М. А. Копин Лабораторные и лабораторно-практические работы по дисциплине «Детали машин и основы конструирования» для специальностей: «Технология обслуживания и ремонт машин в апк» и«Механизация сельского хозяйств
Вид материала | Лабораторная работа |
- Программа дисциплины по кафедре Детали машин детали машин и основы конструирования, 355.21kb.
- Рабочая программа по дисциплине «технология ремонта машин» для студентов очного обучения, 305.78kb.
- Программа дисциплины по кафедре Детали машин детали машин и механизмов, 575.22kb.
- Рабочая программа По дисциплине «Детали машин и основы конструирования» По специальности, 668.69kb.
- И. М. Губкина Кафедра «Техническая механика» Положение о рейтинговой системе оценки, 59.48kb.
- Рабочая программа учебной дисциплины по дисциплине «Детали машин и основы конструирования», 251.9kb.
- Примерная программа дисциплины детали машин и основы конструирования Рекомендуется, 287.02kb.
- Чубенко Елена Филипповна Детали машин и основы конструирования конспект, 86.56kb.
- Рабочая программа по дисциплине опд ф. 02. 04 "Детали машин и основы конструирования", 255.62kb.
- Рабочей программы дисциплины Детали машин и основы конструирования по направлению подготовки, 37.93kb.
«Изучение конструкций соединительных муфт для валов».
Цель работы: изучение конструкций соединительных муфт постоянной группы, недопускающих расцепления валов в процессе эксплуатации машин.
При выполнении работы необходимо:
- Вычертить эскизы следующих типов муфт:
- глухой втулочной и фланцевой муфт;
- кулачково-дисковой и зубчатой компенсирующих муфт;
- упругих втулочно-пальцевой и с резиновой звездочкой муфт.
- глухой втулочной и фланцевой муфт;
- Описать конструкцию, принцип действия, область применения, компенсирующие свойства и принцип передачи крутящего момента.
- Виды несоосности валов показать на схемах отклонений их осей от номинального расположения.
- Определить слабое звено в соединении муфты с валами.
- Перечислить преимущества и недостатки каждой из муфт.
Эскизы муфт:
Муфта втулочная
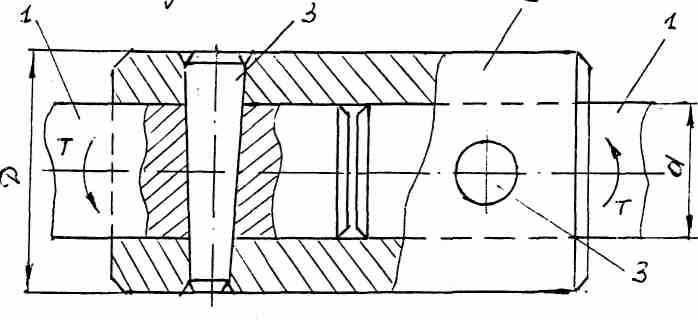
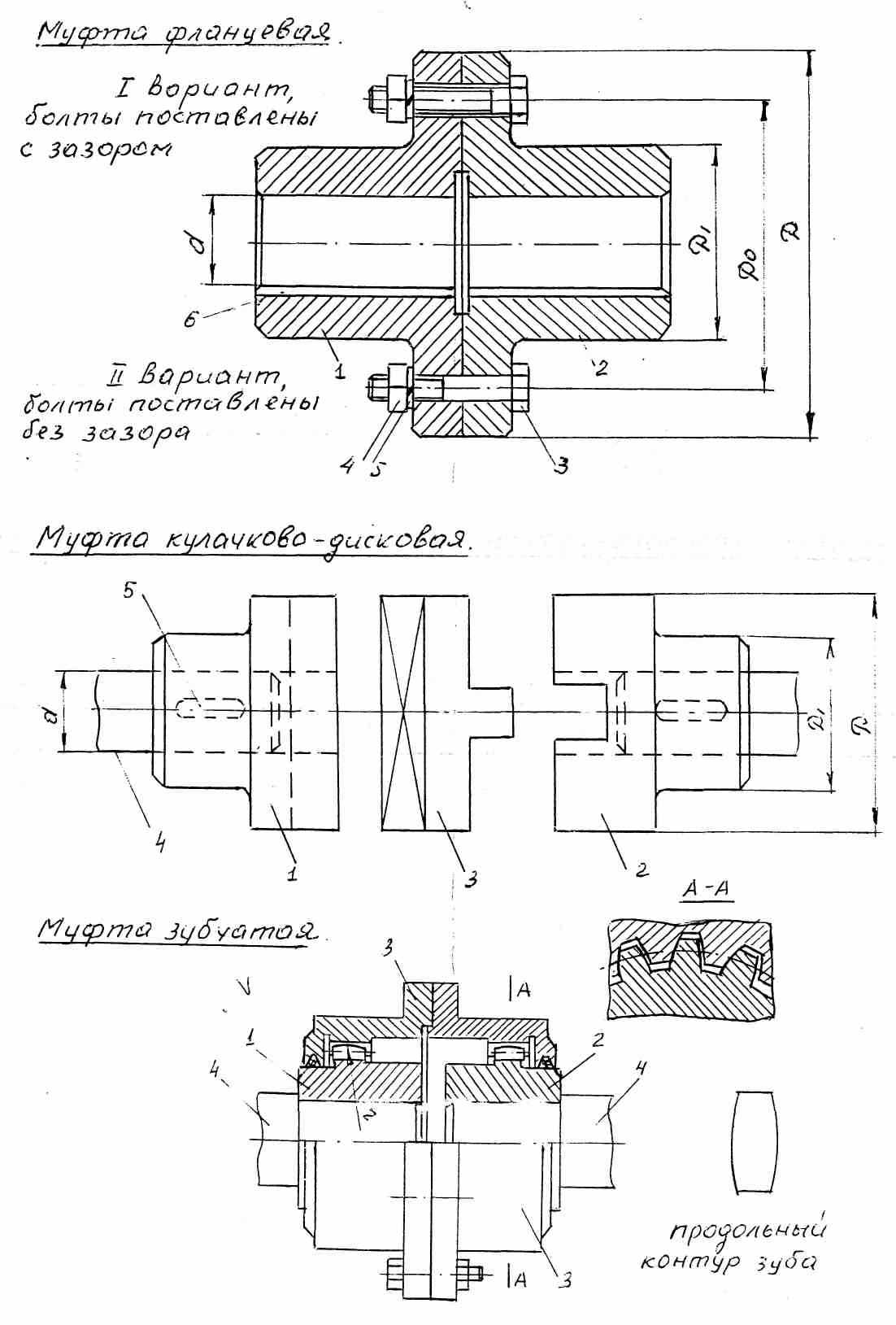
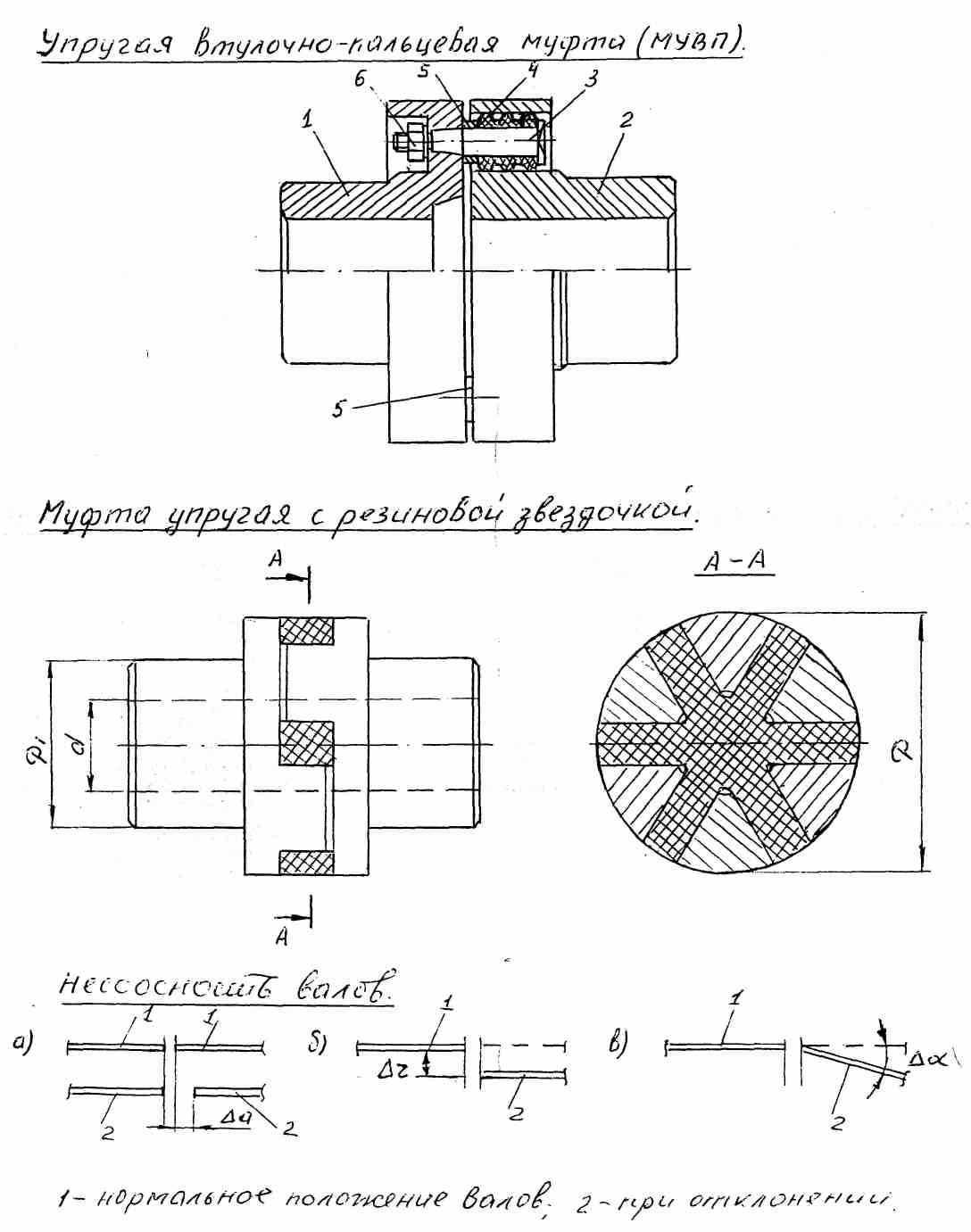
Краткая характеристика муфт.
- Муфта втулочная: Их применяют в легких машинах при диаметрах валов до 60-70мм. Отличаются простотой конструкции и малыми габаритами. При монтаже и демонтаже требуется смещать валы (агрегаты) в осевом направлении. Слабое звено штифты или шлицы. Компенсирующими свойствами не обладает.
- Муфта фланцевая: 1 и 2 – полумуфты; 3 – болт; 4 – гайка; 5 – шайба пружинная; 6 – шпоночная канавка. При I варианте крутящий момент передается силами трения, возникающими в стыке поверхностей полумуфт от затяжки болтов, при II варианте – непосредственно болтами, работающими на срез и смятие. Центровка болтами (II) и выступом (I). Слабое звено – шпонки или шлицы. Муфты с болтами без зазора более распространены, т.к. можно получить меньшие габариты муфт. Их применяют для соединения валов диаметром до 200мм и более. Достоинства – простота конструкции и небольшие габариты. Компенсирующими свойствами не обладает.
- Муфта кулачково-дисковая: 1 и 2 – полумуфты; 3 – промежуточный диск; 4 – вал; 5 – шпонка. На полумуфтах образованы пазы, на диске выступы по взаимно
диаметрам. Выступы располагаются в пазах диск соединяет полумуфты. Муфта компенсирует
r (эксцентриситет):
r до 0,04d;
до 00301. Выступы скользят в пазах, для исключения трения и износа поверхности смазывают. Слабое звено шпонки или изношенные выступы диска.
- Муфта зубчатая: 1 и 2 – полумуфты; 3 – разъемная обойма. На полумуфтах наружные зубья на обойме внутренние. Распространен эвольвентный профиль зубьев. Муфта компенсирует все виды несоосности валов, за счет торцовых и боковых зазоров в зацеплении. Зубья при компенсации несоосности скользят и изнашиваются. Слабое звено - зубья. Зубчатые зацепления смазывают. Зубья имеют бочкообразную форму по длине, при этом приработка и износ меньше. Преимущества – компактность и хорошие компенсирующие свойства. Их применяют для передачи больших «Т».
- Упругая втулочно-пальцевая муфта: 1 и 2 – полумуфты; 3 – палец; 4 – упругий элемент (резина); 5 – шайба; 6 – резьбовое соединение. Благодаря легкости изготовления и замены упругих элементов муфта получила распространение в приводах от электрического двигателя применяют для малых и средних «Т» и диаметров валов до 150мм и Т = 15кН.м. Упругие элементы – гаффрированные резиновые втулки или резиновые кольца трапецеидального сечения. Компенсируют
a ≈ 1÷ 5мм;
r ≈ 0,3 ÷ 0,6мм;
до 10. Слабое звено резина (смятие), палец (изгиб). Все пальцы в муфте нагружены одинаково.
- Муфта упругая с резиновой звездочкой: 1 и 2 – полумуфты с торцовыми выступами; 3 – резиновая звездочка зубья которой расположены между выступами. Зубья звездочки работают на сжатие. При передаче «Т» в каждую сторону работает половина зубьев. Муфта применяется для валов с n = до 3000 ÷ 6000мин-1 и Т = 3 ÷ 120Н .м и d = до 12 ÷ 45мм. Муфта компактна и надежна в работе. Компенсирует
r ≤ 0,2мм;
≥ 10301. Недостаток – смещение валов в осевом направлении при сборке и разборке. Слабое звено – резиновая звездочка – сминается.
^ К лабораторной работе по муфтам:
- Если соосность соединяемых валов в процессе монтажа и эксплуатации строго выдерживается, то допустимо устанавливать жесткие муфты: фланцевые и втулочные.
- Типоразмер муфты выбирают по диаметру вала и по величине расчетного вращающего момента. Тр. = К . Тном ≤ [Т] ГОСТ 20761-80.
- Втулочные муфты проверяют на срез штифтов; муфты со шпоночными и шлицевыми соединениями проверяют по напряжениям смятие
, где
; ^ Т – передаваемый вращающий момент; d – диаметр вала в месте установки шпонки; Асм – площадь смятия Асм = (h – t1) . lp; lp – расчетная длина шпонки; t1 – часть шпонки в теле вала или
. Болты фланцевых муфт – без зазора проверяют в фланцевых муфтах только на срез
.
- Расчет МУВП: Пальцы рассчитывают на изгиб, а резину на σсм.
.
Z – число пальцев;
D1 – диаметр по осям пальцев;
l – длина резиновой втулки;
d1 – диаметр пальца.
- Муфта с резиновой звездочкой. Рассчитывают звездочку по σсм.
.
Z – число зубьев звездочки;
h – длина контакта резины с металлом полумуфты;
D – диаметр звездочки;
d1 – диаметр вала.
6. Кулачково-дисковая муфта. Рассчитывают на σсм выступы диска.
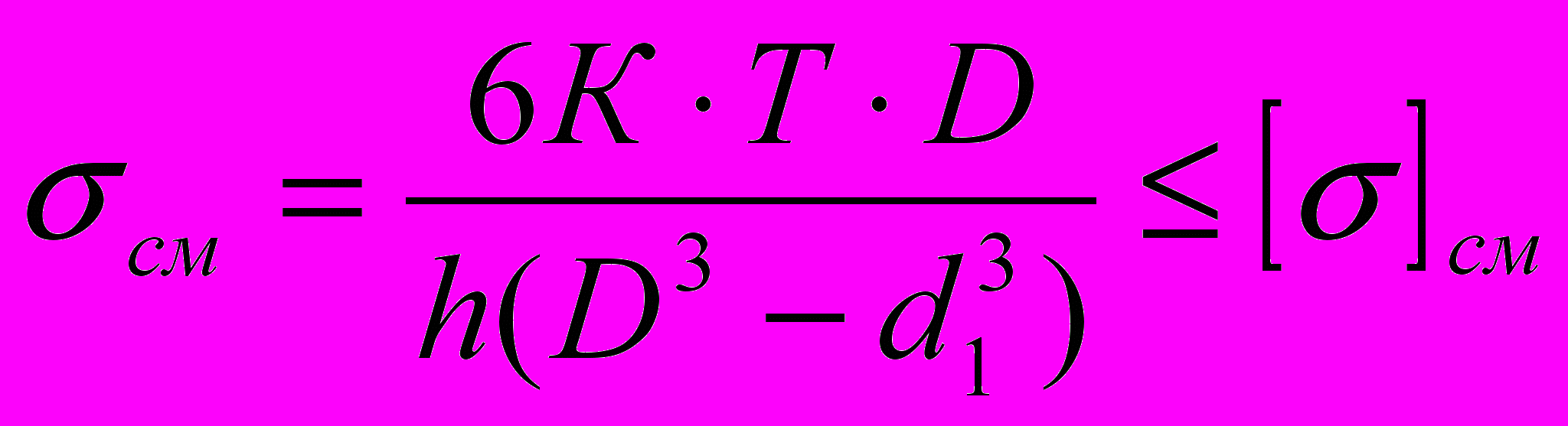
K – коэффициент динамичности режима нагрузки;
h – рабочая высота выступов;
D – диаметр полумуфт (диска);
d1 – диаметр вала;
D/d = 2,5…3.
Муфту изготовляют ст5 (паковка) или 25Л (литье), тяжелонагруженные муфты изготовляют из легированных сталей 15Х; 20Х с цементацией рабочих поверхностей [σсм] = 15÷20МПа.
Лабораторная работа № 5.
«Резьбовые соединения».
Цель работы: Изучение конструкций крепежных деталей, основных типов резьбовых соединений, основных видов стандартных резьб, способов стопорения крепежных деталей.
- Основные крепежные детали.
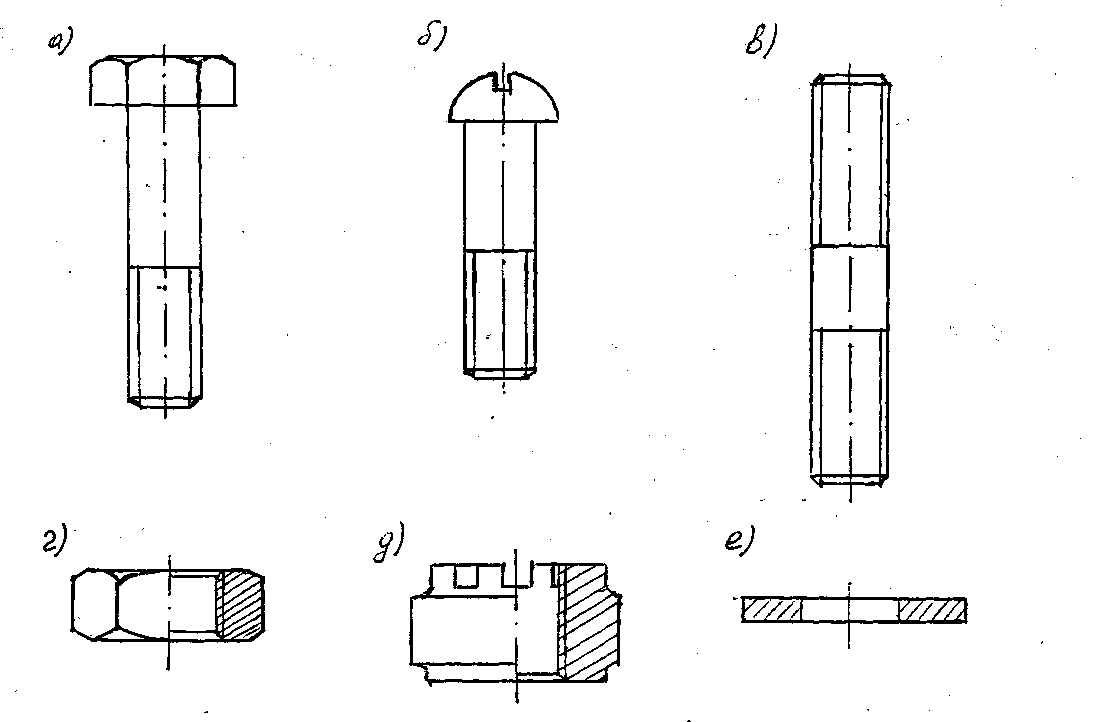
Указать название деталей.
а) ГОСТ
б) ГОСТ
в) ГОСТ
г) ГОСТ
д) ГОСТ
е) ГОСТ
- Основные типы резьбовых соединений
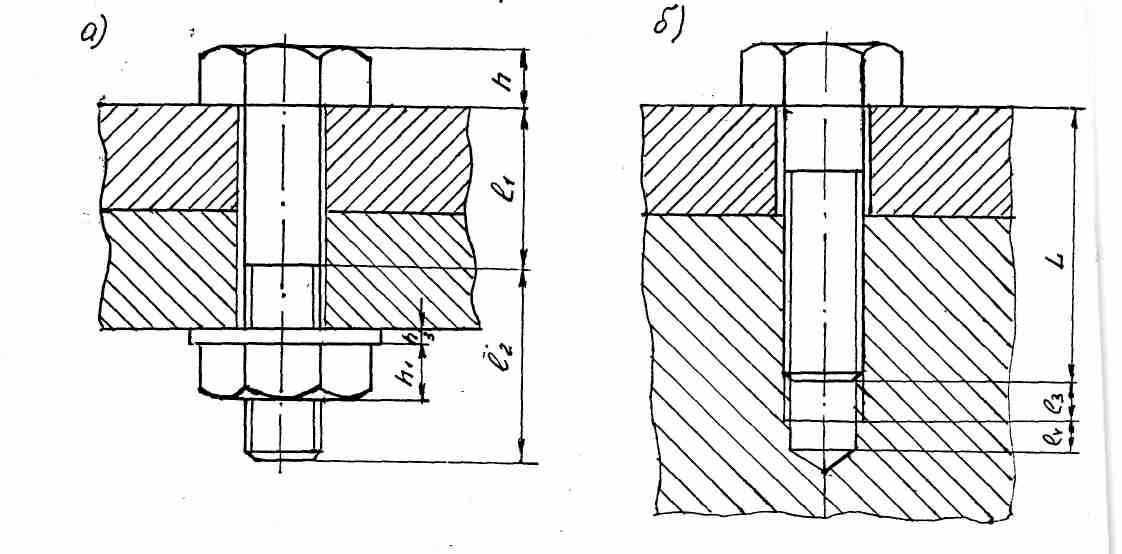
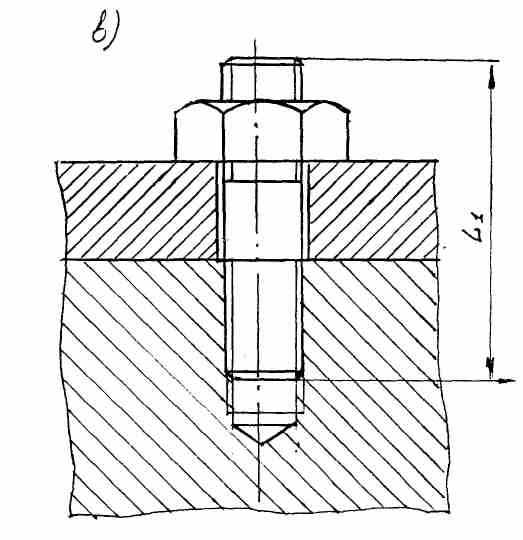
- Указать тип соединения
а)
б)
в)
- Указать наименование размера
h -
h1 -
h3 -
l1 -
l2 -
L -
L1 -
l3 -
l4 -
- Типы распространенных резьб
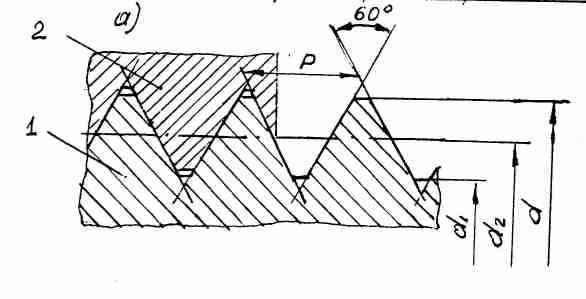
d -
d1 –
d2 –
= 600 –
ρ –
1 –
2 –
Тип резьбы -
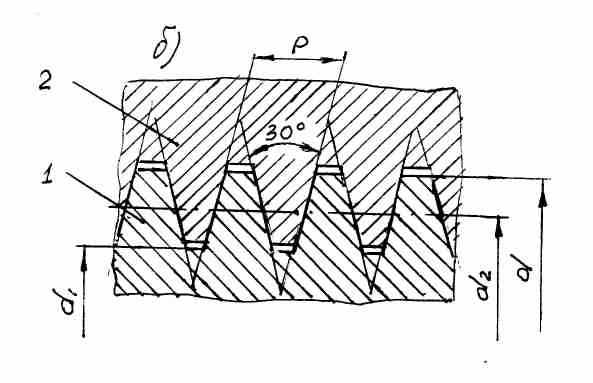
1 –
2 -
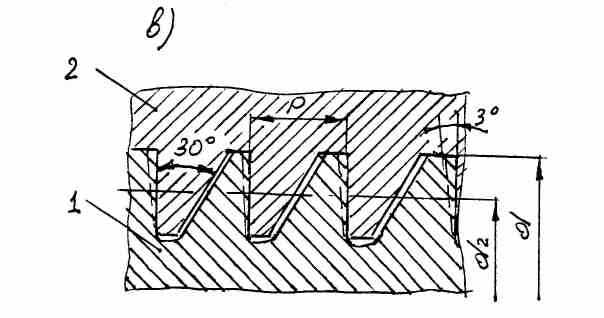
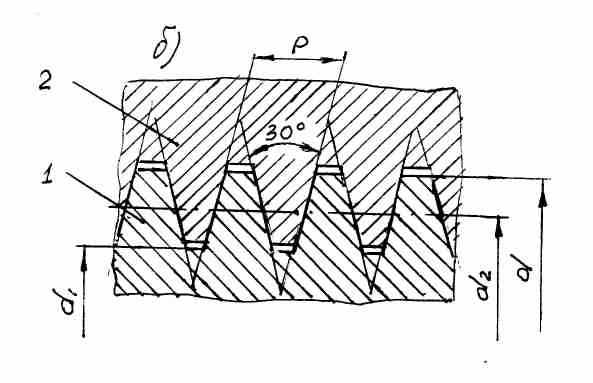
1 –
2 –
30 -
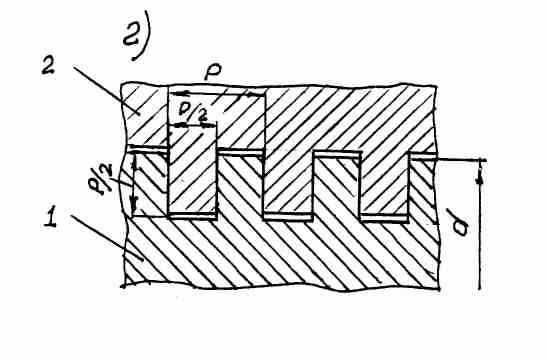
Тип резьбы -
1 –
2 -
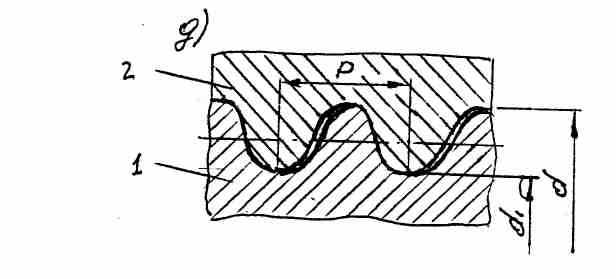
Тип резьбы -
1 –
2 -
- Стопорение крепежных деталей
1. Стопорение созданием дополнительного трения
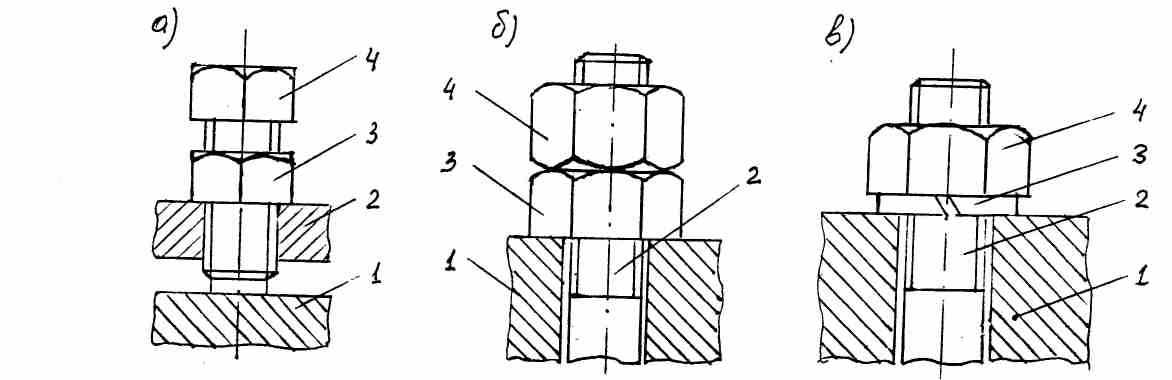
1 - 1 - 1 –
2 - 2 - 2 –
3 - 3 - 3 –
4 - 4 - 4 -
2.Стопорение дополнительными элементами (начертить 2 вида стопо рения):
а) стопорение корончатой б) стопорение гайки
гайки шплинтом; специальной шайбой.
- Ответить на следующие вопросы:
- Что такое резьба (сформулировать).
- Шаг резьбы (сформулировать).
- Назвать основные параметры резьбы.
- Назвать основные крепежные детали.
- Назвать основные типы резьбовых соединений и объяснить их конструктивное исполнение.
- Из представленных типов резьб назвать крепежные и винтовые резьбы.
- Угол профиля резьбы (сформулировать).
- Дать объяснение сущности стопорения созданием дополнительного трения для представленных вариантов.
- Дать объяснение сущности стопорения дополнительными элементами.
- Объяснить сущность стопорения крепежных деталей приваркой и пластическим деформированием.
Лабораторная работа № 6.
«Изучение конструкций фрикционных вариаторов».
Цель работы: Ознакомление с основными типами вариаторов, принципом их работы и определением параметров.
- Лобовой однодисковой вариатор.
Кинематическая схема
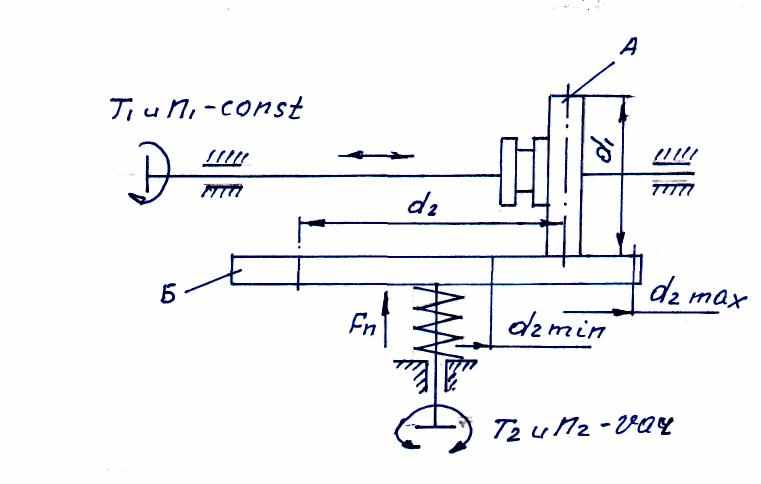
Ведущий ролик ^ А можно перемещать по валу в направлениях, указанных стрелками. При этом передаточное отношение плавно изменяется при изменении рабочего диаметра d2 ведомого диска Б. Если перевести ролик А на левую сторону диска Б, то можно получить изменение направления вращения вала диска – вариатор обладает свойством реверсивности.
В лобовом вариаторе max и min передаточные отношения равны:
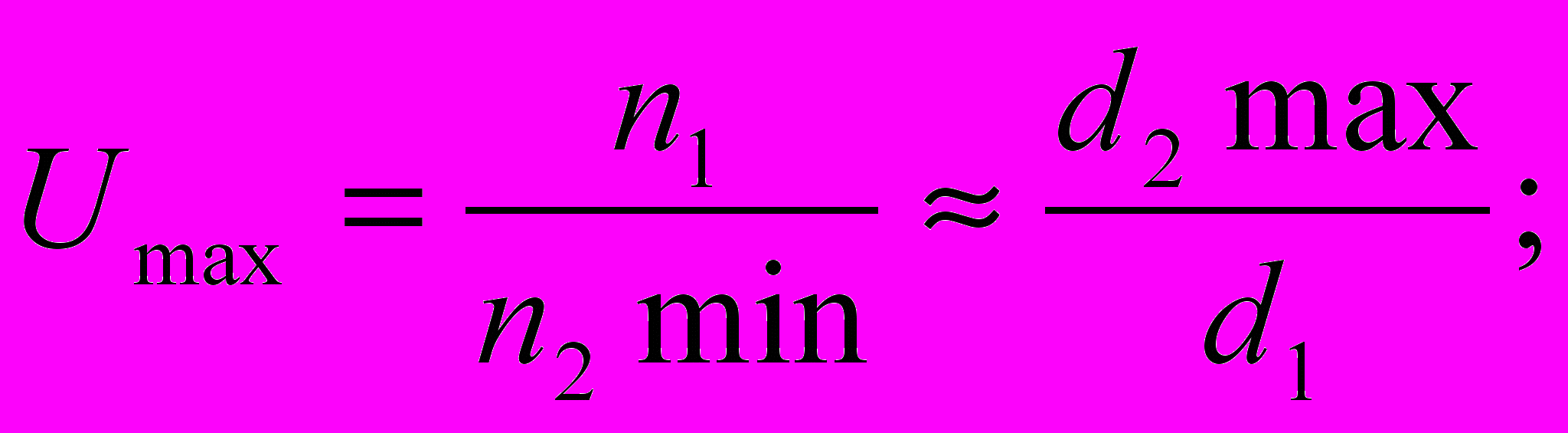
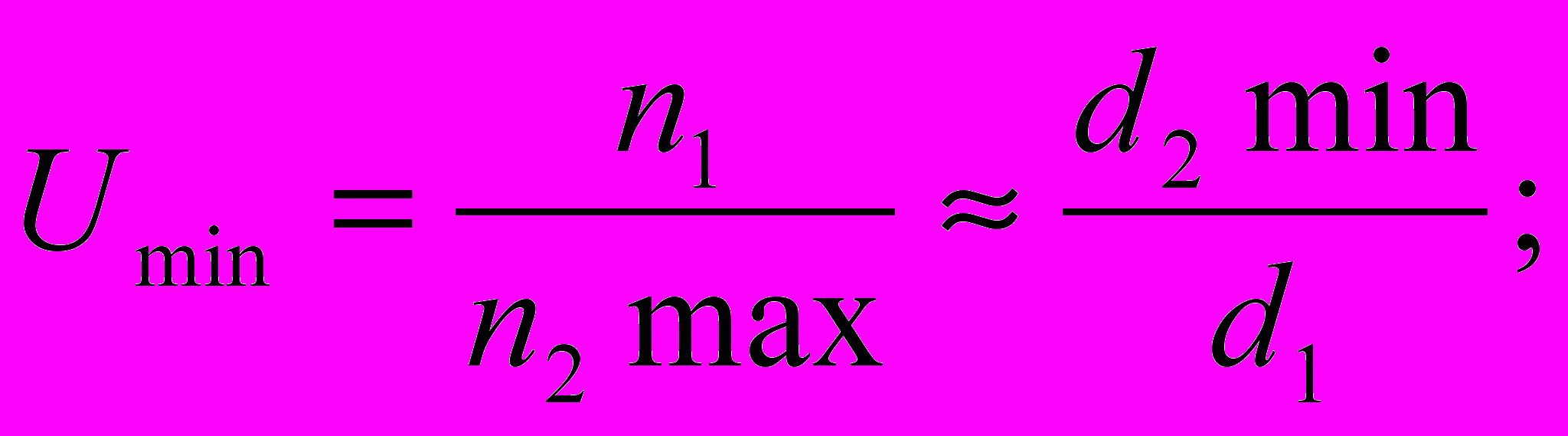
Диапазон регулирования лобового вариатора
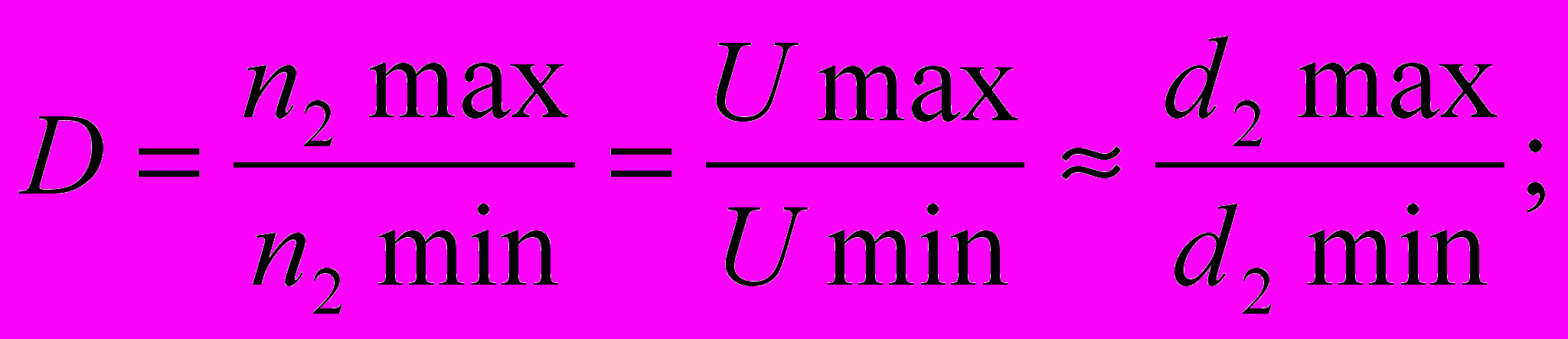
Практически диапазон регулирования ограничивают значениями ^ D ≤ 3. Это объясняется тем, что при малых d2 значительно возрастает скольжение и износ, а КПД понижается. Простота реверсирования обеспечила достаточно широкое применение лобовых вариаторов в маломощных передачах приборов.
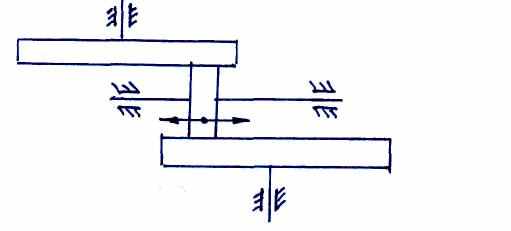
Для повышения диапазона регулирования применяют двухдисковые лобовые вариаторы с промежуточным роликом, получая D = 8….10.
- Вариатор с раздвижными конусами
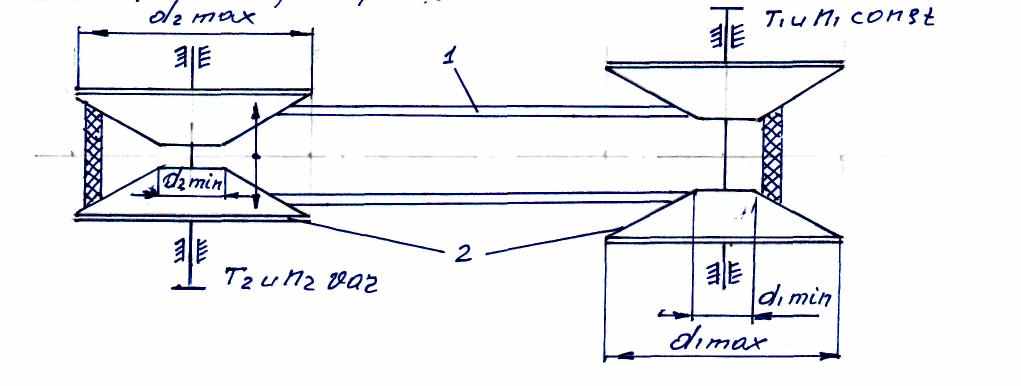
Передающим элементом служит клиновой ремень 1. Конуса 2 раздвигаются и сдвигаются винтовым механизмом управления на одну и ту же величину вдоль осей валов. При этом ремень 1 перемещается на другие рабочие диаметры без изменения своей длины.
Передаточное отношение

Диапазон регулирования
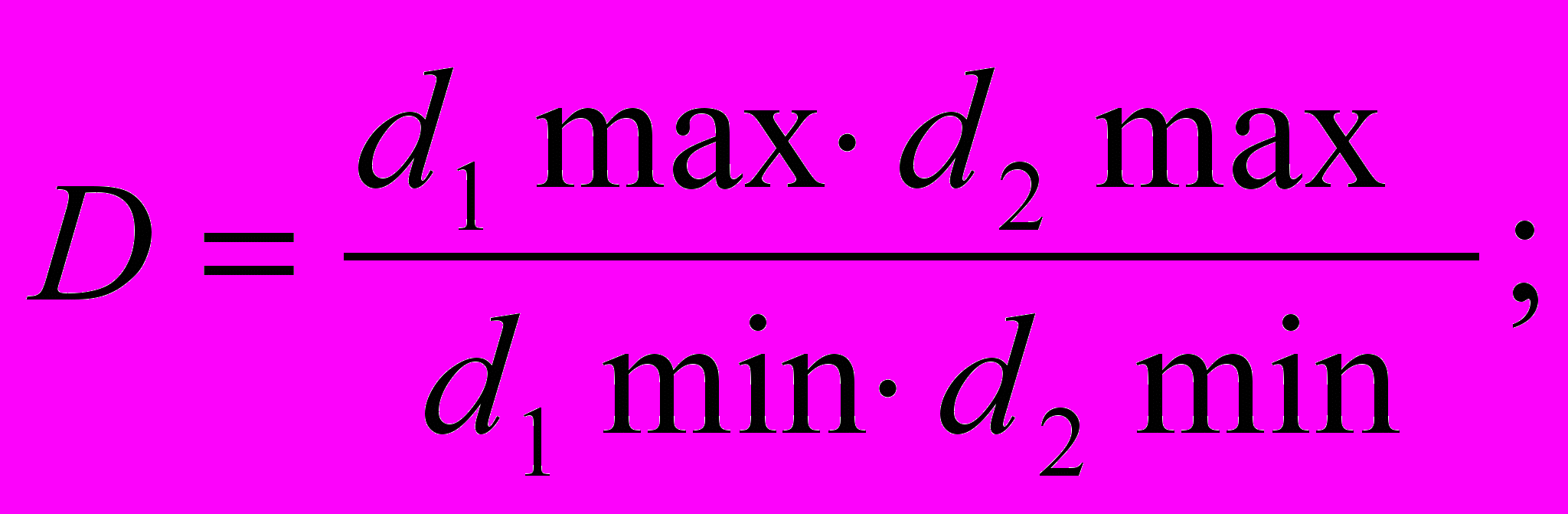
Возможный по условиям конструкции диапазон регулирования зависит от ширины ремня. Стандартные приводные клиновые ремни позволяют получить D до 1,5, а специальные широкие – до 5. Конструкция вариатора с клиновым ремнем достаточно проста и надежна.
- ^ Торовый вариатор.
Кинематическая схема

На ведущем и ведомом валах закреплены соосные катки с торовыми рабочими поверхностями 1 и 2. Между катками зажаты ролики 3. Изменение передаточного отношения достигается поворотом роликов 3 вокруг осей 0. Оси роликов закреплены так, что они всегда располагаются симметрично относительно друг друга. Текущее значение передаточного отношения равно
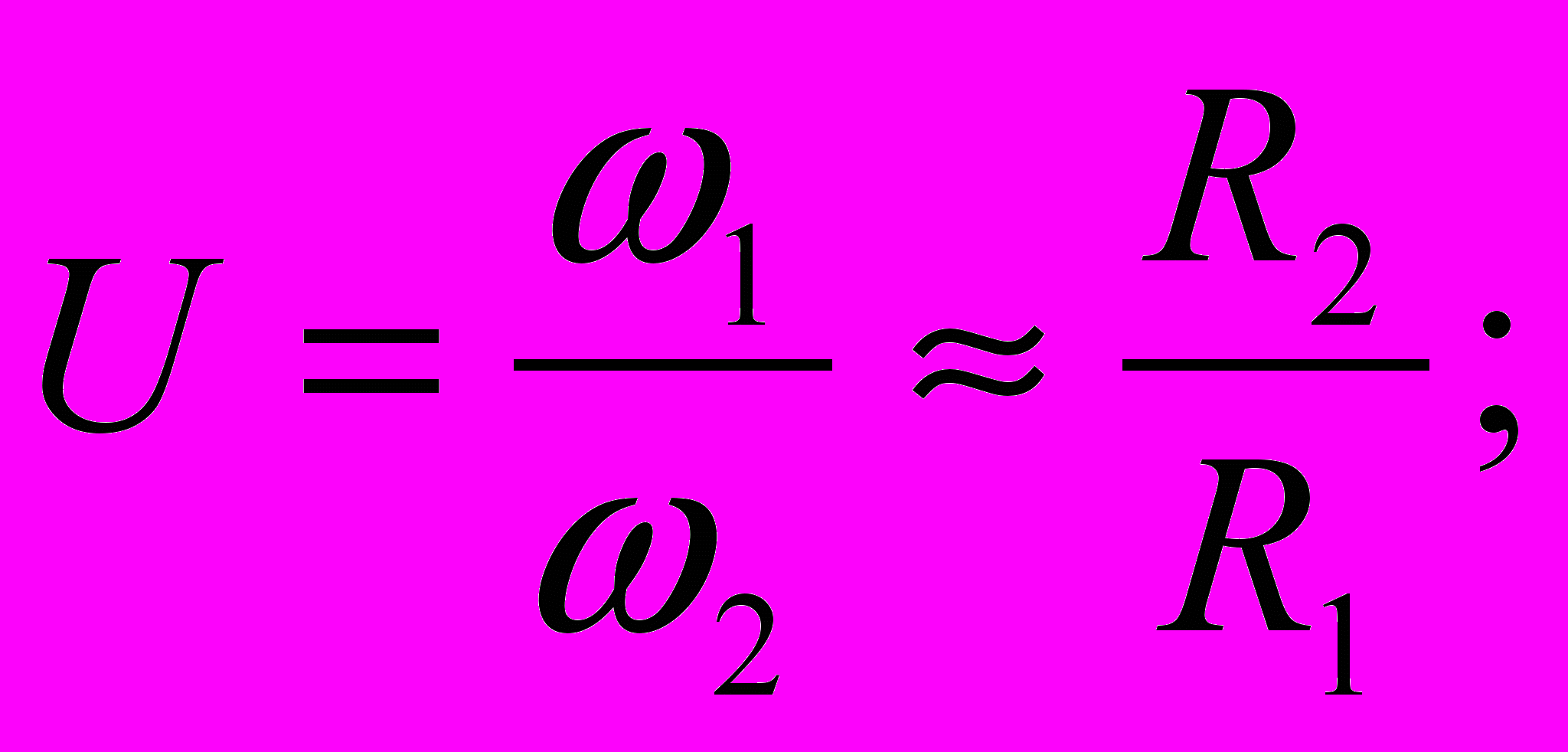
Из всех вариаторов торовые наиболее компактны и совершенны, но имеют сложную конструкцию и требуют высокой точности изготовления. Диапазон регулирования 6….3.
- ^ Дисковой вариатор.
Кинематическая схема.
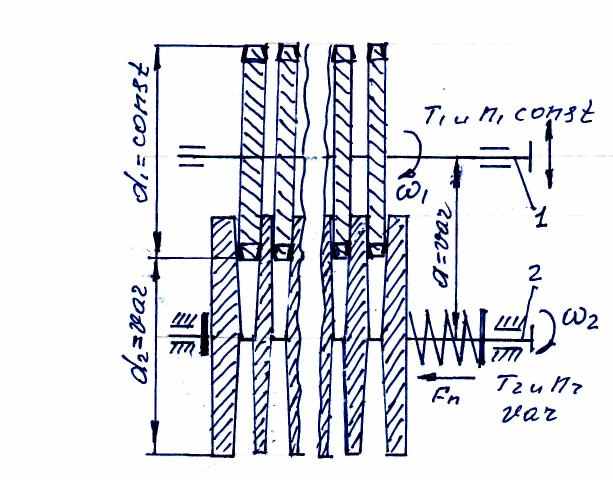
В вариаторе момент передается за счет трения между набором ведущих и ведомых дисков. Изменение передаточного отношения достигается перемещением ведущего вала 1 относительно ведомого вала 2, в направлениях, указанных стрелками. При этом изменяется межосевое расстояние «а» и рабочий диаметр d2. Передаточное отношение
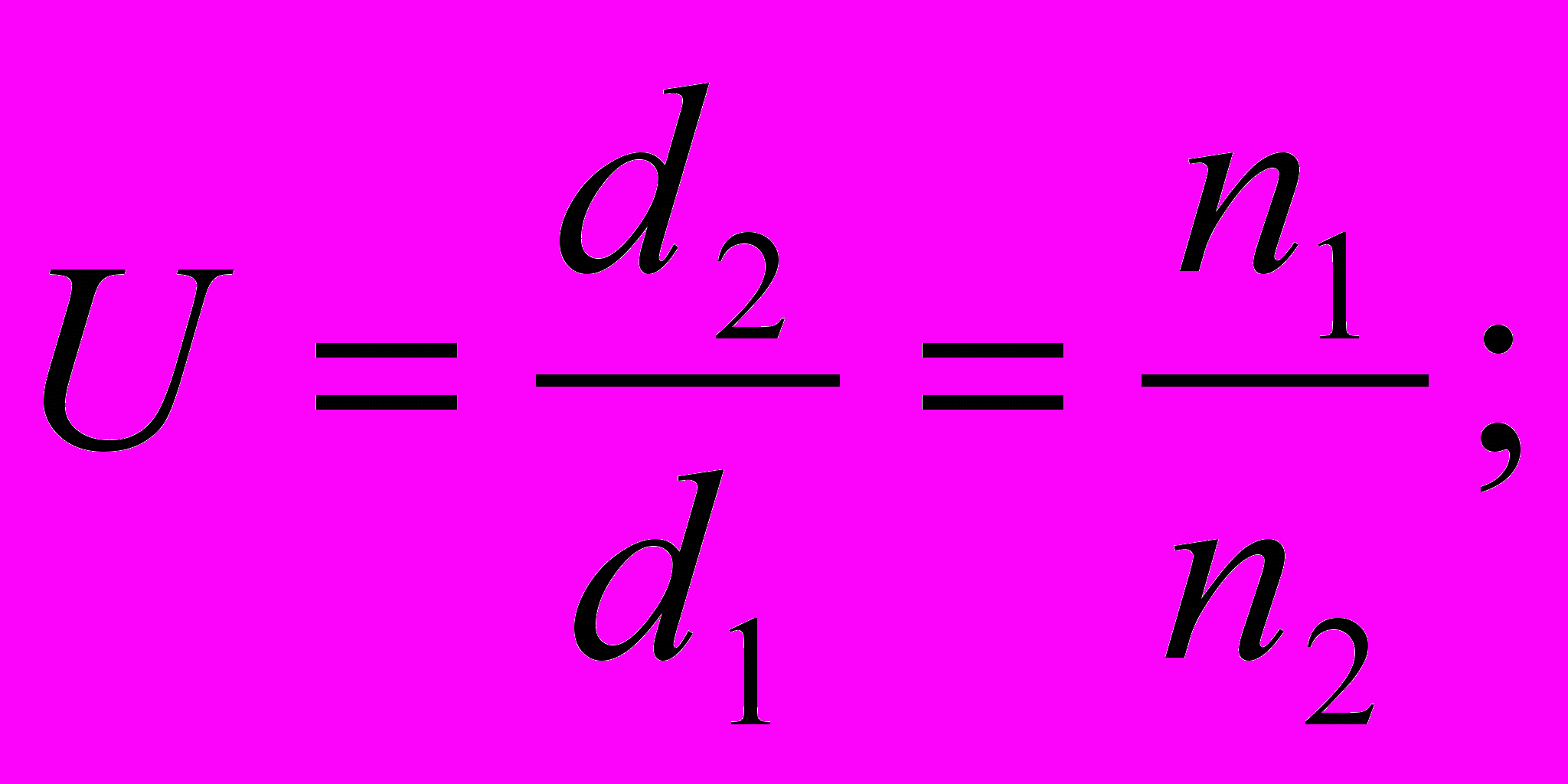
Лабораторно-практическая работа № 7.
«Уплотнения подвижных соединений»
Цель работы: Изучение назначения, конструкций, способов установки, материалов уплотнений подвижных соединений.
Уплотнительные устройства применяют для предохранения от вытекания смазочного материала из подшипниковых узлов, а также для защиты их от попадания извне пыли и влаги.
Тип уплотнения подвижных соединений определяется скоростью и направлением относительного перемещения уплотняемых деталей, видом, температурой и давлением уплотняемой среды, состоянием окружающей среды, допускаемой утечкой жидкости и газа.
- Ориентировочный выбор уплотнения для валов
Окружающая среда | Смазка | Окруж. скорость, м/с | Уплотнительные устройства |
Чистая и сухая | Пластичная | до 5 | Проточки, лабиринты, войлочные кольца. |
Жидкая | > 5 | Проточки, лабиринты, маслоотражательные устройства. | |
Загрязненная | Пластичная | до 5 | Войлочные кольца. |
Жидкая | Войлочные кольца в комбинации с проточками и лабиринтами. | ||
Пластичная и жидкая | до 8 | Резиновые манжеты. | |
Сильно загрязненная и влажная | Пластичная | до 5 | Лабиринты. |
Пластичная и жидкая | от 5 до 9 | Сложные лабиринты, кожаные уплотнения. | |
Жидкая | любые скорости | Сложные лабиринты комбинированного типа. |
- Сальниковые войлочные кольца.
Сальниковые кольца из грубошерстного войлока, изготовляемого по ГОСТ 6418-81 и полугрубошерстного – по ГОСТ 6308-71, предназначены для уплотнения валов, работающих при окружных скоростях ≤ 2 м/с, из тонкошерстного войлока по ГОСТ 288-72 предназначены для уплотнения валов, работающих при окружных скоростях ≤ 5 м/с.
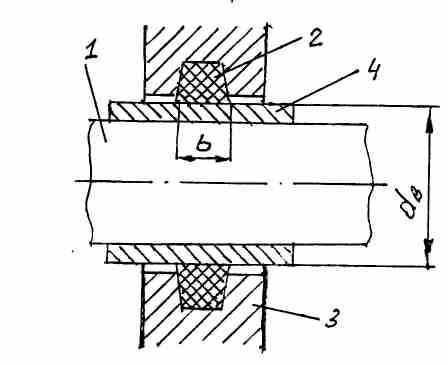
- при работе сальниковых колец в среде, вызывающей повышенный износ валов, рекомендуется устанавливать на вал защитные втулки (рис. 1).
- при установке в подвижные сальники кольца можно сдваивать (рис. 2).
Рис. 1
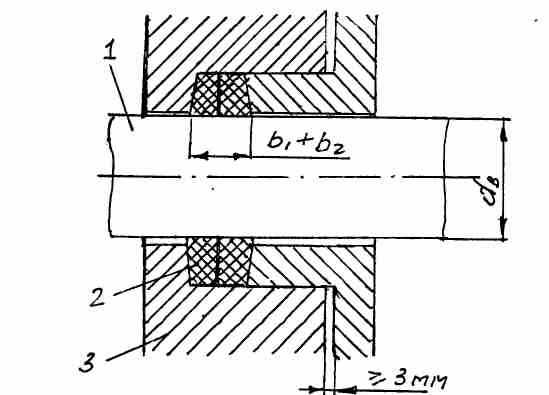
1 – вал с диаметром dB,
2 – сальниковое кольцо,
3 – корпус,
4 – втулка.
Рис. 2
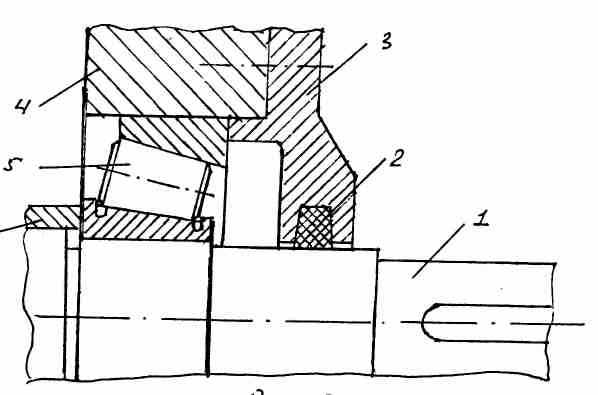
Рис. 3
На рис.3 показана установка сальникового кольца в теле крышки подшипникового узла. 1 – вал, 2 – сальниковое кольцо, 3 – крышка подшипникового узла, 4 – корпус редуктора, 5 – роликовый подшипник, 6 – кольцо.
- Манжетные уплотнения.
Манжетные уплотнения широко применяют в современном машиностроении. Манжеты изготовляют 2-х типов I-однокромочные (рис 4.), II-однокромочные с пыльником. Манжеты I типа предназначены для предотвращения вытекания уплотняемой среды. Манжеты II типа (рис. 5) предназначены для предотвращения вытекания уплотняемой среды и защиты от проникновения пыли.
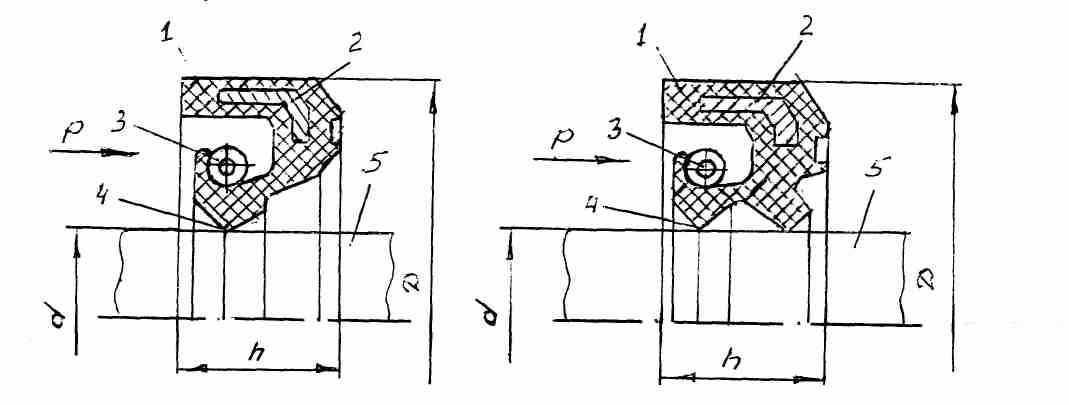
Рис. 4 Рис. 5
1 – резина; 2 – каркас; 3 – пружина; 4 – рабочая кромка; 5 – вал; d - диаметр вала; D – диаметр манжеты; h – ширина манжеты; Р – уплотняемая среда.
Резиновые армированные однокромочные манжеты с пружиной предназначены для уплотнения валов. Манжеты работают в минеральных маслах, воде, дизельном топливе при избыточном давлении до 0,05МПа, скорости вращения вала до 20м/с и температуре от – 60 до + 1700С в зависимости от группы резины.
Манжету обычно устанавливают рабочей кромкой внутрь корпуса (рис. 6), так чтобы обеспечить к ней хороший доступ масла. Каркас придает корпусу манжеты жесткость. Браслетная пружина стягивает уплотняющую часть манжеты, вследствие чего рабочая кромка расширяется до 0,4 ÷ 0,6мм, плотно охватывая поверхность вала.
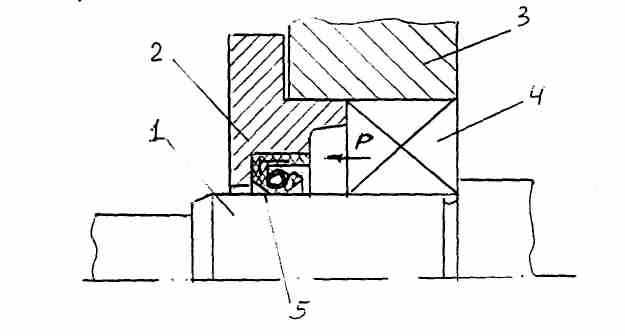
1 – вал;
2 – крышка подшипникового гнезда;
3 – корпус редуктора;
4 – подшипник качения;
5 – манжета;
Р – уплотняемая среда.
- Мазеудерживающие кольца.
При окружных скоростях зубчатых колес ≤ 4м/с предусматривают смазку подшипников пластичными смазочными материалами (консталины, солидолы), конструкция подшипникового узла при этом предусматривает наличие мазеудерживающего кольца, со стороны внутренней полости редуктора исключающего вытекание смазочного материала (рис. 7)).
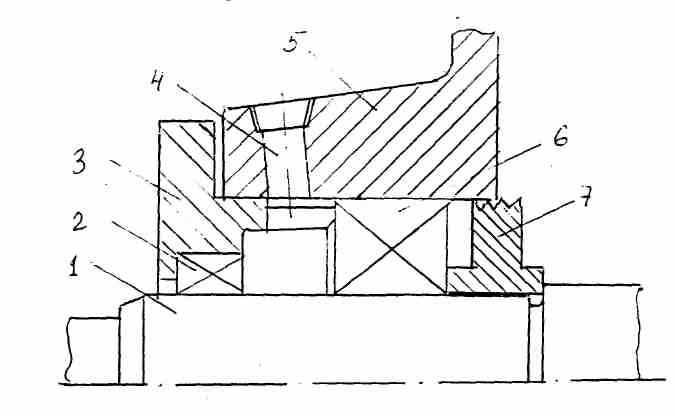
1 – вал; 2 – манжета; 3 – крышка подшипникового узла; 4 - отверстие для нагнетания пластичной смазки; 5- корпус редуктора; 6 – подшипник качения; 7 – мазеудерживающее кольцо.
Лабораторно-практическая работа № 8.