Разработка системы многоаспектной оценки технического состояния и обслуживания высоковольтного маслонаполненного электрооборудования
Вид материала | Автореферат |
- Техническое задание «Разработка системы диагностики технического состояния маслонаполненного, 225.4kb.
- Комплект оборудования для передвижной лаборатории оперативной оценки технического состояния, 47.86kb.
- Комплексное диагностическое моделирование параметров технического состояния силового, 700.09kb.
- Краткий курс лекций по дисциплине «Подвижной состав железнодорожного транспорта» специальность, 910.14kb.
- Разработка и апробация системы оценки состояния гидротехнических сооружений речных, 503.04kb.
- Задание модели системы в пространстве состояний, построение оптимального наблюдателя, 14.7kb.
- Анализ состояния сервисной системы технического обслуживания и ремонта авиационной, 139.65kb.
- О мониторинге технического состояния жилых домов на территории города Москвы, 111.45kb.
- Технического обслуживания и ремонта машин, 361.45kb.
- Учебно-тематический план «Монтаж, наладка, текущий ремонт и контроль технического состояния, 89.17kb.
Таблица 4 - Потоки повреждаемости и уровни интегральной функции распределения, используемые для определения ДЗ и ПДЗ параметров
Виды оборудования | Сроки эксплу-атации, лет | ![]() | Fх для ПДЗ | ![]() | Fх для ДЗ |
Силовые трансформаторы 110-500 кВ | 0-3 | 3,46 | 0,9654 | 8,14 | 0,9186 |
3-15 | 1,6 | 0,984 | 3,77 | 0,9623 | |
15-27 | 3,46 | 0,9654 | 8,14 | 0,9186 | |
27-37 | 1,6 | 0,984 | 3,77 | 0,9623 | |
Свыше 37 | 3,46 | 0,9654 | 8,14 | 0,9186 | |
СТ 35 кВ | - | 1,4 | 0,986 | 4,0 | 096 |
Высоковольтные вводы 110-500 кВ | 0-9 | 0,3-0,5 | 0,997-0,995* | 2,5 | 0,975* |
9-22 | 0,5/1 | 0,995* | 3,7 | 0,963* | |
22-32 | 0,5/1 | 0,995* | 3,7 | 0,963* | |
Свыше 32 | 1 | 0,99 | 4.3 | 0,957* | |
ТН 110-500 кВ | | 1,5 | 0,985* | 3,0 | 0,97 |
ТТ 110 кВ | | 0,5-1 | 0,995* | 2,5 | 0,975* |
ТТ 220-750 кВ | | 2,5 | 0,975* | 5,0 | 0,95 |
*-если мощность выборки не позволяет учесть тысячные доли уровня, то значение округляется до сотых. |
На основании проведенного анализа факторов, влияющих на регламентируемые значения и повреждаемости маслонаполненного оборудования на массивах данных 10 энергосистем, содержащих 17048
результатов АРГ из высоковольтных вводов, 7805 – из ТТ, 4842 - из ТН, 65493 – из силовых трансформаторов и автотрансформаторов; 9588 результатов ФХА масла из высоковольтных вводов, 4978 – из ТТ, 2165 - из ТН, 15930 – из силовых трансформаторов и автотрансформаторов, были определены ДЗ и ПДЗ контролируемых параметров жидкой изоляции.
Подход, при котором для отбраковки оборудования используется только одно значение, страдает формальностью и имеет повышенный риск ошибок 1-го и 2-го рода. Использование ДЗ и ПДЗ позволило разделить развивающиеся дефекты в опасной и неопасной стадии и рекомендовать соответствующие действия персоналу. ДЗ и ПДЗ концентрации газов в масле маслонаполненного оборудования заметно отличаются в зависимости от конструкции, способа герметизации, марки масла, класса напряжения и срока эксплуатации. Если не дифференцировать ДЗ и ПДЗ по найденным факторам влияния, то при оценке технического состояния оборудования возможны ошибки как «перестраховки», так и «недосмотра». В таблице 5 приведены минимальные и максимальные ДЗ и ПДЗ относительных скоростей роста газов, разделенные согласно найденным факторам влияния, по которым видно, насколько сильно влияние конструктивных особенностей и срока службы. Очевидно, что используя критерий 10% роста скорости в месяц введенный для силовых трансформаторов, либо другой, не дифференцированный критерий, мы получали бы в одних случаях ложную отбраковку, а в других могли пропустить оборудование с повреждением.
Таблица 5 – ДЗ, ПДЗ скоростей роста газов герметичных вводов, ТТ, ТН 110-500кВ
Значения относительных скоростей роста, % | Виды оборудования | ||
ТН 110-500 кВ | ТТ 110 кВ | Вводы герметичные | |
ДЗ скорости СН4 | 1-3 | 8-20 | 7-17 |
ПДЗ скорости СН4 | 4-11 | 16-53 | 16-48 |
ДЗ скорости СО2 | 6-17 | 7-15 | 4-19 |
ПДЗ скорости СО2 | 20-35 | 12-55 | 12-45 |
Критерий скорости важен для подтверждения наличия развивающегося дефекта и оценки степени его опасности. Применение двух уровней нормирования скоростей ДЗ и ПДЗ позволит выделить объекты с наиболее быстро развивающимися, а значит более опасными дефектами для принятия незамедлительных решений.
Рассчитанные ДЗ и ПДЗ трендов изменения концентраций можно использовать в системах мониторинга технического состояния маслонаполненного оборудования.
Для оборудования с новыми конструктивными особенностями, по которому еще нет репрезентативного массива значений контролируемых параметров и, следовательно, нет возможности рассчитать пороговые значения, можно использовать ДЗ и ПДЗ контролируемых параметров и их трендов, полученные для оборудования с близкими конструктивными особенностями.
Исследованиями установлено следующее:
- огибающая распределения значений концентраций углеводородных газов и водорода описывается формулой:
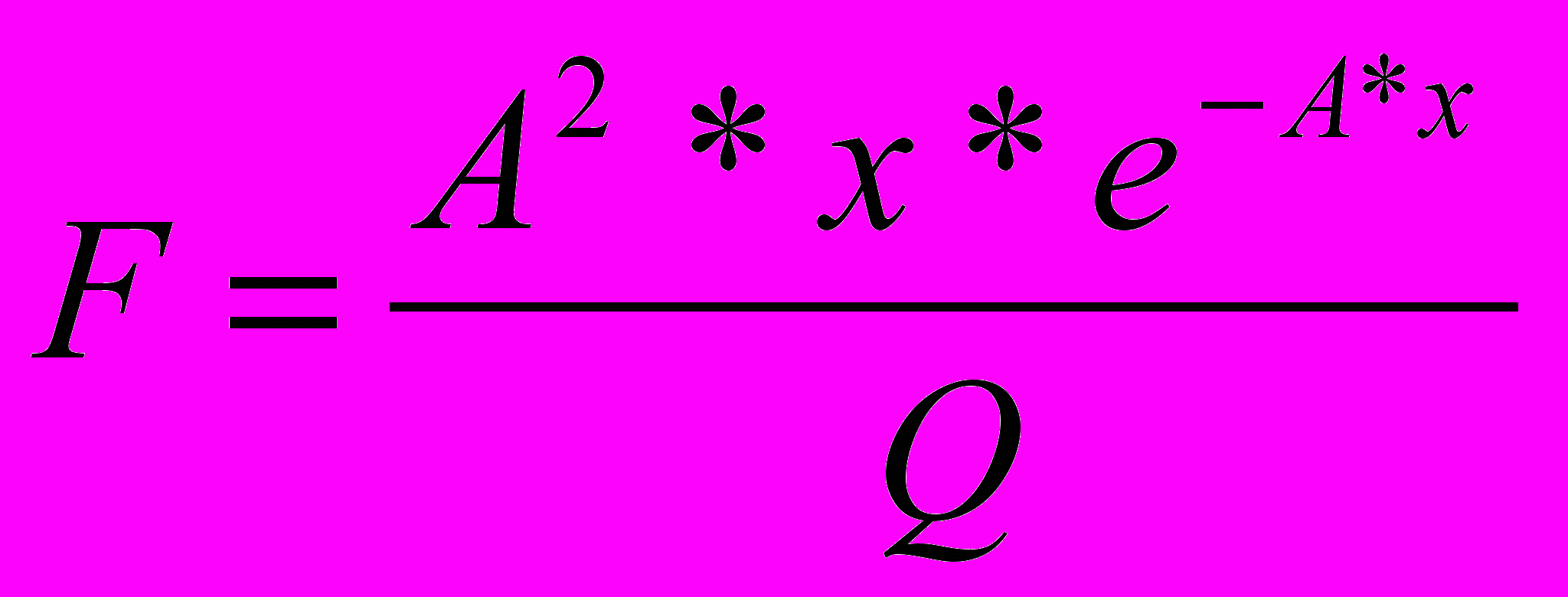
где A- коэффициент, задающий форму огибающей, Q – коэффициент масштабирования, x - значение концентрации анализируемого газа;
- огибающая распределения значений концентраций оксидов углерода выражается формулой:
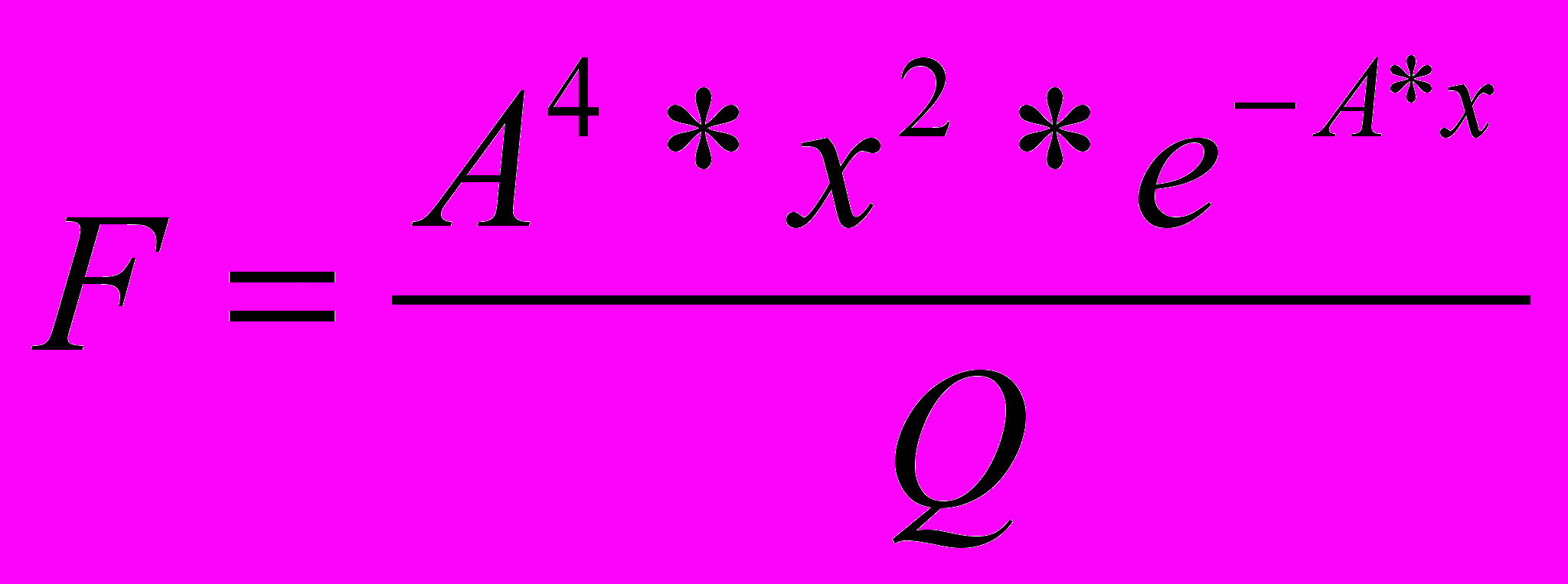
- в формулах функций распределения (9 и 10) с увеличением срока службы оборудования незначительно уменьшается коэффициент А.
Если по новому оборудованию со сроком службы t есть репрезентативный массив данных, то для получения ДЗ и ПДЗ углеводородных газов и водорода для оборудования со сроком службы t+Δt можно предложить найти верхнюю границу XДЗ (искомое ДЗ параметра) из выражения определенного интеграла:

где X0 –предела обнаружения концентрации газа хроматографом, объемн.%; λ – значение потока повреждаемости, %. Аналогично можно вычислить ДЗ оксидов углерода по верхней границе определенного интеграла, используя формулу 10.
Пятая глава посвящена критериям идентификации вида дефекта. Предложены три методики синтеза описаний класса технического состояния оборудования на основе фактов повреждения оборудования в эксплуатации и результатов АРГ: с помощью характерных соотношений пар газов и характерного набора газов, превышающих ДЗ, а также в виде графической модели. Методики состоят из этапов классификации статистических данных, синтеза образа дефектов и тестирования результатов. На этапе классификации (одинакового для всех методик) анализируется вся собранная совокупность фактов А={aRa-факт повреждения оборудования} с целью разработки априорного словаря классов состояния Ω={Ω1,..., ΩY} и априорного словаря признаков состояния X={x1,...,xN}. Полученные описания состояний оборудования классифицируются по областям состояний G={G1,...,GK}, которые содержат несколько классов состояния, различаемых по причинам и/или признакам проявления, но имеющих одинаковый характер протекающих в оборудовании процессов {GkΩkK}. Известные факты повреждений классифицируются экспертами по описаниям обнаруженных при вскрытии дефектов из актов браковок и отказов, в соответствии с разработанным словарем классов состояния {ΩyAyY}, с отслеживанием искажений информации и внесением необходимых поправок в формулировки причины,
характера, степени развития повреждения. Каждый факт помечается набором меток, характеризующих: степень развития дефекта, его достоверность, а также отмечающих наличие сразу нескольких дефектов (метка “сочетание”). Далее делаются выборки фактов по исследуемому классу Ωy состояния (дефекту), взятому из априорного словаря описания классов FΩy:(ПрX={x1, xN}А)АΩy.
Суть первой методики заключается в отборе соотношений пар газов характерных для данного вида дефекта и нахождении их значений позволяющих: определить границы перехода между классами технических состояний в пределах одной области состояний, а также обозначить границу перехода между областями, описывающими различные характеры дефектов.
Суть второй методики состоит в определении характерного для рассматриваемого дефекта набора концентраций газов, превысивших регламентируемые для них значения, а также характерные уровня превышения этих значений.
Для обеих методик в пределах выборки фактов по рассматриваемому дефекту для каждого анализируемого признака определяются границы изменения его значений, рассчитывается математическое ожидание и дисперсия для всей выборки и при отбрасывании крайних значений; определяется доля высоко-достоверных фактов; ранжирование признаков и другие операции, необходимые для конкретной методики. Определение критериев идентификации проходит в несколько итераций с различными значениями меток “развитие”, “достоверность” и “сочетание”. Например, выборка фактов с меткой ”сочетание”=1 дает синтез образа дефекта в чистом виде, а с меткой “сочетание”=2 - образ, отражающий развитие сразу двух видов дефектов.
Для получения критериев распознавания классов технического состояния высоковольтных вводов на основании АРГ была собрана БД из 185 случаев фактов вскрытия вводов. Затем был составлен словарь классов технического состояния маслонаполненных вводов с учетом соответствия между видами дефектов, причинами их возникновения и описанием последствий, обнаруженных после вскрытия оборудования (таблица 6). Далее собранные факты были проанализированы совместно с экспертами, отнесены к классам технического состояния и отмечены необходимыми метками. С использованием предложенных методик для каждого вида дефекта автором были определены характерный набор газов, концентрации которых превышают регламентированные для них значения и степень этого превышения, а также характерные отношения пар газов и их значения. Результаты синтеза описаний классов технического состояния обеими методиками приведены в таблице 6.
В третьей методике признаками состояния X={x1,...,xN} служат концентрации 7 газов, нормированные относительно взвешенной суммы этих газов. Сумма газов находится по формуле:
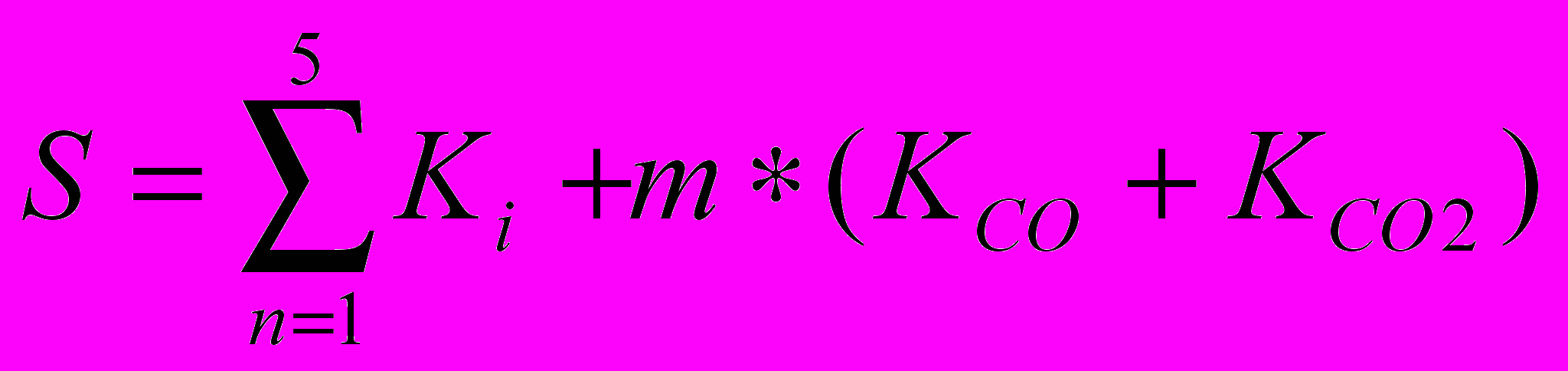
, (12)
где Ki – значения концентраций углеводородных газов и водорода; KCO , KCO2 – значения концентрации оксида и диоксида углерода; m – коэффициент масштабирования, зависит от типа оборудования (например, для ТТ m=0,01).
Таблица 6 -Критерии распознавания вида дефекта, развивающегося в маслонаполненном высоковольтном вводе
Кол-во | Название класса состояния | Причины возникновения | Описание вида дефекта по факту вскрытия | Способы идентификации | |
Характерные газы | Характерные отношения | ||||
3 | Слабые ЧР | Неровные края металлических деталей, диффузия технологических газов из остова | Не проявляются | Н2* | Н2/СН4>5 |
37 | Сильные ЧР | Увлажнение масла (остова), наличие в нем мех. примесей, волокон бумаги, газов. Зазубрины металлических частей. | Точечные пробои в отдельных слоях бумажной изоляции. Углеродный трекинг на краях обкладок. | Н2**, СН4* | Н2/СН4<4 CO/CO2≤0.3 |
21 | Слабый разряд | Смещение деталей, их плохое закрепление, вследствие чего происходит образование контуров, появление перемежающихся контактов. | Частицы углерода в месте перемежающегося контакта. Нарушенная изоляция в результате электрического воздействия. | СН4**и/или С2Н2**, H2*, C2H6* | Н2/СН4≤1 С2Н2/С2Н4≤1 |
18 | Сильный разряд | Путь блуждающего тока, или обрыв, или повреждение измерительного вывода | Цвета побежалости на металлических частях, их оплавление. Частицы углерода в масле. Разрушение бумаги при нахождении на пути тока дуги или при перегреве | С2Н2**, С2Н4*,H2*, C2H6* | С2Н2/С2Н4≥1.5 С2Н4/С2Н6≥3 |
5 | Нагрев | Плохие контакты в верхней части ввода, ухудшение охлаждения | Изменение цвета бумажной изоляции, окисление металла. | С2Н4*, Н2*, C2H6* | С2Н4/С2Н6≥0.8 |
50 | Образование желтого налета | Процессы старения в трансформаторных “теплых” вводах с маслом Т-750 | Налет в виде желтого мелкодисперсного осадка на фарфоровых покрышках и остове. | Н2**, CO2* | H2/CH4>6 CO/CO2<0,3 |
9 | Ползущий разряд | Увлажнение бумаги, или неоднородность электрического поля, или образование осадка и его увлажнение | Науглероженные дорожки и “деревья” как на поверхности остова, так и внутри слоев бумаги | H2**, CH4*, С2H6* | C2H6/CH4>0.3 H2/CH4>6 |
26 | Образование Х-воска | Процессы старения вводов 220 кВ выключателей и ненагруженных трансформаторов с маслом ГК | Отложения в виде воска между слоями изоляции. | Н2**, C2H6**, CH4*, C2H2” | H2/CH4>5 С2Н4/С2Н6<0,7 |
6 | Увлажнение остова | Нарушение герметичности (в герметичных), старение и прямое проникновение влаги в негерметичных вводах | Вспучивание остова | С2Н2**, С2H4*, CH4*,H2”, C2H6” | С2Н2/С2Н4≥1 Н2/СН4≤3 |
13 | Тепловой пробой | Увлажнение, загрязнение слоев бумаги, обрыв проводников присоединения нулевой обкладки | Изменение цвета бумажной изоляции. Ее разрушение: прогар слоев изоляции остова. | С2Н4**и/или Н2**,СH4* C2H2”, С2Н6” | С2Н4/С2Н6>0,8 С2Н2/С2Н4>1 CO/CO2>0,2 |
** - газ с максимальным превышением порогового значения * - газ со значительным превышением порогового значения “ - газ с незначительным превышением порогового значения |
В пределах выборки рассматриваемого дефекта для каждого признака производятся следующие операции: ранжирование признака по возрастанию, определение границ диапазона значений, расчет прироста значений признака относительно предыдущего значения, сглаживание или отбрасывание крайних значений диапазона в зависимости от величины изменения признака; расчет математического ожидания и дисперсии измененной признака.
Далее производится нормировка математических ожиданий 7-ми признаков относительно их суммы. Таким образом, получается образ дефекта, соответствующий определенному классу состояния объекта, описанный в 8-мерном признаковом пространстве состояний (Ωy`)={x1Ωy,...,xNΩy}. Если синтез классов состояния производится в первый раз, то далее переходят к выборке фактов, соответствующих следующему классу технического состояния, взятому из априорного словаря и синтезу образа следующего дефекта Ωy+1. Если образы дефектов уже существовали, то проводится тестирование полученного образа на непротиворечивость уже имеющимся образам. Для этого проводят проверку на соответствие полученного класса состояния своей области состояний путем вычисления средней по области меры близости по среднеквадратичному критерию, взвешенному в соответствии с образами дефектов по формуле:

, (13)
где y - номер класса состояния в области состояний; L – количество дефектов в области состояний; xiΩy - координата нового образа, описывающего дефект, соответствующая i-му газу; Qiy - координата образа y-го дефекта из области состояний, соответствующая i-му газу; hjy - весовой коэффициент, учитывающий информативность i-го газа для y-го дефекта.
Весовые коэффициенты первоначально назначаются экспертами, исходя из характерности генерации газа для данного вида дефекта, затем уточняются с учетом значений дисперсии. При этом соблюдается условие:
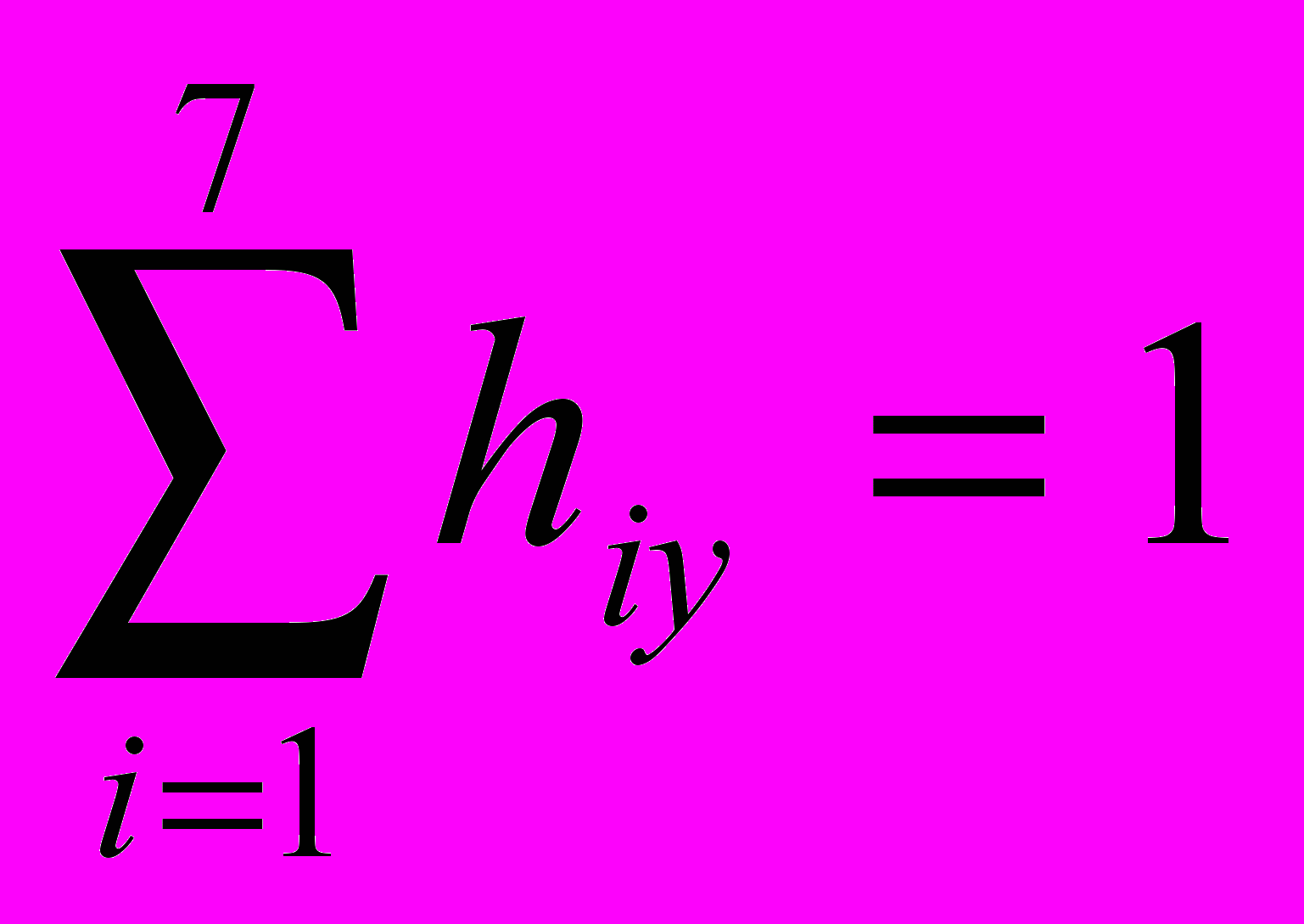
. (14)
Если синтезированный образ имеет минимальную меру близости по своей области состояния и старому образу своего класса состояния и, кроме того, дисперсии параметров нового образа не превышают значения дисперсии, полученные при предыдущем его синтезе, то координаты и дисперсии синтезированного нового образа автоматически заносятся в библиотеку графических образов дефектов БЗ. Иначе - синтезированный образ отклоняется, результаты сравнения выдаются эксперту для анализа. Изложенный выше алгоритм синтеза образа дефекта по результатам АРГ на основе фактов повреждений оборудования реализован в ЭДИС «Альбатрос».
Состояние объекта на основе результатов АРГ предложено отображать в виде 8-лепестковой диаграммы (рисунок 3), где по 7 лучам откладываются значения концентраций газов, а по восьмому лучу – их сумма в абсолютных значениях S (формула 12). Значения концентраций откладываются от окружности, показывающей границу обнаружения газов средствами измерения, которая, для удобства, принята равной 2 ppm по всем газам. Полученные при этом точки соседних радиальных лучей соединяются отрезками прямых, в
результате получается образ состояния диагностируемого объекта. Порядок расположения лучей определен таким образом, что в направлении от Н2 до С2Н2 идет нарастание силы проявления дефектов электрического характера, а в н
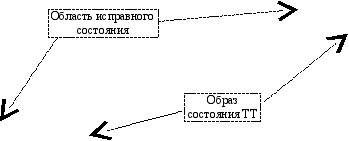
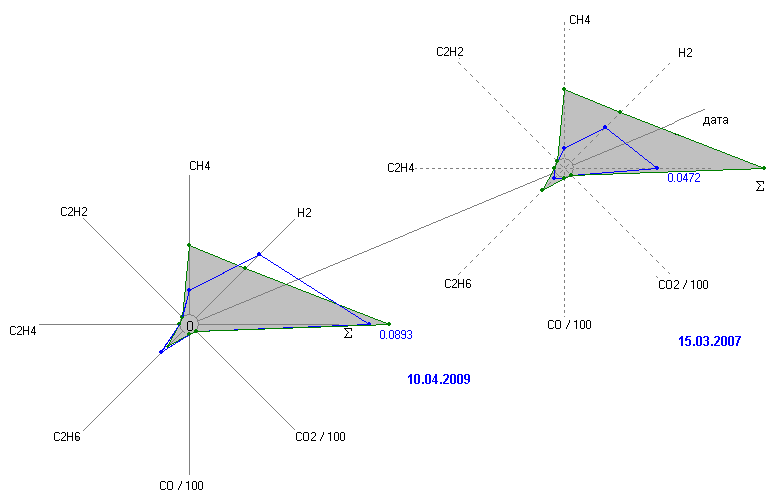
Рисунок 3 - Лепестковые диаграммы результатов АРГ
Известные графические методы идентификации дефектов (диаграмма состава газов относительно газа с максимальной концентрацией, предложенная японскими учеными, треугольник Дюваля, прямоугольники Доренбурга, параллелепипеды Кудерка), по сравнению с предложенной моделью, используют меньшее число газов, не описывают область исправного состояния объекта и не учитывают, насколько концентрации газов превышают свои ДЗ.
На первом этапе диагностики для выявления наличия развивающегося дефекта на лепестковой диаграмме в абсолютных значениях строятся образ состояния диагностируемого объекта по результатом АРГ и соответствующий ему образ ДЗ, зависящий от конструктивных особенностей и срока эксплуатации объекта. Если образ, описывающий диагностируемый объект выходит за пределы области, ограниченной образом ДЗ (заливка серым цветом на рисунке 3), то предполагается наличие развивающегося дефекта. Динамику роста газов можно увидеть, расположив образы, описывающие состояния объекта по оси времени. Сравнив скорости прироста газов с их ДЗ и ПДЗ, делаем вывод о том, быстро ли развивается дефект, и переходим к этапу его идентификации.
Логично предположить, что если конструктивные особенности оборудования влияют на образ его исправного состояния, то они должны влиять и на образ дефекта. Образы дефектов хранятся в виде относительных значений содержания газов, нормированных по взвешенной сумме концентраций семи
газов. Для того чтобы образ дефекта описывал состояние оборудования более точно, применяется следующая процедура его трансформации. Денормируем образы дефектов, умножив их на взвешенную сумму выбранного b-го образа исправного состояния SZb, и трансформируем образы дефектов, умножив их координаты на соответствующие коэффициенты трансформации Rib:
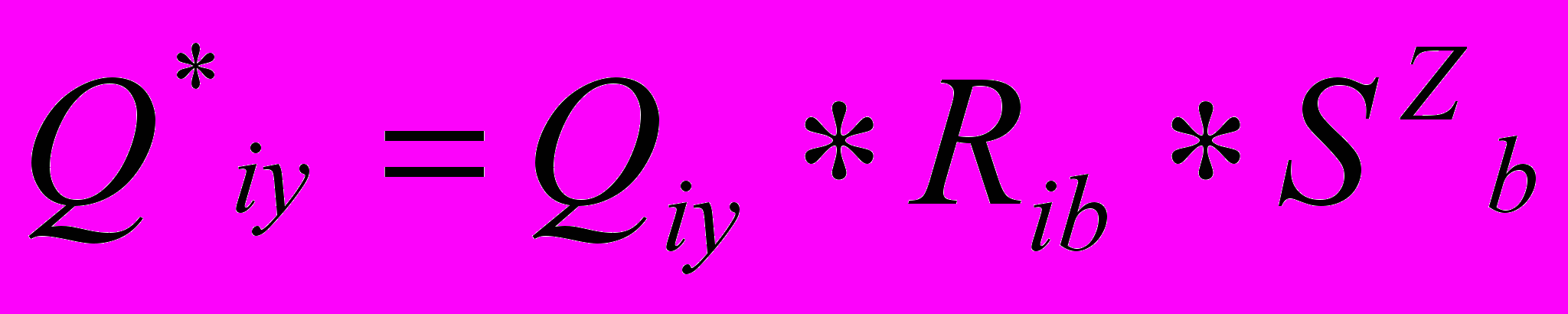
, (15)
где Qiy – i-координата y-го образа дефекта в относительных единицах;
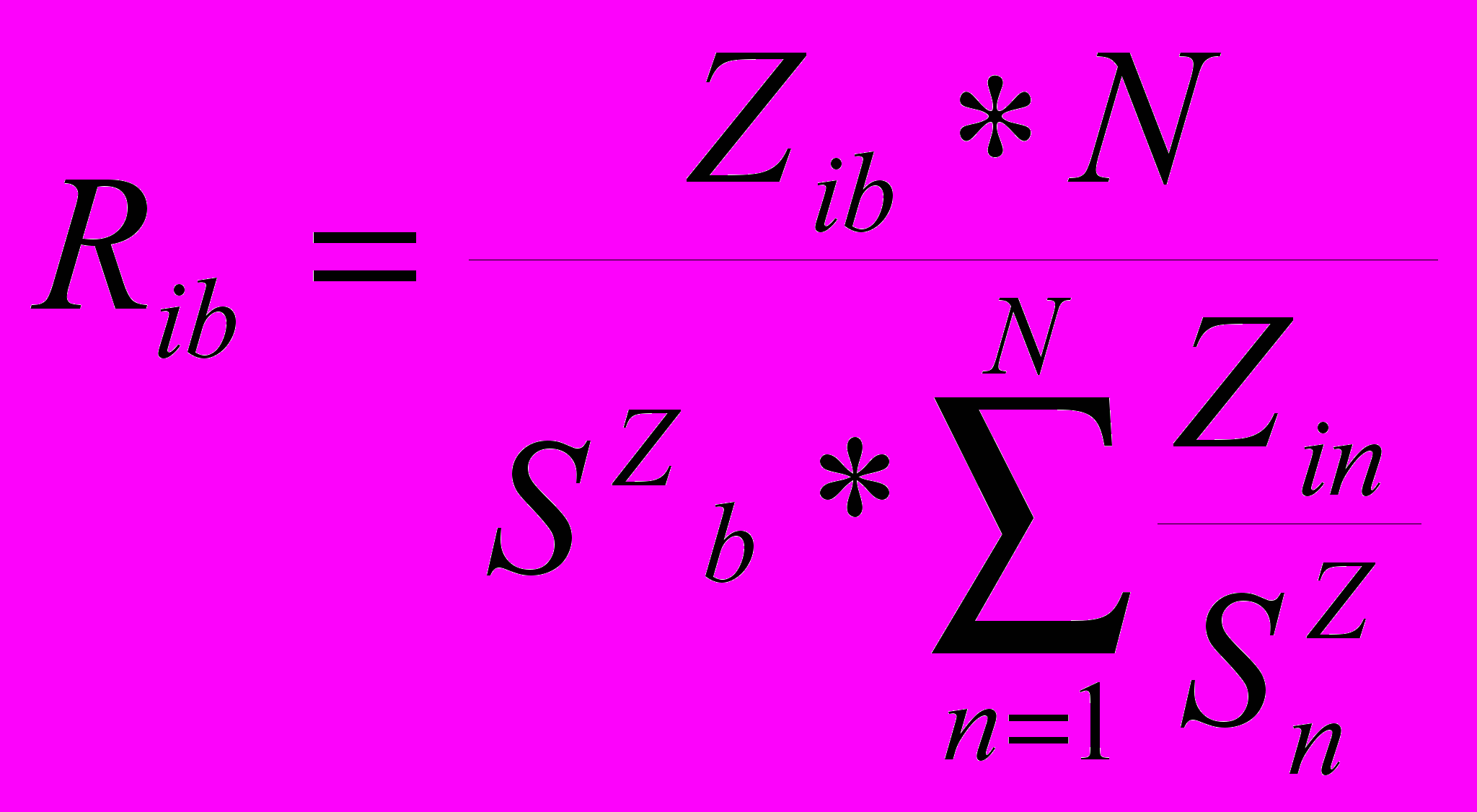
, (16)
где Zib – ДЗ концентрации i–го газа b-го образа исправного состояния в абсолютных величинах; N - количество образов ДЗ; n, b- индексы образов ДЗ.
Затем снова нормируем образы дефектов по взвешенной сумме:
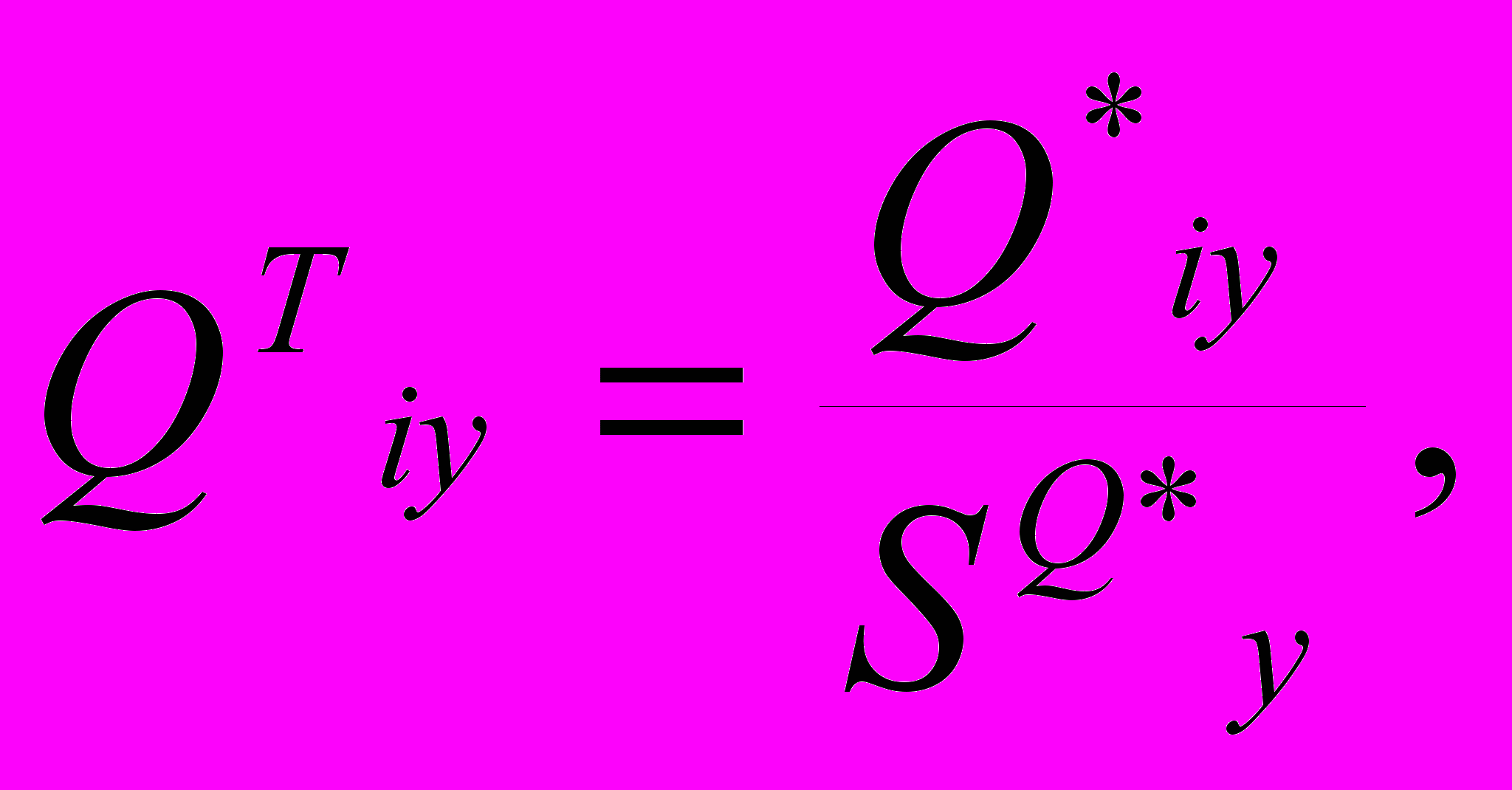
(17)
где SQ*y – взвешенная сумма концентраций газов y-го денормированного образа дефекта.
Далее трансформированные образы масштабируются таким образом, чтобы взвешенная сумма газов образа была равна взвешенной сумме газов диагностируемого объекта.
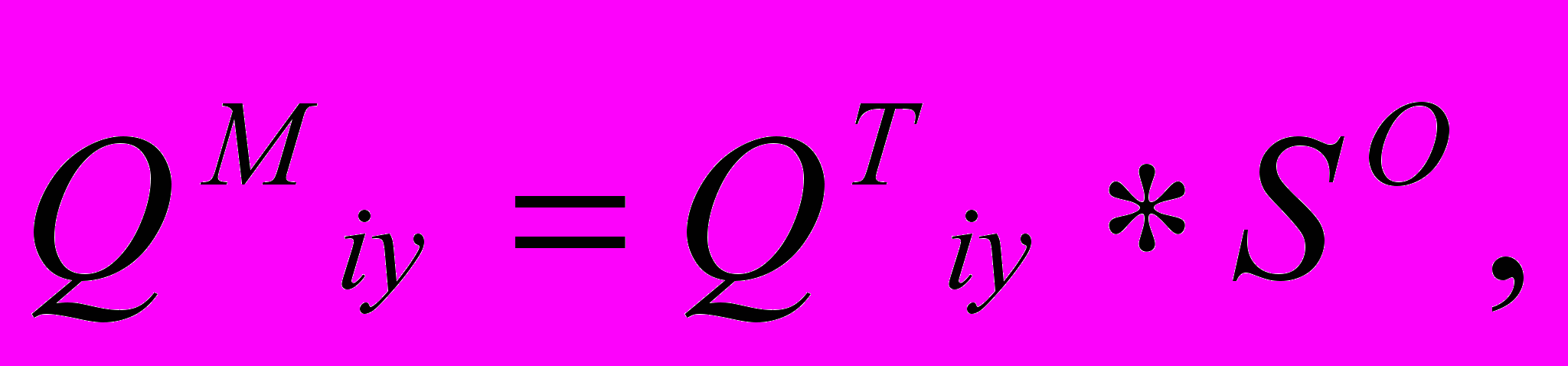
(18)
где SO – взвешенная сумма концентраций газов диагностируемого объекта.
Распознавание дефекта производится в геометрической трактовке путем вычисления меры близости по среднеквадратичному критерию, взвешенному в соответствии с образами дефектов по формуле:
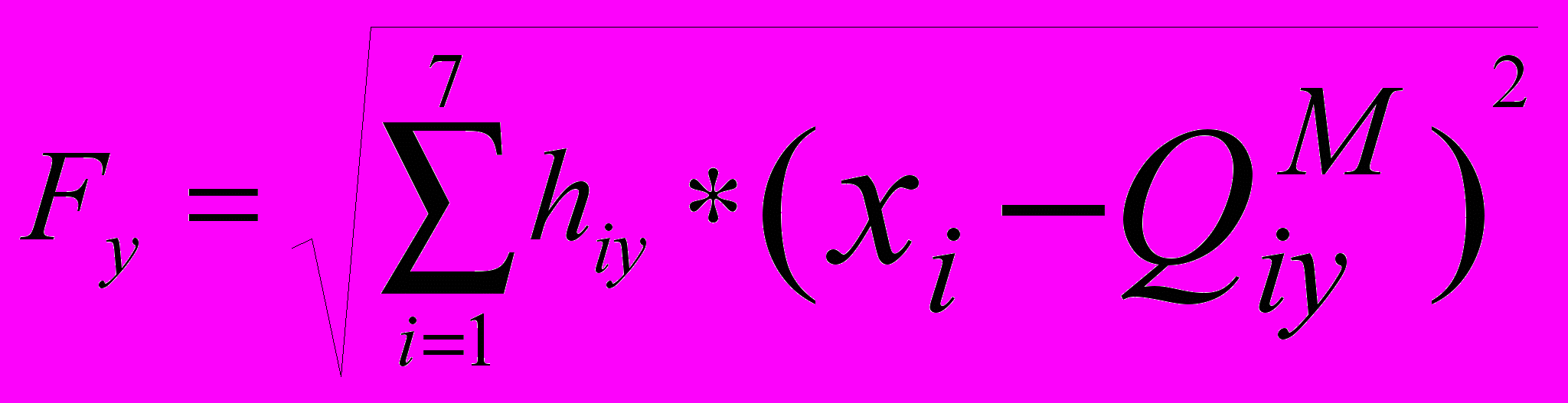
, (19)
где xi - координата образа диагностируемого объекта, соответствующая i-му газу и нормированная по взвешенной сумме газов; QMiy – i-координата масштабируемого образа y-го дефекта; hiy - весовой коэффициент.
Минимальное значение меры близости укажет нам на дефект в диагностируемом объекте. На заключительном этапе распознавания вводится величина, названная “мера родства” dF, позволяющая считать меры близости Fy для различных классов типовых дефектов одинаковыми. Это решение учитывает то, что при проведении АРГ хроматографическим методом погрешность измерения может достигать 20% и более, а также то, что существует неустойчивость, неоднозначность распознавания различных
классов состояния по ряду причин: наличия более одного дефекта; наличия некоторого “фона”, связанного с эксплуатационными причинами (доливка некачественного масла, более жесткий режим работы оборудования, плохая дегазация на заводе-изготовителе и т.д.); нахождения объекта в стадии изменения характера дефекта; нахождения объекта в стадии развития (усугубления) дефекта, т.е. в стадии перехода от одного класса состояния в другой в пределах одной области. Для определения величины “меры родства” dF для каждого класса состояния определяем меру близости Fy координат его образа от координат образов других дефектов из одной области состояний. Далее из всех возможных значений меры близости одной области выбираем минимальное значение, которое и будет искомой мерой родства dFa для области a:
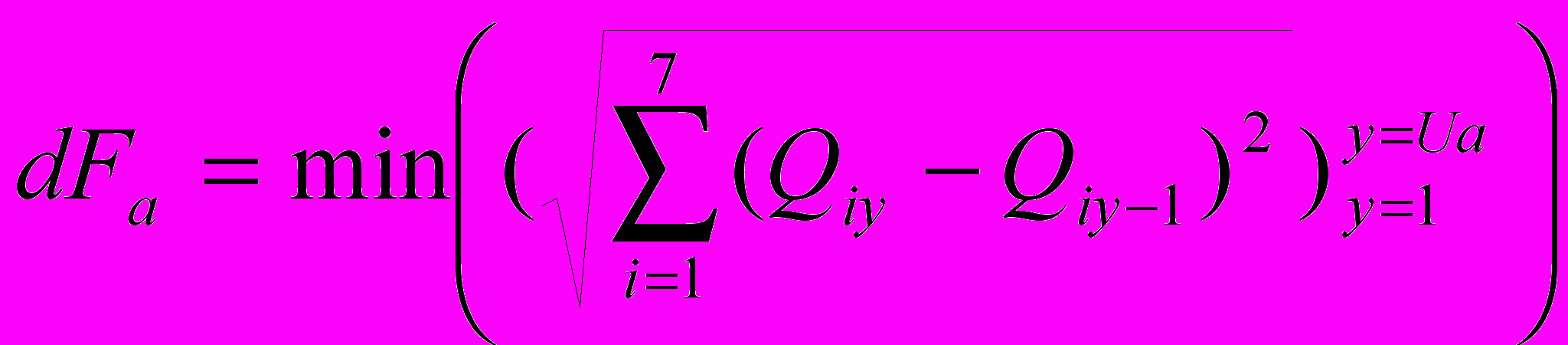
, (20)
г

(21)
Используя необходимую величину “меры родства” dFa, проверяем два дефекта с минимальными мерами близости, следующих за выбранным дефектом F1, могут ли они считаться “одинаково похожими” на образ диагностируемого объекта, т.е. выполняется ли равенство:

где
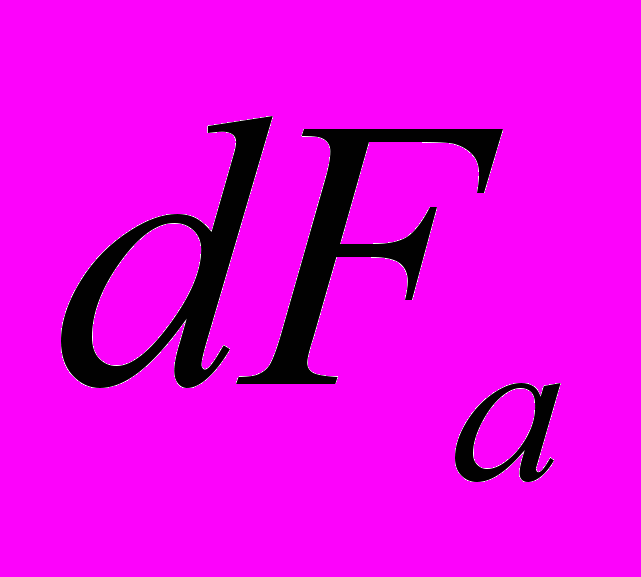
Далее из выбранных образов дефектов, которые считаем "одинаково похожими", для сведения к минимуму ущерба от ошибочного распознавания дефекта, выбираем типовой дефект с максимальным коэффициентом опасности: max(C1,C2,C3). Если после учета коэффициентов опасности неоднозначность в распознавании дефекта осталась, то из дефектов, которые считаем "одинаково похожими и одинаково опасными", выбираем дефект с максимальным коэффициентом вероятности: max(P1,P2,P3).
Значения коэффициентов опасности дефектов определялись на основании экспертных оценок, а коэффициенты вероятности их возникновения рассчитывались на основании статистики повреждаемости данного вида оборудования. Предложенный способ идентификации дефектов с помощью новой графической модели обладает более широкими возможностями по точности и диапазону распознаваемых дефектов, исключает нераспознаваемые состояния объекта. Предложенная графическая интерпретация АРГ,
дополненная алгоритмом распознавания образов и методикой синтеза классов технического состояния, не уступает возможностям нейронной сети с функцией самообучения. Вместе с тем, этот альянс, позволяет эксперту без участия программиста добавлять новые образы, обладает наглядностью, задействует образное мышление человека, а значит, делает процесс анализа информации по диагностике оборудования более эффективным.
Для получения критериев распознавания класса технического состояния ТТ и ТН по результатам АРГ была собрана БД из 98 случаев фактов вскрытия. Далее был составлен словарь классов технического состояния ТТ и ТН с учетом соответствия между видами дефектов, причинами их возникновения и описанием последствий, обнаруженных после вскрытия оборудования. Затем собранные факты были проанализированы совместно с экспертами, отнесены к классам технического состояния и отмечены необходимыми метками. Используя третью методику были синтезированы 9 классов технического состояния для ТТ и 3 для ТН в виде графических образов, приведенных на рисунках 4-12 для ТТ и 13-15 для ТН.
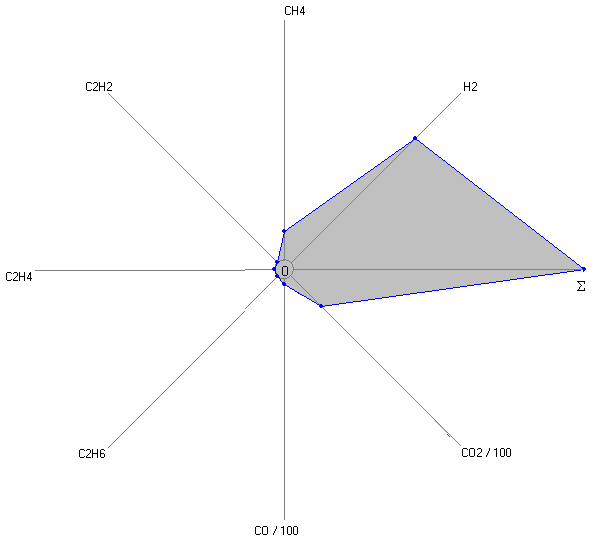
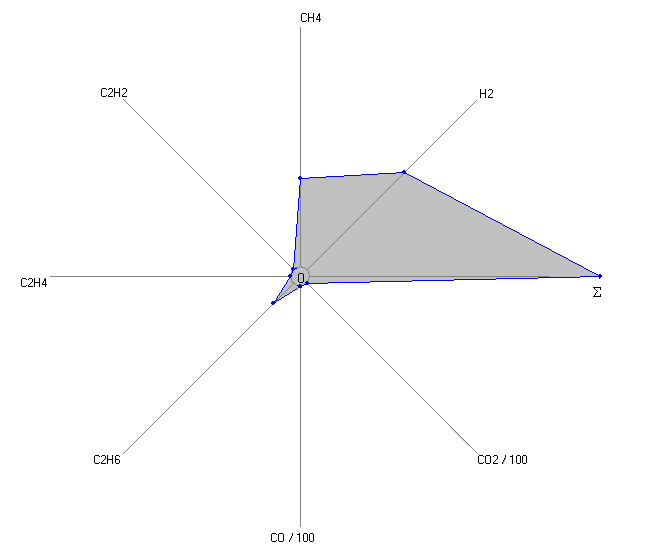
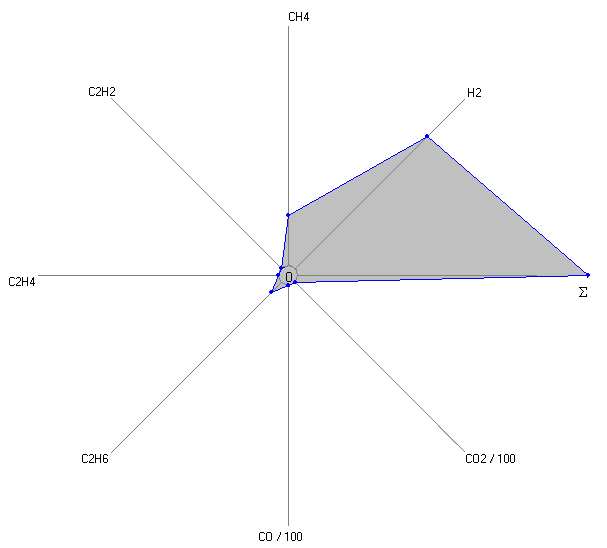
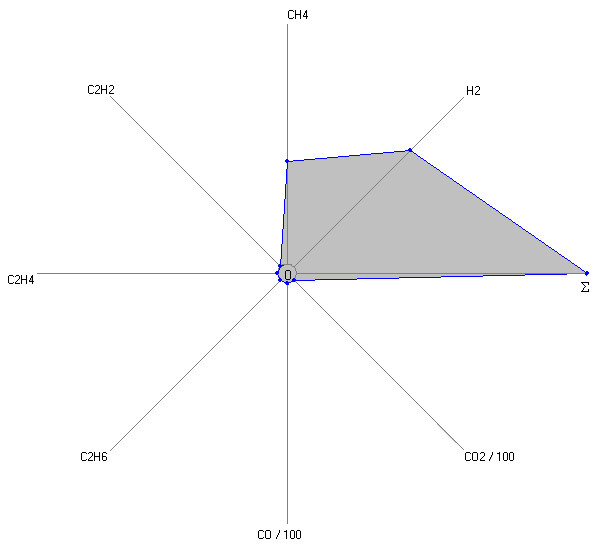
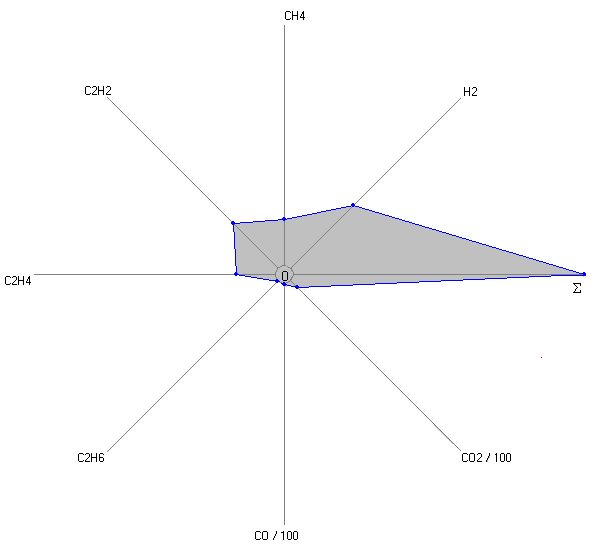
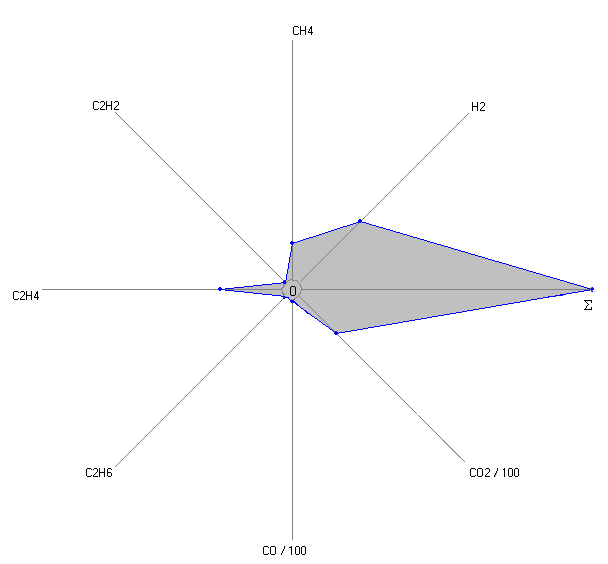
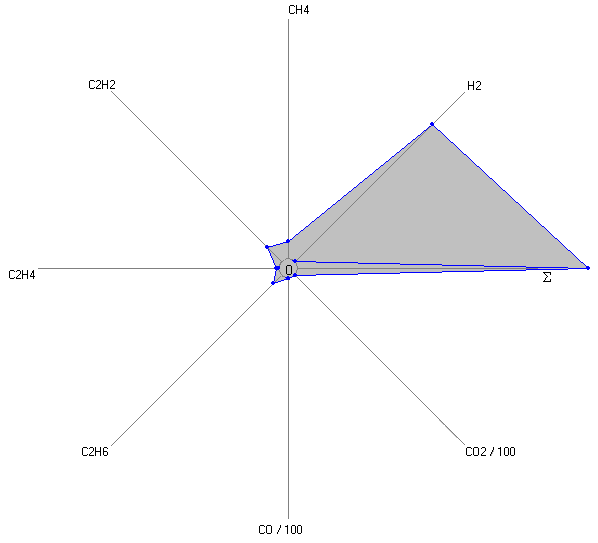
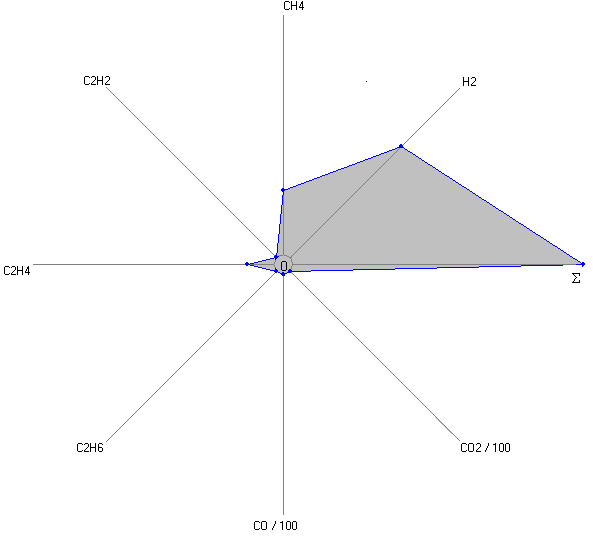
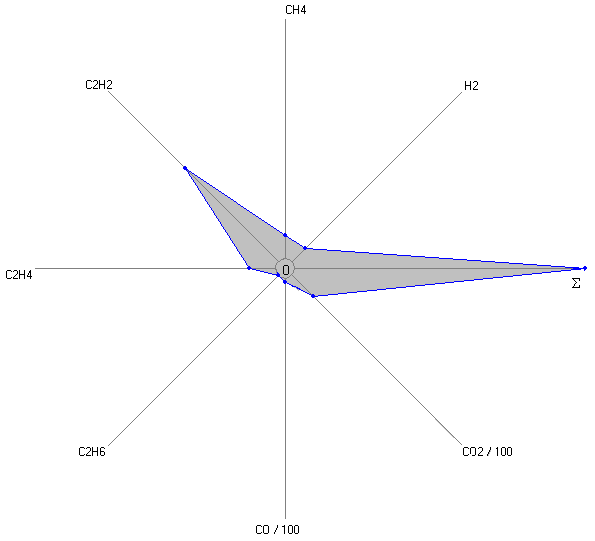
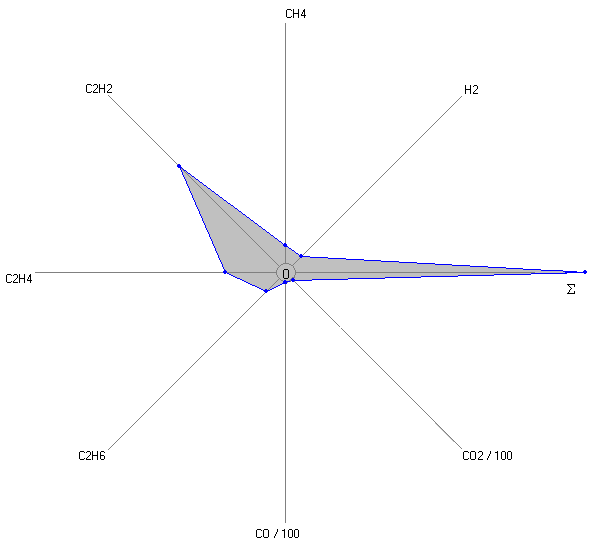
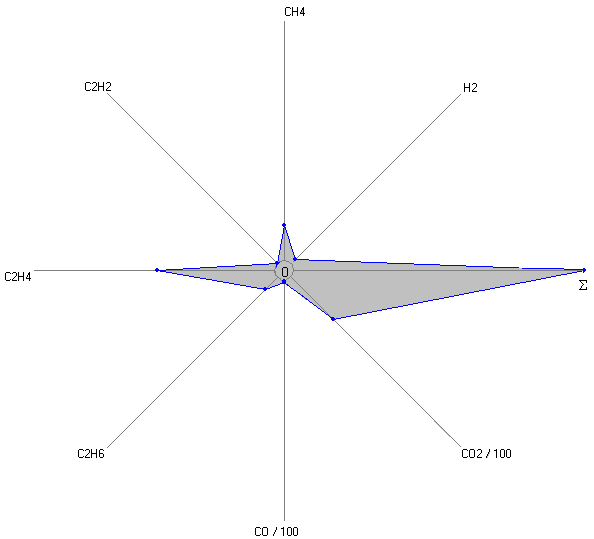