Коршунова Татьяна Евгеньевна материаловедени е конспект
Вид материала | Конспект |
- Т. Ю. Коршунова коршунова Татьяна Юрьевна ведущий научный сотрудник отдела закон, 693.01kb.
- Теряева Татьяна Евгеньевна, учитель начальных классов моу сош №14 города Костромы, 87.95kb.
- Клишина Татьяна Евгеньевна (29,75 балла): г. Пушкино, моу сош № Учитель : Коротаева, 27.99kb.
- Балакирева Татьяна Евгеньевна Постановка цели урок, 76.35kb.
- Т. Е. Зерчанинова социальные потребности молодежи севера, 101.96kb.
- Методическая разработка урока по теме: «Проектирование учебных занятий по немецкому, 80.39kb.
- Т. Ю. Коршунова т. Ю. Коршунова, кандидат юридических наук. Особенности регулирования, 317.69kb.
- Кошкарова Татьяна Викторовна. Служебный телефон: 8-233-2-18-95. 2011г. Предмет: литературное, 56.23kb.
- Елизарова Татьяна Павловна конспект, 722.63kb.
- Козаева Татьяна Вячеславовна); имидж студия «Кокетка», ул. Горького, д. 21(индивидуальный, 31.1kb.
Министерство образования Российской Федерации
Владивостокский государственный университет
экономики и сервиса

Коршунова Татьяна Евгеньевна
М А Т Е Р И А Л О В Е Д Е Н И Е
Конспект лекций
для специальности
230100 Сервис и техническая эксплуатация транспортных средств,
технологических машин и оборудования
Владивосток
Издательство ВГУЭС
2005
1. СТРОЕНИЕ, СВОЙСТВА И СПОСОБЫ ИСПЫТАНИЯ МЕТАЛЛОВ
1.1. Кристаллическое строение металлов
У всех металлов и их сплавов строение кристаллическое. Кристаллические зерна неопределенной формы не похожи на типичные кристаллы — многогранники, поэтому их называют зернами. При затвердевании атомы металлов образуют кристаллы, которые можно рассматривать как геометрически правильные системы, построенные в виде кристаллических решеток. Порядок расположения атомов в решетке может бытъ различным. Многие важнейшие металлы образуют решетки, расположение атомов в элементарных ячейках которых представляет форму центрированного куба (α- и β-железо, α -титан, хром, молибден, вольфрам, ванадий), куба с центрированными гранями (γ-железо, алюминий, медь, никель, свинец, β - кобальт) или гексагональную, как у шестигранной призмы, ячейку (магний, цинк).
Большинство технических металлов имеют кристаллические решетки: объемно-центрированную кубическую, кубическую гранецентрированную или гексагональную.
В узлах решеток находятся положительно заряженные ионы. Ионы не находятся в покое, а непрерывно колеблются около положения равновесия. С повышением температуры амплитуда колебаний увеличивается, что вызывает расширение кристаллов, а при температуре плавления колебания частиц усиливаются настолько, что кристаллическая решетка разрушается.
Кристаллы имеют дефекты и их структура отличается от идеальных решеток. Точечными дефектами являются пустые узлы или вакансии и межузельные атомы; количество этих дефектов возрастает с повышением температуры. Важнейшими линейными дефектами являются дислокации (краевые и винтовые), представляющие как бы сдвиг части кристаллической решетки.
Дислокации характеризуются большой протяженностью в одном направлении и малой в другом.
Дефекты кристаллов оказывают существенное влияние на механические, физические, химические и технологические свойства металлов.
В отдельных кристаллах свойства различны в разных направлениях. Если взять большой кристалл, вырезать из него несколько одинаковых по размеру, но различно ориентированных образцов, и испытать их свойства, то иногда наблюдается значительная разница в свойствах отдельных образцов. Это свойство кристаллов называют анизотропностью. Анизотропность кристаллов объясняется особенностями расположения атомов в пространстве.
Аморфные тела изотропны, т. е. все эти свойства одинаковы во всех направлениях. Излом аморфного тела всегда имеет неправильную, искривленную, так называемую раковистую, поверхность.
Металлы, затвердевшие в обычных условиях, состоят не из одного кристалла, а из множества отдельных кристаллитов, различно ориентированных друг к другу, поэтому свойства литого металла приблизительно одинаковы во всех направлениях; это явление называют квазиизотропностью (кажущейся изотропностью).
Аллотропия металлов (или полиморфизм) — их свойство перестраивать решетку при определенных температурах в процессе нагревания или охлаждения. Аллотропию обнаруживают все элементы, меняющие валентность при изменении температуры, например железо, марганец, никель, олово и др. Каждое аллотропическое превращение происходит при определенной температуре. Например, одно из превращений железа происходит при температуре 911°С, ниже которой атомы составляют решетку центрированного куба, а выше - решетку гранецентрированного куба.
Структура, имеющая ту или иную решетку, называется аллотропической формой или модификацией.
Кристаллизацией металлов называется образование кристаллов в металлах (и сплавах) при переходе из жидкого состояния в твердое (первичная кристаллизация).
К вторичной кристаллизации относят превращения в затвердевшем металле при его остывании. Сюда относятся перекристаллизация из одной модификации в другую (полиморфные превращения), распад твердых растворов, распад (а также образование) химических соединении.
Температура, соответствующая какому-либо превращению в металле, называется критической точкой.
Переход из жидкого состояния в твердое при охлаждении сопровождается образованием кристаллической решетки, т. е. кристаллизацией. Чтобы вызвать кристаллизацию, жидкий металл нужно переохладить несколько ниже температуры плавления.
При затвердевании и при аллотропическом превращении и металле вначале возникают зародыши кристалла (центры кристаллизации), вокруг которых группируются атомы, образуя соответствующую кристаллическую решетку. Центрами кристаллизации могут служить неметаллические включения.
Таким образом, процесс кристаллизации складывается из двух этапов: образования центров кристаллизации и роста кристаллов.
У каждого из возникающих кристаллов кристаллографические плоскости ориентированы случайно, кроме того, при первичной кристаллизации кристаллы могут поворачиваться, так как они окружены жидкостью. Смежные кристаллы растут навстречу друг другу и точки их соприкосновения определяют границы зерен.
^ 1.2. Основные свойства металлов
У металлов выделяют механические, технологические, физические и химические свойства.
К физическим свойствам относятся: цвет, плотность, температура плавления, электропроводность, магнитные свойства, теплопроводность, теплоемкость, расширение и сжатие при нагревании, охлаждении и при фазовых превращениях;
к химическим - окисляемость, растворимость, коррозионная стойкость, жаростойкость;
к механическим - прочность, твердость, упругость, вязкость, пластичность;
к технологическим - прокаливаемость, жидкотекучесть, ковкость, свариваемость, обрабатываемость резанием.
Прочность - способность материала сопротивляться разрушению и появлению остаточных деформаций под действием внешних сил.
Удельная прочность - отношение предела прочности к плотности; для некоторых, например, алюминиевых сплавов или титана, она выше, чем для стали.
Твердостью называется сопротивление тела деформации в поверхностном слое при местном силовом контактном воздействии.
Упругость - свойство материалов восстанавливать свою форму после прекращения действия внешних сил, вызвавших изменение формы (деформацию).
Пластичность - свойство металла деформироваться без разрушения под действием внешних сил и сохранять новую форму после прекращения действия сил. Пластичность - свойство, обратное упругости.
Вязкостью материала называют его способность поглощать механическую энергию и при этом проявлять значительную пластичность вплоть до разрушения. Вязкость - свойство, обратное хрупкости.
Современными методами испытания металлов являются механические испытания, химический, спектральный, металлографический и рентгенографический анализы, технологические пробы, дефектоскопия, а также испытания на обрабатываемость резанием, коррозионные испытания металлов и др. Эти испытании дают возможность получить представление о природе металлов, их строении, составе и свойствах, а также определить качество готовых изделий.
^ Механические свойства. Первое требование, предъявляемое ко всякому изделию, — это достаточная прочность.
Металлы - прочные материалы, поэтому нагруженные детали машин, механизмов и сооружений обычно изготовляются из металлов.
Вязкие металлы применяют в тех случаях, когда детали при работе подвергаются ударной нагрузке.
Пластичность металлов дает возможность обрабатывать их давлением (ковать, прокатывать).
^ Эксплуатационные свойства. Многие изделия, кроме общей прочности, должны обладать еще особыми свойствами, характерными для работы данного изделия. Например, режущие инструменты должны обладать высокой твердостью. Для изготовления режущих и других инструментов применяют инструментальные стали и сплавы, а для рессор и пружин - стали и сплавы, обладающие высокой упругостью.
^ Физические свойства. Вес деталей часто является важнейшей характеристикой.
Способность плавиться при нагревании используется для получения отливок путем заливки расплавленного металла в формы.
Металлы с высокой электропроводностью (медь, алюминий) используют в электромашиностроении, для устройства линий электропередачи, а сплавы с высоким электросопротивлением - для ламп накаливания, электронагревательных приборов.
Магнитные свойства металлов играют роль в электромашиностроении (электрические генераторы, электродвигатели, трансформаторы), в приборостроении (телефонные и телеграфные аппараты) и т.д.
Теплопроводность металлов дает возможность равномерно нагревать их для обработки давлением, термической обработки; она обеспечивает также возможность пайки металлов, их сварки и т. п.
Некоторые сплавы металлов имеют коэффициент линейного расширения, близкий к нулю; такие сплавы применяют для изготовления точных приборов. Расширение металлов должно приниматься во внимание при строительстве длинных сооружений, например мостов, трубопроводов. Нужно также учитывать, что две детали из металлов с разным коэффициентом расширения и скрепленные между собой при нагревании изгибаются.
^ Химические свойства. Коррозионная стойкость важна для изделий, работающих в химически активных средах (колосниковые решетки, детали машин в химической промышленности). Для деталей и сооружений, которые должны обладать высокой коррозионной стойкостью, производят специальные нержавеющие, кислотостойкие и жаростойкие стали. Для изделий также применяют защитные покрытия.
Технологические свойства. Технологические свойства имеют важное значение при тех или иных видах обработки (обработка давлением, сварки и др.).
^ 1.3. Механические испытания
Механические испытания имеют важнейшее значение в промышленности. Детали машин, механизмов и сооружений работают под различного вида нагрузками: одни детали нагружены постоянно действующей в одном направлении силой, другие подвержены ударам, у третьих - силы более или менее часто изменяются по своей величине и направлению. Некоторые детали машин подвергаются нагрузкам при повышенных или низких температурах, при действии коррозии и т. п.; такие детали работают в сложных условиях.
В соответствии с этим разработаны различные методы испытаний, с помощью которых определяют механические свойства металлов.
Наиболее распространенными испытаниями являются испытания на твердость, статическое растяжение, динамические испытания.
Статическими называют такие испытания, при которых испытуемый металл подвергают воздействию постоянной силы или силы, возрастающей медленно.
Динамическими называют испытания, при которых испытуемый металл подвергают воздействию удара или силы, возрастающей быстро.
Кроме того, иногда производят испытания на усталость, ползучесть и износ, которые дают более полное представление о свойствах металлов.
^ Испытания на растяжение. Статическое испытание на растяжение - распространенный способ механических испытаний металлов.
При этих испытаниях по сечению образца создается однородное напряженное состояние и материал находится под действием нормальных и касательных напряжений.
Для статических испытаний изготовляют обычно круглые образцы ^ 1 (рис. 1) испытуемого металла или плоские (2) для листовых материалов. Образцы состоят из рабочей части и головок, предназначенных для закрепления их в захватах разрывной машины.
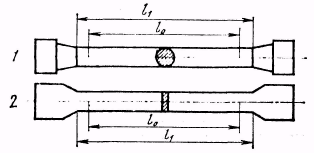
Рис. 1. Образцы для статических испытаний на растяжение
Расчетная длина l0 берется несколько меньше рабочей длины l1. Размеры образцов стандартизованы. Диаметр рабочей части нормального круглого образца 20 мм. Образцы других диаметров называются пропорциональными.
Растягивающее усилие создает напряжение в испытываемом образце и вызывает его удлинение; когда напряжение превзойдет прочность образца, он разорвется.
На рис. 2 приведена диаграмма растяжения “мягкой” стали. По оси ординат отложено усилие ^ Р, Н (кгс), по оси абсцисс - деформация (абсолютное удлинение образца ∆l, мм). Эта диаграмма получается при постепенном увеличении растягивающего усилия вплоть до разрыва испытуемого образца.
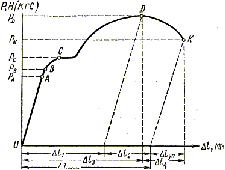
Рис. 2. Диаграмма растяжения «мягкой» стали
Величина напряжения в любой точке диаграммы может быть определена путем деления усилия ^ Р на площадь поперечного сечения образца до испытания. Напряжение обозначается σ.
По диаграмме можно отметить несколько характерных точек. Участок ^ ОА является отрезком прямой и показывает, что до точки А удлинение образца пропорционально нагрузке; каждому приращению нагрузки соответствует и одинаковое приращение деформации. Такая зависимость между удлинением образца и приложенной нагрузкой называется законом пропорциональности.
При дальнейшем нагружении образца наблюдается отклонение от закона пропорциональности: на диаграмме появляется криволинейный участок. До точки В деформации образца упругие.
Точкой С на диаграмме отмечено начало горизонтальной площадки, которая показывает, что образец удлиняется без увеличения нагрузки; металл как бы течет. Наименьшее напряжение, при котором без заметного увеличения нагрузки продолжается деформация испытуемого образца, называется физическим пределом текучести Предел текучести σт определяется по формуле
σт = Pс / F0,
где Рc — нагрузка в точке С.
Текучесть характерна только для низкоуглеродистой отожженной стали и для латуни некоторых марок. Высокоуглеродистые стали и другие металлы не имеют площадки текучести на диаграммах растяжения. Для таких металлов определяют условный предел текучести при остаточном удлинении, равном 0,2 %. Напряжение, при котором растягиваемый образец получает остаточное удлинение, равное 0,2 % своей расчетной длины, называется условным пределом текучести и обозначается σ0,2:
σ0,2 = P0,2 / F0.
Точка D показывает наибольшую нагрузку, которую может выдержать образец. Условное напряжение, отвечающее наибольшей нагрузке, предшествовавшей разрушению образца, называется пределом прочности при растяжении (временным сопротивлением разрыву) и определяется по формуле
σв = PD / F0,
где PD - нагрузка в точке D.
До точки D удлинение ∆l3 образца и сужение его поперечного сечения происходят равномерно по всей длине рабочей части. По достижении точки D деформация образца сосредоточивается в месте наименьшего сопротивления и дальнейшее удлинение ∆l4 протекает за счет образования шейки, по которой происходит разрыв образца при нагрузке РK.
При разрыве упругая деформация ∆lуп исчезает (величина упругой деформации в любой точке кривой (рис.2) будет соответствовать отрезку, отсекаемому на абсциссе нормалью этой точки, и прямой, проведенной из этой точки и параллельной отрезку О А) и абсолютное остаточное удлинение ∆lост сложится из удлинения равномерного ∆l1 и удлинения местного ∆l2 т. е.
∆lост = ∆l1 + ∆l2.
Для оценки пластичности металла важно знать относительное удлинение δ и относительное сужение площади поперечного сечения Ψ в процентах.
Относительное удлинение (%) определяют по формуле
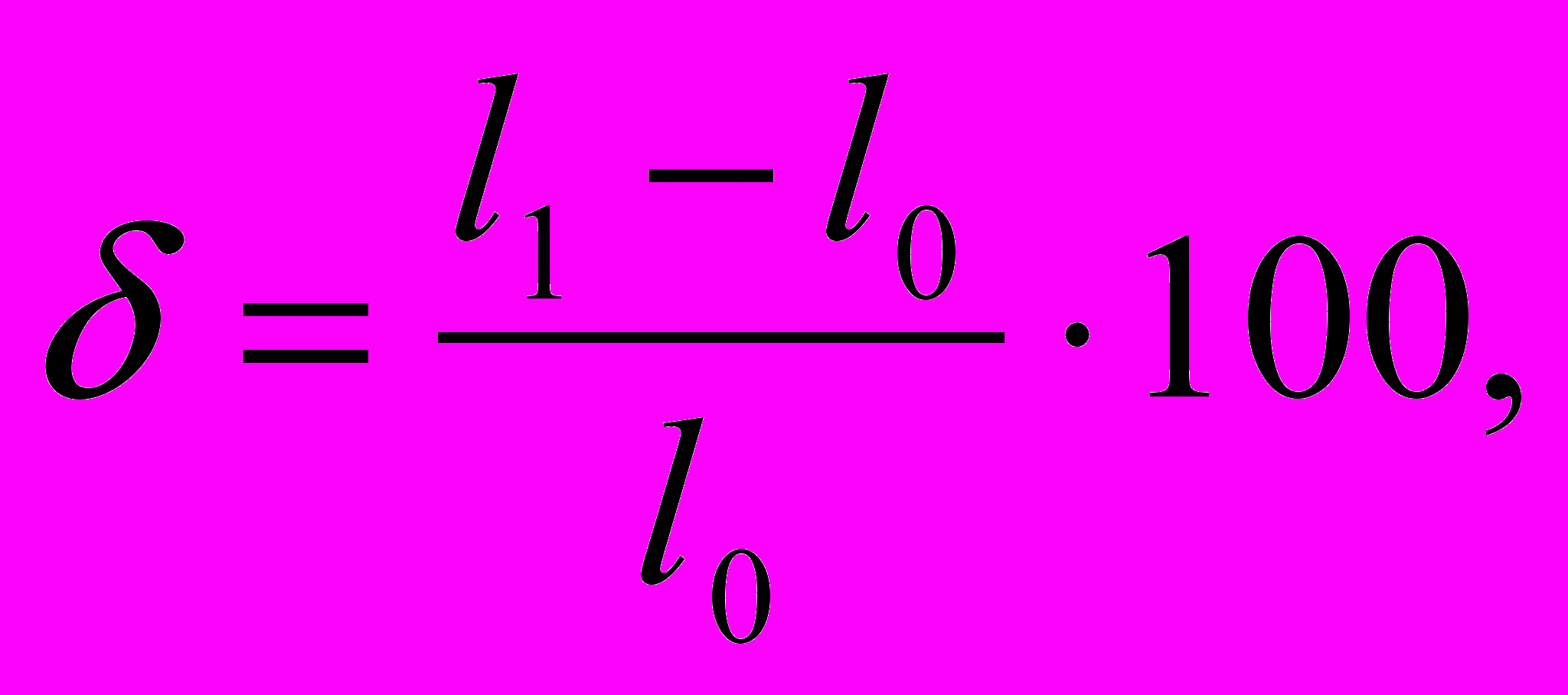
где l1 - длина образца после разрыва, мм;
l0 - расчетная длина образца, мм.
При удлинении одновременно уменьшается площадь поперечного сечения образца. В месте разрыва эта площадь будет наименьшей.
Относительное сужение (%) определяют по формуле
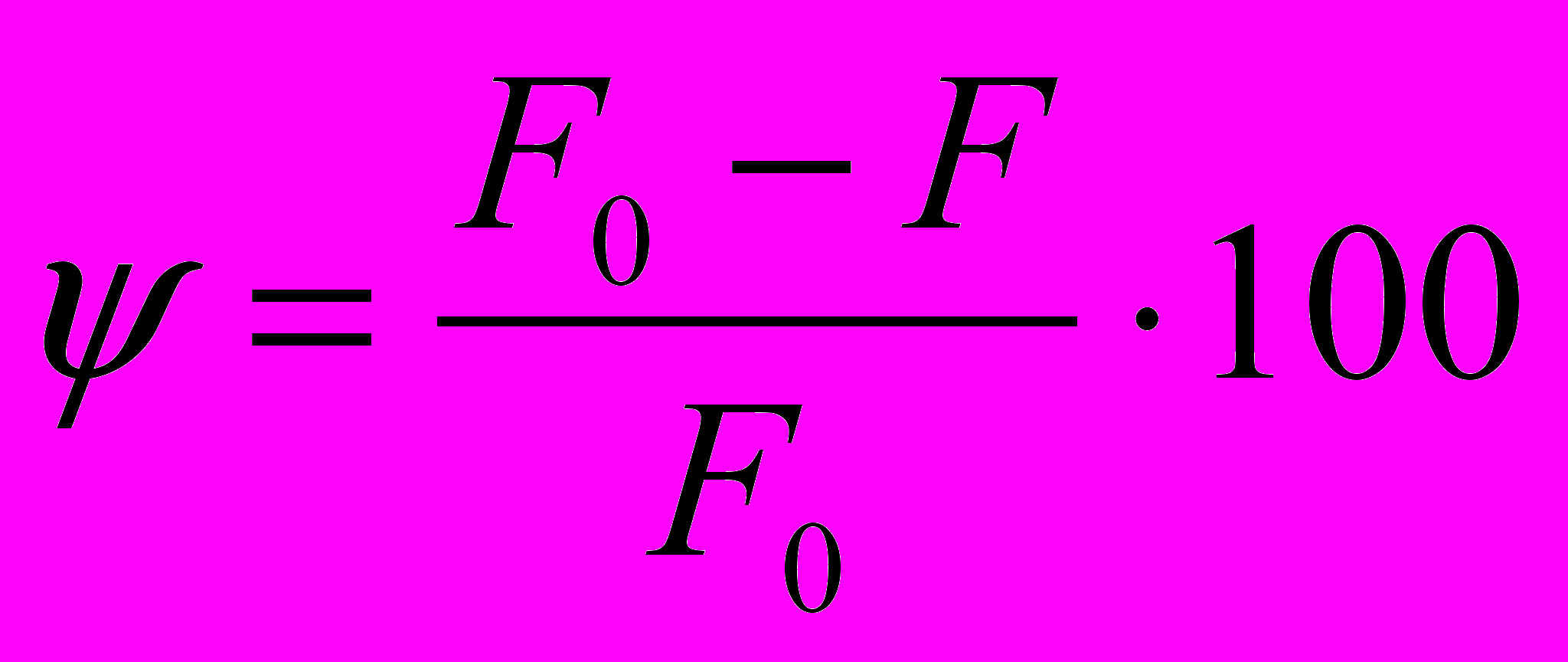
где F0 - начальная площадь поперечного сечения образца, мм2;
F1 - площадь в месте разрыва, мм2.
Таким образом, при статическом испытании на растяжение определяют характеристики прочности σyп, σт (или σ0,2 ), σв и характеристики пластичности δ и Ψ.
Определение твердости. Определение твердости производится быстро и не требует сложных образцов. Кроме того, оценка твердости позволяет в некоторых случаях судить о других механических свойствах металлов (например, о пределе прочности). Поэтому испытания на твердость широко применяют на практике.
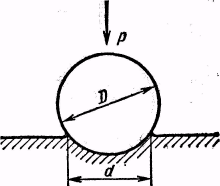
Рис. 3. Отпечаток закаленного шарика
В настоящее время наибольшее распространение имеют методы вдавливания твердого наконечника, рассмотренные ниже.
По методу Бринелля стальной закаленный шарик диаметром D (10; 5 или 2,5 мм) вдавливается в испытуемый образец силой Р. В результате на поверхности образца остается отпечаток в форме шарового сегмента диаметром d (рис. 3). Величина отпечатка будет тем меньше, чем тверже металл. Твердость по Бринеллю НВ вычисляется по формуле
HB=P/F,
где Р - нагрузка на шарик, Н (кгс);
F - величина поверхности отпечатка, мм2.
Каждая нагрузка (сила) пригодна лишь для определенного диапазона твердости, поэтому при определении твердости стали и чугуна нагрузка на шарик Р = 30 D2, для меди, ее сплавов, никеля, алюминия, магния и их сплавов Р = 10 D2, для баббитов Р = 2,5D2.
Толщина металла под отпечатком должна быть не меньше десятикратной глубины отпечатка, а расстояние от центра отпечатка до края образца - не меньше D.
Для испытания на твердость по Бринеллю в настоящее время применяют в основном рычажные прессы.
По методу Бринелля можно испытывать материалы с твердостью НВ до 4500 МПа; если материалы тверже, то стальной шарик может деформироваться. Этот метод непригоден также для испытаний тонколистового материала.
По методу Роквелла испытание на твердость производится путем вдавливания в образец стального шарика диаметром D = 1,58 мм (1/16 дюйма) или алмазного конуса с углом 120°.
Стальной шарик применяется для испытания мягких металлов (твердость по Бринеллю меньше 2200 МПа) при нагрузке 981 Н (100 кгс), алмазный конус — для испытания твердых металлов при нагрузке 1471 Н (150 кгс).
Число твердости по Роквеллу обозначается HR с добавлением индекса шкалы, по которой производилось испытание, например HRB или HRС. Для испытания очень твердых материалов применяют алмазный конус при нагрузке 588 Н (60 кгс), отсчеты производят по черной шкале, а число твердости обозначают HRA.
Метод Виккерса позволяет измерять твердость как мягких, так и очень твердых металлов и сплавов; он пригоден для определения твердости тонких поверхностных слоев (например, при химико-термической обработке). По этому методу в образец вдавливается четырехгранная алмазная пирамида с углом при вершине 136°. Нагрузка может применяться от 49 до 1170 Н (от 5 до 120 кгс). Замер отпечатка по диагонали производится с помощью микроскопа, находящегося при приборе.
Число твердости определяется по формуле
HV=P/d2,
где Р - нагрузка, Н (кгс);
d - длина диагонали отпечатка, мм.
^ Испытания на ударный изгиб. Если та или иная деталь машины или механизма по роду своей службы подвергается ударным нагрузкам, то металл для изготовления такой детали кроме статических
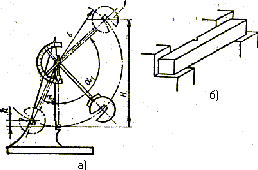
Рис. 4. Маятниковый копр
испытаний испытывают еще динамической нагрузкой, так как некоторые металлы с достаточно высокими показателями статической прочности разрушаются при малых ударных нагрузках. Такими металлами являются, например, чугун и стали с крупнозернистыми структурами.
Для ударных испытаний на изгиб применяют образцы стандартной формы. При испытании образец устанавливают на опорах маятникового копра (рис. 4). Маятник поднимают на высоту Н. Затем маятник освобождают, и он, свободно падая, ударяет по образцу и разрушает его; на это расходуется часть энергии. Оставшаяся энергия поднимает маятник на некоторую высоту h, которую определяют по шкале копра.
Работу, поглощаемую при разрушении образца, называют ударной вязкостью.
Ударная вязкость КС вычисляется по формуле
KC=K/S0 ,
где К - работа удара, затраченная на излом образца, Дж (кгс∙м);
S0 - площадь поперечного сечения образца в месте надреза, м2 (см2).
^ 1.4. Макро- и микроанализ металлов
Макроанализ. Для макроанализа приготовляют образец - шлиф или излом, по которому выявляют макроструктуру - строение металла и сплава, видимое невооруженным глазом или в лупу.
Подготовка шлифа состоит в выравнивании напильником или шлифованием наждачной бумагой поверхности. В случае необходимости шлиф травят кислотами, щелочами или растворами солей, которые
по-разному растворяют или окрашивают различные по составу или ориентации части на шлифе.
При макроисследовании определяют форму и расположение кристаллов в изделиях, полученных литьем или обработкой давлением; с помощью макроанализа можно обнаружить усадочные раковины и рыхлости, пустоты, трещины, неметаллические включения (шлак, графит в сером чугуне и т. д.), наличие и характер расположения некоторых вредных примесей, например серы.
Изломы металла дают представление о величине зерен, характере строения и структуры.
Микроанализ. Шлиф для микроанализа приготовляют так же, как и для макроанализа, но после шлифования его полируют до зеркального блеска.
По шлифу, с помощью металлографического микроскопа, выявляют микроструктуру: наличие, количество и форму тех или иных структурных составляющих, загрязненность посторонними включениями. Наличие и размеры пор и неметаллических включений определяют по нетравленым шлифам; для выявления основной структуры шлиф подвергают травлению.
Наряду с обычным световым микроскопом широко применяют электронный микроскоп, в котором вместо световых лучей используются электронные; эти лучи испускает раскаленная вольфрамовая спираль. Электронный микроскоп обеспечивает электронно-оптическое увеличение в несколько тысяч и десятков тысяч раз.
^ 2. ТЕОРИЯ СПЛАВОВ
Металлическими сплавами называют сочетание двух или нескольких металлов и неметаллов, у которых сохраняются металлические свойства. Большинство сплавов получают в жидком состоянии (сплавлением), однако они могут быть получены также путем спекания, электролиза, конденсации (сгущения) из парообразного состояния и др.
Компонентами называют химические элементы или их соединения в составе сплава.
По числу компонентов сплавы делят на двойные, тройные и т. д. В зависимости от природы компонентов, составляющих сплав, различают:
1) сплав - механическая смесь компонентов;
2) сплав - твердый раствор компонентов;
3) сплав - химическое соединение компонентов.
Сплавы - механические смеси неоднородны и представляют собой мельчайшую смесь кристаллитов компонентов.
Сплавы - твердые растворы и сплавы - химические соединения однородны, причем первые могут образовываться при различном соотношении компонентов, а вторые — только при строго определенном весовом соотношении компонентов, как всякое химическое соединение. В сплавах - твердых растворах атомы растворимого вещества замещают атомы растворителя в кристаллической решетке (рис. 5, а) или выделяются в нее (рис. 5, б); сплавы - химические соединения - образуют новую, особую кристаллическую решетку.
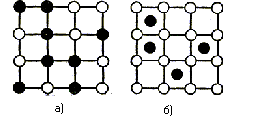
Рис. 5. Схемы твердых растворов
Системой называют совокупность веществ в твердом, жидком и газообразном состояниях. Системы бывают простые и сложные. Простая система состоит из одного компонента. Сложная система включает несколько компонентов и представляет все возможные количественные сочетания их при различных температурах.
Фазой называют однородную часть системы, отделенную от других составляющих (фаз) поверхностью раздела. Следовательно, фазами могут быть химические элементы, твердые и жидкие растворы и химические соединения. В жидком состоянии однородная система содержит одну фазу; при затвердевании всегда имеются две фазы - жидкая и твердая. После затвердевания образуется или одна фаза (химический элемент, химическое соединение, твердый раствор), или сплав, содержащий смесь фаз.
^ 2.1 Диаграммы состояния
Диаграммы состояния представляют системы, компоненты которых полностью взаимно растворяются в жидком состоянии. Они характеризуют процессы затвердевания и структурного изменения различных сплавов и дают наглядное представление о фазах в любом сплаве данной системы. По диаграмме состояния сплавов данных компонентов можно заранее судить о свойствах всех сплавов системы.
Диаграмма состояния позволяет выбирать температуру нагрева сплава при термической обработке, обработке давлением, температуру нагрева для литья. Построение диаграмм состояния производится по кривым охлаждения, полученным посредством термического анализа.
Термический анализ сводится к выявлению критических точек при нагревании и охлаждении металлов и сплавов и обычно сопровождается построением кривых в координатах температура - время.
Если в затвердевшем металле не происходит никаких фазовых превращений, кривая охлаждения (нагревания) будет плавной без перегибов и уступов; если же при охлаждении (или нагревании) металла в нем происходят фазовые превращения, которые сопровождаются выделением (при нагревании - поглощением) тепла, на кривой появятся горизонтальные участки или изломы (т. е. изменения направления кривой). Эти изломы и горизонтальные участки позволяют определять температуры превращений.
^ Диаграммы состояния сплавов, компоненты которых в твердом состоянии образуют механические смеси. Разберем построение диаграммы состояния этого типа на примере системы сплавов свинец -сурьма
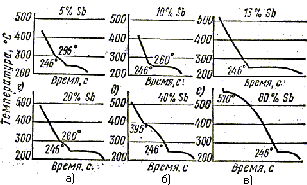
Рис. 6. Кривые охлаждения сплавов
(РЬ - Sb).К системе сплавов свинец-сурьма относятся все составы между чистим свинцом (100 % РЬ) и чистой сурьмой (100 % Sb).
Чтобы не рассматривать сплавы всех составов, ограничимся шестью - с содержанием сурьмы 5, 10, 13, 20, 40 и 80 %. Если нагреть каждый сплав до полного расплавления и с помощью пирометра и самописца снять кривую охлаждения, то получим кривые (рис. 6). Перегибы и горизонтальные участки кривых характеризуют замедление или остановки падения температуры сплавов при равномерном охлаждении и показывают наличие критических точек при данных температурах.
На кривых рис. 6, а, б, г, д, е видно по две критические точки при затвердевании сплавов и только на одной кривой (рис. 6, в) для сплава с 13 % Sb - одна критическая точка - 246ْ С. Верхние критические точки соответствуют началу затвердевания, нижние - полному затвердеванию.
Воспользуемся критическими точками для построения диаграммы состояния сплавов свинец - сурьма, отложим в масштабе но абсциссе точки по составу сплавов, принимая, что слева будет чистый свинец, а справа - чистая сурьма (рис. 7). По вертикали разметим шкалу температуры и отложим критические температуры указанных сплавов. Свинец имеет температуру плавления 327 °C, сурьма - 630 °С. Соединяя нижние критические точки, получим прямую DE, а соединяя верхние точки - две кривые АВ и ВСS сходящиеся в точке В с прямой DE.
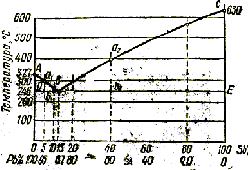
Рис. 7. Диаграмма состояния сплавов, компоненты которой в твердом
состоянии образуют механическую смесь
Построенная диаграмма показывает, что начало затвердевания различных сплавов системы происходит при разных температурах, а окончание затвердевания — при одной температуре для всей данной системы сплавов и что только у одного сплава (13 % Sb) и у чистых металлов - по одной критической точке, каждая из которых отвечает температуре полного затвердевания.
Выше линии ABC все сплавы находятся в жидком состоянии. Линия ABC называется линией ликвидус.
Ниже линии DBE все сплавы находятся в твердом состоянии. Линия DBE называется линией солидус.
Проследим процесс кристаллизации сплавов данной системы и получающуюся в результате структуру.
В точке В при содержании 13 % Sb, 87 % Pb и при температуре 246° кристаллизация свинца и сурьмы происходит одномоментно; образуется тонкая механическая смесь кристаллов свинца и сурьмы (двух фаз). Эта смесь называется эвтектикой, а сплав соответствующего состава - эвтектическим. Эвтектический сплав имеет самую низкую температуру плавления из всех сплавов данной системы. Схема микроструктуры эвтектического сплава свинец - сурьма приведена на рис. 8,а, где видны черточки кристаллов сурьмы на фоне темных участков кристаллов свинца.
Сплавы, содержащие меньше 13 % Sb, называются доэвтектическими, а содержащие больше 13 % Sb - заэвтектическими.
Доэвтектический сплав, содержащий 5 % Sb, выше первой критической точки а1 (рис. 7) находится в жидком состоянии. При охлаждении в точке а1 из жидкого раствора выпадают центры кристаллизации (центрами кристаллизации называют мельчайшие частицы, зарождающиеся в жидком или твердом металле (или сплаве)) чистого свинца, так как свинец в этом сплаве находится в количестве, избыточном по сравнению с эвтектическим составом. При дальнейшем охлаждении между точками а1 и b1 продолжается рост имеющихся кристаллов свинца и выпадение новых, поэтому количество свинца в жидком растворе постепенно уменьшается, и около точки b1 раствор имеет эвтектический состав. Во второй критической точке b1 при температуре 240 °С происходит кристаллизация всего оставшегося раствора эвтектического состава. Ниже точки b1 сплав находится в твердом состоянии и представляет смесь кристаллов избыточного свинца и эвтектики (рис. 8, б).
Аналогично идет процесс кристаллизации заэвтектических сплавов. Сплав, содержащий 40% Sb, выше первой критической точки а2 (рис. 7) находится в жидком состоянии. При охлаждении в точке а2 из жидкого раствора выпадают центры кристаллизации чистой сурьмы. При дальнейшем охлаждении между точками а2 и b1 продолжается рост имеющихся кристаллов сурьмы и выпадение новых, поэтому количество сурьмы в растворе постепенно уменьшается и около точки b2 раствор имеет эвтектический состав. Во второй критической точке b2 при температуре 246°С происходит кристаллизация всего оставшегося раствора эвтектического состава. Ниже точки b2 сплав находится в твердом состоянии и содержит смесь кристаллов сурьмы и эвтектики (рис.8, в).
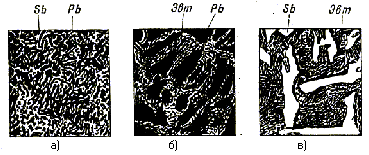
Рис. 8. Микроструктуры сплавов системы Pb-Sb
Обобщая изложенное применительно ко всей системе сплавов свинец - сурьма, отметим следующее:
- по линии А В диаграммы (рис. 7) начинается выпадение кристаллов свинца;
- в области диаграммы ABD находятся кристаллы свинца и жидкий раствор, концентрация которого около линии BD приближается к эвтектической;
- по линии BD затвердевает весь оставшийся раствор эвтектического состава;
- ниже линии BD находятся твердые доэвтектические сплавы, состоящие из кристаллов свинца и эвтектики;
- по линии ВС начинается выпадение кристаллов сурьмы;
- в области диаграммы С BE находятся кристаллы сурьмы и жидкий раствор, концентрация которого около линии BE приближается к эвтектической;
- до линии BE затвердевает весь оставшийся раствор эвтектического состава;
- ниже линии BE находятся твердые заэвтектические сплавы, состоящие из кристаллов сурьмы и эвтектики.
При нагревании сплавов вначале по линии солидуса (DE) расплавляется эвтектика, в которой при дальнейшем нагревании постепенно растворяются кристаллы свинца (у доэвтектических сплавов) или сурьмы (у заэвтектических сплавов); растворение заканчивается по линии ликвидуса (ABC), выше которой находятся жидкие растворы системы сплавов.
^ Правило отрезков (рычага). Пользуясь диаграммой состояния, можно определить количество эвтектики в сплаве, а также количество жидкого раствора (жидкой фазы) и его концентрацию в любой момент затвердевания сплава. Для примера возьмем часть диаграммы системы сплавов свинец — сурьма, характеризующую доэвтектические составы (рис. 9).
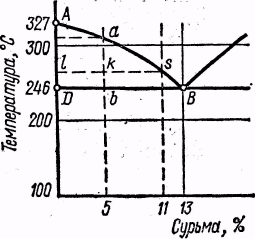
Рис. 9. Графическое отображение правила отрезков (рычага)
Соотношение жидкой и твердой фаз в любой точке отрезка (при любой температуре затвердевания сплава) определяется плечами горизонтального рычага, проведенного через данную точку. Так, масса жидкой фазы в точке k соответствует плечу lk, масса твердой фазы - плечу ks рычага ls, а масса всего сплава - длине рычага ls. Для измерения плеч рычага можно пользоваться любым масштабом; проще всего для этого взять готовую шкалу процентного содержания сурьмы. Пользуясь этой шкалой, находим что жидкая фаза взятого сплава в точке k, составляет 5/11, а твердая - 6/11 от массы сплава. При дальнейшем охлаждении количество жидкой фазы будет постепенно уменьшаться и к точке в составит 5/13 от всего сплава. В этой точке произойдет затвердевание оставшегося жидкого раствора, который перейдет в эвтектику. Следовательно, содержание эвтектики в сплаве 5 % Sb составит 5/13 массы сплава.
Если обозначить через ^ Q массу взятого сплава, через Ql - массу жидкой фазы, через Qs - массу твердой фазы, то по правилу рычага можно написать следующие соотношения: Ql/QS = ls/ks; Ql/Q =lk/ls; Qs/Q = ks/ls.
Концентрация раствора сплава в любой точке отрезка ab определяется проекцией данной точки на линию ликвидуса; так, в точке а раствор будет содержать 5 % Sb, в точке k - 11 % Sb, а в точке b - 13 % Sb. Таким образом, состав раствора данного сплава при затвердевании определяется точками на линии ликвидуса в зависимости от температуры.
^ Ликвация по плотности. Если доэвтектический сплав свинец-сурьма охлаждать медленно, то образующиеся кристаллы свинца, будучи тяжелее раствора, станут опускаться и скапливаться на дне тигля. В затвердевшем таким образом слитке эвтектика окажется в верхней части, а свинец - в нижней. При затвердевании заэвтектических сплавов выпадающие кристаллы сурьмы окажутся легче раствора и всплывут, поэтому в слитке эвтектика окажется внизу, а чистая сурьма - наверху. Это явление носит название ликвации по плотности.
Таким образом, ликвация - неоднородность химического состава сплавов, возникающая при кристаллизации.
В результате ликвации по плотности получаются слитки, неодпородные по составу, структуре и свойствам в различных частях и поэтому непригодные для изделий. Для предотвращения ликвации сплавы следует охлаждать быстрее, чтобы кристаллы не успевали всплывать или тонуть.
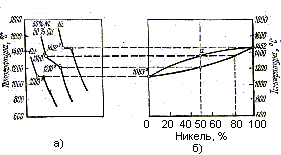
Рис. 10. Диаграмма состояния сплавов
с неограниченной растворимостью компонентов в твердом состоянии
^ Диаграммы состояния сплавов с неограниченной растворимостью компонентов в твердом состоянии. Примером такой диаграммы является диаграмма системы сплавов медь - никель (Сu - Ni).
Если взять несколько сплавов Сu - Ni различной концентрации и наблюдать за их охлаждением, подобно тому как это делалось со сплавами РЬ - Sb, то по полученным критическим точкам можно построить диаграмму состояния системы сплавов Сu - Ni.
На рис. 10, а в координатах температура - время приведены кривые охлаждения чистой меди, сплава, содержащего 50 % Сu и 50 % Ni, и чистого никеля. Как видно из приведенных кривых, горизонтальные участки (кристаллизация при неизменной температуре) имеются лишь у чистых металлов, а сплавы кристаллизуются в интервале температур между ликвидусом и солидусом. На рис. 10, б в координатах температура - концентрация размечены точки по кривым рис. 10, а; при соединении этих точек образуются две кривые: верхняя - ликвидуса и нижняя - солидуса. Эти кривые показывают, что, как начало, так и окончание затвердевания происходят при неодинаковых температурах для различных сплавов системы.
Проследим процесс затвердевания на примере сплава, содержащего 50 % Сu. Выше точки а сплав находится в жидком состоянии. При охлаждении в точке а из жидкого раствора начинают выделяться кристаллы твердого раствора меди в никеле, причем концентрация этого первоначального твердого раствора отличается от исходной повышенным содержанием компонента Ni (с более высокой температурой плавления) и может быть приблизительно определена, если из точки а провести горизонталь до пересечения с линией солидуса. В данном примере концентрация никеля в центрах кристаллизации достигнет 83 %. При дальнейшем охлаждении кристаллы твердого раствора растут неоднородными за счет жидкой фазы,; непрерывно обедняющейся никелем, и последние доли жидкого раствора содержат значительно меньше никеля, чем исходный жидкий раствор.
Однако при медленном охлаждении в каждый момент кристаллизации состав самих кристаллов выравнивается путем диффузии.
Если же охлаждение происходит быстро, состав внутри кристаллов не успевает выровняться и внутренние части каждого кристалла содержат больше тугоплавкого компонента (никеля), чем внешние.
Это явление называется внутрикристаллической (дендритной) ликвацией.
Внутрикристаллическая ликвация может быть устранена отжигом, и тогда сплав - твердый раствор будет всюду одинаков по концентрации никеля (50 %). Следовательно, сплавы - твердые растворы в отличие от сплавов - смесей являются однофазными. Взаимная растворимость компонентов в твердом состоянии определяется:
- близостью их расположения в периодической системе Менделеева (т. е. сходностью строения электронных оболочек их атомов);
- близостью атомных диаметров;
- подобием формы кристаллических решеток;
- близостью температур плавления компонентов.
При уменьшении сродства компонентов по одному или нескольким из этих признаков образуются системы сплавов с ограниченной взаимной растворимостью.
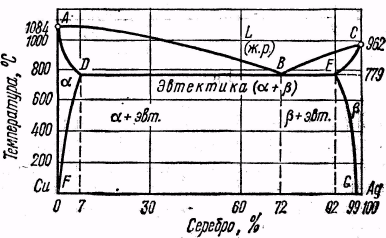
Рис. 11. Диаграмма состояния сплавов
с ограниченной растворимостью компонентов в твердом состоянии
^ Диаграмма состояния сплавов с ограниченной растворимостью компонентов в твердом состоянии. Такова диаграмма, например, для системы сплавов медь - серебро (Сu - Ag). Линия ABC (рис. 11) - ликвидус; выше этой линии находятся жидкие растворы (ж. р.); линия ADBEC - солидус. Верхняя часть диаграммы показывает, что оба компонента взаимно растворимы, но в ограниченном количестве: предельная концентрация раствора а (серебра в меди) - 7 %, а раствора β (меди в серебре) - 8 %. При большей концентрации по линии DE образуется эвтектика растворов а + β. Кривые DF и EG показывают, что при охлаждении ниже линии эвтектики (DE) происходит постепенный распад твердых растворов а и β (выпадение серебра из раствора а и меди из раствора β); при температуре 0о раствор а не существует, а раствор β имеет концентрацию 1 % (в сплавах, содержащих более 1 % меди).
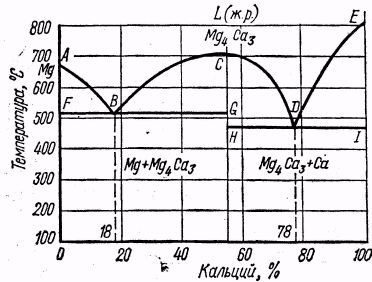
Рис. 12. Диаграмма состояния сплавов с образованием устойчивых
химических соединений компонентов
^ Диаграмма состояния сплавов с образованием устойчивых химических соединений компонентов. На рис. 12 приведена диаграмма состояния системы сплавов магний - кальций (Mg - Са). Химическое соединение Mg4Ca3 можно рассматривать как новый, третий компонент, который делит диаграмму состояния Mg - Са на две диаграммы (Mg - Mg4Ca3 и Mg4Ca3 – Са); каждая из них подобна системе свинец – сурьма. Для первой линия ABC - ликвидус, линия FG - солидус. По линии АВ начинается выпадение кристаллов магния; по линии ВС - выпадение кристаллов соединения Mg4Ca3. В точке В одновременно кристаллизуются Mg и Mg4Ca3, образуя эвтектику. Доэвтектические сплавы этой системы представляют собой смесь кристаллов магния и эвтектики, а заэвтектические - смесь кристаллов соединения Mg4Ca3 и эвтектики.
^ Диаграммы состав - свойство. Эти диаграммы являются дополнением к диаграммам состояния сплавов, так как они для каждой системы характеризуют изменение того или иного свойства сплава в зависимости от состава.
На рис. 13 в верхнем ряду изображены диаграммы состояния компонентов А и В, в среднем — диаграммы изменения твердости Н, в нижнем - диаграммы изменения электропроводности Е.
В сплавах типа Pb - Sb (рис. 13, а) свойства изменяются прямолинейно от одного компонента к другому; в сплавах типа Си - Ni (рис. 13, б) изменение свойств идет неравномерно, причем твердость при увеличении содержания компонента В сначала возрастает, а затем падает; электропроводность наоборот, вначале падает, потом возрастает.
В системе сплавов с ограниченной растворимостью компонентов (рис. 13, в) свойства изменяются в соответствии с принадлежностью той или иной части диаграммы к виду а) или б): сначала, пока образуется смесь растворов, свойства изменяются прямолинейно; затем, когда образуется твердый раствор, прямолинейный ход изменения свойств нарушается.
Изменения свойств в сплавах - химических соединениях (рис. 63, г) выражаются ломаными линиями, и каждое из них может быть представлено двумя различными прямыми на двух отдельных диаграммах, так же
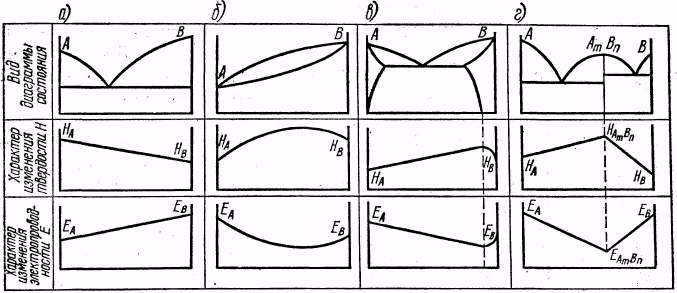
Рис.13. Диаграммы состав - свойство
как и сама диаграмма может быть разделена на две диаграммы вида а), т. е. сплавов - механических смесей.
Помимо твердости, прочности, электропроводности диаграммы состояния дают возможность определять литейные свойства, способность поддаваться горячей механической обработке, обработке резанием и др.
Величина перепада температур между точками ликвидуса и солидуса определяет степень ликвации и возможной неоднородности сплава; эвтектические сплавы имеют лучшие литейные свойства (наиболее низкую температуру плавления из всех сплавов системы, высокую жидкотекучесть, незначительную ликвацию) и обрабатываемость резанием; сплавы - твердые растворы хорошо обрабатываются давлением.