Разработка рационального режима плавки стального полупродукта в сверхмощных дуговых электропечах
Вид материала | Автореферат диссертации |
СодержаниеОбщая характеристика работы Основное содержание работы |
- Трудового Красного Знамени государственный технический университет имени Н. Э. Баумана., 79.25kb.
- Разработка и совершенствование способов компенсации неактивной мощности дуговых сталеплавильных, 255.14kb.
- Разработка технологии и инструмента для непрерывного деформационного получения ультрамелкозернистой, 291.68kb.
- Контрольная работа по курсу: «Возрастная анатомия и физиология ребенка» «Физиолого-гигиеническое, 135.96kb.
- Разработка технологии плавки сульфидных медно-никелевых концентратов с оптимальными, 234.68kb.
- Разработка гидравлической программы проводки скважины 2 Расчет рабочих характеристик, 52.01kb.
- Практические задания для формирования навыка применения знаний по темам, 680.29kb.
- Лямец Ю. Я., Нудельман Г. С., Подшивалин, 158.17kb.
- Концепция научно-технической программы Союзного государства, 270.32kb.
- «Господи, ну и пекло!» думал я, вытирая ручейки пота, стекающие по лицу из-под раскалённого, 2907.59kb.
На правах рукописи
Некрасов Илья Владимирович
РАЗРАБОТКА РАЦИОНАЛЬНОГО РЕЖИМА
ПЛАВКИ СТАЛЬНОГО ПОЛУПРОДУКТА В СВЕРХМОЩНЫХ
ДУГОВЫХ ЭЛЕКТРОПЕЧАХ
Специальность 05.16.02 – Металлургия черных, цветных и редких металлов
Автореферат
диссертации на соискание ученой степени
кандидата технических наук
Екатеринбург – 2010
Работа выполнена в Учреждении Российской академии наук Институт металлургии Уральского отделения РАН, г. Екатеринбург
Научный руководитель - доктор технических наук
Шешуков Олег Юрьевич
Официальные оппоненты: доктор технических наук, профессор
Дерябин Анатолий Андреевич
кандидат технических наук, доцент
Бурмасов Сергей Петрович
Ведущее предприятие - ОАО «Уралгипромез»
(г. Екатеринбург)
Защита состоится 5 марта 2010 г. в 13 00 часов на заседании диссертационного совета Д 004.001.01 при Учреждении Российской академии наук Институт металлургии Уральского отделения РАН по адресу: 620016, г. Екатеринбург, ул. Амундсена, 101, в актовом зале. Тел. (343) 267-91-24, факс (343) 267-91-86, E-mail: admin@imet.mplik.ru
Автореферат разослан «___» февраля 2010 г.
Ученый секретарь
диссертационного совета,
доктор технических наук А.Н. Дмитриев
ОБЩАЯ ХАРАКТЕРИСТИКА РАБОТЫ
Актуальность работы В настоящее время более 30 % мирового производства стали выплавляется в дуговых электропечах. При этом одной из основных тенденций развития металлургии является опережающее развитие электропечного способа производства стали. Современные электросталеплавильные цехи оснащены сверхмощными печами (далее - ДСП) с удельной мощностью трансформатора более 500 кВА/т. В них расплавляют металлошихту и подвергают жидкий металл окислительному рафинированию, решая задачи удаления фосфора и нагрева металла до температуры выпуска. Полученный таким образом жидкий полупродукт доводится до стали средствами ковшовой металлургии.
Важнейшей частью технологии плавки полупродукта в ДСП является вспенивание шлака, имеющее целью экранирование мощных электрических дуг в конце расплавления и по ходу окислительного периода плавки. Укрытие горящих дуг хорошо вспененным шлаком приводит к значительному продлению ресурса футеровки ДСП, ускорению нагрева и плавления металла, снижению насыщения металла азотом. Однако сейчас резервы технологии вспенивания шлака используются не полностью. Это связано с тем, что до настоящего времени физические свойства шлаков, в т.ч. вязкость, изучались в диапазоне температур, не характерном для электропечных шлаков по ходу плавки в ДСП. Кроме того, улучшение вспенивания шлаков требует разработки рациональных режимов плавки, определяющих и протекание процессов рафинирования металла, и влияющих на стойкость футеровки ДСП, а также включающих режим продувки металла кислородом.
С другой стороны, важнейшей задачей является разработка методов контроля и автоматизации электроплавки, в частности, контроля качества вспенивания шлака по параметрам электрического режима. Актуальность исследований, позволяющих связать рациональный технологический и электрический режимы электроплавки, не вызывает сомнений.
Работа выполнялась в рамках Федеральной целевой программы «Исследования и разработки по приоритетным направлениям развития научно-технологического комплекса России на 2007-2012 годы», по программе ОХНМ РАН «Создание новых металлических, керамических, стекло-, полимерных и композиционных материалов», по программе ОХМН РАН «Создание новых видов продукции из минерального и органического сырья» - проект «Создание новых материалов - металлизованного концентрата и магнезиальных шлаковых смесей путем переработки минерального сырья, содержащего карбонаты железа и магния для применения в сталеплавильном производстве», по проекту Института металлургии УрО РАН «Экспериментальные исследования и математическое моделирование электрических и теплофизических процессов в ваннах электропечей с открытой дугой».
Цель работы – улучшение технико-экономических показателей работы сверхмощной ДСП и повышение качества выплавляемого в ней полупродукта за счёт совершенствования технологии плавки, создания и применения метода оперативного контроля качества вспенивания шлака.
В соответствии с поставленной целью основными задачами исследований являлись:
- проведение одновременных измерений температур шлака и металла в конце расплавления и по ходу окислительного периода;
- исследование влияния температуры шлака на процессы дефосфорации и рефосфорации полупродукта;
- оценка вспениваемости шлаков, моделирующих электропечные, в диапазоне температур, характерном для них по ходу плавки полупродукта в ДСП;
- изучение влияния химического состава и температуры шлаков, моделирующих электропечные, на их агрессивность к магнезиальным огнеупорам;
- разработка и промышленные испытания технологических приёмов реализации рационального режима плавки в ДСП;
- разработка метода оперативного контроля качества вспенивания шлака по параметрам электрического режима плавки в ДСП переменного тока.
Методы исследования Для решения задач исследования применён комплексный подход, включающий расчёты характеристик шлаков по полимерной теории строения шлаков, разработанной в ГОУ ВПО «УГТУ-УПИ», термодинамическое моделирование реакций в системе «металл-шлак» с помощью специальных компьютерных программ, экспериментальное изучение вязкости шлаков с помощью электромагнитного вибрационного вискозиметра, петрографические исследования электросталеплавильных шлаков, методы теории нелинейных электрических цепей и математической статистики, средства вычислительной техники.
Достоверность полученных результатов подтверждается практической реализацией разработанного режима плавки в ДСП, публикацией результатов в центральной печати и их апробацией на представительных научных форумах.
Научная новизна работы
Показана перспективность контроля температуры шлакового слоя в качестве дополнительного технологического параметра, позволяющего оценивать возможности рафинирования полупродукта и вспенивания шлака. Впервые исследовано влияние температуры шлака на процесс дефосфорации полупродукта в сверхмощной ДСП. Показано, что при прогнозировании минимально достижимого содержания фосфора в полупродукте по ходу плавки, а также содержания фосфора в полупродукте в конце плавки целесообразно ориентироваться на температуру шлака. Установлено, что наблюдаемый эффект рефосфорации в конце плавки объясняется, в основном, повышением температуры шлака, а не традиционно измеряемой по ходу плавки температуры полупродукта.
В диапазоне температур, характерном для промышленных электропечных шлаков, изучена вспениваемость шлаковых систем, моделирующих электропечные шлаки. Расчётами и промышленными экспериментами на ДСП с температурой выпуска полупродукта 1670-1690°С показано, что для поддержания до конца плавки достаточного уровня шлаковой пены следует формировать гетерогенные шлаки за счёт повышения их основности до 2,7-3,1 ед. при содержании (FeO) = 20-35 %.
Разработан новый метод оперативного контроля качества вспенивания шлака для ДСП переменного тока по параметрам электрического режима.
Практическая значимость работы Определены рациональные параметры технологии плавки для ДСП-135 ОАО «Северский трубный завод», позволяющие стабилизировать вспенивание шлака, повысить качество полупродукта, обеспечить более благоприятные условия эксплуатации футеровки, реализация которых позволила снизить содержания фосфора и азота в полупродукте, соответственно, на 29 и 16 отн. %, удельный расход электроэнергии на 11 кВт·ч/т, а также расходы некоторых технологических материалов с ожидаемым экономическим эффектом 10,34 млн. руб. в год. Получен приоритет ФИПС на патент по заявке № 2008148432 от 08.12.2008 «Способ получения стали в дуговой электросталеплавильной печи».
Апробация работы Основные положения работы докладывались и обсуждались на 9-й Всероссийской научно-практической конференции студентов, аспирантов и специалистов «Энергетики и металлурги настоящему и будущему России» (Магнитогорск, 2008 г.), XII Российской конференции «Строение и свойства металлических и шлаковых расплавов» (Екатеринбург, 2008 г.), Х конгрессе сталеплавильщиков (Магнитогорск, 2008 г.), V Российской ежегодной конференции молодых научных сотрудников и аспирантов (Москва, 2008 г.), 67-й научно-технической конференции МГТУ-ММК по итогам научно-исследовательских работ (Магнитогорск, 2009 г.).
Публикации По материалам диссертации опубликовано 10 печатных работ, в том числе 3 статьи в изданиях, рекомендованных ВАК РФ.
Структура и объём работы Диссертация состоит из введения, четырёх глав, заключения, списка литературы и приложений. Основной текст занимает 145 страниц, включает 43 рисунка, 14 таблиц и 154 источника.
Автор выражает признательность д.т.н. Воробьёву В.П., д.т.н. Сивцову А.В., д.т.н., проф. Истомину С.А., к.т.н. Цымбалисту М.М., к.т.н., доц. Невидимову В.Н., к.г.-м.н. Сапожниковой Т.В. и специалистам ОАО «Северский трубный завод» за помощь при выполнении диссертационной работы.
ОСНОВНОЕ СОДЕРЖАНИЕ РАБОТЫ
Во введении дана оценка состояния решаемой проблемы, обоснована актуальность темы диссертационной работы, определены цель и задачи исследований.
В первой главе проведён обзор литературных данных о современном состоянии электросталеплавильного производства. Отмечено, что на сегодняшний день вспенивание шлака является неотъемлемой частью технологии плавки в ДСП, обеспечивает снижение энерго- и материалоёмкости электроплавки в условиях повышения удельной мощности трансформаторов. Однако на практике потенциал технологии укрытия дуг вспененным шлаком полностью не реализуется. Зачастую достаточный уровень вспенивания шлака наблюдается только в конце расплавления и начале окислительного периода, к концу же плавки высота шлаковой пены снижается, и дуги экранируются не полностью. Из практики известно, что снижение вспениваемости шлаков наблюдается при повышении содержания в них оксидов железа, которое действительно происходит к концу плавки из-за снижения содержания углерода в полупродукте и приводит к снижению вязкости шлака. Однако закономерности изменения вязкости сталеплавильных шлаков до настоящего времени изучались в диапазоне температур, в основном, характерном для полупродукта, а не электропечного шлака. Это ограничивает возможности анализа способов улучшения вспенивания за счёт регулирования вязкости шлаков.
Имеются отдельные данные, что температура шлакового покрова в сталеплавильных агрегатах с мощными электродуговыми установками существенно выше температуры металла и изменяется от 1650 до 1800°С. Причинами перегрева шлака относительно объёма металла, температура которого контролируется по ходу плавки, являются преимущественное расположение зон горения дуг в шлаке и прохождение через него части тока.
В литературе неоднократно отмечалась особенность плавки в сверхмощных ДСП и мартеновских печах – формирование двухфазной (шлако-металлической) зоны в шлаковом покрове, занимающей до 70 % его толщины. Наличие двухфазной зоны и перегрев шлакового покрова относительно металла могут влиять на эффективность решения одной из основных задач плавки – дефосфорации полупродукта. Необходимо учитывать это при оценке возможностей рафинирования металла и разработке рациональных режимов плавки.
Сложная геометрия ванны ДСП и особенности технологии вызывают неравномерный износ футеровки. Стойкость футеровки в целом определяется стойкостью наиболее изнашиваемых зон шлакового пояса, что ограничивает продолжительность кампании сверхмощных ДСП, которая в большинстве случаев не превышает 600-800 плавок. Одним из направлений повышения стойкости футеровки ДСП является выплавка полупродукта под шлаками, одновременно обладающими и меньшей агрессивностью к огнеупорам и повышенной вспениваемостью. Естественно, при этом должны сохраняться достаточные рафинирующие свойства шлаков.
Критический анализ показал, что возможности дальнейшего повышения технико-экономической эффективности ДСП во многом сводятся к разработке рационального шлакового режима, на практике связанного с режимом продувки и другими параметрами технологии. В связи с этим особую важность приобретает исследование температур шлака, чему до настоящего времени не уделялось достаточного внимания.
Во второй главе представлены результаты измерений температур шлака и металла в ДСП-135 ОАО «Северский трубный завод», оснащённой трансформатором мощностью 110 МВА. Температуры шлака измерялись термопарами на уровне примерно половины его толщины в зоне, расположенной над областью замера температуры полупродукта. Практически одновременно с этим измерялась температура полупродукта автоматическим зондом (через рабочее окно). Всего было проведено 16 пар измерений на 14 плавках. Результаты замеров температур металла и шлака по ходу плавки приведены на рисунке 1 в сопоставлении с обобщёнными литературными данными о температурах металла и вспененного шлака в сверхмощной ДСП. Температура шлакового покрова превышает температуру металла примерно на 70 °С и изменяется от 1650 до 1750 °С. Известно, что температура шлака в околоэлектродных зонах может достигать 1800°С (рис.1).
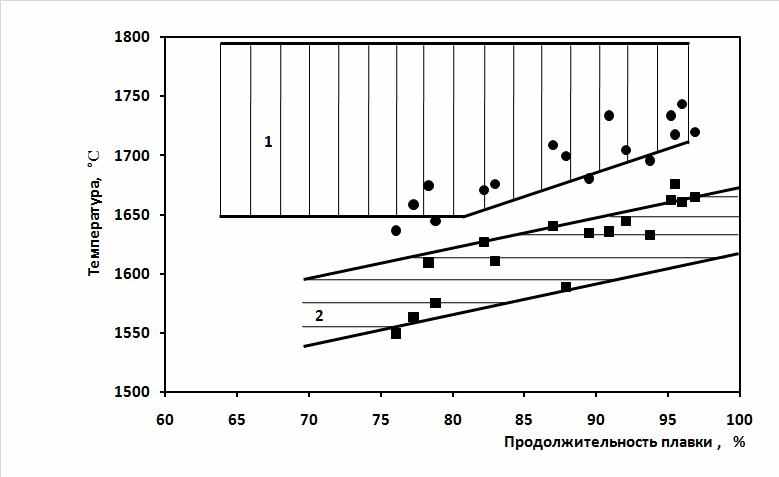
Рисунок 1 – Изменение температур шлакового покрова и металла по ходу плавки полупродукта в сверхмощной ДСП: 1 – температура шлака (литературные данные); 2 – температура металла (литературные данные);
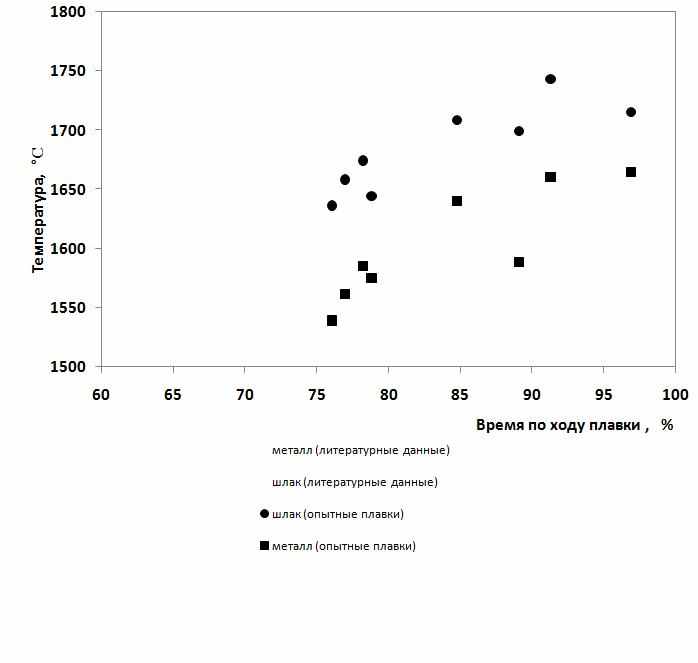
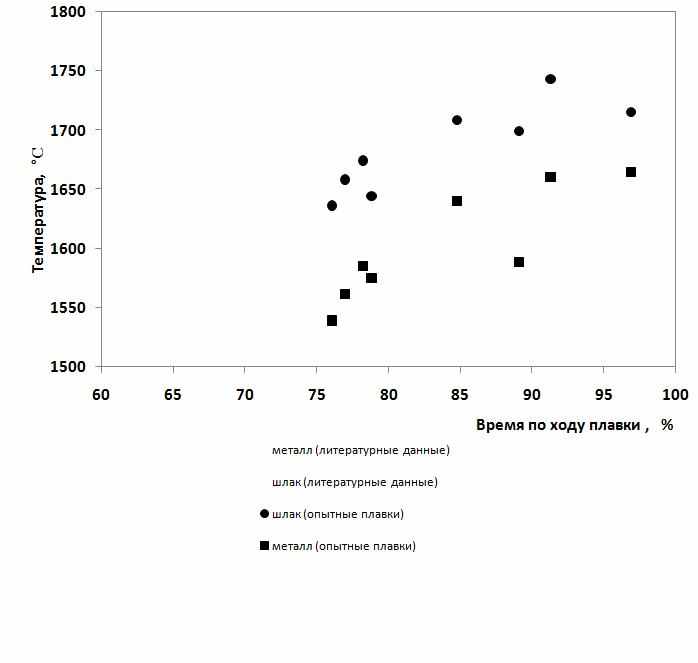
На плавках серийной технологии отмечено вредное явление рефосфорации - повышение содержания фосфора в металле в конце плавки (рис.2). Для разработки методов предотвращения рефосфорации необходимо проанализировать её причины. Использование традиционного метода анализа, основанного на сопоставлении фактического (текущего) содержания фосфора в металле с равновесным, рассчитанным по температуре металла, приводит к ряду противоречий.
На рисунке 2 приведены области фактических содержаний фосфора в металле и равновесных, рассчитанных по измеренной температуре металла (361 точка в каждой области). Область равновесных содержаний получена расчётами по полимерной модели «УГТУ-УПИ», аналогичные области получаются при использовании адаптированной модели Кожеурова, а также моделей Сюито-Иное (Suito – Inoue) и Хили (Healy).
Если анализировать рафинирование полупродукта согласно традиционному подходу, оценивая равновесное содержание фосфора в полупродукте по фактически измеряемой температуре полупродукта, то следует признать, что дефосфорация должна продолжаться и после 80-85% продолжительности плавки. Однако в действительности этого не происходит (рис.2). Кроме того, наблюдаемая рефосфорация должна начинаться после выравнивания фактических концентраций фосфора с равновесными и оставаться в пределах рефосфорации, которая прогнозируется по температуре полупродукта. В действительности же этого также не происходит (рис.2). Область фактических содержаний фосфора в полупродукте никогда не перекрывается с областью равновесных, рассчитанных по температуре полупродукта, несмотря на последовательное протекание процессов дефосфорации и рефосфорации полупродукта. Причём указанные противоречия принципиально не устраняются привлечением в анализ известных закономерностей кинетики дефосфорации металла и возникают, по существу, при рассмотрении термодинамики процесса.
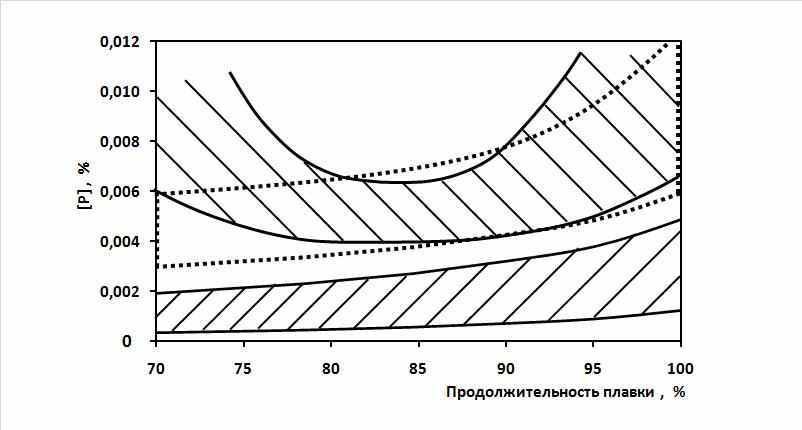
Рисунок 2 – Сопоставление фактических содержаний фосфора (%) в металле и равновесных, рассчитанных по температурам металла и шлака:
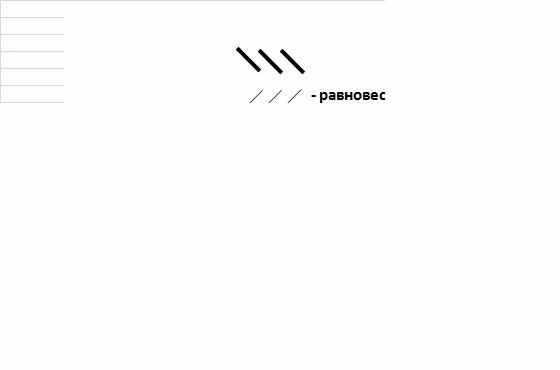
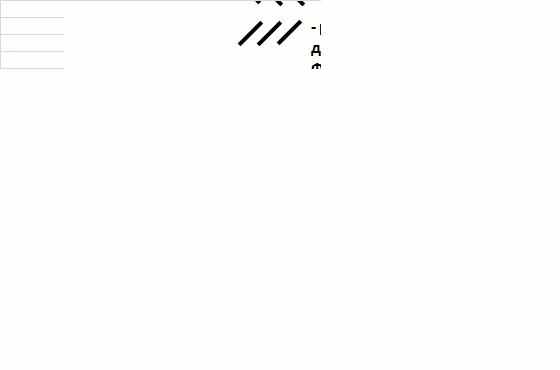
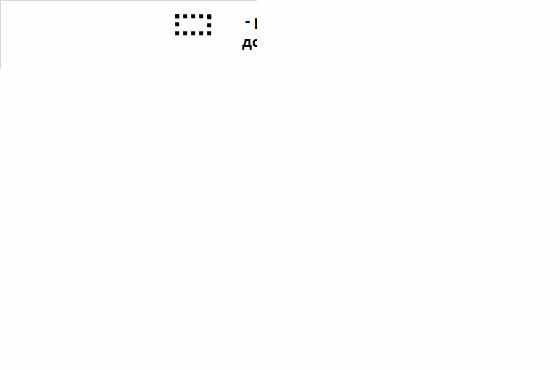
Традиционное для практики представление о том, что равновесие, к которому стремится процесс распределения фосфора между металлом и шлаком, допустимо оценивать по фактически измеряемой температуре объёма металла, обеспечивает лишь качественное объяснение наблюдаемой рефосфорации, только в некотором приближении отражает действительную физикохимию процесса в ванне ДСП. Это не позволяет, например, прогнозировать минимально достижимые по ходу плавки содержания фосфора в полупродукте и конечное содержание фосфора, количественно оценивать степень повышения основности шлака к концу плавки, необходимую для предотвращения рефосфорации.
Таким образом, обоснована необходимость нового подхода к пониманию сложного вопроса о протекании реальных процессов дефосфорации и рефосфорации в ДСП с целью расширения возможностей анализа и корректировки технологии. В связи с этим, на рисунке 2 также приводится область равновесных содержаний, рассчитанных по тем же моделям по температуре шлака, за которую приняты усреднённые результаты собственных измерений температур шлака (рис.1). Из данных, представленных на рисунке 2, следует, что фактические концентрации фосфора в полупродукте, которыми заканчивается его дефосфорация и с которых начинается рефосфорация, близки к равновесию по температуре шлака, а не полупродукта.
Следовательно, при определении рациональных параметров шлакового режима с учётом технологической необходимости дефосфорации полупродукта, целесообразно ориентироваться на температуру шлака. Данный приём обоснован следующим известным фактом. При кипении металлической ванны ДСП формируется двухфазная шлако-металлическая зона в шлаковом покрове, значительно увеличивающая площадь контакта «металл-шлак». Особенности теплогенерации и теплообмена в сверхмощных ДСП приводят к тому, что температура двухфазной зоны существенно выше температуры объёма металла. Петрографические исследования шлаков ДСП-135 подтвердили наличие металлических корольков размером до 3 мм, которые появляются в шлаке благодаря кипению металла при обезуглероживании. Отмечено, что рефосфорация начинается после полного расплавления лома на откосах печи, которое фиксируется по истечении 80-85 % продолжительности плавки. По-видимому, находящийся в шлаке лом, оказывая термостатический эффект на близлежащие объёмы шлака, создаёт благоприятные условия для дефосфорации металла.
В среднем по исследованному массиву, а также на конкретных плавках наблюдаемый эффект рефосфорации объясняется повышением температуры шлака, а не полупродукта. В качестве средней температуры шлака середины окислительного периода рационально принимать 1715°С. Это значение позволяет наиболее точно прогнозировать минимально достижимые содержания фосфора в полупродукте по ходу плавки. Температура шлака в конце плавки может достигать 1750 °С, изменяясь в зависимости от температуры выпуска полупродукта. Анализ рафинирующей способности шлака в этих диапазонах температур показал, что для предотвращения рефосфорации достаточно повышать основность шлака на 0,25-0,5 ед. к концу плавки. Полезно также повышать рафинирующую способность шлака, раскисляя до содержания (FeO) = 20-25 %, и охлаждать его, например, периодическими присадками извести по ходу окислительного периода. Разработка подобных рекомендаций была бы невозможна, если бы для анализа процессов дефосфорации и рефосфорации полупродукта использовалось традиционное приближение – оценка равновесия, к которому стремится реальный процесс распределения фосфора, по фактически измеряемой температуре объёма полупродукта.
В третьей главе проведён анализ возможностей стабилизации вспениваемости шлаков по ходу окислительного периода. В практических условиях плавки полупродукта в сверхмощных ДСП вспениваемость шлаков, в основном, определяется их вязкостью и повышается с ростом вязкости. Опыт показывает, что повышение вязкости шлаков может быть достигнуто их гетерогенизацией, данный эффект объясняется с позиций, изложенных в работах Я.Френкеля и А.Эйнштейна по вязкости суспензий. Поэтому в ряде исследований для повышения вспениваемости электропечного шлака предлагали его гетерогенизировать за счёт насыщения тем или иным соединением. Однако рекомендации по корректировке состава шлака делали, ориентируясь на фактическую температуру металла по ходу плавки, а не самого шлака, т.е. без учёта перегрева шлакового слоя относительно металла. В данном исследовании также предложено корректировать состав электропечных шлаков для их гетерогенизации с целью повышения вязкости, но, исходя из того, что их температура ликвидус должна превышать фактическую температуру самого шлакового слоя.
Были подобраны шлаки, взаимосвязь составов которых имитирует шлакообразование в ДСП. Составы подбирались специально, чтобы все экспериментальные шлаки были связаны друг с другом – состав каждого шлака можно получить из любого другого, изменяя содержание (СаО) и (FeO) и производя пересчёт содержания компонентов на 100 %. Таким образом, имитируются процессы изменения составов и свойств шлаков при изменении соотношения вдуваемых в ДСП угля и кислорода, содержания углерода в металле, подаче в ДСП извести.
С помощью полимерной модели были рассчитаны температуры гомогенизации (температуры ликвидус) экспериментальных шлаков. Во всём исследованном диапазоне температур (1500-1900°С) для данных шлаков, содержащих не более 6 % (MgO), выявлена возможность насыщения только одним веществом – (СаО). Выяснилось, что шлаки обычного состава (основность менее 2,5 ед.) могут сохранять гетерогенность только в конце расплавления и начале окислительного периода. При этом возможное повышение содержания в шлаке (FeO) более 25-30 % переводит шлаки обычного состава в полностью жидкое состояние даже в конце расплавления. На практике это проявляется как снижение вспениваемости шлака при попадании в завалку значительных количеств окисленного лома, «мягком расплавлении» из-за нестабильного усвоения металлом науглероживателя и т.п.
На практике, кроме повышения вспениваемости шлаков, необходимо также обеспечить их высокую рафинирующую способность, т.е. приблизить состав к диапазону (FeO) 20-25 %, где наблюдаются максимальные коэффициенты распределения фосфора. В этом диапазоне достаточно иметь основность 2,7-2,8 ед., чтобы обеспечить гетерогенность шлака до конца плавки. В начале окислительного периода в том же диапазоне (FeO) достаточно иметь основность 2,4-2,5 ед.
Для подтверждения и оценки возможностей повышения вспениваемости шлаков за счёт их насыщения известью проведены лабораторные исследования вязкости шлаков, моделирующих средние обычно применяемые составы и составы с предположительно большей вязкостью, полученных на основе первых добавкой извести (табл.1). Учитывая сложный состав шлаков и возможную гетерогенизацию, было сделано предположение о наличии изменений их структуры по ходу эксперимента, которые, очевидно, не могут протекать с бесконечно высокой скоростью. Вследствие чего исследование вязкости не проводили методом непрерывных измерений при охлаждении шлака, поскольку это может привести к получению участков данных с заниженными значениями и резким ростом вязкости. С целью максимально возможного устранения релаксационных явлений показания вязкости снимали с длительными выдержками при определённых температурах. Из-за наличия объективных трудностей в проведении длительных опытов при высоких температурах, верхний интервал температур при проведении эксперимента ограничили наименьшими температурами шлака, зафиксированными на ДСП-135 (до 1650°С). Полученные данные перестраивались в координатах
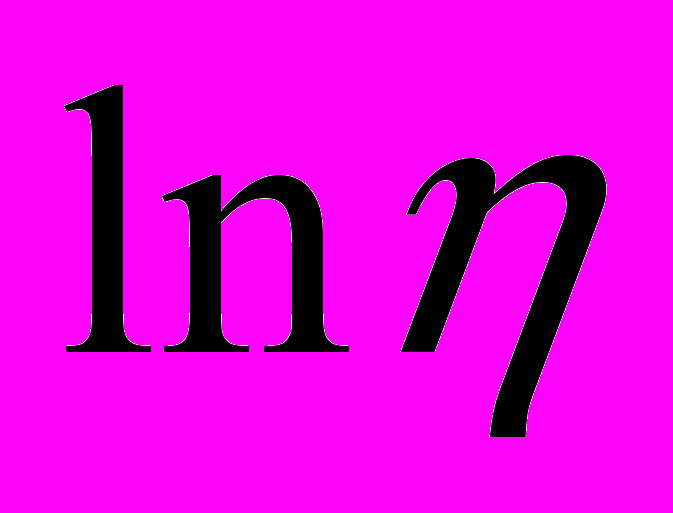
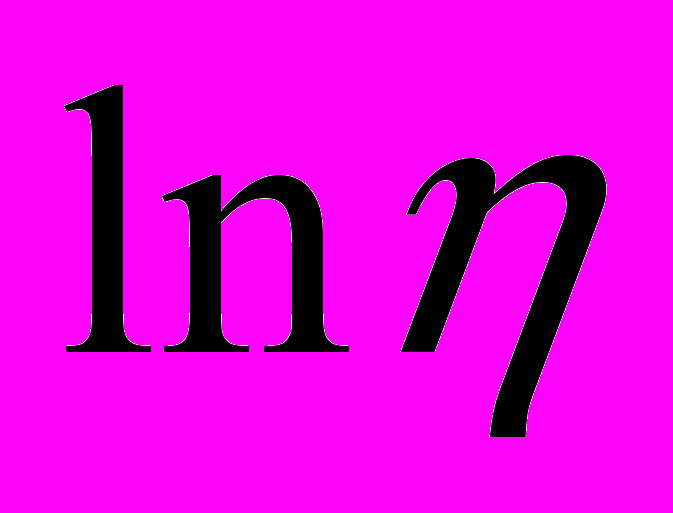
Таблица 1 – Основные характеристики экспериментальных шлаков
Показатель | Группы шлаков | |||||||||
обычного состава | рекомендованного состава | |||||||||
номер шлака | 3 | 2 | 1 | 4 | 5 | 3'' | 2'' | 1'' | 4'' | 5'' |
FeO, % | 16,7 | 21,1 | 25,0 | 28,6 | 31,8 | 13,2 | 16,9 | 20,2 | 23,4 | 26,2 |
Основность, д.е. | 2,0 | 3,1 |
Температуры ликвидус шлаков основности 2,0 ед., зафиксированные по переломам в графиках
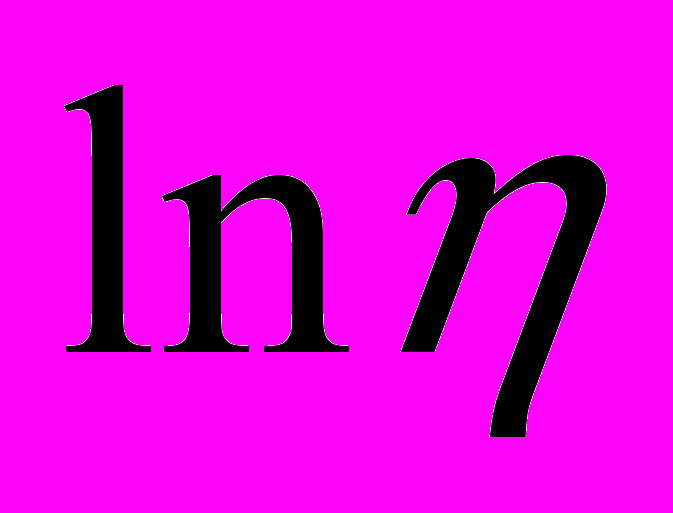
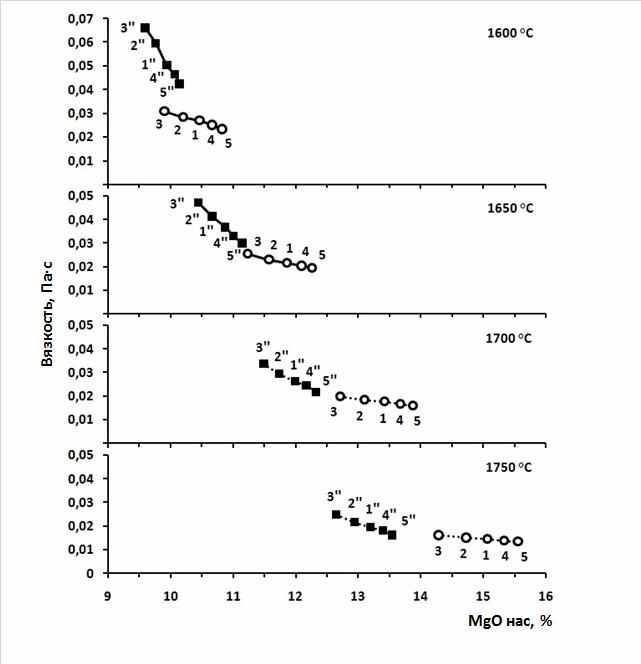
Рисунок 3 - Вязкость и предел растворимости оксида магния (MgO)нас в исследованных шлаках при 1600, 1650, 1700 и 1750 °С:
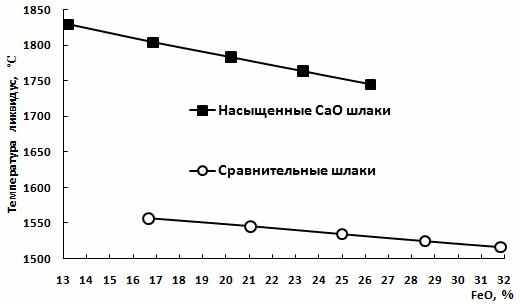
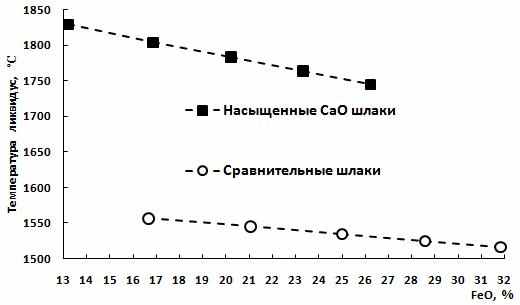
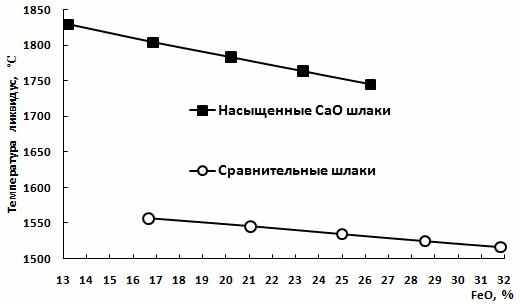
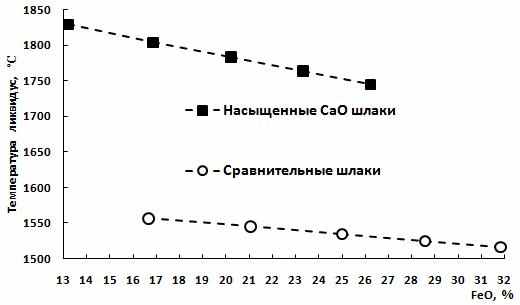
В то же время известно, что повышение основности гомогенных шлаковых расплавов приводит к снижению их вязкости. Эксперимент показал - для шлаков исследованного состава повышение основности приводит к повышению вязкости (рис.3), что может вызываться только гетерогенизацией шлаков из-за неполного растворения введённой извести. Из данных, представленных на рисунке 3, также следует, что формирование более основных и менее железистых шлаков позволяет снизить износ огнеупоров комплексно за счёт повышения вязкости шлаков и снижения растворимости в них (MgO).
В четвёртой главе проведён анализ особенностей технологии плавки полупродукта в ДСП-135 ОАО «Северский трубный завод». Выявлено преимущественное формирование по ходу окислительного периода шлаков с широкими диапазонами содержания (FeO) = 25-50 % и основности 1,8-2,6 ед. Основными причинами формирования таких шлаков являются излишне высокий расход кислорода, нестабильный ввод извести в шлак и угля в шлак и металл из-за уноса части их присадок в газоотводящий тракт, отсутствие в технологической инструкции требования о более высоком и узком интервале основности.
Установлено, что практически всегда на серийных плавках фиксируется режим «плохого» вспенивания шлака, при котором низкий уровень шлака не приводит к достаточному экранированию дуг. Согласно результатам проведённых лабораторных и теоретических исследований неудовлетворительная вспениваемость шлаков серийной технологии вызвана их незначительной вязкостью в температурных условиях окислительного периода. С целью повышения вспениваемости шлаков, улучшения их рафинирующей способности и снижения агрессивности к футеровке было рекомендовано формировать шлаки окислительного периода с содержанием (FeO) = 20-25 % с получением к концу плавки основности 2,7-2,8 ед. Для этого в существующую технологию плавки были внесены следующие изменения: изменён режим продувки со снижением расхода кислорода на плавку с 4745 до 4236 нм3, на 30 % снижена тяга газоочистки, внедрена дополнительная добавка извести и угля по ходу окислительного периода, корректирующая состав шлака «по расплавлении». Соблюдение данных рекомендаций привело к улучшению вспениваемости шлаков, в том числе в конце плавки, и основных технико-экономических показателей плавки полупродукта в ДСП-135.
Практика показала, что введение извести по ходу окислительного периода, т.е. её рассредоточенная присадка позволяет хорошо вспенивать в конце плавки шлаки с содержанием (FeO) до 35 %. По-видимому, это связано с незавершённостью растворения извести и охлаждением шлака. На плавках, проводимых по рекомендованному режиму, практически полностью устраняется рефосфорация, снижаются содержание азота в металле и расход электроэнергии, не отмечаются случаи перегрева воды в панелях и интенсивного износа огнеупоров в горячих зонах футеровки, обычно фиксирующиеся при проведении плавок по принятому режиму. По результатам исследования подготовлена заявка и получен приоритет ФИПС на патент № 2008148432 от 08.12.2008 «Способ получения стали в дуговой электросталеплавильной печи».
Оценку качества вспенивания шлака на серийных и опытных плавках проводили визуально и по уровню шума, а также методом анализа параметров электрического режима плавки. Специально созданный измерительно-вычислительный комплекс позволял снимать сигналы токов и напряжений фаз с низкой стороны трансформатора, представлять полученные данные в виде осциллограмм и вольт-амперных характеристик (ВАХ) токов и напряжений, амплитудно-частотных характеристик (АЧХ) фазных напряжений. Обработка полученных таким образом данных по электрическому режиму плавок при «плохом» и «хорошем» вспенивании позволила разработать новый способ оценки качества вспенивания шлака.
Электрическая схема замещения рабочего пространства ДСП с горящими под шлаком дугами аналогична схеме замещения ферросплавных печей, осуществляющих шлаковый процесс выплавки ферросплавов (рис.4а). Соответственно, динамические ВАХ полезной нагрузки в обоих случаях интерпретируются одинаково (рис.4б):
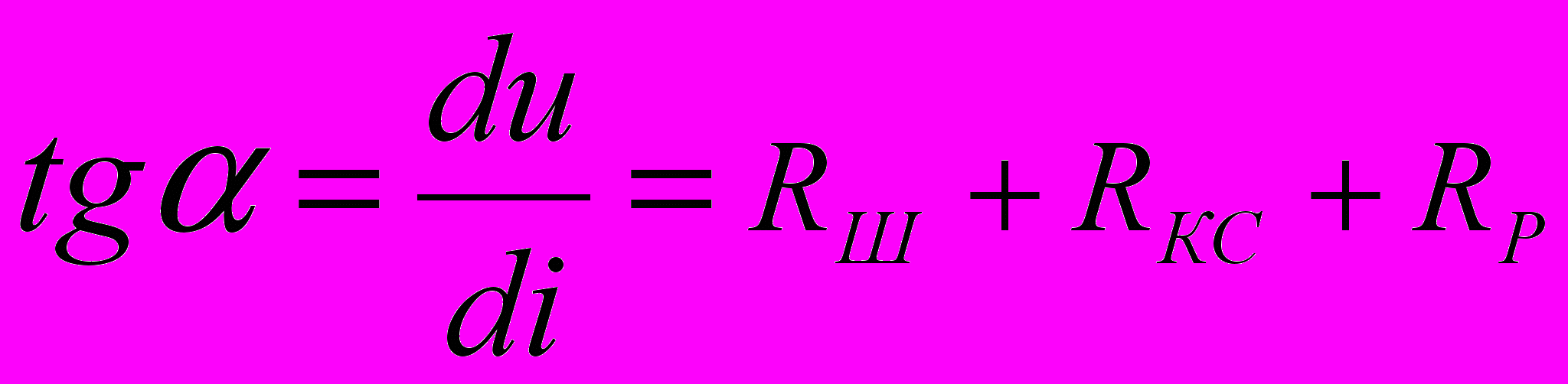
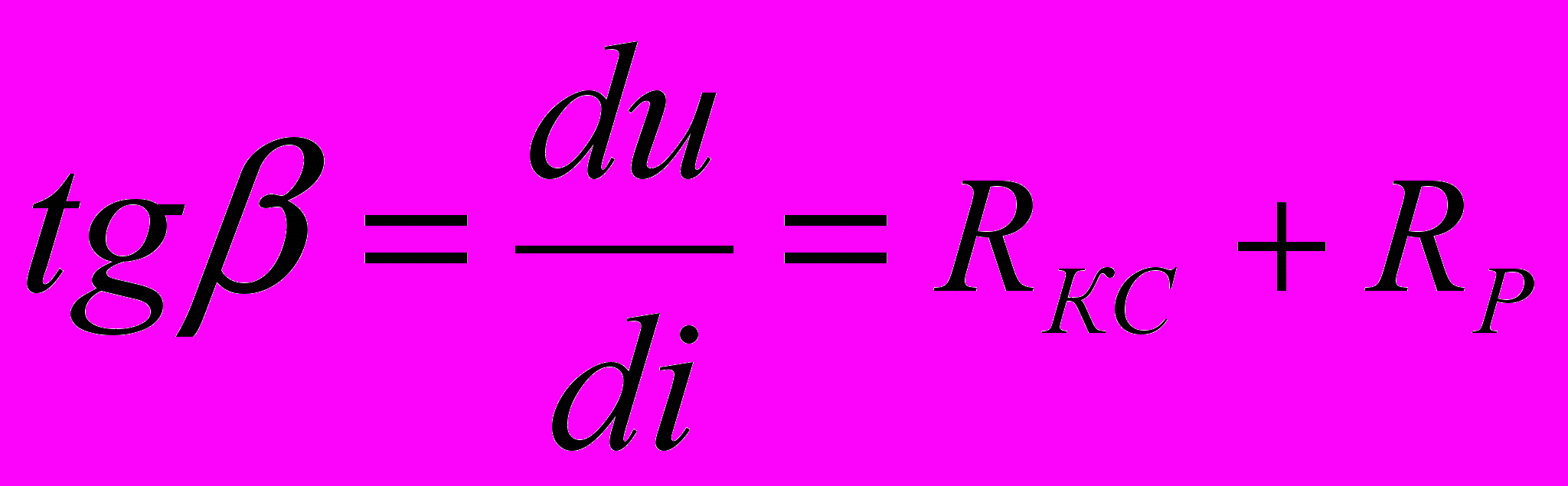
где,
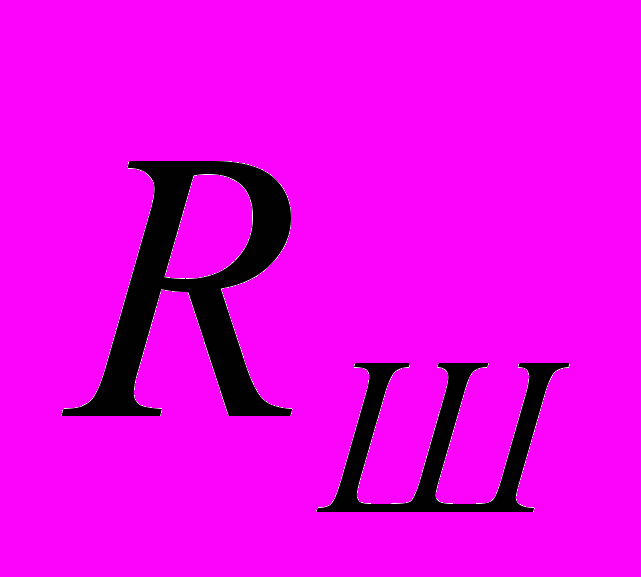
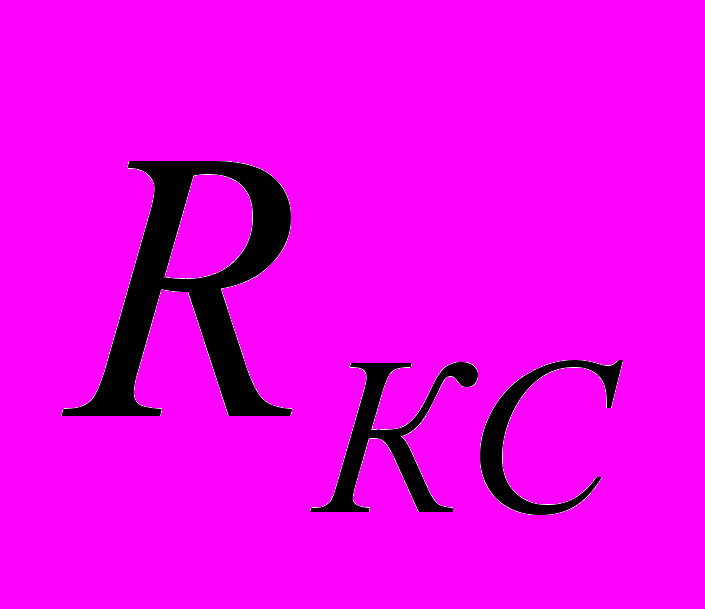
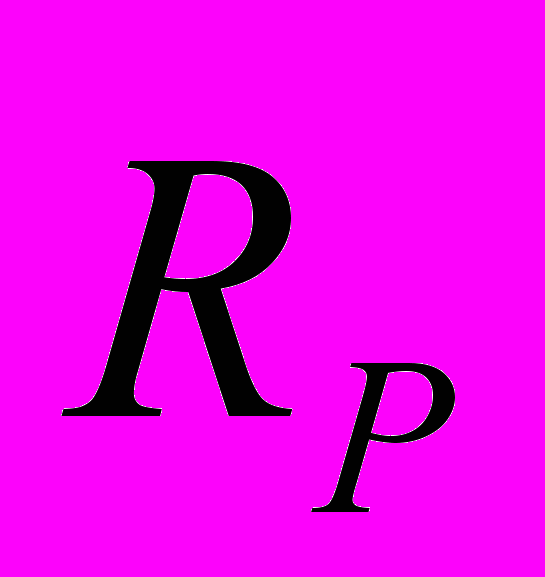
![]() а | ![]() б |
Рисунок 4 – Схема замещения рабочего пространства ДСП, работающих с горящими под шлаком дугами, и ферросплавных печей, осуществляющих шлаковый процесс выплавки ферросплавов (а); идеализированная ВАХ полезной нагрузки (б):
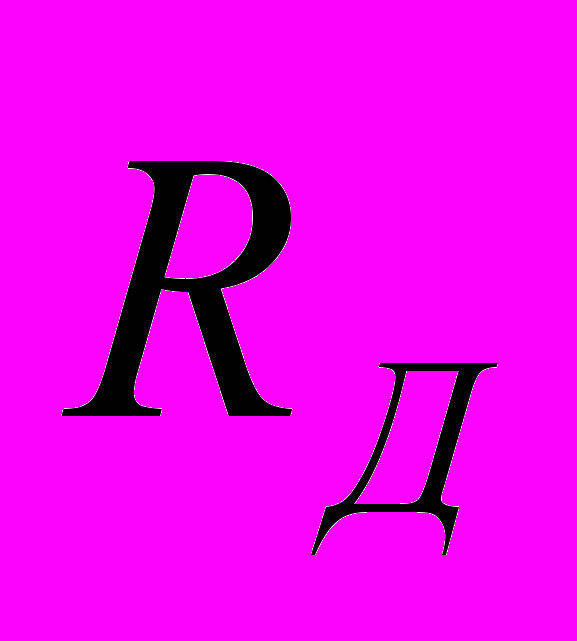
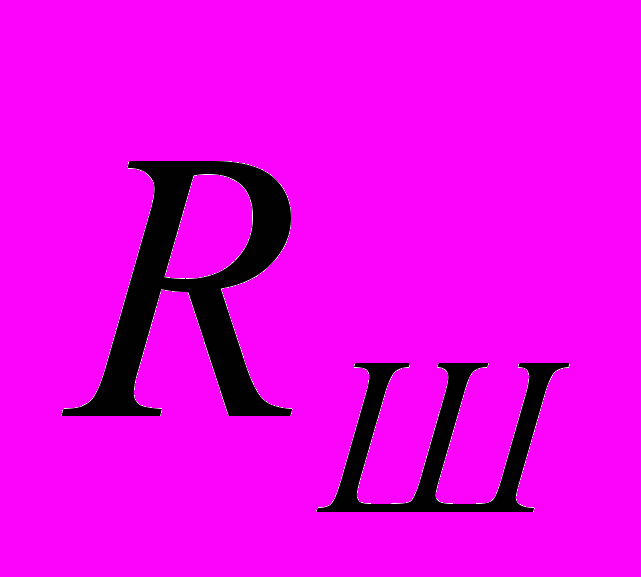
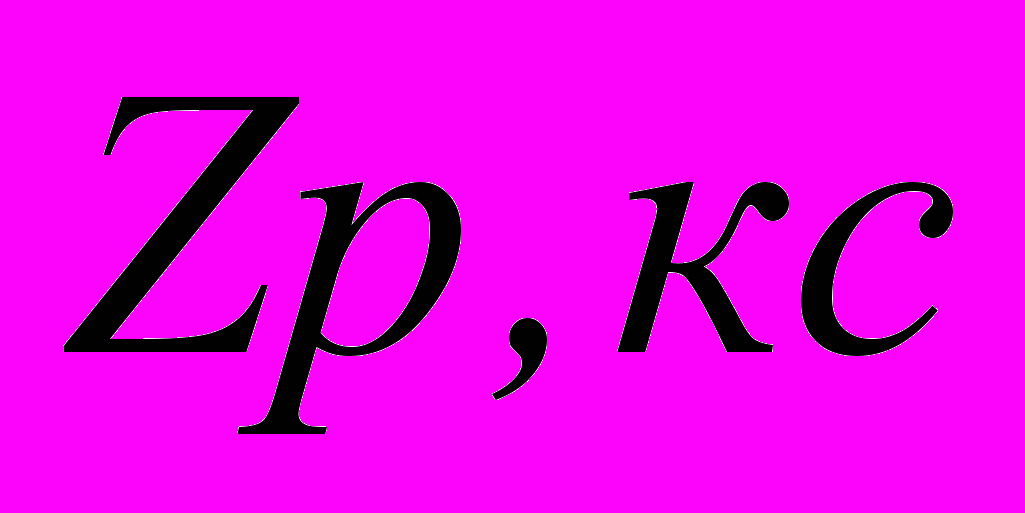
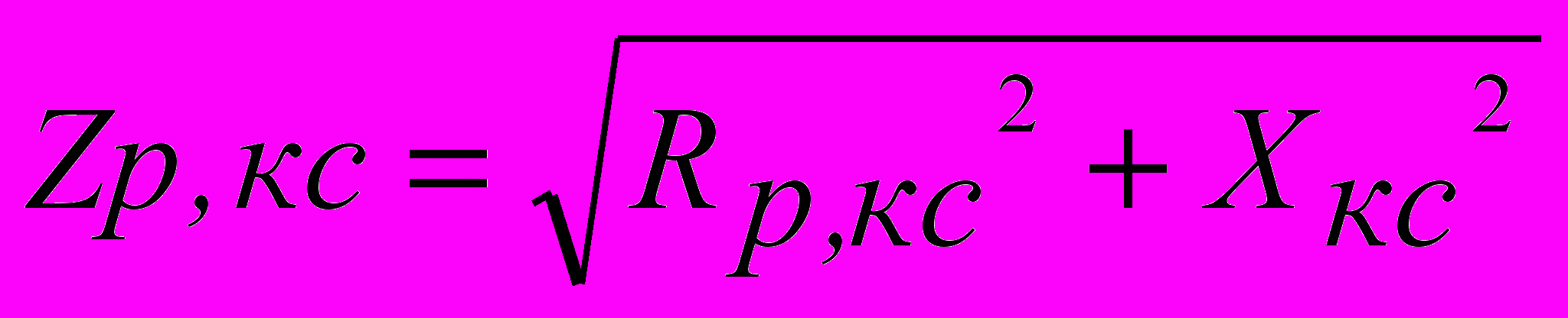
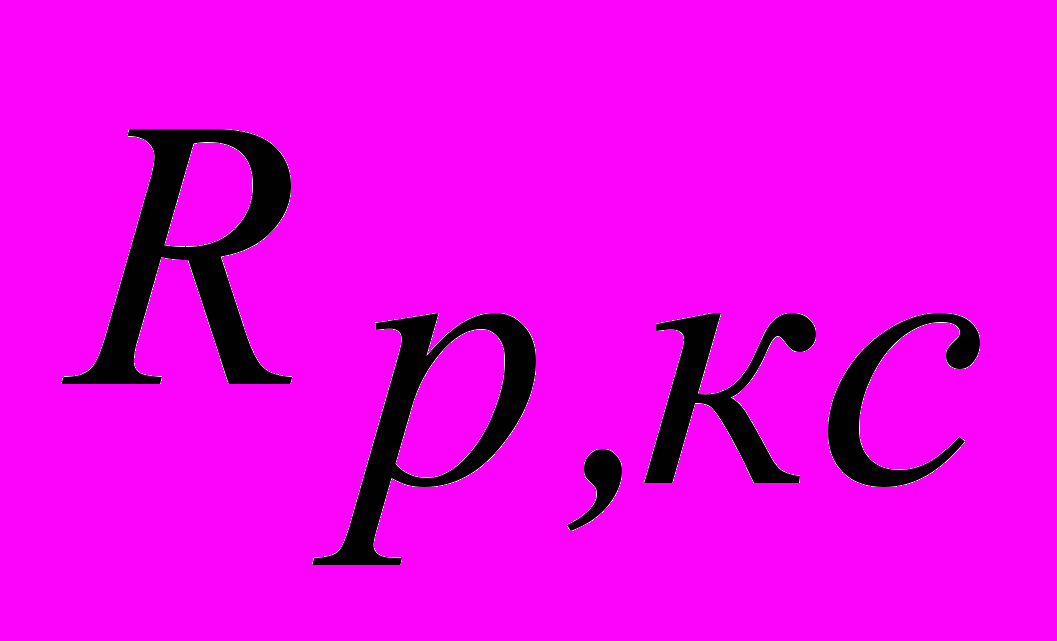
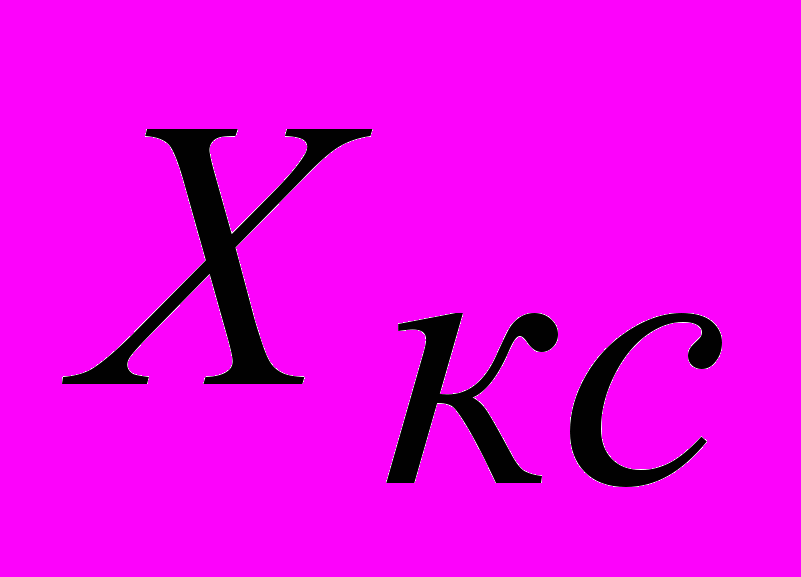
Расчёт нагрузки по значениям
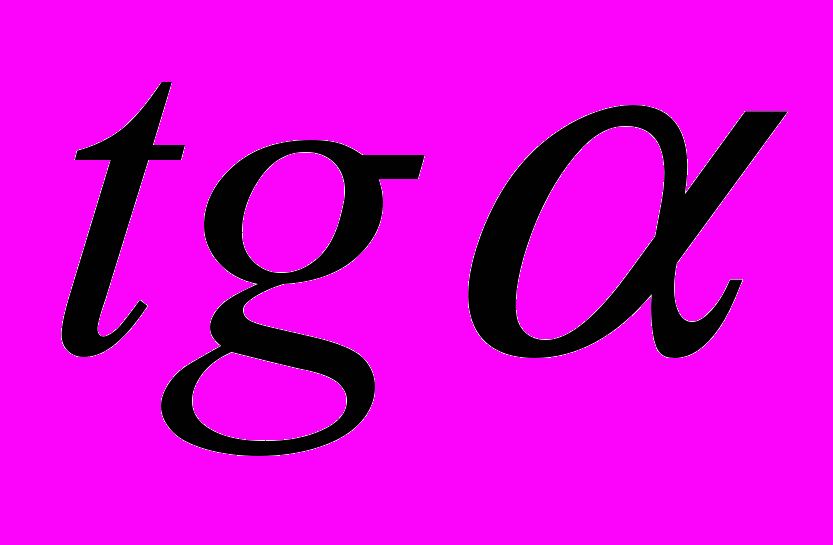
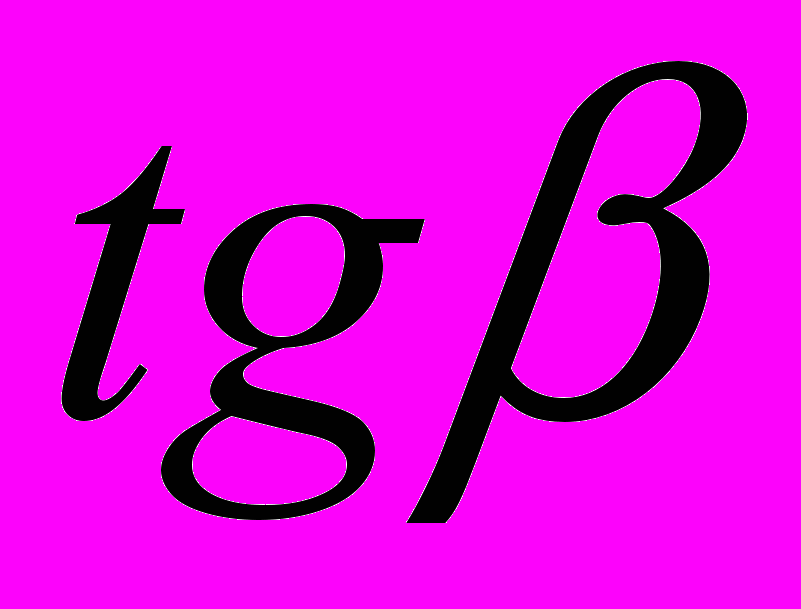
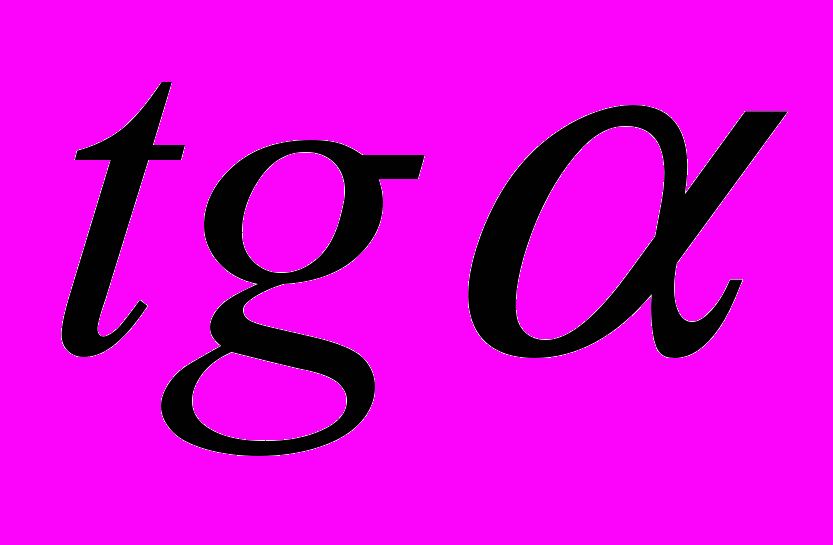
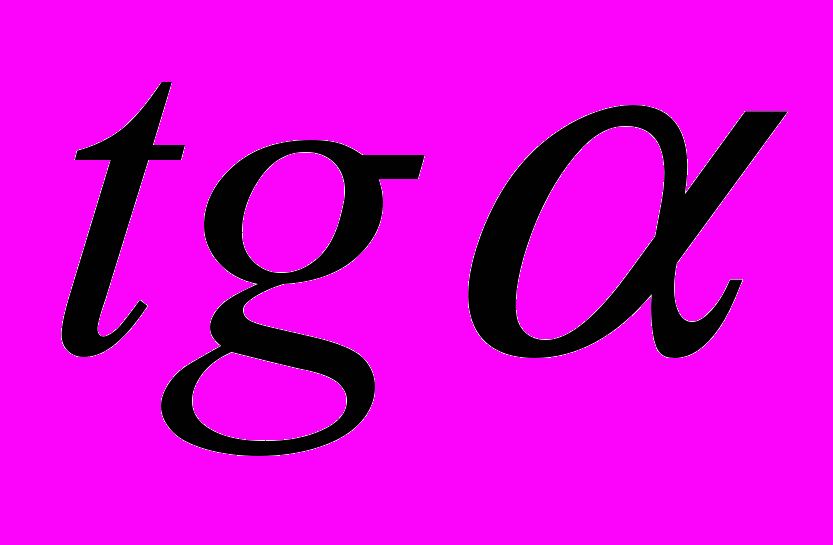
Установлено, что в режиме «плохого вспенивания»
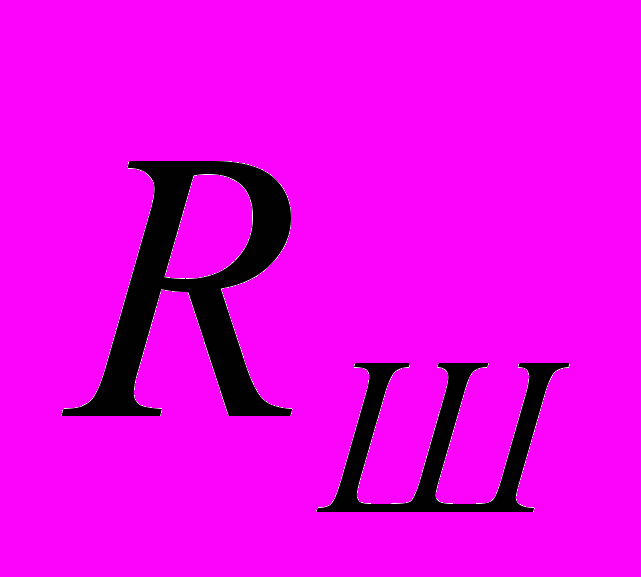
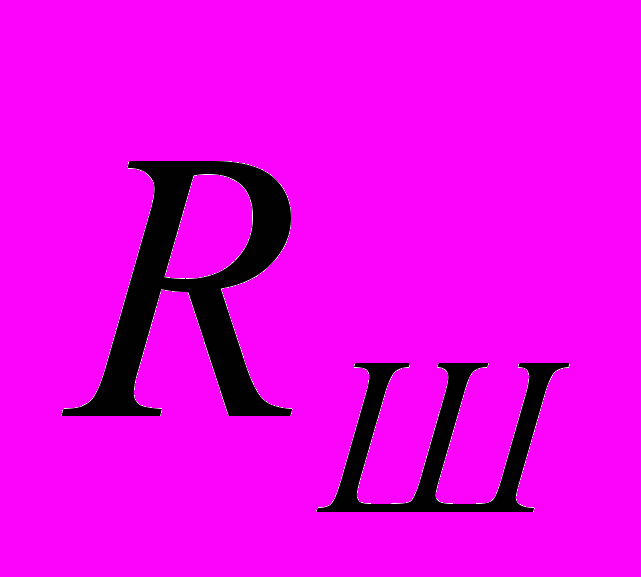
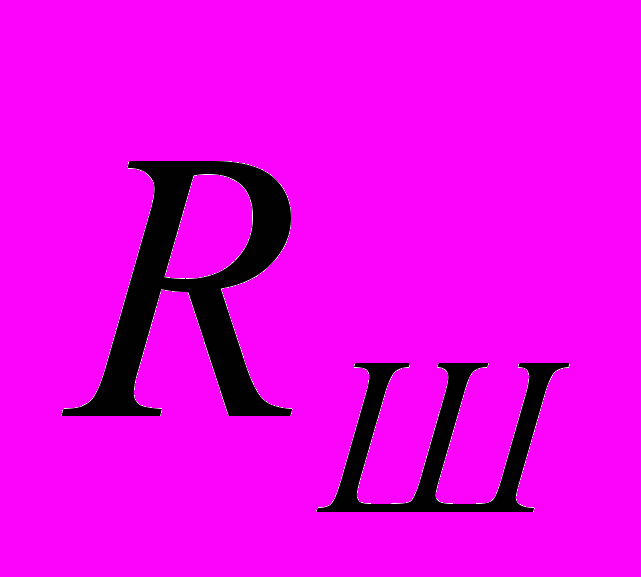
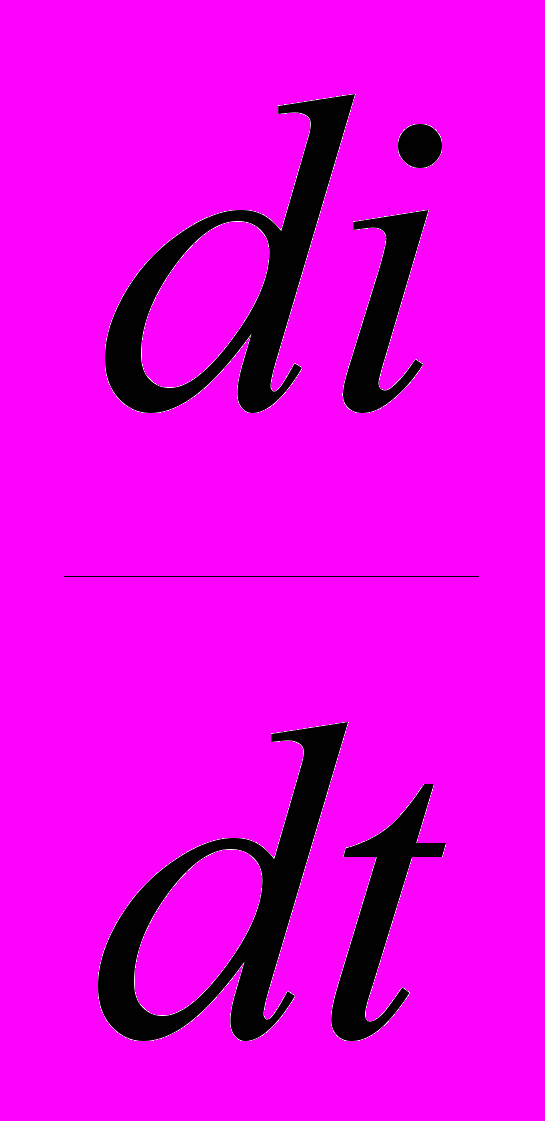
![]() а | ![]() б |
![]() в | ![]() г |
Рисунок 5 – Осциллограммы и динамические ВАХ токов и напряжений низкой стороны трансформатора при «плохом» (а, б) и «хорошем» (в, г) вспенивании шлака
Наличие таких участков свидетельствует о нестабильном тепловом состоянии разрядного промежутка, которое вызывается повышенными потерями энергии дуг на излучение в рабочее пространство печи из-за недостаточного экранирования шлаком. Кроме того, пики зажигания и участки негладкости функции тока свидетельствуют о практически полной ликвидации контакта «электрод-шлак» (шунтирования дуг шлаком). Для фаз с наименьшим погружением электродов в шлак также характерен рост амплитуд высших гармоник фазного напряжения, в т.ч. 7-й и 9-й, рост которых в настоящее время принято связывать с ухудшением теплоизоляции дуги и качества вспенивания шлака (рис.6, табл.2).
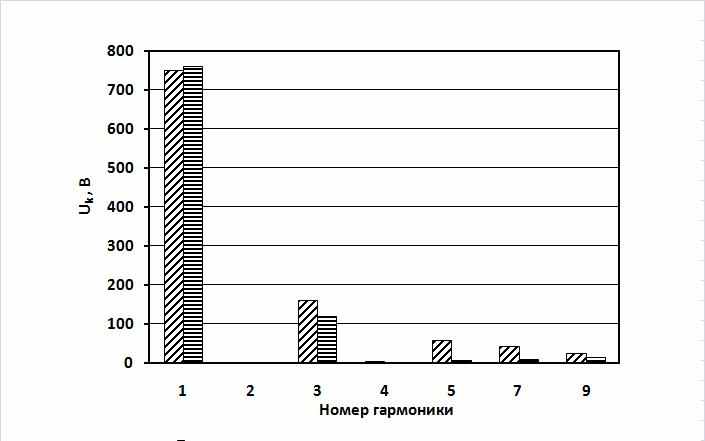
Рисунок 6 – Амплитуды Uk гармонических составляющих фазного напряжения:
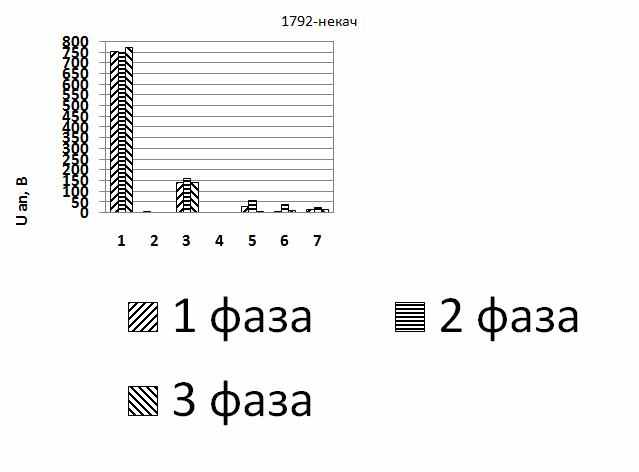
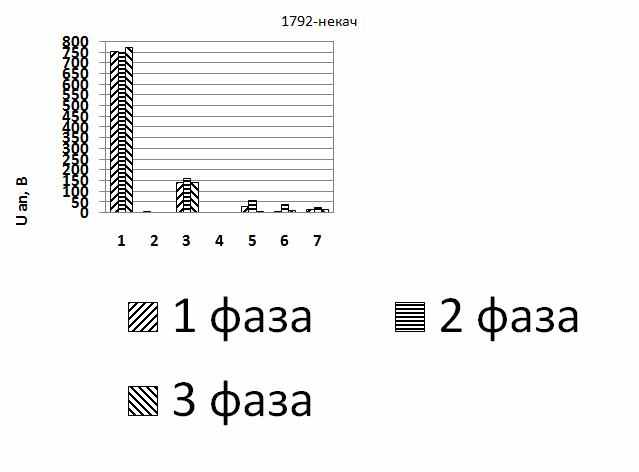
Таблица 2 – Отношение амплитуд высших гармоник фазного напряжения (U1…U9) к действующему фазному напряжению (Uд) для случаев «плохого» и «хорошего» вспенивания (рис. 5 и 6), %
Качество вспенивания | U1/ Uд | U2/ Uд | U3/ Uд | U4/ Uд | U5/ Uд | U7/ Uд | U9/ Uд |
«плохое» | 97,2 | 0,3 | 21,0 | 0,6 | 7,7 | 5,5 | 3,4 |
«хорошее» | 98,7 | 0,3 | 15,6 | 0,2 | 0,8 | 1,5 | 1,9 |
Напротив, при «хорошем» вспенивании шлака, когда уровень шлака в печи выше,
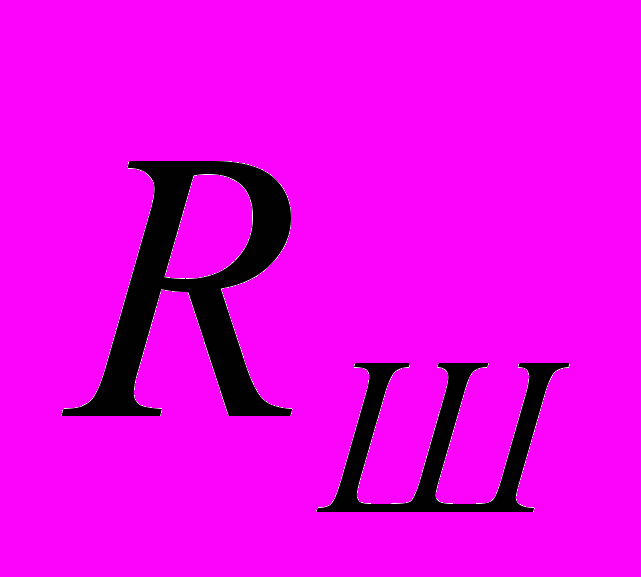
АЧХ фазных напряжений «хорошего» вспенивания обнаруживают достаточно низкий и ровный уровень высших гармоник, в т.ч. 7-й и 9-й, по всем фазам, в сравнении с недостаточно теплоизолированными дугами при «плохом вспенивании» (рис.6, табл.2). Таким образом, при получении хотя бы для одной из фаз значения
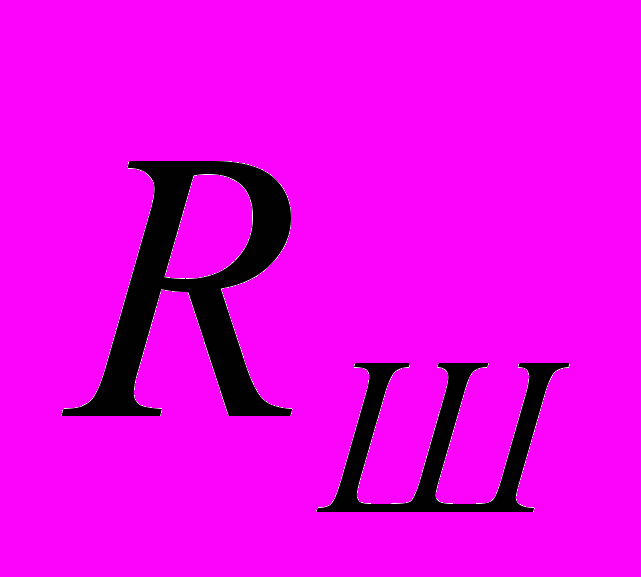
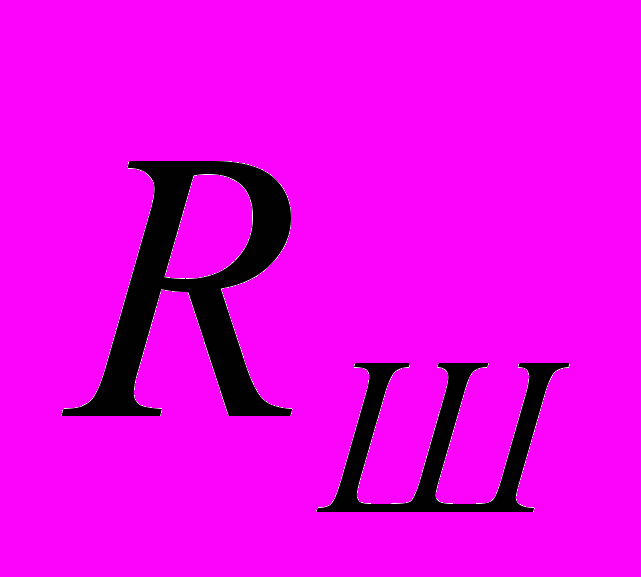
ЗАКЛЮЧЕНИЕ
- На сверхмощной ДСП-135 ОАО «Северский трубный завод» проведены измерения температур шлака и полупродукта в конце расплавления и по ходу окислительного периода. Подтверждено, что температура шлака превышает температуру полупродукта. Установлено, что температура шлака в зоне, расположенной над точкой традиционного замера температуры полупродукта, превышает температуру полупродукта в среднем на 70°С.
- Показано, что при прогнозировании минимально достижимого содержания фосфора в полупродукте по ходу плавки, а также содержания фосфора в полупродукте в конце плавки целесообразно ориентироваться на температуру шлака. Установлено, что наблюдаемый эффект рефосфорации в конце плавки объясняется, в основном, повышением температуры шлака, а не традиционно измеряемой по ходу плавки температуры полупродукта. Для устранения рефосфорации достаточно повышать основность шлака на 0,25-0,5 ед. к концу плавки. Полезно также шлак охлаждать и раскислять до содержания (FeO) = 20-25 %.
- Установлено, что для ДСП с температурой выпуска полупродукта 1670-1690°С формирование шлаков с основностью 2,7-2,8 ед. при снижении содержания (FeO) до 20-25 % обеспечивает поддержание достаточного уровня шлаковой пены до конца плавки. Рассредоточенная присадка извести с получением основности до 3,1 ед. позволяет хорошо вспенивать шлаки в конце плавки с содержанием (FeO) до 35 %.
- Подтверждено, что формирование более основных и менее железистых шлаков способствует снижению износа огнеупоров по механизму их растворения в шлаке. Установлено, что приём гетерогенизации шлаков за счёт насыщения известью дополнительно улучшает экранирование футеровки ДСП от излучения дуг вследствие улучшения вспенивания. Таким образом, показано, в т.ч. промышленными испытаниями, что данный приём является перспективным способом совершенствования электроплавки, позволяющим комплексно улучшить вспениваемость и рафинирующие свойства шлаков, снизить их агрессивность к футеровке.
- С целью исследования влияния технологии вспенивания шлака на параметры электрического режима ДСП-135 была создана и использована специальная измерительно-вычислительная система. На основе комплексного анализа осциллограмм и ВАХ токов и напряжений низкой стороны трансформатора, а также АЧХ фазных напряжений режимов «плохого» и «хорошего» вспенивания выявлены характерные признаки ухудшения экранирования дуг шлаком. Установлено, что признаками «плохого» вспенивания являются: высокое значение (≥ 30 мОм) шунтирующего дугу сопротивления, наличие пиков зажигания и участков негладкости функции тока. Подтверждено, что признаком «плохого» вспенивания также является рост амплитуд высших гармоник фазного напряжения.
- Разработан новый метод оперативного контроля качества вспенивания шлака для ДСП переменного тока по параметрам электрического режима, а именно, посредством оценки величины шунтирующего дугу сопротивления.
- Разработаны и испытаны технологические приёмы реализации рационального режима плавки полупродукта в сверхмощной ДСП-135 ОАО «Северский трубный завод», позволившие улучшить основные технико-экономические показатели работы ДСП-135, что подтверждено Актом испытаний и Расчётом экономического эффекта. Ожидаемый экономический эффект составляет 10,34 млн. руб. в год.
- По результатам исследования подготовлена заявка и получен приоритет ФИПС на патент № 2008148432 от 08.12.2008 «Способ получения стали в дуговой электросталеплавильной печи».
Основное содержание работы изложено в следующих публикациях:
- Сивцов А.В. О перспективных направлениях развития автоматизированных систем управления технологическими режимами выплавки стали в электродуговых печах /А.В. Сивцов, О.Ю. Шешуков, М.М.Цымбалист, И.В. Некрасов, В.Н. Бондаренко //Сталь, 2009. № 10. С. 30-33.
- Некрасов И.В. Перспективы дальнейшего повышения технико-экономической эффективности производства стали в сверхмощных электродуговых печах /И.В. Некрасов, В.С. Гуляков, О.Ю. Шешуков //Энергетики и металлурги настоящему и будущему России: Материалы 9-й Всерос. науч.-практ. конференции студентов, аспирантов и специалистов. Магнитогорск: ГОУ ВПО «МГТУ», 2008. С. 16-18.
- Некрасов И.В. Влияние способов интенсификации электроплавки на стойкость футеровки ДСП /И.В. Некрасов, О.Ю. Шешуков, В.С. Гуляков //Проблемы чёрной металлургии и материаловедения, 2008. № 4. С. 82-85.
- Некрасов И.В. Прогнозирование вязкости гетерогенных шлаков по ходу плавки //Материалы V Российской ежегодной конференции молодых научных сотрудников и аспирантов. 11-13 ноября 2008 г. Под ред. академика РАН Ю.В. Цветкова и др. Перспективные материалы. Специальный выпуск (5), ноябрь 2008 г. С. 217-220.
- Некрасов И.В. Прогнозирование вязкости гетерогенных шлаков /И.В. Некрасов, В.Н. Невидимов, О.Ю. Шешуков //Строение и свойства металлических и шлаковых расплавов: Тр. XII Российской конференции. Т1. Моделирование и расчёт структуры и свойств неупорядоченных систем в конденсированном состоянии - Екатеринбург: УрО РАН, 2008. С. 123-126.
- Сысолин А.В. Влияние химического состава шлака на электрический режим плавки стали в дуговой печи переменного тока /А.В. Сысолин, И.В. Некрасов, О.Ю. Шешуков, В.Т. Луценко, В.С. Гуляков //Строение и свойства металлических и шлаковых расплавов: Тр. XII Российской конференции. Т3. Экспериментальное изучение шлаковых расплавов; взаимодействие металл – шлак - Екатеринбург: УрО РАН, 2008. С. 98-101.
- Шешуков О.Ю. Применение автоматизированной системы контроля и управления (АСКиУ) технологией выплавки стали /О.Ю. Шешуков, А.В. Сивцов, С.В. Житов, К.В. Тихонов, В.Т. Луценко, В.Н. Бондаренко, А.В. Сысолин, И.В. Некрасов //Тр. Десятого конгресса сталеплавильщиков - М.: ОАО «Черметинформация», 2009. С. 377-380.
- Некрасов И.В. Перспективные направления совершенствования плавки и доводки стали в электродуговых печах переменного тока и агрегатах «ковш-печь» /И.В. Некрасов, А.В. Сысолин, О.Ю. Шешуков, В.Т. Луценко, В.Н. Бондаренко, В.С. Гуляков //Тр. Десятого конгресса сталеплавильщиков - М.: ОАО «Черметинформация», 2009. С. 256-260.
- Сысолин А.В. Управление электрическим и технологическим режимами плавки по анализу постоянной составляющей напряжения дуги (ПСНД) /А.В. Сысолин, О.Ю. Шешуков, И.В. Некрасов, В.Т. Луценко, В.Н. Бондаренко, В.С. Гуляков //Тр. Десятого конгресса сталеплавильщиков - М.: ОАО «Черметинформация», 2009. С. 346-353.
- Некрасов И.В. Автоматический контроль состава шлака при обработке стали на агрегатах ковш-печь по параметрам электрического режима /И.В. Некрасов, О.Ю. Шешуков, А.В. Сысолин, В.Т. Луценко, В.Н. Бондаренко //Известия вузов. Чёрная металлургия, 2009. № 10. С.18-21.
- Решение ФИПС о приоритете на патент по заявке № 2008148432 от 08.12.2008. Способ получения стали в дуговой электросталеплавильной печи /О.Ю. Шешуков, И.В. Некрасов, В.С. Гуляков, А.В. Сысолин.
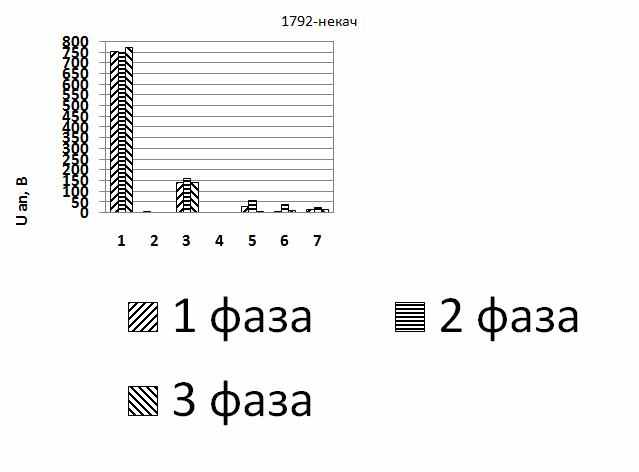
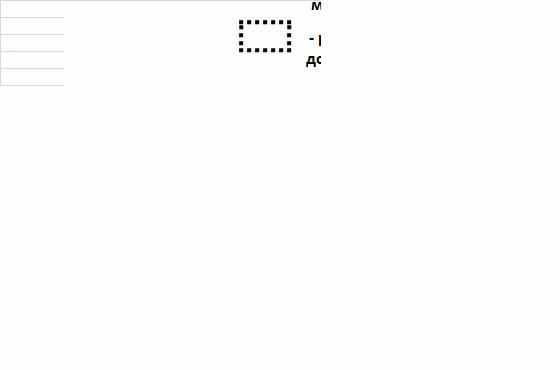
1 Jung S. Foaming characteristics of BOF slags /S. Jung, R.J. Fruehan //ISIJ International, Vol. 40 (2000). № 4. Pp. 348-355