Вторая Всероссийская конференция метизников «Метизное производство для российской автомобильной промышленности»
Вид материала | Документы |
- Международная конференция по привлечению инвестиций в производство комплектующих для, 315kb.
- Всероссийская конференция метизников Развитие метизного производства в России, 993.91kb.
- Темы: Меры государственной поддержки и регулирования в автомобильной промышленности, 138kb.
- Всероссийская конференция учителей в Волгограде, 18.84kb.
- Промышленность Ярославского края в годы предвоенных пятилеток, 296.91kb.
- Годовой отчет открытого акционерного общества «Научно-исследовательский институт технологии, 222.3kb.
- Справочник работ и профессий рабочих Выпуск 48 Разделы: "Общие профессии производств, 10592.39kb.
- Состав научно-технического совета по реализации мероприятий в области развития автомобильной, 49.42kb.
- Ий день существует необходимость защиты отечественной автомобильной промышленности, 139.61kb.
- Состоялось совместное заседание по вопросам автомобильной промышленности, 34.25kb.
Критерий «промышленная сборка» основных автомобильных компонентов
I группа
Сцепление в сборе (8708 93), рулевые механизмы (8708 94), тормозные системы (8708 39), телескопические стойки и амортизаторы (8708 80), мосты ведущие с дифференциалами в сборе (8708 50), мосты неведущие (8708 60). Проектные производственные мощности должны предусматривать наличие в производственном цикле следующих обязательных технологических операций:
– изготовление деталей картерной (корпусной) группы;
– сборочные операции, проверка качества и проведение контрольных тестов на испытательных стендах.
Количество ввозимых в стоимостном исчислении материалов и комплектующих на таможенную территорию Российской Федерации, классифицируемых кодами товарной номенклатуры внешнеэкономической деятельности Российской Федерации для «промышленной сборки», может составлять от общего объема необходимых компонентов для производства конечной продукции не более 50%.
II группа
Сиденья (9401 20), выпускные системы (8708 92)
Проектные производственные мощности должны предусматривать наличие в производственном цикле следующих обязательных технологических операций:
– сборка-сварка каркаса (корпуса);
– сборочные операции, проверка качества и проведение контрольных тестов на испытательных стендах.
Количество ввозимых в стоимостном исчислении материалов и комплектующих на таможенную территорию Российской Федерации, классифицируемых кодами Товарной номенклатуры внешнеэкономической деятельности Российской Федерации для «промышленной сборки», можетт составлять от общего объема компонентов для производства конечной продукции не более 50%.
III группа
Механизмы закрывания дверей (8301 20), ремни безопасности с преднатяжителями (8708 21), подушки безопасности (8708 99 110)
Проектные производственные мощности должны предусматривать наличие в производственном цикле следующих обязательных технологических операций: сборочные операции, проверка качества и проведение контрольных тестов на испытательных стендах.
IV группа
Прочие компоненты
Проектные производственные мощности должны предусматривать наличие в производственном цикле следующих обязательных технологических операций: сборочные операции, проверка качества и проведение контрольных тестов на испытательных стендах.
Количество ввозимых в стоимостном исчислении материалов и комплектующих на таможенную территорию Российской Федерации, классифицируемых кодами Товарной номенклатуры внешнеэкономической деятельности Российской Федерации для «промышленной сборки», может составлять от общего объема компонентов для производства конечной продукции не более 70%.
Автоматы для изготовления пружин и пружинных шайб
Гураль Иван Григорьевич
Хмельницкий завод кузнечно-прессового оборудования «Пригма-Пресс»
Старое название предприятия: «ПО «Хмельницкий завод по выпуску КПО» им. Куйбышева. Предприятие основано в 1898 году, как литейно-механический завод. Начиная с 1975 года, то есть 30 лет, завод выпускает автоматы для изготовления изделий из проволоки.
I. Автоматы для изготовления пружин
1.1. Автоматы для изготовления пружин сжатия, растяжения (без зацепов), конических, бочкообразных и другой формы.
В настоящее время завод освоил гамму пружинонавивочных автоматов, которая состоит из 4-х моделей: АА5109, А5112, АВ5116, АБ5218 и охватывает диапазон перерабатываемой проволоки от 0,2 до 7 мм. Автоматы могут изготавливать цилиндрические, конические и бочкообразные пружины сжатия с поджатыми и неподжатыми витками, с постоянным и переменным шагом, правой и левой навивки, а также пружины растяжения с шагом, равным диаметру проволоки без зацепов и прямых концов. Автоматы могут навивать одновитковые пружины.
Исходным материалом для пружин является стальная пружинная проволока круглого сечения с временным сопротивлением разрыву в пределах τв = 2500 … 1450 МПа.
Принцип работы. Проволока при помощи подающих роликов протягивается через правильное устройство, где происходит правка проволоки в 2-х взаимоперпендикулярных плоскостях и подается через проводки к навивочным упорам механизма диаметра, где формируется диаметр пружины. Одновременно задается шаг для пружин сжатия при помощи шагового пальца или клина. Для пружин растяжения шаговый механизм отключается. После навивки пружины с определенным количеством витков и определенной длиной, пружина автоматически отрезается. Затем цикл повторяется. Управление исполнительными механизмами диаметра, шага и команда на отрезку пружины осуществляются от распределительного вала. Фасонные пружины изготавливаются при помощи специального спрофилированного кулачка и рычажного механизма.
Потенциально завод готов выпускать еще два вида тяжелых пружинонавивочных автоматов АВ5120 и АБ5222 для холодной навивки пружин из проволоки диаметром 10 и 16 мм соответственно.
Таблица 1
Технические характеристики пружинонавивочных автоматов
Наименование параметров | Модели освоенных пружинонавивочных автоматов | Перспектива | ||||
АА5109 | А5112 | АБ5116 | АБ5218 | АБ5220 | АБ5222 | |
Диаметр проволоки, мм (d) максимальный минимальный | 0,8 0,2 | 1,6 0,3 | 4,0 0,8 | 6,3 1,6 | 10,0 4,0 | 16,0 6,3 |
Наружный диаметр пружины, мм (D) максимальный минимальный | 25d 5,5d | 20d 5,5d | 20d 5,5d | 18d 5,5d | 14d 5,5d | 13d 5,5d |
Шаг пружины, мм максимальный минимальный | 0,5(D-d) d | 0,5(D-d) d | 0,5(D-d) d | 0,5(D-d) d | 0,55d d | 0,55d d |
Наибольшая длина заготовки пружины, мм | 2500 | 3200 | 7550 | 30000 | 32500 | 42000 |
Производительность, шт./мин. | 12-420 | 8-320 | 200 | 100 | 90 | 20-70 |
Мощность, кВт | 1,1 | 2,2 | 5,5 | 5,5 | 13,2 | 20,0 |
Габаритные размеры, мм слева-направо спереди-назад высота | 700 735 1275 | 1050 730 1500 | 1575 1150 1800 | 2000 1480 1745 | 2850 1600 2050 | 3900 2300 2300 |
Масса автомата, кг | 445 | 650 | 2400 | 3030 | 5600 | 10800 |
1.2. Автоматы для изготовления пружин кручения с разнообразной формой зацепов.
Автоматы предназначены: для навивки пружин кручения с прямыми концами с последующей гибкой концов для придания им нужной конфигурации.
Освоено три модели автоматов: А5810, А5814 и А5816, которые охватывают диапазон проволоки от 0,2 до 4 мм.
Автоматы выполняют следующие операции: правку и подачу проволоки для образования первого и второго концов пружины, навивку пружины необходимого диаметра с заданным количеством витков правой и левой навивки, отрезку пружины и гибку концов различной конфигурации.
Таблица 2
Технические характеристики автоматов для изготовления пружин кручения
Наименование параметра | А5810 | А5814 | А5816 |
Диаметр навиваемой проволоки (d), мм | 0,2-1,0 | 0,8-2,5 | 1,6-4,0 |
Внутренний диаметр навиваемой пружины, мм | 5d-12d | 5d-12d | 5d-12d |
Наибольшее перемещение навивочного шпинделя (длина пружины), мм | 45 | 90 | 140 |
Наибольшая длина концов пружины, мм | 48 и 50 | 80 и 120 | 120 и 140 |
Число оборотов навивочного шпинделя (регулируемое), мин-1 | 0-70 | 0-70 | 0-40 |
Наибольший диаметр навивочной оправки, мм | 10 | 20 | 40 |
Производительность (регулируемая), шт./мин. | 18-100 | 12-70 | 10-40 |
Габаритные размеры, мм слева-направо спереди-назад высота | 650 1200 1400 | 875 2000 1680 | 1300 2700 2100 |
Масса автомата, кг | 720 | 1700 | 3900 |
1.3. Комплекс оборудования для изготовления манжетных пружин.
Комплекс включает в себя автомат пружинонавивочный модели А5009, предназначенный для навивки пружин и автоматы модели АО531 и АО535 для стыковки манжетных пружин в кольцо.
Таблица 3
Техническая характеристика автомата модели А5009
Наименование параметра | Значение |
Диаметр навиваемой проволоки (d), мм | 0,3-0,8 |
Наружный диаметр навиваемой пружины, (D), мм наименьший наибольший | 5d 10d |
Длина навиваемой пружины, включая коническую часть, мм | 32-400 |
Наибольшая скорость подачи проволоки, регулируемая, м/мин. | 130 |
Наибольшая длина заготовки пружины, не менее, мм | 11260 |
Габаритные размеры, мм слева-направо спереди-назад высота | 960 900 1520 |
Мощность электроприводов, кВт | 1,65 |
Масса, кг | 520 |
Таблица 4
Техническая характеристика стыковочных автоматов
Наименование параметра | АО531 | АО535 |
Длина цилиндрической части пружины, мм | 277-120 | 70-320 |
Диаметр пружин, наружный, мм | 1,8-3,0 | 1,8-3,0 |
Диаметр проволоки пружин, мм | 0,3-0,5 | 0,3-0,5 |
Производительность, шт./мин. наименьшая наибольшая | 25 60 | 25 50 |
Мощность электродвигателя, кВт | 0,25 | 0,25 |
Габариты автомата, мм слева-направо спереди-назад высота | 900 560 1385 | 800 650 1385 |
Масса автомата, кг | 320 | 320 |
1.4. Автомат для изготовления матрацных пружин модели АА5013.
Автомат предназначен для навивки двухконусных пружин, завязки узлов на крайних витках и термической обработки пружин.
Исходный материал: проволока диаметром 2,2 мм ТУ14-4-920-78 или проволока П2,2 ГОСТ9389-75, поставляемая в мотках.
Автомат модели АА5013 является специальным. За один цикл на автомате изготавливается 2-х конусная пружина с двумя закрученными узлами на опорных витках, термически обработанная.
Процесс изготовления пружины осуществляется следующим образом: проволока с приводного устройства через петлеобразователь, правильное устройство и механизм подачи подается к диаметрообразующему ролику. Процесс образования диаметров 2-х конусных пружин происходит по одноупорной схеме с одновременным формированием шага.
Навитая 2-х конусная пружина обрезается и перекладывается в транспортный ротор, при помощи которого пружина транспортируется к позициям закрутки узлов на опорных витках и термообработки, далее она поступает на стапелирование в приемный лоток.
Таблица 5
Техническая характеристика автомата модели АА5013
Наименование параметра | Значение |
Диаметр навиваемой проволоки, мм | 2,2 |
Наружный диаметр опорного витка пружины, мм | 88 |
Высота пружины, мм | 80; 100; 120 |
Полное число витков пружины, мм | 4; 5 |
Наибольшая скорость навивки, м/мин. | 90 |
Производительность, шт./мин. | 40; 60 |
Габаритные размеры, мм слева-направо спереди-назад высота | 1600 1820 1700 |
Мощность установленная, кВт | 23 |
Масса, кг | 2500 |
1.5. Автомат для горячей навивки пружин модели АБ5424.
Предназначен для горячей навивки пружин сжатия и растяжения правой и левой навивки из мерных прутков диаметром 8-25 мм. Возможно изготовление пружин с различным шагом навивки, количеством витков, а также пружин с поджатыми или неподжатыми начальными и конечными витками.
Исходный материал: проволока группы «А», «Б», «В», «Г» по ГОСТ14963-79, ГОСТ2590-71 (в прутках мерной длины).
Таблица 6
Техническая характеристика автомата модели АБ5424
Наименование параметра | Значение |
Диаметр заготовки (d), ММ | 8-25 |
Длина заготовки, наибольшая, мм | 9000 |
Внутренний диаметр навиваемой пружины (D), мм минимальный максимальный | 2,5d 250 |
Длина пружины, наибольшая, мм | 1000 |
Шаг навиваемой пружины, при D=250 мм, наибольший, мм | 60 |
Производительность, шт./мин. | 20-50 |
Габаритные размеры, мм слева-направо спереди-назад высота | 2150 1030 1680 |
Мощность установленная, кВт | 6,3 |
Масса, кг | 3200 |
1.6. Приспособления для формирования ушек пружин.
На предприятии разработан целый ряд пневматических приспособлений для загиба ушек пружин. На них можно загибать ушки английского, немецкого и американского типов, а также вытянутые ушки.
II. Автоматы для изготовления пружинных шайб
2.1. Гамма автоматов для изготовления пружинных шайб гровера.
Гамма включает в себя 5 моделей автоматов: А5715; А5721А; А5723А; А5725А; А5727А, которые охватывают изготовление шайб с внутренним диаметром шайбы от 3 до 48 мм из проволоки квадратного и трапециевидного сечения.
Процесс изготовления шайбы заключается в следующем. Правка подаваемой проволоки неприводным правильным устройством, установленным на оси подачи проволоки; навивка проволоки в спираль соответствующего диаметра посредством проталкивания проволоки клещами через навивочный инструмент; отрезка шайбы от спирали подвижным ножом, совершающим вертикальное перемещение при радиальном резе; сброс отрезанной шайбы в тару.
Таблица 7
Технические характеристики гаммы шайбонавивочных автоматов
Наименование параметра | А5715 | А5721А | А5723А | А5725А | А5727А |
Внутренний диаметр шайбы, условный, мм | 2-3 | 3-12 | 10-22 | 18-36 | 24-48 |
Размеры квадратного сечения обрабатываемой проволоки, мм | 0,50,5 11 | 11 2,52,5 | | | |
Размеры трапециевидного сечения проволоки, мм | - | 1,2 3,0 | 23 25 4,56 | 4,5 9 | 5,58 12 |
Число циклов в минуту | 400-600 | 320-550 | 180-400 | 140-250 | 120-210 |
Мощность двигателя, кВт | 1,1 | 1,8 | 6,0 | 8,0 | 14,0 |
Габаритные размеры, мм слева-направо спереди-назад | 960 605 | 850 870 | 1450 1040 | 1850 1400 | 2800 1700 |
Масса, кг | 380 | 560 | 1420 | 2650 | 4350 |
2.2. Автомат для изготовления 2-х и 3-х витковых путевых шайб модели АВ0624.
Предназначен для изготовления пружинных шайб для крепления верхних железнодорожных путей из калиброванной проволоки трапецеидального сечения размером 810 мм из стали 65Г.
Шайбы изготавливаются в пространстве навивочного и опрессового штампов. В этих механизмах осуществляется последовательно следующие операции: навивка проволоки трапециевидного сечения в спираль; отрезка заготовки шайбы; передача шайбы в пресс для опрессовки; сброс готовой шайбы. За один рабочий ход изготавливается одна шайба.
Процесс изготовления шайбы заключается в следующем. Проволока трапециевидного сечения с размоточного устройства подается в отрезной агрегат, где отрезается конец проволоки и подготавливается начало проволоки для заправки в автомат. Вспомогательные ролики вставляют проволоку в подающие сегменты, откуда она поступает в навивочный инструмент и завивается в спираль с соответствующим шагом. При помощи отрезного механизма происходит отрезка от спирали одного и трех четверти витка. Отрезанные витки затем специальным устройством переносятся по направляющим в пресс, где изготовленной шайбе придается нужная форма. При отходе ползуна высадки шайба высвобождается и сбрасывается в тару. Далее процесс повторяется.
Таблица 8
Техническая характеристика автомата модели АВ0624
Наименование параметра | Значение |
Внутренний диаметр навиваемых шайб, условный, мм | 25 |
Размеры трапециевидного сечения обрабатываемой проволоки, наибольшие, мм | 8,510 |
Число циклов в минуту, мм | 50 |
Наибольшая длина подаваемого материала, мм | 320 |
Габаритные размеры, мм слева-направо спереди-назад высота | 3200 2000 1950 |
Мощность установленная, кВт | 21,0 |
Масса, кг | 12300 |
Заключение
Предприятие выпускает также много других автоматов по изготовлению изделий из проволоки, это:
- гамму проволочно-гвоздильных автоматов по изготовлению гвоздей диаметром 0,8-6 мм и длиной от 5 до 200 мм;
- оборудование для галтовки и упаковки гвоздей;
- автоматы для изготовления сетки «рабица»;
- гамму правильно-отрезных автоматов для правки и порубки мерных прутков из бунта. Диаметр проволоки 1,8-16 мм длина до 12 метров;
- автоматы для изготовления одноосновной и двухосновной колючей проволоки;
- другие специальные автоматы для изготовления изделий по чертежам заказчика.
Хмельницкий завод по выпуску кузнечно-прессового оборудования намерен и в дальнейшем вести разработку и освоение новых видов оборудования для изготовления изделий из проволоки, в том числе и специального, под конкретное изделие.
Завод участвует в различных международных выставках и экспортирует свою продукцию более чем в 25 стран дальнего зарубежья и в страны СНГ.
Современные профильношлифовальные станки для изготовления резьбонакатных плашек
Гриханов Михаил Иванович
«Кербер Шляйфринг», Германия
Тезисы доклада:
Разработана технология профильного шлифования закаленных HRC 62 резьбонакатных плашек из инструментальной и быстрорежущей стали, основанная на применении высокопроизводительного метода врезного глубинного шлифования, специализированных профильношлифовальных станков с ЧПУ фирм Мегерле АГ Машиненфабрик/Швейцария и Блом Машиненбау ГмбХ/Германия, оснащенных устройствами подачи СОЖ мощностью до 200-300 л/мин, шлифовальными кругами размерами до 500 х 180 мм.
Это позволяет производить шлифование рифленного профиля закаленных резьбонакатных плашек при глубинах шлифования 1,0 мм и более и получать требуемую шероховатость и точность обработанной поверхности.
Пример обработки резьбонакатной плашки:
- Материал: быстрорежущая сталь закаленная HRC 62
- Размеры плашки: 130 x 50 мм
- Шлифование рифленного профиля с заходной и выходной частью,
припуск: 1 мм
- Метод шлифования: врезное глубинное попутное шлифование с
интерполяцией осей
- 2 прохода: черновой проход припуск 0,99 мм
чистовой проход припуск 0,01 мм
- Правка: стальной или алмазный ролик
- Время обработки: 6,5 мин

Преимущества современной шлифовальной технологии:
- cокращение времени обработки
- повышение стойкости плашек
- улучшение качества, повышение точности и стабильности
параметров накатанных изделий
- уменьшение производственных издержек
- уменьшение затрат на инструмент.
Технологические особенности изготовления шаровых пальцев с повышенной эксплуатационной стойкостью
Лавриненко Владислав Юрьевич, к.т.н.
МГТУ им. Баумана
Шаровые пальцы шарниров рулевого управления и подвески автомобиля (рис.1) являются ответственными деталями, от эксплуатационной стойкости и долговечности которых зависит безаварийная и безотказная эксплуатация автомобиля.
Анализ основных возможных причин выхода из строя шаровых шарниров автомобиля показал, что из-за значительного износа рабочих контактных поверхностей шаровой головки и вкладыша шарового шарнира между корпусом шарнира и шаровой головкой появляется зазор, который приводит к появлению высоких ударных нагрузок в галтели - месте перехода от головки к стержневой части шарового пальца. [1, 2].
![]() |
Рис.1. Шаровой шарнир автомобиля: 1 – вкладыш; 2 - шаровой палец; 3 – нижний корпус; 4 – верхний корпус; 5 – заливочный материал |
Поэтому можно сделать вывод о том, что создание благоприятного волокнистого строения в рабочей контактной зоне и галтели шаровых пальцев дает возможность увеличить износостойкость контактной поверхности шаровой головки, уменьшить ударные нагрузки и повысить эксплуатационную стойкость и срок службы детали в 2-4 раза.
Проведенные предварительные исследования зависимости износостойкости от характера расположения волокнистого строения относительно контактной поверхности показали значительное влияние различной ориентировки волокон макроструктуры на стойкость на истирание поверхности [3].
Для дальнейшего изучения влияния различного расположения волокнистого строения на стойкость на истирание контактной поверхности была проведена серия экспериментов. Было сделано предположение о том, что наиболее благоприятное расположение волокон будет соответствовать их направлению вдоль контактной поверхности, когда угол наклона к контактной поверхности будет равен нулю.
Исходя из этих предпосылок, было проведено исследование стойкости на истирание образцов из трех различных сталей: 40Х, 45 и 38ХГНМ с различными углами выхода волокон на контактную поверхность: 0º (продольное расположение волокон), 45º и 90º (поперечное расположение волокон) и с различными режимами термической обработки.
Испытания проводили на стандартной испытательной машине трения «Шкода-Савин». Машина предназначена для определения сопротивления материалов износу роликом из твердого сплава ВК-6 (диаметр ролика 30 мм, ширина 2.5 мм), работающим при постоянных условиях и практически не подверженному износу. Ролик внедрялся в поверхность образца под определенной нагрузкой. Износ при нормальных условиях опыта определялся длиной или объемом углубления, образованного в испытываемом образце вращающимся роликом при постоянном общем количестве оборотов ролика.
Образцы представляли собой кубики с размерами 20х20х20мм. Образцы имели различный угол выхода волокон на контактную поверхность: 0º, 45º и 90º (рис.2).
Для образцов с продольным расположением волокон испытания проводили в двух различных взаимно перпендикулярных направлениях: параллельно и перпендикулярно волокнам (рис.2,а, б).
![]() | |||
а | б | в | г |
Рис.2. Расположение волокон относительно контактной поверхности в образцах: а) угол выхода волокон 0º, испытания параллельно волокнам; б) угол выхода волокон 0º, испытания перпендикулярно волокнам; в) угол выхода волокон 45º; г) угол выхода волокон 90º |
Образцы из стали 40Х были подвергнуты термической обработке по двум различным режимам:
1) отжиг 700 °С, 5 ч;
2) закалка 830 °С + отпуск 550 °С.
Образцы из стали 45 были подвергнуты термической обработке по двум различным режимам:
1) отжиг 700 °С, 5 ч;
2) закалка 830 °С + отпуск 200 °С.
Образцы из стали 38ХГНМ также были подвергнуты термической обработке по двум различным режимам:
1) отжиг 700 °С, 5 ч;
2) закалка 880 °С + отпуск 620 °С.
Относительную износостойкость вычисляли по формуле:
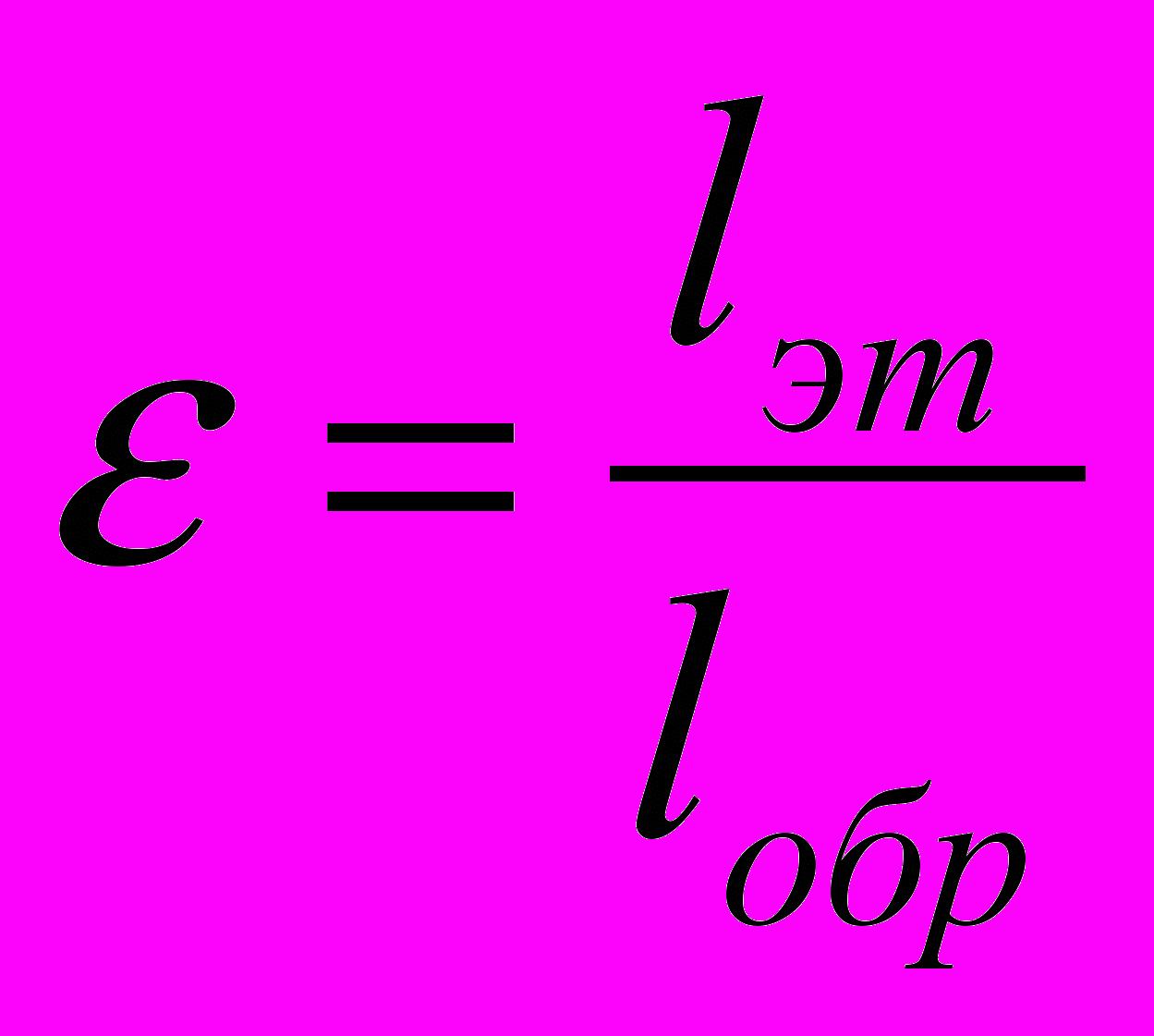
где lэт - длина углубления, образовавшегося в эталоне; lобр - длина углубления в образце.
В табл. 1 и на рис.3 представлены значения относительной износостойкости испытываемых образцов.
Проанализировав результаты испытаний на истирание, необходимо отметить, что относительная износостойкость имеет максимальные значения у образцов с выходом волокон на контактную поверхность под углом 0°, а минимальные значения – у образцов с выходом волокон на контактную поверхность под углом 90°. При этом разница значений максимальной и минимальной относительной износостойкости для отожженных образцов из стали 40Х составляет 17 %, для закаленных образцов 10 %; для отожженных образцов из стали 45 разница составляет 40 %, а для закаленных образцов – 15 %; для отожженных и закаленных образцов из стали 38ХГНМ – приблизительно 10%. Можно отметить, что наибольшая разница в значениях относительной износостойкости имела место для отожженных образцов из стали 45.
Относительная износостойкость образцов с выходом волокон на контактную поверхность под углом 45° имеет промежуточные значения для всех материалов и режимов их термической обработки.
При испытании образцов с выходом волокон на контактную поверхность под углом 0º при внедрении ролика в контактную поверхность образца в двух различных взаимно перпендикулярных направлениях - параллельно и перпендикулярно волокнам существенной разницы в значениях относительной износостойкости не наблюдалось.
Таблица 1.
Относительная износостойкость образцов с различными углами выхода волокон на контактную поверхность
Угол выхода волокон на контактную поверхность | Материал | ||
Сталь 40Х | Сталь 45 | Сталь 38ХГНМ | |
0º Параллельно Перпендикулярно | 1.291 / 1.723 1.169 / 1.604 | 1.224 / 1.641 1.210 / 1.641 | 1.147 / 1.307 1.067 / 1.244 |
45° | 1.122 / 1.543 | 0.964 / 1.469 | 0.941 / 1.280 |
90° | 1.079 / 1.428 | 0.761 / 1.422 | 0.764 / 1.244 |
Примечание: в числителе приведены значения износостойкости для образцов после отжига; в знаменателе – после закалки и отпуска |
![]() | ![]() |
а | б |
![]() | |
в | |
Рис.3. Относительная износостойкость образцов с различным расположением волокон относительно контактной поверхности: а – сталь 40Х; б – сталь 45; в - сталь 38ХГНМ |
Для изучения особенностей формирования волокнистого строения поковок шаровых пальцев при высадке в зависимости от основных технологических параметров высадки были проведены экспериментальные исследования [4].
При проведении экспериментальных исследований использовали физическое моделирование высадки стали холодной высадкой заготовок из прессованного пруткового алюминия 20-0.3 мм марки 1050А (АД-0, ГОСТ 4784-97) в отожженном состоянии на прессе УИМ-50 (универсальная испытательная машина номинальной силой 0,5 МН).
При проведении экспериментов для построения регрессионных математических моделей методами факторного планирования были составлены матрицы планов экспериментов. В качестве независимых факторов, влияющих на проведение процесса высадки, были приняты: величина относительной высаживаемой длины ψ; угол скоса торца заготовки и способ предварительной наборной высадки – в коническом пуансоне или в цилиндрической матрице.
Были спроектированы штампы для экспериментальной одно- и многопереходной высадки поковок шаровых пальцев.
Для исследования волокнистого строения поковок при высадке использовали метод травления на макроструктуру.
В качестве показателей симметричности волокнистого строения рассматривали значения максимального смещения max - наибольшее из смещений центрального волокна относительно центральной оси поковки i по абсолютной величине и среднего смещения ср - полусумма абсолютных величин смещений i; показатель плавности n, численно равный количеству смещений центрального волокна относительно центральной оси поковки, а также величину угла наклона центрального волокна относительно оси поковки в верхней части шаровой головки (рис.4).
![]() | |||
а | |||
![]() | ![]() | ![]() | ![]() |
б | в | ||
Рис.4. Волокнистое строение исходной заготовки (а), шаровой головки при однопереходной (б) и многопереходной высадке (в) |