Лекция Влияние различных факторов на пластичность металла. Влияние омд на структуру и свойства металлов. Основные законы теории пластических деформаций. Нагрев заготовок при омд
Вид материала | Лекция |
- Лекция Теоретические основы омд. Пластическая деформация моно- и поликристалла. Основы, 89.4kb.
- Материалы с высокой проводимостью, 428.45kb.
- Строения металлов и их свойства, 394.29kb.
- Название диссертации, 326.98kb.
- Данной работы- «Основные законы теории организации и их влияние на жизненный цикл организации», 63.42kb.
- Программа курсов повышения квалификации итр по теме: «Материаловедение, термообработка,, 570.18kb.
- Сорбционные свойства и проницаемость материалов. Основные характеристики, приборы, 54.52kb.
- Влияние факторов внешней среды на деятельность организации (на примере ОАО «Кировский, 44.93kb.
- Материаловедение и технология конструкционных материалов, 37.46kb.
- Лекция №4 Механизм деформации и разрушение материалов Напряжения, 79.59kb.
Лекция 9. Влияние различных факторов на пластичность металла. Влияние ОМД на структуру и свойства металлов. Основные законы теории пластических деформаций. Нагрев заготовок при ОМД.
1. Влияние различных факторов на пластичность металла.
1.1. Влияние химического состава
Чистые металлы обладают более высокой пластичностью, чем их сплавы. Например, медь пластичнее ее сплава с оловом (бронзы). Сплавы, образующие твердые растворы, обычно более пластичны, чем сплавы, образующие химические соединения и механические смеси. Большей пластичностью обладают металлы, у которых больше разница между пределами прочности и текучести.
Компоненты сплава также влияют на его пластичность. С повышением содержания углерода в стали пластичность уменьшается. При содержании углерода свыше 1,5% сталь с трудом поддается ковке.
Кремний понижает пластичность стали. Поэтому кипящая малоуглеродистая сталь (08кп, 10кп) с малым содержанием кремния применяется при изготовлении деталей холодной штамповкой глубокой вытяжкой.
В легированных сталях хром и вольфрам уменьшают, а никель и ванадий повышают пластичность стали.
Сера, соединяясь с железом, образует сульфид железа
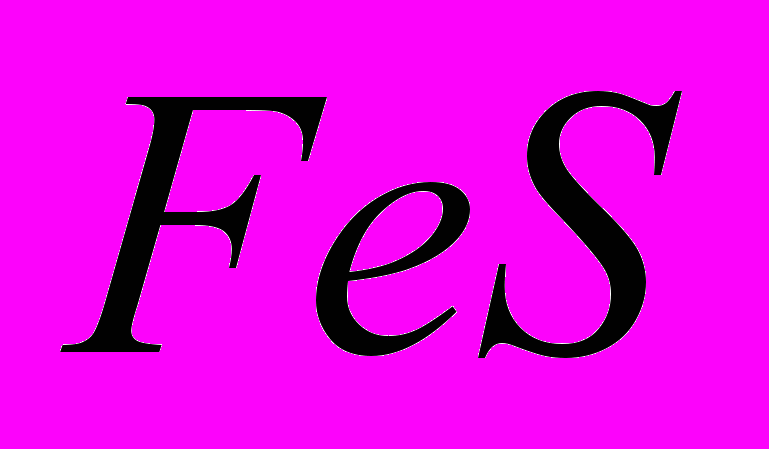
Марганец, образуя тугоплавкое соединение
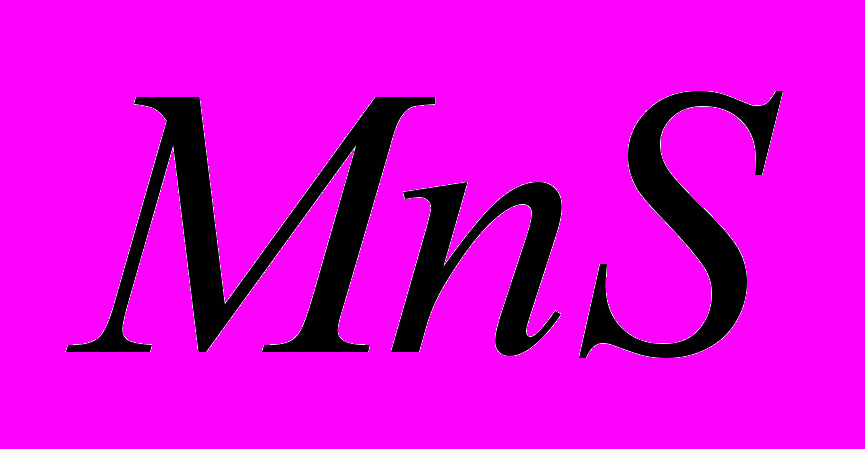
Фосфор увеличивает пределы прочности и текучести, но уменьшает, особенно при низких температурах, пластичность и вязкость сталей, вызывая их хладноломкость.
Пластичность литого крупнозернистого металла ниже, чем деформированного, имеющего мелкозернистую структуру. Снижают пластичность поры, газовые пузыри, неметаллические включения, микро- и макротрещины.
1.2. Влияние температуры
Качественная зависимость пластичности от температуры представлена на рис.
Влияние температуры неоднозначно. Малоуглеродистые и среднеуглеродистые стали, с повышением температуры, становятся более пластичными (1). Высоколегированные стали имеют большую пластичность в холодном состоянии (2). Для шарикоподшипниковых сталей пластичность практически
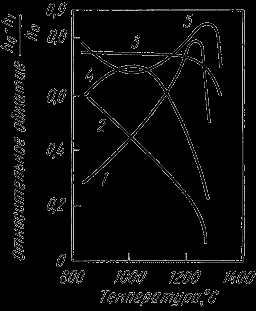
Рис. Влияние температуры на пластичность сталей
не зависит от температуры (3) . Отдельные сплавы могут иметь интервал повышенной пластичности (4). Техническое железо в интервале 800…1000 0С характеризуется понижением пластических свойств (5). При температурах, близких к температуре плавления пластичность резко снижается из-за возможного перегрева и пережога.
Для углеродистых сталей в интервале температур 100–300оС, называемом зоной синеломкости, пластичность несколько уменьшается, а прочность возрастает. Это явление объясняется выпадением мельчайших частиц карбидов по плоскостям скольжения при деформации. Пластичность также несколько снижается в области фазовых превращений.
Резкое снижение пластичности при высоких температурах связано с чрезмерным ростом зерен. Это явление называется перегревом. Структуру перегретой стали в большинстве случаев можно исправить отжигом. При нагреве стали до температуры, близкой к температуре плавления, происходит образование оксидов по границам зерен и расплавление легкоплавких межзеренных прослоек, что приводит к появлению трещин и потере пластичности. Это явление называется пережогом. Оно не устраняется термической обработкой, и пережженный металл отправляется на переплавку.
1.3. Влияние скорости деформации
Скорость деформации – это изменение степени деформации
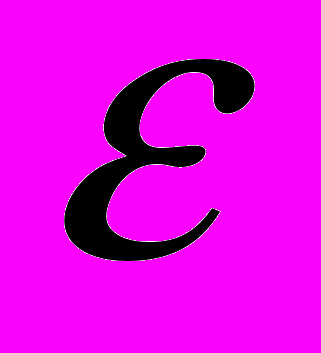
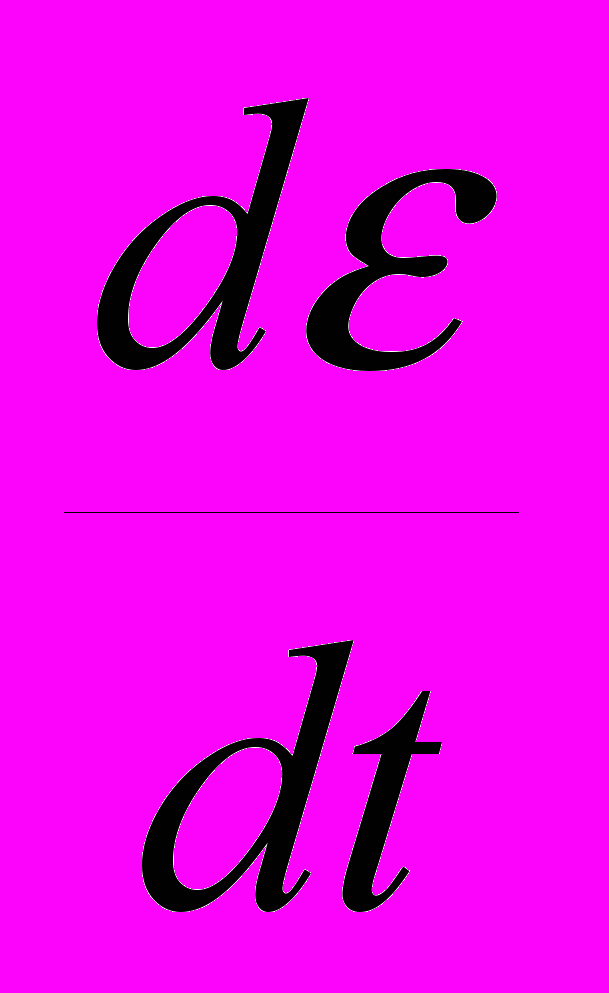
1.4. Влияние напряженного состояния
Напряженное состояние характеризуется схемой главных напряжений, действующих в элементарно малом объеме, выделенном в деформируемом теле.
Главными называют нормальные напряжения, действующие в трех взаимноперпендикулярных площадках, на которых касательные напряжения равны нулю. Всего имеется девять схем главных напряжений: четыре объемные, три плоские и две линейные. При обработке металлов давлением встречаются две объемные схемы напряженного состояния:
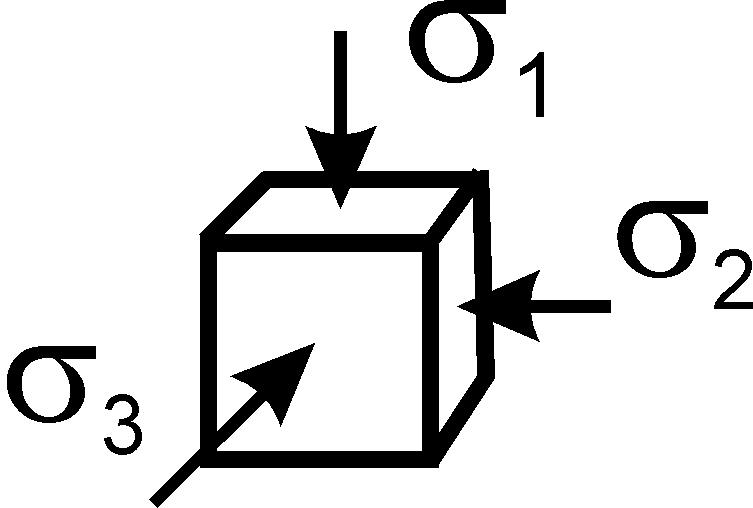
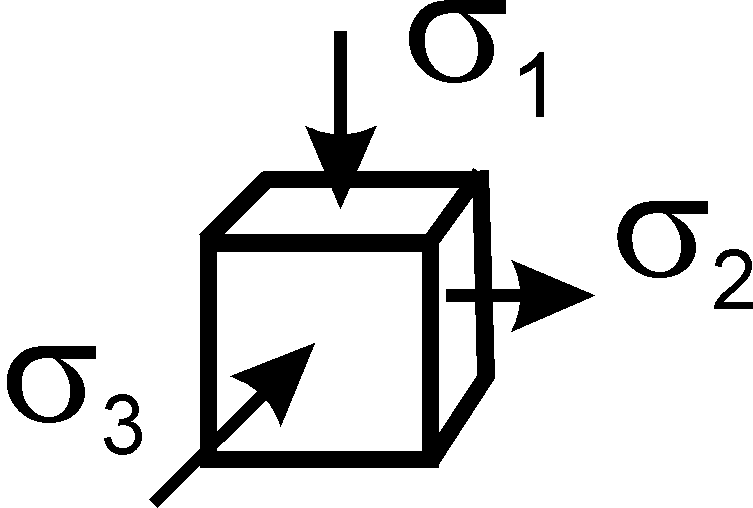
1) объемное трехосное сжатие металла, когда по всем трем осям действуют главные напряжения сжатия. Эта схема наблюдается при свободной ковке, объемной штамповке, прокатке, прессовании.
2) объемное напряженное состояние металла, когда по двум осям действуют главные напряжения сжатия, а по третьей – главное напряжение растяжения. Эта схема наблюдается при волочении и в некоторых случаях листовой штамповки.
Схема главных напряжений позволяет судить о пластичности металла. Чем большую роль играют напряжения сжатия, тем выше пластичность металла в процессе его обработки. Поэтому, например, пластичность металла при прессовании выше, чем при волочении. Повысить сжимающие напряжения при обработке давлением можно, например, оказывая боковое давление на металл жесткими стенками инструмента.
Деформированное состояние в элементарно малом объеме металла характеризуется схемой главных деформаций. Главными называются деформации в направлении трех осей, перпендикулярных к площадкам, в которых касательные напряжения отсутствуют. При обработке давлением различают три схемы главных деформаций:
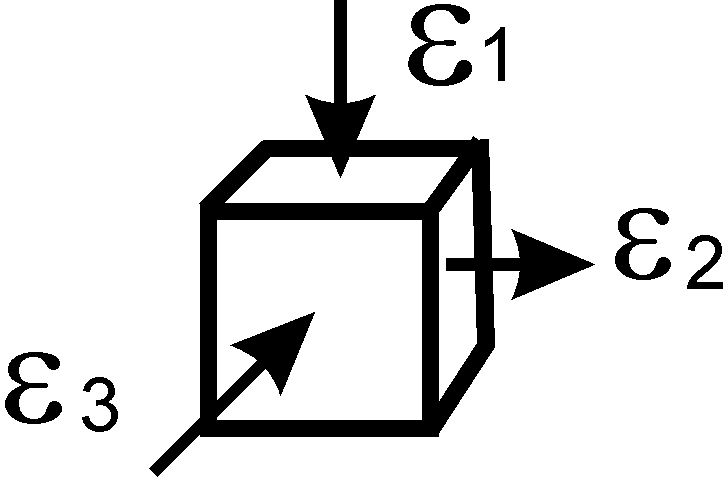
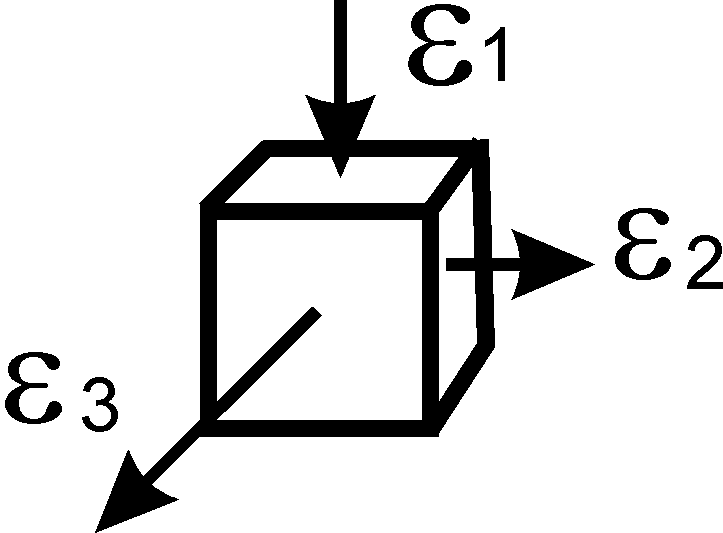
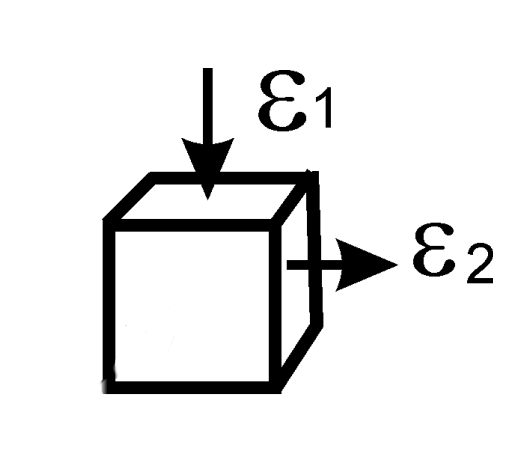
1) по двум осям – главные деформации сжатия, по третьей – главная деформация растяжения. Эта схема наблюдается при волочении и прессованию.
2) по одной оси – главная деформация сжатия, а по двум другим – главные деформации растяжения. Эта схема наблюдается при прокатке узкой полосы на гладкой бочке, при прокатке в калибрах, при свободной ковке и объемной штамповке.
3) по одной оси – главная деформация сжатия, по второй – главная деформация растяжения, а по третьей деформации не происходит. Эта схема наблюдается при прокатке широкой полосы на гладких валках, в некоторых случаях листовой штамповки.
Схема главных деформаций дает представление о характере формирования волокна и зерен. Максимальная главная деформация определяет текстуру деформации, предопределяет физико-механические свойства металла при обработке давлением.
2. Влияние ОМД на структуру и свойства металлов
Заготовками при ОМД часто являются слитки. Структура слитков неоднородна. Основу ее составляют зерна первичной кристаллизации (дендриты) различной величины и формы, на границах которых скапливаются примеси и неметаллические включения. В структуре слитка имеются также поры, газовые пузыри. При ОМД при высоких температурах происходит дробление зерен, а также частичное заваривание пор. Зерна и межкристаллические прослойки вытягиваются в направлении наибольшей деформации. В результате структура металла приобретает полосчатое (волокнистое) строение. Вследствие протекания диффузионных процессов происходит некоторое выравнивание химического состава. То есть при ОМД структура слитка улучшается.
При последующей термообработке волокнистое строение изменить невозможно. Волокнистость оказывает влияние на механические характеристики, вызывая их анизотропию. При сравнительно неизменных во всех направлениях характеристиках прочности характеристики пластичности (особенно ударная вязкость) металла вдоль волокон получаются выше, чем поперек волокон. В поперечном направлении ударная вязкость на 50–70% оказывается ниже, чем вдоль волокон.
Анизотропию свойств деформированного металла следует учитывать при проектировании и изготовлении деталей. Надо стремиться получить в них такое расположение волокон, чтобы наибольшие растягивающие напряжения действовали вдоль волокон, а если элемент работает на срез , то перерезывающие усилия – поперек волокон, и чтобы волокна у поверхности детали повторяли ее очертания и не перерезались при обработке резанием. В этом случае повышаются прочность и другие служебные свойства деталей.
На рисунке представлен коленчатый вал, изготовленный резанием (а) и ковкой (б). Как соотносится прочность представленных на рисунках деталей?
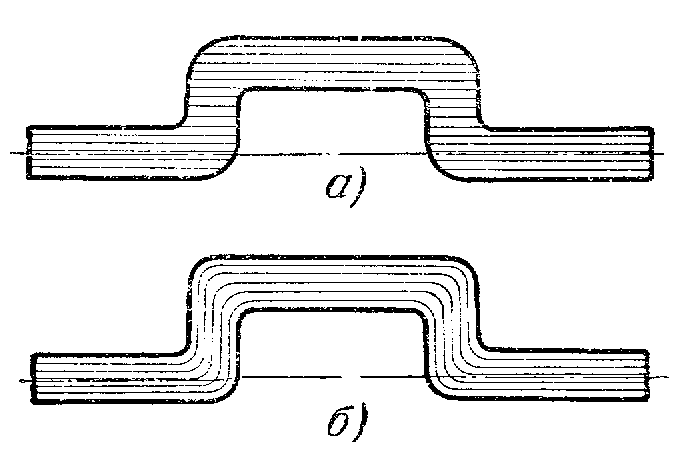
Прочность детали а) меньше прочности детали б).
При холодном деформировании металлов повышается плотность дефектов кристаллического строения и возрастает сопротивление их перемещению. С увеличением степени деформации пределы прочности, твердость увеличиваются, а пластичность и вязкость снижаются. Упрочнение металлов при пластической деформации называется наклепом. В результате упрочнения пластические свойства металла могут снизиться настолько, что дальнейшая деформация вызывает разрушение.
При нагреве наклепанного металла до температур, составляющих (0,2–0,3) Тпл (температуры возврата или отдыха), частично уменьшаются искажения кристаллической решетки и внутренние напряжения без существенного изменения микроструктуры и механических свойств деформированного металла.
При нагреве деформированных металлов выше температур 0,4 Тпл (для сплавов 0,6 Тпл) образуются новые равноосные зерна, и свойства металла возвращаются к исходным до деформации. Процесс образования новых центров кристаллизации и новых равноосных зерен в деформированном металле при нагреве, сопровождающийся уменьшением прочности, увеличением пластичности и восстановлением других свойств, называется рекристаллизацией.
3. Холодная и горячая деформация
В зависимости от температурно-скоростных условий при деформировании могут происходить два противоположных процесса: упрочнение, вызываемое деформацией, и разупрочнение, обусловленное рекристаллизацией. В соответствии с этим различают холодную и горячую деформацию. Холодное деформирование происходит при температурах ниже температур рекристаллизации и сопровождается наклепом металла. Горячее деформирование протекает при температурах выше температур рекристаллизации. При горячей деформации также происходит упрочнение металла, но оно полностью снимается в процессе рекристаллизации. Деформация, после которой происходит только частичное разупрочнение, называется неполной горячей деформацией.
Величина зерна металла после горячей обработки в основном зависит от температуры и степени деформации. Степень деформации представляет отношение разности начальной
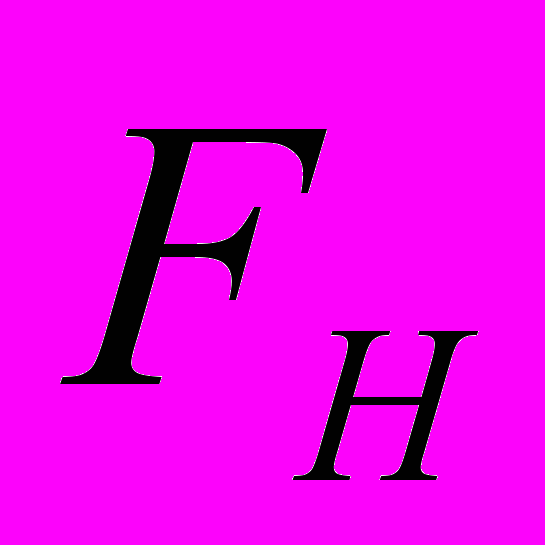
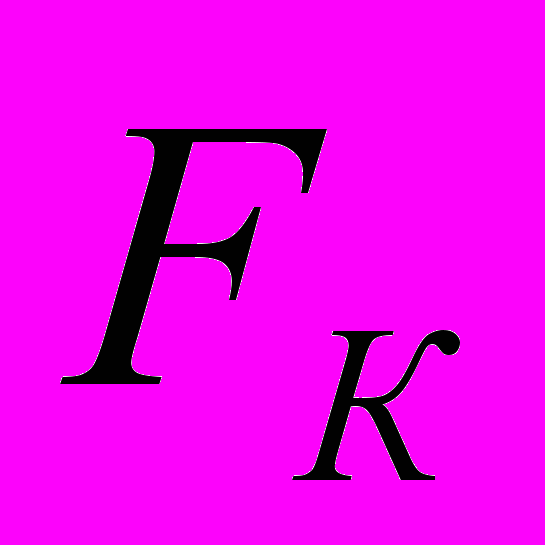
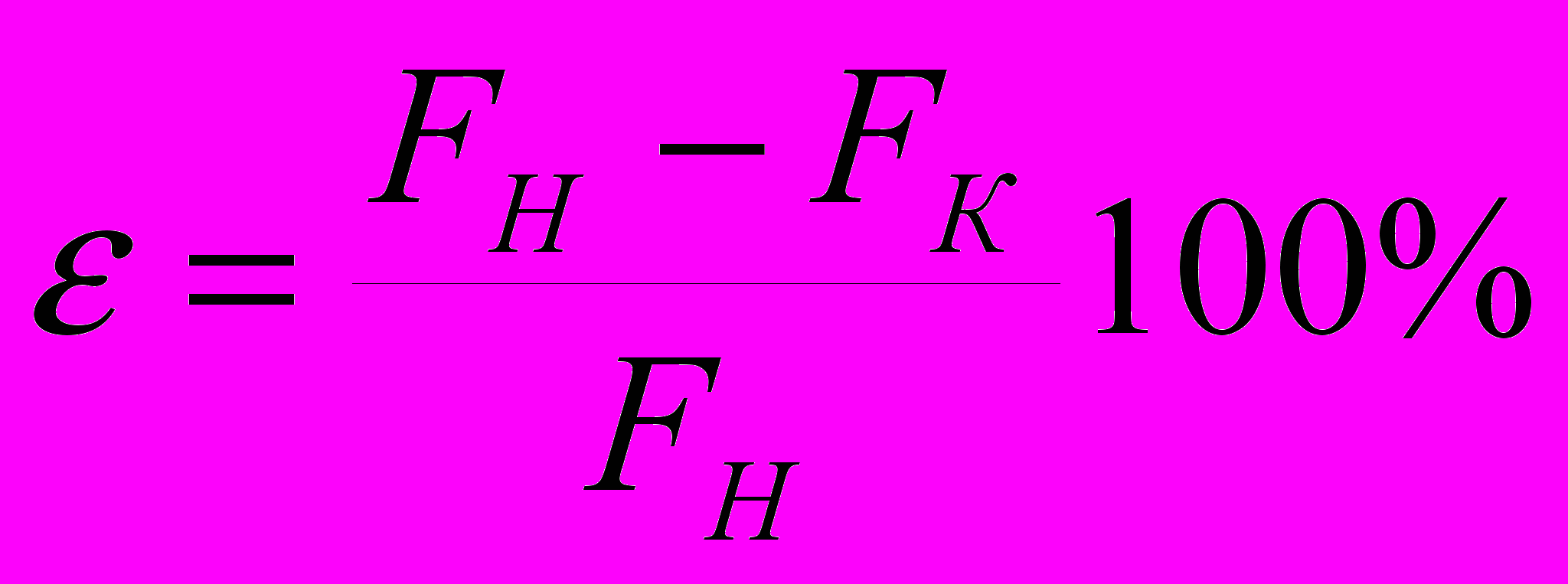
Степень деформации
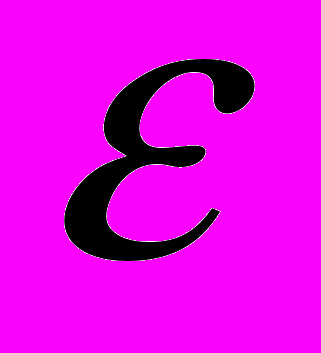
4. Основные законы пластической деформации
1. Закон постоянства объема. Объем тела до деформации практически равен объему тела после деформации. Этот закон используют для определения размеров заготовок, предназначенных для обработки давлением.
2. Закон наименьшего сопротивления. В случае возможности перемещения точек деформируемого тела в различных направлениях каждая точка этого тела перемещается в направлении наименьшего сопротивления. Закон позволяет определить, какие размеры и форму поперечного сечения получит заготовка с тем или иным сечением в процессе обработки давлением.
3. Закон сдвигающего напряжения. Пластическая деформация может начаться только в том случае, если сдвигающие напряжения, возникающие в деформируемом теле, достигнут определенной величины, зависящей от природы тела и условий деформации.
4. Закон подобия. При осуществлении в одинаковых условиях одних и тех же процессов пластического деформирования геометрически подобных тел из одинакового материала отношение усилий деформирования равно квадрату, а отношение работ – кубу отношений соответствующих линейных размеров. Этот закон основан на принципе моделирования и позволяет приближенно определить усилия и работы деформирования.
5. Нагрев заготовок при ОМД
Нагрев заготовок при обработке давлением проводят с целью повышения пластичности металлов. Для каждого металла существует такой температурный интервал, в котором условия для обработки давлением оптимальны. Интервал выбирается с учетом диаграммы состояния сплава. Для сталей температурный интервал при ОМД выбирают по диаграмме железо-цементит.
В зависимости от характера передачи тепла к металлу различают два способа нагрева – прямой и косвенный.
1) Прямой способ.
Тепло аккумулируется непосредственно в самом металле, а температура окружающей среды остается ниже температуры металла. Нагрев металла происходит при пропускании через него электрического тока. Количество выделяемого тепла при прямом нагреве определяется законом Джоуля-Ленца:
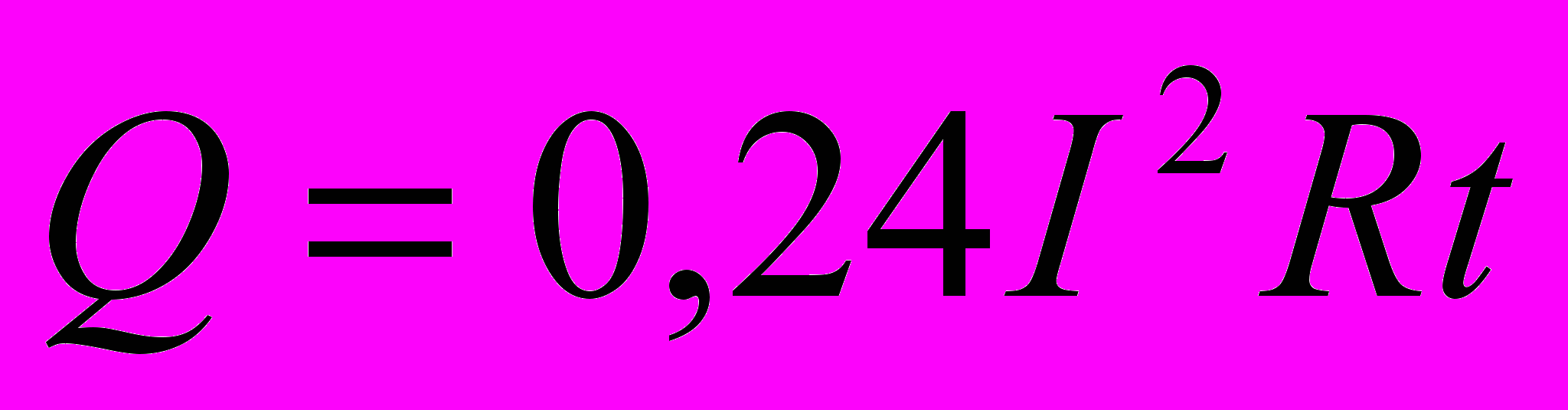
где
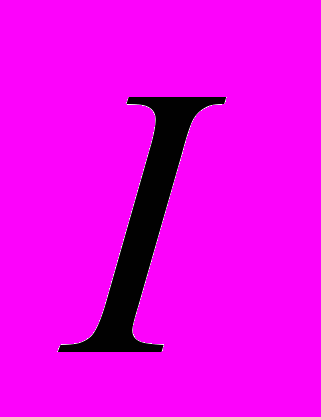
2) Косвенный способ.
Тепло передается металлу за счет соприкосновения его поверхности с какой-либо средой – газообразной, жидкой или твердой, нагретой до более высокой температуры. (Нагрев в печах, расплавленных солях, электролите). Тепло передается металлу следующими способами: конвекцией, лучеиспусканием, теплопроводностью.
Тепло с поверхности нагреваемого металла внутрь его передается не мгновенно, а со скоростью, зависящей от его теплопроводности. Чем больше в стали углерода, тем ниже его теплопроводность. При нагревании легированных и высоколегированных сталей, а также крупных слитков возникают температурные напряжения, в результате которых могут появиться трещины, поэтому нагрев до 650–850оС производится медленно.
Температура начала ОМД (ковки) должна лежать на 100–150оС ниже температуры плавления во избежание появления перегрева и пережога:

Заканчивать ОМД (ковку) следует при температурах

где С – содержание углерода в %.
Температурные интервалы начала и конца ковки
Марка материала | Температуры ковки | |
начала | конца | |
Ст 1 | 1300 | 900 |
Ст 2 | 1250 | 850 |
Ст 3 | 1200 | 850 |
Сталь У7, У8, У9 | 1150 | 800 |
Сталь У10, У12, У13 | 1130 | 870 |
Медные сплавы | 900 | 700 |
Дуралюмин | 470 | 400 |
Титановые сплавы | 1100 | 900 |
Продолжительность нагрева определяется по формуле Доброхотова:
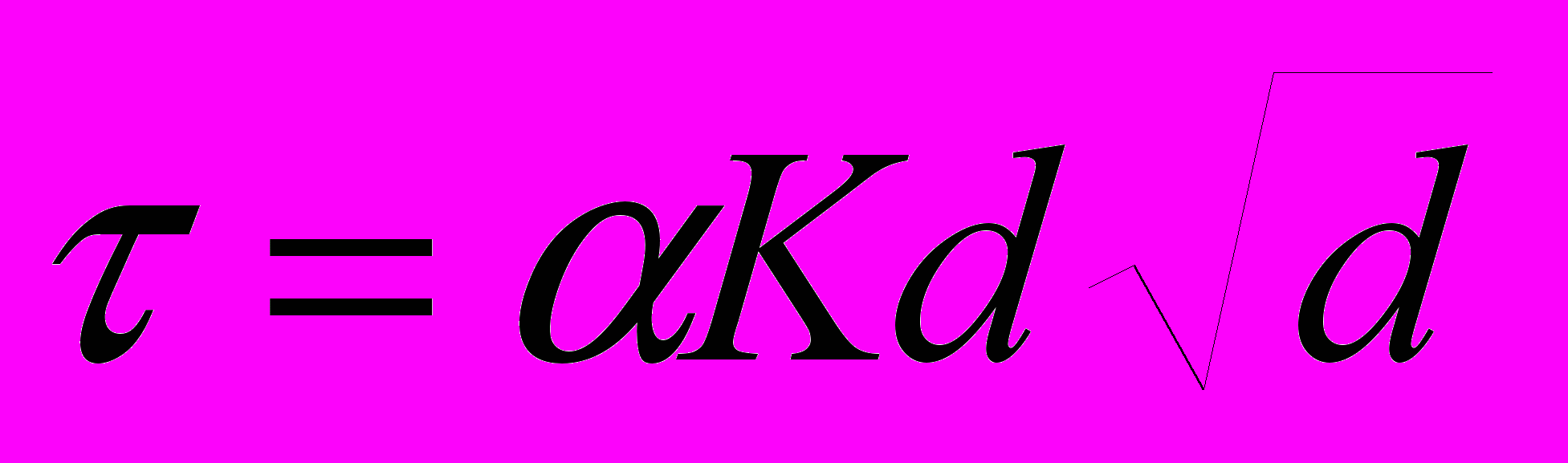
где
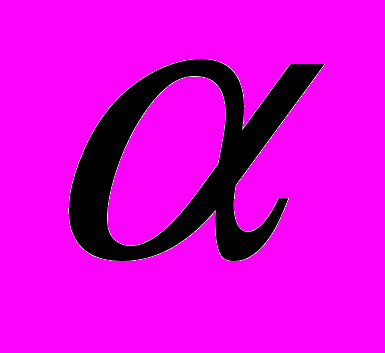
К–коэффициент, зависящий от марки стали (для малоуглеродистых К=10, для высокоуглеродистой и легированной К=20);
d–сторона или диаметр нагреваемой заготовки, м.
При высоких температурах происходит активное химическое взаимодействие стали с окружающими газами (воздухом, печным), в результате чего поверхностные слои окисляются и обезуглероживаются.
Окисленный слой металла представляет собой окалину (

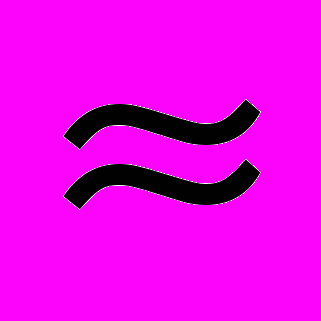
- при прокатке слитки предварительно пропускают между рифлеными валками, сбивающими окалину;
- гидроочистка, заключающаяся в кратковременном действии на заготовку струи воды под давлением 100–150 атм.
Обезуглероживание стали распространяется на глубину 1,5–2 мм и заключается в выгорании углерода с поверхностных слоев за счет взаимодействия с кислородом и водородом. Угар металла при нагреве в пламенных печах составляет 2,5–3%.
Нагревательные устройства
По источнику энергии нагревательные устройства различают пламенные и электрические.
К пламенным относят пламенные печи. Работают на жидком или газообразном топливе. Нагрев заготовок осуществляется в рабочем пространстве печи. Печи бывают камерные и методические. В камерных печах температура рабочего пространства печи одинаковая, заготовки находятся неподвижно на поду печи. В методических печах температура повышается от окна загрузки заготовок к окну их выгрузки, а заготовки двигаются навстречу потоку горячего воздуха.
К электрическим относят электрические печи сопротивления и электронагревательные устройства (для индукционного и контактного нагрева сопротивлением). В электрических печах сопротивления в стенках монтируются металлические или карборундовые сопротивления, которые подключаются к сети. Сопротивление, нагреваясь, излучает тепло, которое и передается металлу заготовки. Скорость нагрева заготовки в 8–10 раз больше, чем в пламенных печах, а угар металла в4–5 раз меньше. Практически отсутствует окалина на заготовках. Используется для нагрева заготовок под горячую объемную штамповку.
Для нагрева высокореактивных металлов находят применение методы безокислительного нагрева – это нагрев в расплавленных солях хлористого бария и натрия (
