Хранилищ газа и нефти
Вид материала | Методические указания |
СодержаниеМетодические указания Методические указания Методические указания Вопросы для самоконтроля |
- Правила создания и эксплуатации подземных хранилищ газа в пористых пластах*1 пб 08-621-03, 484.04kb.
- Разработка технологии и методов регулирования хранения попутного газа в пластах-коллекторах, 402.61kb.
- Правила создания и эксплуатации подземных хранилищ газа в пористых пластах I. Область, 575.4kb.
- Правила создания и эксплуатации подземных хранилищ газа в пористых пластах Настоящим, 537.31kb.
- Положение о научно-образовательном центре «Нефтегазовое дело», 89.57kb.
- История кафедры геологии нефти и газа, 289.6kb.
- Цифровые инженерно-геологические картографические модели планирования подземных хранилищ, 237.94kb.
- Рабочая программа учебной дисциплины ен. Р. 02 Математическое моделирование процессов, 353.5kb.
- Геохимические методы поисков месторождений нефти и газа содержание учебной дисциплины, 74.47kb.
- «Об административной ответственности за правонарушения в сфере использования нефти, 9.48kb.
Студент д о л ж е н:
знать: способы ремонта подводных переходов и их технологию,
v м е т ь: производить расчет несущей способности льда
Способы ремонта подводных переходов, основные проблемы, обоснование применяемого способа. Плавсредства, оборудование и механизмы для выполнения берегоукрепителъных, кессонных и других работ. Расчет несущей способности и льда и способы увеличения этой способности. Размыв трубопровода, дефектация, сварочные и изоляционные работы. Контроль качества ремонтных pa6oт
Методические указания
Одновременно с организацией сбора разлившейся нефти должно быть проведено водолазное обследование подводного перехода для уточнения места и характера повреждения, после чего руководитель работ определяет способ ремонта.
Основными видами аварийных дефектов на ППМН являются свищи, трещины в сварных швах, разрывы и пробоины. В зависимости от характера повреждения восстановление несущей способности трубопровода в русловой части может производиться: прокладкой новой нитки подводного перехода; ремонтом с применением кессоннов, полукессонов (рис. 3).
Отметим особенности второго способа. Ремонт с применением кессонов и полукессонов проводится на глубине до 30 м, для обеспечения их функциональности применяется комплекс спецоборудования (плавсредства грузоподъемностью 120 т и более; кран для опускания и монтажа кессона; компрессорная установка; дизель-электростанции мощностью 20 кВт и более; насосное оборудование для откачки воды, средства радиосвязи и др.).
Перед установкой кессона удаляется грунт с аварийного участка и вокруг него разрабатывается котлован необходимых размеров.
С трубопровода удаляется футеровка и изоляция на длине, равной длине кессона плюс 500 мм с каждой стороны.
Для монтажа кессона гидромониторами разрабатывается грунт, обе половины кессона и шахта установливаются на трубе и герметизируются. Воду из кессона откачивают погружным насосом, затем монтируют дренажный насос и системы жизнеобеспечения.
Выбор метода ремонта зависит от характера повреждения и выполняется способами, применяемыми для ремонта подземных трубопроводов. Работы по устранению дефекта ничем не отличаются от подобной наземной операции.
Через шахту (обычно изготовленную из трубы диаметром 1000 мм) в камеру подаются части ремонтной муфты. После установки муфты проводится контроль сварных швов. В качестве защитного слоя используются материалы на основе армированных изоляционных материалов. Изоляционное покрытие обычно наносится в кессоне, что позволяет проконтролировать его качество.
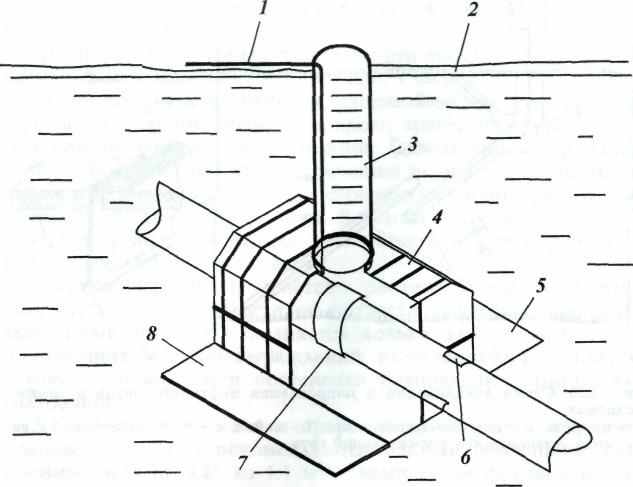
Рис.3. Схема расположения глубинного кессона при ремонте дефекта на подводном переходе магистрального нефтепровода в зимних условиях:
1 - система жизнеобеспечения; 2 - лед; 3 - шахта; 4 - камера; 5, 8 - балла-стировочная площадка (засыпается грунтом); 6 - уплотнительная обойма; 7 -ремонтная муфта
Вопросы для самоконтроля
- Способы ремонта подводных переходов
- Оборудование и механизмы для выполнения ремонтных работ с использованием кессона
Тема 3.7. Техническое обслуживание и ремонт линейной арматуры
Студент должен:
знать: неисправности линейной арматуры и способы их устранения;
уметь: ликвидировать неисправности линейной арматуры и производить ее ремонт.
Основные неисправности линейной арматуры, причины их возникновения. Техническое обслуживание и ремонт линейной арматуры.
Методические указания
Техническое обслуживание запорной арматуры проводится не менее 1 раза в месяц и включает: внешний осмотр запорной арматуры для выявления утечек нефти, утечек масла через неплотности редуктора, нарушений герметичности кабеля и электродвигателя; проверку наличия смазки в редукторе и ванне конечных выключателей, отсутствия мелких неисправностей и поломок, наличия колпаков для защиты штока задвижки от пыли, грязи, осадков, наличия четко обозначенных знаков и надписей, указателей положения (штока); устранение всех выявленных при внешнем осмотре недостатков; устранение при необходимости с наружных поверхностей задвижек, обратных клапанов, с площадок самообслуживания грязи, ржавчины, льда, воды, подтеков масла.
Подтяжка сальников проводится по необходимости, но не реже 2 раз в год.
Протяжка всех фланцевых соединений проводится не реже 2 раз в год при подготовке к работе в осенне-зимний и весенне-летний сезоны.
Вопросы для самоконтроля
- Виды работ, выполняемых при техническом обслуживании запорной арматуры
- Периодичность проведения технического обслуживания запорной арматуры
Раздел 4. ТЕХНИЧЕСКОЕ ОБСЛУЖИВАНИЕ II РЕМОНТ ХРАНИЛИЩ ГАЗА И НЕФТИ
Тема 4.1. Техническое обслуживание и ремонт резервуаров
Студент должен:
знать: причины выхода из строя резервуаров и методы их ремонта;
уметь: производить расчеты протекторной зашиты днища резервуара и средств пожаротушения.
Организация технического обслуживания и ремонта резервуаров. Причины нарушения прочности резервуаров. Подготовка резервуаров к ремонту, вывод из эксплуатации, проветривание, пропарка, снятие пробы воздуха, очистка от парафина и механических осадков.
Методы ремонта основания, днища, корпуса и крыши резервуара.
Контроль качества ремонтных работ.
Методические указания
Осмотр и техническое обслуживание резервуаров должны проводиться в соответствии с картами технического обслуживания.
При осмотре РВС необходимо обратить внимание на следующее: утечки нефти; образование трещин по сварным швам и основному металлу; появление хлопунов и вмятин; неравномерную осадку резервуара.
В резервуарах со стационарной крышей (без понтона) необходимо контролировать избыточное давление, его соответствие установленному.
Визуальный осмотр поверхности понтона требуется проводить в верхнем его положении через световой люк. При осмотре необходимо проверить наличие или отсутствие отпотин или нефти на ковре понтона и в открытых коробах, состояние затвора.
Плавающую крышу следует осматривать с верхней кольцевой площадки. При осмотре необходимо проверить положение плавающей крыши, ее горизонтальность, отсутствие нефти в центральной части плавающей крыши, зимой — наличие снега на плавающей крыше, состояние защитных щитков кольцевого уплотняющего затвора, положение задвижки системы водоспуска.
При техническом обслуживании резервуара с плавающей крышей следует проверить состояние катучей лестницы, погружение плавающей крыши, отсутствие нефти в коробах и в отсеках между ними, техническое состояние затвора и его элементов, ливнеприемника.
На железобетонных резервуарах (ЖБР) с водонаполненным покрытием в условиях положительной температуры уровень водяного экрана должен постоянно поддерживаться на проектной отметке. На ЖБР с земляной насыпью на кровле поверхность должна быть спланирована.
При появлении нефти в дренажном и шахтном колодцах, камере управления, а также при выходе ее на поверхность обсыпки резервуара или территорию резервуарного парка резервуар должен быть опорожнен для выявления и устранения имеющихся неисправностей.
Текущий ремонт проводится в плановом порядке без очистки резервуара по заранее разработанному графику.
При текущем ремонте РВС выполняются следующие работы: ремонт кровли; верхних поясов стенки; ремонт сифонных кранов; набивка сальников задвижек; ремонт отмостки; ремонт заземления; ремонт прочего оборудования, расположенного с внешней стороны резервуара, который может быть выполнен без вывода резервуара из эксплуатации.
При текущем ремонте ЖБР выполняются следующие виды работ: ремонт кровли резервуара, а также защита бетона путем пропитки его или покраски различными составами; набивка сальников задвижек; ремонт заземления; замена кассет на огневых предохранителях.
Вопросы для самоконтроля
- Организация технического обслуживания резервуаров
- Техническое обслуживание ж/б резервуаров
- Техническое обслуживание резервуаров с плавающей крышей
- Текущий ремонт резервуаров
Тема 4.2. Техническое обслуживание и ремонт трубопроводов перекачивающих станций и нефтебаз
Студент должен:
знать: дефекты трубопроводов и оборудования;
уметь: определять характер дефекта и выбирать способ его ликвидации.
Организация технического обслуживания и ремонта трубопроводов перекачивающих станций и нефтебаз Дефекты трубопроводов ПС и нефтебаз и их оборудования, обнаружение дефектов и способы их устранения.
Методические указания
В период эксплуатации трубопроводов следует осуществлять постоянный контроль за состоянием трубопроводов и их элементов (сварных швов, фланцевых соединений, арматуры), антикоррозионной защиты и изоляции, дренажных устройств, компенсаторов, опорных конструкций и т.д. с записями результатов в эксплуатационном журнале.
При периодическом контроле следует проверять: техническое состояние трубопроводов наружным осмотром и, при необходимости, неразрушающим контролем в местах повышенного коррозионного и эрозионного износа, нагруженных сечений и т.п.; устранение замечаний по предыдущему обследованию и выполнение мер по безопасной эксплуатации трубопроводов; полноту и порядок ведения технической документации по обслуживанию, эксплуатации и ремонту трубопроводов.
Трубопроводы, подверженные вибрации, а также фундаменты под опорами и эстакадами для этих трубопроводов в период эксплуатации должны тщательно осматриваться с применением приборного контроля за амплитудой и частотой вибрации. Максимально допустимая амплитуда вибрации технологических трубопроводов составляет 0,2 мм при частоте вибрации не более 40 Гц.
Наружный осмотр трубопроводов, проложенных открытым способом, при периодических обследованиях допускается производить без снятия изоляции.
Наружный осмотр трубопроводов, уложенных в непроходимых каналах или в земле, производится путем вскрытия отдельных участков длиной не менее 2 м. Число участков устанавливается в зависимости от условий эксплуатации.
Основным методом контроля за надежной и безопасной эксплуатацией технологических трубопроводов является периодическая ревизия, которая проводится в установленном порядке.
Результаты ревизии служат основанием для оценки состояния трубопровода и возможности его дальнейшей эксплуатации.
Для трубопроводов высокого давления [свыше 10 МПа (100 кгс/см2)] предусматриваются следующие виды ревизии: выборочная, генеральная выборочная и полная. Сроки выборочной ревизии устанавливаются в зависимости от условий эксплуатации, но не реже одного раза в 4 года.
Первую выборочную ревизию трубопроводов, транспортирующих неагрессивные или малоагрессивные среды, следует производить не позднее чем, через 2 года после ввода трубопровода в эксплуатацию.
При проведении ревизии внимание следует уделять участкам, работающим в особо сложных условиях, где наиболее вероятен максимальный износ трубопровода вследствие коррозии, эрозии, вибрации и других причин. К таким относятся участки, где изменяется направление потока (колена, тройники, врезки, дренажные устройства, а также участки трубопроводов перед арматурой и после нее) и где возможно скопление влаги, веществ, вызывающих коррозию (тупиковые и временно неработающие участки).
При ревизии трубопроводов с давлением до 10 МПа (100 кгс/см2) следует: а) провести наружный осмотр трубопровода; б) измерить толщину стенки трубопровода приборами неразрушающего контроля, а в необходимых случаях - сквозной засверловкой с последующей заваркой отверстия.
Количество участков для проведения толщинометрии и число точек замера для каждого участка определяется в соответствии с документацией и в зависимости от конкретных условий эксплуатации.
Толщину стенок измеряют на участках, работающих в наиболее сложных условиях (коленах, тройниках, врезках, местах сужения трубопровода, перед арматурой и после нее, местах скопления влаги и продуктов, вызывающих коррозию, застойных зонах, дренажах), а также на прямых участках трубопроводов.
При этом на прямых участках внутриустановочных трубопроводов длиной до 20 м и межцеховых трубопроводов длиной до 100 м следует выполнять замер толщины стенок не менее, чем в трех местах.
Во всех случаях контроль толщины стенки в каждом месте следует производить в 3 - 4 точках по периметру, а на отводах - не менее чем в 4 - 6 точках по выпуклой и вогнутой частям.
Во время осмотра проверяют наличие коррозии, трещин, уменьшения толщины стенки труб и деталей трубопроводов;
При необходимости проводится радиографический или ультразвуковой контроль сварных стыков и металлографические и механические испытания;
Проверка механических свойств металла труб, работающих при высоких температурах и в водородсодержащих средах, проводится в случаях, предусмотренных проектом. Механические свойства металла следует проверять также и в случаях, если коррозионное действие среды может вызвать их изменение.
При неудовлетворительных результатах ревизии следует определить границу дефектного участка трубопровода (осмотреть внутреннюю поверхность, измерить толщину и т.п.) и выполнить более частые замеры толщины стенки всего трубопровода.
При полной ревизии разбирается весь трубопровод полностью, проверяется состояние узлов труб и деталей, а также арматуры, установленной на трубопроводе.
Все трубопроводы и их участки, подвергавшиеся в процессе ревизии разборке, резке и сварке, после сборки подлежат испытанию на прочность и плотность.
После истечения проектного срока службы независимо от технического состояния трубопровод должен быть подвергнут комплексному обследованию (экспертизе промышленной безопасности) с целью установления возможности и сроков дальнейшей эксплуатации.
Во время эксплуатации следует принять необходимые меры по организации постоянного и тщательного контроля за исправностью арматуры, а также за своевременным проведением ревизии и ремонта.
Ревизию и ремонт трубопроводной арматуры, в том числе и обратных клапанов, а также приводных устройств арматуры (электро-, пневмо-, гидропривод, механический привод), как правило, производят в период ревизии трубопровода.
При ревизии арматуры, в том числе обратных клапанов, должны быть выполнены следующие работы: а) внешний осмотр; б) разборка и осмотр состояния отдельных деталей; в) осмотр внутренней поверхности и при необходимости контроль неразрушающими методами; г) притирка уплотнительных поверхностей (при необходимости); д) сборка, опробывание и опрессовка на прочность и плотность.
Вопросы для самоконтроля
- Организация технического обслуживания и ремонта трубопроводов перекачивающих станций и нефтебаз
- Порядок проведения периодической ревизии технологических трубопроводов
- Порядок проведения полной ревизии технологических трубопроводов
Тема 4.3. Техническое обслуживание и ремонт оборудования станций подземного хранения газа, ЛГНКС, БСТ, ГРС, ГРП
Студент д о л ж е н:
знать: систему технического обслуживания и ремонта оборудования СПХГ;
уметь: определять вид ремонтных работ для любого оборудования СПХГ.
Система технического обслуживания и ремонта для СПХГ. Характерные виды работ для различных цехов и установок: установок подготовки газа, компрессорного цеха и др.
Перспективная техника и технология на СПХГ, БСГ, АГНКС, АГЗС, ГРС и ГРП.
Методические указания
Компрессорная станция. В газовых хранилищах с высоким давлением, если оно больше, чем давление в газопроводе, сжатие газа необходимо во время его нагнетания в хранилище в летнее время.
Потребность в компримировании колеблется более интенсивно в зимнее время, так как изменения мпературы вызывают значительные колебания в потреблении газа из хранилища. Для большинства хранилищ необходимо сооружать компрессорную станцию с производительностью, учитывающей максимальный отбор и нагнетание газа.
Летом нагрузка хранилища более устойчива и обычно ниже средней и максимальной загрузки в зимнее время. Это положение неприменимо к хранилищам с высоким давлением, где требуются очень небольшие нагрузки на компримирование, или оно совершенно не требуется.
Вследствие всего этого компрессорная станция хранилища должна иметь широкие пределы производительности и давления при сжатии. Поэтому расчет и выбор компрессоров необходимо делать с большой тщательностью.
Обычно желательно иметь компрессорные установки с двумя различными мощностями, например 1000 и 2000 л. с.
Осушка газа. В большинстве случаев требуется осушка газа, отбираемого из хранилища. Даже если в хранилище нагнетается сухой газ, он отбирается из пласта насыщенным влагой. Иногда устанавливают дегидраторы у устья скважины, хотя экономичнее осушать газ в одном центральном пункте на выходе из газосборной сети.
Существуют два способа осушки газа: жидким поглотителем (ди- или триэтиленгликоль); твердым поглотителем (хлористый кальций, боксит). Твердый поглотитель влаги дает лучшие результаты, но первоначальная стоимость установки с твердым поглотителем почти на 50% выше стоимости гликолевой установки.
Масло, попадающее из компрессора, засоряет твердый поглотитель и делает его неэффективным. Поэтому необходимо тщательно очистить газ от масла до поступления его на осушку. Осушка газа до сжатия требует применения емкостей большего объема, но более низкого давления.
Если предусмотрено центральное замерное устройство на входе и выходе газа из хранилища, то осушку газа лучше проводить до счетчиков. Таким образом, как при закачке, так и при отборе сухой газ будет замерен и не будет необходимости в поправках на содержание воды в газе, отбираемом из хранилища.
Во многих случаях гликолевую установку целесообразно установить перед компрессией, в особенности если высока степень сжатия.
Для обеспечения нормальной работы ГРС должна периодически подвергаться профилактическим осмотрам с целью своевременного выявления повреждений.
Периодичность и содержание работ по техническому обслуживанию и ремонту оборудования устанавливается положением по технической эксплуатации ГРС. Для оборудования и систем ГРС устанавливаются следующие виды обслуживания и ремонта: 1) периодическое техническое обслуживание - комплекс операций по поддержанию работоспособности оборудования через установленные в эксплуатационной документации интервалы времени; 2) текущий ремонт - вид ремонта, при котором обеспечивается нормальная эксплуатация оборудования до очередного планового ремонта. Во время текущего ремонта устранение неисправности и восстановление работоспособности оборудования осуществляется путем замены или восстановления отдельных деталей, сборочных единиц и узлов; 3) капитальный ремонт. Он проводится в зависимости от технического состояния ГРС и связан с заменой основных узлов и деталей, в том числе и оборудования.
При ремонте запорных кранов на линиях редуцирования и другого оборудования подача газа потребителям производится по обводной линии.
Для проведения профилактических и ремонтных работ один раз в год осуществляется остановка ГРС. Ремонтные работы, связанные с отключением ГРС, должны проводиться в период наименее интенсивного отбора газа и должны быть согласованы потребителем. В случае возникновения предаварийных и аварийных ситуаций ГРС останавливается немедленно с обязательным последующим уведомлением потребителя.
В ГРС индивидуального проектирования и БК ГРС с постоянным присутствием обслуживающего персонала осмотр оборудования, арматуры и механизмов проводится ежедневно, а в АГРС, где отсутствует постоянный обслуживающий персонал, осмотр производится еженедельно. При проведении регламентных работ на ГРС рекомендуется:проверить арматуру газа на выходе подогревателя; проверить величину выходного давления по показаниям манометров; продуть фильтры; проверить работоспособность системы защитной автоматики; в случае необходимости наполнить рабочую емкость одоризатора одорантом из подземной емкости; очистить оборудование, арматуру и механизмы от пыли.
В зависимости от времени года, температуры окружающего воздуха, температуры протекающего газа, его точки росы и расхода практически установить необходимость подогрева и количества работающих горелок. При этом необходимо избегать нагрева газа до температуры, вызывающей частое срабатывание терморегулятора.
Необходимость пополнения рабочей емкости одорантом следует определить по указателю уровня. Наполнение рабочей емкости одорантом производится из резервной подземной емкости путем создания в ней избыточного давления согласно инструкции.
Независимо от результатов профилактических осмотров, не реже одного раза в год, производить проверку точности работы, полную ревизию запорной, регулирующей, защитной арматуры и фильтров. При этом арматура и фильтры должны быть разобраны, а их детали тщательно очищены и промыты уайт-спиритом. Затворы арматуры необходимо тщательно осмотреть. При необходимости заменить седла, затворы и резиновые уплотнительные кольца. Произвести полную замену сальниковых набивок, смазки и уплотняющих прокладок. После сборки арматуры провести проверку её ходовой части на плавность и легкость перемещений. После сборки арматуры и коммуникаций на участках, работающих под давлением, проверить герметичность стыков и соединений. Обнаруженные дефекты необходимо устранить.
Вопросы для самоконтроля
- Система технического обслуживания и ремонта для СПХГ
- Способы осушки газа
- Виды ремонта оборудования ГРС
Раздел 5. ОХРАНА ОКРУЖАЮЩЕЙ СРЕДЫ