Предприятия черной металлургии
Вид материала | Лекция |
СодержаниеПредприятия цветной металлургии В медной промышленности В свинцовой промышленности В никелевом производстве Алюминиевая промышленность. |
- Предприятий черной металлургии л. В. Царёва И. Ю. Евстафьева, 40.59kb.
- Черной металлургии. Ключевые вопросы, внесённые в программу: Как, 151.01kb.
- Морфофункциональная характеристика размножения амфибий и рептилий из популяций, испытывающих, 356.29kb.
- Эколого-морфологическая характеристика размножения мелких млекопитающих из популяций,, 635.9kb.
- Правила безопасности в газовом хозяйстве металлургических и коксохимических, 2518.2kb.
- Сафошин Виктор Васильевич создание на ОАО «рудоавтоматика» электротехнического научно-производственного, 219.04kb.
- Программа второй день (четверг 24 марта), 55.36kb.
- Тема лекции, 77.49kb.
- Информация о результатах пилотного проекта разработки профессиональных стандартов для, 2710.95kb.
- Моделирование и прогнозирование финансово-экономической деятельности предприятия цветной, 440.73kb.
Предприятия цветной металлургии
Цветная металлургия представляет собой отрасль тяжелой промышленности, включающая добычу и обогащение руд, производство и обработку цветных металлов и их сплавов. Попутной продукцией цветной металлургии являются многие химические соединения минеральные удобрения, стройматериалы и т.д.
Производственный комплекс отрасли состоит из горнодобывающих предприятий, обогатительных фабрик, металлургических и металлообрабатывающих заводов
Укажем, что в отличие от других полезных ископаемых содержание цветных и редких металлов в рудах крайне низко. Для получения 1 тонны цветного металла добывается и перерабатывается от сотен до десятков тысяч тонн сырья, поэтому цветная металлургия одна из самых энергоемких отраслей. Наиболее энергоемкими в отрасли являются электролизные производства (электролиз водных растворов и электролиз расплавов) [24, 25]. Вместе с тем более 65% руд добываются наиболее экономичным открытым способом, обеспечивающим комплексное извлечение металлов из недр.
В рудном сырье вместе с «основными» элементами: алюминием, медью, свинцом, цинком, никелем, оловом, вольфрамом, молибденом,- содержаться попутные: золото, серебро, платиновые метомы кобальт, мышьяк, рений, индий, рубидий, галлий, селен, теллур, кадмий, скандий, таллий, германий, сера, барий и другие, ценность которых иногда превосходят ценность основных металлов.
В медной промышленности процесс конвертирования принято делить на два периода. Первый период заканчивается удалением из штейна всего железа. Оставшийся сульфид меди (белый мат) окисляется во втором периоде кислородом воздуха по реакции:
Cu2S+O2=2Cu+SO2. (1.1)
Конечным продуктом конвертирования медных штейнов является черновая медь.
В свинцовой промышленности конвертированию подвергаются медно-свинцовые штейны; содержание до 30% Cu, 10-20% Pb, 5-15% Zn, 20-40% Fe и 18-22% S. В первом периоде продувки одновременно с сульфидом железа частично окисляется сульфиты цинка и свинца. Окислы этих металлов при взаимодействии с кремнеземом образуют шлак. Пасть цинка и свинца переходит в паровую фазу и улавливается в пылеулавливающих устройствах в виде конвертерной пыли. При переработке медно-свинцовых штейнов получаемая во втором периоде черновая медь отличается повышенным содержанием свинца.
В никелевом производстве получение чернового металла из никелевых штейнов затруднено, последнее связано с тем, что после удаления всего сернистого железа в первом периоде протекания реакции
Ni3S2+2O2=3Ni+2SO2 (1.2)
возможно лишь при температурах выше 15000С.
Алюминиевая промышленность. По размерам производства и потребления алюминий занимает первое место среди цветных металлов. Алюминиевая промышленность охватывает следующие основные производства, составляющие общий промышленный цикл: добычу алюминиевых руд (бокситы, нефелиновые сиениты, алуниты и др.), производство глинозема (оксиды алюминия) из руд или концентратов, производство электродов и анодной массы, фтористых солей (криолита, фторидов), выплавку металлического алюминия и получение полуфабрикатов из него. Важнейшие потребители: авиационная, электротехническая, автомобильная и ряд других отраслей машиностроительной и металлообрабатывающей промышленности, а также строительство, железнодорожный транспорт, химическая пищевая промышленность.
Бокситы всегда загрязнены окислами железа или кремневой кислотой. Для получения чистой окиси алюминия бокситы перерабатывают нагреванием с CaO и Na2CO3 (сухой способ) или нагреванием с едким натром в автоклавах при температуре 220-240ºС. При обоих способах окись алюминия в виде алюминатов переходит в раствор, который затем разлагают пропусканием двуокиси углерода либо добавлением заранее приготовленной гидроокиси алюминия. В первом случае разложение происходит по уравнению
2[Al (OH4)]– + CO2 → Al (OH)3+CO32–+H2O (1.3)
Разложение по второму способу основано на том, что раствор алюмината, полученный при нагревании в автоклаве, метастабилен. Добавляемая гидроокись алюминия ускоряет распад алюмината:
[Al(OH)]–→ Al(OH)3+OH–. (1.4)
Полученную гидроокись алюминия прокаливают при 12000С, в результате получается чистый глинозем [28].
Используется электролизеры трех основных конструкции:
1. Электролизеры с самообжигающимися анодами и боковым подводом тока.
2. То же, но с верхним подводом тока.
3. Электролизеры с обожженными анодами.
Электролитная ванна представляет собой железный кожух, футерованный внутри тепло-электроизолирующим материалом – огнеупорным кирпичом, и выложенный угольными плитами и блоками. Рабочий объем заполняется расплавленным электролитом, состоящим из 6-8% глинозема и 94-92% криолита (обычно с добавкой и около 5-6% смеси фторидов калия и магния). Катодом служит подина ванны, анодом – погруженные в электролит угольные обожженные блоки или же набивные самообжигающиеся электроды. При прохождении тока на катоде выделяется расплавленный алюминий, который накапливается на подине, а на аноде кислород, образующий с угольным анодом СО и СО2.
Удельный расход электроэнергии по отдельным заводам колеблется от 16000 до 20000 кВтч/т, что определяется качеством исходного сырья, различным характером оборудования, режимом работы и организацией технического процесса производства.
В производственной практике на алюминиевых заводах вместо удельного расхода технической энергии постоянного тока часто пользуются величиной обратной ему - выходом по энергии. Выход по энергии - это количество граммов алюминия, полученного на 1 кВтч затраченной электроэнергии постоянного тока; определяется по формуле

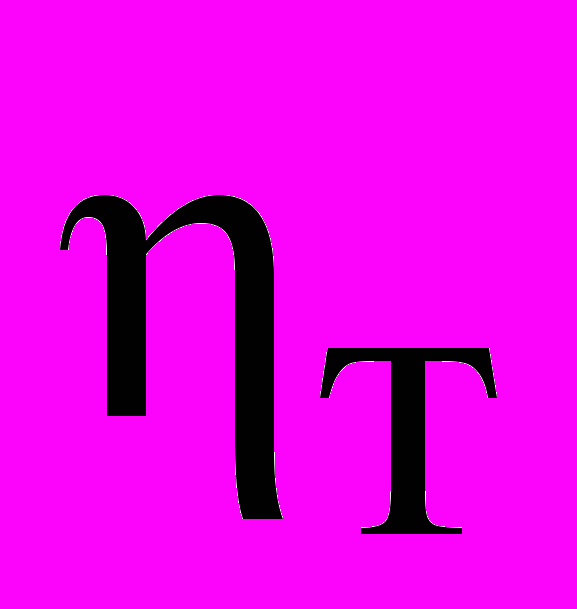
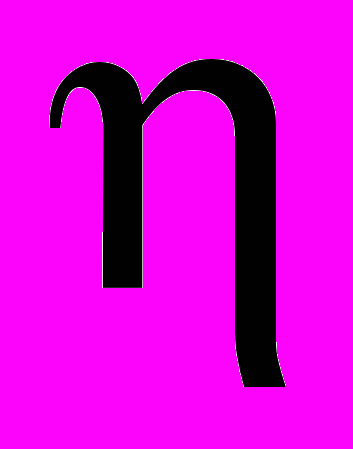
Было установлено, что температура процесса электролиза - это наиболее важный фактор, влияющий на технико-экономические показатели ванны. Длительной практикой установлено, что оптимальная температура электролита находится в пределах 950-965ºС.
Лекция 3