М. А. Копин Лабораторные и лабораторно-практические работы по дисциплине «Детали машин и основы конструирования» для специальностей: «Технология обслуживания и ремонт машин в апк» и«Механизация сельского хозяйств
Вид материала | Лабораторная работа |
- Программа дисциплины по кафедре Детали машин детали машин и основы конструирования, 355.21kb.
- Рабочая программа по дисциплине «технология ремонта машин» для студентов очного обучения, 305.78kb.
- Программа дисциплины по кафедре Детали машин детали машин и механизмов, 575.22kb.
- Рабочая программа По дисциплине «Детали машин и основы конструирования» По специальности, 668.69kb.
- И. М. Губкина Кафедра «Техническая механика» Положение о рейтинговой системе оценки, 59.48kb.
- Рабочая программа учебной дисциплины по дисциплине «Детали машин и основы конструирования», 251.9kb.
- Примерная программа дисциплины детали машин и основы конструирования Рекомендуется, 287.02kb.
- Чубенко Елена Филипповна Детали машин и основы конструирования конспект, 86.56kb.
- Рабочая программа по дисциплине опд ф. 02. 04 "Детали машин и основы конструирования", 255.62kb.
- Рабочей программы дисциплины Детали машин и основы конструирования по направлению подготовки, 37.93kb.
«Требования, предъявляемые к выполнению
машиностроительных чертежей».
Цель работы: Изучение некоторых требований выполнения чертежей при проектировании деталей машин.
- ^ Допуски формы и расположения поверхностей на чертеже.
а) валы
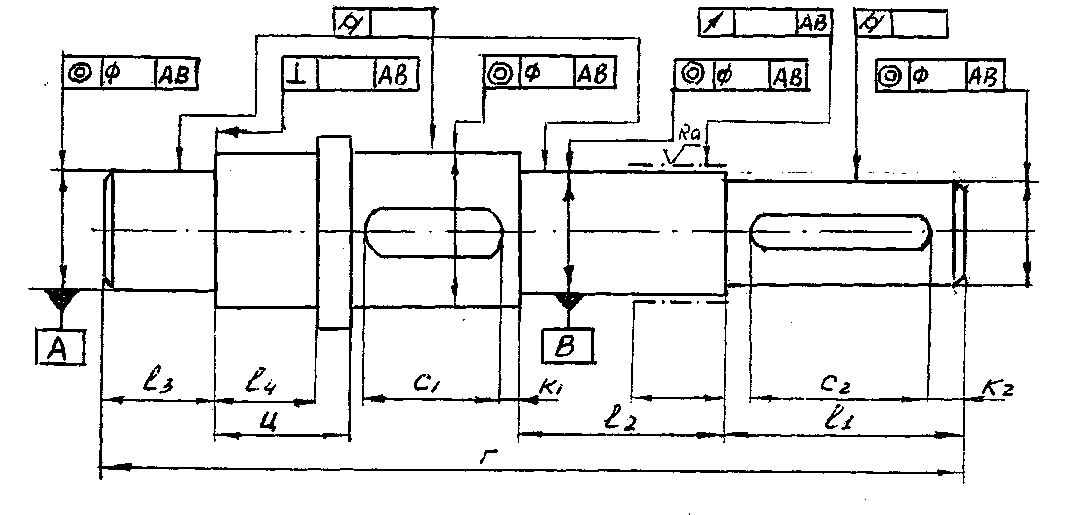
С1 и С2 – размеры сопряженные – длины шпоночных пазов; Г и Ц - габаритный и цепочный размеры; К1 и К2 – размеры, координирующие расположение шпоночных пазов; l1 – длина выступающего конца вала; l1, l2, l3, l4 - длины поверхностей; (индексы 1, 2, 3, 4 – последовательность токарной обработки поверхностей вала).
На чертежах деталей – тел вращения (валы, валы-шестерни, червяки, колеса и др.) следует располагать:
а) осевые линейные размеры под изображением детали не более чем на четырех уровнях; б) условное обозначение базовой поверхности под изображением детали; в) условные обозначения допусков формы и расположения над изображением детали не более чем на двух уровнях; г) условное изображение параметров шероховатости – на верхних частях детали, а на торцовых поверхностях – под изображением детали; д) полки-линии выноски, указывающие поверхности для термообработки и покрытий – над изображением детали.
^ Обозначения допусков формы и расположения поверхностей.
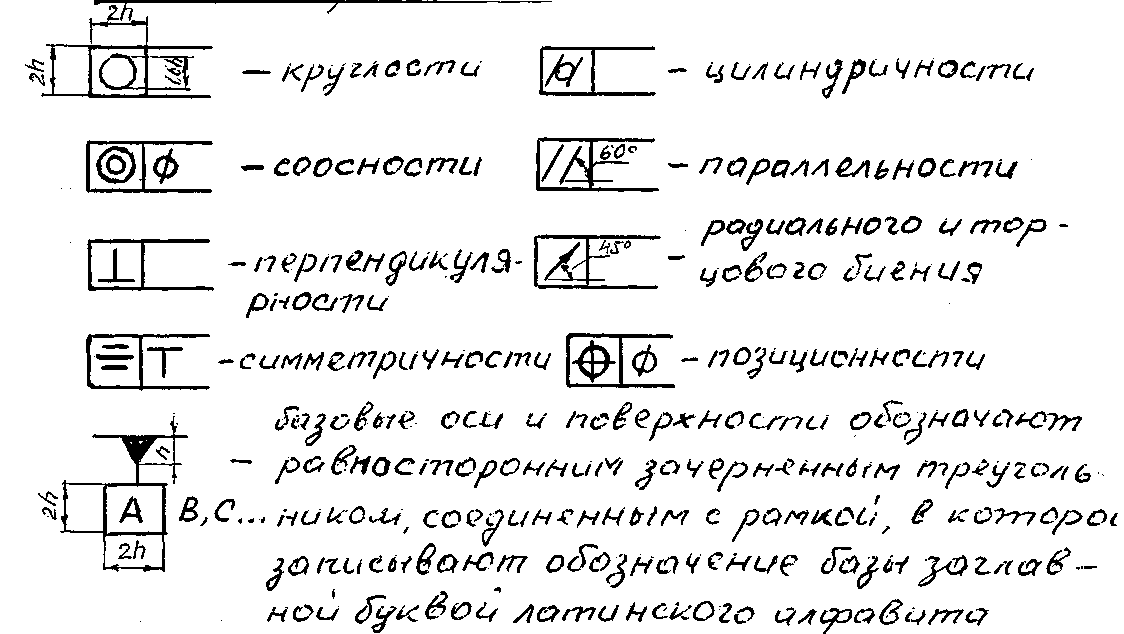
Нанесение на чертежах деталей обозначений баз,
допусков формы и расположения.
а) если базой является поверхность, а не ось, то зачерненный треугольник располагают на достаточном расстоянии от конца размерной линии;
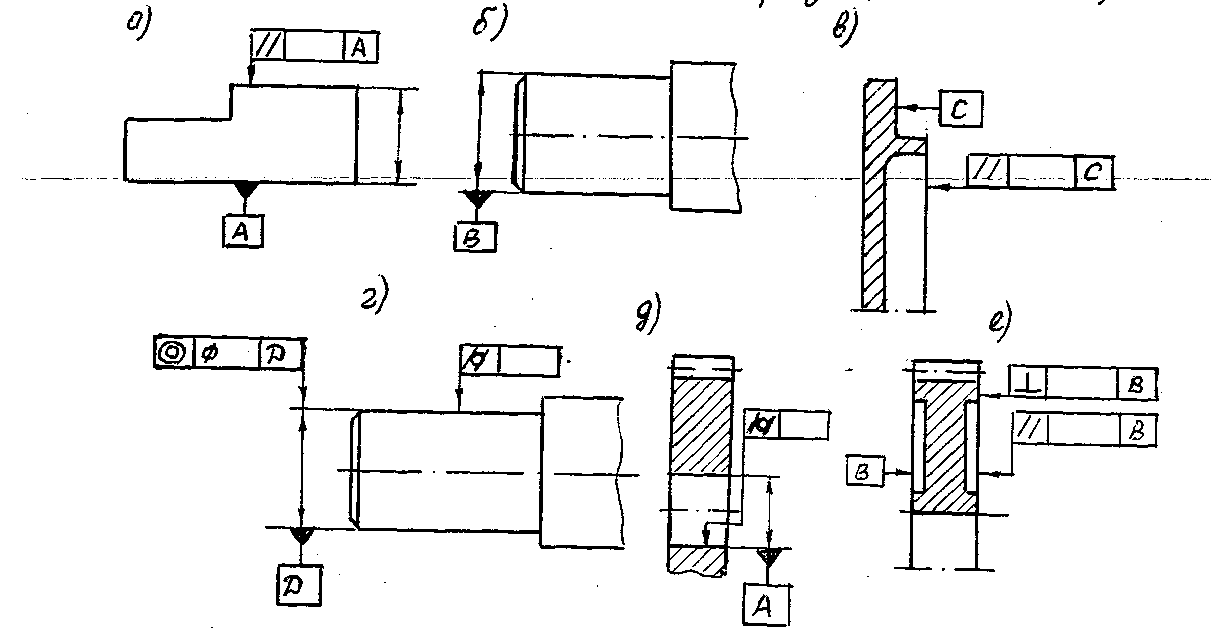
б) если базой является ось или плоскость симметрии, то зачерненный треугольник располагают в конце размерной линии;
в) если нет необходимости назначать базу, вместо зачерненного треугольника применяют стрелку;
г) если допуск относится к поверхности, а не к оси элемента, то стрелку располагают на достаточном расстоянии от конца размерной линии (а,2);
д) если же допуск относится к оси или плоскости симметрии, то конец соединительной линии должен совпадать с продолжением размерной линии (2); е) допуск цилиндричности посадочной поверхности (д) назначают, чтобы ограничить концентрацию контактных давлений по посадочной поверхности;
ж) допуск параллельности торцов ступицы (е) задают, чтобы создать точную базу для подшипников качения и уменьшить перекос колец подшипников.
- ^ Шероховатость поверхности.
Наибольшее применение в машиностроении нашли следующие параметры шероховатости ГОСТ 2789-73:
Rz – высота неровностей профиля, мкм;
Ra – среднее арифметическое отклонение профиля, м.
Параметр Rz назначают на поверхности, получаемой литьем, ковкой, чеканкой, т.к. он дает минимальную информацию о поверхности детали (5 измерений высоты неровностей поверхности).
Параметр Ra – измерение всех впадин и выступов на поверхности, поэтому он дает полную информацию о поверхности детали. Параметр Ra назначают на все обработанные поверхности деталей.
Значение шероховатости указывают: для параметров Ra – без символа (например, 0,8); для параметров Rz – после символа (например, Rz 20).
Для обозначения на чертежах шероховатости поверхностей применяют знаки:
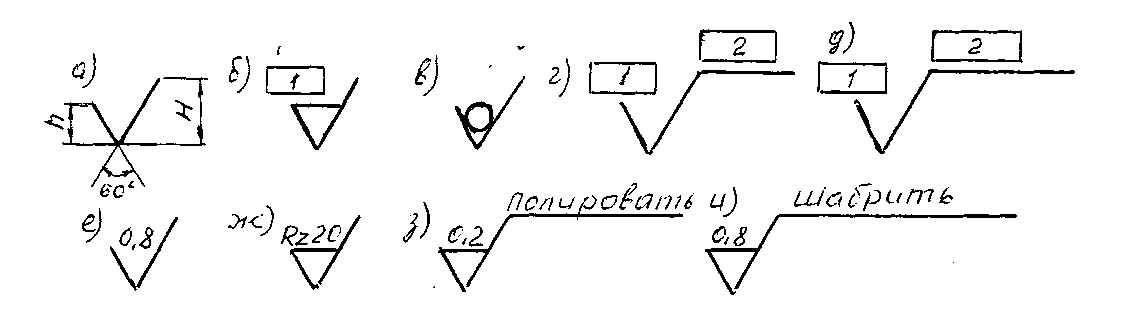
Высоту h принимают равной высоте размерных чисел на чертеже, высоту Н – в зависимости от объема записи (Н = 1,5 ÷ 3,0h).
Если вид обработки поверхности конструктор не устанавливает, применяют знак (рис.а). Этот знак является предпочтительным. Если требуется при образовании поверхности удаление слоя материала (шлифование, полирование и др.) применяют знак (рис.б).
Если поверхность образована без удаления слоя материала (чеканка, накатывание роликами и др.) применяют изображение знака (рис.в), а также на поверхностях не обрабатываемых по данному чертежу.
На месте прямоугольника ^ 1 (рис.б,г,д) записывают числовые значения параметров Ra или Rz (рис.е,ж), а на месте прямоугольников 2 – вид обработки поверхностей (рис.з,и).
Обозначение шероховатости поверхностей на изображении детали располагают на линиях контура, на выносных линиях в непосредственной близости от размерной линии (рис.а) или на полках линий-выносок при недостатке места на размерной линии или на ее продолжении (рис.б).
Если шероховатость одной и той же поверхности различна, то ее разделяют тонкой линией и на каждой части поверхности показывают свое изображение шероховатости (рис.в).
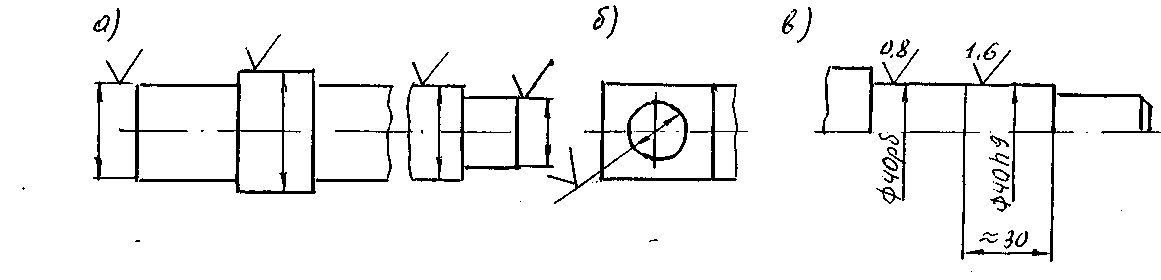
Обозначение преобладающей шероховатости показывают в правом верхнем углу поля чертежа (рис.а).
Если преобладающее число поверхностей не обрабатывают по данному чертежу, то шероховатость их показывают в правом верхнем углу поля чертежа (рис.б).
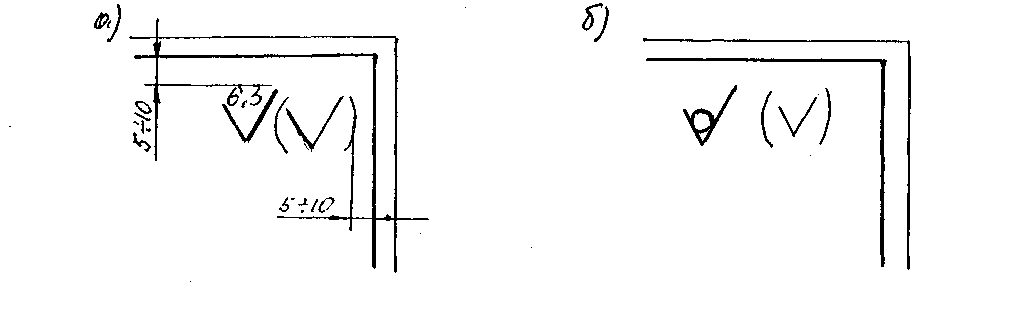
- ^ Обозначения термической обработки.
Если термообработке подвергают отдельный участок детали, то его обводят на чертеже утолщенной штрихпунктирной линией, а на полке линии-выноски наносят показатели свойств материала (рис.а).
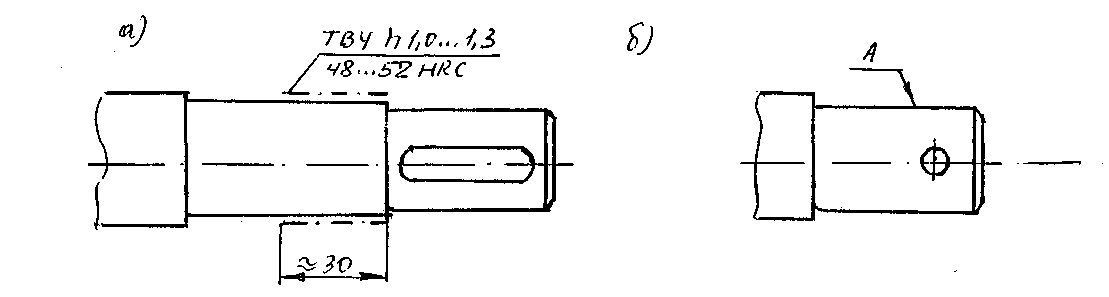
Если всю деталь подвергают одному виду термообработки, а некоторые ее части другому или оставляют без обработки в технических условиях делают запись по типу:
55…60HRс, кроме места, указанного особо (рис.а).
40…45HRс, кроме поверхности А (рис.б).
- Ответить на следующие вопросы:
- Как располагают на чертежах деталей тел вращения линейные размеры и обозначение базовых поверхностей?
- Где располагают и с какими параметрами обозначение баз?
- Расшифровать обозначения допусков формы и расположения поверхностей?
- Расшифровать нанесение на чертежах деталей обозначений баз, допусков формы и расположения?
- Расшифровать обозначения шероховатости и термической обработки для различных условий.
Лабораторно-практическая работа № 9.
«Шпоночные и шлицевые соединения».
Цель работы: Изучение конструкций соединений, их параметров и характеристик. Примеры расчета шпоночного и шлицевого соединений.
- Выбор шпонок для ступенчатых валов.
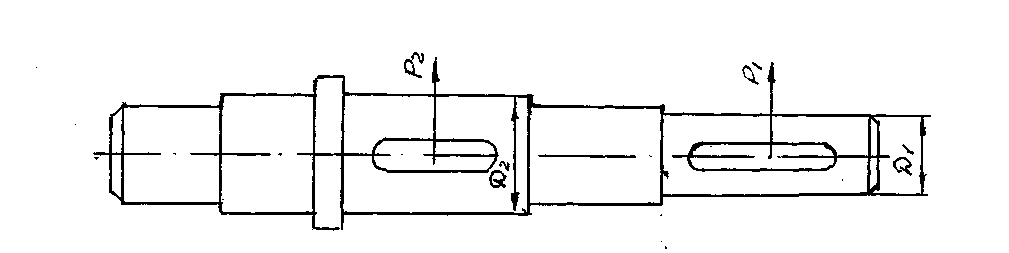
Рис. 1 Ступенчатый вал.
На участке между серединами шпонок (Рис.1.) передается постоянный вращающий момент Т. Силы Р1 и Р2, действующие на шпонки и приложенные на плече, равном радиусу соответствующей ступени вала, составляют
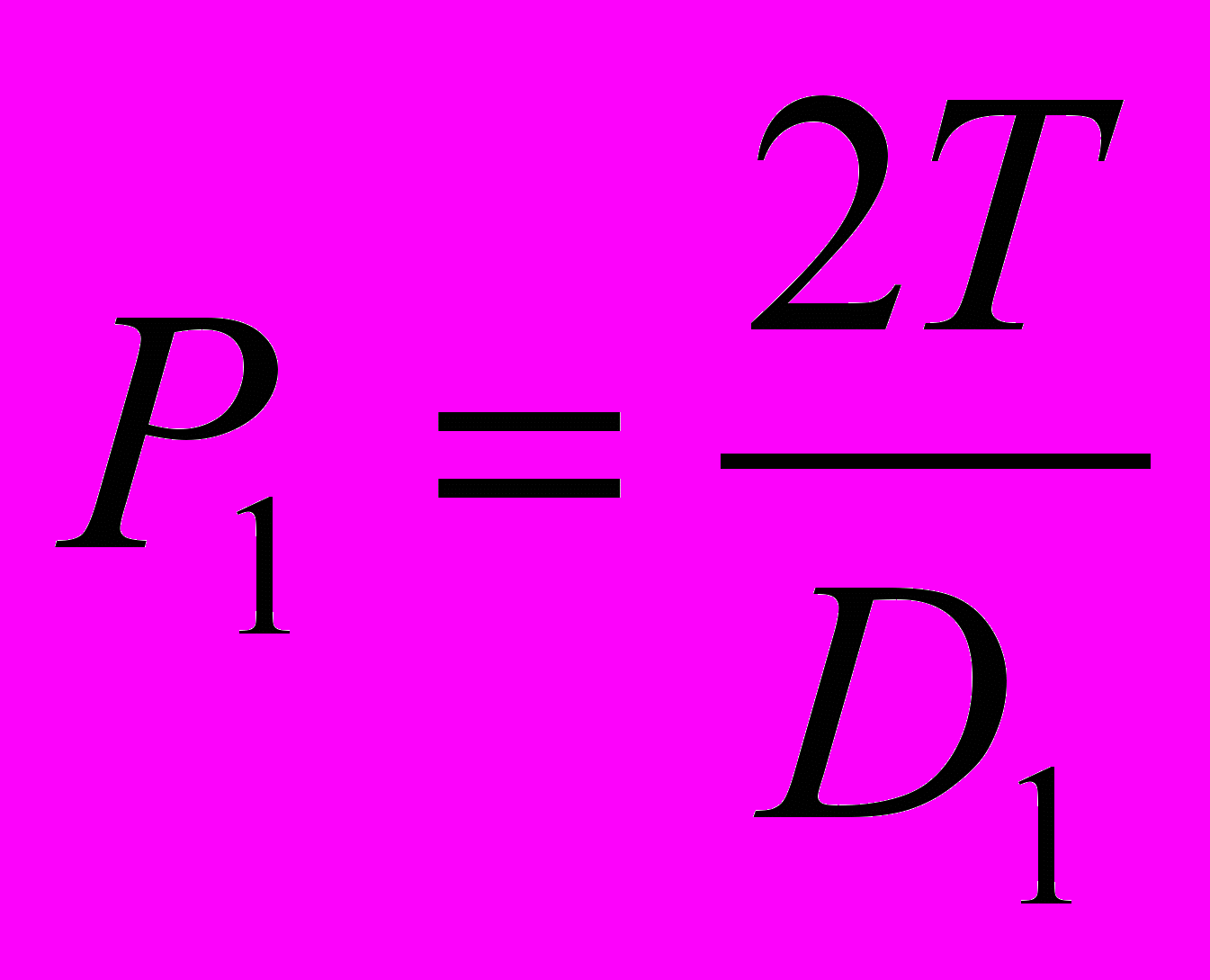
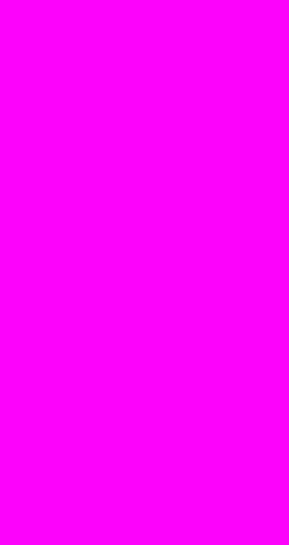
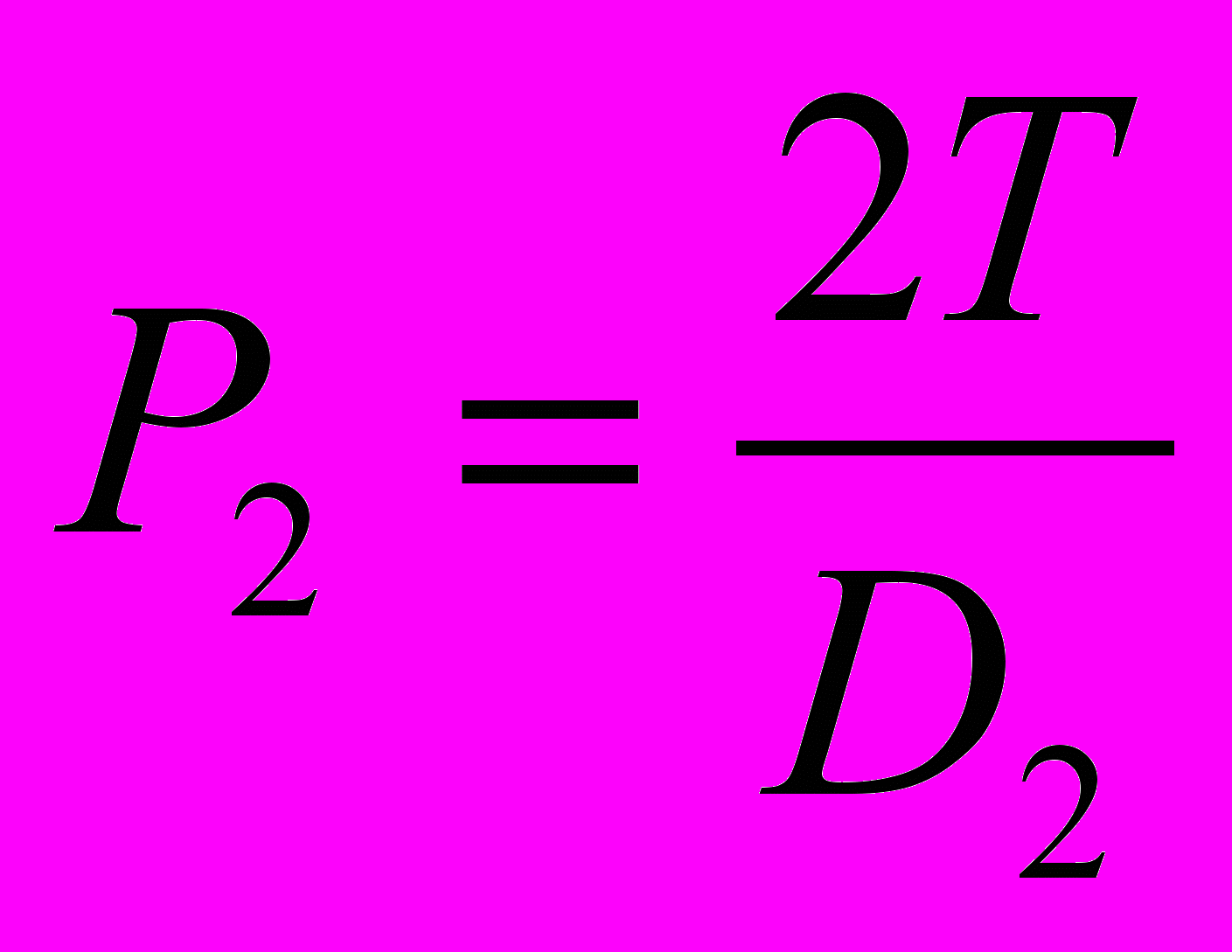
D2 > D1, значит, шпонка ступени D2 нагружена меньше шпонки ступени D1. По соображениям прочности и работоспособности шпоночных соединений нет оснований к назначению для ступени D2 шпонки большей, чем для ступени D1. Наоборот, чем больше диаметр ступени ступенчатого вала, тем меньше для нее может быть сечение шпонки.
Наличие на одном валу шпоночных пазов, одинаковых по сечению и длине улучшает технологичность конструкции вала. Таким образом, рекомендуется назначать одинаковые шпонки для всех ступеней вала исходя из ступени наименьшего диаметра, имеющего шпоночный паз.
- Расчет шпонок.
- Призматическая шпонка (рис.2.)
- Призматическая шпонка (рис.2.)
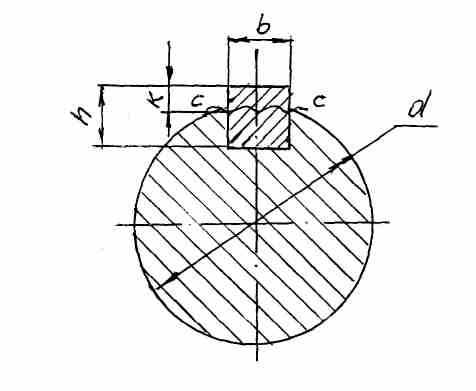
Рабочие грани проверяют на смятие, сечение С – С на срез.
Условие прочности на смятие
[Tmax] = 0,5 . d . K . l[σсм]
Условие прочности сечения С – С на срез:
[Tmax] = 0,5( d + K) .b . l[τсм].
где: [Tmax] – наибольший допускаемый вращающий момент, Н.м; l – рабочая длина шпонки, мм; d – диаметр вала, мм; b – ширина шпонки, мм; h – высота шпонки, мм; K – высота шпонки, выступающей из тела вала, мм; [σсм] - допускаемые напряжения смятия, МПа; [τсм] – допускаемые напряжения среза, МПа.
При расчете принимают нагружение шпонки по длине равномерным. На срез шпонки проверяют в особо ответственных случаях. В случае установки двух противоположно расположенных шпонок вводят поправочный коэффициент 0,75.
- Пример расчета: Подобрать призматическую шпонку со скругленными торцами для передачи момента от стальной шестерни к валу (рис.3.) и определить допускаемую величину передаваемого вращающего момента.
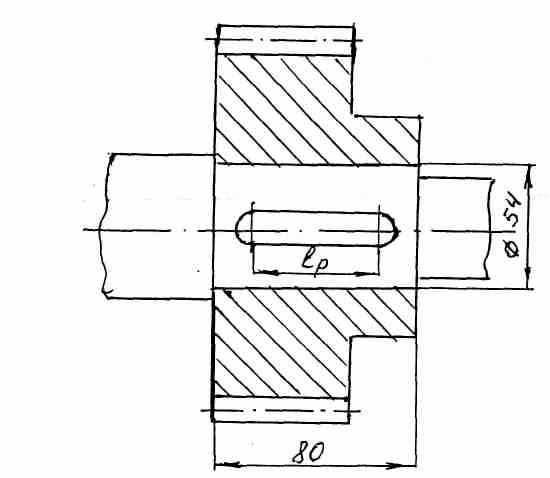
Решение: 1. По ГОСТ 8788-68 для вала, имеющего диаметр d = 54мм, рекомендованы размеры сечения шпонки b x h = 16 x 10мм.
2. Принимаем длину шпонки на 10мм меньше длины ступицы из рекомендованных в таблице размеров l = 70мм.
3. Расчетная длина шпонки
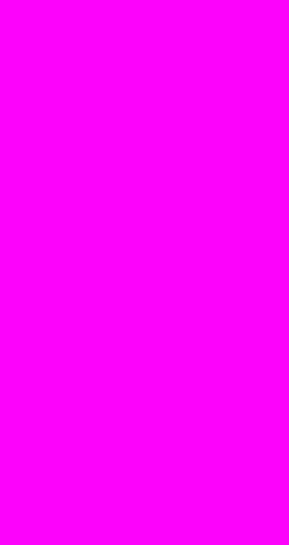
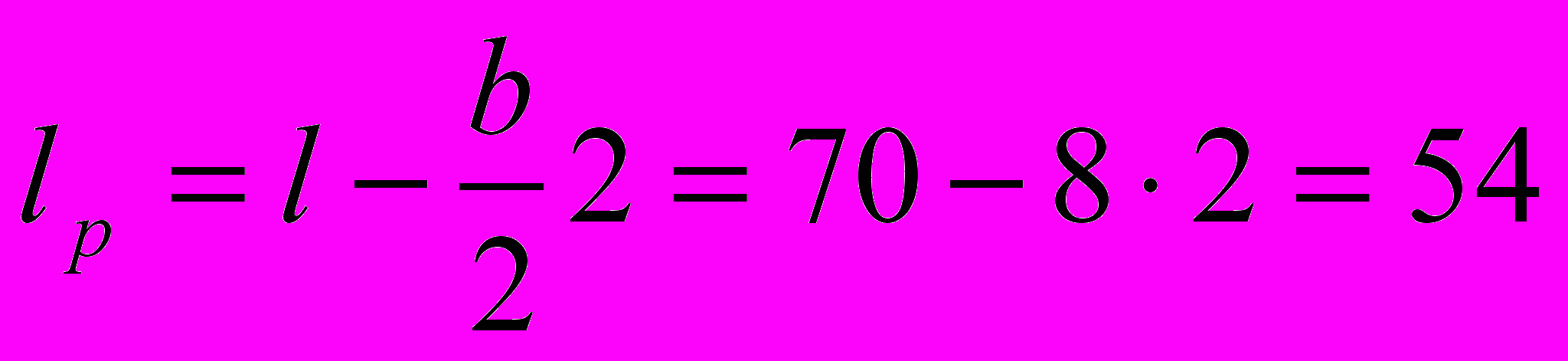
Рис. 3
- Допускаемый момент, исходя из условия прочности шпоночного соединения на смятие:
[Tmax] = 0,5 . d . к . lp[σсм] = 0,5 . 54 . 5 . 54 . 150 = 1093,5Н.м
[σсм] = 150Н/мм2 – допускаемое напряжение на смятие при шестерне, изготовленной из стали.
- Допускаемый момент, исходя из условия прочности шпонки на срез:
[Tmax] = 0,5(d + к)b . lp[τср] = 0,5(54 + 5) . 16 . 54 . 90 = 2099,5Н.м
[τср] = 90Н/мм2. Принимаем окончательно допускаемый момент
[Tmax] = 1000Н.м (с округлением) по напряжениям смятия, как мень ший по величине.
- Шлицевые соединения.
- Расчет на прочность прямобочного соединения.
Боковые поверхности зубьев шлицевого соединения работают на смятие, а их основание на изгиб и срез. Для применяемых соотношений элементов шлицевых соединений основным является расчет на смятие:
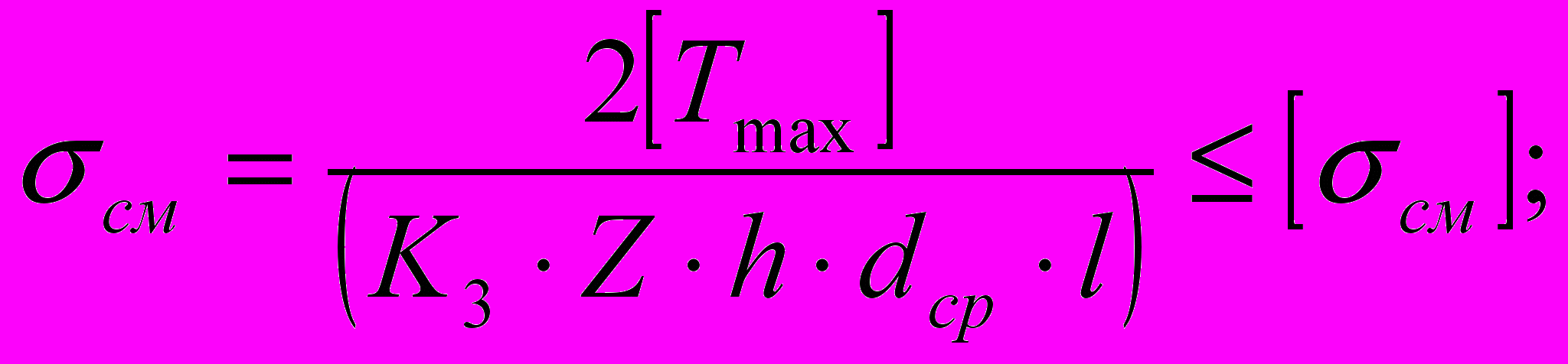
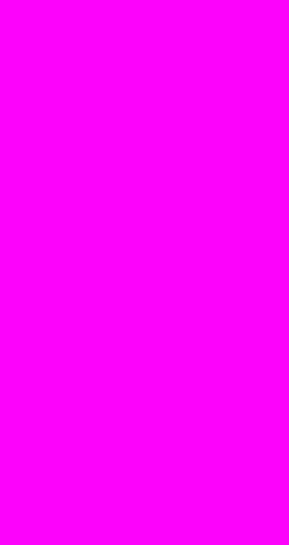
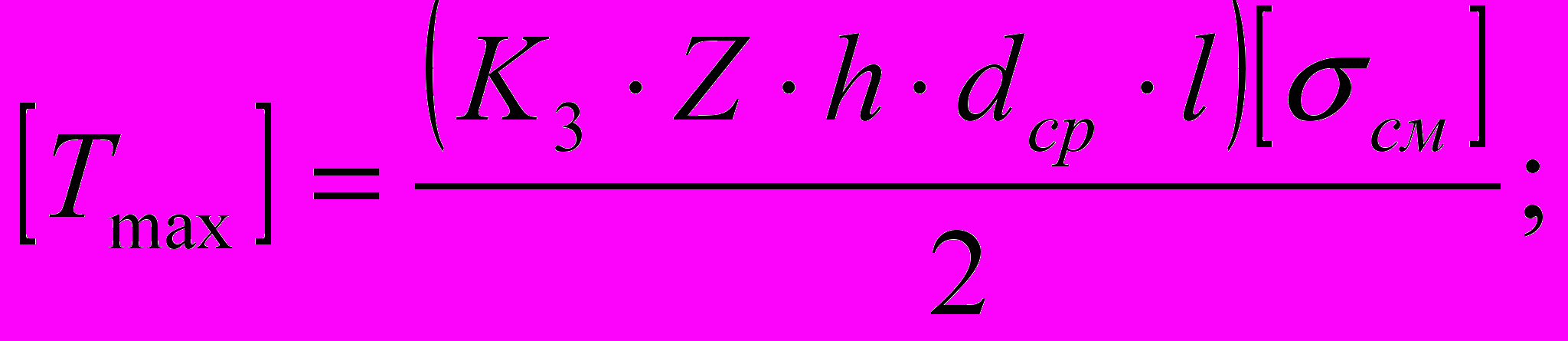
где: [Tmax] – максимальный крутящий момент (наибольший из длительно действующих); К3 = 0,7÷0,8 – коэффициент неравномерности нагрузки по зубьям; Z – число зубьев; h – рабочая высота зубьев; l – рабочая длина зубьев; dcp – средний диаметр соединения.
Для прямобочных зубьев h = 0,5(D – d) – 2f; dcp = 0,5(D + d); (см. рис.4.)
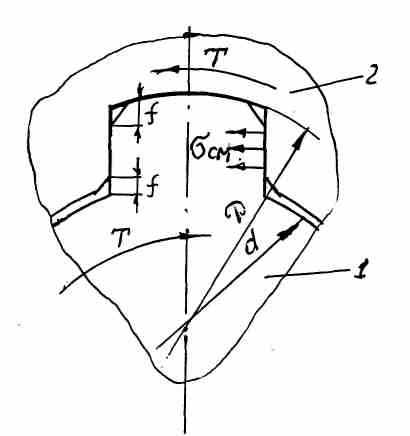
Расчет на смятие предупреждает пластические деформации рабочих поверхностей зубьев при перегрузках. При записи расчетных формул принято все корректирующие коэффициенты учитывать при расчете допускаемых напряжений.
Рис. 4.
3.2. Пример расчета: Заменим шпоночное соединение (рис.3) шлицевым прямобочным и сравним величины допускаемых крутящих моментов. Соединение неподвижное, условия эксплуатации средние, рабочие грани шлицов подвергнуты термообработке. Длину поверхности контакта зубьев принимаем l = 70мм.
Решение:
1. По таблице находим размеры шлицевого соединения с наружным диаметром вала D = 54мм. Средняя серия

f = 0,5мм – величина зазора. Z – число зубьев – 8.
2. Находим рабочую высоту контактируемых поверхностей зубьев и сред ний диаметр.
h = 0,5(D – d) – 2f = 0,5(54 – 46) – 2 . 0,5 = 3мм.
dcp = 0,5(D + d) = 0,5(54 + 46) = 50мм.
3. Допускаемый момент при [σсм] = 140Н/мм2
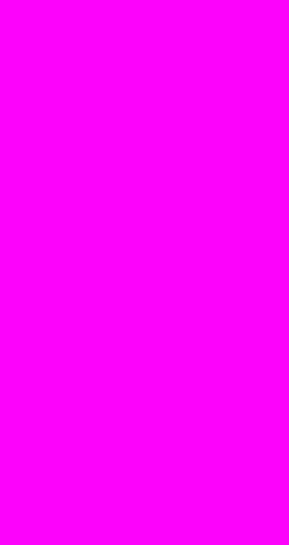

При одинаковой длине поверхности контакта и диаметре вала шлицевое соединение обладает большей нагрузочной способностью, чем шпоночное в 4,4 раза.
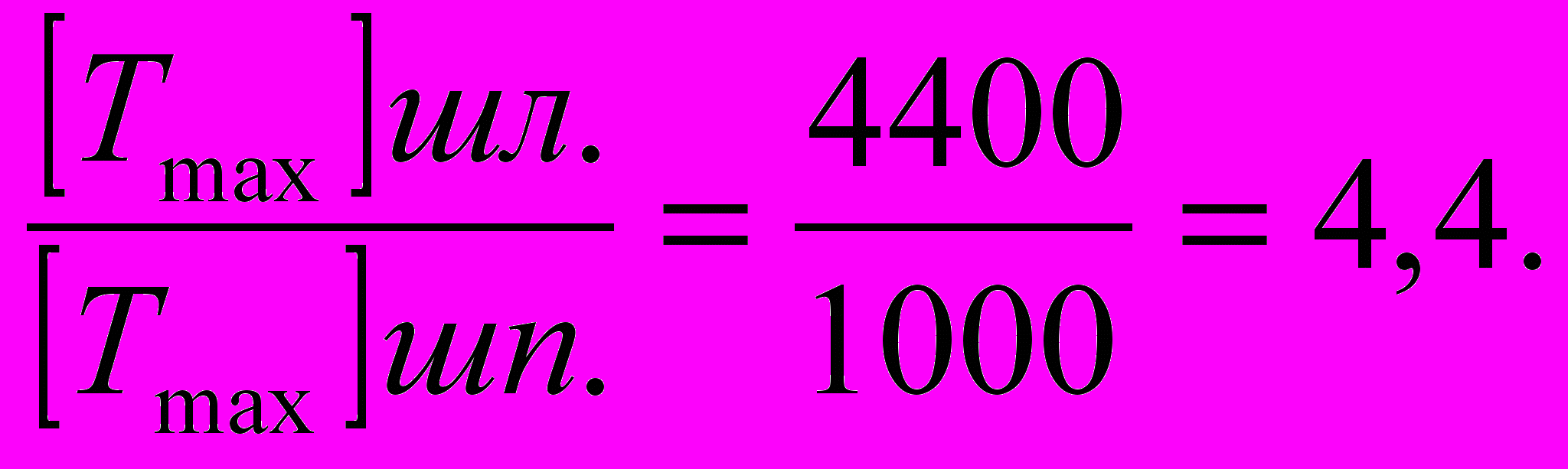
Используемая литература.
- М.Н. Иванов «Детали машин», М. Высшая школа, 2002г.
- О.П. Леликов «Основы расчета и проектирования деталей и узлов машин», конспект лекций. М. Машиностроение, 2002г.
- Д.В. Чернилевский «Детали машин – проектирование приводов технологического оборудования», М. Машиностроение, 2002г.
- П.Ф. Дунаев, О.П. Леликов «Детали машин – курсовое проектирование», М. Высшая школа, 2002г.
- А.В. Ерогин и др. «Детали машин и основы конструирования» Учебное пособие, М. Колос, 2004г.