Методические рекомендации по выполнению для специальности 2-36 01 01 "Технология машиностроения" специализации 2-36 01 01 31 "Технология обработки материалов на станках и автоматических линиях"
Вид материала | Методические рекомендации |
- Программа преддипломной практики студентов специальности 1-36 01 01 «Технология машиностроения», 336.91kb.
- Рабочая программа и методические указания к выполнению контрольной работы для заочной, 305.14kb.
- Методические указания по выполнению лабораторных работ по курсу «Системы автоматизированного, 369.98kb.
- Технический Университет Молдовы, специальность «Металлорежущие станки и инструмент», 13kb.
- Методические рекомендации по изучению учебной дисциплины, задания для домашней контрольной, 567.53kb.
- Программа вступительного экзамена по специальности 05. 27. 06 «Технология и оборудование, 81.6kb.
- Программа и контрольные задания для учащихся-заочников по специальности 2-36, 764.27kb.
- Методические указания к выполнению лабораторной работы №10 для студентов очной формы, 240.19kb.
- Методические указания к выполнению контрольной работы №1 для студентов заочной формы, 246.46kb.
- Методические указания рассмотрены и рекомендованы к изданию методическим семинаром, 405.03kb.
МИНИСТЕРСТВО ОБРАЗОВАНИЯ РЕСПУБЛИКИ БЕЛАРУСЬ
УЧРЕЖДЕНИЕ ОБРАЗОВАНИЯ
«ГОМЕЛЬСКИЙ ГОСУДАРСТВЕННЫЙ МАШИНОСТРОИТЕЛЬНЫЙ ТЕХНИКУМ»
КУРСОВОЙ ПРОЕКТ
по дисциплине: Проектирование технологических процессов
обработки материалов на станках и автоматических линиях
МЕТОДИЧЕСКИЕ РЕКОМЕНДАЦИИ ПО ВЫПОЛНЕНИЮ
для специальности 2-36 01 01 "Технология машиностроения"
специализации 2-36 01 01 31 "Технология обработки материалов на станках и автоматических линиях"
Гомель, 2004
Разработчик: Голуб Е.И., преподаватель Учреждения образования
«Гомельский государственный машиностроительный
техникум»
Методические рекомендации разработаны для учащихся специальности 2-36 01 01 специализации 2-36 01 01 31 дневной, вечерней и заочной формы обучения, изучающих дисциплину «Проектирование технологических процессов обработки материалов на станках и автоматических линиях», и выполняющих по ней курсовой проект. Кроме того, рекомендациями могут пользоваться учащиеся, находящиеся на дипломном проектировании, при выполнении технической части дипломного проекта, а также учащиеся, находящиеся на технологической или преддипломной практике, подбирающие материал для будущего проектирования.
Обсуждено и одобрено на заседании цикловой комиссии
"Технология и автоматизация машиностроения"
Протокол № 7 от февраля 200 4 г.
Содержание
Задание на курсовое проектирование 4
Предисловие 5
Рекомендации по выполнению отдельных частей курсового проекта 5
Введение 5
1 Анализ исходных данных 6
1.1 Описание конструкции и служебного назначения детали 6
1.2 Определение типа производства и его характеристика 7
1.3 Анализ детали на технологичность 8
2 Разработка технологии обработки детали 10
2.1 Анализ технических требований, предъявленных к детали.
Рекомендации по их обеспечению и контролю 10
2.2 Выбор вида и обоснование метода получения заготовки 11
2.2.1 Описание метода получения заготовки 11
2.2.2 Определение припусков и допусков по стандартам. Расчет
размеров и массы заготовки, коэффициента использования материала 11
2.3 Разработка проектного технологического процесса 12
2.3.1 Анализ базового технологического процесса и составление
последовательности обработки для проектируемого техпроцесса 12
2.3.2 Выбор и обоснование технологических баз 12
2.3.3 Выбор оборудования и технологической оснастки 13
2.4 Разработка операционного технологического процесса 14
2.4.1 Определение межоперационных припусков и операционных
размеров 14
2.4.2 Определение режимов резания на проектируемые операции
(переходы). Сводная таблица режимов резания 14
2.4.3 Нормирование проектируемой операции. Сводная таблица
норм времени 15
3 Организация производства на участке 16
3.1 Определение количества оборудования на участке 16
3.2 Определение количества производственных рабочих 17
4 Разработка плана участка 19
5 Сравнительная характеристика базового и проектного вариантов
техпроцесса механической обработки детали 20
Приложение А 21
Приложение Б 24
Приложение В 25
Приложение Г 26
Приложение Д 28
Приложение Е 29
Приложение Ж 30
Литература 31
МИНИСТЕРСТВО ОБРАЗОВАНИЯ РЕСПУБЛИКИ БЕЛАРУСЬ
УЧРЕЖДЕНИЕ ОБРАЗОВАНИЯ
«ГОМЕЛЬСКИЙ ГОСУДАРСТВЕННЫЙ МАШИНОСТРОИТЕЛЬНЫЙ ТЕХНИКУМ»
«Утверждаю»
Председатель цикловой комиссии
_______________________________
" " 200__ г.
ЗАДАНИЕ
на курсовое проектирование
Учащемуся___________________________________________________________________________________________
курса __________________группы____________________
по дисциплине «Проектирование технологических процессов обработки материалов на станках и автоматических линиях»
Тема курсового проекта: Разработка технологического процесса механической обработки детали__________________
___________________________________________________________________________с применением станков с ЧПУ
Исходные данные
Годовой объём выпуска _________________________ Режим работы участка___________________________
Прочие данные_______________________________________________________________________________
СОСТАВ И ГРАФИК ВЫПОЛНЕНИЯ ПРОЕКТА
СОСТАВ ПРОЕКТА | Срок |
1 | 2 |
А ПОЯСНИТЕЛЬНАЯ ЗАПИСКАВведение
Технический эскиз | |
2.2.2 Определение припусков и допусков по стандартам. Расчёт размеров и массы заготовки | |
| |
| |
| |
2.4.3 Нормирование проектируемой операции. Сводная таблица норм времени | |
| |
4. Разработка плана участка | |
5. Сравнительная характеристика базового и проектного вариантов технологического процесса Заключение | |
Б КОМПЛЕКТ ТЕХНОЛОГИЧЕСКОЙ ДОКУМЕНТАЦИИ
| |
В ГРАФИЧЕСКАЯ ЧАСТЬ
| |
| |
4 Чертеж плана участка (0,25 …0,5 формата А1) | |
Дата выдачи «_____»_____________________200__г Дата окончания «_____»____________________200__г
Преподаватель – руководитель
курсового проекта______________________________ Подпись учащегося____________________
ПРЕДИСЛОВИЕ
Курсовой проект является комплексной работой, которая выполняется с целью обобщения, систематизации, углубления и закрепления знаний по технологии машиностроения и проектированию технологических процессов, выработки навыков самостоятельного проектирования рациональных технологических процессов, работы со справочной, нормативной и технической литературой, решения конкретных технологических задач.
Задание на курсовое проектирование, оформленное на бланке установленного образца, выдается учащемуся во время технологической практики и содержит название темы проекта и исходные данные, необходимые для проектирования.
Рекомендации по выполнению проекта содержатся в настоящем пособии.
Правила оформления курсового проекта регламентированы в стандарте Учреждения образования «Гомельский государственный машиностроительный техникум» «Оформление дипломных и курсовых проектов» системы стандартов для специальности 2-36 01 01.
РЕКОМЕНДАЦИИ ПО ВЫПОЛНЕНИЮ ОТДЕЛЬНЫХ ЧАСТЕЙ КУРСОВОГО ПРОЕКТА
ВВЕДЕНИЕ
Во введении отражаются перспективы развития той отрасли машиностроения, для которой разрабатывается проект; приводятся основные сведения о предприятии и выпускаемой им продукции. Описывается назначение изделия, включающего деталь, заданную для проектирования.
Введение обязательно должно быть увязано с темой проекта: в нем отмечаются основные цели и мероприятия, связанные с дальнейшим повышением технического уровня производства, принятые при разработке измененного варианта технологического процесса (ТП) механической обработки детали, заданной для проектирования. Изменения могут вносить с целью повышения степени механизации, роста производительности труда, снижения материалоемкости, уменьшения себестоимости и в случае изменения типа производства, существовавшего на предприятии, для реорганизации производства.
Работа над введением начинается перед проектированием и завершается по его окончании.
1 АНАЛИЗ ИСХОДНЫХ ДАННЫХ
- Описание конструкции и служебного назначения детали
При разработке этого пункта составляется описание назначения самой детали, основных ее поверхностей и влияния их взаимного расположения, размерной точности и шероховатости на качество работы сборочной единицы в целом. При описании назначения основных поверхностей детали ссылки должны даваться на номера поверхностей детали по техническому эскизу.
Описание должно быть выполнено в соответствии с рекомендациями: [9, с.10…11]; [10, c.10…11]; [15, с.20…21] и содержать характеристику химического состава и механических свойств материала, выбранные по соответствующему стандарту на материал детали и оформленные в таблицы: 1.1-Химический состав материала и 1.2–Физико-механические свойства материала.
Технический эскиз выполняется в пояснительную записку на листе бумаги необходимого формата в соответствии со стандартами ЕСКД и содержит:
1 − чертеж детали в необходимом количестве проекций, видов, разрезов, сечений с указанием всех размеров и их точности в квалитетах в соответствии с ГОСТ 25347-82; допусков отклонений от геометрической формы поверхностей, допусков отклонений от взаимного расположения поверхностей и осей условными обозначениями по ГОСТ 2.308-79; шероховатости поверхностей по параметру Ra предпочтительного применения по ГОСТ 2789-73 условными обозначениями по ГОСТ 2.309-73 с учетом изменений, внесенных в него ИУС РБ № 3 2003;
2 − технические требования, предъявленные к детали;
3 − массу и материал детали с указанием стандарта в соответствующих графах основной надписи;
4 − номера всех обрабатываемых конструктивных элементов, проставленные в кружочках на концах выносных линий от соответствующих элементов.
Конструктивным элементом является поверхность или совокупность поверхностей, представляющих собой единый элемент: ступень в отверстии или на наружной поверхности; самостоятельно оформленный торец; резьбовая, зубчатая, шлицевая, шпоночная, и др. поверхность; паз, фаска, канавка для выхода шлифовального круга или сбега резьбы; отверстие под крепёж и т.д.
Технический эскиз располагается в пояснительной записке между первой и второй частями.
- Определение типа производства и его характеристика
Тип производства определяется по коэффициенту закрепления операций (Кзо). Предварительно на основе типового технологического процесса его можно определить по формуле:
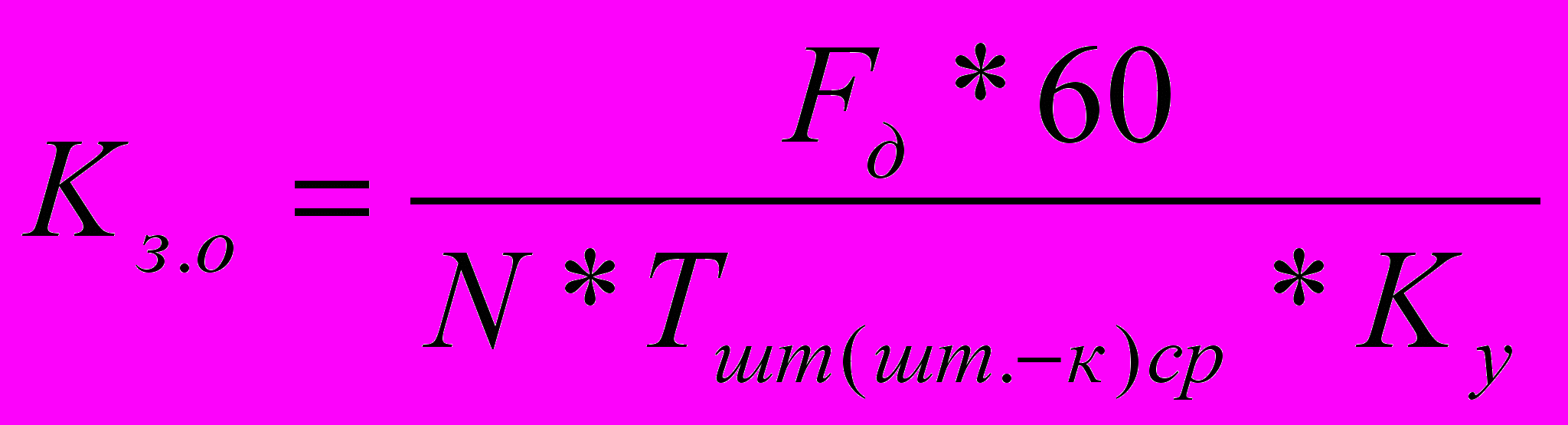
где Fд - действительный годовой фонд времени работы оборудования, час,
[9, с.22, таблица 2.1];
N - годовой объём выпуска детали, шт.;
Тшт(шт.-к)ср - среднее штучное (для массового производства) или штучно-
калькуляционное (для серийного производства) время, мин.;
kУ - коэффициент ужесточения заводских норм, kУ=0,7…….0,8.
По полученной величине КЗ.О. определить тип производства:
КЗ.О. | Тип производства |
До 1 | Массовый |
Свыше 1 до 10 | Крупносерийный |
Свыше 10 до 20 | Среднесерийный |
Свыше 20 до 40 | Мелкосерийный |
Свыше 40 | Единичный |
В зависимости от полученного типа производства определить такт выпуска (для массового производства) или величину производственной партии (для серийного производства).
Такт выпуска (t):
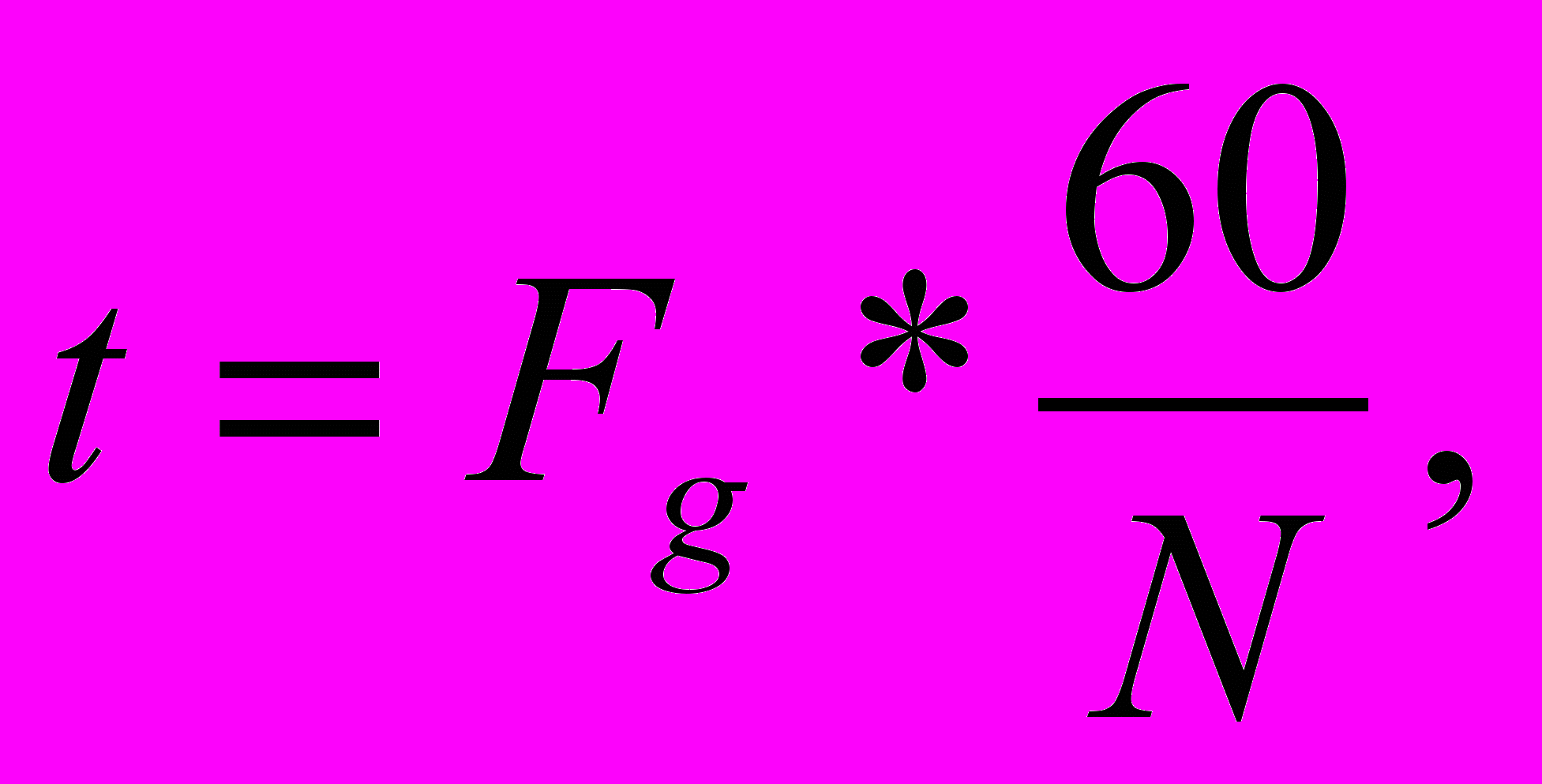
Величина производственной партии (ng):
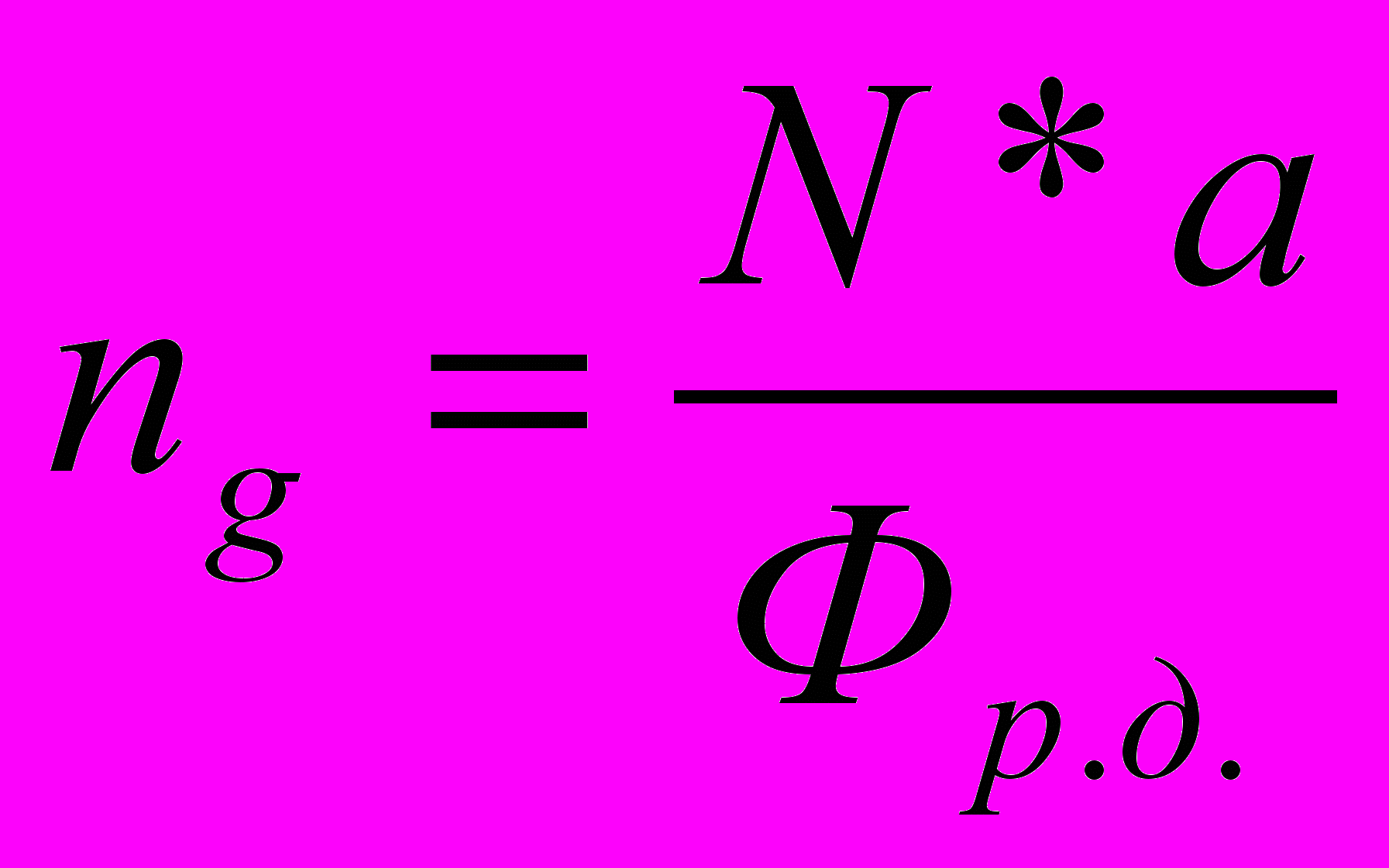
где a – число дней, на которые необходимо иметь запас деталей.
a=2…5 дней – для крупных деталей;
a=3…15 дней – для средних деталей;
a=10…30 дней – для мелких деталей.
Фр.д. – число рабочих дней в году:
Фр.д.=365-(104+8)=253 дня.
Привести краткую характеристику полученного типа производства.
Проанализировать вид существующей на производстве заготовки с учетом полученного типа производства.
Произвести анализ заводского техпроцесса механической обработки детали с точки зрения организации производства, применяемого оборудования и технологической оснастки, режимов резания и норм времени, в соответствии с типом производства.
1.3 Анализ детали на технологичность
Выполнить качественный анализ детали на технологичность в соответствии с методикой: [9, c.10…18]; [10, c.11….19]; [15, c.21…23]; [21, c.26…28].
Количественный анализ детали на технологичность заключается в расчете коэффициентов унификации (Ку) и использования материала (КИМ).
Для расчета коэффициента унификации необходимо выполнить отработку элементов детали на унифицированность, заполняя таблицу.
Таблица 1.3 - Отработка элементов детали на унифицированность
Номер элемента | Выдерживаемые размеры | Стандарт на элемент |
1 | 2 | 3 |
Первые две графы заполняются по техническому эскизу.
В третью графу необходимо заносить данные, показывающие выполнен ли конструктивный элемент по требованиям соответствующего стандарта (с указанием номера стандарта). Проверку степени унифицированности проводить по стандарту на соответствующие конструктивные элементы детали или по справочникам [7], [2].
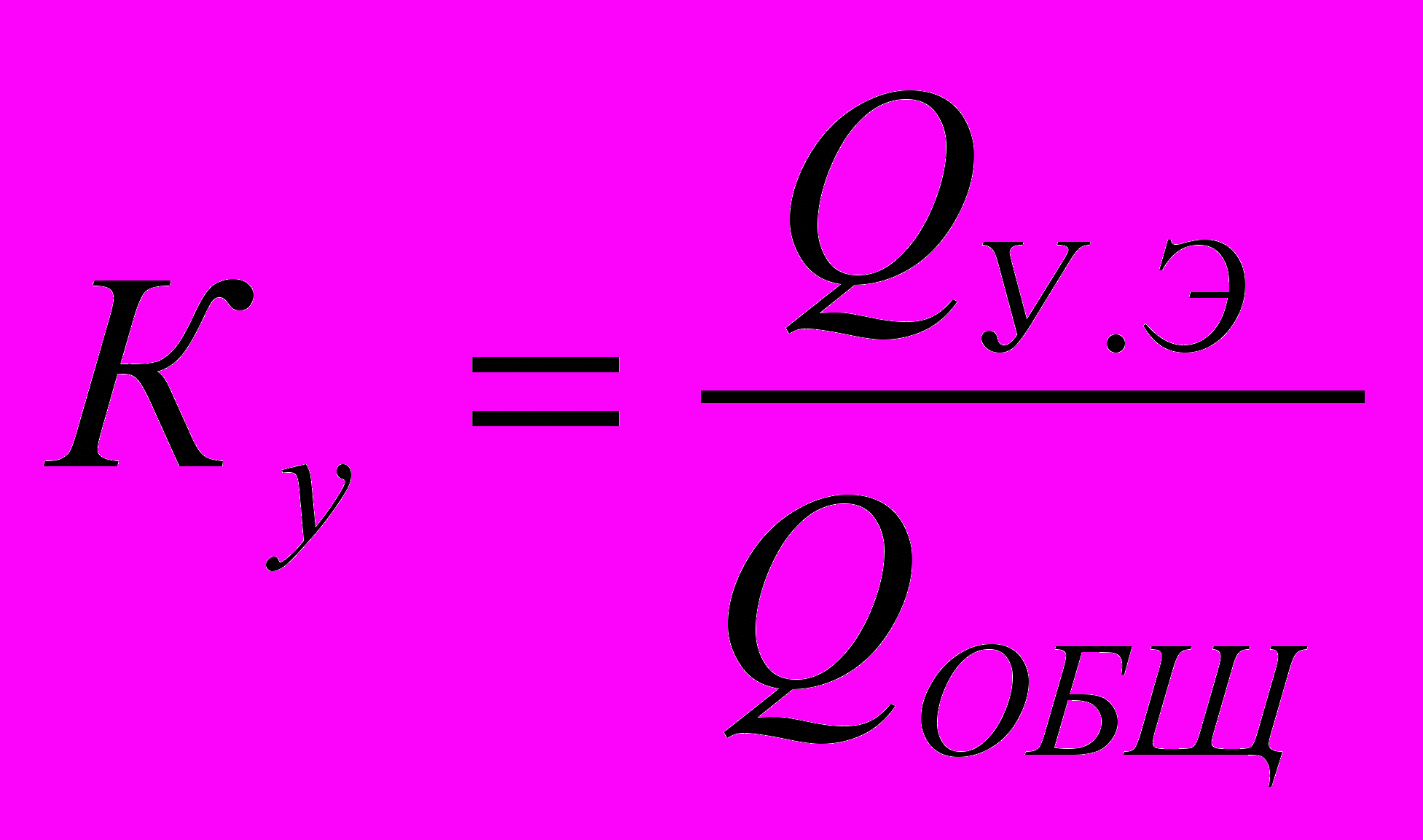
где QУ.Э. - число конструктивных элементов детали, которые выполнены по
стандартам: резьбовые, зубчатые, шлицевые поверхности, шпоночные пазы, фаски, радиусы скругления, отверстия под крепеж, отверстия центровые, канавки для сбега резьб, резьбовые недорезы, сбеги, проточки и фаски, канавки для установки уплотнений на деталях пневмо-и-гидроаппаратуры, канавки для выхода резцов при тонком точении и растачивании или для выхода шлифовальных кругов, поверхности опорные под винты, болты, гайки, заклепки, шайбы, шурупы и т.д.; или в соответствии с нормальными рядами размеров и
конусов: диаметральные размеры ступеней в отверстиях и на наружных поверхностях, конические поверхности и т.д.;
QОбЩ. - число всех конструктивных элементов детали.
Деталь считается технологической, если КУ>0,6.
Коэффициент использования материала определяется по формуле:
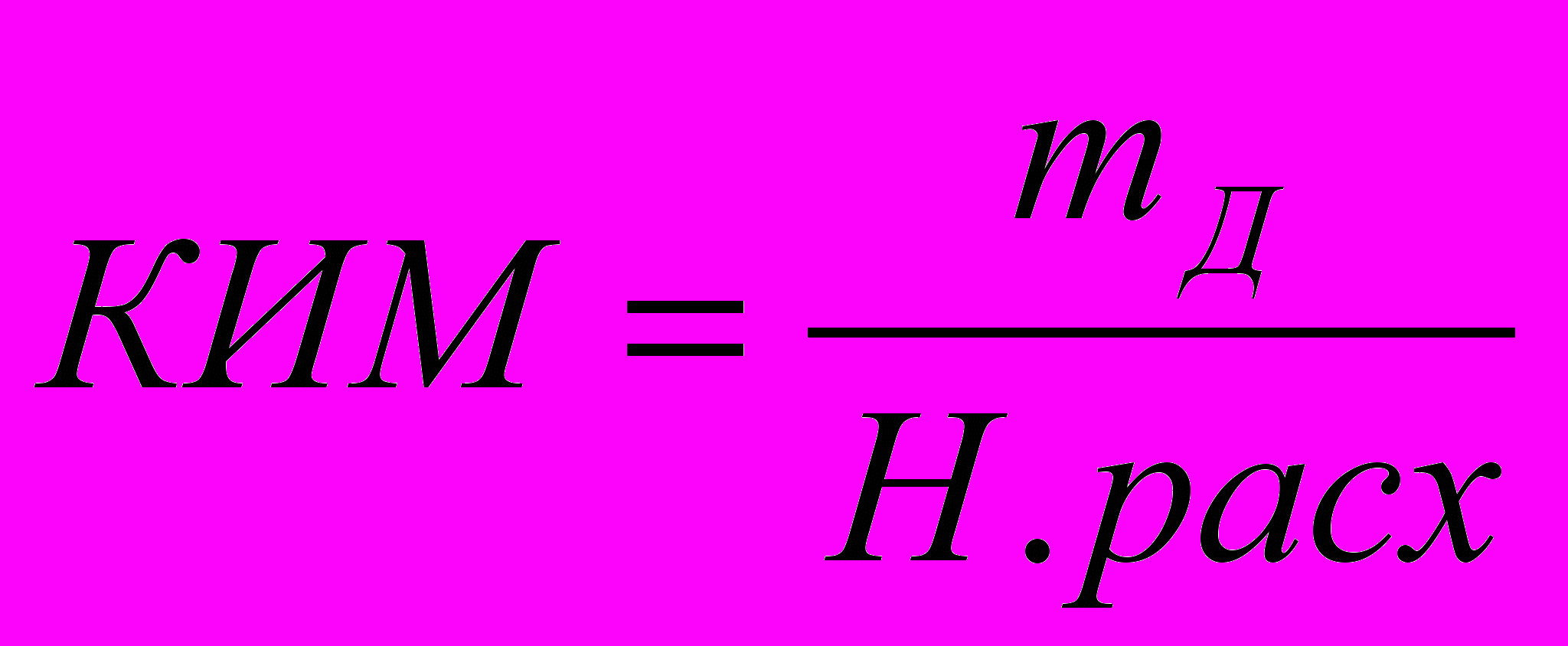
где тД - масса детали, кг;
Н.расх - норма расхода материала, кг.
Данные по Н.расх предварительно можно подобрать по типовому ТП механической обработки детали.
Деталь считается технологичной, если КИМ:
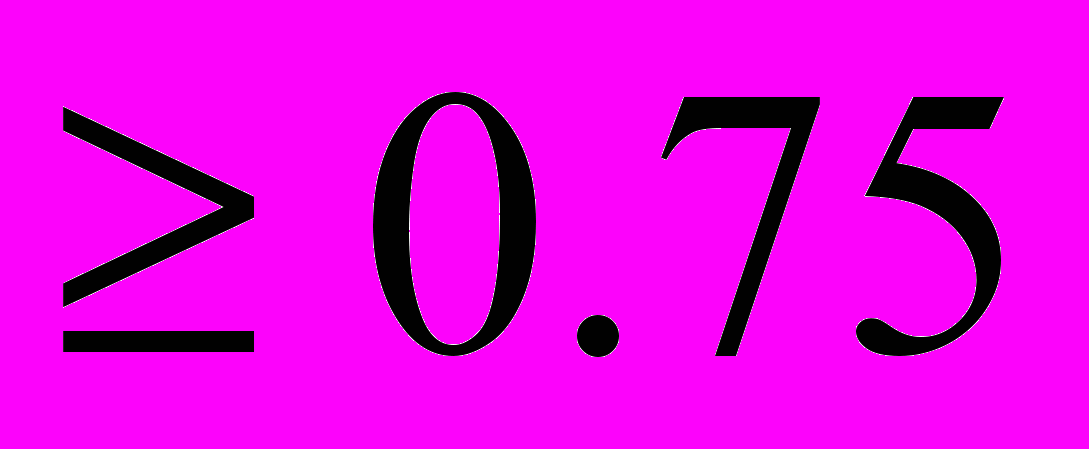
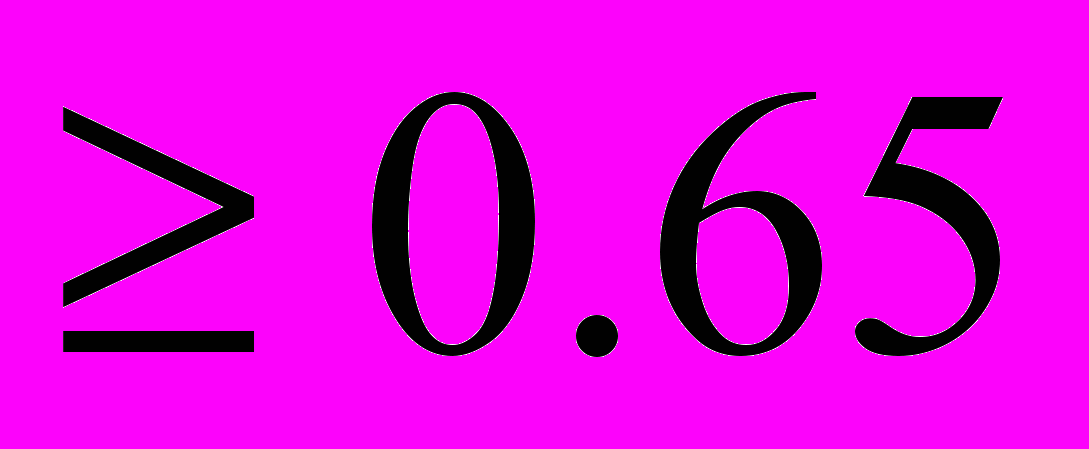
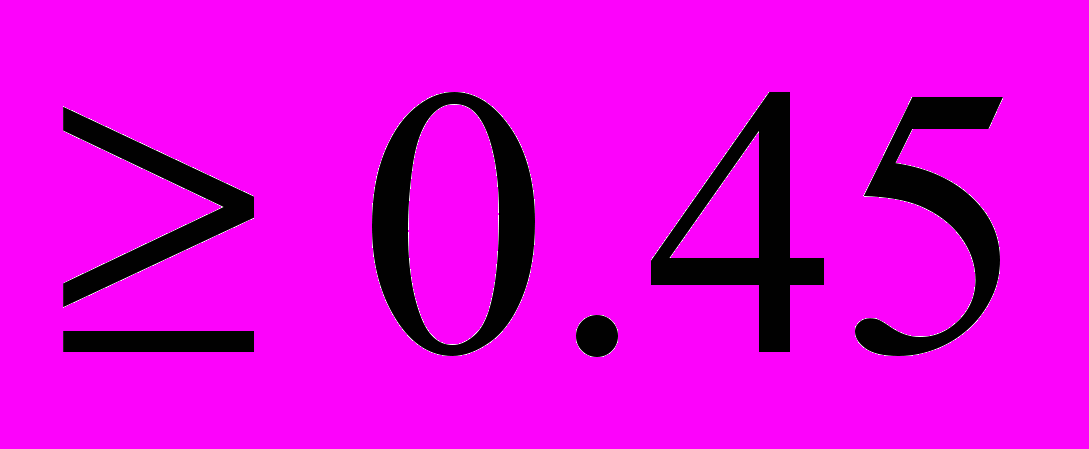
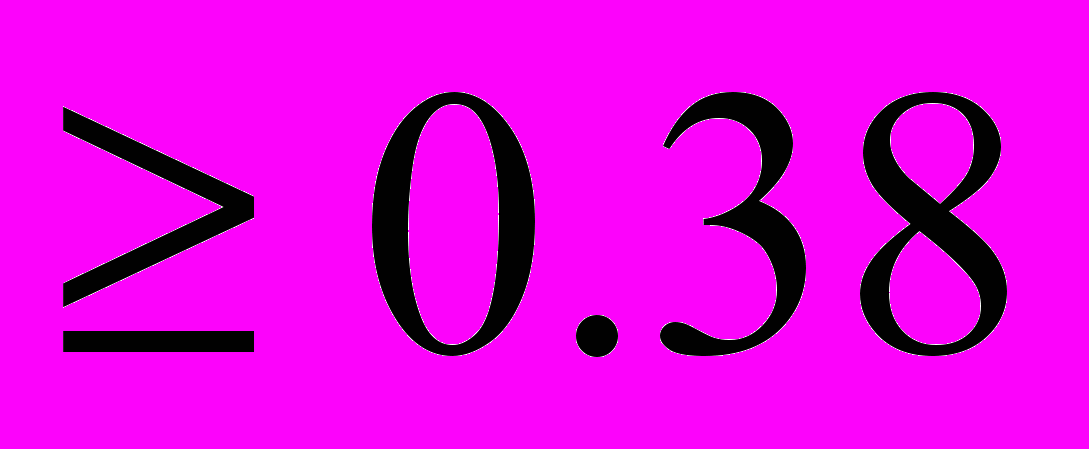
При отсутствии типовых данных Н.расх можно рассчитать по формуле:
Н.расх=тЗ+тОТХ.З., кг (1.6)
где тОТХ..З. - масса отходов при производстве заготовки.
Для штамповок, полученных на молотах, тОТХ..З. составляет около 20% массы заготовки. Для штамповок, полученных на прессах, и для отливок – от 10% (для крупных
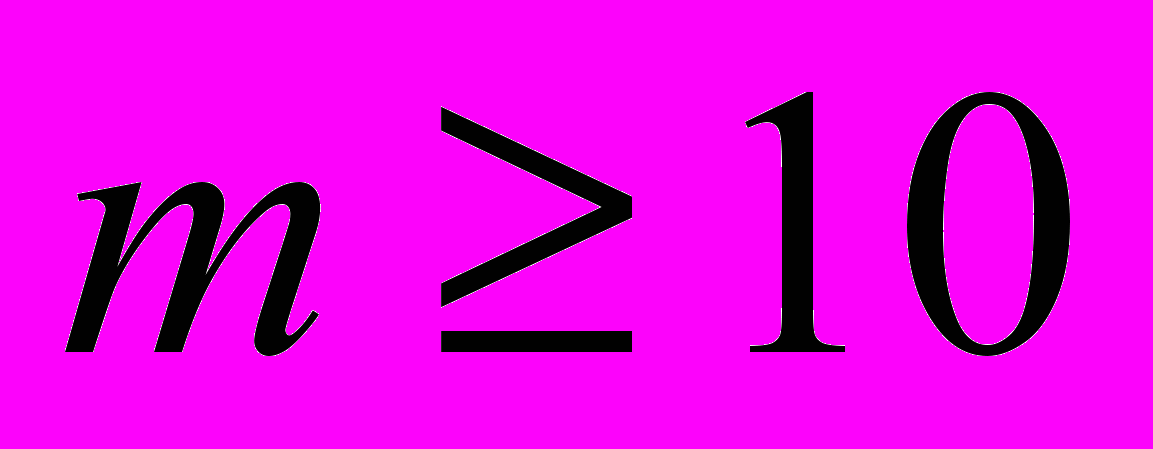
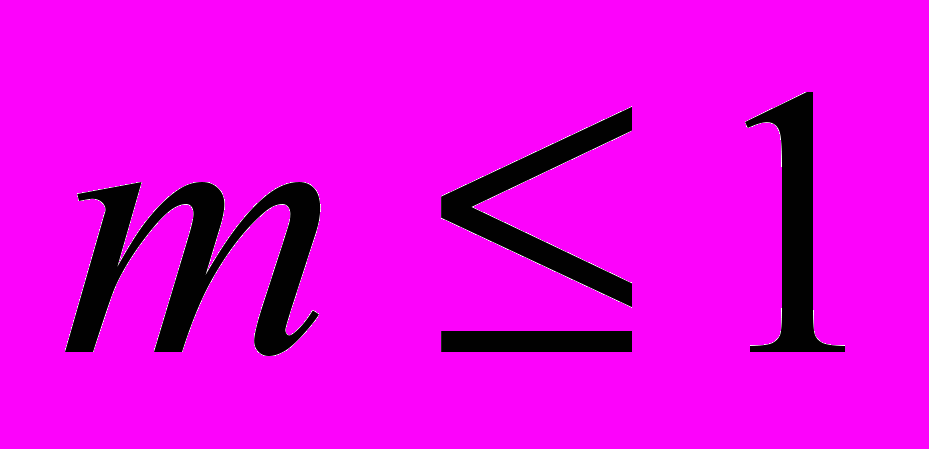
Для заготовок в виде проката тОТХ..З. состоит из ширины пропила или отрезки, длины концевого отхода, оставшегося в патроне или цанге, длины отхода на некратность.
2 РАЗРАБОТКА ТЕХНОЛОГИИ ОБРАБОТКИ ДЕТАЛИ
- Анализ технических требований, предъявленных к детали.
Рекомендации по их обеспечению и контролю
Этот пункт выполняется в виде таблицы.
Таблица 2.1-Анализ технических требований
Номер конструктивного элемента | Размеры и требования к их размерной и геометрической точности | Требования к шеро-ховатости поверхности | Требования к точности взаимного расположения поверхностей и осей | Методы достижения точности: способы базирования и виды обработки | Методы контроля и средства измерения |
1 | 2 | 3 | 4 | 5 | 6 |
Первые четыре графы заполняются по техническому эскизу и чертежу детали.
Во вторую графу, кроме посадки и точности размера в квалитетах, заносятся требования к геометрической точности поверхности.
В пятой графе должны быть отображены соображения по методам обеспечения заданных параметров.
При этом необходимо указывать не только последний переход механической обработки, но и все предыдущие, например: тонкое растачивание, выполняемое после чернового и чистового растачивания.
Кроме того следует помнить о том, что вид обработки обеспечит только размерную точность и точность геометрической формы отдельных поверхностей.
Для достижения размерной точности большого числа поверхностей, а так же точности взаимного расположения поверхностей и осей необходимо правильно назначить базовые поверхности детали при обработке: либо одна из поверхностей должна быть обработана при базировании по другой, либо они должны быть обработаны без переустановки за одну операцию от единой базы.
Разработанными рекомендациями по обеспечению технических требований, предъявленных к детали, необходимо руководствоваться при составлении технологического процесса механической обработки детали, учитывая и последовательность обработки (при этом сам вид обработки может быть изменен на аналогичный), и выбранную схему базирования.
2.2 Выбор вида и обоснование метода получения заготовки
2.2.1 Описание метода получения заготовки
Составить подробное описание вида и способа получения заготовки с обоснованием принятой точности и указанием применяемого при этом оборудования. Вид и способ получения заготовки необходимо увязать с типом производства: не всегда заготовка, более приближенная к конфигурации детали, выгодна в реальном производстве, несмотря даже на экономию материала, из-за ее удорожания.
Общие рекомендации: [9, с.25…39]; [10, с.25…40]; [15, с.26…47]; [21, с.32…34].
2.2.2 Определение припусков и допусков по стандартам. Расчет
размеров и массы заготовки, коэффициента использования материала
Назначить общие припуски на все обрабатываемые поверхности в соответствии с ГОСТ 26645-85 для отливок и ГОСТ 7505-89 для поковок. Рассчитать размеры заготовки предварительно.
В качестве исходных данных необходимо указать все параметры точности заготовки и соответствующий стандарт.
Назначение припусков и расчет размеров заготовки свести в таблицы 2.2 и 2.3 (смотри приложение А). По результатам расчетов скорректировать общие припуски и размеры заготовки на ее чертеже.
Произвести расчет массы спроектированной заготовки по формуле:
mз=mд+mотх.м.о, кг (2.1)
где mд - масса детали, кг (принимается по чертежу детали);
mотх.м.о- масса отходов механической обработки, кг;
mотх.мех.обр =Vотх.*ρ, кг (2.2)
где ρ - плотность материала заготовки, кг/мм3;
Vотх.м.о. - суммарный объём удаляемого в процессе механической обработки
материала, т.е. объем припусков, мм3.
Vотх.м.о. = V1 + V2 + … + Vп , мм3 (2.3)
где п – множество удаляемых с поверхности заготовки припусков.
После определения массы спроектированной заготовки рекомендуется рассчитать коэффициент использования заготовки и пересчитать коэффициент использования материала.
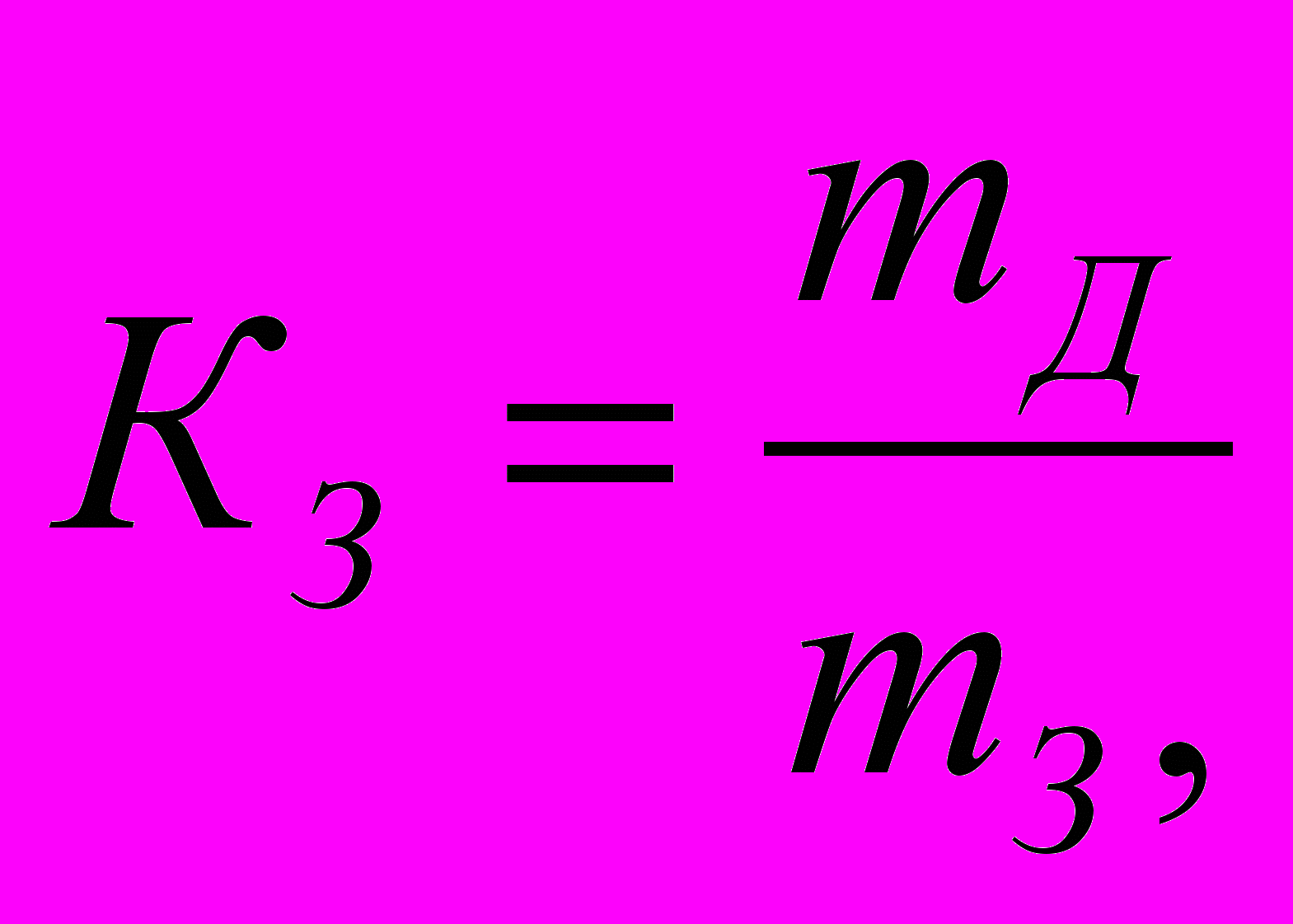
где mЗ - масса заготовки, кг (расcчитана по результатам назначения общих
припусков ).
Рекомендации: [15, с.38].
По результатам расчетов сравнить КИМ базовой и проектной заготовки.
Сделать вывод о том, какой вид заготовки следует принять к разработке в проекте: существующий на заводе или предлагаемый, принимая во внимание не только величину коэффициента использования материала, но и затраты на изготовление заготовки по различным вариантам.
2.3 Разработка проектного технологического процесса
2.3.1 Анализ базового технологического процесса и составление
последовательности обработки для проектируемого техпроцесса
Представить перечень последовательности операций механической обработки детали по существующему на предприятии техпроцессу. Указать конкретные недостатки базового технологического процесса.
В соответствии с типом производства и направлениями совершенствования производства в отрасли и на базовом предприятии предложить изменения в существующий технологический процесс и кратко описать новую технологию.
Подробно проектный вариант технологического процесса со всеми операциями и переходами механической обработки занести в графы 1, 2, 3 сводной таблицы режимов резания (приложение Е).
Параллельно оформить в тонких линиях операционные эскизы механической обработки в полуконструктивном исполнении, а также карты эскизов комплекта документов.
Разработанная технология обработки детали должна быть представлена в комплекте документов (КД).
Необходимо привести в полное соответствие друг с другом последовательность обработки по сводной таблице, на чертежах операционных эскизов и в комплекте документов.
2.3.2 Выбор и обоснование технологических баз
Cоставить подробное описание поверхностей, которые служат технологическими базами на всех операциях механической обработки. Обосновать выбор черновых и чистовых баз.
При этом необходимо руководствоваться следующими соображениями:
2.3.2.1 в качестве чистовых технологических баз следует принимать те элементы детали, которые являются базами конструкторскими и измерительными, что уменьшает погрешность базирования, т.к. выполняется принцип совмещения баз;
2.3.2.2 строить обработку целесообразно таким образом, чтобы чистовые технологические базы были одними и теми же на протяжении всего ТП, что обеспечивает выполнение принципа постоянства баз и является предпосылкой для увязки баз черновых и чистовых;
2.3.2.3 смена чистовых баз целесообразна в том случае, если необходимо выполнить принцип совмещения баз для обеспечения нулевой погрешности базирования;
2.3.2.4 в качестве черновых баз на первых операциях назначают те элементы, относительно которых обрабатываются будущие чистовые базы, и используют черновые базы только один раз;
2.3.2.5 к поверхностям, используемым в качестве черновых баз, предъявляют следующие требования:
- их припуски и уклоны должны быть минимальными;
- эти поверхности должны быть без следов прибылей и других дефектов заготовки;
- они не должны являться поверхностями разъёма;
- должны принадлежать матрице, а не пуансону при штамповке и форме, а не стержню при отливке;
- должны иметь наиболее высокую точность размеров и качество поверхности заготовок;
- в качестве черновых баз целесообразно использовать те поверхности заготовки, которые останутся необработанными в готовой детали.
Более подробные рекомендации: [14, с. 56…57].
2.3.3 Выбор оборудования и технологической оснастки
Данные по выбранному для изготовления детали оборудованию заносятся в таблицу (смотри приложение Б).
Общие рекомендации: [18, с.81…82].
При выборе оборудования руководствуются следующим:
1 обеспечением предъявленных к детали технических требований по точности;
2 взаимосвязью оборудования с размерами обрабатываемой детали;
3 типом производства;
4 производительностью станка;
5 мощностью станка.
Выбор оснастки осуществляется в соответствии с конструктивными особенностями изготовляемой детали, схемой её базирования, выбранным для об
работки оборудованием.
Данные заносятся в таблицы (смотри приложение В).
По итогам выполнения пункта 2.3 заполняется маршрутная карта (МК).
МК оформляется по ГОСТ 3.1118-82 и содержит основную надпись, номера операций, их коды и наименования, модели оборудования и их коды, справочно-нормативные показатели по каждой операции.
Рекомендации: [21, с.34…46], ГОСТ 3.1128-93, ГОСТ 3.1129-93.
2.4 Разработка операционного технологического процесса
2.4.1 Определение межоперационных припусков и операционных
размеров
Расчет припусков, по возможности, должен быть представлен на одну наружную и одну внутреннюю поверхность.
На ту поверхность, которая должна пройти наибольшее количество переходов обработки, припуски определяются расчётно-аналитическим методом. Методику расчёта смотри в приложении Г.
По результатам аналитического расчёта оформить схему расположения допусков и припусков.
На другую точную поверхность припуски по переходам назначаются из таблиц справочников: [4]; [27]. Назначение и расчёты целесообразно вести в табличной форме в соответствии с методикой приложения Д.
По результатам расчётов откорректировать на чертеже заготовки и в таблице 2.3 размеры поверхностей, на которые рассчитаны припуски.
Глубина резания в сводной таблице режимов резания и в операционных картах по всем переходам механической обработки поверхностей, на которые определялись припуски, должна соответствовать результатам, полученным при расчёте и назначении припусков на эти переходы.
2.4.2 Определение режимов резания на проектируемые операции (переходы). Сводная таблица режимов резания
На один вид обработки режимы резания определяются по эмпирическим формулам, на один вид назначаются по нормативам с подробным описанием.
На остальные переходы и операции механической обработки режимы резания назначаются, исходя из производственного опыта.
Все расчёты заносятся в сводную таблицу режимов резания (смотри приложение Е).
Параллельно с заполнением сводной таблицы прорисовываются чертежи операционных эскизов в полуконструктивном исполнении с целью уточнения направлений перемещения инструментов во время обработки, длин резания и
рабочих ходов, величин пробега инструментов на холостом ходу, распределения припусков между отдельными рабочими ходами.
После отработки чертежей операционных эскизов рекомендуется оформить операционные карты и карты эскизов комплекта технологических документов.
На всех операционных картах (ОК) механической обработки и в табличках на чертежах операционных эскизов режимы резания должны соответствовать рассчитанным и занесённым в сводную таблицу режимов резания.
2.4.3 Нормирование проектируемой операции. Сводная таблица норм времени
На одну проектируемую операцию механической обработки назначение норм времени должно быть выполнено с подробным описанием выбора и расчётов.
В том случае, если проектируемая операция выполняется на станке с ЧПУ, необходимо предварительно составить управляющую программу обработки и только после этого приступать к нормированию времени.
На все остальные операции назначение норм времени выполняется параллельно с заполнением сводной таблицы норм времени.
Форма таблицы представлена в приложении Ж.
При определении норм времени основное время (Т0) на каждую операцию должно быть назначено по сводной таблице режимов резания.
В картах комплекта документов (операционных и маршрутных) величина основного, вспомогательного, штучного или штучно-калькуляционного, а также подготовительно-заключительного времени и объёма партий обрабатываемых деталей должна соответствовать сводной таблице норм времени.
3 ОРГАНИЗАЦИЯ ПРОИЗВОДСТВА НА УЧАСТКЕ
3.1 Определение количества оборудования на участке
В серийном производстве пооперационное расчётное количество станков определяется по формуле:
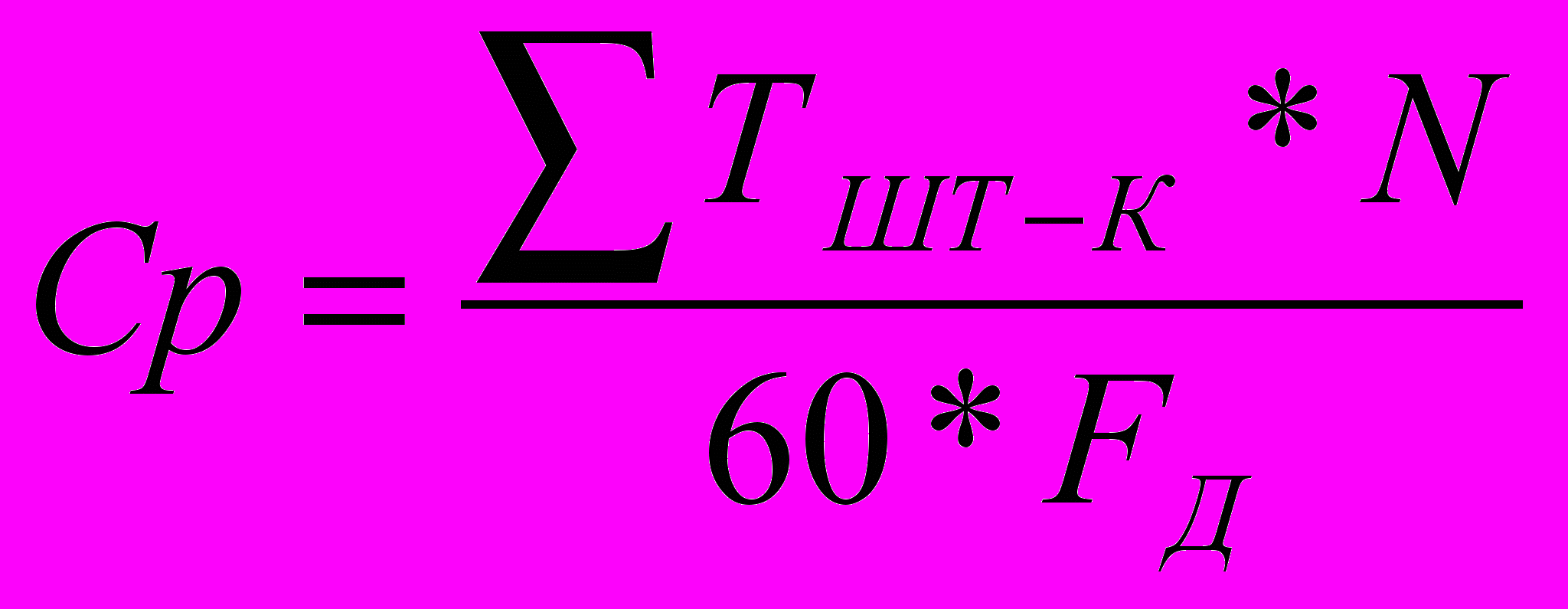
где ΣТШТ-К – суммарное штучно-калькуляционное время всех операций, выпол-
няемых на станке данной модели, мин;
N - годовой объём выпуска детали, шт;
FД - действительный годовой фонд производственного времени работы
оборудования, час (определяется индивидуально для каждой модели
оборудования в зависимости от категории его ремонтной сложности по
таблице [9, с 22, таблица 2.1]).
Расчётное количество оборудования округляют до целого числа всегда в большую сторону.
Коэффициент загрузки оборудования рассчитывается по формуле:
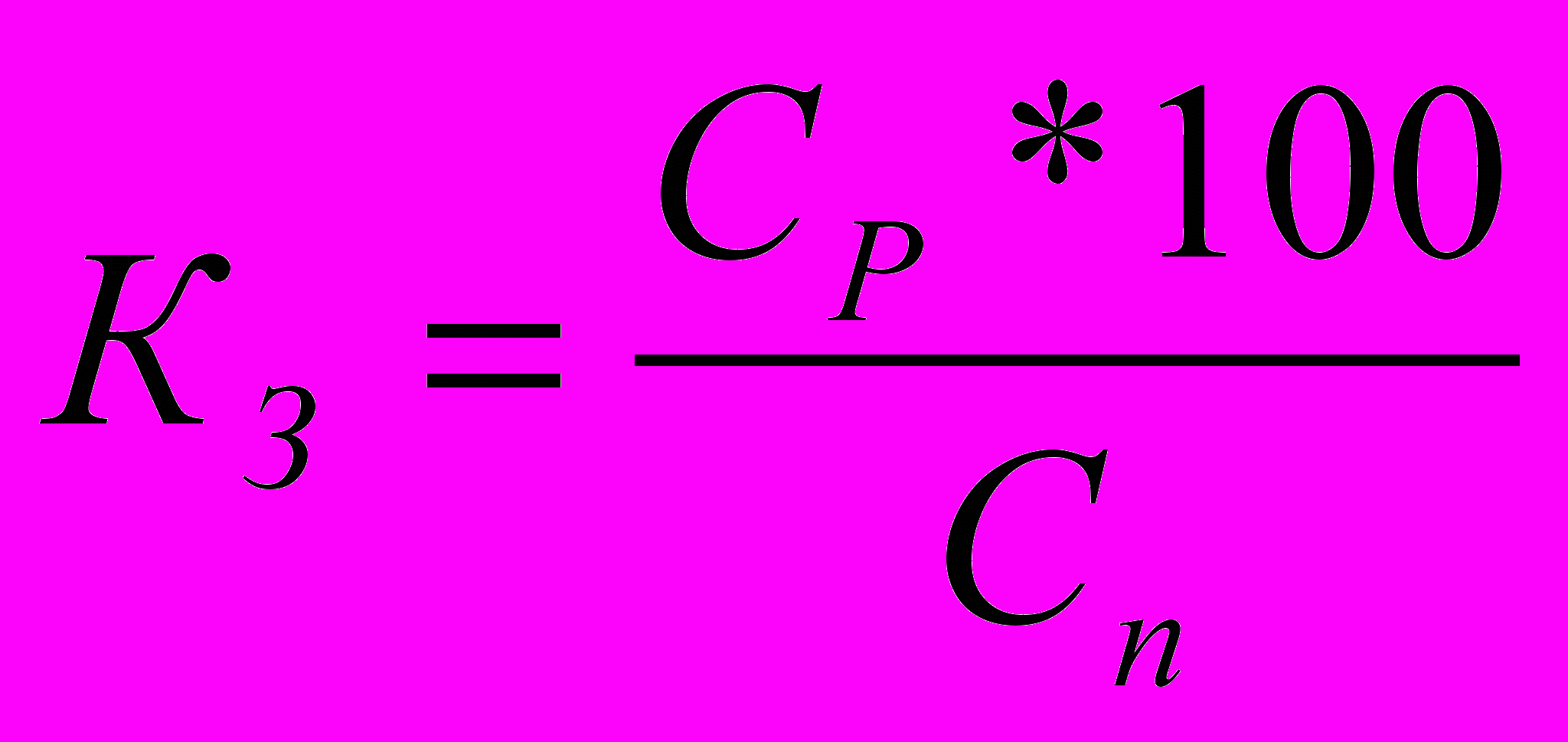
где Сп - принятое количество станков данной модели.
Рекомендуется подробно описать в пояснительной записке расчёт для изменяемых операций технологического процесса по базовому и проектному вариантам. Результаты расчетов по остальным операциям сразу заносить в таблицу 3.2. На основании проведённых расчётов строится график загрузки оборудования (пример: [21, с.106]).
На графике обязательно должна быть показана помодельная догрузка оборудования. Например, если в технологическом процессе механической обработки две разные операции обрабатываются на станках одной модели, то на одном и том же станке сначала выполняют одну операцию, а после его переналадки - другую; два одинаковых недогруженных станка на участке не устанавливают.
Кроме того, оборудование должно быть догружено до нормативной величины КЗ обработкой типовых деталей. Перечень типовых деталей для дозагрузки должен быть представлен в виде таблицы 3.1 после графика загрузки оборудования.
Таблица 3.1 - Описание механической обработки однотипных деталей
Наимено- вание и номер деталей | Годовой объем выпуска, шт | Масса, кг | Номер и наименование операции | Мо-дель стан-ка | Время обработки, мин | |||
Детали | Заго-товки | ТМ.С. | ТЗан | ТЦА | ||||
1 | 2 | 3 | 4 | 5 | 6 | 7 | 8 | 9 |
ТМ - машинное время обработки детали, т.е. время обработки, когда не требуется вмешательство рабочего в работу станка. Для станков с ЧПУ в шестую графу заносится время цикла: ТЦ=ТМО+ТМВ.
ТВР - вспомогательное ручное время, затрачиваемое на установку и съем; на переходы, выполняемые станком под ручным управлением рабочего; на измерение (неперекрываемое основным машинным временем).
В девятой графе для типовых деталей может быть записано ТШТ (при отсутствии нормирования ТП-З в технологических процессах механообработки типовых деталей).
Операции механообработки типовых деталей, которыми догружаются станки до нормативного КЗ, в таблице 3.1 должны быть выделены подчеркиванием.
Результаты всех расчетов по базовому и проектному вариантам технологических процессов заносятся в таблицу 3.2 только по детали-представителю.
При этом в графе "Стоимость станка" для станков с ЧПУ приводятся две величины через дробь: над чертой записывается балансовая стоимость станка, а под чертой - его стоимость с учетом коэффициента загрузки обработкой детали-представителя. Например, при общей стоимости станка 10млн.рублей и КЗ=0,21 запись будет произведена: 10/2,1.
3.2 Определение количества производственных рабочих
Численность производственных рабочих для каждого рабочего места индивидуально определяется по формуле:
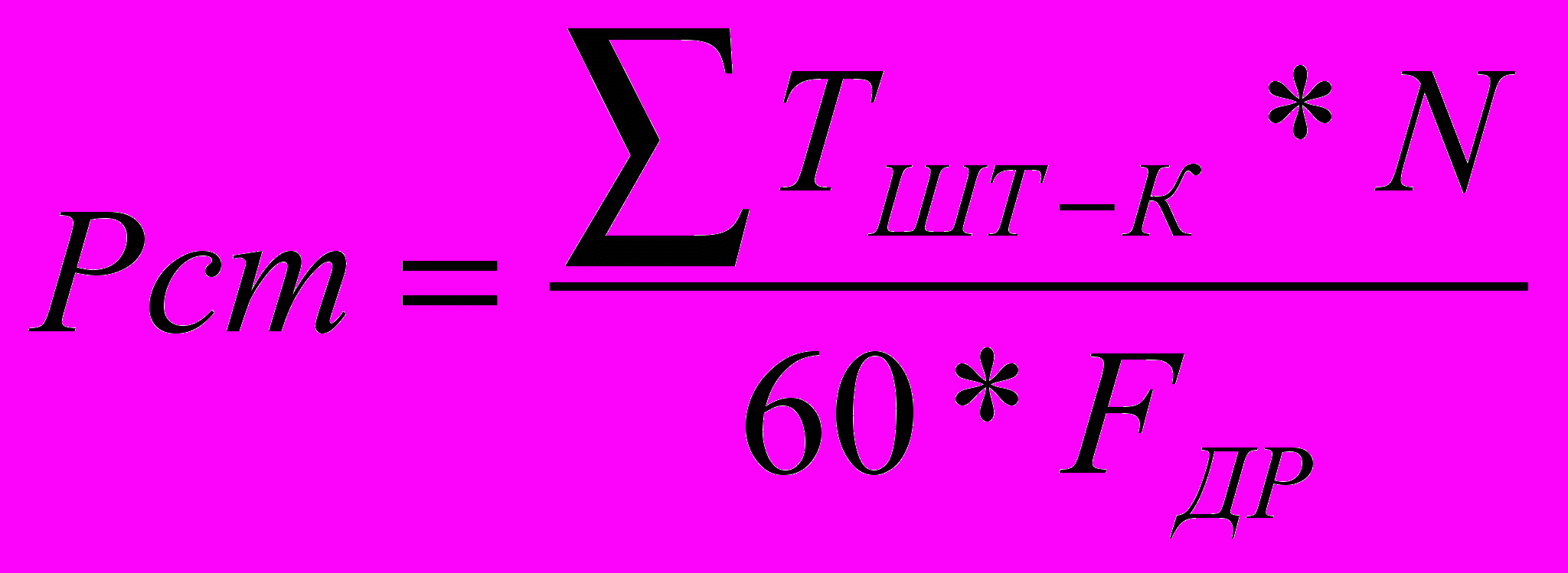
где FДР - эффективный годовой фонд времени станочника, ч, [21, с 107]
Расчётная численность рабочих округляется в большую сторону до целого числа.
Затем в соответствии с методикой [21, с.108…110] и [31, с.157…159] производится анализ возможности организации многостаночного обслуживания (с построением графика многостаночного обслуживания оборудования) и совмещения профессий.
При этом обязательно учитывается разряд рабочих каждой профессии, занятых на каждой операции механической обработки.
Только после этого делается окончательный вывод о принятой численности производственных рабочих на участке с учетом совмещения профессий и многостаночного обслуживания.
Результаты расчёта заносятся в таблицу 3.2 с указанием итоговой суммы по числу операций, по общей стоимости станков, по штучно-калькуляционному времени, по принятому числу станков, по расчетной и принятой численности производственных рабочих в базовом и проектном вариантах.
Таблица 3.2 - Расчет количества оборудования и численности производственных рабочих.
Номер опера-ции | Модель станка | Стоимость станка, млн.руб. | Тшт-к, мин. | Ср. | Сп. | Кз,% | Профессия рабочего и разряд работ | Рст | Рп |
1 | 2 | 3 | 4 | 5 | 6 | 7 | 8 | 9 | 10 |
Базовый вариант механообработки | |||||||||
| | | | | | | | | |
Проектный вариант механообработки | |||||||||
| | | | | | | | | |