Лабораторная работа №4
Вид материала | Лабораторная работа |
Содержание1 между двумя шлифовальными кругами. Шлифующий круг 2 |
- Методические указания к лабораторным работам Лабораторная работа, 357.24kb.
- Лабораторная работа №3 кпк лабораторная работа №3 Тема: карманный персональный компьютер, 173.34kb.
- Методические возможности стенда Особенности работы на стендах уилс-1 Ознакомительное, 1487.3kb.
- Лабораторная работа по курсу «Физические основы микроэлектроники», 136.21kb.
- Лабораторная работа, 166.92kb.
- Самостоятельная работа по учебным пособиям, 471.48kb.
- Конспект урока в 9 классе по теме: «Магний», 84.54kb.
- Лабораторная работа №1 Введение в Windows. Работа с окнами и приложениями в Windows, 67.41kb.
- Знакомство c Excel, 1212.51kb.
- Лабораторная работа, 105.21kb.
Лабораторная работа №4
Абразивная обработка
Абразивная обработка осуществляется твердыми и термостойкими зернами, имеющими острые кромки. В абразивных инструментах (шлифовальных и заточных кругах, брусках и шкурках) зерна находятся в связанном состоянии. Применяется также обработка свободными зернами в виде порошков, суспензий и паст.
К естественным абразивным материалам относятся наждак, корунд и природные алмазы. Однако их применяют сравнительно редко — первые в связи с неоднородностью и недостаточной стабильностью своих свойств, а алмазы — из-за дефицитности и высокой стоимости.
Среди искусственных материалов наибольшее использование нашел электрокорунд, получаемый электродуговой плавкой глинозема. Нормальный электрокорунд, который может быть трех видов и обозначается марками 13А, 14А и 15А, содержит 91—96 % кристаллической окиси алюминия А12Оз. Инструменты из него обычно имеют светло-коричневый цвет. В электрокорунде белом (23А—25А) всего 1—3 % примесей, благодаря чему выше режущие свойства. Его применяют для чистовой обработки материалов с высокой прочностью на разрыв (сталь, ковкий чугун, мягкая бронза).
Разновидность электрокорунда — монокорунд (43А—45А), получаемый в виде отдельных кристаллов или их осколков. Его используют для окончательного шлифования труднообрабатываемых сталей и сплавов. Для повышения производительности обработки применяют электрокорунды, легированные хромом, титаном, цирконием.
Карбид кремния SiC (карборунд) получают сплавлением в электропечах кремнезема, содержащегося в кварцевом песке, с углеродом (коксовым порошком). Он бывает двух видов: менее качественный черный (53С—55С) и зеленый (63С, 64С), для изготовления которого используют более чистые исходные материалы.
Карбид кремния обладает весьма высокими режущими свойствами благодаря высокой твердости и остроте кромок, получаемых при дроблении. Однако он хрупок и применяется поэтому при обработке материалов с малым пределом прочности на разрыв (чугун, бронзовые и алюминиевые отливки и др.). Зеленый карбид кремния целесообразно использовать для заточки твердосплавных инструментов.
Карбид бора В4С по твердости приближается к алмазу, но обладает еще большей хрупкостью, чем карбид кремния. Поэтому его обычно применяют в свободном состоянии для доводки различных твердых материалов и сплавов. В качестве абразивных материалов в последнее время широко используют также эльбор и синтетические алмазы, описанные в 8.7.
Чистота обработанной поверхности при абразивной обработке в значительной степени зависит от размеров зерен, которые принято делить на четыре основные группы: шлифзерно, шлиф-порошки, микрошлифпорошки и тонкие микрошлифпорошки. Зернистость, характеризующая размеры зерен, обозначается для первых двух групп в сотых долях миллиметра и определяется по размеру стороны квадратной ячейки сита в «просвете», через которые не проходят зерна при просеивании. Например, при зернистости 80 зерна задерживаются на сите с ячейками 0,8 х 0,8 мм.
Зернистость микрошлифпорошков обозначают буквой «М» и наибольшим размером зерна в микрометрах, например М63, М28, М10. Самые мелкозернистые порошки М5 имеют зерна размерами не более 5 мкм. Для алмазных и эльборовых зерен дробью показывают наибольшие и наименьшие предельные размеры.
Для закрепления зерен в инструментах применяют связки. Наибольшее распространение получила керамическая связка, обозначаемая буквой «К» и номером, например К1 или К10. В ее состав входят кремнезем (SiC) и глинозем (А12Оз), а также добавки из жидкого стекла, окислов некоторых металлов и других
элементов.
Инструменты на керамической связке обладают достаточно высокой прочностью, жесткостью и термостойкостью, но сравнительно хрупки. Их применяют для всех видов шлифования, кроме обдирки, прорезания узких пазов и отрезания.
Бакелитовую связку, обозначаемую буквой «Б», изготовляют на основе самотвердеющих органических смол. Она обладает по сравнению с керамической более высокой прочностью, особенно при работе на сжатие, и большей упругостью. Ее применяют при изготовлении инструментов всех форм и размеров, прежде всего тонких (до 1 мм) прорезных и отрезных кругов. Недостаток бакелитовой связки — невысокая термостойкость, так как при температуре 200 °С она становится хрупкой, а при длительном нагревании до 250—300 °С выгорает.
Вулканитовая связка (В) является провулканизированной смесью синтетического каучука и серы. Изготовленные на ее основе абразивные инструменты имеют высокую прочность, эластичность и влагостойкость. Применяют их при полировании и других отделочных видах обработки, а также для глубинного шлифования, резки и т. п. Основной недостаток этой связки — быстрое засаливание инструмента (заполнение его пор отходами).
Для изготовления алмазных и эльборовых кругов используют также металлические связки, включающие в качестве наполнителей порошки металлов и их сплавов, чаще всего — бронзы.
Важная характеристика абразивных инструментов — твердость, под которой понимают способность связки удерживать абразивные зерна от выкрашивания под действием внешних сил. Чем мягче инструмент, тем легче из него выкрашиваются зерна, прежде всего затупившиеся. В результате происходит постоянное обновление режущей способности инструмента, т. е. процесс самозатачивания. Однако это ведет к быстрому изменению размеров и формы инструмента и большому расходу инструментального материала.
С другой стороны, при слишком высокой твердости снижение выкрашиваемости затупившихся зерен способствует увеличению трения, тепловыделения и затрат мощности, на обработанной поверхности появляются прижоги. Все это требует частой правки (заточки) инструмента и снижает производительность обработки.
Правку выполняют срезанием поверхностного слоя инструмента алмазными карандашами, обкаткой стальными или твердосплавными дисками и звездочками (шарошками), а также абразивными дисками из черного карбида кремния на керамической связке.
Твердость абразивного инструмента выбирают в зависимости от свойств обрабатываемого материала и требуемого качества обработки: чем тверже материал заготовки, тем мягче должен быть инструмент, а чем выше заданная точность обработанной поверхности, тем большую твердость он должен иметь.
По твердости абразивные инструменты подразделяются на восемь групп: ВМ — весьма мягкие, М — мягкие, СМ — средне-мягкие, С — средние, СТ — среднетвердые, Т — твердые, ВТ — весьма твердые и ЧТ — чрезвычайно твердые. В пределах каждой группы может быть два-три номера твердости в порядке ее повышения, например инструмент МЗ тверже М2, но мягче, чем СМ1.
В абразивных инструментах связка не заполняет полностью все пространство между зернами, образуя поры, способствующие лучшему удалению стружки и охлаждению зерен, а также самозатачиванию. Однако инструмент с высокой пористостью менее прочен и быстрее изнашивается.
Соотношение между объемами, занимаемыми зернами, связкой и порами, характеризует структуру инструмента, обозначаемую номерами от 0 до 12. Этим пределам соответствует содержание абразивных зерен в объеме инструмента от 62 до 38 %. В некоторых случаях применяются высокопористые шлифовальные круги с номерами структур 13—21.
В зависимости от выполняемой обработки используются круги различной формы (рис. 99). Все описанные характеристики с помощью принятых обозначений, указанных выше, приводятся в маркировке шлифовальных кругов.
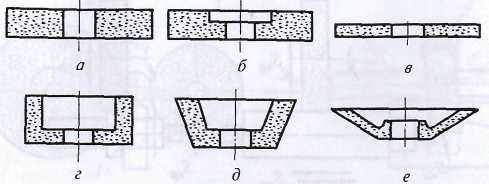
Рис. 99. Формы шлифовальных кругов:
а — прямого профиля (ПП); б— прямого профиля с выточкой (ПВ); в —дисковый (Д);
г — чашечный цилиндрический (ЧЦ); д — чашечный конический (ЧК);
е — тарельчатый (Т)
Алмазные круги диаметром более 13 мм состоят из двух частей: корпуса из дюралюминия или стали и алмазоносного слоя толщиной 1—5 мм, нанесенного на его рабочую поверхность. Иногда используют корпусы из пластмасс или обычных шлифовальных кругов. Аналогичную конструкцию имеют круги из эльбора.
Абразивная лента (шкурка) состоит из бумажной или тканевой основы, на которую наклеены абразивные зерна. Выпускают ее в виде рулонов или листов. Для обработки с охлаждением следует использовать специальные водостойкие шкурки.
В абразивных пастах зерна связывают маслами, воском, стеарином и т. п. Для повышения эффективности обработки в них вводят химически активные добавки. В результате химического воздействия на обрабатываемой поверхности образуется мягкая пленка, которая легко удаляется абразивом. Широко применяемая паста ГОИ содержит 75—80 % окиси хрома, 2—3 % безводной кремниевой кислоты, 15—20 % стеарина и 2 % керосина.
При абразивной обработке главное движение резания обычно совершает режущий инструмент. Благодаря высокой твердости и термостойкости абразивных зерен большинство видов обработки производится при высокой скорости резания, которая может достигать 80 м/с и более. Допускаемая скорость указывается в маркировке круга.
Абразивная обработка наружных поверхностей вращения осуществляется на круглошлифовальных станках. Заготовки на них устанавливают и приводят во вращение так же, как при центровой токарной обработке. Схемы круглого наружного шлифования показаны на рис. 100.
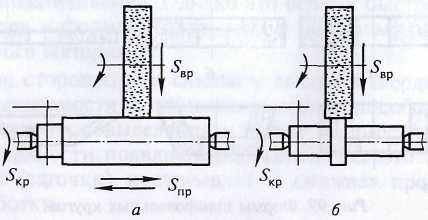
Рис. 100. Схемы круглого наружного шлифования с продольной подачей (а) и врезного (б)
При достаточно большой длине обрабатываемой поверхности заготовка совершает возвратно-поступательное движение продольной подачи Snp вдоль оси (рис. 100, а). При этом она медленно поворачивается в движении круговой подачи S, ДЛЯ образования поверхности вращения.
В конце продольного перемещения заготовки осуществляется поперечная подача (врезание) 5"вр на требуемую глубину резания для следующего прохода. Врезание может производиться на каждый или двойной ход, например только у правого торца заготовки. В конце обработки делается несколько ходов «выхаживания» без поперечной подачи.
Если ширина шлифовального круга больше длины обрабатываемой шейки, то продольная подача не требуется. В этом случае поперечная подача осуществляется непрерывно. Такое шлифование называется врезным (рис. 100, б). При достаточной мощности станка и жесткой системе СПИД его можно выполнять одновременно несколькими шлифовальными кругами, благодаря чему производительность обработки существенно повышается.
Повысить производительность можно также бесцентровым шлифованием (рис. 101). Заготовку располагают на опоре 1 между двумя шлифовальными кругами. Шлифующий круг 2 имеет больший диаметр и совершает быстрое главное движение резания. Ведущий круг 3 прижимает заготовку к шлифующему, придавая ей под действием силы трения медленное движение круговой подачи. Для исключения огранки обработанной поверхности ось заготовки должна располагаться немного выше оси кругов.
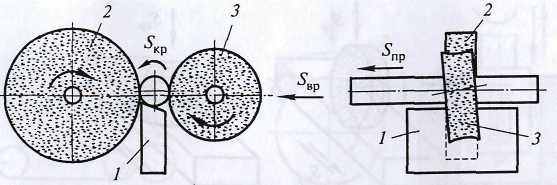
Рис. 101. Схемы наружного бесцентрового шлифования врезного (а) и продольного (б): 1 — опора; 2 — шлифующий круг; 3 — ведущий круг
Если оси кругов параллельны между собой, а длина обрабатываемой шейки меньше их ширины, то продольная подача отсутствует. При большой длине обрабатываемой поверхности ось ведущего круга поворачивают на небольшой угол (до 5°) по отношению к осям заготовки и шлифующего круга. В результате перекрещивания осей появляется осевая составляющая силы резания, под действием которой заготовка перемещается на опоре вдоль своей оси (рис. 101, б).
При внутреннем шлифовании, применяемом для чистовой обработки отверстий, заготовку устанавливают в патроне (рис. 102, а) и медленно поворачивают в движении круговой подачи. Шлифовальный круг, располагающийся внутри обрабатываемого отверстия на консольной оправке, совершает главное вращательное движение и два движения подачи: возвратно-поступательное продольное Snp вдоль оси и поперечное 5вр на каждый двойной ход.
Некоторые внутришлифовальные станки имеют поворотную шлифовальную бабку для обработки конических отверстий. В массовом производстве применяют бесцентровые внутришлифовальные станки.
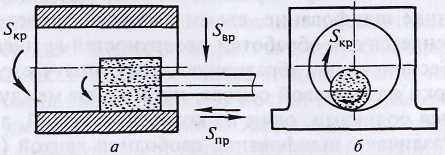
Рис. 102. Схемы внутреннего шлифования в патроне (а) и планетарного (б)
Отверстия в заготовках, которые невозможно установить в патроне из-за больших габаритов или неудобной формы, обрабатывают планетарным внутренним шлифованием (рис. 102, б).
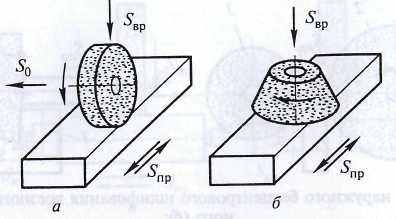
Рис. 103. Схемы плоского шлифования периферией круга прямого профиля (а) и торцом чашечного круга (б)
Заготовка установлена на столе станка и неподвижна, а движение круговой подачи осуществляет шлифовальный круг в результате вращения его оси вокруг оси отверстия. Остальные движения такие же, как при патронном варианте.
Плоские поверхности шлифуют на плоскошлифовальных станках с возвратно-поступательным движением заготовки. При этом обработка выполняется периферией круга прямого профиля (рис. 103, а) или торцом чашечного (рис. 103, б). В последнем случае вследствие относительно большой площади контакта круга и заготовки имеет место значительное тепловыделение, вследствие чего приходится снижать режимы резания.
Тем не менее периферийное шлифование уступает по производительности торцовому, если ширина обрабатываемой поверхности больше ширины круга и требуется поперечная подача So вдоль его оси на каждый или двойной рабочий ход. Диаметр же чашечного круга выбирают таким образом, чтобы он перекрывал обрабатываемую поверхность по ширине полностью или как можно больше, чтобы уменьшить количество ходов.
Для этой цели иногда, особенно в крупносерийном и массовом производствах, используют сегментные круги большого диаметра. На торце их металлического корпуса закреплены на определенных расстояниях друг от друга сегменты из абразивного материала, что способствует лучшему охлаждению зоны резания.
Ленточное шлифование, схемы которого приведены на рис. 104, применяется для обработки поверхностей вращения и плоскостей. «Бесконечную» абразивную ленту, получаемую склеиванием шкурки на тканевой основе, натягивают между двумя вращающимися роликами, один из которых ведущий, а другой натяжной. Различают шлифование свободной лентой (рис. 104, а) и контактное (рис. 104, б).
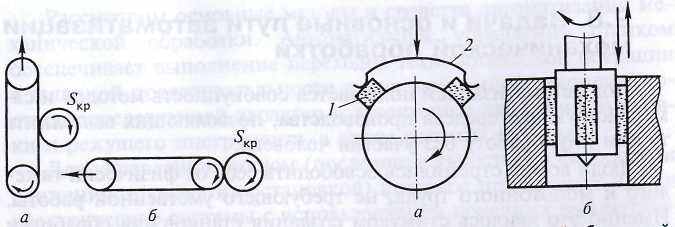
Рис. 104. Схемы ленточного Рис. 105. Схемы отделочной абразивной
шлифования свободной лентой обработки:
(а) и контактного (о) а — суперфиниш; б — хонингование; 1 — абразивный брусок; 2 — пружина
При весьма высоких требованиях к качеству обработанных поверхностей применяют специальные методы окончательной абразивной обработки, называемые отделочными. К ним прежде всего следует отнести механическую притирку (доводку) и полирование, которые в отличие от аналогичной ручной обработки, описанной в 4.2, выполняют на станках.
Высокая точность и чистота наружных цилиндрических поверхностей достигается суперфинишированием, схема которого приведена на рис. 105, а. Обработка производится мелкозернистыми абразивными брусками 1, прижатыми пружиной 2 к обрабатываемой поверхности. Бруски совершают возвратно-поступательное движение с высокой частотой вдоль оси медленно вращающейся заготовки.
Аналогичная обработка отверстий называется хонингованием. Она производится брусками, смонтированными в хонинговальной головке, совершающей вращательное и возвратно-поступательное продольное движения относительно оси заготовки (рис. 105, б). На каждый двойной ход бруски раздвигаются в радиальном направлении на небольшую величину с помощью специального устройства.
Кроме высокой точности хонингование обеспечивает получение перекрестных штрихов шероховатости, благодаря чему уменьшается износ в процессе эксплуатации детали, так как в местах пересечения впадин шероховатостей (так называемых узлах) хорошо удерживается смазка. Хонингование применяют, например, для окончательной обработки цилиндров двигателей внутреннего сгорания.