Конспект лекций «материаловедение»
Вид материала | Конспект |
- Конспект лекций по теме: «Материаловедение» для специальности 120100 "Технология, 104.18kb.
- Конспект лекций по теме: «Материаловедение» для специальности 120100 "Технология, 5022.76kb.
- Е. в конспект лекций «материаловедение» ч. 1 конспект, 33.7kb.
- Конспект лекций «материаловедение», 249.86kb.
- Конспект лекций «материаловедение», 137.13kb.
- Конспект лекций 2008 г. Батычко В. Т. Административное право. Конспект лекций. 2008, 1389.57kb.
- Конспект лекций 2010 г. Батычко Вл. Т. Муниципальное право. Конспект лекций. 2010, 2365.6kb.
- Конспект лекций «материаловедение», 123.26kb.
- Конспект лекций 2011 г. Батычко В. Т. Семейное право. Конспект лекций. 2011, 1718.16kb.
- Конспект лекций 2011 г. Батычко Вл. Т. Конституционное право зарубежных стран. Конспект, 2667.54kb.
© СЗТУ кафедра МТМиП, Шадричев Е.В конспект лекций «МАТЕРИАЛОВЕДЕНИЕ» ч.1
Глава 3. ИЗМЕНЕНИЕ СТРУКТУРЫ И СВОЙСТВ
МЕТАЛЛОВ ПРИ ПЛАСТИЧЕСКОЙ
ДЕФОРМАЦИИ И ПОСЛЕДУЮЩЕМ НАГРЕВЕ
Известно (см. раздел 1.3), что если возникающее при нагружении тела напряжение превышает предел текучести (0,2) данного металла, в нем возникает необратимая остаточная или пластическая дёформация.
3.1. ВЛИЯНИЕ ПЛАСТИЧЕСКОЙ ДЕФОРМАЦИИ НА
СТРУКТУРУ И СВОЙСТВА МЕТАЛЛОВ
Пластическая деформация происходит путем скольжения или сдвига отдельных участков решетки вдоль определенных плоскостей под действием сдвиговых (касательных) напряжений. Механизм этого сдвига в идеальных (бездефектных) кристаллах предполагает одновременное перемещение всех атомов одной части кристалла относительно другой. В реальных кристаллах сдвиг осуществляется последовательным эстафетным движением дислокаций вдоль плоскостей скольжения (см. раздел 1.2).
В поликристаллических металлах такой сдвиг происходит в отдельных зернах по плоскостям скольжения различного направления, а также в блоках, из которых состоят эти зерна. При значительных деформациях зерна сплющиваются, вытягиваются в направлении пластического течения, создается слоистая, волокнистая структура (рис. 3.1).
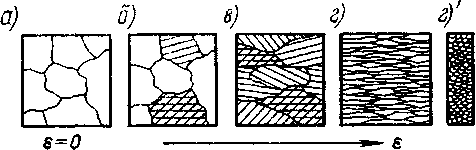
Рис. 3.1. Схема изменения структуры поликристаллического металла при возрастающей степени пластической деформации :
а - недеформированный металл; б - сдвиги лишь в отдельных зернах по различным плоскостям скольжения; форма зерен практически не меняется;
в - следы деформаций (сдвиги) во всех зернах; меняется (вытягивается) форма зерен; г - образование волокнистой структуры, ориентированной в направлении пластического течения металла (г' - поперечное сечение)
При степенях деформации1 >40 % деформированные зерна поворачиваются вдоль направления деформации, приобретая одинаковую кристаллографическую ориентацию - текстуру деформации. Наличие текстуры приводит к появлению анизотропии свойств поликристаллического металла (см. раздел 1.2).
Процессы сдвига, происходящие при деформировании металла, рождают множество экстраплоскостей, т. е. резко увеличивают количество дислокаций. Если в недеформированном металле плотность дислокаций р обычно составляет 106...108 см-2, то при степенях деформации >80...90 % 1011...1012 см-2. Значительно возрастает количество точечных и поверхностных дефектов (вакансий, межузельных атомов, границ и блоков). Такое увеличение числа дефектов решетки (в первую очередь дислокаций) затрудняет дальнейшее скольжение дислокаций, повышает сопротивление металла сдвигу, т. е. его прочность (см. раздел 1.3). Упрочнение металла под действием пластической деформации называется наклепом или нагартовкой. С другой стороны, ограничение подвижности дислокаций уменьшает способность металла к пластической деформации, т. е. снижает его пластичность.
Н
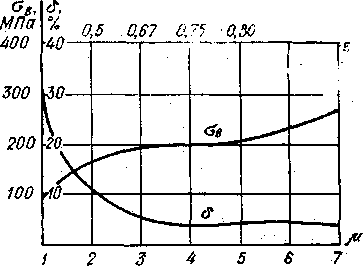
Рис. 3.2. Влияние степени пластической деформации на механические свойства металла (медь). По оси абсцисс отложена величина вытяжки =S0/S; со степенью пластической деформации (шкала в верхней части рисунка) она связана соотношением =1-1/ (см. примечание на с. 34)
Резкое увеличение дефектности решетки при пластической деформации отражается и на физико-химических свойствах металлов. Например, вызванные дефектами нарушения периодического электрического поля ионов решетки повышают сопротивление направленному движению электронов, рассеивая их, т. е. уменьшают электропроводность (рис. 3.3).
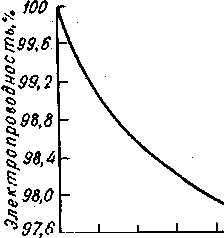
Рис. 3.3. Влияние степени пластической деформации на относительную электропроводность меди. За 100% принята электропроводность недеформированной меди
3.2. ВЛИЯНИЕ НАГРЕВА НА СТРУКТУРУ И СВОИСТВА
ПЛАСТИЧЕСКИ ДЕФОРМИРОВАННОГО МЕТАЛЛА
Большая часть энергии, затрачиваемой на пластическую деформацию металла, превращается в теплоту (металл нагревается). Остальная часть этой энергии (5...10 %) расходуется на повышение потенциальной энергии атомов, смещенных из исходных положений равновесия, т. е. на образование дефектов решетки. О наличии этой доли запасенной металлом энергии свидетельствует резкое повышение количества всех видов дефектов решетки, о чем говорилось в предыдущем разделе, а также рост внутренних напряжений в деформированном металле.
В главе 2 отмечалось, что состояние системы (материала) с повышенной внутренней (свободной) энергией является термодинамически неустойчивым. Поэтому неравновесная структура наклепанного металла может длительно существовать лишь при достаточно низких температурах, где диффузия атомов практически отсутствует. При нагреве такого металла до температур, при которых атомы приобретают заметную подвижность, в его структуре протекают диффузионные процессы, приводящие к постепенному возвращению свойств к исходному недеформированному состоянию с минимальной свободной энергией. Различают две основных стадии этого процесса - возврат и рекристаллизацию.
3.2.1. Возврат
Возврат начинается при сравнительно небольших температурах, меньших 0,2 Тпл. Процесс возврата захватывает только субструктуру зерен (изменяется форма блоков, из которых состоят зерна), форма и размер самих зерен не меняются. Уменьшаются плотность дефектов решетки и остаточные напряжения. В результате несколько снижаются твердость и прочность (обычно не более 10...20 %) и повышается пластичность (рис. 3.4).
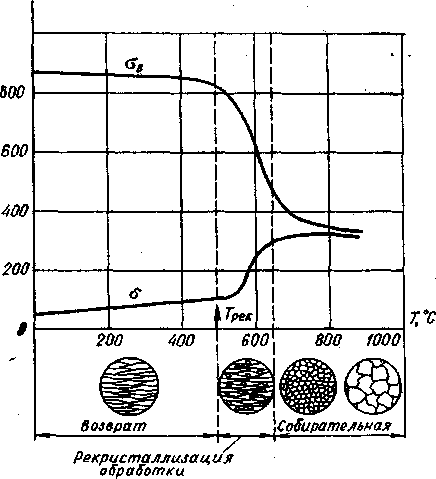
Рис. 3.4. Изменение механических свойств наклепанного металла (техническое железо) при нагреве
3.2.2. Рекристаллизация
При дальнейшем повышении температуры атомы приобретают значительную подвижность. В результате появляется возможность образования зародышей новых равноосных зерен. Рост этих зародышей приводит к восстановлению не ориентированной крупнозернистой (при достаточно высоких температурах) структуры, свойственной недеформированному металлу.
Этот процесс зарождения и роста новых зерен называется рекристаллизацией. Первый его этап - рекристаллизация обработки (или первичная рекристаллизация) начинается при Т=Tрек, называемой температурой или порогом рекристаллизации. Температура рекристаллизации связана с температурой плавления металла соотношением2
Tрек = a Тпл, (3.1)
Коэффициент а зависит от «степени дефектности решетки» (о чем подробнее в разделе 3.2.4), в частности, от чистоты металла. В металлах технической чистоты а = 0,3...0,4.
При Т=Tрек на границах деформированных зерен, где скапливаются дислокации и точечные дефекты (см. раздел 1.2) и, следовательно, наиболее высока свободная энергия и низка устойчивость, зарождаются новые равноосные зерна. Эти зерна имеют .неискаженную решетку с минимальным количеством дислокаций и точечных дефектов. Образование таких зерен сопряжено с уменьшением свободной энергии (энергетически выгодно - см. раздел 2.1), т. е. переводит металл в более устойчивое состояние. Плотность дислокаций при этом падает с 1010...1012 см-2 до 106...108 см-2, снижается количество других дефектов, в результате значительно уменьшаются прочность и твердость, повышается пластичность (рис. 3.4).
Таким образом, Tрек - это температура начала рекристаллизации, при которой происходит резкое изменение свойств наклепанного металла (в частности, его разупрочнение) вследствие образования новых недеформированных зерен.
Вторым этапом процесса рекристаллизации является собирательная рекристаллизация - диффузионный рост новых зерен с неискаженной решеткой. Рост зерен происходит в результате диффузионного перемещения атомов от одних зерен к другим через границу раздела. При этом одни зерна постепенно уменьшаются и исчезают, за их счет укрупняются соседние, т. е. крупные зерна «поедают» мелкие.
Этот процесс энергетически выгоден, так как сопровождается уменьшением свободной энергии, точнее ее «поверхностной части»
Fпов = S, (3.2)
где S - площадь поверхности зерен; - поверхностная энергия.3
Укрупнение зерен приводит к уменьшению относительной доли их поверхности. Действительно, если принять форму равноосных зерен, близкой к округлой, то отношение их поверхности S к объему V будет изменяться обратно пропорционально радиусу зерна r:
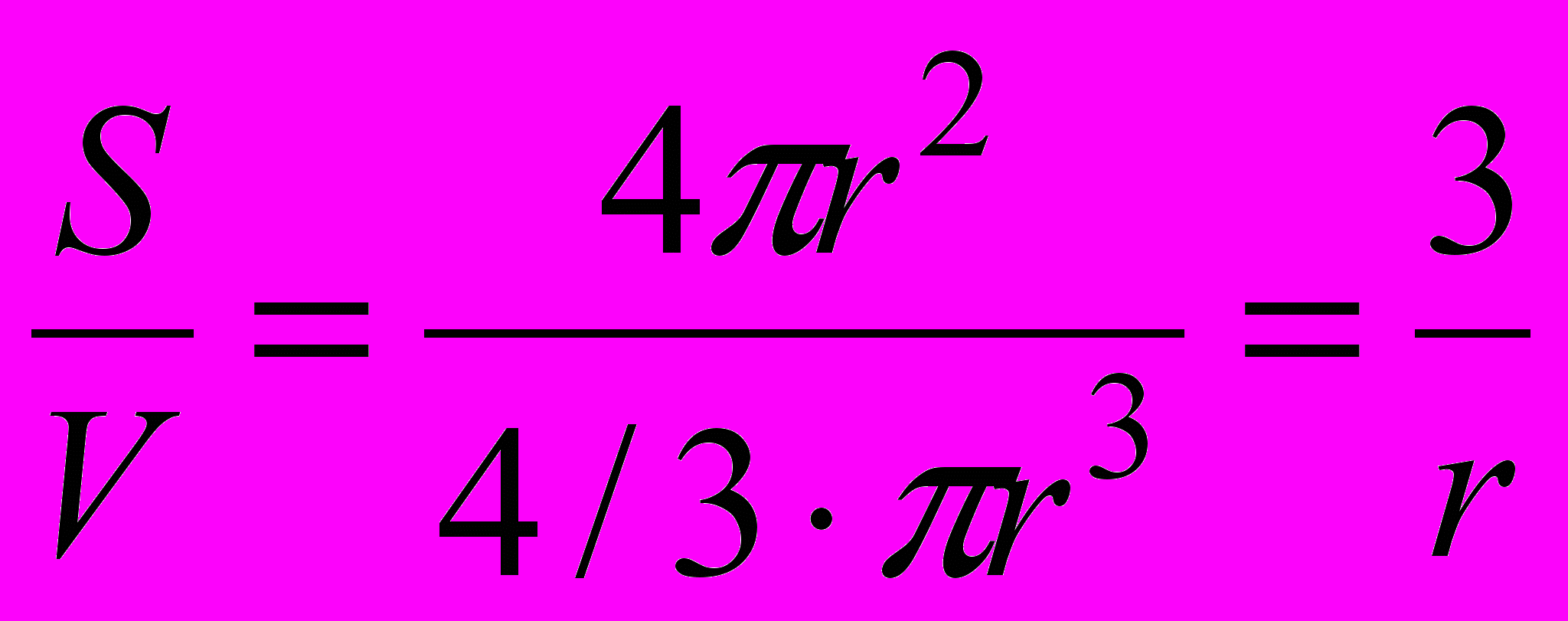
Значит укрупнение зерен (увеличение их радиуса r) уменьшает площадь межзеренных поверхностей раздела S, соответственно снижается Fпов и общая свободная энергия. Это приводит структуру и свойства металла к равновесному, недеформированному состоянию — упрочнение, вызванное пластической деформацией (наклеп), ликвидируется. Повышение температуры углубляет (ускоряет) этот процесс (рис. 3.4).
Таким образом, рекристаллизация — типичный процесс кристаллизации (см. главу 2), его движущей силой является уменьшение свободной энергии пластически деформированного металла. Механизм осуществления рекристаллизации - это диффузионные процессы зарождения и роста кристаллов новых, почти свободных от дефектов зерен с минимальной свободной энергией.
3.2.3. Размер зерна при рекристаллизации.
Диаграмма рекристаллизации
Из предыдущего раздела ясно, что рёкристаллизация - диффузионный процесс. Поэтому рост зерна при рекристаллизации управляется законами диффузии. Это имеет важное практическое значение, поскольку позволяет, меняя режим рекристаллизационного отжига (нагрев и выдержка деформированного металла при Т>Трек), получать нужную структуру (размер зерна) и свойства металла.
Известно, что интенсивность протекания диффузионных процессов экспоненциально возрастает с температурой Т, а также пропорционально (~), где - время выдержки, при данной Т. Поэтому размер зерна d подчиняется аналогичным зависимостям от Т и (рис. 3.5,a,б).
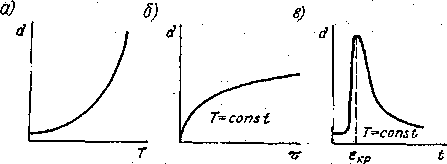
Рис. 3.5. Влияние температуры нагрева (а), времени выдержки (б) и степени пластической деформации (в) на размер зерна при рекристаллизации
Кроме того, как следует из рис. 3.5, в, размер зерна при рекристаллизации зависит от степени предшествующей пластической деформации е. Видно, что существует некоторая критическая степень деформации екр, рекристаллизационный отжиг после которой приводит к получению аномально большого зерна и соответственно ухудшению механических свойств. Отсюда для получения мелкого зерна металл в процессе обработки давлением необходимо подвергать деформациям с >кр. Величина кр для различных металлов колеблется в пределах 3...15 %.
Характер зависимости d=f() (рис. 3.5,в) может быть понят на основании «энергетического подхода», который применяется для объяснения процессов кристаллизации (глава 2). Его суть: самопроизвольные структурные превращения происходят лишь в направлении уменьшения свободной энергии F, поэтому для начала такого превращения необходимо, чтобы система в исходном состоянии обладала повышенным уровнем F.
Выше говорилось, что пластическая деформация приводит металл а неравновесное состояние с повышенной свободной энергией. Очевидно, что разность свободных энергий F между пластически деформированным наклепанным состоянием Fпд и недеформированным равновесным состоянием Fр увеличивается пропорционально степени пластической деформации :
F =( Fпд- Fр)~ . (3.4)
При малой величине <кр изменения в структуре металла незначительны (наклепа почти нет), она мало отличается от исходной. Поэтому мала F, и значит нет главного условия для образования зародышей новых зерен при рекристаллизации.
Если деформация производилась с >кр, то F велика, и при нагреве такого металла выше Трек в нем протекает типичный рекристаллизационный процесс зарождения и роста новых равновесных и равноосных зерен. Причем с увеличением растет F, поэтому возрастает скорость образования зародышей новых зерен, а скорость их диффузионного роста практически не изменяется, так как процесс рассматривается при Т = const (>Трек). В связи с этим значительное увеличение е приводит к измельчению зерна в металле при рекристаллизационном отжиге (рис. 3.5, в).4
При относительно небольшой степени деформации =кр металл деформируется неоднородно - имеются сильно деформированные зерна с большой величиной Fпд и мало деформированные с меньшей величиной Fпд. При отжиге такого металла зерна с малой величиной Fпд (т. е. более устойчивые, так как для них близка к 0) интенсивно растут за счет неустойчивых зерен с большой величиной Fпд. Этим обусловлено резкое возрастание размера зерна при отжиге металла, деформированного с =кр (рис. 3.5, в).
Таким образом, размер зерна при рекристаллизации в наибольшей мере зависит от температуры нагрева и степени предшествующей пластической деформации металла. Эта зависимость d=f(Т, ) изображается трехмерной «диаграммой рекристаллизации» (рис. 3.6). Такие диаграммы, построенные для различных промышленных сплавов, имеют важное практическое значение, поскольку позволяют выбрать режимы пластической деформации е и рекристаллизационного отжига / для получения зерна заданного размера. Напомним, что размер зерна при прочих равных условиях определяет механические и технологические свойства металла.
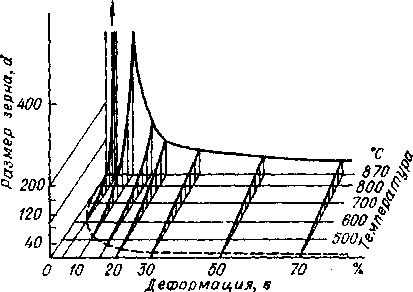
Рис. 3.6. Диаграмма рекристаллизации (техническое железо) Зависимость Трек =f()
3.2.4. Влияние различных факторов на температуру рекристаллизации
Для правильного назначения температуры рекристаллизационного отжига необходимо прежде всего знать температуру рекристаллизации Трек, которая, согласно выражению (3.1), определяется температурой плавления материала а также коэффициентом пропорциональности а. В общем случае величина коэффициента а зависит от степени пластической деформации и чистоты металла.5
Со степенью пластической деформации связано количество дефектов решетки в деформированном металле, а чистота металла характеризует уровень дефектности его решетки в исходном и рекристаллизованном состояниях. Таким образом, можно считать, что величина коэффициента а (а значит и Трек) зависит от «степени дефектности решетки» деформированного и рекристаллизованного металла. Характер этой зависимости можно понять также на основании энергетического подхода (см. раздел 3.2.3).
Движущей силой рекристаллизации является разность свободных энергий F между неравновесным, пластически деформированным Fпд и равновесным, рекристаллизованным Fр состояниями - см. соотношение (3.4). Увеличение степени пластической деформации е повышает дефектность решетки деформированного металла - растет Fпд и соответственно F, возрастает неустойчивость металла, в результате процесс рекристаллизации может начаться при достаточно низких температурах нагрева. Другими словами, чем больше величина F=Fпд-Fр, характеризующая степень неустойчивости деформированного металла, тем ниже значения коэффициента а~1/F и Трек. Поэтому с увеличением величины а и Трек уменьшаются. При достаточно больших степенях пластической деформации, когда Fпд насыщается и F становится постоянной, значения а и Трек перестают зависеть от (это видно на диаграмме рекристаллизации, рис. 3.6.). В этом случае коэффициент а уже не является функцией и, как следует из дальнейшего, определяется только чистотой металла6.
Действительно, при данной степени пластической деформации и соответствующей ей величине Fпд разность свободных энергий F будет определяться вариацией значений Fр. Уровень Fр рекристаллизированного металла зависит от степени дефектности его решетки и возрастает с увеличением содержания примесей в направлении: чистый металл технический металл с примесями сплав. В этом же направлении убывает величина F и, соответственно, возрастает Tрек, так как для того чтобы «сдвинуть» процесс рекристаллизации при малой энергии F, нужна достаточно высокая температура, активизирующая диффузионные процессы зарождения и роста новых зерен.
Таким образом, повышение дефектности решетки рекристаллизованного металла или другими словами, снижение его чистоты увеличивает значение коэффициента а (и Трек). Этому способствует и то обстоятельство, что примеси замедляют скорость диффузии собственных атомов металла. Соответственно величина а в выражении (3.1) в зависимости от чистоты металла изменяется следующим образом: 0,1...0,2 - в чистых металлах; 0,3...0,4 - в металлах технической чистоты и 0,5...0,8 - в сплавах (твердых растворах).
3.3. ХОЛОДНАЯ И ГОРЯЧАЯ ДЕФОРМАЦИЯ
При обработке металлов давлением различают холодную н горячую пластическую деформацию (обработку). Эта классификация определяется не самой температурой обработки металла, а ее соотношением с температурой рекристаллизации.
Деформирование металла при Т<Трек называется холодной обработкой. Она сопровождается наклепом металла, появлением анизотропии свойств из-за образования текстуры деформации (см. раздел 3.1).
При горячей обработке - деформирование при Т>Трек также происходит упрочнение металла, но оно частично или полностью снимается одновременно протекающим процессом рекристаллизации.
Для облегчения горячей обработки металла (увеличения пластичности, устранения наклепа) деформирование проводят обычно при температурах, значительно превосходящих Трек. Например, для железа и сталей - сплавов на его основе Трек450 °С, температура рекристаллизационного отжига 600...700 °С, температура горячей обработки 900...1300 °С.
Металл после горячей обработки часто имеет анизотропные свойства. Обычно это обусловлено закономерным расположением примесей и неметаллических включений, которые вытягиваются в направлении деформации, образуя волокнистую или, иногда, полосчатую (слоистую) структуру. Рекристаллизационные процессы, протекающие при горячей обработке, не изменяют такой структуры, так как затрагивают лишь зерна самого металла.
Пониженная пластичность таких слоев приводит к значительному ухудшению свойств металла в направлении, перпендикулярном этим слоям (волокнам). При нагружении изделия вдоль слоев их отрицательное влияние почти полностью компенсируется основным металлом, занимающим подавляющую часть площади сечения и воспринимающим практически всю нагрузку.
Особенно сильно такое волокнистое строение металла отражается на анизотропии пластичности и ударной вязкости.
При измерении Этих свойств в образцах, вырезанных поперек волокон, характеристики пластичности ( и )на 20…40 %, а ударная вязкость на 50...70 % ниже, чем в «продольных» образцах.
Анизотропия свойств пластически деформированного металла должна учитываться при изготовлении изделий. Для получения наилучших эксплуатационных свойств конструкция и технология изготовления детали должны обеспечить такую конфигурацию волокнистой структуры, при которой главные действующие усилия были бы направлены не поперек, а вдоль волокон. Обычно это достигается, когда волокна огибают контуры детали.
3.4. О ПРАКТИЧЕСКОМ ЗНАЧЕНИИ ЯВЛЕНИЯ НАКЛЕПА И РЕКРИСТАЛЛИЗАЦИИ
Из предыдущего ясно, что пластическое деформирование металла, приводящее к наклепу, и последующий нагрев, вызывающий рекристаллизацию структуры, оказывают сильное влияние на механические и другие свойства металла. Естественно, что значение наклепа и рекристаллизации для практики огромно.
Говоря о практическом значении этих явлений, нужно учитывать два аспекта их влияния на свойства металлических изделий. Оно может быть как положительным, так и отрицательным.
Отрицательная роль наклепа проявляется главным образом в том, что он затрудняет механическую обработку при производстве заготовок и готовых изделий. В первую очередь это касается процессов обработки металлов давлением, широко применяемых в промышленности. Известно, что обработке давлением подвергаются около 90 % всей выплавляемой стали и свыше 50 % цветных металлов.
В разделе 3.3 уже говорилось о том, что при горячей обработке (обычно слитков) для облегчения деформирования металла необходимо нагревать его до высоких температур, что, естественно, усложняет и удорожает процесс.
При холодной обработке (например, холодной формовке в открытых штампах, глубокой вытяжке), упрочнение и снижение пластичности металла может быть столь велико, что для продолжения деформирования необходимо вводить в технологический процесс дополнительную операцию рекристаллизационного отжига.
При обработке металлов резанием также возникает наклеп, в результате твердость обрабатываемого поверхностного слоя может повышаться в 2 раза. Глубина наклепанного слоя в зависимости от физико-механических свойств материала и условий резания может изменяться от тысячных долей до нескольких миллиметров. Этот слой затрудняет процесс резания, затупляет инструмент, вследствие чего ухудшается качество обрабатываемой поверхности. Некоторые (обычно пластичные) металлы наклепываются так сильно, что практически не поддаются обработке резанием (и давлением). Таким свойством обладает, например, сталь с высоким содержанием (13 %) марганца, поэтому детали из нее изготавливаются литьем.
Рассмотренные выше примеры, относятся в основном хотя к к важным, но не завершающим, как правило, операциям технологического процесса производства изделий. Во всяком случае, стальные изделия (а их большинство в машиностроении) после механической обработки подвергаются термической, которая и формирует их окончательную структуру и свойства.
Во многих случаях, однако, операции пластического деформирования или рекристаллизационного отжига являются завершающими в технологическом процессе и оказывают поэтому решающее влияние на эксплуатационные свойства готовых изделий. Так, для технических металлов и многих сплавов, не упрочняемых термической обработкой, наклеп — единственный способ упрочнения в достаточно больших сечениях. Это используется, например, для повышения прочности медных и алюминиевых электропроводов (табл. 3.1, см. также рис. 3.2).
Склонность к интенсивному наклепу упомянутой выше высокомарганцевой стали позволяет успешно применять ее в качестве износостойкого материала для изготовления траков гусеничных машин, крестовин рельсов, черпаков землеройных машин и т. п.
В промышленности широко распространены малоотходные высокопроизводительные методы холодной штамповки. Так, в автомобилестроении штамповкой из листового материала получают около 60 % деталей, в точном машино- и приборостроении до 75 %, а в производстве товаров широкого потребления - до 98 %. При холодной штамповке металл наклепывается, приобретает достаточную для эксплуатации прочность (табл. 3.2).
Таблица 3.1
Влияние наклепа на механические свойства алюминия и меди
(технической чистоты)
-
Металл
Механические свойства
в , МПа
нв, МПа
, %
А1
Сu
140/90
1250/550
320/250
3/50
12/30
450/220
Примечание. В числителе - металл в наклепанном (нагартованном) состоянии; в знаменателе - после рекристаллизационного отжига.
Таблица 3.2
Влияние наклепа на механические свойства сплава Амц
(1 % Мn, 99 % А1)
-
Механические
свойства
Состояние сплава
М
П
Н
в, МПа
130
160
220
, %
23
10
5
Примечание. М - мягкое (рекристаллизационный отжиг) состояние; П - полунагартованное; Н - нагартованное.
В ряде случаев изделия, изготавливаемые методами обработки металлов давлением, не испытывают при эксплуатации значительных механических нагрузок. Например, трубопроводы из медных сплавов, применяемые в морском судостроёнии. Тогда рекристаллизационный отжиг прессованных труб на заданную величину зерна обеспечивает однородную мелкозернистую структуру, обладающую хорошим сочетанием механических свойств и коррозионной стойкости.
Особо следует отметить целенаправленное использование наклепа для повышения эксплуатационных свойств изделий. Примером этого является поверхностное упрочнение стальных изделий методами поверхностного пластического деформирования (дробеструйная обработка, обкатка роликами). Такая финишная обработка создает слой глубиной 0,2...0,4 мм с повышенной твердостью и высоким уровнем полезных остаточных напряжений сжатия. В результате существенно возрастает предел выносливости (усталости)7 и долговечность работающих изделий. Так, после дробеструйной обработки предел выносливости стальных рессор повышается в 1,5…2 раза. Такой обработке подвергают и другие изделия машиностроения - шестерни, зубчатые колеса, гильзы и поршни, лопатки компрессоров и т, п. Обкатка роликами применяется в основном для упрочнения шеек валов.
Приведенные выше примеры не исчерпывают, конечно, всего многообразия случаев учета и использования явлений наклепа и рекристаллизации. Однако и эти данные позволяют сделать вывод о том, что процессы пластической деформации и нагрева (отжига) металла, вызывающие наклеп и рекристаллизацию, являются эффективными методами воздействия на свойства металлов через изменение их структуры при неизменном химическом составе.
В двух последующих главах будет продемонстрирована возможность целенаправленного воздействия на структуру и свойства металлических материалов посредством изменения их химического состава в результате сплавления компонентов.
1 Степень деформации может быть определена как =(S0-S)100%/S0, где S0 и S - площадь оперечного сечения образца до и после деформации соответственно.
2 Температура в этом соотношении выражается в абсолютной шкале, т. е. в К.
3 Величина (в физике - поверхностное натяжение на границе двух сред) характеризует различие в энергетических состояниях атомов на поверхности и внутри кристалла. На поверхности атом менее привязан к соседям, более подвижен, имеет повышенную энергию. Атом внутри кристалла находится в равновесном состоянии с минимальной энергией (в потенциальной яме) .
4 Зависимость d=f() подобна зависимости размера зерна при кристаллизации расплава от степени переохлаждения Т (раздел 2.4). Это связано с тем, что рост и Т и приводит к увеличению разности свободных энергий исходного (жидкого; деформированного) и нового (кристаллического; рекристаллизованного) состояний, соответственно повышается скорость образования зародышей нового состояния – измельчается зерно.
5 Последняя определяется концентрацией чужеродных атомов, т.е. химическим составом металла (сплава).
6 Указанные ниже значения а, обычно приводимые в литературе, от носятся именно к этому случаю больших степеней пластической деформации (когда а и Трек не зависят от ).
7 Предел выносливости - наибольшее напряжение, которое может выдержать металл без разрушения за большое (специально устанавливаемое, обычно >106) число циклов изменения знакопеременных напряжений (растяжение - сжатие), возникающих при циклическом нагружении образца.