Нормирование точности и технические измерения курсовая работа Шифр
Вид материала | Курсовая |
- Экзаменационные вопросы по дисциплине «Нормирование точности и технические измерения», 20.38kb.
- Нормирование точности зубчатых колес, 105.1kb.
- Преподаватель: Енгалычев Александр Нинельевич, 47.03kb.
- Аннотация дисциплины «Взаимозаменяемость и нормирование точности», 4.86kb.
- Программа учебной дисциплины "Допуски, посадки и технические измерения " предназначена, 164.04kb.
- Рабочая программа дисциплины сд. 07. 03. «Стандартизация и технические измерения» (код, 206.39kb.
- Курсовая работа по дисциплине «Технология приборостроения», 388.53kb.
- Учебно-методический комплекс по дисциплине «технические измерения и приборы», 64.72kb.
- Программа 2-ой Российской конференции с международным участием «Технические и программные, 381.44kb.
- Курсовая работа на тему "Качественные и количественные характеристики информации Свойства, 215.02kb.
Министерство образования РБ
Белорусско-Росийский Университет
Кафедра”Технология машиностроения”
НОРМИРОВАНИЕ ТОЧНОСТИ
И
ТЕХНИЧЕСКИЕ ИЗМЕРЕНИЯ
Курсовая работа
Шифр:
Выполнил:ст.гр.АХЗ
Проверил:
Могилёв,2004
СОДЕРЖАНИЕ
1. Допуски цилиндрических зубчатых колёс………………………3
1.1 Исходные данные……………………………………………….3
1.2 Назначение степеней точности зубчатых колёс………………3
1.3 Выбор вида сопряжения по боковому зазору…………………3
1.4 Назначение комплексов показателей для контроля зубчатого колеса………………………………………………………………….4
2. Расчёт посадок с зазором………………………………………….8
3. Выбор универсальных измерительных средств…………..……..10
4. Расчет размерной цепи методом полной взаимозаменяемости .……………………………………………………………………...…11
Список ипользуемой литературы………………………………13
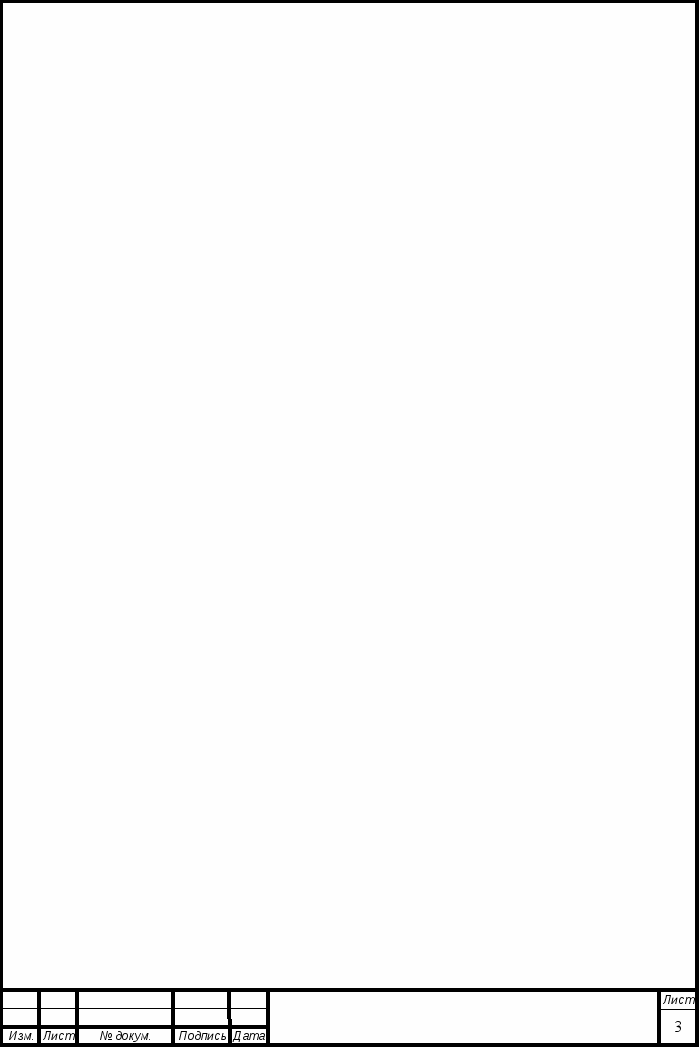
1.1 Из таблицы 2(1)выписываем исходные данные зубчатой передачи:
число зубьев большого колеса z1=24;число зубьев малого колеса z2=20;окружная скорость V,м/с-11;модуль m,мм-3,5.
Геометрические параметры зубчатой передачи:
делительный диаметр большого колеса
d1=m*z1=3.5*24=84 мм
делительный диаметр меньшей окружности
d2=m*z2=3.5*20=70 мм
межосевое расстояние
aw=m*(z1+z2)/2=3.5*(24+20)/2=77 мм
ширина зубчатого венца В=(8…10)m=(8…10)3.5=(28…35) мм
Принимаем В=30 мм ;
диаметр посадочного отверстия зубчатого колеса ориентировочно принимаем:
D = m*z1/3=3.5*24/3=28 мм
Диаметр соответствует нормальному линейному размеру по ГОСТ 6636-69.
^ 1.2 Назначение степеней точности зубчатой передачи.
По окружной скорости передача относится к среднескоростным. По таблице3(1) степень точности по норме плавности-6.Используя принцип комбинирования, назначаем 7-ю степень точности по кинематической точности. Степень точности полноты контакта-6.
По таблице 3 шероховатость рабочей поверхности зубьев Ra,мкм-0.63.
^ 1.3Боковой зазор-это зазор между нерабочими профилями зубьев. Величину бокового зазора, необходимого для размещения смазки, ориентировочно можно определить:
In min.расч. =Vсмазки =0.02*3.5=0.07 мм для среднескоростных передач.
По найденному значению In min.расч и межосевому расстоянию aw по таблице 13
По ГОСТ 1643-81 выбираем вид сопряжения по боковому зазору –С
In min.расч=74 мкм ≥ In min.расч =70 мкм
^ 1.4 Назначение комплексов показателей для контроля зубчатого колеса.
Нормы точности на зубчатые колёса и передачи представляют собой набор требованиё к точности геометрических и кинематических параметров зубтых колёс и передач для оценки этой точности в отношении определённого эксплуатационного признакам.
Называются эти нормы:
нормы кинематической точности
- нормы плавности работы
- нормы полноты контакта зубьев
- нормы бокового зазора
В нормах кинематической точности нормируются требования к таким геометрическим и кинематическим параметрам колеса и передачи, погрешность которого влияет на погрешность передаточного отношения за полный оборот колеса,т.е.характерезует погрешность в узле поворота за один его оборот по сравнению с тем, если бы вместо него находилось абсолютно точное колесо.
В нормах плавности работы нормируются требования к точности таких геометрических и кинематических параметров колеса и передач, погрешность которых также влияет на кинематическую точность, но эта погрешность проявляется многократно за один оборот колеса, т.е. один или несколько раз на каждом зубе. Эти требования имеют наибольшее значение для передач, работающих на больших скоростях, поскольку такие погрешности являются источником ударов, приводящих к появлению шума и вибрации.
В нормах контакта нормируются требование к таки геометрическим и кинематическим параметрам колёс и передач, погрешность которых влияет на величину площади поверхности касания при вращении зубьев сопрягаемых колес.
Требование к контакту поверхностей имеют особо ванное значение для передач, работающих с большими нагрузками.
В нормах бокового зазора нормируется требования к таким параметрам колес и передач, которые влияют на зазор по нерабочим профилям зубьев при соприкосновении по рабочим профилям зубьев.
Эти нормы важны для передач, работающих в тяжелых температурных условиях, при большой загрязненности и для реверсивных передач.
В соответствии с ГОСТ1643-81 и рекомендации изложенные в таблице 4(1) назначаем комплексы контроля большого колеса z1=24 колеса.
Выписываем из ГОСТ 1643-81 допуски на выбранные показатели и заносим их в таблицу 1.
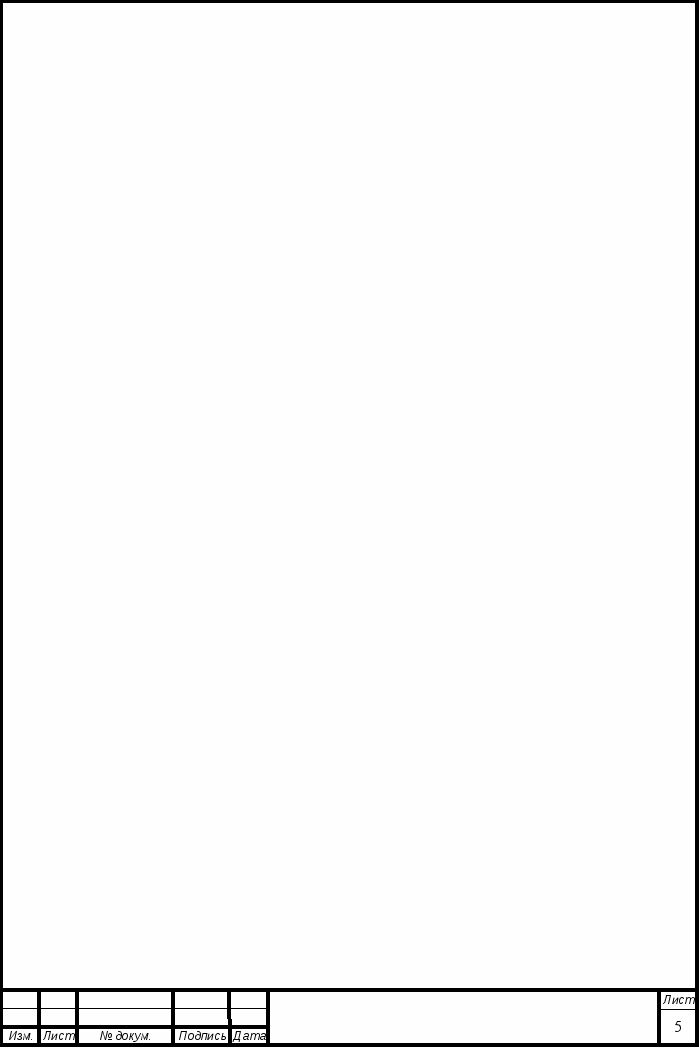
^ Таблица 1.Показатели и приборы для контроля зубчатых колеса.
Нормы точности | Наименование и условное обозначение контролирующего параметра | Условное обозначение и численное значение допуска, м | Наименование и модель прибора |
Кинематическая точность(степень 7) | Колебания измерительного межосевого расстояния за оборот Fir” Колебания длинны общей нормами Fir | Fi”=0.05 F =0.02 | Прибор для контроля кинематической погрешности БВ-936,межцентромерМИ-320М, нормамер БВ-5045 |
Плавность работы (степень 6) | Колебание измерительного межосевого ратояния одном зубе fir” | Fi”=0.014 | Прибор для контроля измерительного межосевого расстояния МЦ-320М |
Контакт зубьев | Суммарное пятно контакта | %по длине зуба, неменее -70 | Контрольно-обкатные станки, контрольные приспособления в рабочем корпусе |
% по высоте зуба, неменее -50 | |||
Боковой зазор(с) | Смещение исходного контура Тн*, наименьшее дополнительное смещение исходного контура Енs | Тн==0,1 Енs=0.087 | Зубомеры смещения 2301(m=2…10) |
где Fr=36 мкм- допуск на радиальное биение зубчатого колеса по таблице 5.7, стр.317(5) или таблица 6 ГОСТ 1643-81.из таблицы справочника на стр.360(5)определяем длину общей нормали для зубчатого колеса с модулем m=1,z1=24,W1=7.71645 по среднему столбцу таблицы.
Определим длину общей нормали
W=m*W1=3.5*7.71645=27.007575
Из ГОСТ 1643-81 или по таблице 5.21 стр.344(5) определяем допуски на длину общей нормали.
Tw =70 мкм при Fr =36мкм
Определяем придельное отклонение на длину обшей нормали. Наименьшее отклонения средней длины общей нормали Ewms определяем по таблице 5.20(5) слагаемое 1 равно 60 мкм ля вида сопряжения С и 6-й степени точности по нормам плавности; слагаемое 2 равно 9 при величине допуска на радиальное биениеFr=36 мкм по таблице 5.7,стр.317(5).Тогда Ewms=60+9=69 мкм. Допуск на среднюю длину общей нормали Twm определяем по таблице 5.21(5) Twm=50мкм для вида сопряжения С и вида допуска бокового размера С.
Нижнее отклонение средней длины общей нормали
(|Ewms|+Twm)=-(69+50)=-119
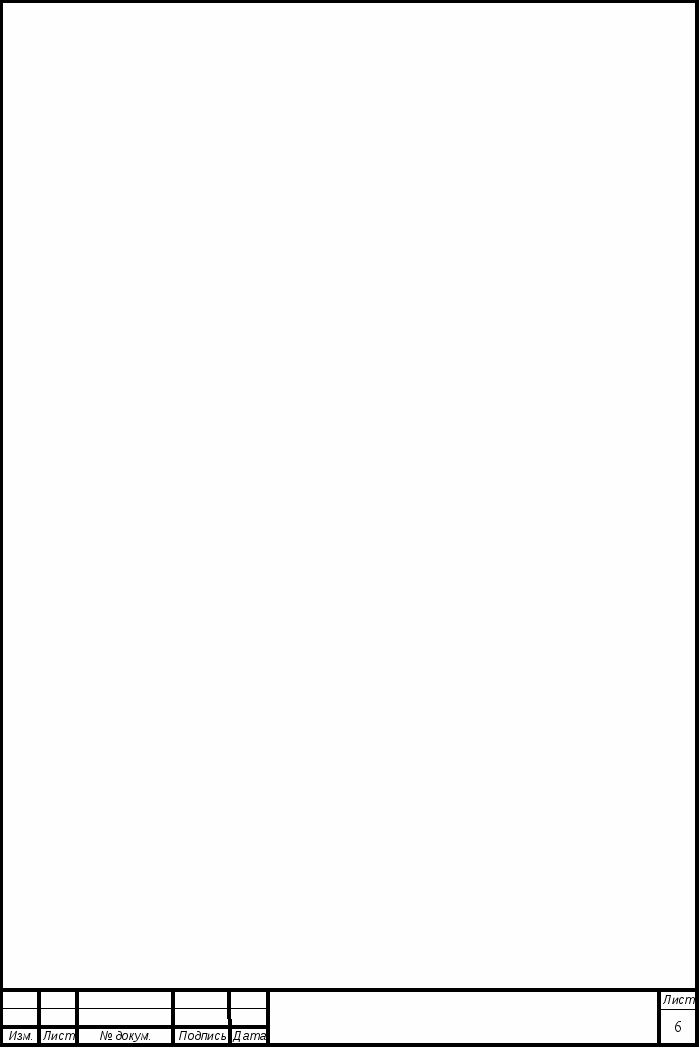
Допуск на размер и форму отверстия (вала)=IT7(IT6)
Допуск на диаметр наружного цилиндра 48.Допуски определены в соответствии с методическими указаниями подтаблицам 5.24,5.25,5.27,(5).Например, допуск на диаметр наружного диаметра цилиндра определен по таблице5.24(требования точности заготовка), гдеуказано значенипо рекомендации NCODR 1328. Для степени точности зубчатых колес 6,7,8 допуск надиаметр наружного цилиндра равен JT8.Допуск на диаметр наружного цилиндра JT8 может быть применен при использовании в качестве базы для контроля размера зуба, или 414-417 СТСЭВ 144-75, но не более 0,1m для 3-7-й степени точности и 0,2m для 8-12-й степени точности. Существует 4 варианта использования наружного цилиндра заготовки. Для вариантов 1,3,4 допуски на диаметр наружного цилиндра назначается, как на свободные размеры – см. таблицу5.26(5,стр. 354)
Радиальное биение наружного цилиндра
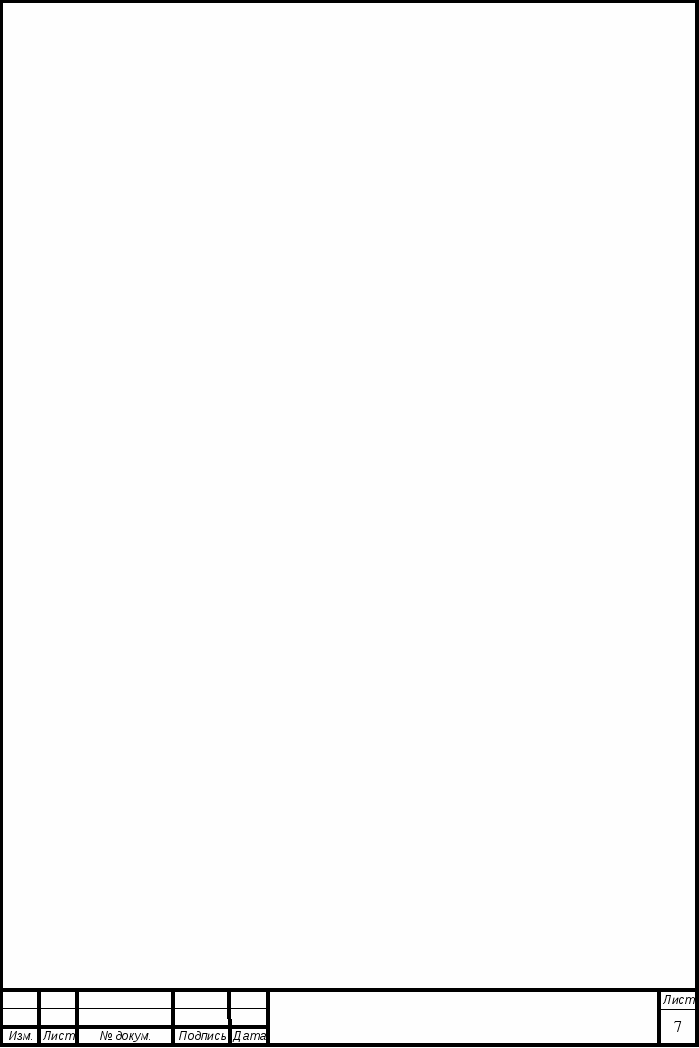
Где dal =d1+2m=84+2*3.54=91мм
Допуск на торцовое биение заготовки Fт=Fт.таб*d1/100=16.8=18мкм
Где Fт.таб –для 6-й степени точности. Выполняем рабочий чертеж колеса на формате А3.
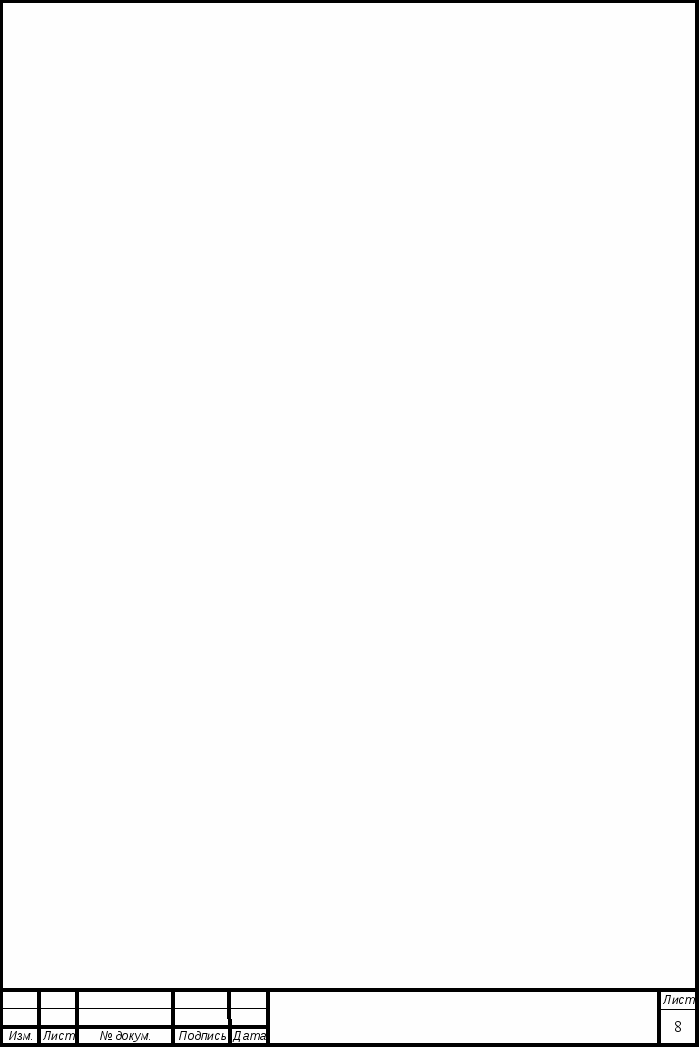
Исходные данные:D=28мм; длина соединения по методическим указаниям принимается равной l=b+5+15=30+5+15=50мм, где b из задачи1, остальные исходные данные выбиваем из таблицы 6(1).Радиальная нагрузкаR=80H; частота вращения вала n1=800 мин-1; марка масла –турбинное Т30 (динамическая вязкость при 500С µ=0,025-0,029 Па*с); Шероховатость вала Rz1=4Ra=4*0.63=2.52мкм
Минимальная толщина масляного слоя, при котором обеспечивается жидкостная смазка hmin =K (Rz1+ Rz2+∆д)=2(2,52+1,6+2)=12,24мкм; где Rж.с. - коэфицент запаса надежности по толщине масляного слоя. опредиляем минимальный расчетный зазор
Smin =2 hmin/1-x=2*12.24/0.5=49мкм
Опредиляем минимальный функциональный зазор
Smin ф. = Smin-2(Rz1+ Rz2) =49-2(2, 52+1, 6) =41мкм
Максимальный функциональный зазор равен
Smax ф=55*10-3*µ*n*l*d3/R* hmin=
55*10-3*0.027*800*0.05*0.0283*103/80*20*10-6=0.814мм
Определим эксплуатационный допуск,учитывая,что конструкторский допускпосадки будет соответсвовать 8-му квалитету.
TSэ= Smax ф- Smin ф.-(TD+Td) =0.841-0.041-(0.033+0.033) =0.734мм
Определим гарантированный запас на эксплуатацию при Кэ=0,8
TSгз.э. = Кэ*TS э=0, 8*0,734=0,587мм
Определим гарантированный запас на сборку при Кс=0,08
TSгз.э= Кс*TS э=0, 08*0,734=0,059мм
Наиболее подходящей посадкой по ГОСТ25347-82 или по таблице3.13(1) будет H8/d8, обеспечивающая S min т ,мкм 0,065> Smax ф
TSз.с =0,024 > TSгз.э=0,059-данное условие не выполняется.
Посмотри другие посадки из ГОСТа:
H9/d9 Smax =168мкм, S min=65мкм, -условие гарантированного запаса также не выполняется.
H7/c8 Smax =164мкм, S min=110мкм- условие гарантированного запаса по сборке TSз.с =0,069 > TSгз.с=0,059-условия выполняется.
Угловая скорость ω =πn/30=3.14*800/30=83.8рад/с
Среднее давление на единицу площади
P=R/(dl)=80/(28*50)=0.057 МПа
Относительные зазоры для Smax ф и S min т
ψ1= S min т/d=0.11/28=0.003928;
ψ2= Smax ф/d =0.814/28=0.02907;
Определяем безразмерные коэффициенты нагружения потшипника для S min т и Smax ф
CR1=P *ψ12/ µ ω =57000*0.0039282/0.027*83.8=0.39
CR2= P* ψ22/µ ω=57000*0.0299072/0.027*83.8=21.3
по таблице16(2) находим относительный эксцентриситет х1=23, х2=0,95.
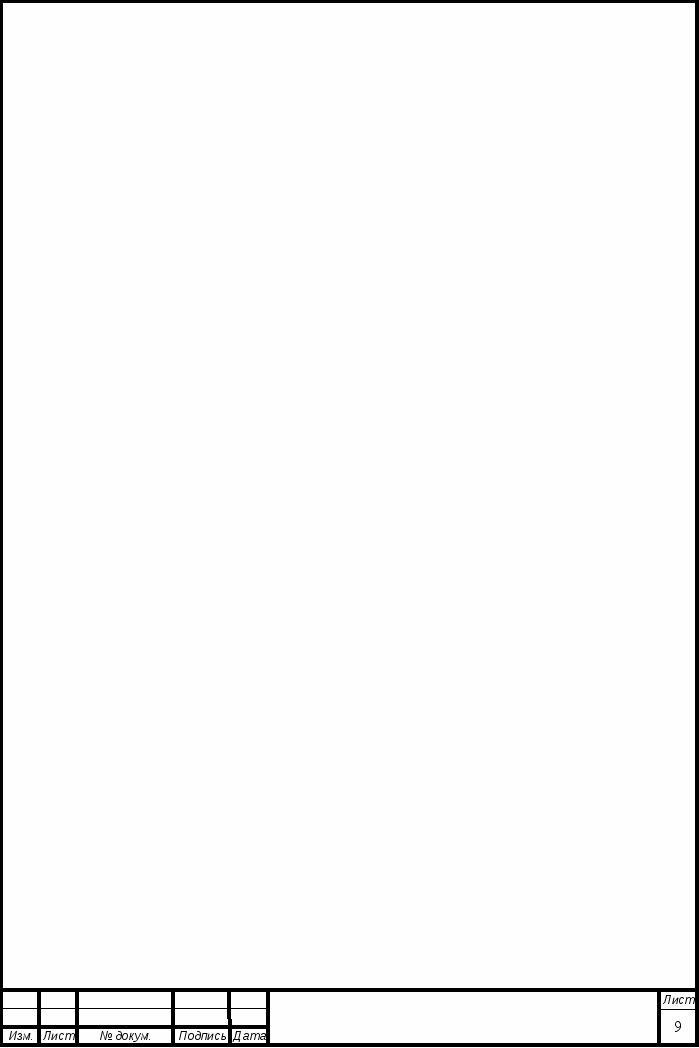
Поэтому для повышения надежности работы соединения задаем Кс=0,1.
Тогда TSгз.с= Кс* TSэ=0,1*0,7340,073мм
В в случае наиболее подходящей будет внесистемная посадка H8/b9,для которой Smax =245мкм, S min=160мкм,
TSзс=0,119мкм, TSз.э=0,569
ψ1= S min т/d=0.16/28=0.00571
CR1=57000*0.005712/0.027*83.8=0.82
По таблице16(2) находим относительный эксцентриситет х1=0,38
Определим минимальную толщину масляного слоя при S min т и Smax ф
h min1= S min т/2(1- х1)=160/2(1-038)=49.6мкм
h min2= S max ф/2(1- х1)=841/2(1-0,95)=20,35мкм
Определим коэффициент запаса надежности по толщине масляного слоя
K1= h min1/(Rz1+ Rz2+h д)=49,6/(2,52+1,6+2)=8>2
K2= h min2/(Rz1+ Rz2+h д)=20,35/(2,52+1,6+2)=3,3>2
Выбранная посадка H8/b9 оптимальная(и единственная внесистемная с необходимыми параметрами), обеспечит надежную работу соединения и имеет достаточный эксплуотационнй запас на износ. Посадка в системе отверстия.
Поля допусков посадок h8/b9, H7/c8, H9/d9 показываем в графической части курсовой работы.
^ 3 Выбор универсальных измерительных средств.
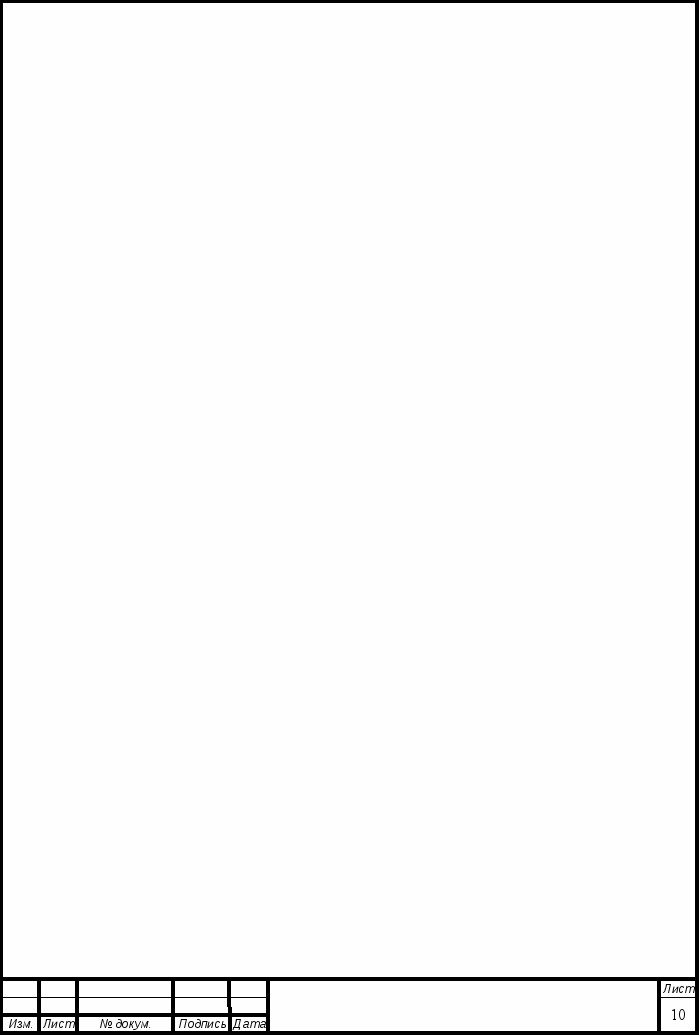
В соответствии с ГОСТ 8.051-81 допускаемая погреешь измерений составляет от20 до 35% допуска на измеряемый размер. В приложении А2(1)приводятся значения допусков и допускаемых погрешностей измерения для квалитетов от 5 до 9 и для размеров от 3 до 315мм.
Отверстие: допуск Т-33 мкм, погрешность δ-8мкм;
вал: допуск Т-52мкм, погрешность δ-12мкм.Выбор технических средств проводим проводим по их техническим характеристикам. Результаты выбора оформляем виде таблицы 2.
Таблица2.Универсальные средства измерения.
Номинальный размерполя допуска | Допуск иделия,мкм | Допуск погрешности измерения, δ, мкм | Наименования средств измерения,модуль,ГОСТ | Цена деления отсчетного устроства, мкм | Педельная погрешность измерения, ±Δ, мкм |
О28H9 | 33 | 8 | Индикаторный нурромер 6-50 ГОСТ 9244-75 | 2 | ±4 |
O28b9 | 52 | 12 | Рычажный микрометр МР100 ГОСТ 4381-68 | 2 | ±3 |
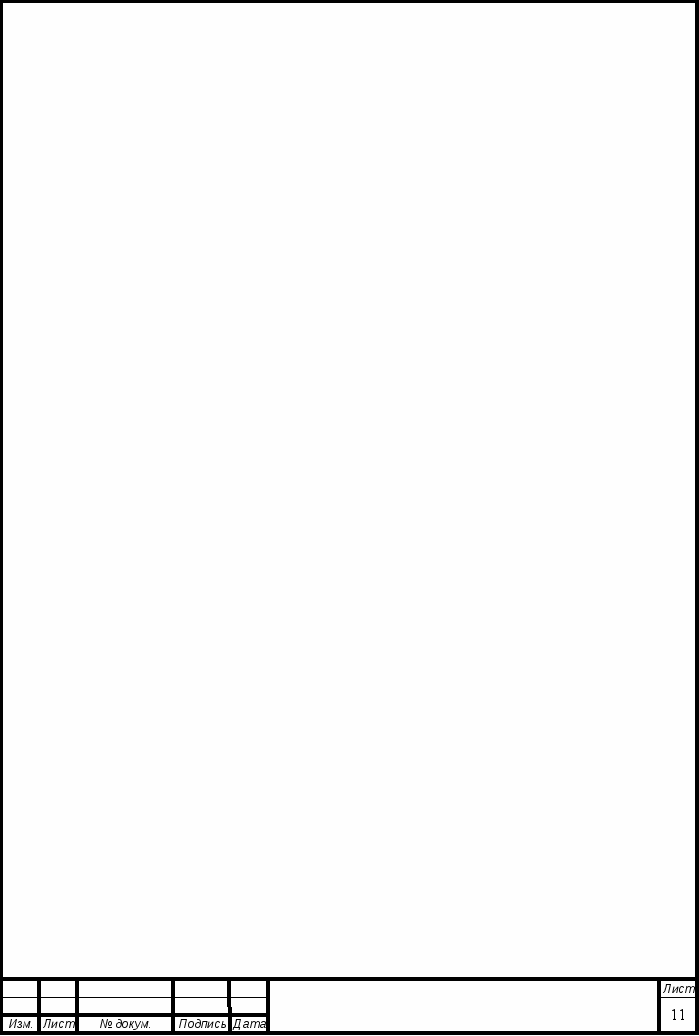
Исходные данные: А Δ, мм – 0…0,96.
Сущность метода состоит в том, что точность замыкающего звена обеспечивается у всех изделий без исключения, изделий, без какого-либо подбора или подгонки.
Записываем параметры замыкающего звена:
А Δ=0+0,96; ЕSА Δ=0; Т А Δ=0,96;
Ес А Δ=( ЕSА Δ+EI А Δ)/2=0.48мм
Составляем размерную цепь по рисунку 2(1), конструктивно определяем номинальное значение составляющих звеньев:
А1+А5=15мм для шарикоподшипника радиального легкой серии №205 ГОСТ 8338-75:
d=25мм, D=52мм, B=15мм, A2=8мм, A3=50мм (из задачи 2), A4=40мм, A6=A8=6мм, A7=140мм.
Данная размерная цепь состоит изодного увеличивающего звена, пяти уменьшающих и двух меж центровых (не относящиеся к валу или отверстию) размеров.
А Δ= Аiyв- Аiyм;
Где n-число увеличивающих звеньев; р - число уменьшающих звеньев.
Проверяем правильность определения номинальных значений звеньев.
А Δ =А7-(А1+А2+А3+А4+А5+А6+А8)=140-(15*2+8+50+40+6*2)=0
Определяем средние значения допусков составляющих звеньев
TAicp=T А Δ/m-1=0.96/9-1=0.120мм.
По номинальным размерам составляющих звеньев, используя ГОСТ 25347-82, корректируем полученное средне значение допусков.
ТА1=ТА5=0,12мм допуск при классе точности PG для подшипников определяем по таблице4.82(5); ТА2=0,090мм; ТА3=0,100мм; ТА4=0,100мм; ТА6=ТА8=0,120мм; ТА7=0,190.
Проверим правильность корректировки допусков
0,96=0,12+0,09+0,1+0,1+0,12+0,120,19+0,12=0,96
Придельные отклонение составляющих звеньев, кроме звена 7:
ESA1=0мм, EIA1=-0.120мм, ESA2=0мм, EIA2=-0.090мм, ESA3=0мм, EIA3=-0.100мм,
ESA4=0мм, EIA4=-0.100мм, ESA5=0мм, EIA5=-0.120мм,
ESA6=0,060мм, EIA6=-0.060мм,
ESA8=0,060мм, EIA8=-0.060мм.
Координаты средин полей допусков составляющих звеньев кроме 7;
Ec1=-0.060мм, Ec2=-0.045мм, Ec3=-0.050мм, Ec4=-0.050мм, Ec5=-0.060мм, Ec6,8=-0мм,
Координаты средины поля допуска звена :
ЕсΔ=Ес7-Ес1-Ес2-Ес3-Ес4-Ес5-Ес6-Ес8;
Ес7= ЕсΔ+Ес1+Ес2+Ес3+Ес4+Ес5+Ес6+Ес8=0,48-0,060-0,045-0,050-0,050-0,060=0,215мм.
Придельное отклонение звена 7:
EIA7=0,215-0,5*0,19=-0.120мм;
ESA7=0,215+0,5*0,19=0,310мм.
Результаты расчета:
А1=15-0,120; А2=8-0,090; А3=50-0,100; А4=40-0,100; А5=15-0,150; А6=6±0,060; А7=+0,320+0,120; А8=6±0,060.
Проверка правильности расчетов :
ЕSА Δ= Ес7-Ес1-Ес2-Ес3-Ес4-Ес5-Ес6-Ес8+(ТА1+ТА2+ТА3+ТА4+ТА5+ТА6+ТА7+ТА8)/2;
+0,96=0,215+0,060+0,045+0,050+0,050+0,060+(0,120+0,090+0,100+0,100+0,120+0,120+0,190+0,120)/2=+0,96;
ЕIА Δ= Ес7-Ес1-Ес2-Ес3-Ес4-Ес5-Ес6-Ес8+
+(ТА1+ТА2+ТА3+ТА4+ТА5+ТА6+ТА7+ТА8)/2.
0=0,215+0,060+0,045+0,050+0,050+0,060--(0,120+0,090+0,100+0,100+0,120+0,120+0,190+0,120)/2=0
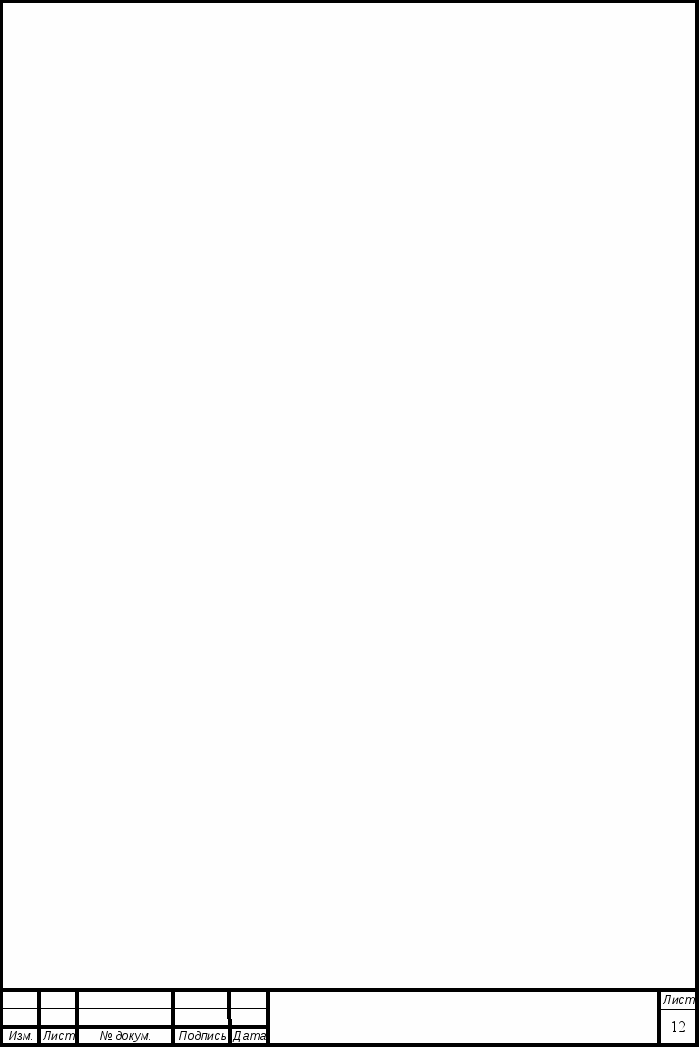
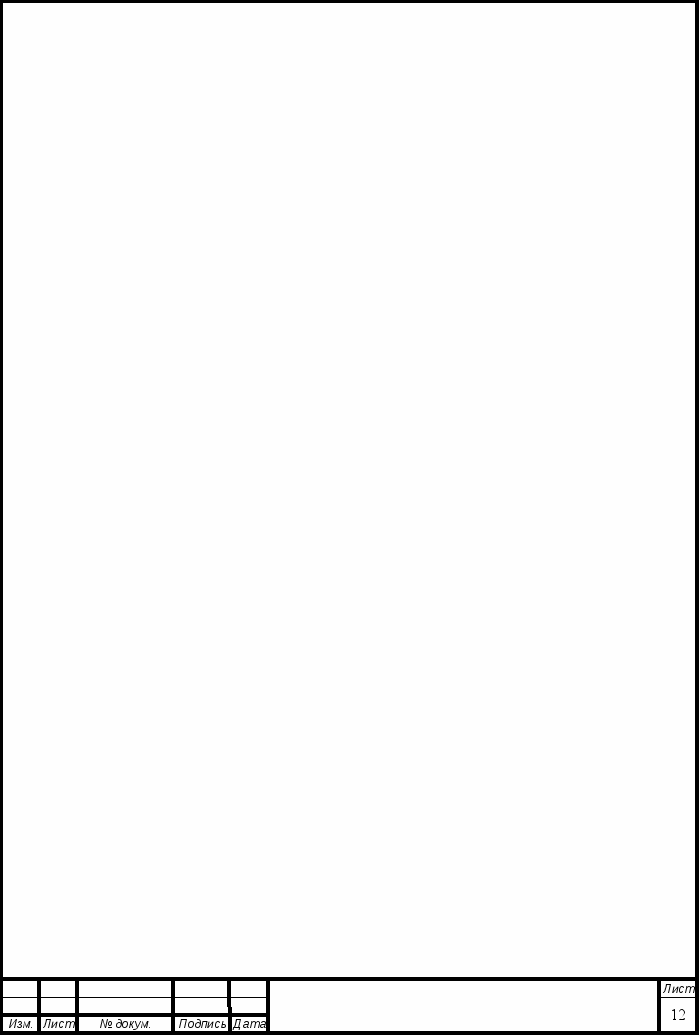
1 Нормирование точности и техническое измерение. Методические указания для студентов всех специальностей заочного факультета. Могилев, ММИ 1997г.
2 Якушев А.И. Взаимозаменяемость, стандартизация и технические измерения.3-е изд. перераб. и доп.-М.: Машиностроение, 1974г
3 Справочник машиностроительного завода. Допуски, посадки, линейные измерения, А.Н.Виноградов, Ю.А. Воробьёв, Л.В. Воронцов и др. 3-е изд. перераб. и доп.-М.: Машиностроение, 1980г
4 Единая система допусков и посадок СЭВ в машиностроение и приборостроение: Справочник в 2т – 2-е изд. перераб. и доп.-М.:Издательство стандартов. 1989г
5 Допуски и посадки .Справочник в 2-х ч. М.А. Полей ,А.Б.Романов, В.А. Брагинский 6-е изд. перераб. и доп.-Л. Машиностроение Ленинградское отделение, 1983г
6 Якушев А.И. Взаимозаменяемость, стандартизация и технические изменения.Учебник для втузов 6-е изд. перераб. и доп.-Л. Машиностроение, 1987г
7 Лукашенко В.А., Шадуро Р.Н. Расчет точности механизма Учебное пособие по курсу “Взаимозаменяемость, стандартизация и технические изменения” для студентов машиностроительных специальностей. – Могилев: ММИ, 1992г