Принципы и задачи проектирования 1 Уровни, аспекты и этапы проектирования
Вид материала | Документы |
- Лекция: Организация разработки ис: Каноническое проектирование ис. Стадии и этапы процесса, 312.68kb.
- А. П. Марков Технологические практикум, 91.28kb.
- "Сапр web pack ise. Этапы и технология проектирования устройств на базе плис. Примеры, 449.82kb.
- А. Е. Стешков методология проектирования металлорежущих инструментов, 74.74kb.
- 1 Цели и задачи курсового проектирования, 12.27kb.
- Программа дисциплины Проектирование информационных систем Семестры, 9.14kb.
- С. П. Колотовкин организация курсового проектирования, преддипломной практики и дипломного, 276.32kb.
- Список билетов для экзамена по курсу Моделирование и исследование систем, 99.07kb.
- 05. 13. 12 Системы автоматизации проектирования (по отраслям) Формула специальности, 21.27kb.
- Методы автоматизированного проектирования системы прогнозирования землетрясений 05., 315.41kb.
3.4 Использование типовых решений при синтезе
технологических маршрутов обработки изделий
3.4.1 Индивидуальные и обобщенные технологические маршруты
При технологическом проектировании наибольшее распространение получил метод структурного синтеза, основанный на использовании типовых решений и относящийся к методам выделения варианта из обобщенной структуры [2,3,7].
Уровень типизации технологических процессов с широкой нормализацией и унификацией конструкций деталей во многом определяет трудоемкость технологической подготовки производства на предприятии. Особенно это важно при создании автоматизированной системы подготовки производства и, в частности, автоматизированного проектирования технологических процессов обработки резанием (при этом необходимо иметь четкие правила, условия назначения операций и т. п.).
Типовые процессы разрабатывают на основе анализа, систематизации и обобщения технологических решений с учетом научных достижений технологии машиностроения и передового производственного опыта. Предусматривают применение высокопроизводительного оборудования, средств механизации и автоматизации, использование прогрессивных методов выполнения заготовок и их обработки. Типовой процесс должен быть рациональным в конкретных производственных условиях, должен характеризоваться единством содержания и последовательности большинства технологических операций для группы изделий, обладающих общими конструктивными признаками.
Проектирование маршрутов обработки деталей является основным этапом технологического проектирования.
Оно включает в себя:
- формирование технологических операций с указанием наименования и сущности выполняемой работы;
- установление последовательности их выполнения;
- оценку полученных результатов.
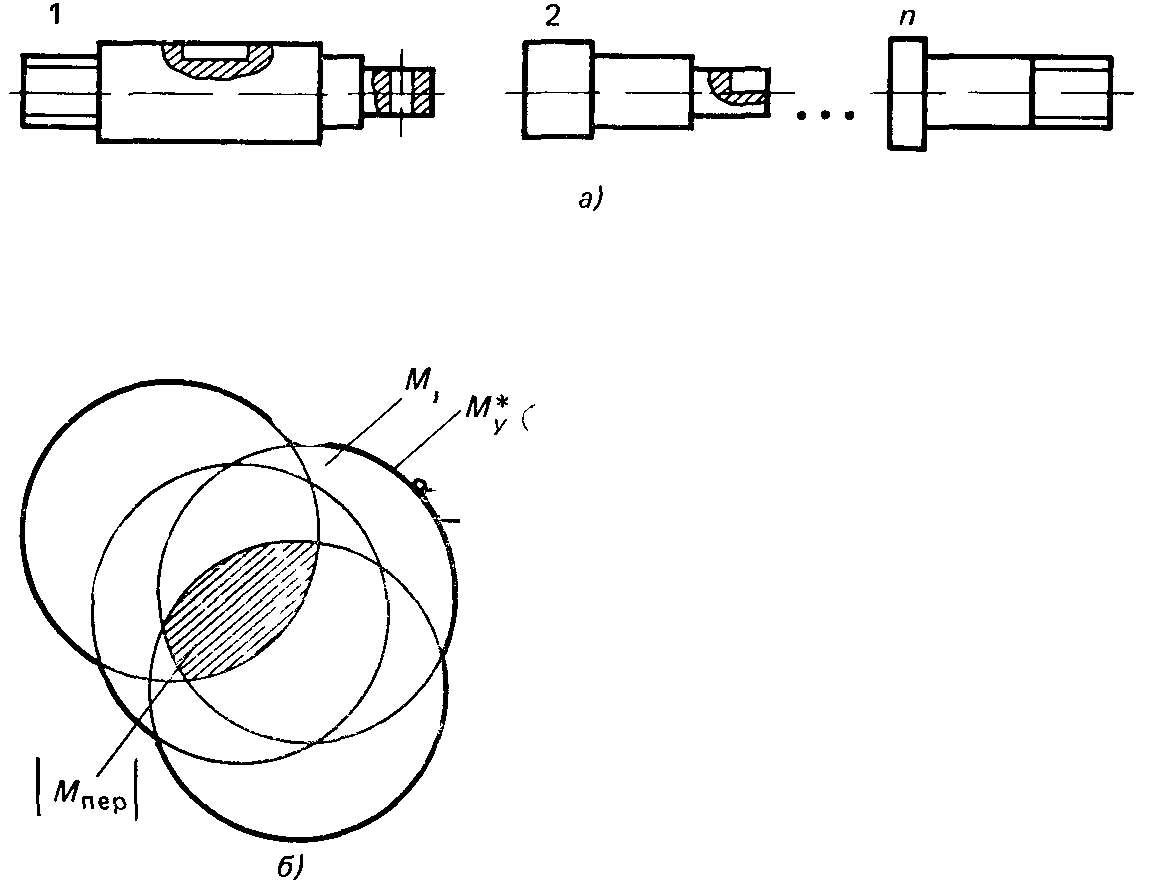
Рисунок 3.5 - Схема объединения технологических маршрутов.
Исходными данными при этом служат конструктивные особенности детали, технические условия приемки, программа выпуска и вид заготовки. В качестве исходных данных служат также сведения об оборудовании, приспособлениях и инструменте.
Конкретную деталь относят к типовому классу (валы, диски, корпусные детали и др.), подклассу, группе или более мелкой градации (подгруппе, типу) в соответствии с принятым классификатором.
Для данного класса (подкласса, группы, подгруппы или типа) деталей синтезируется обобщенный маршрут обработки, включающий перечень операций обработки, характерных для этого класса. Перечень представляет собой упорядоченное множество операций существующих индивидуальных маршрутов. Эти маршруты имеют типовую последовательность и содержание, причем на уровне предприятия учитываются его передовой опыт и традиции, а также научно-технические достижения и перспективы развития отрасли.
На рисунке 3.5 показана схема объединения технологических маршрутов М обработки класса деталей в обобщенный маршрут. Если имеем множество индивидуальных маршрутов M1, M2, .... Мi., ..., Мп (где 1, 2, .., i, ..., п — номера индивидуальных маршрутов) для какого-то класса или группы деталей (рисунок 3.5а), то при объединении этих маршрутов (рисунок 3.5б) Мi Му*, где My*— обобщенный маршрут. Каждый типовой индивидуальный маршрут М представляет собой множество операций со своими кодами Ci. Код операции содержит несколько знаков, например при четырехзначном коде первые два знака характеризуют вид операции (токарные, фрезерные и т. д.), последние знаки учитывают особенности выполнения операции, например обработку детали в патроне, центрах, люнете и т. п.
Необходимым условием включения индивидуального маршрута в обобщенный является наличие области пересечения, например Мi и Мj как непустого множества: Мi ∩ Мj≠0
Важной характеристикой формирования обобщенного маршрута является мощность пересечения множеств операций индивидуальных маршрутов |Л1пер|, т. е. количество операций с одинаковыми кодами, входящими в это пересечение
Мпер=∩i=1 Mi.
Мощность пересечения множества операций в обобщенном маршруте желательно увеличивать, поскольку при этом мощность обобщенного маршрута Му*=∩i=1 Mi уменьшается. Следовательно, обобщенный маршрут представляет множество индивидуальных маршрутов, представленных своими кодами операций. В Мпер двух или нескольких маршрутов входят эквивалентные операции. Эти операции должны иметь один и тот же код. Значения |Мпер| и |Му*| могут служить ориентиром для анализа и совершенствования работ по типизации технологических процессов, так как количество эквивалентных операций для различных деталей одной группы (класса или подкласса) позволяет оценить возможность объединения деталей в группу и уровень проведенных работ на предприятии по типизации.
Описание операции в технологическом маршруте должно включать ее наименование и сущность выполняемой работы.
В результате анализа описаний для каждого предприятия, группы предприятий или отрасли по реальным технологическим процессам создают конкретный справочник формулировок операций. В таблице 3.1 показаны фрагменты формулировок операций по обработке ступенчатых валов и корпусных деталей коробчатого типа (мелкосерийное производство).
Эти справочники формулировок как правило содержат:
- эскиз детали;
- код операции;
- формулировку операции.
Таблица 3.1 - Фрагмент справочника формулировок операций.
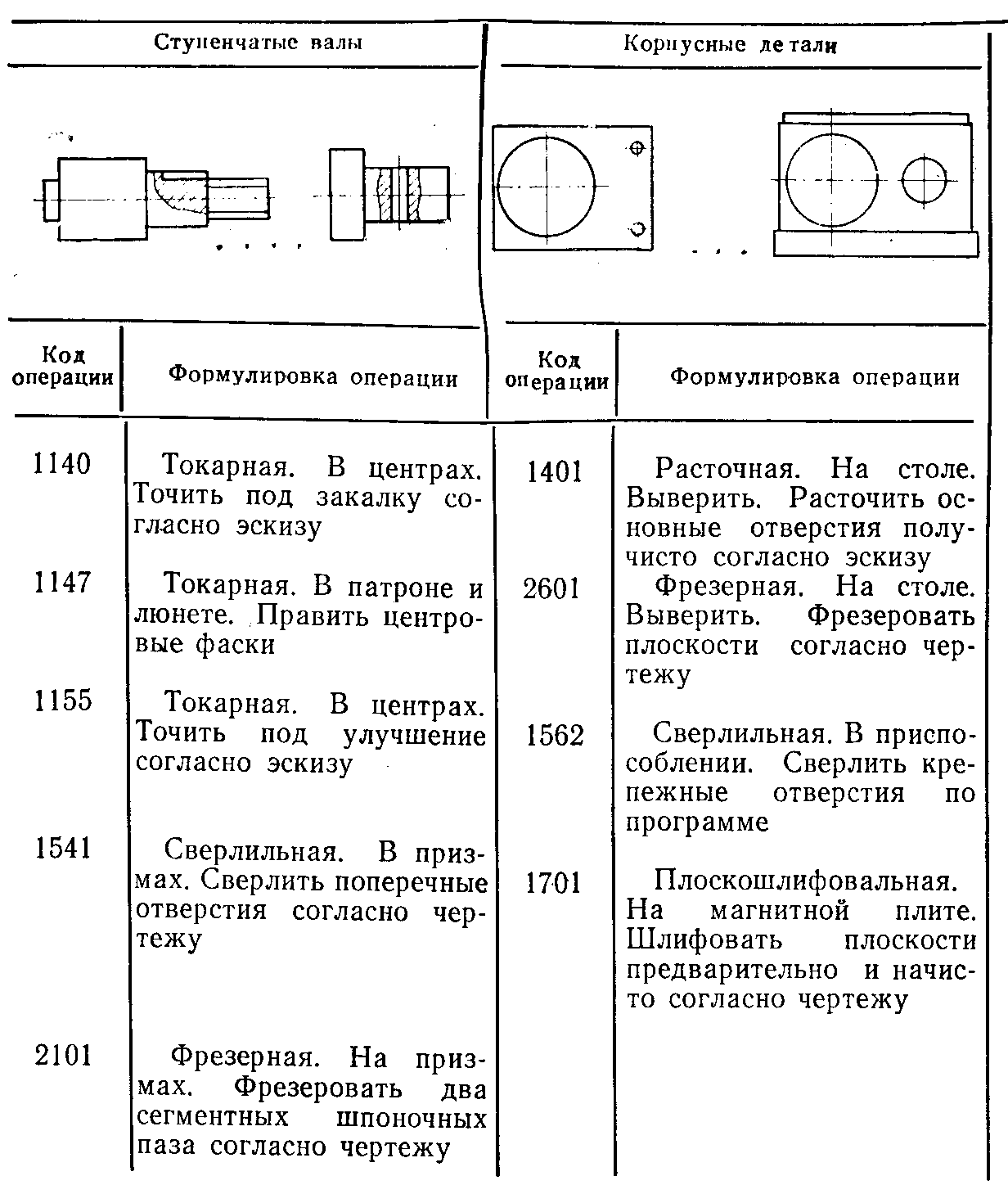
3.4.2 Условия назначения операций и индивидуальный технологический маршрут
При синтезе технологического маршрута обработки детали необходимо решить задачи:
- выбор из составленных справочников типовых формулировок операций нужных операций для обеспечения требований качества обрабатываемой детали, а затем определение места выбранной операции в технологическом маршруте. Решение этих задач основано на том, что для каждой операции выявляются условия, которые будут определяющими при ее включении в технологический маршрут. Как видно из справочника формулировок (см. таблицу 3.1), операции с кодами 1140 и 1155 следует включать в технологический маршрут, если необходима термическая обработка, соответственно закалка или улучшение. Из формулировок других операций, например 1147 , сразу не вытекают условия включения этих операций в технологический маршрут. Однако в одном случае установка ступенчатого вала в патроне и люнете определяется отношением длины к приведенному диаметру L/Dnp и необходимостью править центровые фаски, в другом случае использование гидрокопировального токарного полуавтомата при обтачивании хвостовика вилки зависит от количества ступеней. Поэтому важно выявление условий назначения операций в маршруте на основе технологических предпосылок.
Применяемые заготовки также влияют на выбор операций и их последовательность в технологическом маршруте. Например, в условиях мелкосерийного и среднесерийного производства для изготовления валов применяют горячекатаный прокат, штамповки, изготовленные на молотах, горизонтально-ковочных и ротационно-ковочных машинах и др. Каждому виду заготовки соответствуют свои типовые формулировки операций, включение той или иной операции термической обработки, например искусственного старения для литых чугунных корпусов. Вид заготовок влияет на содержание черновых операций, связанных с удалением напуска. В свою очередь, использование индивидуальных простейших заготовок или прогрессивных, приближающихся к контуру детали, а также комплексных заготовок для группы деталей определяется программой выпуска, конструкцией изделия и характерными особенностями того или иного предприятия или отрасли. Уточнение выбора индивидуальных и комплексных заготовок производят с помощью ЭВМ с учетом затрат на изготовление и черновые операции обработки резанием.
Важное значение имеют условия, определяющие погрешности размера, формы и положения поверхностей, а также качество поверхностного слоя. Заданные погрешности размера и формы обеспечиваются соответствующими методами обработки, характерными для предприятия или отрасли. Выбор операций по этим условиям легко осуществляется использованием табличных моделей. Погрешность положения обрабатываемых поверхностей непосредственно связана с назначением схем базирования, которые связываются с формулировками операций.
В конструктивно-технологической группе деталей в качестве условий при выборе операций учитывают разновидности термической обработки, например для ступенчатых валов нормализацию, улучшение, закалку, отпуск и др.; для корпусных деталей из чугуна — искусственное старение и т. д. Эти операции назначаются в технологический маршрут при выполнении условий, вытекающих из технических требований на изготовление детали. Условия, характеризующие шероховатость обрабатываемых поверхностей, определяются характером производства. Например, при обработке наружных цилиндрических поверхностей валов выполнение условия, обеспечивающего шероховатость поверхности с Ra = 1,25 ... 0,32, требует введения операции шлифования.
Условия, связанные с габаритными размерами детали, как правило, являются двусторонними неравенствами (больше или меньше граничного значения). Граничные значения для различных групп деталей — разные; более того, они различаются для одной и той же конструктивно-технологической группы в зависимости от традиций и опыта проектирования технологических процессов на предприятиях и в отрасли. Так, часто нежесткой деталью называют, например, ступенчатый вал, если соотношение его длины к приведенному диаметру (L/Dnp)>12. Но в некоторых отраслях машиностроения данное отношение может быть другим. Это соотношение обусловливает варианты схем установки заготовок при их обработке. Например, вал можно установить в центрах, патроне и люнете, в центрах с люнетом и т. д.
Габаритные размеры обрабатываемой детали и их граничные значения, а также размер партии запускаемых в производство изделий в значительной степени влияют на выбор оборудования и технологической оснастки.
Для выбора операций при синтезе технологического маршрута создают справочники условий. В таблице 3.2 приведен фрагмент такого справочника для выбора операций при обработке ступенчатых валов. Например, операцию обработки ступенчатого вала с формулировкой «Токарная. В патроне и люнете. Подрезать торцы в размер и править центровые фаски согласно эскизу» включают в маршрут при условии (L/Dnp)>12 (условие А84), причем в случае, если перед этим была термическая обработка — улучшение (условие А70). Таким образом, операция должна следовать после термической обработки — улучшения и предикат, определяющий выбор указанной операции, будет иметь вид A70/\A84. Однако эта же операция может следовать также и после термической обработки — закалки, когда вследствие коробления заготовки необходимо обработать торцы и править центровые гнезда. В этом случае логическая функция будет иметь вид A67/\A84. Обобщение сказанного выражается предикатом (A70/\A84) V (A67/\A84).
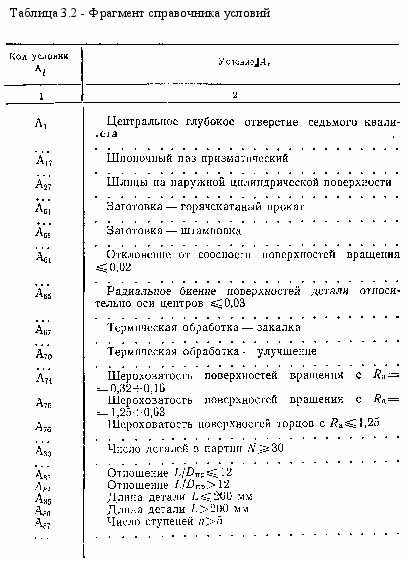
В общем случае логическая функция выбора й-й операции
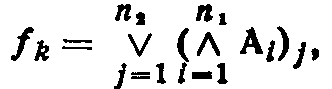
где Аi — условие из справочника условий для класса (группы) деталей; п1 — количество условий, связанных операцией конъюнкции; n2—количество конъюнкций, связанных операцией дизъюнкции.
Количество условий, связанных операцией конъюнкции, например для группы ступенчатых валов, обычно не превышает двух-трех. Для других конструктивных групп их может быть и больше. Это количество устанавливают при 'разработке справочника условий. Ограничения по количеству дизъюнкций не устанавливают. Таким образом, логическая функция (3.1) представляет собой совокупность наборов (
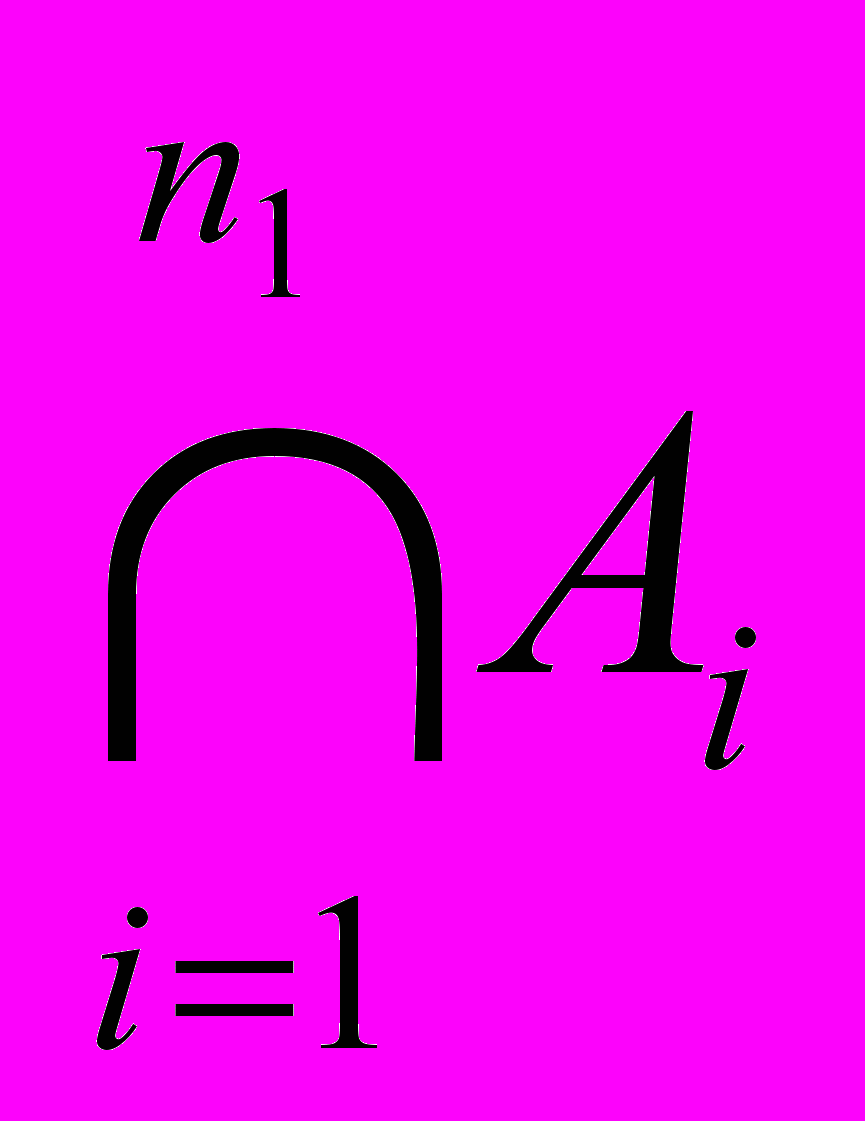
В условиях практического использования автоматизированного проектирования технологических маршрутов необходимо выявить применяемость сочетаний конструктивно-технологических условий для определенного класса (группы) деталей. Анализ показал, что, например, для ступенчатых валов, вилок, дисков, корпусов коробчатого типа и других деталей количество таких сочетаний ограничено. С повышением уровня типизации технологических процессов и унификации изделий количество сочетаний будет уменьшаться, а это, в свою очередь, упрощает синтез технологических маршрутов.
Упорядоченный перечень операций позволяет синтезировать индивидуальные маршруты для конкретных деталей с учетом геометрических, технологических и других особенностей (условий).
Величины n1,n2 строго определены на каждом шаге решения задачи, но могут изменяться по мере изменения множеств условий при построении обобщенного маршрута. Тогда множество, определяющее обобщенный маршрут,
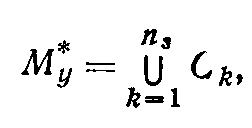
где k=n3 — количество операций (кодов СR) в обобщенном маршруте.
3.5.3 Формирование обобщенного технологического маршрута
Ф
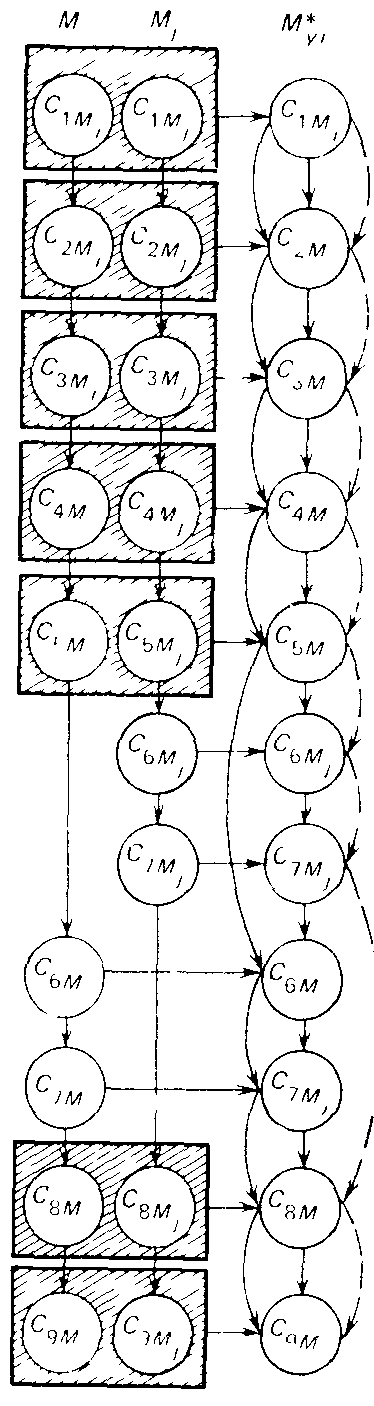
На рисунке 3.6 показана схема построения обобщенного маршрута. К базовому маршруту Mi присоединяется маршрут Мj В результате получается обобщенный маршрут М*yi . Заштрихованные области показывают эквивалентные операции, которые определяют мощность пересечения двух маршрутов. Эквивалентность операций устанавливается по совпадению кодов.
В случае эквивалентности двух операций в обобщенный маршрут включается одна из них. В сформированном обобщенном маршруте не должен нарушаться порядок следования операций любого из объединяемых индивидуальных маршрутов.
Рисунок 3.6 - Схема построения
обобщенного маршрута
Схема построения обобщенного маршрута (рисунок 3.6) иллюстрируется примером технологии обработки ступенчатых валов. Базовый маршрут М, включал в себя следующие операции:
1) отрезка заготовки; 2) подрезка торцов и зацентровка при установке заготовки в самоцентрирующихся призмах; 3) черновая обработка ступеней вала на токарном гидрокопировальном полуавтомате; 4) чистовая обработка ступеней вала на том же станке; 5) обработка левой стороны вала на токарном станке; 6) термическая обработка шеек вала; 7) шлифование шеек вала; 8) мойка; 9) контроль. В присоединяемом маршруте Му операции 1—5 совпадают с операциями 1—5 маршрута Мг, затем следуют операции: 6) фрезерование шпоночного паза; 7) зачистка заусенцев; 8) мойка; 9) контроль. Обобщенный маршрут с учетом вышеприведенных условий представляет собой упорядоченное множество операций для обработки двух (в данном случае) разновидностей деталей. Далее происходит присоединение следующего маршрута и т. д.
3.4.4 Синтез технологических маршрутов.
Синтез индивидуальных технологических маршрутов осуществляется путем их выделения из обобщенного маршрута. Исходными данными для такого выделения являются условия ЛД, характерные для конкретной детали класса (группы). Обобщенный маршрут содержит элементарные логические функции, соответствующие каждой операции:
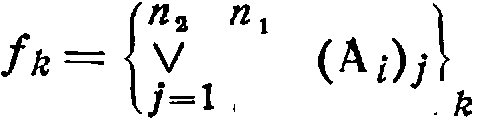
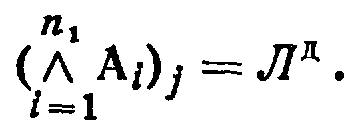
Если fk =0, то из блока 5 дается команда на вызов следующей операции обобщенного маршрута My* до тех пор, пока не будут просмотрены все операции My*.
Пуск

1. Вызов обобщенного маршрута М*у с логическими функциями fк
2. Вызов условий ЛД, характеризующих деталь.

Печать маршрутной карты

3. Вызов к-й операции М*у
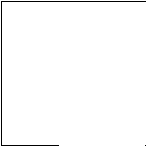


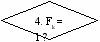

5. Формирование кодов индивидуального маршрута

нет
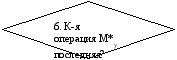
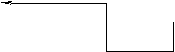
Останов


Рисунок 3.7 – Алгоритм синтеза технологических маршрутов
3.5 Направленный перебор при синтезе маршрута обработки поверхности детали
3.5.1 Многовариантность задачи синтеза маршрута обработки поверхности детали.
При решении задач синтеза маршрута обработки поверхностей используют методы направленного перебора, динамического программирования и др. Рассмотрим синтез маршрута обработки поверхности на основе направленного перебора, суть которого заключается в определении количества переходов за счет использования допустимых режимов резания при условии выполнения ограничений и минимизации (максимизации) целевой функции.
При многопереходной обработке поверхности каждый предыдущий переход существенно влияет на результаты последующего (главным образом на точность обработки). Поэтому различные варианты выполнения последующего перехода могут рассматриваться только после того, как выбраны определенные параметры предыдущего перехода.
Различные варианты многопереходной обработки поверхности должны рассматриваться как отличные друг от друга по количеству и основным характеристикам наборы переходов, выполняемых в строго определенной последовательности. Каждый такой набор дает определенную точность обработки и связан с конкретными затратами.
Если задана стойкость инструмента, то скорость резания можно принять производной от глубины резания и подачи. Следовательно, два последних параметра и определяют многовариантный характер рассматриваемой задачи. Глубина резания на первом переходе теоретически может принимать значения от максимального tmax, равного общему максимальному припуску на рассматриваемую поверхность, до минимального tmin, допустимого физикой процесса резания. Каждое последующее значение глубины резания может отличаться от предыдущего на величину t, характеризуемую возможностью устойчивого регулирования при данной конструкции настроечного устройства. Таким образом, на первом переходе глубина резания выражается величиной tmax.—jt, где j==0, 1, 2,..., р. Каждая из указанных глубин резания может образовывать новый вариант первого перехода в сочетании с различными величинами подач, принимающими значение от Smax до Smin. В результате образуется определенное множество вариантов выполнения первого перехода, неравноценных как по получаемой точности обработки, так и по затратам (например, технологической себестоимости).
Особенности выполнения первого перехода оказывают большое влияние на количество возможных вариантов последующих переходов, и в первую очередь за счет изменения глубины резания. Количество вариантов маршрутов на последующих переходах будет тем больше, чем больше та часть припуска, которая осталась неиспользованной после первого перехода. Вариант первого перехода в сочетании с различными вариантами выполнения второго перехода дает набор неравнозначных вариантов двухпереходной обработки. Аналогично определяют возможные варианты с третьим, четвертым и последующими переходами.
Варианты маршрута многопереходной обработки поверхности могут быть представлены графом, вершины которого соответствуют какому-нибудь показателю (например, погрешности обработки поверхности), а ребра, соединяющие две вершины,—определенным параметрам перехода. Различные цепи, выходящие из вершины графа, соответствующей какому-либо показателю заготовки, имеют последнее ребро, рассматриваемое как последний переход. Сами цепи описывают варианты многопереходной обработки. Поэтому формально различные варианты переходов и их последовательностей могут быть представлены ребрами и цепями графа. Дерево вариантов маршрута обработки поверхности детали представлено на рисунке 3.8.
Чтобы каждая цепь отражала вариант многопереходной обработки, представляющий практический интерес, необходимо установить определенные технологические правила, которым она должна удовлетворять.
При выборе плана маршрута многопереходной обработки поверхности детали резанием в первую очередь преследуется цель удалить слой металла (припуск) и достичь заданной точности за наименьшее число переходов. В этом отношении рационально начинать построение графа с минимального числа переходов, постепенно увеличивая их число.Тогда и расчеты должны проводиться в той же последовательности, что значительно уменьшит их объем. Этого правила надо придерживаться и при выборе последовательности рассмотрения различных значений подач. На завершающем переходе на подачу накладываются ограничения, обусловленные заданной шероховатостью поверхности.
Поэтому при построении графа достаточно из ряда подач, имеющихся на данном станке, принять ограниченное число, например, пять-шесть, одна-две из которых будут меньше определяемой требуемой шероховатостью поверхности, а остальные, предназначенные для первых переходов, — больше. В общем случае каждое значение глубины резания может сочетаться с любым значением подачи из ряда Smax, ..., Sk,..., Smin. Практически нецелесообразно на последующем переходе использовать подачу большую, чем на предшествующем. Поэтому при построении графа количество ребер, исходящих из одной вершины, будут зависеть от того, какому значению подачи соответствует предшествующее им ребро. Но и в этом случае не все возможные сочетания глубины резания и подачи должны приниматься во внимание при
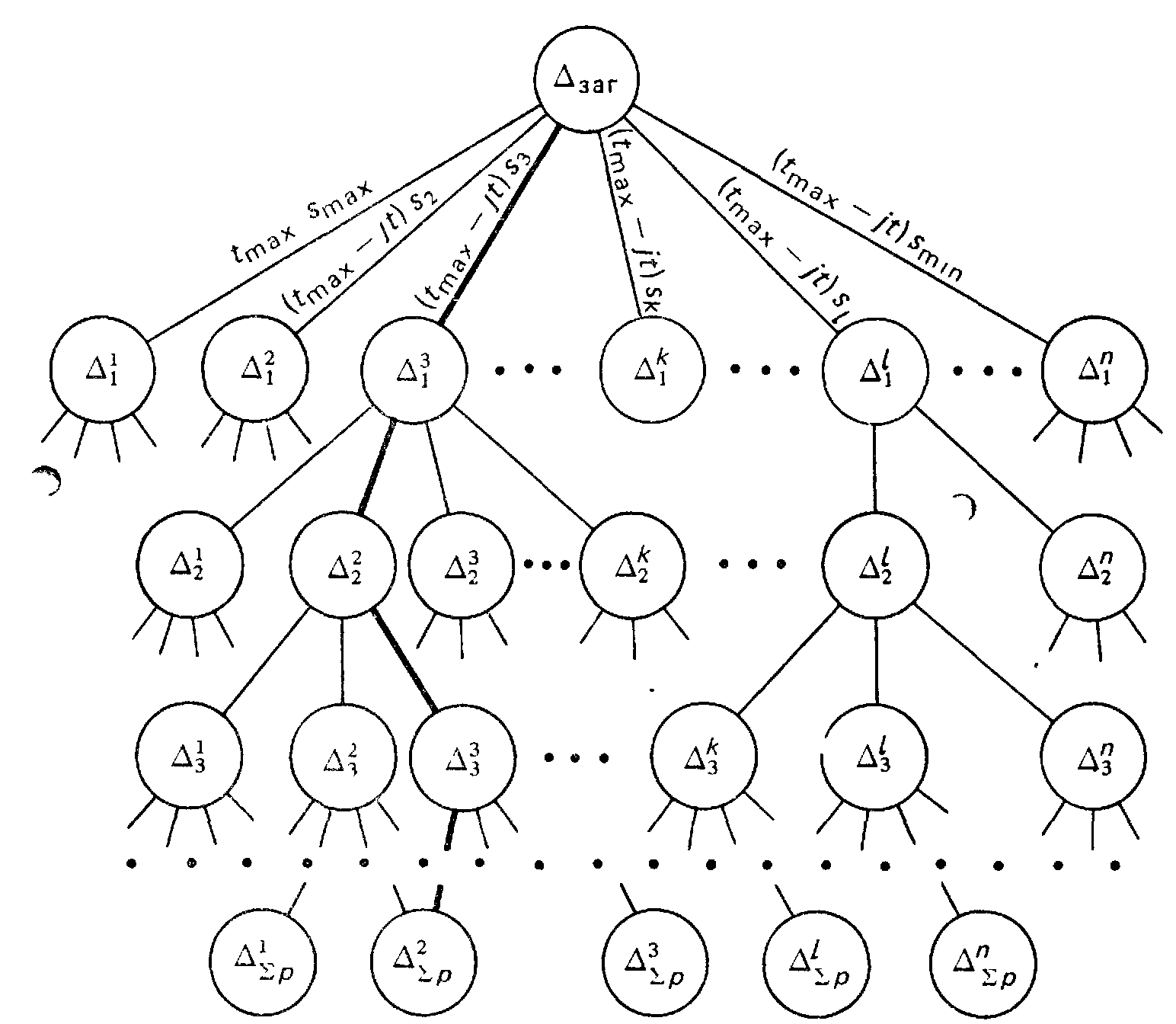
Рисунок 3.8 – Дерево вариантов маршрута обработки поверхности
детали
построении графа.
Порядок изменения глубины резания при построении графа регламентируют некоторые технологические правила. Наиболее важное из этих правил устанавливает связь между технической характеристикой настроечного устройства и изменениями глубины резания в различных вариантах переходов. Согласно ему, при построении ребер одной цепи должно выполняться условие закономерного уменьшения первичных погрешностей обработки, т. е. ti ti-1, где ti—глубина резания, соответствующая рассматриваемому ребру; ti-1—глубина резания, относящаяся к предшествующему ребру той же цепи
С учетом принятых ограничений уже на первом переходе глубина резания не должна быть меньше определенного значения. В общем случае минимальная глубина резания, рассматриваемая на р-м переходе,
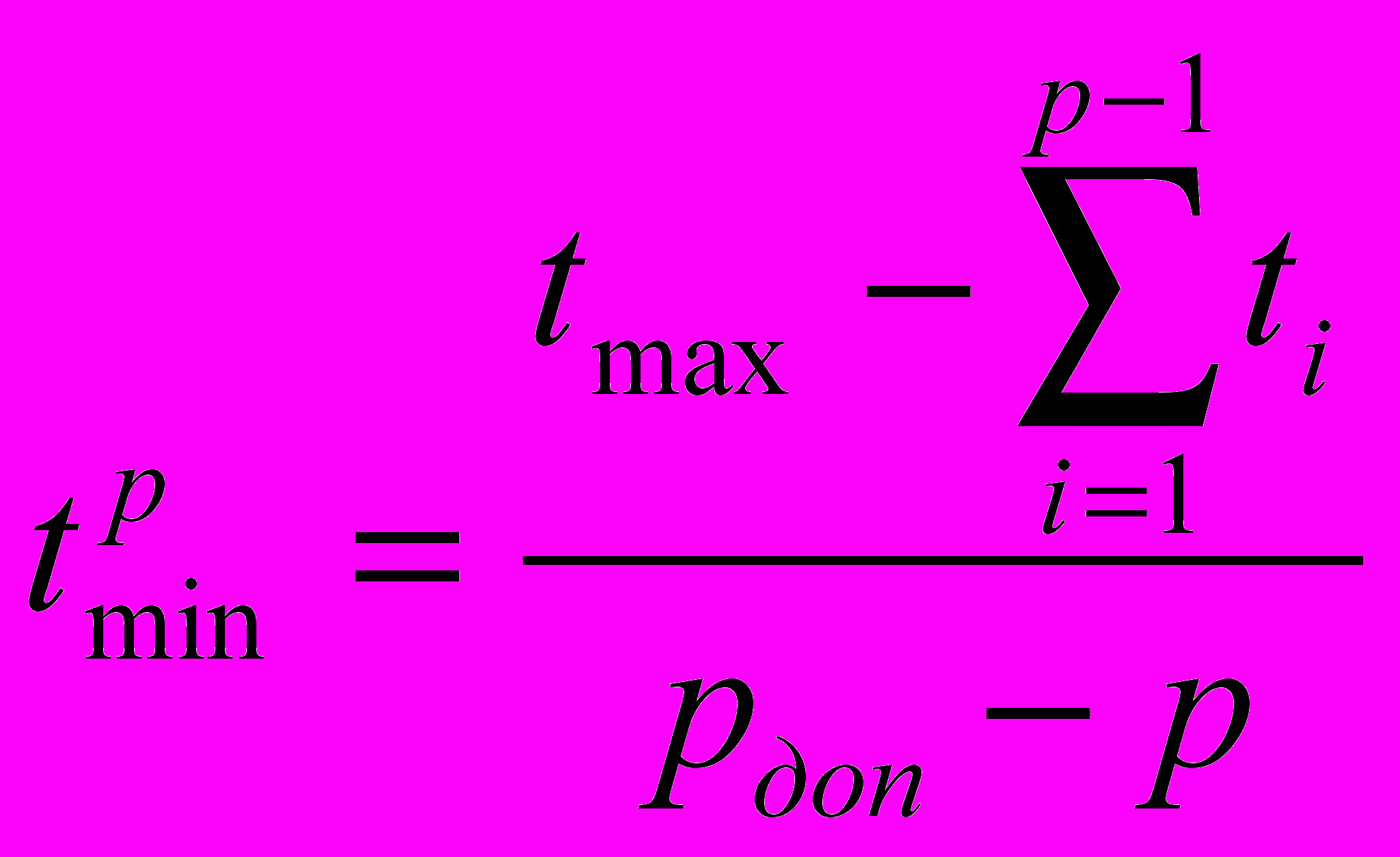
где tmax—максимальная глубина резания при обработке
всего припуска за один переход;
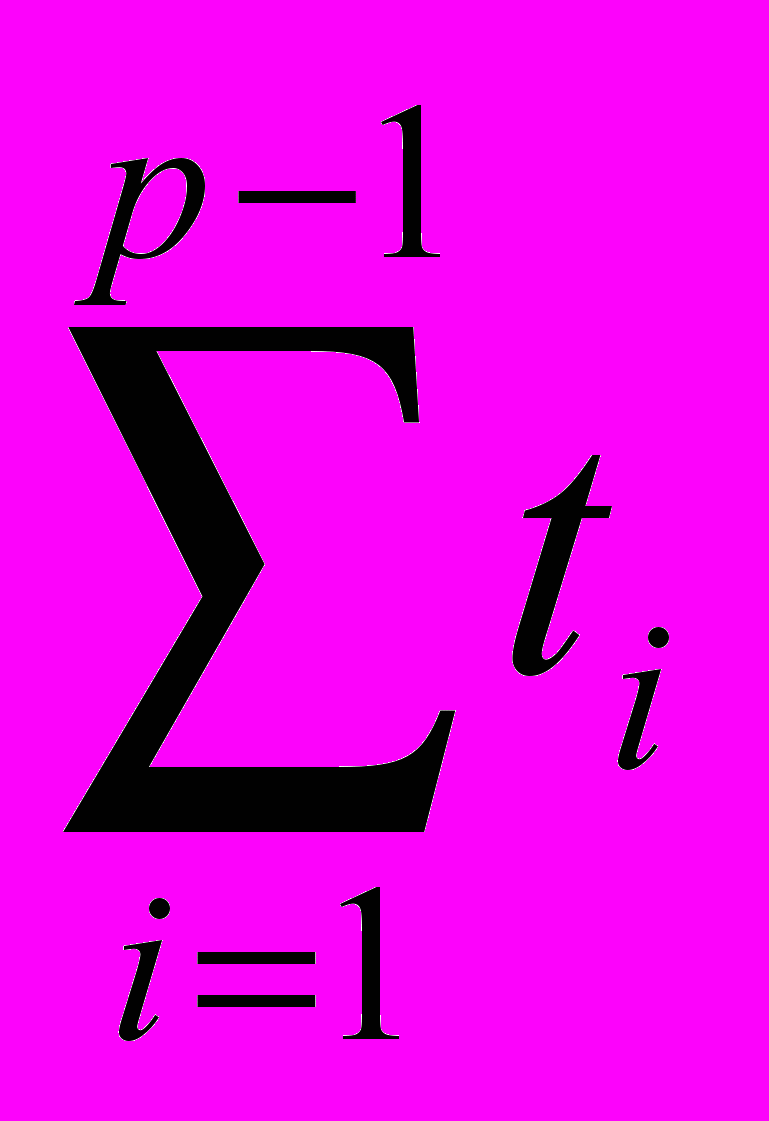
pдоп—максимально допустимое число переходов, принимаемое для данного расчета.