На правах рукописи
Вид материала | Автореферат |
- Печатная или на правах рукописи, 21.09kb.
- Удк 796/799: 378 , 770.24kb.
- На правах рукописи, 399.58kb.
- На правах рукописи, 726.26kb.
- На правах рукописи, 1025.8kb.
- На правах рукописи, 321.8kb.
- На правах рукописи, 552.92kb.
- На правах рукописи, 514.74kb.
- На правах рукописи, 670.06kb.
- На правах рукописи, 637.26kb.
В четвертой главе приводятся данные по влиянию режима электролиза на показатели процессов катодного осаждения серебра и анодного растворения вольфрама и серебра, а также сплавов на их основе.
Установлено, что при переходе к импульсным режимам осаждения поляризация возрастает, особенно этот эффект проявляется при увеличении скважности импульсов. Катодная поляризуемость () при этом также возрастает (рис. 6).
![]() | Рис. 6. Зависимость катодной поляризуемости от плотности тока при осаждении серебра из пирофосфатно-аммиакатного электролита для стационарного (1) и импульсного (2) режимов электролиза. 3 – расчетная кривая (для jd = 1,2 А/дм2). |
При сочетании тафелевской и концентрационной поляризации (т.е. при смешанной кинетике), зависимость поляризуемости от плотности тока описывается уравнением:
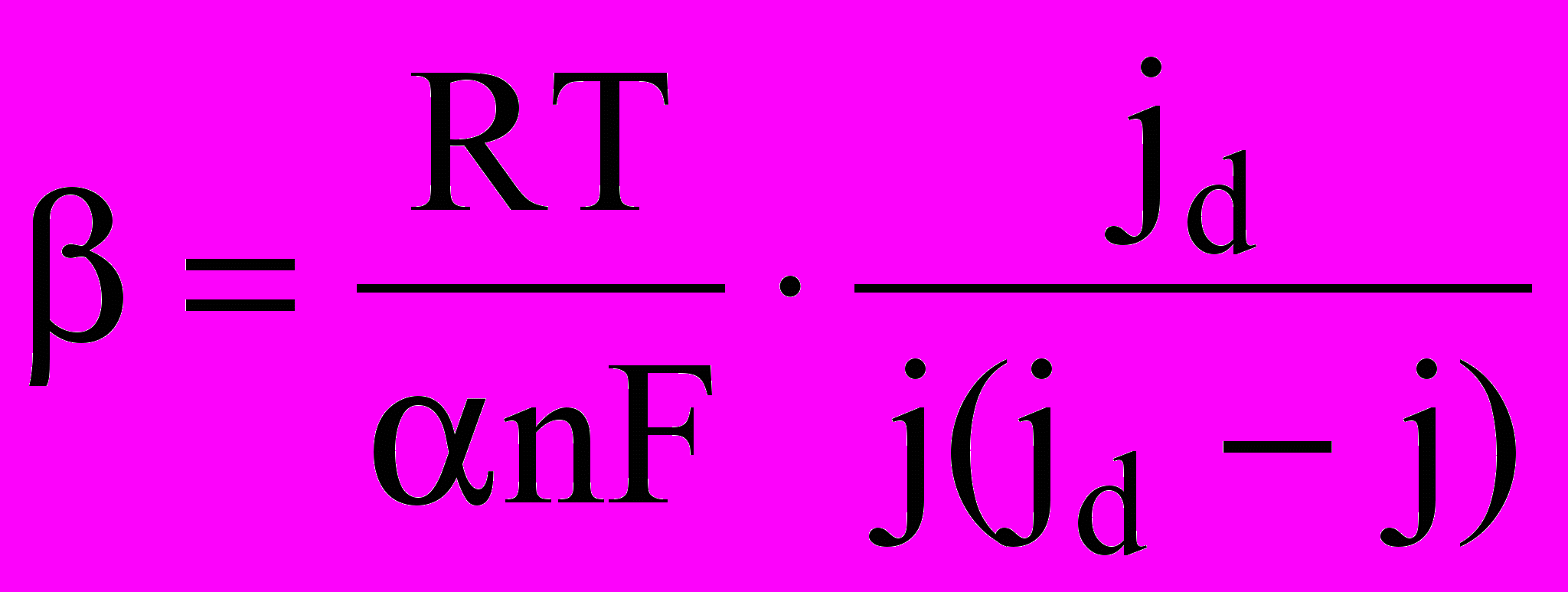
Отсюда следует, что основным фактором, влияющим на поляризуемость, является величина диффузионного тока jd – чем она меньше, тем поляризуемость выше. Поэтому высокопроизводительные электролиты, характеризующиеся большими значениями jd, по самой своей природе обладают низкой поляризуемостью, а следовательно, и рассеивающей способностью (если выход по току не зависит от плотности тока). Как видно из рис. 6, максимальных значений поляризуемость достигает либо при низких плотностях тока, либо при jjd. Поскольку при стационарном режиме электролиза осаждение в области диффузионного контроля приводит к ухудшению качества осадка, при нанесении покрытия на изделия сложной конфигурации для улучшения равномерности распределения металла приходится значительно снижать плотность тока. Применение импульсного режима осаждения дает возможность без ухудшения структуры катодного осадка работать при повышенных плотностях тока, что позволяет повысить поляризуемость и одновременно интенсифицировать катодный процесс, не меняя состава раствора. При импульсном режиме наблюдается улучшение распределения металла на внутренней поверхности цилиндрического трубчатого катода (рис. 7). В пирофосфатно-аммиакатном электролите на трубчатом катоде данный эффект достигается при средней плотности тока близкой к 0,7 А/дм2. Этот факт объясняется тем, что при увеличении плотности тока на наиболее нагруженных участках катода достигается потенциал, соответствующий выходу на площадку предельного тока, вызванного обеднением приэлектродной зоны ионами серебра. В результате происходит перераспределение тока вдоль поверхности электрода и выравнивание толщины осадка.
![]() | Рис. 7. Распределение серебра по внутренней поверхности трубчатого катода при электроосаждении из пиро-фосфатно-аммиакатного электролита серебрения: □ – привес металла в стационарном режиме, ■ – привес металла в импульсном режиме (f=50 Гц, отсечка шага 1/4 Т). jср= 0,7 А/дм2. |
Форма тока влияет и на микроструктуру осадка. Во всех случаях шероховатость серебряного осадка увеличивается по сравнению с исходной поверхностью. Однако относительное увеличение Rа покрытий, осажденных с использованием различных режимов импульсного тока меньше, чем у осадков, полученных на постоянном токе. Уменьшение длительности импульсов тока и увеличение их амплитуды способствует снижению шероховатости.
Наилучшие результаты достигаются при импульсном режиме с отсечкой шага в 1/4 Т, при средней катодной плотности тока 0,5 А/дм2. Как видно из рис. 8, использование импульсных режимов электроосаждения способствует уменьшению размера зерен образующихся кристаллов серебра, т.е. формированию более равномерной структуры катодного осадка вследствие возрастания перенапряжения во время катодного импульса. Применение импульсного режима способствует также уменьшению внутренних напряжений и пористости покрытий.
![]() | ![]() |
Рис. 8. Микрофотографии поверхности серебряного покрытия (х2500):
а – стационарный режим; б – импульсный режим.
При анодной обработке применение импульсного режима позволяет управлять процессами пассивации, что особенно важно при обработке легко пассивирующихся металлов. Как видно из рис. 9, в водном растворе хлорида натрия при наложении постоянного потенциала сплав ВК8 быстро пассивируется, тогда как при импульсном режиме, несмотря на спад тока в начальный период времени, полной пассивации не наблюдается. В растворе, содержащем моноэтаноламин, при потенциостатическом включении практически мгновенно устанавливается стационарный ток, величина которого возрастает при использовании импульсного режима.
![]() | Рис. 9. Хроноамперограммы для сплава ВК8 при потенциале 4 В: 1, 2 – в растворе 1 М NaCl; 3, 4 – в растворе 1 М NaCl + 6 М МЭА (1, 3 –без наложения импульсов, 2, 4 – импульсный режим с наложением прямоугольного напряжения амплитудой 1 В, f=200 Гц). |
Применение нестационарного режима часто способствует повышению качества поверхности (табл. 6), причем максимальный эффект обеспечивается при анодной обработке в водно-органических электролитах.
Таблица 6.
Зависимость шероховатости поверхности сплава ВК8 от потенциала.
Состав и концентрация электролита | Высота микронеровностей Rz, мкм при потенциале, В | |||
1,3 | 2,3 | 3,3 | 4,0 | |
1М NaCl | ![]() | ![]() | ![]() | ![]() |
1М NaCl + 6М МЭА | ![]() | ![]() | ![]() | ![]() |
(В числителе указаны значения Rz при растворении в потенциостатическом режиме, а в знаменателе – при наложении прямоугольного напряжения,
f=200 Гц).
Положительный результат от применения нестационарного режима обработки был получен и при электрополировании серебра и сплава СрМ925. Было установлено, что оптимальный эффект сглаживания микропрофиля достигается при длительности импульса 0,5–1 с и скважности 8–10. Максимальное сглаживание микропрофиля имеет место при обработке серебра в импульсном режиме в растворе, содержащем глицерин (рис. 10, табл. 5).
| ![]() | ![]() |
![]() | ![]() |
Рис. 10. Профилограммы поверхности серебра после анодной обработки в растворах 4М KSCN (а, б) и 4М KSCN + 0,4М С3Н8О3 (в, г): а, в – постоянный ток, j=0,07 А/см2; б, г – импульсный ток, jи=0,7 А/см2, tи=1с, скважность 10. Продолжительность обработки 1 мин, Т=298 К. Вертикальное увеличение ×5000, горизонтальное увеличение ×100.
Ведение в роданидный электролит многоатомного спирта в оптимальной концентрации (0,4 моль/л) способствует также повышению отражательной способности обработанной поверхности на 15-20%.
Глава 5. Поведение металлов при химической обработке
В разделе 5.1 приведены результаты исследований поведения титана и меди в процессе химического полирования. Химическое полирование титана может быть использовано как в процессе предварительной подготовки деталей под гальванические покрытия, так и в качестве самостоятельной операции финишной обработки изделий из титановых сплавов. Традиционно применяемые в промышленности растворы для химического полирования титана содержат фтористоводородную и азотную кислоты. Такие растворы отличаются высокой агрессивностью по отношению к оборудованию, в ходе обработки образуется большое количество оксидов азота. Нами было предложено использовать в качестве активатора кислый фторид аммония, а в качестве окислителя - солянокислый гидроксиламин (Патент РФ № 2260634).
При изучении влияние концентраций компонентов раствора на стационарный потенциал титанового электрода установлено, что, изменяя соотношение концентраций окислителя и активатора, возможно достижение компромиссного потенциала поверхности, соответствующего протеканию коррозионного процесса в режиме полирования.
Наряду с составом раствора на показатели полирования большое влияние оказывает и температура. При низких температурах коррозионный ток недостаточен для получения эффекта сглаживания поверхности. Увеличение температуры от 250С до 800С приводит к увеличению скорости растворения почти в 3 раза.
По величинам расчетного коррозионного тока температурно-кинетическим методом была рассчитана эффективная энергия активации. Ее значения (в интервале температур 25-900С) находятся в пределах 16-22 кДж/моль, что указывает на протекание процесса со смешанным диффузионно-кинетическим контролем. Увеличение концентрации окислителя приводит к уменьшению энергии активации.
Электрохимическое поведение титана в растворе фторида аммония и в растворе химического полирования, представлено на рис. 11. По сравнению с чисто фторидным раствором, в растворе полирования катодная стадия процесса ускоряется, а анодная – тормозится.
![]() | Рис. 11. Циклические потенцио-динамические (50 мВ/с) поляризационные кривые титанового электрода в растворах: 1 – 2,8 М NH2OHHCl + 1,4 М NH4FHF; 2 - 1,4 М NH4FHF. Т=293 К. |
В отличие от чисто фторидного раствора, величина анодного тока в большей степени зависит от гидродинамических условий, что свидетельствует о существенной роли диффузионных ограничений. При увеличении скорости вращения дискового электрода возрастает как высота анодного тока максимума, так и значения токов на катодной ветви кривых. Следовательно, на скорость процесса влияет как подвод NH2OHHCl к поверхности электрода, так и отвод продуктов растворения титана от поверхности в объем раствора, причем, судя по отношениям токов на вращающемся и неподвижном электродах, стадия отвода продуктов влияет сильнее.
Изменение содержания окислителя во фторидном растворе влияет и на анодный и на катодный процессы. При использовании неподвижного электрода увеличение концентрации окислителя приводит к уменьшению анодных токов начала пассивации титана, а на вращающемся электроде, наоборот, к повышению токов.
При увеличении концентрации NH2OHHCl роль диффузии в растворе возрастает, о чем свидетельствуют результаты, представленные на рис. 12. Следует отметить, что в случае чисто диффузионного контроля зависимость jд -
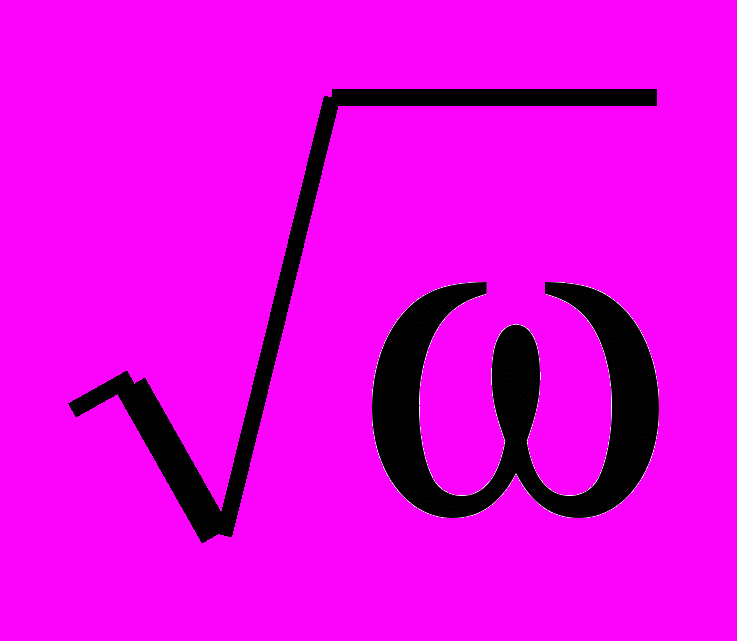

где p – порядок реакции; jk – кинетический ток, jd – диффузионный ток.
![]() | Рис. 12. Зависимость плотности тока в максимуме поляризационной кривой от скорости вращения титанового дискового электрода в растворах, содержащих 1 М NH4FHF и различное количество NH2OHHCl, моль/л: 1 – 2,1; 2 – 2,8; 3 – 3,4. Т=298 К. |
Определенное из зависимости lg j – lg (1-j/jd) значение кинетического тока составило 0,44 А/см2, а порядок реакции оказался близким к нулю. Такое же значение порядка реакции по окислителю было получено из угла наклона зависимости lgjmax – lgCNH2OHHCl. По-видимому, гидроксиламин не принимает непосредственного участия в анодной стадии процесса, а некоторое увеличение анодного тока с ростом его концентрации обусловлено уменьшением поляризации сопряженного катодного процесса.
Изучение механизма растворения титана в процессе полирования проводили также при потенциостатических исследованиях. Одновременно со значениями тока и количества прошедшего через систему электричества измеряли убыль массы образца, из которой рассчитывали коррозионный ток, соответствующий растворению титана (в расчете на Ti (IV)). Вид кривых, построенных исходя из количества пропущенного электричества и из убыли массы, аналогичен, но значения плотностей тока заметно отличаются, за исключением области пассивации. Причина этого заключается в стадийном механизме окисления титана. В раствор переходят ионы титана в низших степенях окисления, а доокисление до TI(IV) происходит в объеме электролита кислородом воздуха (в случае чисто фторидного раствора) или с участием окислителя. В растворе, содержащем окислитель, растворение титана начинается при более положительном потенциале вследствие усиления роли оксидной пленки, и значения измеренных и рассчитанных токов заметно ниже.
О стадийном механизме окисления титана во фторидсодержащих средах и переходе в раствор в виде ионов Ti(III) свидетельствуют и результаты волюмометрических измерений. Объем водорода, выделяющегося при растворении титана, соответствует реакции окисления до Ti(III). Переход титана во фторидсодержащий раствор в виде Ti(III) отмечен и в работах Л.Е. Цыганковой и В.И. Вигдоровича. Эффективная степень окисления (nэф) титана, рассчитанная принимая для анодной реакции ВТ=100%, меняется от 2 до 4, возрастая при увеличении потенциала анода. При потенциале, соответствующем максимуму анодного тока nэф=3.
Несмотря на высокую концентрацию активирующих фторид-ионов, на поверхности титана присутствует оксидный слой, о чем свидетельствуют результаты, полученные методом ФЭП. Свойства этого слоя изменяются в зависимости от состава раствора и электродного потенциала. Во фторидном растворе без NH2OHHCl в области активного растворения фото-ЭДС близка к нулю, то есть роль оксидной пленки невелика и начинает заметно сказываться лишь в области пассивации (табл. 7). Введение в раствор окислителя способствует ускорению окислительных процессов и препятствует накоплению ионов Ti3+ в оксидном слое, что обеспечивает увеличение амплитуды фотоответа. Таблица 7.
Зависимость фото-ЭДС титанового электрода от потенциала после обработки во фторидсодержащих растворах.
Состав раствора | Vфэп, мкВ после обработки при потенциале, В | ||||
-1,6 | -1,3 | -1,0 | -0,7 | -0,4 | |
1 М NH4FHF | -10 | -50 | -130 | -80 | -110 |
2,8 М NH2OHHCl, 1 М NH4FHF | -260 | -300 | -170 | -540 | -600 |
Импедансные измерения показали, что введение NH2OHHCl во фторидный раствор приводит к резкому уменьшению емкости (на частоте 1000 Гц она снижается с 38,24 мкФ/cм2 до 17,73 мкФ/cм2). Электрическое сопротивление пленки, сформированной во фторидсодержащем растворе без окислителя, в 2 раза ниже, чем после обработки в растворе, содержащем гидроксиламин (5,01 и 10,21 Омсм2 соответственно). Следовательно, увеличение содержания окислителя в растворе полирования приводит к изменению структуры и состава поверхностных пленок, что способствует уменьшению шероховатости.
Показатели процесса химического полирования титана во многом определяются соотношением концентраций активирующего компонента раствора и окислителя. При низкой концентрации NH2OHHCl и при высокой концентрации NH4FHF происходит растравливание поверхности. Увеличение содержания окислителя способствует повышению эффекта полирования. Повышение температуры раствора положительно влияет на качество поверхности.
Процесс глянцевания предпочтительнее проводить при температуре 104-1060С в растворе, содержащем NH2OHHCl 200-250 г/л и NH4FHF 60-100 г/л в течение 1-1,5 мин. В этих условиях отражательная способность достигает 60-80% при исходном значении 7-8 %, а степень сглаживания 70-85% (исходное Ra=0,7 мкм). При химическом полировании деталей, не требующих высокой степени блеска и имеющих точные размеры, обработку целесообразно проводить при меньшей температуре (80-900С) в растворе, содержащем NH2OHHCl 200-250 г/л и NH4FHF 60-80 г/л в течение 1 - 1,5 мин. При таких условиях сглаживание поверхности составляет от 48 до 75% (конечное Ra=0,2–0,3 мкм), отражательная способность 30-57%.
Используемые в настоящее время растворы химического полирования меди и ее сплавов на основе азотной кислоты характеризуются высокой агрессивностью, а процесс обработки в таких растворах сопровождается выделением большого количества оксидов азота. Нами был разработан ряд новых растворов для химического полирования меди и ее сплавов на основе фосфорной кислоты, в которых вместо азотной кислоты использованы ее соли.
Поляризационные измерения показали, что введение окислителя в раствор фосфорной кислоты способствует деполяризации катодного процесса, тогда как значение анодного тока не изменяется или даже уменьшается. Скорости как катодной, так и анодной реакций заметно зависят от гидродинамических условий и возрастают при увеличении скорости вращения дискового электрода.
Компромиссный потенциал коррозионного процесса при введении окислителя смещается в сторону положительных значений, что обусловлено усилением пассивационных явлений. При увеличении скорости вращения электрода он смещается в отрицательную сторону. Такого рода зависимости характерны для процессов коррозии, осложненных диффузией продуктов растворения от поверхности электрода в объем раствора.
На анодной ветви обратного ходе наблюдается область предельного тока. Высота этой площадки линейно зависит от квадратного корня из скорости вращения дискового электрода. Следовательно, процесс химического полирования протекает при наличии на поверхности меди слоя продуктов анодного окисления, растворение которых протекает с диффузионным контролем. О существенной роли оксидных слоев в процессе ХП меди свидетельствуют значения фото – ЭДС, полученные при анодной поляризации меди в растворе фосфорной кислоты и при добавлении окислителя – в окислительной среде фото–ЭДС заметно выше (рис. 13).
![]() | Рис. 13. Зависимость ЭДС фотоэлектрополяризации медного электрода от потенциала после обработки в растворах: 1 – 15 М H3PO4; 2 – 15 М H3PO4 + 3 M NH4NO3. |
Положительный знак фотоответа свидетельствует о формировании на поверхности полупроводниковой пленки с дырочной проводимостью. В таком поверхностном слое ионы меди способны перемещаться по катионным вакансиям, а электроны – по электронным дыркам (катионам более высокой степени окисления).
Для изучения свойств поверхностных слоев непосредственно в процессе обработки нами был использован метод электродного импеданса. При наложении потенциала, соответствующего области предельных токов растворения меди в фосфорной кислоте, имеет место линейная зависимость активной и реактивной составляющей импеданса от ω-1/2 (рис. 14), обусловленная уменьшением толщины диффузионного слоя с ростом скорости вращения электрода в соответствии с уравнением: = 1,61D1/31/6-1/2. Такого рода зависимости характерны для случая замедленной стадии отвода продуктов растворения от электрода в объем раствора (полирование за счет формирования солевой пленки). Поэтому увеличение скорости вращения электрода, способствующее уменьшению толщины резистивного слоя, приводит к снижению активного высокочастотного сопротивления.
В растворе, содержащем нитрат аммония, при вращении электрода активная и реактивная составляющие импеданса при высоких скоростях вращения перестают зависеть от числа оборотов дискового электрода. По-видимому, в этом случае имеет место изменение природы лимитирующей стадии: ограничения по отводу ионов меди снимаются, и преобладающее влияние приобретает подвод акцепторов, необходимых для растворения оксидного слоя.
![]() | ![]() |
Рис. 14. Зависимости активной (1) и реактивной (2) составляющих импеданса медного дискового электрода от скорости вращения в растворах: а – 15 М Н3РО4. Еа=0,72 В; б – 15 М H3PO4 + 3 M NH4NO3. f=5000 Гц, Т=298 К.
Величины составляющих импеданса при обработке меди в окислительной среде заметно выше, чем значения, полученные в растворе фосфорной кислоты. Это свидетельствует об усилении влияния оксидного слоя при обработке меди в растворе химического полирования.
Таким образом, несмотря на существенное различие в электрохимических свойствах титана и меди, причины, определяющие возможность достижения эффекта химического полирования, остаются прежними – замедленность стадии массопереноса в растворе и формирование на поверхности металла полупроводникового оксидного слоя.
Дополнительные возможности управления процессом дает совместное введение в состав раствора полирования двух окислителей, восстановление одного из которых сопровождается выделением газа и возникновением конвективных потоков, а продукты восстановления второго остаются в жидкой фазе. При этом скорость растворения металла несколько снижается, но увеличивается интенсивность сглаживания микрорельефа.
Используя комбинации кислородсодержащих окислителей и реагентов, восстановление которых протекает без участия ионов гидроксония, а изменения сводятся к перезаряду иона, можно целенаправленно влиять на величину рН приэлектродного слоя и формирование оксидных слоев на поверхности металла. Реакции перезаряда ионов протекают с низким электрохимическим перенапряжением, вследствие чего возрастает роль диффузионных ограничений.
Исходя из вышеизложенных положений, нами были разработаны малоагрессивные растворы для обработки меди и сплавов на ее основе, содержащие одновременно два окислителя. Преимущества от введения второго окислителя видны из данных, представленных в табл. 8.
Таблица 8.
Показатели обработки поверхности меди и латуни ЛС59 в растворах различного состава.
№ п.п. | Показатель | Металл | Состав раствора, г/л | |
H3PO4 -1400 KNO3 - 450 | H3PO4 -1400 NH4NO3 – 280 Ox2 - 10 | |||
1 | Шероховатость поверхности Ra, мкм | Медь | 0,362 | 0,228 |
Латунь | 0,375 | 0,304 | ||
2 | Отражательная способность поверхности, % | Медь | 59 | 81 |
Латунь | 78 | 94 | ||
3 | Удельный объем выделяющегося газа, см3/г | Медь | 230 | 46 |
Латунь | 235 | 49 | ||
4 | Температура раствора, оС | | 90 - 100 | 20 - 40 |
Предлагаемые растворы характеризуются невысокой скоростью съема металла (3 – 5 мкм/мин.), что облегчает управление процессом. Пониженная температура и скорость растворения металла дают возможность вести обработку деталей насыпью в установках барабанного типа. Их применение позволяет в 4 – 5 раз сократить количество вредных выбросов оксидов азота.
В разделе 5.2 рассмотрены вопросы подготовки поверхности титана перед электрохимическим серебрением. Для обеспечения прочного сцепления покрытия с титаном применяют сложные многостадийные схемы, включающие нанесение промежуточных подслоев никеля и меди. Однако при эксплуатации деталей в жестких климатических условиях при нарушении сплошности серебряного покрытия возникают гальванические пары (Ag-Cu, Ag-Ni), что приводит к коррозии и сокращению срока эксплуатации деталей. По этой причине целесообразно осаждать серебро непосредственно на титан. Для обеспечения надежного сцепления покрытия с основой, его сплошности и равномерности необходима высокая степень активности поверхности и ее сохранение в момент погружения деталей в электролит. Такие свойства поверхности титана обеспечивает гидридная обработка.
Установлено, что значения фото-ЭДС и комплексного сопротивления титанового электрода после различных способов обработки согласуются с данными по прочности сцепления серебра с титаном. Наиболее эффективное активирование поверхности обеспечивается при гидридной обработке в растворах HCl - 425 г/л или HCl - 230 г/л + H2SO4 - 600 г/л при температуре 500С. Для обеспечения надежного сцепления серебра осаждаемого из синеродисто-роданистого электролита, загрузку деталей в ванну следует производить под током.
В разделе 5.3 рассмотрены вопросы защиты поверхности серебра от потемнения. Установлено, что при взаимодействии серосодержащего органического пассиватора (диэтилдитиокарбамата натрия) с серебром на поверхности металла образуется хемосорбированный защитный слой. С помощью импедансных измерений показано, формирующаяся защитная пленка обладает повышенным электрическим сопротивлением. Установлено, что для количественной оценки состояния поверхности после пассивации можно использовать метод фрактальной геометрии.
В случаях, когда основной задачей пассивирующей обработки является сохранение декоративных свойств изделия, концентрация диэтилдитиокарбамата натрия не должна превышать 10 г/л, а содержание КОН – 2 г/л. По эффективности защиты такие растворы не уступают хромсодержащим и в то же время намного менее токсичны.