски по ГОСТ 2284-79 в виде цилиндра, подшипники устанавливали на прошлифованные шипы крестовины и измеряли радиальный зазор в ПУ, собранный шарнир устанавливали в силовой контур стенда и нагружали крутящим моментом с временной выдержкой, после разгрузки шарнир демонтировали и извлекали из ПУ металлические полоски с «информацией» — отпечатками. Далее с применением микроскопа МПБ-2 определяли средние значения максимальной длины отпечатков игольчатых роликов в зоне наиболее нагруженного ролика и суммарной длины отпечатков роликов в каждом ПУ.
Объектом статических исследований работоспособности соединения «шип крестовины — втулка» являлся КШ IV типоразмера с подшипниками № 804704 и крестовиной с втулками (RU 2232309). Экспериментальное определение усилия напрессовки втулки на шип крестовины при сборке соединения проводили на машине Р–5, а момента поворота втулки на шипе использовали машину КМ–50–1. В процессе испытаний фиксировали усилие напрессовки и перемещение втулки, крутящий момент и угол закручивания, а также диаграммы процессов.
На основании расчетного и экспериментально-статистического методов установлены значения режимов нагружения КШ VII типоразмера, применяемых в МТ КСК-100А, К-700А+ПРТ-16М, Т-150К, КамАЗ-53212 и др., и IV типоразмера, применяемых в МТ ГАЗ-53А, МТЗ-82+РОУ-6 и др. Анализ уровней нагружения КШ позволил принять следующие значения режимов стендовых испытаний: 1) для VII типоразмера — TКШ=2,0 кН·м, n=1000 мин-1, βг=10,5±1,5°, βв=±1,5°, ν=1 Гц; 2) для IV типоразмера — TКШ=600 Н·м, n=1000 мин-1, β=9°. Принятые режимы наиболее близки к режимам граничных испытаний.
Продолжительность ресурсных стендовых испытаний по критерию контактной усталости определяем на основании математической модели (10).
Для проведения стендовых ресурсных испытаний шарниров КП используем модернизированный стенд (рисунок 14), который содержит станину 1, электродвигатель 2, упругую муфту 3, неподвижную опору 4 и вал 5, ведущую вилку-фланец 6, крестовину 7 с игольчатыми подшипниками и ведомую вилку-фланец 8, кольцевую крестовину 9 с игольчатыми подшипниками, ведущую 10 и ведомую 11 вилки, полый торсионный вал 12, с тензометрическим звеном, рычаги 13 и резьбовые стяжки 14 с упругими элементами, вертикальную 15 и горизонтальную 16 рамки с указателями угла излома, шлицевой вал 17 и опору 18, кривошипно-шатунный механизм 19, редуктор 20 и мотор-редуктор 21.
Общий вид стенда представлен на рисунке 15.
![]() | ![]() |
Рисунок 14 – Схема стенда | Рисунок 15 – Общий вид стенда |
Для испытаний КП разработан стенд (рисунок 16) с технологической передачей в виде зубчатого редуктора (RU 2134412, RU 2205377). Стенд содержит электродвигатель 1, упругую муфту 2, вал 3 в опоре 4, коническое колесо 5, жестко закрепленное на валу 3 и входящее в зацепление с коническим колесом 6, нагружающую муфту 7, которая соединена с коническим колесом 6 и валом 8, испытываемую КП 9, соединенную с зубчатым колесом 5 и валом 8 (рисунок 17).
![]() | ![]() |
Рисунок 16 – Схема стенда для испытания КП | Рисунок 17 – Общий вид стенда |
Момент прекращения испытаний фиксируем по повышению температуры в ПУ на ∆Т=3...6 °С (∆Т=5…10 °С) и параметров вибрации на ∆VΣ=∆AΣ=3...6 дБ. В процессе испытаний КШ фиксируют: крутящий момент, параметры вибрации, частоту вращения, угол излома, температуру в ПУ, продолжительность испытаний, износ ПУ путем измерения радиального зазора в шарнире.
Для оценки ресурса при 80 % доверительной вероятности с 20 % относительной погрешностью на стенде необходимо испытать не менее восьми ПУ.
^ 5 Экспериментальные исследования мероприятий повышения надежности карданных передач
Проявления отказа КШ изучали по выборке крестовин V типоразмера в сборе с подшипниками № 804805К5. Отказы элементов КШ представлены повреждениями цилиндрической (усталостное выкрашивание и фреттинг-износ – 53,4 %) и торцевой (задиры – 41,7 %) поверхностей шипов и донышка (задиры – 26,7 %) подшипников. Оценка износов элементов КШ IV типоразмера с подшипниками № 804704К5 показала, что случайное распределение величин износов шипов, крестовин по торцам, подшипников и роликов подчиняется теоретическому закону распределения Вейбулла. Количество деталей, пригодных к эксплуатации, составляет: по износу поверхности шипа – 72%; по износу торцов шипов – 55%; по износу игольчатых подшипников – 61%. Вероятность возникновения дефектов крестовин и ПУ составляет 0,60 и 0,76.
Напряженное состояние модели ПУ в продольной плоскости для е=0 (серийный вариант), характеризуется неравномерностью распределения напряжений в модели шипа под моделью ролика с наличием четко выраженного краевого эффекта в контакте у торца шипа и игольчатого ролика. Благоприятным является вариант нагружения e=+1 (опытный) со смещением радиальной нагрузки в направлении основания шипа крестовины примерно на 0,1…0,2 длины контакта.
При статических испытаниях КШ исследовали влияние кодированных факторов положения оси поворота е, мм, проушины опытной вилки (X1), крутящего момента T, кHм, (X2) и радиального зазора в ПУ крестовины Δi и шарнире Δш, мкм, (X3), на параметры оптимизации функции отклика, а именно суммарную длину ΣLi, мм, отпечатков роликов в ПУ (Y1), длину LQmax, мм, отпечатка под наиболее нагруженным роликом (Y2), при условиях оптимизации ΣLi→max и LQmax→max. После обработки результатов при фиксировании величины радиального зазора (фактор X3) окончательно получили следующие регрессионные уравнения:
- при Х3(Δi)=53...77 мкм


- при Х3(ΔШ)=-23...262 мкм


Графическая интерпретация уравнений (рисунки 18, 19) позволяет, например, для КШ комбайна КСК-100А, при нагружении Tкш=1410 Н·м и зазорах ∆ш=-23...262 и ∆i=53...77 мкм по зависимости ΣLi=f(e,T) определить параметр e графическим методом, как показано на рисунке 18. Аналогично выполняется определение параметра е по рисунку 19 по зависимости LQmax=f(е,Т) при ∆ш=-23...262 и ∆i=53...77 мкм. Таким образом, что для диапазона нагруженности шарниров КП по моменту Tкш=1120...1410 Н·м среднее значение параметра составляет e≈+3,75 мм.
При статических испытаниях опытного соединения «шип крестовины — втулка» исследовали влияние кодированных факторов номинального диаметра dНС, мм, соединения (Х1) и натяга N, мкм, в соединении (Х2) на параметры оптимизации функции отклика, а именно наибольшее усилие RПmax, Н, напрессовки (Y1) и минимальный момент ТПmin, Н·м, поворота (Y2), при условиях оптимизации RПmax→min и ТПmin→max.
В результате регрессионного анализа получены регрессионные модели


а) ![]() ![]() | б) ![]() ![]() | |
Рисунок 18 – Зависимость ΣLi=f(e,T) для радиального зазора в КШ ∆ш=-23...262 мкм (а) и в ПУ ∆i=53...77 мкм (б) | ||
а) ![]() ![]() | б) ![]() ![]() | |
Рисунок 19 – Зависимость LQmax=f(е,Т) для радиального зазора в КШ ∆ш=-23...262 мкм (а) и в ПУ ∆i=53...77 мкм (б) | |
Для изучения полученных моделей построены трехмерные зависимости в раскодированных обозначениях RП=f(dНС, N) и ТП=f(dНС, N) (рисунки 20, 21). Полученные поверхности относятся к поверхностям второго порядка типа минимакса. Таким образом, для определения оптимальных значений факторов необходимо из максимальных значений усилия напрессовки принять минимальное, а из минимальных значений момента поворота — максимальное.
![]() | ![]() |
Рисунок 20 – Зависимость RП=f(dНС, N) | Рисунок 21 – Зависимость ТП=f(dНС, N) |
Исследование уравнений (42) и (43) на экстремум и анализ плоских сечений трехмерный зависимостей по рисункам 20 и 21 позволяют принять следующие оптимальные значения натяга N=6,8...17,1 мкм и диаметра dНС=19,6...19,8 мм, при которых усилие напрессовки и момент поворота не превышают RП=1100 Н и ТП=46 Н·м.
Оценку влияния динамического изменения угла излома шарнира на ресурс КШ проводили расчетно-экспериментальным методом по сравниваемым вариантам нагружения: 1) расчет при угле излома βst=10,5º; 2) расчет при βst=12º; 3) результаты испытаний серийных ПУ при угле излома βd=10,5±1,5º.
Отношение средней предельной наработки при βst=12º к аналогичному показателю при βd=10,5±1,5º равно 1,065, а отношение средней предельной наработки при βst=10,5º к аналогичному показателю при βd=10,5±1,5º — 1,22. Таким образом, при динамическом угле излома долговечность шарнира снижается на 6,5 и 21,8 %, в соответствии с режимами. Измерение параметров вибронагруженности КШ показало, что амплитуда изменения значений виброскорости и виброускорений при динамическом изменении угла излома увеличивается на опоре 4 (рисунок 15) — на А=10,1 дБ (14,3 %) и V=5,5 дБ (3,7%), на опоре 18 — на А=10,4 дБ (11,9 %) и V=8,0 дБ (5 %).
Для экспериментальной оценки повышения долговечности КШ путем улучшения их приспособленности к эксплуатационному нагружению были проведены ресурсные стендовые испытания конструкции КШ VII типоразмера с поворачивающимися проушинами при e≈+3,75 мм (RU 2106548). Испытаниям подвергали КШ, содержащий крестовину в сборе, ПУ № 1 и № 3 которой находились в проушинах серийной вилки, а № 2 и № 4 — опытной вилки. Коэффициент повышения долговечности составляет KLh=1,28 для значений начального радиального зазора ∆н=44...121 мкм. По средней наработке на отказ серийных ПУ определяем динамическую грузоподъемность ПУ при Kβ=1,065 и получаем Cсер=40,0 кН. При известных значениях радиального зазора в серийных и опытных испытанных ПУ ∆Нсер и ∆Ноп получаем для сравниваемых пар ПУ CОп=43,4...44,1 кН, что на 7,8...9,3 % больше грузоподъемности серийного ПУ.
Экспериментальная оценка повышения долговечности КШ (RU 2075878) способом замены рабочих поверхностей ПУ без проведения разборки ПУ при ТО проведена по величине коэффициента использования ресурса КИР, определяемого на основании результатов ресурсных стендовых испытаний, как отношение долговечности Lha серийного КШ к суммарной долговечности КШ до LДha и после LПha проведения замены рабочих поверхностей при значениях радиального зазора в ПУ ∆н1 и ∆н2=∆пр1. Применение предложенного ремонтопригодного КШ позволяет реализовать ресурс ПУ на 67...88 % или в среднем в 1,8 раза, что следует из отношения средних значений наработок, которому соответствует средний коэффициент ресурса KИР=0,557.
На основании ресурсных стендовых испытаний, на примере КШ VII типоразмера, получена математическая модель для случая расчета потенциальной долговечности Lha max с учетом рассмотренных факторов

Исследования повышения долговечности КШ при ремонте и в эксплуатации способом замены рабочих поверхностей ПУ (RU 2232309) проводили на примере КШ IV типоразмера. При обработке результатов ресурсных испытаний введены параметры: наработка каждого ПУ – Lhiоп; средняя наработка для КШ – Lhоп; наработка до поворота элементов ПУ – Lhдоп; наработка после поворота для каждого из ПУ – Lhпоп; суммарная наработка – LΣоп; отношение наработки до поворота к наработке ПУ (относительное время поворота) — Lhдоп/Lhiоп; отношение суммарной наработки к средней наработке — LΣоп/Lhоп; отношение суммарной наработки к наработке ПУ — LΣоп/Lhiоп.
Цель испытаний — изучение влияния угла поворота (Х1) и относительного времени Lhдоп/Lhiоп поворота (Х2) на суммарную наработку LΣоп, ч, КШ (Y). Угол поворота элементов ПУ варьировался на двух уровнях 0º и 180º. При 180º функцией отклика являлась наработка опытных крестовин, а при 0º — серийных, что позволяло имитировать поворот без замены рабочих поверхностей. В результате получена регрессионная модель в виде полинома второй степени

Исследование полученной зависимости показало, что максимум функция имеет при значении угла поворота 180º, а оптимальное время поворота наступает при достижении КШ наработки, порядка 0,6 от расчетной.
На основании результатов испытаний построены зависимости между относительным временем поворота Lhдоп/Lhiоп (Х) и соотношениями суммарной наработки КШ к средней по шарниру LΣоп/Lhоп (вариант I – Y1), а также суммарной наработки КШ к расчетной для ПУ LΣоп/Lhiоп (вариант II – Y2) (рисунок 22).
В результате аппроксимации экспериментальных данных получаем


Следовательно, для шарнира оптимальное время поворота втулок наступает при наработке 0,74 от расчетной (вариант I), при этом долговечность повышается в 1,68 раза, а для дифференцированного поворота ПУ — при 0,82 от расчетной наработки (вариант II), повышение долговечности составляет 1,73 раза.
|
Рисунок 22 – Определение оптимальной периодичности замены рабочих поверхностей |
С целью оценки эффективности разработанных мероприятий выполним прогнозирование их надежности в эксплуатации. Рассмотрим реализацию метода статистического моделирования при испытаниях КШ повышенной долговечности (RU 2106548) и ремонтопригодности (RU 2075878) на примере КШ VII типоразмера.
Объект моделирования — модель долговечности КШ по формуле (44). Средние значения и среднеквадратические отклонения изучаемых факторов составляют: 1) Кβср=1,065, σ=0,060; 2) CОпср=43,8 кН, σ=0,27 кН; 3) KИРср=0,557, σ=0,024. Варьирование параметров распределения проводили в пределах ХСр±σ.
Значение параметров нагружения принимаем на основе режимов нагружения шарниров КП трактора Т-150К в эксплуатации – TЭКШ=0,82 кН·м и при стендовых испытаниях – TСтКШ=2,0 кН·м. Средний эксплуатационный начальный зазор в ПУ – ΔН=69 мкм. Средний ресурс КШ до капремонта – 4250 ч.
Для стендового режима (рисунок 23, а) увеличение грузоподъемности карданных ПУ по решению RU 2106548 позволяет получить 50 % ресурс равный 926 ч, а 90% — 910 ч; выполнение замены рабочих поверхностей ПУ при ТО без разборки ПУ по решению RU 2075878 (рисунок 24, а) обеспечивает 50 % ресурс – 918 ч, а 90 % — 850 ч, а совместное применение мероприятий дает 50 % ресурс равный 905 ч и 90 % — 830 ч.
![]() |
а – при стендовом нагружении; б – при эксплуатационном нагружении |
Рисунок 23 – ВБР КШ повышенной долговечности RU 2106548 |
![]() |
а – при стендовом нагружении; б – при эксплуатационном нагружении |
Рисунок 24 – ВБР ремонтопригодного КШ RU 2075878 |
При эксплуатационном нагружении (рисунок 23, б) увеличение грузоподъемности позволяет получить 50 % ресурс шарнира порядка 15800 ч, а 90 % — 15500 ч; замена рабочих поверхностей ПУ по решению RU 2075878 (рисунок 24, б) обеспечивает реализацию 50 % ресурса в 15770 ч, а 90 % — 14900 ч. Применение комбинации мероприятий позволило получить 50 % ресурс порядка 15600 ч, а 90 % — 14100 ч.
По средней предельной наработке ПУ серийных КШ и результатам численного эксперимента (рисунки 23, а и 24, а) в условиях стендового нагружения средний коэффициент повышения долговечности составляет
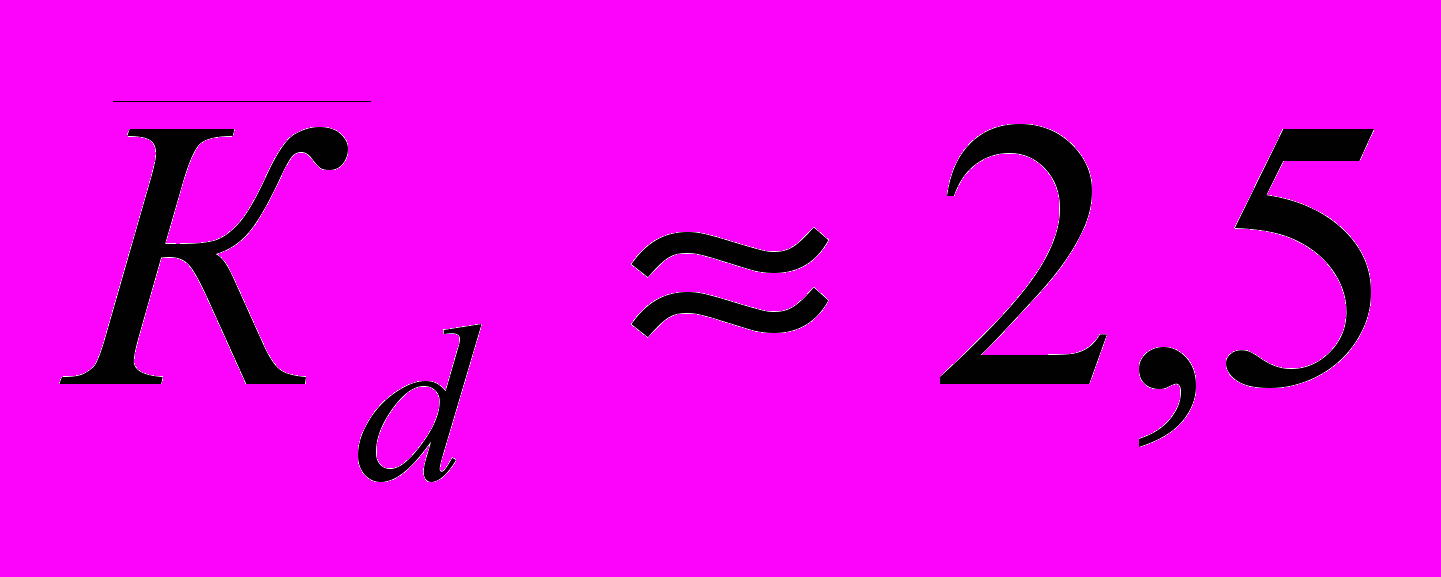
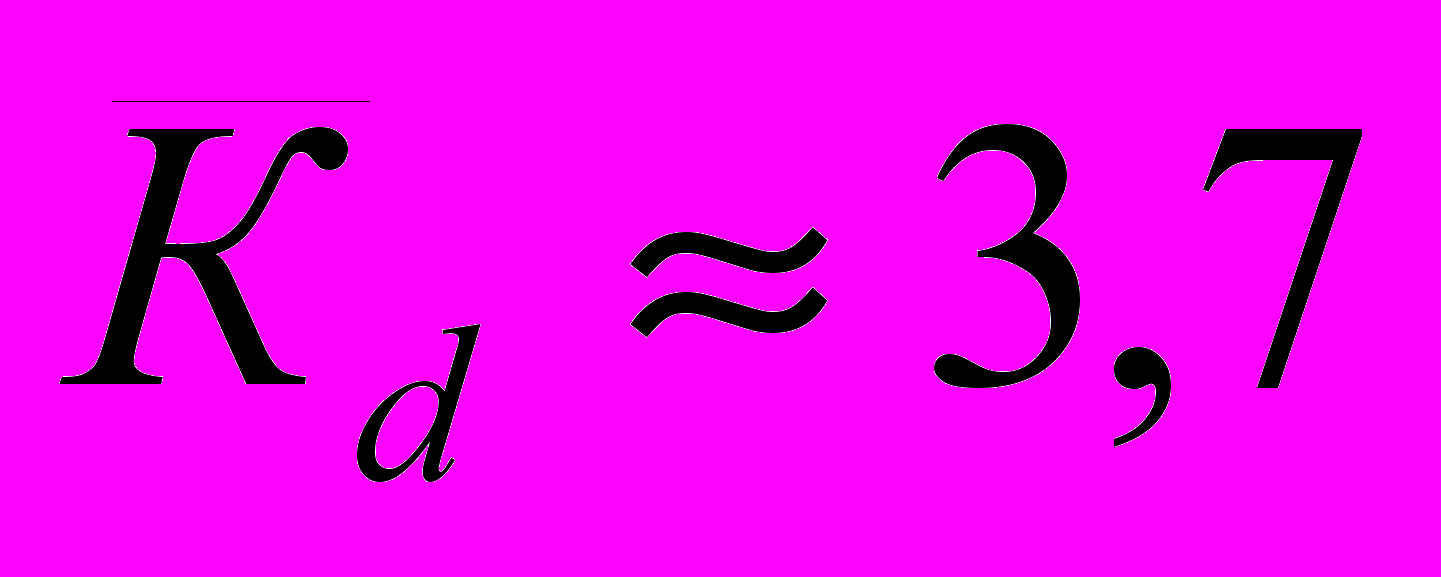
Оценку эффективности повышения долговечности шарниров КП путем применения ремонтопригодного КШ и способа его ТО (RU 2232309) проводили на примере КШ IV типоразмера, применяемого в приводах ВОМ РОУ-6 и КПРН-3,0, трансмиссии ГАЗ-53А и др., методом статистического моделирования на основе моделей (10, 17) при эксплуатационном уровне нагружения.
Варьируемые параметры: 1) ΔНср=30,6 мкм, =5,63 мкм; 2) k1Рcр=0,818, =0,114; 3) k1ТОср=0,757, =0,070. Варьирование параметров объекта осуществлялось в пределах Хср3. Результаты расчетов представлены на рисунке 25.
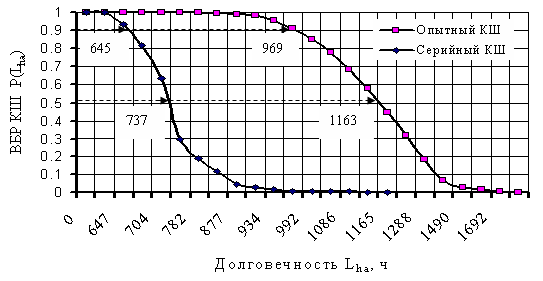
Рисунок 25 — ВБР серийного и опытного КШ
Оценка долговечности ремонтопригодного КШ методом статистических испытаний при эксплуатационных режимах показала, что 50 % ресурс опытных КШ составляет 1163 ч, серийных – 737 ч, а 90 % ресурс опытных КШ составляет 969 ч, серийных – 645 ч. Таким образом, 50 % ресурс опытных превышает ресурс серийных в 1,58 раза, а 90 % ресурс – в 1,5 раза.
^ 6 Производственная апробация, внедрение и технико-экономическая оценка разработок
Технико-экономическая оценка свидетельствует о том, что внедрение КШ с ПУ увеличенной грузоподъемности (RU 2106548) при повышении долговечности в 1,28 раза дает расчетный экономический эффект около 1400 руб., на примере трактора Т-150К; экономический эффект от внедрения ремонтопригодного КШ приспособленного к проведению ТОР (RU 2232309) при повышении долговечности в 1,5 раза составляет более 500 руб., на примере МТА МТЗ-82+РОУ-6, а экономический эффект от внедрения модернизированного стенда и методики ресурсных испытаний КШ СХТ составляет около 24,7 тыс. руб.
Результаты оценки эффективности рациональных способов ТОР (RU 2234008 и RU 2232309) по радару конкурентоспособности, на примере КШ VII и IV типоразмеров, по сопоставляемым способам ТОР представлены на рисунке 26. Сравнивали следующие способы: 1 – вибродуговая наплавка, 2 – железнение, 3 – пластическая деформация, 4 – электроконтактная приварка стальной ленты, 5 – газопламенное напыление, 6 – замена изношенной детали новой, 7 – предлагаемые способы ремонта. В качестве оценочных показателей приняты: стоимость восстановления крестовины (1), стоимость восстановленной детали в сборе (2), коэффициент долговечности (3), технико-экономический критерий (4), произведение стоимости новой детали на коэффициент долговечности (5), отношение показателя 5 к показателю 2 (6), минимальная цена восстановленной детали (7) и экономическая эффективность восстановления крестовины в сборе (8). Наибольшие значения коэффициент конкурентоспособности имеет для предлагаемых способов КК=0,665 и КК=0,819, а наименьшие — при замене отказавших КШ новыми.
![]() | ![]() |
а) VII типоразмер КШ | б) IV типоразмер КШ |
Рисунок 26 – Радар конкурентоспособности для способов ТОР КШ |
Совокупность теоретических и экспериментальных исследований при решении научной проблемы повышения надежности КП СХТ дает возможность получить научные и практические результаты, обобщенные в следующих общих выводах.
^ ОБЩИЕ ВЫВОДЫ
- Долговечность карданных передач механических трансмиссий тракторов, грузовых автомобилей и сельскохозяйственных машин в 1,5…2,0 раза меньше долговечности основных агрегатов, при этом 67…95 % всех отказов карданных передач приходится на крестовину в сборе с подшипниками.
- В результате теоретических исследований выявлен резерв повышения схемной надежности карданных шарниров, выполнена оценка точности размерных цепей радиального, осевого и окружного зазоров в карданных подшипниковых узлах, обоснованы направления и предложены способы повышения надежности карданных передач при техническом обслуживании и ремонте.
- Предложены конструкции карданных шарниров, позволяющие увеличить динамическую грузоподъемность подшипниковых узлов на 7,4…9,3 %, вероятность безотказной работы карданных шарниров в 1,3…1,5 раза и их ремонтопригодность на 30 % при повышении долговечности в 1,28…1,88 раза за счет их приспособленности к эксплуатационному нагружению, техническому обслуживанию и ремонту. Данные технические решения защищены 10 патентами РФ на изобретение (RU 2075878, RU 2106548, RU 2205304, RU 2215207, RU 2220338, RU 2224917, RU 2224918, RU 2232309, RU 2234008, RU 2238446).
- Усовершенствованы и разработаны методы оптико-поляризационных и статических испытаний, методики и технические средства стендовых ресурсных (RU 2134412, RU 2205377) и статистических испытаний, позволяющие осуществлять оптимизацию конструктивных параметров, оценку и прогнозирование долговечности шарниров карданных передач в эксплуатации.
- Получены количественные значения теоретически обоснованных и экспериментально подтвержденных параметров уточнения математических моделей долговечности карданных передач, учитывающих влияние динамического изменения угла излома шарниров (формула 10), более полное использование их ресурса (формулы 13 и 14) и приспособленность к эксплуатационному нагружению (формулы 11 и 12), техническому обслуживанию и ремонту (формулы 16 и 17).
- Стендовые ресурсные и статистические эксплуатационные испытания показали высокую надежность опытных карданных шарниров по сравнению с серийными. Применение карданных шарниров, приспособленных к нагруженности (RU 2106548) и замене рабочих поверхностей подшипниковых узлов (RU 2075878) в эксплуатации повышает их 90 % ресурс в 2,5…3,7 раз, что соответствует сроку службы карданных передач до второго капитального ремонта на примере трактора Т-150К. Эксплуатация карданного шарнира, приспособленного к ремонту путем постановки втулки и проведения технического обслуживания заменой рабочих поверхностей подшипниковых узлов (RU 2232309), позволяет повысить их 90 % ресурс в 1,5…1,6 раза, что соответствует безотказной работе привода вала отбора мощности сельскохозяйственных машин на протяжении четырех-пяти лет.
- Разработаны рациональные технологические процессы ремонта карданных передач сельскохозяйственной техники, основанные на оригинальных решениях замены рабочих поверхностей подшипниковых узлов (RU 2234008) и постановки дополнительной ремонтной детали-втулки (RU 2232309). Технико-экономическая оценка показала, что предлагаемые способы обладают экономической целесообразностью, конкурентоспособностью и перспективны для рынка технического сервиса, при этом стоимость восстановленных изделий составляет 52…74 % от цены нового изделия, а повышение ресурса достигнуто в 1,5…2,0 раза.
- Опытные экземпляры шарниров карданных передач, способы их технического обслуживания и ремонта проходили эксплуатационную проверку в аграрных и производственную апробацию на ремонтных предприятиях Белгородской области. Технические материалы по разработанным конструкциям, предложенным технологическим процессам и изготовленным стендам для ресурсных испытаний карданных передач и их элементов переданы на предприятия производители и сервиса техники для агропромышленного комплекса.