Тезисы докладов
Вид материала | Тезисы |
- Тезисы докладов, 3726.96kb.
- Тезисы докладов, 4952.24kb.
- Правила оформления тезисов докладов Тезисы докладов предоставляются в электронном виде, 22.59kb.
- «Симпозиум по ядерной химии высоких энергий», 1692.86kb.
- Требования к тезисам докладов, 16.83kb.
- Тезисы докладов научно-практической, 6653.64kb.
- Тезисы докладов 1 Межвузовская научно -практическая конференция студентов и молодых, 100.64kb.
- Тезисы докладов и заявки на участие, 104.97kb.
- Тезисы докладов, принятые Оргкомитетом для опубликования в Материалах форума, 788.61kb.
- Тезисы докладов, принятые Оргкомитетом для опубликования в Материалах форума, 1066kb.
Объединённый институт геологии, геофизики,
и минеарологии СО АН СССР, г. Новосибирск
^ О НОВЫХ ВОЗМОЖНОСТЯХ ЦЕНТРОБЕЖНЫХ МЕЛЬНИЦ ПРИ ТОНКОМ ИЗМЕЛЬЧЕНИИ РУД
(стр. 15 – 16)
1. Среди требований, предъявляемых технологией к тонкоизмельчённым веществам при первичной обработке минерального сырья, важное место занимает получение продукта с заданным спектром крупности, в частности класса -70+20 мкм и с наименьшим по возможности содержанием фракции 20 мкм, которая трудно поддаётся обогащению традиционными методами.
2. В качестве одного из эффективных путей решения данной задачи можно рассматривать использование мельниц повышенной энергонапряжённости применительно к рудам, подвергнутым предварительному измельчению в шаровых и стержневых мельницах до крупности 1 … 2 мм и менее.
Воздействие увеличенных импульсов движения возникает при центробежном разрушении материала: W = F х v, где F – сила действия шара на материал; v – скорость приложения силы. Например, использование центробежной мельницы периодического действия М - 3 при измельчении оловянной руды позволило сократить по сравнению с шаровой мельницей выход шламов крупностью менее 20 мкм с 30,1% до 23,4% и снизить извлечение олова из них (показатель возможных потерь) с 15,8% до 12,3%. В центробежном измельчителе непрерывного действия типа ЦКИ выход шлама сократился почти в 2 раза по сравнению с шаровым измельчителем и составил 16,7% при снижении извлечении олова из него до 7,7%.
Достигнутый эффект объясняется не только возросшими механическими воздействиями, но и непрерывной классификацией материала и выносом тонких фракций из зоны измельчения. Преимущества аппарата состоят также в сокращении продолжительности измельчения.
3. В настоящее время СКБ горно-обогатительных машин Минмета СССР разработаны центробежные мельницы-активаторы близкого к ЦКИ принципа действия производительностью до 2 т/ч и более, что открывает пути промышленной реализации. Но в применении к указанной задаче могут быть и другие измельчители, в частности дезинтеграторы, ударно-отражающие и струйные мельницы, изучение которых представляет большой практический интерес.
4. Имеющийся опыт показывает, что в силу измененности дефектного состояния поверхности минералов, измельченных в мельницах повышенной энергонапряжённости, их физико-химические свойства также изменяются. Поэтому технологические режимы флотационного, магнитного, электростатического и других методов обогащения руд должны разрабатываться с учётом новой дефектности, а иногда и структурных преобразований.
УДК 621.926:662.73 А. Н. Владыкин, В. А. Федотовских, Э. В. Лебанов, А. Ф. Моторин
Экспериментальный многопрофильный научно-
технический кооператив “КРИПТОН”, г. Свердловск
^ РАЗРАБОТКА ПРАКТИЧЕСКИХ ТЕХНОЛОГИЙ С ИСПОЛЬЗОВАНИЕМ КОМПЛЕКСНЫХ ТЕХНОЛОГИЧЕСКИХ УСТАНОВОК ИЗМЕЛЬЧЕНИЯ И СЕПАРАЦИИ ТОНКИХ ПОРОШКОВ
(стр. 17 – 18)
Комплексные технологические установки основаны на использовании высокоскоростных центробежных измельчителей, работающих в замкнутом герметичном контуре с технологическими аппаратами, реализующими механические процессы (например, классификацию частиц, осаждение), химические (окисление, гидрирование, выщелачивание, растворение) и др.
В последнее время с применением установок решён ряд вопросов практической технологии:
1. Изготовление высокоэффективных постоянных магнитов из сплавов редкоземельных металлов: самарий – кобальт и ниодим – железо – бор. Новая технология позволила повысить значение остаточной индукции до 0,95 Тл, при этом увеличить коэрцитивную силу намагниченности до 636,6 кА/м, а магнитную энергию до 20х105 ГсхЭ, что значительно выше показателей по ГОСТ 2155.59-76.
2. Эффективная технология переработки катодных осадков из электролизеров в производстве циркония, обеспечивающая реализацию концепции безотходности производства.
3. Технология переработки вредных токсичных металлов: висмута, теллура, селена, кремния, теллуридов до получения тонких неокисленных порошков в герметичном объёме.
4. Технология измельчения золотосодержащих пород, позволяющая измельчать золото в виде песчинок и пластин.
5. Технология измельчения обожженной керамики 22 ХС, используемой в электронной промышленнности.
6. Технология измельчения и подготовки порошков ионообменных смол КУ-8, ЭДЭ-10П, АВ-17-8 в производстве ионообменных мембран.
7. Технология получения порошковых глиняных смесей в производстве кирпича, плитки и черепицы.
В конструкции установок, являющихся разработками нового поколения, введены усовершенствования, обеспечивающие надёжность работы и повышение ресурса:
роторы установок после статической и динамической балансировок проходят инерционные испытания на скоростных стендах;
с целью повышения износостойкости поверхности роторов упрочнены взрывом и защищены хромалмазным покрытием;
по-новому решены вопросы конструктивного устройства и смазки высокоскоростных опор ротора;
использованы высокоскоростные клиноременные передачи оригинальной разработки, что позволит реализовать линейные скорости ремня более 40 м/с;
для герметизации использованы магнитно-жидкостные уплотнения, обеспечивающие проведение процессов с применением инертных газов.
УДК 621.928 О. В. Сизова, В. Е. Мизонов, О. А. Песнохорова
Ивановский энергетический институт
ОБ ОДНОМ НАПРАВЛЕНИИ УЛУЧШЕНИЯ ХАРАКТЕРИСТИК СЕПАРИРУЮЩЕГО ОБОРУДОВАНИЯ (стр. 18 – 19)
В настоящее время, по-видимому, считается очевидным преимущественное использование для тонкого измельчения замкнутых циклов. Особенно это актуально для дезинтеграторной технологии, ориентированной на получение тонких и особо тонких порошков. Однако положительные эффекты от использования замкнутого цикла в полной мере проявляется при достаточно высокой эффективности мельничного классификатора, достижение которой при требуемых весьма тонких границах разделения и высокой производительности является сложной технической задачей.
В докладе рассмотрены основные положения и выполнены расчётно-экспериментальные оценки эффективности достаточно нового направления в совершенствовании процесса – оптимального управления потоком несущего газа. Его научную основу составляет постановка и решение ряда вариационных задач по определению распределений скоростей газа, обеспечивающих стационарные значения некоторых функционалов, характеризующих поведение движущихся в газе частиц. Решение подобной задачи в осесимметричной постановке позволило выявить оптимальное распределение по радиусу вихревого потока радиальных и окружных скоростей газа, причём показано, что оптимальное распределение по радиусу вихревого потока радиальных и распределение по радиусу вихревого потока радиальных и окружных скоростей газа, причём показано, что оптимальное раокружных скоростей отличается от естественно устанавливающегося квазипотенциального. Рассмотрены различные варианты аппаратурного обеспечения оптимального распределения, основанные на вращении боковых стенок, а также струйном управлении потоком. Приведены результаты экспериментальной проверки оптимальных воздействий.
УДК 621.926.47+621.928.6+621.635 Я. В. Тамм
Таллиннский технический университет
ОБ АЭРОДИНАМИЧЕСКИХ ИСПЫТАНИЯХ И НАЛАДКЕ ДЕЗИНТЕГРАТОРНЫХ СИСТЕМ С ВНЕШНИМ ВОЗДУШНЫМ СЕПАРАТОРОМ (стр. 19 – ??)
Дезинтеграторные комплексы с внешним сепаратором в общем случае достаточно сложные аэродинамические системы, включающие кроме дезинтегратора ещё и вентиляторы, циклоны, фильтры, дроссели, трубопроводы и др. Определение рабочих характеристик таких комплексов аналитическим способом практически невозможно и очевидно целесообразно. Этим объясняются трудности при наладке сложных размольных комплексов.
В таком случае оказывается целесообразным определить аэродинамические характеристики составных частей комплекса отдельно опытным путём и применить эти результаты при составлении общей аэродинамической модели. Эта работа заключается в следующем:
1. Аэродинамическое испытание дезинтегратора и вентилятора (или вентиляторов). Их работа характеризуется такими аэродинамическими параметрами, как производительность Q, полным PV, статическим PSV и динамическим PDV давлением, потребляемой мощностью N.
30, 45 мин. Прочность гранул из такой шихты в 5 ... 6 раз выше, чем из рядовой шихты.
^ Результаты экспериментов по механической активации шихты ДМЗ
Условия опыта | Влажность гранул, % | Прочность гранул, кг/гранулу | |
влажных | подсушенных | ||
1. Неактивированная шихта 2. Активированная шихта 3. Шихта, выдержанная после активации, мин: 15 30 45 4. Активированный известняк, шихта без активации | 9,6 8,2 7,0 7,6 7,7 6,7 7,6 6,3 7,4 | 0,22 0,22 0,17 0,13 0,15 0,17 0,14 0,19 0,14 | 1,20 0,70 1,10 3,90 4,60 6,06 5,64 4,98 3,38 |
Проведён также эксперимент по активации не всей шихты ДМЗ (Джезказганского медеплавильного завода), а одного из её компонентов – известняка. Полученные гранулы характеризуются повышенной прочностью по сравнению с гранулами из неактивированной шихты, но их прочность ниже, чем гранул, полученных при активации шихты и её выдержке перед гранулированием.
Таким образом, показано положительное влияние предварительной механической активации шихты ДМЗ в дезинтеграторе на прочность получаемых из ней гранул.
УДК 662.62 В. А. Грузных, А. Г. Пройдаков, А. В. Полубенцев
Институт нефте- и углехимического синтеза
при Иркутском госуниверситет, г. Иркутск
СПЕКТРОСКОПИЯ ЭПР МЕХАНООБРАБОТАННЫХ УГЛЕЙ (стр. 119)
Процессы механодеструкции, происходящие при диспергировании углей, обуславливают создание на вновь образующейся поверхности различных по своей природе активных центров. Их количество может определять степень активации углей, что будет приводить к изменению реакционной способности механообработанных углей в различных химических процессах.
Целью данного исследования являлось изучение механообработанных углей методом спектроскопии ЭПР. На основании определения концентрации парамагнитных центров (ПМЦ) в углях, обработанных в механоактивирующих устройствах различного типа (дезинтеграторы, дисмембраторы, мельницы планетарного типа, шаровые центробежные и вибрационные мельницы и др.), проведена оценка их эффективности как активаторов угля. Получены и обсуждаются результаты по изменению концентрации ПМЦ при обработке углей в различных условиях (влияние растворителей, времени и интенсивности обработки, температуры и др.). Проведено сопоставление параметров концентрации ПМЦ и дисперсности (удельной поверхности) механообработанных углей. Обсуждаются вопросы, связанные с возможностями использования результатов спектроскопии ЭПР в качестве критерия оценки активности механообработанных углей в различных химических процессах, в частности при их ожижении.
УДК 552.57 Л. В. Гирина, Н. А. Преображенский, В. П. Стригуцкий
Институт физико-органической химии и углехимии
АН УССР, г. Донецк
СТЕПЕНЬ РАЗУПОРЯДОЧЕНИЯ СТРУКТУРЫ БУРОГО УГЛЯ ПРИ МЕХАНИЧЕСКИХ ВОЗДЕЙСТВИЯХ РАЗЛИЧНОГО ВИДА (стр. 120 – 121)
Степень структурных преобразований бурого угля Александрийского месторождения, деструктированного механическими воздействиями высокой интенсивности различной природы, оценивали с помощью физических методов: спектроскопия электронного парамагнитного резонанса (ЭПР) рентгеноструктурного анализа (РСА).
Для свежедеструктированных образцов при любом виде механического воздействия установлено небольшое снижение концентрации парамагнитных центров (ПМЦ, NS) относительно исходного угля (NSИ.У.): 0,87 … 0,89 (см. таблицу).
^ Изменение структурных параметров бурого угля при различных видах механического воздействия
Вид механического воздействия преимущественно | Параметры | ||||
ЭПР (РЭ 1308) | ^ РСА (ДРОН-3) | ||||
![]() отн. ед. | ![]() отн. ед. | d002, ангстрем | В, мрад | LC, ангстрем | |
Исходный уголь | 1 | 1 | 3,75 | 96 | 19 |
Свободный удар (ДИ, V = 210 м/с) | 0,87 | 0,89 | 3,73 | 114 | 16 |
Стеснённый удар со сдвигом (ПМ, V = 5 мин) | 0,89 | 0,55 | 3,82 | 131 | 14 |
Примечание: ДИ – дезинтегратор (ДУ-16Б); ПМ – планетарная мельница (АИР-0,015),
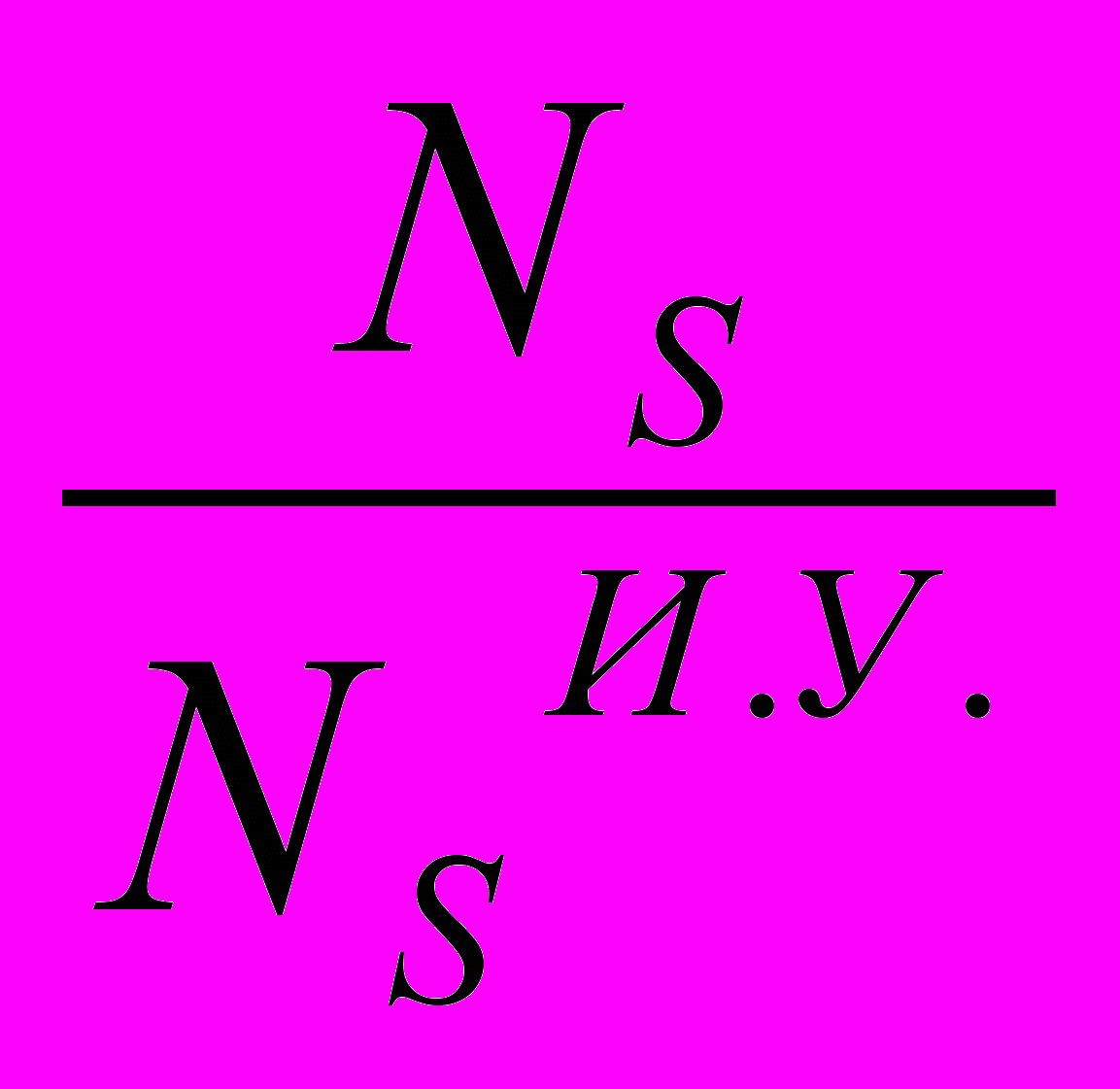
Обнаружено, что формирование устойчивой структуры угля, деструктированного в условиях сдвига (ПМ), не завершается после прекращения механического воздействия: концентрация ПМЦ такого образца относительно исходного угля со временем составила 0,55, т.е. снизилась почти в 2 раза. С измельчённым свободным ударом (ДИ) образцом угля изменений во времени не происходило (см. таблицу).
Общепризнанным является то, что упорядочение структуры твёрдых горючих ископаемых в процессе метаморфизма приводит к возрастанию уровня парамагнетизма. Полученные данные свидетельствуют о том, что при механической обработке бурого угля происходят изменения, приводящие к снижению жёсткости его структуры. Наблюдаемые отличия между образцами после завершения релаксационных процессов являются отражением глубины преобразований химической структуры угля: при механодеструкции стеснённым ударом, сопровождаемым сдвигом, они существеннее.
Результаты РСА подтвердили, что при разрушении угля в условиях сдвига изменения, идущие в сторону разупорядочения структуры (увеличение d002 и уменьшение LC), более значительны (см. таблицу).
Структурные преобразования закономерно приводят к изменению химических свойств угля. В частности установлено, что способность подвергаться щелочному гидролизу существенно выше у образцов угля, предварительно деструктированных под воздействием сдвига.
УДК 662.642.66.092 Н. Л. Голденко
Институт горючих ископаемых, г. Москва
ВЛИЯНИЕ ДЕЗИНТЕГРАТОРНОЙ ОБРАБОТКИ НА ПАРАМЕТРЫ ДИСПЕРСНОСТИ БУРОГО УГЛЯ И ВОЗМОЖНОСТЬ ПРОВЕДЕНИЯ ПРОЦЕССА МЕХАНОАКТИВАЦИИ (стр. 122 – 123)
Целью работы явилось изучение связи между параметрами дисперсности и структуры бурого угля, в том числе для проб угля, измельчённого при разных частотах вращения роторов дезинтегратора. Измельчению подвергали уголь крупностью до 3 мм. Для этого был использован лабораторный дезинтегратор, имеющий 4- и 6-рядные роторы. Частоту вращения изменяли от 4000 до 16000 об/мин. После обработки пробы исследовали методом седиментационного анализа. При измельчении в дезинтеграторе размер частиц во всех опытах составил менее 90 мкм. При измельчении 4-рядными роторами наиболее мелкая фракция была получена при 8000 об/мин. Максимальный размер частиц составил 48 мкм, а минимальный – 2,5 мкм. При 8000 об/мин фракция угля менее 20 мкм для 6-рядных роторов составляет около 80%.
Показано, что двухкратная обработка угля приводит к уменьшению максимального размера частиц и к увеличению выхода фракции менее 5 мкм. При двухкратной обработке для 8000 об/мин содержание частиц менее 5 мкм составило 42,4%, а максимальный размер частиц – 48 мкм.
Методом ИК-спектроскопии определены различные параметры структуры для исходного бурого угля и для проб угля, измельченных при различных частотах вращения роторов дезинтегратора. При измельчении в дезинтеграторе изменяется содержание углерода в метильных, метиленовых и СН-ароматических группах, а также в конденсированной ароматической форме. При 8000 об/мин происходит возрастание содержания метиленовых групп, уменьшение доли углерода в конденсированной ароматической форме и увеличение концевых СН3 и СН-ароматических групп.
Наблюдаемые методами ИК-спектроскопии изменения фрагментов структуры органической массы угля после его дезинтеграторной обработки указывают на механохимические процессы, связанные с разрушением С – О и С – С связей органических веществ угля. Полученные данные показывают целесообразность применения дезинтегратора для получения тонкоизмельченных проб углей и осуществления процесса механоактивации.
УДК 662.62 А. В. Полубенцев, А. Г. Пройдаков
Институт нефте- и углехимического синтеза
при Иркутском госуниверситет, г. Иркутск
ДИСПЕРСНОСТЬ И АКТИВАЦИЯ МЕХАНООБРАБОТАННЫХ УГЛЕЙ (стр. 123 - 124)
Целью данного исследования являлось изучение взаимосвязи реакционной способности механообработанных в различных аппаратах углей с величиной их удельной поверхности.
В качестве параметра реакционной способности углей использована степень их превращения в процессе последующего ожижения в суперкритических условиях в среде изопропилового спирта. Величины относительной удельной поверхности механообработанных углей оценены исходя из их дисперсности, определённой по результатам седиментационного анализа.
Из приведённых в таблице результатов видно, что между величинами степени превращения углей в процессе ожижения и параметрами их дисперсности не наблюдается никакой зависимости. Очевидно, что в данных случаях значительную роль играет активация углей. Причём в зависимости от характера и интенсивности механического воздействия может достигаться различная степень активации обрабатываемого вещества, при этом интенсивность релаксационных процессов также будет различной, т. е. эффективное диспергирование углей и их высокая активация могут в значительной степени нивелироваться релаксационными процессами, которые могут приводить как к снижению активности вещества, так и к укрупнению измельченного материала за счёт взаимодействия между активными частицами.
^ Степень превращения в процессе ожижения (К, в % на ОМУ) и дисперсность углей, предварительно механообработанных в различных активирующих устройствах.
^ Условия механообработки | Параметры дисперсности | К, % на ОМУ | ||
Устройство | ζ, мин | dM, мкм | SУД. (ОТН.) | |
Исходный уголь Шаровая центробежная мельница “Рульверизетте-6” ^ Активатор-измельчитель АИ-2 Планетарная центробежная мельница Дисмембратор ЗУ-2 Дисмембратор роторного типа Дезинтегратор ДС-106 ГРПА-90/3л+2ш ГРПА-90/3л+2ш ГРПА-90/3л+2ш ГРПА-90/3л+2ш ГРПА-90/3л+2ш ГРПА-90/3л+2ш | - 60 15 10 10 3 На проход 3 5 10 15 20 30 | 76 18 40 10 15 26 10 60 55 40 26 24 25 | 1,0 4,2 1,9 7,6 5,0 3,0 7,6 1,3 1,4 1,9 3,0 3,1 3,0 | 33,8 41,2 62,0 40,2 55,6 42,5 40,5 33,5 36,8 51,3 68,2 68,5 65,3 |
Обозначения: ζ – время оработки;
dM – медианный диаметр частиц измельченного угля;
SУД. (ОТН.) – относительная удельная поверхность