Конспект лекций «материаловедение»
Вид материала | Конспект |
Содержание4.2. Твердые фазы в металлических сплавах 4.2.1. Твердые растворы В располагаются в междоузлиях решетки растворителя А 4.2.2. Химические соединения 4.3. Влияние сплавления на свойства металлов |
- Конспект лекций по теме: «Материаловедение» для специальности 120100 "Технология, 104.18kb.
- Конспект лекций по теме: «Материаловедение» для специальности 120100 "Технология, 5022.76kb.
- Е. в конспект лекций «материаловедение» ч. 1 конспект, 33.7kb.
- Конспект лекций «материаловедение», 249.86kb.
- Конспект лекций 2008 г. Батычко В. Т. Административное право. Конспект лекций. 2008, 1389.57kb.
- Конспект лекций 2010 г. Батычко Вл. Т. Муниципальное право. Конспект лекций. 2010, 2365.6kb.
- Конспект лекций «материаловедение», 123.26kb.
- Конспект лекций 2011 г. Батычко В. Т. Семейное право. Конспект лекций. 2011, 1718.16kb.
- Конспект лекций 2011 г. Батычко Вл. Т. Конституционное право зарубежных стран. Конспект, 2667.54kb.
- Конспект лекций «материаловедение», 197.98kb.
© СЗТУ кафедра МТМиП, Шадричев Е.В конспект лекций «МАТЕРИАЛОВЕДЕНИЕ» ч.1
Глава 4. СТРОЕНИЕ И СВОЙСТВА МЕТАЛЛИЧЕСКИХ СПЛАВОВ
4.1. ОСНОВНЫЕ ПОНЯТИЯ
В главе 1 отмечалось, что технические металлы имеют низкую прочность, и одним из наиболее общих методов ее повышения является создание сплавов. Очевидно, что метод сплавления позволяет получить и более широкий диапазон специфических полезных свойств (например, жаропрочность, коррозионную стойкость, износостойкость и др.).
Сплавы - это материалы, полученные сплавлением или спеканием (порошковая металлургия) двух или более компонентов.
Компоненты - вещества, образующие сплав; ими могут быть химические элементы или устойчивые химические соединения.
Структура сплава и его свойства определяются в первую очередь типом фаз, которые образуются при сплавлении компонентов. Очевидно, что любой химический элемент может находиться в зависимости от температуры (и давления) 8 твердой, жидкой или газообразной фазах. Эти фазы отличаются агрегатным состоянием вещества. Химические элементы - однокомпонентные системы. Многокомпонентные системы - сплавы - и в твердом состоянии могут иметь сложное, многофазное строение. Уточним понятие твердой (в смысле кристаллической, в отличие от жидкой) фазы в таких системах.
Фаза - однородная по всем характеристикам (химический состав, тип решетки, свойства) и обособленная (отделенная поверхностью раздела) часть сплава.
^ 4.2. ТВЕРДЫЕ ФАЗЫ В МЕТАЛЛИЧЕСКИХ СПЛАВАХ
В зависимости от характера ;физико-химического взаимодействия компонентов в металлических сплавах могут присутствовать три основных типа твердых фаз: 1) химические элементы, 2) твердые растворы, 3) химические соединения.
Если какое-либо взаимодействие между компонентами А и В (химические элементы) при сплавлении отсутствует, то в затвердевшем сплаве они присутствуют в виде изолированных кристаллов, образуя двухфазную механическую смесь. Каждый такой кристалл, следовательно, является однокомпонентной фазой, т. е. химическим элементом с присущими ему кристаллическим строением и свойствами, которые обсуждались в главе 1. Поэтому здесь более подробно следует рассмотреть строение и свойства многокомпонентных1 фаз - твердых растворов и химических соединений.
^ 4.2.1. Твердые растворы
Твердые растворы - фазы, в которых атомы одного компонента (В) размещены (растворены) в кристаллической решетке другого компонента (А - «растворителя»). По мере увеличения количества растворенных атомов В в решетке А химический состав и свойства твердого раствора плавно изменяются (в частности, температура плавления). Таким образом, твердый раствор - фаза переменного состава. Количество растворенных атомов (предел растворимости) в твердом растворе зависит от индивидуальных свойств компонентов А и В и, обычно, - температуры.
Сплав, представляющий собой твердый раствор, является однофазным веществом € решеткой, присущей основному компоненту (растворителю). Атомы второго компонента (растворенного) размещены в решетке растворителя, как правило, случайным, неупорядоченным образом.
По способу размещения |атомов растворенного вещества (В) в решетке растворителя (А) различают два основных типа твердых растворов - растворы замещения и внедрения (рис. 4.1).
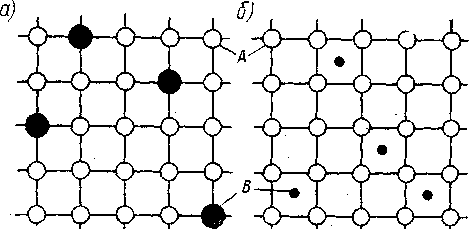
Рис. 4.1. Твердые растворы замещения (а) и внедрения (б)
Видно, что при образовании твердых растворов замещения (рис. 4.1,а) атомы В располагаются в пустых узлах (вакансиях, см. раздел 1.2) решетки компонента А, т. е. «замещают» ее собственные атомы. Количество атомов В в решетке А в этом случае может изменяться в широких пределах. Возможна даже неограниченная (100%-ная) взаимная растворимость компонентов в твердом состоянии, если выполняются следующие условия: 1) кристаллические решетки компонентов А и В однотипны (изоморфны); 2) размеры атомов А и В отличаются не более, чем 1на 10...15 %; 3) близкое строение внешних электронных оболочек атомов А и В.
В случае твердых растворов внедрения (рис. 4.1,6) атомы ^ В располагаются в междоузлиях решетки растворителя А. Понятно, что это возможно, если размеры ^томов В сравнимы с размерами межатомных пустот решетки А. Поэтому растворы внедрения образуют первые четыре элемента таблицы Менделеева (Н, В, С, N), имеющие малый диаметр, приблизительно 0,15 нм, с металлами, у которых атомы, а значит и межатомные пустоты, достаточно велики - например, переходными металлами с атомным диаметром примерно 0,25 нм.
Твердые растворы внедрения всегда имеют ограниченную растворимость, так как ограничены размеры (и количество) межатомных пустот. Из-за несоответствия размеров пустот с размерами размещающихся в них атомов возникают упругие искажения решетки, препятствующие дальнейшему растворению.
^ 4.2.2. Химические соединения
Вторым типом двухкомпонентных фаз в сплавах являются химические соединения. В типичных химических соединениях преобладают ионный или ковалентный типы межатомных связей. Такие соединения характеризуются следующими признаками:
1) определенным соотношением чисел атомов элементов (компонентов) А и В в соединении, которое соответствует формуле АпВт, где п и т - простые числа;
2) различием кристаллической решетки соединения и решеток исходных компонентов (атомы А и В в решетке АпВт расположены упорядоченным образом);
3) определенными свойствами (в частности, постоянной температурой плавления), существенно отличающимися от свойств исходных компонентов. Если в сплаве химический состав отклоняется от заданного формулой АпВт, свойства резко изменяются.
Все эти признаки отличают такие соединения от твердых растворов.
Следует, однако, сказать, что классические химические соединения, строго удовлетворяющие всем этим требованиям, не играют большой роли в металлических сплавах. Обычно это неметаллические включения (оксиды, сульфиды), которые образуются в сплавах в процессе их производства и присутствуют в небольших количествах.
Большое значение в металлических сплавах имеют соединения, в которых в значительной мере присутствует металлический тип связи. Специфика такой связи - ненаправленность и ненасыщенность (см. стр. 6, 10), - приводит к тому, что эти соединения отличаются рядом особенностей - они не подчиняются правилу валентности (см. стр. 10) и имеют переменный состав. Эти особенности сближают такие соединения с твердыми растворами. Подобные соединения относят к промежуточным фазам, их существует несколько типов. В сталях, например, наибольшее значение имеют такие разновидности промежуточных фаз, как фазы внедрения.
Фазы внедрения - это промежуточные фазы, образуемые переходными металлами (М: Fе, Мn, W, Тi, ...) с элементами (X), имеющими малый атомный радиус (X: Н, N, B, С). Т. е. это гидриды, нитриды, бориды, карбиды. Величина их атомных радиусов удовлетворяет соотношению rх/rм<0,59. В этом случае атомы неметалла способны размещаться в межатомных пустотах решетки металла в значительных количествах. Фазам внедрения можно приписать химическую формулу типа МХ (например, WС, FеВ, ТiС), М2Х (W2С, Fе2В), М4Х (Fе4N). Однако они имеют переменный состав (подобно твердым растворам). Состав, отвечающий химической формуле, характеризует лишь максимально возможную концентрацию неметалла в соединении. Тип кристаллической решетки фаз внедрения не совпадает с типом решетки исходного металла (как при образовании классических химических соединений).
Для дальнейшего важно отметить, что химические соединения независимо от их природы, как правило, более тверды и хрупки (менее пластичны), чем твердые растворы тех же компонентов (подробнее об этом в следующем разделе).
^ 4.3. ВЛИЯНИЕ СПЛАВЛЕНИЯ НА СВОЙСТВА МЕТАЛЛОВ
В сплаве - твердом растворе атомы растворенного компонента (В) являются точечными дефектами решетки растворителя (А). Это очевидно из сравнения рис. 4.1 и рис. 1.6.
Следовательно, растворенные атомы В искажают решетку основного металла А, вызывают в ней внутренние напряжения. Внутренние напряжения, как известно (глава 1), тормозят скольжение дислокаций, затрудняют пластическое деформирование металла, т. е. повышают его прочность. Упрочняющее влияние растворенных атомов проявляется еще и в том, что они скапливаются в растянутой области решетки под дислокацией, взаимодействуют с ней, делают ее малоподвижной. Для движения дислокации необходим отрыв ее от примесного облака, что требует дополнительных усилий, т. е. опять-таки повышает прочность.
Таким образом, сплавление, приводящее к образованию твердого раствора, само по себе вызывает повышение прочности исходного металла (растворителя А). Очевидно, что эффект упрочнения в этом случае должен в основном определяться концентрацией К растворенных атомов В и степенью искажения решетки растворителя А, создаваемого каждым атомом В. Степень искажения решетки растворителя обычно выражают параметром несоответствия радиусов атомов растворителя rА и растворенного компонента rВ .
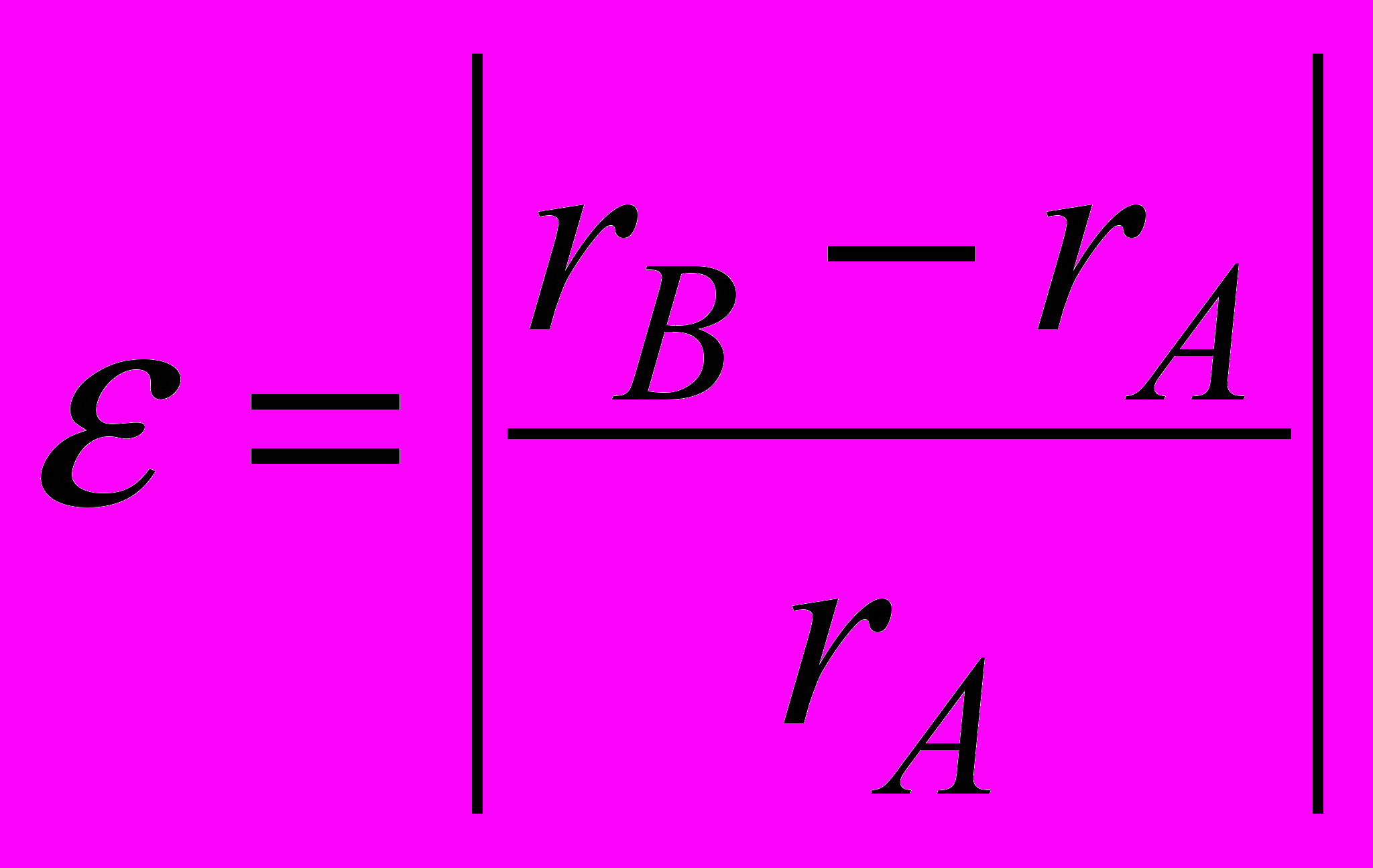
Теория показывает, что предел текучести т твердого раствора описывается соотношением
т =2,5G4/3K, (4.1)
где G - модуль сдвига.2
Отсюда следует, что упрочнение металла (растворителя) при образовании твердого раствора линейно зависит от концентрации растворенных атомов К и в несколько большей степени (4/3) от различия размеров е их атомов и атомов растворителя. Последнее объясняет известный факт большего упрочнения (твердых растворов внедрения (где разница в размерах атомов наибольшая и значит максимальны искажения решетки растворителя) по сравнению с растворами замещения.
На рис. 4.2 показана зависимость эффекта упрочнения металлов от указанных параметров К и .
С
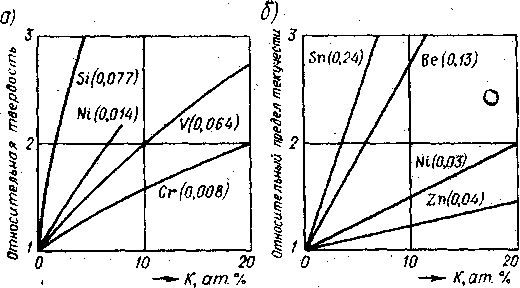
Рис. 4.2. Упрочнение железа (а) и меди (б) при образовании твердых растворов различного химического состава и концентрации К
Числа в скобках у обозначений растворенных химических элементов - величины параметра несоответствия . По осям ординат откладываются отношения твердости и прочности (предела текучести) сплавов - твердых растворов к твердости и прочности исходного компонента (растворителя).
Упрочнение, происходящее при образовании твердых растворов, сопровождается, как правило, снижением пластичности, так как торможение дислокаций отрицательно сказывается на способности металла к пластическому деформированию.
Искажения решетки растворителя, вызванные проникновением в нее чужеродных атомов, повышают также электросопротивление. Электросопротивление твердого раствора А(в) отличается от сопротивления исходного металла - растворителя А на величину
= А(в) - А = K(1-K), (4.2)
где К - концентрация растворенных атомов В; - коэффициент, определяемый эффективностью рассеяния электронов растворенными атомами; зависит от разности размеров атомов А и В и различий в их электронной структуре (ср. со сказанным выше о параметре ).
При малых концентрациях растворенных атомов К(1-К)К, тогда
K (4.3)
Из сравнения выражений (4.1) и (4.3) видно, что повышения сопротивления металла пластической деформации т и сопротивления направленному движению электронов , вызываемые образованием твердого раствора, подчиняются аналогичным закономерностям. Это естественно, поскольку первопричина обоих явлений - искажение решетки металла растворенными чужеродными атомами.
Из приведенных данных следует, что образование сплава - твердого раствора может заметно повлиять на свойства исходного металла (растворителя).
Значительно большее изменение свойств происходит, если при сплавлении компонентов образуются химические соединения. Как отмечалось в разделе 4.2.2., кристаллическая решетка химического соединения отличается от решеток образующих его компонентов. Уже этого достаточно, чтобы понять причину резкого различия свойств сплава - химического соединения и исходных компонентов. В качестве примера в табл. 4.1 приведены свойства металла (Тi) и соединений на его основе.
Таблица 4.1
Температура плавления Tпл и микротвердость Н титана и его соединений
-
Материал
Свойства
Tпл , К
Н , ГПа
Тi
ТiO2
ТiN
ТiС
1941
2143
3223
3530
0,73
10,7
20,5
31,7
Известно, что в химических соединениях большую роль играет ковалентная связь, более жесткая и прочная, чем металлическая. С этим связано повышение температуры плавления и твердости при образовании соединений. Последние два соединения в табл. 3 относятся к фазам внедрения. Эти фазы отличаются исключительно высокой твердостью и тугоплавкостью. Карбиды играют важную роль в формировании механических свойств сталей и служат основой группы теплостойких инструментальных материалов - спеченных твердых сплавов. Карбиды и нитриды широко используются для нанесения износостойких покрытий на стальные изделия.
Для дальнейшего важно отметить, что присутствующие в металлических сплавах химические соединения независимо от их природы, как правило, более тверды, но менее пластичны, чем твердые растворы. Поэтому частицы химических соединений в двухфазных сплавах играют роль упрочнителей. До сих пор говорилось об однофазных (двухкомпонентных) сплавах - твердых растворах или химических соединениях. Большинство промышленных сплавов при нормальных температурах состоят из кристаллов двух или более фаз. Свойства таких сплавов в общем случае зависят от свойств индивидуальных фаз и их относительных количеств. Так, прочность сплава, состоящего из фаз и , может быть выражена как
= V + V . (4.4)
где каждое слагаемое - произведение прочности соответствующей фазы на ее относительное количество (объемную долю). Или, с учетом того, что V+V=1,
= + V( - ). (4.5)
Если фаза более прочная ( > ), то из (4.5) следует, что прочность двухфазного сплава будет линейно возрастать с увеличением объемной доли более прочной фазы V.
Если, например, при сплавлении компонентов А и В не образуются химические соединения и твердые растворы, т. е. отсутствует взаимная растворимость компонентов в твердом состоянии, то такой сплав представляет собой механическую смесь кристаллов А и В. То есть в данном случае фаза А, В. Тогда очевидно, что сплавление в этом случае приводит к повышению прочности исходного металла А пропорционально количеству второго более прочного компонента В, но максимальная прочность сплава не может превосходить прочности компонента В - при VB=1, = B.
Экспериментальное исследование прочности двухфазных сплавов часто обнаруживает значительные отклонения от приведенной закономерности (4.5). Это обусловлено тем, что на прочность сплава большое влияние оказывает не только относительное количество упрочняющей фазы, но и размеры, форма и взаимное расположение ее кристаллов. Если, например, более твердая, но хрупкая упрочняющая фаза окаймляет непрерывным слоем зерна матричной фазы, то это приводит к снижению и прочности и пластичности сплава (такая ситуация может иметь место в высокоуглеродистых сталях).
Другой пример охрупчивающего влияния слоев второй фазы рассматривался в главе 3, когда обсуждалась анизотропия свойств горячедеформированного металла.
Практический опыт показывает, что наилучшему сочетанию свойств конструкционных металлических сплавов (высоким значениям прочности и ударной вязкости) соответствует структура, в которой мелкодисперсные частицы твердой фазы (химических соединений) равномерно и достаточно плотно распределены в менее прочной, но пластичной матричной фазе (твердом растворе). Из теории следует, что предел текучести двухфазного сплава обратно пропорционален расстоянию l между частицами упрочняющей фазы:
т ~ 1/l . (4.5)
При больших расстояниях между частицами упрочняющей фазы пластическая деформация матрицы происходит почти беспрепятственно, т. е. сопротивление сплава деформированию невелико, характеристики прочности (т, в) имеют малую величину.
Установлено, что наибольшее упрочнение достигается, когда дисперсные частицы упрочняющей фазы (размером около 10 нм) распределены достаточно плотно, так что расстояние l между ними составляет несколько десятков периодов решетки (20...40 нм). При таком распределении упрочняющих частиц они наиболее эффективно тормозят скольжение дислокаций. Обычно подобные структуры в двухфазных сплавах получают путем термической обработки.
В заключение данного раздела подчеркнем, что сплавление является эффективным способом воздействия на свойства металлов, в частности, на их прочность.
Сплавление компонентов может приводить к получению качественно новых материалов с иным химическим составом, структурой и соответственно с другими, часто резко отличающимися свойствами (вспомним, например, скачкообразное изменение свойств при образовании химических соединений).
При этом сплавы могут быть однофазными - твердыми растворами или химическими соединениями. В двухфазных сплавах возможны различные сочетания из трех типов твердых фаз - химических элементов, твердых растворов, химических соединений. Очевидно, что свойства сплавов зависят от природы и индивидуальных свойств образующихся при сплавлении фаз. Но, как отмечалось выше, на свойства влияют и относительные количества фаз, размеры, форма и взаимное расположение зерен. Все эти факторы в сумме определяют понятие - структура сплава. Нередко бывает так, что один и тот, же сплав заданного химического и фазового состава может иметь различные свойства в зависимости от особенностей его строения - структуры. Понятна в связи с этим необходимость знания закономерностей формирования структуры сплавов различного химического состава. Такие закономерности могут быть установлены при изучении диаграмм фазового равновесия (диаграмм состояния), чему посвящена следующая глава.
1 В этой и следующих темах рассматриваются только двухкомпонентные (двойные сплавы). Такое ограничение оправдано, так как упрощает изложение основных закономерностей теории строения сплавов, которые являются общими в системах с различным числом компонентов.
2 Модуль сдвига G - это модуль касательной упругости (модуль Гука), характеризует сопротивление материала упругой деформации сдвига в отличие от модуля нормальной упругости (модуля Юнга Е, см. раздел 1.3. Глава I), характеризующего сопротивление. упругой продольной деформации растяжения - сжатия. Для многих металлов G0,4Е. Напомним, что пластическая деформация - течение металла - происходит под действием сдвиговых, касательных напряжений.