М. И. Юликов, # Б. И. Горбунов, Н. В. Колесов Проектирование и производство режущего инструмента москва «машиностроение» 1987 ббк 34. 6 Ю34
Вид материала | Документы |
- Методические указания к курсовому проекту "Расчет и проектирование режущего инструмента", 243.14kb.
- Рекомендации для расчета режущего инструмента при выполнении дипломного и курсового, 204.72kb.
- Физические свойства вакуумно-плазменных покрытий для режущего инструмента, 338.06kb.
- Физический факультет, 286.54kb.
- Методические указания к выполнению курсового проекта по дисциплине "Проектирование, 233.41kb.
- Тема: «Повышение эксплуатационных свойств режущего инструмента из твердого сплава Т15К6, 102.82kb.
- Работы режущего инструмента, основная нагрузка приходится на его рабочую поверхность,, 335.67kb.
- Вестник Брянского государственного технического университета. 2010. №1(25), 124.33kb.
- Курс лекций содержит принципиальные положения и основные исходные сведения для подготовки, 10.16kb.
- Автоматизация выбора режущего инструмента для процесса точения на многофункциональном, 267.6kb.
как это видно из прил. 7, чтобы | ^ | > (36ч>40°), Тпр0д> (12ч-32°),
|Я,С| > (20ч-35°). Поэтому примем comlo ~ (—20ч 24°); мень-
шее значение (—24°) — для более вязких материалов и при боль-
ших lid.
Возможные значения ^ для зенкеров с левыми канавками в ряде работ 123] рекомендуются от —7-=—14° до —22-s—25°. Учитывая, что увеличение абсолютного значения |^х| способствует выходу стружки вперед, а также что с увеличением |^| до 40° сила резания меняется незначительно, примем большие отрицательные значения угла %i до —30-5—36°. При малых | ^ |, как видно из прил. 7, получить угол То >0 затруднительно. Увеличение отрицательных значений ^ может привести к слишком большим положительным значениям Тпрод- Поэтому в алгоритме Предусмотрены УСЛОВИЯ, ПрИ КОТОрЫХ Тпрод < Тпрод та,
значение угла Тпрод на зенкере совпадает одновременно со значением продольного переднего угла в точке А кромки АВ и значением переднего угла в торцовом сечении ТТ на калибрующей части. Максимальное значение Тпрод шах ограничивается прочностью кромки в точке А. Ориентировочные значения Тпродпмх можно установить 10—35ч в зависимости от твердости (прочности)
материала детали, выбирая большие значения фпроя шах для более мягких материалов.
Таким образом, принимаем
*W = -12-г-16°; comln =-20-^-24°;
Ain»x = —12-5 15°; *i mm = —30 -f- —36°; (3.1)
Фс max = 65°; фс mm = 35°; Упрод max = 10 -f- 35°.
При наличии новых опытных данных, прежде всего с точки зрения обеспечения выхода стружки, указанные предельные значения должны корректироваться.
Величина ус выбирается по таблицам в зависимости от обрабатываемого материала ОМ (см. прил. 1):
Тс-/(ОМ). (3.2) Задний угол принимается а„ = 64-8°.
Значение ус, найденное из (3.2), может корректироваться с учетом состояния поверхности (например, окалина), жесткости технологической системы и надежности.
Принимаются значения со ((о == упоп) и fcj., при которых ус имеет максимально возможное значение:
w = сагаах; %! = (3.3)
С использованием уравнения (2.39) и учитывая, что для зенкера ю = упоп (см. рис. 2.26), находят максимально допустимое значение ф0 = фСПИХ1, при котором упрод < упроЯгш«:
Ctg фс max 1 = (tg К + tg Упрод max) Ctg Си. (3.4)
Если Фс max 1 <: фс max. то идти к (3.6), иначе — к (3.7); (3.5)
фс max = Фс max 1, ДЗЛее — К (3.10). (3.6)
Если фс max 1<Фс nun. то идти к (3.8), иначе — к (3.9). (3.7)
Выполнение условия (3.7) означает, что из-за ограничения максимальной величины упроптах нет возможности выбора угла ф0, и допускается лишь одно его значение, определяемое из (3.8):
Фс = Фс mm. (3.8)
далее идти к (3.19);
Фетах — ИЗ (3.1); (3.9)
далее — к (3.10).
С использованием (2.44) определяется значение ф0 = фр, при котором ус имеет максимальное значение:
* = -з1$тг: * = /2,25 + г; sin2 фр - ¥ё (KiXm + ¥TJ~=e).
(3.10) 159
Если Фр>Фет», где ф0шах определяется из (3.6) или из (3.9), то фс = Фотах и далее переходить к (3.14); (3.11) иначе к (3.12).
Если Фр<Фот1п. принять ф„ = ф0 тщ и далее переходить
к (3.14); иначе к (3.13): (3.12)
Фо = ФР; (3.13)
С учетом (2.34) и (2.28) определяется максимальное значение Ye- которое можно получить при заданных условиях:
tgVo max = tgC^>COSeCфв — tg^COS^,,. (3.14)
Если Tomax>Vo. где Yc — из (3.2), идти к (3.16); иначе к (3.17). (3.15)
Хх, при котором Yo принимает заданное из (3.2) значение:
tg К = (tg е> cosec фс — tg y0) sec ф0, (3.16)
где Ye — из (3.2); далее — к (3.17).
Выполнение неравенства (3.15) означает, что возможно уменьшение со или увеличение по сравнению с принятыми в (3.3); угол Ye получится требуемой величины. В данном алгоритме для этого случая предусмотрено увеличение Я.-., поскольку его минимальное значение принято несколько меньше рекомендуемого. Увеличенное "кг рассчитывается из (3.16).
tgYnPoB = tgcoctgVo-tgX1. (3.17)
Выводить на печать:
ф0; y0; ««>; К\ YnPoA; (3.18)
Рассчитать Yo из (3.19) и Упрод из (3.17), приняв в обоих случаях фо = фс mm:
tgYo = tgcйcosecф0 — tg^cc^o. (3.19)
При расчете из (3.19) значение у0 получится меньше, чем требуемое, найденное из (3.2); разница в некоторых случаях может быть весьма большой, но при заданных в (3.1) и (3.2) параметрах обеспечивается наименьшая ее величина.
Если Yo находится из (3.19), следует печатать: «для
(3.20)
увеличения ув необходимо увеличить Ynpoflmax либо
уменьшить Фотш»; печатать также значения тех же
углов, что и в (3.18).
Для изготовления, контроля, а также в качестве дополнительных сведений могут быть рассчитаны и другие геометрические параметры зенкера, показанные на рис. 2.26. Например, для контроля и заточки удобнее задаваться не углом ф0, а углом фь
160
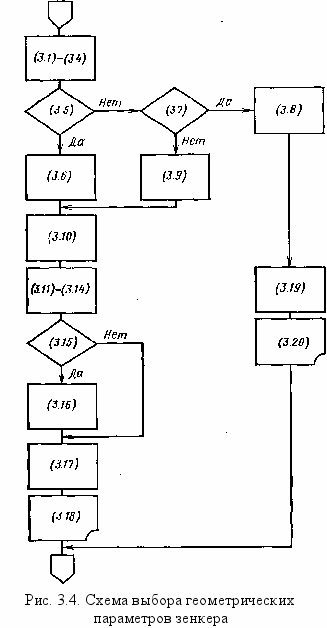
который может значительно отличаться от срс. Для заточки и контроля также удобнее задаться на чертеже углом анс вместо ас. Значение фх рассчитывается из (2.30); а„с — из (2.23).
Схема выбора геометрических параметров зенкера представлена на рис. 3.4.
6 Юг; -г*.t М. И. и др.
161
Пример расчета
Исходные данные: обрабатываемый материал — латунь средней твердости НВ < 140; диаметр отверстия d 25 мм, длина отверстия / 30 мм; зенкер выполняется из быстрорежущей стали Р6М5 (см рис. 2.26), с левыми канавками; точность отверстия по квалитету 11, шероховатость после зенкерования Rz = = 10 мкм. Остальные условия — режимы резания, жесткость СПИД и др. — средние, нормативные.
Выбор геометрических параметров производится по алгоритму (3.1)—(3.20) (рис. 3.4). В соответствии с (3.1)—(3.2), учитывая, что материал детали невысокой твердости и отношение lid невелико:
w„..,4 16°; шт1п = -24°;
^i max —~ 20°; %i min =- —36°;
Фс tnax — 65°;
c ruin — 35°;
Vc = 15°; ac = 8°; упрод max = 30°.
Из (3.3): ш = —16°; Xt = 36°.
Из (3.4): ctg ?ctnaK1 = [tg (-36°) -fig 30°] ctg (-16°) = 0,520295;
Cmaw = = 62,51°;
Из (3.5): фс max i = 62,51 ° < фг max = 65°; Из (3.6): фс max = фс max x = 62,51°;
Из (3 10)" а- Ч^16") - °'08222 0 Q5192 из p.iuj. g- 3tg,(._36o) 1,58359 u>ub192-
e = V2,30192 1,51721;
sin2 фр = 3/0,05192 (^3,01721 + ^—0,01721) = 0,4427546;
sin фр = 0,665398; фр = 41,7°.
Из (3.11): фр = 41,7° <фСтах = 62,5°; Из (3.12): фр = 41,7°>фс тт = 35°; Из (3.13): фс = фр = 41,7°; Из (3.14):
tg Yc max = tg (-16°) cosec (41,7°) — tg (-36°) cos 41.7° =- 0,1114175; Vc max *= 6,36°;
Из (3.15): Ycmax^ 6,36°
Из (3.17): tgynpoH = tg (-16°) ctg 41,7°- tg (36°)- 0,404706; упред = = 22,03°.
В соответствии с (3.18) печатается: фс - 41,7°; ус — 6,4°; ас 8°; Х1 = = -36°; Упрод- 22°; w 16'.
Отметим для сравнения, что если принять обычно рекомендуемое для зенкеров значение угла фх — 60е (фс = 56,3°), то при Xt - —30° и ы — —25° передний угол ус =" —13,5е, что значительно ухудшит работу и стойкость зенкера. Даже если принять Х1 и ш те же, что рассчитаны выше (—36° и —16°), то передний угол имел бы значение у с 1.8° при величине упр0д = 29,3°.
3.3.3. Расчет радиальных фасонных резцов
. Изложенный ниже алгоритм предназначен для проектирования фасонных радиальных резцов для обработки поверхностей тел вращения, включает блоки 3—5 и 10 СПРИ (см. рис. 1.1) и является общим для дисковых и призматических резцов из быстрорежущих сталей. Выбор геометрических параметров (блок 4) приведен для наиболее распространенных резцов с обычными параметрами и установкой при А, = а = р= О = 0, е — 0 (см. п. 2.4.2.8). Блоки 15 и 16 СПРИ достаточно легко могут быть формализованы, но требуют существенного увеличения «сходных данных и здесь не рассматриваются. Исходные данные (блоки 1 и 2).
Деталь: материал, твердость (прочность) — ОМ (см. прил. 1);
профиль детали: г,, г2, r3 rh .... rk; z01, z^, z0J, zoh
(см. п. 2.4.2.8 и рис. 2.34. рис. 2.35); k — количество узловых точек профиля; t — глубина профиля; 1Л — длина детали (ширина профиля).
Операция: режимы резания S, v.
Станок и державка для резца: жесткость технологической системы (в зависимости от длины детали, способа ее крепления, способа крепления резца) — средняя, пониженная или повышенная.
Инструмент: наружный радиус резца Rt; для дисковых резцов /?! Ф 0 (величина Rt определяется ниже), для призматических резцов Rx = 0; g и п — номера узловых точек профиля резца, в которых задаются значения статических задних углов в сечениях, нормальных к проекции кромки на основную плоскость; tyg> — углы профиля детали (резца) соответственно в точках g и п; acg и асп — значения задних углов резца в точках g и п соответственно. Значения углов acg и асп задаются как минимально допустимые. Точки g и п следует выбирать среди тех точек /, где углы ас имеют наименьшее значение по сравнению с другими точками кромки резца. При симметричном профиле углы acg и асп могут быть равны.
tl4 — метка; при расчете профиля резца в нормальном к его задней поверхности сечении NN принимается tlt = 0; при расчете по передней поверхности tu = 1.
Другие исходные данные, например условия мг ... ul3 (см. п. 2.4.2.3), Для выбора марки инструментального материала задаются в зависимости от формы соответствующих таблиц (см. табл. 2.9).
Угловые размеры задаются в градусах, линейные — в миллиметрах; величины ОМ, k, g, п, tu, иь .... u13 — безразмерные. Режимы резания (S и v), жесткость технологической системы входят в число условий ult м|3 и задаются либо как средние (ц = 1), повышенные (и = 2) или пониженные (и = 3) (см. п. 2.4.2).
Выбор марки инструментального -материала (ИМ), в данном случае быстрорежущей стали, осуществляется по таблице соответствий (см. п. 2.4.2.3, табл. 2.10). При обработке обычных конструкционных материалов наиболее часто используются марки Р6М5 (Р6АМ5) и Р6М5К5.
Предварительный (блок 4) и окончательный выбор геометрических параметров резца (блок 12), в данном случае при заранее
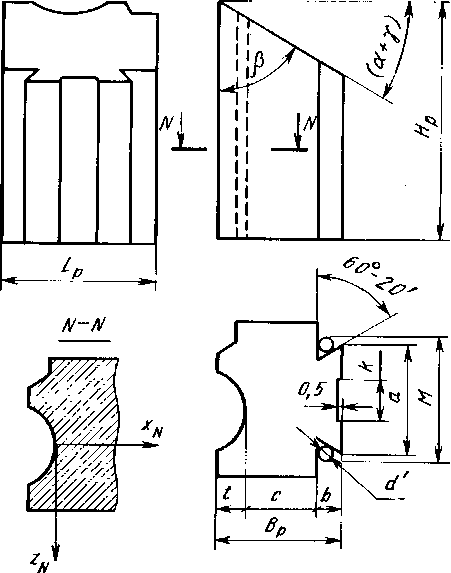
Рис. 3.5. Габаритные размеры призматического реаца
заданной форме передней и задней поверхностей и при к = о—\i = $ — е~0 (см. п. 2.4.2.8), целесообразно осуществлять совместно, после выбора габаритных размеров.
Определение габаритных размеров. Длина Lp резца в общем случае определяется (рис. 2.34, рис. 2.35, рис. 3.5)
Lv — /д + Mi + Kh + fhb,
(3.21)
где lx — 1-т-З мм — на выходе резца из детали; /2 = = 2-Г-5 мм — поясок во избежание заострения кромки; Ь — 2н-8 мм — выступ участка кромки под отрезку; величины kx—ks задаются конструктором в зависимости от конфигурации профиля детали и количества к указанных участков: kx = 1 или 2; к2 — 0; 1 или 2; ks — 0 или 1.
Для дискового резца (при Rt Ф 0) рассчитывается сила резания Рг:
Рт = Рт (*д + ksb) комкф, (3.22)
где ка и Ъ определяют из (3.21); рг — удельная сила резания — из табл. 3.11; kOM — коэффициент, зависящий от материала детали; £ф — коэффициент, зависящий от формы профиля детали. Значения коэффициента koli даны ниже.
ОМ ... 1 41; 52 53 2; 6; 7; 12; 3; 8; 45; 13; 47; 125
54; 62 124
йом • • • 0,75 0,8 0,9 1,0 1,1 1,2
ОМ. . . 48 46 126 14 9 11
йом - • • 1.25 1,3 1,35 1,6 1,8 2,2
Диаметр оправки дискового резца может быть определен из табл. 3.12 из условия жесткости в зависимости от силы Pz при (D/Lp) <: 3. При 11 000 Н < Рг < 14 600 Н можно принять d = 40 мм.
Значения коэффициента k$ приведены ниже.
Форма профиля детали..
КЛ ...
0,85
0,90
Г, О
1,05
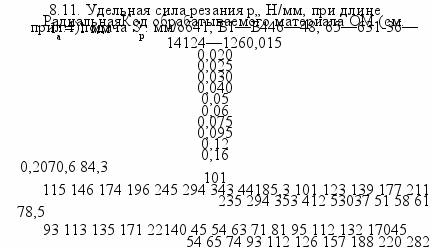
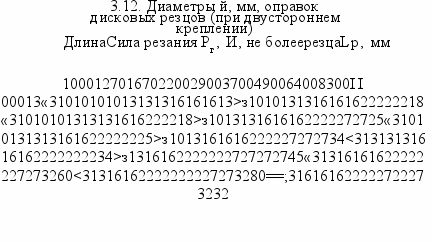
Наружный диаметр дискового резца
D = 2Ry = 2 (t + le + 0,75d), (3.23)
где Z0 — размер для выхода стружки (от 3 до 10 мм; большее значение — для бблыних t и /д). Значение D округляется до ближайшего большего из стандартного ряда: 32; 40; 50; 63; 70; 80; 90; 100; 112; 120.
Если после расчета D отношение (D/Z~) > 3, следует снова повторить выбор d из табл. 3.12 и расчет D по (3.23). На практике размеры d и D должны выбираться с учетом имеющегося набора оправок, допускаемых державкой резца, что может быть учтено путем соответствующих изменений в табл. 3.12 и в стандартном ряду D.
3.13. Основные размеры Для призматических резцов
Л1 | а | Ь | | d' | "г |
18,58 | 15 | 4 | 7 | 3 | 75 |
24 | 20 | 6 | 10 | 4 | 75 |
34,46 | 25 | 6 | 15 | 6 | 75 |
45,77 | 30 | 10 | 20 | 10 | 90 |
55,77 | 40 | 10 | 25 | 10 | 90 |
83,66 | 15 | 15 | 40 | 15 | 100 |