Машинобудування України очима молодих: прогресивні ідеї – наука – виробництво”
Вид материала | Документы |
- Аналітична довідка за 2011 рік щодо економічного розвитку вінницької області промислове, 109.63kb.
- Агропромисловий комплекс (виробництво та переробка сільськогосподарської продукції);, 288.16kb.
- Відбулась фінальна частина акції “Охорона праці очима дітей”, 18.49kb.
- Національна академія наук України оголошує конкурс на здобуття премій молодих учених, 39.89kb.
- Національна академія наук України Міністерство освіти та науки України бюлетень, 2255.17kb.
- Міністерство освіти І науки україни східноукраїнський національний університет імені, 206.5kb.
- Тема Менеджмент як наука, 242.26kb.
- Інформація щодо реалізації реформ Президента України в агропромисловому комплексі району, 40.61kb.
- Балака Максим Миколайович, асистент кнуба міщук Дмитро Олександрович, асистент кнуба, 73.22kb.
- Політична історія України, 110.04kb.
1 2
Міністерство освіти і науки України
Державний комітет молодіжної політики, спорту та туризму України
Сумська обласна державна адміністрація
Житомирський інженерно-технологічний інститут
Запорізький державний технічний університет
Кримський державний індустріально-педагогічний інститут
Національний технічний університет України
“Київський політехнічний інститут”
Національний технічний університет України
“Харківський політехнічний інститут”
Сумський державний університет
Сумський державний центр
науково-технічної і економічної інформації
Технологічний університет Поділля
^ Тези доповідей
Першої Всеукраїнської молодіжної науково-технічної конференції
“Машинобудування України очима молодих:
прогресивні ідеї – наука – виробництво”
^ 31 жовтня – 3 листопада 2001 року
Суми – 2001
Міністерство освіти і науки України
Державний комітет молодіжної політики, спорту та туризму України
Сумська обласна державна адміністрація
Житомирський інженерно-технологічний інститут
Запорізький державний технічний університет
Кримський державний індустріально-педагогічний інститут
Національний технічний університет України
“Київський політехнічний інститут”
Національний технічний університет України
“Харківський політехнічний інститут”
Сумський державний університет
Сумський державний центр
науково-технічної і економічної інформації
Технологічний університет Поділля
^ Тези доповідей
першої Всеукраїнської молодіжної науково-технічної конференції
“Машинобудування України очима молодих:
прогресивні ідеї – наука – виробництво”
^ 31 жовтня – 3 листопада 2001 року
Суми – 2001
УДК 621.9
Тези доповідей Першої Всеукраїнської науково-технічної конференції «Машинобудування України очима молодих: прогресивні ідеї – наука - виробництво». – Суми: СумДУ, 2001. – ХХХ стр.
Збірник містить тези доповідей молодих вчених-машинобудівників України присвячені проблемам технології машинобудування, теоретичним та експериментальним досліжденням процесів механічної обробки, удосконаленню різального інструмента та верстатів.
Тези доповідей становлять інтерес для студентів, аспірантів, наукових та інженерно-технічних робітників машинобудівного профілю.
Сумський державній університет
Экспериментальное исследование
влияния режима резания на технологические показатели
процесса тангенциального точения
А. С. Ануфриев, асп., С. В. Зеленський, студ.
Сумський державний університет, Суми
В докладе отмечается, что одним из основных вопросов современного машиностроения является решение проблемы обеспечения долговечности и качества продукции на каждом этапе ее изготовления и эксплуатации. При данных условиях прогнозирование выходных показателей процессов механической обработки, в частности, показателей качества, в условиях автоматизированного производства является актуальной задачей.
Процесс тангенциального точения (ТТ) позволяет реализовать роторные станки для обработки коротких тел вращения в условиях серийного и массового производства. Они имеют простую конструкцию, занимают меньшие производственные площади, обладают высокими производительностью и показателями качества обработки, работают без применения СОЖ, что особенно важно для повышения экологической безопасности современного производства. Одним из перспективных направлений в станкостроении является создание малогабаритных роторных станков для обработки коротких тел вращения. Вместе с тем, их проектирование существенно затрудняется отсутствием информации о показателях процесса ТТ при обработке различных металлов и сплавов.
В данной работе представлены результаты экспериментальных исследований процесса точения канавок с прямолинейной попутной тангенциальной подачей в заготовках из бронзы. Изучалось влияние режима резания на проекции силы резания, шероховатость и погрешность формы и взаимного расположения обработанной поверхности.
Проведенные исследования и теоретические выкладки дали возможность сделать выводы о влиянии режимов резания на проекции силы резания, качество обработанной поверхности (шероховатость, погрешность формы и взаимного расположения) коротких тел вращения из бронзы при тангенциальном точении.
Выполненная работа позволила сформулировать цели и задачи дальнейших исследований качества обработанной поверхности после тангенциального точения.
^ ДОСЛІДЖЕННЯ ДИНАМІКИ РУХУ ВІБРАЦІЙНО-ВІДЦЕНТРОВИХ ЗМІЦНЮВАЛЬНИХ ПРИСТРОЇВ З ЕЛЕКТРОМАГНІТНИМ ПРИВОДОМ
І.С. Афтаназів, д.т.н., проф., О.Р. Баранецька, к.т.н., ст.викл., Я.М. Кусий
Національний університет “Львівська політехніка”, Львів
Нові перспективні методи та сучасні технології викінчувально-зміцнювального оброблення деталей машин та механізмів вимагають грунтовного дослідження як власне самих методів, так і моделювання виконавчих рухів спроектованого технологічного обладнання, оптимізації режимів оброблення та автоматизації розрахунків конструктивних параметрів зміцнювальних пристроїв.
Розроблені у Національному університеті “Львівська політехніка” вібраційно-відцентрові зміцнювальні пристрої з електромагнітним приводом та пружними системами, на нашу думку, є найбільш придатними для вирішення однієї із головних проблем машинобудування – підвищення надійності та забезпечення довговічності поверхонь довгомірних циліндричних деталей, зокрема внутрішніх.
Скориставшись методом механічного імпедансу та енергетичним методом розрахунку вібраційних систем, виведено математичні залежності, що описують рух однопривідного електромагнітного вібраційно-відцентрового зміцнювального пристрою. Розв’язок cистеми рівнянь отримано за допомогою прикладних програм на ПЕОМ, зокрема Mathlab, Mathcad.
Експериментальне підтвердження адекватності отриманих рівнянь руху зміцнювального інструменту здійснено за допомогою вібровимірювального комплексу, який включає давач моделі “VS-080”, що сприймає вібрації визначених точок елементів зміцнювального інструменту та перетворює їх у електричний сигнал, прилада-перетворювача “VIBROTEST 30” фірми SCHENCK, що перетворює електричний сигнал в аналоговий, 16-ти розрядного аналого-цифрового перетворювача (звукової карти ПЕОМ), що сприймає сигнал від прилада-перетворювача, та програмного забезпечення (програми Sound Forge версії 4.5) для оброблення закодованої інформації.
Результати експериментальних досліджень свідчать про адекватність отриманих математичних залежностей, відносна похибка між експериментальним та теоретичним значенням амплітуд коливань досліджуваних елементів пружних систем не перевищує 12 %.
Рівняння руху зміцнювального інструменту дозволяють вирішувати дві взаємно обернені задачі:
- за конструктивними розмірами та характеристиками складників зміцнювального пристрою, що визначені в результаті попередніх розрахунків, встановлюють амплітуди коливань руху елементів пружних систем та оптимальні значення зазорів між складниками електромагнітного приводу розмахи коливань виконавчих органів для здійснення ППД
- за наперед заданими величинами коливань складників зміцнювального пристрою розраховують конструктивні параметри елементів пружних систем.
Напрямки удосконалення чистових торцевих фрез для обробки плоских поверхонь деталей
В. М. Бушля, асп.
Житомирський інженерно – технологічний інститут, Житомир
Серед перспективних технологічних напрямків при фінішній обробці площин на даний час можна відмітити застосування процесів чистового торцевого фрезерування, що забезпечують необхідну якість та продуктивність обробки. При цьому виникає задача визначення інструмента для чистової обробки плоских поверхонь.
Відсутність стандартних торцевих фрез, які оснащені НТМ, пояснюється протиріччям рекомендацій що до раціональних конструкцій торцевих фрез. Тому задача визначення інструмента для чистової обробки вирішується проектуванням нових фрез. Серед багатьох напрямків для вирішення цієї задачі можна визначити використання торцевих фрез з спірально - ступінчатими схемами різання. При використанні спірально - ступінчастої схеми різання ножі фрези розташовані в радіальному напрямку на різній відстані від осі фрези (по різних видах спіралей), а в осьовому – ступенями зі змінним значенням вильоту.
За ціль даної роботи було поставлено розробку методики визначення раціональної схеми різання для спірально - ступінчатого варіанту, тобто отримання найкращої кількості ступенів та відповідного виду спіралі. Для вирішення поставленої цілі проводився аналіз впливу кількості ножів т, що одночасно приймають участь в різанні, від схеми та змінних параметрів різання. Цей вплив розглядався для періоду сталого різання. В якості параметрів для визначення раціональності приймалася середня кількість ножів
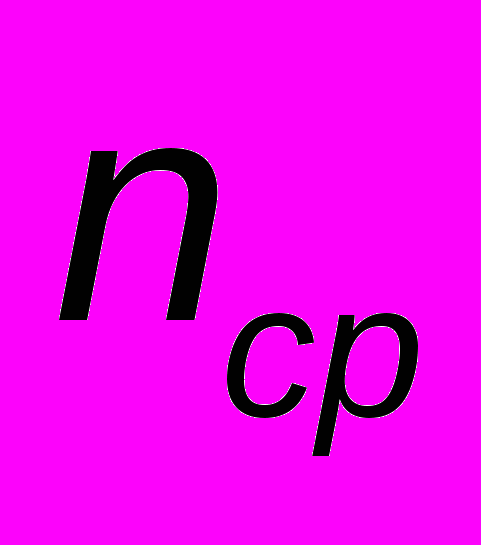
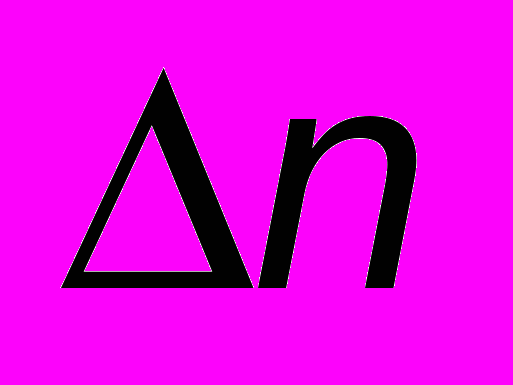
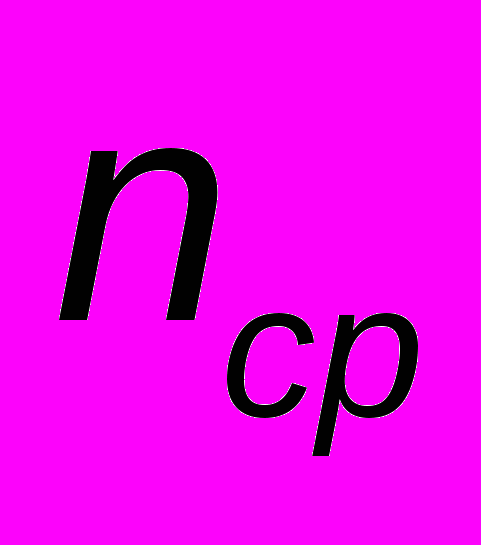
В якості об’єкта приймалася торцева фреза з різними кількостями ступіней та архімедовою, логарифмічною та евольвентною спіралями. Аналіз даних за першим параметром виділяє одно – та двоступеневі схеми різання як варті розгляду, в той час як останні два параметри вказують на раціональність саме двоступеневої схеми різання, через її кращі показники перед всіма іншими. Тому визначення раціонального виду спіралі будемо проводити саме для двоступеневої схеми різання. Аналіз проведений за тією ж самою методикою виділяє як найбільш сприятливу евольвентну спіраль. Для доведення незалежності зроблених висновків від зміни режимів різання були проведені додаткові розрахунки по впливу подачі на зміну пріоритетів для раціональності схеми різання з її варіюванням від S=0.05 до 0.5 мм/об з кроком 0,05 мм/об, всі інші параметри залишалися сталими, з величинами як і в основному розрахунку. Їх проведення підтвердило попередні результати та висновки. Тобто вказало на раціональність двоступінчастої фрези, а найкращої спіралі для такої схеми на евольвенту.
Підсумовуючи проведену роботу можна зробити висновок, що розроблена методика, її алгоритм та параметри оцінки дозволяють визначати конструктивні параметри фрези.
Анализ факторов, влияющих на качество автоматической сборки резьбовых соединений
Н. В. Водолазская, асп.
Донбасская государственная машиностроительная академия, Краматорск
Резьбовые детали являются наиболее часто встречающимися элементами сборочных единиц и используются практически во всех изделиях. От качества выполнения процесса сборки резьбовых соединений зачастую зависят работоспособность и надежность всего узла или машины. Одним из условий обеспечения качества сборки резьбовых соединений является механизация и автоматизация работ. Однако, уровень механизации и автоматизации сборки резьбовых соединений, как и других сборочных работ, все еще значительно отстает от уровня обрабатывающих областей производственного процесса. Одним из преимуществ автоматической сборки является то, что значительно повышается качество выпускаемых (собираемых) изделий, так как большинство сборочных автоматов может работать только при поступлении на сборку качественных деталей резьбового соединения, тогда как при ручной сборке могут быть употреблены и детали, имеющие значительные отклонения от заданных технических условий. Автоматическая сборка, таким образом, обеспечивает стабильное качество собираемых изделий, что не всегда возможно при ручной сборке ввиду недостаточно высокой квалификации рабочих или из-за ошибок, совершаемых рабочими по причине невнимательности, утомляемости и т. п. Кроме того, стабильность качества при автоматической сборке достигается за счет того, что в автоматическом оборудовании имеются устройства, поддерживающие необходимые показатели технологическою процесса (например, усилие, крутящий момент) строго в заданных пределах, что не всегда возможно при ручной сборке. Наконец, автоматизация регулировочных операций, имеющих место в технологическом процессе сборки, также дает лучшие результаты, чем выполнение этих операций вручную.
На качество процесса автоматизированной сборки резьбовых соединений влияют следующие факторы:
- качество деталей, входящих с резьбовое соединение;
- технологичность конструкции сборочного узла и его составляющих;
- точность сборочного оборудования;
- условия ориентации (т.к. неправильная ориентация резьбовых деталей приводит к срыву первых витков, что нарушает весь технологический процесс автоматической сборки);
- условия базирования (критерии собираемости резьбового соединения);
- усилия затяжки;
- условия стопорения (изменение конфигурации деталей резьбового соединения, ввод дополнительных элементов в резьбовое соединение);
- контроль сборочной единицы;
- дополнительные условия необходимые для конкретного резьбового соединения.
Таким образом, обеспечение высокого качества автоматизированной сборки резьбовых соединений представляет сложную комплексную проблему, одним из методов решения которой является использование системного подхода.
^ ИССЛЕДОВАНИЕ ИЗМЕНЕНИЙ НАПРЯЖЕНИЙ И ДЕФОРМАЦИЙ В ТОНКОЛИСТОВОЙ МЕТАЛЛОКОНСТРУКЦИИ ОБШИВКИ ВАГОНА ДИЗЕЛЬПОЕЗДА, ПОСЛЕ СБОРКИ-СВАРКИ И ПОСЛЕ ХОДОВЫХ ИСПЫТАНИЙ
Гедрович А. И., проф., Гальцов И. А., асп., Друзь О.Н., асп., Ткаченко С.А., инж.
Восточноукраинский национальный университет, Луганск
На ГХК «Лугансктепловоз» освоен выпуск пригородных дизельпоездов. С целью повышения коррозионной стойкости, обшивку локомотива выполняют из нержавеющей метастабильной стали 10Х13Г18Д ТУ 14-4-435-98.
Но при сборке и сварке элементов обшивки локомотива (боковые стенки, входные и тамбурные двери и. т. д.) представляющие собой сварные тонколистовые металлоконструкции, с толщиной 1,5 мм, а также после ходовых испытаний вагонов, возникает серьезная научно-технологическая проблема связанная с получением металлоконструкции требуемого качества и геометрии.
Сварка как технологический процесс получения неразъемного соединения характеризуется высоколокальным введением тепловой энергии в металл. В результате сварочного термодеформационного цикла в деталях и узлах появляются остаточные сварочные деформации и напряжения, последние могут превосходить предел текучести материала, достигая, в частности, для хромо-марганцевых аустенитных сталей значений (1,8-2)т. Этому способствует то, что нержавеющие аустенитные стали имеют низкий коэффициент теплопроводности, высокий коэффициент линейного разширения и склонны к упрочнению.
В результате экспериментальных замеров было установлено, что после сборки-сварки вагона в шве и околошовной зоне сварных соединений из стали 10Х13Г18Д напряжения превосходят предел текучести металла т в (1,6 – 1,8) раза, при допускаемых напряжениях рекомендуемых МПС по ГОСТ 14892-69 для пассажирских вагонов (0,85т); сборочно-сварочные деформации превышают предельно допустимые в 1,5-2 раза, при допускаемых деформациях рекомендуемых МПС (2 мм на 1 м изделия и не более 5 мм на все изделие).
При ходовых испытаниях вагон подвергается значительной динамической нагрузке (вибрации, ударам) в результате чего в швах обшивочных листов происходит резкое уменьшение остаточных сварочных напряжений релаксация т. е. перераспределение напряжений в металле шва и околошовной зоне с появлением деформаций до предельно допустимых, с резким возрастанием деформации в листах обшивки, превышающих предельно допустимые в 3-4 раза.
Деформации на входных и тамбурных дверях увеличивающиеся при обкатке и релаксации напряжений, приводят к заклиниванию их при открывании, перекосу, а также неплотному прилеганию к дверным проемам.
Все это приводит к нарушению герметичности вагона (течи), трещинам, отслоению мастик и лакокрасочных покрытий вагона, трещинам в стеклах, значительному ухудшению внешнего вида и аэродинамических свойств.
^ АНАЛИЗ ОХЛАЖДАЮЩИХ ЖИДКОСТЕЙ, ПРИМЕНЯЮЩИХСЯ В ПРОМЫШЛЕННОСТИ И ВОЗМОЖНОСТЬ ИХ ИСПОЛЬЗОВАНИЯ В СВАРОЧНОМ ПРОИЗВОДСТВЕ
А.И. Гедрович, д.т.н., проф., О.Н. Друзь, асп.
Восточноукраинский национальный университет, Луганск
Сложившаяся ситуация в машиностроительном комплексе Украины настоятельно требует применения новейших ресурсосберегающих технологий. Одним из таких направлений является обработка металла (резка, точение, шлифование, сварка) с искусственным охлаждением. Нами проводятся исследования применительно к разработке технологических процессов сварки с принудительным охлаждением. Применение таких технологий особенно актуально при изготовлении металлоконструкций из металла небольшой толщины. Причиной высокого уровня остаточных напряжений является большой размер зоны пластических деформаций. Поэтому перспективным направлением уменьшения остаточных напряжений и деформаций сварных конструкций является уменьшение размеров активной зоны при сварке, например, принудительный отвод тепла из свариваемого изделия, который по времени совмещен с процессом сварки.
Целью настоящей работы было выявление возможности применения известных водных растворов в качестве охлаждающей среды при сварке черных и легированных сталей. Были проанализированы жидкости, используемые в холодильных установках, автомобильных двигателях, процессах обработки резанием, процессах закалки металлов, литейном производстве и пожарной охране.
К охладителям, применяемым при сварке, сформулированы и предъявляются следующие требования: недефицитность, дешевизна, негорючесть, нетоксичность (жидкости и продуктов ее разложения), адгезия жидкости, текучесть, устойчивость к высоким температурам, не агрессивность по отношению к свариваемому металлу.
Кроме того, охлаждающий раствор должен обеспечивать стабилизацию горения электрической дуги, изоляцию сварочной ванны от атмосферного воздуха и удовлетворительное качество сварного шва.
Технологически существует три варианта охлаждения: охлаждение сварного шва, охлаждение шва и зоны пластических деформаций, и охлаждение только зоны пластических деформаций. В данном случае свойства охладителя определялись возможностью реализации только третьего варианта.
На основании проведенного литературного анализа свойств охладителей были сделаны следующие выводы: наиболее перспективным для уменьшения активной зоны при сварке является применение водных растворов поверхностно активных веществ (ПАВ), так как эффективность охлаждения раствором ПАВ на 80...100°С выше, чем эффективность охлаждения распыленной водой при прочих равных условиях. Основной вклад в теплопоглощение раствора ПАВ вносят эндотермические эффекты физико-химических превращений.
^ ОПТИМІЗАЦІЯ ПАРАМЕТРІВ ВИСОКОТОЧНИХ ШПИНДЕЛЬНИХ ВУЗЛІВ
О. П. Герасимчук, асп.; О. Ф. Гордєєв, к.т.н., проф.
Луцький державний технічний університет, Луцьк
В даній роботі оптимізуються параметри шпиндельних вузлів з точки зору їх здатності гасити коливання (по демфуючій властивості). Враховується, що шпиндельні вузли високоточних верстатів оснащуються гідростатичними опорами.
В роботі розглянуто два напрями оптимізації, які в комплексі можуть привести до значного підвищення демфуючих властивостей шпиндельного вузла, а отже й точності виготовлення на ньому виробів:
Оптимізація параметрів шпиндельних вузлів з гідростатичними опорами по демфуючій властивості.
Вирішення питань оптимальної конструкції з використанням нерухомих з’єднань в якості демферів, які здатні гасити коливання за рахунок сил тертя.
Перший напрям оптимізації ґрунтується на високих демфуючих властивостях гідростатичних опор і передбачає найбільш повне використання цих властивостей при проектуванні. При цьому застосовується метод аналізу динамічних характеристик вузлів метод визначення еквівалентної постійної часу демфування
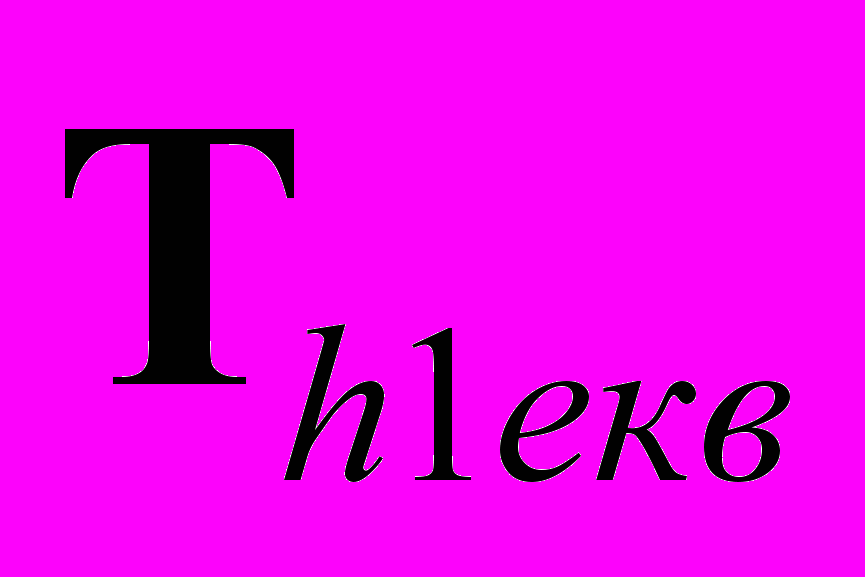
Другий напрям використовує властивості сил тертя гасити коливання в нерухомих стиках. Вектор сили тертя завжди направлений в сторону, протилежну напрямку швидкості відносних коливань спряжених деталей і тому його роль зводиться до гасіння цих коливань.
Висновки
Оптимізація гідростатичних опор по демфуючій властивості забезпечує високу здатність системи гасити коливання, а отже підвищує точність і якість оброблених на верстаті виробів.
Оптимізація конструкції як шпиндельного вузла, так і верстата в цілому шляхом збільшення кількості нерухомих стиків дає можливість отримати систему з високими демфуючими властивостями.
Як перший, так і другий напрям оптимізації, підвищуючи демфуючі властивості, знижує жорсткість системи, що впливає на точність оброблених на верстаті виробів. Одержуються деталі з меншою хвилястістю але більшими макродефектами. А тому при проектуванні важливою задачею є створення систем з оптимальними демфуючими властивостями при досягненні раціональних жорсткісних параметрів.
^ ПРОГНОЗУВАННЯ ТОЧНОСТІ ШПИНДЕЛЬНИХ ВУЗЛІВ НА ГІДРОСТАТИЧНИХ ОПОРАХ
О. Ф. Гордєєв, к.т.н., проф.; В. М. Тимчук , асп.
Луцький державний технічний університет, м. Луцьк
Для прогнозування вихідних параметрів точності шпиндельних вузлів і їх частотних характеристик зручно використовувати метод початкових параметрів в матричному формулюванні.
Прогнозування вихідних параметрів точності шпинделя і частотних характеристик шпиндельних вузлів (ШВ) практично зводиться до визначення амплітуд стаціонарних вимушених коливань шпинделя на передньому кінці від збурень зі сторони процесу різання, приводних механізмів та ін. Лінійна постановка задачі дозволяє використати принцип суперпозиції і поступово прогнозувати характеристики ШВ для кожного із регламентованих параметрів точності шпинделя.
Використання матричного методу початкових параметрів для прогнозування зміщень переднього кінця шпинделя і частотних характеристик системи шпиндель-опори показано на прикладі ШВ на гідростатичних опорах. Шпиндель розбито на три ділянки. На протязі кожної ділянки згинаючу жорсткість EJ вважають постійною і рівною деякому середньому значенню жорсткостей його частин. При значних перепадах діаметрів різних частин шпинделя число ділянок слід збільшити, так як приведення до середньої жорсткостей частин шпинделя може привести до росту похибки прогнозування. На кінцях шпинделя розміщені зосереджені маси, які відповідають планшайбі і шківу пасової передачі. На шпиндель діють збурення зі сторони процесу різання – сила
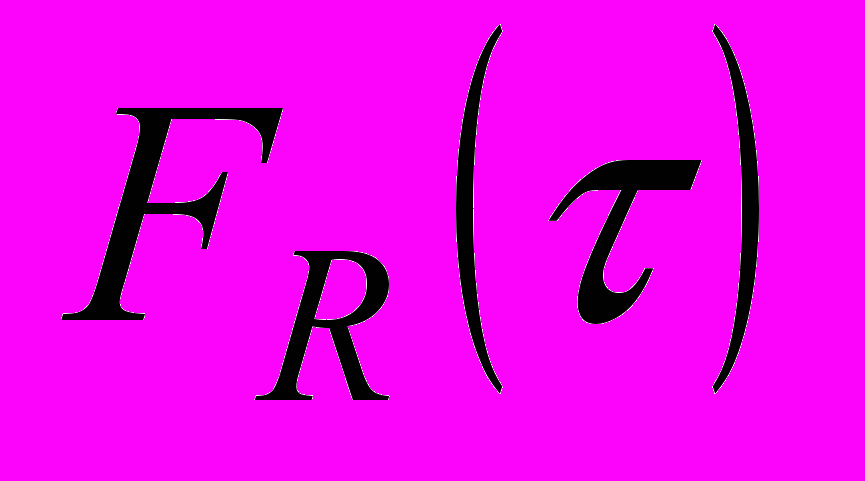
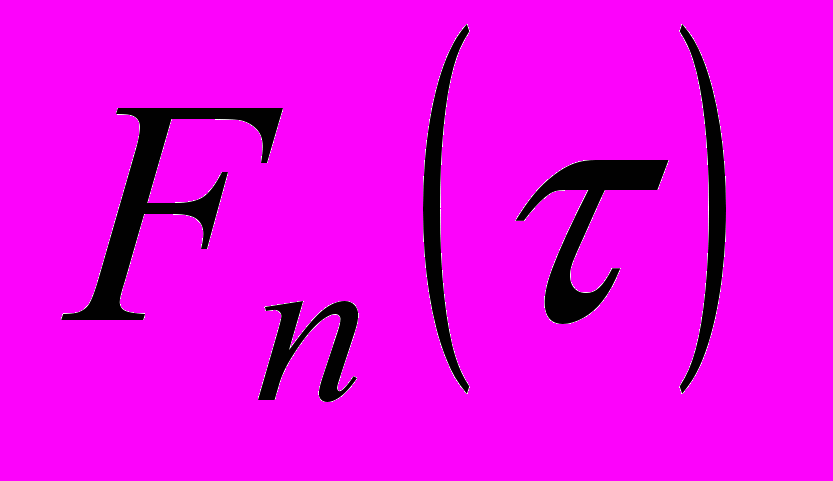
Розв’язок диференційного рівняння коливань шпинделя виражають через параметри напружено-деформованого стану
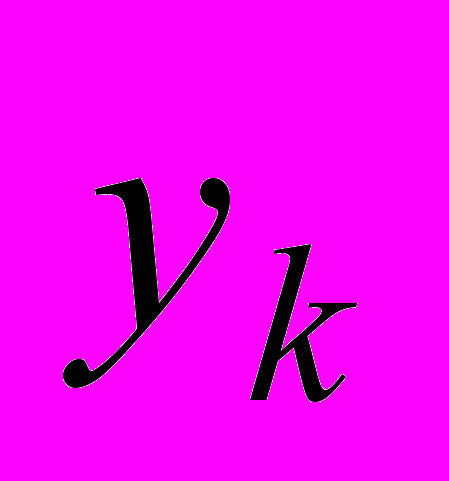
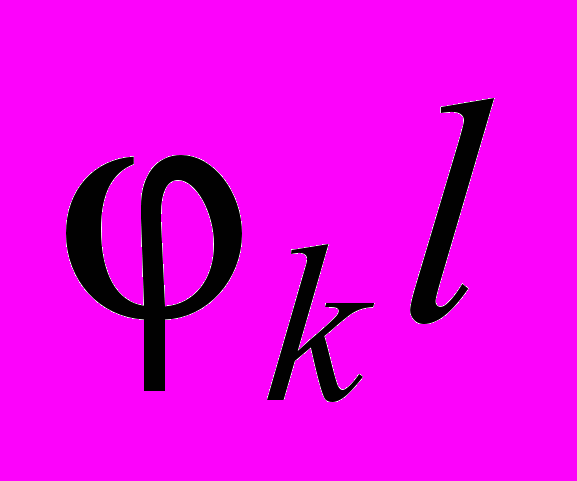
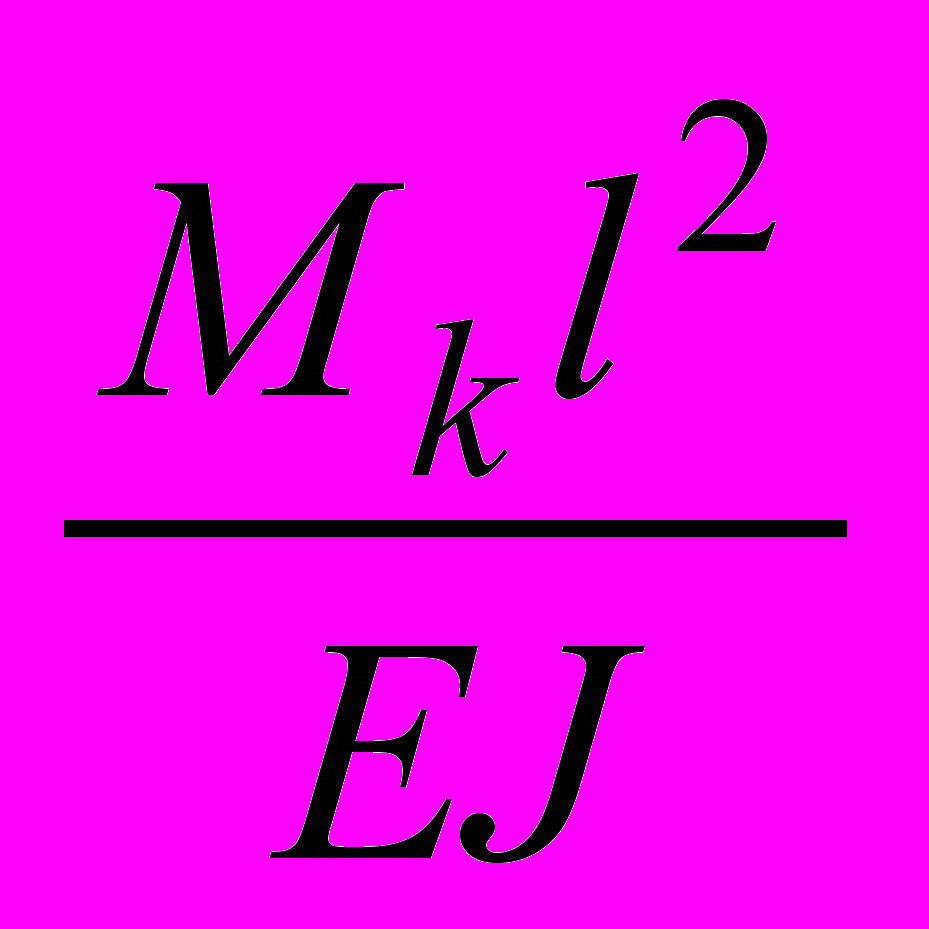
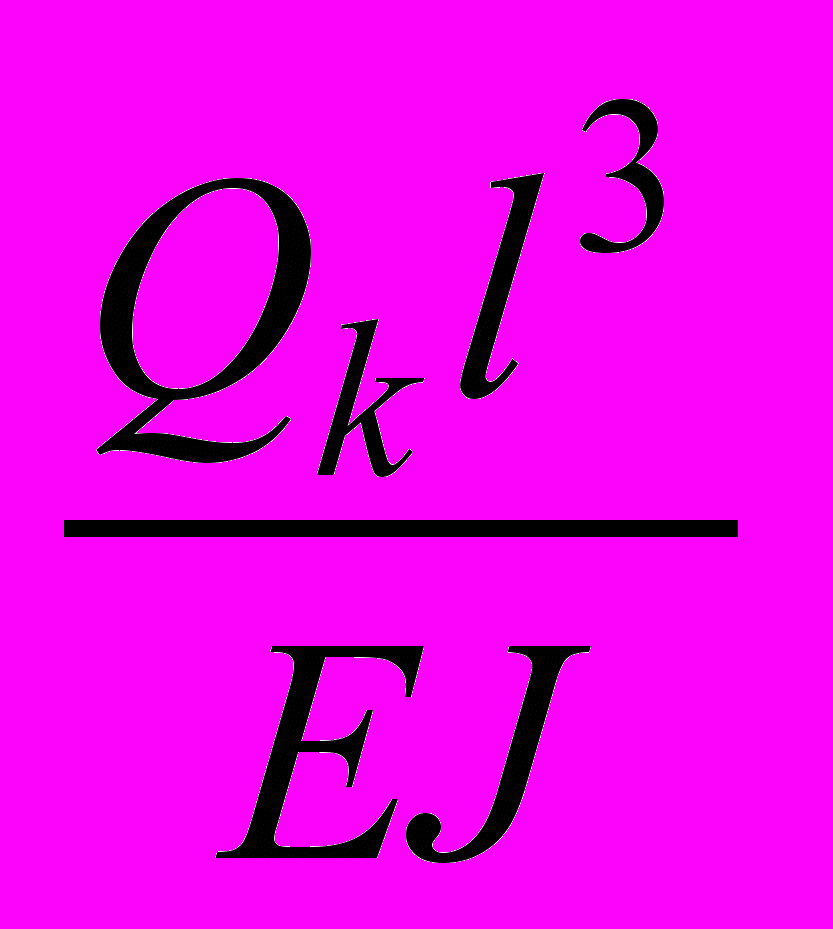
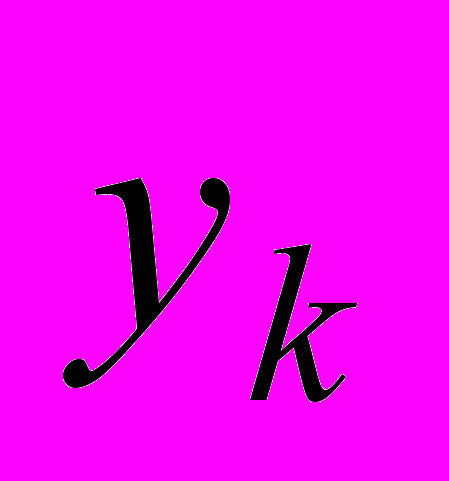
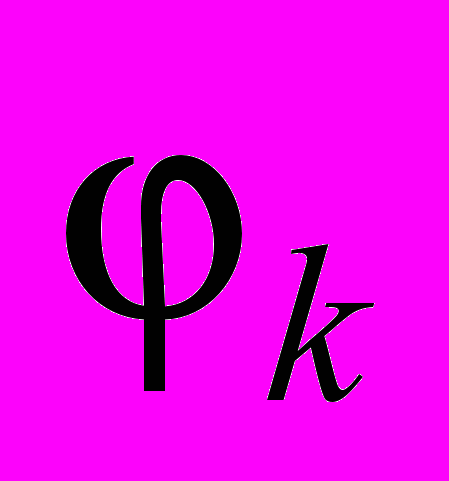
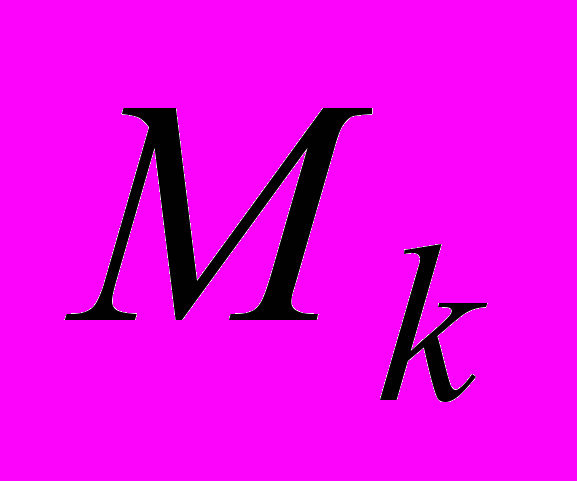
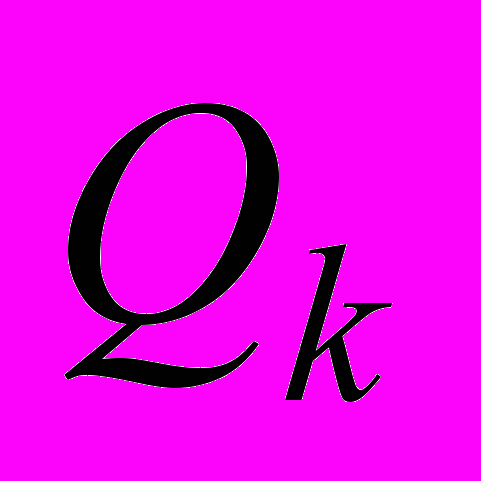
Метод дозволяє зв’язати параметри в нульовому перерізі шпинделя через перехідні матриці його перерізів і ділянок з такими ж параметрами на його задньому кінці. Складання матричного рівняння, яке пов’язує параметри на кінцях шпинделя, значно полегшується і систематизується при використанні каталогу перехідних матриць.
Над опорою один із параметрів стану – перерізаючи сила – змінюється стрибком на величину реакції опори (мають місце пружна і дисипативна складові реакції).
Для розрахунку параметрів траєкторій при анізотропних властивостях радіальних опор і (або) несиметричному навантаженні зовнішніми силами необхідно організувати зовнішній цикл розрахунків по часу
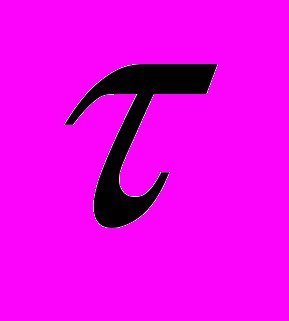
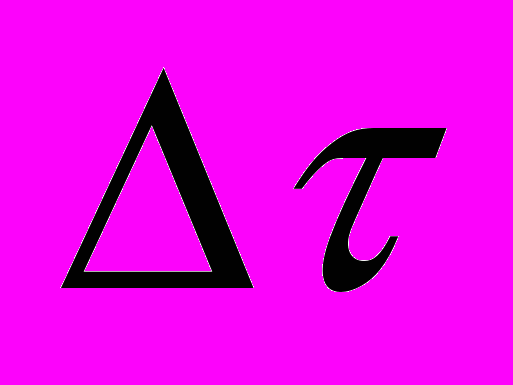
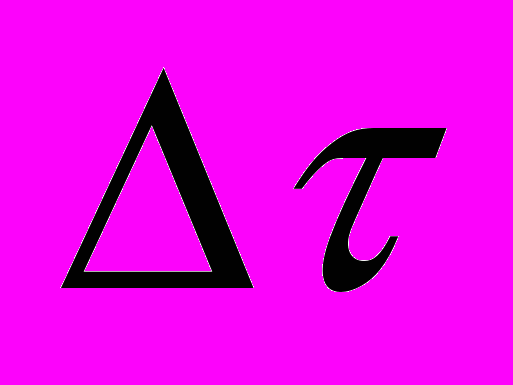
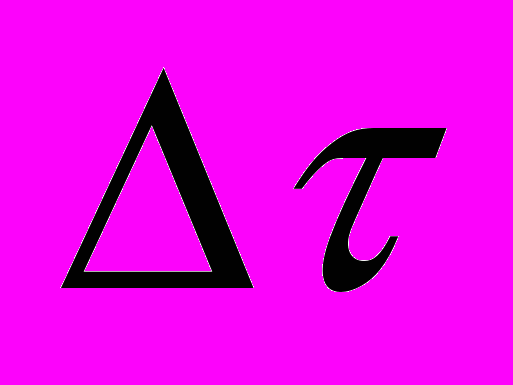
Описана математична модель руху шпинделя в гідростатичних опорах дозволяє прогнозувати положення осі шпинделя при зміні аргументів, які входять в моделі, не тільки для гідростатичних опор, але також для гідродинамічних і газо статичних.
^ ВПЛИВ ТЕХНОЛОГІЧНИХ ПАРАМЕТРІВ НА РІЗАЛЬНІ ВЛАСТИВОСТІ КЕРМЕТІВ НА ОСНОВІ КАРБІДУ ТИТАНУ
Т.П. Гребенок, студ., Л. Г. Бодрова, к.т.н., доц.
Тернопільський державний технічний університет імені Івана Пулюя, Тернопіль
Сплави на основі карбіду титану (кермети) із добавками карбіду ванадію, NiCr - металічною зв’язкою відзначаються високим рівнем фізико-механічних властивостей і можуть бути застосовані як матеріал різального інструменту.
В роботі досліджено різальні властивості кермету TiC–5VC–18NiCr, одержаного методом порошкової металургії за різними технологіями. Перший – за стандартною технологією, що включає гомогенізацію компонентів TiC, VC, Ni, Cr, холодне пресування та спікання, а другий – попередню операцію одержання твердого розчину TiC–VC.
Дослідження різальних властивостей кермету проводились при обробці сталей: 35, 45, 40Х, 40ХН, 60С2, У8А. Із сплаву виготовлялися багатогранні різальні пластини з отворами та зі стружечними канавками.
Дослідження проводились при точінні заготовок на токарно-гвинторізному верстаті мод. 16К20. Зношування пластин проходило переважно по задній поверхні, що і було прийнято за критерій оцінки різальних властивостей. Параметри режиму обробки за умови найбільшої стійкості інструменту отримали в результаті розрахунку динамічної стійкості процесу точіння.
Аналіз мікроструктур сплавів показав, що метод одержання сплавів помітно впливає на розмір карбідної фази. Сплави, одержані за другою технологією, відзначаються більшою дисперсністю структури і, відповідно, більш високими механічними характеристи-ками. Результати дослідження різальних властивостей сплавів, отриманих за різними технологіями, приведені на рис.1.
![]() |
Рис. 1 – Залежність зношення різців із кермету від тривалості роботи та технології виготовлення |
^ ИССЛЕДОВАНИЕ ИЗМЕНЕНИЯ ГЕОМЕТРИЧЕСКИХ
ПАРАМЕТРОВ УНИВЕРСАЛЬНО-СБОРНЫХ РЕЗЦОВ
С ПОВОРОТНОЙ РЕЖУЩЕЙ ЧАСТЬЮ
Ю.А. Гринёв, П.Г. Матюха, д.т.н., проф.,
Донецкий национальный технический университет, Донецк
Универсально-сборные резцы с поворотной режущей частью, оснащенной многогранной неперетачиваемой пластиной (МНП), обладают широкой универсальностью за счет поворота пластины на опорной поверхности. Они позволяют вести обтачивание наружных поверхностей с различными углами в плане, осуществлять подрезку торцев. Поворот режущей пластины осуществляется вокруг оси, перпендикулярной опорной поверхности, положение которой рассчитано для определенных базовых параметров режущей части. Естественно, при повороте пластины будет происходить изменение не только углов в плане, но и углов в главной и вспомогательной секущих плоскостях.
Полученные нами формулы позволяют рассчитывать углы режущей части после осуществления поворота четырехгранной МНП на угол (верхний знак при повороте против часовой стрелки, нижний знак - по часовой стрелке):
- угол наклона вспомогательной режущей кромки 1:

- вспомогательный задний угол 1:

- вспомогательный передний угол 1:

- угол наклона главной режущей кромки :

- главный задний угол :

- главный передний угол :

где 0, N – угол наклона главной режущей кромки и статический нормальный угол, которые обеспечивают установкой пластины в базовом положение;
- вспомогательный угол.
Вспомогательный угол для четырехгранной МНП определяется с помощью следующих зависимостей:
- соответственно, для главной и вспомогательной режущих кромок


Эти формулы позволяют проанализировать закономерности изменения углов. На основании анализа можно предложить следующие рекомендации при проектировании УСР с поворотной режущей частью:
- в процессе эксплуатации поворот должен осуществляться в разных направлениях, а базовое положение пластины, по которому рассчитывается положение опорной поверхности должно находиться посередине диапазона регулирования ;
- для резца оснащенного четырехгранной МНП с базовой геометрией (=45, N=10, =10, 1=45) диапазон углов регулирования по условию когда главный и вспомогательный задние углы больше нуля (например, равен пяти градусам) составляет для главного угла =25, передних углов ,1=-13…-5, углов наклона режущей кромки ,1=5…13.
Оценка состояния режущего инструмента
по выходным данным мониторинговой системы
О. Г. Деревянченко, д.т.н. проф.,
Одеський національний технічний університет, м. Одеса
А. І. Грабченко, д.т.н. проф., Д.Б. Романенко, асп.
Національний технічний університет України «ХПІ», м. Харьков
Современное машиностроительное производство все более широко связано с применением наукоемких технологий, характеризуемых прецизионностью рабочих процессов, которые должны обеспечивать основные показатели процесса: высокая надежность, высокая производительность, высокая точность и минимальная шероховатость.
К качеству режущих инструментов, эксплуатируемых в таких условиях, предъявляются повышенные требования – высокое качество режущей кромки и минимальный радиус округления.
Эффективность работы режущего инструмента при прецизионной обработке может рассматриваться как комплексный показатель состояния режущего инструмента, включающий такие свойства, как надежность, способность формировать обработанную поверхность в заданных пределах точности, шероховатости и других параметров качества поверхностного слоя.
Особенностью прецизионного процесса резания являются малые сечения среза, соизмеримость толщин среза с величиной радиуса округления режущей кромки, неравномерность нагрузки различных участков режущей части вдоль кромки. Эти и другие особенности обусловливают неравномерность износа поверхностей лезвия инструмента, появление таких дефектных элементов структуры режущего инструмента, как следы концентрированного износа, риски износа и др. Каждый из этих элементов режущей части может являться причиной отказа режущего инструмента
Разработка мониторинговой системы обусловлена необходимостью использования новых, современных методов контроля и исследования процесса резания, оперативного сбора информации, обработки экспериментальных данных с целью охвата возможно большего числа неконтролируемых параметров процесса прецизионного резания, предупреждения отказов режущего инструмента и прогнозирования его остаточного ресурса.
Мониторинговая система создавалась на основе компьютерного оборудования и программ, написанных на языке высокого уровня LabVIEW.
LabVIEW программный пакет для систем измерения, контроля, диагностики и управления, обеспечивающий сбор и обработку сигналов в реальном времени.
Эксперименты проводились при торцовом точении отрезным резцом из гексанита-Р закаленной стали ШХ 15 (HRCЭ 64), при этом режимы резания изменялись в следующих пределах: подача от 10 мкм/об до 30 мкм/об, глубина от 10 мкм до 30 мкм, скорость резания 80 – 100 м/мин. Компьютер фиксировал составляющие силы резания и виброакустическую информацию о процессе обработки.
Полученные результаты возможно использовать для адаптивного управления процессом прецизионной обработки труднообрабатываемых материалов.
Анализ существующих конструкций
центрирующих станочных приспособлений
А. Д. Дедов, к.т.н., доц., С. Ю. Стародубов, асист., М. В. Ивашина, асп.
Донбасский горно-металургический институт, Алчевск
Известно, что по характеру проявления все базы разделяются на явные и скрытые. Исследование комплектов баз показывает, что среди полных комплектов баз (6 связей) возможен 21 комплект, содержащий одну, две или три скрытых базы. Эти комплекты имеют различную применяемость на практике.
Наиболее распространенными схемами являются: У(я)Н(с)О(я); 2Н(с)О(я)О(я): У(с)2О(с)О(я).
Анализ теоретической и нормативной литературы по технологии машиностроения, производственного опыта позволили выявить следующие подходы к базированию деталей при наличии в комплекте скрытых баз:
- Смена баз, как правило, неорганизованная. Скрытая база заменяется геометрически связанной СМНТП ней явной базой.
- Материализация скрытых баз (установка СМНТП выверкой).
- Применение базирующе-зажимных механизмов.
Для оценки этих способов предложены три критерия: точность, трудоёмкость реализации, себестоимость изготовления оснастки. Определена область применения каждого способа.
Детально анализировались базирующе-зажимные механизмы. Установлено, что их особенностью является наличие в конструкции кроме геометрических также кинематических и динамических связей. Были рассмотрены более 300 конструкций таких устройств, авторские свидетельства и патенты на которые были выданы в период СМНТП 1975 года, а также типовые схемы центрирующих устройств. Отметим, что используемые механизмы отличаются, главным образом, видом силового привода. Для базирования используется небольшой выбор установочных элементов, реализующих связи. Разработана их систематизация.
Целью проведённого анализа являлось выявление степени совершенства предложенных конструкций базирующе-зажимных приспособлений СМНТП точки зрения статической определённости схемы установки и наличия эффекта самоустановки, разработка рекомендаций по конструированию таких устройств.
Статическая неопределённость в механизме, как известно, приводит к самонагружению дополнительными реакциями связи, что может послужить причиной разрушения механизма, а в случае станочного приспособления обязательно приведёт к снижению точности обработки (по данным некоторых авторов – от 2 до 5 раз). Задача анализа осложняется тем, что в настоящее время отсутствуют критерии оценки наличия эффекта самоустановки.
Предлагается формула для анализа структуры станочного приспособления, базирующего заготовку по явным и скрытым базам. Разработан алгоритм анализа. Сформулированы рекомендации по проектированию станочных приспособлений.
^ РАЗРАБОТКА СТРУКТУРЫ ОПЕРАЦИЙ МОДУЛЬНЫХ ТЕХНОЛОГИЧЕСКИХ ПРОЦЕССОВ
Думанчук М.Ю., асист.
Сумський державний університет, Суми
В соответствии с последовательностью проектирования модульных технологических процессов до начала разработки структуры отдельных операций должны быть выполнены следующие работы:
- разбиение детали на модули поверхностей в соответствии с принятой классификацией;
- на основе анализа на технологичность сформированы интегральные модули поверхностей;
- из существующей базы данных выбраны необходимые типовые технологические модули;
- в соответствии с реальной конфигурацией модулей поверхностей в типовых технологических модулях отобраны необходимые технологические переходы и из них сформированы рабочие технологические модули;
- сформированы интегральные технологические модули путем объединения одноименных этапов рабочих технологических модулей (перечень которых соответствует модулям поверхностей, входящих в интегральный модуль поверхностей).
ГОСТ 3.1109-82 определена следующая структура операций: операция – установ – позиция – технологический переход.
Принципами модульной технологии устанавливается, что в интегральный модуль поверхностей включаются те модули поверхностей, обработка которых может быть выполнена при неизменном положении заготовки на станке.
При формировании технологических операций модульного техпроцесса необходимо выполнить следующее:
- выявить среди существующих одноименных этапов интегральных технологических модулей те, которые могут быть выполнены при неизменном положении заготовки (сформировать позиции);
- внутри сформированных позиций упорядочить технологические переходы с целью минимизации времени на холостые перемещения органов технологического оборудования;
- выявить среди сформированных позиций те, которые могут быть реализованы с одной установки заготовки. Технологические установы формируются объединением таких позиций;
- Проверка сформированных установов с точки зрения возможности их объединения в операцию.
При выполнении этих работ необходимо учитывать общность используемых схем базирования, технологического оборудования, средств технического оснащен возможность, наличие необходимого количества инструментов в магазине.
При упорядочивании технологических переходов необходимо обеспечить неизменность их последовательности для каждого отдельно взятого технологического модуля.
Предлагаемая методика позволяет упорядочить процесс формирования структуры технологических операций, упростить автоматизацию данного вида работ, что в целом положительно скажется на качестве и продолжительности их выполнения, и, как следствие, на себестоимости детали в целом.
^ ТЕХНОЛОГІЯ СИНТЕЗУ ТЕРМІТНИХ ВИСОКОМІЦНИХ ЧАВУНІВ
Ю. Ю. Жигуц, к.т.н., доц., Ю. Ю. Скиба, асп.
Ужгородський національний університет, Ужгород
В 30-х роках вперше було запропоновано метод отримання рідкої сталі в результаті горіння термітної суміші. Сучасні дослідження в області металотермії значно розширили діапазон синтезованих сплавів.
Мета даної роботи полягала у заміні порошку алюмінію в стандартному терміті порошком магнію для модифікування утвореного рідкого чавуну надлишковим магнієм та глобуляризації графіту.
Для цього до стандартного терміту, що вміщує 20–25% порошку алюмінію і 75–80% оксидів заліза (за масою) додають залізомагнієвий терміт, який вміщує надлишок магнію: 30–35% порошку магнію на 70–65% оксидів заліза.
Маса шихти у мікроплавках знаходилася у межах від 150 до 500 г, а у наступному доведена до 10 кг. Підпал шихти виконувався титановим запалом.
В результаті проведеної роботи розроблено склад екзотермічної суміші (у % за масою): дисперсний вуглець (у вигляді частинок або волокон) 3–8; феросиліцій та силікокальцій (разом) до 10; феромарганець 0,2–1,0; залізо-алюмінієвий і залізомагнієвий терміт – решта.
Ефективність модифікування термітного чавуну магнієм визначалась металографічним методом з використанням шкали ССГ (ступені сфероідизації графіту).
Значну кількість виливків, що виготовляються з магнієвого чавуну можна оперативно перевести на техно-логію з використанням термітних ливарних додатків. Застосувавши термітні ливарні додатки, втрати металу можна знизити до 10% і менше.
Цілі виливки з термітного магнієвого чавуну до-цільно виготовляти при терміновому отриманні литих заготовок запасних частин та інших дефіцитних деталей при відсутності плавильного обладнання та зовнішніх джерел енергії
Проведена робота дозволила встановити:
1. Екзотермічна суміш для термітних ливарних додатків, повинна вміщувати залізоалюмінієвий терміт, з метою отримання у додатковій частині форми рідкого магнієвого чавуна, аналогічного за складом магнієвому чавуну залитому у ливарну форму, який підпалює екзотермічну суміш у порожнині додатку, в той же час суміш додатково вміщує залізомагнієвий терміт з над-лишком порошку магнію 9,2–31,6% (за масою):
2. Екзотермічна суміш для отримання високоміц-них чавунів крім феросиліцію може вміщувати магній у вигляді лігатури ЖКМ або ЖКМК.
3. Екзотермічна суміш для виготовлення з тер-мітного металу цілих виливків або для термітного зварю-вання виливків цим металом може зовсім не вміщувати феромарганець.
4. Ці ж екзотермічні суміші можуть бути вико-ристані і для термітного зварювання чавуну.
Проведена робота дозволяє зробити також загаль-ний висновок, що за механічними властивостями синтезо-вані високоміцні чавуни не поступаються “ординарним” – отриманим традиційними технологіями, а самі методи придатні для синтезу, в принципі, будь-якого чорного і кольорового сплаву.
Об одной конструкции крепления
сменных многогранных неперетачиваемых пластин
в режущей части вихревой головки
В. О. Залога, д.т.н., проф.; Д. Г. Голдун, студ.
Сумський державний університет, м. Суми
Процесс вихревого нарезания резьбы по своей кинематике относится к прерывистым нестационарным процессам резания. В работе участвуют одновременно три режущие кромки последовательно каждого из 4-20 лезвий режущей части вихревой головки (ВГ). Такой режим работы обуславливает кратковременность цикла «резание» и изменение толщины среза и большими градиентами ударного импульса. В связи с этим крепление лезвий к корпусу режущей части ВГ оказывает значительное влияние на качество получаемой резьбы и работоспособность ВГ в целом. На наш взгляд применение в ВГ напайных уже пластин является нерациональным в современных условиях. Согласно нашим расчетам большую стойкость, точность и производительность можно достичь благодаря использованию сменных многогранных неперетачиваемых пластин (СМНТП). Однако этот подход требует обеспечения (1) минимальных габаритов узла крепления СМНТП в режущей части ВГ и (2) простоты его эксплуатации, (3) высокой точности базирования СМНТП и (4) надежности их закрепления.
В настоящее время инструментальная промышленность выпускает СМНТП для нарезания трапецеидальных резьб с большим шагом. Это, например, радиальные пластины фирмы Widia Valentine 4Ex.xTR. Их широко применяют для нарезания резьбы резцом. Для этой цели разработаны державки и узлы крепления пластин в них по силовой схеме “Р”. Однако применение известных конструкций узлов крепления в режущей части ВГ невозможно из-за невозможности обеспечить (1) и (2) требования.
Проведенное нами патентное исследование позволило разработать конструкцию крепления СМНТП, удовлетворяющую указанным требованиям. На торцевой поверхности корпуса режущей части ВГ выполнены кольцевой паз фасонной формы с углом 60 и пазы с точными боковыми поверхностями в радиальном направлении. В каждом из радиальных пазов располагаются вставки, на поверхности которой располагается СМНТП с отверстием и штифт. Закрепление производится винтом.
Данная конструкция узла позволяет обеспечить:
- точность расположения СМНТП за счёт базирования всех пластин по поверхности кольцевой фасонного паза, выполняемого с одного установа;
- надёжность закрепления СМНТП за счёт положительного угла между силой резания и силой закрепления;
- минимальные габариты;
- простоту эксплуатации за счет применения одного крепежного винта, расположенного на торце режущей части ВГ.
Узел прост в изготовлении, поскольку содержит всего четыре поверхности, к которым предъявляются повышенные требования по точности изготовления: кольцевой фасонный паз, основание радиальных пазов и боковые поверхности вставки.
^ НОВІ МОДЕЛІ ПІДШИПНИКІВ ШПИНДЕЛЬНИХ ВУЗЛІВ ДЛЯ НАДВИСОКОШВИДКІСНОЇ ОБРОБКИ
П. О. Захаров, к.т.н., доц., В. М. Місюк , асп.
Луцький державний технічний університет, м. Луцьк
Підшипники кочення, гідравлічні (гідродинамічні і гідростатичні), газові (аеродинамічні і аеростатичні) та магнітні, які використовуються в якості опор високошвидкісних шпинделів, не забезпечують одночасно повний комплекс вимог, які ставляться до них: висока швидкохідність, малі втрати на тертя, високі статична та динамічна жорсткість і довговічність.
Відомі спроби, які направлені на суміщення в одній конструкції переваг гідравлічних та газових підшипників.
Запропонованований підшипник з гідрогазовим мастилом є одним з можливих конструктивних рішень гідрогазової опори. Опора складається з втулки, яка обертається з кутовою швидкістю ω, і нерухомого шипа. Між поверхнями втулки і шипа знаходиться шар рідини, який обертається з втулкою, та шар газу.
За рахунок відцентрових сил, що діють на частинки рідини в шарі, виникає гідростатичний тиск з додатнім градієнтом вглиб шару в напрямку поверхні втулки. При достатньо великій кутовій швидкості ω шар рідини можна рахувати квазітвердим з ідеальною кільцевою поверхнею. При накладанні сили Q втулка зміщується на шип на величину ексцентриситету е