И в свет разрешаю на основании "Единых правил", п. 14 Зам первого проректора начальник организационно-методического управления В. Б. Юскаев конспект
Вид материала | Конспект |
- И в свет разрешаю на основании "Единых правил", п 14 Заместитель первого проректора-, 427.3kb.
- И в свет разрешаю на основании "Единых правил", п 14 Заместитель первого проректора-, 350.14kb.
- И в свет разрешаю на основании «Единых правил», п 14 Заместитель первого проректора, 1301.38kb.
- Альнейшем исполнитель, в лице первого проректора-проректора по научной работе Лысака, 69.99kb.
- Копбаев Кайрат Рашидович заместитель начальника Главного управления начальник организационно-аналитического, 1180.28kb.
- Копбаев Кайрат Рашидович заместитель начальника Главного управления начальник организационно-аналитического, 956.76kb.
- Копбаев Кайрат Рашидович заместитель начальника Главного управления начальник организационно-аналитического, 1044.49kb.
- Копбаев Кайрат Рашидович заместитель начальника Главного управления начальник организационно-аналитического, 834.36kb.
- План работы методического объединения учителей иностранного языка Линник Лариса Александровна, 227.63kb.
- План 2005 р., поз. Формат 60х84/16. Ум друк арк. Підп до друку Зам. № Обл вид арк., 1751.92kb.
МИНИСТЕРСТВО НАУКИ И ОБРАЗОВАНИЯ УКРАИНЫ
СУМСКИЙ ГОСУДАРСТВЕННЫЙ УНИВЕРСИТЕТ
К печати и в свет
разрешаю на основании
“Единых правил”,
п. 2.6.14
Зам. первого проректора –
начальник организационно-методического
управления В.Б.Юскаев
КОНСПЕКТ ЛЕКЦИЙ
по курсу “Источники энергии”
для студентов специальности
7.000008 “Энергетический менеджмент”
дневной и заочной форм обучения
Все цитаты, цифровой и
фактический материал,
библиографические сведения
проверены, написание единиц
отвечает стандартам
Составители: С.С.Антоненко
А.А.Руденко
Ответственный за выпуск А.А.Евтушенко
Декан инженерного факультета А.А.Евтушенко
Сумы
Изд-во СумГУ
2006
МИНИСТЕРСТВО НАУКИ И ОБРАЗОВАНИЯ УКРАИНЫ
СУМСКИЙ ГОСУДАРСТВЕННЫЙ УНИВЕРСИТЕТ
КОНСПЕКТ ЛЕКЦИЙ
по курсу “Источники энергии”
для студентов специальности
7.000008 “Энергетический менеджмент”
дневной и заочной форм обучения
Утверждено на заседании
кафедры как конспект лекций по курсу «Источники энергии».
Протокол № 1 от 30.08.2006 р.
Сумы
Изд-во СумГУ
2006
МИНИСТЕРСТВО НАУКИ И ОБРАЗОВАНИЯ УКРАИНЫ
СУМСКИЙ ГОСУДАРСТВЕННЫЙ УНИВЕРСИТЕТ
КОНСПЕКТ ЛЕКЦИЙ
по курсу “Источники энергии”
для студентов специальности
7.000008 “Энергетический менеджмент”
дневной и заочной форм обучения
Сумы
Изд-во СумГУ
2006
Конспект лекций по курсу «Источники энергии» для студентов специальности 7.000008 «Энергетический менеджмент» дневной и заочной форм обучения / Составители С.С.Антоненко, А.А.Руденко. – Сумы: Изд-во СумГУ, 2006. - 88 с.
Кафедра «Прикладная гидроаэромеханика»
Содержание С.
Введение ....5
1 Общая характеристика источников энергии ....6
1.1 Структура природных источников энергии ....6
1.2 Энергетические ресурсы мира ....6
1.3 Топливо. Виды топлива ....7
1.4 Общие характеристики топлива ....7
1.5 Горение ....9
2 Устройства для сжигания твердого топлива.
Системы приготовления твердого топлива ....11
2.1 Топки ....11
2.2 Устройства для сгорания твердого пылевидного топлива ....12
3 Жидкие и газообразные топлива ....14
3.1 Общая характеристика ....14
3.2 Подготовка к сжиганию мазута и природного газа ....17
3.3 Топочные камеры для жидкого и газового топлива ....19
4 Технологическое оборудование производства тепловой энергии ....21
4.1 Классификация паровых котлов ....21
4.2 Технологическая схема производства пара ....22
4.3 Котельные установки и их оборудование ....24
4.4 Потери тепла ....25
5 Типы и принципиальные схемы тепловых электростанций ....27
5.1 Тепловая электрическая станция (ТЭС) ....27
5.2 Электростанции конденсационного типа (КЭС) ....27
5.3 Общий принцип производства тепловой энергии пара ....31
5.4 Паровые турбины. Общие понятия и определения ....32
5.5 Схемы и рабочие процессы газотурбинных установок (ГТУ) ....33
6 Технико-экономическая оценка работы ТЭС ....37
6.1 Тепловая экономичность ....37
6.2 Коэффициент полезного действия ....38
6.3 Надежность работы электростанции и резерв
основного оборудования ....40
6.4 Нагрузочные режимы электростанции ....41
6.5 Себестоимость энергии, вырабатываемой на ТЭС ....43
6.6 Основные требования, предъявляемые к эксплуатации
и управлению ТЭС ....45
7 Вода как глобальный источник энергии ....46
7.1 Характеристика природных вод ....46
7.2 Основные показатели качества воды ....47
7.3 Качество природных вод ....48
7.4 Технологические методы обработки воды ....49
8 Гидроэнергетика ....51
8.1 Общие положения ....51
8.2 Гидроэлектрические станции ....52
8.3 Гидравлическое аккумулирование энергии ....53
8.4 Приливные электростанции ....56
9 Двигатели ....60
9.1 Общая характеристика работы двигателей ....60
9.2 Отличия ДВС от паровых двигателей ....63
9.3 Использование тепла и КПД двигателей ....66
9.4 Тепловой баланс и определение мощности двигателя ....68
9.5 Топливо, смесеобразование и топливная аппаратура ....69
9.6 Дизель-генераторные установки ....70
10 Атомные электрические станции ....72
10.1 Основные понятия о ядерной энергетике ....72
10.2 Тепловые схемы атомных электростанций и типы реакторов ....77
11 Вторичные источники энергии ....80
11.1 Принцип получения искусственного холода ....80
11.2 Характеристика оборудования получения
гидравлической энергии и энергии сжатого газа ....82
Список литературы ....87
Введение
Целью изложения дисциплины является теоретическая и практическая подготовка будущих специалистов в области получения, преобразования и использования различных источников энергии, а также их анализ с целью максимальной экономии топливно-энергетических ресурсов, выявления и использования вторичных энергоресурсов, интенсификации, оптимизации и осуществления экологически чистых современных энергосберегающих процессов.
В результате изучения дисциплины студенты обязаны: знать энергетическую и энерготехнологическую терминологию; знать источники разных видов энергии; знать назначение, принцип действия и конструкции различных видов энергетического оборудования; уметь осуществлять анализ и выбор эффективных методов получения и взаимного преобразования различных видов энергии; уметь определять и разрабатывать методы снижения затрат энергии на собственные нужды объектов энергетического обследования.
Данный конспект лекций представляет собой базовую информацию, в которой фрагментарно изложен только теоретический материал в виде основных понятий и положений. Детальное рассмотрение представленного материала осуществляется на лекционных занятиях, где непосредственно приводятся пояснительные иллюстрации, примеры, комментарии, методики расчета и т.д.
Изложение лекционного материала предполагает, что студенты имеют базовые знания по физике, теории гидравлики и газа, химии, термодинамике и по машиностроительным предметам, что облегчает задачу в полноценном восприятии, понимании и запоминании всего курса изучаемого предмета.
1 Общая характеристика источников энергии
1.1 Структура природных источников энергии
Энергетическими ресурсами называются природные источники энергии, преобразуемые в дальнейшем в формы энергии, которые используются в производственных процессах, на транспорте, в быту.
Основное место в балансах запасов, добычи и потребления занимают каменные угли, нефть и природный газ.
Такие виды топлив, как торф, дрова, отходы сельского хозяйства в современных энергобалансах составляют небольшой процент.
В общих энергобалансах роль гидроэнергии незначительна, а в производстве электроэнергии – существенна. В некоторых странах вся энергетика базируется на гидроэнергии.
Ветроэнергетические ресурсы мира составляют примерно 70 триллионов кВт∙ч в год. Однако фактическое их использование невелико. Основным недостатком ветровой энергии является ее пространственная рассредоточенность и связанная с этим относительно малая мощность установок (до 100 кВт). Второй существенный недостаток - непостоянство времени скорости ветра. Интересным для исследователей представляется вопрос об использовании энергии недр земли. Эта энергия исчисляется огромными цифрами. Однако на современном техническом уровне использование в полной степени этой энергии не представляется возможным.
Энергия солнечной радиации в настоящее время используется не полностью, т.к. не существует более-менее приемлемого технического решения о преобразовании ее в электрическую.
Огромную роль в энергетике в настоящее время играет энергия ядерных реакций. Это самый дешевый из всех видов энергии. Однако такой вид энергии является потенциально самым опасным, поэтому его использование требует особых подходов.
1.2 Энергетические ресурсы мира
Данные о мировых энергетических ресурсах мира не остаются постоянными и все время изменяются. Продолжающееся изучение недр Земли приводит к открытию новых месторождений угля, нефти, природного газа. Теоретически энергетические запасы Земли неисчерпаемы, однако запасы, добыча которых экономически оправдана, ограничены, поэтому говорить о неисчерпаемости является не совсем правильным.
Примерные данные о мировых запасах:
уголь -1,60000 млрд тонн, нефть – 520 млрд тонн, природный газ-160·1012 м3, торф – 261 млрд тонн, в то время как запасы, доступные для извлечения, составляют: уголь -4000 (25%), нефть-260 (50%), природный газ 140∙1012 м3 (78%), торф -90 (25%), т.е. более 25% всех разведанных запасов.
Для возможности количественного сопоставления разных видов топлив параллельно с данными других видов вводится понятие значения тонны условного топлива (т.у.т). Тепловой эквивалент т.у.т составляет 7106 ккал (1 т.у.т.=7106 кКал=29,33∙109 Дж=8,2103 кВт·ч).
1.3 Топливо. Виды топлива
После рассмотрения основных понятий об энергетических ресурсах и источниках энергии необходимо рассмотреть один из главных видов энергии, используемой человеком,- тепловую энергию.
Основным источником получения тепла в промышленности, транспорте, в сельском хозяйстве, в быту являются горючие вещества органического происхождения. Большое значение в настоящее время имеет и ядерное горючее. В зависимости от назначения различают топливо энергетическое, технологическое и бытовое.
Все виды органического топлива могут быть разделены по агрегатному состоянию на твердые, жидкие и газообразные, а по способу получения на естественные и искусственные.
К естественному твердому топливу относятся: антрациты, каменные и бурые угли, торф, дрова, опилки. Искусственные виды топлива: брикеты (торфяные, буроугольные, каменноугольный), кокс, полукокс, древесный уголь. Естественное жидкое топливо - сырая нефть. Искусственное жидкое топливо- бензин, керосин, мазут, спирт и т.д. Естественное газообразное топливо - природный газ. Искусственные виды - газы (доменный, коксовый, генераторный).
1.4 Общие характеристики топлива
Топливо в том виде, в каком оно поступает потребителю, называют рабочим топливом. Твердое и жидкое рабочее топливо состоит из углерода С, водорода Н2, кислорода О2, азота N2, серы S, негорючих примесей А и влаги W.
Твердые негорючие примеси характеризуют зольность топлива. Поэтому величина А обычно означает содержание золы в топливе.
Состав твердого и жидкого топлива принято выражать в весовых процентах:

Топливо, из которого в результате сушки полностью удалена влага, называется абсолютно сухим топливом:

где составляющие - процент в абсолютно сухом топливе.
Если предположить, что из абсолютно сухого топлива удалены негорючие примеси А, то остаются пять компонентов, которые называют горючей массой топлива:

Сера в топливе содержится в различных соединениях:
- сульфатная Sc – входит в состав СaSO4, NaSO4, K2SO4;
- колчеданная Sk – в соединении с металлами и FeS2;
- органическая – в составе органических соединений, Sop и Sk участвуют в горении топлива и их сумма составляет серу топлива Sл=Sop+Sk.
При исключении из горючей массы колчеданной серы останется топливо такого состава Со+Но+Оо+No+So=100%. Такой состав топлива называется органической массой. В большинстве случаев содержание серы в топливе невелико (десятые доли процента). Поэтому состав органической массы иногда записывают упрощенно:

Основной горючий элемент топлива - углерод, составляющий большую часть рабочей массы (50-75% для твердых топлив и 83-85% для мазутов). Количество углерода в твердых топливах невелико. Сера же, несмотря на малое содержание ее в топливе (0,2-0,5%), при сгорании образует вредные соединения и вызывает коррозию оборудования.
Влажность топлива колеблется в широких пределах: для каменных углей Wp=5-14%, для бурых - до 40%. Влага в топливе нежелательна, потому что из-за нее уменьшается доля горючих компонентов в единице массы топлива, удорожается его транспорт, усложняется разгрузка, возникают трудности при сжигании, снижается тепловой эффект горения, т.к. часть теплоты затрачивается на испарение.
При проектировании и эксплуатации устройств для производства тепла часто приходится пересчитывать состав топлива. Состав рабочего топлива может изменяться, т.к. величины Ар и Wр могут колебаться в широких пределах. В то же время состав горючей массы топлива более стабилен. Это позволяет с приемлемой точностью находить состав рабочего топлива путем пересчета, не производя каждый раз полного элементарного анализа топлива. Если известны состав горючей массы (СГ, НГ и т.д.) зольность Ар, влажность Wр рабочего топлива, то можно найти состав рабочего топлива:
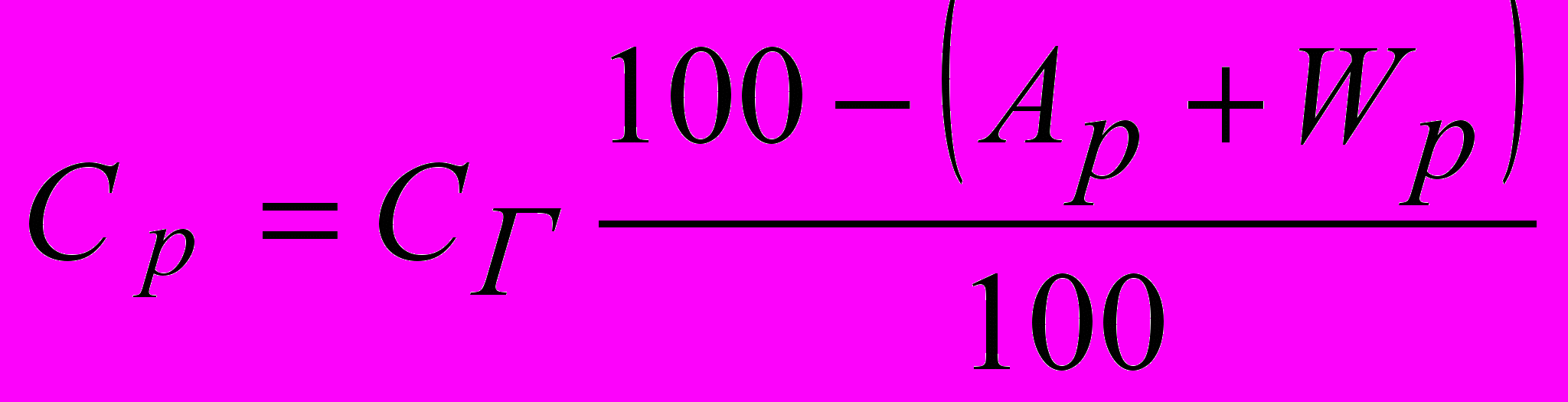
Пользуясь этим же коэффициентом, можно найти содержание в рабочем топливе остальных компонентов (Нр, Ор и т.д.).
1.5 Горение
Горением называют процесс интенсивного соединения горючего вещества с окислителем (кислородом), протекающий при высокой температуре (1000-20000С) и характеризующийся интенсивным тепловыделением.
Механизм горения достаточно сложен и для некоторых веществ мало изучен. Тем более он сложен для таких комплексных органических соединений, как органическое твердое топливо. Однако для выполнения первого, самого простого этапа тепловых расчетов тепловых агрегатов (котлов, печей) достаточно знать начальное и конечное состояние системы горючее - окислитель, не рассматривая механизма горения.
Формулы газовых расчетов получают из соотношений реагирующих веществ в молях, единицах массы, единицах объема:
С + О2=СО2 ; S + O2=SO2;
12кг+32кг=44 кг; 32,07кг+32кг=64,07кг;
2C + O2=2CO; 2H2+O2=2H20;
24кг+32кг=56 кг; 4,032кг+32кг=36,032 кг;
2СО + О2=СО2 ; СН4 + 2О2=СО2+2Н2О;
2м3 1м3 3 м3 ; 1м3 2 м3 1 м3 2 м3.
Минимальное количество воздуха, необходимое для полного сгорания топлива, называется теоретическим количеством воздуха.
Балластом рабочего топлива являются сера, зола и влага. Несмотря на то что сера - горючий элемент, ее относят к балласту, т.к. в результате ее сохранения образуются вредные продукты: сернистый и серный ангидриды. Они отравляют атмосферу и вызывают коррозию оборудования. Процентное содержание серы в горючей массе разных видов топлива SГ: торф, древесина, нефть - 0,3-0,4%, антрацит, каменный уголь и бурый уголь - 2-6%.
Зольность топлива состоит из внутренней и внешней (порода, минеральные вещества, внесенные в процессе добычи и транспортировки). Зольность некоторых топлив: 0,3% - нефть, 5-35%- уголь, 4-20% - торф. При нагревании топлива без доступа воздуха (сухой перегонке) происходит термическое разложение топлива с выделением летучих веществ и образованием твердого остатка. Летучие вещества - смесь газов и паров. Кокс – твердый остаток, состоит из углерода и золы. Процесс сухой перегонки при температуре 1050-11000С называется коксованием и широко применяется для получения высококачественного металлургического кокса. Реже применяется полукоксование - перегонка при 500-6000С. Основная цель такого процесса - получение ценных жидких и газообразных продуктов.
В современных устройствах для сжигания топлива практически достигается полное сгорание топлива. В этом случае продукты сгорания состоят из углекислого газа СО2, сернистого ангидрида SO2, неиспользованных в процессе горения азота N2, избыточного кислорода О2 и водяного пара Н2О. Сумма


2 Устройства для сжигания твердого топлива. Системы приготовления твердого топлива
2.1 Топки
Топками называют технические устройства, в которых осуществляется сжигание топлива. В технике получили распространение топки различных конструкций в зависимости от свойств топлива и производительности агрегата. Основные требования, которым должно удовлетворять топочное устройство, - надежность в эксплуатации и высокая экономичность. Кроме того, топки должны иметь высокую производительность, универсальность при простоте конструкции, обслуживания и ремонта. По методу организации процесса сжигания топочные устройства делятся на слоевые и камерные. Слоевые топки применяются для сжигания твердого топлива. В топках этого типа процесс горения в основном происходит в слое топлива, лежащего на колосниковой решетке. В камерных топках можно эффективно сжигать различные виды топлива - твердое, жидкое, газообразное. Горение в таких топках происходит в топочной камере. В свою очередь, камерные топки в зависимости от аэродинамики потока делятся на факельные (прямоточные) и вихревые (циклонные).
При факельном способе сжигания мелкие частицы топлива легко транспортируются потоком воздуха и образующихся газов в сечении топочной камеры. Сгорание топлива происходит в этом случае в объеме топочной камеры за короткое время (1-2 с). Скорость сгорания и тепловыделения во времени определяются поверхностью горения.
При вихревом способе сжигания частицы топлива находятся в интенсивном вихревом движении. В отличие от факельного способа частицы топлива подвергаются интенсивному обдуванию потоком и быстро сгорают. Этот способ позволяет сжигать более крупную угольную пыль. В таких топках развивается более высокая температура, поэтому шлаки переходят в жидкое состояние.
В слоевой топке находящееся на решетке измельченное топливо с частицами размером 1-6 мм продувается потоком воздуха с такой скоростью, что частицы всплывают над решеткой и совершают возвратно-поступательное движение в вертикальной плоскости. При этом скорость газовоздушного потока в пределах кипящего слоя больше, чем над ним. Более мелкие и частично выгоревшие частицы поднимаются в верхнюю часть кипящего слоя, где скорость потока снижается, и там сгорают. Кипящий слой увеличивается в объеме в 1,5-2 раза, его высота составляет 0,5-1 м.
Если размеры угольных кусочков большие, то эффективность его сгорания невелика. Для того чтобы твердое топливо сгорало с наибольшей эффективностью, производится его специальная подготовка к сгоранию. Основная идея такой подготовки - как можно более максимальное измельчение топлива (до 0,5 мм) и удаление влаги из топлива. Превращение кускового топлива в угольную пыль производится в два этапа: вначале сырое топливо подвергается дроблению до размера 15-25 мм. Затем измельченное топливо поступает в бункеры сырого угля, после чего подвергается размолу в углеразмольных мельницах до окончательного продукта - угольной пыли с размерами частиц до 0,5 мм. Одновременно с размолом топливо подсушивается для обеспечения хорошего сгорания пыли.
Системы приготовления топочной пыли - совокупность оборудования, необходимого для размола топлива, его сушки и подачи готовой пыли в горелки топочной камеры. Системы пылеприготовления бывают центральными и индивидуальными. В первом случае пыль приготовляется в одном месте и пылепроводами поступает к каждому из потребителей. Во втором случае пыль получают в оборудовании, находящемся непосредственно около потребителей.
Индивидуальные системы приготовления являются более простыми и надежными, чем центральные. Индивидуальные системы приготовления разделяют на: замкнутые (с прямым вдуванием пыли в топочную камеру или с промежуточным бункером пыли), разомкнутые (подача пыли с горячим воздухом).
2.2 Устройства для сгорания твердого пылевидного топлива
Необходимая интенсивность горения и полнота выгорания пылевидного топлива в топке достигаются правильной подачей топлива (аэропыли) и правильным смешением его с воздухом. Этот процесс осуществляется в горелочных устройствах или горелках. В горелках не происходит возгорания топлива. Их задача - подготовить два потока - пылевоздушную смесь и вторичный воздух - к воспламенению топлива и активному горению в топке.
Различают два вида горелок: вихревые и прямоточные. Через вихревые горелки в топку подаются закрученные струи пылевоздушной смеси, образуют в топке конусообразный факел. Прямоточные горелки подают в топку прямые струи аэропыли и воздуха. Перемешивание осуществляется взаимным расположением горелок в топке.
Прямоточные горелки отличаются от рассмотренных ранее вихревых меньшей турбулизацией выходящего потока. Поэтому хорошее и полное сжигание топлива достигается путем взаимодействия струй разных горелок в топочной камере. Они применяются в основном для сжигания бурых углей, торфа и каменных углей с высоким выходом летучих веществ. Скорость пылевоздушной смеси на выходе из горелок принимают равной V=20-28 м/с, а скорость воздуха Vв=(1,5-1,7)V.
Горелки на стенках топок располагают таким образом, чтобы обеспечить наилучшие условия сгорания топлива. Так, вихревые горелки создают более короткий факел по длине, но больший по углу раскрытия, чем прямоточные горелки. Перемешивание потоков происходит за счет энергии вихревого движения, что приводит к выгоранию 90-95% топлива.
3 Жидкие и газообразные топлива
3.1 Общая характеристика
Все ископаемые - твердые топлива и нефть - получились в процессе длительного преобразования исходной растительной массы и отмерших животных организмов под слоем земли или воды, причем этот процесс протекал с различной скоростью в направлении постепенного обуглероживания (углефикации) топлива, т.е. повышения в нем содержания углерода и уменьшения количества кислорода и водорода.
Сырая нефть является смесью органических соединений и включает в себя небольшое количество жидких сернистых и азотных соединений, парафинов и смол. После извлечения легких фракций и масел (бензина, лигроина, керосина, газойля, солярового масла) остаются сильновязкие тяжелые фракции - мазут, который и используется как энергетическое жидкое топливо. При этом минеральные примеси, входящие в нефть, концентрируются в мазуте.
Природные газы образуются одновременно с нефтью либо получаются в результате синтеза в присутствии воды и карбидов металлов на больших глубинах под воздействием высокого давления и температуры. Во многих случаях выход газов сопутствует добыче нефти. Это так называемые попутные газы, которые также возможно использовать в качестве энергетического топлива.
Преимущества жидких и газообразных топлив повышает общую культуру эксплуатации электростанций, но и приводит к ощутимому снижению стоимости основного оборудования, росту КПД установок. Так, при сооружении электростанций, сжигающих газ и мазут, удельные капиталовложения по сравнению с электростанцией, равной мощности на угле, снижаются на 20-24%, а экономичность газомазутных станций по отпуску электроэнергии на 4% выше, чем работающих на угле.
Однако разведанные запасы природных газов и нефти ограничены и составляют около 6% всех мировых запасов органических топлив. Кроме того, природные газы и нефть являются ценнейшим сырьем для народного хозяйства. Запасы же угля превышают 71% мировых разведанных ресурсов топлива и являются основным органическим топливом.
Вязкость топлива. Как техническая характеристика вязкость является важнейшим показателем качества мазута и положена в основу маркировки мазута.
Вязкость мазутов выражают в единицах кинематической вязкости (в сантистоксах - сСт) или в градусах условной вязкости (0ВУ). Для нормального транспорта по трубопроводам и тонкого распыления мазута в механических форсунках необходимо поддерживать его вязкость на уровне 2-3,50ВУ. Вязкость мазута сильно зависит от температуры. Изменение вязкости мазутов с температурой определяется присутствием в них углеводородов парафинового ряда. Для транспорта мазута по трубопроводам и нормальной работы мазутных насосов его температура должна поддерживаться около 60-700С.
Реологические свойства. При невысокой температуре (10-250С) сильно вязкий мазут обладает свойством налипать на стенки емкостей, труб, аппаратуры и прочно удерживаться на них тем большим слоем, чем ниже температура. Это явление определяется реологическим свойством мазута, т.е. способностью перестройки структуры углеводородных молекул с температурой. При нагреве мазута до 700С и выше он не налипает на стенки.
Плотность топлива. Обычно пользуются относительной плотностью мазутов (плотностью по отношению к плотности воды при температуре 200С). Последняя составляет 0,99-1,06. С повышением температуры относительная плотность мазутов уменьшается.
Зольность топлива. При переработке нефти содержащиеся в ней минеральные примеси концентрируются в основном в тяжелых фракциях, главным образом в мазуте. Золовой остаток после сжигания мазута невелик и составляет на сухую массу не более 0,1%. Особенностью золы мазута является наличие в ней ванадия, содержание которого может достигать 50% и более.
Влажность топлива. Содержание воды в мазуте обычно составляет 1-3%. Значительное его обводнение (до 10-15%) может происходить в процессе разогрева мазута перед сливом из цистерн за счет конденсации пара. Влага в небольшом количестве способствует распаду мазута и улучшает характеристики воспламенения. При повышенном содержании влаги растет опасность коррозионных процессов в конвективных поверхностях нагрева и увеличиваются потери теплоты с продуктами сгорания.
Сернистость топлива. Нефть и твердое топливо содержат серу в виде сложных серосодержащих соединений. В процессе сжигания мазута и твердого топлива сера окисляется и часть ее при избытке кислорода в зоне горения образует полный окисел S0з, создающий коррозионную среду для поверхностей нагрева. Количество серы в мазуте (0,5-3%) находится на уровне твердого топлива, но коррозионная опасность газовой среды после сжигания мазута в несколько раз выше.
Температура застывания. За температуру застывания принимают температуру нефтепродукта, при которой он загустевает настолько, что в пробирке при ее наклоне под углом 450 остается неподвижным в течение 1 мин. Высокой температурой застывания (25-350С) характеризуются высокосернистые мазуты с большим содержанием парафинов (марок М-100 и М-100В). Температура застывания оказывает непосредственное влияние на выбор технологической схемы хранения мазута и его транспорта.
Температура вспышки. За температуру вспышки принимают температуру, при которой пары мазута в смеси с воздухом вспыхивают при контакте с открытым пламенем. Мазут имеет температуру вспышки 90-1400С, у парафиниcтых мазутов она может снизиться до 600С, у сырой нефти составляет 20-400С. Во избежание пожара температура подогрева мазута в открытых системах должна быть ниже температуры вспышки и не выше 950С во избежание вскипания влаги, находящейся в толще мазута.
Основными техническими характеристиками природного газа являются плотность, взрываемость и токсичность.
Плотность газа. Почти все виды газового топлива легче воздуха, поэтому при утечке газ скапливается под перекрытиями. В целях безопасности перед пуском парового котла обязательно проверяют отсутствие газа в наиболее вероятных местах его скопления.
Взрываемость. Смесь горючего газа с воздухом в определенной пропорции при наличии огня или даже искры может взорваться, т.е. происходит процесс его воспламенения и сгорания со скоростью, близкой к скорости распространения звука. Взрывоопасные концентрации горючего газа в воздухе зависят от химического состава и свойств газа.
При концентрациях меньше нижнего предела воспламенения газовоздушная смесь не горит. При концентрациях газа в воздухе, превышающих верхний предел, газ горит без взрыва.
Токсичность. Под токсичностью понимают способность газа вызывать отравление живых организмов. Наиболее опасными в этом отношении компонентами газа являются окись углерода СО и сероводород Н2S
Поскольку в природном газе все его компоненты перемешаны равномерно, то концентрацию в воздухе вредных газов можно определить по присутствию метана, процентное содержание которого устанавливают прибором - метаномером. Одновременно определяется и вероятность взрывоопасной ситуации. Почти все природные газы совсем не имеют запаха. Для обнаружения утечки газа и принятия мер безопасности природный газ до поступления в магистраль одорируют, т.е. насыщают веществом, имеющим резкий запах.
3.2 Подготовка к сжиганию мазута и природного газа
Для перекачки мазута, заполнения и слива его из емкостей температура мазута должна быть не ниже 60-700С, что соответствует вязкости не выше 300ВУ.
Технологический тракт подготовки мазута (рис.3.1) включает: приемно-сливное устройство (сливные эстакады с желобами, приемные резервуары с погруженными перекачивающими насосами), основные резервуары для хранения постоянного запаса мазута, мазутонасосную, систему трубопроводов для мазута и пара, группу подогревателей мазута и фильтров. Подготовка мазута перед сжиганием заключается в удалении механических примесей, повышении давления мазута и его подогреве, необходимых для снижения потерь энергии на транспорт мазута к котлам электростанции и его тонкого распыления в форсунках горелочных устройств. Температура мазута в баках поддерживается на уровне 60-800С в любое время года за счет циркуляционного подогрева путем возврата в бак части (до 50%) разогретого во внешних подогревателях мазута.
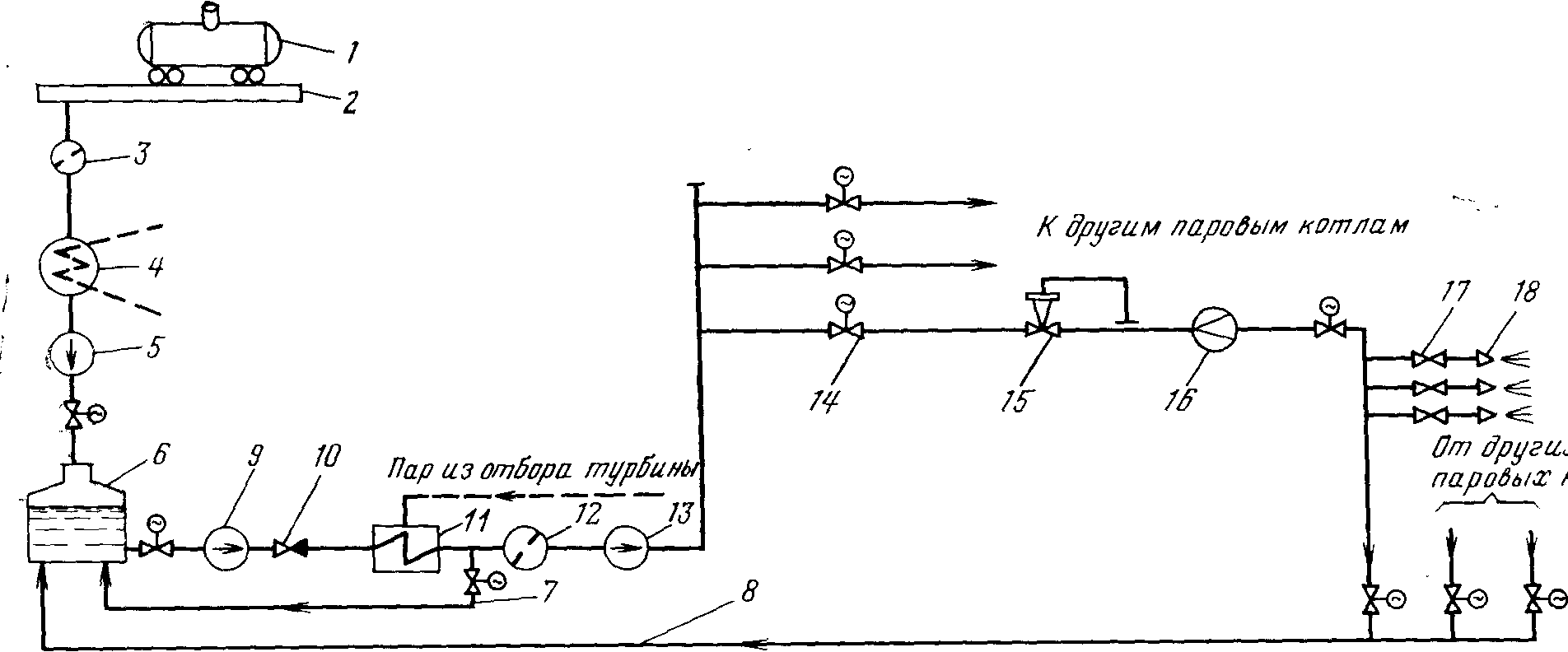
Рисунок 3.1 – Технологическая схема подготовки мазута на электростанции: 1- цистерна с мазутом; 2- сливное устройство; 3- фильтр грубой очистки; 4 – сливной резервуар с подогревом; 5 – перекачивающий насос; 6 – основной резервуар; 7, 8 – линии рециркуляции мазута; 9 – насос первого подъема; 10- обратный клапан; 11- подогреватель мазута; 12- фильтр тонкой очистки; 13- насос второго подъема; 14- запорная задвижка; 15 – регулятор расхода; 16 – расходомер; 17 – задвижка; 18 – форсунка
Данная схема является типовой двухступенчатой схемой подачи топлива. По этой схеме подача топлива в устройства для подготовки к сжиганию (подогрев, перемешивание мазута в резервуарах, фильтрация от внешних загрязнений) осуществляется при низком давлении мазута (около 1 МПа), а насосы второго подъема перекачивают в главное здание мазут при высоком давлении (3,5-4,5 МПа).
Повышение температуры мазута обеспечивается в паровых подогревателях до температуры, меньшей температуры вспышки паров. Для поддержания температуры мазута на нужном уровне независимо от потребления его обеспечивается непрерывный расход его через линию за счет частичного возврата в бак (рециркуляция).
Газ поступает на электростанцию от магистрального газопровода или газораспределительной станции (ГРС) с давлением 0,7-1,3 МПа. Для снижения давления поступающего газа до необходимого уровня у горелок (0,13-0,2 МПа) предусматривается его дросселирование в газорегуляторном пункте (ГРП), который ввиду повышенной взрывоопасности и резкого шума при дросселировании газа размещают в отдельном помещении.
3.3 Топочные камеры для жидкого и газового топлива
Условия сжигания природного газа и мазута имеют много общего, что позволяет выполнять топочные камеры для этих видов топлива одинаковой конструкции. Как правило, в таких топочных устройствах основным топливом является мазут, а резервным - природный газ. Близость характеристик сжигания газа и мазута выражается в следующих показателях:
- при практическом отсутствии внешней влаги в топливах образуются близкие объемы продуктов сгорания;
- горение мазута и газа происходит в парогазовом состоянии (гомогенная среда). Интенсивность горения в обоих случаях определяется условиями перемешивания;
- практическое отсутствие золы при сжигании этих топлив (мазут имеет Ас<0,3%) исключает вероятность шлакования стенок топки и необходимость в шлакоудаления;
- более легкие условия перемещения воздуха с топливом в газовом состоянии обеспечивают практически полное сжигание топлива с низкими избытками воздуха (гор=1,02-1,05) при одинаковой температуре его подогрева (Тг.в=250-3000С). Это позволяет выполнять комбинированные газомазутные горелки с близкими объемными расходами воздуха.
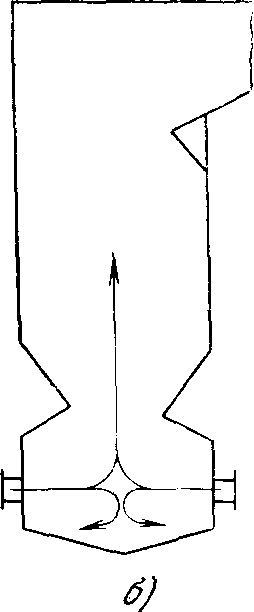
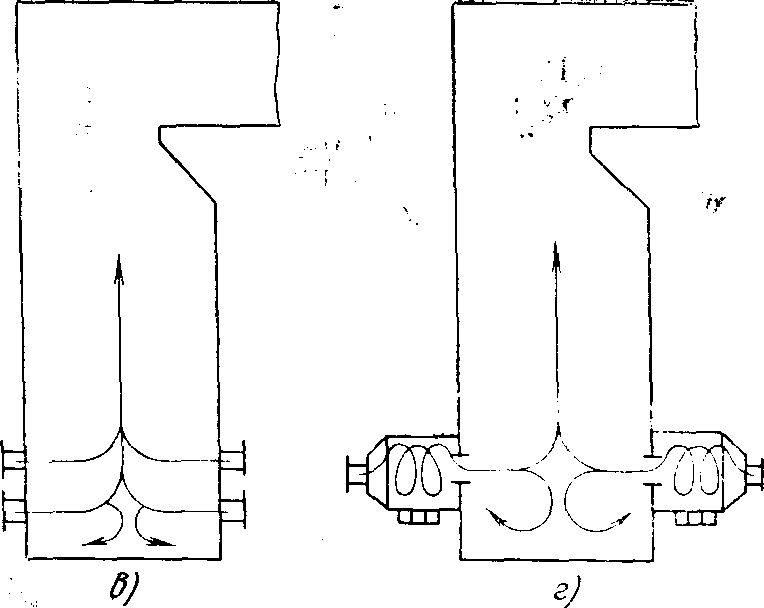
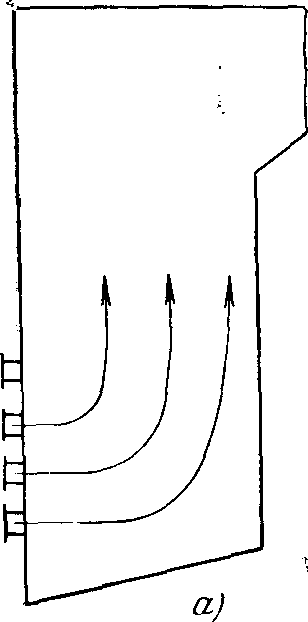
Рисунок 3.2 - Виды топочных камер газомазутных паровых котлов: а) открытая топка с однофронтальными многоярусными горелками; б) топка с пережимом и встречным (двухфронтальным) расположением горелок; в) открытая топка со встречным двухъярусным расположением горелок; г) топка со встречными циклонными предтопками
Тип горелок выбирают в зависимости от расположения горелок на стенах топки, исходя из обеспечения наилучшего заполнения топки факелом. В зависимости от метода распыления мазута различают механические, паромеханические и паровые форсунки.
Одним из преимуществ комбинированных горелок является возможность легкого перехода с одного вида топлива на другое. При этом сжигание каждого из них должно происходить в оптимальных условиях. Одновременное сжигание двух видов топлива приводит к ухудшению выгорания одного из них (чаще мазута), что связано с различными условиями смешения и временем воспламенения.
4 Технологическое оборудование производства тепловой энергии
Основным тепловым агрегатом любой теплоэлектростанции (ТЭС) является паровой котел. Паровой котел представляет собой системы поверхностей нагрева для производства пара из непрерывно поступающей в него воды путем использования теплоты, выделяющейся при сжигании топлива, которое подается в топку вместе с необходимым для горения воздухом. Поступающую в паровой котел воду называют питательной водой. Питательная вода подогревается до температуры насыщения, испаряется, а выделившийся из кипящей (котловой) воды насыщенный пар перегревается.
При сжигании топлива образуются продукты сгорания, которые на поверхностях нагрева отдают теплоту воде и пару, называемой рабочим телом. После поверхностей нагрева продукты сгорания при относительно низкой температуре удаляются из котла через дымовую трубу в атмосферу. В результате горения твердого топлива остаются зола и шлак, которые также удаляются из котла.
В число устройств и механизмов, обеспечивающих работу парового котла, входят: топливоприготовительные устройства; питательные насосы (подающие в котел питательную воду); дутьевые вентиляторы (подающие воздух для горения); дымососы (для отвода продуктов сгорания через дымовую трубу в атмосферу) и др. Паровой котел и весь комплекс перечисленного оборудования составляют котельную установку. Современная мощная котельная установка представляет собой сложное техническое сооружение для производства пара, в котором все рабочие процессы полностью механизированы.
4.1 Классификация паровых котлов
В соответствии с законами фазового перехода получение перегретого пара характеризуется последовательным протеканием следующих процессов: подогрева питательной воды до температуры насыщения, парообразования и перегрева насыщенного пара до заданной температуры. Эти процессы имеют четкие границы протекания и осуществляются в трех группах поверхностей нагрева. Подогрев воды до температуры насыщения происходит в экономайзере, образование пара - в парообразующей (испарительной) поверхности нагрева, перегрев пара - в пароперегревателе.
В целях непрерывного отвода теплоты и обеспечения нормального температурного режима металла поверхностей нагрева рабочее тело в них - вода в экономайзере, пароводяная смесь в парообразующих трубах и перегретый пар в пароперегревателе - движется непрерывно.
Различают паровые котлы с естественной циркуляцией, с принудительной циркуляцией и прямоточные.
4.2 Технологическая схема производства пара
В отечественной энергетике наиболее широкое распространение получили паровые котлы с П-образным профилем (рис.4.1).
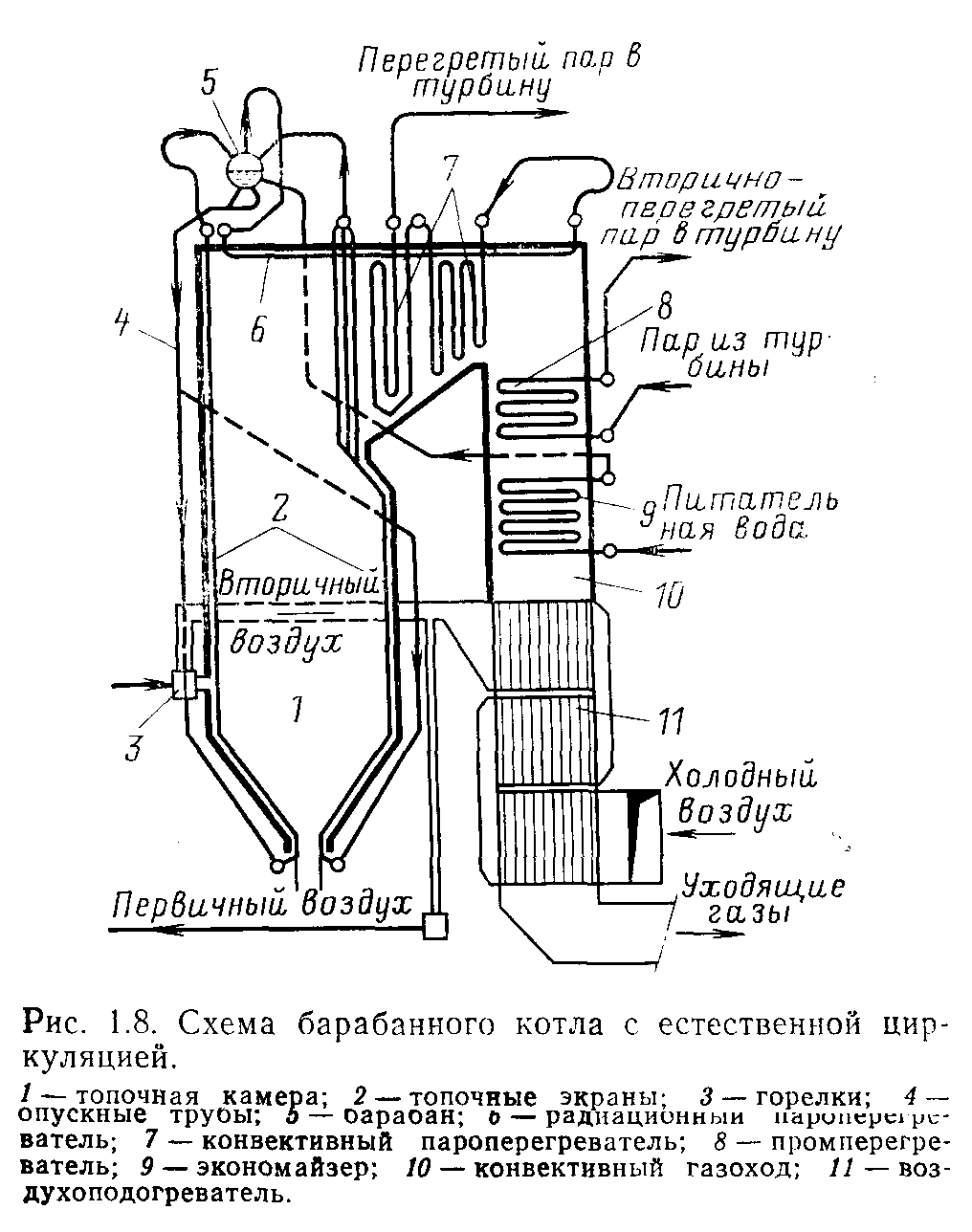
Рисунок 4.1 - Схема барабанного котла с естественной циркуляцией: 1 - топочная камера; 2 - топочные экраны; 3 -горелки; 4 - опускные трубы; 5 - барабан; 6 - радиационный пароперегреватель; 7 - конвективный пароперегреватель; 8 - пароперегреватель; 9 - экономайзер; 10 - конвективный газоход; 11 - воздухоподогреватель
Это две вертикальные призматические шахты, соединенные вверху горизонтальным газоходом. Первая шахта является топочной камерой. В зависимости от мощности агрегата и сжигаемого топлива ее объем колеблется в широких пределах - от 1000 до 30000 м3 и более. В топочной камере по всему периметру и вдоль всей высоты стен обычно располагаются трубные плоские системы - топочные экраны.
Вторая вертикальная шахта и соединяющий ее с топочной камерой горизонтальный газоход служат для размещения поверхностей нагрева, получающих теплоту конвекцией и потому называются конвективными газоходами, а сама вертикальная шахта-конвективной шахтой.
После отдачи теплоты топочным экранам продукты сгорания покидают топку при температуре 900-12000С (в зависимости от вида топлива) и поступают в горизонтальный газоход.
По мере движения в трубах топочных экранов вода превращается в пар.
Питательная вода содержит примеси. В процессе парообразования увеличивается содержание пара, концентрация примесей возрастает. При достижении определенных концентраций в конце зоны парообразования на внутренней поверхности труб образуются отложения в виде накипи. Теплопроводность отложений в десятки раз меньше теплопроводности металла, из которого выполнены поверхности нагрева. Это ухудшает теплопередачу к рабочей среде и при интенсивном обогреве в топочной камере приводит к перегреву металла труб, снижению прочности и разрыву под действием внутреннего давления рабочей среды.
Из конвективного пароперегревателя перегретый пар заданных параметров (давления и температуры) направляется в турбину. Частично отработавший в турбине пар снова направляют в паровой котел для вторичного (промежуточного) перегрева до температуры, обычно равной температуре пара, выдаваемого основным пароперегревателем. Этот пароперегреватель получил название промежуточный.
На выходе из промежуточного пароперегревателя продукты сгорания имеют еще высокую температуру (500-6000С) и поэтому содержащуюся в них теплоту утилизируют в конвективном экономайзере. В него поступает питательная вода, которая подогревается до температуры, меньшей температуры насыщения. За экономайзером температура продуктов сгорания составляет 300-4500С и более. Дальнейшая утилизация теплоты осуществляется в следующей конвективной поверхности нагрева для подогрева воздуха - воздухоподогревателе. Воздухоподогреватель представляет собой систему вертикальных труб, через которые проходят продукты сгорания, а между трубами - нагреваемый воздух. Температура воздуха на входе в воздухоподогреватель (холодный воздух) 30-600С, на выходе (горячий воздух) 250-4200С в зависимости от топлива и способа его сжигания.
При сжигании твердого топлива в пылевидном состоянии горячий воздух делят на два потока. Первичный воздух служит для подсушки топлива при размоле и транспорта готовой топливной пыли через горелки в топочную камеру. Температура топливно-воздушной смеси 70-1300С. Вторичный воздух поступает через горелки в топку непосредственно (минуя мельничную систему) при температуре за воздухоподогревателем.
После воздухоподогревателя продукты сгорания имеют уже достаточно низкую температуру (110-1600С). Дальнейшая утилизация теплоты этих продуктов сгорания экономически нецелесообразна, и их выбрасывают дымососом через дымовую трубу в атмосферу. Они получили название - уходящие газы.
В результате сжигания топлива остается зола, которая в основной массе уносится продуктами сгорания. Ее улавливают в золоуловителе, размещаемом перед дымососом. Этим предотвращаются абразивный износ дымососов и загрязнение атмосферы золой. Уловленная зола удаляется устройствами золоудаления. Часть золы выпадает в нижнюю часть топки.
4.3 Котельные установки и их оборудование
Комплекс оборудования, предназначенный для превращения энергии горения топлива в тепловую энергию, выдаваемую потребителю в виде воды с высокой температурой или водяного пара, называются котельной установкой.
С целью обеспечения стабильной и безопасной работы котельной установки ее снабжают дополнительным оборудованием: тягодутьевые установки (вентилятор, дымосос, дымовая труба) для подачи воздуха в топки и удаления продуктов сгорания из котлоагрегата; золоулавливающее устройство для очистки продуктов сгорания от золы с целью охраны окружающей атмосферы от загрязнения; питательные насосы для подачи воды в котлоагрегат; оборудование для сушки и размола топлива. Кроме того, котельная установка имеет дополнительное вспомогательное оборудование, обеспечивающее нормальную ее эксплуатацию. К такому оборудованию относятся устройства для подачи топлива к установке, устройство для удаления шлака, золы, система водоподготовки для котлов, т.е. обработки воды с целью удаления из нее растворимых солей и газов.
Котельные установки, снабжающие паром турбины тепловых электростанций, называют энергетическими. Для снабжения паром производственных потребителей и отопления зданий в ряде случаев создают специальные производственные и отопительные котельные установки.
К отопительным котельным, которые, как правило, бывают водогрейными (но могут быть и паровыми) - относятся котельные, обслуживающие системы отопления и работающие вследствие этого лишь в течение отопительного периода.
Отопительно-производственные котельные (обычно только паровые) вырабатывают тепло не только для целей отопления, но и для вентиляции, горячего водоснабжения и технологических процессов.
Технологическое котельное оборудование может все находиться в здании или частично располагаться вне его. В зависимости от этого котельные подразделяются на закрытые, в которых все оборудование находится в здании, полуоткрытые, в которых часть вспомогательного оборудования располагается снаружи, и открытые, в которых под укрытием находятся только зоны обслуживания котлов.
4.4 Потери тепла
Потеря тепла с уходящими газами является наибольшей из всех тепловых потерь. Величина их составляет в крупных агрегатах 4-8%, а в мелких котлах - 10-20%. Эта потеря имеет место потому, что продукты сгорания топлива оставляют агрегат при высокой температуре (в крупных агрегатах 115-1500С, в мелких - еще выше).
Для уменьшения потерь, соответственно увеличения КПД, необходимо глубокое охлаждение газов в агрегате. Предел целесообразной глубины охлаждения продуктов сгорания определяется технико-экономическими расчетами, так как при слишком глубоком охлаждении газов сильно растут необходимые размеры тепловоспринимающей поверхности нагрева. В крупных котлоагрегатах при сжигании сухих топлив температура уходящих газов составляет 115-1300С.
Потеря тепла от химической неполноты сгорания определяется суммарной теплотой сгорания продуктов неполного горения, содержащихся в уходящих газах. Как уже отмечалось, при налаженном процессе сжигания в продуктах горения не может быть заметного количества окиси углерода.
Причиной возникновения этих потерь чаще всего бывает неудовлетворительное использование кислорода вследствие несовершенного перемешивания топлива с воздухом и неудовлетворительной аэродинамики топки. Кроме того, могут быть и другие причины: недостаточное общее количество подводимого воздуха, низкая температура топки и т.п. В топках рациональной конструкции при нормальной их эксплуатации величина потерь составляет менее 1%.
Потеря тепла от механической неполноты сгорания при сжигании твердого топлива происходит тогда, когда удаляемый из топки шлак в провал, а также уносимая в газоходах летучая зола содержит некоторое количество горючих веществ (углерода).
Величина потерь зависит от свойств топлива (зольности, выхода летучих веществ, спекаемости), типа топки (камерная, слоевая, механическая, ручная), режима процесса сжигания и колеблется в широких пределах - от 1-2% для крупных камерных топок до 10-15% в мелких установках.
Потеря тепла от наружного охлаждения обусловлена тем, что наружная поверхность обмуровки котлоагрегата и изоляции его деталей имеют более высокую температуру, чем воздух и стены котельной. Потеря тем меньше, чем больше единичная производительность агрегата. Для данного агрегата потеря уменьшается с ростом степени его нагрузки.
Для мощных энергетических котлоагрегатов величина потерь мала и составляет доли процента (0,2-0,3%). В мелких установках может достигать значений 3-4%.
Потеря с физическим теплом шлака в большинстве случаев невелика.
5 Типы и принципиальные схемы тепловых электростанций
5.1 Тепловая электрическая станция (ТЭС)
ТЭС - это совокупность взаимосвязанных установок, общим технологическим назначением которых является преобразование химической энергии сжигаемого топлива в электрическую (рис.5.1).

Рисунок 5.1 - Схема преобразования энергии на ТЭС
Первичными двигателями на тепловых электростанциях являются паровые и газовые турбины, двигатели внутреннего сгорания.
Станции с газовыми турбинами на современном этапе не могут конкурировать с паротурбинными. Единичные мощности газотурбинных агрегатов пока не превышают 40-50 тыс.кВт, технико-экономические показатели заметно ниже. Однако высокая маневренность (простота и быстрота процессов пуска и остановки) делает целесообразным применение их для покрытия кратковременных «пиков» нагрузки энергосистем.
Различают два типа паротурбинных тепловых электростанций:
1) конденсационные, вырабатывающие только электрическую энергию;
2)теплофикационные или когенерационные (теплоэлектроцентрали), где осуществляется комбинированная выработка электрической и тепловой энергии; горячая вода или пар передаются от теплоэлектроцентралей по трубопроводам промышленным и коммунально-бытовым потребителям.
5.2 Электростанции конденсационного типа (КЭС)
Электростанции конденсационного типа (КЭС) являются наиболее распространенным типом тепловых электростанций (рис.5.2).
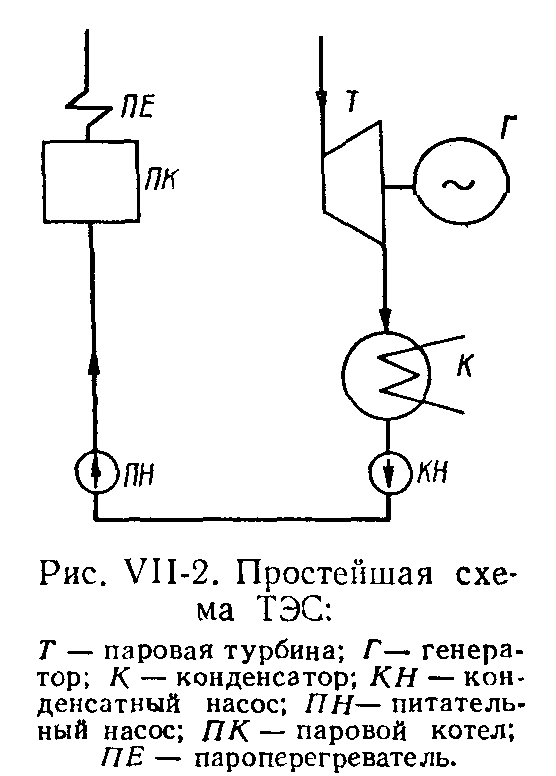
Рисунок 5.2 - Простейшая схема КЭС: Т- паровая турбина; Г - генератор; К- конденсатор; КН- конденсатный насос; ПН - питательный насос; ПК - паровой котел; ПЕ - пароперегреватель
Пар, отработавший в паровых турбинах этих станций, направляется в конденсаторы. Конденсат откачивается насосами и как питательная вода направляется в котлы.
Охлаждающая вода по выходе из конденсаторов обладает низким температурным потенциалом (25-350С), в связи с чем она не может быть использована как теплоноситель, и тепло, заключенное в ней, теряется.
Как показывают термодинамические расчеты, на современных КЭС может быть превращено в электроэнергию немногим более 40% тепла израсходованного топлива. Неизбежный отвод тепла из цикла в окружающую среду (через конденсатор) приводит к потере более половины всего тепла, подводимого к циклу.
На теплоэлектростанциях (ТЭЦ) достигается более высокая экономичность, поскольку тепло отработавшего в турбинах пара полностью или частично используется потребителями. Полезная отдача энергии на ТЭЦ при благоприятном сочетании электрической и тепловой нагрузок достигает 60-70%.
Подогрев сетевой воды для нужд централизованного отопления производится на ТЭЦ в бойлерах (сетевых подогревателях), где тепло отработавшего пара воспринимается водой.
В то же время даже при максимальной централизации теплоснабжения на базе промышленных и районных ТЭЦ последними может быть обеспечено не более 27-30% требуемой электроэнергии. Таким образом, несмотря на то, что КПД конденсационных электростанций значительно уступает КПД ТЭЦ, превалирующее место КЭС в энергосистемах сохранится и в дальнейшем.
В состав тепловой электростанции входят: топливное хозяйство и система подготовки топлива к сжиганию; котельная установка - совокупность котла и вспомогательного оборудования; турбинная установка - совокупность турбины и вспомогательного оборудования; установки водоподготовки и конденсатоочистки; системы технического водоснабжения, система золошлакоудаления; электротехническое хозяйство; система управления энергооборудованием. Совокупность каналов (воздуховодов и газоходов) и различных элементов оборудования, по которым проходят воздух и дымовые газы, образуют газовоздушный тракт тепловой электростанции. Входящие в его состав дымососы, дымовая труба и дутьевые вентиляторы составляют тягодутьевую установку.
Для надежной и экономичной работы тепловых электростанций необходима правильная организация водного режима котельных агрегатов. Природная вода без соответствующей подготовки не может служить добавкой к турбинному конденсату, так как в ней содержатся механические примеси, различные растворенные соли и газы. Попадая в котел, растворенные в воде твердые вещества образуют накипь и шлам, а растворенные коррозионно-активные газы (кислород и углекислый газ) вызывают коррозию стенок котлов.
Цель обработки исходной воды - умягчение, т.е. уменьшение содержания в воде кальциевых и магниевых солей, определяющих ее жесткость, либо обессоливание воды. Существует ряд способов умягчения воды: термические, реагентные, ионного обмена, комбинированные.
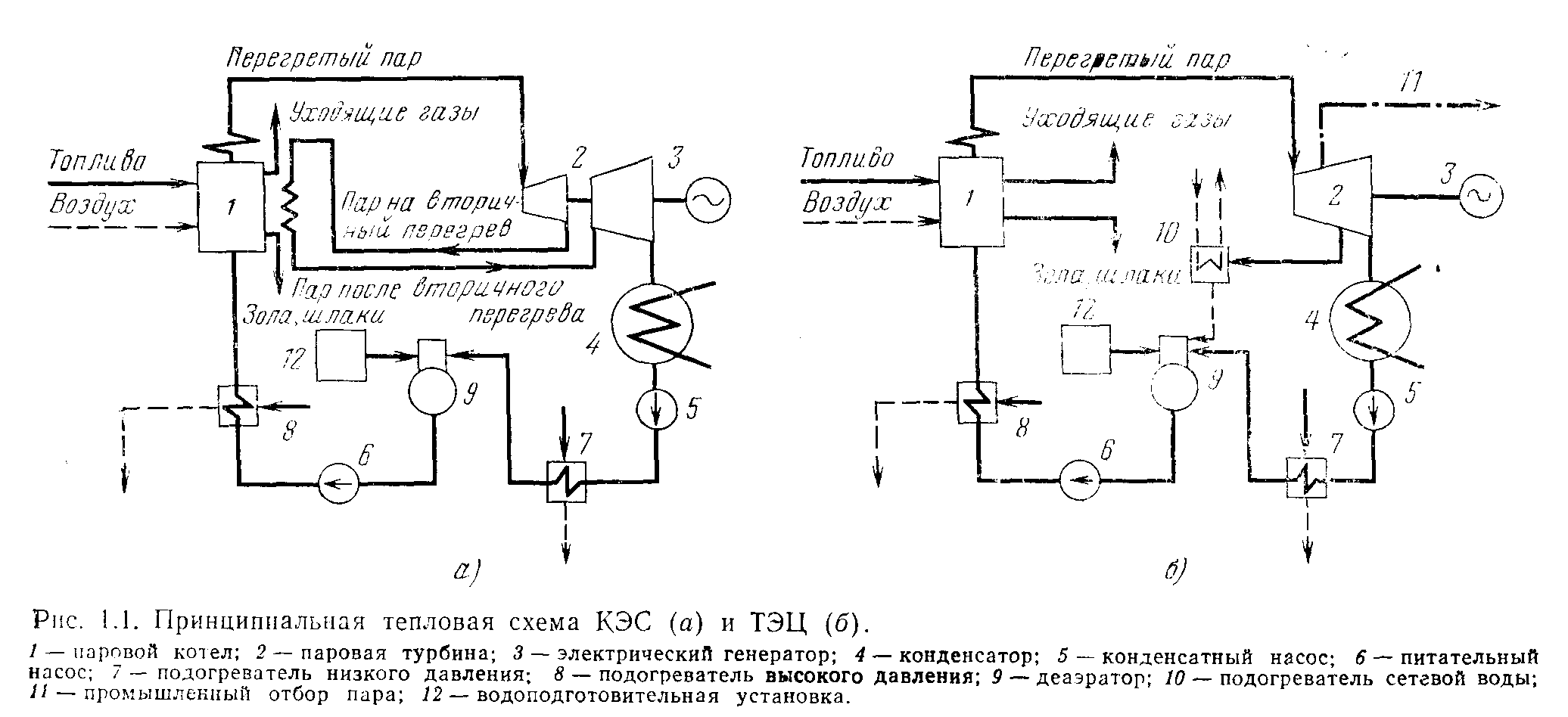
Рисунок 5.3 – Принципиальная тепловая схема КЭС (а) и ТЭЦ (б): 1- паровой котел; 2- паровая турбина; 3- электрический генератор; 4- конденсатор; 5- конденсатный насос; 6- питательный насос; 7 – подогреватель низкого давления; 8 – подогреватель высокого давления; 9- деаэратор; 10- подогреватель сетевой воды; 11 -промышленный отбор пара; 12- водоподготовительная установка
5.3 Общий принцип производства тепловой энергии пара
При сжигании топлива химически связанная энергия превращается в тепловую, образуются продукты сгорания, теплоноситель, которые в поверхностях нагрева котла отдают теплоту воде и образующемуся из нее пару.
Совокупность оборудования, отдельных его элементов, трубопроводов, по которым движутся вода и пар, образует водопаровой тракт станции.
В котле вода нагревается до температуры насыщения, испаряется, а образовавшийся из кипящей (котловой) воды насыщенный пар перегревается. Из котла перегретый пар направляется по трубопроводам в турбину, где его тепловая энергия превращается в механическую, передаваемую валу турбины. Отработавший в турбине пар поступает в конденсатор, отдает теплоту охлаждающей воде и конденсируется.
На современных тепловых электростанциях с агрегатами единичной мощностью 200 МВт и выше применяют промежуточный перегрев пара. В этом случае турбина имеет две части: часть высокого и часть низкого давления.
Отработав в части высокого давления турбины, пар направляется в промежуточный перегреватель, где к нему дополнительно подводится теплота. Далее пар снова возвращается в турбину, в часть низкого давления, а из нее поступает в конденсатор. Промежуточный перегрев пара увеличивает КПД турбинной установки и повышает надежность ее работы.
Из конденсатора конденсат откачивается конденсатным насосом и, пройдя через подогреватели низкого давления (ПНД), поступает в деаэратор. Здесь он нагревается паром до температуры насыщения, при этом из него выделяются и удаляются в атмосферу кислород и углекислота для предотвращения коррозии оборудования. Из деаэратора деаэрированная вода, называемая питательной водой, питательным насосом прокачивается через подогреватели высокого давления (ПВД) и подается в котел.
Конденсат в ПНД и деаэраторе, а также питательная вода в ПВД подогреваются паром, отбираемым из турбины. Такой способ подогрева означает возврат (регенерацию) теплоты в цикл и называется регенеративным подогревом. Благодаря ему уменьшается поступление пара в конденсатор, а следовательно, и количество теплоты, передаваемой охлаждающей воде, что приводит к повышению КПД паротурбинной установки.
В конденсаторе охлаждающей воде передается около 55% теплоты пара, поступающего в турбину; эта часть теплоты не используется для выработки электроэнергии и бесполезно пропадает.
Эти потери значительно уменьшаются, если отбирать из турбины частично отработавший пар и его теплоту использовать для технологических нужд промышленных предприятий или для подогрева воды на отопление. Таким образом, станция становится теплоэлектроцентралью (ТЭЦ), обеспечивающей комбинированную выработку электрической и тепловой энергии. На ТЭЦ устанавливаются специальные турбины с отборами пара - так называемые теплофикационные.
Конденсат пара, отданного тепловому потребителю, подается на ТЭЦ насосом обратного конденсата. На ТЭС существуют внутренние потери конденсата и пара, обусловленные неполной герметичностью водопарового тракта, а также безвозвратным расходом пара и конденсата на технические нужды станции. Они составляют небольшую долю общего расхода пара на турбины (около 1-1,5%).
На ТЭЦ могут быть и внешние потери пара и конденсата, связанные с отпуском теплоты промышленным потребителям. В среднем они равны 35-50%. Внутренние и внешние потери пара и конденсата восполняются предварительно обработанной в водоподготовительной установке добавочной водой.
Таким образом, питательная вода котлов представляет собой смесь турбинного конденсата и добавочной воды.