Разработка технологий изготовления порошковых магнитных материалов для электротехнических изделий
Вид материала | Автореферат |
СодержаниеПятая глава В шестой главе |
- Конспект Тема: Содержание и расчет калькуляционных статей расходов, 84.19kb.
- Разработка ресурсосберегающих технологий переплава стружечных отходов для изготовления, 324.1kb.
- Создание нового класса крепежных изделий (резьбовые соединения) за счет поверхностного, 27.37kb.
- Учебная программа курса конструирование, моделирование швейных изделий; Технология, 60.36kb.
- Зависит прежде всего от качества используемого материала, четкой проработки модели, 857.47kb.
- Приказ Минздрава России от 26. 03. 01 N 89 Огосударственной регистрации новых пищевых, 114.31kb.
- Бизнес-план изготовления кровельного покрытия и жестяных изделий, 563.97kb.
- Методические указания к курсовому проекту, 194.16kb.
- Конспект лекций по курсу "Экономический анализ", 83.5kb.
- Учебно-методическое пособие для специалистов по приготовлению мучных кондитерских изделий, 1556.12kb.
Пятая глава «Разработка технологических методов изготовления элементов магнитных систем, полученных МПМ» посвящена в основном дискретным режимам прессования магнитных систем и экспериментальному исследованию серии П-, Ш-, Г-, С-, Т-, Б- и Н-образных магнитных систем. На основе сравнительного испытания магнитомягких спеченных и шихтованных магнитных систем показана возможность замены листовой электротехнической стали на прессованный материал для изготовления магнитных систем электрических аппаратов следующих типов: РПУ-1, ПМЕ-221, РПУ-4, ПМА-2000, ПМЕ-111, ПМ-12, РПК-1. Проведенные исследования показали, что для получения аналогичных характеристик электрических аппаратов с магнитными системами из прессованного магнитного материала и листовой электротехнической стали необходимо для спеченной магнитной системы создавать напряженность магнитного поля в два раза меньше, и следовательно число ампер-витков должно быть заложено в два раза меньшей величины, что позволяет экономить обмоточную медь. Это объясняется тем, что магнитная проницаемость спеченной магнитной системы в средних полях выше, чем для листовой электротехнической стали.
На электромагнитах переменного тока проведено систематизированное исследование в зависимости от давления прессования следующих характеристик: магнитной индукции магнитопровода, кратности пускового тока катушки, коэффициента мощности, тяговой характеристики и времени срабатывания электромагнита. Показано, что с увеличением давления прессования величина магнитной индукции магнитопровода возрастает, кратность пускового тока увеличивается, коэффициент мощности снижается, тяговая характеристика повышается и время срабатывания уменьшается, что позволяет широко регулировать параметры электротехнических изделий.
Разработка новой технологии изготовления спеченных слоистых магнитопроводов показала, что данные магнитопроводы могут заменить магнитопроводы из листовой электротехнической стали. Это имеет особенно большое значение с точки зрения возможности упразднить трудоемкие операции по прокатке заготовок, резке листов, штамповке и изолированию листов, окончательной сборке и клепке, а также значительно уменьшить отходы и снизить стоимость изготовления магнитопроводов из спеченных материалов.
Разработаны матричные схемы прессования и расчета магнитных систем. Структурная матричная схема прессования универсальна, она применима как для призматической формы, так и для цилиндрической формы магнитопроводов. Важным достоинством структурных матричных схем прессования является возможность анализа общих свойств сложных конструкщий магнитных систем. Поэтому для облегчения расчета и анализа сложных конструкций магнитных систем необходимо производить расчеты с помощью компьютера, при этом достоинства матрично-топологических методов прессования проявляются в полной мере.
Начатая работа по исследованию дискретного способа прессования изделий позволит в будущем расширить функциональные возможности, выявить новые характеристики и раскрыть новые неизвестные свойства магнитных систем. Получены слоистые дискретные магнитопроводы с различными магнитными проницаемостями. Осуществляя монодискретный и полидискретный способы прессования магнитопроводов, получены электромагниты с постепенным сдвигом магнитных потоков по фазе. Для расчета и изготовления сложных магнитопроводов переменного тока могут быть применены матричные схемы прессования. Прессование слоев для магнитных систем переменного тока производилось в виде структурной матричной схемы следующего вида:
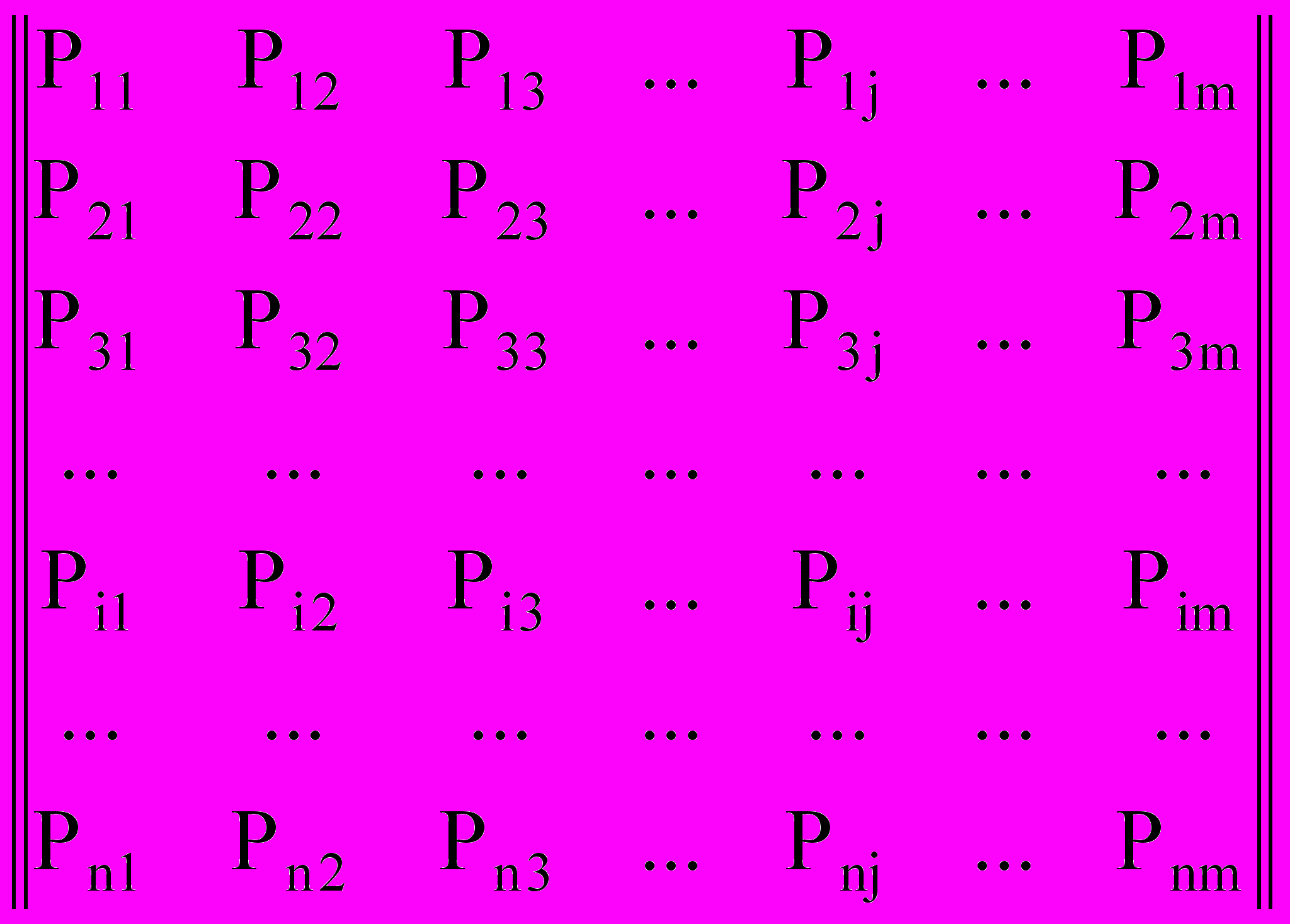
Компоненты структурной матричной формы схемы представляют собой слои из магнитомягких материалов для магнитопроводов. Общее число строк в структурной матричной схеме равно числу пакетов магнитопроводов. Число столбцов структурной матричной схемы равно числу слоев из магнитомягких материалов для магнитопроводов.
Простое слоистое прессование магнитопровода осуществляется при следующих коэффициентах структурной матричной схемы:
Коэффициенты строк:
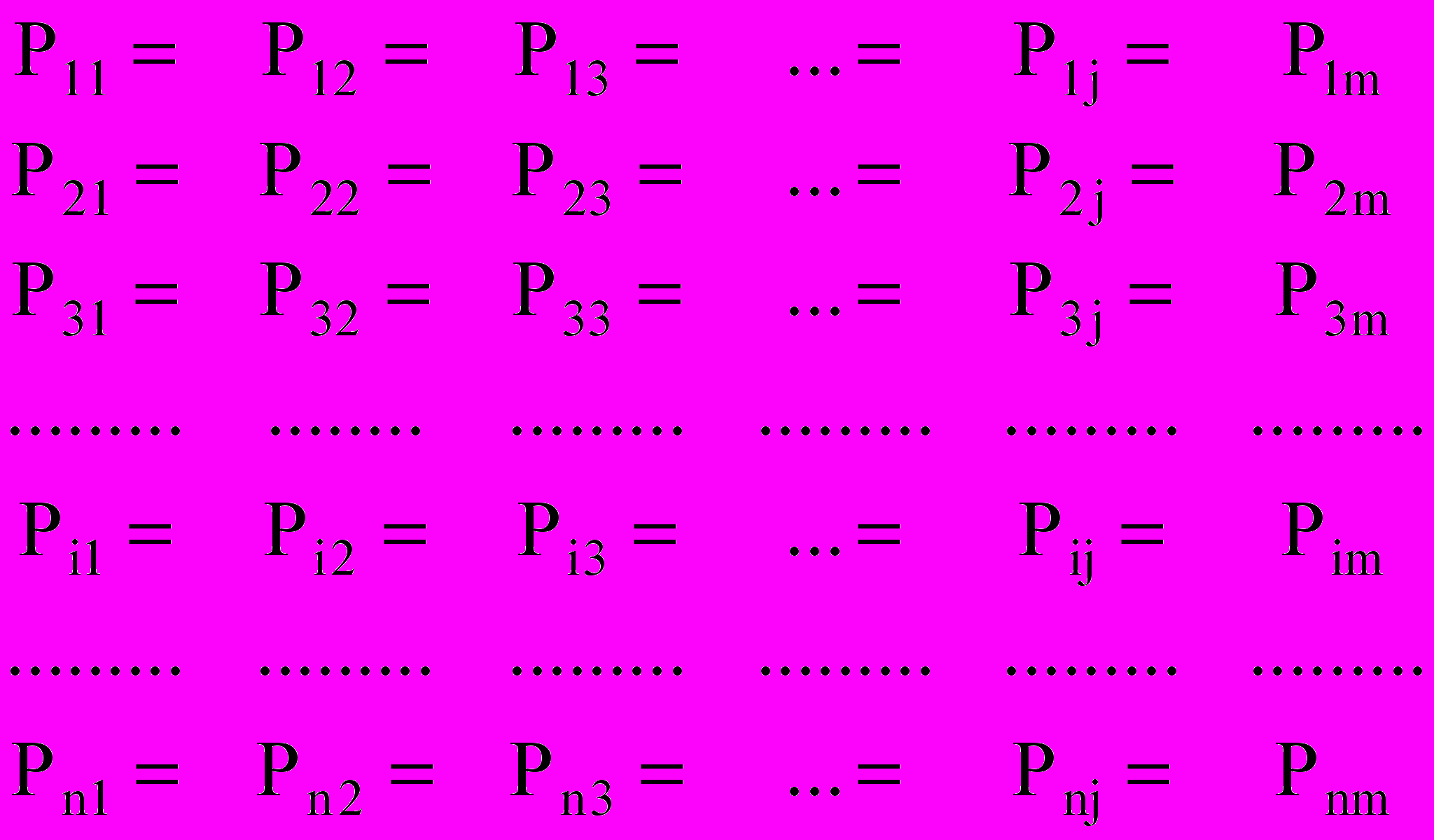

Коэффициенты столбцов:


При монодискретном прессовании магнитопроводы выполнялись в виде периодически прессованных пакетов, причем каждый слой, начиная с первого, прессовали с последовательным уменьшением усилия прессования. Таким образом, каждый последующий слой отличался от предыдущего на величину постоянного давления прессования. Давление прессования, соответствующее j-му дискретному слою, можно рассчитать по формуле:
Рij=P11P(m-1), (14)
где Рij – давление прессования j-го слоя;
Р11 – давление прессования 1-го слоя;
P – снижение давления.
Монодискретное прессование магнитопровода осуществляется при следующих коэффициентах матрицы:
Коэффициенты строк:
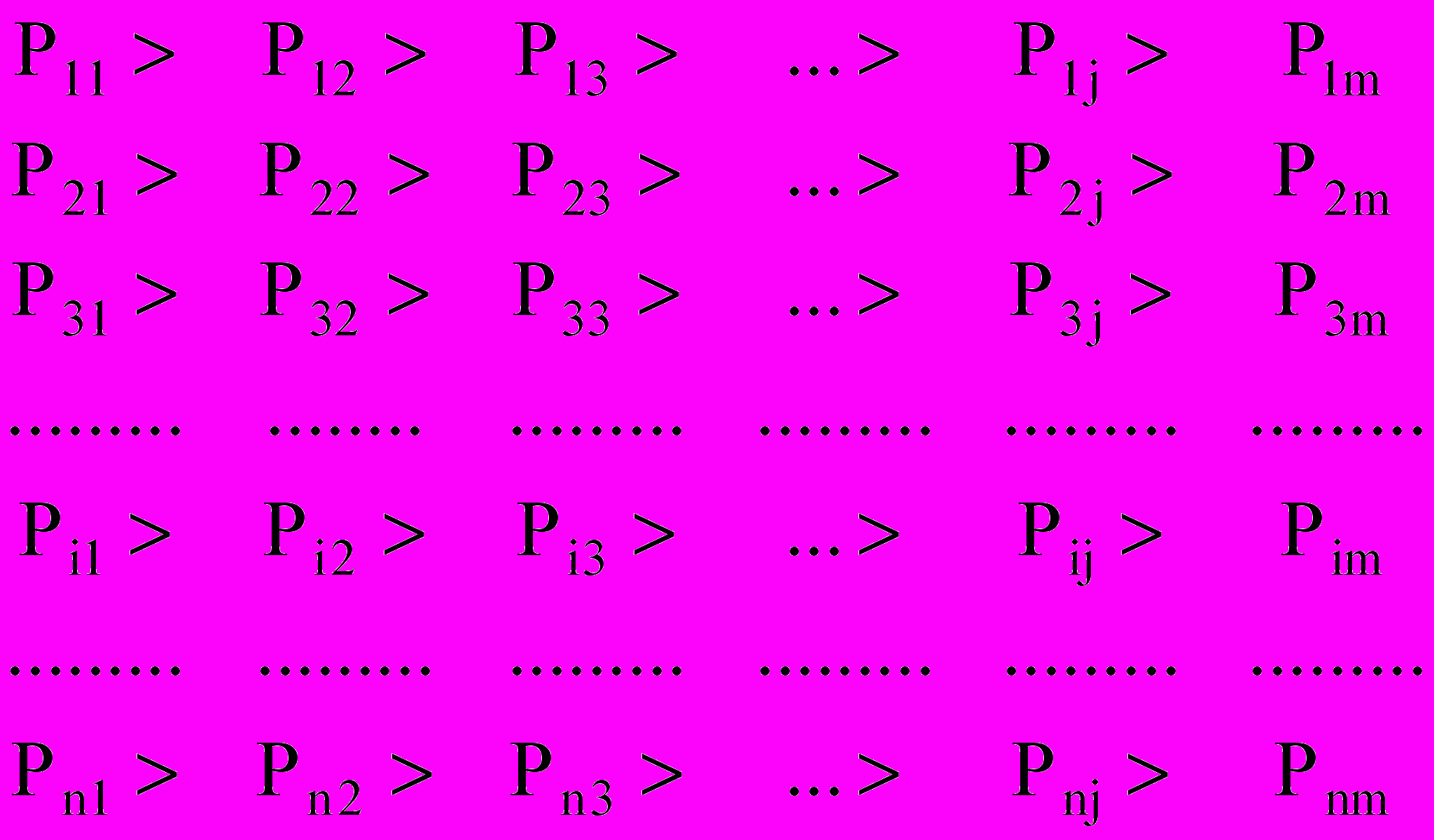

Коэффициенты столбцов:


Для более равномерного сдвига магнитных потоков прессование можно осуществлять полидискретным способом. Полидисретное прессование магнитопровода можно выполнять в соответствии со следующей формулой:
Рij=(P11+ei)P(m-1), (17)
где ei – величина смещения давления прессования, eiz;
z – множество чисел.
Полидискретное прессование осуществляется при следующих коэффициентах матрицы
Коэффициенты строк:
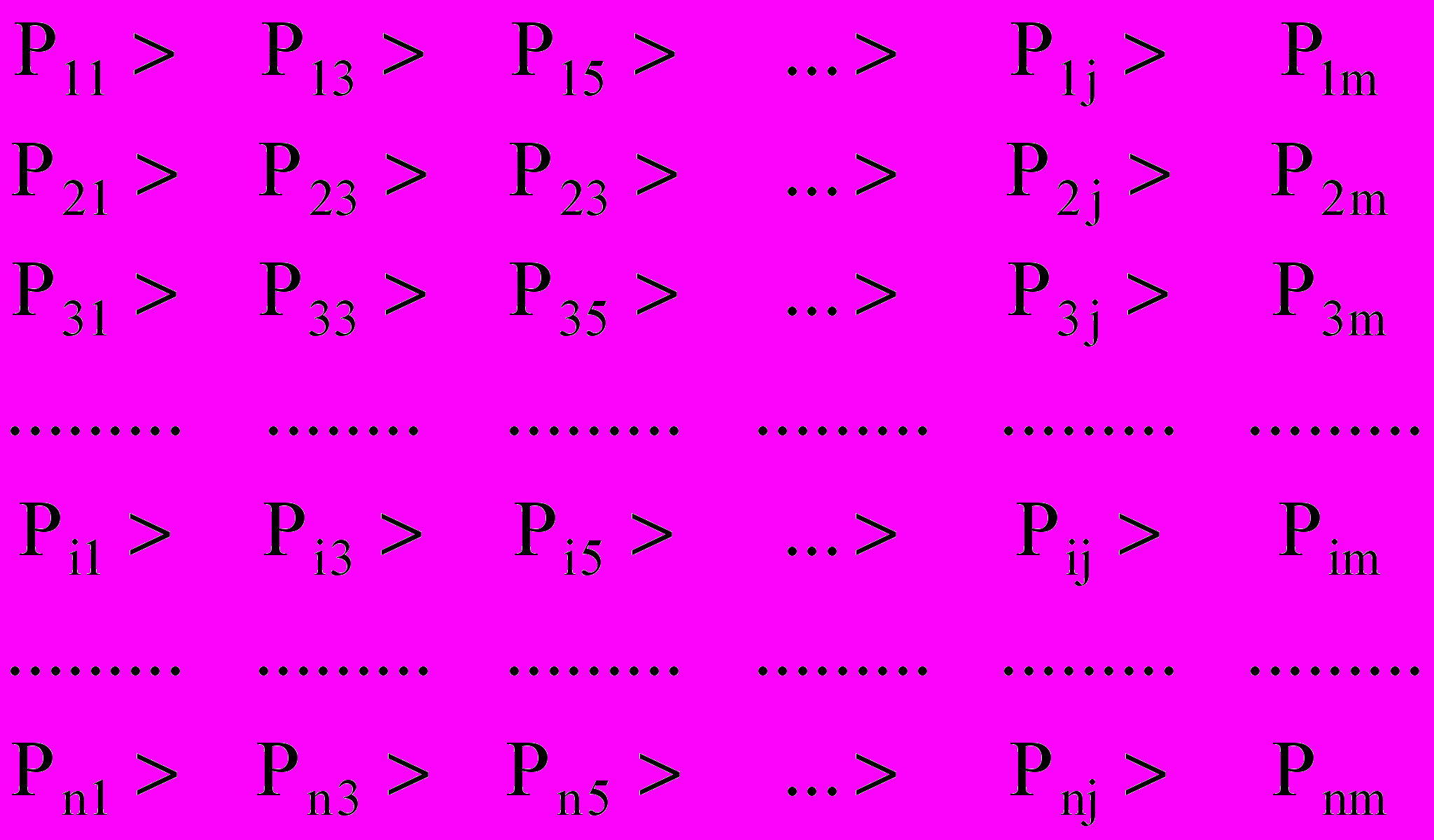

Коэффициенты столбцов:
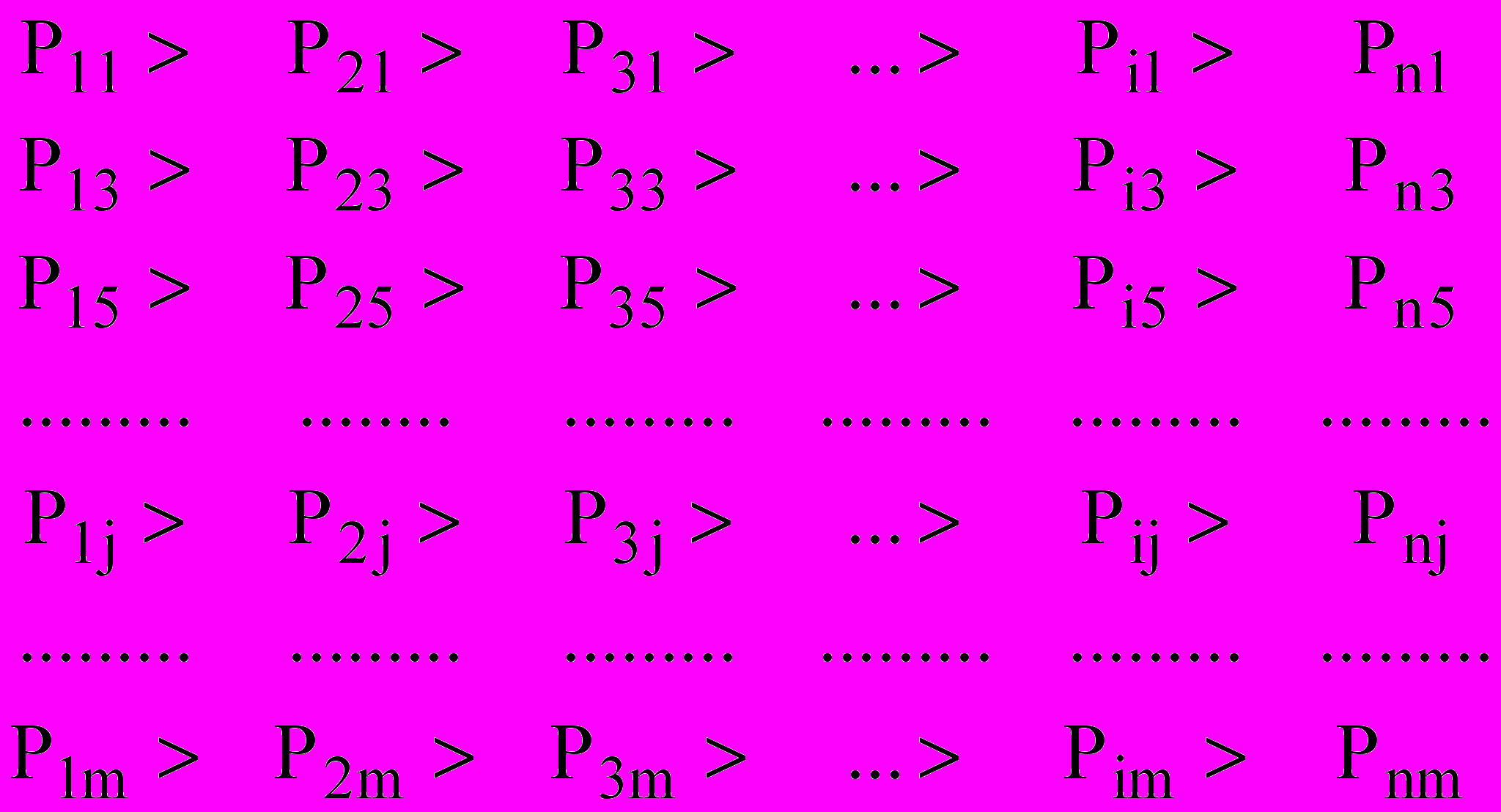

Слои, выполненные дискретным способом с большим давлением прессования, можно осуществить в соответствии со следующей формулой:
Рij=P11qm-1, (20)
где q – разность давления прессования.
Прессуя магнитопровод при переменном давлении, получим магнитопровод, имеющий неодинаковое контактное сопротивление между прессуемыми частицами, что ведет к различной магнитной проницаемости слоев. Составим матричную схему для структурной схемы магнитных проницаемостей слоистого магнитопровода:

С целью расширения функциональных возможностей магнитопровода разработана спеченная дискретная композиционная магнитная система, обладающая магнитомягкими и магнитотвердыми свойствами. Для этого магнитопровод был выполнен из слоев с чередованием слоев из магнитомягкого материала (МММ), в частности, железокремнистого материала и слоев из магнитотвердого материала (МТМ), преимущественно, SmCo5 при следующей периодической последовательности материалов и ингредиентов дискретного содержания кремния в слоях из железокремнистого материала: Fe; МТМ; FeSi (0,5± 0,03% Si); МТМ; FeSi (1,5± 0,05% Si) ; МТМ; FeSi (2,5± 0,06% Si); МТМ; FeSi (3,5±0,08% Si); МТМ ; FeSi (4,5± 0,1% Si); MTM; FeSi (5,5± 0,12% Si); МТМ; FeSi (6,5+0,15% Si).
Запишем спрессованные слои композиционного магнитопровода в виде структурной матричной схемы следующего вида:
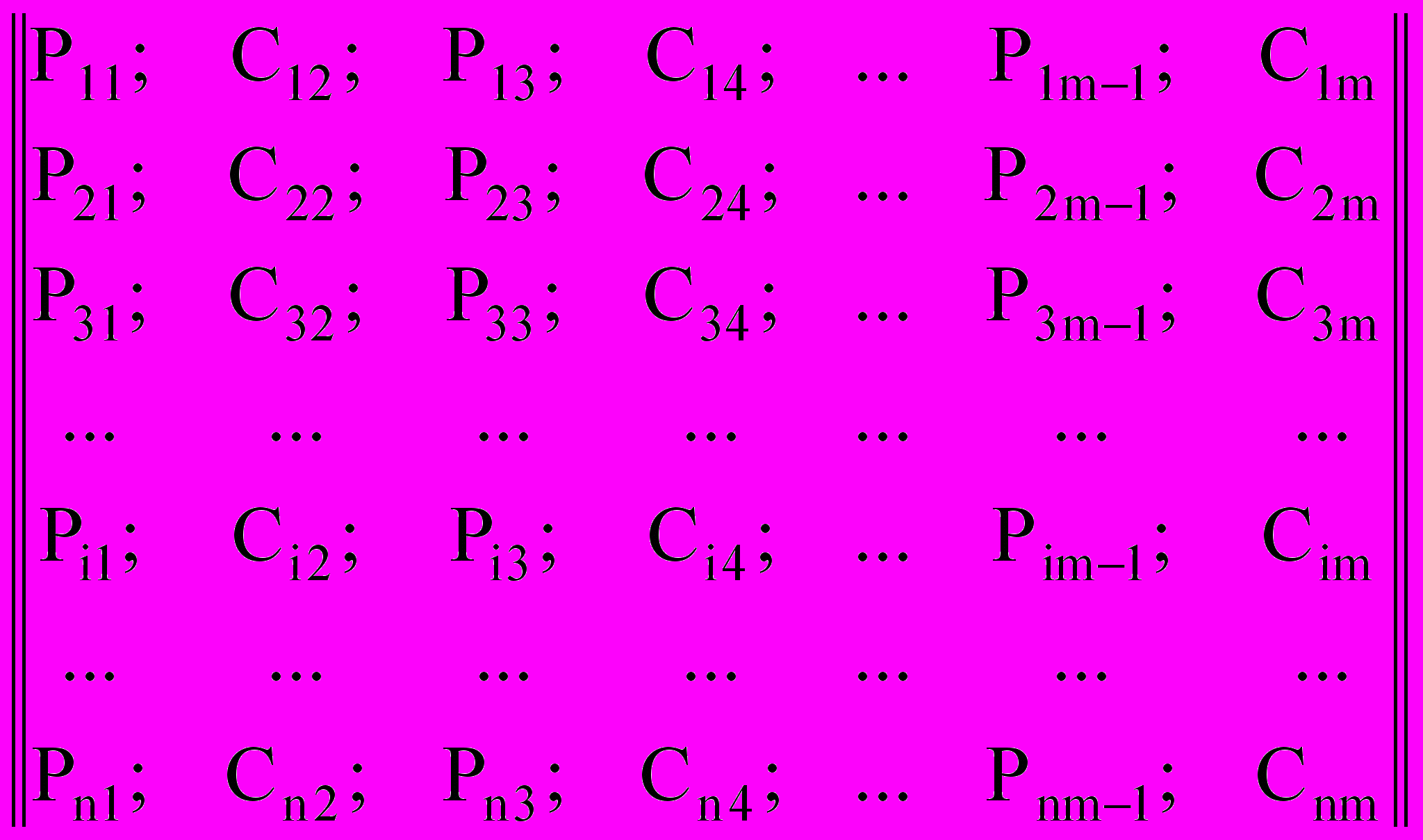
Компоненты матричной формы схемы прессования представляют собой слои композиционных материалов для магнитопроводов. Общее число строк в структурной матричной схеме равно числу пакетов магнитопровода. Число столбцов матричной схемы равно числу слоев из композионных материалов для магнитопроводов.
В реферируемой работе приводятся результаты исследования реле со спеченными магнитопроводами. Одна из задач проведенных исследований заключалась в проведении испытаний на механическую износостойкость и проверке реле на ресурсный срок службы. В результате проведенных испытаний установлено, что при 90°-ной разности углов направления обработки якоря и сердечника износ магнитной системы становится наименьшим, с увеличением частоты срабатывания магнитных систем интенсивность износа уменьшается.
Эффективность работы магнитных систем в основном зависит от применяемых материалов. С этой целью были исследованы различные магнитные системы, применяемые в реле, так как от магнитных свойств материалов зависят характеристики реле. Исследованию подвергнуты в основном магнитные системы реле передовых иностранных фирм. По характеристикам кривых намагничивания магнитных систем на переменном токе частотой 50 Гц в порядке снижения магнитной индукции насыщения исследованные типы реле расположились в следующей последовательности: 1. CA2-DN131 фирмы «Telemecanique Electric» (Франция); 2. PAK-10UR фирмы «Togami electric» (Япония); 3. SRC3631 фирмы «Fuji electric» (Япония); 4. DSL 6-44 фирмы «Metzenauer jung» (ФРГ); 5.РПУ-1 (Россия); 6. ЗТА69 фирмы «Siemens» (ФРГ); 7. GO-31 фирмы «Scverde» (США); 8.HSA-0 фирмы «Broun Bovery» (ФРГ); 9. MV-2 фирмы «Danfoss» (Дания); 10. UCO 5-10 фирмы «МТЕ» (Англия).
Самую высокую индукцию насыщения имеет магнитная система релеCA2-DN131 и самую низкую магнитную индукцию насыщения –магнитная система реле UCO 5-10/ Опытная слоистая магнитная система реле РПУ – 1, содержащая 6,5% Si в кремнистом железе, по магнитной индукции насыщения отстает от реле типов СА2-DN131, PAK-10UR, SRC3631, DSL 6-44, но превосходит магнитные системы реле 3ТА69, GO-31, HAS-0, MV-2, UCO 5-10.
При этом для намагничивания магнитной системы реле РПУ-1 требуется ампер-витков в два раза меньше, чем для намагничивания магнитной системы реле CA2-DN131 фирмы «Telemecanique Electric» (Франция) и в 6 раз меньше, чем для намагничивания магнитной системы реле UCO 5-10 фирмы «МТЕ» (Англия), что позволяет значительно экономить обмоточную медь.
В шестой главе «Применение элементов технологии изготовления магнитопроводов МПМ в современных электротехнических устройствах» рассмотрен анализ и обобщены материалы по проблеме оптимального проектирования магнитных систем, который свидетельствует еще о незаконченности проведенных исследований в этом направлении. Например, изучение традиционных электромагнитов промежуточных реле показало, что магнитный поток по высоте сердечника распределяется крайне неравномерно и по меньшей мере отличается в полтора раза в верхней и нижней его части.
Такое положение приводит к тому, что рассеяние магнитного потока
достигает больших величин.
В работе представлены разработанные оригинальные конструкции электромагнитов постоянного тока, причем магнитные системы изготовлялись с учетом технологических возможностей прессования магнитомягких материалов. Конструкция сердечника в электромагнитике постоянного тока, позволившая добиться постоянной магнитной индукции В=const по всей своей высоте, выполнена в виде усеченного параболоида. Геометрическая форма сердечника, выполненная в виде усеченного параболоида, сложна, поэтому для его упрощения можно применить форму усеченного конуса, образующая которого является линейной аппроксимацией параболы, максимально приближающая к ней.
Магнитная индукция в верхней части выбранного сердечника увеличена на 75%, а масса сердечника по сравнению с применяемым сердечником на серийных конструкциях электромагнитов уменьшена на 34%. Для распространенных электромагнитов постоянного тока с внешним поворотным якорем клапанного типа разработана новая конструкция управляющей катушки, позволившая сохранить равномерную коллимацию магнитного потока по высоте сердечника и одновременно снизить массу обмоточной меди катушки по сравнению с применяемой катушкой на серийных конструкциях электромагнитов на 16%, уменьшить потребляемую электрическую энергию электромагнитом на 18%. Такая конструкция сердечника и катушки позволяет уменьшить средний диаметр обмотки, что одновременно приводит к уменьшению сопротивления среднего витка катушки, к увеличению добротности катушки, к снижению потребляемой энергии, к возрастанию относительной магнитной проницаемости, к уменьшению расхода обмоточной меди для катушки, к уменьшению расхода материала для сердечника, к повышению индуктивности электромагнита, что можно описать следующей системой уравнений:
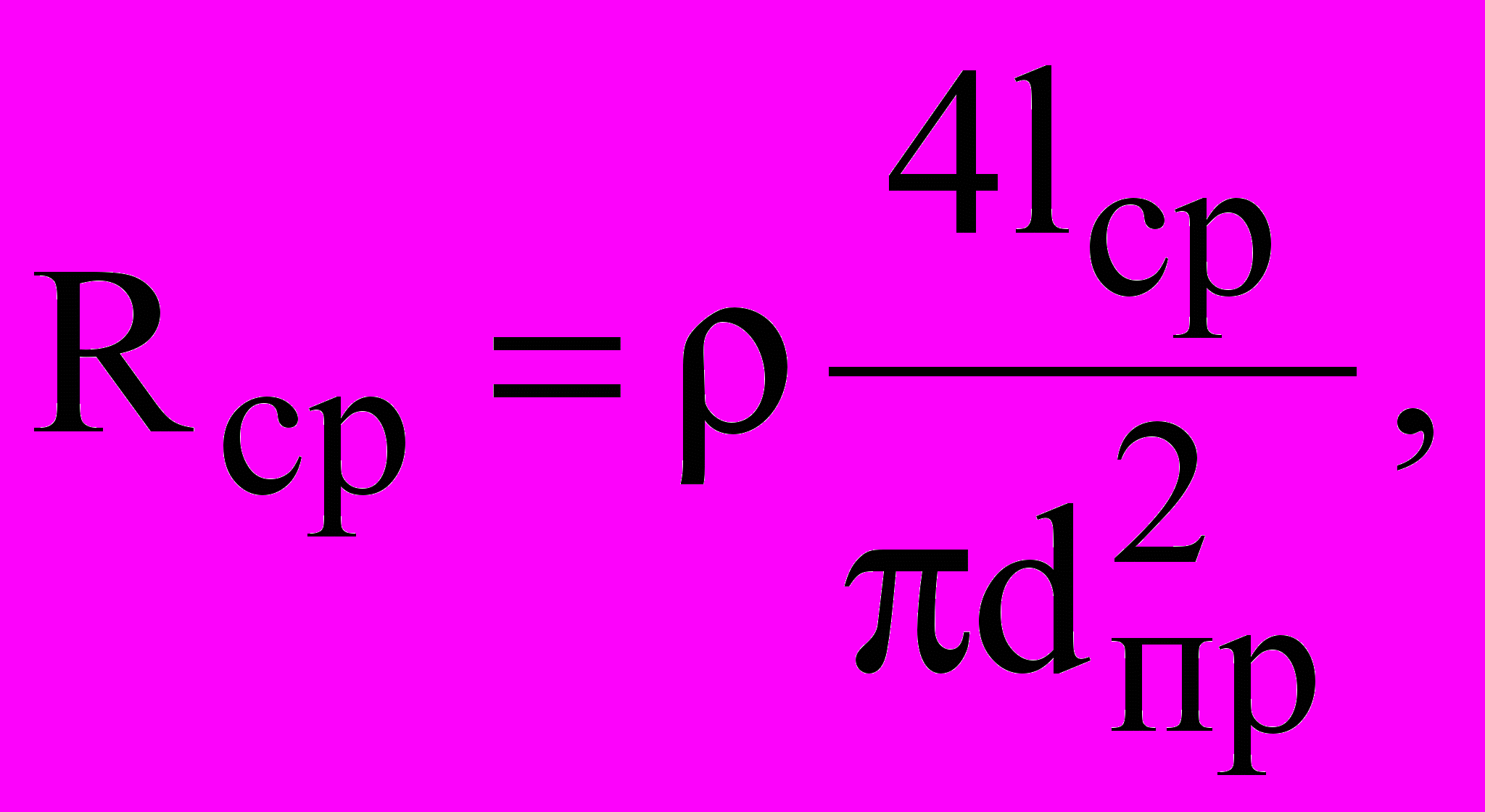
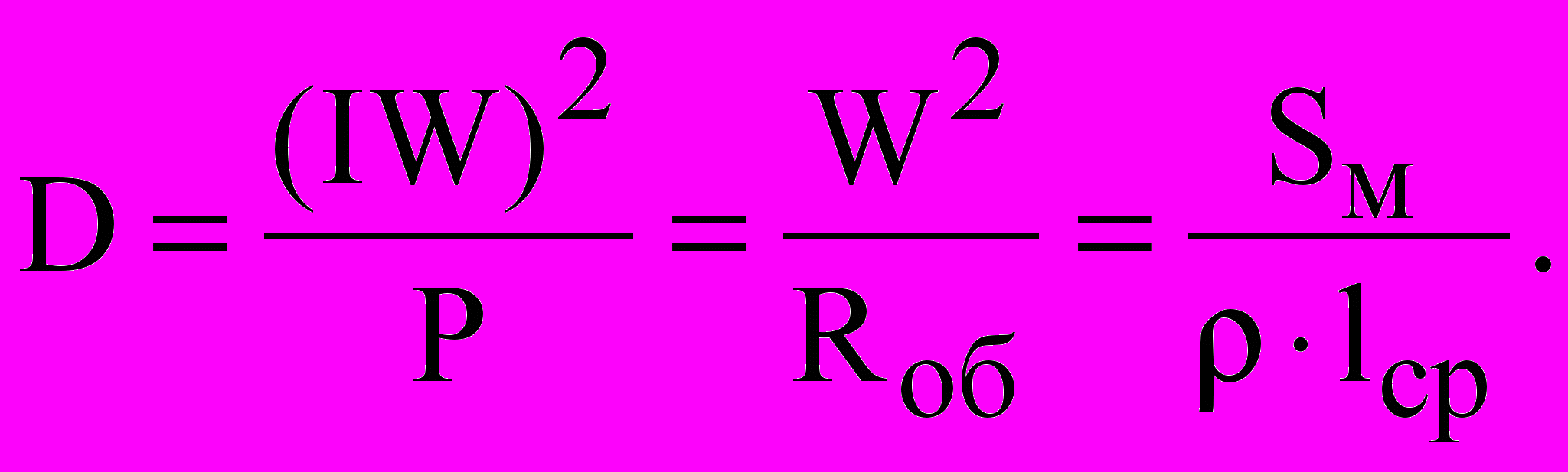
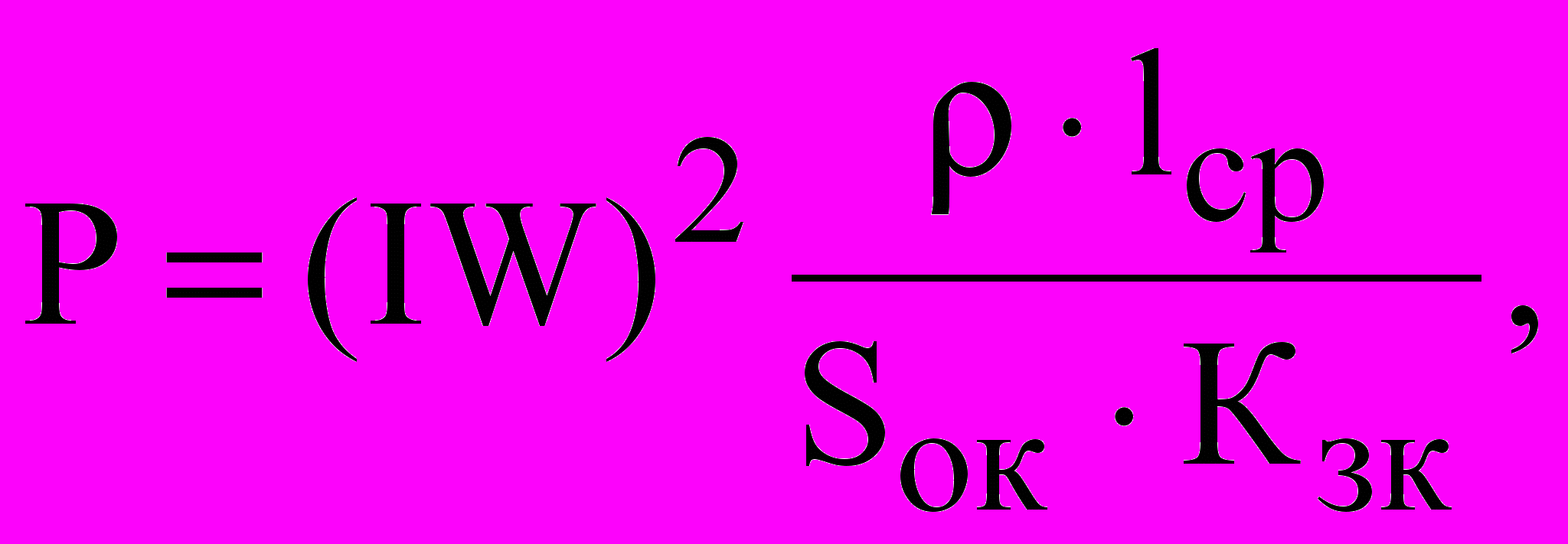
m=В/m0Н. (26)
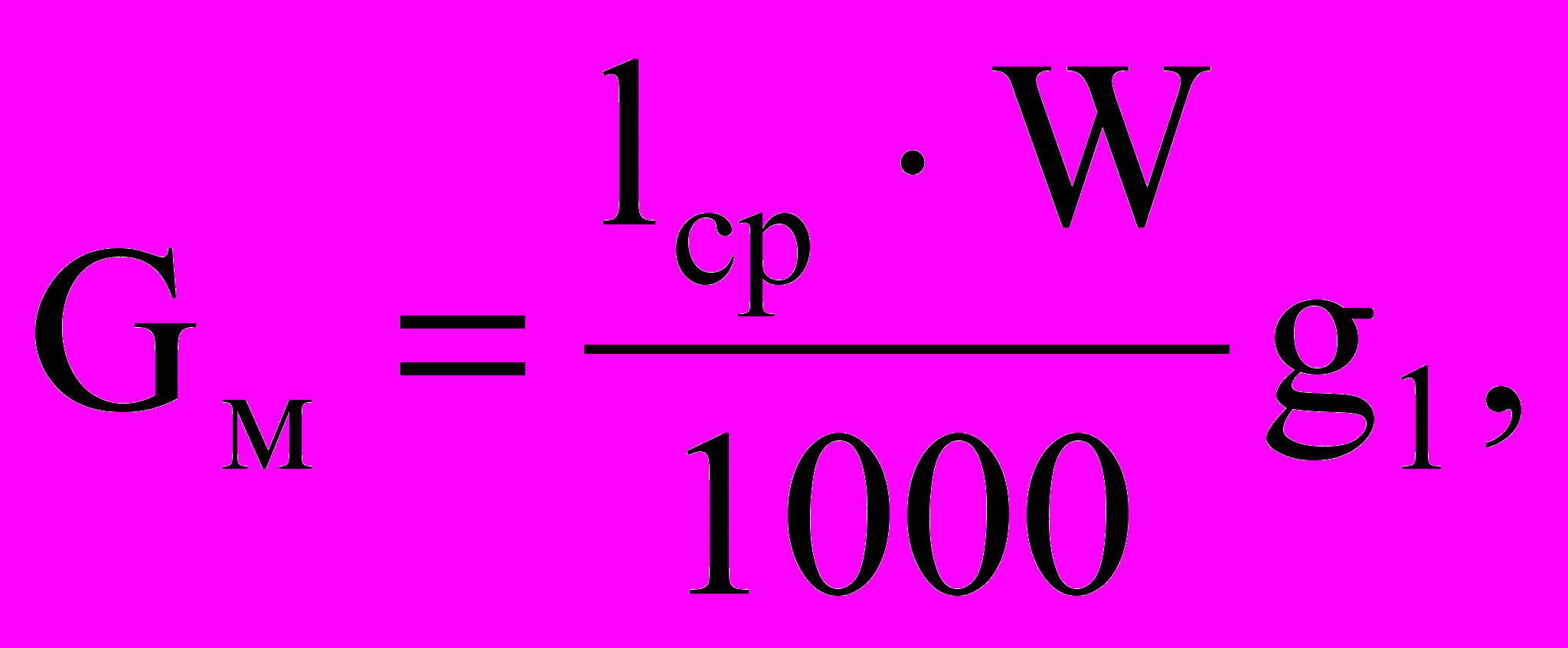
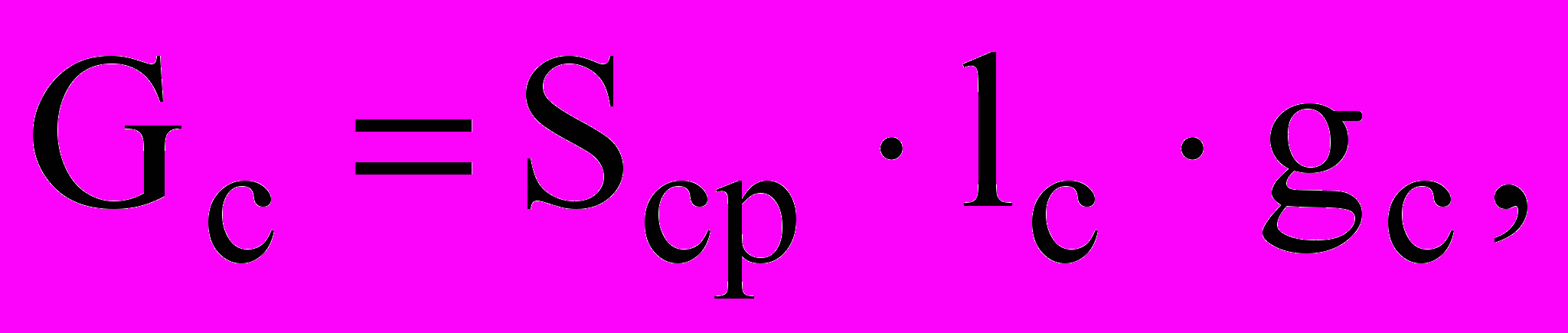
L=mm0W2p
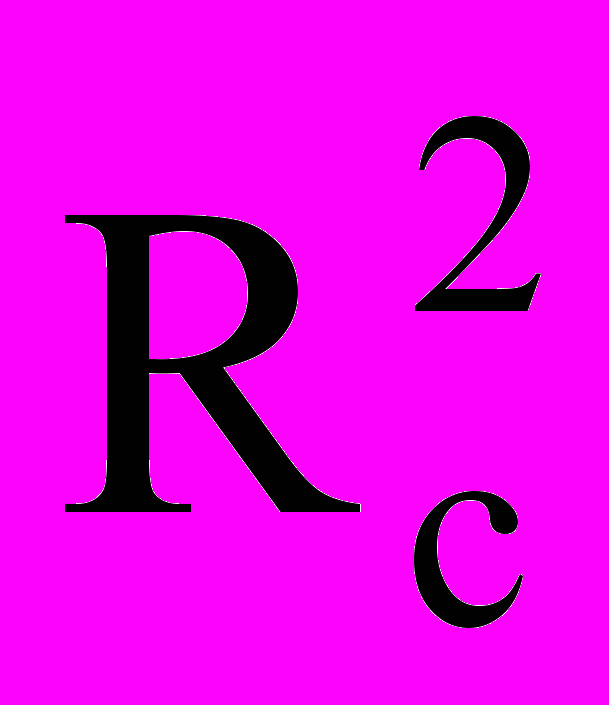
где Rср – сопротивление среднего витка катушки;
– удельное сопротивление материала провода;
dпр – диаметр намоточного провода;
D – добротность катушки;
AW– намагничивающая сила катушки;
Rоб –сопротивление обмотки;
Sм – суммарное сечение проводников обмотки;
Р – мощность катушки;
Soк – площадь окна обмотки;
Кз – коэффициент заполнения обмотки;
– относительная магнитная проницаемость;
0 – абсолютная магнитная проницаемость;
Н – напряженность магнитного поля;
Gм – масса обмоточной меди;
g м– удельный вес провода на единицу длины;
Gс – масса спеченного порошкового материала сердечника;
Sср – среднее сечение сердечника;
gс- удельный вес спеченного порошкового материала сердечника на единицу объема;
lс – длина сердечника;
L – индуктивность.
При постепенном уменьшении угла наклона образующей сердечника к его основанию магнитный поток в воздушном зазоре вначале увеличивается, затем при коэффициенте отношения диаметров сердечника, равного 0,84, магнитный поток становится максимальным, при дальнейшем уменьшении угла наклона образующей сердечника магнитный поток уменьшается, что вызвано постепенным увеличением насыщения сердечника. Эти исследования показывают, что, изменяя угол наклона образующей сердечника к его основанию, можно оперативно видоизменять тяговую характеристику электромагнита. На рисунке 3 для сравнения показана кривая 9, соответствующая характеристике электромагнита с цилиндрическим сердечником. Различное отклонение кривых 1,2, 3, 4, 5 и 6 вниз от кривой 9 в конце хода якоря связано с влиянием различной степени насыщения усеченного конического сердечника. Хотя в начале хода якоря тяговые характеристики электромагнитов 5, 6, 7 и 3, магнитные системы которых намагничены до насыщения, проходят выше кривой 9.
Разработана новая эффективная конструкция электромагнита переменного тока. Ш-образные магнитные системы были изготовлены таким образом, что позволили устанавливать магнитные шунты без изменения габаритов магнитных систем. Применение магнитного шунта из спрессованного магнитомягкого материала привело к улучшению тяговой характеристики электромагнита переменного тока.
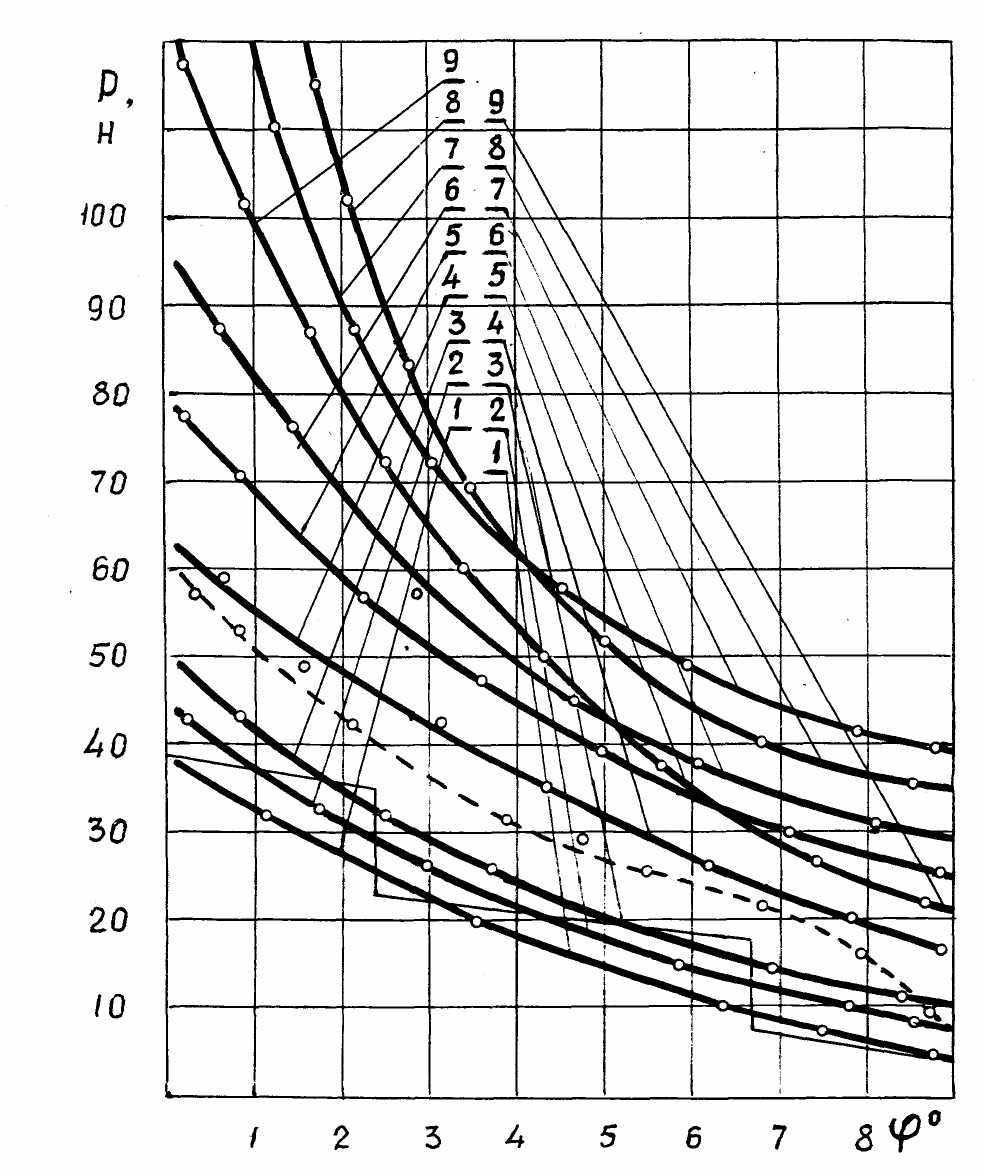
Рис..3. Статические тяговые характеристики электромагнита с внешним поворотным якорем клапанного типа
1 – сердечник Кд =0,44; 2 – сердечник Кд =0,48;
3 – сердечник Кд =0,52; 4 – сердечник Кд =0,6;
5 – сердечник Кд =0,68; 6 – сердечник Кд =0,76;
7 – сердечник Кд =0,84; 8 – сердечник Кд =0,92;
9 – сердечник Кд =1,0
Замена традиционной листовой электротехнической стали на спеченный магнитный материал из порошкового кремнистого железа в асинхронных двигателях переменного тока является важной проблемой современного электромашиностроения.
Разработана новая конструкция синхронного двигателя на основе инновационной технологии, не имеющей аналогов в электромашиностроении. Технический результат достигается тем, что указанная технология дозирования состоит в одновременной подаче в пресс-форму по винтовой линии магнитомягкого материала, содержащего железокремнистый материал с дискретно увеличивающимся ингредиентом кремния, и магнитотвердого материала, содержащего редкоземельный материал самарий с кобальтом, с чередованием слоев по длине ротора в следующей периодической последовательности:
Fe; SmCo5; Fe-Si(l,5 ± 0,05 % Si); SmCo5;
Fe-Si(3,0 ± 0,05 % Si); SmCo5; Fe-Si(4,5 ± 0,1 % Si);
SmCo3; Fe-Si(6.0 ± 0,15 % Si).
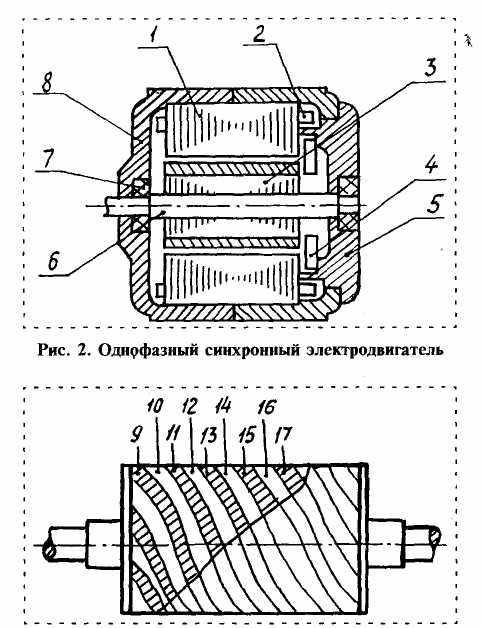
Рис. 4. Однофазный синхронный двигатель
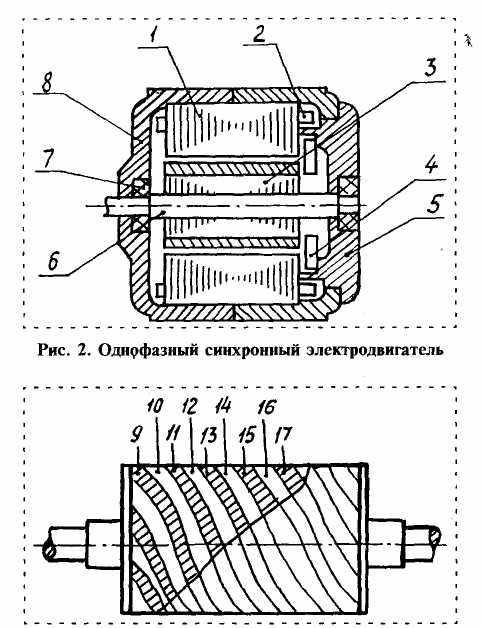
Рис. 5. Ротор однофазного синхронного двигателя
Однофазный синхронный двигатель (рис. 4) содержит явнополюсный статор 1 с обмотками возбуждения 2, короткозамкнутый ротор 3, дополнительный магнитопровод 4, который находится внутри ступицы 5, выполненной путем заливки из немагнитного материала, а также вал 6, подшипники 7 и подшипниковые щиты 8. Ротор состоит из многозаходных (в частности, девятизаходных) винтовых композиционных слоев (рис. 5).
Слои 9, 10, 11, 12, 13, 14, 15, 16 к 17 расположены с чередованием магнитомягкого материала с магнитотвердым материалом. Слой 9 выполнен из железного порошка, а слои 11, 13, 15 и 17 выполнены из порошка кремнистого железа, причем с различным содержанием кремния. Слой 11 содержит 1,5 + 0,05 % Si, слой 13 содержит 3,0 ± 0,05 % Si, слой 15 содержит 4,5 ± 0,1 % Si, а слой 17 – 6,0 +0,15 % Si.
Сравнительное исследование синхронного двигателя показало, что использование предлагаемого синхронного двигателя по сравнению с традиционным синхронным двигателем позволяет уменьшить затраты стали на 33 %, повышает КПД на 14 %, снизить потребление электрической энергии на 17 %, снизить ток холостого хода на 24 %, повысить cos на 11 %, и увеличить вращающий момент на 13 %., что в целом позволит улучшить его энерго- и ресурсосберегающие показатели.
Наряду с исследованием магнитных систем, работающих в динамическом режиме, проводились исследования магнитных систем, работающих в статическом режиме. К магнитным системам, работающим в статическом режиме, относится трансформатор напряжения, имеющий самое большое распространение в электротехнике. В отличие от электрических машин трансформатор не имеет движущихся частей, поэтому он не имеет и механических потерь при работе.
Были изготовлены трансформаторы следующих конструктивных исполнений: стержневые, броневые, кольцевые. Исследование магнитных свойств производилось на трансформаторах со стержневыми сердечниками следующих размеров: общая ширина составляла 8010-3 м, высота 12010-3 м,; ширина каждого керна 25 10-3 м. Все сердечники были выполнены одинаковой толщины 4010-3 м, имели 80 слоев толщиной 0,510-3 м.
После проведения опыта холостого хода ставили трансформатор под
нагрузку. Различная нагрузка устанавливалась плавным перемещением движка реостата. Затем проводили опыт короткого замыкания. Для этого вначале снимали нагрузку с трансформатора, после чего закорачивали вторичную обмотку трансформатора. Далее плавно увеличивали ЛАТРом напряжение на первичной обмотке до тех пор, пока ток на вторичной стороне не становился равным номинальному.
Исследования показали, что трансформаторы, изготовленные по методу порошковой металлургии, обладают рядом преимуществ по сравнению с трансформаторами, изготовленными по базовой технологии: уменьшена, масса магнитомягкого материала на 21,8%, снижен расход обмоточной меди на 24%, снижены удельные магнитные потери в два раза и cos увеличен на 23 %.
На основе критического технологического процесса порошковой металлургии создан индукторный генератор. На примере традиционного серийного генератора Г-700 показано, что использование предлагаемого индукторного генератора в номинальных режимах позволяет уменьшить падение напряжения в 3,4 раза, снизить ток возбуждения в 1,58 раза и повысить нагрузочный ток на 16 %.
Предложена инновационная энергосберегающая технология изготовления асинхронного двигателя на основе порошковых материалов, которая позволила превысить уровень физико-механических свойств аналогичного двигателя УАД-54, изготовленного по методу традиционного металлургического процесса. При штамповке идет в металлолом в виде отходов листовая электротехническая сталь, которая удаляется при формировании внешних контуров статора и ротора асинхронного двигателя. Реально норма расхода листовой электротехнической стали составляет 0,34 кг, а норма расхода порошковой массы – 0,19 кг, т.е. отход металла в металлолом составляет 44 %.
Использование предлагаемого асинхронного двигателя по сравнению с традиционным асинхронным двигателем позволяет снизить потребление электрической энергии, поднять КПД, снизить ток ХХ, повысить cos и увеличить вращающий момент, что в целом дает возможность улучшить его энерго- и ресурсосберегающие показатели.
В электротехнической промышленности имеется большая группа сложных изделий, изготовление которых связано со значительными техническими трудностями и высокой трудоемкостью. Такая проблема существует при изготовлении магнитных систем для однофазного индукционного счетчика электрической энергии, точность и надежность работы которого зависит от технологии изготовления деталей.
Исследование индукционных счетчиков производилось на магнитных системах Ш-, Б-, Н-, С-, П- и Т-образных форм. Затем для испытания и эксплуатации были изготовлены магнитные системы Б-, Ш- и П-образных форм, как наиболее конструктивные и технологичные системы.
В магнитных системах, изготовленных методом порошковой металлургии, создается магнитный поток большей величины, образуются малые потери и обмотки имеют меньшее потребление энергии по сравнению с аналогичными магнитными системами. Исследования показали, что чем меньше потребление знергии и ниже потери имеет индукционный счетчик, тем выше его точность и, следовательно, ниже его погрешность. Погрешность индукционного счетчика, детали которого изготовлены методом порошковой металлургии, для номинальной нагрузки 5А составляет 0,03 %, что примерно на 1,8 % меньше погрешности индукционного счетчика, изготовленного по базовой технологии.
Изучение электромагнита с внешним поворотным якорем клапанного типа с цилиндрическим сердечником показало, что такой электромагнит имеет следующие недостатки: малая величина рабочего магнитного потока и большая величина магнитного потока рассеяния, высокая температура нагрева сердечника и катушки, увеличенный расход электротехнической стали и обмоточной меди, низкая механическая износостойкость и увеличенные габариты электромагнита, высокая индуктивность и большое время срабатывания электромагнита. Для устранения этих недостатков была разработана конструкция электромагнита с внешним поворотным якорем клапанного типа с полым сердечником, не имеющая аналогов в электротехнической промышленности.