М. И. Юликов, # Б. И. Горбунов, Н. В. Колесов Проектирование и производство режущего инструмента москва «машиностроение» 1987 ббк 34. 6 Ю34
Вид материала | Документы |
- Методические указания к курсовому проекту "Расчет и проектирование режущего инструмента", 243.14kb.
- Рекомендации для расчета режущего инструмента при выполнении дипломного и курсового, 204.72kb.
- Физические свойства вакуумно-плазменных покрытий для режущего инструмента, 338.06kb.
- Физический факультет, 286.54kb.
- Методические указания к выполнению курсового проекта по дисциплине "Проектирование, 233.41kb.
- Тема: «Повышение эксплуатационных свойств режущего инструмента из твердого сплава Т15К6, 102.82kb.
- Работы режущего инструмента, основная нагрузка приходится на его рабочую поверхность,, 335.67kb.
- Вестник Брянского государственного технического университета. 2010. №1(25), 124.33kb.
- Курс лекций содержит принципиальные положения и основные исходные сведения для подготовки, 10.16kb.
- Автоматизация выбора режущего инструмента для процесса точения на многофункциональном, 267.6kb.
^ Рис. 2.28. Последовательность определения параметров в характеристик рабочей части инструмента
Следует учесть, что для многозубого инструмента 2-й подгруппы, у которого зубья выполняют роль черновых и чистовых, выбор их параметров усложняется. Однако главным условием все же остается обеспечение правильного формообразования и качества обработанной поверхности детали.
В процессе выполнения этого пункта расчета решается задача обеспечения необходимого числа переточек инструмента 1-й и 2-й подгрупп при соблюдении условий формообразования. Поэтому возникает необходимость введения механизма регулирования размеров рабочей части инструмента. Для нерегулируемых конструкций 2-й подгруппы необходимо рассчитывать форму и размеры задних поверхностей исходя из получения после переточки режущей кромки на новой производящей поверхности, приемлемой для правильного процесса формообразования.
После определения размеров калибрующей части необходимо перейти к определению размеров режущей (черновой) части для инструмента 3-й подгруппы. Исходными данными являются принятая схема срезания припуска и ее параметры. Далее можно определить остальные габаритные размеры рабочей части инструмента этой подгруппы.
Определение наружного диаметра мерного инструмента. Для инструмента, обрабатывающего отверстия, наружный диаметр режущей части определяется следующим образом. Для нового инструмента номинальное значение наружного диаметра равно номинальному значению диаметра обрабатываемого отверстия D„ = = D0. Верхнее отклонение наружного диаметра [ВО] = А —
- р'тах- Нижнее отклонение [НО] = Д — р'тах — N— / = р'тщ, где Л — допуск на обрабатываемое отверстие; ^ N — допуск на изготовление инструмента; / — допуск на износ инструмента; р^, Р'тт — соответственно максимальная и минимальная величина разбивки отверстия.
Диаметр предельно изношенного инструмента D„ ma ■= D0 —
- Pmin-
Аналогично определяются размеры и допуски на диаметральные размеры калибрующей части метчика. При назначении допуска на внутренний диаметр Dt учитывается, что он не должен принимать участия в работе. Поэтому верхнее отклонение можно было бы расположить по номиналу. Однако для стандартных метчиков дано некоторое его превышение над номиналом с целью получения большей гарантии, что заусенцы после сверла будут срезаны и резьбовой калибр свободно сможет войти в отверстие гайки. Это превышение установлено одинаковым для метчиков всех степеней точности и равно приблизительно половине зазора между профилями резьбы болта и гайки или D16 = &х + 0,55РЖ, где D16 — наибольший внутренний диаметр резьбы метчика; dt — номинальный внутренний диаметр резьбы; Рх — шаг резьбы.
При расчете круглой протяжки для обработки отверстия принято за номинальное значение диаметра калибрующих зубьев принимать не номинальное значение диаметра отверстия, а его верхнее значение (наибольшее с учетом разбивки при протягивании), В этом случае наружный диаметр круглой протяжки, равный диаметру калибрующих зубьев, определяется так: dH — dmax — р', где р" — величина разбивки отверстия при протягивании.
Определение наружного диаметра немерного инструмента. Для иемерного инструмента имеются определенные ограничения при выборе наружного диаметра D В частности, такие ограничения могут быть связаны со станком, обрабатываемой деталью, выполняемой операцией, числом переточек и т. д. Несмотря на это, задача выбора D ограничена определенными значениями.
У цилиндрических и торцовых фрез изменение наружного диаметра не влияет на изменение процесса формообразования. Восстановление параметров установки инструмента осуществляется с помощью механизмов стайка.
Для цилиндричесхих фрез наружный диаметр выбирается с учетом прочности и жесткости инструмента и оправки (для насадного инструмента). В этом случае D — d + 2 (m + Ия), где D — наружный диаметр; d — диаметр посадочного отверстия; т — толщина тела (корпуса); Ия — высота зуба.
Размеры d и т определяются из условия прочности и жесткости оправки и инструмента; Ня — из условия прочности и обеспечения необходимого числа переточек зуба. Расчет наружного диаметра для фрез с зубьями четырех типовых форм дан в работе [12 ].
При выборе наружного диаметра торцовых фрез пользуются зависимостью D — (1,4-=-1,8) В, где В — ширина фрезерования.
В случае ограничений по мощности и жесткости фрезерного станка определяют значение Ps и Nv по соответствующим формулам из теории резания металлов [21 j или с помощью соответствующих практических рекомендаций. Диаметры торцовых фрез в зависимости от мощности электродвигателя станка приведены ниже.
Мощность, кВт ... . До 3,5 3,5- -5,5 5,5 -7.5 7,5—12
^ Диаметр торцовых фрез, мм 100 ! 60 200 250—315
Иногда бывает выгоднее нарушить последнюю зависимость, применив фрезу меньшего диаметра (при заданном В), и вести обработку в несколько проходов по ширине. Экономическую целесообразность этого варианта обработки необходимо проверять по следующей формуле:
0,5D1M4-J3[I 4-(i/M)]
где Д7* — разница в продолжительности обработки сравниваемых фрез; М = DlDi — отношение диаметра фрезы, обрабатывающей изделие за один проход, к диаметру фрезы, обрабатывающей за несколько проходов; В — ширина детали, мм; /. длина детали,
St — минутная подача при работе фрезой меньшего диаметра; Sx — минутная подача холостого хода. Если ДГ^О, предпочтение отдается фрезе меньшего диаметра.
^ При назначении номинального делительного диаметра зуборезных долбяхов и дисковых шеверов этот диаметр выбирают как можно большим.
Долбяк большего диаметра (делительного, а следовательно, и наружного) обеспечивает получение увеличенных высот эволь-вентных участков профиля зуба нарезаемого колеса и позволяет брать большую коррекцию, т. е. большее число переточек. При этом качество обработанной поверхности улучшается.
Шевер дисковый большего делительного диаметра также имеет преимущества: обеспечивает требуемую высоту рабочих участков зубьев обрабатываемых колес, уменьшает передаточное число между шевером и колесом, что приводит к уменьшению разницы скорости резания на выступах и впадинах зуба шевера и выравниванию износа лезвий.
Однако следует учесть, что наибольшие значения делительных диаметров долбяков и шеверов могут ограничиваться станком, а также условиями их изготовления. Например, числа зубьев долбяка из условия шлифования (потери размеров корундового круга вследствие его осыпания) не должны превышать при т = = 0,1ч-0,9 мм — 120 зубьев, при т == 1—=—12 мм — 76 зубьев.
Для долбяков, обрабатывающих колеса внутреннего зацепления, дополнительно имеются ограничения на выбор чисел зубьев из условий отсутствия среза головки и ножки зубьев колеса.
^ Определение числа зубьев инструмента. Выбор числа зубьев инструмента зависит от ряда факторов: 1) диаметра инструмента; 2) объема стружечных канавок; 3) размеров деталей механизма крепления и регулирования (для сборных конструкций); 4) ограничивающих условий, накладываемых на процесс резания: постоянства суммарного сечения среза, ограничения по усилию резания и мощности и др.
В настоящее время задача по обоснованию выбора количества зубьев, как комплексная вариационная задача, не может быть решена до конца, так как многие зависимости отсутствуют. Однако частично эти зависимости экспериментально найдены, а для таких инструментов, как зуборезные долбяки и дисковые шеверы, число зубьев определяется, при знании номинального делительного диаметра, математически.
В связи с указанным инструмент с точки зрения определения числа зубьев можно разбить на три группы: а) инструмент, для которого число зубьев выбирается по практическим рекомендациям (зенкеры, развертки, метчики и плашки); б) инструмент, для которого число зубьев определяется по эмпирическим формулам (разнообразные фрезы, в том числе зуборезные); в) инструмент, для которого число зубьев рассчитывается (протяжки, долбяки. шеверы).
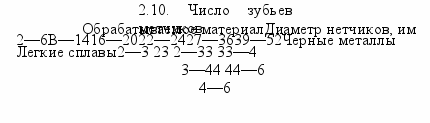
Метчики гаечные, машинные и ручные имеют число зубьев согласно данным табл. 2.10.
Для торцовых фрез сборной конструкции рекомендуется число зубьев определять по эмпирическим зависимостям, которые учитывают расположение и размеры ножей, механизмов крепления и регулирования. Эти зависимости имеют вид: при обработке стали для D <. 200 мм г = (0,04—0,06) D; для D > 200 мм z == (0,04ч-—0,06) D 4- 2; при обработке чугуна г = (0,08ч-0,10) D.
Часто бывает так, что фрезы с указанными выше зубьями не могут быть использованы из-за недопустимых значений усилий резания или мощности. В этом случае, как следует из теории резания металлов, выгоднее снижать скорость резания, а не число зубьев фрезы.
В том случае, когда по каким-либо причинам нельзя уменьшить скорость резания, уменьшают число аубьев до значений, определяемых по формуле
_ 10*^8*1 Z ~ l,15NyvSztBn'
где N, — полная мощность электродвигателя станка, Вт; т) — КПД главного привода; Nya — удельная эффективная мощность, Вт.
При назначении числа зубьев необходимо стремиться к удовлетворению условия равномерности фрезерования. Для этого при торцовом фрезеровании необходимо, чтобы в работе находилось не менее двух зубьев, т. е. чтобы удовлетворялось неравенство В 55 D sin (2n/z).
При DlB = 1,4ч-1,6 неравенство имеет вид
Z ^ ;—
arcsin(0,6-т-0,7)
Фрезы фасонные затылованные со шлифованным зубом имеют число зубьев, которое зависит не только от прочности зуба, возможности осуществления его шлифования, но и от высоты профиля детали.
Для обеспечения прочности зуба и возможности получения достаточного количества переточек принимают, что толщина зуба должна составлять 0,8—1,0 его высоты. С увеличением размеров профиля высота зуба возрастает значительно быстрее, чей диаметр, поэтому для обеспечения достаточной прочности зуба приходится уменьшать число зубьев фрезы г.
Рекомендуется число зубьев определять по формуле
г = 0,967r,/ftB-4S2,
где гг = 0,85d — радиус окружности впадин стружечных канавок; ha — высота профиля; d — диаметр отверстия (оправки) фрезы.
Полученное число зубьев фрезы необходимо проверить с точки зрения обеспечения равномерности фрезерования:
г =* 480р/arccos l(D — 2t)/D 1,
где р — количество одновременно работающих зубьев; ^ D — диаметр фасонной фрезы; t — глубина фрезерования.
Проверка проводится также на наибольшее число зубьев фрезы, допустимое по размещаемости стружки в стружечной канавке:
Zme, = 0,2D/(^'a5xS°'s).
Выбор числа зубьев для других инструментов приведен также в [121.
Задние поверхности зубьев для инструментов с неизменным профилем после его переточки (рис. 2.29, табл. 2.11). Фасонные резцы. Выполнение неизменности условий формообразования, а следовательно, неизменности профиля инструмента после его переточки легкоосуществимо. Все фасонные резцы (винтовые, дисковые и призматические) могут быть изготовлены с задними поверхностями, удовлетворяющими этому условию. В общем случае такими поверхностями могут быть поверхности с постоянной образующей и направляющей разнообразного вида. Однако для простоты изготовления инструмента в качестве последних берут винтовую линию, окружность или прямую. В результате у дисковых резцов задней поверхностью является цилиндрическая винтовая поверхность или поверхность вращения (частный случай — плоскость).
- Реечный инструмент, работающий по методу огибания, имеет профиль, соответствующий профилю инструментальной рейки (при у = О эти профили совпадают). Следовательно, реечный инструмент должен иметь задние поверхности, удовлетворяющие условию неизменности профиля. С точки зрения удовлетворения этого требования и других (наличие требуемых углов и технологичность задней поверхности) в качестве задних поверхностей принимают цилиндрическую поверхность. Для прямолинейного профиля рейки цилиндрическая поверхность вырождается в плоскость.
- Фасонные дисковые фрезы для цилиндрических поверхностей. Этот инструмент после переточки имеет уменьшающийся наружный диаметр (D — пере-
^ Изменяются (1-я и 2-я подгруппы инструмента)
Не изменяются (3-я подгруппа инструмента)
Восстанавливаются
Не восстанавливаются
в в в а со
:83
S4 >>
0-2
ЯО) с ; s
s в га Р . я
<ц 2 3
и Я X
™ CU 0)
1
- р.
w i- 3 (- и в
• ■ I <0 гя |
Е* Ills
ll^S SB
х
е Г§ § 11 «1 в &-&а
2
га к Ч
н а) ш •» ЕС г*
.. о о S g-p Ч о
£■2
См о
8-SR
CU &
S t- С
га о в
В 3 И
в g
га >j
х S в
о) *> К
38 о.д
§ Ш я Я и о 2 о * с а. ts
U Ч и
В "В ш В
у Р
В о
в
"5 в 3 ы 55 н а> о
>,хо сх са в о.
U 0)
<и Е в >. « а.
&.в
си в
т Я са *я о. Я в
у о. Я <и о. So о га
а « в о-
CU *
га *Я
о .- я
cd с
§.8ь
що Я ■ it «
о я а
Во)
2 >, Я S
о 3* я Q.P сч В
х л) са
Я 0
* с в
S Э к о.
g gxo
s 2 S в
tee §а
^ Задние поверхности должны обеспечить постоянство формы и размеров профилирующих кромок
Задние поверхности разные, не ограничиваются
профилированием
Задние поверхности рассчитывают из условия обеспечения правильного формообразования
^ Рис. 2.29. Классификация режущих инструментов по виду задних поверхностей
менный). Обеспечить требуемую поверхность обрабатываемой детали в данном случае можно при неизменном профиле фасонной фрезы, соблюдая следующее условие: в момент формообразования фреза должна иметь профиль, совпадающий с профилем обрабатываемой поверхности. Указанное условие соблюдается при наличии у затылованной фрезы переднего угла 7 = 0.
Фрезы е эатылованными нешлифованными зубьями при уфО. Рассмотрим случай затылования резцом фасонной фрезы, имеющей V Ф 0, способом, показанным на рис. 2.30.
4 Юлжкоа М. И. в др. 97
Инструмент | D | V | M |
Фасонные резцы: | | | |
стержневые и | ею | const | oo |
призматические | | | const |
дисковые | const | const | |
Реечный инстру- | оо | const | oo |
мент, работающий | | | |
по методу огиба- | | | |
ния | | | |
^ Фасонные диско- | const | const | CO |
вые фрезы для | | | |
цилиндрических | | | |
поверхностей (ре- | | | |
гулируемые) | | | |
^ Фасонные диско- | var | 0 | oo |
вые фрезы для | | | |
цилиндрических | | | |
поверхностей (не- | | | |
регулируемые) | | | |
^ Фасонные диско- | const | const | const |
вые фрезы для | | | |
винтовых поверх- | | | |
ностей | | | |
Инструмент с ка- | const | const | const |
либрующими зубь- | (CO) | (0) | (oo) |
ями | | | |
^ Теоретически требуемая задняя поверхность
0>