Машинобудування України очима молодих: прогресивні ідеї – наука – виробництво”
Вид материала | Документы |
- Аналітична довідка за 2011 рік щодо економічного розвитку вінницької області промислове, 109.63kb.
- Агропромисловий комплекс (виробництво та переробка сільськогосподарської продукції);, 288.16kb.
- Відбулась фінальна частина акції “Охорона праці очима дітей”, 18.49kb.
- Національна академія наук України оголошує конкурс на здобуття премій молодих учених, 39.89kb.
- Національна академія наук України Міністерство освіти та науки України бюлетень, 2255.17kb.
- Міністерство освіти І науки україни східноукраїнський національний університет імені, 206.5kb.
- Тема Менеджмент як наука, 242.26kb.
- Інформація щодо реалізації реформ Президента України в агропромисловому комплексі району, 40.61kb.
- Балака Максим Миколайович, асистент кнуба міщук Дмитро Олександрович, асистент кнуба, 73.22kb.
- Політична історія України, 110.04kb.
1 2
, а в конфузорній частині газового шару виникає аеродинамічний тиск. Оскільки тиск на поверхні рідинного шару рівний нулю, то за рахунок аеродинамічного тиску він деформується на деяку глибину. Інтеграл тиску по дузі деформованого шару забезпечує реакцію газорідинного підшипника на навантаження, тобто його навантажувальну здатність.Недоліком першої запропонованої конструкції є те, що вона передбачає нетрадиційну компоновку роторної системи, коли обертається не ротор, а втулка.
Особливістю другої конструкції, яка реалізує запропонований спосіб мащення являється використання в якості робочої рідини маcтила, яке володіє феромагнітними властивостями (ФМР - феромагнітна рідина). Гільза встановлена з зазором на шип, при цьому гільза розміщена в конструкції нерухомо, шип – з можливістю обертання. Зазор між шипом та гільзою заповнюють розрахованою кількістю магнітної рідини. Під дією обертового магнітного поля шар рідини рухається в коловому напрямку по поверхні гільзи. Під дією відцентрових сил в шарі рідини, яка обертається, виникає тиск: мінімальний – на вільній границі шару рідини; максимальний – на стінці гільзи; таким чином створюється квазітверда, ідеально кільцева поверхня. Відмінність двох конструкцій полягає в тому, що за рахунок ефекту налипання рідини на нерухому поверхню втулки в останньому випадку необхідно очікувати збільшення втрат на тертя в пограничному шарі рідкої фази мастила. Однак слід передбачити стабілізуючу дію радіального градієнта тиску і орієнтуючої дії магнітного поля на розвиток турбулентних процесів в пограничному шарі магнітної рідини. Перевагою другої схеми є можливість управління режимом тертя в рідкій та газовій фазах мастила в залежності від умов роботи підшипника. Приведені конструкції підшипників далеко не обмежують можливі конструктивні реалізації запропонованого способу мащення.
^ ПРИМЕНЕНИЕ НЕЙРОСЕТЕЙ ПРИ ОЦЕНКЕ ИНФОРМАТИВНОСТИ ЧАСТОТ ДИАГНОСТИЧЕСКОГО СИГНАЛА
С.В. Ковалевский, д.т.н., проф., В.В. Медведев, асп.
Донбасская государственная машиностроительнаям академия, Краматорск
Для контроля состояния технологической системы в “безлюдном” производстве, как правило, пользуются косвенными методами, которые предполагают измерение параметров, сопутствующих процессу обработки. Наиболее информативными являются колебательные процессы: акустическая эмиссия, вибрации и.т.п. После их обработки средствами контроля судят о состоянии технической системы. Основной задачей является выделение информационных частот из диагностических сигналов. В ряде существующих алгоритмов при этом начинают с выделения наиболее адекватных технологическим параметрам частотных диапазонов сигнала.
Предложенная методика позволяет снизить время определения информативных частот и их зависимость от конкретных технологических параметров. Как известно диапазон колебаний, сопутствующих процессу обработки лежит в пределах от 1 Гц до нескольких десятков мегагерц. В него входят вибрации, акустическая эмиссия и электромагнитное излучение. Однако, существующие методы контроля состояния технологической системы по колебательным процессам в зоне резания, не обеспечивают необходимой точности. Кроме того, требуется их предварительная настройка на каждый станок, которая включает в себя проведение большого числа предварительных экспериментов для тарировки датчиков. С появлением компьютерных эмуляторов искусственных нейронных сетей стало возможно снизить количество предварительных экспериментов.
Нами разработанная система включающая в себя датчики, аналогово-цифровые и спектральные преобразователи, эмулятор нейронной сети с периферийными блоками поддержки обучения. Методика заключается в свойстве нейронных сетей распознавать образы на основе поступающих сигналов. После обучения структура сети настраивается таким образом, что по спектру сигналов со станка она распознает технологические параметры.
Эксперименты проводились на токарном станке 1А64, обрабатывались заготовки из Стали 45, использовались резцы с трехгранными и четырёхгранными режущими пластинами (=90° и =45°). Целью экспериментов являлась оценка адекватности информативных частот технологическим параметрам.
По полученной, в процессе обучения, структуре нейронной сети выводилась эмпирическая зависимость между диагностическим сигналом и технологическими параметрами. Это позволило выявить наиболее информативные частоты, инструмента с высокой точностью определять в режиме реального времени режимы резания и состояние инструмента.
Вывод. С помощью полученной методики стало возможно получать зависимость весомости частот сигналов датчиков от различных технологических параметров. С помощью выработанной методики изучения спектра определили, в частности, наиболее значимые диапазоны акустической эмиссии от частоты вращения шпинделя и глубины резания. С помощью данной методики можно получать и другие зависимости весомостей частот для построения интеллектуальных систем диагностики.
^ СИСТЕМНЫЙ ПОДХОД К ОЦЕНКЕ ВЛИЯНИЯ
ТЕХНОЛОГИЧЕСКИХ ФАКТОРОВ НА КАЧЕСТВО ДЕТАЛЕЙ МАШИН
Л. П. Колот, к. т. н., доц., Ю.А. Бойко, асп.
Донбасская государственная машиностроительная академия, Краматорск
Технологические факторы и параметры точности деталей представляют собой множество взаимосвязанных элементов, выступающих как единое целое. Такое множество является системой. Система рассматривается как объективно существующий комплекс связей, характеризующий размеры и форму детали на каждой операции.
Системный подход к исследованию точности детали при ее изготовлении получает свое проявление в постановке и определении комплекса методов: оценки значимости влияния отдельных элементов конструкции на точность деталей, определение влияния отдельных параметров на точность деталей, установление связей между погрешностями формы деталей и методами их изготовления.
Систему связей производственных факторов и признаков точности изготовления деталей, на примере нежестких корпусных деталей можно представить следующим образом: главный объект системы Т - точность размеров и формы нежестких корпусных деталей находится в определенной связи с М - материалом детали, ее геометрической формой - Г и стабилизирующими методами термообработки - СТО.
Целостный характер системы проявляется в том, что между различными ее объектами в данном состоянии существуют связи. Связь между любыми двумя объектами образует элемент системы- подсистему. Таким образом, конструируемая система представляет собой совокупность связанных элементов-подсистем.
Увеличение второстепенных элементов усложняет математическое моделирование системы в целом и не приводит к повышению уровня и достоверности из-за случайного характера связей.
Отбор объектов для включения в систему производится на основе оценки значимости их свойств в том аспекте, в котором объекты образуют систему. Параметрами системы является вход, процесс, выход. Состояние системы описывается множеством величин по каждому системному параметру. Под входом понимается исходное состояние главного системного объекта Т, то есть исходные показатели точности размеров и формы деталей перед механообработкой (первый вход) и перед термообработкой (второй вход). Исходное состояние объекта Т изменяется в процессе механообработки и в конце этого процесса Т переходит в конечное состояние или в первый выход. Первый выход является вторым входом объекта Т, который изменяется в процессе термообработки и в конце данного процесса дает второй выход.
Таким образом, рассматриваемая система выделяется из общей технологической системы тем, что в ней указаны процессы, дающие выход. Система связей имеет два выхода, т.е. два конечных состояния системы, фиксируемых как результаты процессов механообработки и термообработки в виде деформации детали. В рассматриваемых подсистемах связи представляются как элементы, характеризующие отношения системных объектов Г, СТО и М результатами изменения объекта Т в процессе обработки.
Таким образом, для изучения структуры системы использованы физические модели и статистические методы исследования. Представлены примеры практической реализации способов повышения точности обработки нежестких деталей.
Прогнозирование силы резания
при резании с переменной толщиной среза
Д. В. Криворучко, асп.
Сумський державний університет, м. Суми
Процессы резания с переменной толщиной среза широко распространены в современном машиностроении. Это фрезерование, шлифование, вихревое нарезание резьбы, тангенциальное точения и др. Создание нового оборудования и инструмента, а также эффективная эксплуатация имеющегося в новых условиях требуют надежного прогнозирования силы резания, интенсивности износа лезвий, температуры резания и других показателей указанных процессов обработки. На наш взгляд создание прогнозирующей модели этих процессов является наиболее перспективным. Несмотря на большой объем исследований в этой области, выполненных как отечественными так и зарубежными авторами, в полном смысле прогнозирующих моделей процесса резания все еще не создано.
В докладе представлена прогнозирующая модель процесса прямоугольного резания пластических материалов округленным лезвием при непрерывно изменяющейся в больших пределах толщиной среза. Для прогнозирования контактных напряжений применен метод линий скольжения. Обрабатываемый материал считается неупрочняющимся и несжимающимся.
При построении поля линий скольжения учтены граничные условия в напряжениях на поверхности лезвия и на верхней границе пластической зоны, которая возникает перед режущей кромкой. Принято равномерное распределение касательных напряжений на участке пластического контакта. Их направление выбиралось противоположным направлению относительной скорости.
Границы застойной зоны, являющейся точкой разделения потоков материала, определись в зависимости от величины касательных напряжений на поверхности лезвия. Высота валика перед режущим лезвием определялась из условия равенства его объема объему материала, который уже взаимодействовал с режущей кромкой. Считалось, что стружка начинает образовываться в момент окончания увеличения объема валика.
Исходя из описанных положений была получена система уравнений. Для их решения был разработан алгоритм и программа в среде MATLAB. Следует отметить, что исходными данными являются механические свойства обрабатываемого материала, геометрия лезвия, режим резания.
Проведенная экспериментальная проверка показала удовлетворительное количественное совпадение результатов прогнозирования силы резания с данными экспериментов, проведенных как непосредственно автором, так и другими исследователями. Погрешность прогнозирования не превосходит 20 %.
Таким образом, удовлетворительная точность прогнозирования и малое время, необходимое для выполнения расчетов, позволяет применить модель для оптимизации процессов резания с переменой толщиной среза.
^ ДОСЛІДЖЕННЯ НАВАНТАЖУВАЛЬНОЇ ЗДАТНОСТІ
ПІНОЛЬНИХ МЕХАНІЗМІВ СИЛОВИХ ВУЗЛІВ АГРЕГАТНИХ ВЕРСТАТІВ
Крижанівський В.А., к. т. н., доц.; Гречка А. І., асп.
Кіровоградський державний технічний університет, Кіровоград
Відомо, що ефективність приводів подач головним чином визначається умовами функціонування їх вихідних органів. Пінолі представляють собою широко розповсюджений у верстатах, особливо агрегатних, клас виконавчих органів приводів подач. Однією з найважливіших характеристик пінольних механізмів є навантажувальна здатність. Для кількісної оцінки навантажувальної здатності застосовується ряд показників: коефіцієнт корисної дії, коефіцієнт тертя, коефіцієнт передачі сил. Найбільшу інформативність про співвідношення силових потоків на вході (сили технологічного навантаження) і виході (сили кінематичних ланцюгів подачі) пінольного механізму має коефіцієнт передачі сил.
Як відомо, навантажувальна здатність будь-якого механізму визначається схемою його навантаження. У результаті проведеного аналізу застосовуваних у верстатобудуванні конструкцій пінольних механізмів та прогнозування можливих варіантів для рішення задач оптимізації була запропонована узагальнена просторова схема навантаження пінольного механізму.
Перевагою даної схеми є урахування просторового розташування технологічної сили, сил подачі та реативних силових факторів. Крім того, представлена схема навантаження дає змогу розглядати приводи подач як традиційної, так і нової, перемінної структури. Розташування кожної навантажуючої сили характеризується двома лінійними і трьома кутовими координатами. Для кількісної характеристики співвідношення між силовими потоками приводів подач введено коефіцієнт переміни структури. Під дією зазначених сил у парі піноль-корпус виникають реакції, приведені до трьох силових факторів: двох реактивних сил та одного реактивного моменту пари. Плече моменту пари вважається відомим, кутові координати розташування реактивних сил – невідомі. При переміщенні пінолі у місцях прикладення реакцій на неї також діють сили тертя. Приймається, що сили тертя пропорційні реакціям.
Таким чином, схема навантаження представлена шістьмома невідомими силовими факторами. Для знаходження їх величин складена система з шести рівнянь. У результаті аналітичного рішення даної системи рівнянь були отримані формули для визначення коефіцієнта передачі сил, сили подачі і сил тертя.
Навантажувальна здатність пінольного механізму підвищується при зменшенні коефіцієнту передачі сил. Установлено, що мінімальне значення коефіцієнта передачі сил має місце при співвісному розташуванні навантажуючих сил. Збільшення ексцентриситетів точок прикладання навантажуючих сил, приводить до значного зростання коефіцієнта передачі сил. Розташування навантажуючих зусиль під кутом до осі пінолі значно ускладнює характер залежностей коефіцієнта передачі сил. При цьому співвісне розташування навантажуючих сил вже не являється раціональним, зате збільшується область раціональних значень деяких конструктивних параметрів, при яких значення коефіцієнта передачі сил мінімальне.
моделирование случайных размерных параметров инструмента, определяющих динамику процесса шлифования
Леснинов И.Ю., асп., Иванова П.С., Маклаков А.Н.
Севастопольский государственный технический университет, Севастополь
Качество обрабатываемых изделий в большой степени зависит от состояния инструмента, который оказывает существенное влияние на ход технологического процесса. В силу того, что отклонение формы шлифовального круга от заданной определяется большим количеством не контролируемых независимых случайных факторов; они относительно стабильны в процессе обработки каждой детали, а отклонение формы может характеризоваться квазистационарным гауссовским случайным процессом. Такой процесс характеризуется математическим ожиданием (параметрами формы круга) и отклонениями формы, характеризуемыми корреляционной функцией. Корреляционная функция строится непосредственно по профилограмме круга:

где Е – операция взятия математического ожидания;
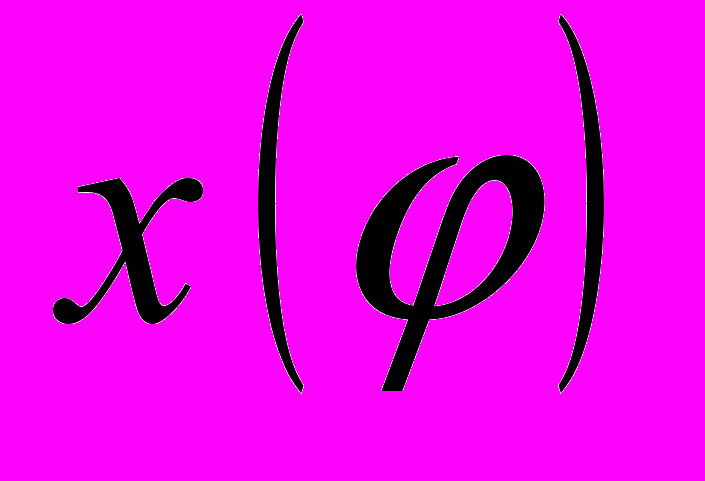
Для конечных реализаций всегда существуют спектральные плотности, определяемые преобразованиями Фурье по формулам Виннера – Хинчина:
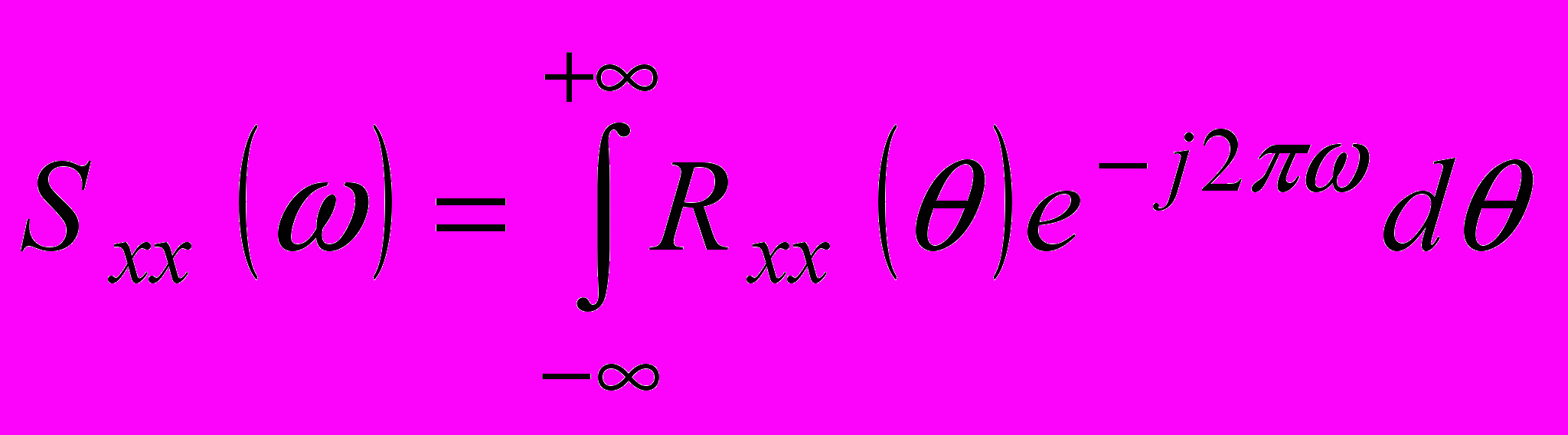
Корреляционная функция отклонения от формы с достаточной степенью точности аппроксимируется зависимостью:

где
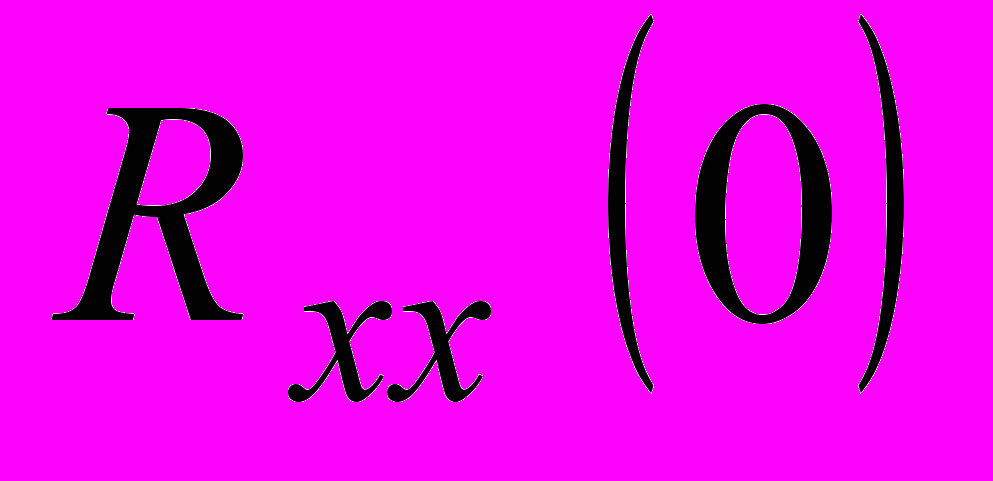
Соотношение (3) позволяет непосредственно оценить интервал корреляции, который может служить одним из критериев качества инструмента.
Подстановка зависимости (3) в (1) приводит к результату:

Соответствующий формирующий фильтр представляет собой минимально-фазовое звено второго порядка с передаточной функцией, имеющей изображение по Лапласу :
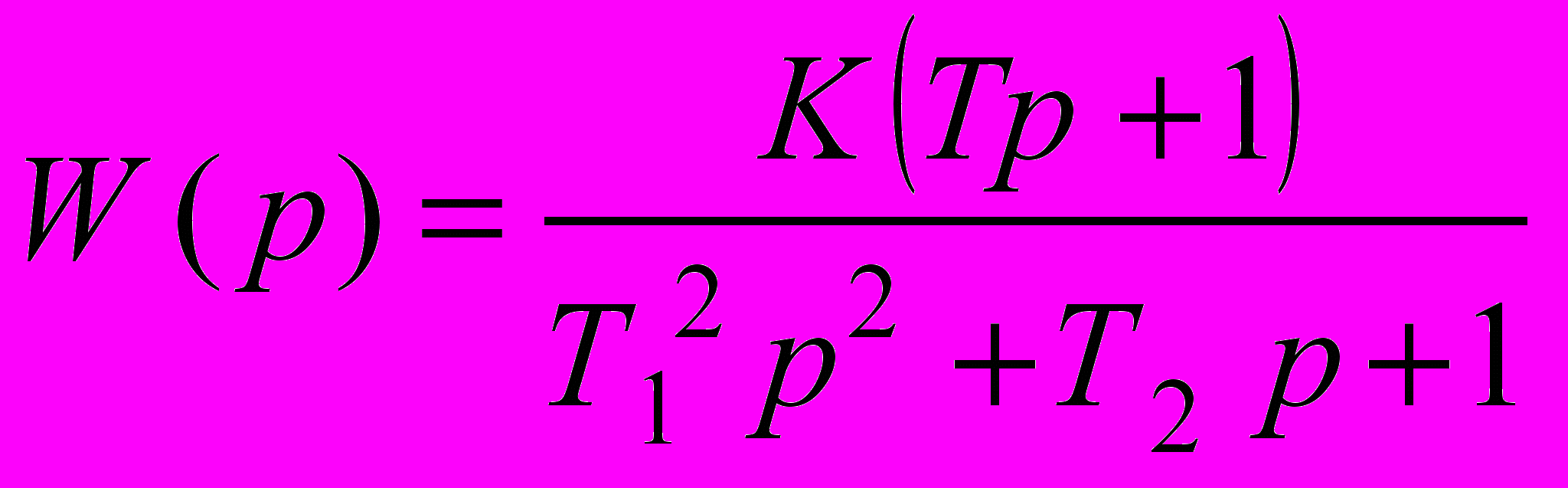
где K, T, T1, T2 –параметры передаточной функции, определяемые приравниванием коэффициентов при соответствующих степенях
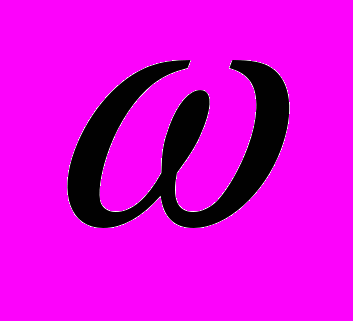
Построенный формирующий фильтр может быть использован: при анализе и синтезе систем управления для операций шлифования, при численном моделировании для получения окрашенных шумов, характеризующих погрешности формы шлифовального круга, при моделировании динамки процесса обработки и непосредственно для оценок необходимых характеристик элементов механических систем шлифовальных станков.
^ ПОСТРОЕНИЕ СТРАТЕГИИ ОЦЕНКИ ШЕРОХОВАТОСТИ
ПОЛИМЕРНЫХ ОПТИЧЕСКИХ ИЗДЕЛИЙ
М. В. Литвиненко, асп.
Національний технічний університет України «ХПІ», м. Харьков
Оптические полимеры хорошо зарекомендовали себя в физике высоких энергий, где в настоящее время большие усилия направлены на решение проблемы создания электромагнитных и адронных калориметров нового поколения. Составными частями калориметров являются полимерные пластины большого объема, длинной до пяти метров.
К основным эксплуатационным показателям оптических изделий относятся: высокий световой выход и длина затухания, хорошая однородная чувствительность и высокий уровень стабильности параметров в течении длительного срока эксплуатации.
Получение оптических поверхностей со 100% отражением, обеспечивается параметрами минимальной шероховатости (
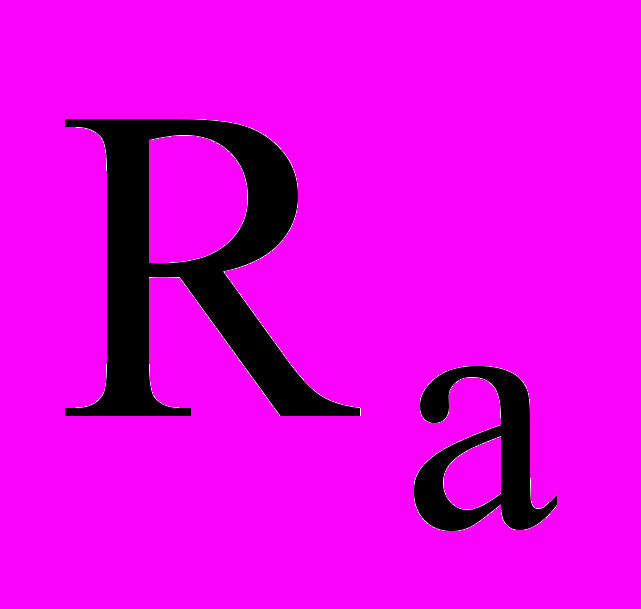
Одним из путей повышения качества поверхностного слоя оптических изделий является контроль и оценка параметров шероховатости обработанных поверхностей.
Анализ частотных характеристик неровностей, особенностей их формы и расположения, оказывающих на эксплуатационные (оптические) свойства не меньшее влияние, чем высота неровностей, показал, что для более полного контроля и описания качества поверхности требуется разработка новых методов оценки шероховатости.
Создание моделей шероховатости поверхности является оправданным при условии учета индивидуальных особенностей метода и условий обработки. При моделировании микропрофиля объектом для исследования являются профилограммы поверхностей, которые хорошо интерпретируются как реализации случайного поля, а их сечения как реализации случайного процесса, являющегося марковским процессом с нормальным распределением амплитуд. В такой модели параметры шероховатости поверхности будут функционалами, заданными на множестве значений случайной функции.
В качестве подобных функционалов рассматривается сумма квадратов N - точечных отсчетов значений случайной функции, связанной со случайной поверхностью.
Для оценки шероховатости полимерных оптических изделий разработан алгоритм и программное обеспечение, позволяющее произвести расчет статистических характеристик квадратичных функционалов при различных значениях параметров. Использованы современные методы и средства программного обеспечения и представления данных.
По результатам оценки принимается решение о качестве обработки и назначаются (или корректируются) параметры прецизионного технологического процесса резания оптических изделий.
^ АВТОМАТИЗАЦІЯ ПОБУДОВИ СХЕМИ ПЕРЕКРИТТЯ ВИБОЮ ШАРОШКАМИ, ОЗБРОЄНИМИ КЛИНОВИДНИМИ ЗУБКАМИ
Марцінковська І. П., асп.
Івано-Франківський національний технічний університет нафти і газу,
Івано-Франківськ
Схема перекриття вибою традиційно вважається обов’язковою в пакеті конструкторських документів тришарошкового долота.
Оригінальність пропозиції автора в тому, що відомий конструкторам трудоємкий ручний метод викреслювання традиційної схеми перекриття вибою шарошками долота може бути покладений в основу автоматизованої процедури відображення складної схеми як на екрані дисплея, так і викреслювання на графопобудовувачі без внесення додаткових помилок.
Викладена інформація не відступає від існуючої в галузі термінології, базується на сучасних методах конструювання і правильно відображає основні тенденції, що складаються у нафтовому машинобудуванні.
Матеріал, викладений в статті, становить практичний інтерес в галузі конструювання породоруйнуючого інструменту.
Проектування бурового долота процес складний і багато ітераційний, тому застосування сучасних комп’ютерних технологій дозволить проектувальнику багаторазово покращувати конструкцію без великих зусиль і затрат часу.
Основну роботу (розрахунки, побудову креслень) автоматично виконує комп’ютер, який працює по запропонованій програмі. Людина синтезує конструктивні схеми, керує ходом обчислювального процесу, оцінює результати.
Створена схема перекриття дозволяє якісно і кількісно оцінити картину перекриття вибою запроектованим озброєнням шарошок, побачити не перекриті ділянки, профілі гребінок та розрахувати коефіцієнт перекриття забою за вибраними конструктивними параметрами.
Побудова схеми перекриття вибою полягає в суміщенні (почерговому накладанні) робочих всіх трьох шарошок на одному зображенні.
Профілі не перекритих гребінок забою дають підстави щодо вдалого чи невдалого розташування вінців на шарошках, визначення зон небезпечних перерізів шарошок, призначених для руйнування абразивних порід.
Рішення щодо переміщення того чи іншого вінця шарошки приймається за візуальною оцінкою. Це потребує відповідного переміщення спряжених з ним сусідніх шарошок на схемі розгортки шарошок і повторення всіх трудоємких процедур розрахунку і викреслювання.
Коефіцієнт перекриття вибою визначається за такою формулою:
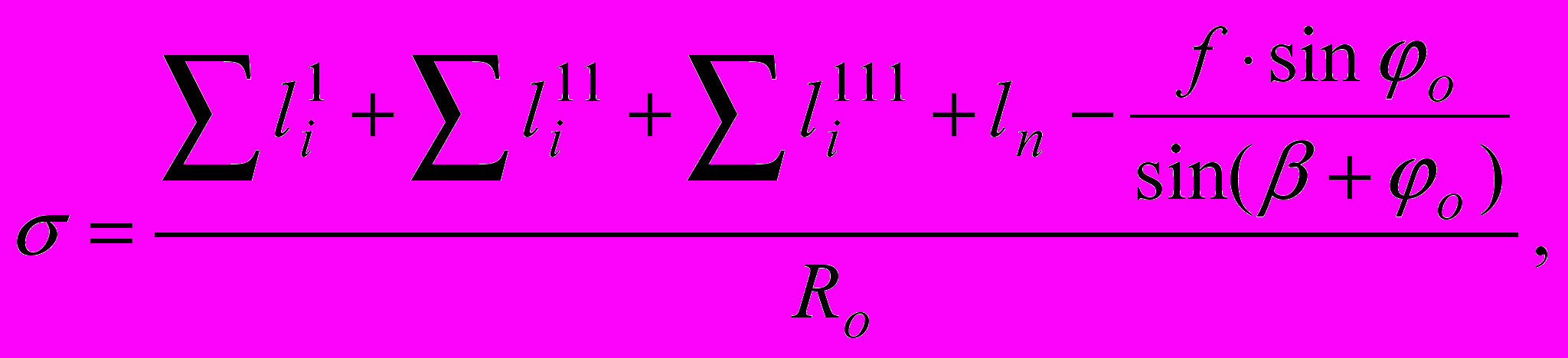
де li1 – довжина зубів на першій шарошці без периферійного вінця; li11 – те ж на другій шарошці; li111 – те ж на третій шарошці; ln – довжина найдовшого зуба периферійного вінця; f – виліт шарошки за вісьб долота; γо – кут нахилу осі шарошки до осі долота;
β – половина кута основного конуса шарошки.
^ ДИНАМИЧЕСКИЙ РАСЧЕТ СБОРНОГО ИНСТРУМЕНТА ДЛЯ ТЯЖЕЛЫХ СТАНКОВ В ПРОЦЕССЕ РЕЗАНИЯ
С.Л.Миранцов, асп.
Донбасская государственная машиностроительная академия, г. Краматорск
Колебания системы СПИЗ снижают производительность обработки, ухудшают качество обработанной поверхности, сокращают срок службы металлорежущего оборудования и инструмента. Несмотря на известную сложность явления, в настоящее время накоплен обширный материал в области изучения природы колебаний при резании. Однако недостаточно изучены вопросы колебаний инструмента для тяжелых станков.
В процессе работы на режущую часть инструмента и деталь, обрабатываемую на станке, действуют периодические во времени составляющие силы резания.
Радиальная Py и тангенциальная Pz составляющая силы резания, действующие на режущий инструмент и обрабатываемую деталь, определяются не линейными эмпирическими выражениями относительно толщины и ширины.
Выражения для составляющих силы резания показывают, что они зависят от смещения режущей кромки инструмента в тангенциальном и радиальном направлении.
Математическая модель процесса колебаний системы, включающей сборный инструмент для условий поперечного точения, будет представлять систему из восьми дифференциальных уравнений.
Для практического моделирования колебаний разработана прикладная программа для ПЭВМ «OSCLab 2.0».
^ ПРОБЛЕМА ОБОСНОВАНИЯ И ВЫБОРА ЦЕЛЕВОЙ ФУНКЦИИ
ПРИ СИНТЕЗЕ ТЕХНОЛОГИЧЕСКИХ ОПЕРАЦИЙ
Е. В. Мишура, асп.
Донбасская государственная машиностроительная академия, Краматорск
Переход к рыночной экономике требует от машиностроительного предприятия повышения эффективности производства, конкурентоспособности продукции, основанной на внедрении достижений научно–технического прогресса, эффективных форм хозяйствования и управления производством.
Важная роль в реализации этой задачи отводится синтезу технологических операций, который неразрывно связан с оптимизацией технологического процесса механообработки. При этом целью оптимизации должно быть не только снижение себестоимости и повышение производительности как станочных операций, так и всего процесса, но и, в конечном итоге, его экономичность и достижение максимальной прибыли.
На сегодняшний день оптимизация станочных операций основывается на математическом моделировании исследуемых процессов, причем осуществляется комплексная оптимизация основных параметров перехода на основе строгого математического анализа. Для этого предлагается использовать программы-эмуляторы сетей с одномерной структурой, которые способны обрабатывать не только большие потоки информации, но и информацию довольно противоречивую и не полную.
Выбор целевой функции имеет большое значение, так как необоснованное ее назначение может привести к ошибочным выводам и рекомендациям. Принципиально возможны следующие критерии выбора режимов резания при построении оптимальной операции: прибыль, наименьшая технологическая себестоимость, максимальная производительность, максимальная стойкость инструмента, а также такие критерии оптимальности, как показатель наименьших приведенных затрат.
В современных условиях производства особого внимания заслуживают три целевые функции: максимум прибыли, минимум технологической себестоимости и максимум производительности при выполнении операции. Эти целевые функции относятся к отдельной операции. Их решение определяет предельные возможности синтезированной операции, если отсутствуют ограничения организационного характера.
Основываясь на результатах проведенного сравнительного анализа целевых функций можно сделать следующие выводы:
Целевую функцию минимальная себестоимость выгоднее применять при обработке на универсальном и недорогом оборудовании.
Целевая функция - максимальная производительность в полной мере соответствует целям производства, то есть производительной обработке, но в условиях использования неавтоматизированного универсального оборудования дает повышенную стоимость обработки.
Целевая функция максимальной прибыли не принимает граничных значений, поскольку учитывая такие внешние факторы как цена, объём производства и другие, недоступные для остальных функций, учитывает и тип производства (единичное, серийное, массовое) поэтому создание моделей технологической операции на основе функции прибыли целесообразно для создания техпроцессов и для процессов принятия оптимального технологического решения в реальных производственных условиях.
Параметрический синтез СБОРОЧНЫХ УСТРОЙСТВ
^ ДЛЯ СБОРКИ УПЛОТНИТЕЛЬНЫХ СОЕДИНЕНИЙ
Ю. К. Новосёлов, д.т.н., проф., А. Ю. Тараховский
Севастопольский государственный технический университет, Севастополь
Анализ сборочных устройств для сборки уплотнительных соединений (эластичная кольцевая деталь- канавка отверстия) показывает, что сборочное устройство обладает всеми признаками технических динамических систем.
В связи с этим задача синтеза оптимальных структур сборочных устройств может рассматриваться как задача общей теории синтеза технических систем, но имеет ряд своих особенностей, связанных:
- с требованиями, предъявляемыми к сборочному устройству;
- с особенностью физического процесса сборки.
Синтез сборочного устройства может быть выполнен на основе использования методов структурной и параметрической оптимизации технических систем.
На первом этапе решения задачи синтеза системы сборочного устройства при формировании множества структур учитываем в качестве признаков и характеристик технологических элементов их различное влияние на выходные показатели, как технологической системы, так и процесса сборки. При этом целесообразно применить аппарат морфологического анализа. Однако, этот метод в чистом виде использовать нельзя, так как при выборе рационального варианта не учитываются реальные условия процесса сборки уплотнительных соединений. Поэтому морфологический анализ берём в качестве аппарата на первых двух этапах синтеза для формирования множества структур и оценки вариантов по укрупнённым показателям.
На основе структурной схемы технологической системы сборочного устройства возможно построение группы морфологических матриц, различных уровней иерархии.
После заполнения морфологической матрицы переходим к синтезу вариантов структуры сборочного механизма. Методика поиска оптимальной структуры при заданных требованиях состоит в следующем. Вначале из множества признаков /n = 1, 2, …, N/ технологического элемента "сборочное устройство" /Сб/ выделим наиболее приемлемые.
Пусть имеется М типов n-го узла, причём m - порядковый номер типа данного узла /m = 1, 2, …, M/. Обозначив через Xnm совокупность параметров n - го узла m - типа, множество состояний элемента "сборочное устройство" выразим в виде матрицы:
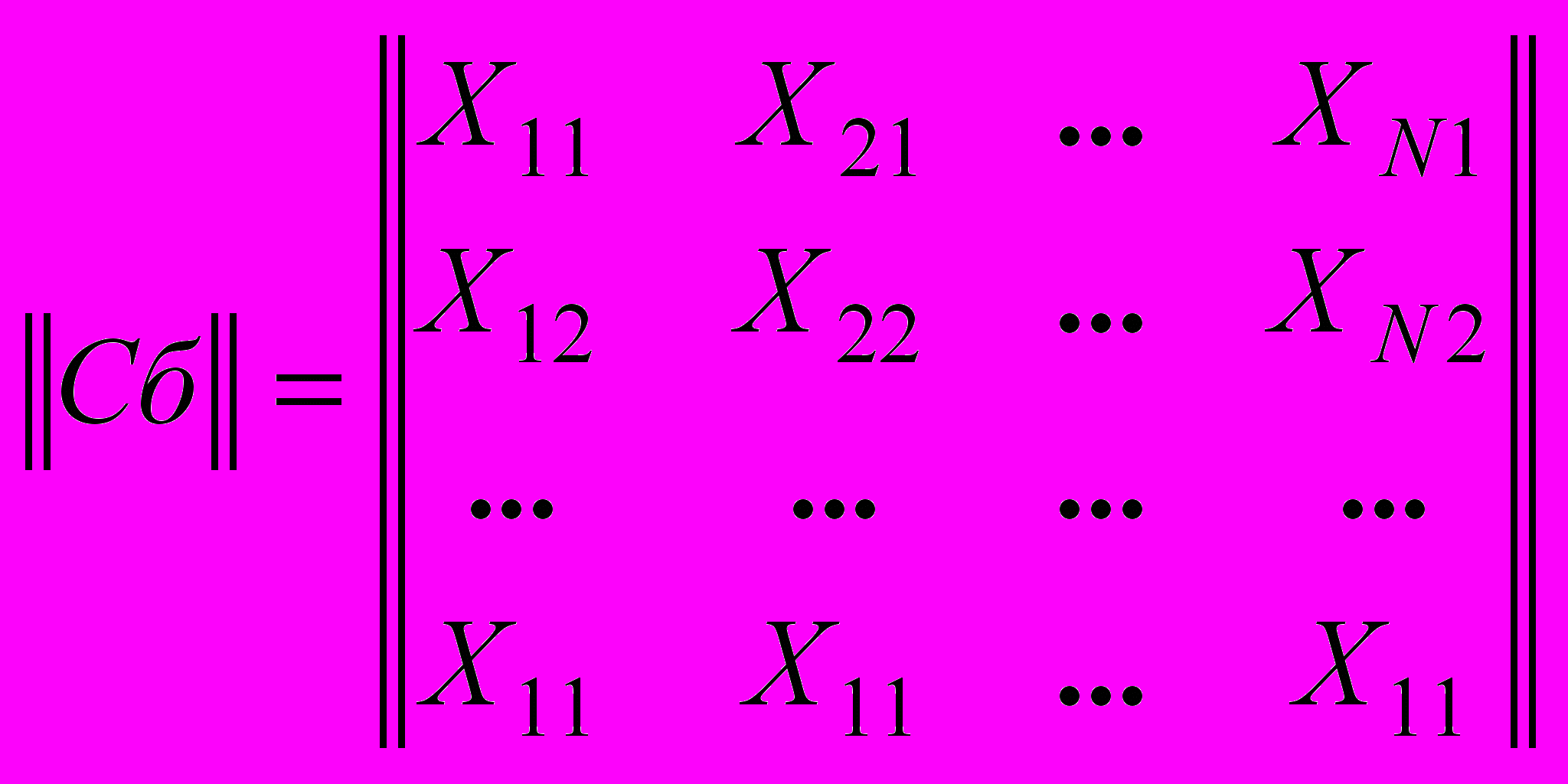
Аналогично строим матрицы для состояний элементов "Загрузочное устройство", "Базовая деталь" и "Эластичная кольцевая деталь". Характеристики узлов выбираем в качестве основы для построения графа, характеризующего множество возможных вариантов технологических элементов сборочного устройства, которое равно числу путей в графе.
С учётом большого количества вариантов синтез решения осуществляем, начиная с выбора вариантов основных элементов, включая все более и более существенные признаки.
Моделирование процесса обработки зубчатых конических колес с круговым зубом на ЭВМ
И. Н.Павлюченко, асп., В. Ю. Клименко, асп., Ю.Н.Внуков, д.т.н., проф.
Запорізький державний технічний університет, Запоріжжя
В настоящее время имеются различные методики расчета наладочных параметров оборудования и параметров зуборезных головок для обработки зубчатых конических колес с круговым зубом. Эти методики основаны на исследовании локальных характеристик поверхностей зубьев в расчетной точке и в ее окрестностях на базе общей модели станочного зацепления обрабатываемого и производящего колеса. Производящей поверхностью является поверхность вращения режущих кромок резцов зуборезной головки вокруг своей оси. Производящая поверхность профилирует обрабатываемую поверхность, определяющую характеристики зацепления.
Мощные компьютеры позволили реализовать процесс зубонарезания визуально, получить реальную модель детали, что в дальнейшем позволит проверить качество передачи. При этом используется не упрощенная производящая поверхность, а реальная математическая модель инструмента и заготовки. Их взаимное положение в пространстве рассчитывается по существующим методикам. В результате моделирования процесса станочного зацепления выявлены погрешности расчетов, которые отражаются на траектории перемещения инструмента и зацеплении в целом.
^ АНАЛИЗ СИЛОВОГО ЗАМЫКАНИЯ В СТАНОЧНЫХ ПРИСПОСОБЛЕНИЯХ
Ю.В. Пипкин, асп.
Донбасский горно-металлургический институт, г. Алчевск
Силовое замыкание в станочных приспособлениях (СП) является необходимым условием существования данной технической системы (ТС-СП), которое обеспечивается приложением усилия зажима заготовки. Значение анализа силового замыкания определяется его результатами – расчетом необходимого усилия зажима, оптимизацией расположения установочных и зажимных элементов СП, прогнозированием износа и упругих деформаций установочных и крепежных элементов, выбором параметров передаточного механизма и привода.
Основы анализа силового замыкания заложены в работах проф. Корса-
кова В.С., в которых представлены зависимости усилия зажима от коэффициентов трения и жесткости элементов силового замыкания с учетом коэффициента запаса, рассмотрены несколько частных случаев.
Изучение приведенных в учебных и справочных изданиях рекомендаций выявил противоречия в анализе силового замыкания в СП.
Утверждение о статической разрешимости уравнений равновесия заготовки противоречит форме вывода уравнений, когда используется понятие о предельной деформаций механизма зажима. Статическая определимость уравнений равновесия СП, по-видимому, должна обосновываться в каждом конкретном случае, и по возможности реализовываться конструкцией СП. Кроме уравнений равновесия геометрической статики (равенство нулю главных векторов и моментов системы сил) удобно использовать основное уравнение аналитической статики, уравнение Лагранжа (равенства нулю работ внешних сил, приложенных к системе материальных точек, на виртуальных перемещениях точек системы).
Логику предельных состояний упругой деформации силового замыкания, положенную в основу вывода уравнений равновесия заготовки, делает не эффективной использование коэффициента запаса, который переводит процесс зажима в область допредельных состояний. Решение формул, приведенных в литературе для механизмов зажима различного типа, в допредельной области при равенстве жесткостей и коэффициентов трения приводит к противоречивым результатам.
Сложный характер процессов в силовом замыкании СП подтверждают данные исследований разных авторов. При исследовании с целью определения наименьшего допустимого усилия зажима основным результатом для рассматриваемого вопроса явилось то, что полученные значения минимального предельного усилия зажима в несколько (2,58) раз меньше значений, оцененных теоретическим расчетом по известным формулам. Исследования влияния типа механизма зажима на качество обработки, показали предпочтительность зажимов второй группы по В.С. Корсакову при условии отсутствия промежуточного зажимного механизма (повышение точности на 1-2 квалитета, уменьшение шероховатости на 3040%). Эти результаты и результаты других авторов указывают на актуальность углубленного исследования силового замыкания в ТС-СП.
Разработанная методика построения и анализа математических моделей СП позволяет исследовать силовое замыкание. Для получение аналитического решения в общем виде систем невысокой размерности применялся математический пакет
Maple 6.
^ ПРОЕКТИРОВАНИЕ ПРОТЯЖЕК
С ИСПОЛЬЗОВАНИЕМ ПРОГРАММ SOLIDWORKS И EXCEL
Филимонов Е. В.
Национальный технический университет Украины «ХПИ», Харьков
Автоматизация конструкторско-технологической подготовки производства позволяет предприятию быстро реагировать на изменение спроса, в короткое время переналаживаться на новые виды продукции. Целые комплексы CAD-систем активно внедряются на машиностроительных предприятиях. При этом может использоваться широкий спектр программ - от управления документооборотом предприятия, до обеспечения непосредственно производства, с интеграцией всех ветвей между собой.
Зачастую такая интеграция или вложенность современных программ позволяет избавить пользователя от непосредственно программирования. Проектирование с последующим созданием 3D-модели и её визуализацией всегда будет иметь преимущество, позволяя избежать ошибок в процессе разработки и принять оптимальное решение. 3D-модель может участвовать во всех операциях и процедурах автоматизированного проектирования и производства в целом. Возможности 3D-моделирования использованы авторами при проектировании шпоночных протяжек.
Пример проектирования основывается на программах Solid Works и Excel, часто использующихся при подготов-ке производства, причем полностью интегрированных между собой.
Solid Works позволяет создавать библиотеки стандартных твердотельных моделей. Вся расчётная часть выполняется при помощи Excel с её возможностями в создании и управлении базами данных, поиском решений и оптимизацией.
На первом этапе была разработана параметризованная 3D-модель шпоночной протяжки, обладающая всеми возможными конструктивными признаками. На этом этапе также целесообразно создать связанный с моделью чертёж протяжки с отображением всех параметров.
Второй этап - создание Excel-таблицы. Модель должна быть полностью определена с занесением всех параметров базовой конфигурации в управляющую строку таблицы.
На заключительном этапе была создана база данных с описанием всего массива стандартных параметров, таких как размеры хвостовика, зубьев, рекомендуемые длины протяжек и т.д., с разработкой на её основе расчётной части по какой-либо из методик.
Теперь процесс проектирования может производиться либо по минимальным исходным данным (особенно если проектируется типовая протяжка для стандартного шпоночного паза), либо с необходимой коррекцией и оптимизацией для более сложных задач.
Все вышеописанные действия не требуют от разработчика приложения опыта в программировании. Успешность разработки CAD-приложения ограничивается лишь навыками во владении программой и знаниями в области проектирования режущих инструментов.
Однако, следует отметить, что иногда целесообразно осуществить полный процесс проектирования на более глубоком уровне при помощи различных языков программирования с задействованием специалистов более высокого класса.
Зміст
Ануфрієв О. С., Зеленський С. В. Экспериментальное исследование влияния режима резания на технологические показатели процесса тангенциального точения 4
Афтаназів І. С., Баранецька О. Р., Кусий Я. М. Дослідження динаміки руху вібраційно-відцентрових зміцнювальних пристроїв з електромагнітним приводом 4
Белозеров О. В. Синтез гидроприводов подачи точного позиционирования
Бобро Ю. Г., Редько О. І. Особливості структури та зносостійкості нових литих композитних матеріалів, створених на базі сірого чавуну, легованого міддю, оловом та свинцем
Бушля В. М. Напрямки удосконалення чистових торцевих фрез для обробки плоских поверхонь деталей 6
Водолазська Н. В. Анализ факторов, влияющих на качество автоматической сборки резьбовых соединений 7
Гедрович А. І., Гальцов І. А., Друзь О. М., Ткаченко С. А. Исследование изменений напряжений и деформаций в тонколистовой металлоконструкции обшивки вагона дизельпоезда, после сборки-сварки и после ходовых испытаний 8
Гедрович А. І., Друзь О. М. Анализ охлаждающих жидкостей, применяющихся в промышленности и возможность их использования в сварочном производстве 10
Герасимчук О. П., Гордєєв О. Ф. Оптимізація робочих характеристик високоточних шпиндельних вузлів 11
Гордєєв О. Ф., Тимчук В. М. Прогнозування точності шпиндельних вузлів на гідростатичних підшипниках 12
Гребенок Т. П., Бодрова Л. Г. Вплив технологічних параметрів на різальні властивості керметів на основі карбіду титану 13
Гріньов Ю. А., Матюха П. Г. Исследование изменения геометрических параметров универсально-сборных резцов с поворотной режущей частью 14
Деревянченко О. Г., Грабченко А. І., Романенко Д. Б. Оценка состояния режущего инструмента по выходным данным мониторинговой системы 17
Дєдов О. Д., Стародубов С. Ю., Івашина М. В. Анализ существующих конструкций центрирующих станочных приспособлений 18
Думанчук М. Ю. Разработка структуры операций модульных технологических процессов 19
Дядюра К. О., Кас’янов Л. О. Условия нагружения режущего лезвия инструмента с покрытием при попутном тангенциальном точении
Жигуц Ю. Ю., Скиба Ю. Ю. Технологія синтезу термітних високоміцних чавунів 20
Залога В. О., Голдун Д. Г. Выбор рациональной конструкции крепления СМНТП в режущей части вихревых головок 22
Захаров П. О., Місюк В. М. Нові моделі підшипників шпиндельних вузлів для надвисокошвидкісної обробки 23
Захаров П. О., Ткачук М. П. Навантажувальні характеристики газогідравлічних інерційних підшипників
Ковалевський С. В., Медведев В. В. Применение нейросетей при оценке информативности частот диагностического сигнала 24
Колот Л. П., Бойко Ю. А.. Системный подход к оценке влияния технологических факторов на качество деталей машин 26
Криворучко Д. В. Прогнозирование силы резания в процессах с переменной толщиной среза 27
Крижанівський В. А., Гречка А. І. Дослідження навантажувальної здатності пінольних механізмів силових вузлів агрегатних верстатів 28
Леснінов І. Ю., Іванова П.С., Маклаков О. М. Моделирование случайных размерных параметров инструмента, определяющих динамику процесса шлифования 30
Литвиненко М. В. Построение стратегии оценки шероховатости полиметріх оптических изделий 31
Мазур М. П., Крижанівський С. А. Разработка прогнозирующей модели управления точностью процесса контурного фрезерования концевым инструментом
Марцінковська І. П. Автоматизація побудови схеми перекриття вибою шарошками, озброєними клиновидними зубками 32
Міранцов С. Л. Динамический расчет сборного инструмента для тяжелых станков в процессе резания 33
Мішура Є. В. Проблема обоснования и выбора целевой функции при синтезе технологических операций 34
Новосьолов Ю. К., Тараховський О. Ю. Параметрический синтез сборочных устройств для сборки уплотнительных соединений 36
Обравіт Т. Г. Рациональные конструкции и технологические процессы изготовления деталей зерноперерабатывающих механизмов
Охріменко О. А. Особенности профилирования точных червячных зуборезных фрез
Павлюченко І. М., Кліменко В. Ю., Внуков Ю. М. Моделирование процесса обработки зубчатых конических колес с круговым зубом на ЭВМ 37
Піпкін Ю.В. Анализ силового замыкания в станочных приспособлениях 38
Філімонов Є. В. Проектирование протяжек с использованием программ solidworks и excel 39
Чибиряк Я. І. Оптимизация технологических процессов сборки в машиностроении
Швабюк В. І., Захаров П. О., Зубовецька Н. Т. Критерії подібності газогідравлічних інерційних підшипників
Укладач
Залога Вільям Олександрович
Відповідальний за випуск
Ануфрієв Олексій Станіславович
Оформлення орігінал-макета
Криворучко Дмитро Володимирович
Віддруковано у комп’ютерному центрі
Сумського держаного університету
Наклад 40 прим.
СумДУ, 40007, м. Суми, вул. Римського-Корсакова, 2 |