Тезисы докладов
Вид материала | Тезисы |
- Тезисы докладов, 3726.96kb.
- Тезисы докладов, 4952.24kb.
- Правила оформления тезисов докладов Тезисы докладов предоставляются в электронном виде, 22.59kb.
- «Симпозиум по ядерной химии высоких энергий», 1692.86kb.
- Требования к тезисам докладов, 16.83kb.
- Тезисы докладов научно-практической, 6653.64kb.
- Тезисы докладов 1 Межвузовская научно -практическая конференция студентов и молодых, 100.64kb.
- Тезисы докладов и заявки на участие, 104.97kb.
- Тезисы докладов, принятые Оргкомитетом для опубликования в Материалах форума, 788.61kb.
- Тезисы докладов, принятые Оргкомитетом для опубликования в Материалах форума, 1066kb.
Дезинтеграторная технология. Тезисы докладов VIII Всесоюзного семинара. Киев 1 – 3 октября 1991 г. (1991 год, 208 страниц, 600 экземпляров).
Советская механохимическая ассоциация
Научно-производственное объединение “Дезинтегратор”
Киевский технологический институт
пищевой промышленности
Минвуз УССР
ДЕЗИНТЕГРАТОРНАЯ
ТЕХНОЛОГИЯ
Тезисы докладов
VIII Всесоюзного семинара
1 – 3 октября 1991 г.
Киев 1991
603.08
---------
Д 28
На Восьмом Всесоюзном семинаре по дезинтеграторной технологии, проводимом в Киеве на базе Технологического института пищевой промышленности, как и на предыдущих, представлены доклады большинства ведущих советских школ измельчения, механоактивации, механохимии. Хотя тематика докладов очень разнообразна – разработка и эксплуатация измельчительного оборудования, исследование процессов измельчения, механизмов механоактивации различных материалов, механохимических процессов, значительная часть работ выполнена с использованием дезинтеграторного оборудования, что оправдывает название семинара.
Качественный и количественный рост работ свидетельствует о возрастающем интересе к данной области. Надеемся, что в обновляющихся экономических условиях существенно ускорится внедрение наиболее удачных разработок в практику.
Оргкомитет
ISBN 5 – 7763 – 0951 – 4 © Научно-производственное
объединение “Дезинтегратор”, 1991
УДК 621.926.47 Л. С. Ванаселья, Б. М. Кипнис
НПО “Дезинтегратор”, г. Таллинн
^ ОБ ОБЩИХ ПРИНЦИПАХ И ПЕРСПЕКТИВНЫХ НАПРАВЛЕНИЯ
ПРИМЕНЕНИЯ ДЕЗИНТЕГРАТОРНОЙ ТЕХНОЛОГИИ (стр. 3 – 5)
В докладе рассматриваются общие принципы применения дезинтеграторов в различных технологиях исходя из особенностей воздействия дезинтеграторной обработки на твёрдые и жидкие системы. Рассмотрены также конструктивные разновидности дезинтеграторов, конкретные примеры их использования в технологиях измельчения, механоактивации, механохимии материалов, гомогенизации систем.
К основным принципам применения относятся требования к исходным материалам: обычно размер частиц от 1 … 2 до 20 … 30 мм, твёрдость по шкале Мооса не выше 6 … 7, для жидких систем ограничение по вязкости – менее 10 Па/с. Обработка частиц твёрдых материалов обычно осуществляется 3 … 8 ударами со скоростью 100 … 300 м/с, для жидких систем – сдвигово-распыляющее воздействие на тонкие плёнки с высокими градиентами сдвига до 500 … 1000 м/с на 1 мм толщины слоя (обычно толщина 50 … 300 мкм), время нахождения материала в зоне воздействия менее 0,01 … 0,1 с. Всё это определяет оптимальное место дезинтегратора в технологических линиях измельчения: после установок для предварительного дробления (молотковых, щековых, конусно-инерционных, ножевых дробилок) в большинстве технологий – перед сепарационными устройствами, мельницами тонкого помола (вибро- и валковыми мельницами, струйными и планетарными мельницами), поскольку тонина получаемых в дезинтеграторе продуктов редко достигает нескольких микрометров, а в большинстве случаев для неорганических материалов – 10 … 50 мкм, для полимеров и пластичных металлических материалов до нескольких сотен микрометров.
С точки зрения механоактивации и механохимии полученные в дезинтеграторе порошки обычно имеют меньшие нарушения структуры (аморфизация, микроискажения решётки), характеризуются меньшим разогревом вещества, но более высоким выходом свободных радикалов по сравнению с порошками аналогичной дисперсности, полученными в шаровой и вибромельницах. Важна также возможность дезинтеграторной обработки веществ в инертных и активных газовых средах с предварительным нагревом или охлаждением вещества, использованием вещества роторов в качестве катализаторов или микродобавок (продуктами износа)или микродобавоквещества роторов в качестве катализаторовнием вещества. вободных радикалов по сравнению с порошками аналогичной. Всё это позволяет наряду с изменением интенсивности механических воздействий варьировать физико-химическими свойствами получаемых продуктов. При хранении обработанных веществ и систем уровень механоактивации обычно снижается, хотя в отдельных реакционных системах технологические свойства при хранении улучшаются (например, вследствие завершения реакций гидролиза оксирановых циклов в эпоксиолиномерах).
В некоторых технологиях (для порошковых красок, порошковой металлургии) полезной является более близкая к правильным многогранникам форма частиц, в других – сохранение частиц определённой формы (селективное разрушение дендритов Fe2O3, применяемой в качестве носителя магнитной записи), удаление (с металлических гранул и порошков, полученных распылением) хрупкой оксидной плёнки путём варьирования режимов обработки и зоны подачи материалов, получение заданного гранулометрического распределения частиц. Возможно также насыщение систем газом (при биоочистке сточных вод, для окисления ненасыщенных жиров в производстве лакокрасочных материалов), транспортировка на несколько метров обработанных материалов создаваемым в дезинтеграторе воздушным потоком, сохранение аморфной структуры металлических материалов и т.д.
Исходя из практического опыта особенно перспективно применение дезинтеграторов в следующих отраслях:
измельчение, механоактивация, поверхностная механомодификация, механохимия легкоплавких органических и биологических веществ и полимеров и систем их включающих;
приготовление, активация, реактивация гетерогенных катализаторов, активация инициаторов, сорбентов;
измельчение отходов композиционных полимерных материалов;
измельчение, активация реагентов для химических, биохимических, нефтехимических процессов, компонентов, используемых в порошковой металлургии, приготовлении керамик, ферромагнетиков, полимерных материалов;
одновременное измельчение, механоактивация и гомогенизация компонентов порошковых гранулированных и жидких систем для производства строительных и тампонажных материалов, в том числе и восстановление вяжущих свойств лежалых цементов.
В период с 1974 по 1990 г. разработано и внедрено в различных производствах более 70 промышленных дезинтеграторных технологий, изготовлено свыше 800 промышленных (производительностью от 0,05 до 80 т/ч) и более 350 исследовательских дезинтеграторных установок.
УДК 621.926.47 Т. А. Мюрк, Л. Ф. Моллер
НПО “Дезинтегратор”, г. Таллинн
^ ИССЛЕДОВАТЕЛЬСКОЕ ДЕЗИНТЕГРАТОРНОЕ ОБОРУДОВАНИЕ НПО “ДЕЗИНТЕГРАТОР”
(стр. 5 – 6)
Известно, что порошки, получаемые в различных измельчающих аппаратах, имеют различия в геометрии и физико-химических свойствах частиц. Существенную роль в этом играет механизм разрушения частиц. В дезинтеграторе преобладает механизм ударного разрушения, при этом частицы материала или их осколки получают в суммарном направлении движения несколько мощных ударов, а энергия ударов с каждым последующим ударом возрастает. Эффективность использования дезинтегратора значительно возрастает, когда наряду с основной целью – получением ювенальной поверхности удаётся использовать и другие явления, наблюдаемые в дезинтеграторе в процессе обработки материала. Эти явления (механическая активация материала, близкое к идеальному смешению на микроуровне, влияние повышенной температуры и т.д.) могут способствовать получению требуемого технологического результата в последующих процессах. При таком количестве факторов влияния трудно предсказать, каким могло бы стать их оптимальное соотношение для решения конкретных задач. Изучить эту проблему позволяет исследовательское дезинтеграторное оборудование, выпускаемое в НПО "Дезинтегратор". Здесь можно назвать настольные установки (базовая модель “Дези-11”), установки для фундаментальных исследований (базовая модель “Дези-12”) и универсальные установки, имеющие промышленный аналог (базовая модель “Дези-15”). Все исследовательские дезинтеграторы позволяют варьировать число ударов, их энергию, конфигурацию рабочих элементов, конструкционный материал рабочих элементов, количество материала в рабочей зоне и т.д. Можно получать многокомпонентные смеси, обрабатывать жидкости и приготовлять различные суспензии. Имеются варианты моделей, позволяющие проводить измельчение в контролируемых средах (вакуум, защитный газ).
В целом опыт показывает, что для достижения конкретной технологической цели необходима дезинтеграторная установка с вполне определёнными параметрами, определяемыми экспериментально.
УДК 621.926.47 И. А. Ридали
НПО “Дезинтегратор”, г. Таллинн
ЛИНИИ ДЛЯ ВЫПУСКА МИКРОПОРОШКОВ ТОНИНОЙ ОТ 10 ДО 100 МКМ (стр. 6 – 8)
НПО ”Дезинтегратор”выпускает безопасные для окружающей среды комплекты опытных образцов оборудования, обеспечивающие микроизмельчение с использованием в качестве основных элементов линии дезинтегратора и классификатора. Линии, где применяется микроклассификатор, сблокированный непосредственно с дезинтегратором, намного упрощаются и повышается надёжность их работы благодаря отсутствию лишних транспортных звеньев. Оба варианта линии гарантируют заданную тонину готового продукта с одновременным лимитированием процентного содержания частиц конкретного размера. Есть возможность оперативной регулировки тонины готового продукта.
Доклад сопровождается показом слайдов, иллюстрирующих разработанные технологические схемы и основные виды оборудования, в том числе:
1. Схема линии, в которой использована система полного прохода воздуха через аспирационную систему, дезинтеграторы типа “Дези-11”, “Дези-12”, “Дези-15” и “Дези-18”, с которыми микроклассификатор объединён в один агрегат.
1.1. Лабораторная линия микроизмельчения производительностью до 20 кг/ч на базе дезинтегратора типа “Дези-12”, работает в лаборатории НПО “Дезинтегратор”, позволяет плавно регулировать тонину готового продукта, например известняка, в пределах 20 … 100 мкм.
1.2. Лабораторная линия малой производительности (200 кг/ч) на базе дезинтегратора “Дези-15”.
Первая линия работает в лаборатории Таллиннского технического университета. Она позволяет плавно регулировать тонину готового продукта в пределах 20 … 100 мкм. Одна из модификаций этой линии позволяет получать тонину 10 ... 50 мкм.
1.3. Линия микроизмельчения со вредней производительностью до 3 т/ч, на базе дезинтегратора “Дези-18” для опытной базы НПО “Дезинтегратор”. Тонина продукта регулируется в пределах 15 … 100 мкм.
Перечисленные линии позволяют наряду с тонким продуктом выпускать и отдельные фракции, например, фракцию 50 … 100 мкм и др., в зависимости от требований к готовому продукту.
2. Схема линии с контуром циркулирования воздуха, где лишь относительно малая часть используемого воздуха выходит из основной системы аспирации. Дезинтегратор типа “Дези-21” с классификатором, объединённым в один агрегат, производительностью 5 … 15 т/ч, позволяет плавно регулировать тонину готового продукта в пределах 30 … 100 мкм. Линия работает на Таллиннской водоочистительной станции и обеспечивает при помоле негашеной извести, доломита и известняка d95 = 40 мкм.
^ Техническая характеристика дезинтегратора “Дези-21М5”, входящего в состав линии
Показатели | При помоле CaO | При помоле CaCO3 |
Производительность, т/ч Тонина помола, мкм: d95 d75 Удельный расход электроэнергии, кВт ч/т: нетто брутто | 7 40 20 15 30 | 7 40 20 30 45 |
3. Схема линии с контуром циркулирования воздуха, где лишь относительно малая часть используемого воздуха выходит из основной системы аспирации, а основным элементом линии является микроклассификатор. Производительность линии 0,5 ... 3 т/ч, возможна плавная регулировка тонины готового продукта в пределах 10 ... 50 мкм и работа без ор. алая часть используемого воздуха выходит из основной системы аспирации, а основным элементом линии являетизмельчителя.
Линия будет установлена в 1991 г. на предприятии “Сааре доломийт” (Эстония) для выпуска микропорошков. Аналогичная схема на базе крупных классификаторов позволяет достигать производительности 90 т/ч с плавным регулированием тонины в пределах 50 … 250 мкм.
УДК 621.926.47 М. Ю. Колобов, В. Б. Лапшин, З. А. Шарова, В. Н. Блиничев
Ивановский химико-технологический институт
ДЕЗИНТЕГРАТОР (стр. 8 – 9)
Одним из основных направлений развития техники измельчения является разработка новых компактных малоэнергоёмких и надёжных измельчителей интенсивного действия.
Разработан дезинтегратор (А. С. СССР № 1572649, В 02С 13/22) с плоскими ударными элементами переменной длины, которая возрастает от центра дезинтегратора к периферии.
Увеличение длины лопаток в 2 – 2,5 раза в каждом последующем ряду ударных элементов позволяет повышать скорость нагружения материала по мере уменьшения размера частиц в процессе их измельчения до скоростей, достаточных для их эффективного дальнейшего измельчения. Увеличение числа лопаток в 2 – 2,5 раза в каждом последующем ряду ударных элементов позволяет устранить проскок частиц измельчаемого материала и уменьшить длину свободного пробега частиц. Такое конструктивное выполнение дезинтегратора позволяет повысить эффективность процесса измельчения, снизить энергозатраты.
Разработанный нами дезинтегратор внедрён на Ивановском заводе искусственных кож в технологии получения тентовых материалов.
Высокая интенсивность обработки, достигаемая в дезинтеграторе, в сочетании с механической активацией смешиваемых ингредиентов позволяет увеличить степень наполнения ПВХ-композиций за счёт введения функциональных добавок, которые дополнительно улучшают перетирку и гомогенизируют получаемую смесь.
Экономический эффект от внедрения дезинтегратора образуется за счёт уменьшения трудовых и сырьевых затрат и составляет 190,1 тыс. руб. в год.
УДК 621.926 Н. М. Смирнов, В. Н. Блиничев
Ивановский химико-технологический институт
РАЗРАБОТКА СЕПАРАЦИОННОЙ ЦЕНТРОБЕЖНОЙ ПРОТИВОТОЧНОЙ МЕЛЬНИЦЫ ДЕЗИНТЕГРАТОРНОГО ТИПА (стр. 9 – 10)
В настоящее время в качестве крупнотоннажного помольного оборудования широко используются дезинтеграторы, мельницы ударно-отражательного действия, струйные мельницы и т.п. Причём каждый тип оборудования имеет свои достоинства и недостатки.
В последнее время разработан ряд конструкций центробежных противоточных мельниц, в которых исходный материал разгоняется центробежными силами и разрушается во встречных потоках. Тем самым реализуются положительные эффекты дезинтеграторной технологии. Недостатком центробежных противоточных мельниц является то, что готовый продукт получается с широким гранулометрическим составом.
Для решения указанной задачи нами была разработана, изготовлена и исследована операционная центробежная противоточная мельница (см. рисунок) для измельчения различных материалов средней твёрдости (например, известняка, глины и т.д.).
Мельница содержит два корпуса, соединённых между собой зоной помола. В каждом корпусе имеются роторы, равнонаклонённые относительно друг друга.
Мельница работает следующим образом. Измельчённый материал через загрузочные патрубки подаётся на роторы, разгоняется и выбрасывается в зону помола, где частицы измельчённого материала нагружаются в пересекающихся потоках. Недоизмельчённые частицы, продолжая движение, попадают в каналы возврата и затем в загрузочные патрубки. Частицы измельчённого материала вместе с транспортирующим воздухом отводятся через выгрузочный патрубок.
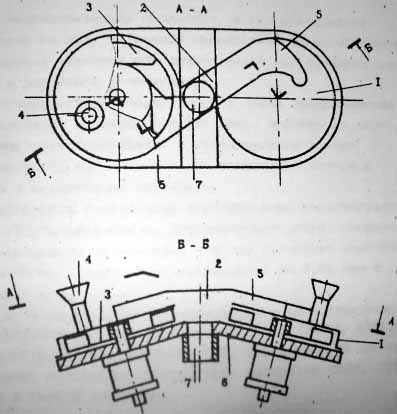
^ Сепарационная центробежная противоточная мельница:
1 – корпус, 2 – зона измельчения, 3 – ротор, 4 – загрузочный патрубок,
5 – канал возврата, 6 – плита, 7 – выгрузочный патрубок
Преимущества представленной мельницы перед центробежными противоточными заключается в том, что крупные частицы, которые получались в процессе разрушения или были в исходном материале, но не разрушались, отделяются за счёт центробежных сил от основного потока и направляются в загрузочный патрубок вместе с исходными материалами на доизмельчивание.
За счёт того, что центробежная противоточная мельница оснащена встроенным сепаратором, в мельнице данной конструкции можно получить готовый продукт более узкого гранулометрического состава с размером частиц 90% менее 40 … 60 мкм при намоле железа 0,01 … 0,001%.
УДК 621.926.47 Е. А. Лукьянов, В. И. Кукушкин, С. С. Черников
Институт химической физики АН СССР,
п. Черноголовка
ГИДРОДИНАМИЧЕСКИЙ ДИСПЕРГАТОР ГД-100 И ЕГО ПРИМЕНЕНИЕ В ТЕХНОЛОГИЧЕСКИХ ПРОЦЕССАХ (стр. 11)
Разработана конструкция гидродинамического диспергатора-дезинтегратора, принцип действия которого основан на интенсивном гидродинамическом воздействии на дезинтегрируемый материал за счёт больших градиентов скоростей, напряжений сдвига и наложения на течение материала воздействий колебаний разных частот и амплитуд. Будут также представлены экспериментальные данные по дезинтеграции различных материалов (с целью получения высокодисперсных систем в жидких средах и приготовления сверхтонких эмульсий) и по смешению с целью получения однородных систем.
В ИХФ (п. Черноголовка) гидродинамический дезинтегратор разработан в трёх модификациях с диаметром рабочих дисков 50, 100, 150 мм и объёмом рабочих камер 300 … 500, 1500, 3000 см3 с внутренней и внешней циркуляцией.
Разработанный гидродинамический дезинтегратор опробован при получении фотоэмульсий, эмульсий замасливания, а также при получении различных материалов в дисперсном состоянии (целлюлоза, хитин, графит, бентонит, кадмий, кожа, сажа, слюда, маргарин).
Разработанные устройства защищены тремя авторскими свидетельствами и успешно используются в лабораториях института и в ряде организаций. Будут приведены примеры применения диспергатора ГД-100 в различных технологических процессах.
УДК 621.926.47 В. И. Кукушкин, Л. Н. Милорадов, В. М. Тимин, В. К. Энман
Институт химической физики АН СССР,
п. Черноголовка
ЭКСТРУЗИОННЫЕ ДЕЗИНТЕГРАТОРЫ В НАУЧНЫХ ИССЛЕДОВАНИЯХ И НАУКОЁМКИХ ТЕХНОЛОГИЯХ (стр. 11 – 12)
Процесс экструзионного дезинтегрирования является ключевой операцией многих технологических процессов, в которых влияние развитой поверхности за счёт получения сверхтонких эмульсий (суспензий) имеет решающее значение для производства необходимого конечного продукта с заданными свойствами.
Способ дезинтегрирования, реализуемый в новых экструзионных дезинтеграторах высокого давления (до 350 мПа), основан на скоростном течении эмульсии (суспензии) в узком щелевом зазоре 0,1 … 0,001 мм, где возникает значительное напряжение сдвига и соударение частиц с неподвижным экраном.
В ИХФ (п. Черноголовка) разработаны экструзионные дезинтеграторы высокого давления (ВД) лабораторного, крупнолабораторного, полупромышленного и промышленного назначения, которые позволяют получить размеры частиц (капель) в эмульсиях (суспензиях) до 0,01 мкм с полидисперсностью около 20%.
Разработанные экструзионные дезинтеграторы прошли апробацию при получении бесклеточных препаратов, кормового белка, пищевых веществ, кровозаменителей, фотоэмульсии ЦОК, пенорезины из латексов, различных дисперсных материалов (ферролака, пигментов сажи, графита и т.д.), а также в генной инженерии.
Разработанные устройства защищены 25 авторскими свидетельствами на изобретения и успешно используются в 40 организациях различных министерств и ведомств.
УДК 549.758.1+541.18.053 В. И. Козлов, В. Ф. Редькин, Ф. Р. Кребель
Красноярский политехнический институт
РОТОРНЫЕ ШАРОВЫЕ МЕЛЬНИЦЫ-АКТИВАТОРЫ (стр. 12 – 15)
Для тонкого измельчения, интенсивной механической активации твёрдых материалов в сухом состоянии или в суспензиях предлагаются аппараты двух типов: ЦМА (или МА) и ЭМА. Поиск их принципиальных схем ориентирован условием: должна быть минимальной хаотичность в движении мелющих шаров, поскольку случайные удары с малым импульсом не производят полезной работы, а избыточные импульсы быстро разрушают мелющий агрегат.
В табл. 1 приведены технические данные трёх лабораторных моделей, а табл. 2 – характеристики некоторых обработанных материалов.
Таблица 1
Технические данные лабораторных моделей
Модель | Мощность электродвигателя, кВт | Масса мельницы, кг | ^ Габаритные размеры, мм |
ЦМА-02 МА-09 ЭМА-100 | 1,1 1,1 0,55 | 47,0 44,5 25,7 | 520х240х320 459х232х354 345х250х465 |
Примечание: Производительность всех лабораторных моделей равна 0,5 … 5,0 кг/ч
Таблица 2
Характеристики некоторых материалов
Материал | Твёрдость по Моосу | ^ Качество помола | Качество механической активации |
Графит | 1 … 1,2 | 36% – 1 мкм | Устраняется аморфная база скрытнокристаллического графита |
^ Гидроксид алюминия | 2 ... 2,5 | - | Рентгеноаморфность при первой обработке – 65%, при повторных обработках – 100 % |
^ Фосфоритная руда | 5 | 92% - 0,44 мкм | До 60% лимонно-растворимой пятиокиси фосфора, до 100% при повторных обработках |
^ Кварцевый песок | 7 | 85% - 1 мкм | Снижение ширины пиков на рентгенограммах в 1,5 … 2 раза, высоты – в 2,5 … 3 раза |
Найден ряд конструктивных решений, способствующих применению аппаратов в научных исследованиях и заводских экспресс-анализах. Например, в процессе эксплуатации аппаратов исходный материал подаётся непрерывно, а готовый продукт может отгружаться в стакан-накопитель, в любую другую ёмкость или поступать в приёмное устройство механического или пневматического транспорта. Разборка и сборка мелющего агрегата с целью его очистки от остатков предыдущей пробы материала не требуют применения инструмента. При этом фиксация взаимного расположения элементов мелющего агрегата осуществляется при закрытии звукоизолирующего кожуха. Постоянный тепловой режим обеспечивается жидкостным охлаждением корпуса.
В настоящее время лабораторные аппараты поставляются организациям по индивидуальным заказам и могут быть модернизированы по техническим заданиям заказчиков. Представляется возможным обеспечение заданной газовой среды в рабочем пространстве; снижение степени загрязнения продукта материалом от намола шаров и деталей путём применения особоизносостойких сплавов и неметаллов; дальнейшее снижение размеров и массы лабораторной мельницы или увеличение её размеров и производительности до 200 ... 300 кг/ч и более.
Технические данные к проекту опытно-промышленного образца ЭМА-900 (табл. 3) получены при стендовых испытаниях макета и расчётах. Ожидаемая производительность относится к эталону – кварцевому песку с исходной крупностью 0,2 … 1,0 мм и удельной поверхностью продукта 500 … 550 м2/кг.
Таблица 3
Технические данные опытно-промышленного образца ЭМА-90
^ Мощность электродвигателя, кВт | Масса мельницы, кг | Габаритные размеры, мм | Производительность, т/ч |
75 | 4812 | 1720х1240х2140 | 1,0 … 1,5 |
В табл. 4 показана зависимость удельных затрат энергии W при измельчении выбранного эталона от удельной поверхности F продукта в интервале высоких значений F. С погрешностью менее 5% строка экспериментальных данных аппроксимируется линейной функцией: W = 0,158F – 29,6. Известная нелинейность наблюдалась при более низких значениях F, которые в табл. 4 не приведены.
Таблица 4
Затраты энергии в зависимости от качества измельчения
^ Удельная поверхность продукта F, м2/кг | 468 | 542 | 634 | 695 | 771 | 857 |
Удельные затраты энергии W, кВт ч/т экспериментальные расчётные | 46,5 44,3 | 54,0 56,0 | 70,0 70,6 | 80,9 80,2 | 93,0 92,2 | 108 106 |
В создании опытных моделей мельниц, их испытаниях и анализе продуктов активации участвовали инженеры В. Ф. Редькин, А. В. Попов, С. А. Козырев, Ф. Р. Кребель, к.х.н. Н. П. Коцупало, В. П. Исупов и др. Координация этих работ и научные консультации проведены член-корр. АН СССР В. В. Болдыревым.