Принципы и задачи проектирования 1 Уровни, аспекты и этапы проектирования
Вид материала | Документы |
СодержаниеПостановка задачи синтеза маршрутов обработки 1 — возможные варианты; 2 — |
- Лекция: Организация разработки ис: Каноническое проектирование ис. Стадии и этапы процесса, 312.68kb.
- А. П. Марков Технологические практикум, 91.28kb.
- "Сапр web pack ise. Этапы и технология проектирования устройств на базе плис. Примеры, 449.82kb.
- А. Е. Стешков методология проектирования металлорежущих инструментов, 74.74kb.
- 1 Цели и задачи курсового проектирования, 12.27kb.
- Программа дисциплины Проектирование информационных систем Семестры, 9.14kb.
- С. П. Колотовкин организация курсового проектирования, преддипломной практики и дипломного, 276.32kb.
- Список билетов для экзамена по курсу Моделирование и исследование систем, 99.07kb.
- 05. 13. 12 Системы автоматизации проектирования (по отраслям) Формула специальности, 21.27kb.
- Методы автоматизированного проектирования системы прогнозирования землетрясений 05., 315.41kb.
Постановка задачи синтеза маршрутов обработки
поверхности детали
При построении графа принимались во внимание заданные глубины резания на каждом переходе, которые могут существенно отличаться от фактических, упругие отжатия, износ инструмента и т. д. Граф, построенный по изложенной методике, формально описывает возможные варианты обработки какой-то детали из определенной заготовки на заранее выбранном оборудовании. Каждому ребру произвольной цепи, построенному для конкретного заданного значения глубины резания ti и подачи Si, будет соответствовать определенная технологическая себестоимость Cnep i при выполнении данного перехода i. Поэтому задача оптимизации структуры плана маршрута многопереходной обработки поверхностей деталей формально может быть представлена следующим образом: среди определенного множества цепей графа, построенного для конкретного случая обработки, нужно отыскать цепь, удовлетворяющую ограничениям и дающую минимальное значение целевой функции:
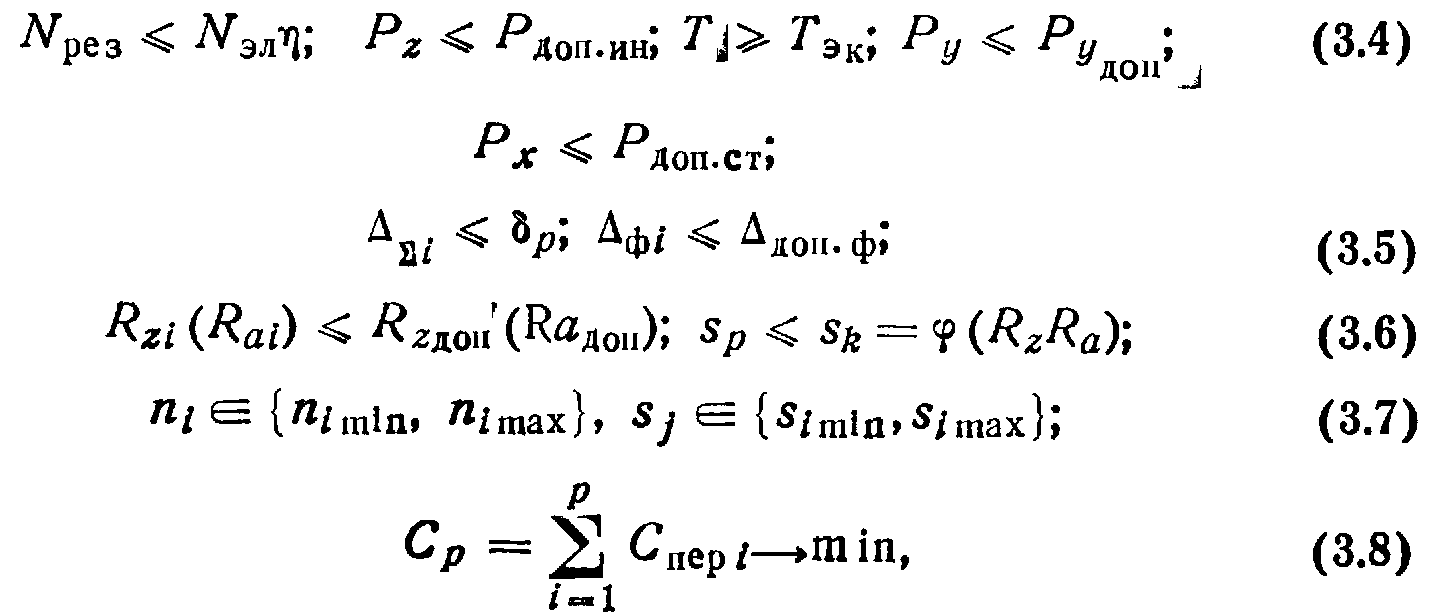
где Nрез—мощность, расходуемая на резание; Рz, Py, Px—тангенциальная, радиальная и осевая составляющие усилий резания; Δi—суммарная погрешность обработки; Δфi — отклонение формы; Nэлη — мощность привода станка; Рдоп.ин—допускаемая нагрузка на инструмент; Т— стойкость инструмента; Тэк—экономическая стойкость инструмента; Рудоп— допускаемая радиальная сила резания; Рдоп.ст—усилие, допускаемое механизмом подачи станка; р—допуск на размер; Δдоп.ф—допускаемое отклонение формы обрабатываемой поверхности; Rz—высота неровности; Рzдоп—допускаемая высота неровности; Ра —среднее арифметическое отклонение профиля; Рzдоп —допускаемое среднее арифметическое отклонение профиля; Sp—значение подачи при выполнении р-го перехода; Sk—значение подачи, обеспечивающее требуемое значение Рz или Ra ; ni и si—частота вращения шпинделя и подача на i-м переходе; {nimin, nimax} — предельные значения частот вращения шпинделя по паспортным данным станка; {Simin, Simax} — предельные значения подач по паспортным данным; Сперi—технологическая себестоимость i-го перехода.
В качестве целевой функции можно принимать себестоимость Ср выполнения р переходов при обработке
поверхности
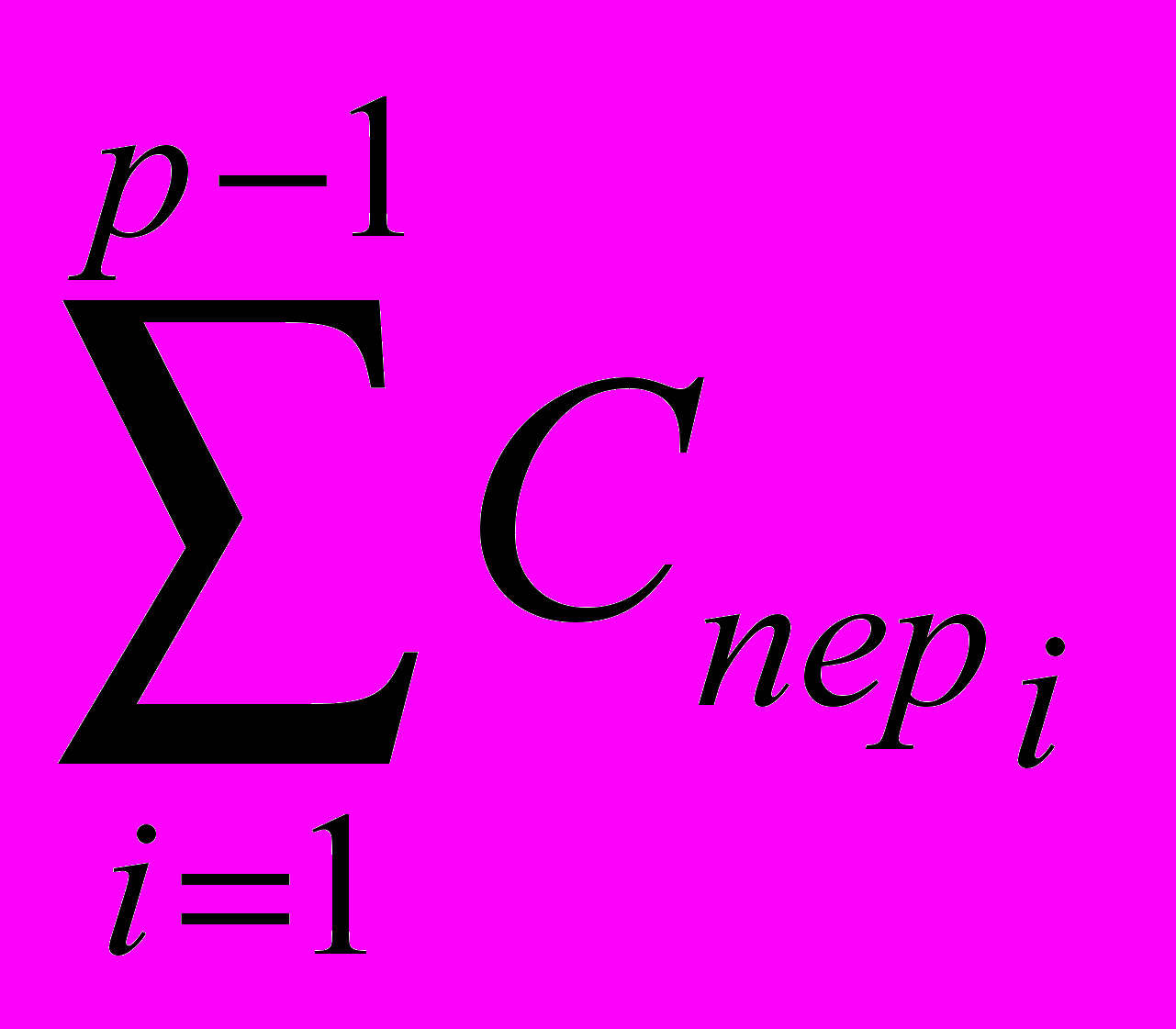
t’шт, оперативное t’on или основное to.
Условия (3.4) используют только на черновых переходах. В каждом конкретном случае отдельные ограничения можно не учитывать, если они не активны.
Оптимальное решение находится путем определения экстремального значения функции (3.8) для всего подмножества ребер, исходящих из каждой вершины.
3.5.3 Решение задачи синтеза маршрута обработки
поверхности детали
Для поиска оптимального варианта плана маршрута обработки поверхностей используют динамическое программирование. Общей особенностью моделей динамического программирования является сведение задач принятия решений к получению рекуррентного соотношения, которое можно представить как

где fn {рi) — технологическая себестоимость, отвечающая стратегии минимальных затрат для плана обработки от технологического перехода рi, если до последнего перехода остается п шагов; Срi — технологическая себестоимость при выполнении технологического перехода pi, причем переход pi предшествует переходу pj.
Возможные варианты обработки поверхности могут быть представлены в виде сети или графа.
Методика поиска наилучшего варианта маршрута обработки поверхности предусматривает распределение заданного общего минимального припуска Zo min на N этапов. Величина припуска на первом этапе (нумерация этапов ведется от поверхности обработанной детали) равна l 1= tmin, где tmin —наименьшая глубина резания, допускаемая процессом резания. Величина припуска на втором этапе l2 = tmin +, на третьем — l3 = tmin +2 и т. д. Величина припуска на этапе с номером т равна lmin = tmin +(m-1). Шаг определяется возможностью станка перемещать режущий инструмент или заготовку на заданный настроечный размер.
Поверхность заготовки в процессе обработки может иметь ряд значений промежуточных технологических допусков: 3, i, Д (3—допуск на размер поверхности заготовки; i —промежуточный допуск на размер; Д— допуск на размер поверхности детали).
Выбор оптимального варианта проводится начиная с первого этапа. Этот этап соответствует заключительному переходу обработки поверхности и при назначении его необходимо знать параметры предшествующего перехода. Располагая зависимостью суммарной погрешности обработки от управляемых переменных, т. е. i = f(t, s, v), где t—глубина резания; s—подача; v— скорость резания, для конкретного метода механической обработки резанием и зная параметры планируемого перехода, можно было бы рассчитать ожидаемую погрешность обработки. Однако, не имея данных о предпоследнем переходе, делают различные предположения о том, какая погрешность обработки может иметь место после его выполнения. Следуя принципу оптимальности динамического программирования, для каждого из этих предположений необходимо выбрать такие переменные, чтобы на заключительном переходе получить оптимальное решение. Этот принцип сохраняется при выборе оптимального варианта на каждом этапе.
На этапе 1 для уменьшения количества расчетных вариантов перебор возможных допусков 1,i начинают с 1,i = 3. При этом глубина резания t1 = tmin +1,i + Д. Определяют ожидаемую погрешность обработки. Если i Д то для этого варианта вычисляются значения целевой функции (рекуррентное соотношение) :

где минимум берется по всем подачам из массива подач А(S).
Подача Sдоп в этом случае должна удовлетворять ограничению, связанному с шероховатостью поверхности детали Sдоп SRz, где SRz — подача, обеспечивающая заданную величину неровности Rz- Значения допусков на отклонение размера поверхности после предшествующего перехода на этапе 1, обеспечивающее Д , образуют массив A1().
На этапе 2 - l2 = tmin + , глубина резания t2 = (tmin +) + 2,i + Д, а рекуррентное соотношение
С2(2,i ) = min g2( t2 , 2,i Sдоп , ) (3.11)
Поэтому план нахождения g2( t2 , 2,i Sдоп , ) обеспечивает заданный параметр точности Д обработанной поверхности и образует массив А2() промежуточных допусков.
Однако на этапе 2 возможна обработка поверхности за один переход (р=1) и за два перехода (р=2). При р=2 необходимо обеспечить не только заданный допуск Д , но и допуск ранее выполненного перехода (этапа) k, принадлежащего массиву допусков А(), для которого уже имеется план обработки. При этом максимально возможная подача определяется ограничениями по мощности привода станка, прочности и стойкости режущего лезвия инструмента и т. д.
Глубина резания на этапе r при р==2

Подставляя значения подач s{smin, Smax}, допусков Аr(){Аr()min, Аr()max }, можно рассчитать ожидаемую погрешность на этапе r, т. е. r, i , и проверить условиеr, i R . В результате образуются массивы допусков Аr()и подач Аr(S). Так как при одном и том же допуске заготовки , r ,i при разных значениях подачи можно получить различные допуски r, j предшествующего этапа, то варианты на этапе r будут отличаться по технологической себестоимости.
Сравнивая возможные однопереходные и двухпереходные планы обработки, можно составить вариант с наименьшим значением технологической себестоимости:
Сr=(r, i) = min gr( tr , Sr,i , Sдоп , ) (3.12)
Возможны планы обработки за один (p=1), два (p=2) и три (p=3) перехода. Величина припуска на этапе будет lq = tmin +(q-1).
Первый и второй варианты маршрута обработки определяются расчетом аналогично расчету ранее рассмотренного этапа с номером r.
При трехпереходном маршруте обработки p=3, tq= (q-r)+q, i находят значения q, i и Sq, i, которые образуют соответственно массивы допусков Аq()и подач Аq(S) на этапе q при условии q, i r, i. Технологическая себестоимость обработки при р==3 складывается из себестоимости обработки и величины Сг(r, i).
В общем случае для этапа с номером и1 возможны различные варианты маршрутов обработки поверхности р=1 и p>1. Величина припуска на этапе и будет 1и= tmin+(u - 1). Тогда рекуррентное соотношение будет иметь вид
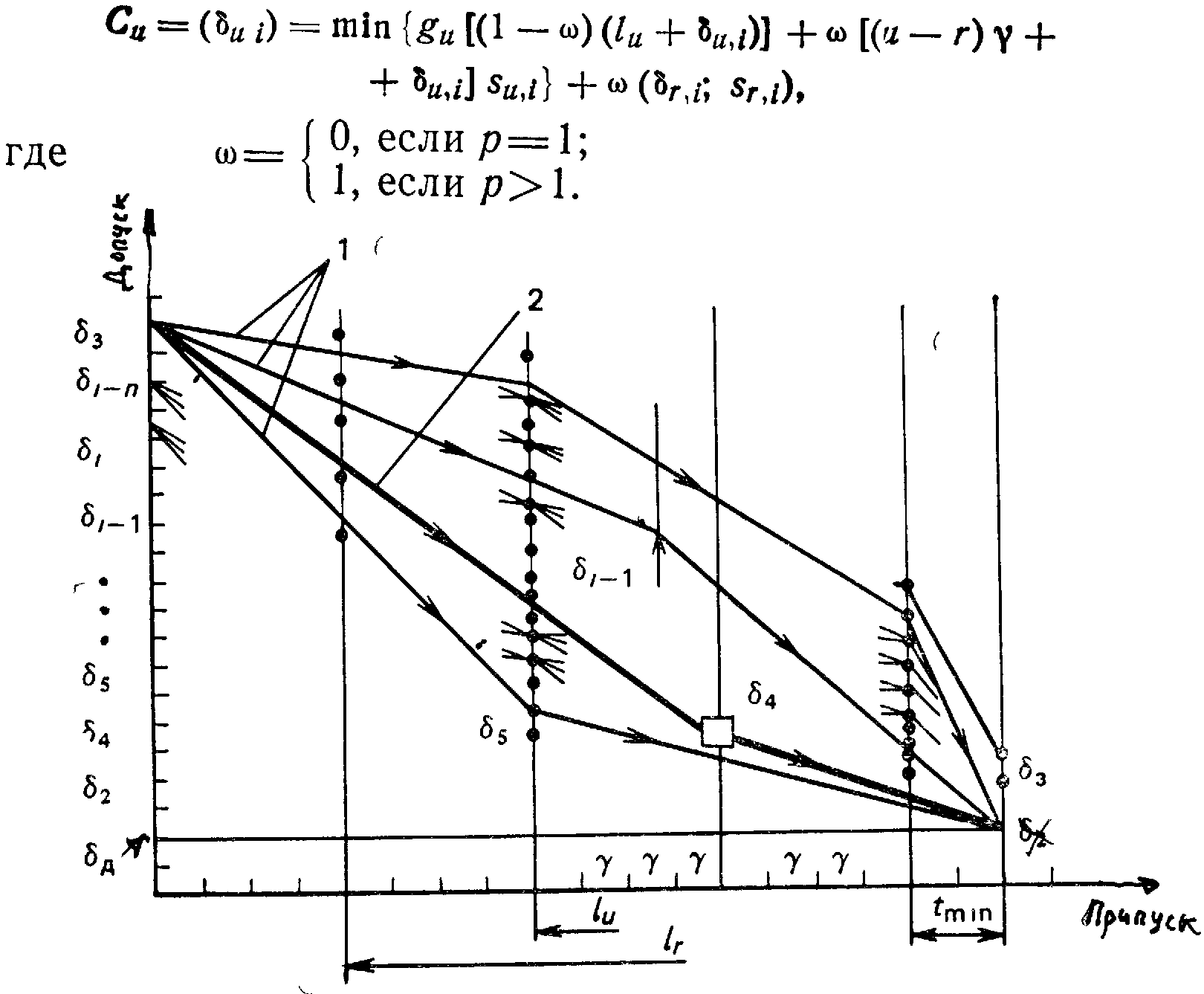
Рисунок 3.9 - Общая схема нахождения оптимального варианта плана маршрута обработки поверхности детали:
1 — возможные варианты; 2 — оптимальный вариант
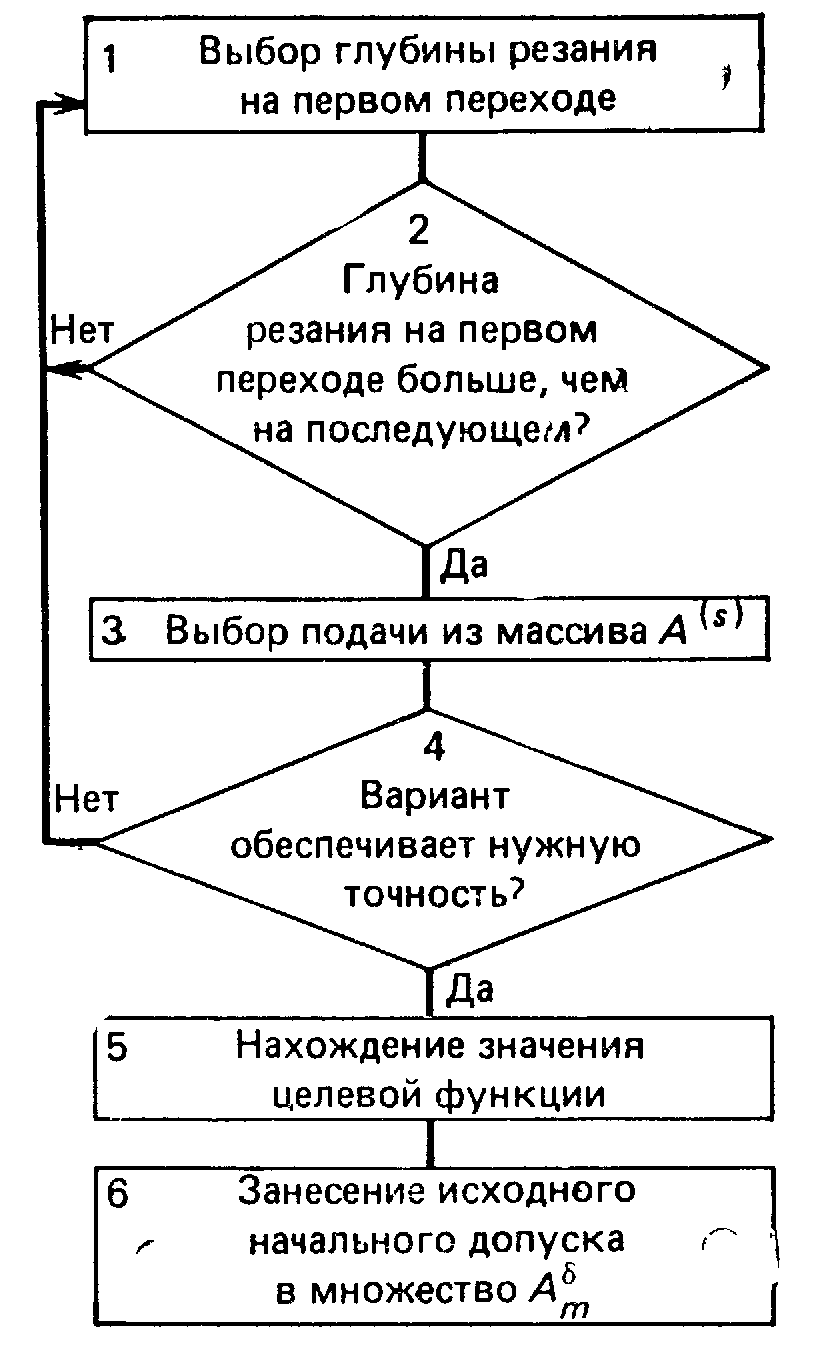
Это соотношение позволяет из множества сформулированных вариантов выбрать один оптимальный по технологической себестоимости вариант с указанием глубин резания, подач и скоростей резания по технологическим переходам (рисунок 3.9). В случае многопереходной обработки число вариантов для сравнения по технологической себестоимости определяют от первого перехода
(от заготовки). Для этого предусматривают несколько шагов (рисунок 3.10)
Рисунок 3.10 - Схема алгоритма нахождения варианта плана маршрута обработки поверхности детали с учетом технологических параметров
3.6 Выводы
Проектирование - процесс, заключающийся в преобразовании исходного описания объекта в окончательное описание. Оно различается на неавтоматизированное, автоматизированное и автоматическое.
Основные принципы проектирования – декомпозиция и иерархичность описания объектов, многоэтапность и итерационность, типизация и унификация проектных решений и средств проектирования.
Стадии, этапы, проектные процедуры и операции являются составными частями процесса проектирования.
Цепочка: синтез - анализ - оценка и модификация параметров или изменение структуры или корректировка технического задания является типичной последовательностью проектных процедур при автоматизации технологического проектирования.
При синтезе технологических маршрутов и операций обработки деталей используют метод структурного синтеза, основанный на использовании типовых решений и относящийся к методам выделения варианта из обобщенной структуры.
Для поиска оптимального варианта плана маршрута обработки поверхностей используют методы направленного перебора, динамического программирования и другие.
Первым аспирантом стал Кунгуров В.В., который до настоящего времени успешно работает в АлтГТУ. Под руководством Т.В. Ершова за период его работы на кафедре было подготовлено 13 кандидатских диссертаций. Большинство выпускников аспирантуры остались работать на кафедре: это кандидаты технических наук, доценты Каменская А.А., Ковалова Р.И., Лукин Л.Н., Гончаров В.Д., Федорова Н.П., Аскалонова Т.А., Лабецкий В.М., Неверов В.И..
Огромная роль в оснащении лабораторий станками, технологической оснасткой, исследовательской аппаратурой принадлежит ветерану кафедры и института Ласкину Виктору Алексеевичу, который заведовал лабораториями более 30 лет. Имея золотые руки мастера и инженерное мышление, он участвовал как соавтор и исполнитель многих научных и инженерных разработок как для исследовательских работ своей кафедры, так и по заказам других кафедр и заводов.
За весь период работы кафедрой "Технология машиностроения" выпущено более 10 тыс. инженеров-технологов. Большинство из них стали ведущими специалистами производства и крупными руководителями предприятий. Мэр г. Барнаула Баварин В.Н. – выпускник кафедры. Генеральным директором ОАО "Барнаульский станкостроительный завод" много лет работал выпускник специальности "Технология машиностроения" герой социалистического труда, почетный гражданин города Барнаула Кулагин П.С., и сейчас этот завод возглавляет выпускник кафедры Яшкин В.А. Главными инженерами предприятий города в 70-е – 80-е годы работали Лунев А.В., Егоров В.Н., Цемахович А.Д., главными технологами – Майданский Я.В., Сорокин Г.П. (Продолжение на стр.165).