Основы микроэлектроники (курс лекций)
Вид материала | Курс лекций |
- Лекция №11 Сжатие изображений Курс лекций «Алгоритмические основы машинной графики», 54.41kb.
- Основы семейной психопедагогики (курс лекций), 11111.59kb.
- О. В. Свидерская Основы энергосбережения Курс лекций, 2953.76kb.
- Курс лекций введение в профессию "социальный педагог", 4415.45kb.
- Курс лекций по дисциплине " основы компьютерных технологий" Часть I. Microsoft Word, 432.92kb.
- Курс лекций Барнаул 2001 удк 621. 385 Хмелев В. Н., Обложкина А. Д. Материаловедение, 1417.04kb.
- Курс лекций. Учебное пособие / В. Е. Карпов, К. А. Коньков, 68.87kb.
- Курс лекций по автоматизированному электроприводу для итр проектный организаций с применением, 24.37kb.
- Программа курса лекций (1 курс магистратуры, 1 сем., 36 ч, экзамен) Профессор,, 34.75kb.
- Основы политологии: Курс лекций. 2-е изд., доп. Ростов на/Дону.: Феникс, 1999. 573, 14.9kb.
ОСНОВЫ МИКРОЭЛЕКТРОНИКИ
(курс лекций)
Лекция 1 (принести на лекцию литературу и экспонаты)
Раздел 1. ОСНОВНЫЕ ПОЛОЖЕНИЯ
Интегральные микросхемы (ИМС) являются элементной базой ЭВМ. Сложные вычислительные системы содержат несколько миллионов элементов. Поэтому важнейшее значение приобретают проблемы повышения надежности и микроминиатюризации ЭВА.
Если бы мы попытались реализовать современный компьютер на обычных дискретных компонентах, как это делалось лет 30 назад (вспомните наши отечественные телевизоры), то получилось бы следующее: один транзистор в корпусе занимает объем около 1 см3. Только сам процессор в этом случае имел бы объем в 5–10 млн куб. см — т.е. 5–10 кубометров. Это не считая плат, блоков, стоек, и т.д. Потребовалось бы около 20 млн паек как минимум. Если рассчитать по формулам надежность (т.е. время наработки на отказ) этой системы, то оно составило бы менее одной секунды. Иначе говоря, такая ЭВМ вообще никогда бы не заработала. Для тех, кто заинтересуется, я в свободное время мог бы рассказать, как мы работали на больших машинах класса ЕС (лучшая машина ЕС уступает устаревшей IBM-286 и работает в 10 000 раз медленнее "Пентиума"). Так что интегральные схемы по-существу решили судьбу вычислительной техники.
Теперь о литературе. Мы будем изучать не самые новые разработки ИМС (понимание современной микроэлектроники требует другой физики, которую вы не изучали), и для вас будет полезной любая книга издания после 1980 г. Но некоторые особенно полезны:
1. И. П. Степаненко, Основы микроэлектроники, — М., Сов. радио, 1980 г., 423 с.
2. Р. Маллер и Т. Кейминс, Элементы интегральных схем. — М., Мир, 1989 г., 632 с.
3. Ю. М. Калниболотский, Ю. В. Королев, Г. И. Богдан, В. С. Рогоза, Расчет и конструирование микросхем. — Киев, Выща школа, 1983 г., 208 с.
4. Конструирование и технология микросхем. Курсовое проектирование (под ред. Л. А. Коледова). — М., Высшая школа, 1984 г., 232 с.
5. У. Тилл и Дж. Лаксон, Интегральные схемы — материалы, приборы, изготовление, М.— Мир, 1985 г., 504 с.
Различают интегральную и функциональную микросхему. Примером первой является ИМС, полученная на одной полупроводниковой подложке, скажем, операционный усилитель или процессор. Примером второй служит пьезоэлектрический резонатор.
Небольшой экскурс в историю: электроника как наука зародилась еще в 19 веке благодаря исследованиям в области физики переноса электрических зарядов в различных средах и взаимодействия зарядов в электрических и магнитных полях. Существуют три направления развития электроники (с точки зрения элементной базы):
- Вакуумная: электровакуумные и газоразрядные лампы, электронно-лучевые приборы, фотоэлектрические приборы, рентгеновские трубки;
- Твердотельная: полупроводниковые приборы, ИМС, оптоэлектронные приборы;
- Квантовая: лазеры и мазеры, радиоастрономические приборы, голографические приборы.
Интегральная микросхема (или просто — интегральная схема) есть совокупность
взаимосвязанных компонентов (транзисторов, диодов, конденсаторов, резисторов и т.п.), изготовленная в едином технологическом цикле (т.е. одновременно), на одной и той же несущей конструкции — подложке, и выполняющая определенную функцию преобразования информации.
Компоненты, которые входят в состав ИС и поэтому не могут быть выделены из нее в качестве самостоятельных изделий, называются элементами ИС или интегральными элементами. В отличие от интегральных элементов, конструктивно обособленные элементы и детали, свойственные "домикроэлектронной" эпохе, будем называть дискретными компонентами, а электронные узлы и блоки, построенные на их основе — дискретными схемами.
Не следует смешивать слова "микроминиатюризация" и "микроэлектроника". Микроэлектроника — это область электроники, охватывающая проблемы исследования,
– 2 – Лекция 1
конструирования, изготовления и применения электронных устройств с высокой степенью интеграции, реализованных на одной подложке, так что саму ИМС можно рассматривать как конструктивно единый радиоэлемент (со всеми вытекающими отсюда последствиями: надежность — как у одного элемента, число выводов — как у одного элемента, и т.д.).
Современные задачи уже невозможно решать на основе старой элементной базы. Основными факторами, лежащими в основе смены элементной базы, являются: надежность, габариты и масса, стоимость и мощность. Простой пример иллюстрирует причины перехода от этапа транзисторной техники к этапу микроэлектроники.
Пусть требуется построить компактное электронное устройство, содержащее 108 компонентов. Если попытаться решить эту задачу на дискретных компонентах, характеризуемых средней мощностью 15 мВт, средним размером (с учетом соединений) 1 см3, средней массой 1 г, средней ценой 50 коп, и вероятностью отказа 10–5 час–1, то результат будет следующий: мощность, рассеиваемая устройством — 1,5 тысячи кВт, габариты 100 м3, масса 100 т, стоимость (без учета монтажных работ) — 50 млн гривен (около 10 млн долларов).
Кроме того, на монтаж устройства даже при двухсменной работе потребуется 10 человеко-лет, и серийный выпуск его может оказаться непосильным для народного хозяйства. (Забудем пока о том, что даже опытный радиомонтажник допускает 3–5 ошибок на 1000 паек, которые потом приходится выискивать.)
Однако самый главный недостаток состоит в том, что средняя частота отказов (10–5.108) оказывается равной 103/час, т.е. около 1 отказа за 3 сек, что, конечно, говорит о неработоспособности устройства.
Применяемые при изготовлении ИМС технологические процессы имеют групповой характер (т.е. на одной пластине создается сразу много микросхем). Допустим, что таких ИМС 100 штук, и каждая имеет по 1000 транзисторов и пассивных элементов. Значит, грубо говоря, число спаев составило бы около 100 тыс. (вообще-то — намного больше), а число ошибок — не менее 300. В ИМС же подобные ошибки отсутствуют, так как припаивать отдельные элементы друг к другу нет нужды.
Элементная база электронных устройств претерпела несколько этапов развития:
Первое поколение. Дискретная электроника с преобладанием электровакуумных и газоразрядных приборов. Затем роль активных радиокомпонентов стали играть транзисторы. РЭА собирали на отдельных платах или модулях, которые объединяли в блоки, блоки — в стойки, стойки — в устройства.
Второе поколение. Появление в 1948 г. точечного биполярного транзистора (Бардин и Бронштейн) а затем — более надежного сплавного транзистора (Шокли) ознаменовало второе поколение РЭА и ЭВА. В точечных полупроводниковых приборах p-n-переходы создавались в месте контакта двух заточенных проволочек с полупроводником. Однако точечные контакты были нестабильными.
В сплавных p-n-переходах контакт p- и n-областей достигается взаимодействием жидкой фазы вплавляемого электрода, содержащего легирующую примесь, с твердым полупроводником. Хотя сплавные приборы более стабильны, чем точечные, они характеризуются довольно низким коэффициентом усиления по току (из-за толстой базы порядка 10 мкм) и низкой fгр (из-за довольно больших емкостей p-n-переходов, обусловленных большими площадями этих переходов).
Более перспективными оказались транзисторы, получаемые с помощью процессов диффузии примесей в полупроводниковую подложку. Толщина базы может составлять здесь 0,2–0,3 мкм. В конце 50-х г.г. зародилась планарная технология, в которой были воплощены идеи получения p-n-переходов на основе процессов диффузии. Эта технология подготовила зарождение элементной базы третьего поколения — ИМС.
И наконец, четвертое поколение элементной базы РЭА и ЭВА составляют функциональные схемы.
Нужно сказать, что все перечисленные поколения существуют и ныне, непрерывно развиваясь. Так, применение печатного монтажа, более совершенных материалов, трансформаторов, разъемов, уменьшение габаритов электронных и полупроводниковых приборов позволили существенно уменьшить размеры
– 3 – Лекция 1- 2
радиотехнических систем. Например, удельная емкость керамических конденсаторов за 30 лет увеличилась в 250–300 раз, а габариты резисторов снижены в 2–10 раз. Появился даже такой термин, как микроминиатюризация — реализация электронных схем, блоков, узлов и аппаратуры в целом из микроминиатюрных радиодеталей и узлов. Типовым решением задачи микроминиатюризации является создание микромодулей с последующей их герметизацией. Если в обычной печатной схеме плотность упаковки составляет 3–5 деталей / см3, то в микромодулях — 10–20 дет/см3. Увеличение плотности упаковки всегда влечет за собой повышение надежности аппаратуры.
Высокая надежность ИМС и микроэлектронной аппаратуры объясняется также применением особо чистых материалов, специальных условий изготовления, герметичностью ИМС, а также отсутствием паянных соединений. Очень малые габариты ИМС и потребляемые токи делают их весьма экономичными устройствами по сравнению с обычными РЭ устройствами.
Постоянное сокращение площади, занимаемой одним элементом (с 50 50 мкм2 до 11 мкм2 и менее), позволяет увеличивать степень интеграции k = lg N, где N — число элементов и компонентов, входящих в ИМС.
Так, при N = 1 ... 10 k = 0 ... 1, получаем ИМС первой степени интеграции,
N = 10 ... 100 k = 1 ... 2 — ИМС 2-й степени интеграции,
N = 100 ... 1000 k = 2 ... 3 — ИМС 3-й степени интеграции,
N = 1000 ... 10 000 k = 3 ... 4 — ИМС 4-й степени интеграции,
N = 10 000 ... 100 000 k = 4 ... 5 — ИМС 5-й степени интеграции.
Применяют еще и такие термины:
а) если k 1 (N 10) — простая ИМС,
б) если 1 k 2 (10 N 100) — средняя ИМС (СИС),
в) если 2 k 4(100 N 10 000) — большая ИМС (БИС),
г) если k 4 (N 10 000) — сверхбольшая ИМС (СБИС).
Примером СБИС является микропроцессор (плотность упаковки элементов — это число элементов, чаще всего — транзисторов, на единицу площади — 500–1000 элементов / мм2 и более — на сегодняшний день порядка 100 000).
По способу реализации различают: 1) полупроводниковые ИМС; 2) пленочные ИМС тонкопленочные (пленки толщиной до 1 мкм) и толстопленочные (более 1 мкм); 3) гибридные ИМС (пленочные пассивные элементы и навесные активные компоненты); 4) совмещенные ИМС (пленочные пассивные элементы и полупроводниковые активные элементы в полупроводниковой подложке).
(Конец лекции 1)
Лекция 2
Раздел 2. ОСНОВЫ ТЕХНОЛОГИИ ИМС
2.1. Основные этапы изготовления ИМС
В качестве основного полупроводника используется кремний (Si). Это очень распространенный на земле элемент (25,7 % земной коры по весу).
Атомный номер — 14
Атомный вес — 28,06
Температура плавления — 1420 С
Ширина запрещенной зоны Eg = 1,12 эВ (при 300 К)
Подвижность свободных электронов n = 1350 см2/(В.с) (при 300 К)
Подвижность дырок p = 480 см2/(В.с) (при 300 К)
Диэлектрическая проницаемость = 12
Акцепторы: B, Al
– 4 – Лекция 2
Доноры: P, As, Sb
Удельное сопротивление = 2,5 . 105 Ом . см (300 К)
Концентрация пар ni = 1,5 . 1010 см-3 (300 К) (кстати, для германия ni = 2,5 . 1013 см-3)
Постоянная решетки: 5,43 Å (300 К)
Число атомов в 1 куб. см вещества: 5 . 1022 см-3.
Германий тоже используется в полупроводниковой технологии, но только для производства дискретных диодов и транзисторов. Для производства ИМС германий не применяется. Во-первых, для германия Eg = 0,77 эВ, поэтому германий чувствителен к изменению температуры. Во-вторых, двуокись германия GeO2 может иметь два типа кристаллической решетки — кубическую и гексагональную, из которых первую трудно получить, а вторая растворяется в воде. Как мы увидим дальше, окисел, выращенный на поверхности полупроводника, играет важную роль как пассивирующий слой. В общем, GeO2 не может играть роль пассивирующего слоя, а SiO2 — может. Кроме того, на поверхности кремния можно нарастить слой нитрида кремния Si3N4, который равномерно ложится на поверхность полупроводника. И наконец, SiO2 играет роль маски благодаря своей низкой температурной чувствительности и стойкости к водным растворам.
Но самая главная причина — это низкая температура плавления германия, не позволяющая проводить высокотемпературную диффузию примесей. Как мы увидим ниже, для того чтобы внедрить примеси в полупроводник за реальное время (пусть даже несколько часов), его нужно нагреть не менее чем до 1000 градусов. Германий при этой температуре уже расплавится (температура плавления 936 С). А загонять примеси при безопасной для германия температуре — 700 750 С пришлось бы многие месяцы и годы.
По этим причинам кремний является более технологичным для производства полупроводниковых ИМС, чем германий.
Еще одним полупроводником для ИМС является арсенид галлия GaAs (AIIIBV):
Eg = 1,4 эВ
n = 11 000 см2/(В.с)
p = 450 см2/(В . с)
= 4.108 Ом . см
ni = 1,5.106 см-3 .
Благодаря своей широкой Eg он еще менее чувствителен к температуре, чем кремний. А ввиду очень высокого n коэффициенты усиления транзисторов получаются больше, чем в кремниевых приборах, и, кроме того, частотные свойства транзисторов оказываются существенно лучше, чем на основе кремния. Так как арсенид галлия — многодолинный полупроводник (объяснить, что это) то он находит применение в СВЧ-микросхемах для создания генераторов (на основе эффекта Ганна). Правда, GaAs намного дороже, чем Si. Кроме того, хотя сам GaAs нетоксичен, но его технология высоко токсична.
Итак, основным элементом современных ИМС является кремний.
Теперь рассмотрим самую упрощенную последовательность технологических операций изготовления ИМС (опустим этап подготовки пластин — резка, полировка и т.д.). Я не буду перечислять все операции, а дам лишь краткую характеристику того, что приходится делать. (Тилл и Лаксон, с. 15.)
1. Проектирование схемы
2. Проектирование фотошаблонов
3. Изготовление фотошаблонов
4. Фотолитография
5. Локальное внедрение примесей (4 и 5 повторяются несколько раз)
6. Металлизация
7. Травление металла
8. Контроль на пластине
9. Скрайбирование (резка пластины на отдельные кристаллы)
10. Выходной контроль
– 5 – Лекция 2
11. Установка в корпус
12. Создание выводов из корпуса.
Это — лишь краткий перечень. Обычно число операций составляет 50–200. Ниже мы рассмотрим лишь небольшой фрагмент технологии — по изготовлению самих ИМС.
Но прежде я хотел бы сделать одно замечание, касающееся пункта 1. Традиционные методы проектирования дискретных схем, где в максимальной степени используются пассивные элементы, приходится отвергнуть как бесполезные, поскольку транзисторы занимают на кристалле меньше места, чем пассивные компоненты. Катушек индуктивности попросту не существует, конденсаторы велики по площади и малы по емкости, а для резисторов с большим сопротивлением требуется слишком много места.
А теперь — собственно об изготовлении:
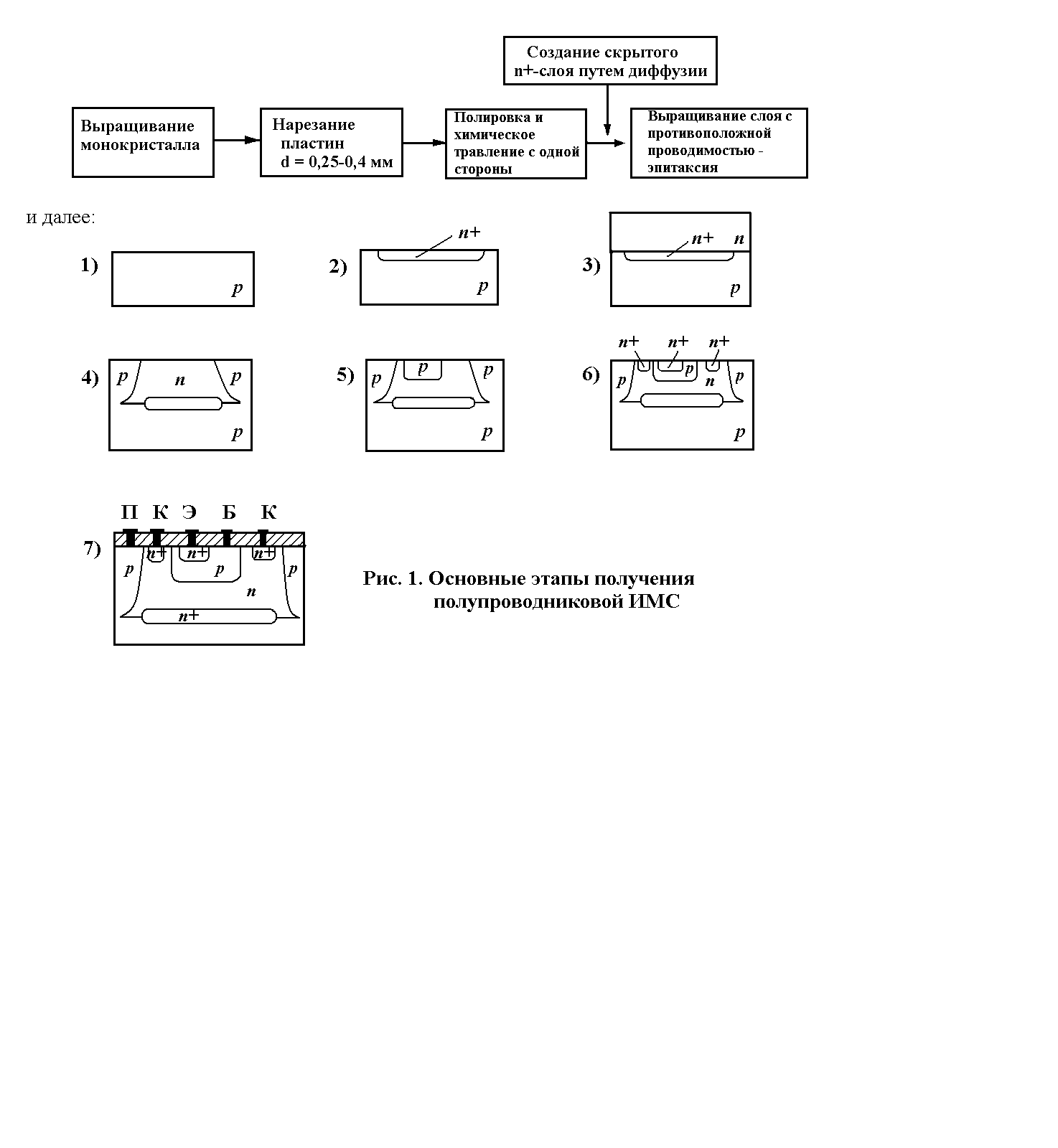
Для получения полной конфигурации ИМС требуется использовать 5–6 фотошаблонов для биполярной ИМС или до 10 — для МДП БИС. Изготовление фотошаблонов требует высокой точности. Далее с помощью компьютера оригинал копируется на двух-координатном графопостроителе с 20-кратным уменьшением. Затем рисунок уменьшается еще в 20 раз с помощью шагового процесса мультипликации. Последний воспроизводит
(мультиплицирует) фотошаблон 100–1000 раз, четко располагая копии по строкам и столбцам — так получаются сотни и тысячи одинаковых фотошаблонов. На фотошаблоне размещают контрольные области, которые дают возможность контролировать процесс реализации ИМС поэтапно.
Другой способ получения фотошаблонов сразу в натуральную величину — нанесение их лучом сканирующего электронного микроскопа, который управляется компьютером.
– 6 – Лекция 2
После каждой процедуры получения очередного р- или n-слоя полупроводник покрывают слоем двуокиси кремния SiO2. Затем на SiO2 наносят слой фоторезиста (позитивного или негативного) и фотошаблон.
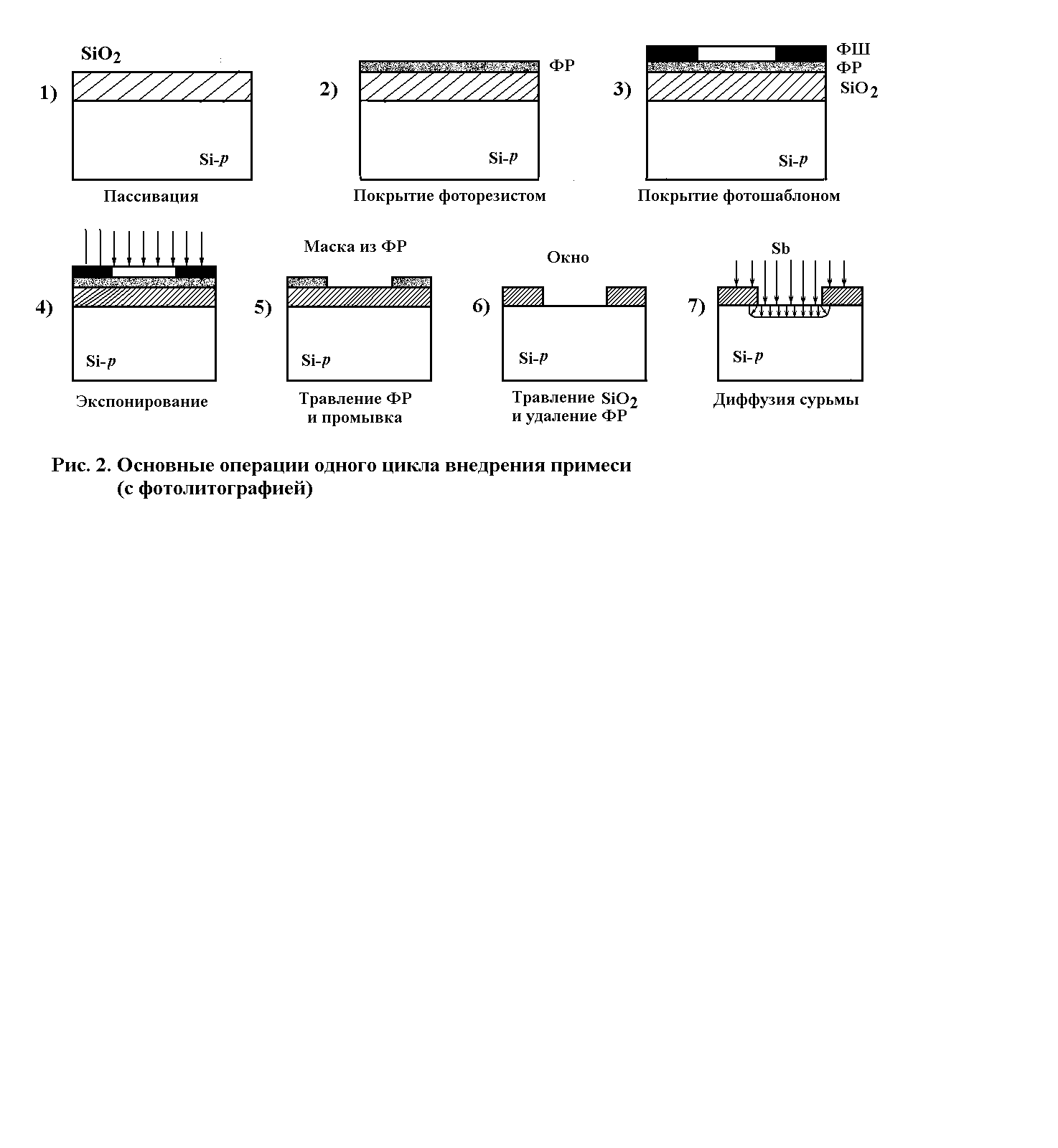
Позитивный ФР твердеет в местах, не облученных светом, негативный — наоборот. Далее структуру подвергают действию света (экспонирование), ФШ снимают, а экспонированную структуру проявляют и промывают. В тех местах, где произошло задубливание ФР, последний остается на поверхности структуры. Например, в случае позитивного ФР он задубливается в тех местах, которые находились под непрозрачными участками ФШ, в случае негативного — наоборот. Задубленный ФР образует маску, которая защищает поверхность SiO2 на последующей операции его травления. Травление SiO2 осуществляется плавиковой кислотой HF.
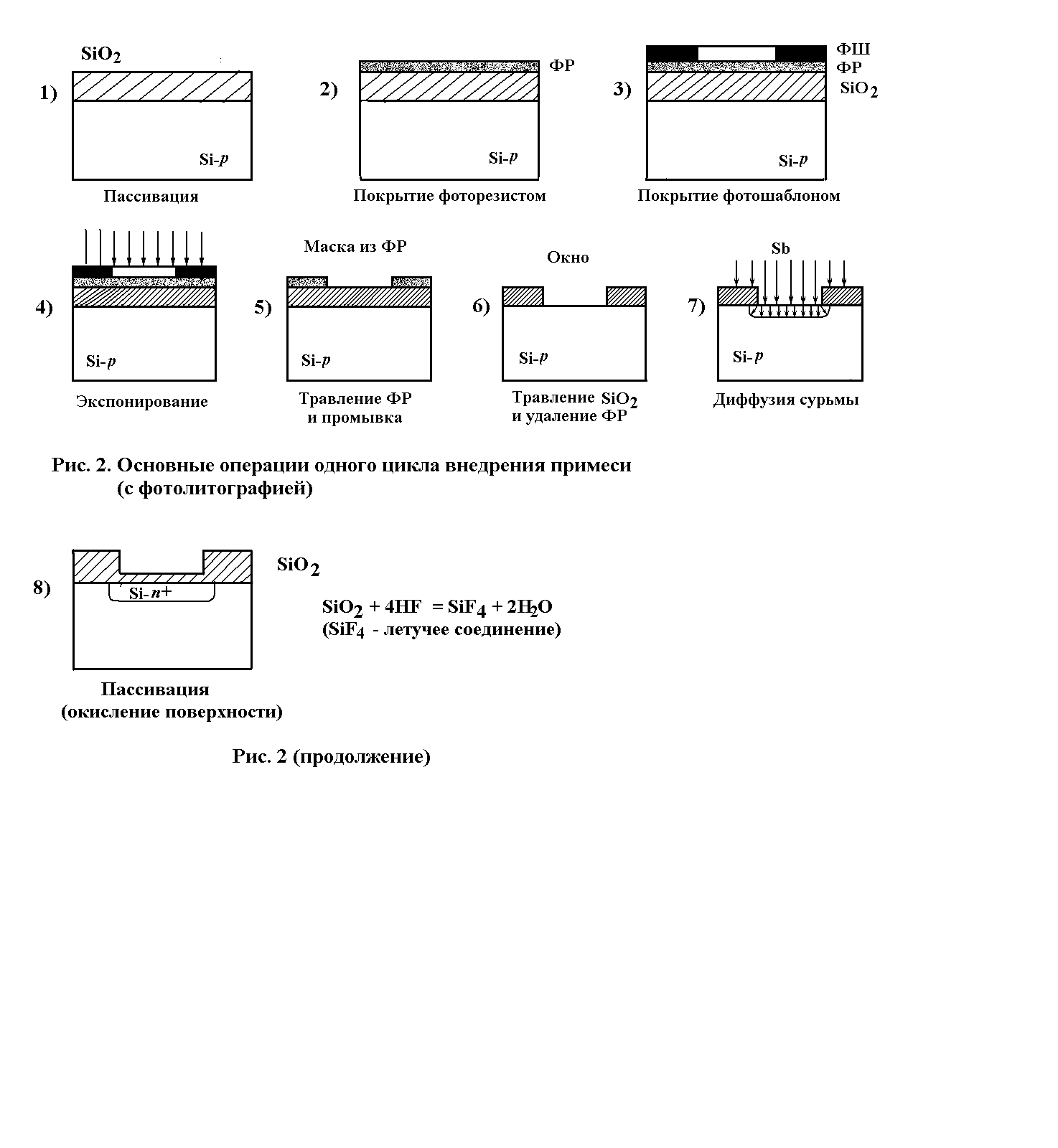
Плавиковая кислота растворяет SiO2 в тех местах, которые не защищены маской из ФР. Так образуются в SiO2 окна.
Затем выполняют диффузию легирующих примесей в кремний, тщательно выдерживая состав среды и температуру. Так, в р-кремнии для создания n-области можно использовать фосфор и сурьму. Если исходной пластиной является n-кремний, то для создания р-области обычно используют бор. Затем после процесса диффузии полученную структуру пассивируют.
Все описанное выше называется фотолитографией. Этот процесс повторяется несколько раз для формирования транзисторов, диодов, резисторов и конденсаторов в эпитаксиальном слое.
– 7 – Лекции 2–3
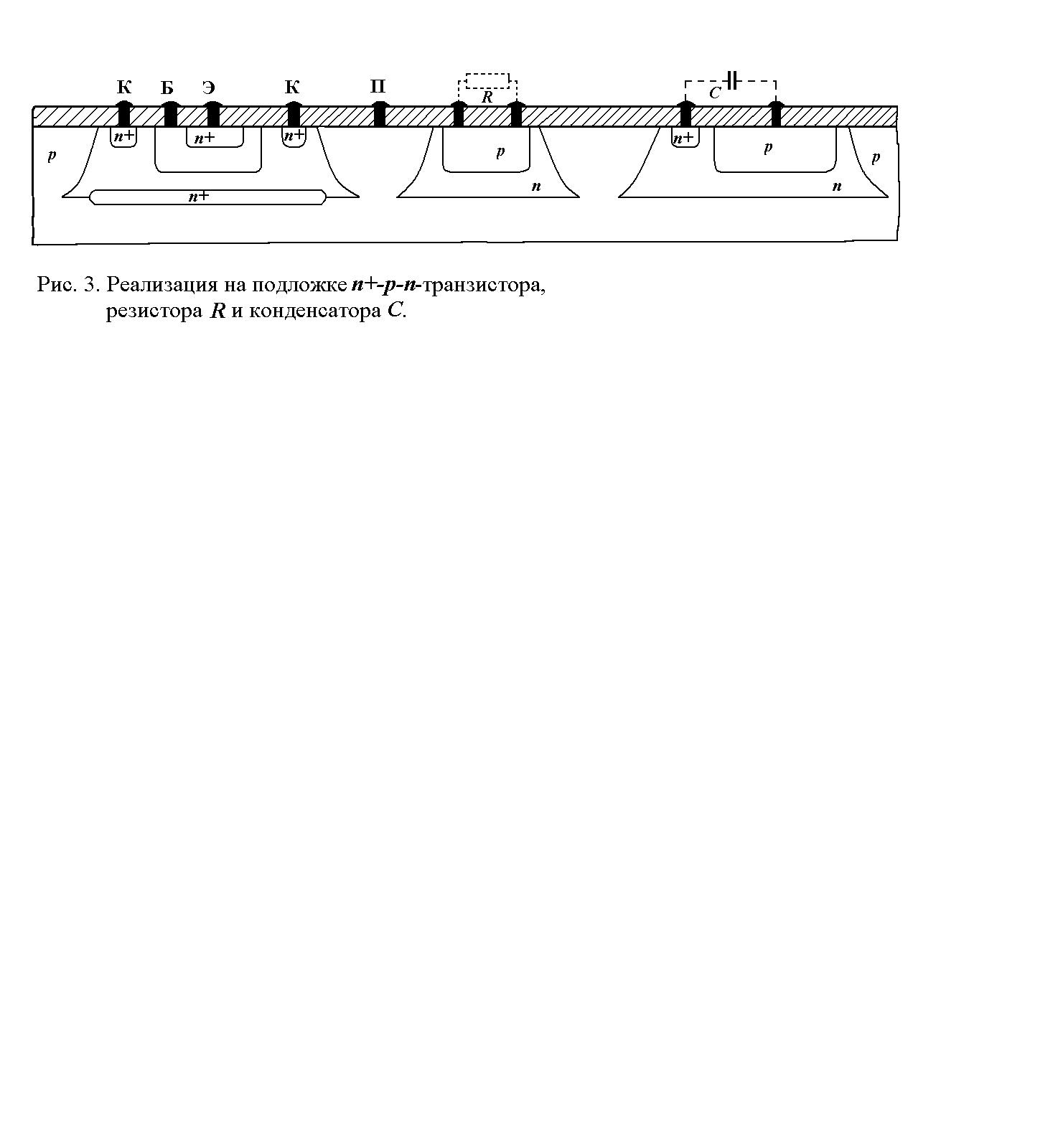
(Конец лекции 2)
Лекция 3
После того как в подложке получены все необходимые элементы ИМС, в SiO2 травятся
окна для получения в нужных местах металлических контактов (обычно — алюминиевых). Алюминий наносится в вакууме на всю пластину либо осаждением паров, либо электронно-лучевым методом. Лишний металл удаляют, используя фотошаблон, аналогично тому, как было описано выше, т.е. травлением, и оставляют его в тех местах, где требуется, для межсоединений и контактов. Этот фотолитографический процесс иногда называется фотогравировкой. Затем полученную структуру отжигают, чтобы сделать алюминий более плотным, и покрывают структуру слоем пассивирующего окисла SiO2.
(На примере курсового проекта и стекляшек рассмотреть все маски,
требуемые для изготовления ИМС.)
После изготовления ИМС испытываются. Бракованные ИМС помечают чернилами. Затем пластину скрайбируют — либо алмазным резцом, либо лучом лазера, и разламывают на отдельные кристаллы. Каждый такой кристалл (их иногда называют чипами) помещают в отдельный корпус и присоединяют к нему внешние выводы методом термокомпрессии — прижимают волосок к контактной площадке и пропускают электрический разряд через место соединения для приваривания.
И наконец, на заключительном этапе выполняется герметизация ИМС в корпусе.
Выводы
1. n- и р-области полупроводниковой ИМС получаются в результате таких операций, как эпитаксия, диффузия, и некоторых других (например, ионная имплантация).
2. Выборочное травление и диффузия примесей в полупроводниковую подложку осуществляется с помощью фотолитографического процесса.
3. После каждой фотолитографии структура пассивируется пленкой SiO2.
2.2. Эпитаксия
Эпитаксией называют процесс выращивания монокристаллических слоев на подложке, при котором кристаллографическая ориентация выращиваемого слоя повторяет кристаллографическую ориентацию подложки.
В настоящее время эпитаксия обычно используется для получения тонких рабочих слоев однородного полупроводника на сравнительно толстой подложке, играющей роль несущей конструкции.
Типовой — хлоридный процесс эпитаксии применительно к кремнию состоит в следующем. Монокристаллические кремниевые пластины загружают в тигель ("лодочку")
– 8 – Лекция 3
и помещают в кварцевую трубу. Через трубу пропускают поток водорода, содержащий немного примеси тетрахлорида кремния SiCl4. При высокой температуре (около 1200 С), которая обеспечивается высокочастотным нагревом тигля, на поверхности пластин происходит реакция
SiCl4 + 2Н2 = Si + 4НCl.
В результате реакции на подложке постепенно осаждается слой чистого кремния, а пары НCl уносятся потоком водорода. Эпитаксиальный слой осажденного кремния монокристалличен и имеет ту же кристаллографическую ориентацию, что и подложка. Химическая реакция, благодаря подбору температуры, происходит только на поверхности пластины, а не в окружающем пространстве. Чтобы осаждение кремния из газовой фазы
было эпитаксиальным, нужно сильно нагреть пластину, так чтобы осаждающиеся атомы кремния могли перемещаться в положения, в которых они образовывали бы с подложкой ковалентные связи. При этом атомы должны успеть продолжить монокристаллическую решетку до того, как они будут накрыты следующими слоями осаждающихся атомов. Это и определяет температуру эпитаксии — от 900 до 1250 С.
Если к парам тетрахлорида кремния добавить пары соединений бора (В2Н6) или фосфора (РН3), то эпитаксиальный слой будет иметь уже не собственную, а cоответствен-но дырочную или электронную проводимость, поскольку в ходе реакции в осаждающийся кремний будут внедряться акцепторные атомы бора или донорные атомы фосфора.
Таким образом, эпитаксия позволяет выращивать монокристаллические слои любого типа проводимости и любого удельного сопротивления на подложке, обладающей также любым типом и величиной проводимости.
Эпитаксиальная пленка может отличаться от подложки по химическому составу. Способ получения таких пленок называют гетероэпитаксией, в отличие от гомоэпитаксии, описанной выше. Конечно, при гетероэпитаксии материалы пленки и подложки должны по-прежнему иметь одинаковую кристаллическую решетку. Например, можно выращивать кремниевую пленку на сапфировой или шпинельной подложке. (Шпинель — общая химическая. формула — А2+В23+О4, где А — Fe, Mg, Zn, Mn и др.;
B — Al, Cr, Ti и др. Прозрачная красная и синяя шпинель — драгоценный камень.)
Граница между эпитаксиальным слоем и подложкой не получается идеально резкой, так как примеси в процессе эпитаксии частично диффундируют из одного слоя в другой. Это обстоятельство затрудняет создание сверхтонких (менее 1 мкм) и многослойных эпитаксиальных структур. Основную роль в настоящее время играет однослойная эпитаксия. Она существенно пополнила арсенал полупроводниковых технологий: получение таких тонких однородных слоев (1–10 мкм), какие обеспечивает эпитаксия, невозможно иными средствами.
2.3. Легирование — введение примесей в полупроводник
Избирательное введение примесей в монокристалл кремния дает возможность наладить массовый выпуск электронных схем с исключительно малыми размерами.
Представьте себе решетку монокристалла кремния. В идеальном случае мы хотели бы заменить некоторые горизонтальные и вертикальные ряды атомов кремния атомами акцепторной или донорной примеси р- или n-типа. К сожалению, такое направленное идеальное введение примеси невозможно. Две доступные технологии введения примесей — диффузия и ионное внедрение (ионная имплантация).
Метод диффузии состоит в том, что примесь приводится в соприкосновение с поверх-ностью монокристалла кремния. Когда монокристалл разогрет, атомы примеси проникают внутрь монокристалла и заменяют атомы кремния, "вытряхнутые" со своих мест.
– 9 – Лекция 3
Метод ионного легирования состоит в том, что на поверхность монокристалла кремния направляют пучок ионов примеси, имеющих высокую скорость. Эти ионы проникают в толщу кристалла и в результате взаимодействия с атомами решетки замедляются и останавливаются.
Мы рассмотрим виды диффузии, возможные в кремнии, законы, которым подчиняется процесс диффузии, поведение коэффициента диффузии, а также вопросы растворимости примесей в кремнии. Будут проведены решения уравнений диффузии (второй закон Фика) в двух случаях и обсуждены некоторые способы расчета диффузионных слоев. Будет также описан процесс ионного внедрения и рассмотрена связь общей концентрации
примеси и распределения концентрации с параметрами имплантационной системы: током пучка и ускоряющим напряжением.
Виды диффузии (Ч. Уэрт и Р. Томсон, Физика твердого тела, с. 75–87)
Данный материал тесно связан с природой дефектов, о которых рассказывается в курсе МЭТ. Рассматривая температуру как тепловую вибрацию, можно предположить, что решетка трясется настолько сильно, что некоторые атомы покидают свои места и замещаются другими. Если поблизости окажется атом примеси приблизительно с тем же размером и валентностью, он может заменить ушедший атом в узле решетки. Такой процесс называется диффузией замещения или диффузией по вакансиям. Атомы примеси прыгают по узлам решетки стохастически (случайно) во всех направлениях. Допустим, что этот случайный процесс начался в какой-то одной области с некоторой концентрацией примесей. Тогда количество атомов, способных вернуться в область с более высокой концентрацией примеси, будет меньше числа атомов, способных попасть в область с более низкой концентрацией. Таким образом, движение примеси будет в целом направлено в сторону снижения концентрации. Но для движения примеси в кристалле требуется, чтобы на пути атома примеси встречались вакансии. Значит, скорость диффузии замещения зависит от скорости возникновения вакансий в решетке.
Однако, атом примеси может найти себе место в кристалле и не замещая атом исходного элемента. Это так называемые междоузлия. При высоких температурах атомы примеси могут перепрыгивать с одного междоузлия на другой, передвигаясь таким образом по решетке кристалла. Такое движение называется диффузией внедрения. Диффузия внедрения имеет гораздо бóльшую скорость распространения, чем диффузия замещения, поскольку междоузлия, как правило, свободны, а для осуществления замещения приходится ждать образования вакансий.
В кристаллической решетке может иметь место комбинация указанных видов диффузии. Некая доля примеси совершает диффузию внедрения, а остальная часть — диффузию замещения. Чтобы построить модель процесса диффузии внедрения, будем считать, что этот процесс может начаться от узла решетки или междоузлия и кончаться тоже как на узле решетки, так и на междоузлии, но движение атома идет только по междоузлиям.
Все доноры и акцепторы, применяемые обычно для кремния, диффундируют по вакансиям. По междоузлиям диффундируют золото, железо, медь и литий. Железо, медь и литий обычно нежелательны, но золото намеренно вводят процессом диффузии в некоторые быстродействующие ИМС. Атомы золота диффундируют по междоузлиям, но большинство из них останавливается в узлах решетки, образуя примесь замещения. Атомы золота не очень подходят к решетке кремния. Они образуют в ней что-то вроде неоднородности. Поскольку рекомбинация электронно-дырочной пары происходит вблизи неоднородности, то атомы золота являются причиной увеличения скорости рекомбинации и соответственного уменьшения среднего времени жизни подвижных
– 10 – Лекции 3 – 4
носителей заряда. Атомы золота уменьшают время жизни носителей и в силу этого увеличивают скорость переключения. Правда, по многим причинам применение золота для увеличения скорости переключения сейчас стараются вытеснить другими методами — модификацией геометрии элементов, техники изготовления и проектирования схем.
Скорость диффузии зависит от ряда факторов, связанных со структурой материала, в частности, от межатомного расстояния, химического номера элемента, типа связи между атомами в решетке, и т.д. Однако поскольку частота скачков отдельных атомов экспоненциально зависит от температуры, то уравнение диффузии в функции от температуры часто записывают в виде
D = D0 . e–Q/(kT), (1)
где D0 называется частотным фактором (не зависящим от температуры), а Q — энергия активации. D0 и Q для большинства практически используемых материалов можно найти в литературе (Уэрт и Томсон, с. 87, Э. А. Матсон и Д. В. Крыжановский [СППКМ], и др.)
Концентрация примеси в материале не может быть сколь угодно большой: она ограничена особым параметром — предельной растворимостью примеси, которая сама зависит от температуры: при некоторой температуре достигает максимального значения, а затем снова уменьшается. Максимальные предельные растворимости вместе с соответствующими температурами для некоторых материалов я вам сейчас приведу (Степаненко [ОМ] — с. 162, Тилл и Лаксон [ИСМПИ] — с. 74–75):
Примесь | As | P | B | Sb |
Nпр, см-3 | 20.1020 (1150 С) | 13.1020 (1150 С) | 5.1020 (1200 С) | 0,6.1020 (1300 С) |
Процесс диффузии в твердом теле при одномерном рассмотрении (эквивалентно изотропной диффузии в трех измерениях) можно описать двумя дифференциальными уравнениями, которые получили название законов Фика:
(Конец лекции 3)
Лекция 4
Первый закон Фика
J = – D dN/dx. (2)
Здесь J — плотность потока диффузанта, т.е. число атомов диффундирующего вещества, проходящих в результате направленной диффузии через единичное сечение полупроводника; dN/dx — градиент концентрации в направлении диффузии; D — коэффициент диффузии, который имеет размерность [см2/сек] и численно равен числу атомов вещества, диффундирующих за 1 сек через единичную площадку при единичном градиенте концентрации (см. предыдущее уравнение). Знак минус показывает, что поток диффундирующих атомов направлен в сторону уменьшения концентрации примесей.
Интуитивно первый закон совершенно понятен, а приведенная выше формула есть лишь лаконичная запись тезиса: плотность потока диффундирующих атомов пропорциональна градиенту концентрации.
Второй закон Фика
N/t = D 2N/x2. (3)
– 11 – Лекция 4
Второй закон Фика так же понятен, как и первый. Нужно лишь, глядя на его формулу, немного больше сосредоточиться: скорость накопления атомов диффузанта в трубке с единичным сечением и длиной x пропорциональна скорости изменения градиента концентрации. Если градиент N/x постоянен на отрезке x, то 2N/x2 = 0 и накопления атомов в трубке не будет, т.е. сколько войдет слева, столько выйдет справа. Чтобы частицы накапливались, необходимо, чтобы градиент у левого сечения трубки отличался от градиента у правого сечения, и чтобы знак этой разности совпадал со знаком градиента. В противном случае произойдет не накопление, а рассасывание диффузанта.
Вывод законов Фика очень прост, и его можно найти во многих учебниках (Тилл и Лаксон, Уэрт и Томсон, и др.). Я его приводить не буду. А вот на следствиях этого закона,
а именно — на решении дифференциального уравнения, соответствующего второму закону Фика, мы немного задержимся.
Решив дифференциальное уравнение, можно найти функцию N(x, t), т.е. распределение концентрации N(x) в любой момент времени t. Для этого следует ввести два граничных условия.
Пусть координата х = 0 соответствует той плоскости пластины, через которую вводятся примеси. Тогда координата противоположной плоскости равна толщине пластины d. На практике глубина диффузионных слоев всегда меньше толщины пластины, поэтому можно положить N(d) = 0. С математической точки зрения удобнее считать пластину бесконечно толстой и в качестве первого граничного условия принять
N(, t) = 0. (4)
Второе граничное условие имеет два варианта, которые соответствуют двум разновидностям реального технологического процесса.
1. Случай неограниченного источника примеси. В этом случае диффузант непрерывно поступает к пластине, так что в ее приповерхностном слое концентрация примеси поддерживается постоянной. Граничное условие для этого варианта имеет вид:
N(0, t) = Ns = const , (5)
где Ns — поверхностная (точнее — приповерхностная) концентрация. Обычно количество поступающего диффузанта обеспечивает режим предельной растворимости, т.е. Ns = Nпр.макс.
2. Случай ограниченного источника примеси. В этом случае сначала в тонкий приповерхностный слой пластины вводят некоторое количество атомов диффузанта, а потом источник диффузанта отключают, и атомы примеси перераспределяются по глубине пластины при неизменном их общем количестве. Первую стадию процесса называют загонкой, а вторую — разгонкой примеси.
Для этого варианта можно записать условие в виде
N(x) dx = Q = const, (6)
0
где Q — количество атомов примеси на единицу площади (задается на этапе загонки).
(Примечание: здесь Q — не энергия активации, которая встречалась выше.)
– 12 – Лекция 4
Решая уравнение (3) при граничных условиях (4) и (5), получаем распределение концентрации при неограниченном источнике (рисунок слева).
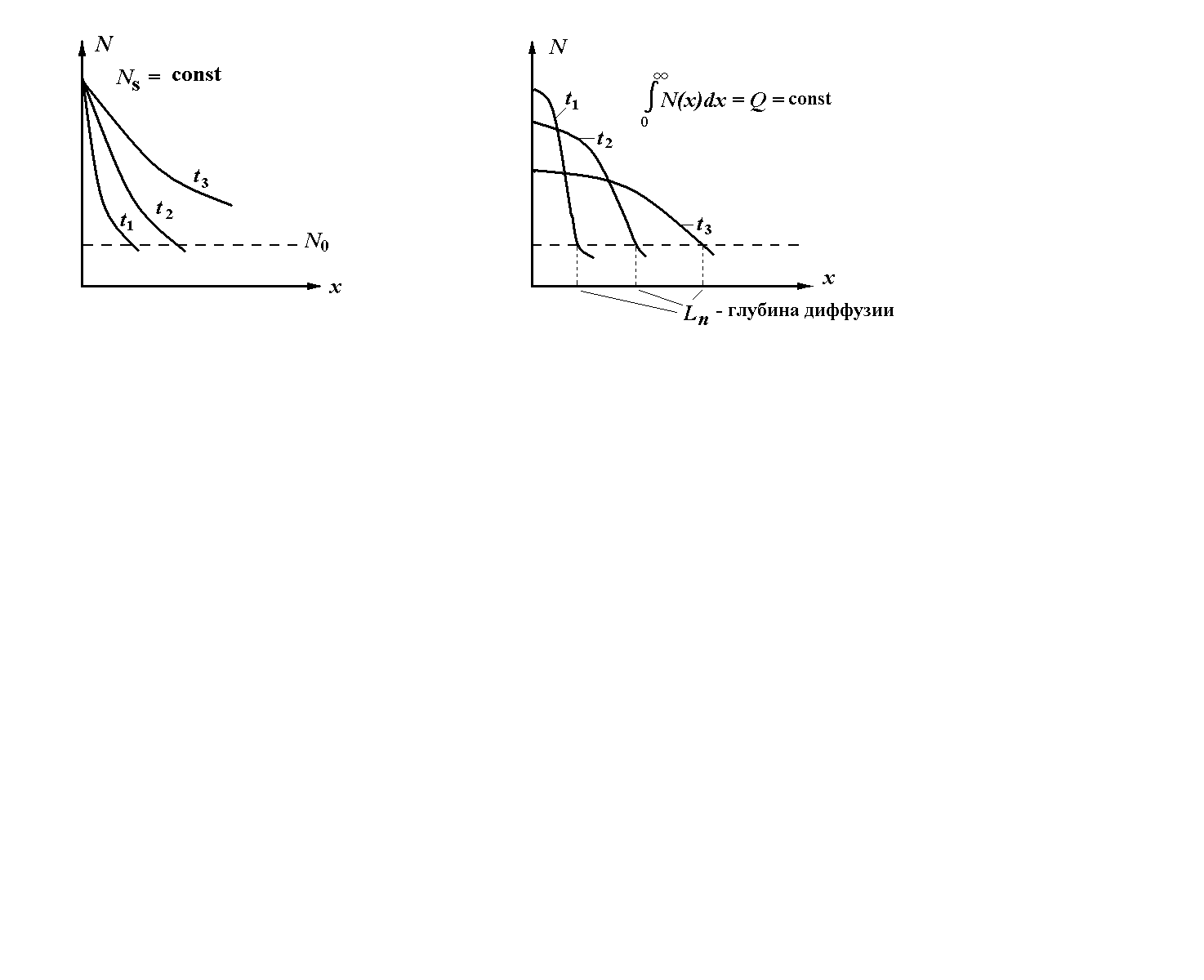
N(x, t) = Ns . erfc [x/(2Dt)] = Ns . erfc(z), (7)
где erfc(z) - дополнительная функция ошибок, близкая к показательной функции 1 – е– z.
Я напомню, что это такое. Из курса математики вы должны знать, что такое интеграл вероятности или функция ошибок:
_ 2
erf(z) = (2/). е–y . dy (8)
0
(связь между z и y мы не будем здесь обсуждать), а дополнительная функция ошибок имеет вид:
erfc(z) = 1 – erf(z) . (9)
Это все относилось к случаю неограниченного источника примеси. А теперь — для ограниченного источника. Решая уравнение (3) при условиях (4) и (6), получаем распределение концентрации при ограниченном источнике (рисунок справа):
___ 2
N(x, t) = [Q /(Dt)]. e –x /(4Dt) . (10)
___
Здесь Q/(Dt) = Ns' — эквивалентная поверхностная концентрация, зависящая от времени. В данном случае концентрация описывается кривой нормального распределения, которая характеризуется нулевой начальной производной, наличием точки перегиба и почти экспоненциальным "хвостом" после этой точки.
Описание процессов диффузии с помощью функции ошибок имеет то свойство, что при многоразовом воздействии различных температур на слой примеси профиль этого слоя качественно не изменится, т.е. он будет описываться тем же математическим выражением, в котором изменяются лишь параметры под знаком erfc.
Тонкий слой, насыщенный атомами примеси, создается обычно путем проведения диффузии первоначально из источника с неограниченным количеством примеси. Интегрируя выражение (7) в интервале 0 х , получим вместо (6)
_ ___
Q = (2Ns/) D1t1 . (11)
Учитывая выражения (8), (9) и (11), можно получить зависимость для распределения атомов примеси в полупроводнике при двухстадийной диффузии:
___________
N(x, t) = (2Ns/) (D1t1) / (D2t2) exp [–x2/(4D2t2)], (12)
– 13 – Лекция 4–5
где D1 и t1 — коэффициент диффузии и время ее проведения на первой стадии "загонки" примеси в тонкий полупроводниковый слой; D2 и t2 — коэффициент диффузии и время ее проведения на второй стадии "разгонки" примеси из тонкого слоя. Разумеется, уравнение (12) справедливо при условии D2t2 >> D1t1, иначе нельзя считать, что на второй стадии диффузия идет из ограниченного источника. (Матсон, с. 127.)
Коэффициент диффузии (Тилл и Лаксон, с. 72)
При повышении температуры кристалла растет энергия атомов диффундирующей примеси, поэтому увеличивается и скорость их движения сквозь решетку. Как мы знаем, коэффициент диффузии связан с температурой следующей зависимостью:
D = D 0 . e–Q/(kT) .
Рассматривая вместо D его натуральный логарифм, получим:
lnD = (1/T) . (–Q/k) + lnD0.
Если построить график зависимости lnD от 1/Т (такие координаты называются координатами Аррениуса), то получится прямая с отрицательным наклоном. Экспериментальные данные показывают то же самое (см. рисунок).
(Конец лекции 4)
Лекция 5
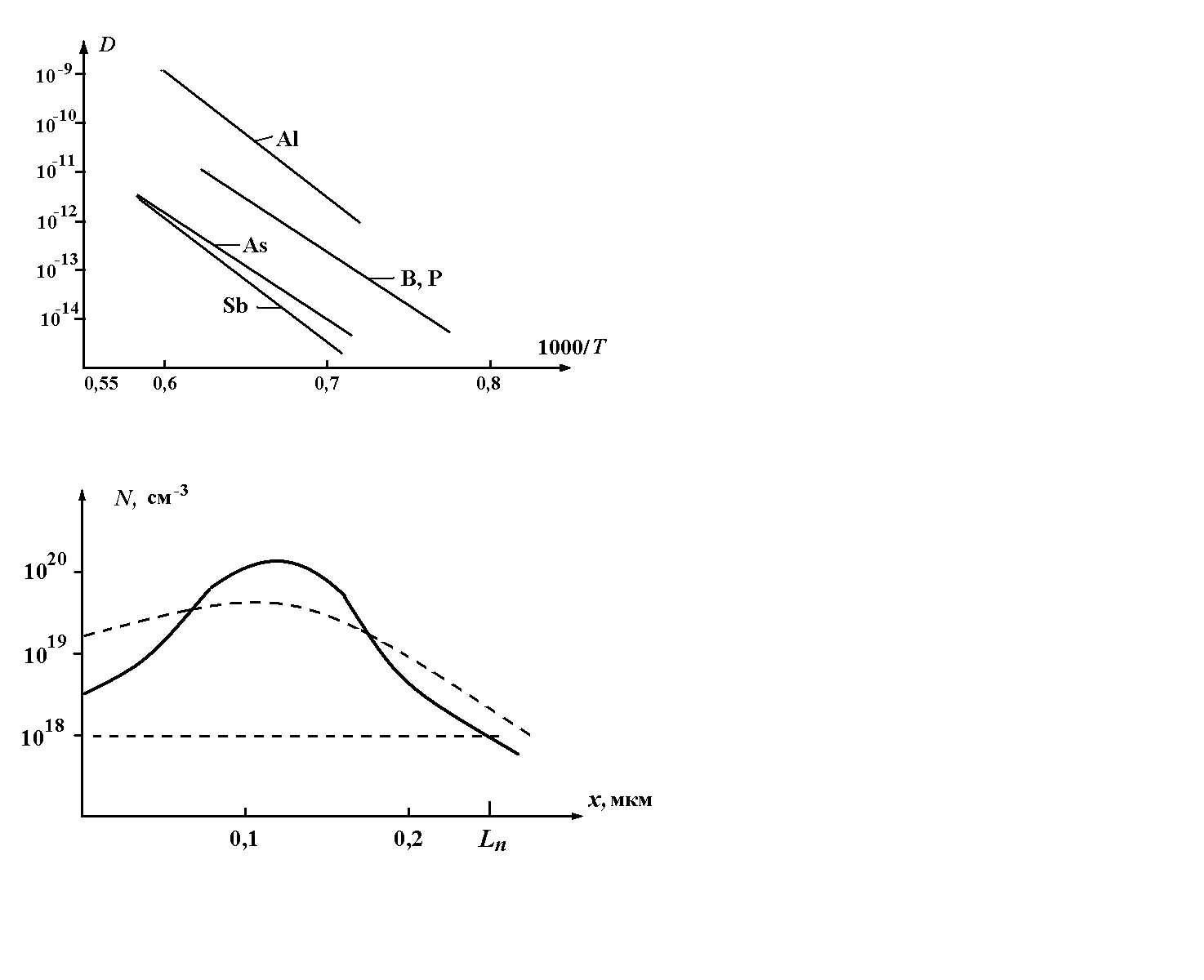
Температура фигурирует в показателе степени уравнения, а это значит, что коэффици-ент диффузии, а с ним и ее скорость, очень чувствительны к изменению температуры. Колебания температуры всего лишь в пределах нескольких градусов могут разрушить базу транзистора. Поэтому в полупроводниковой промышленности температуру диффузии регулируют с точностью до 0,25 С вплоть до 1250 С.
При обычных условиях легирования коэффициент диффузии не зависит от концентрации. При более высоких уров-нях легирования он растет вместе с концентрацией примеси.
В качестве возможных добавок n-типа в производстве ИС используются фосфор, cурь-ма и мышьяк. К счастью, у разных примесей очень разные коэффициенты диффузии. Из рисунка видно, что коэффициент диффузии фосфора раз в 10 больше, чем у сурьмы или мышьяка. Это одна из причин, по которым для эмиттерной диффузии применяют фосфор. В свою очередь, сурьма или мышьяк могут применяться в качестве добавок n-типа в эпи-таксиальные слои пластин ИС именно в силу их малой скорости диффузии. При проведе-нии изолирующей, базовой и эмиттерной диффузии эпитаксиальный n-слой будет слабо диффундировать в подложку р-типа из-за малого коэффициента диффузии этих примесей.
Ионная имплантация (Составлено по книге Степаненко, с. 166)
Ионной имплантацией называют метод легирования пластины (или эпитаксиального слоя) путем бомбардировки ионами примеси, ускоренными до энергии, достаточной для
их внедрения в глубь твердого тела. Ионизация атомов примеси, ускорение ионов, и
– 14 – Лекция 5
фокусировка ионного пучка осуществляются в специальных установках типа ускорителей частиц в ядерной физике. Примесями служат те же материалы, что и при диффузии.
Глубина внедрения ионов зависит от их скорости и массы. Чем больше энергия, тем больше получается толщина имплантированного слоя. Однако с ростом энергии возрастает и количество радиационных дефектов в кристалле, т.е. ухудшаются его электрофизические параметры. Поэтому энергию ионов ограничивают величиной 100–150 КэВ. При таком диапазоне энергий глубина слоев лежит в пределах 0,1–0,4 мкм, т.е. она значительно меньше типичной глубины диффузионных слоев.
Концентрация примеси в имплантированном слое зависит от плотности тока в ионном пучке и времени процесса или, как говорят, от времени экспозиции. В зависимости от плотности тока и желательной объемной концентрации время экспозиции составляет от нескольких секунд до 3–5 минут и более (иногда до 1–2 часов). Опять же, чем больше время экспозиции, тем больше количество радиационных дефектов.
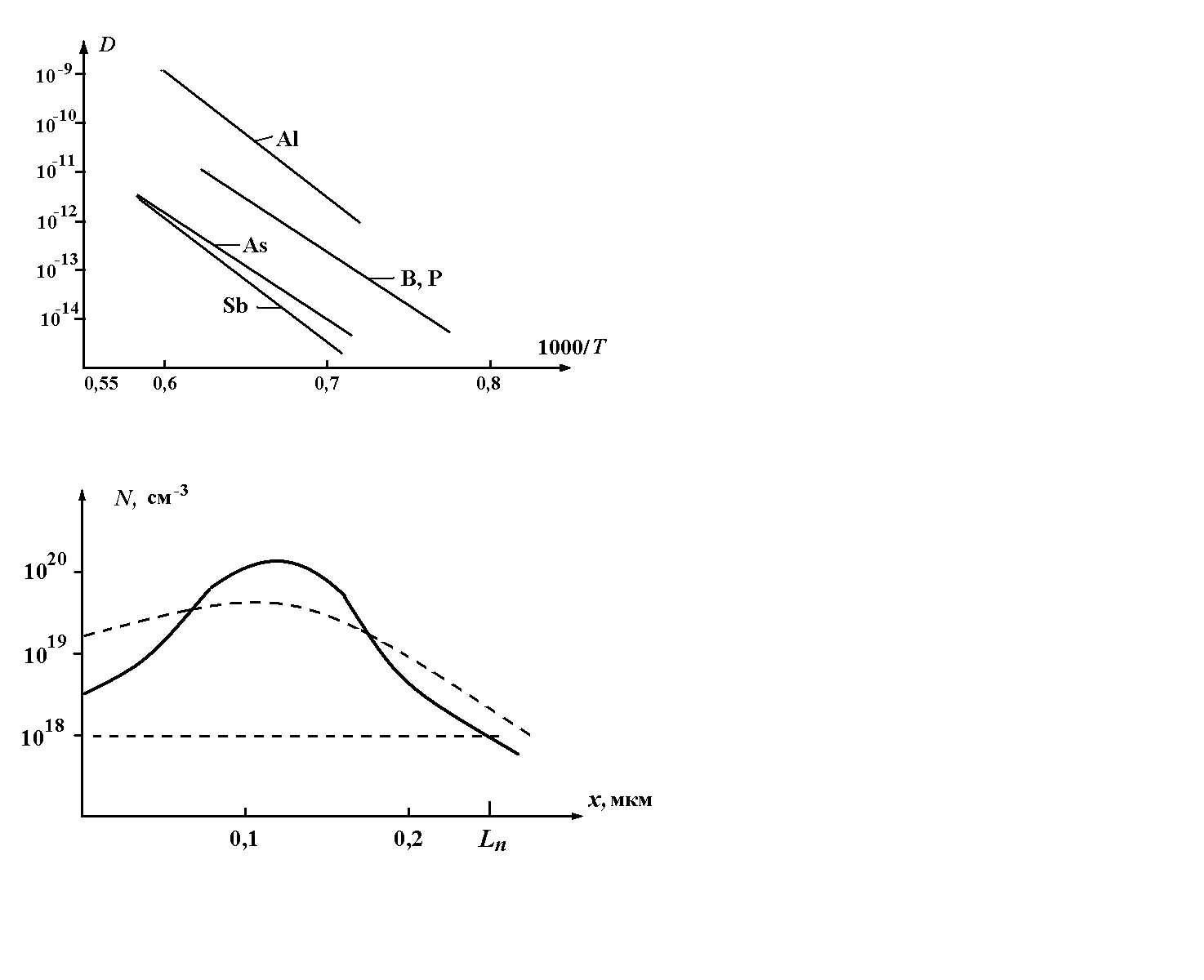
Профиль концентрации примеси
в функции от глубины при ионном внедрении (сплошная линия — сразу после имплантации, штриховая — после отжига).
Типичное распределение примеси при ионной имплантации показано на рисунке сплошной кривой. Как видно, это распределение существенно отличается от диффузионного наличием максимума. Вблизи максимума кривая хорошо аппроксимируется функцией Гаусса.
Поскольку площадь ионного пучка (1–2 мм2) меньше площади пластины (а иногда и кристалла), приходится сканировать пучок, т.е. плавно или шагами перемещать его (с помощью специальных отклоняющих систем) поочередно по всем "строкам" пластины, на которых расположены отдельные ИС.
По завершении процесса легирования пластину обязательно подвергают отжигу при температуре 500–800 С, для того чтобы упорядочить кристаллическую решетку кремния и устранить (хотя бы частично) неизбежные радиационные дефекты. При температуре отжига процесс диффузии несколько меняет профиль распределения.
Ионная имплантация, как и диффузия, может быть общей и локальной (избирательной). В последнем, более типичном, случае, облучение (бомбардировка) проводится через маски, в которых длина пробега ионов должна быть значительно меньше, чем в кремнии. Материалом для масок могут служить распространенные в ИС двуокись кремния и алюминий. При этом важным достоинством ионной имплантации является то, что ионы, двигаясь по прямой линии, внедряются только в глубь пластины, а аналогия боковой диффузии (под маску) практически отсутствует.
В принципе ионную имплантацию, как и диффузию, можно проводить многократно, "встраивая" один слой в другой. Однако сочетание энергий, времен экспозиции и режимов отжига, необходимое для многократной имплантации, оказывается затруднительным. Поэтому ионная имплантация получила главное распространение при создании тонких одинарных слоев.
– 15 – Лекции 5–6
Главными достоинствами ионной имплантации являются: низкая температура процесса и его хорошая контролируемость, а также отсутствие боковых дефектов. Недостатки: неглубокие профили, повреждения кристаллической решетки (необходимость последующего отжига) и громоздкость оборудования.
Таким образом, можно считать, что диффузия и ионная имплантация — это два дополняющих друг друга, а не конкурирующих метода.
И еще следует сказать об одной особенности ионного внедрения (Тилл, с. 89). В монокристаллической мишени типа кремния существует множество каналов, по которым может пройти внедренный ион. Вдоль этих каналов, из-за открытой структуры решетки, вероятность ионно-ядерного столкновения оказывается намного меньше. Если падающий пучок имеет направление с малым кристаллографическим индексом, то из-за каналирования пробег ионов увеличивается в 2–3 раза. Каналирования в процессе обработки полупроводников стараются избегать, поскольку в этом случае распределение примеси чувствительно ко многим факторам и плохо регулируется. С каналированием борются, поворачивая падающий пучок ионов так, чтобы его направление не совпадало с каналами в решетке.
Термическое окисление
(Маллер и Кейминс —- с. 92–101, Пичугин и Таиров — с. 260-269, Зи-1 — с. 174-222, Тилл — с. 203–208, Степаненко — с. 15–161, Калниболотский, ... , Рогоза — с. 7–8)
Окисление кремния — один из самых важных процессов в технологии ИМС. Получаемая при этом пленка двуокиси кремния (SiO2) выполняет несколько важных функций, в том числе:
- функцию защиты — пассивации поверхности и, в частности, защиты вертикальных участков р-n-переходов, выходящих на поверхность;
- функцию маски, через окна которой вводятся необходимые примеси;
- функцию тонкого диэлектрика под затвором МОП-транзистора.
Такие широкие возможности двуокиси кремния — одна из причин того, что кремний
стал основным материалом для изготовления полупроводниковых ИМС.
Поверхность кремния всегда покрыта "собственной" окисной пленкой, получающейся в результате "естественного" окисления при самых низких температурах. Однако эта пленка имеет слишком малую толщину, чтобы служить защитой чистому кремнию (5 нм — это пара десятков атомных расстояний). Поэтому в технологии ИМС пленки SiO2 получают искусственным путем.
Лекция 6
Получение слоев окисла
Окисел кремния можно осадить путем пиролитического разложения кислородно-кремниевых соединений или вырастить из самой кремниевой основы термическим процессом. (Пиролиз — нагрев без доступа воздуха с химической реакцией.) Очевидным преимуществом пиролитического процесса является отсутствие необходимости подвергать пластину воздействию высокой температуры, порядка 1100 С, которая необходима для процесса термического выращивания. Но полученные термически слои кремния, как правило, ровнее и более высокого качества. Они используются в некоторых случаях избирательного окисления для получения изоляции. Пиролитическое разложение проводится в печах, похожих на эпитаксиальные реакторы, но при более низких температурах.
– 16 – Лекция 6
В процессе термического выращивания окиси расходуется исходный кремний. Толщина выращенного слоя окисла примерно в 2,27 раза больше толщины слоя затраченного на это кремния. В основе выращивания окиси кремния лежит простая химическая реакция, которая проходит на поверхности соприкосновения Si – SiO2:
Si + O2 SiO2.
Рост происходит на поверхности контакта Si и SiO2, поэтому (Степаненко, с. 260) должна происходить диффузия О2 через уже существующий слой окисла. Ясно, что скорость роста окисла со временем должна убывать, так как новым атомам кислорода приходится диффундировать через все более толстый слой окисла. Полуэмпирическая формула, связывающая толщину окисной пленки со временем термического окисления, имеет вид: __
d k t ,
где k - параметр, зависящий от температуры и влажности кислорода.
Если использовать влажный (т.е. пропущенный через воду при 95 С) кислород, то реакция будет такова:
Si + 2Н2О SiO2 + 2Н2.
Это уравнение не дает детального описания всего процесса. Как уже говорилось, молекулы воды склонны диссоциировать в окиси кремния, образуя так называемые немостовые гидроксильные группы. Вблизи поверхности ионы гидроксила образуют с атомами кремния группы Si - O - Si, при этом высвобождается водород. Молекулы Н2 улетучиваются и могут по дороге вступать в реакцию с мостовыми ионами кислорода, образуя немостовые гидроксильные группы, а от этого структура кварцевого стекла ослабевает и становится пористой.
Скорость роста слоя окисла в атмосфере влажного кислорода примерно в 10 раз превосходит скорость его роста в атмосфере сухого кислорода. Частично это получается из-за большего коэффициента диффузии D воды, а частично — из-за более высокой твердой растворимости воды в SiO2 (3.1019 молекул/см3 для воды, 5,2.1016 молекул/см3 для О2 при 1000 С и 1 атм). Твердая растворимость как раз и определяет поверхностную концентрацию диффузанта, и вместе с коэффициентом диффузии — также и скорость диффузии примеси в окисел. Скорость роста окисла первоначально ограничена скоростью химической реакции на поверхности кремния. После того как вырастет достаточно толстый слой, скорость дальнейшего роста ограничена скоростью диффузии.
В атмосфере сухого, а не влажного кислорода происходит крайне быстрый начальный рост слоя окисла. Так как толщина окисла в затворе МОП-транзистора достигает всего лишь несколько сот ангстрем, этот феномен очень важен. Здесь следует сказать, что в технологии ИМС различают "толстые" и "тонкие" окислы SiO2. Толстые окислы (0,7 0,8 мкм) выполняют функции защиты и маскировки, а тонкие (0,06 0,2 мкм) — функции подзатворного диэлектрика в МОП-транзисторах.
Реальные значения времени окисления для типовых процессов: для выращивания пленки SiO2 толщиной 0,5 мкм в сухом кислороде при 1000 С требуется около 5 часов, а во влажном — всего 20 мин. С уменьшением температуры на каждые 100 С время окисления возрастает в 2-3 раза.
Создание межсоединений (Степаненко, ОМ — с. 181-183)
Чтобы изготовить ИС, нужно соединить друг с другом проводящими дорожками отдельные приборы, полученные с помощью планарной технологии. Нужно сделать также контактные площадки для подведения к ним выводов из корпуса микросхемы. Все эти процедуры носят общее название: создание межсоединений (interconnections) или металлизация, или фотогравировка.
– 17 – Лекция 6
Основным материалом для металлизации служит алюминий. Он оказался оптимальным в силу следующих положительных качеств: малое удельное сопротивление; хорошая адгезия к окислу SiO2 (металлизация осуществляется по окислу); возможность получения сварных контактов с алюминиевой и золотой проволокой (при осуществлении внешних выводов); отсутствие коррозии; пластичность; низкая стоимость, и др.
При создании металлической разводки сначала на всю поверхность ИМС напыляют сплошную пленку алюминия толщиной около 1 мкм. Эта пленка контактирует со слоями кремния в специально сделанных (с помощью предыдущей фотолитографии) окнах в окисле. Основная часть алюминиевой пленки лежит на поверхности окисла. Покрывая пленку алюминия фоторезистом, экспонируя его через соответствующий фотошаблон и проявляя, получают фоторезистную маску, которая защищает будущие полоски металлизации и контактные площадки от травителя. После вытравливания алюминия с незащищенных участков и удаления фоторезиста остается запланированная металличе-ская разводка. Ширина полосок в обычных ИМС составляет 10–15 мкм, а в больших ИС — до 5 мкм и менее. Погонное сопротивление полоски шириной 10 мкм и толщиной 1 мкм составляет около 2 Ом/мм. Для контактных площадок, к которым в дальнейшем присоединяются внешние выводы, типичны размеры 100 100 мкм. Присоединение
внешних выводов непосредственно к полоскам металлизации невозможно из-за их малой ширины.
Разумеется, рисунок межсоединений предполагает отсутствие пересечений, т.е. коротких замыканий. Однако в ИС с большой степенью интеграции не удается спроектировать металлическую разводку так, чтобы избежать пересечений. В этих случаях используется многослойная или многоуровневая разводка, т.е. несколько этажей металлизации, разделенных изолирующими слоями. Необходимые соединения между разными уровнями осуществляются через специальные окна в изолирующих слоях. Изоляцию между слоями обычно обеспечивают путем напыления диэлектрика по завершении очередной металлической разводки. В качестве диэлектрика чаще всего используют моноокись кремния SiO. Количество этажей при многоуровневой металли-зации для современных БИС лежит в пределах от 2 до 4.
Как вам поступить в вашей курсовой работе, если вы не можете сделать однослойную разводку без пересечений? Надо провести диффузионную перемычку (Коледов, с. 27). Так д
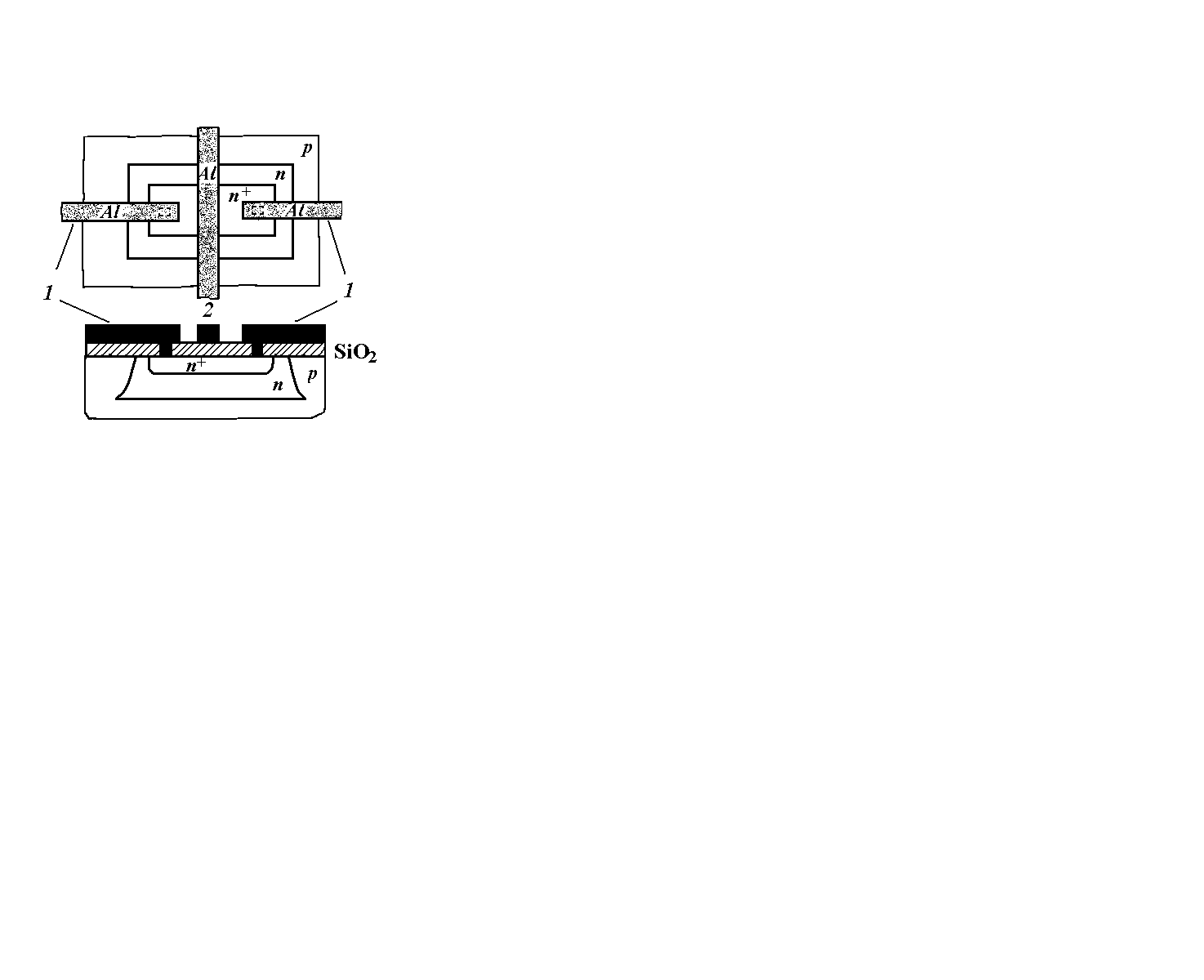
проводников, первый из которых расположен поверх
защитного окисла, а второй "подныривает" под него
в виде участка n+-слоя. Этот участок имеет заметное
сопротивление (3–5 Ом), вносит дополнительную
паразитную емкость и занимает сравнительно большую
площадь (для него делается отдельная изолированная
область), поэтому диффузионной перемычкой пользуются в исключительных случаях. Диффузионные перемычки не применяют в цепях питания, в которых идут большие токи.
Проблема омических контактов при использовании алюминия состоит в следующем. Если пленку алюминия просто напылить на поверхность кремния, то образуются барьеры Шоттки, причем, барьер на границе с n-слоем является не омическим, а выпрямляющим. Чтобы избежать барьеров Шоттки, алюминий вжигают в кремний при температуре около 600 С. При этом на границе алюминиевой пленки с кремнием образуется слой, в котором растворен практически весь прилегающий алюминий. После застывания сплав представляет собой кремний, легированный алюминием; концентрация последнего составляет около 5.1018 см-3.
– 18 – Лекции 6–7
Поскольку алюминий является акцептором по отношению к кремнию, возникает новая проблема: предотвращение образования р-n-переходов в слоях. Действительно, если концентрация доноров в n-слое меньше 5.1018 см-3, то атомы алюминия создадут в нем приповерхностный р-слой. Чтобы этого избежать, область n-слоя вблизи контакта специально легируют, превращая ее в n+-слой с концентрацией доноров 1020 и более. Тогда концентрация алюминия оказывается недостаточной для образования р-слоя, и р-n-переход не образуется.
Если n-слой с самого начала сильно легирован (например, эмиттерный слой транзистора), то дополнительного легирования не требуется. Не возникает проблем и при контакте алюминия с р-слоями, так как растворение в них алюминия приводит к образованию приповерхностных р+-слоев, что способствует повышению качества омического контакта.
(Конец лекции 6)
Лекция 7
Способы изоляции приборов в интегральных схемах (Степаненко, с. 194-)
Если не принимать специальных мер изоляции элементов, находящихся на одной пластине, они окажутся связанными друг с другом через легированную (т.е. проводящую) подложку. Поэтому элементы биполярных ИМС нужно изолировать друг от друга, с тем, чтобы необходимые соединения осуществлялись только путем металлической разводки. Кстати, далее будет показано, что в униполярных ИС изоляции элементов друг от друга, вообще говоря, не требуется.
Все известные способы изоляции можно разделить на два основных типа: изоляция обратно-смещенным р-n-переходом и изоляция диэлектриком. Различие это не столько количественное, сколько структурное. Изоляция р-n-переходом — двухфазный способ, поскольку материал подложки отличается от материала изолятора.
Изоляция р-n-переходом сводится к реализации двух встречно включенных диодов между изолируемыми элементами. Для того чтобы оба изолирующих диода находились
под обратным смещением, на подложку задают максимальный отрицательный потенциал о
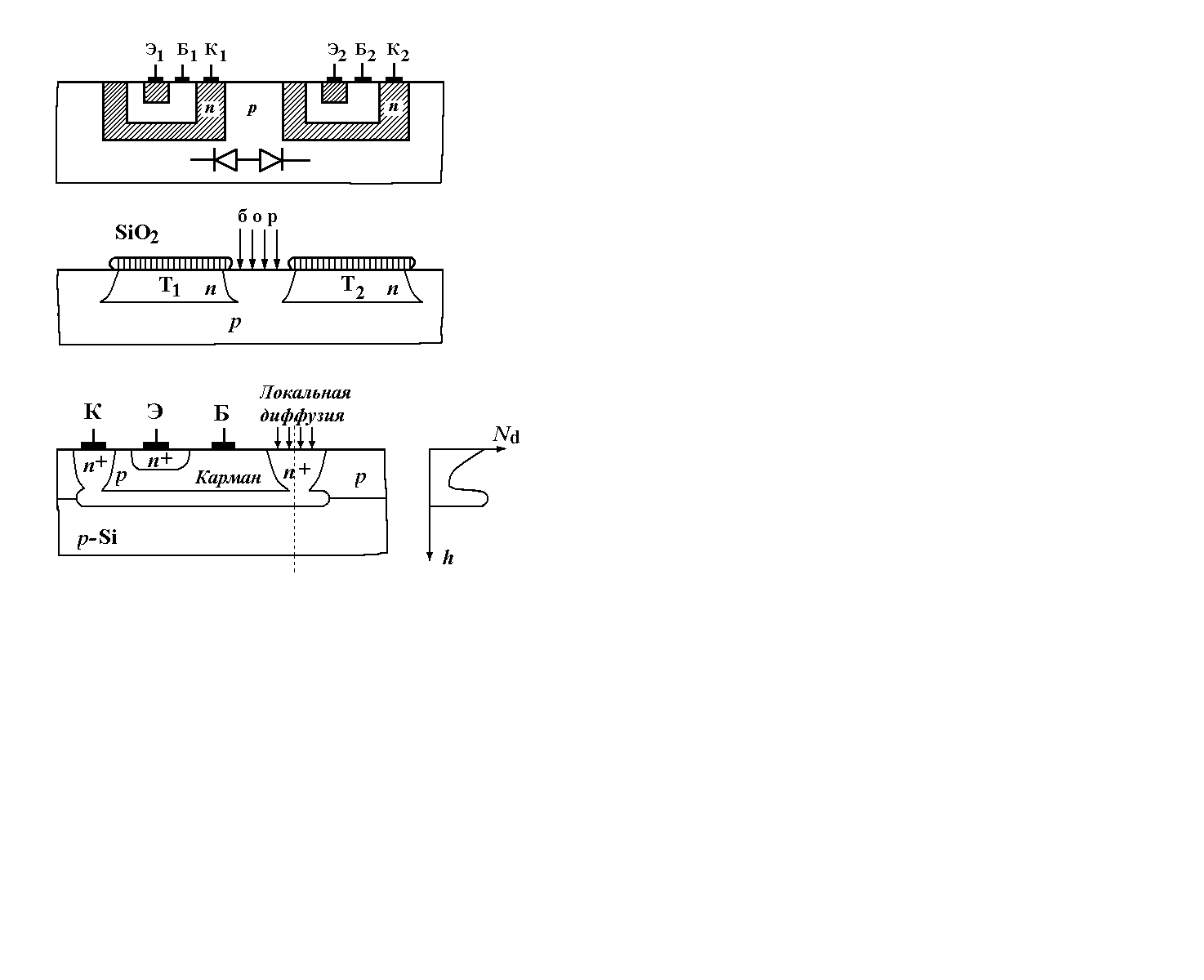
Как делается такая изоляция? Надо сказать, что сплошные проводящие подложки в настоящее время уже не используются. Делают эпитаксиальный слой на высокоомной (низколегированной) подложке.
С помощью диффузии примеси через окна в слое окисла (между транзисторами) в эпитаксиальном слое делают разделения. Островки n-типа, оставшиеся в эпитаксиальном слое после разделительной диффузии, называют карманами.
– 19 – Лекция 7
Один из вариантов разделительной диффузии обратно-смещенными р-n-переходами — изоляция коллекторной диффузией (ИКД). Данный способ используется, когда под небольшим (несколько микрон) эпитаксиальным слоем р-типа (базовая область)
р
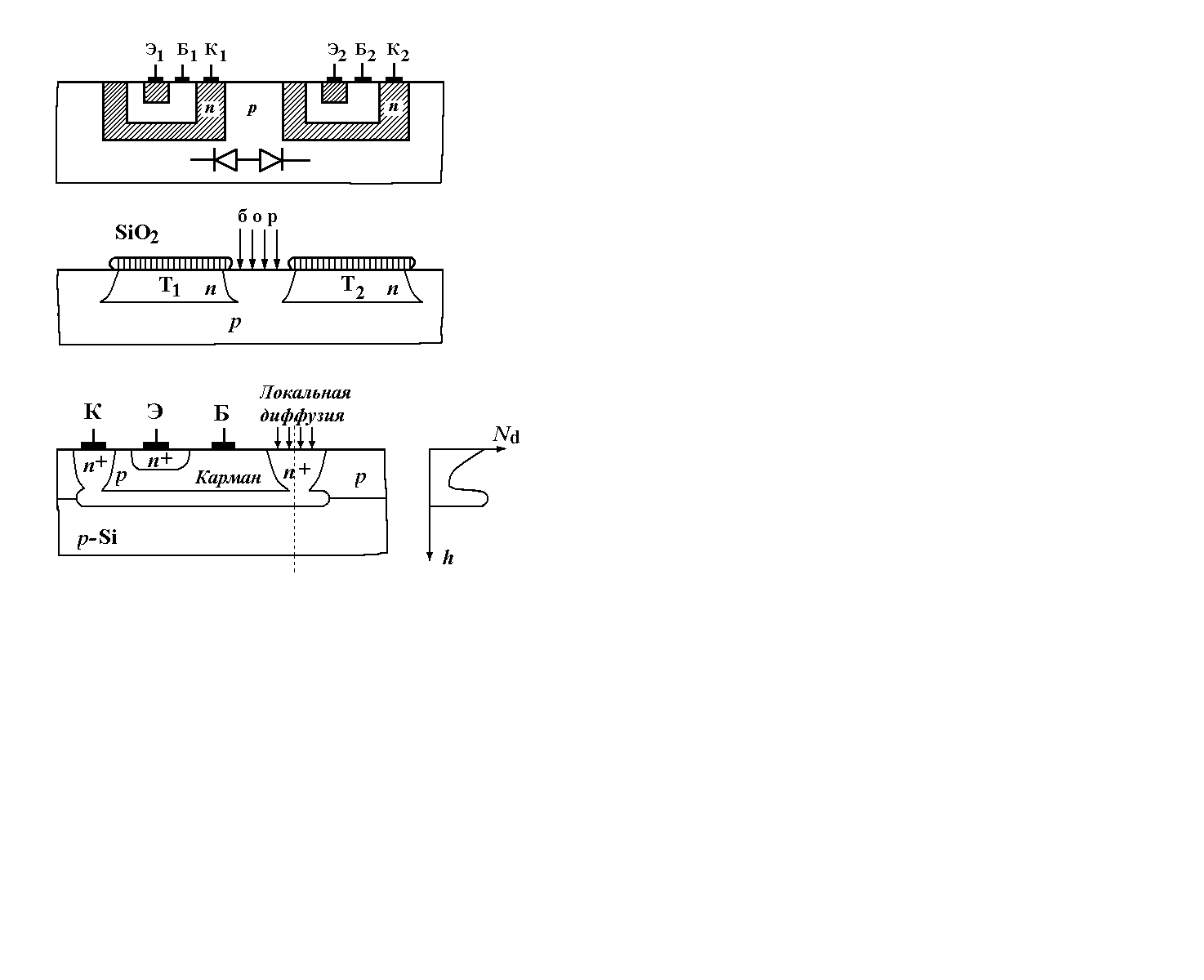
Изоляция диэлектриком (Степаненко, ОМ, с. 200)
Широко известен способ, называемый "эпик-процессом", схема которого приводится
ниже.
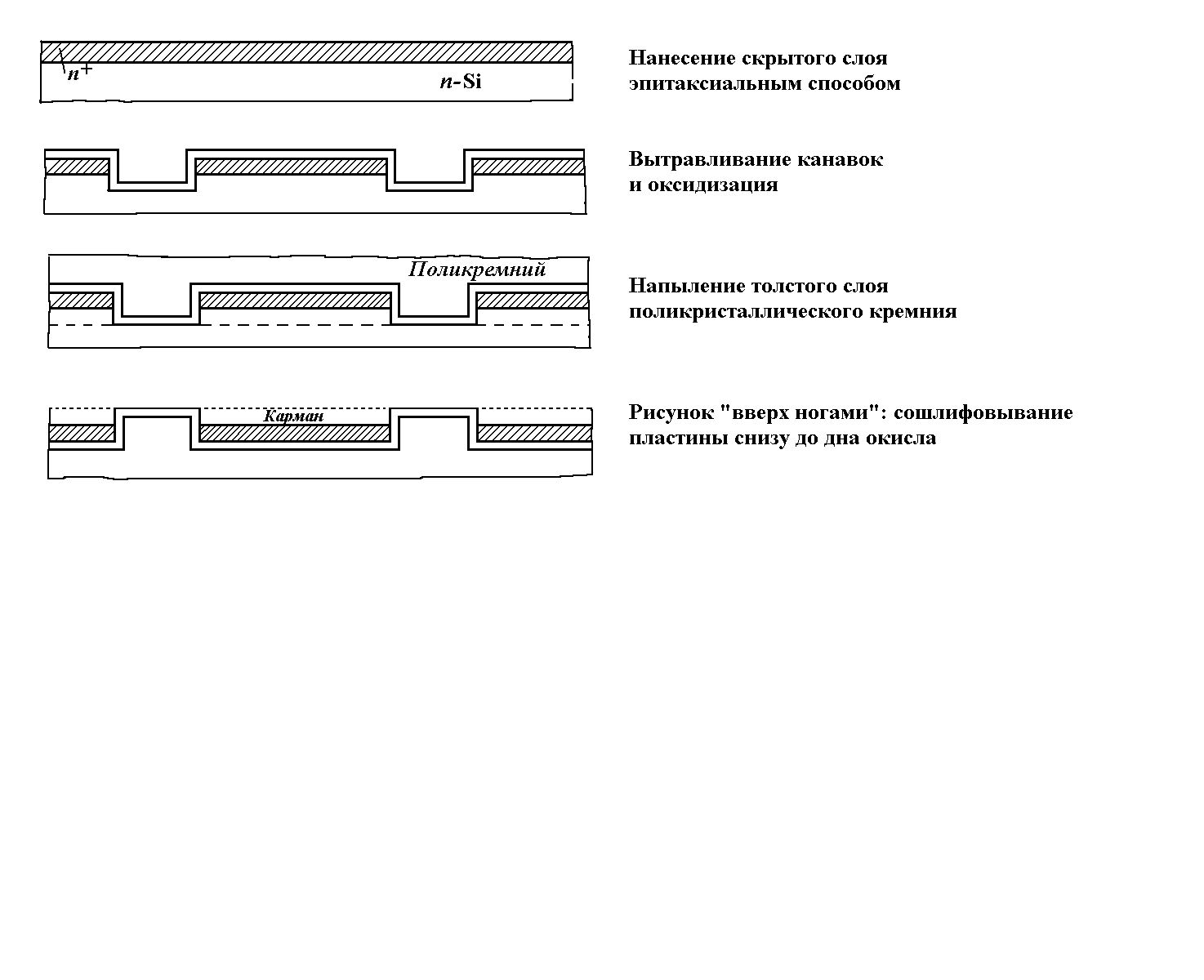
Если вместо поликремния напылять изоляционную керамику, качество изоляции получается лучше, но технология — сложнее.
Другие виды изоляции: кремний на сапфире (КНС) - ОМ, с. 200 и рис. 7.9; изопланарная технология, рис. 7.10; изоляция V-канавками, рис. 7.11. Все эти виды изоляции используются в настоящее время различными предприятиями-изготовителями ИМС. "Изопланары" хорошо описаны у Коледова, с. 30–34.
Кроме того, статус лекций имеют оба методических пособия — по расчету пассивных элементов и по расчету транзисторов. Пассивные элементы изложены частями на лабораторных занятиях, а транзисторы — как отдельные 2 лекции. Весь материал является сокращенным изложением полного курса по микроэлектронике, читавшегося 10 лет назад на нашей специальности. Полный конспект есть у Терешина М.А.
(Конец лекции 7)
– 20 –
Лекция 8
Раздел 3. БИПОЛЯРНЫЕ ТРАНЗИСТОРЫ (Коледов, с. 11)