Сварка деталей с большой разницей толщин
Вид материала | Автореферат |
- Программа вступительного экзамена в аспирантуру по специальности 05. 03. 06 «Сварка, 131.86kb.
- «Электрошлаковая сварка», 183.55kb.
- Лабораторная работа №2 Автоматическая сварка под слоем флюса, 33.88kb.
- Тема: сварка алюминия и его сплавов, 56.75kb.
- Лекция 13. Сварка металлов. Ее роль в современном производстве, 104.24kb.
- Лекция 16. Способы сварки давлением. Контактная сварка. Стыковая, точечная, шовная, 82.74kb.
- Ручная электро-дуговая сварка, 1686.86kb.
- Зварачныя работы правiлы правядзення Издание официальное Министерство архитектуры, 2913.92kb.
- Программа вступительного экзамена в аспирантуру по специальной дисциплине 05. 02., 266.3kb.
- Программа профессионального модуля сварка и резка деталей из различных сталей, цветных, 528.35kb.
При исследованиях температурного поля рассматривали стыковое соединение деталей. Сварочную дугу представляли как мощный быстродвижущийся поверхностный нормально-круговой источник тепла. На стыке массивной и тонкой деталей одновременно выполняются граничные условия первого и второго рода: температура и тепловые потоки в стыке деталей равны между собой. В качестве модели тонкой детали принимали пластину с двумерным распределением температуры в прямоугольной системе координат. Температурное поле в массивной детали рассматривали для квазистационарного случая как осесимметричное поле в четверть пространстве с осью симметрии ОХ, вдоль которой движется центр источника тепла О. Решения, применяемые в этих случаях, имеют сложный вид и не выражаются через известные функции. Однако на их основе с помощью интегральных преобразований и применения теории обобщённых функций для нашего случая, при наличии теплового контакта деталей, Н.В. Дилигенским получены достаточно простые решения, выраженные в виде ряда по степеням ординат:
![]() |
![]() ![]() |
Здесь θ1 и θ2 – температура в тонкой и в массивной деталях;
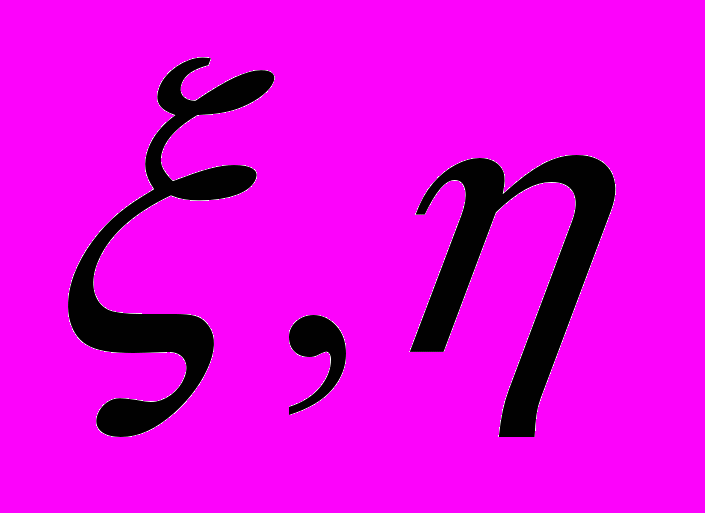
и ордината рассматриваемой точки; Nm(ξ) – функция дробного дифференцирования производящей функции
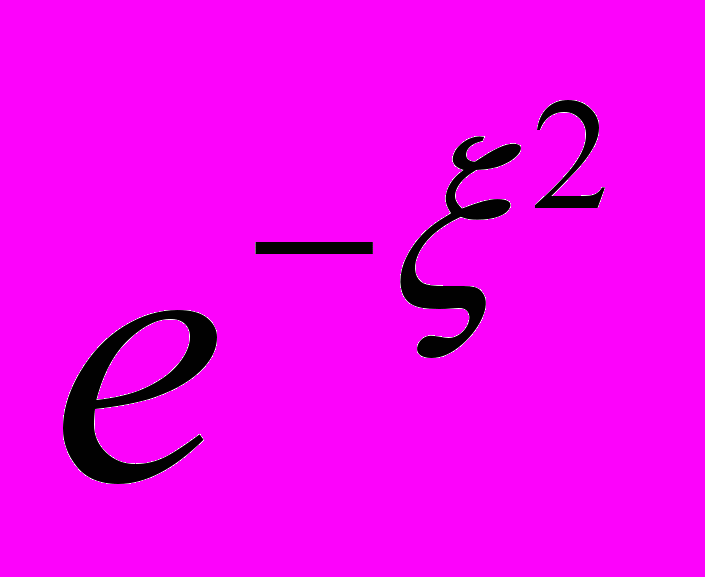
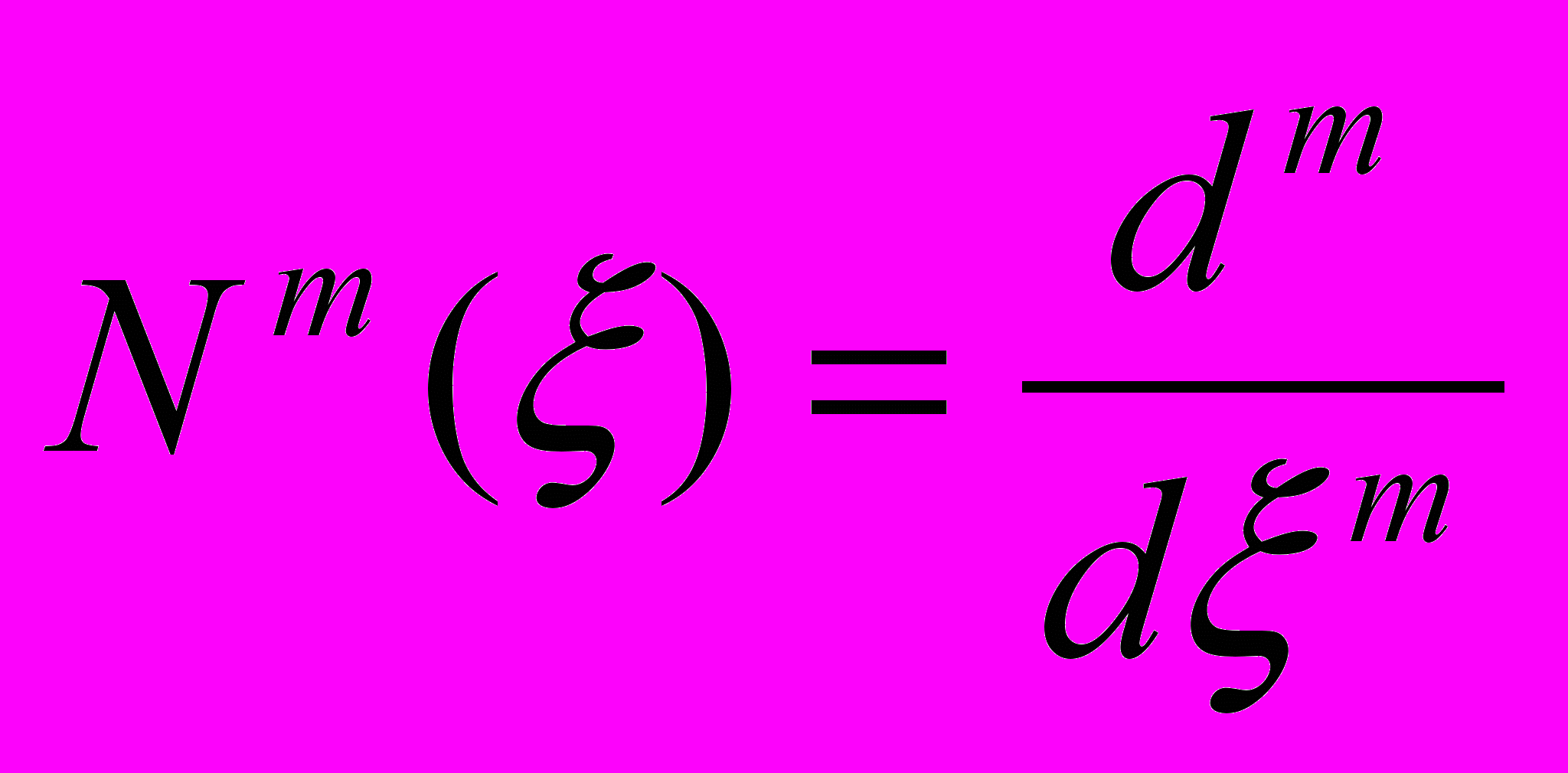
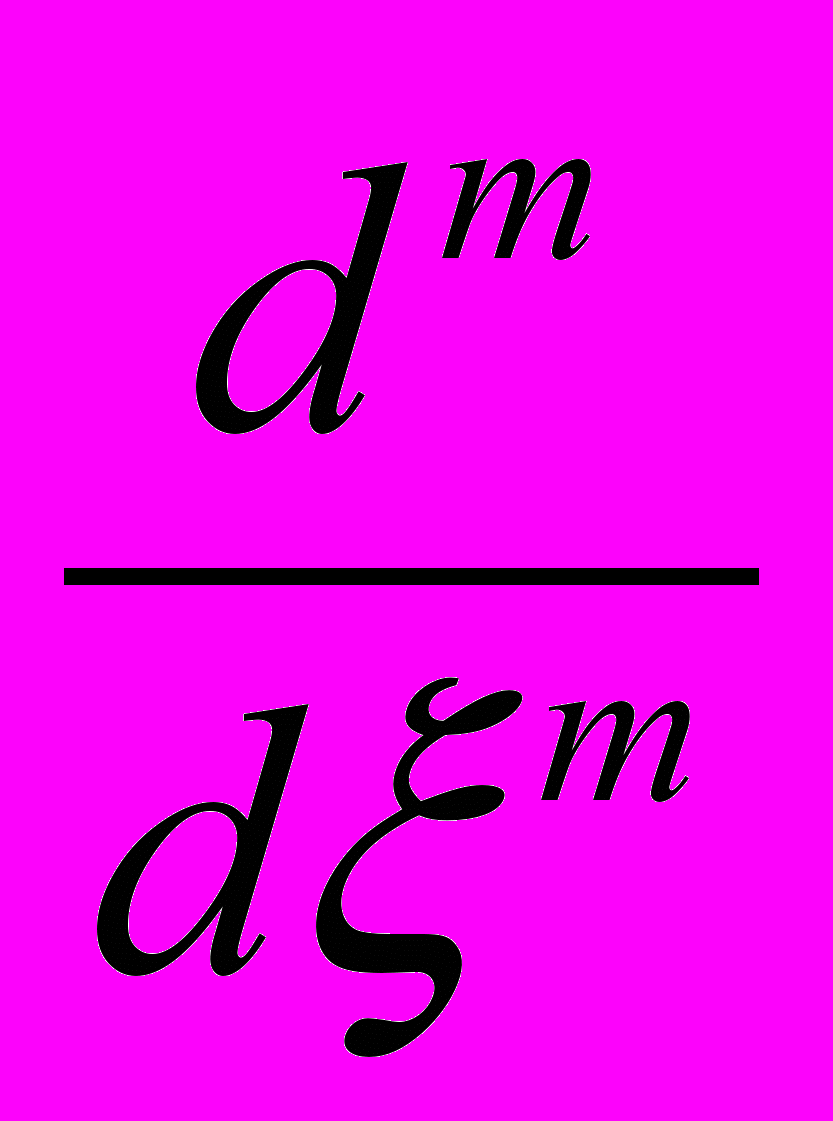
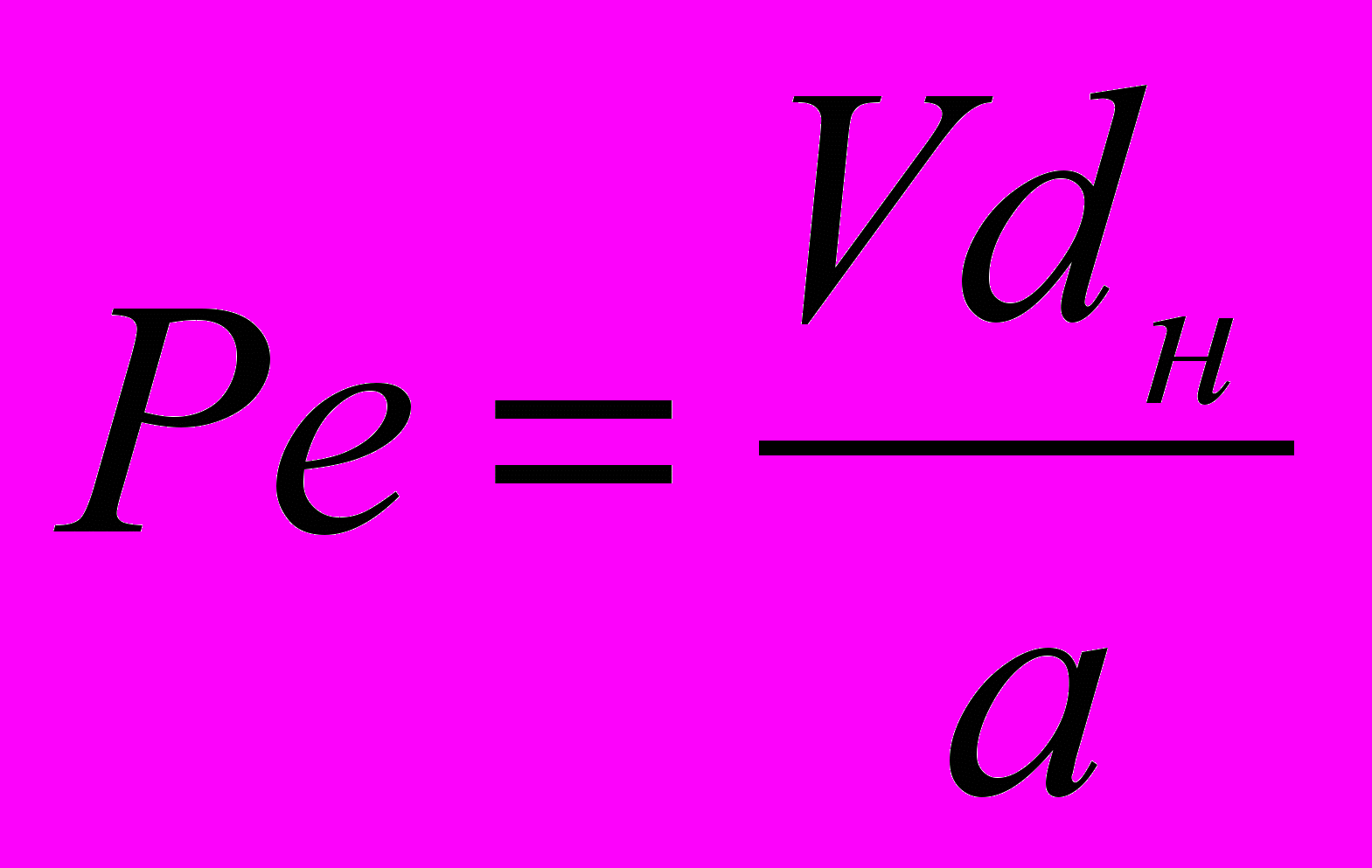
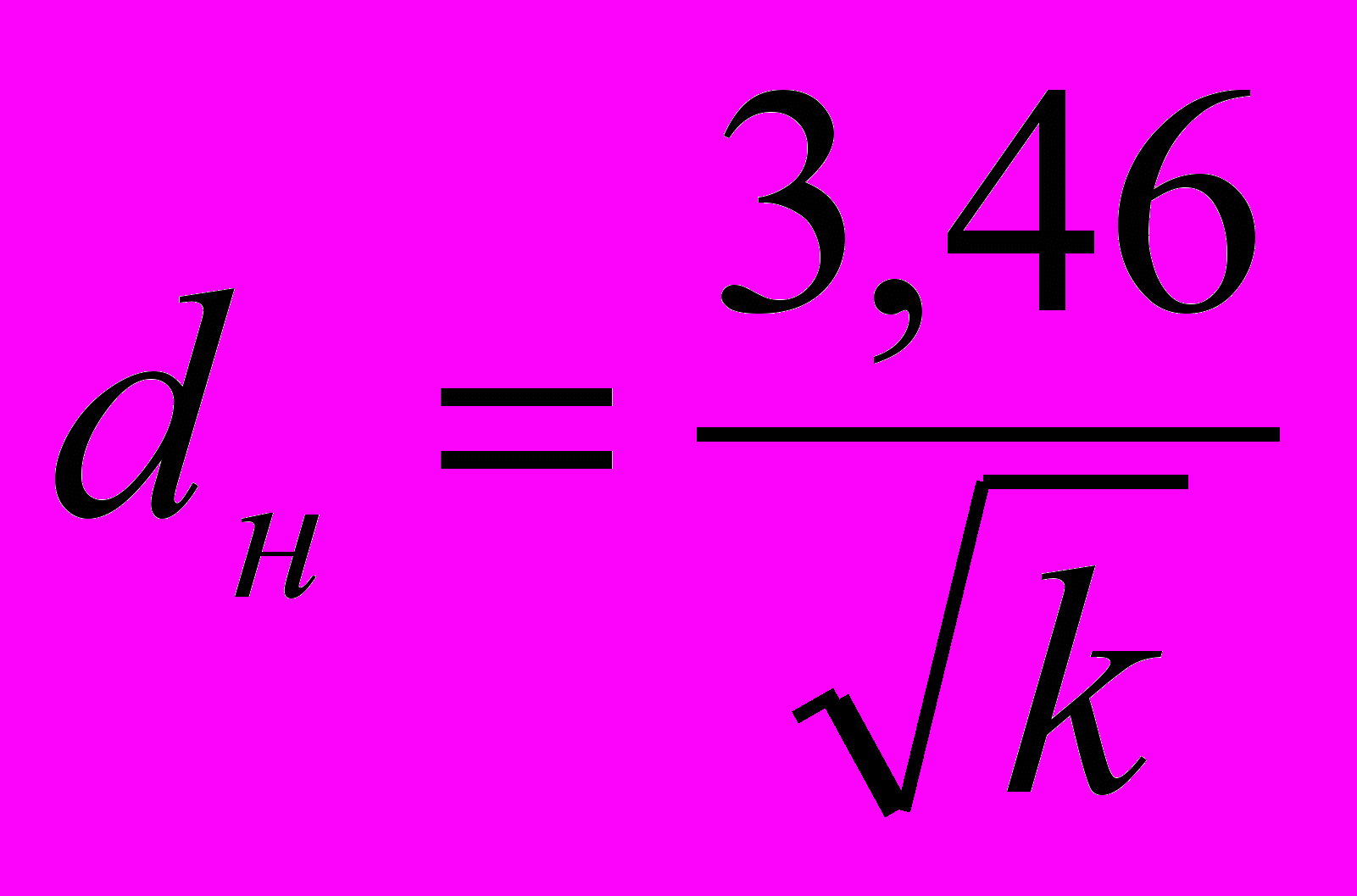
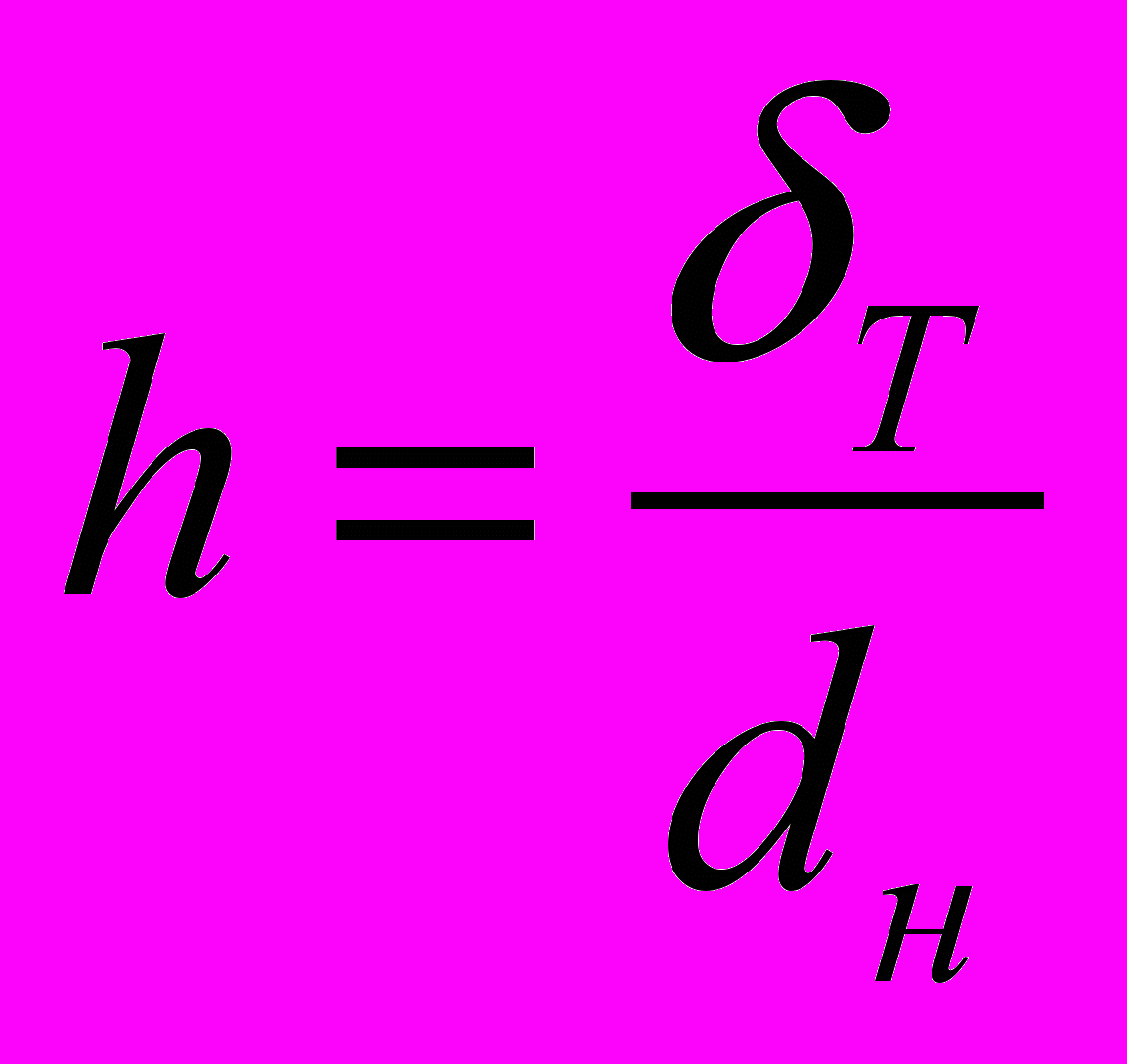
На основе этих решений определена величина и направление теплового потока через стык деталей:

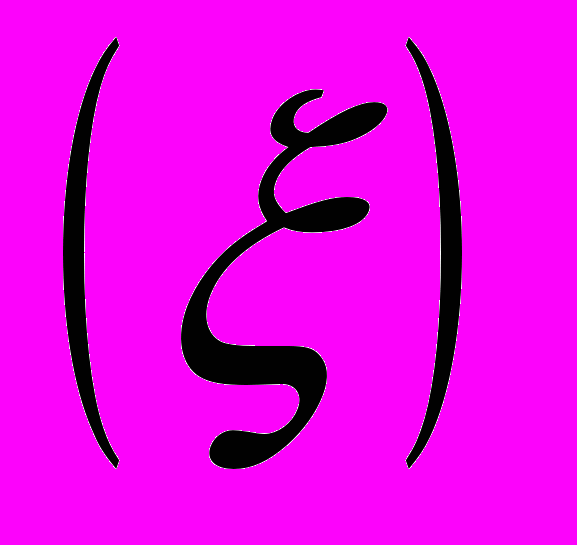
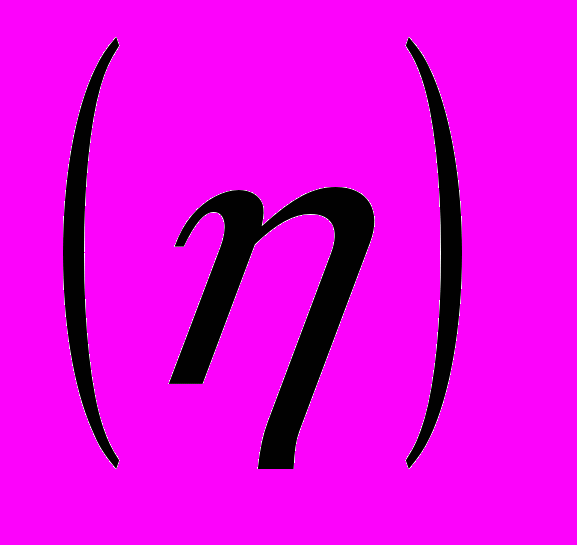

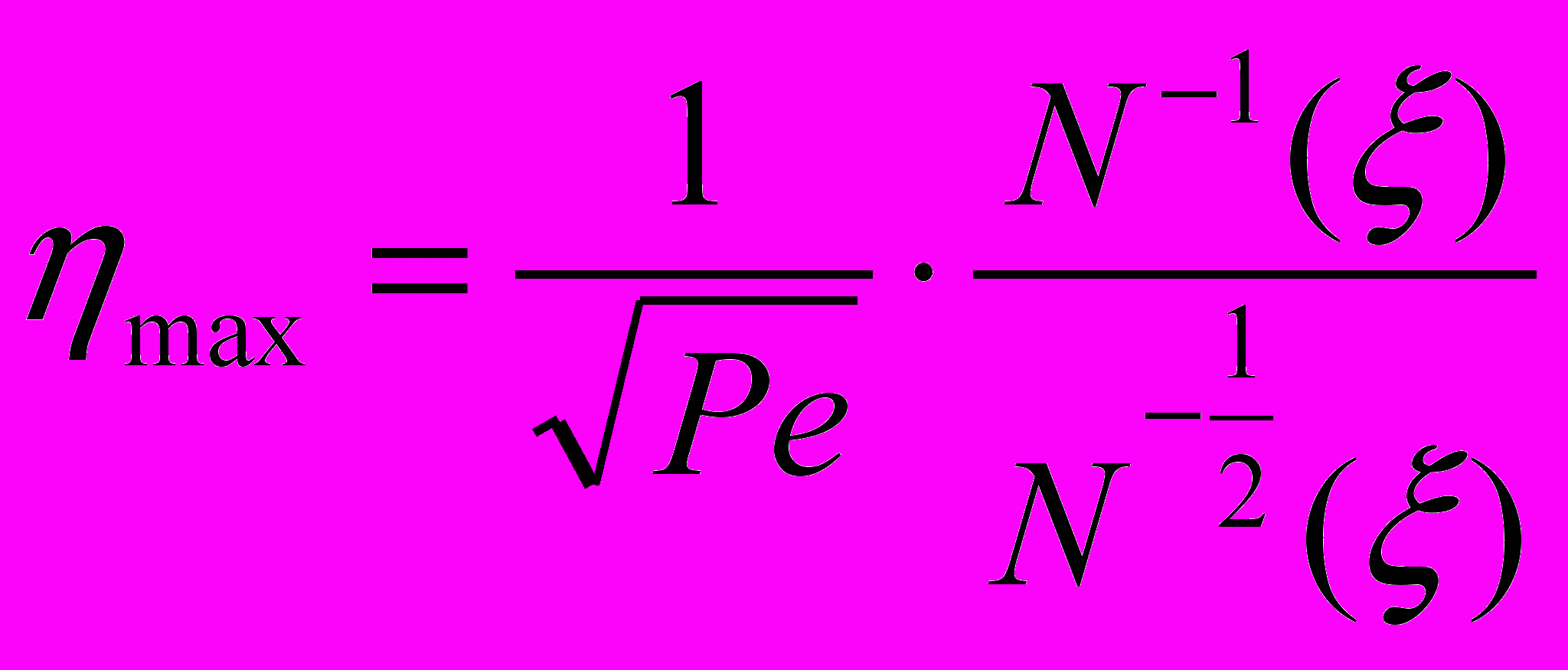
С ростом Ре (с увеличением скорости сварки) координата ηm убывает незначительно, несмотря на то, что ξm при этом заметно возрастает – изотермы становятся более растянутыми вдоль оси ξ. Следовательно, изменением скорости сварки не удаётся приблизить точку θmax к стыку деталей.
Физическое моделирование на свинцовой модели подтвердило асимметрию Т – поля. Электроаналоговым моделированием определено, что эту асимметрию можно уменьшить смещением центра пятна нагрева источника тепла на массивную деталь. Однако при этом абсолютное значение Тmax уменьшается в 4…5 раз и становится ниже температуры плавления свариваемого металла. Это требует повышения мощности источника, что вновь сместит θmax на тонкую кромку и увеличит вложение тепла в неё. Таким образом, смещение источника тепла в сторону массивной детали без применения других приёмов не является достаточным для эффективного регулирования температурного режима тонкой кромки. Этим объясняется не прекращающийся поиск способов дуговой сварки деталей с БРТ. Большинство этих способов основано на изменениях конструкции стыка.
После некоторого значения толщины тонкой кромки формирование шва приобретает качественно иной характер независимо от толщины массивной детали. Сделали попытку анализа характера нагрева тонкой кромки в зависимости от её толщины. Приняли расчётную схему: по стыку массивной детали с пластиной толщиной δ перемещается со скоростью V источник тепла мощностью 2q. При этом кромка пластины полностью расплавляется на ширине bр, а кромка массивного тела оплавляется на глубину, равную δ, образуя проплавление с сечением в виде четверти круга радиусом δ. На кромке массивного тела действует точечный источник тепла мощностью qт = q, на кромке пластины - линейный qл = q. Чтобы обеспечивалось проплавление этой кромки на глубину δ, мощность источника q и скорость его движения V должны быть связаны соотношением q = f(V) или, в безразмерном виде, qb = f(Pe). Здесь
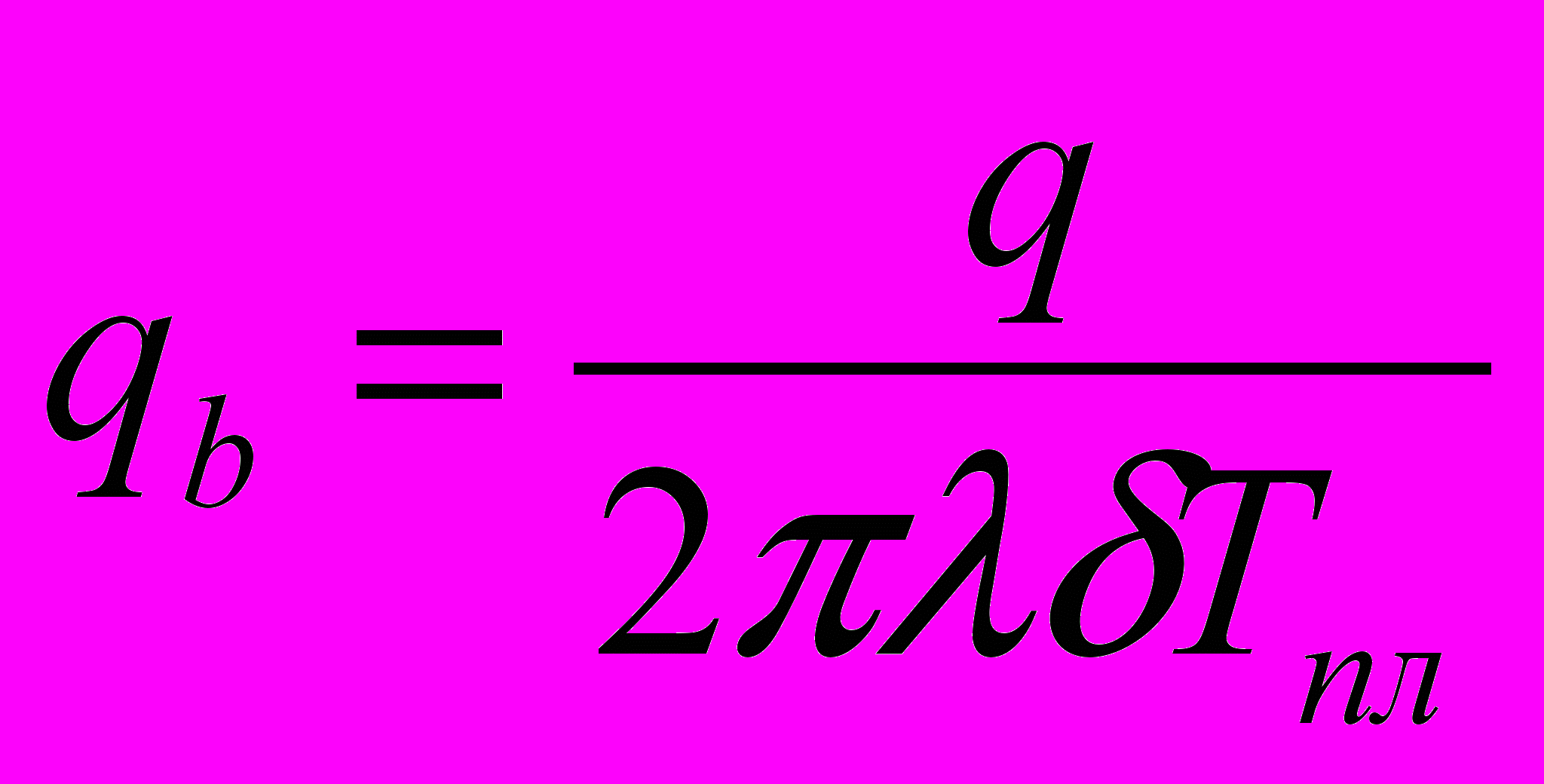
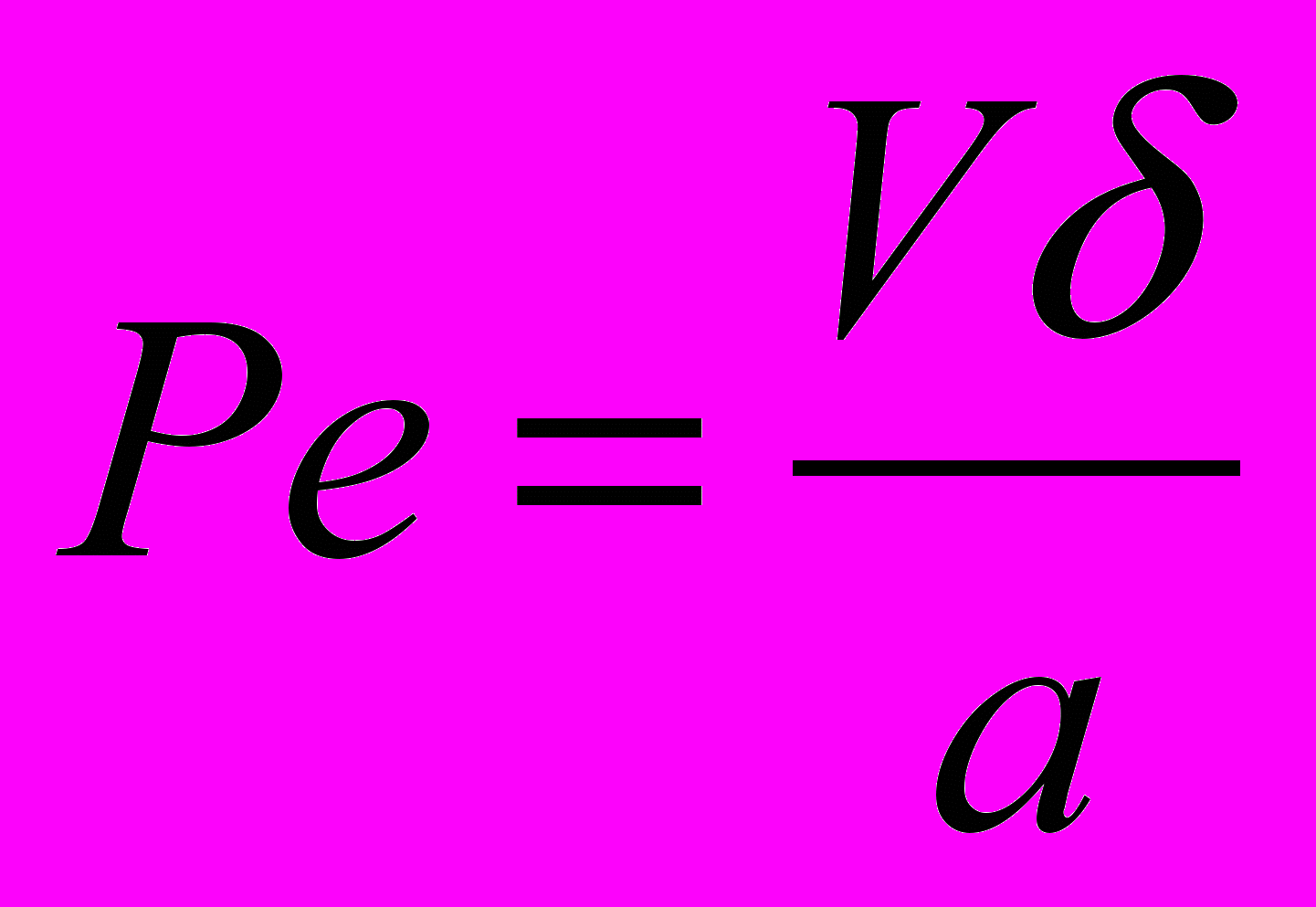
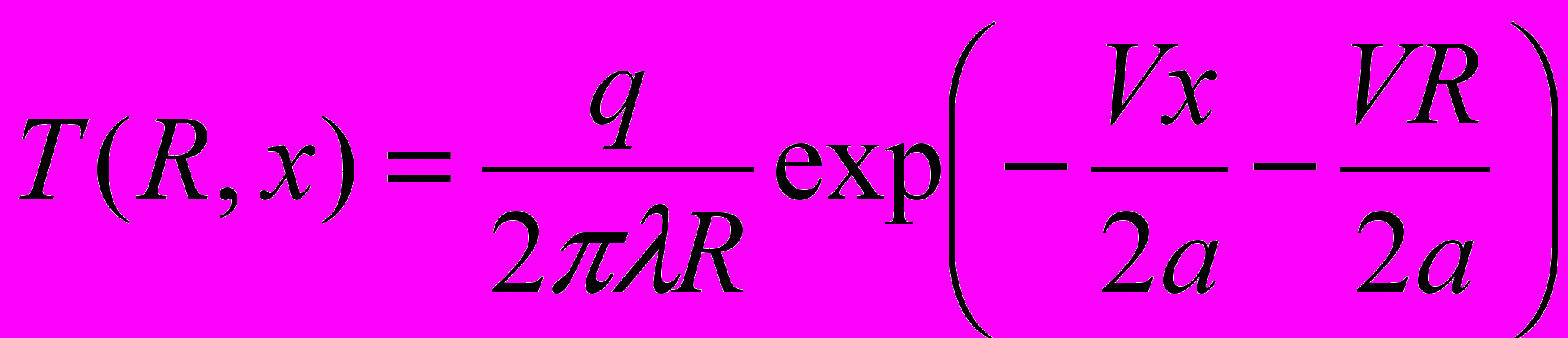
.
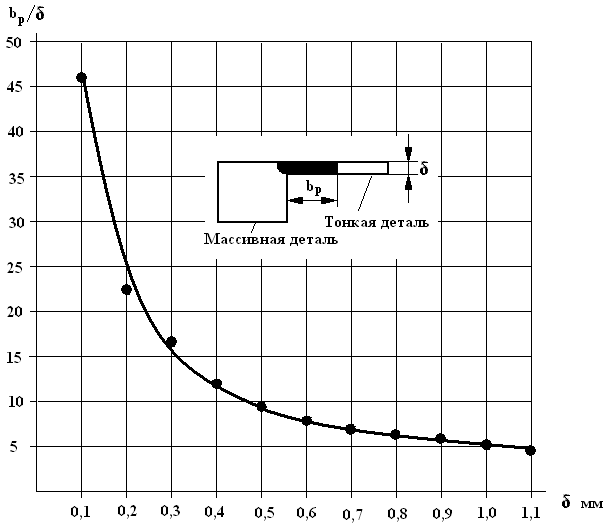

О
Рис. 4. Относительная ширина зоны расплавления тонкой кромки в зависимости от её толщины.
казалось, что эту зависимость можно аппрок- симировать с относительной погрешностью менее 1% выражением:
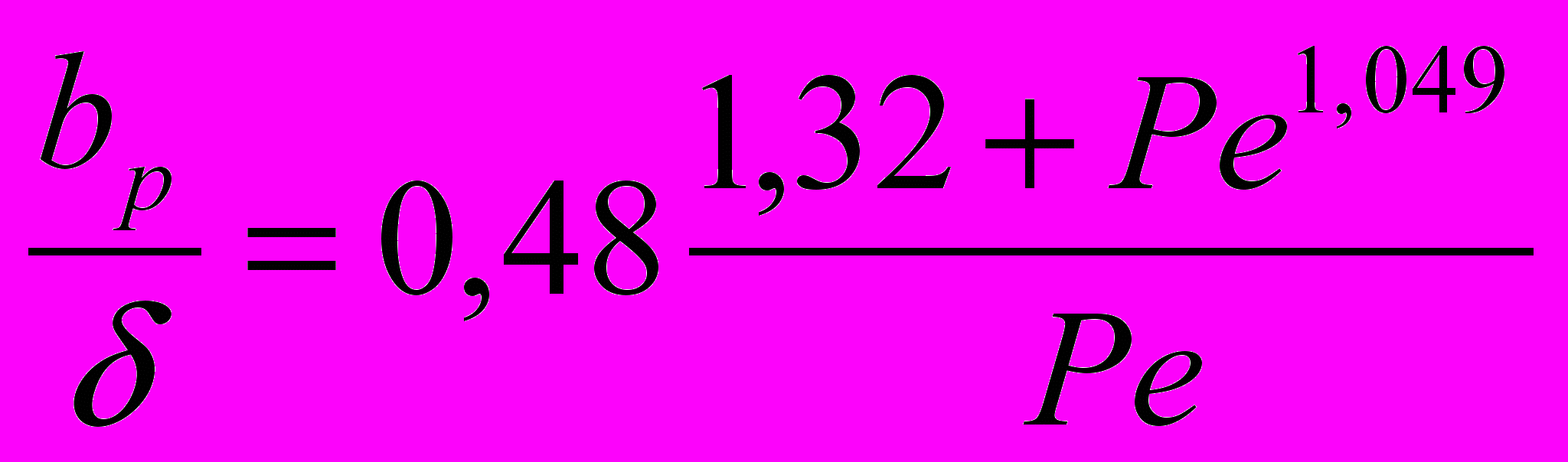
Исследования Т-поля позволили сформулировать условия, которые необходимо выполнять при разработке процессов сварки плавлением деталей с БРТ, обеспечивающих качество и надёжность соединений: конструкция стыка деталей должна обеспечивать фиксацию тонкой кромки относительно массивной детали; источник тепла необходимо смещать на массивную деталь и обеспечивать раздельный нагрев деталей при сварке.
П
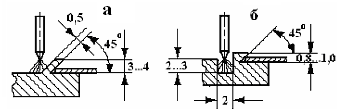
Рис. 5. Экранирующие бурты (а.с.СССР № 299314). а – наклонный; б – со скосом на кромке канавки в массивной детали
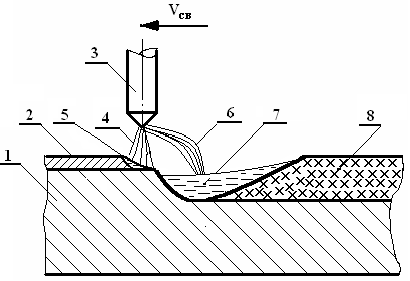
Рис.6. Способ сварки с использованием эффекта отставания дуги (патент РФ № 2231431.
ейтрализует влияние зазора между деталями. С применением экранирующего бурта погонная энергия может быть уменьшена на 36%, вложение тепла в тонкую кромку снижается в 1,5 раза.
Для увеличения производительности разработан способ сварки непрерывной дугой, при котором источник тепла располагается над тонкой кромкой на расстоянии 20δ от её торца (рис. 6). Разделение источника обеспечили за счёт использования эффекта отставания анодного пятна движущейся дуги от оси электрода. Отставание может доходить до 12 мм, его можно регулировать, изменяя скорость сварки и вводя в дугу оксиды и галогениды. Источник разделяется на два: соосный электроду 3 газодинамический поток 4, нагревающий поверхность тонкой детали 2 и проплавляющий её насквозь, и анодное пятно, смещающееся вдоль оси шва в сторону обнажившейся массивной детали 1 и образующее на ней вторую ванну 7, которая, сливаясь в хвостовой части с первой 5, формирует шов 8. Это удовлетворяет второму и третьему условиям повышения надёжности: обеспечивается раздельный нагрев деталей и смещение части источника тепла на массивную деталь. Но фиксация кромки при этом не обеспечивается.
П
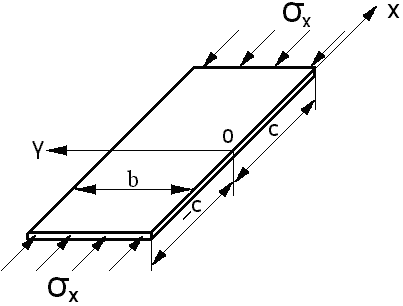
Рис.7. Модель воздействия источника тепла (точка О) на тонкую кромку.
редположили, что при проплавлении оболочки и при высокой скорости сварки деформации тонкой детали могут быть уменьшены. За расчетную модель приняли пластинку, закреплённую по трем сторонам, со свободной продольной стороной, по которой движется источ- ник тепла. На пластинку действуют продольные сжимающие напряжения σx, приложенные к коротким сторонам (рис. 7). Критические сжимаю- щие усилия на единицу длины можно определить по формуле:
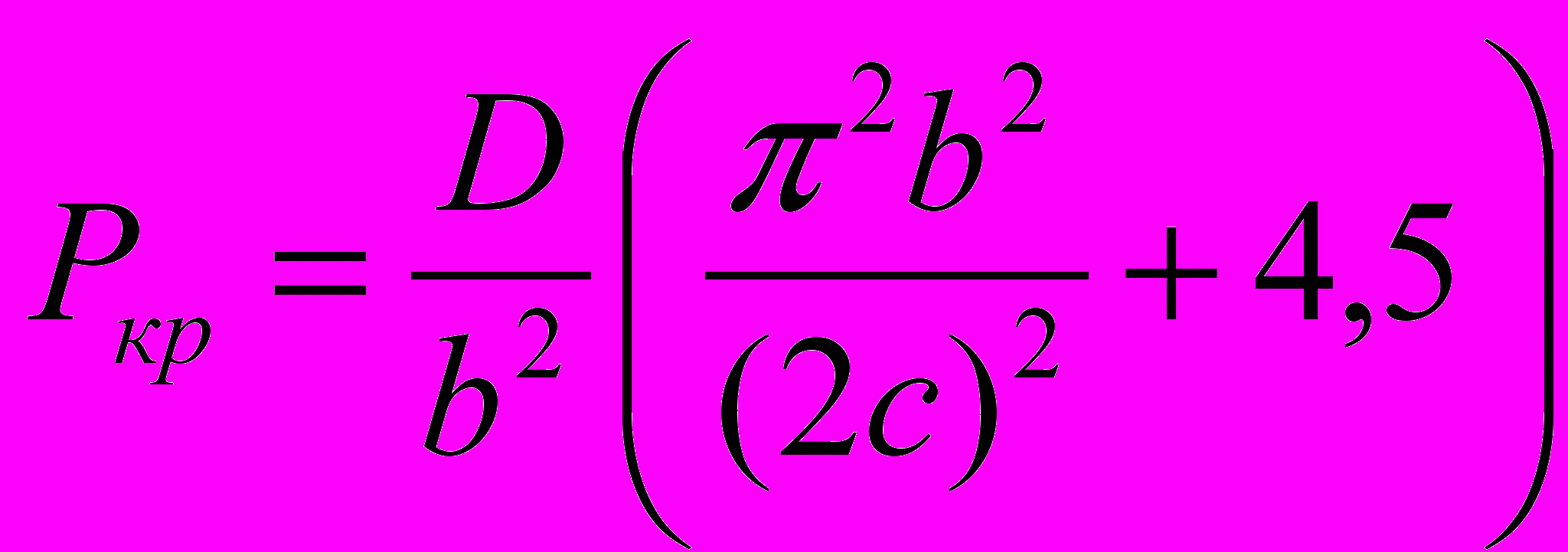
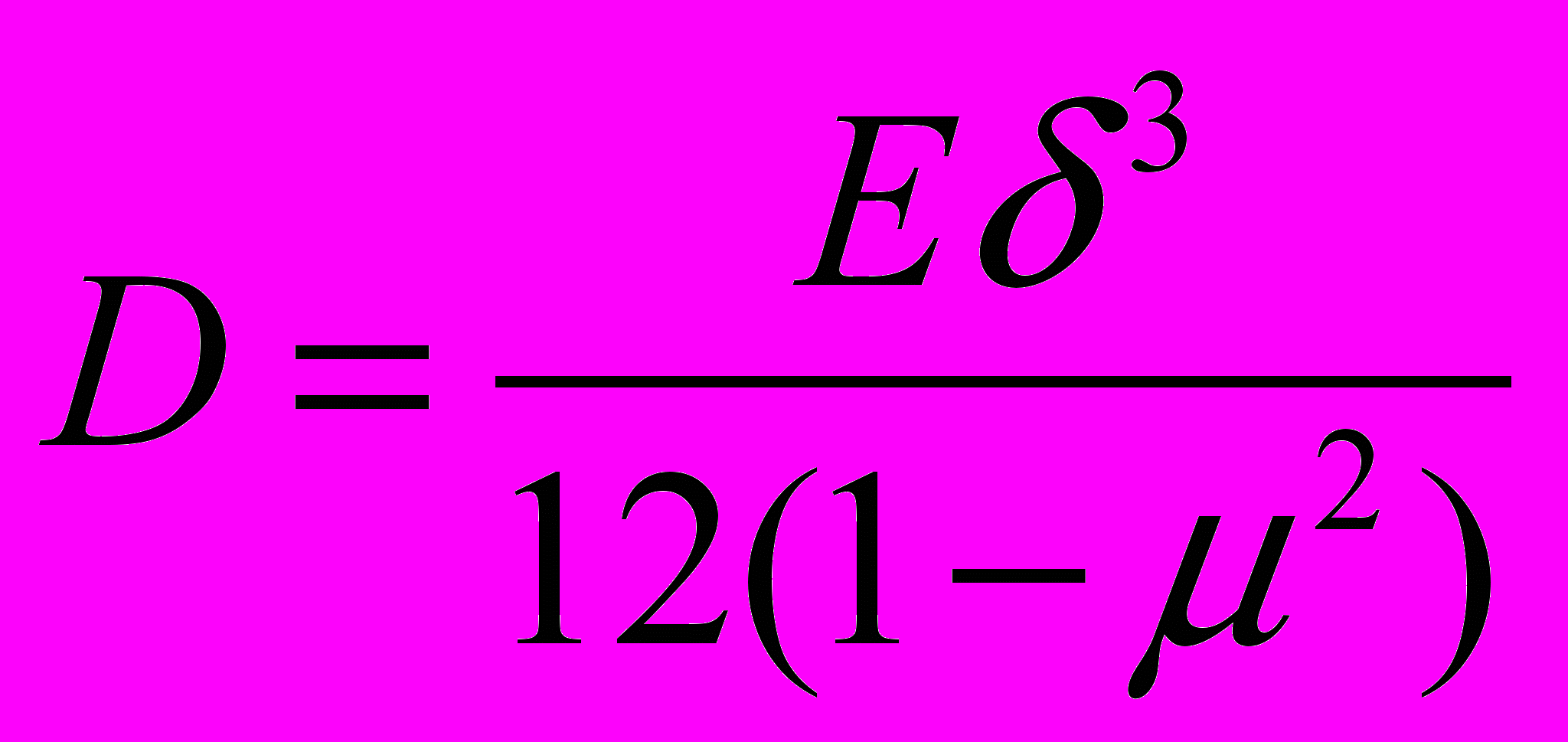

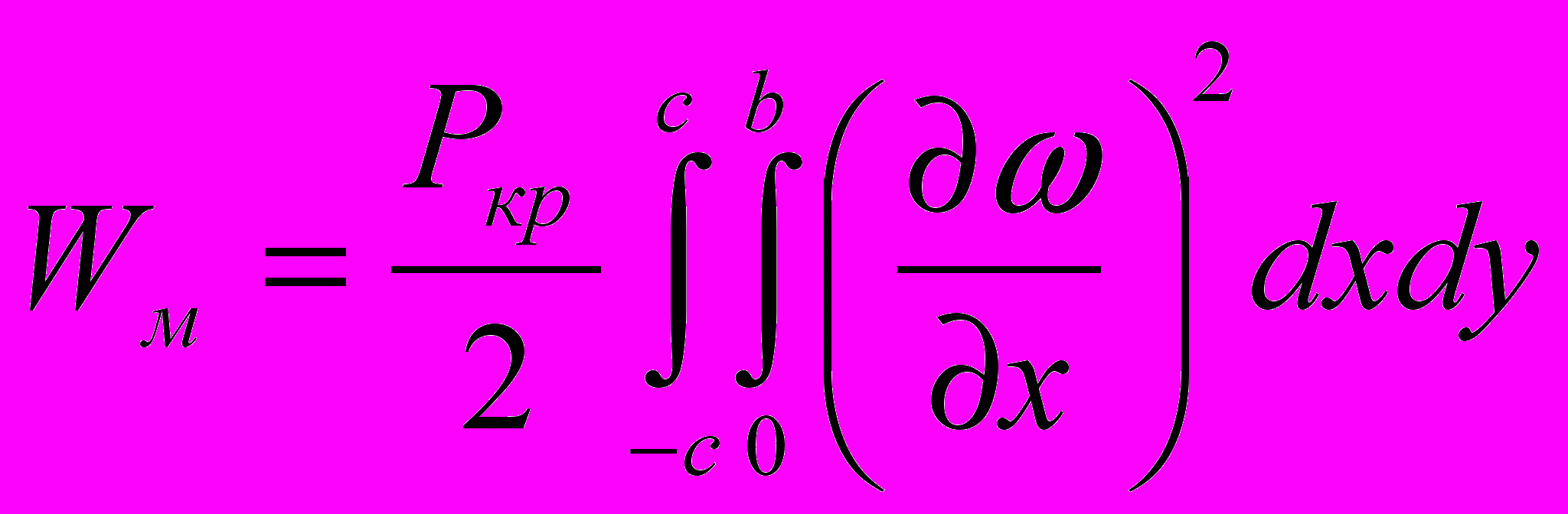
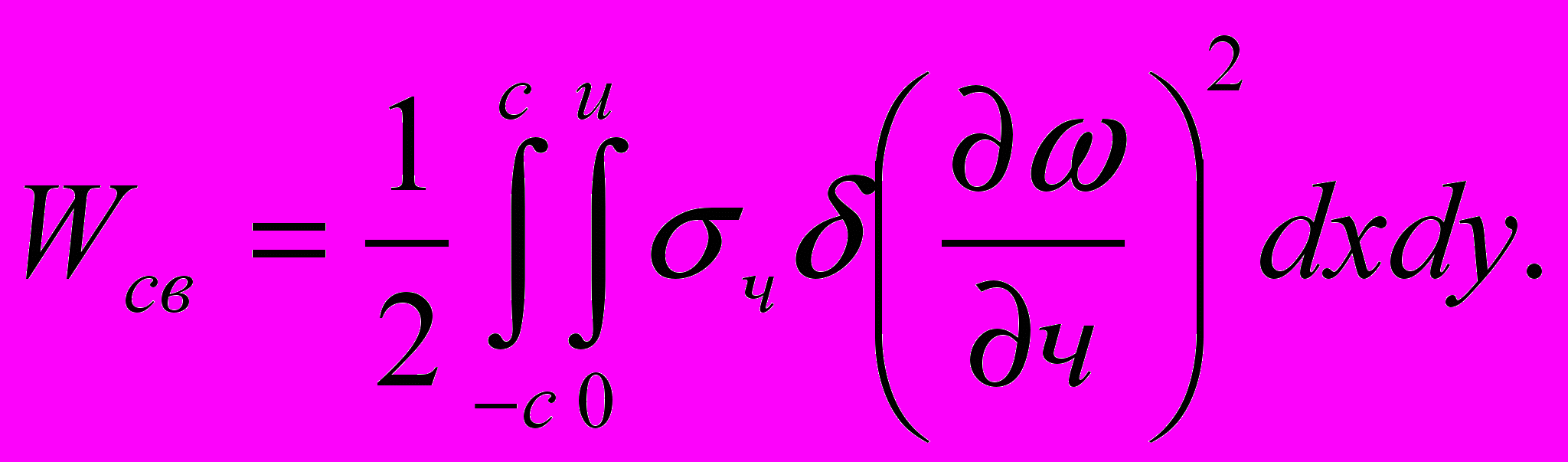
Преобразовав, получили
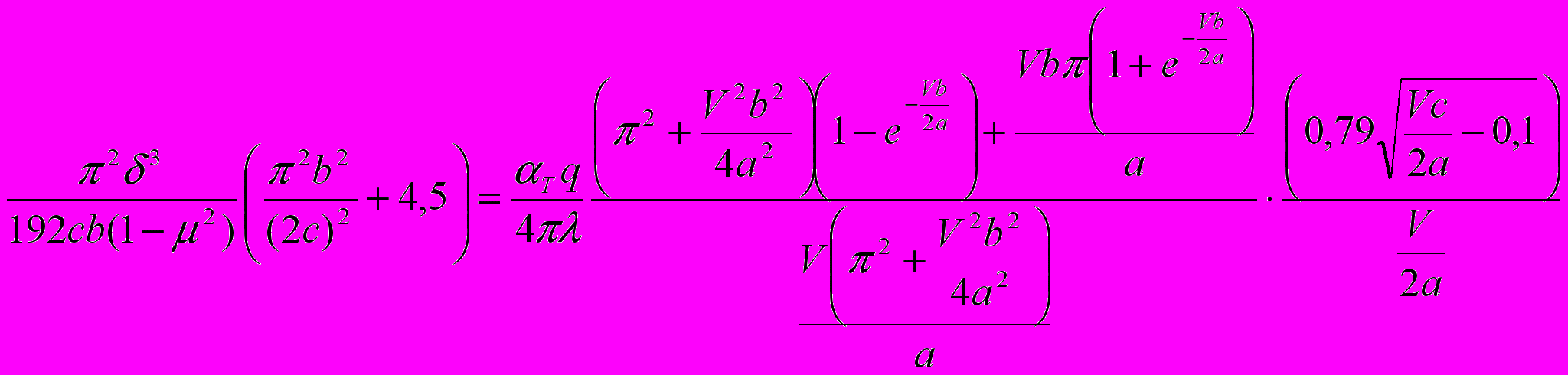
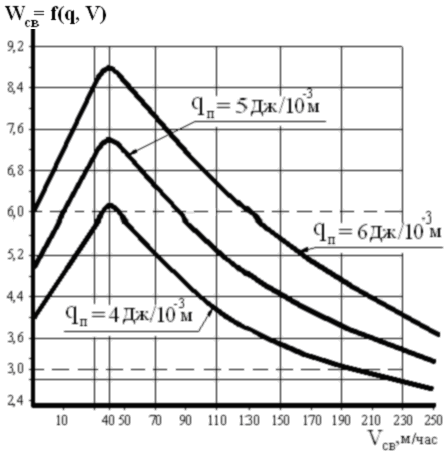
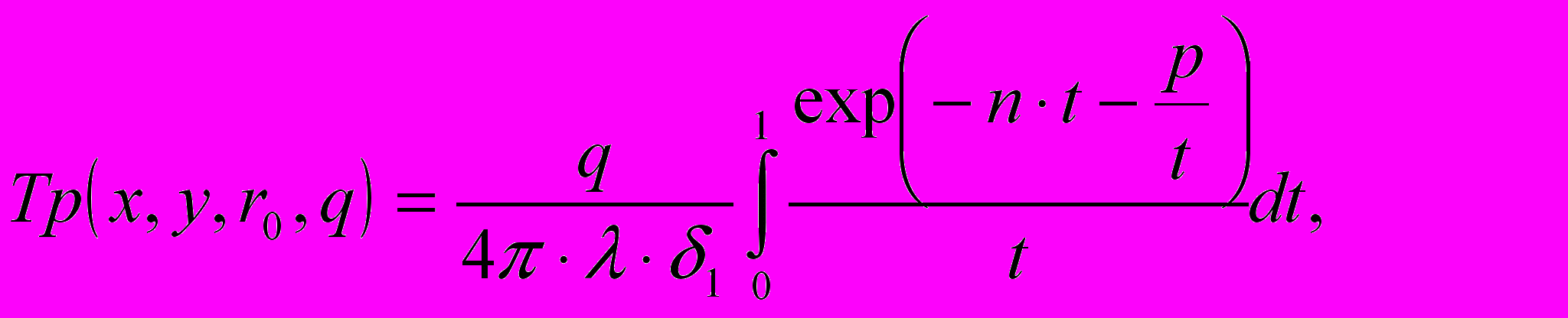
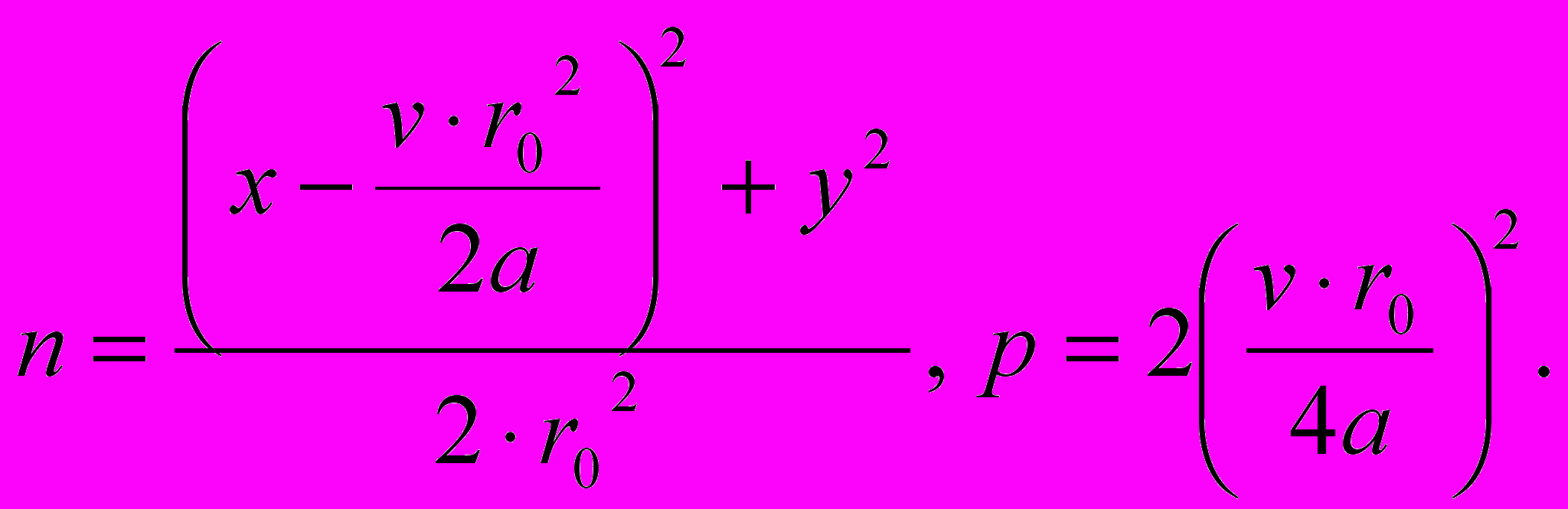

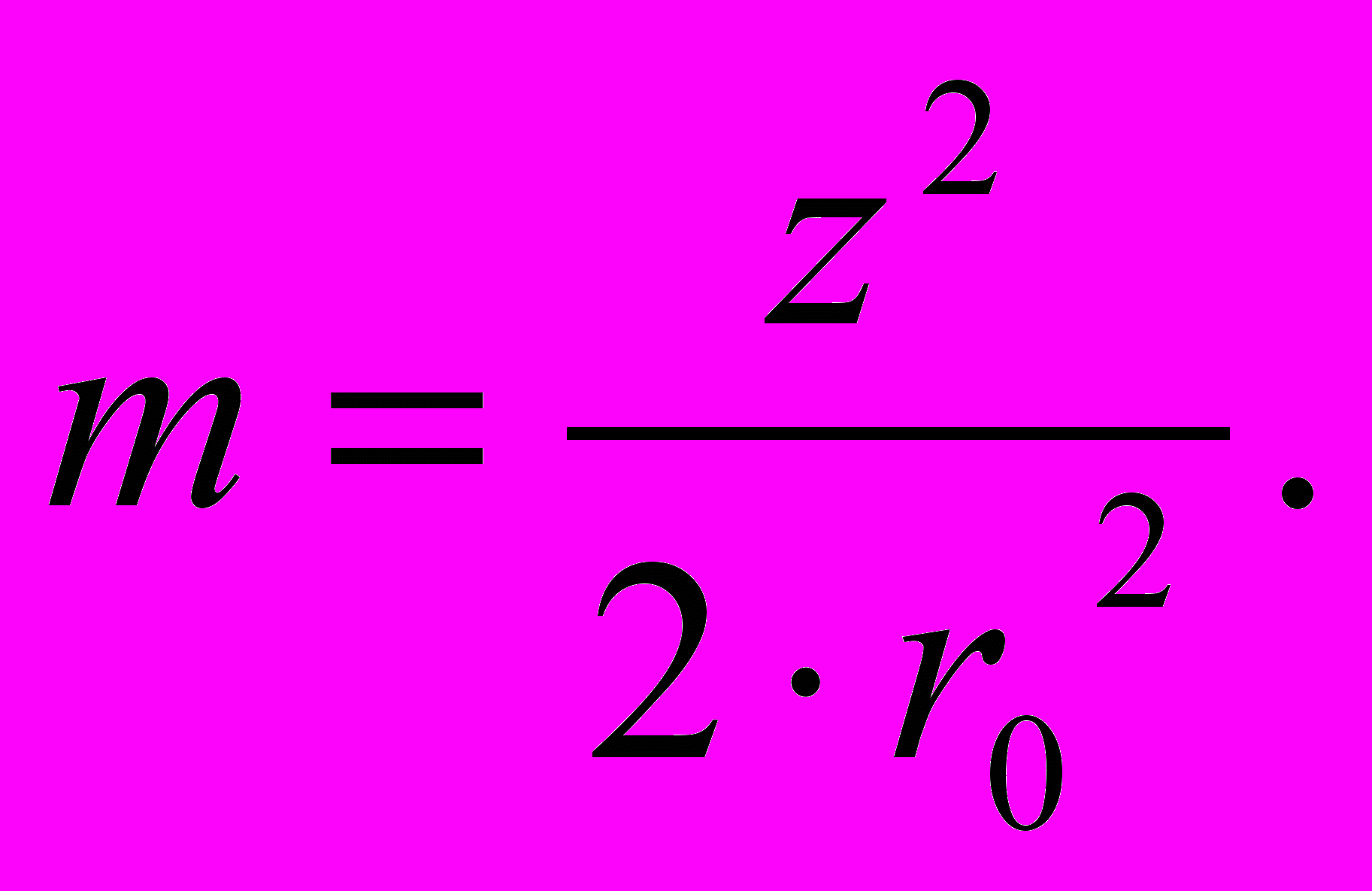
Рис. 8. .Зависимость Wсв от скорости Vсв и погонной энергии qп сварки
На основе этих решений определяли размеры и форму ванны и сечения шва. За основу расчета температурных полей были взяты параметры режимов сварки, использованные в предварительных экспериментах. Значение коэффициента Кр определяли при совпадении расчетных конфигураций сварочных ванн на тонкой и массивной деталях с полученными при сварке образцов на тех же режимах, какие задавались при расчете. Оказалось, что доля мощности источника тепла, поступающей в тонкую деталь Кр =0,35 q. По этим данным определили величины погонной энергии, которые необходимо использовать при исследовании функции Wсв= f(q,v): qП=4; 5; 6 Дж/10-3м. Скорость сварки изменяли от 5 до 250 м/час. В результате получили зависимости функции Wсв = f(q;v) от скорости сварки, при различных значениях погонной энергии qп (рис. 8). Для определения qп, при которой обеспечится устойчивость тонкой кромки, вычислили WМ = 3,0·10-3. Сравнивая эту величину c значениями Wcв= f(q;v), можно сделать вывод что обеспечить устойчивость тонкой кромки можно только при qП=4 Дж/10-3м, при этом величина скорости сварки должна быть более 200 м/час. Экспериментально установили, что при Vсв> 100 м/час процесс не стабилен. Значит, обеспечить отсутствие коробления кромки тонкой детали в процессе сварки можно, только прибегая к фиксации сопрягаемой части тонкой оболочки, т.е. обеспечивая первое условие надёжности процесса сварки. Это можно сделать, изменив величину критических сил Ркр, приложив к рассматриваемой пластинке (рис. 7) силы, направленные противоположно действию Ркр. Для этого можно создать перед сваркой в сопрягаемой части оболочки растягивающие напряжения при помощи сборки соединения с натягом. Оказалось, что наибольшее напряжение в сопрягаемой части оболочки при её деформации в упругой области составляет
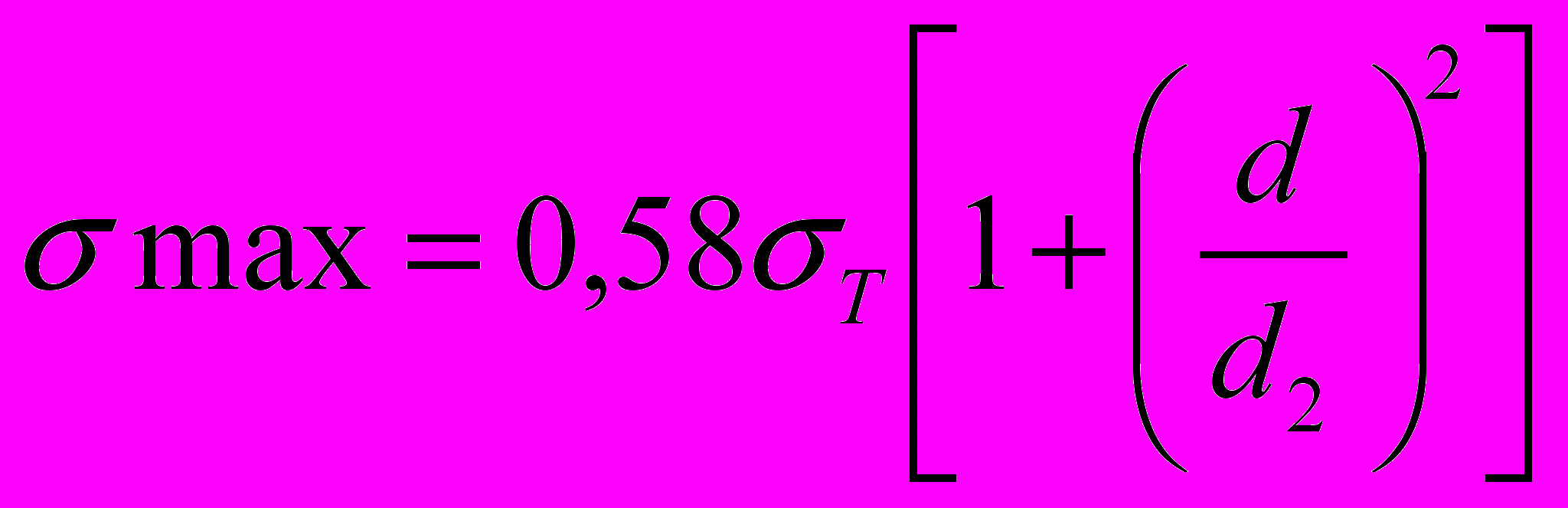
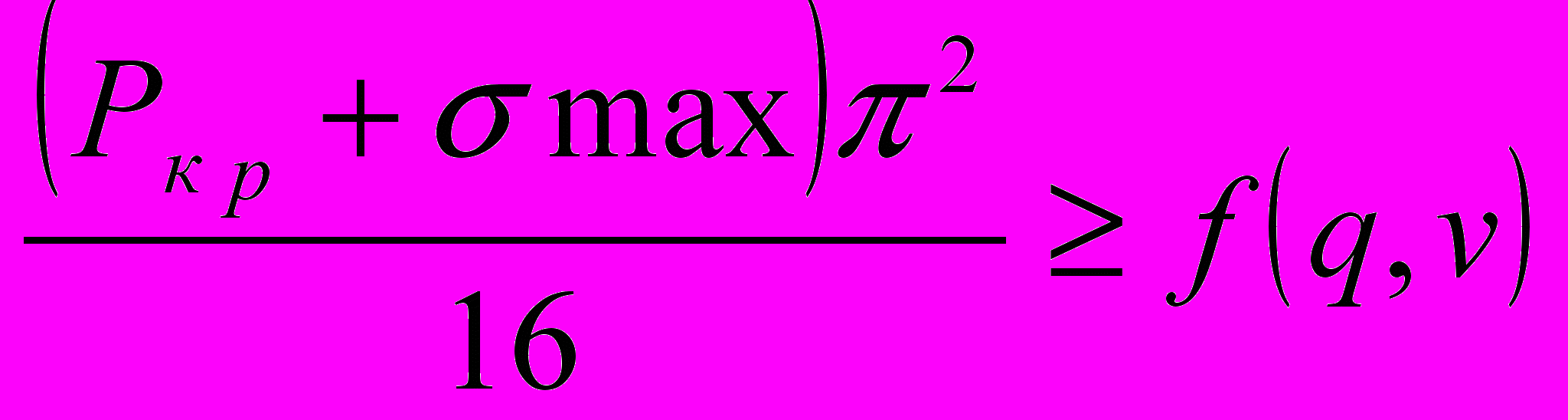
При малых диаметрах стыка деталей, характерных для мембранных узлов и соединений фланцев с тонкими оболочками, трудно обеспечить стабильность ширины шва и проплава по всей длине стыка. В этом случае температурное поле не достигает квазистационарного состояния в зоне формирования шва в течение всего процесса сварки. Ширина шва может возрастать в 1,5…2,0 раза, а проплава – в 2…4 раза по сравнению с начальным участком, в конце шва могут возникать дефекты. В таких случаях целесообразно уменьшать тепловложение по мере перемещения источника тепла по стыку. Однако особенности температурного поля при круговых и кольцевых стыках деталей связаны не только с диаметром шва, но и с теплофизическими свойствами материала деталей и со скоростью сварки, которая, в свою очередь, зависит от тепловой мощности источника и от толщины свариваемых кромок. Необходим критерий малости диаметра кругового шва. Экспериментально установили, что трещины в конце шва могут образовываться при увеличении его ширины более, чем на 10% от номинального значения. Обозначим ширину шва на его начальном участке bн, а на конечном bm. Тогда её максимальное относительное увеличение:
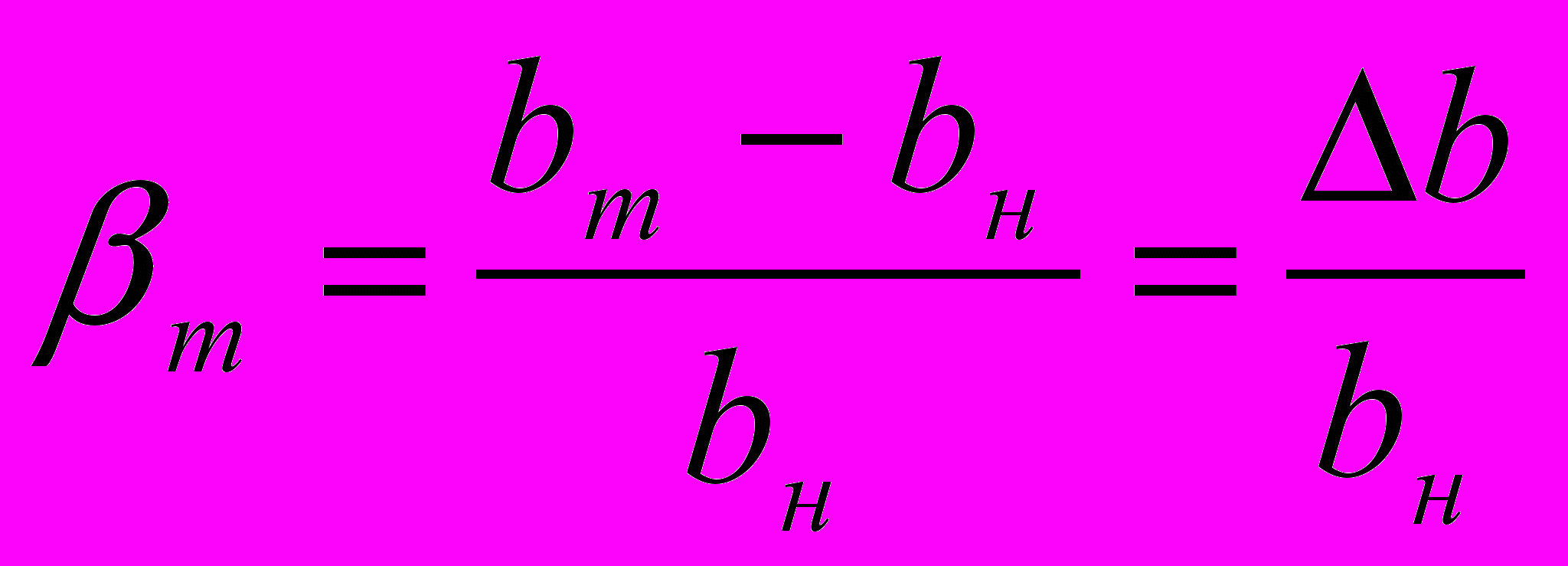
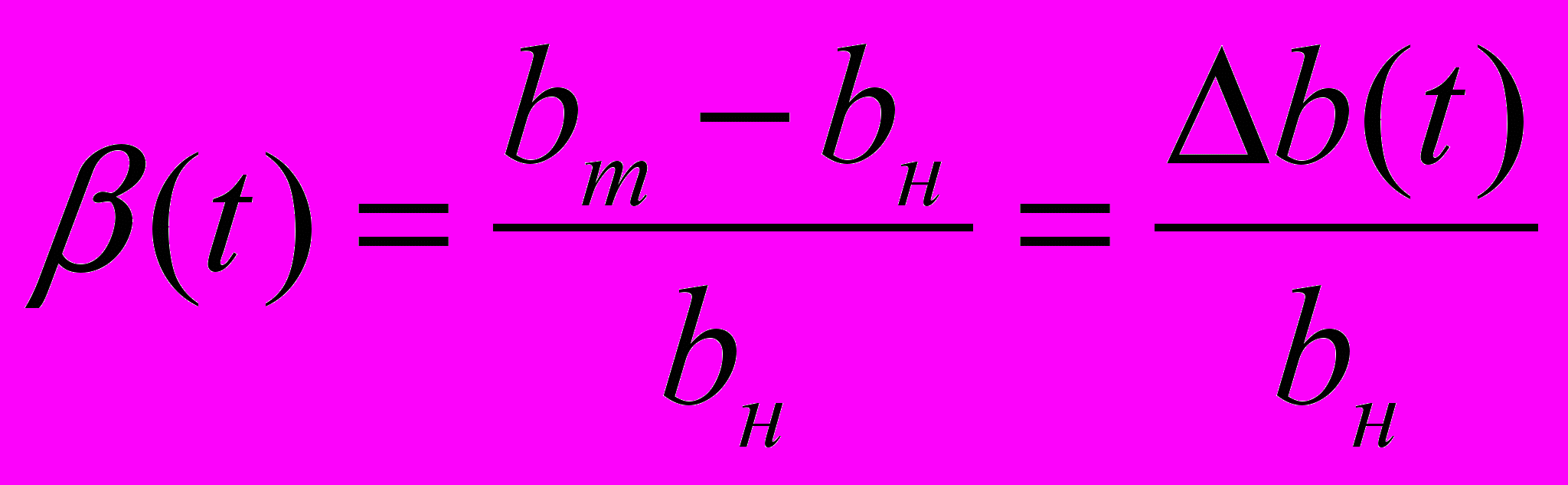
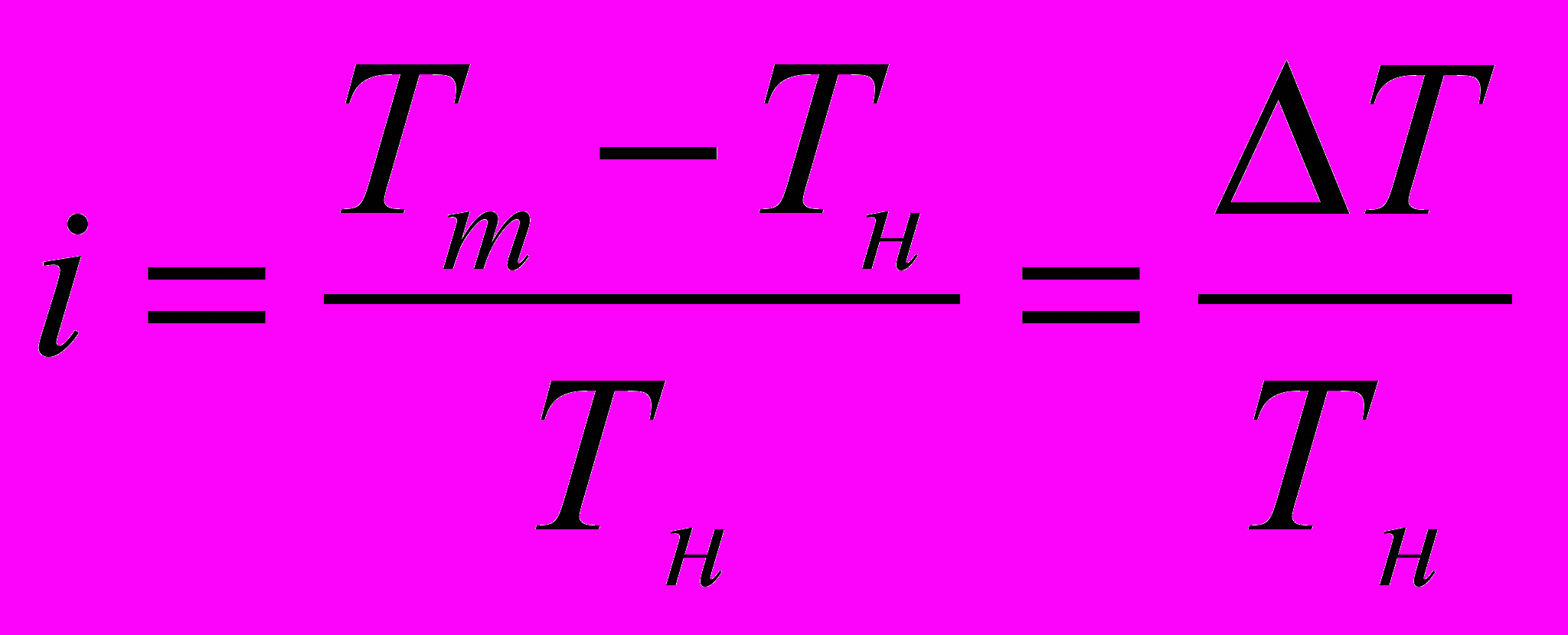
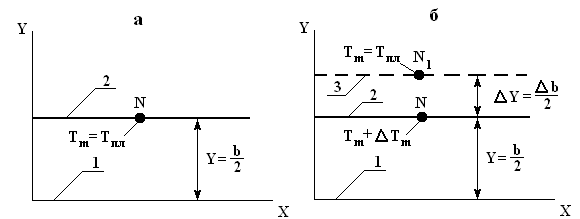
Рис. 9. Схема определения со- отношения между βд и i. а – шов на начальном участке, б – шов на конечном участке.
1 – ось шва, 2 –и 3 – линии сплавления.
Тн – номинальная температура в характерной точке N при номинальной ширине проплава bн. Оказалось, что численно i = д . Значит регулировать тепловложение необходимо, если i > 0,1. Значения i определяли через безразмерную температуру θ используя известные формулы Р.З. Сайфеева для определения Т- поля в пластине при круговом движении источника теплоты. Выразив θ через комплексные параметры Ре и Ро, получим:.

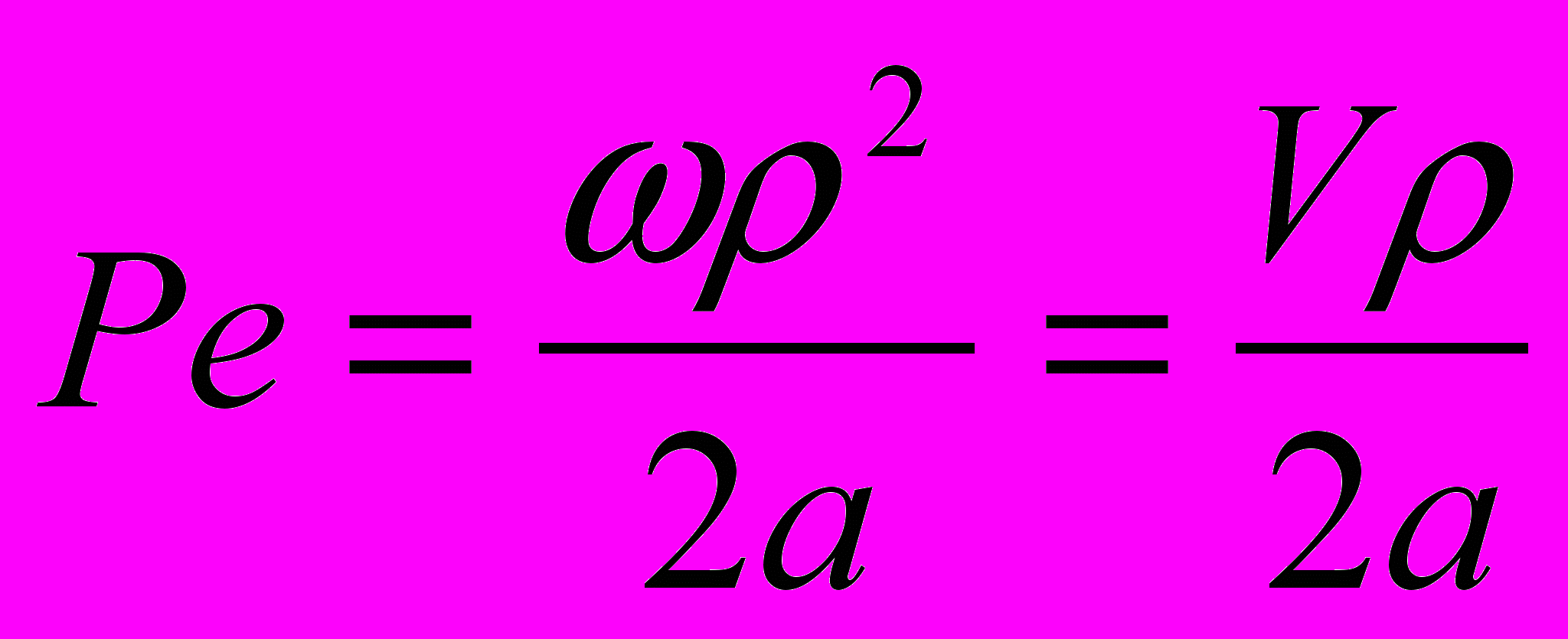
вая координата источника тепла;
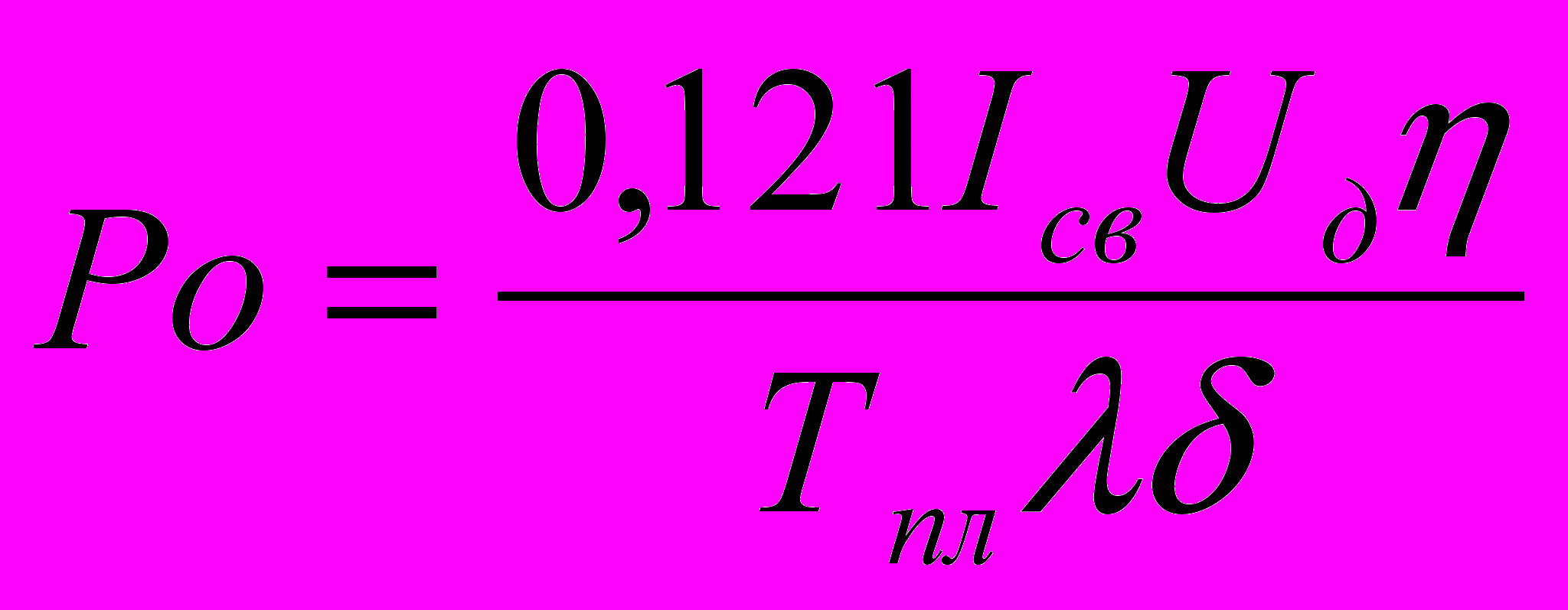
Если 1< θ < 1,1, то регулирования тепловло- жения не требуется, при θ > 1,1 его необходимо регулировать. Рис. 10. Безразмерная температура θ = f(Ре, Ро) точки N1 в зоне перекрытия начала кругового шва. ![]() |